无凸缘筒形件拉深模设计与制造 ppt课件
第一节 圆筒形零件拉深

式中 d——冲件直径; D——坯料直径;
m1——第一次拉深系数;
m均——第一次拉深以后各次的平均拉深系数
拉 深 过 程 的 应 力 与 应 变 状 态
下标1、2、3分别代表坯料径向、 厚度方向、切向的应力和应变
圆 筒 形 件 拉 深 时 凸 缘 变 形 区 的 应 力 分 布
②推算方法 A.由表5-4或表5-5中查得各次的极限拉深系数; B.依次计算出各次拉深直径,即
d1=m1D;d2=m2d1;…;dn=mndn-1
C.当dn≤d时,计算的次数即为拉深次数。
一、无凸缘圆筒形零件拉深 7、拉深次数与工序尺寸 1)拉深次数的确定
③计算方法 拉深次数
lg d 1gm1D n 1 lg m均
D2 ri H i 0.25 d 0 . 43 (di 0.32ri ) i d di i
一、无凸缘圆筒形零件拉深
8、后续各次拉深的特点 后续各次拉深所用的毛坯不是平板而是筒形件,因此,它与 首次拉深相比,有许多不同之处. 9、圆筒形零件拉深的压料力和拉深力 1)压料装置与压料力 在模具结构上采用压料装置防止拉深过程中的起皱,可按 表5-7判断。 压料装置产生的压料力Fy大小应适当; 在保证变形区不起皱的前提下,尽量选用小的压料力。
一、无凸缘圆筒形零件拉深
5、旋转体拉深件坯料尺寸的确定
1)坯料形状和尺寸确定的依据
(1)体积不变原则 若拉深前后料厚不变,拉深前坯料表面积与拉深后工件表面 积近似相等。
(2)相似原理
毛坯的形状一般与工件截面形状相似,但坯料的周边必须是 光滑的曲线连接。形状复杂的拉深件,需多次试压,反复修改, 才能最终确定坯料形状。 拉深件的模具设计顺序: 先设计拉深模,坯料形状尺寸确定后再设计冲裁模。 切边工序:拉深件口部不整齐,需留切边余量。
无凸缘一次拉深
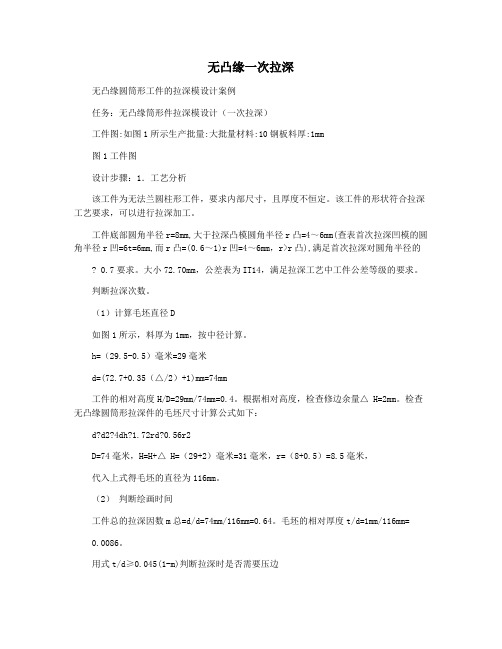
无凸缘一次拉深无凸缘圆筒形工件的拉深模设计案例任务:无凸缘筒形件拉深模设计(一次拉深)工件图:如图1所示生产批量:大批量材料:10钢板料厚:1mm图1工件图设计步骤:1.工艺分析该工件为无法兰圆柱形工件,要求内部尺寸,且厚度不恒定。
该工件的形状符合拉深工艺要求,可以进行拉深加工。
工件底部圆角半径r=8mm,大于拉深凸模圆角半径r凸=4~6mm(查表首次拉深凹模的圆角半径r凹=6t=6mm,而r凸=(0.6~1)r凹=4~6mm,r>r凸),满足首次拉深对圆角半径的? 0.7要求。
大小72.70mm,公差表为IT14,满足拉深工艺中工件公差等级的要求。
判断拉深次数。
(1)计算毛坯直径D如图1所示,料厚为1mm,按中径计算。
h=(29.5-0.5)毫米=29毫米d=(72.7+0.35(△/2)+1)mm=74mm工件的相对高度H/D=29mm/74mm=0.4。
根据相对高度,检查修边余量△ H=2mm。
检查无凸缘圆筒形拉深件的毛坯尺寸计算公式如下:d?d2?4dh?1.72rd?0.56r2D=74毫米,H=H+△ H=(29+2)毫米=31毫米,r=(8+0.5)=8.5毫米,代入上式得毛坯的直径为116mm。
(2)判断绘画时间工件总的拉深因数m总=d/d=74mm/116mm=0.64。
毛坯的相对厚度t/d=1mm/116mm=0.0086。
用式t/d≥0.045(1-m)判断拉深时是否需要压边(1米)?0.045(1?0.64)? 0.0162至0.0451T/D呢?0.0086? 0.045(1米)?0.0162,因此有必要对侧环加压。
由相对厚度查表(无凸缘圆筒件用压边圈拉伸时的拉伸系数)得首次拉深的极限拉深因数m1=0.54。
由于m始终大于m1,工件只需一次拉深。
2.确定工艺方案本工件首先需要落料,制成直径d=116mm的圆片(由冲裁工艺完成),然后以d=116mm? 待拔坯料的内径为0.7?72.70mm无法兰圆筒,内圆角r为8mm,最后压入h=29.5mm进行修边。
第四章 拉深工艺及模具设计PPT课件

屈强比 s 小b ,板料不容易起皱。
23.09.2020
18
拉深过程中起皱条件
平端面凹模拉深时,毛坯首次拉深不起皱的条件:
t 0.09~0.071d
D
D
锥形凹模首次拉深时,材料不起皱的条件:
t 0.031 d
D
D
采用或不采用压边圈的条件
拉深方法
用压边圈 可用可不用 不用压边圈
23.09.2020
28
【例】如图所示的圆筒形拉深件,材料为08钢,料厚为2 mm,求其毛
坯尺寸。
解: h200t 2001199 2
d90t 90288
因该零件相对高度
h /d 1/9 8 9 8 2 .26
而高度 h19 195 ~2 000
查表4-3可知,修边余量 8mm,因而毛坯直径为 d1 82 mm
23.09.2020
22
筒壁的拉裂
主要取决于: 一方面是筒壁传力区中的拉应力;另一方面是筒壁传力区 的抗拉强度。
当筒壁拉应力超过筒壁材料的抗拉强度时,拉深件就会在底部圆 角与筒壁相切处——“危险断面”产生破裂。
防止拉裂的措施:
根据板材的成形性能,采用适当的拉深比和压边力,增加凸模 的表面粗糙度,改善凸缘部分变形材料的润滑条件,合理设计模具
它是冲压基本工序之一。可以加工旋转体零件,还可加 工盒形零件及其它形状复杂的薄壁零件。
23.09.2020
3
拉深工艺分类:
不变薄拉深: 把毛坯拉压成空心体,或者把空心体拉压成外
形更小而板厚没有明显变化的空心体的冲压工序。
变薄拉深: 是指凸、凹模之间间隙小于空心毛坯壁厚,把
空心毛坯加工成侧壁厚度小于毛坯壁厚的薄壁制件 的冲压工序。
无凸缘筒形件的拉深模具设计说明

无凸缘筒形拉深件模具设计目录一、概述 (3)1. 模具概述 (3)2. 冷冲模具工业的现状 (3)3. 冷冲模具的发展方向 (3)二、工艺方案分析及确定 (4)1. 零件工艺性分析 (4)i. 材料分析 (4)ii. 结构分析 (4)iii. 一次拉深成形条件 (4)iv. 拉深件所能达到的偏差 (4)v. 变形特点的分析 (5)2. 工艺方法的确定 (5)三、零件工艺计算 (5)1. 拉深工艺计算 (5)i. 确定零件修边余量 (5)ii. 确定坯料尺寸D (5)iii. 判断是否采用压边圈 (6)iv. 确定拉深次数 (6)v. 确定各次拉深半成品尺寸 (6)vi. 拉深件工序尺寸图 (6)vii. 排样计算 (7)2. 拉深压力计算与设备的选择 (8)i. 首次拉深 (8)ii. 二次拉深: (8)iii. 压力中心的计算 (9)iv. 压力设备的选择 (9)3. 拉深模工作零件设计与计算 (9)i. 凸、凹模刃口尺寸计算 (9)ii. 落料拉深复合模其它工艺计算 (11)四、模具结构的确定 (12)1. 模具的形式 (12)i. 正装式特点 (12)ii. 倒装式特点 (12)2. 定位装置 (13)3. 卸料装置 (13)i. 条料的卸除 (13)ii. 出件装置 (13)4. 导向零件 (13)5. 模架 (13)i. 标准模架的选用 (13)五、第二次拉深凹模零件图 (15)i. 拉深凹模如图5-1所示 (15)六、第二次拉深凸模零件图 (15)ii. 拉深凸模如图5-2所示 (15)七、模具的工作原理 (15)1. 拉深的变形过程 (15)2. 各种拉深现象 (16)i. 起皱: (16)ii. 变形的不均匀: (16)iii. 材料硬化不均匀 (16)八、总结 (17)九、参考文献 (18)一、概述1.模具概述模具是高新技术产业的一个组成部分,是工业生产的重要基础装备.用模具生产的产品,其价值往往是模具价值的几十倍。
无凸缘筒形件拉深模设计与制造

F落 KLt
1.3 3.14105 2 320N
274310.4N 274.3kN
F压
4
[D2
(d1
t
2rA )2 ]P
F拉 d1t b K1
3.14 55.65 2 400 0.8N 111834.24N 111.8kN
[1052 (55.65 2 28)2 ] 2.2N
模零件图
A
深15
落料拉深复
A
合模凸凹模
装后磨
零件图
落料拉深复 合模卸料板 零件图
A
落料拉深复 合模凸模零 件图
A
均布
六、第二次拉深 模具装配图
9
8 7 6 5 4 3 2 1
10 11 12 13
14 15 16 17
第二次拉深上模 座零件图
0.8
A 与下模座配镗
深15
上模座
制图
第二次拉深 下模座零件 图
4.第四次拉深模工艺计算 (1)拉深凸、凹模尺寸计算 因为零件标注外形尺寸( 32 0.04)mm,所以要先计算 凹模,即
DA
(d m ax
0.75
)
0
A
(32.04
0.75
0.08)
0.08 0
mm
31.98
0.08 0
mm
DT
(DA
2Z
)
0 T
(31.98
(3)判断是否采用压边圈
零件的相对厚度 t 100 2 100 1.9,经查压边圈为可用可不
D
筒形件拉深模具设计无凸缘

前言1.1冲压的概念、特点及应用冲压是利用安装在冲压设备(主要是压力机)上的模具对材料施加压力,使其产生分离或塑性变形,从而获得所需零件(俗称冲压或冲压件)的一种压力加工方法。
冲压通常是在常温下对材料进行冷变形加工,且主要采用板料来加工成所需零件,所以也叫冷冲压或板料冲压。
冲压是材料压力加工或塑性加工的主要方法之一,隶属于材料成型工程术。
冲压所使用的模具称为冲压模具,简称冲模。
冲模是将材料(金属或非金属)批量加工成所需冲件的专用工具。
冲模在冲压中至关重要,没有符合要求的冲模,批量冲压生产就难以进行;没有先进的冲模,先进的冲压工艺就无法实现。
冲压工艺与模具、冲压设备和冲压材料构成冲压加工的三要素,只有它们相互结合才能得出冲压件。
与机械加工及塑性加工的其它方法相比,冲压加工无论在技术方面还是经济方面都具有许多独特的优点。
主要表现如下。
(1) 冲压加工的生产效率高,且操作方便,易于实现机械化与自动化。
这是因为冲压是依靠冲模和冲压设备来完成加工,普通压力机的行程次数为每分钟可达几十次,高速压力要每分钟可达数百次甚至千次以上,而且每次冲压行程就可能得到一个冲件。
(2)冲压时由于模具保证了冲压件的尺寸与形状精度,且一般不破坏冲压件的表面质量,而模具的寿命一般较长,所以冲压的质量稳定,互换性好,具有“一模一样”的特征。
(3)冲压可加工出尺寸范围较大、形状较复杂的零件,如小到钟表的秒表,大到汽车纵梁、覆盖件等,加上冲压时材料的冷变形硬化效应,冲压的强度和刚度均较高。
(4)冲压一般没有切屑碎料生成,材料的消耗较少,且不需其它加热设备,因而是一种省料,节能的加工方法,冲压件的成本较低。
但是,冲压加工所使用的模具一般具有专用性,有时一个复杂零件需要数套模具才能加工成形,且模具制造的精度高,技术要求高,是技术密集形产品。
所以,只有在冲压件生产批量较大的情况下,冲压加工的优点才能充分体现,从而获得较好的经济效益。
冲压地、在现代工业生产中,尤其是大批量生产中应用十分广泛。
第08章--拉深模具设计PPT课件
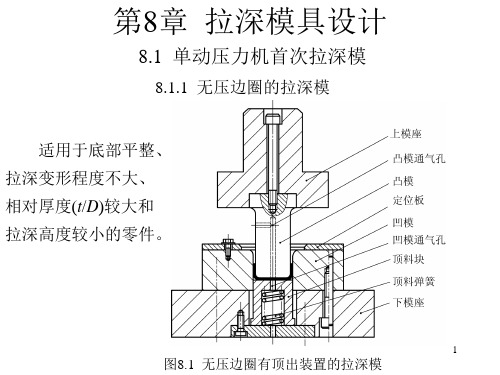
以由弹簧或橡皮产生,也可以由气垫产生。
5
带凸缘零 件的拉深模结 构,毛坯用定 位板定位,在 下模座上安装 了定距垫块, 用来控制拉深 深度,以保证 制件的拉深高 度和凸缘直径。
图8.6 凸缘件拉深模(定距垫块) 6
图8.7 凸缘件拉深模(打料块定距)
毛坯用固定挡料销定位,打料块同时起定距垫块的作用, 作用同样是控制拉深高度和凸缘直径。
第8章 拉深模具设计
8.1 单动压力机首次拉深模
8.1.1 无压边圈的拉深模
适用于底部平整、 拉深变形程度不大、 相对厚度(t/D)较大和 拉深高度较小的零件。
1
图8.1 无压边圈有顶出装置的拉深模
8.1.2 带压边圈的拉深模
板料毛坯 被拉入凹模。 在拉簧力的作 用下,刮件环 又紧贴凸模, 在凸模上行时 可以将制件脱 出,由下模座 孔中落下。
下止点
30°
60°
曲轴转角α
90° 23
8.6.4 模具工作部分尺寸的计算
1. 凸、凹模间隙 2. 凸、凹模圆角半径 3. 凸、凹模工作尺寸及公差 4. 凸模通气孔
24
8.6.5 模具的总体设计
模具的总装图如 图8.26所示。
采用正装式结构, 落料拉深凸凹模安装 在上模;
刚性卸料板卸去 废料,也起导尺作用,
线,
若落料拉深力曲线处于许用负荷曲线之下,则所选设备符合
工作要求;
若落料拉深力曲线超出许可范围(见图8.25),则需选择标称
压力更大型号的压力机,继续以上校核过程。
26
图8.25 许用负荷与实际负荷
27
用导尺和固定挡 料销定位;
打料块将卡在凸 凹模内的工件推出。
图8.26 落料首次拉深复合模 25
筒形件拉深模具设计无凸缘

前言1.1冲压的概念、特点及应用冲压是利用安装在冲压设备〔要紧是压力机〕上的模具对材料施加压力,使其产生不离或塑性变形,从而获得所需零件〔俗称冲压或冲压件〕的一种压力加工方法。
冲压通常是在常温下对材料进行冷变形加工,且要紧采纳板料来加工成所需零件,因此也喊冷冲压或板料冲压。
冲压是材料压力加工或塑性加工的要紧方法之一,隶属于材料成型工程术。
冲压所使用的模具称为冲压模具,简称冲模。
冲模是将材料〔金属或非金属〕批量加工成所需冲件的专用工具。
冲模在冲压中至关重要,没有符合要求的冲模,批量冲压生产就难以进行;没有先进的冲模,先进的冲压工艺就无法实现。
冲压工艺与模具、冲压设备和冲压材料构成冲压加工的三要素,只有它们相互结合才能得出冲压件。
与机械加工及塑性加工的其它方法相比,冲压加工不管在技术方面依然经济方面都具有许多独特的优点。
要紧表现如下。
(1)冲压加工的生产效率高,且操作方便,易于实现机械化与自动化。
这是因为冲压是依靠冲模和冲压设备来完成加工,一般压力机的行程次数为每分钟可达几十次,高速压力要每分钟可达数百次甚至千次以上,而且每次冲压行程就可能得到一个冲件。
〔2〕冲压时由于模具保证了冲压件的尺寸与外形精度,且一般不破坏冲压件的外表质量,而模具的寿命一般较长,因此冲压的质量稳定,互换性好,具有“一模一样〞的特征。
〔3〕冲压可加工出尺寸范围较大、外形较复杂的零件,如小到钟表的秒表,大到汽车纵梁、覆盖件等,加上冲压时材料的冷变形硬化效应,冲压的强度和刚度均较高。
〔4〕冲压一般没有切屑碎料生成,材料的消耗较少,且不需其它加热设备,因而是一种省料,节能的加工方法,冲压件的本钞票较低。
然而,冲压加工所使用的模具一般具有专用性,有时一个复杂零件需要数套模具才能加工成形,且模具制造的精度高,技术要求高,是技术密集形产品。
因此,只有在冲压件生产批量较大的情况下,冲压加工的优点才能充分表达,从而获得较好的经济效益。
冲压地、在现代工业生产中,尤其是大批量生产中应用十分广泛。
- 1、下载文档前请自行甄别文档内容的完整性,平台不提供额外的编辑、内容补充、找答案等附加服务。
- 2、"仅部分预览"的文档,不可在线预览部分如存在完整性等问题,可反馈申请退款(可完整预览的文档不适用该条件!)。
- 3、如文档侵犯您的权益,请联系客服反馈,我们会尽快为您处理(人工客服工作时间:9:00-18:30)。
h10.25(D d12 d1)0.43dr11(d10.32 r1)
0.25(102555 .6)5mm 0.43 8 (55 .650.328)mm
55 D d22 d2)0.43 dr22(d20.3r22)
0.25 (10254.34)1mm 0.43 6.5 (4.341 0.32 6.5)mm
h d
8012.63 30
,经查得修边余量
h6mm ,
所以,修正后拉深件的总高应为79+6=85mm。
(2)确定坯料尺寸
由无凸缘筒形拉深件坯料尺寸计算公式得
D d24dh1.7d2r0.5r62 32 0430 851.72 30 40.56 42mm 10m 5m
(3)判断是否采用压边圈 零件的相对厚度 t 10021001.9,经查压边圈为可用可不
二、工艺方案的制定
零件的生产包括落料、拉深、切边等工序,为了提高生 产效率,可以考虑工序的复合,本例中采用落料与第一次拉 深复合,经多次拉深成形后,由机械加工方法切边保证零件 高度的生产工艺。
三、工艺计算
1.拉深工艺计算
零件的材料厚度为2mm,所以所有计算以中径为准。
(1)确定零件修边余量
零件的相对高度
D A ( d 1 t ) 0 A ( 5 .6 5 2 5 ) 0 0 .0 m 8 5 . m 6 0 7 0 .0 5 m 8 m
D T ( D A 2 Z ) 0 T ( 5 .6 7 6 ) 5 0 0 .0 m 5 5 . m 6 0 1 0 .0 5 m 5 m
DT (DA Zmin)0T (104.5650.246)00.025mm 104.31900.025mm
2)首次拉深凸、凹模尺寸计算 第一次拉深件后零件直径为55.65mm,由公式ZtmaxKt 确定拉深凸、凹模间隙值,查得 K0.5 ,所以间隙 Z 2 m 0 .m 5 2 m 3 m ,则m
F落KLt
1.33.14105232N 0
2743.41N027.43kN
F压
[D2
4
(d1
t
2rA)2]P
F拉d1tbK1
3.1455.6524000.8N 1118.234N 411.18kN
[1052 (55.65228)2]2.2N
(5)确定各工序件直径 调整各次拉深系数分别为 m1 0.53,m2 0.78,m3 0.82,则 调整后每次拉深所得筒形件的直径为
d 1 m 1 D 0 .5 1 3m 0 5 m .6 5 m 5m
,
d 2 m 2 d 1 0 .7 5 8 .6 5 m 5 4 m .4 3 m 1m
裁成宽109.6mm,长1000mm的条料,则每张板料所出 零件数为
1105.69001100.560013 9117
裁成宽109.6mm,长1500mm的条料,则每张板料所出 零件数为
1100.69001105.5600914126
则最终的排样图见下图。
(3)力的计算 模具为落料拉深复合模,动作顺序是先落料后拉深,现 分别计算落料力、拉深力和压边力。
(3)排样计算
零件采用单直排排样方式,查得零件间的搭边值为
1.5mm,零件与条料侧边之间的搭边值为1.8mm,若模具采
用无侧压装置的导料板结构,则 条料上零件的步距为106.5mm, 条料的宽度应为
B (Dmax 2ac)0 (105 21.81)00.7 mm 109.600.7 mm
选用规格为2mm×1000mm×1500mm的板料,计算裁 料方式如下。
拉深工序件图如图所示。
2.落料拉深复合模工艺计算 (1)落料凸、凹模刃口尺寸计算 根据零件形状特点,刃口尺寸计算采用分开制造法。 落料尺寸为φ 10500.87,经验算满足不等式 T A≤ ZmaxZmin 所以
DA (DmaxXΔ)0A (1050.50.87)00.035mm 104.56500.035mm
无凸缘筒形件拉深模设计与制造实例
材料:10钢 料厚:2mm
一、工艺性分析
1.材料分析 08钢为优质碳素结构钢,属于深拉深级别钢,具有良好 的拉深成形性能。 2. 结构分析 零件为一无凸缘筒形件,结构简单,底部圆角半径为R3, 满足筒形拉深件底部圆角半径大于一倍料厚的要求,因此, 零件具有良好的结构工艺性。 3. 精度分析 零件上尺寸均为未注公差尺寸,普通拉深即可达到零件的 精度要求。
d 2 [ m 2 ] d 1 0 .7 5 5 .5 m 2 3 m .3 9 m 8m
d 3 [ m 3 ] d 2 0 .7 3 8 .3 9 m 8 3 m .7 0 m 2m
d 4 [ m 4 ] d 3 0 .8 3 .7 m 0 2 2 . m 5 m 4 8 3 m m 0m 所以共需4次拉深。
,
d 3 m 3 d 2 0 .8 4 2 .4 3 m 1 3 m .6 5 m 0m
第四次拉深时的实际拉深系数
m4
d d3
335.6000.84,其大于
第三次实际拉深系数 m 3 和第四次极限拉深系数 [m 4 ] ,所以
调整合理。第四次拉深后筒形件的直径为 30mm 。
(6)确定各工序件高度 根据拉深件圆角半径计算公式,取各次拉深筒形件圆角 半径分别为r1 , 8mm r2 , 6.5mm r3 , 5mm r4 4mm,所以每次拉深后 筒形件的高度为
D 105
用的范围,为了保证零件质量,减少拉深次数,决定采用压 边圈。
(4)确定拉深次数 查得零件的各次极限拉深系数分别为[ m1]=0.5, [ m2]=0.75,[ m3]=0.78,[ m4]=0.8。所以,每次拉深后筒形 件的直径分别为
d 1 [m 1 ]D 0 .5 1m 0 5 5 m .5 m 2 m
4.341
4.341
5.55m 7 m
h30.25(D d32 d3)0.43dr33(d30.32 r3)
0.25(102535 .60 )mm 0.43 5 (35 .600.325)mm
35 .60
35 .60
70 .77mm
第四次拉深后筒形件高 度应等于零件要求尺寸, 即 。 h4 85mm