橡胶密封件的失效分析.
橡胶密封件的失效分析(0001)

橡胶密封件的失效分析橡胶密封件的失效分析橡胶密封件常见的失效原因主要有4种:设计错误、选材错误、密封件质量问题和使用不当。
1. 设计错误设计错误通常是由於设计人员对产品认识不足造成的。
比如对密封件承受的压力估计不足、对密封面上接触应力分布的认识有误、安放密封件的沟槽设计不合理等。
有限元分析(FEA)常常被用来辅助密封件的设计和失效分析。
我们曾为某美国客户做过一个密封件,该密封件以塑料为主体,局部包上橡胶。
客户在检测零件的过程中发现,塑料部分在测试时容易破裂,从而得出结论是:塑料件在二次成型时(即将橡胶包覆在塑料件上)被损坏了。
经我们分析後发现,塑料件都是在一个地方破裂的。
通过有限元分析,我们发现,塑料件的破损部位实际上是密封件受到最大应力的地方,此处应力已经远远超过塑料所能承受的。
如果在设计的时候客户就用有限元方法分析过该产品,不但可以避免类似的错误,还可以节省其时间和金钱。
当然,想要成功的分析预测橡胶密封件的性能,不但要有合适的有限元分析软件,还要有丰富的材料经验、建模经验和长期的数据积累。
2. 选材错误常用的橡胶密封材料有三元乙丙橡胶(EPDM)、丁腈橡胶(NBR)、硅橡胶(VMQ)、氟橡胶(FKM或者FPM)和氯丁橡胶(CR)等。
这些橡胶的特性各不相同,应用也不同。
选择材料要从多方面考虑,比如使用温度、材料是否耐受介质、材料的硬度、压缩永久变形和耐磨性等各种因素。
选材错误常常是因为设计人员对各种材料的性能不熟悉。
一个经验丰富的橡胶密封件供应商能一开始就指出选材的问题。
我们有个国内客户不喜欢正在使用的O圈,因为这个O圈很容易坏。
我们检查了更换下来的样品,发现样品表面有龟裂,纹路很像臭氧老化。
我们又询问了O 圈的使用环境,发现周围有很多机械设备和电动马达。
这下答案就有了:电动马达的火花能产生臭氧,造成了局部小环境臭氧浓度较高;而客户所选材料为丁腈橡胶,不耐受臭氧。
为了验证结论,我们在实验室臭氧老化箱中做了测试,结果客户提供的新O圈表面也出现了类似的裂纹。
橡胶密封件的失效分析与橡胶断口形态
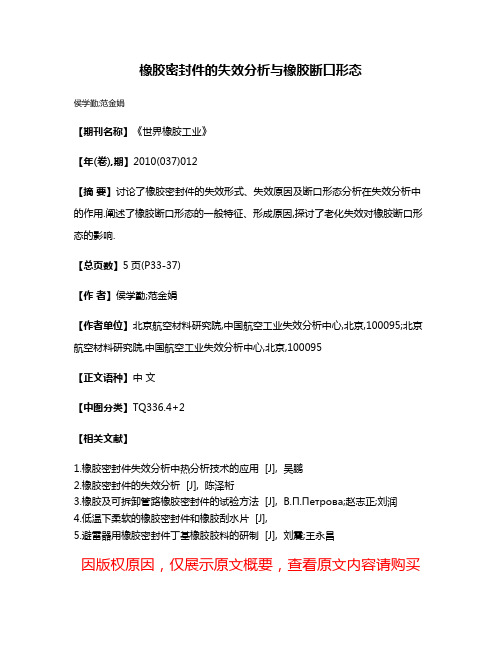
橡胶密封件的失效分析与橡胶断口形态
侯学勤;范金娟
【期刊名称】《世界橡胶工业》
【年(卷),期】2010(037)012
【摘要】讨论了橡胶密封件的失效形式、失效原因及断口形态分析在失效分析中的作用.阐述了橡胶断口形态的一般特征、形成原因,探讨了老化失效对橡胶断口形态的影响.
【总页数】5页(P33-37)
【作者】侯学勤;范金娟
【作者单位】北京航空材料研究院,中国航空工业失效分析中心,北京,100095;北京航空材料研究院,中国航空工业失效分析中心,北京,100095
【正文语种】中文
【中图分类】TQ336.4+2
【相关文献】
1.橡胶密封件失效分析中热分析技术的应用 [J], 吴鹏
2.橡胶密封件的失效分析 [J], 陈泽桁
3.橡胶及可拆卸管路橡胶密封件的试验方法[J], В.П.Петрова;赵志正;刘润
4.低温下柔软的橡胶密封件和橡胶刮水片 [J],
5.避雷器用橡胶密封件丁基橡胶胶料的研制 [J], 刘震;王永昌
因版权原因,仅展示原文概要,查看原文内容请购买。
橡胶密封圈失效及裂纹形成原因分析
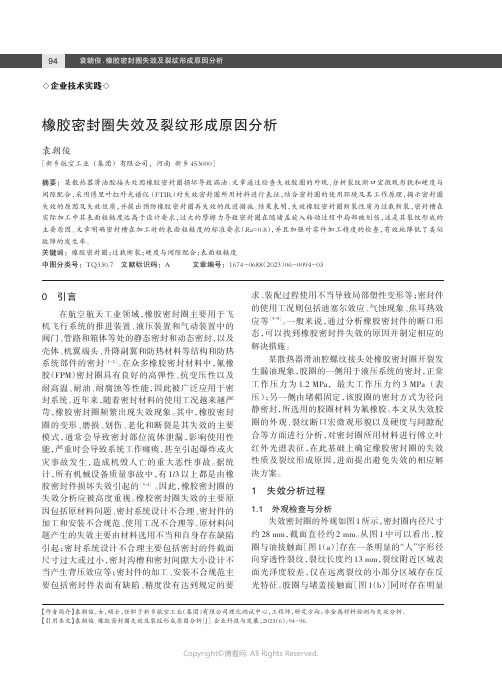
0引言在航空航天工业领域,橡胶密封圈主要用于飞机飞行系统的推进装置、液压装置和气动装置中的阀门、管路和箱体等处的静态密封和动态密封,以及壳体、机翼端头、升降副翼和防热材料等结构和防热系统部件的密封[1-2]。
在众多橡胶密封材料中,氟橡胶(FPM )密封圈具有良好的高弹性、抗变压性以及耐高温、耐油、耐腐蚀等性能,因此被广泛应用于密封系统。
近年来,随着密封材料的使用工况越来越严苛,橡胶密封圈频繁出现失效现象。
其中,橡胶密封圈的变形、磨损、划伤、老化和断裂是其失效的主要模式,通常会导致密封部位流体泄漏,影响使用性能,严重时会导致系统工作瘫痪,甚至引起爆炸或火灾事故发生,造成机毁人亡的重大恶性事故。
据统计,所有机械设备质量事故中,有1/3以上都是由橡胶密封件损坏失效引起的[3-4]。
因此,橡胶密封圈的失效分析应被高度重视。
橡胶密封圈失效的主要原因包括原材料问题、密封系统设计不合理、密封件的加工和安装不合规范、使用工况不合理等。
原材料问题产生的失效主要由材料选用不当和自身存在缺陷引起;密封系统设计不合理主要包括密封的件截面尺寸过大或过小,密封沟槽和密封间隙大小设计不当产生背压效应等;密封件的加工、安装不合规范主要包括密封件表面有缺陷、精度没有达到规定的要求、装配过程使用不当导致局部塑性变形等;密封件的使用工况则包括迪塞尔效应、气蚀现象、焦耳热效应等[5-9]。
一般来说,通过分析橡胶密封件的断口形态,可以找到橡胶密封件失效的原因并制定相应的解决措施。
某散热器滑油腔螺纹接头处橡胶密封圈开裂发生漏油现象,胶圈的一侧用于液压系统的密封,正常工作压力为1.2MPa ,最大工作压力约3MPa (表压);另一侧由堵帽固定,该胶圈的密封方式为径向静密封,所选用的胶圈材料为氟橡胶。
本文从失效胶圈的外观、裂纹断口宏微观形貌以及硬度与间隙配合等方面进行分析,对密封圈所用材料进行傅立叶红外光谱表征,在此基础上确定橡胶密封圈的失效性质及裂纹形成原因,进而提出避免失效的相应解决方案。
丁腈橡胶o形密封圈失效原因分析
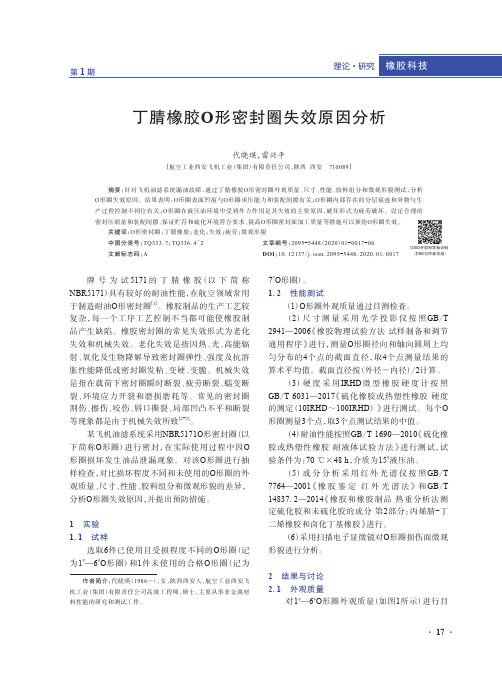
丁腈橡胶O形密封圈失效原因分析代晓瑛,雷兴平[航空工业西安飞机工业(集团)有限责任公司,陕西西安710089]摘要:针对飞机油滤系统漏油故障,通过丁腈橡胶O形密封圈外观质量、尺寸、性能、胶料组分和微观形貌测试,分析O形圈失效原因。
结果表明:O形圈表面凹痕与O形圈承压能力和装配间隙有关;O形圈内部存在的分层痕迹和异物与生产过程控制不到位有关;O形圈在液压油环境中受到外力作用是其失效的主要原因,破坏形式为疲劳破坏。
设定合理的密封压缩量和装配间隙、保证贮存和硫化环境符合要求、提高O形圈密封面加工质量等措施可以预防O形圈失效。
关键词:O形密封圈;丁腈橡胶;老化;失效;疲劳;微观形貌中图分类号:TQ333.7;TQ336.4+2 文章编号:2095-5448(2020)01-0017-06文献标志码:A DOI:10.12137/j.issn.2095-5448.2020.01.0017牌号为试5171的丁腈橡胶(以下简称NBR5171)具有较好的耐油性能,在航空领域常用于制造耐油O形密封圈[1]。
橡胶制品的生产工艺较复杂,每一个工序工艺控制不当都可能使橡胶制品产生缺陷。
橡胶密封圈的常见失效形式为老化失效和机械失效。
老化失效是指因热、光、高能辐射、氧化及生物降解导致密封圈弹性、强度及抗溶胀性能降低或密封圈发粘、变硬、变脆。
机械失效是指在载荷下密封圈瞬时断裂、疲劳断裂、蠕变断裂、环境应力开裂和磨损磨耗等。
常见的密封圈割伤、擦伤、咬伤、唇口撕裂、局部凹凸不平和断裂等现象都是由于机械失效所致[2-3]。
某飞机油滤系统采用NBR5171O形密封圈(以下简称O形圈)进行密封,在实际使用过程中因O 形圈损坏发生油品泄漏现象。
对该O形圈进行抽样检查,对比损坏程度不同和未使用的O形圈的外观质量、尺寸、性能、胶料组分和微观形貌的差异,分析O形圈失效原因,并提出预防措施。
1 实验1.1 试样选取6件已使用且受损程度不同的O形圈(记为1#—6#O形圈)和1件未使用的合格O形圈(记为7#O形圈)。
密封失效的原因

密封失效的原因1、密封失效主要有下述三种原因:(1)、密封面打开在修理机械密封时,85%的密封失效不是因磨损造成,而是在磨损前就已泄漏了。
当密封面一打开,介质中的固体微粒在液体压力的作用下进入密封面,密封面闭合后,这些固体微粒就嵌入软环(通常是右墨环)的面上,这实际成了一个“砂轮”会损坏硬环表面。
由于动环或橡胶圈紧固在轴(轴套)上,当轴串动时,动环不能及时贴合,而使密封面打开,并且密封面的滞后闭合,就使固体微粒进入密封面中。
同时轴(轴套)和滑动部件之间也存在有固体微粒,影响橡胶圈或动环的滑动(相对动密封点,常见故障)。
另外,介质也会在橡胶圈与轴(轴套)磨擦部位产生结晶物,在弹簧处也会存有固体物质,都会使密封面打开。
(2)、过热因密封面上会产生热,故橡胶圈使用温度应低于设计规范。
氟橡胶和聚四氟乙烯的使用温度为216℃,丁晴橡胶的使用温度为162℃,虽然它们都能承受较高的温度,但因密封面产生的热较高,所以橡胶圈有继续硫化的危险,最终失去弹性而泄漏。
(冷区考虑冷脆)密封面之间还会因热引起介质的结晶,如结碳,造成滑动部件被粘住和密封面被凝结。
而且有些聚合物因过热而焦化,有些流体因过热而失去润滑等甚至闪火。
过热除能改变介质的状况外,还会加剧它的腐蚀速率。
引起金属零件的变形,合金面的开裂,以及某些镀层裂缝,设计应选用平衡型机械密封,以降低比压防止过热。
(3)、超差正确的装配公差,对于安装机械密封是很必要的,轴(轴套)必须有合适的表面粗糙度和正确的尺寸,但制造者很少提供公差数据,这些数据对安装来讲都是很关键的。
(依靠经验和常识)机械密封的尺寸精度及形位公差必须符合图纸要求,超差将会导致密封提前失效。
机封工作应注意问题:1.安装时注意事项a.要十分注意避免安装中所产生的安装偏差(1)上紧压盖应在联轴器找正后进行,螺栓应均匀上支,防止压盖端面偏斜,用塞尺检查各点,其误差不大于0.05毫米。
(2)检查压盖与轴或轴套外径的配合间隙(即同心度),四周要均匀,用塞尺检查各点允差不大于0.01毫米。
橡胶密封件的失效分析
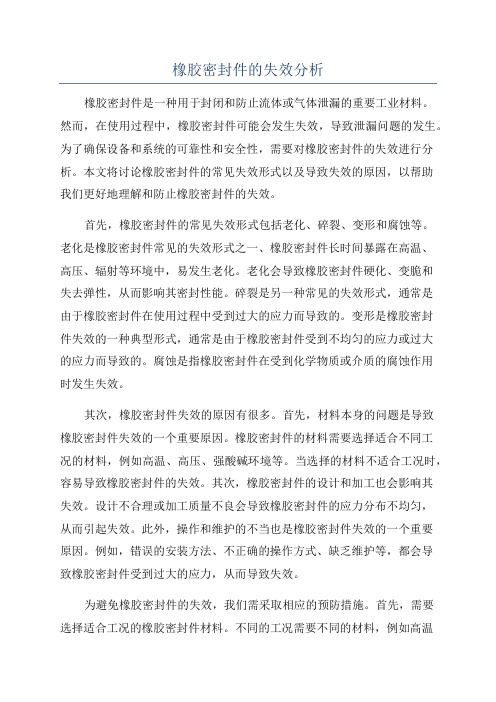
橡胶密封件的失效分析橡胶密封件是一种用于封闭和防止流体或气体泄漏的重要工业材料。
然而,在使用过程中,橡胶密封件可能会发生失效,导致泄漏问题的发生。
为了确保设备和系统的可靠性和安全性,需要对橡胶密封件的失效进行分析。
本文将讨论橡胶密封件的常见失效形式以及导致失效的原因,以帮助我们更好地理解和防止橡胶密封件的失效。
首先,橡胶密封件的常见失效形式包括老化、碎裂、变形和腐蚀等。
老化是橡胶密封件常见的失效形式之一、橡胶密封件长时间暴露在高温、高压、辐射等环境中,易发生老化。
老化会导致橡胶密封件硬化、变脆和失去弹性,从而影响其密封性能。
碎裂是另一种常见的失效形式,通常是由于橡胶密封件在使用过程中受到过大的应力而导致的。
变形是橡胶密封件失效的一种典型形式,通常是由于橡胶密封件受到不均匀的应力或过大的应力而导致的。
腐蚀是指橡胶密封件在受到化学物质或介质的腐蚀作用时发生失效。
其次,橡胶密封件失效的原因有很多。
首先,材料本身的问题是导致橡胶密封件失效的一个重要原因。
橡胶密封件的材料需要选择适合不同工况的材料,例如高温、高压、强酸碱环境等。
当选择的材料不适合工况时,容易导致橡胶密封件的失效。
其次,橡胶密封件的设计和加工也会影响其失效。
设计不合理或加工质量不良会导致橡胶密封件的应力分布不均匀,从而引起失效。
此外,操作和维护的不当也是橡胶密封件失效的一个重要原因。
例如,错误的安装方法、不正确的操作方式、缺乏维护等,都会导致橡胶密封件受到过大的应力,从而导致失效。
为避免橡胶密封件的失效,我们需采取相应的预防措施。
首先,需要选择适合工况的橡胶密封件材料。
不同的工况需要不同的材料,例如高温环境需要耐高温橡胶密封件,化学介质环境需要耐腐蚀的橡胶密封件。
其次,需要合理设计和精确加工橡胶密封件。
在设计过程中,需要考虑应力分布的均匀性,避免应力集中;在加工过程中,需要采用适当的工艺和设备,确保加工质量。
此外,正确的操作和维护也是防止橡胶密封件失效的关键。
橡胶密封件的失效分析

橡胶密封件的失效分析橡胶密封件常见的失效原因主要有4种:设计错误、选材错误、密封件质量问题和使用不当。
1. 设计错误设计错误通常是由於设计人员对产品认识不足造成的。
比如对密封件承受的压力估计不足、对密封面上接触应力分布的认识有误、安放密封件的沟槽设计不合理等。
有限元分析(FEA)常常被用来辅助密封件的设计和失效分析。
我们曾为某美国客户做过一个密封件,该密封件以塑料为主体,局部包上橡胶。
客户在检测零件的过程中发现,塑料部分在测试时容易破裂,从而得出结论是:塑料件在二次成型时(即将橡胶包覆在塑料件上)被损坏了。
经我们分析後发现,塑料件都是在一个地方破裂的。
通过有限元分析,我们发现,塑料件的破损部位实际上是密封件受到最大应力的地方,此处应力已经远远超过塑料所能承受的。
如果在设计的时候客户就用有限元方法分析过该产品,不但可以避免类似的错误,还可以节省其时间和金钱。
当然,想要成功的分析预测橡胶密封件的性能,不但要有合适的有限元分析软件,还要有丰富的材料经验、建模经验和长期的数据积累。
2. 选材错误常用的橡胶密封材料有三元乙丙橡胶(EPDM)、丁腈橡胶(NBR)、硅橡胶(VMQ)、氟橡胶(FKM或者FPM)和氯丁橡胶(CR)等。
这些橡胶的特性各不相同,应用也不同。
选择材料要从多方面考虑,比如使用温度、材料是否耐受介质、材料的硬度、压缩永久变形和耐磨性等各种因素。
选材错误常常是因为设计人员对各种材料的性能不熟悉。
一个经验丰富的橡胶密封件供应商能一开始就指出选材的问题。
我们有个国内客户不喜欢正在使用的O圈,因为这个O圈很容易坏。
我们检查了更换下来的样品,发现样品表面有龟裂,纹路很像臭氧老化。
我们又询问了O圈的使用环境,发现周围有很多机械设备和电动马达。
这下答案就有了:电动马达的火花能产生臭氧,造成了局部小环境臭氧浓度较高;而客户所选材料为丁腈橡胶,不耐受臭氧。
为了验证结论,我们在实验室臭氧老化箱中做了测试,结果客户提供的新O圈表面也出现了类似的裂纹。
超详细的橡胶密封件老化原因!
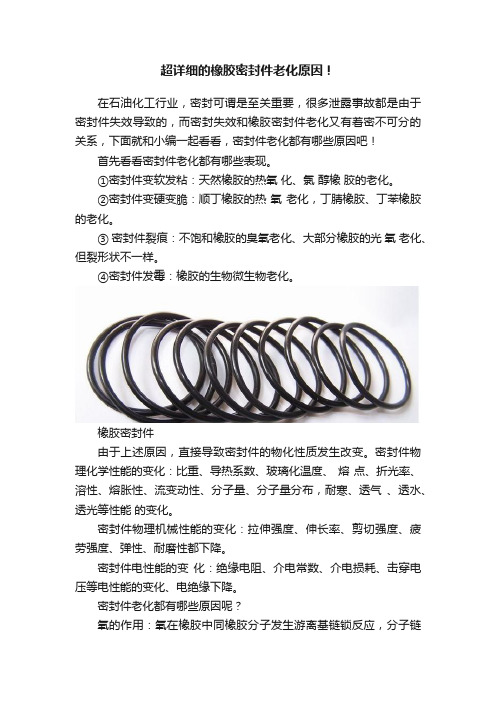
超详细的橡胶密封件老化原因!在石油化工行业,密封可谓是至关重要,很多泄露事故都是由于密封件失效导致的,而密封失效和橡胶密封件老化又有着密不可分的关系,下面就和小编一起看看,密封件老化都有哪些原因吧!首先看看密封件老化都有哪些表现。
①密封件变软发粘:天然橡胶的热氧化、氯醇橡胶的老化。
②密封件变硬变脆:顺丁橡胶的热氧老化,丁腈橡胶、丁苯橡胶的老化。
③ 密封件裂痕:不饱和橡胶的臭氧老化、大部分橡胶的光氧老化、但裂形状不一样。
④密封件发霉:橡胶的生物微生物老化。
橡胶密封件由于上述原因,直接导致密封件的物化性质发生改变。
密封件物理化学性能的变化:比重、导热系数、玻璃化温度、熔点、折光率、溶性、熔胀性、流变动性、分子量、分子量分布,耐寒、透气、透水、透光等性能的变化。
密封件物理机械性能的变化:拉伸强度、伸长率、剪切强度、疲劳强度、弹性、耐磨性都下降。
密封件电性能的变化:绝缘电阻、介电常数、介电损耗、击穿电压等电性能的变化、电绝缘下降。
密封件老化都有哪些原因呢?氧的作用:氧在橡胶中同橡胶分子发生游离基链锁反应,分子链发生断裂或过度交联,引起硅橡胶制品性能的改变。
氧化作用是橡胶老化的重要原因之一。
热的作用:提高温度可引起硅橡胶制品的热裂解或热交联。
但热的基本作用还是活化作用。
提高氧扩散速度和活化氧化反应,从而加速橡胶氧化反应速度,这是普遍存在的一种老化现象——热氧老化。
水分的作用:水分的作用有两个方面:硅橡胶制品在潮湿空气淋雨或浸泡在水中时,容易破坏,这是由于橡胶中的水溶性物质和清水荃团等成分被水抽提溶解。
特别是在水浸泡和大气曝光交替作用下,会加速橡胶密封件的破坏。
但也存在一些情况下,水分对橡胶不起破坏作用,甚至会延缓老化。
臭氧的作用:臭氧的化学活性氧高得多,破坏性更大,它同样是使分子链发生断裂,但臭氧对橡胶的作用情况随橡胶变形与否而不同。
当作用于变形的橡胶(不饱和橡胶)时,会出现向着应力方向的裂纹,即所谓的“应力龟裂”,当作用于非变形的橡胶时,仅表面生成氧化膜而不龟裂。
- 1、下载文档前请自行甄别文档内容的完整性,平台不提供额外的编辑、内容补充、找答案等附加服务。
- 2、"仅部分预览"的文档,不可在线预览部分如存在完整性等问题,可反馈申请退款(可完整预览的文档不适用该条件!)。
- 3、如文档侵犯您的权益,请联系客服反馈,我们会尽快为您处理(人工客服工作时间:9:00-18:30)。
橡胶密封件的失效分析橡胶密封件常见的失效原因主要有4种:设计错误、选材错误、密封件质量问题和使用不当。
1. 设计错误设计错误通常是由於设计人员对产品认识不足造成的。
比如对密封件承受的压力估计不足、对密封面上接触应力分布的认识有误、安放密封件的沟槽设计不合理等。
有限元分析(FEA)常常被用来辅助密封件的设计和失效分析。
我们曾为某美国客户做过一个密封件,该密封件以塑料为主体,局部包上橡胶。
客户在检测零件的过程中发现,塑料部分在测试时容易破裂,从而得出结论是:塑料件在二次成型时(即将橡胶包覆在塑料件上)被损坏了。
经我们分析後发现,塑料件都是在一个地方破裂的。
通过有限元分析,我们发现,塑料件的破损部位实际上是密封件受到最大应力的地方,此处应力已经远远超过塑料所能承受的。
如果在设计的时候客户就用有限元方法分析过该产品,不但可以避免类似的错误,还可以节省其时间和金钱。
当然,想要成功的分析预测橡胶密封件的性能,不但要有合适的有限元分析软件,还要有丰富的材料经验、建模经验和长期的数据积累。
2. 选材错误常用的橡胶密封材料有三元乙丙橡胶(EPDM)、丁腈橡胶(NBR)、硅橡胶(VMQ)、氟橡胶(FKM或者FPM)和氯丁橡胶(CR)等。
这些橡胶的特性各不相同,应用也不同。
选择材料要从多方面考虑,比如使用温度、材料是否耐受介质、材料的硬度、压缩永久变形和耐磨性等各种因素。
选材错误常常是因为设计人员对各种材料的性能不熟悉。
一个经验丰富的橡胶密封件供应商能一开始就指出选材的问题。
我们有个国内客户不喜欢正在使用的O圈,因为这个O圈很容易坏。
我们检查了更换下来的样品,发现样品表面有龟裂,纹路很像臭氧老化。
我们又询问了O圈的使用环境,发现周围有很多机械设备和电动马达。
这下答案就有了:电动马达的火花能产生臭氧,造成了局部小环境臭氧浓度较高;而客户所选材料为丁腈橡胶,不耐受臭氧。
为了验证结论,我们在实验室臭氧老化箱中做了测试,结果客户提供的新O圈表面也出现了类似的裂纹。
由於该密封件只与空气长期接触,没有矿物油等其他物质,我们最终推荐了三元乙丙橡胶来代替客户的现有产品。
有时使用环境比较复杂,或者是一个全新的设计,选择材料就不是件非常容易的事了。
除了仔细甄别各种影响因素外,还需要进行功能测试。
3. 密封件质量密封件的生产质量与最终产品的可靠性密切相关。
常见的问题有:原材料质量不稳定、橡胶混炼时投错原料、原料或者混炼胶储存不当(交叉污染)、胶料混炼不均匀、硫化条件(温度、时间、压力等)不妥、密封件产品保存不当、模具使用不当等。
这些问题往往涉及到生产过程中的质量控制。
定货方在选择密封件生产厂时,应该经过多次考察、调研并进行产品测试。
在供货的过程中,还可要求密封件的生产企业提供真实、准确的检验报告。
4. 密封件使用不当一个好密封件,如果使用不当,也会造成整个产品失效,比如润滑油使用错误。
我们的某个客户反馈说O圈零件的尺寸与要求差异很大。
当我们分析样品时才发现,客户用错了润滑油。
该O圈是由三元乙丙橡胶制成,材料本身不耐矿物油类的润滑油。
客户涂上这种润滑油,会造成产品体积溶胀。
後来让客户改用硅油就没有问题了。
另外一类常见的问题为安装错误。
比如在O圈装配过程中产生了扭曲;由於安装不当而造成密封件受压不均匀;密封件的润滑不够等失误。
如果这些失误是由密封件的生产厂家造成的,那么这属於生产质量所控制的范围之内。
如果由定货方或者第三方造成,那么就属於使用不当了。
当今科技日新月异,巿场上出现了很多新的密封件材料和工程设计,以满足各种苛刻的使用要求。
同时,大多数密封件的制造商也采用了科学的质量管理体系。
遗憾的是,这些努力都不能杜绝密封件失效。
因而,失效分析就显得更为重要了。
橡胶密封件失效分析橡胶密封件失效分析不但要求技术人员具有全面的材料知识,还必须具有丰富的工程经验,并且要善於使用一些分析仪器和设备,因此复杂的失效分析往往需要一个团队来完成。
当客户的产品发生密封故障时,他们首先想到的原因往往是橡胶密封件,他们最常提出的问题是:供应商是否换过材料?其实,从上文中可以看出,材料更换只是可能的影响因素之一。
所以,当碰到密封故障时,应该从以下四个方面出发,全面掌握资料,根据数据而不是凭猜想作结论。
1. 选择合适的机构来进行密封件失效分析现实中,客户常常首选该橡胶密封件的供应商来做失效分析,或者找装备精良的大学实验室(或专业测试公司)来做。
但是,橡胶密封件失效分析不但要求技术人员具有全面的材料知识,还必须具有丰富的工程设计经验,并且要善於使用一些专业的分析仪器和设备。
而只有资深的橡塑元件生产商才有这样的技术力量。
另外,分析中可能会涉及到一些客户的技术机密,因此,最好找一个有信誉的公司来进行分析。
2. 搜集背景资料遇到密封故障时,首先应该搜集如下背景资料,用来初步判断失效是否和材料有关:密封件的生产厂家是谁;胶料名称是什么(客户有可能会搞错供应商)。
失效产品中所用的密封件批号或者订单号,这样可以方便以後查询。
如果密封件失效仅与某批次相关,那么很有可能是由密封件生产中的某些变化造成的。
密封件失效是怎么被发现的?密封件使用的条件是什么(温度、压力、介质、使用频率等)?如果结构特殊,可能还需要图纸或者组合件的照片。
失效产品占多少比例(%)。
如有可能,请客户送回部分样品:失效的密封件、没有失效的密封件、以及同批号中没有使用过的密封件。
这样便於以後做比较测试。
值得注意的是,有些样品可能残留有毒物质,一定要提醒客户和相关人员做好防护措施,并且妥善送交样品。
得到这些信息後,分析员最好能够建立相应的档案。
一来便於今後追踪跟进调查情况;二来可以为将来的类似案例提供线索。
3. 初步分析如果是由密封件供应商进行失效分析,在得到样品後,最好还是先做一些简单的材料分析(比如硬度、拉伸强度、永久压缩变形、比重等物性测试和尺寸检查),以再次确认该产品的确是自己的产品。
因为很多橡胶件看起来都一样(比如O 圈)。
我们就有这样的经历,客户一再强调是我们的产品XYZ。
但是经过材料分析後,样品的成分和性能与我们的XYZ产品大相径庭。
同时,也可以用这些测试结果来判断材料是否有问题。
有时候还可以在失效密封件上找到一些特征。
有经验的技术人员凭这些特征就可以初步断定失效原因。
另外,在失效特征的附近,还要注意观察是否有异物、气泡、流痕或者毛边等异常情况。
这些特征常常和密封件生产质量有关。
可通过肉眼、放大镜、显微镜和电子扫描显微镜(SEM)等进行观察。
根据以上这些线索,可以初步辨别造成失效的大致原因,如果需要,可进一步安排其他分析测试。
4. 深度分析如果初步分析无法解决材料方面的疑问,那么就需要采用一些更精密的化学分析方法。
常见的有示差扫描量热仪(DSC),热重分析仪(TGA),动态力学分析仪(DMA)和热机械分析仪(TMA)等热分析技术和傅里叶变换红外光谱仪(FTIR)等光谱方法。
这些分析仪器大都很贵,但是一般在几天内就可获得分析结果。
示差扫描量热仪(DSC)常用来测试橡胶材料的玻璃化温度,在失效分析中可以用来检查橡胶材料的耐低温性能。
热重分析仪(TGA)常用来研究材料的组分,借此可以快速间接地看出某些成分是否有问题。
动态力学分析仪(DMA)常用来测试在一定条件下材料的刚度与阻尼,借此可以判断在实际使用环境中该密封件是否合适(比如抗冲击性能)。
傅里叶变换红外光谱(FTIR)常用来测定分子组成和结构,在失效分析中可以用来确定橡胶本身和某些成分是什么、密封件上的异物成分、在使用中密封件发生了什么化学变化等信息。
这些技术曾仅用於大学和科研院所的基础科学研究。
而今,在橡胶工业中,尤其是欧美一些高端技术企业中,这些技术成功地用在密封件失效分析上。
对於这些技术,很多文献都有更详细的论述和使用实例,在此不再赘述。
除了凭借经验和上述的各种测试外,有限元分析(FEA)也常常被用来辅助密封件的失效分析。
上文在“机械设计错误”中所举的就是一个很好的例子。
5. 实地考察失效分析的一个重要部分是实地考察密封件生产过程或者使用方的安装、使用过程。
因为有时仅凭实验室的分析还不能够得出最终结论。
比如经实验室分析,密封件物料可能有污染。
为了确认这种猜测,分析人员最好实地到生产厂家考察,看看有什么操作漏洞,并在各个可能的生产环节取样。
如果实地样品验证了分析结果,那么就可以确诊了。
其结果可帮助生产厂家改善生产流程,以避免将来发生类似的问题。
再如,我们曾有一个产品在使用中没有达到预期的寿命就失效了。
经过实验室分析和对密封件生产厂的考察,我们仍然无法找出原因。
最後,我们的技术人员去参观了客户的安装流水线後发现,装配过程中所使用的一个元件上有毛刺,装配中橡胶件表面被划伤,从而造成橡胶密封件在使用中过早失效。
在客户更换了这种元件後,橡胶密封件就完全达到使用要求了。
综上所述,橡胶密封件的失效分析常常是一个复杂的工作。
技术人员不仅需要有丰富的经验和知识,还要有认真仔细的态度、坚韧不拔的毅力和一定的逻辑推理能力。
同时,失效分析对分析仪器和设备等硬件也有一定的要求。
耐油橡胶的定义及分类点击次数:20 发布时间:2011-11-181.耐燃油性:氟橡胶FKM 和氟硅橡胶FMVQ对燃料油的抗耐性最好。
而氯丁橡胶和氯化聚乙烯橡胶CPE耐燃油性最差。
丁晴橡胶的耐燃油性随丙烯晴含量增加而提高。
氯醇橡胶的耐燃油性比丁晴橡胶好。
2.耐混合燃油性:氟硅橡胶FMVQ和氟橡胶FKM 对混合燃料油的抗耐性最好。
丙烯酸酯橡胶耐耐混合燃油性最差。
丁晴橡胶的耐混合燃油性随丙烯晴含量增加而提高。
含氟量高的氟橡胶对混合燃油的稳定性较好胶种汽油/甲醇85/15 平均溶涨度(54度)/%汽油/乙醇85/15平均溶涨度(54度)/%3.耐酸性氧化燃油性:对酸性氧化燃油来说,酸性氧化燃油中的氢过氧化物可使硫化胶的性能恶化,所以在燃油系统中常用的丁晴橡胶,氯醇橡胶难以满足长期使用的要求。
只有含氟弹性体如氟橡胶FKM ,氟硅橡胶FMVQ,氟化磷晴和氢化丁晴橡胶性能较好。
普通的丁晴橡胶胶料,不能在125度的酸性汽油中长时间工作。
只有采用氧化镉活化的低硫-给硫体以及白碳黑为主要原料的丁晴橡胶,才能较好的耐酸性汽油。
增加丙烯晴的含量,可使酸性汽油的渗透性降低。
4.耐矿物油性:丁晴橡胶是常用的耐矿物油橡胶。
丁晴橡胶的耐矿物油性随丙烯晴含量增加而提高。
但高丙烯晴含量的丁晴橡胶耐热性有限。
当油温达到150度时,应该采用氢化丁晴橡胶,氟橡胶FKM ,氟硅橡胶FMVQ和丙烯酸酯橡胶。
油温达到150度时,氟橡胶FKM ,氟硅橡胶FMVQ效果最好。
但成本高,为降低成本,可以在氟橡胶FKM 中并入50%以下的丙烯酸酯橡胶,并用后的硫化胶性能下降不大于20%。
丙烯酸酯橡胶耐矿物油性好于丁晴橡胶.丙烯酸乙酯型的橡胶丙烯酸酯橡胶的耐热油性,比丙烯酸丁酯型的橡胶好。