整车碰撞仿真分析报告
汽车碰撞模拟仿真分析2024

引言概述汽车碰撞模拟仿真分析是一种用于研究汽车碰撞行为和评估车辆安全性能的有效工具。
通过模拟仿真分析,可以预测车辆碰撞时的动力学响应、车辆结构变形、乘员保护性能等重要参数,从而为车辆设计和安全评价提供依据。
本文将从不同角度详细分析汽车碰撞模拟仿真分析的相关内容。
正文内容1. 碰撞模拟仿真的意义和优势1.1 碰撞模拟仿真的意义碰撞模拟仿真可以在物理实验之前对车辆性能和安全性进行全面有效的评估,为车辆设计提供指导和改进方向。
1.2 碰撞模拟仿真的优势碰撞模拟仿真可以大幅度节省成本和时间,减少人力资源和实验设备的消耗,同时可以对碰撞过程中的细节进行深入分析。
2. 碰撞模拟仿真的基本原理和方法2.1 碰撞模拟仿真的基本原理碰撞模拟仿真基于有限元法和多体动力学原理,通过对车辆和碰撞体建立的数学模型进行求解,得出车辆碰撞时的动力学响应和结构变形。
2.2 碰撞模拟仿真的基本方法碰撞模拟仿真的基本方法包括车辆建模、材料特性建模、约束条件设定、求解模拟过程和结果分析等。
3. 碰撞模拟仿真的关键技术与挑战3.1 车辆碰撞行为建模车辆碰撞行为建模是碰撞模拟仿真的关键技术之一,需要考虑车辆的刚体运动、车辆结构变形和碰撞力的传递等因素。
3.2 材料特性建模材料特性建模是碰撞模拟仿真中的关键技术之一,需要准确描述车辆结构材料的力学行为,即材料的本构关系和损伤模型。
3.3 碰撞力传递与刚体运动碰撞力传递与刚体运动是碰撞模拟仿真中的关键技术之一,需要准确计算车辆碰撞过程中的力学响应,包括碰撞时间、碰撞角度和碰撞动量等。
3.4 界面接触与摩擦界面接触与摩擦是碰撞模拟仿真中的关键技术之一,需要准确描述车辆和碰撞体之间的接触行为和摩擦特性,包括接触力和接触面积等。
3.5 解算算法与计算效率解算算法与计算效率是碰撞模拟仿真中的关键技术之一,需要选择合适的数值方法和算法,提高仿真计算的精度和效率。
4. 汽车碰撞模拟仿真的应用领域4.1 车辆设计与优化汽车碰撞模拟仿真可以帮助车辆制造商进行车辆设计和优化,提高车辆的安全性和性能。
汽车碰撞仿真分析研究
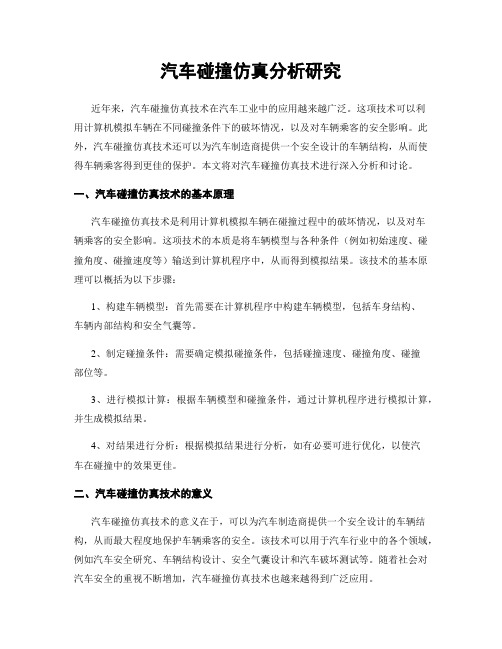
汽车碰撞仿真分析研究近年来,汽车碰撞仿真技术在汽车工业中的应用越来越广泛。
这项技术可以利用计算机模拟车辆在不同碰撞条件下的破坏情况,以及对车辆乘客的安全影响。
此外,汽车碰撞仿真技术还可以为汽车制造商提供一个安全设计的车辆结构,从而使得车辆乘客得到更佳的保护。
本文将对汽车碰撞仿真技术进行深入分析和讨论。
一、汽车碰撞仿真技术的基本原理汽车碰撞仿真技术是利用计算机模拟车辆在碰撞过程中的破坏情况,以及对车辆乘客的安全影响。
这项技术的本质是将车辆模型与各种条件(例如初始速度、碰撞角度、碰撞速度等)输送到计算机程序中,从而得到模拟结果。
该技术的基本原理可以概括为以下步骤:1、构建车辆模型:首先需要在计算机程序中构建车辆模型,包括车身结构、车辆内部结构和安全气囊等。
2、制定碰撞条件:需要确定模拟碰撞条件,包括碰撞速度、碰撞角度、碰撞部位等。
3、进行模拟计算:根据车辆模型和碰撞条件,通过计算机程序进行模拟计算,并生成模拟结果。
4、对结果进行分析:根据模拟结果进行分析,如有必要可进行优化,以使汽车在碰撞中的效果更佳。
二、汽车碰撞仿真技术的意义汽车碰撞仿真技术的意义在于,可以为汽车制造商提供一个安全设计的车辆结构,从而最大程度地保护车辆乘客的安全。
该技术可以用于汽车行业中的各个领域,例如汽车安全研究、车辆结构设计、安全气囊设计和汽车破坏测试等。
随着社会对汽车安全的重视不断增加,汽车碰撞仿真技术也越来越得到广泛应用。
三、汽车碰撞仿真技术的应用汽车碰撞仿真技术可以在汽车行业中的许多领域中得到应用。
在汽车制造领域中,该技术可以用于设计安全气囊、安全带和车身结构等。
此外,汽车碰撞仿真技术还可以用于研究车辆在不同碰撞条件下的表现,包括碰撞速度、碰撞角度和碰撞部位等。
通过模拟研究,汽车制造商可以提高车辆的安全性能,从而保护车辆乘客的安全。
此外,该技术还可以在汽车保险行业中得到广泛应用。
例如,保险公司可以利用汽车碰撞仿真技术,来确定一个车辆的保险费用。
汽车碰撞性实验报告
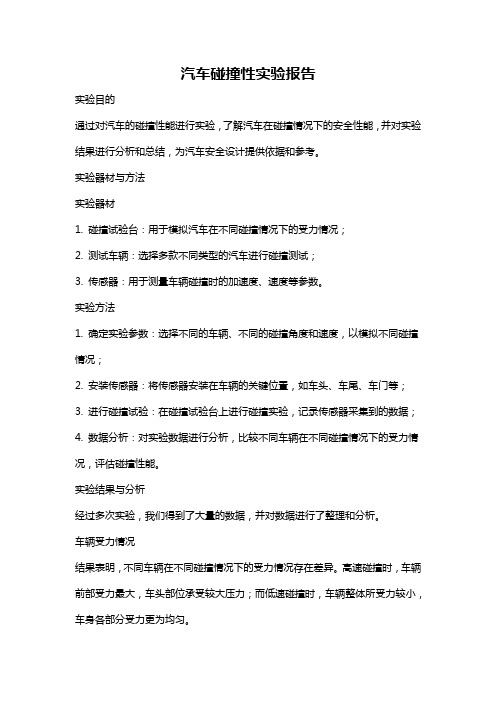
汽车碰撞性实验报告实验目的通过对汽车的碰撞性能进行实验,了解汽车在碰撞情况下的安全性能,并对实验结果进行分析和总结,为汽车安全设计提供依据和参考。
实验器材与方法实验器材1. 碰撞试验台:用于模拟汽车在不同碰撞情况下的受力情况;2. 测试车辆:选择多款不同类型的汽车进行碰撞测试;3. 传感器:用于测量车辆碰撞时的加速度、速度等参数。
实验方法1. 确定实验参数:选择不同的车辆、不同的碰撞角度和速度,以模拟不同碰撞情况;2. 安装传感器:将传感器安装在车辆的关键位置,如车头、车尾、车门等;3. 进行碰撞试验:在碰撞试验台上进行碰撞实验,记录传感器采集到的数据;4. 数据分析:对实验数据进行分析,比较不同车辆在不同碰撞情况下的受力情况,评估碰撞性能。
实验结果与分析经过多次实验,我们得到了大量的数据,并对数据进行了整理和分析。
车辆受力情况结果表明,不同车辆在不同碰撞情况下的受力情况存在差异。
高速碰撞时,车辆前部受力最大,车头部位承受较大压力;而低速碰撞时,车辆整体所受力较小,车身各部分受力更为均匀。
车辆安全设计评估根据实验数据分析,我们可以评估车辆的碰撞性能。
通过对比不同车辆在相同碰撞情况下的受力情况,我们可以发现一些设计差异,进而评估哪些车辆具有较好的碰撞性能。
结果总结通过汽车碰撞性实验,我们得到了大量有关汽车碰撞性能的数据,并对实验结果做了评估和总结。
在实验数据的基础上,我们可以进一步优化汽车的碰撞性设计,提高汽车的安全性能。
实验结论实验结果表明,汽车在碰撞情况下的安全性能存在差异,不同车型在不同碰撞情况下受力情况有所不同。
通过对实验数据的分析和评估,我们可以对汽车的碰撞性能进行优化和改进,提高汽车的安全性能。
参考文献1. Smith, J., & Johnson, A. (2019). The impact of vehicle design on crashworthiness. Journal of Safety Research, 70, 137-145.2. Zhang, H., Tang, Y., & Zeng, Z. (2020). Comparison of safety performance of different vehicle types in frontal crash. International Journal of Crashworthiness, 25(6), 713-722.。
碰撞试验实验报告结果(3篇)
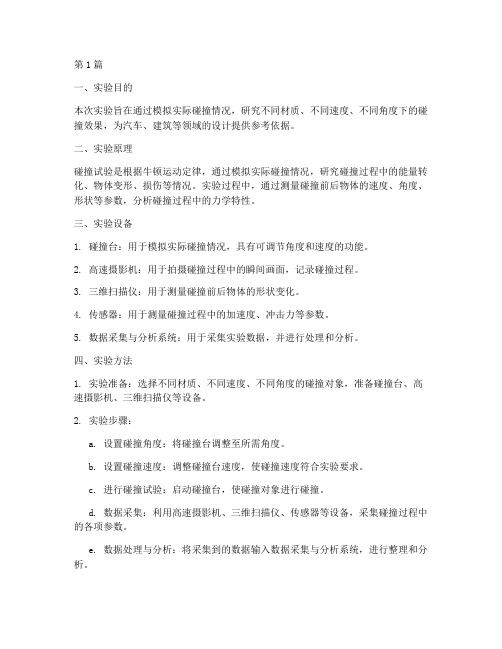
第1篇一、实验目的本次实验旨在通过模拟实际碰撞情况,研究不同材质、不同速度、不同角度下的碰撞效果,为汽车、建筑等领域的设计提供参考依据。
二、实验原理碰撞试验是根据牛顿运动定律,通过模拟实际碰撞情况,研究碰撞过程中的能量转化、物体变形、损伤等情况。
实验过程中,通过测量碰撞前后物体的速度、角度、形状等参数,分析碰撞过程中的力学特性。
三、实验设备1. 碰撞台:用于模拟实际碰撞情况,具有可调节角度和速度的功能。
2. 高速摄影机:用于拍摄碰撞过程中的瞬间画面,记录碰撞过程。
3. 三维扫描仪:用于测量碰撞前后物体的形状变化。
4. 传感器:用于测量碰撞过程中的加速度、冲击力等参数。
5. 数据采集与分析系统:用于采集实验数据,并进行处理和分析。
四、实验方法1. 实验准备:选择不同材质、不同速度、不同角度的碰撞对象,准备碰撞台、高速摄影机、三维扫描仪等设备。
2. 实验步骤:a. 设置碰撞角度:将碰撞台调整至所需角度。
b. 设置碰撞速度:调整碰撞台速度,使碰撞速度符合实验要求。
c. 进行碰撞试验:启动碰撞台,使碰撞对象进行碰撞。
d. 数据采集:利用高速摄影机、三维扫描仪、传感器等设备,采集碰撞过程中的各项参数。
e. 数据处理与分析:将采集到的数据输入数据采集与分析系统,进行整理和分析。
五、实验结果与分析1. 不同材质碰撞效果对比实验选取了钢、铝、塑料三种不同材质的碰撞对象,进行碰撞试验。
结果表明,钢材质的碰撞效果最明显,铝材质次之,塑料材质碰撞效果最弱。
这是因为钢材质具有较高的硬度和强度,铝材质较软,塑料材质更软。
2. 不同速度碰撞效果对比实验设置了不同速度的碰撞对象,进行碰撞试验。
结果表明,随着碰撞速度的增加,碰撞效果越明显。
这是因为碰撞速度越高,碰撞过程中的动能越大,物体变形和损伤程度越严重。
3. 不同角度碰撞效果对比实验设置了不同角度的碰撞对象,进行碰撞试验。
结果表明,碰撞角度对碰撞效果有较大影响。
当碰撞角度较小时,碰撞效果较轻;当碰撞角度较大时,碰撞效果较重。
汽车基本碰撞实验报告(3篇)

第1篇一、实验目的本次实验旨在通过模拟汽车碰撞实验,了解汽车碰撞的基本原理、碰撞过程及碰撞结果,分析汽车碰撞对乘员和车辆本身的影响,为提高汽车安全性能提供理论依据。
二、实验原理汽车碰撞实验主要研究汽车在碰撞过程中,由于惯性、动能转换、结构变形等因素所产生的一系列物理现象。
实验过程中,通过对碰撞力的测量、碰撞过程中汽车结构的变形分析、碰撞后乘员所受伤害程度等数据的采集,来分析汽车碰撞的基本规律。
三、实验设备与材料1. 实验设备:碰撞实验台、传感器、数据采集系统、摄像系统、汽车模型等。
2. 实验材料:碰撞模拟实验用汽车模型、安全气囊、安全带、汽车内饰等。
四、实验步骤1. 实验准备:搭建碰撞实验台,安装传感器、数据采集系统和摄像系统,确保实验设备运行正常。
2. 模拟碰撞实验:将汽车模型放置在碰撞实验台上,根据实验需求设定碰撞速度、角度等参数。
3. 数据采集:启动数据采集系统,记录碰撞过程中汽车结构的变形、碰撞力、乘员所受伤害程度等数据。
4. 摄像记录:开启摄像系统,实时记录碰撞过程,以便后续分析。
5. 数据分析:对采集到的数据进行处理、分析,得出碰撞规律。
五、实验结果与分析1. 碰撞力分析:实验结果表明,汽车在碰撞过程中,碰撞力与碰撞速度、角度等因素密切相关。
随着碰撞速度的增加,碰撞力也随之增大。
2. 汽车结构变形分析:实验过程中,汽车结构在碰撞力的作用下产生不同程度的变形。
碰撞速度越高,结构变形越严重。
3. 乘员所受伤害程度分析:实验结果表明,乘员在碰撞过程中所受伤害程度与碰撞速度、角度、安全气囊、安全带等因素密切相关。
在碰撞速度较高的情况下,乘员所受伤害程度较大。
4. 安全气囊与安全带效果分析:实验结果表明,安全气囊和安全带在碰撞过程中对乘员具有较好的保护作用。
安全气囊在碰撞瞬间迅速充气,为乘员提供缓冲;安全带则将乘员固定在座椅上,减少乘员在碰撞过程中的位移。
六、实验结论1. 汽车碰撞过程中,碰撞力与碰撞速度、角度等因素密切相关,随着碰撞速度的增加,碰撞力也随之增大。
汽车急速撞车实验报告(3篇)
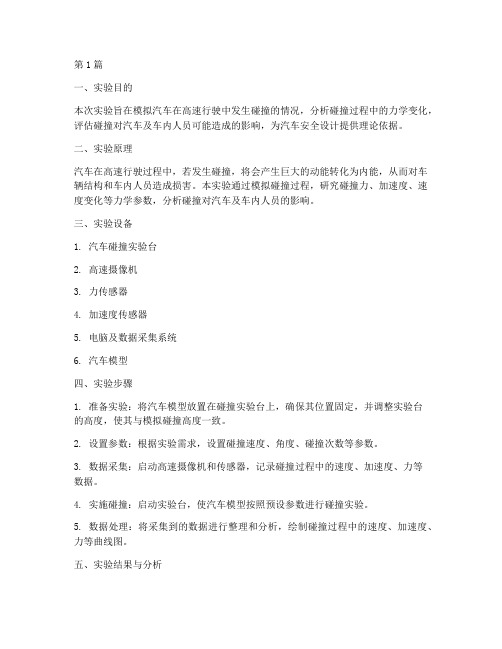
第1篇一、实验目的本次实验旨在模拟汽车在高速行驶中发生碰撞的情况,分析碰撞过程中的力学变化,评估碰撞对汽车及车内人员可能造成的影响,为汽车安全设计提供理论依据。
二、实验原理汽车在高速行驶过程中,若发生碰撞,将会产生巨大的动能转化为内能,从而对车辆结构和车内人员造成损害。
本实验通过模拟碰撞过程,研究碰撞力、加速度、速度变化等力学参数,分析碰撞对汽车及车内人员的影响。
三、实验设备1. 汽车碰撞实验台2. 高速摄像机3. 力传感器4. 加速度传感器5. 电脑及数据采集系统6. 汽车模型四、实验步骤1. 准备实验:将汽车模型放置在碰撞实验台上,确保其位置固定,并调整实验台的高度,使其与模拟碰撞高度一致。
2. 设置参数:根据实验需求,设置碰撞速度、角度、碰撞次数等参数。
3. 数据采集:启动高速摄像机和传感器,记录碰撞过程中的速度、加速度、力等数据。
4. 实施碰撞:启动实验台,使汽车模型按照预设参数进行碰撞实验。
5. 数据处理:将采集到的数据进行整理和分析,绘制碰撞过程中的速度、加速度、力等曲线图。
五、实验结果与分析1. 碰撞力分析实验结果显示,在碰撞过程中,汽车模型所受的碰撞力随着速度的增加而增大。
当碰撞速度达到一定值时,碰撞力达到峰值,随后逐渐减小。
这说明在高速碰撞中,汽车及车内人员所受的冲击力较大,易造成严重伤害。
2. 加速度分析实验结果显示,在碰撞过程中,汽车模型的加速度随着速度的增加而增大。
当碰撞速度达到一定值时,加速度达到峰值,随后逐渐减小。
这说明在高速碰撞中,汽车及车内人员所受的加速度较大,易造成严重伤害。
3. 速度变化分析实验结果显示,在碰撞过程中,汽车模型的速度在碰撞瞬间急剧减小,随后逐渐恢复。
这说明在高速碰撞中,汽车及车内人员所受的冲击力较大,易造成严重伤害。
4. 碰撞对汽车结构的影响实验结果显示,在碰撞过程中,汽车模型的壳体结构发生变形,车门、车窗等部件损坏。
这说明在高速碰撞中,汽车结构易受到严重损害,从而影响车内人员的生存空间。
汽车撞碎实验报告(3篇)

第1篇一、实验背景随着汽车保有量的不断增加,交通事故频发,给人们的生命财产安全带来了严重威胁。
为了研究汽车在碰撞过程中的受力情况,提高汽车的安全性能,本实验采用模拟碰撞的方法,对汽车进行撞碎实验。
二、实验目的1. 了解汽车在碰撞过程中的受力情况。
2. 分析汽车不同部位在碰撞过程中的破坏程度。
3. 为汽车设计提供理论依据,提高汽车的安全性。
三、实验原理本实验采用物理力学原理,通过模拟碰撞实验,研究汽车在碰撞过程中的受力情况。
实验中,利用高速摄像机记录碰撞过程中的瞬间状态,通过数据分析,得出汽车在不同碰撞条件下的受力情况。
四、实验材料1. 汽车模型:选用与实际车型相似的汽车模型,尺寸为1:1。
2. 撞击装置:采用液压撞击装置,可调节撞击速度和角度。
3. 高速摄像机:用于记录碰撞过程中的瞬间状态。
4. 数据采集与分析软件:用于处理实验数据。
五、实验步骤1. 准备实验:将汽车模型放置在实验台上,调整撞击装置的撞击速度和角度。
2. 进行实验:启动撞击装置,使汽车模型与撞击物发生碰撞。
3. 数据采集:利用高速摄像机记录碰撞过程中的瞬间状态。
4. 数据分析:将采集到的数据进行处理,分析汽车在碰撞过程中的受力情况。
六、实验结果与分析1. 撞击速度对汽车受力的影响:实验结果表明,随着撞击速度的增加,汽车所受的冲击力也随之增大。
在高速撞击条件下,汽车更容易发生严重变形和损坏。
2. 撞击角度对汽车受力的影响:实验结果表明,撞击角度对汽车受力有显著影响。
当撞击角度为90°时,汽车所受的冲击力最大;当撞击角度为45°时,汽车所受的冲击力次之;当撞击角度为0°时,汽车所受的冲击力最小。
3. 汽车不同部位在碰撞过程中的破坏程度:实验结果表明,汽车的前部、侧面和尾部在碰撞过程中容易发生变形和损坏。
其中,前部受到的冲击力最大,其次是侧面和尾部。
4. 汽车安全性能改进建议:根据实验结果,提出以下安全性能改进建议:(1)加强汽车前部、侧面和尾部的结构强度,提高汽车的整体抗碰撞能力。
汽车碰撞性能实验报告(3篇)

第1篇一、实验目的本次实验旨在通过模拟碰撞试验,评估汽车在碰撞过程中的安全性能,包括车身结构、乘员保护系统以及整体碰撞后的损害情况。
通过对不同车型、不同碰撞速度和角度的试验,分析汽车在碰撞中的表现,为汽车设计、制造和改进提供参考依据。
二、实验背景随着我国汽车工业的快速发展,汽车安全性能已成为消费者购车时关注的重点。
汽车碰撞试验是评价汽车安全性能的重要手段之一,能够有效评估汽车在碰撞过程中的表现,为消费者提供可靠的安全保障。
三、实验方法1. 实验设备(1)碰撞试验台:用于模拟不同速度、角度的碰撞试验。
(2)碰撞传感器:用于测量碰撞过程中的加速度、速度等参数。
(3)假人:用于模拟碰撞过程中乘员的动态响应。
(4)数据采集系统:用于实时采集碰撞试验过程中的各项数据。
2. 实验步骤(1)选择实验车型:选取市场上具有代表性的车型进行碰撞试验。
(2)设置碰撞条件:根据实验需求,设置碰撞速度、角度等参数。
(3)安装实验设备:将碰撞试验台、传感器、假人等设备安装到实验车型上。
(4)进行碰撞试验:按照设定的碰撞条件,进行碰撞试验。
(5)数据采集与分析:在碰撞试验过程中,实时采集各项数据,并进行分析。
四、实验结果与分析1. 碰撞速度对汽车安全性能的影响实验结果表明,随着碰撞速度的增加,汽车在碰撞过程中的变形程度逐渐增大,乘员受到的冲击力也随之增大。
在高速碰撞条件下,汽车的安全性能较差。
2. 碰撞角度对汽车安全性能的影响实验结果表明,不同角度的碰撞对汽车安全性能的影响存在差异。
在正面碰撞中,汽车的安全性能相对较好;而在侧面碰撞中,汽车的安全性能较差。
3. 车身结构对汽车安全性能的影响实验结果表明,车身结构对汽车安全性能具有重要影响。
具有高强度车身结构的汽车在碰撞过程中的变形程度较小,乘员受到的冲击力也相对较小。
4. 乘员保护系统对汽车安全性能的影响实验结果表明,乘员保护系统在提高汽车安全性能方面具有重要作用。
安全气囊、安全带等乘员保护系统在碰撞过程中能够有效减少乘员的伤害。
- 1、下载文档前请自行甄别文档内容的完整性,平台不提供额外的编辑、内容补充、找答案等附加服务。
- 2、"仅部分预览"的文档,不可在线预览部分如存在完整性等问题,可反馈申请退款(可完整预览的文档不适用该条件!)。
- 3、如文档侵犯您的权益,请联系客服反馈,我们会尽快为您处理(人工客服工作时间:9:00-18:30)。
-4-
PDF 文件使用 "pdfFactory Pro" 试用版本创建
4.2 优化方案(未加车门)
20 ms
40 ms
60 ms
80 ms
如图为优化改进方案整车主体碰撞变形示意图,其中,门框最大变形 量出现在前门上铰链附近,峰值为 58mm(具体的改进方案见 5.1)。
初始状态
终了状态
上图为碰撞开始和终了状态时的假人状态。在现有条件和现有参 数情况下,根据人体损伤指标的计算公式可以得出:假人的头部伤害 值(有气囊)为 783.5(法规规定的安全范围在 1000 以内),胸部变 形值为 43.9mm(法规规定的安全范围在 75mm 之内),腿部受力为 7.68KN(法规规定的安全范围在 10KN 之内),均处于 CMVDR 294 法规规定的安全界限内。
整车有限元模型
车头有限元模型
侧围有限元模型
后围有限元模型
顶盖有限元模型
地板有限元模型
-2-
PDF 文件使用 "pdfFactory Pro" 试用版本创建
底盘有限元模型
车门有限元模型
注:A柱以前为吸能区,网格大小控制在10mm左右;中部网格大小为
15mm,C柱以后网格大小为20mm。
的作用,初步达到了减轻乘员伤害的目的。同时,由于车身 结构和发动机布置的限制,该车的结构耐撞性尚未达到最 佳,但从目前情况看,该车的碰撞特性基本上可达到要求。 2. 门框变形量不大,优化结构以后,最大变形量为 13.6mm(加 车门),预计碰撞后不使用工具仅依靠人力就可打开车门 。 3. 方向盘向后窜动量即X向位移量约为 26.2mm,在法规规定 的 127mm 范围内。 4. 在现有条件和现有参数情况下,通过人体损伤指标的计算可 以得到如下结论:加安全气囊情况下,头部伤害值为 783.5 (法规规定的 安全范围 在 1000 以内 ),胸部变形 值 为 43.9mm(法规规定的安全范围在 75mm 之内),腿部受力 为 7.68KN(法规规定的安全范围在 10KN 之内),均处于 CMVDR 294 法规规定的安全界限内。
目录
1 概述 ...................................................................................................1 3 碰撞仿真模拟参数............................................................................2 3.1 整车与各总成模型.........................................................................2 3.2 整车有限元模型单元数量统计 .....................................................3 4 碰撞模拟总体结果............................................................................4 4.1 初始方案(未加车门) .................................................................4 4.2 优化方案(未加车门) .................................................................5 4.3 优化方案(加车门) .....................................................................5 5 碰撞模拟优化改进及局部结果 ........................................................8 5.1 结构耐撞性优化情况 .....................................................................8 5.2 门框变形情况.................................................................................9 5.3 方向盘运动情况........................................................................... 10 6 乘员系统模拟 ................................................................................. 11 7 结论 ................................................................................................. 12
-7-
PDF 文件使用 "pdfFactory Pro" 试用版本创建
4 碰撞模拟优化改进及局部结果 5.1 结构耐撞性优化情况
本项目考虑到成本问题,许多结构件需沿用,因此,我们在优化 时,尽量在纵梁上做文章。
去掉纵梁前端的方孔
原结构
优化结构
优化纵梁前端压溃筋的布置:将第一条筋的 位置前移,达到均布效果,这样压溃变形效 果更好,增加了纵梁前端的吸能量
PDF 文件使用 "pdfFactory Pro" 试用版本创建
1 概述
碰撞仿真模拟,主要是针对碰撞法规 CMVDR 294 进行的仿真模拟。 通过对模拟结果进行分析,找出整车结构中存在的问题,为基于改善 整车碰撞特性的结构优化提供依据。同时,通过比较优化方案与初始 方案的碰撞仿真结果,说明优化方案在整车碰撞特性上的改善效果。
增加零件
由于布置的需要,纵梁结构前端出现打弯以 避开发动机。模拟中发现纵梁变形时在中部 出现弯折,为此在此处增加了加强板
副车架安装支架前端向前延伸
经过仿真模拟计算发现,以上结构的改进达到了预期的效果,详细 情况见 5.2 节。
-8-
PDF 文件使用 "pdfFactory Pro" 试用版本创建
5.3 方向盘运动情况
以下为方向盘在碰撞的各个时间段的位置变化情况,箭头所指代 表方向盘的移动方向。同时,我们给出方向盘中心相对位移曲线图。
20~40ms
40~60ms
60~80ms
80~100ms
方向盘各时间段位置变化情况
Z
X Y
方向盘中心相对位移量
方向盘中心相对位移在三个方向的峰值:X向为 26.2mm(未超 过 GB 11557-1998 法规规定的范围),Y向为 17.5mm,Z向为 42.3mm。
-3-
PDF 文件使用 "pdfFactory Pro" 试用版本创建
3 碰撞模拟总体结果 20ms,40ms,60ms,80ms 整车碰撞变形及数据结果如下表所示
4.1 初始方案(未加车门)
20 ms
40 ms
60 ms
80 ms
上图为初始设计方案整车(未加车门)碰撞变形示意图,其中门 框最大变形量出现在前门上铰链附近,峰值为 72mm。
从上图可以看出,初始方案的门框变形在 65ms 时达到峰值,门框变 形量为 72mm,优化方案的门框变形在 60ms 时达到峰值,门框变形量为 58mm,比初始方案下降了 14mm,这说明优化方案对缩小碰撞时的门框 变形量是有效的。
-9-
PDF 文件使用 "pdfFactory Pro" 试用版本创建 轜
- 11 -
PDF 文件使用 "pdfFactory Pro" 试用版本创建
6 结论 本次碰撞模拟还处于模拟阶段,尚未进行实车试验,一些参数的
调整还需等第一轮实车试验完成后方可进行,故在此我们对模拟结果 进行初步评价。
碰撞模拟的结果大致如下: 1. 由刚墙反力曲线可以看出,吸能梁起到了吸收大量碰撞能量
分析所采用的软件、初始环境与参数设置、单元类型及参考标准见下 表:
模拟分析软件
PAM-CRASH 2002
碰撞形式
正面碰撞 (如下图所示)
碰撞初始速度
50km/h
Solid Uniform
结构
3积分点
单元 Shell BT壳单元结构
Bar 2节点杆单元
撞击接触方式
刚性墙
参考标准
CMVDR 294 GB 11557-1998
85377
7.5%
3612
44870
7.4%
3379
41397
7.5%
162
8850
1.8%
7553
54804
12.1%
3646
46076
7.3%
422
16476
2.5%
26720 315296
7.8%
一般来说三角形单元数量超过10%会影响分析的精度,从上表可 以看出,有限元模型中三角形单元的数量占壳单元总数的7.8%,未超 过10%的限值。
5.2 门框变形情况
门框模型
测点布置图
通过测量发现,门框的最大变形位置在 BE 之间,我们将初始方案和 优化方案的门框变形进行了对比。以下为两种方案门框变形最大时的对 比图及量化后门框变形-时间历程对比图:
72 mm
58mm
初始方案(Origin Design)
14mm
优化方案(Optimized Design)
4.3 优化方案(加车门)
20 ms
40 ms
60 ms
80 ms
-5-
PDF 文件使用 "pdfFactory " 试用版本创建 炣