渣油加氢脱硫装置的设计和试运行
柴油加氢脱硫工艺流程设计与参数优化

柴油加氢脱硫工艺流程设计与参数优化随着环境保护意识的增强和大气污染治理要求的日益严格,柴油加氢脱硫工艺在石油炼制工业中扮演着重要的角色。
本文旨在设计一个高效的柴油加氢脱硫工艺流程,并对关键参数进行优化,以满足环保要求和经济效益。
一、工艺流程设计柴油加氢脱硫工艺主要包括催化剂选择、反应器设计、氢气供应系统以及产物分离装置等。
在设计工艺流程时,需要考虑以下因素:1. 催化剂选择选择合适的催化剂对于工艺的成功实施至关重要。
常用的催化剂包括硫化钴、硫化钼、硫化镍等。
根据柴油的具体要求和工艺条件,选取合适的催化剂。
2. 反应器设计反应器是柴油加氢脱硫工艺中的核心设备,其设计直接影响到反应效果和产物质量。
应根据催化剂的活性、反应物质的浓度等因素确定反应器的体积和长度。
3. 氢气供应系统氢气是柴油加氢脱硫过程中的必要原料,合理的氢气供应系统可以保证反应过程的稳定性和连续性。
应根据柴油加氢脱硫反应速率和反应物的摩尔比例来设计氢气供应系统。
4. 产物分离装置柴油加氢脱硫过程产生的产物中除了脱硫后的柴油,还含有一些杂质和副产物。
为了得到高纯度的柴油产品,需要设计合适的分离装置,包括蒸馏塔、冷凝器等。
二、参数优化在设计柴油加氢脱硫工艺流程时,关键参数的优化对于提高工艺效果和经济效益非常重要。
以下是几个需要优化的关键参数:1. 催化剂用量催化剂的使用量直接影响柴油加氢脱硫反应的效果和成本。
过低的催化剂用量可能导致反应效果不理想,过高的催化剂用量则会增加生产成本。
应通过试验和经验确定合适的催化剂用量。
2. 反应温度反应温度是柴油加氢脱硫工艺中的另一个重要参数。
适当的反应温度可以提高反应速率和脱硫效果,但过高的反应温度会增加能耗和催化剂烧结的风险,过低则会降低反应速率。
应通过试验和模拟计算确定最佳的反应温度。
3. 氢气流量氢气是柴油加氢脱硫反应的重要参与物,适量的氢气流量可以提高反应效果和脱硫程度。
过高的氢气流量会增加成本,过低则会影响脱硫效果。
170万吨、年渣油加氢装置操作法
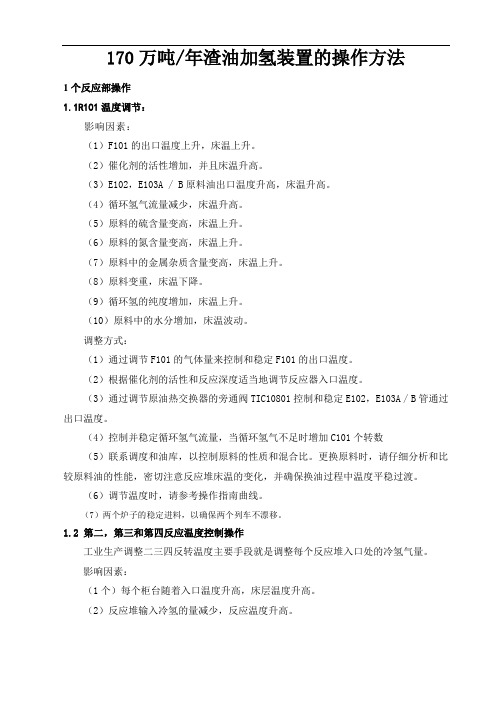
170万吨/年渣油加氢装置的操作方法1个反应部操作1.1R101温度调节:影响因素:(1)F101的出口温度上升,床温上升。
(2)催化剂的活性增加,并且床温升高。
(3)E102,E103A / B原料油出口温度升高,床温升高。
(4)循环氢气流量减少,床温升高。
(5)原料的硫含量变高,床温上升。
(6)原料的氮含量变高,床温上升。
(7)原料中的金属杂质含量变高,床温上升。
(8)原料变重,床温下降。
(9)循环氢的纯度增加,床温上升。
(10)原料中的水分增加,床温波动。
调整方式:(1)通过调节F101的气体量来控制和稳定F101的出口温度。
(2)根据催化剂的活性和反应深度适当地调节反应器入口温度。
(3)通过调节原油热交换器的旁通阀TIC10801控制和稳定E102,E103A / B管通过出口温度。
(4)控制并稳定循环氢气流量,当循环氢气不足时增加C101个转数(5)联系调度和油库,以控制原料的性质和混合比。
更换原料时,请仔细分析和比较原料油的性能,密切注意反应堆床温的变化,并确保换油过程中温度平稳过渡。
(6)调节温度时,请参考操作指南曲线。
(7)两个炉子的稳定进料,以确保两个列车不漂移。
1.2 第二,第三和第四反应温度控制操作工业生产调整二三四反转温度主要手段就是调整每个反应堆入口处的冷氢气量。
影响因素:(1个)每个柜台随着入口温度升高,床层温度升高。
(2)反应堆输入冷氢的量减少,反应温度升高。
(3)反应深度增加并且反应温度升高。
(4)原材料油性质对反应温度的影响与R101相同。
(5)催化剂的活性增加并且床温升高。
(6)循环氢的纯度增加,反应温度升高。
调整方式:(1个)通过监管每个柜台进口冷氢量调整输入口腔温度和床地板温度保持每张床的温度上升≯28℃。
(2)为了防止温度过度波动,温度调节范围应在0.5℃关于。
(3)将转换深度控制在设计范围内。
(4)原材料油当性质改变时,调节反应温度的方法与R101相同。
柴油加氢脱硫工艺流程设计与设备选型

柴油加氢脱硫工艺流程设计与设备选型柴油加氢脱硫是一种常见的燃料处理技术,主要用于去除柴油中的硫元素,提高燃料的环保性能。
本文将对柴油加氢脱硫工艺流程设计以及设备选型进行探讨。
一、工艺流程设计柴油加氢脱硫的工艺流程设计主要包括前处理、加氢反应、脱硫反应和后处理四个步骤。
1. 前处理前处理主要是对原料柴油进行预处理,去除其中的杂质和重金属等有害成分。
常见的前处理步骤包括脱水、脱硫、脱氮和脱尘等。
这些步骤可以通过物理和化学方法来完成,例如使用吸附材料、催化剂和膜分离等技术。
2. 加氢反应加氢反应是柴油加氢脱硫的核心步骤,主要通过将加氢剂与柴油在一定的温度和压力下进行接触,使其发生化学反应。
常见的加氢剂有氢气、石蜡和钴钼催化剂等。
在加氢反应中,硫化物被还原生成硫化氢,从而实现柴油中硫的脱除。
3. 脱硫反应脱硫反应是对加氢反应产物中残留的硫化氢进行进一步处理的过程。
常见的脱硫反应方式有吸收、吸附和化学反应等。
其中,吸收是将硫化氢溶于适当的溶剂中,而吸附则是利用吸附剂吸附硫化氢分子。
化学反应则是通过柴油中的其他成分与硫化氢发生反应,将其转化为无害物质。
4. 后处理后处理主要包括对反应产物的分离和净化。
常见的后处理技术有蒸馏、萃取和析出等。
这些技术能够将脱硫后的柴油进一步提纯,使其符合燃料标准要求。
二、设备选型柴油加氢脱硫的设备选型需要考虑多个方面的因素,包括处理规模、设备投资和使用成本等。
根据处理规模的大小,柴油加氢脱硫设备可以分为小型和大型两种。
小型设备适用于处理较少的柴油量,投资和使用成本较低,但处理效率可能相对较低。
大型设备适用于处理大量柴油,具有较高的处理效率,但投资和使用成本较高。
在设备选型中,还需要考虑设备的稳定性和可靠性。
柴油加氢脱硫设备通常需要在高温高压的工况下运行,在设备选型时要选择质量可靠、性能稳定的设备。
此外,设备的维护和保养也是一个重要的考虑因素。
此外,还需要考虑柴油加氢脱硫设备的能源消耗和环境影响。
渣油加氢脱硫装置试运行技术分析

渣油加氢脱硫装置试运行技术分析摘要:四川石化有限责任公司300万吨/年渣油加氢脱硫装置开工试运行6个月。
结果表明本套渣油加氢脱硫装置设计合理、设备选配适当、催化剂性能优良、活性稳定。
虽然在开工运行中出现个别小问题,但经过小技措改造,目前装置运行平稳。
关键词:渣油加氢脱硫运行技术分析中国石油天然气股份有限公司四川石化分公司300×104t/a渣油加氢脱硫装置采用CLG公司的固定床渣油加氢脱硫工艺技术,以哈萨克斯坦、南疆及北疆原油的减压重蜡油和减压渣油为原料,经过催化加氢反应,进行脱除硫、氮、金属等杂质,降低残碳含量,为催化裂化装置提供原料,同时生产部分柴油,并副产少量石脑油和燃料气。
一、装置概况本装置的原料主要有来自常减压装置的减压渣油、减压重蜡油,来自于渣油原料罐区的减压渣油、减压重蜡混合油,进料中减压渣油与减压重蜡油的混合比例为89.7:10.3。
渣油产品大部分送催化装置,少部分送催化裂化原料罐区;柴油送柴油加氢装置;石脑油送乙烯装置罐区;含硫燃料气送加氢裂化装置脱硫后并入工厂燃料气管网。
含硫富氢气体,送加氢裂化装置脱硫后去PSA 回收氢气。
该工艺技术满足操作周期8000小时,柴油产品硫含量不大于500PPm、加氢常渣产品硫含量不大于0.3w%、残炭不大于5.0w%、Ni+V不大于15PPmwt的指标要求。
装置由美国CLG公司提供工艺包,洛阳石化工程公司负责基础设计和详细设计,中油一建施工。
装置经历了单机试车、联动试车,从2013年1月16日正式引入物料,进入投料试车阶段。
到1月28日正式生产的产品分析合格。
截止5月30日,装置运行平稳,各项产品指标合格。
1.本装置的主要工艺技术特点有:1.1采用上流式反应器。
反应部分设置两个系列,每个系列可以单开单停(单开单停是指装置内二个系列分别进行正常生产和停工更换催化剂)。
由于渣油加氢脱硫装置的设计操作周期与其它主要生产装置不一致,从全厂生产安排的角度,单开单停可以有效解决原料储存、催化裂化装置进料量等问题,并使全厂油品调配更灵活。
生产一区常压渣油加氢脱硫ARDS装置

8-V-06装置防雷防静电接地
5-V-01A装置防雷防静电接地
V-07装置防雷防静电接地
5-V-01B装置防雷防静电接地
V-08装置防雷防静电接地
4-F-01装置防雷防静电接地
V-09装置防雷防静电接地
5-V-01C装置防雷防静电接地
5-E-05装置防雷防静电接地
8-V-11A装置防雷防静电接地
V-01装置防雷防静电接地
E-01装置防雷防静电接地
3-E-06/AB装置防雷防静电接地
6-V-01装置防雷防静电接地
3-E-05/AB装置防雷防静电接地
3-H-01装置防雷防静电接地
V-26装置防雷防静电接地
联合烟囱
3-E-09/AB装置防雷防静电接地
1-R-04装置防雷防静电接地
1-R-02装置防雷防静电接地
7#
8#
9#
10#
11#
12#
13#
14#
15#
16#
17#
18#
19#
20#
21#
22#
23#
24#
25#
26#
27#
28#
29#
30#
31#
32#
33#
34#
35#
36#
37#
38#
39#
40#
41#
42#
43#
44#
45#
46#
47#
48#
49#
50#
51#
52#
53#
54#
55#
56#
57#
5-V-06装置防雷防静电接地
3-V-103B装置防雷防静电接地
渣油加氢装置工艺参数及产品质量控制方法

渣油加氢装置工艺参数及产品质量控制方法10.3.1加氢反应器R-l01入口温度反应温度是反应部分的最主要工艺参数,是脱硫,脱氮效果的主要变量,是加氢精制的重要调节参数。
反应温度主要根据原料油的性质、反应进料量、催化剂活性和产品的质量要求等因素进行选择。
操作的最佳温度是满足产品质量的最低温度。
控制目标:指令值的±1℃控制范围:375~390℃相关参数:反应炉两路出口温度TIC10501A 、TIC10501B;燃料气压控PIC10506A、PIC10506B;热高分入口温度TIC10801;反应进料量FIC10303;循环氢流量FI10901及纯度等。
控制方式:R-l01入口温度是由TIC10501A 、TIC10501B分别串级F101燃料气压控PIC10506A、PIC10506B通过控制燃料气量来实现的,如图所示。
设置的温控TIC10801是通过调整进出换热器的物料量来控制热高分入口温度。
当满足热高分温度时,应尽量关小TIC10801提高F101入口温度,减少瓦斯消耗。
反应炉负荷过小时,为了反应炉正常的燃烧,保证反应器入口温度稳定,可以适当调节TIC10801的开度,给F101以一定的调节余量,以便于反应入口温度的灵活调节。
提降温度和进料量应遵循先提量后提温,先降温后降量的原则。
影响因素:(1)F101的出口温度升高,床层温度上升。
(2)催化剂的活性提高,床层温度上升。
(3)E102、E103A/B的原料油出口温度提高,床层温度上升。
(4)循环氢流量减小,床层温度上升。
(5)原料含硫量变高,床层温度上升。
(6)原料含氮量变高,床层温度上升。
(7)原料中金属杂质含量变高,床层温度上升。
(8)原料变重,床层温度下降。
(9)循环氢纯度提高,床层温度上升。
(10)原料含水增加,床层温度波动。
调节方法:(1)通过调节F101的瓦斯量来控稳F101的出口温度。
(2)根据催化剂表现的活性和反应深度适当调整反应器入口温度。
渣油加氢装置运行中存在问题及解决措施

渣油加氢装置运行中存在问题及解决措施摘要:经济发展和时代的发展趋势进一步促进了炼油厂工业生产的发展趋势,而渣油加氢加工工艺以及机器设备做为当中的关键环节,对所有领域的进步有着至关重要的危害。
与此同时,在渣油的生产加工中,渣油加氢装置可以提升油品质量。
殊不知,因为多种缘故,渣油加氢装置在运转环节中常常出现异常,不能合理提升油品质量。
对渣油加氢装置运作中存在问题开展了剖析,并指出了相对的解决方案。
关键词:渣油加氢工艺;装置运行引言:伴随着社会经济的飞速发展,现阶段大家已经离不了石油。
在炼油厂工业生产的发展趋势中,必须借助渣油加氢加工工艺以及机器设备,对渣油开展生产加工和过滤,提升油品质量,为大家的日常生活给予协助。
但机器设备存在的不足会限定油品质量和加氢裂化机器设备的功效。
仅有不断完善和提升,才可以更好地发挥功效。
一、渣油加氢装置工艺重要性固定床渣油加氢加工工艺做为现阶段最成熟稳定的工艺,在渣油加氢加工工艺中占主导性。
因为原料油的复杂和劣质性及其固定床反应釜的特性,固定床渣油加氢装置的运行周期时间较短,通常仅有一年,有的装置运行2年,而做为冶炼厂关键生产制造装置的催化裂化装置的运行周期时间大多数在三年以上,造成渣油加氢装置和催化裂化装置的运行周期时间不配对。
渣油加氢停产期内,必须对催化裂化原料开展更新以确保正常的运行,这对公司的石油选购和配制明确提出了很高的规定,对公司的经济收益造成了危害。
因而,消除影响渣油加氢装置平稳运行的多种要素,适度增加渣油加氢装置的运行时长具备关键实际意义。
在其中,渣油加氢装置应用的原料主要是常减压装置的常压渣油和减压渣油的混合物质。
最后产品是脱硫、脱氮、脱金属材料、脱残炭的加氢渣油,所占比例大,也会形成小量的石脑油和柴油。
生产制造的渣油可以为催化裂化装置的原料,降低焦炭的生成,大大提高催化裂化装置的产量,并对催化裂化装置生产制造的柴油和汽油的提质增效。
因而,渣油加氢装置的运转效果和质量对全部炼油厂工业生产至关重要。
170万渣油加氢装置培训资料装置操作法

170万渣油加氢装置培训资料装置操作法渣油加氢装置(Residue Hydrocracking Unit)是炼油厂中的一种重要设备,主要用于转化高温渣油中的重油组分,将其转化为高质量的轻质产品,以提高产品质量和增加产能。
以下是关于渣油加氢装置操作法的一些培训资料,共计1200字以上。
一、渣油加氢装置的工作原理和主要设备渣油加氢装置主要通过催化剂的作用,在高温高压的条件下将渣油中的重油组分进行裂解和重整,得到较为轻质的产品。
主要包括以下工艺流程和设备:1.进料处理:将渣油经过预热和脱盐等处理后进入催化剂床层。
2.加氢反应:在催化剂床层中,将渣油与氢气混合后,在高温高压的条件下进行化学反应,催化剂起到催化作用。
3.催化剂再生:催化剂在反应过程中逐渐失活,需要进行再生,去除积聚在催化剂上的杂质和炭质。
4.产品分离和净化:经过反应后的物料通过分离装置进行产品分离,得到不同质量级别的轻质产品。
二、装置操作注意事项1.操作前准备:操作人员应在操作前检查催化剂床层情况、催化剂再生设备等操作部位的状态。
2.安全操作:操作人员应穿戴个人防护装备,并熟悉工艺流程和装置设备的安全操作规程。
3.温度和压力控制:操作人员应控制好加氢反应的温度和压力,确保在正常工作范围内。
4.操作流程控制:按照工艺操作规程,控制好物料的进料速度、催化剂再生周期、产品分离装置的操作等,确保装置的正常运行。
5.催化剂管理:操作人员应监测催化剂的性能和活性,及时更换并处理废催化剂。
6.灾害防范:操作人员应时刻注意装置的安全状况,避免发生火灾、爆炸等意外事故,并及时响应紧急情况。
三、装置操作技巧1.合理调整操作参数:根据渣油的性质和产品要求,合理调整加氢反应的温度、压力和催化剂用量等操作参数,以达到最佳反应效果。
2.善于处理异常情况:操作人员应具备处理异常情况的能力,如催化剂塌陷、过压、过热等情况,及时采取相应的措施。
3.及时维护设备:对于装置设备的维护保养工作,应及时进行,保证装置的正常运行和使用寿命。
- 1、下载文档前请自行甄别文档内容的完整性,平台不提供额外的编辑、内容补充、找答案等附加服务。
- 2、"仅部分预览"的文档,不可在线预览部分如存在完整性等问题,可反馈申请退款(可完整预览的文档不适用该条件!)。
- 3、如文档侵犯您的权益,请联系客服反馈,我们会尽快为您处理(人工客服工作时间:9:00-18:30)。
) 2)
炼油设计
2000 年第 30 卷
位控制采用双套调节阀; » 热高压分离器液位采 用射线液位开关进行报警和自保联锁。
设计 标定 设计 标定 设计 标定
密度( 20 e ) / kg#m- 3
758. 2 748. 1 867. 5 868. 2 927. 5 932. 2
硫含量/ Lg#g- 1
15 3 019* 150 160 5 200 4 200
氮含量/ Lg#g- 1
15 2. 2 305 80. 58 1 500 1 290
一的渣油加氢脱硫( S- RHT) 工艺技术及渣油加氢 系列催化剂, 实现了工艺技术和工程设计的国产 化, 结束了渣油加氢技术依赖进口的局面。
¦ 采用催化剂分级装填技术, 不设置保护床 反应器, 每台反应器均采用单床层。
§ 反应部分从加氢进料泵后至循环氢脱硫 前采用并列的两个系列。
¨ 为保证反应所需氢分压, 设置循环氢提浓 设施, 该设施为目前规模最大( 40. 0 dam3/ h) 的高 压氢气膜分离设施。
1 工艺流程 该装置由反应( 含压缩机、循环氢脱硫、循环
氢提浓) 、分馏、气体脱硫及公用工程等部分组成 ( 见图 1) 。反应部分从加氢进料泵后至循环氢脱 硫前分为并列的两个系列, 每一系列包括反应进 料加热炉、串联的 5 台加氢反应器、独立的高压换 热器及冷、热高压分离器等。
2 装置的主要技术特点 ¥ 采用 SINOPEC/ 九#五0十条龙攻关项目之
表 5 第 Ó 套 RFCC 装置 全部加工脱硫渣油的产品性质
项目
汽油 加工脱硫渣油前 加工脱硫渣油后
柴油 加工脱硫渣油前 加工脱硫渣油后
密度( 20e ) / g#cm- 3
0. 722 4
0. 724 9
0. 894 1
0. 949 1
腐蚀
合格
合格
酸度/ mgKOH#( 100mL) - 1
0. 45
主题词: 减压渣油 加氢脱硫 设计 催化裂化 原料
茂名石油化 工公司 2. 0 Mt / a 渣油加氢脱硫 装 置 ( S- RHT ) 是 中 国 石 油 化 工 集 团 公 司 ( SINOPEC) / 九#五0 期间/ 十条龙0 科技攻关项目 之一, 采用抚顺石油化工研究院( FRIPP) 开发的固 定床渣油加氢脱硫工艺技术及渣油加氢系列催化 剂, 由洛阳石油化工工程公司( LPEC) 承担该项目 的工程技术开发、工程设计和总承包。该装置于 1998 年完成详细设计, 1997 年 6 月破土动工, 1999 年 12 月一次投产成功。
装置设计的原料为沙特阿拉伯轻质原油减压 渣油、伊朗原油减压渣油及伊朗原油减压蜡油的 混合原料, 其主要产品加氢脱硫渣油( 下称脱硫渣 油) 能满足重油催化裂化( RFCC) 进料性质要求, 最终实现渣油的完全转化, 该装置同时生产部分 优质柴油馏分和石脑油。
开工及试运结果表明, 该装置工艺技术先进, 工艺流程的设计先进合理并具有灵活性, 工程设 计满足生产需要, 各项技术指标都达到或超过设 计及攻关目标。
炼油设计
2000 年第 30 卷
率有所下降, 液化石油气中饱和烃增加。汽油、柴 烃含量降低了约 10 个单位, 有利于全厂汽油调合
油的产品性质见表 5。与未加工 S- RHT 脱硫渣油 和生产烯烃含量< 35% 的清洁燃料要求。柴油的
相比, 裂化汽油的胶质明显下降, 诱导期延长, 烯 硫含量也有较大幅度下降。
2000 年 7 月
炼油设计 PETROLEUM REFINERY ENGINEERING
第 30 卷 第 7 期
加工工艺
渣油加氢脱硫装置的设计和试运行
朱华兴 刘景洲
洛阳石油化工工程公司( 河南省洛 阳市 471003)
摘要: 介绍由洛阳石油化工工程公司总承包的茂名石 油化工公司 2. 0 Mt / a 渣 油加氢脱 硫装置的 设计概况、主 要技术特点和运行情况。从装置运行初期的标定数据和设计 数据的对 比, 对有关 操作条件、产品性质 等进行了 分 析。装置以减压渣油和减压蜡油的混合油为原料, 脱硫渣油完 全满足重 油催化裂 化原料性 质的要求, 为最终实 现 渣油的完全转化创造了条件。
¬反应进料加热炉的对流段加热分馏塔的 轻油进料, 使装置的热量平衡及流程更趋于优化。 辐射段每一管程设单独的辐射室, 并在炉管两面 设置火嘴, 使炉管受热均匀, 减少结焦倾向。同时 反应炉还设置侧墙火嘴, 以便必要时提高炉子的 热负荷。
完善可靠的自保联锁系统: ¹ 高、低压有 串压危险时, 采用自保切断阀; º 热高压分离器液
± 设备实现了大型化、国产化。实现了国内 最大直径( 4. 2 m) 加氢反应器及其内构件的工程 设计和设备制造的国产化; 设计了直径为 1. 8 m,
单台换热面积达 1 400 m2 的渣油蒸汽发生器; 设 计选用了国产化最大功率( 轴功率 3 315 kW) 的氢 气压缩机。
² 循 环 氢 压 缩 机 采 用 TBS 密 封 ( Trapped Bushing Seal) , 简化了机组流程, 省掉了高压的气 封气冷却器和气封气分液罐, 便于生产操作。
图 1 S-RHT 装置工艺流程
3 S-RHT 的试运及初期标定情况 3. 1 初期运行及标定概况
该装置自开汽以来, 运行平稳, 处理量一直保 持 80% 负荷, 脱硫渣油产品合格率达 100% , 满足 Ó套催化裂化装置全炼常压渣油的要求。为了考 察装置的处理能力、国产催化剂的性能和主要设 备、操作单元的运行情况, 于 2000 年 2 月 21~ 23 日对装置进行了初期满负荷标定, 标定数据及与 设计的对比见表 1~ 4 。装置设计能耗为 1 213. 7
Ni V
初期标定 987. 8 79. 73 7 3. 32 2 797 12. 64
设计 987. 5 200
18 3. 10 2 800 12. 88
18. 9
26. 8
51. 9
83. 8
Fe
5. 7
<5
Na
0. 28
<3
Ca
1. 07
<5
表 2 主要产品的性质Βιβλιοθήκη 项目石脑油柴油
脱硫渣油
C5~ 160 e 馏分 160~ 350 e 馏分 350 e + 馏分
101. 60
* 工业标定氢耗为总氢耗, 设计基础氢耗为化学氢耗。
4 催化裂化装置全部加工脱硫渣油的情况 茂名石油化工公司 Ó套重油催化裂化装置在
S-RHT 装置投产后全部改为加工脱硫渣油, 并进 行了两次满负荷标定。标定结果表明全部加工脱 硫渣油时, 总轻油产品收率与原设计相当, 干气产
) 4)
重金属( Ni+ V) 含量与设计指标相当。由于杂质
含量较低, 此加氢脱硫渣油可直接作为 RFCC 装
置的进料, 达到了设计要求。
¨ 标定期间反应物料平衡及产品分布: 由于 标定的反应温度较低, 导致渣油加氢转化率较低, 因此相对于设计基础, 氢耗、柴油产率、气体产率 较低, 尾油产率较高。但是高转化率并不是固定 床渣油加氢工艺技术追求的目标, 在产品合格和 加氢脱硫渣油可直 接进 RFCC 装置的前提下, 低 反应温度、低转化率有利于延长开工周期和催化
Ñ 125. 3( 125) 0. 20( 0. 20)
86. 1 678( 650) 355. 7( 385) 15. 56( 15. 7)
346. 7 349
350. 2 362. 2 364. 9
1. 29
Ò 125. 2 0. 20 86. 0
679 356. 1 15. 56
347. 1 349. 3 351. 1 362. 2 365. 1
剂的使用寿命。
表 3 设计和初期标定主要操作条件
反应系列 进料/ t#h- 1 体积空速/ h- 1 混氢量/ dam3#h- 1 第一反应器入口气油体积比 各反应器总加权平均反应温度/ e 系统压力/ MPa 床层平均温度分布 / e
第一反应器 第二反应器 第三反应器 第四反应器 第五反应器 反应器压力降/ MPa 第一反应器~ 第五反应器
³ 由于该装置加工的是渣油, 易凝易堵, 所 以设置了冲洗油系统。原料油系统和分馏塔塔底 油系统的机泵、管道, 均设有固定的冲洗油管道。
´ 设置了高压仪表冲洗油系统, 由高压柱塞 泵连续注入易凝易堵部分的仪表引压管和液位计 引出管, 冲洗介质选用机械透平油。
µ 增加氢气优化利用 措施。将热低压分离 器溶解的氢气单独设置脱硫塔, 脱硫后的氢气回 收利用, 减少了装置的用氢量。
损失 合计
6. 699 0. 436 1. 480 4. 242 12. 042 212. 211 0. 738
2. 859 0. 186 0. 632 1. 810 5. 139 90. 560 0. 315 101. 501
2. 80 0. 16 1. 97 1. 90 10. 22 84. 55
压力降均十分接近, 说明两系列反应物流分配合 理, 无偏流现象发生。
表 1 设计和初期标定的原料油性质
项目 密度( 20e ) / kg#m- 3 运动粘度( 100 e ) / mm2#s- 1 凝点/ e 硫质量含量, % 氮含量 / Lg#g- 1 康氏残炭, % 重金属含量/ Lg#g- 1
凝点/ e
- 15 - 10
8
十六烷值
38. 4 47
康氏残炭, %
6. 48 5. 98
重金属含量/ Lg#g- 1
Ni