微电机制造工艺
小型发电机的制作方法

小型发电机的制作方法
小型发电机是一种可以用来发电的装置,通常由发电机组、电机、电源、控制系统等部分组成。
如何制作小型发电机呢?以下是一些基本制作方法:
1. 确定所需功率和电压:首先需要根据实际需求确定小型发电机的功率和电压。
这将决定所需材料、设计和制造成本。
2. 选择适当的发电机组件:小型发电机通常由转子、定子、磁场系统和电刷组成。
可以选择自己制作或者购买现成的发电机组件。
3. 制作转子:转子通常由强烈磁性的材料制成,例如钕铁硼或铁氧体。
可以使用车床或者铣床等机器进行制作。
4. 制作定子:定子通常由铜线或者铜箔绕制而成,可以按照设计图纸进行制作。
5. 制作磁场系统:磁场系统通常由永磁体或者电磁铁构成。
可以将永磁体或者电磁铁安装在转子和定子之间的位置上。
6. 安装电刷组件:电刷组件通常用于从转子中提取电能。
可以根据转子形状和材料选择适当的电刷。
7. 完成电路连接:最后将电机、电源和控制系统连接起来,进行测试和调试。
需要注意的是,制作小型发电机需要一定的专业知识和技能,建议在制作之前仔细学习相关知识和安全规范。
- 1 -。
小型电机生产流程
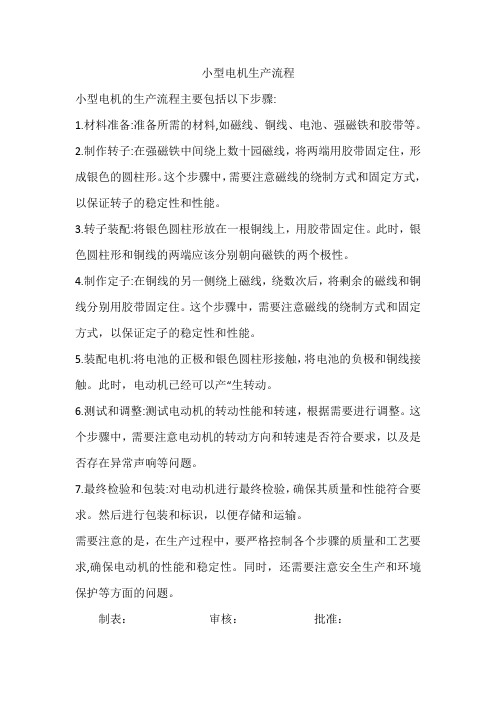
小型电机生产流程
小型电机的生产流程主要包括以下步骤:
1.材料准备:准备所需的材料,如磁线、铜线、电池、强磁铁和胶带等。
2.制作转子:在强磁铁中间绕上数十园磁线,将两端用胶带固定住,形成银色的圆柱形。
这个步骤中,需要注意磁线的绕制方式和固定方式,以保证转子的稳定性和性能。
3.转子装配:将银色圆柱形放在一根铜线上,用胶带固定住。
此时,银色圆柱形和铜线的两端应该分别朝向磁铁的两个极性。
4.制作定子:在铜线的另一侧绕上磁线,绕数次后,将剩余的磁线和铜线分别用胶带固定住。
这个步骤中,需要注意磁线的绕制方式和固定方式,以保证定子的稳定性和性能。
5.装配电机:将电池的正极和银色圆柱形接触,将电池的负极和铜线接触。
此时,电动机已经可以产“生转动。
6.测试和调整:测试电动机的转动性能和转速,根据需要进行调整。
这个步骤中,需要注意电动机的转动方向和转速是否符合要求,以及是否存在异常声响等问题。
7.最终检验和包装:对电动机进行最终检验,确保其质量和性能符合要求。
然后进行包装和标识,以便存储和运输。
需要注意的是,在生产过程中,要严格控制各个步骤的质量和工艺要求,确保电动机的性能和稳定性。
同时,还需要注意安全生产和环境保护等方面的问题。
制表:审核:批准:。
电机生产工艺标准规范
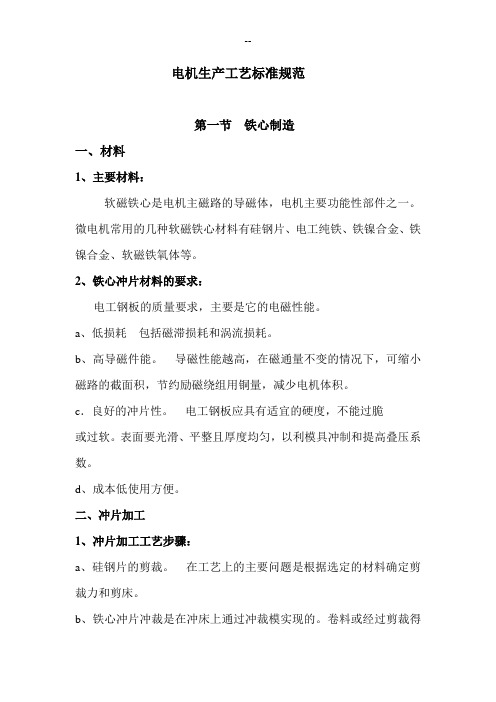
电机生产工艺标准规范第一节铁心制造一、材料1、主要材料:软磁铁心是电机主磁路的导磁体,电机主要功能性部件之一。
微电机常用的几种软磁铁心材料有硅钢片、电工纯铁、铁镍合金、铁镍合金、软磁铁氧体等。
2、铁心冲片材料的要求:电工钢板的质量要求,主要是它的电磁性能。
a、低损耗包括磁滞损耗和涡流损耗。
b、高导磁件能。
导磁性能越高,在磁通量不变的情况下,可缩小磁路的截面积,节约励磁绕组用铜量,减少电机体积。
c.良好的冲片性。
电工钢板应具有适宜的硬度,不能过脆或过软。
表面要光滑、平整且厚度均匀,以利模具冲制和提高叠压系数。
d、成本低使用方便。
二、冲片加工1、冲片加工工艺步骤:a、硅钢片的剪裁。
在工艺上的主要问题是根据选定的材料确定剪裁力和剪床。
b、铁心冲片冲裁是在冲床上通过冲裁模实现的。
卷料或经过剪裁得到的钢片条料,在冲床上经过冲模的冲裁即得到所需的冲片。
根据所用冲裁模的不同,相应有单式冲裁、复式冲裁、多工序组合冲裁、级进式冲裁等。
c、毛刺及其消除。
冲模间隙过大,冲模安装不当或冲模刃口磨钝等,都会使冲片产生毛刺。
减小毛刺的基本措施是:在冲模制造时,严格控制凸凹模的间隙,而且要保证冲裁时有均匀的间隙;冲裁过程中,要保持冲模工作正常,经常检查毛刺的大小。
d、冲片的退火处理。
软磁材料在出厂时,有的已具有标准规定的磁性能。
有的材料则需待加工后进行最后的退火处理才具有规定的磁性。
e、冲片加工的自动化:对大批量生产的微电机,冲片及铁心加工的自动化是提高生产效率、保证产品质量、降低产品成本的重要途径。
采用高速自动冲床和多工位级进式冲模、使用卷料钢片连续冲裁,这是比较先进冲裁方式。
2、铁心冲片的质量检查:冲片质量主要反映在四个方面:(1)冲片尺寸、形状的准确度。
(2)毛刺的大小。
(3)冲片绝缘层的质量。
(4)冲片的铁耗和导磁性能。
由于冲片绝缘不是经常检查以及一般只检查冲片叠压后的铁心损耗,故冲片加工质量的检查,主要是冲片的尺寸精度与毛刺。
伺服电机生产工艺
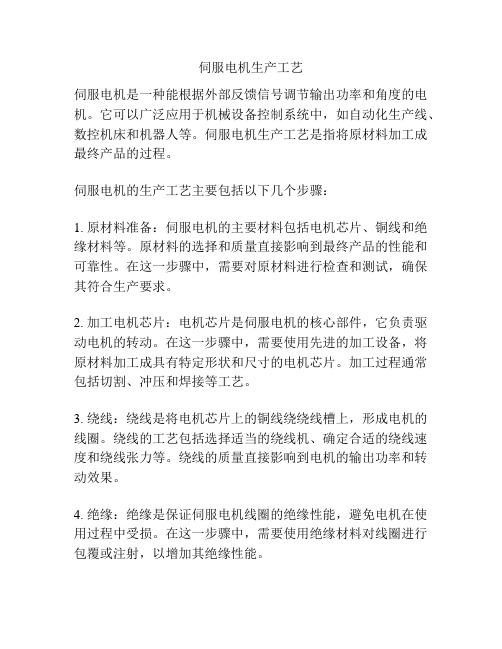
伺服电机生产工艺伺服电机是一种能根据外部反馈信号调节输出功率和角度的电机。
它可以广泛应用于机械设备控制系统中,如自动化生产线、数控机床和机器人等。
伺服电机生产工艺是指将原材料加工成最终产品的过程。
伺服电机的生产工艺主要包括以下几个步骤:1. 原材料准备:伺服电机的主要材料包括电机芯片、铜线和绝缘材料等。
原材料的选择和质量直接影响到最终产品的性能和可靠性。
在这一步骤中,需要对原材料进行检查和测试,确保其符合生产要求。
2. 加工电机芯片:电机芯片是伺服电机的核心部件,它负责驱动电机的转动。
在这一步骤中,需要使用先进的加工设备,将原材料加工成具有特定形状和尺寸的电机芯片。
加工过程通常包括切割、冲压和焊接等工艺。
3. 绕线:绕线是将电机芯片上的铜线绕绕线槽上,形成电机的线圈。
绕线的工艺包括选择适当的绕线机、确定合适的绕线速度和绕线张力等。
绕线的质量直接影响到电机的输出功率和转动效果。
4. 绝缘:绝缘是保证伺服电机线圈的绝缘性能,避免电机在使用过程中受损。
在这一步骤中,需要使用绝缘材料对线圈进行包覆或注射,以增加其绝缘性能。
5. 装配:装配是将加工好的电机芯片和其他配件组装成最终的产品。
装配的工艺包括按照工艺流程进行组装,检查和调试组装好的产品。
在这一步骤中,需要使用专业的工具和设备,确保产品的质量和性能。
6. 测试:测试是对装配好的产品进行性能和可靠性测试的过程。
测试的内容包括输出功率、转动效果和可靠性等指标。
通过测试,可以对产品的质量进行评估和验证,确保产品符合设计要求和客户需求。
7. 包装和发货:在完成测试后,需要对产品进行包装,并安排发货。
包装的目的是保护产品不受损坏,并方便运输和存储。
以上是伺服电机生产工艺的基本步骤,不同的厂家和产品可能会有一些差异。
通过合理的工艺和严格的质量控制,可以生产出质量可靠、性能优良的伺服电机产品。
微电机生产工艺

微电机生产工艺
微电机生产工艺是指将原材料经过一系列的工艺流程和生产操作,最终制造出符合要求的微电机产品的过程。
下面将介绍一个常用的微电机生产工艺流程。
1. 原材料准备:根据产品要求,准备合适的原材料,通常包括导线、铁芯、绝缘材料等。
2. 铁芯制备:将铁芯材料经过裁剪、加工成合适的形状和尺寸。
铁芯是微电机的重要组成部分,对电机的性能和效率影响较大。
3. 绕线:使用导线将绕组绕制在铁芯上。
绕组是微电机的关键部件,它通过通电和产生磁场来产生电力。
4. 绝缘处理:在绕组上涂覆绝缘漆,以提高绕组的绝缘性能,防止短路和电击。
5. 焊接和组装:将绕组与其他零部件进行焊接和组装。
这包括定子、转子、轴等部件的安装和固定。
6. 平衡和校准:对微电机进行平衡处理,以减小振动和噪音。
同时对微电机的性能参数进行校准,保证产品符合要求。
7. 测试和调试:对生产出的微电机进行各项性能测试和调试,确保产品的质量和性能达到标准要求。
8. 包装和出厂:将合格的微电机进行包装和标识,准备出厂销
售。
在微电机生产过程中,还需要进行质量控制和管理。
包括原材料的入库检验,生产过程中的检测和监控,以及最终的产品检验和质量保证。
此外,还需要进行生产计划和进度控制,以保证生产的效率和质量。
以上是一个简单的微电机生产工艺流程,实际的生产过程可能根据产品的不同而有所差异。
随着技术的不断发展,微电机的生产工艺也在不断改进和更新,以提高产品的性能和质量。
微电机定、转子冲片制造新工艺
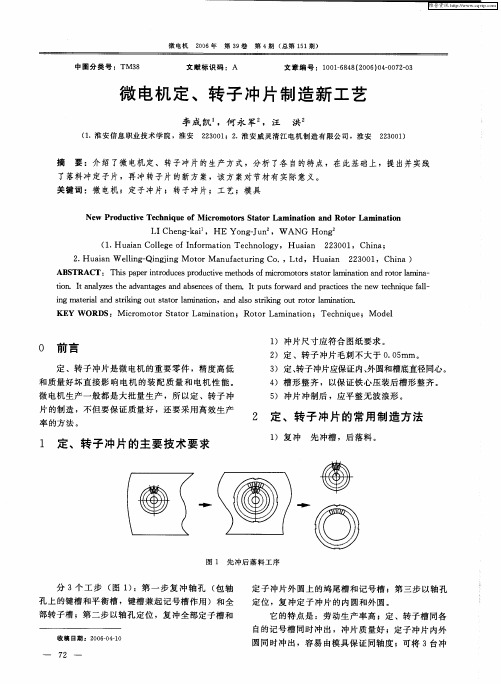
LICh n — a H E Yo g J n , W ANG n e g k i, n —u Ho g
( . u in Colg fI f r ain Te h oo y H u in 2 3 0 , Ch n ; 1 H aa l eo n o m to c n lg , e aa 2 0 1 ia
1 复冲 ) 先 冲槽 ,后 落料 。
1 定 、转 子 冲 片 的主 要技 术 要 求
-
图 1 先 冲 后 落 料 工 序
分 3个 工 步 ( 1 :第 一 步 复 冲 轴 孔 ( 轴 图 ) 包
孔 上 的键槽 和平 衡槽 ,键槽兼 起 记号槽 作用 ) 和全
定 子 冲 片外 圆上 的鸠尾 槽 和记号 槽 ;第三 步 以轴 孔 定位 ,复 冲定 子 冲片 的 内圆和外 圆 。 它 的特 点是 :劳动 生产 率高 ;定 、转子槽 同各 自的记 号槽 同时 冲 出 ,冲片 质量好 ;定 子冲 片 内外 圆同时 冲 出 ,容 易 由模具 保证 同轴 度 ;可将 3台冲
和 质量好 坏直 接 影 响 电机 的装 配 质 量 和 电机 性 能 。
微 电机 生产一 般都 是 大批量 生产 ,所 以定 、转 子 冲 片 的制 造 ,不但 要保证 质量 好 ,还 要采用 高效 生产
率 的方 法 。
5 冲 片冲制 后 ,应平 整无 波浪 形 。 )
2 定 、转 子 冲 片 的 常 用 制造 方法
维普资讯
微 电机
20 0 6年
第3 9卷
第 4期 ( 第 1 1期 ) 总 5
中 图 分 类 号 :TM3 8
文 献 标 识 码 :A
文章 编 号 :1 0—8 8 20 )40 7—3 0 164 (0 6 0 —0 20
微电机制造工艺

PPT文档演模板
微电机制造工艺
1.3.3 工艺方案设计分类
n a、新产品样机试制; n b、新产品小批量试制; n c、批量生产; n d、老产品改进。
ห้องสมุดไป่ตู้
PPT文档演模板
微电机制造工艺
1.3.4 工艺方案设计内容
不同类型的工艺方案其内容也是不同的, 以新产品样机试制为例说明其内容。
PPT文档演模板
微电机制造工艺
1.4.3 工艺规程编制依据
原则:即要保证产品质量,又要考虑生产成本。
n a、研究产品图纸及技术条件等资料; n b、产品类型及本厂生产条件是工艺规程制定的重要因
素之一; n c、制备毛坯及加工时应尽量考虑采用少无切削新工艺; n d、工艺过程分阶段; n e、选择合理的定位基准; n f、应考虑零部件中隐含的要求。
PPT文档演模板
微电机制造工艺
1.2 生产类型及特点
n 1.2.1 单件的批量生产
一个批次只生产几台、几十台、数百台电机。
n 1.2.2 中等批量生产
产品周期地进行成批生产。
n 1.2.3 大批量生产
同一产品,大批量、经常反复地生产。 说明:生产类型的年产量根据各企业产品具体情况而定。
PPT文档演模板
1.4 工艺规程
n 专用工艺规程 针对每一个产品和零部件所设计的工艺规程
n 通用工艺规程 为一组结构相似的零部件所设计工艺规程
n 标准工艺规程 已纳入标准的工艺规程,例如金属材料热处理 规范等
PPT文档演模板
微电机制造工艺
1.4.1 工艺规程的文件形式 及使用范围
n a、工艺过程卡,主要用于单件小批量产品; n b、工艺卡片,用于各种批量生产的产品; n c、作业指导书,用于关键件、重要件和质量
精选微电机制造工艺

3.2 绝缘处理
绝缘既是电机可靠运行的可靠保证,又常常是电机寿命最薄弱环节,是非常重要的,一旦绝缘出了问题,电机将不能正常运转。绝缘材料一般指电阻系数在1000MΩcm以上的材料最基本的最常用分类方法是按耐热程度分级,Y A E B F H C 90 105 120 130 155 180 >180℃
4 铁心制造
铁心是电机主磁路的导磁体,是电机功能性部件之一,铁心制造是微电机生产的重要工序。
4.1 铁心冲片制造工艺
一般采用冲压方法加工,只有当在样机试制时(数量较小),可采用线切割方法加工。冲片冲压加工是由冲模在曲柄压力机(冲床)上来实现的。
4.1.1 冲模
单工序冲模,一付模具只完成一种工序的冲模,如冲孔、落料等,微电机中有时采用单槽冲。复合模,在冲床一次行程中,在一付模具的同一位置上完成几个不同工序的冲模,完成两个工序的有凸凹模,位置精度最高。级进模,也叫连续模,在冲床的一次行程中,在一付模具的不同位置上同时完成两道或两道以上的冲模。常在高速冲床上使用,需要进料机构,用于自动化生产。
3.3.2 表面化学处理
钢件的氧化:发蓝铜及合金的钝 化:工件浸入铬酸盐形成钝化层,防护作用增强。
3.3.3 表面涂漆
目的:防锈、防腐、绝缘、装饰涂漆方法:常用刷涂、喷涂、浸漆等较先进的工艺: 静电喷涂,同熔槽绝缘时的静电喷漆一样,不适合于内腔涂敷。 电泳涂漆,
3.4 塑料件
1.2.1 单件的批量生产 一个批次只生产几台、几十台、数百台电机。1.2.2 中等批量生产 产品周期地进行成批生产。1.2.3 大批量生产 同一产品,大批量、经常反复地生产。说明:生产类型的年产量根据各企业产品具体情况而定。
1.3 工艺方案
2.1.3 有底结构
- 1、下载文档前请自行甄别文档内容的完整性,平台不提供额外的编辑、内容补充、找答案等附加服务。
- 2、"仅部分预览"的文档,不可在线预览部分如存在完整性等问题,可反馈申请退款(可完整预览的文档不适用该条件!)。
- 3、如文档侵犯您的权益,请联系客服反馈,我们会尽快为您处理(人工客服工作时间:9:00-18:30)。
2.1.2 直筒结构
a 、 毛坯 卷铆机壳:由钢板卷制焊接而成 卷焊机壳:由钢板卷制对铆而成 无缝钢管:量少时可选用标准型材,量
大时可定做管材,直接轧制成所需尺寸。
b、加工工艺
卷制机壳
卷制机壳一般用于性能要求不高的力能类直流电机, 其装配时多采用缩口或翻铆方式。
针对导磁材料,如冲片、机壳等,为了 改善其磁性能,也需进行必要的热处理。
3.1.1 分类及用途
a、退火、正火 目的:
▪ 软化钢件,便于切削; ▪ 消除残余应力,防止变形、开裂; ▪ 细化晶粒、改善组织,提高钢的机械性
能或磁性能; ▪ 为最终热处理(淬火十回火)作准备;
b、调质
可获得较好的综合机械性能,如轴的调 质一般在粗车后,精车(或磨)前进行。
注意应有粗、精加工之分。 铸造成形:注意机加工前需退火处理。
例:机壳零件图及工艺
A
2.2 转轴
轴是电机的重要零件之一 对轴的要求: ▪ 有是足够的强度和刚度; ▪ 合理的尺寸精度和形位公差; ▪ 轴的结构尽量合理,如台阶尽量少。
2.2.1 轴的结构形式
a、光轴(无台阶轴)
光轴生产效率很高,适合于批量生产。光轴又可分为: 全光轴、压筋光轴、滚花光轴(用的少)。其中后两 种是在全光轴上的安装铁心段及换向器段进行压筋及 滚花。
4 铁心制造
铁心是电机主磁路的导磁体,是电 机功能性部件之一,铁心制造是微 电机生产的重要工序。
4.1 铁心冲片制造工艺
一般采用冲压方法加工,只有当在样机 试制时(数量较小),可采用线切割方 法加工。
冲片冲压加工是由冲模在曲柄压力机 (冲床)上来实现的。
4.1.1 冲模
单工序冲模,一付模具只完成一种工序的冲模, 如冲孔、落料等,微电机中有时采用单槽冲。
把一台微电机零部件的加工关 系用图表表示出来,称之。
2 机械加工
在微电机机加工中,机械加工 占有很大的比重,主要有机壳、转 轴、端盖及其他零部件加工
2.1 机壳加工
永磁直流电机的机壳一般情况 下既起支承作用,又起导磁作用, 机壳材料一般采用10#钢或20#钢 等低碳钢。
2.1.1 机壳结构
直筒式结构,即所谓的双端盖机壳; 有底结构,即所谓的单端盖结构。
省之 c、冲片退火处理 d、绝缘处理
以上工序力能类永磁直流电机视情况取舍,
冲片绝缘处理
目的:为了减少冲片叠成后的涡流损失,以减 少铁心发热
对绝缘处理的要求:
①冲片绝缘层有足够的绝缘电阻值; ②足够的机械强度、附着力和韧性; ③要均匀(一般为为0.015~0.02mm)提高叠压数,保证铁心有效 长度; ④有良好的导热及耐热性; ⑤绝缘工艺方法简单、适用。
1.2.1 单件的批量生产
一个批次只生产几台、几十台、数百台电机。
1.2.2 中等批量生产
产品周期地进行成批生产。
1.2.3 大批量生产
同一产品,大批量、经常反复地生产。 说明:生产类型的年产量根据各企业产品具体情况而定。
1.3 工艺方案
加工一个零件,或完成一个加工要 求,可以设计若干个不同的工艺过程或 工艺方法,即可以有多种工艺方案。
控制点的工序; d、工艺守则,某一专业应共同遵守的操作要
求,如金属材料热处理规范等; e、毛坯图; f、工艺附图,常与a、b项配合使用。
1.4.2 工艺规程的特点
多样性 因批量大小、生产厂家、加工设备和设 计人员的不同而不同。
合理的工艺规程才是好的工艺规程 并不是越先进越好。
1.4.3 工艺规程编制依据
3.2.3 绕组的绕注绝缘
直流无刷定子环氧浇注——定子通孔式; 直流力矩电机转子与换向器一起浇注;
常用真空浇注。
3.3 表面处理
微电机中有许多零件需要进行 表面涂覆处理,其目的是提高表面 的防护性能及装饰效果。
3.3.1 表面金属镀层
a、电镀——最广泛使用的方法 b、化学镀 c、表面合金化,如渗氮等。
切削加工时,粗、精加工分开,减小变 形。
端盖止口与轴承室尽量一次装夹精车, 如果两次装夹精车,应采取措施保证两 者的同轴度要求。
3 微电机中使用的专业工艺
微电机制造工艺中,除了机械 制造工艺外,还有用于微电机加工 的专用工艺,如热处理、绝缘、塑 压、表面处理、粘接等
3.1 热处理
为改善轴、机壳等结构件的加工特能、 机械性能及尺寸稳定性需进行热处理。
3.3.2 表面化学处理
钢件的氧化:发蓝 铜及合金的钝 化:工件浸入铬酸盐形成
钝化层,防护作用增强。
3.3.3 表面涂漆
目的:防锈、防腐、绝缘、装饰 涂漆方法:常用刷涂、喷涂、浸漆等 较先进的工艺:
静电喷涂,同熔槽绝缘时的静电喷漆一 样,不适合于内腔涂敷。 电泳涂漆,
3.4 塑料件
在微电机中塑料主要用作绝缘件及结构 件,如刷架、换向器、接线板、出线盒、 端罩、集电环等,近年来在串激电机也 用作绝缘端板及槽楔架(整体)。
2.2.3 注意事项
a、为保证尺寸及位置精度,粗车同精车分开; b、铣键槽、铣扁时,如轴较粗时,可在精磨
后铣,这样键槽对称性好,轴细时怕变形,可 在精度前进行;
c、加工台阶轴时,一般以中心孔作为加工、 测量及设计基准,保持基准一致性。
d、为改善轴的切削性能及尺寸稳定性,应分 别在校直、粗车、半精车前后,适当车排合适 的热处理。
是指导产品工艺准备工作的依据。
1.3.1 工艺方案设计原则
主要应在保证产品质量(技术指标)的 同时,充分考虑经济效益(生产周期、 成本及环保);
根据本企业的能力,积极采用先进的工 艺及工装。
1.3.2 工艺方案设计依据
a、产品图纸及有关技术文件; b、产品的生产性质及生产类型; c、本企业现有的生产条件; d、国内外同类产品的工艺技术情报; e、有关技术政策; f、企业技术领导对工艺工作的要求及有
3.5 粘接
永磁直流电机:定子粘接 无刷直流电机:转子粘接。
注意事项
a、一般粘接面,如机壳内孔,转子导磁环等 粘接表面应喷砂处理。
b、粘接面应擦洗干净,不能有油污。 c、转子线速度转速较高时,如大于3000转时,
常给磁钢外圆热套一个加固套,转速不高时, 也可用涂有环氧胶的布带缠绕转子外表面, 防护加固。 d、烘干温度不能高于磁钢允许温度,以防磁 钢退磁。
加工工序:落料→卷型(铆)→焊接→整形→(退 火)
无缝钢管
切削加工主要有车机壳内孔、止口、外圆、端面, 钻孔、攻丝等。一般应分粗车和精车,并在粗精车之 间加退火。目的:提高机壳的磁性能,减少机壳变形。
2.1.3 有底结构
拉深成形:一般多用于小型机壳,效率 高,适合于批量生产。多用08钢板材。
挤压成形:效率高,适合于批量生产。 棒料加工:一般用于单件小批量生产,
复合模,在冲床一次行程中,在一付模具的同 一位置上完成几个不同工序的冲模,完成两个 工序的有凸凹模,位置精度最高。
级进模,也叫连续模,在冲床的一次行程中, 在一付模具的不同位置上同时完成两道或两道 以上的冲模。常在高速冲床上使用,需要进料 机构,用于自动化生产。
4.1.2 冲片制造
a、冲裁 b、去毛刺,一般毛刺小于0.05mm时可
原则:即要保证产品质量,又要考虑生产成本。
a、研究产品图纸及技术条件等资料; b、产品类型及本厂生产条件是工艺规程制定的重要因
素之一; c、制备毛坯及加工时应尽量考虑采用少无切削新工艺; d、工艺过程分阶段; e、选择合理的定位基准; f、应考虑零部件中隐含的要求。
1.5 工艺规程举例--工艺路线表
c、淬火
▪ 目的是提高强度、硬度、耐磨性。在磨
前进行,电机上一般用的不多,常用表 面淬火,好齿轮表面淬火。
3.1.2 冲片的退火处理
a、冷轧无取向硅钢 其电绝缘层耐热温度为700~900℃,相 应退火温度为650~680℃,属低温退火;
b、铁镍合金 例如:1J50、1J79,退火温度为 1050~1150 ℃,属于高温退火。必须在 真空炉或氢气炉中进行,防止氧化。
按塑料分类:热固性塑料、热塑性塑料。
3.4.1 塑件设计的工艺要求 (结构工艺性)
a、脱模斜度 b、壁厚 c、加强筋 d、支承面(基准面) e、圆角 f、嵌件
3.4.2 成形工艺
a、压塑成形 b、挤塑成形 c、注射成形
压塑成形和挤塑成形适用于热固性塑料 注射成形适用于热塑性塑料
3.2.2.1 浸化的方法及设备
a、沉浸
常压浸(一般浸漆):用于线径较粗,匝数少、槽满 率低的绕组浸漆。 真空浸:用于控制类微电机及线径细、匝数多、槽满 率高的电机。
b、滴浸
常在半自动及全自动滴漆设备上进行。 必须采用无溶剂漆,主要原因是能迅速固化。
3.2.2.2 绝缘浸漆的工艺过程
浸漆的工艺过程主要包括: a、预热 b、浸漆 c、烘干 d、检验
b、台阶轴
是微电机中的一种主要结构形式,一般都带中心孔, 其加工一般都以中心孔做为定位基准。
2.2.2 加工工艺
a、光轴
主要工艺过程有: 下料、较直→平端面→调质处理→(校直)→ 粗磨→精磨→(压筋)→检查等。
b、台阶轴
主要工艺过程有: ቤተ መጻሕፍቲ ባይዱ料→平端面→打中心孔→粗车→调质处理→ 精车(半精车)→铁心、换向器段压筋(滚花) →精磨铁心段→铣键槽
1.4 工艺规程
专用工艺规程 针对每一个产品和零部件所设计的工艺规程
通用工艺规程 为一组结构相似的零部件所设计工艺规程
标准工艺规程 已纳入标准的工艺规程,例如金属材料热处理 规范等
1.4.1 工艺规程的文件形式 及使用范围
a、工艺过程卡,主要用于单件小批量产品; b、工艺卡片,用于各种批量生产的产品; c、作业指导书,用于关键件、重要件和质量