(模具设计)筒形凸缘件拉深模设计
带凸缘拉深件模具设计说明书

设计题目:宽凸缘圆筒形件拉深模具设计。
设计与计算步骤:1. 拉深工艺计算(1)修边余量的确定查表4-2(来自《冲压模具课程设计指导与范例》——化学工业出版社,以下所查各表均出自此)得修边余量∆R=4.3(2)毛坯尺寸的计算查表4-4,知222212124342()4d d h r d d r d d ππ+++++-其中1d =72,2d =78,3d =84,4d =109.6,r=3,h=32 计算出D=152mm 。
(3)确定拉深次数和拉深系数查表4-9得工件第一次拉深的最大相对高度11/0.6h d = 查表4-10得第一次拉深时的拉深系数10.51m =/0.487h d =<11/0.6h d =,所以工件可一次拉出。
2. 拉深力的计算查表4-19. 13 3.14722410 1.1203.9l b F d t k KN πσ==⨯⨯⨯⨯=3. 压边力和压边装置的设计查表4-11,确定此拉深工艺需要采用压边圈,采用弹性压边装置td11-推杆; 12-推板;13-紧固螺钉; 14-紧固螺栓; 15-空心垫板; 16-压边圈; 17-螺母; 18-下模座压边力的计算: 221[(2)]4Y A F D d r P π=-+查表4-27、4-28。
计算得:22[152(7229.6)]334.8,49.6Y A F KN π=-+⨯⨯===其中r 4.压力机吨位的选择203.934.8238.7KN F F F >+=+=压拉压力机行程应满足:S>2.5h 100mm =工件 根据表9-9,选择压力机型号J23-80。
其主要技术规格如下。
KN mm mm mm mm⨯公称压力:1000最大装模高度:480工作台尺寸:7101080连杆调节量:100滑块行程:1305.拉深模结构设计(1)拉深凸、凹模圆角半径a.凹模圆角半径r 9.6A === b.凸模圆角半径(0.6~1)0.89.67.68T A r r ==⨯= (2)拉深凸、凹模间隙查表4-32,取单边间隙Z/2=2.2mm(3)凸、凹模工作零件尺寸计算A0.12A max00000T max T0.080.08D(0.75)80d0.75Z75.6DDδδ++---=-∆==-∆-==凹模尺寸凸模尺寸()(80-0-4.4)其中A Tδδ、由表4-34查取。
带凸缘圆筒形件拉深模设计
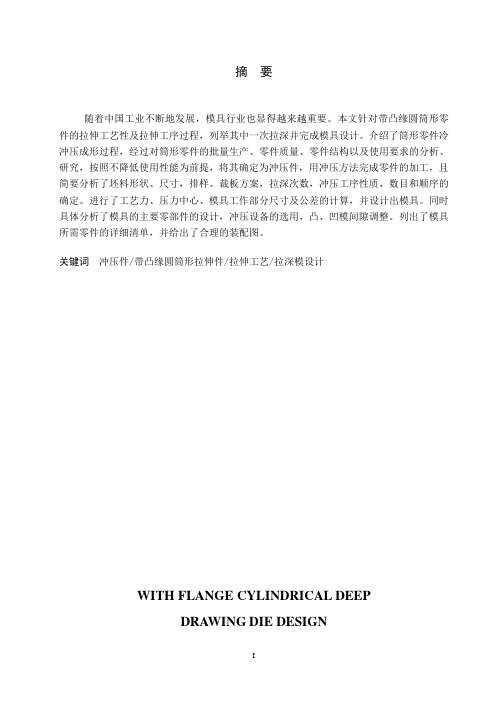
摘要随着中国工业不断地发展,模具行业也显得越来越重要。
本文针对带凸缘圆筒形零件的拉伸工艺性及拉伸工序过程,列举其中一次拉深并完成模具设计。
介绍了筒形零件冷冲压成形过程,经过对筒形零件的批量生产、零件质量、零件结构以及使用要求的分析、研究,按照不降低使用性能为前提,将其确定为冲压件,用冲压方法完成零件的加工,且简要分析了坯料形状、尺寸,排样、裁板方案,拉深次数,冲压工序性质、数目和顺序的确定。
进行了工艺力、压力中心、模具工作部分尺寸及公差的计算,并设计出模具。
同时具体分析了模具的主要零部件的设计,冲压设备的选用,凸、凹模间隙调整。
列出了模具所需零件的详细清单,并给出了合理的装配图。
关键词冲压件/带凸缘圆筒形拉伸件/拉伸工艺/拉深模设计WITH FLANGE CYLINDRICAL DEEPDRAWING DIE DESIGNABSTRACTAs China's industrial development unceasingly, the mold industry also appears more and more important. This paper belt of flange cylindrical parts stretching manufacturability and stretching process process, list one time deep drawing and complete the mold design. Cold stamping process of cylindrical parts is introduced, after mass production of the cylindrical parts, parts quality, parts structure, and use requirement analysis, research, according to not reduce the usability for the premise, to identify it for stamping parts, complete parts processing, with stamping method and the brief analysis of the blank shape, size, layout, cutting board, deep drawing, stamping process in nature, the determination of number and order. The technology force, pressure center, mold working parts dimension and tolerance of calculation, and design the mold. At the same time, concrete analysis of main components of the mold design, the selection of stamping equipment, convex and concave die clearance adjustment. Lists the mould needs a detailed list of spare parts, and gives the reasonable assembly drawing.KEYWORDS stamping parts, flange cylindrical stretching, stretching, deep drawing die design process目录1 前言 (1)1.1 模具的概论 (1)1.1.1 冲压与冲模 (1)1.1.2 我国冲压现状与发展方向 (2)1.1.3 国外模具发展趋势及行业特点 (2)1.1.4 模具设计及加工技术的现状 (3)1.1.6 冲模的零部件 (4)1.2 冲压件工艺分析 (5)1.2.1 冲压加工的经济性分析 (5)1.2.2 冲压件的工艺性分析 (5)1.3 本设计要求 (6)2 工艺方案 (7)2.1 工艺性分析 (7)2.1.1 拉深件的结构与尺寸 (7)2.1.3拉深件材料 (7)2.2 设计方案的确定 (7)3 主要工艺参数计算 (8)3.1 确定排样、裁板方案 (8)3.1.1 工艺分析 (8)3.1.2 确定修边余量 (8)3.1.3 坯料直径 (8)3.1.4 排样 (9)3.1.5 压力中心的确定 (10)3.2 拉深工艺的计算 (10)3.2.1 压边 (10)3.2.2 总拉深系数 (10)3.2.3 预算拉深次数 (10)3.2.4 确定首次拉深工序件尺寸 (11)3.2.5 确定拉深次数及以后各次拉深的工序件尺寸 (12)3.2.6 第二次拉深直径和高度 (13)3.2.7 第三次拉深直径和高度 (13)3.2.8 修边 (14)3.2.9 拉深速度 (14)3.3 工艺力计算 (14)3.3.1 拉深力 (14)3.3.2 压料力 (15)3.4 压力机的选择 (16)3.4.1 初选压力机 (16)3.4.2拉深功 (16)3.4.3压力机电动机功率 (16)3.4.4功率校核 (17)4 拉深模设计 (17)4.1拉深模具结构设计 (17)4.2模具工作部分尺寸计算 (17)4.2.1 凸凹模间隙 (17)4.2.2 凸凹模圆角半径 (17)4.2.3凸凹模工作尺寸及公差 (17)4.3标准件的选取 (18)4.3.1 模架 (18)4.3.2下模座 (19)4.3.3上模座 (19)4.3.4 导柱、导套 (19)4.3.5 销钉 (19)4.3.6 螺钉 (20)4.3.7 模柄 (20)4.3.8带螺纹推杆(顶杆) (20)4.3.9 打杆 (20)4.3.10 打杆螺母 (21)4.3.11 橡胶的选取 (21)4.3.12 橡胶螺杆 (22)4.3.13 ;螺杆螺母 (22)4.3.14 模柄紧固螺钉 (22)4.4模具非标准件的设计 (22)4.4.1 拉深凸模的设计 (22)4.4.2拉深凹模的设计 (23)4.4.3 凸模固定板设计 (24)4.4.4压料圈的设计 (24)4.4.6 托板的设计 (25)5 压力机的校核 (25)6 模具装配图 (26)结束语 (27)致谢 (28)参考文献 (29)1 前言板料冲压是金属加工的一种基本方法,他用以生产各种板料零件,具有生产效率高、尺寸精度好、重量轻、成本低并易于实现机械化和自动化等特点。
凸缘圆筒形工件的拉深设计要点

凸缘圆筒形工件的拉深设计要点凸缘圆筒形工件的拉深设计要点:设计确定拉深模具结构时为充分保证制件的质量及尺寸的精度,凸缘圆筒形工件拉深设计注意点:拉深高度应计算准确,且在模具结构上要留有安全余量,以便工件稍高时仍能适应拉深凸模上必须设有出气孔,并注意出气孔不能被工件抱住面而失去作用3)有凸缘拉深件的高度取决于上模行程,模具中药设计限程器,以便于模具调整4)对于形状复杂,须经多次拉深的零件,需先做拉深模,经试压确定合适的毛坯形状和尺寸再做落料模,并在拉深模上按已定形的毛坯,设计安装定位装置。
5)弹性压料设备必须有限位器,防止压料力过大6)模具结构及材料要和制件批量适应7)模架和模具零件,要尽量是使用标准化8)放入和取出制件必须方便安全2、有凸缘圆筒形件的拉深方法及工艺计算有凸缘筒形件的拉深原理与一般圆筒形件是相同的,但由于带有凸缘,其拉深方法及计算与一般筒形件有一定差别。
1)有凸缘拉深件可以看成是一般筒形件在拉深未结束时的半成品,即只将毛坯外径拉深到等于法兰边直径d时的拉深过程就结束。
因此其变形力的压力状态和变形特点与筒形件相同。
2)根据凸缘的相对直径有凸缘筒形件可分为:窄凸缘筒形件和宽凸缘筒形件3、宽凸缘筒形件的工艺计算要点1)毛坯尺寸的技术,毛坯尺寸的计算仍按等面积原理进行,其中要考虑修边余量:根据拉深系数的定义,宽凸缘件总拉深系数仍可表示为:2)判断工件是否一次拉成,这只须比较工件实际所需的总拉深系数和h/d与凸缘件第一次拉深系数和极限拉深系数的相对高度即可。
M总>M1,当h/d4、拉深凸模和凹模的间隙拉深模间隙是指单面间隙,间隙的大小对拉深力,拉深件的质量,拉深模的寿命都有影响,若c值大时,凸缘区变厚的材料通过间隙时,校正和变形的阻力增加,与模具表面的摩擦,磨损严重,使拉深力增加,零件变薄,甚至拉破,模具寿命降低。
间隙小时得到的零件侧壁平直而光滑,质量好,精度较高。
间隙过大时,对毛坯的校直和挤压作用减小,拉深力降低,模具的寿命提高,但零件的质量变差,冲出的零件侧壁不直。
课程设计带凸缘筒形件首次拉深的拉深模设计
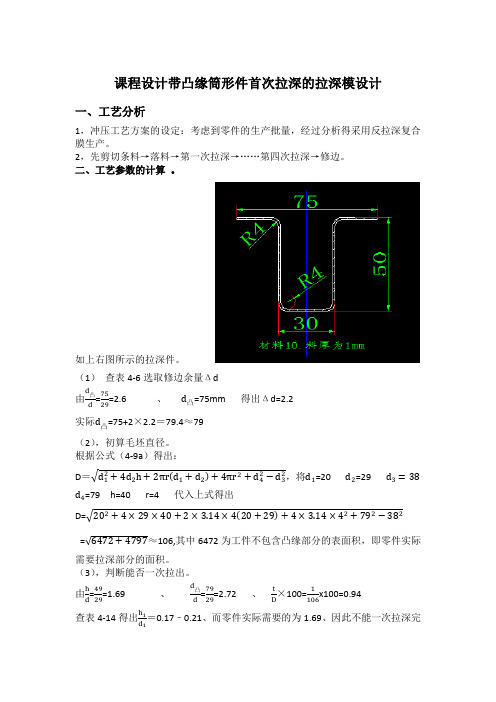
课程设计带凸缘筒形件首次拉深的拉深模设计一、工艺分析1,冲压工艺方案的设定:考虑到零件的生产批量,经过分析得采用反拉深复合膜生产。
2,先剪切条料→落料→第一次拉深→……第四次拉深→修边。
二、工艺参数的计算 。
如上右图所示的拉深件。
(1) 查表4-6选取修边余量Δd 由d 凸d=7529=2.6 、 d 凸=75mm 得出Δd=2.2实际d 凸=75+2×2.2=79.4≈79 (2),初算毛坯直径。
根据公式(4-9a )得出:D =√d 12+4d 2h +2πr (d 1+d 2)+4πr 2+d 42−d 32,将d 1=20 d 2=29 d 3=38d 4=79 h=40 r=4 代入上式得出D=√202+4×29×40+2×3.14×4(20+29)+4×3.14×42+792−382 =√6472+4797≈106,其中6472为工件不包含凸缘部分的表面积,即零件实际需要拉深部分的面积。
(3),判断能否一次拉出。
由h d =4929=1.69 、d 凸d=7929=2.72 、 t D ×100=1106x100=0.94查表4-14得出h1d 1=0.17﹣0.21、而零件实际需要的为1.69、因此不能一次拉深完成。
(4),计算拉深次数及各工序的拉深直径。
,因此需要用试凑法计算利用表4-14来进行计算,但由于有两个未知数m和d td1拉深直径。
下面用逼近法来确定第一的拉深直径。
的值为由于实际拉深系数应该比极限拉伸系数稍大,才符合要求,所以上表中d td11.5、1.6、1.7的不合适。
因为当d t的值取1.4的时候,实际拉深系数与极限拉深系数接近。
故初定第一次d1拉深直径d1=56.因以后各次拉深,按表4-8选取。
故查表4-8选取以后各次的拉深系数为当m2=0.77时d2=d1×m2=56×0.77=43mm当m2=0.79时d3=d2×m3=43×0.79=34mm当m3=0.81时d4=d3×m4=34×0.81=27mm<29mm因此以上各次拉程度分配不合理,需要进行如下调整。
带凸缘筒形件拉深模工作零件设计实例汇总

职业教育材料成型与控制技术专业教学资源库
三、第三次拉深凸、凹模尺寸计算
零件标注内形尺寸( 拉深凸模: ),计算应以凸模为基准。
拉深凹模:
其他金属材料成型技术课程
职业教育材料成型与控制技术专业教学资源库
其他金属材料成型技术课程
带凸缘筒形件拉深模 工作零件设计实例
主讲教师:吕淑艳 包头职业技术学院
职业教育材料成型与控制技术专业教学资源库
目
1 1 2 3
录
首次拉深凸、凹模尺寸计算
第二次拉深凸、凹模尺寸计算
第三次拉深凸、凹模尺寸计算
其他金属材料成型技术课程
职业教育材料成型与控制技术专业教学资源库
一、首次拉深凸、凹模尺寸计算
第一次拉深件后零件直径为86.35mm,首先确定
拉深凸、凹模间隙,查表得拉深凸、凹模间隙系
数
,则间隙为
其他金属材料成型技术课程
职业教育材料成型与控制技术专业教学资源库
拉深凹模
拉深凸模
其他金属材料成型技术课程
职业教育材料成型与控制技术专业教学资源库
二、第二次拉深凸、凹模尺寸计算
第二次拉深后零件直径为Φ68.21mm,拉深凸、凹模
间隙值仍为2.25mm,由于第二次拉深为中间过渡工序件,
所以在计算时,既可以先计算凹模刃口尺寸,也可以先计 算凸模尺寸,本例中先计算凹模尺寸,具体如下。
其他金属材料成型技术课程来自职业教育材料成型与控制技术专业教学资源库
拉深凹模
拉深凸模
其他金属材料成型技术课程
带凸缘圆筒形件的拉深
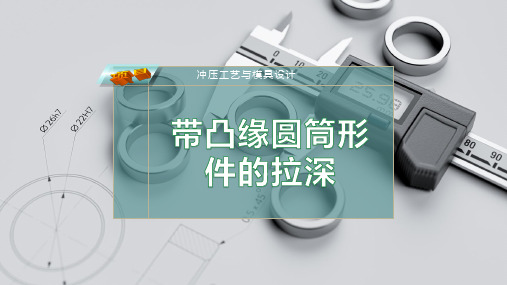
带凸缘圆筒形件的拉深
带凸缘圆筒形件
带凸缘圆筒形件的拉深
1.1 窄凸缘圆筒形件的拉深
窄凸缘圆筒形件第一种拉深方法
带凸缘圆筒形件的拉深
1.1 窄凸缘圆筒形件的拉深
窄凸缘圆筒形件第二种拉深方法
带凸缘圆筒形件的拉深
1.2 宽凸缘圆筒形件的拉深
当 r凸 = r凹 = r 时,宽凸缘圆筒形件毛坯直径 D 为:
根据拉深系数的定义,宽凸缘圆筒形件的拉深系数为:
带凸缘圆筒形件的拉深
1.2 宽凸缘圆筒形件的拉深
宽凸缘圆筒形件的尺寸
带凸缘圆筒形件的拉深
1.2 宽凸缘圆筒形件的拉深
毛坯尺寸的 计算
判断工件是 否一次拉深
成形
凸缘件多次 拉深成形
原则
带凸缘圆筒形件的拉深
1.2 宽凸缘圆筒形件的拉深
这种工件通常采用 减小筒部直径、增加筒部 高度来达到最终尺寸。圆 角半径在整个拉深过程中 基本不变。
8)根据表4-5选取以后各次拉深系数 m2、m3、…、mn,并预算出 各工序的拉深直径 d2=m2d1、d3=m3d2、…、dn=mndn-1。 若 dn<d,按式(4-2)放大 K 值,于是各次拉深直径为:
d2 = m2d1K、d3 = m3d2 K、…、dn = mndn-1 K。
带凸缘圆筒形件的拉深
时,可一次拉成。否则需要多次拉成。 4)根据表4-8选取 m1,计算 d1=m1D。初选第1次拉深的相对凸 缘直径为 dt/d1=1.1,若 m1 选的不合理,选 dt/d1=1.2、1.3…,直 到 m1 选择合理为止。 5)按照式(4-3)、式(4-4)计算第1次拉深模的凹、凸模圆角 半径。 6)根据宽凸缘圆筒件的拉深原则来修正毛坯直径D,并计算首次 拉深半成品高度 h1 为:
冲压模具设计-带凸缘圆筒件

带凸缘圆筒拉深模设计班级:姓名:学号:日期:前言冷冲压模具的设计与制造一材料的塑性变形理论为基础,综合了塑性力学、机械力学、机械原理与设计、机械设计制造工艺等多学科的应用,是一门理论性和应用性很强的课程。
围绕冷冲模设计,前向有冲压工艺,后有制造工艺,在数字化技术应用高度发展的今天,冷冲模开发的三个层面已经高度集成,紧密融合在一起。
通过冷冲压的理论学习,然后再将理论知识用于实际中,不仅有助于理论知识的消化吸收,也可以提高自身的工程能力。
为此,进行必要的冷冲模的课程设计很有必要。
结合所学到的理论知识和自身掌握的情况,特以带凸缘的圆筒件来设计冷冲压模具。
此制件结构简单,容易上手学习,并且涵盖了所学的知识点,是一个很好的设计素材。
本设计大致分为三个部分,一是制件及模具的参数确定,一是模具的结构设计,一是制件的成形分析。
目录前言 (I)一制件工艺分析 (1)1.1 制件分析 (1)1.2坯料直径确定 (1)1.3 拉深成型次数计算 (2)1.4 凸凹模圆角半径计算 (3)1.5 拉深深度计算 (4)1.6 拉深力的计算 (4)1.7 凸凹模间隙计算 (5)1.8 凸凹模工件尺寸计算 (5)1.8.1 凸凹模计算公式 (5)1.8.2 公差确定 (6)1.9 凸模通气尺寸 (6)二拉深模结构设计 (8)2.1 拉深凸凹模结构 (8)2.2 模具总体结构的设计 (8)三 Dynaform软件仿真分析 (10)3.1网格划分 (10)3.2 毛坯轮廓线计算 (11)3.3 制件厚度分析 (11)3.4 主应力分布 (12)3.5 制件成形情况 (14)总结 (15)参考文献 (17)附表 (18)一制件工艺分析1.1 制件分析所选的制件为带凸缘圆筒件,剖视图如下,厚度为2mm,材料为08钢。
图1 带凸缘圆筒件此带凸缘圆筒件为旋转体,壁厚为2mm,整个结构尺寸较小,适合冲压成型。
底部外直径为42mm,筒深大约为60mm,材料为08钢,拉深性能较好,适合于拉伸成型。
宽凸缘圆筒形拉伸件级进模具设计实例
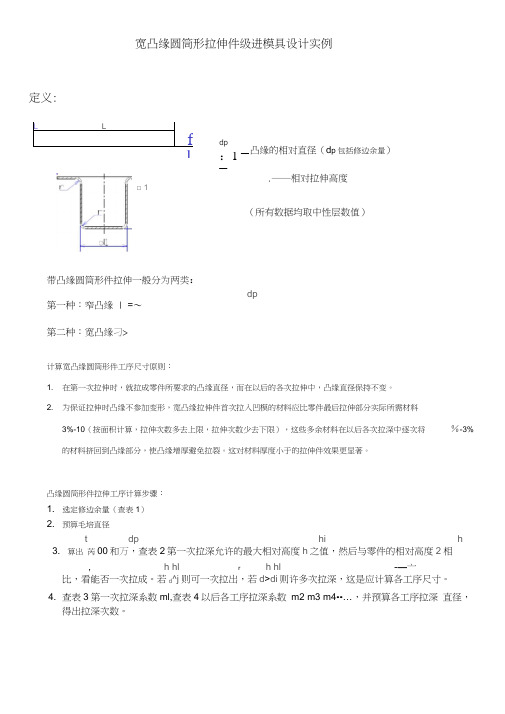
宽凸缘圆筒形拉伸件级进模具设计实例.――相对拉伸高度□ 1(所有数据均取中性层数值)带凸缘圆筒形件拉伸一般分为两类:dp第一种:窄凸缘 | =〜 第二种:宽凸缘刁>计算宽凸缘圆筒形件工序尺寸原则:1. 在第一次拉伸时,就拉成零件所要求的凸缘直径,而在以后的各次拉伸中,凸缘直径保持不变。
2. 为保证拉伸时凸缘不参加变形,宽凸缘拉伸件首次拉入凹模的材料应比零件最后拉伸部分实际所需材料3%-10(按面积计算,拉伸次数多去上限,拉伸次数少去下限),这些多余材料在以后各次拉深中逐次将 %-3%的材料挤回到凸缘部分,使凸缘增厚避免拉裂。
这对材料厚度小于的拉伸件效果更显著。
凸缘圆筒形件拉伸工序计算步骤:1. 选定修边余量(查表1)2. 预算毛培直径tdp hi h3. 算出 芮00和万,查表2第一次拉深允许的最大相对高度h 之值,然后与零件的相对高度2相 , h hl rh hl -—亠 比,看能否一次拉成。
若d ^j 则可一次拉出,若d >di 则许多次拉深,这是应计算各工序尺寸。
4. 查表3第一次拉深系数ml,查表4以后各工序拉深系数 m2 m3 m4••…,并预算各工序拉深 直径,得出拉深次数。
定义:LLf1dp:1 ——凸缘的相对直径(d p 包括修边余量)5. 调整各工序拉深系数。
计算实例凸缘直径:d p= 拉伸直径:d= 拉伸高度:H= 材料厚度:t=12. 修边余量表1带凸缘拉深件修边余量相对凸缘尺寸:|;|]=74/ =;根据上面的表格(表1) v' =<2 ;50<dp=74 <1004<100则,带凸缘的拉伸件修边余量:2〜3,取值3贝带凸缘的拉伸件修边余量:△ d=3 mm3. 展开根据成型前后中性层的面积不变原理使用UC测量出拉深件中性层面积mmL (不推荐使用公式计算,个人感觉一般计算得数偏大, 故本文省略公式)则,展开尺寸D= ' —一—1 . : = ~ 97 mm\R2,54. 拉深系数确定表3带凸缘拉深件的首次拉深最大相对高度 h1/d1表4带凸缘拉深件的以后各次拉深系数674-9/ y*、一..L展开直径:D=97 凸缘直径:d 凸=80.9 拉伸直径:d=43.15 拉伸高度:H=19.5 材料厚度:t=1修边余量:△ d=3(1) 验证可否一次完成拉伸材料相对厚度:t/D=1/97 X 100=~ 1凸缘相对直径:dp/d==总的拉伸系数:M=d/D=97=根据上表(附表2): < t/D < 1; < dp/d <2则有工艺切口的首次最小拉伸系数M1=M根据上表(附表3)有工艺切口的首次拉伸最大相对高度:h/d==>所以,根据M仁M和h/d=> ,判定一次拉伸不能成功,需要多步拉伸。
- 1、下载文档前请自行甄别文档内容的完整性,平台不提供额外的编辑、内容补充、找答案等附加服务。
- 2、"仅部分预览"的文档,不可在线预览部分如存在完整性等问题,可反馈申请退款(可完整预览的文档不适用该条件!)。
- 3、如文档侵犯您的权益,请联系客服反馈,我们会尽快为您处理(人工客服工作时间:9:00-18:30)。
普通本科课程设计说明书课题名称筒形凸缘件拉深模设计学院班级学号姓名目录设计任务书 (3)筒形凸缘件拉深模设计 (3)一.拉深件工艺分析 (3)二.零件主要参数的计算 (3)1.计算毛坯直径D (3)2.判断拉深次数 (3)3.落料凸、凹模尺寸 (4)4.拉深凸、凹模尺寸 (5)5.拉深凸、凹模圆角 (5)6.整体落料凹模板的厚度H的确定 (6)7.凸凹模长度 (6)8.冲孔凸模长度 (6)三.相关力的计算 (7)1、落料力的计算 (7)2.卸料力错误!未找到引用源。
和顶件力错误!未找到引用源。
的计算 (7)3.压边力及压边装置的确定 (8)4.拉深力的计算 (8)四.排样图和裁板方案 (9)五.模具结构图........................................................................................ 错误!未定义书签。
1.总装配图...................................................................................... 错误!未定义书签。
2.落料凹模 (9)3.凸凹模 (10)4.拉深凸模 (10)5.模架 (11)设计任务书一、设计题目: 筒形凸缘件拉深模设计生产批量: 大批量材 料: H62材料厚度: 0.5 mm筒形凸缘件拉深模设计一.拉深件工艺分析1.材料:H62是黄铜,平均屈服极限为235MPa ,抗拉强度为错误!未找到引用源。
300~350MP ,现取错误!未找到引用源。
300MP ,剪切强度错误!未找到引用源。
240~280MP ,现取错误!未找到引用源。
100MP ,具有较好的可拉深性能。
2.零件结构:该制件为筒形带凸缘拉深件,形状简单,尺寸小且精度要求不高,属于普通拉深件,由落料和拉深即可成形。
3.尺寸精度:材料厚度为0.5mm ,零件图上所有未注公差的尺寸,属于自由尺寸,可按IT13级确定工件尺寸的公差。
二.零件主要参数的计算1.计算毛坯直径D查课本表4.2.2,取错误!未找到引用源。
切边余量△R=2故带切边余量的拉深件凸缘直径为 错误!未找到引用源。
392235=⨯+=f d mm 错误!未找到引用源。
4.18.12139≥==d d f(该件为宽凸缘) 5844.34222=-+=rd H d d D f 2.判断拉深次数由毛坯的相对厚度t/D ×100=0.8,从课本表 4.2.4查得各次拉深系数:82.0,80.0,77.0,54.04321====m m m m 。
零件的总拉伸系数34.058/5.19/2===D d m 总≤0.54,该工件需经多次拉深才能达到所需尺寸。
32.315854.011=⨯==D m d1.2432.3177.0122=⨯==d m d3.191.248.0233=⨯==d m d可知零件要拉深3次3.落料凸、凹模尺寸落料时,零件的基本尺寸为D=58mm ,此处没有零件公差,其值按标准公差(GB/T1800.3-1998)取,公差等级取IT13,查得:零件公差 错误!未找到引用源。
落料板坯所用材料为H62,厚度t 为0.5,查表(《金属塑性加工模具设计与制造》P166,表5-2),得:最小间隙错误!未找到引用源。
;最大间隙错误!未找到引用源。
;所要落料的零件为圆形件,制造公差查表得:凸模制造公差错误!未找到引用源。
;凹模制造公差错误!未找到引用源。
;错误!未找到引用源。
因为错误!未找到引用源。
,不符合要求,故:错误!未找到引用源。
;错误!未找到引用源。
;已查出,零件公差错误!未找到引用源。
磨损系数由查表(《金属塑性加工模具设计与制造》P170,表5-6)得,错误!未找到引用源。
计算:凹模直径mm x D D 024.00024.00077.5746.05.058)+++=⨯-=∆-=)((凹凹δ凸模直径0016.00016.00min 76.5701.046.05.058)---=-⨯-=-∆-=)((凸凸δZ x D D 错误!未找到引用源。
4.拉深凸、凹模尺寸由零件参数可知:零件公差 错误!未找到引用源。
查表(《实用冲压工艺及模具设计》)P152,表5-20),得:凸模制造公差错误!未找到引用源。
;凹模制造公差错误!未找到引用源。
有压边圈时凸凹模单边间隙值:错误!未找到引用源。
,此处取错误!未找到引用源。
,故错误!未找到引用源。
;凹模直径mm d d p 070.00070.00089.19)15.075.020()75.0+++=⨯-=∆-=δ(凹凸模直径 004.006.17)2.215.075.020()75.0(--=-⨯-=-∆-=P Z d d δ凸mm5.拉深凸、凹模圆角考虑到实际采用的拉深系数均接近其极限值,故首次拉深凹模圆角半径r 1d 应取大些,由公式mm t r d 65.012)18~12(1=⨯==第一次凸模圆角半径mm r r d p 8.468.0)0.1~7.0(11=⨯==以后各次拉深凹凸模圆角半径由公式:)1()8.0~6.0(-=n d dn r r 2/)2(21)1(t d d r n n n p --=---即圆角半径分别为:8.42=d r 11.32=p r84.33=d r 9.13=p r6.整体落料凹模板的厚度H 的确定计算按公式:错误!未找到引用源。
式中:K 为厚度系数S 为凹模刃口最大尺寸K 值查表(《冲压工艺与模具设计》P93,表3-19)可知,其值取0.20~0.30,此处取0.25, 计算:mm KS H 45.14)024.077.57(25.0=+⨯==壁厚9.282==H C mm7.凸凹模长度落料时凸模长度计算按公式:错误!未找到引用源。
式中:错误!未找到引用源。
为凸模固定板厚度,一般取值(0.6~0.8)H,此处取10mm;错误!未找到引用源。
为卸料板厚度,一般取值(5~20mm),此处取10mm;错误!未找到引用源。
为导料板厚度,查表(《冲压工艺与模具设计》P98,表3-21),得,取值6mm;h为附加长度,主要考虑凸模进入凹模的深度(0.5~1.0mm)及模具闭合状态下卸料板到凸模固定板间的安全距离(一般取15~20mm),此处分别取值0.6mm,16mm.计算:8.冲孔凸模长度冲孔凸模长度等于落料凹模的厚度,取值14.45mm三.相关力的计算1、落料力的计算式中:L为冲裁轮廓的总长度t为板料厚度错误!未找到引用源。
为材料的抗剪强度H62错误!未找到引用源。
故:⨯⨯⨯=π⨯5.058=300N.F133.1355落料2.卸料力错误!未找到引用源。
和顶件力错误!未找到引用源。
的计算式中,错误!未找到引用源。
为卸料力系数;错误!未找到引用源。
为顶件力系数;查表(《冲压工艺与模具设计》P56表3-15)知:错误!未找到引用源。
错误!未找到引用源。
故:N F K F 21.1413.35504.0=⨯==落卸卸N F K F 31.2113.35506.0=⨯==落顶顶3.压边力及压边装置的确定在生产中采用压边的目的是为了防止变形区板料在拉深过程中的起皱,拉深时压边力必须适当,压边力过大会引起拉深力的增加,甚至造成制件拉裂,压边力过小则会造成制件直壁或凸缘部分起皱,所以是否采用压边装置主要取决于毛坯或拉深系数和相对厚度 由于相对厚度t/D ×100=0.8错误!未找到引用源。
拉深系数34.058/5.19/2===D d m 总查表(《冲压工艺与模具设计》P197,表5-11)知,该工件拉深时应该采用平板压边圈 1)压边力:错误!未找到引用源。
p 为单位面积压料力,其值查表(《冲压工艺与模具设计》P199,表5-12),得:错误!未找到引用源。
KNp r d D F 77.52.2)]2220(58[)]2([2424=⨯⨯+-=⨯+-=ππ压边 错误!未找到引用源。
2)压边圈尺寸:计算按公式:压边圈内经错误!未找到引用源。
;压边圈外径错误!未找到引用源。
错误!未找到引用源。
为拉深凸模外径,D 为拉深前半成品工件内经计算:内径 mm d d 62.176.1702.002.0=+=+=凸内外径 97.1903.02003.0=-=-=d d 外mm4.拉深力的计算计算按公式:错误!未找到引用源。
式中: d 为零件直径t 为模具厚度错误!未找到引用源。
为H62抗拉强度错误!未找到引用源。
为修正系数,其值查表(《冲压工艺与模具设计》P200,表5-13)得:错误!未找到引用源。
=1.0;KN K dt F b 18.95.013005.1914.31=⨯⨯⨯⨯==σπ四.排样图和裁板方案1. 制件的毛坯为简单的圆形件,而且尺寸比较小,考虑到操作方便,宜采用单排。
由于料厚t=0.5mm2.排样设计查课本表2.5.2,确定搭边值两工件间的横搭边错误!未找到引用源。
;两工件间的纵搭边错误!未找到引用源。
; 步距S=D+a=58+1.2=59.2mm条料宽度mm a D B 046.0046.0046.0146.61)46.05.1258()2(---=+⨯+=∆++=2.落料凹模凹模采用整体凹模,刃口尺寸6mm 。
整体结构如下图:3.凸凹模结合工件外形并考虑加工,将凸凹模设计成带肩台阶式圆凸凹模,采用车加工,结构如图:4.拉深凸模拉深凸模采用台阶式,采用车床加工,与凸模固定板的配合按H7/m6的配合。
结构如下图:5.模架采用滑动导向后侧导柱式模架的导向方式,模架的结构与尺寸都直接由标准中选取,相关参数如下:上模座规格:250×250×50导柱规格:35×230导套规格:35×125×48总体设计图如下:。