渣油加氢工艺流程
石油化工技术《加氢处理工艺流程(二)》

扬州工业学院信息化设计教案下面这张图所示。
我们来详细解读一下这个工艺流程。
首先,柴油馏分与加氢生成油在换热器中换热后,进入加热炉中,在加热炉出口与循环氢混合,依次进入串联的两个加氢处理反响器。
加氢生成油经过与循环氢、分馏塔进料和原料油换热后注入软化水,以清洗加氢反响过程中生成的氨和硫化氢,防止生成多硫化铵或其他铵盐堵塞设备。
然后经过冷却,再进入高压别离器,别离出含铵盐的污水排出。
高压别离器别离出的循环氢大局部进入分液器,进一步别离出携带的油滴后,进入循环氢压缩机,并在加氢系统中循环使用,另一局部循环氢作为燃料气排出装置。
加氢过程中消耗的氢气由新氢压缩机提供。
加氢生成油分出循环氢后经减压进入低压别离器,别离出的燃料气从顶部排出装置,底局部离出的油品与加氢生成油换热后进入分馏塔,分馏塔底部吹入过热水蒸气,以保证柴油的闪点合格。
塔顶油气经冷凝冷却后进入油水别离罐,别离出的汽油一局部回流分馏塔内,其余送出装置。
分馏塔底部出来的就是柴油馏分。
〔小组讨论教师总结〕二、渣油加氢处理工艺流程具体讲授:接下来要介绍的是渣油加氢处理工艺流程。
我们知道渣油就是石油经蒸馏加工后剩余的残渣,其中的杂质含量相当高,其加工难度要比汽油、柴油的大得多,因此渣油加氢处理就需要更苛刻的反响条件以及更高效的催化剂。
下面这张图是齐鲁石化公司减压渣油加氢脱硫装置的工艺流程图。
其工艺流程与前面介绍的汽柴油的加氢处理工艺流程相似,主要还是有这三个局部组成:即固定床加氢反响系统,加氢生成油别离系统以及循环氢系统。
这里我们就不详细给同学们解读渣油加氢处理的工艺流程图了,因为其根本原理是跟前面介绍的汽油、柴油的加氢处理工艺流程图是相同的。
齐鲁石化VRDS装置流程〔小组讨论教师总结〕。
渣油加氢操作规程
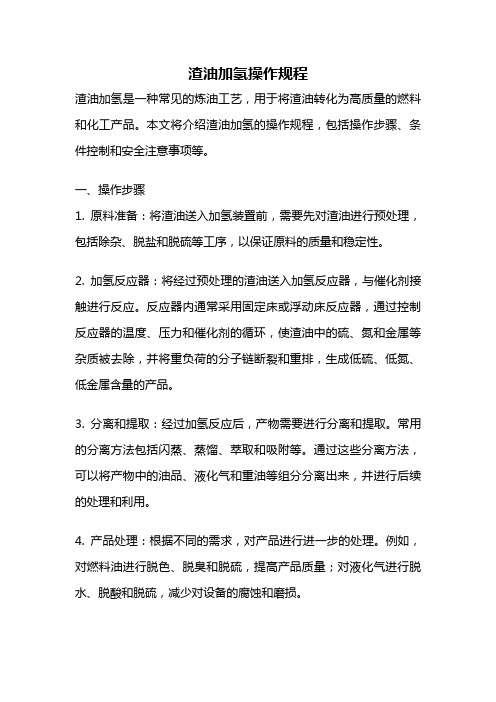
渣油加氢操作规程渣油加氢是一种常见的炼油工艺,用于将渣油转化为高质量的燃料和化工产品。
本文将介绍渣油加氢的操作规程,包括操作步骤、条件控制和安全注意事项等。
一、操作步骤1. 原料准备:将渣油送入加氢装置前,需要先对渣油进行预处理,包括除杂、脱盐和脱硫等工序,以保证原料的质量和稳定性。
2. 加氢反应器:将经过预处理的渣油送入加氢反应器,与催化剂接触进行反应。
反应器内通常采用固定床或浮动床反应器,通过控制反应器的温度、压力和催化剂的循环,使渣油中的硫、氮和金属等杂质被去除,并将重负荷的分子链断裂和重排,生成低硫、低氮、低金属含量的产品。
3. 分离和提取:经过加氢反应后,产物需要进行分离和提取。
常用的分离方法包括闪蒸、蒸馏、萃取和吸附等。
通过这些分离方法,可以将产物中的油品、液化气和重油等组分分离出来,并进行后续的处理和利用。
4. 产品处理:根据不同的需求,对产品进行进一步的处理。
例如,对燃料油进行脱色、脱臭和脱硫,提高产品质量;对液化气进行脱水、脱酸和脱硫,减少对设备的腐蚀和磨损。
二、条件控制1. 温度控制:加氢反应需要在一定的温度范围内进行,通常在300-450摄氏度之间。
温度过低会导致反应速率慢,温度过高则会引起催化剂的失活和热力学反应的副产物生成。
2. 压力控制:加氢反应需要一定的压力条件,通常在10-30兆帕之间。
高压可以促进反应速率和产物质量的提高,但同时也会增加设备成本和操作难度。
3. 催化剂选择:催化剂是加氢反应的核心,对反应效果起着决定性的影响。
选择合适的催化剂可以提高反应效率和产物质量,同时也需要注意催化剂的稳定性和寿命。
4. 氢气供应:加氢反应需要大量的氢气供应,通常通过压缩空气或氢气制备装置供应。
氢气的纯度和供应稳定性对反应效果和设备安全具有重要影响。
三、安全注意事项1. 加氢反应是一种高温、高压的化学过程,需要严格控制操作条件和设备安全性。
操作人员应穿戴好防护装备,严格遵守操作规程,确保人身安全。
渣油加氢处理技术

渣油加氢处理技术渣油加氢处理技术是一种重要的炼油技术,可以将高凝固点、高黏度、高硫等低品质石油产品转化为高品质的燃油和化工原料。
该技术已经成为世界上许多石油公司进行渣油处理的主要方法。
本文将对渣油加氢处理技术进行更详细的介绍。
一、渣油加氢处理技术的基本原理渣油加氢处理技术是通过在高压条件下将渣油与氢气进行反应,加氢裂化和氢解等化学反应,将渣油中难以分解的长链烃、多环芳烃和含酸、硫、氮等杂质转化为具有稳定性能的低含杂油品,以此提高油品品质,实现资源的最大化利用。
渣油加氢处理技术的反应过程主要分为以下几个步骤:1.加氢裂化:由于渣油中含有较多的长链烃和多环芳烃,会影响油品的流动性和燃烧性能。
在高温、高压和氢气的作用下,长链烃和多环芳烃被裂化成较短的链烃和芳烃,从而提高油品的流动性和燃烧性能。
2.脱氮脱硫:渣油中含有较多的含氮、含硫杂质,这些杂质会对环境和设备都造成不良影响。
在高温、高压和氢气的作用下,氮、硫杂质被脱除或转化为无毒、无害的氮气和二氧化硫。
3.重整反应:在加氢反应中,芳香族化合物也会遭受损失,因此需要进行重整反应,使芳香族化合物的产生和消耗相互平衡,以保证油品的质量。
整个反应过程需要控制一系列反应参数,包括反应温度、反应压力、氢气流量、加氢速率和催化剂种类等,以获得最佳的反应效果和油品品质。
二、渣油加氢处理技术的应用渣油加氢处理技术可以将低品质石油产品转化为高品质的燃油和化工原料,提高燃油产出,降低能耗和环境污染。
在现代炼油行业中,渣油加氢处理技术已经得到广泛应用,成为炼油企业提高经济效益和技术水平的重要手段。
渣油加氢处理技术的应用主要包括以下几个方面:1.生产高质量柴油:渣油加氢处理技术可以将高凝固点的渣油转化为低凝固点的柴油,减少低温时柴油的结冰现象,提高柴油的稳定性和流动性能。
2.生产航空燃油:渣油加氢处理技术可以将渣油中的硫和芳香族化合物降到目标值以下,获得高品质的航空燃油,满足航空工业对燃油质量的严格要求。
渣油加氢工艺标准说明

第一节工艺技术路线及特点一、工艺技术路线300×104t/a渣油加氢脱硫装置采用CLG公司的固定床渣油加氢脱硫工艺技术,该工艺技术满足操作周期8000h、柴油产品硫含量不大于500ppm、加氢常渣产品硫含量不大于0.35w%、残炭不大于5.5w%、Ni+V 不大于15ppm的要求。
二、工艺技术特点1、反应部分设置两个系列,每个系列可以单开单停(单开单停是指装置内二个系列分别进行正常生产和停工更换催化剂)。
由于渣油加氢脱硫装置的设计操作周期与其它主要生产装置不一致,从全厂生产安排的角度,单开单停可以有效解决原料储存、催化裂化装置进料量等问题,并使全厂油品调配更灵活。
2、反应部分采用热高分工艺流程,减少反应流出物冷却负荷;优化换热流程,充分回收热量,降低能耗。
3、反应部分高压换热器采用双壳、双弓型式,强化传热效果,提高传热效率。
4、反应器为单床层设置,易于催化剂装卸,尤其是便于卸催化剂。
5、采用原料油自动反冲洗过滤器系统,滤除大于25μm以上杂质,减缓反应器压降增大速度,延长装置操作周期。
6、原料油换热系统设置注阻垢剂设施,延长操作周期,降低能耗,而且在停工换剂期间可减少换热器和其它设备的检修工作。
7、原料油缓冲罐采用氮气覆盖措施,以防止原料油与空气接触从而减轻高温部位的结焦程度。
8、采用炉前混氢流程,避免进料加热炉炉管结焦。
9、第一台反应器入口温度通过调节加热炉燃料和高压换热器旁路量来控制,其他反应器入口温度通过调节急冷氢量来控制。
10、在热高分气空冷器入口处设注水设施,避免铵盐在低温部位的沉积。
11、循环氢脱硫塔前设高压离心式分离器除去携带的液体烃类,减少循环氢脱硫塔的起泡倾向,有利于循环氢脱硫的正常操作。
12、设置高压膜分离系统,保证反应氢分压。
13、冷低压闪蒸罐的富氢气体去加氢裂化装置脱硫后去PSA回收氢气。
14、新氢压缩机采用二开一备,每台50%负荷,单机负荷较小,方便制造,且装置有备机。
渣油加氢工艺流程

渣油加氢工艺流程渣油加氢工艺是一种将高硫、高含蜡的渣油通过加氢反应降低硫含量和提高产品质量的工艺。
该工艺的主要流程包括预处理、加氢反应和分离三个步骤。
首先是预处理步骤。
在这一步骤中,渣油经过加热后进入预加热器,以达到合适的反应温度。
然后,预加热后的渣油进入加工器,在这个设备中与一定量的催化剂进行接触。
接触时间的长短和温度的高低可以根据实际需求进行调整。
在接触过程中,催化剂能够去除渣油中的杂质,如硫、氮和有机蜡,从而减少对后续催化剂的影响,并提高反应效率。
接下来是加氢反应步骤。
预处理后的渣油进入加氢反应器,与高效加氢催化剂接触,进行加氢反应。
在加氢反应中,渣油中的硫、氮和重蜡等杂质会与催化剂发生作用,从而被还原、分解或结构改变,生成较少含硫、含氮和较轻的石蜡等反应产物。
加氢反应的条件通常包括反应温度、压力和催化剂的加载量。
较低的反应温度和较高的压力可以提高催化剂的活性,加速杂质的去除。
此外,催化剂的特性也会对反应结果产生一定影响。
最后是分离步骤。
在加氢反应后,反应物进入分离器进行相应的处理。
分离过程主要通过不同组分的沸点差异实现,包括气液分离和液液分离。
液相分离主要是通过凝固和冷凝的方式,使较重的组分凝结成液体,而较轻的组分则通过冷凝回收。
气相分离则利用分析和纯化设备,对气体中的各种组分进行分别处理,从而得到高纯度的产品。
总的来说,渣油加氢工艺流程包括预处理、加氢反应和分离三个步骤。
通过预处理可以去除渣油中的杂质,提高反应效率;加氢反应则通过与催化剂的作用,将渣油中的硫、氮和重蜡等杂质转化为较少含硫、含氮和较轻的石蜡等反应产物;最后的分离步骤则通过不同组分的沸点差异,将反应产物进行分离和纯化,得到高质量的产品。
渣油加氢工艺在石油化工行业中具有重要的应用价值,能够有效改善石油产品的质量,并满足环保要求。
渣油加氢现场操作规程

渣油加氢现场操作规程10.4.1高压换热器操作方法10.4.1.1使用前的检查、准备工作1)检查换热器静电接地是否良好。
2)检查地脚螺栓及各联接法兰螺栓是否松动。
(滑动端应留有间隙)3)检查换热器壳体表面有无变形、碰伤裂纹、锈蚀麻坑等缺陷。
4)检查内、外圈顶丝是否拧紧、顶丝数量是否齐全。
5)气密试验与系统一起进行, 试验时,要检查信号孔有无泄漏现象。
10.4.1.2换热器的投用和停用1)在投用换热器前应首先检查放空阀是否关闭。
2)投用换热器时应先开冷流,后开热流。
停用时应先停热流,后停冷流。
3)在投用过程中,先开出口,后开入口,防止憋压。
4)在投用过程中,热流侧开关阀门要缓慢,防止因升温过快而出现泄漏。
5)用蒸汽吹扫换热器时,吹扫一程时,要将另一程的放空阀或进出口阀打开,防止介质受热膨胀而憋压。
引蒸汽时要缓慢,以防水击。
6)要经常检查换热器的温度、压力是否正常,管壳程是否有内漏,头盖、丝堵、法兰、放空阀等有无渗漏。
10.4.1.3使用中的注意事项1)严禁超温、超压,以免影响使用寿命及损坏设备2)严禁换热器单面受热,以免发生泄漏,一旦发生泄漏,应及时做相应处理。
3)严禁升降温速度过快,流量调节要缓慢。
4)正常使用中注意检查信号孔有无泄漏。
如果有,应将顶丝拧紧,拧紧顶丝时要包含所有顶丝。
5)检查换热器的膨胀量。
6)系统升压时,高压换热器两侧的压差要小于规定值,以免出现内漏现象。
10.4.2低压换热器操作方法10.4.2.1使用前的检查准备工作1)检查换热器静电接地是否良好。
2)检查地脚螺栓及各联接法兰螺栓是否松动。
(滑动端应留有间隙)3)检查出入口阀门是否完好,手轮是否齐全好用。
4)检查换热器壳体表面有无变形、碰伤裂纹、锈蚀麻坑等缺陷。
5)检查温度、压力表等仪表是否好用6)试压合格后,方可使用;10.4.2.2使用时的注意事项1)严禁超温、超压,以免影响使用寿命及损坏设备2)严禁换热器单面受热,以免发生泄漏,一旦发生泄漏,应及时切除。
渣油加氢
≯4.0 ≯13.0 ≯130 ≯5.0
•
新氢:新氢纯度≮90v%;CO+CO2< 30µ g/g(其中CO < 10µ g/g);氯含量< 1.0L/L。
渣油加氢设计
渣油加氢工艺控制
• • • • • • 一反入口氢分压 催化剂体积空速 反应器入口氢油体积比 循环氢纯度 反应温度 总压降
FRIPP
• 7、PSA或重整:提供合格氢气;
• 8、常减压:接收气体 • 9、酸性水:接收酸性水 • 10、硫磺:接收酸性气
渣油加氢建设期安装
• 建设期安装:
FRIPP
• 1 、基础施工:反应器、塔、循环氢压缩机、
新氢压缩机、高压换热器、高压泵等
• 2、地管施工
• 3、钢结构安装 • 4 、换热器、加热炉安装;塔安装;机组安装; 泵安装;
FRIPP
循环氢中硫化氢 浓度,v%
1000(2h),500 4/0 (进VGO) (3h)/-0/-0/-8/8 8/8
渣油加氢开停工
• 停工主要步骤:
FRIPP
• 1、降温降量、切进料
• 2、热氢带油,分馏退油 • 3、反应系统氮气置换 • 4、分馏系统吹扫
渣油加氢首次开车
• 首次开工主要步骤:
渣油加氢工艺流程
渣油加氢流程
FRIPP
• 最终反应产物经过换热降温后进入热高压分离 器进行气液分离。热高分油进入热低压分离器 进行闪蒸分离。热高分气分别与反应进料、混 合氢换热后,进入热高分气空冷器,经冷却后 进入冷高压分离器进行气、油、水三相分离。 冷高分气体(循环氢)经循环氢脱硫塔脱除 H2S,并经循环氢压缩机升压后,循环回反应 部分。
渣油加氢设计
170万渣油加氢装置培训资料装置操作法
170万渣油加氢装置培训资料装置操作法渣油加氢装置(Residue Hydrocracking Unit)是炼油厂中的一种重要设备,主要用于转化高温渣油中的重油组分,将其转化为高质量的轻质产品,以提高产品质量和增加产能。
以下是关于渣油加氢装置操作法的一些培训资料,共计1200字以上。
一、渣油加氢装置的工作原理和主要设备渣油加氢装置主要通过催化剂的作用,在高温高压的条件下将渣油中的重油组分进行裂解和重整,得到较为轻质的产品。
主要包括以下工艺流程和设备:1.进料处理:将渣油经过预热和脱盐等处理后进入催化剂床层。
2.加氢反应:在催化剂床层中,将渣油与氢气混合后,在高温高压的条件下进行化学反应,催化剂起到催化作用。
3.催化剂再生:催化剂在反应过程中逐渐失活,需要进行再生,去除积聚在催化剂上的杂质和炭质。
4.产品分离和净化:经过反应后的物料通过分离装置进行产品分离,得到不同质量级别的轻质产品。
二、装置操作注意事项1.操作前准备:操作人员应在操作前检查催化剂床层情况、催化剂再生设备等操作部位的状态。
2.安全操作:操作人员应穿戴个人防护装备,并熟悉工艺流程和装置设备的安全操作规程。
3.温度和压力控制:操作人员应控制好加氢反应的温度和压力,确保在正常工作范围内。
4.操作流程控制:按照工艺操作规程,控制好物料的进料速度、催化剂再生周期、产品分离装置的操作等,确保装置的正常运行。
5.催化剂管理:操作人员应监测催化剂的性能和活性,及时更换并处理废催化剂。
6.灾害防范:操作人员应时刻注意装置的安全状况,避免发生火灾、爆炸等意外事故,并及时响应紧急情况。
三、装置操作技巧1.合理调整操作参数:根据渣油的性质和产品要求,合理调整加氢反应的温度、压力和催化剂用量等操作参数,以达到最佳反应效果。
2.善于处理异常情况:操作人员应具备处理异常情况的能力,如催化剂塌陷、过压、过热等情况,及时采取相应的措施。
3.及时维护设备:对于装置设备的维护保养工作,应及时进行,保证装置的正常运行和使用寿命。
关于渣油加氢处理催化剂及工艺技术
关于渣油加氢处理催化剂及工艺技术关于渣油加氢处理催化剂及工艺技术一、渣油加氢处理技术概况当今世界,石油资源逐渐变劣、变重,使轻质油品收率下降,而世界经济的快速发展对轻质油品的需求却日益增长。
如何合理利用和深度加工劣质或重质原油,是炼油工业面临的一个迫切需要解决的难题。
在国内,原油资源满足不了我国国民经济快速发展的需要,进口中东原油以增加我国的能源供给势在必行。
中东原油加工的主要技术难点是高硫原油的合理利用,从当今炼油技术水平来看,渣油固定床加氢处理是合理利用含硫渣油的最为有效的手段之一二、渣油加氢处理过程的化学反应及催化剂1、渣油加氢处理过程的化学反应在重油加氢处理过程中,主要的化学反应有:加氢脱金属(HDM);加氢脱硫(HDS);加氢脱氮(HDN);加氢裂化(HC);不饱和键的加氢(如芳烃饱和-HDA)等。
针对这些反应,渣油加氢处理催化剂主要包括渣油加氢保护剂,脱金属催化剂,脱硫催化剂和脱氮催化剂四大类。
2、减压渣油加氢处理系列催化剂(FZC-XX系列)该系列催化剂自1986年开始研制以来,现已研究开发成功四大类共十六个牌号的催化剂。
研究开发过程中共申请国内外专利六十余项,有效地保护了我国自力更生开发的渣油固定床加氢处理技术(简称S-RHT技术)。
FZC-XX系列催化剂特点和作用类别第一代第二代特点作用保护剂FZC-10FZC-10Q大孔容(>1.0ml/g),大孔径(有400nm以上大孔)脱金属杂质及垢物,保护下游催化剂,防止床层压力降快速升高FZC-11FZC-11QFZC-12FZC-12QFZC-13FZC-13QFZC-14FZC-14QFZC-15FZC-10UFZC-16FZC-11UFZC-17FZC-18脱金属剂FZC-20FZC-23大孔容(≥0.7 ml/g),大孔径(有100nm以上大孔)最大限度地脱镍、钒FZC-21FZC-24FZC-22FZC-25FZC-26FZC-27脱硫剂FZC-30FZC-33较强的酸性,较小的孔径,较大的比表面积脱硫、部分脱氮FZC-31FZC-34FZC-32FZC-35FZC-36脱氮剂FZC-40FZC-41强酸性,小孔径,大比表面积,高金属含量高活性脱氮、转化3、常压渣油加氢处理系列催化剂(FZC-XXX系列)1995年我国开始针对进口高硫原油开展了常压渣油加氢处理系列催化剂的研究开发工作。
渣油加氢工艺流程
第一节工艺技术路线及特点一、工艺技术路线300×104t/a渣油加氢脱硫装置采用CLG公司的固定床渣油加氢脱硫工艺技术,该工艺技术满足操作周期8000h、柴油产品硫含量不大于500ppm、加氢常渣产品硫含量不大于0.35w%、残炭不大于5.5w%、Ni+V不大于15ppm的要求。
二、工艺技术特点1、反应部分设置两个系列,每个系列可以单开单停(单开单停是指装置内二个系列分别进行正常生产和停工更换催化剂)。
由于渣油加氢脱硫装置的设计操作周期与其它主要生产装置不一致,从全厂生产安排的角度,单开单停可以有效解决原料储存、催化裂化装置进料量等问题,并使全厂油品调配更灵活。
2、反应部分采用热高分工艺流程,减少反应流出物冷却负荷;优化换热流程,充分回收热量,降低能耗。
3、反应部分高压换热器采用双壳、双弓型式,强化传热效果,提高传热效率。
4、反应器为单床层设置,易于催化剂装卸,尤其是便于卸催化剂。
5、采用原料油自动反冲洗过滤器系统,滤除大于25μm以上杂质,减缓反应器压降增大速度,延长装置操作周期。
6、原料油换热系统设置注阻垢剂设施,延长操作周期,降低能耗,而且在停工换剂期间可减少换热器和其它设备的检修工作。
7、原料油缓冲罐采用氮气覆盖措施,以防止原料油与空气接触从而减轻高温部位的结焦程度。
8、采用炉前混氢流程,避免进料加热炉炉管结焦。
9、第一台反应器入口温度通过调节加热炉燃料和高压换热器旁路量来控制,其他反应器入口温度通过调节急冷氢量来控制。
10、在热高分气空冷器入口处设注水设施,避免铵盐在低温部位的沉积。
11、循环氢脱硫塔前设高压离心式分离器除去携带的液体烃类,减少循环氢脱硫塔的起泡倾向,有利于循环氢脱硫的正常操作。
12、设置高压膜分离系统,保证反应氢分压。
13、冷低压闪蒸罐的富氢气体去加氢裂化装置脱硫后去PSA回收氢气。
14、新氢压缩机采用二开一备,每台50%负荷,单机负荷较小,方便制造,且装置有备机。
- 1、下载文档前请自行甄别文档内容的完整性,平台不提供额外的编辑、内容补充、找答案等附加服务。
- 2、"仅部分预览"的文档,不可在线预览部分如存在完整性等问题,可反馈申请退款(可完整预览的文档不适用该条件!)。
- 3、如文档侵犯您的权益,请联系客服反馈,我们会尽快为您处理(人工客服工作时间:9:00-18:30)。
格式号:P R O C -2-b第一节工艺技术路线及特点一、工艺技术路线300×104t/a 渣油加氢脱硫装置采用CLG 公司的固定床渣油加氢脱硫工艺技术,该工艺技术满足操作周期8000h 、柴油产品硫含量不大于500ppm 、加氢常渣产品硫含量不大于0.35w%、残炭不大于5.5w%、Ni+V 不大于15ppm 的要求。
二、工艺技术特点1、反应部分设置两个系列,每个系列可以单开单停(单开单停是指装置内二个系列分别进行正常生产和停工更换催化剂)。
由于渣油加氢脱硫装置的设计操作周期与其它主要生产装置不一致,从全厂生产安排的角度,单开单停可以有效解决原料储存、催化裂化装置进料量等问题,并使全厂油品调配更灵活。
2、反应部分采用热高分工艺流程,减少反应流出物冷却负荷;优化换热流程,充分回收热量,降低能耗。
3、反应部分高压换热器采用双壳、双弓型式,强化传热效果,提高传热效率。
4、反应器为单床层设置,易于催化剂装卸,尤其是便于卸催化剂。
5、采用原料油自动反冲洗过滤器系统,滤除大于25μm 以上杂质,减缓反应器压降增大速度,延长装置操作周期。
6、原料油换热系统设置注阻垢剂设施,延长操作周期,降低能耗,而且在停工换剂期间可减少换热器和其它设备的检修工作。
7、原料油缓冲罐采用氮气覆盖措施,以防止原料油与空气接触从而减轻高温部位的结焦程度。
8、采用炉前混氢流程,避免进料加热炉炉管结焦。
9、第一台反应器入口温度通过调节加热炉燃料和高压换热器旁路量来控制,其他反应器入口温度通过调节急冷氢量来控制。
10、在热高分气空冷器入口处设注水设施,避免铵盐在低温部位的沉积。
11、循环氢脱硫塔前设高压离心式分离器除去携带的液体烃类,减少循环氢脱硫塔的起泡倾向,有利于循环氢脱硫的正常操作。
12、设置高压膜分离系统,保证反应氢分压。
13、冷低压闪蒸罐的富氢气体去加氢裂化装置脱硫后去PSA 回收氢气。
14、新氢压缩机采用二开一备,每台50%负荷,单机负荷较小,方便制造,且装置有备机。
15、分馏部分采用主汽提塔+分馏塔流程,在汽提塔除去轻烃和硫化氢,降低分馏塔材质要求。
分馏塔设侧线柴油汽提塔及中段回流加热原料油,降低塔顶冷却负荷,提高能量利用率,减小分馏塔塔径。
16、利用常渣产品发生部分低压蒸汽。
通过对装置换热流程的优化,把富裕热量集中在温位较高的常渣产品,发生低压蒸汽。
17、考虑到全厂能量综合利用,正常生产时常渣在150℃送至催化裂化装置。
在催化裂化装置事故状态下,将常渣冷却至90℃送至工厂罐区。
18、催化剂预硫化按液相预硫化方式设置。
三、工艺流程说明 (一)工艺流程简述1、反应部分原料油自进装置后至冷低压分离器(V-1812)前的流程分为两个系列,以下是一个系列的流程叙述:原料油在液位和流量的串级控制下进入滤前原料油缓冲罐(V-1801)。
原料从V-1801底部出来由原料油增压泵(P1801/S )升压,经中段回流油/原料油换热器(E-1801AB )、常渣/原料油换热器(E-1802AB 、E-1803AB )分别与中段回流油和常渣换热,然后进入原料油过滤器(S-1801)以除去原料油中大于25μm 的杂质。
过滤后的原料油进入滤后原料油缓冲罐(V-1802),原料油从V-1802底部出来后由加氢进料泵(P1802/S )升压,升压后的原料油在流量控制下进入反应系统。
原料油和经热高分气/混合氢换热器(E-1805AB )预热后的混合氢混合,混合进料经反应流出物/反应进料换热器(E-1804)预热后进入反应进料加热炉(F-1801)加热至反应所需温度进入第一台加氢反应器(R-1801),R-1801的入口温度通过调节F-1801的燃料量和E-1804的副线量来控制,格式号:P R O C -2-bR-1801底部物流依次通过其它三台反应器(R-1802、R-1803、R-1804),各反应器的入口温度通过调节反应器入口管线上注入的冷氢量来控制。
从R-1804出来的反应产物经过E-1804换热后进入热高压分离器(V-1803)进行气液分离, V-1803底部出来的热高分液分别在液位控制下减压后,进入热低压分离器(V-1804)进行气液分离,V-1803顶部出来的热高分气分别经热高分气/混合氢换热器、热高分气蒸汽发生器(E-1806)换热后进入热高分气空冷器(E-1807),冷却到52℃进入冷高压分离器(V-1806)进行气、油、水三相分离。
为了防止铵盐在低温位析出堵塞管路,在热高分气空冷器前注入经注水泵(P-1803/S )升压后的脱硫净化水等以溶解铵盐。
从V-1806顶部出来的冷高分气体(循环氢)进入高压离心分离器(V-1807)除去携带的液体烃类,减少循环氢脱硫塔(C-1801)的起泡倾向。
自V-1807顶部出来的气体进入C-1801底部,与贫胺液在塔内逆向接触,脱除H 2S ,脱硫溶剂采用甲基二乙醇胺(MDEA ),贫胺液从贫胺液缓冲罐(V-1809)抽出经贫溶剂泵(P-1804/S )升压后进入C-1801顶部,从塔底部出来的富胺液降压后进入富胺液闪蒸罐(V-1810)脱气。
富液脱气后出装置去溶剂再生,气体去硫磺回收。
自C-1801顶不出来的循环氢进入循环氢压缩机入口分液罐(V-1808)除去携带的胺液,V-1808顶部出来的循环氢分成两路,一路去氢提浓(ME-1801)部分,提浓后的氢气经提浓氢压缩机(K-1804)升压后与新氢压缩机(K-1802A.B.C )出口新氢汇合,释放气去轻烃回收装置;另一路进入循环氢压缩机(K-1801)升压,升压后的循环氢分为三部分,第一部分与新氢压缩机来的新氢混合,混合氢去反应部分;第二部分作为急冷氢去控制反应器入口温度;第三部分至E-1807前作为备用冷氢和K-1801反飞动用。
循环氢压缩机选用背压蒸汽透平驱动的离心式压缩机。
从两个反应系列的冷高压分离器底部出来的冷高分液分别在液位控制下减压混合后,进入冷低压分离器(V-1812)进行气液分离,冷低分液体在液位控制下从罐底排出并进入热低分气/冷低分液换热器(E-1809)、柴油/冷低分油换热器(E-1811)、常渣/冷低分油换热器(E-1812)换热后进入汽提塔(C-1803)。
V-1812顶部出来的冷低分气去轻烃回收装置脱硫。
冷高压分离器底部的含H 2S 、NH 3的酸性水进入酸性水脱气罐(V-1823)集中脱气后送出装置。
两个反应系列的热低分油在液位控制下从V-1803底部排出去分馏部分。
热低分气体经E-1809换热后进入热低分气空冷器(E-1810)冷却到54℃,然后进入冷低压闪蒸罐(V-1811)进行气液分离,为了防止在低温位的地方有铵盐析出堵塞管路,在E-1810前注水以溶解铵盐。
V-1811顶部出来的富氢气体直接送至加氢裂化装置进行脱硫,然后去PSA 装置回收氢气;从下部出来的冷低压闪蒸液进入到冷低压分离器。
新氢从全厂氢网送入,进入新氢压缩机经三段压缩升压后分两路分别与两个系列循环氢压缩机出口的循环氢混合,混合氢气分别返回到各自的反应部分。
新氢压缩机设三台,二开一备,每一台均为三级压缩,每台的一级入口设入口分液罐,级间设冷却器和分液罐。
2、分馏部分来自反应部分的热低分油与经加热后的冷低分液一起进入汽提塔(C-1803)。
塔底采用水蒸汽汽提。
塔顶部气相经汽提塔顶空冷器(E-1814)冷凝冷却后进入汽提塔顶回流罐(V-1814)进行气液分离,V-1814气体与冷低分气一起出装置送至轻烃回收统一脱硫;V-1814底部出来的液体经汽提塔顶回流泵(P-1805/S )升压后分成两部分,一部分作为回流返回到塔顶部,另一部分去石脑油加氢。
V-1814底部分水包排出的酸性水进入V-1823脱气后出装置。
为减轻塔顶管道和设备的腐蚀,在汽提塔的顶部管道注入缓蚀剂。
汽提塔底油经分馏塔进料加热炉(F-1802)加热至合适温度进入分馏塔(C-1804),分馏塔设一个柴油抽出侧线和一个中段回流,塔底采用水蒸汽汽提,塔顶气相经分馏塔顶空冷器(E-1815)冷凝冷却后进入分馏塔顶回流罐(V-1815)进行气液分离;V-1815底部出来的液体经分馏塔顶回流泵(P-1806/S )升压后分成两部分,一部分作为塔顶回流返回到塔顶部,另一部分在V-1815液位控制下与C-1803塔顶油一道送出装置。
V-1815底部分水包排出的含油污水经含油污水泵(P-1807/S )升压后送注水罐回用。
未汽提柴油从分馏塔抽出进入柴油汽提塔(C-1805),柴油汽提塔底设重沸器,以分馏塔底油为热源,C-1805顶气体返回到分馏塔。
柴油从塔底部抽出经柴油泵(P-1811/S )升压后再经柴油/低分油换热器、柴油空冷器(E-1816)冷却到50℃出装置。
中段回流油从分馏塔集油箱用分馏塔中段回流泵(P-1809/S )抽出,进入E-1801A.B 换热后返回分馏塔。
分馏塔底油(加氢常渣)经分馏塔底泵(P-1810/S )加压后依次经柴油汽提塔重沸器(E-1818)、常渣/原料油换热器、常渣蒸汽发生器(E-1817)等换热至168℃作为热供料去催化裂化装置,或再经常渣空冷器(E-1819)冷却至90℃出装置至罐区。
3、催化剂预硫化为了使催化剂具有活性,新鲜的或再生后的催化剂在使用前均必须进行预硫化,设计采用液相硫化法,硫化剂为二甲基二硫化物(DMDS )。
两个系列催化剂可以分别独立进行预硫化,以下是一个系列硫化的流程叙述:硫化时,系统内氢气经循环氢压缩机按正常操作路线进行循环,冷高压分离器压力为正常操作压力。
DMDS 自硫化剂罐(V-1831)来,至加氢进料泵入口管线,硫化油采用蜡油。
自R-1804来的流出物经E-1804、V-1803、E-1805A.B 、E-1806、E-1807冷却后进入冷高压分离器V1806进行分离,冷高分气体经循环氢压缩机K-1801循环,催化剂预硫化过程中产生的水从V4004底部间断排出。
(二)主要操作条件如下:格式号:P R O C -2-b1 反应部分反应器液时空速,h-1 0.20 总气油比,SOR/EOR1132/1232 反应器入口压力,SOR/EOR MPa (g ) 19.45/19.88 平均反应温度,SOR/ EOR ℃ 391/402 2 热高压分离器 温度 ℃ SOR/EOR 371/374 压力MPa(G) 17.8 3 冷高压分离器 温度℃ 52 压力MPa(G) 17.5 4 反应进料加热炉入口/出口温度℃ 337/365(SOR ) 350/378(EOR )压力MPa(G) 20.6 5 循环氢压缩机 入口温度℃61入口/出口压力MPa(G) 17.46/21.43 循环氢压缩机设计能力m3n/h 224315(单台) 6 新氢压缩机 入口温度℃40 入口/出口压力MPa(G) 2.4/21.2 新氢压缩机设计能力m3n/h 51400(单台) 7 提浓氢压缩机 入口温度℃60入口/出口压力MPa(G) 4.18/21.37 提浓氢压缩机设计能力m3n/h 31800 8 循环氢脱硫塔 塔顶温度℃ 61 塔顶压力MPa(G) 17.5 9 汽提塔进料温度℃ 364/366(SOR/EOR ) 塔顶温度℃ 189/172(SOR/EOR ) 塔顶压力MPa(G) 1.1塔底温度℃350/344(SOR/EOR )格式号:P R O C -2-b10 分馏塔 进料温度℃ 371塔顶温度℃ 124/129(SOR/EOR ) 塔顶压力MPa(G) 0.14塔底温度℃ 354/322(SOR/EOR ) 10 柴油汽提塔 进料温度℃ 226/231 塔顶温度℃ 227/247 塔顶压力MPa(G) 0.17 塔底温度℃293第二节 副产品的回收、利用及“三废”处理方案一、副产品的回收和利用该装置副产品富氢气体和含硫燃料气。