本科机械工程专业毕业设计外文翻译(中文部分)
锻造、铸造、焊接外文翻译

毕业设计(论文)外文翻译学生姓名:系别:机械工程系专业:机械设计制造及其自动化班级:学号:译文出处:Science and Technology Engl-ish for Mechanical EngineeringCasting、Forging and Welding1. CastingMetal casting is one of the oldest of all industries, both ancient and medieval history offering examples of the manufacture and use of casting. From simple axeheads poured from copper in open moulds some 5000 years age, casting in the pre-Christian world developed to a point at which elaborate bronze statuary could be produced in two-piece and cored moulds. By the end of the medieval period, decorated bronze and pewter casting had begun to be used in European church and domestic life.The widespread adoption of cast iron as engineering material awaited the success of Abraham Darby in 1790 in smelting in the coke blast furnace; this paved the way for the massive use of cast iron in construction during the years following the industrial revolution.Many foundries sprang up after the industrial revolution, the vast majority being for the manufacture of the cast iron then being used as a structural material. The quantity production of iron castings in the nineteenth century was not matched by a universal advance in quality and the engineering use of the products encountered more serious risks in a non-ductile material.Despite the skill of the molder in producing complex forms, there was little change in the metallurgical and engineering situation until the modern era brought a better understanding of the factors determining quality. With modern techniques of process control the rudimentary judgment of the operator could give way to objective measurements of metal temperature, molding material properties and other production variables. These improvements have been applied not only to cast iron but to a wide range of cast alloys.There are four basic casting methods: sand-casting, die-casting, investment-casting, and centrifugal casting.Sand-casting is the most widely used method employed in foundry. In this process, sand moulds are contained in metal molding boxes that have four sides but no top or bottom. During the molding operation the boxes are located togetherby pins so that they can be separated to remove the pattern, and replaced in the correct position before the metal is poured in. The boxes are clamped together, or the cope (top section) weighted down when pouring to prevent the cope from “floating away”from the drag (lower section) when the mould is full of molten metal. The sequence when molding the simple two-part mould to cast a bracket is illustrated as follows.At the first stage the pattern is seated on the moulding board. The pattern is covered with facing sand, which is a specially prepared sand of good quality, which can take a clean and smooth impression, and can resist the heat from the molten metal that will be in contact with it. The facing sand is backed up with molding sand, which is old facing sand from previous moulds. The molding sand is carefully rammed up so that it is fairly tight around the pattern to produce a good solid mould, yet permeable enough to allow the gases produced during casting to escape. The sand is finally leveled off.At the second stage the mould with the pattern still in position is inverted; the exposed sand lightly covered with parting sand, and the exposed pattern with facing sand.(The parting sand has no cohesion, and is introduced to permit a clean separation when the mould is opened up to remove the pattern .) The second molding box is located in position on the first box and filled with molding sand. Two or more plugs are introduced when the second box is being filled (these are removed later, leaving channels in the sand). One of these plugs is positioned to one side of the pattern. The sand is rammed up and leveled off.Now, at stage 3, to allow the pattern to be removed. This is done by screwing a bar with a threaded end into a suitable insert in the pattern, damping the sand around the pattern, and gently rapping the bar in all directions so that the pattern can be carefully withdrawn. To facilitate the removal of the pattern without scuffing the sides of the impression, all surfaces that lie in the direction of pattern removal are inclined slightly by a small amount (the draw angle).A groove called a gate is cut in the sand face to allow the channel producedby the plug that is outside the pattern to connect with the impression .The metal is poured through this channel (called the runner), and the gate prevents it from dropping straight into the impression and damaging it .The cross-section of the gate is slightly smaller than that of channel so that a full runner will always supply metal to the gate at a slight pressure.Finally, the mould is reassembled, carefully locating and securing the two sections. The top section is known as the cope, and the lower section is known as the drag. The sand in the cope is vented. These vents allow the sand to be rammed up more tightly at the earlier stages without the risk of gases being trapped in the molten metal and forming blowholes in the solid metal. A sand-feeding gate (also called a pouring or bowl) is added to make it easier to pour the metal into the runner. The molten metal is poured through the runner and the air will escape through the riser.The impression will be filled with molten metal when it is completely filled. Gases can escape through the runner and the riser, which also act as headers to supply the impression with more metal to compensate for the contraction of the metal when cooling in the molten state.2. ForgingForging is the plastic working of metal by means of localized compressive forces exerted by manual or power hammers, presses, or special forging machines. It may be done either hot or cold. however, when it is done cold, special names usually are given to the processes. Consequently, the terms“forging” usually implies hot forging done above the recrystallization temperature.Modern forging is a development form the ancient art practiced by the armor makers and the immortalized village blacksmith. High-powered hammers and mechanical presses have replaced the strong arm, the hammer, and the anvil and modern metallurgical knowledge supplements the art skill of the craftsman in controlling the heating and handling of the metal.Forge ability is the term used in the industry to denote a material relative resistance to deformation and its plasticity. While considerable disagreementexists as to precisely what characteristics the word “forge ability” should include, the term as used here is defined as the tolerance of a metal or alloy for deformation without failure, regardless of forging pressure requirements.Raw material used for forging is generally bar or billet stock hot rolled from ingots melted in open-hearth, electric arc, or vacuum arc furnace .other forms and shapes such as rolled slabs, plats, and stock produced by continuous casting techniques are occasionally used .for certain grades ,vacuum arc melting imparts better forge ability than does conventional arc melting . However, the major purpose of vacuum melting is the improvement of mechanical properties and cleanliness, not forging behavior.Equipment behavior influences the forging progress since it determines the feasibility of forging a part and affects the rate of deformation and the temperature conditions.The hammer is the most economical type of equipment for generating load and energy necessary to carry out a forging process, provided that the material being forged can support high deformation velocities. It is most commonly used hot forging equipment for repeated blows on the same workpiece and cannot be overloaded.There are various types of hammers: air-lift gravity drop hammers, power drop hammers, power drop hammers, Counterblow hammers ect. In a simple gravity drop hammer the upper ram is positively connected to a board, a belt, a chain or a piston. When forging the ram is lifted to a certain height and then dropped on the stock placed on the anvil. During the down stroke, the rain is accelerated by gravity and builds up the blow energy. The upstroke takes place immediately after the blow, the force necessary to ensure quick lift-up of the ram can be 3 to 5 times the ram weight. The operation principle of a power-drop hammer is similar to that of an air drop hammer. During the down stroke, in addition to gravity, the ram is accelerated by steam, cold air or hot air pressure. In an electro hydraulic gravity-drop hammer, the ram is lifted with oil pressure against an air cushion. The compressed air slows down the upstroke of the ram and contributes to its acceleration during the down stroke .thus; the electrohydraulic hammer also has a minor power hammer action.Press forging employs a slow squeezing action in deforming the plastic metal, as contrasted with the rapid-impact blows of a hammer. Hydraulic forging press is operated by large pistons driven by high-pressure hydraulic or hydrometric system. The squeezing action is carried completely to the center of the part being pressed, thoroughly working the entire section. These presses are the vertical type and may be either mechanically or hydraulically operated. The mechanical presses, which are faster operating and most commonly used, range in capacity from 5000 to 10000 tons.In the forging press a grater proportion of the total work put into the machine is transmitted to the metal than in a drop hammer. The machine and foundation absorb much of the impact of the drop hammer .press reduction of the metal is faster, and the cost of operation is consequently lower. most press forging s are symmetrical in shape ,having surfaces, which are quite smooth, and provide a closer tolerance than is obtained by a drop hammer .however ,drop forging can forge many parts of irregular and complicated shapes more economically. Forging presses are often used for sizing operations on parts made by other forging processes.For small forgings closed impression dies are used, and only one stroke of the ram is normally require to perform the forging operation .the maximum pressure is built up at the end of the stroke ,which forces the metal into shape .dies may be mounted as separate units, or all the cavities may be put into a single block. for small forgings individuals die units are more convenient .large ingots are now almost always forged with hydraulic presses instead of with steam hammers, since the work done by a press goes deeper. Further, the press can take a cooler ingot and can work to closer dimensions.The forging should be done at about the same temperature as rolling; the process improves the physical properties of the steel just as rolling does. In the final forging it is important not to have the steel too hot, for overheated steel will have poor mechanical properties when cooled. in heating for forging the temperature is usually judged by the eye, but where a large number of thesame patterns will be made, the pieces to be forged are heated in furnaces in which the temperature is indicated by pyrometers, and often is automatically controlled.3. weldingWelding techniques have become so versatile that it is difficult nowadays to define “welding”. Formerly welding was “the joining of metals by fusion”, that is, by melting, but this definition will no longer do. Welding was next defined as the “joining of metals by heat”, but this is not a proper definition either. Not only metals can be welded, so can many of the plastics. Furthermore several welding methods do not require heat. Every machinist is familiar with heatless welding method under some circumstances. Besides these, we can weld with sound and even with the famous laser. Faced with a diversity of welding methods that increase year by year, we must here adopt the following definition of welding:" welding is the joining of metals and plastics by methods that do not employ fastening devices”.There is also no uniform method of naming welding processes. Some processes are named according to the heat source or shielding method, other certain specialized processes are named after the type of joint produced. Examples are spot and butt welding. But an overall classification can not take account of this because the same type of joint may be produced by a variety of processes. Spot welding may be done by electric resistance, arc, or electron-beam processes and butt welding by resistance, flash or any of a number of other methods. Many welding processes are named depending on the heat applied, equipment used, and type of metal to be joined and the strength of the joint.Soldering is the process of joining two metals by a third metal to be applied in the molten state. Solder consists of tin and lead, while bismuth and cadmium are often included to lower the melting point. One of the important operations in soldering is that of cleaning the surface to be joined, this may be done by some acid cleaner. Soldering gives a satisfactory joint for light articles ofsteel, copper or brass, but the strength of soldering joint is rather less than a joint which is brazed, riveted or welded. These methods of metal are normally adopted for strong permanent joints.Pressure welding is known as the simplest method of welding two pieces of metal together. The ends of metal are heated to a while heat—for iron, the welding temperature should be about 1300℃—in a flame. At this temperature the metal becomes plastics. The ends are then presses or hammered together, and the joint is smoothed off. Care must be taken to ensure that the surfaces are thoroughly clean first, for dirt will weaken the weld. Moreover, the heating of iron or steel to a high temperature causes oxidation, and a film of oxide is formed on the heated surfaces. For this reasons, a flux is applied to the heated metal. At welding heat, the flux melts, and the oxide Particles are dissolved in it together with any other impurities which may be present. The metal surfaces are pressed together, and the flux is squeezed out from the center of the weld.Gas welding includes all the processes in which gases are used to obtain a hot flame. Those commonly used are acetylene, natural gas, and hydrogen in combination with oxygen. The maximum temperature developed by oxyhydrogen welding is 3600℉ (1980℃). Hydrogen is produced either by the electrolysis of water or by passing steam over coke. An oxyacetylene weld is produced by heating with a flame obtained from the combustion of oxygen and with or without the use of a filler metal. In most cases the joint is heated to a state of fusion, and as a rule, no pressure is used.Are welding is a process in which coalescence is obtained by heat produced from an electric arc. The electrode or filler metal is heated to a liquid state and deposited into the joint to make the weld. Contact is first made between the electrode and the work to create an electric circuit, and then, by separating the conductors, an arc is formed. The electric energy is converted into intense heat in the arc, which attains a temperature around 10 000°F (5500℃). Either direct or alternating current can be used for arc welding, direct current being preferred for most purposes. A d-c welder is simply a motor-generator set ofconstant-energy type, having the necessary characteristics to produce a stable arc. Arc welding uses commonly metal electrodes or carbon electrodes.Laser Welding is used because of laser’s high heat intensity. It can be operated in any transparent medium without contact with the workpiece, since the laser delivers its energy in the form of light. In welding, the power is delivered in pulses rather than as a continuous beam, the beam is focused on the workpiece and the intense heat produces a fusion weld. Laser welding is slow and is used only for special jobs involving small weldments. Its greatest use is found in the electronics industry.Explosion welding is a process that uses energy from the detonation of an explosive to join two pieces of metal. The explosion accelerates the pieces to a speed at which a metallic bond will form between them when they collide. The weld is produced in a fraction of a second without the addition of filler metal. This is essentially a room temperature process in that gross heating of the workpieces does not occur. The faying surfaces, however, are heated to some extent by the energy of the collision, and welding is accomplished through plastic flow of the metal on those surfaces. Welding takes place progressively as the explosion and the forces it creates advance from one end of the joint to the other. Deformation of the weldment varies with the type of joint. There may be no noticeable deformation at all in some weldments, and there is no loss of metal.译文:铸造、锻造和焊接1.铸造金属铸造是最古老的产业之一,远古时期和中世纪就有人使用和制造铸件了。
孙明明 外文资料翻译
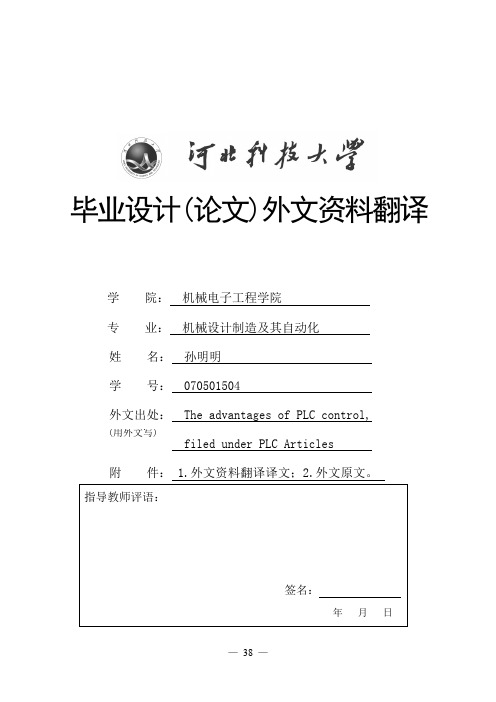
毕业设计(论文)外文资料翻译学院:机械电子工程学院专业:机械设计制造及其自动化姓名:孙明明学号: 070501504外文出处: The advantages of PLC control,filed under PLC Articles附件: 1.外文资料翻译译文;2.外文原文。
(用外文写)附件1:外文资料翻译译文PLC的控制优势任何控制系统从概念到进入工厂工作都要经历四个阶段。
PLC系统在每一个阶段都有优势。
第一阶段是设计,对工厂的需要进行研究和制定控制策略,传统的运行平台的设计和制造必须在设计进行前完成。
PLC系统仅仅需要的是一个模糊的关于机器的可能大小的想法和I/O数量的要求(多少输入和输出接口)。
在这个阶段输入和输出芯片十分便宜,所以可以内置一个很健全的备用容量,它允许用来补充遗漏项目和为未来的扩充做准备。
其次是设计。
传统的方案是,每一项工作都是“一次成型”这不可避免的造成了工程拖延和增加成本。
一个的PLC系统使用最简单的标准件螺栓连接在一起。
在这样的连接下开始编写 PLC程序(或者至少是写入详细的程序规范)。
下一阶段是安装,安装是一种繁琐和昂贵的工作,例如安装传感器、执行器、限制开关系统和主机的连接。
分布式PLC系统使用串行链路式的预编译,测试界面可以简化安装它带来了巨大的成本优势。
PLC的程序多数在这个阶段完成。
最后是调试,而这正是PLC真正的优势被发掘的部分。
没有任何设备在第一次就正常工作。
人性就是这样,总会有一些疏漏。
与传统的系统变动情况的耗时和昂贵相比,PLC的设计师提供了系的内置备用内存容量、备用I/O和一些备用多芯电缆线,多数的变动能迅速和相对便宜的完成。
另外一个好处是,所有的变化PLC都有记录,程序的调试和修改不会因为没有被记录而遗失,这是一个经常发生在常规系统中的问题。
还有一个额外的第五阶段,维护,一旦启动工作,并移交生产就产生了维护的问题。
所有设备都有缺点,大多数设备在错误的模式中度过了它们的大部分的时间。
机械毕业设计英文外文翻译336年轻工程师竞相建造更高效更环保的汽车 - 副本

附录ABudding engineers compete to build more efficient, greener cars. University teams take varied technological approaches in vying for the Challenge X prize.The 17 Chevrolet Equinox sport utility vehicles that pulled up to the US Department of Energy headquarters on 21 May were identically equipped when they came off the assembly line in 2005. Four years later all resemblance ended at the exterior. In the intervening time, teams of students from 17 universities had torn the guts out of their donated crossover SUVs—those built on a car frame—and installed radically new drive systems of their own design. The goal of the makeover contest, sponsored by DOE, General Motors Corp, and others, was to improve the fuel economy and reduce the tailpipe emissions of the SUVs without sacrificing vehicle safety or performance.For GM and other US automakers, the Challenge X: Crossover to Sustainable Mobility competition got a new generation of engineers and scientists to work on "sustainable and innovative solutions" to reducing the country's dependence on oil, GM vice president for environment and energy Beth Lowery told the crowd at the ceremonial finish line. GM is beginning to move to electric-poweredvehicles, she said, adding, "There has never been a more exciting time to be involved in the auto industry."The winning team, from Mississippi State University, achieved a 38% gain in mileage over the stock vehicle with a "through-the-road parallel" hybrid system powered by a turbo-diesel engine running on 20% biodiesel fuel. Through-the-road parallel hybrids, the architecture selected by 13 teams, feature one set of wheels powered by the engine and the other set driven by electric motors. Ryan Williams, an MSU mechanical engineering undergraduate, said his team used computer-aided design software to help marry the drive train to the vehicle. Team members fabricated the one-of-a-kind brackets and other necessary structural components using computer numerical control tools available in the university's machine shop. Like many other participants in the Challenge X, Williams said he hopes to go on to a career in the automotive industry'.Bells and whistlesThe University of Wisconsin-Madison team won second place with a virtually identical drive architecture, adding a few bells and whistles that included an expensive stereo and an infrared camera that can spot a deer on the road ahead. Ben Fjellanger, a UW mechanical engineering student, said that several members of histeam will be interning this summer at the GM assembly plant in Janesville, Wisconsin.In addition to supplying the vehicles, GM put up $10 000 in seed money and up to $25 000 worth of additional production parts, including the GM engine of its choice, to each team. Ten teams, including the top three scorers, opted for a 1.9-liter direct-injection turbodiesel, which ironically isn't available in the US market. Universities were required to match the seed funding, grant release time of one course per semester for a faculty adviser, and provide an auto shop and computer lab. Institutions also committed to granting course credits to at least a core subgroup of the team members.A Canadian entry, from the University of Waterloo, was the only vehicle with hydrogen fuel-cell propulsion. A major challenge was to get the cell, which was made for stationary applications, to fit under the car's hood, explained Charles Hua, a chemical engineering graduate student. Although It was the only zero-emissions vehicle in the competition, its range was limited to 150 miles per tank by a contest rule that restricted the liquid hydrogen storage to 5000 pounds per square inch, half the pressure that is currently practical. There's also the matter of finding hydrogen fuel, although Hua said he knows of at least two filling stations in Ontario.A belt-driven motor paired with a flexible-fuel engine was the Texas Tech University entry. To reduce the load on the engine, the eleventh place team fitted a small fuel-cell and hydrogen tank in the trunk to power the lights, air conditioning, and other electric accessories. Team member Stephen Barrett explained that hydrogen can be injected to boost engine combustion under full acceleration conditions. Barrett has already landed a job with National Instruments Corp, a contest sponsor; his work on the vehicle's electronics package won a $700 prize from NI, which supplies electronic control equipment to automakers and others. Hydraulic driveArguably the most exotic drive train was a hydraulic hybrid system designed and built by last-place finisher University of Michigan. Its engine does not supply power directly but drives a pump that pressurizes hydraulic fluid in two onboard "accumulator" tanks. That stored energy is used to drive hydraulic motors turning the front and rear axles. The drive system requires no battery or transmission, explained team member Javier Somoza, who said that he'd "definitely" be looking for a career in hybrid propulsion R&D once he's completed his master's in mechanical engineering. Teams were initially instructed to follow the development process GM uses wben introducing a new model. After a year ofmodeling, simulation, and testing of the selected drive trains, teams were given two years to integrate them into their vehicles. The final year was devoted to ensuring customer acceptability and proving vehicle reliability in real-world conditions. Teams were graded periodically on their progress, their outreach efforts, and metrics such as acceleration, emissions, and fuel economy. More esoteric criteria included "well-to-wheel" greenhouse gas emissions reductions, well-to-wheel petroleum use, and "dynamic consumer acceptability."Awards totaling $79 500 were doled out to top-ranking competitors in various categories. As first overall, MSU won $7000.A 300-mile road rally from New York to Washington, DC, marked the end of the road for Challenge X, but DOE, GM, and Natural Resources Canada have already selected the 17 teams for a three-year contest that kicks off this fall. Argonne National Laboratory, which managed Challenge X, will also manage the new program, in which Saturn SUVs will be reengineered to meet California's tough zero-emissions standard. Most of the schools from Challenge X, including the top three finishers, will be back.附录B年轻工程师竞相建造更高效更环保的汽车大学队在采取各种挑战大奖的技术方法。
机械工程专业外文文献及翻译
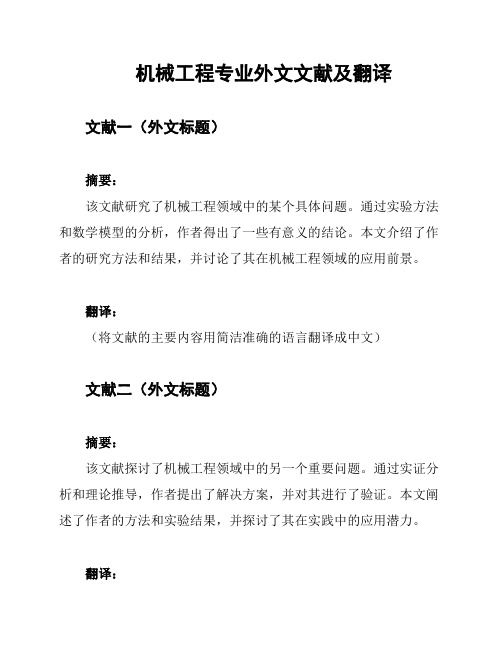
机械工程专业外文文献及翻译文献一(外文标题)
摘要:
该文献研究了机械工程领域中的某个具体问题。
通过实验方法和数学模型的分析,作者得出了一些有意义的结论。
本文介绍了作者的研究方法和结果,并讨论了其在机械工程领域的应用前景。
翻译:
(将文献的主要内容用简洁准确的语言翻译成中文)
文献二(外文标题)
摘要:
该文献探讨了机械工程领域中的另一个重要问题。
通过实证分析和理论推导,作者提出了解决方案,并对其进行了验证。
本文阐述了作者的方法和实验结果,并探讨了其在实践中的应用潜力。
翻译:
(将文献的主要内容用简洁准确的语言翻译成中文)
文献三(外文标题)
摘要:
该文献研究了机械工程领域中的另一个新颖课题。
作者通过数
值模拟和实验验证,得出了一些有趣的发现。
本文介绍了作者的研
究过程和结果,并讨论了其对机械工程领域的影响。
翻译:
(将文献的主要内容用简洁准确的语言翻译成中文)
总结
本文档介绍了三篇机械工程专业的外文文献,包括摘要和翻译。
这些文献都对机械工程领域中的不同问题进行了研究,并提出了相
关的解决方案和发现。
希望这些文献能为机械工程专业的学生和研
究人员提供有价值的参考和启发。
机械工程毕业设计外文翻译---可视化的PLC程序使用XML
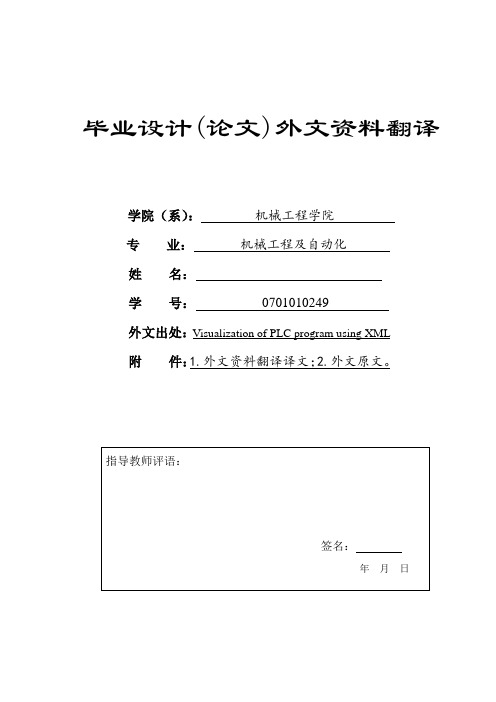
毕业设计(论文)外文资料翻译学院(系):机械工程学院专业:机械工程及自动化姓名:学号:0701010249外文出处:Visualization of PLC program using XML附件:1.外文资料翻译译文;2.外文原文。
指导教师评语:签名:年月日附件1:外文资料翻译译文可视化的PLC程序使用XML米巴尼尤尼斯和G.弗雷摘要:由于P LC程序日益复杂,在PLC应用方面有越来越多的兴趣爱好者。
形式化方法,让僵化的证明系统属性被核查和验证。
一个传统思路的方法就是在PLC 编程中设立一个正式的设计方法。
不过,现有的软件已被优化,改变,或移植到新系统.有需要找到从某一PLC程序开始的方法。
因此,规范PLC程序是一个现在研究的热点。
该文章概述了基于形式化的PLC程序基础上从新启动的方法。
转型成为一个独立的格式和可视化的结构,在这个过程中,PLC程序的确定是作为这项措施的重要中间步骤。
这表明如何XML和相应的技术可用于形式化和可视化现有的PLC程序。
一导言可编程逻辑控制器(PLC)是一种特殊类型的计算机,它应用于工业和安全的关键地方。
应用PLC的目的是控制某一特定的或可选择的过程,它是通过产生的电控制信号回应电器中相关的输出信号来实现的。
应用在制造业和化工过程控制,机械加工,交通,电力分配,以及其他许多领域。
PLC控制有着极大的不同,自动化应用范围的复杂性从一个简单的小组运作到控制一个会议室的的灯光和自动窗成为一个全自动化的生产线。
随着他们应用PLC知识的增加,他们把PLC应用到复杂性和品质要求高的地方,特别是对安全性要求特别严格的地方。
由于在有限的时间里PLCD的发展应用日益复杂,现有的软件或PLC的模块也在迅速发展,以此,需要一个正式的办法加以规范。
为了确保高品质的要求,我们需要检查和验证程序,以及分析和模拟现有系统[2] 。
其中一个重要的领域就是已经在最近的时间成长在规范化的PLC程序是逆向工程[3] 。
机械设计外文翻译--- 轴承的摩擦与润滑
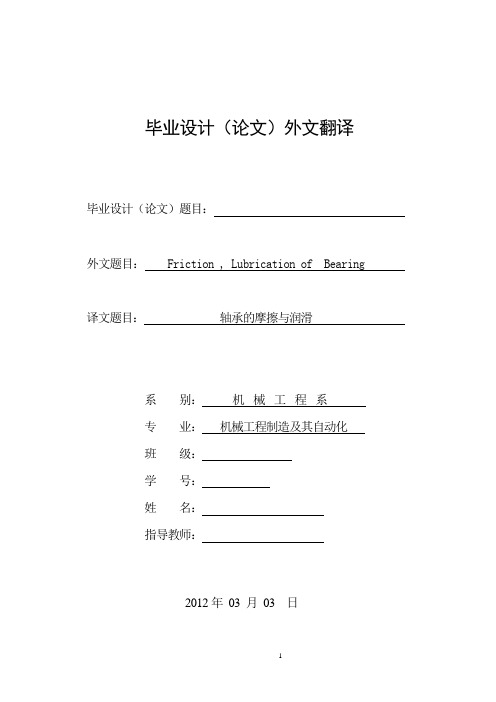
毕业设计(论文)外文翻译毕业设计(论文)题目:外文题目:Friction , Lubrication of Bearing 译文题目:轴承的摩擦与润滑系别:机械工程系专业:机械工程制造及其自动化班级:学号:姓名:指导教师:2012年03 月03 日外文文献原文:Friction , Lubrication of BearingIn many of the problem thus far , the student has been asked to disregard or neglect friction . Actually , friction is present to some degree whenever two parts are in contact and move on each other. The term friction refers to the resistance of two or more parts to movement.Friction is harmful or valuable depending upon where it occurs. friction is necessary for fastening devices such as screws and rivets which depend upon friction to hold the fastener and the parts together. Belt drivers, brakes, and tires are additional applications where friction is necessary.The friction of moving parts in a machine is harmful because it reduces the mechanical advantage of the device. The heat produced by friction is lost energy because no work takes place. Also , greater power is required to overcome the increased friction. Heat is destructive in that it causes expansion. Expansion may cause a bearing or sliding surface to fit tighter. If a great enough pressure builds up because made from low temperature materials may melt.There are three types of friction which must be overcome in moving parts: (1)starting, (2)sliding,and(3)rolling. Starting friction is the friction between two solids that tend to resist movement. When two parts are at a state of rest, the surface irregularities of both parts tend to interlock and form a wedging action. To produce motion in these parts, the wedge-shaped peaks and valleys of the stationary surfaces must be made to slide out and over each other. The rougher the two surfaces, the greater is starting friction resulting from their movement .Since there is usually no fixed pattern between the peaks and valleys of two mating parts, the irregularities do not interlock once the parts are in motion but slide over each other. The friction of the two surfaces is known as sliding friction. As shown in figure ,starting friction is always greater than sliding friction .Rolling friction occurs when roller devces are subjected to tremendous stress which cause the parts to change shape or deform. Under these conditions, the material in front of a roller tends to pile up and forces the object to roll slightly uphill. This changing of shape , known as deformation, causes a movement of molecules. As a result ,heat is produced from the added energy required to keep the parts turning and overcome friction.The friction caused by the wedging action of surface irregularities can be overcome partly by the precision machining of the surfaces. However, even these smooth surfaces may require the use of a substance between them to reduce the friction still more. This substance is usually a lubricant which provides a fine, thin oil film. The film keeps the surfaces apart and prevents the cohesive forces of the surfaces from coming in close contact and producing heat .Another way to reduce friction is to use different materials for the bearing surfaces and rotating parts.This explains why bronze bearings, soft alloys, and copper and tin iolite bearings are used with both soft and hardened steel shaft. The iolite bearing is porous. Thus, when the bearing is dipped in oil, capillary action carries the oil through the spaces of the bearing. This type of bearing carries its own lubricant to the points where the pressures are the greatest.Moving parts are lubricated to reduce friction, wear, and heat. The most commonly used lubricants are oils, greases, and graphite compounds. Each lubricant serves a different purpose. The conditions under which two moving surfaces are to work determine the type of lubricant to be used and the system selected for distributing the lubricant.On slow moving parts with a minimum of pressure, an oil groove is usually sufficient to distribute the required quantity of lubricant to the surfaces moving on each other .A second common method of lubrication is the splash system in which parts moving in a reservoir of lubricant pick up sufficient oil which is then distributed to all moving parts during each cycle. This system is used in the crankcase of lawn-mower engines to lubricate the crankshaft, connecting rod ,and parts of the piston.A lubrication system commonly used in industrial plants is the pressure system. In this system, a pump on a machine carries the lubricant to all of the bearing surfaces at a constant rate and quantity.There are numerous other systems of lubrication and a considerable number of lubricants available for any given set of operating conditions. Modern industry pays greater attention to the use of the proper lubricants than at previous time because of the increased speeds, pressures, and operating demands placed on equipment and devices.Although one of the main purposes of lubrication is reduce friction, any substance-liquid , solid , or gaseous-capable of controlling friction and wear between sliding surfaces can be classed as a lubricant.V arieties of lubricationUnlubricated sliding. Metals that have been carefully treated to remove all foreign materials seize and weld to one another when slid together. In the absence of such a high degree of cleanliness, adsorbed gases, water vapor ,oxides, and contaminants reduce frictio9n and the tendency to seize but usually result in severe wear; this is called “unlubricated ”or dry sliding.Fluid-film lubrication. Interposing a fluid film that completely separates the sliding surfaces results in fluid-film lubrication. The fluid may be introduced intentionally as the oil in the main bearing of an automobile, or unintentionally, as in the case of water between a smooth tuber tire and a wet pavement. Although the fluid is usually a liquid such as oil, water, and a wide range of other materials, it may also be a gas. The gas most commonly employed is air.Boundary lubrication. A condition that lies between unlubricated sliding and fluid-film lubrication isreferred to as boundary lubrication, also defined as that condition of lubrication in which the friction between surfaces is determined by the properties of the surfaces and properties of the lubricant other than viscosity. Boundary lubrication encompasses a significant portion of lubrication phenomena and commonly occurs during the starting and stopping off machines.Solid lubrication. Solid such as graphite and molybdenum disulfide are widely used when normal lubricants do not possess sufficient resistance to load or temperature extremes. But lubricants need not take only such familiar forms as fats, powders, and gases; even some metals commonly serve as sliding surfaces in some sophisticated machines.Function of lubricantsAlthough a lubricant primarily controls friction and ordinarily does perform numerous other functions, which vary with the application and usually are interrelated .Friction control. The amount and character of the lubricant made available to sliding surfaces have a profound effect upon the friction that is encountered. For example, disregarding such related factors as heat and wear but considering friction alone between the same surfaces with on lubricant. Under fluid-film conditions, friction is encountered. In a great range of viscosities and thus can satisfy a broad spectrum of functional requirements. Under boundary lubrication conditions , the effect of viscosity on friction becomes less significant than the chemical nature of the lubricant.Wear control. wear occurs on lubricated surfaces by abrasion, corrosion ,and solid-to-solid contact wear by providing a film that increases the distance between the sliding surfaces ,thereby lessening the damage by abrasive contaminants and surface asperities.T emperature control. Lubricants assist in controlling corrosion of the surfaces themselves is twofold. When machinery is idle, the lubricant acts as a preservative. When machinery is in use, the lubricant controls corrosion by coating lubricated parts with a protective film that may contain additives to neutralize corrosive materials. The ability of a lubricant to control corrosion is directly relatly to the thickness of the lubricant film remaining on the metal surfaces and the chermical composition of the lubricant.Other functionsLubrication are frequently used for purposes other than the reduction of friction. Some of these applications are described below.Power transmission. Lubricants are widely employed as hydraulic fluids in fluid transmission devices.Insulation. In specialized applications such as transformers and switchgear , lubricants with highdielectric constants acts as electrical insulators. For maximum insulating properties, a lubricant must be kept free of contaminants and water.Shock dampening. Lubricants act as shock-dampening fluids in energy transferring devices such as shock absorbers and around machine parts such as gears that are subjected to high intermittent loads.Sealing. Lubricating grease frequently performs the special function of forming a seal to retain lubricants or to exclude contaminants.The object of lubrication is to reduce friction ,wear , and heating of machine pars which move relative to each other. A lubricant is any substance which, when inserted between the moving surfaces, accomplishes these purposes. Most lubricants are liquids(such as mineral oil, silicone fluids, and water),but they may be solid for use in dry bearings, greases for use in rolling element bearing, or gases(such as air) for use in gas bearings. The physical and chemical interaction between the lubricant and lubricating surfaces must be understood in order to provide the machine elements with satisfactory life.The understanding of boundary lubrication is normally attributed to hardy and doubleday , who found the extrememly thin films adhering to surfaces were often sufficient to assist relative sliding. They concluded that under such circumstances the chemical composition of fluid is important, and they introduced the term “boundary lubrication”. Boundary lubrication is at the opposite end of the spectrum from hydrodynamic lubrication.Five distinct of forms of lubrication that may be defined :(a) hydrodynamic;(b)hydrostatic;(c)elastohydrodynamic (d)boundary; (e)solid film.Hydrodynamic lubrication means that the load-carrying surfaces of the bearing are separated by a relatively thick film of lubricant, so as to prevent metal contact, and that the stability thus obtained can be explained by the laws of the lubricant under pressure ,though it may be; but it does require the existence of an adequate supply at all times. The film pressure is created by the moving surfaces itself pulling the lubricant under pressure, though it maybe. The film pressure is created by the moving surface to creat the pressure necessary to separate the surfaces against the load on the bearing . hydrodynamic lubrication is also called full film ,or fluid lubrication .Hydrostatic lubrication is obtained by introducing the lubricant ,which is sometime air or water ,into the load-bearing area at a pressure high enough to separate the surface with a relatively thick film of lubricant. So ,unlike hydrodynanmic lubrication, motion of one surface relative to another is not required .Elasohydrodynamic lubrication is the phenomenon that occurs when a lubricant is introduced between surfaces which are in rolling contact, such as mating gears or rolling bearings. The mathematical explanation requires the hertzian theory of contact stress and fluid mechanics.When bearing must be operated at exetreme temperatures, a solid film lubricant such as graphite or molybdenum disulfide must be use used because the ordinary mineral oils are not satisfactory. Must research is currently being carried out in an effort, too, to find composite bearing materials with low wear rates as well as small frictional coefficients.In a journal bearing, a shaft rotates or oscillates within the bearing , and the relative motion is sliding . in an antifriction bearing, the main relative motion is rolling . a follower may either roll or slide on the cam. Gear teeth mate with each other by a combination of rolling and sliding . pistions slide within their cylinders. All these applications require lubrication to reduce friction ,wear, and heating.The field of application for journal bearing s is immense. The crankshaft and connecting rod bearings of an automotive engine must poerate for thousands of miles at high temperatures and under varying load conditions . the journal bearings used in the steam turbines of power generating station is said to have reliabilities approaching 100 percent. At the other extreme there are thousands of applications in which the loads are light and the service relatively unimportant. a simple ,easily installed bearing is required ,suing little or no lubrication. In such cases an antifriction bearing might be a poor answer because because of the cost, the close ,the radial space required ,or the increased inertial effects. Recent metallurgy developments in bearing materials , combined with increased knowledge of the lubrication process, now make it possible to design journal bearings with satisfactory lives and very good reliabilities.参考文献:1. Chambers T. L., Parkinson A. R., 1998, “Knowledge Representation and Conversion ofHybridExpert Systems.” Transactions of the ASME, v 120,pp 468-4742. Koelsch, James R., 1999, “Software boosts mold design efficiency“ Molding Systems,v57, n 3,p16-23.3. Lee, Rong-Shean, Chen, Y uh-Min, Lee, Chang-Zou,1997 “Development of a concurrentmolddesign system: A knowledge-based approach”, Computer Integrated Manufacturing Systems, v 10,n 4, p 287-3074. Steadman Sally, Pell Kynric M, 1995, “ Expert systems in engineering design: An applicationforinjection molding of plastic parts“ Journal of Intelligent Manufacturing, v6, p 347-353.5. Fernandez A., Castany J., Serraller F., Javierre C., 1997, “CAD/CAE assistant for the designofmolds and prototypes for in jection of thermoplastics “Information Technological, v 8, p 117-124.6. Douglas M Bryce, 1997, “Plastic injection molding -Material selection and product design”, v 2,pp1-48.7. Douglas M Bryce, 1997, “Plastic injection molding-Mold design fundamentals”, v2, pp 1-120 中文译文:轴承的摩擦与润滑现在看来,有很多这种情况,许多学生在被问到关于摩擦的问题时,往往都没引起足够的重视,甚至是忽视它。
外文翻译----设计基础的基本原理

机械工程学院毕业设计(论文)外文资料翻译教科部:工业设计专业:工业设计姓名:学号:外文出处:Basic design : the cultivation ofwisdom, reason and sensibility 附件:Introduction Philosophy of Basic DesignDesign is a factor to be considered in all endeavors of art. The basic Design course structure is beneficial to every student, irrespective of his or her major. Anyone taking the basic course is treated as a future designer. To achieve this, Basic Design attempts to cultivate within the student:1. The Ability to Discover and Solve ProblemsProjects are developed so one not only finds solutions, but also creates one’s own design problems, and continually re-evaluates one’s progress towa rd achieving a satisfying resolution to the problem. This means that solutions found in earlier assignments can suggest new problems for future assignments.2. The Ability to CompromiseAs one confronts and discovers both the artificial and inherent limitations of a particular assignment, one learns to compromise and alter the original conception of the solution. This mental flexibility allows for continual re- examination and reworking of projects in the attempt to search for more variations as a regular part of all design assignments.3. Increased CreativityEveryone is directed to discard the obvious or traditional in favor of creating one’s own unique solutions. All are encouraged to be different, and to show one’s findings in public. This is the best way to protect original work from being copied or imitated by others. This, along with learning new methods of analyzing design problems, opens the way for increasing creativity. 4. Improved Self-understandingThrough design everyone learns to analyze and im prove one’s own method of problem solving and to find what tends to block one’s creative thinking and to learn ways to overcome such obstacles. Not only dose one discovers one’s design abilities, but also learns how these abilities are able to relate to other art forms.5. CraftsmanshipCareful craftsmanship is required on all projects. Everyone learns patience, precision and the use of basic tools which allows one to create finished works of professional quality.6. RelevanceThis Basic Design course gives an introduction of basic geometry, engineering principles, and their relationship to artistic design. This course helps to develop abilities useful not only by artists or designers such as observation, analysis, innovation, adaptation, planning and creativity.The assignments in this Basic Design course are unique in that each project is built one on each other. This approach allows people to gain new insights by looking at one’s previous work. In addition, this course can direct everyone’s individuality, allowing one’s work to reflect their own personality and cultural background. All aspects of the results obtained will be beneficial.Although this Basic Design course is for teachers and students of design, it can be applied to many other fields as well.This book can be read in any order. However, to take full advantage, it is recommended that all assignments are taken in sequence. It is crucial to use only basic drafting tools to compete each assignment rather than high tech equipment. The assignments in this book are highly adaptable to any future studies by its reader. They are not simply focused on one area of study such as design or art or architecture but are designed to teach principles useful for everyone.This book is divided into two main sections: twenty-six “issues” and twenty-eight assignments, the latter sub-divided into three parts.1) The Introduction includes the philosophy of basic design and twenty-six issues. Each issue reveals the reasons for writing this book and the philosophy of teaching design. Some issues will be illustrated with the author’s own design works.2) Numerous design assignments are included in three parts--each part addresses a problem through a sequence of assignments that may seem, at first, to be unrelated. An illustration appears at the end of each of the parts for review.a. Part one starts with adding a third dimension to a square--challenging 2D and 3D as one. All assignments that follow allow one to go through changes, improving the senses through comparison and the ability to rationally understand the results.b. Part two begins with marking a joint out of two pieces of paper, and follows many related lessons. This leads to the design of a new font based on all 26 letters of the alphabet.c. Part three deals with the visual connection between two letters. Working with geometricprinciples, one learns to simplify the drawing process, and to understand and work with negative spaces. The concepts of mass production and work with 2D and 3D modular systems are introduced.设计基础的基本原理在所有的艺术行业中,设计是一个必须要考虑的因素。
机械工程外文翻译
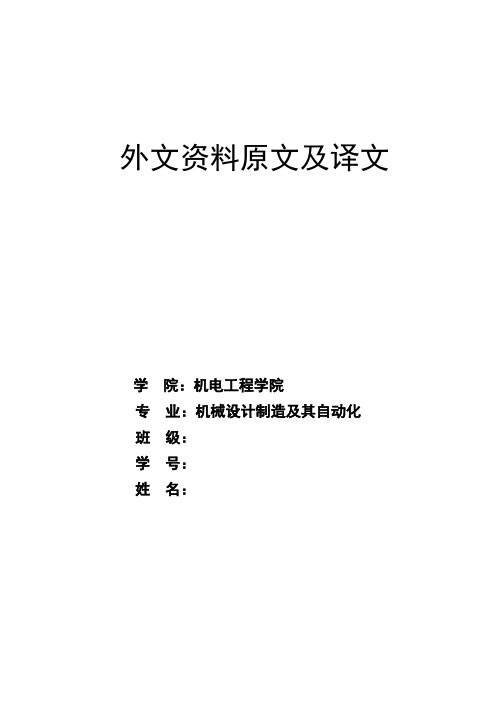
外文资料原文及译文学院:机电工程学院专业:机械设计制造及其自动化班级:学号:姓名:Mechanical engineering1.The porfile of mechanical engineeringEngingeering is a branch of mechanical engineerig,itstudies mechanical and power generation especially power and movement.2.The history of mechanical engineering18th century later periods,the steam engine invention hasprovided a main power fountainhead for the industrialrevolution,enormously impelled each kind of mechznicalbiting.Thus,an important branch of a new Engineering –separated from the civil engineering tools and machines on thebranch-developed together with Birmingham and the establishment of the Associantion of Mechanical Engineers in1847 had been officially recognized.The mechanicalengineering already mainly used in by trial and error methodmechanic application technological development intoprofessional engineer the scientific method of which in theresearch,the design and the realm of production used .From themost broad perspective,the demend continuously to enhance theefficiencey of mechanical engineers improve the quality of work,and asked him to accept the history of the high degreeof education and training.Machine operation to stress not onlyeconomic but also infrastructure costs to an absolute minimun.3.The field of mechanical engineeringThe commodity machinery development in the develop country,in the high level material life very great degree is decided each kind of which can realize in the mechanical engineering.Mechanical engineers unceasingly will invent the machine next life to produce the commodity,unceasingly will develop the accuracy and the complexity more and more high machine tools produces the machine.The main clues of the mechanical development is:In order to enhance the excellent in quality and reasonable in price produce to increase the precision as well as to reduce the production cost.This three requirements promoted the complex control system development.The most successful machine manufacture is its machine and the control system close fusion,whether such control system is essentially mechanical or electronic.The modernized car engin production transmission line(conveyer belt)is a series of complex productions craft mechanization very good example.The people are in the process of development in order to enable further automation of the production machinery ,the use of a computer to store and handle large volumes of data,the data is a multifunctional machine toolsnecessary for the production of spare parts.One of the objectives is to fully automated production workshop,three rotation,but only one officer per day to operate.The development of production for mechanical machinery must have adequate power supply.Steam engine first provided the heat to generate power using practical methods in the old human,wind and hydropower,an increase of engin .New mechanical engineering industry is one of the challenges faced by the initial increase thermal effciency and power,which is as big steam turbine and the development of joint steam boilers basically achieved.20th century,turbine generators to provide impetus has been sustained and rapid growth,while thermal efficiency is steady growth,and large power plants per kW capital consumption is also declining.Finally,mechanical engineers have nuclear energy.This requires the application of nuclear energy particularly high reliability and security, which requires solving many new rge power plants and the nuclear power plant control systems have become highly complex electroonics,fluid,electricity,water and mechanical parts networks All in all areas related to the mechanical engineers.Small internal combustion engine,both to the type (petrol and diesel machines)or rotary-type(gas turbines andMong Kerr machine),as well as their broad application in the field of transport should also due to mechanical enginerrs.Throughout the transport,both in the air and space,or in the terrestrial and marine,mechanial engineers created a variety of equipment and power devices to their increasing cooperation with electrical engineers,especially in the development of appropration control systems.Mechanical engineers in the development of military weapons technology and civil war ,needs a similar,though its purpose is to enhance rather than destroy their productivity.However.War needs a lot of resources to make the area of techonlogy,many have a far-reaching development in peacetime efficiency.Jet aircraft and nuclear reactors are well known examples.The Biological engineering,mechanical engineering biotechnology is a relatively new and different areas,it provides for the replacement of the machine or increase the body functions as well as for medical equipment.Artficial limbs have been developed and have such a strong movement and touch response function of the human body.In the development of artificial organ transplant is rapid,complex cardiac machines and similar equipment to enable increasingly complex surgery,and injuries and ill patients life functions can besustained.Some enviromental control mechanical engineers through the initial efforts to drainage or irrigation pumping to the land and to mine and ventilation to control the human environment.Modern refrigeration and air-conditioning plant commonaly used reverse heat engine,where the heat from the engine from cold places to more external heat.Many mechanical engineering products,as well as other leading technology development city have side effects on the environment,producing noise,water and air pollution caused,destroyed land and landscape.Improve productivity and diver too fast in the commodity,that the renewable natural forces keep pace.For mechanical engineers and others,environmental control is rapidly developing area,which includes a possible development and production of small quantities of pollutants machine sequnce,and the development of new equipment and teachnology has been to reduce and eliminate pollution.4.The role of mechanical engineeringThere are four generic mechanical engineers in common to the above all domains function.The 1st function is the understanding and the research mechanical science foundation.It includes the power and movement of therelationship dynamics For example,in the vibration and movement of the relationship;Automatic control;Study of the various forms of heart,energy,power relations between the thermodynamic;Fluidflows; Heat transfer; Lubricant;And material properties.The 2nd function will be conducts the research,the desing and the development,this function in turn attempts to carry on the essential change to satisfy current and the future needs.This not only calls for a clear understanding of mechanical science,and have to break down into basic elements of a complex system capacity.But also the need for synthetic and innovative inventions.The 3rd function is produces the product and the power,include plan,operation and maintenance.Its goal lies in the maintenance either enhances the enterprise or the organization longer-tern and survivabilaty prestige at the same time,produces the greatest value by the least investments and the consumption.The 4th function is mechanical engineer’s coordinated function,including the management,the consultation,as well as carries on the market marking in certain situation.In all these function,one kind unceasingly to use the science for a long time the method,but is not traditional orthe intuition method tendency,this is a mechanical engineering skill aspect which unceasingly grows.These new rationalization means typical names include:The operations research,the engineering economics,the logical law problem analysis(is called PABLA) However,creativity is not rationalization.As in other areas,in mechanical engineering, to take unexpected and important way to bring about a new capacity,still has a personal,marked characteristice.5.The design of mechanical engineeringThe design of mechanical is the design has the mechanical property the thing or the system,such as:the instrument and the measuring appliance in very many situations,the machine design must use the knowledge of discipline the and so on mathematics,materials science and mechanics.Mechanical engineering desgin includeing all mechanical desgin,but it was a study,because it also includes all the branches of mechsnical engineering,such as thermodynamics all hydrodynamics in the basic disciplines needed,in the mechanical engineering design of the initial stude or mechanical design.Design stages.The entire desgin process from start to finish,in the process,a demand that is designed for it and decided to do the start.After a lot of repetition,thefinal meet this demand by the end of the design procees and the plan.Design considerations.Sometimes in a system is to decide which parts needs intensity parts of geometric shapes and size an important factor in this context that we must consider that the intensity is an important factor in the design.When we use expression design considerations,we design parts that may affect the entire system design features.In the circumstances specified in the design,usually for a series of such functions must be taken into account.Howeever,to correct purposes,we should recognize that,in many cases the design of important design considerations are not calculated or test can determine the components or systems.Especially students,wheen in need to make important decisions in the design and conduct of any operation that can not be the case,they are often confused.These are not special,they occur every day,imagine,for example,a medical laboratory in the mechanical design,from marketing perspective,people have high expectations from the strength and relevance of impression.Thick,and heavy parts installed together:to produce a solid impression machines.And sometimes machinery and spare parts from the design style is the point and not the other point of view.Our purpose is to make those you do notbe misled to believe that every design decision will need reasonable mathematical methods.Manufacturing refers to the raw meterials into finished products in the enterprise.Create three distinct phases.They are:input,processing exprot.The first phase includes the production of all products in line with market needs essential.First there must be the demand for the product,the necessary materials,while also needs such as energy,time,human knowledge and technology resourcess . Finall,the need for funds to obtain all the other resources. Lose one stage after the second phase of the resources of the processes to be distributed.Processing of raw materials into finished products of these processes.To complete the design,based on the design,and then develop plans.Plan implemented through various production processes.Management of resources and processes to ensure efficiency and productivity.For example,we must carefully manage resources to ensure proper use of funds.Finally,people are talking about the product market was cast.Stage is the final stage of exporting finished or stage.Once finished just purchased,it must be delivered to the users.According to product performance,installation and may have to conduct furtherdebugging in addition,some products,especially those very complex products User training is necessary.6.The processes of materials and maunfacturingHere said engineering materials into two main categories:metals and non-ferrous,high-performance alloys and power metals.Non-metallic futher divided into plastice,synthetic rubber,composite materials and ceramics.It said the production proccess is divided into several major process,includingshape,forging,casting/ founding,heat treatment,fixed/connections ,measurement/ quality control and materal cutting.These processes can be further divide into each other’s craft.Various stages of the development of the manufacturing industry Over the years,the manufacturing process has four distinct stages of development, despite the overlap.These stages are:The first phase is artisanal,the second Phase is mechanization.The third phase is automation the forth Phase is integrated.When mankind initial processing of raw materials into finished products will be,they use manual processes.Each with their hands and what are the tools manuslly produced.This is totally integrated production take shape.A person needs indentification,collection materials,the design of a productto meet that demand,the production of such products and use it.From beginning to end,everything is focused on doing the work of the human ter in the industrial revolution introduced mechanized production process,people began to use machines to complete the work accomplished previously manual. This led to the specialization.Specialization in turn reduce the manufacture of integrated factors.In this stage of development,manufacturing workers can see their production as a whole represent a specific piece of the part of the production process.One can not say that their work is how to cope with the entire production process,or how they were loaded onto a production of parts finished.Development of manufacting processes is the next phase of the selection process automation.This is a computer-controlled machinery and processes.At this stage,automation island began to emerge in the workshop lane.Each island represents a clear production process or a group of processes.Although these automated isolated island within the island did raise the productivity of indivdual processes,but the overall productivity are often not change.This is because the island is not caught in other automated production process middle,but not synchronous with them .The ultimate result is the efficient working fast parkedthrough automated processes,but is part of the stagnation in wages down,causing bottlenecks.To better understand this problem,you can imagine the traffic in the peak driving a red light from the red Service Department to the next scene. Occasionally you will find a lot less cars,more than being slow-moving vehicles,but the results can be found by the next red light Brance.In short you real effect was to accelerate the speed of a red Department obstruction offset.If you and other drivers can change your speed and red light simultaneously.Will advance faster.Then,all cars will be consistent,sommth operation,the final everyone forward faster.In the workshop where the demand for stable synchronization of streamlined production,and promoted integration of manufacturing development.This is a still evolving technology.Fully integrated in the circumstances,is a computer-controllrd machinery and processing.integrated is completed through computer.For example in the preceding paragraph simulation problems,the computer will allow all road vehicles compatible with the change in red.So that everyone can steady traffic.Scientific analysis of movement,timing and mechanics of the disciplines is that it is composed of two pater:staticsand dynamics.Statics analyzed static system that is in the system,the time is not taken into account,research and analysis over time and dynamics of the system change.Dynameics from the two componets.Euler in 1775 will be the first time two different branches: Rigid body movement studies can conveniently divided into two parts:geometric and mechanics.The first part is without taking into account the reasons for the downward movement study rigid body from a designated location to another point of the movement,and must use the formula to reflect the actual,the formula would determine the rigid body every point position. Therefore,this study only on the geometry and,more specifically,on the entities from excision.Obviously,the first part of the school and was part of a mechanical separation from the principles of dynamics to study movement,which is more than the two parts together into a lot easier.Dynamics of the two parts are subsequently divided into two separate disciplines,kinematic and dynamics,a study of movement and the movement strength.Therefore,the primary issue is the design of mechanical systems understand its kinematic.Kinematic studies movement,rather than a study of its impact.In a more precise kinematic studies position,displacement,rotation,speed,velocity and acceleration of disciplines,for esample,or planets orbiting research campaing is a paradigm.In the above quotation content should be pay attention that the content of the Euler dynamics into kinematic and rigid body dynamics is based on the assumption that they are based on research.In this very important basis to allow for the treatment of two separate disciplines.For soft body,soft body shape and even their own soft objects in the campaign depends on the role of power in their possession.In such cases,should also study the power and movement,and therefore to a large extent the analysis of the increased complexity.Fortunately, despite the real machine parts may be involved are more or less the design of machines,usually with heavy material designed to bend down to the lowest parts.Therefore,when the kinematic analysis of the performance of machines,it is often assumed that bend is negligible,spare parts are hard,but when the load is known,in the end analysis engine,re-engineering parts to confirm this assnmption.机械工程1.机械工程简介机械工程是工程学的一个分支,它研究机械和动力的产,尤其是力和动力。
- 1、下载文档前请自行甄别文档内容的完整性,平台不提供额外的编辑、内容补充、找答案等附加服务。
- 2、"仅部分预览"的文档,不可在线预览部分如存在完整性等问题,可反馈申请退款(可完整预览的文档不适用该条件!)。
- 3、如文档侵犯您的权益,请联系客服反馈,我们会尽快为您处理(人工客服工作时间:9:00-18:30)。
中文翻译2.3切削热模型如果公式(2.12)中所有的主剪切所做的功都转化为热量,并且这些热量全部传入切屑,这会使切屑的温度平均上升1T ∆()1cos sin cos k k T C Cαγρφφαρ∆=≡- (2.14) 上式中,C ρ是切屑材料的热容。
表2.2给出了()/k C ρ的一些常见值。
假设机械加工中会产生数量级大于2的剪切应力(第2.2章节),很明确在切屑中或许存在着显著的温度上升。
这是在没有考虑刀具与切屑之间因摩擦而产生的额外那部分热量的情况下判断的。
计算出有多少热量传递到切屑中是十分重要的,还有研究切屑与刀具摩擦所产生的额外的温度上升也是十分重要的。
1aT ∆是在 2.5γ≈和0.85β≈时取得的;b 测量时,刀具的等级要和工件材料相适合。
这一章节的主要内容是通过简单的分析和观察来确定影响温度上升的参数以及它们近似的影响。
如果这些参数也可以被精确的求出,那么研究结果会给包括建立更加复杂的数字模型(在接下来的章节中介绍)在内的研究工作提供基础。
因此,从切屑形成的简单示意图可以观察到,第一、第二剪切区域是平面的,图2.17(a)中OA 和OB 所表示的平面。
章节2.3.1主要介绍的是热对流的传递阻止了热量沿OA 传入工件(图2.17(b))。
而章节2.3.2则侧重于介绍摩擦热是如何沿OB 在刀屑间传递的(图2.17(c)),还有刀屑摩擦带来的温升是怎样的。
附录2给出了研究这个部分所必需的热量传递理论。
图2.17为了计算温度,将 (a)工件、切屑和刀具分解成(b)工件和(c)切屑与刀具的区域2.3.1主剪切所产生的热量主剪切所产生的那部分热量,用β表示,这个章节中主要计算的是传入工件材料的那部分热量。
当这一部分计算出来后,剩余的进入切屑的那一部分热量()1β-也可以计算出来。
这一部分决定了切屑的温度上升。
图2.17(b)中,选择了工件上一部分有限体积'AA 。
如图,工件携带着这一部分体积以速度z u ∙和x u ∙朝向并通过了剪切平面。
其中sin z u U φ∙=工件,cos z u U φ∙=工件。
当这部分体积第一次到达剪切平面时(如图所示),它就开始被加热了。
如图,当这部分体积达到切削刃(O 点)时,沿着z 的方向就可以建立温度分布。
通过对流的方式,散出的热量传入工件的比率(每单位切削深度)就是所产生的温升量,工件材料的热容,速度x u ∙的乘积沿着z 方向的积分:00=()d z Q u T T C z ρ∞∙-⎰转化进入工件 (2.15a )温度分布()0T T -在附录2.3.1给出:一旦温度沿着z 方向达到了一个稳定的值,就可以得到下面的等式/112=d z u z x x zzu u q Q q e z u u κκ∙∙∙∞-∙∙≡⎰转化进入工件 (2.15b )式中,1q 是每单元区域剪切平面工作率,κ是工件材料的热扩散率。
在整个剪切平面上每单位切削深度的发热率是与1q 和剪切面长度有关,即()1/sin q f φ。
传入工件的那部分热量β是公式(2.15b )和这个部分的比。
由于考虑到公式(2.15b )是在热量最大限度传入工件的情况下得出的(温度分布的稳定值或许还没有达到),用U 工件代替x u ∙和z u ∙的值,得到下面的式子tan U f κβφ≤工件 (2.16)根据公式(2.16),传入工件的热量由tan /U f φκ⎡⎤⎣⎦工件这个热常数决定。
这个常数与热量传递理论(附录A2.3.2)中的佩克莱常数的形式类似。
这个常数越大,散出的热量越少,传入切屑的热量越多。
无论再怎么详细,也依然是近似值,Weiner (1955)已经做了一定的分析。
公式(2.16)的结果与他的结果相一致,提出主剪切的佩克莱常数大于5。
对于较小的值,公式(2.16)如果依然使用,就变得差别很大。
图2.18(a )将Weiner 的结果和Tay 所收集、Oxley 所发表(1989)的验证公式(2.16)所做的实验和数字模型的预测相比。
Weiner 的结果与所观察到的结果大致相同。
β只随着tan /U f φκ⎡⎤⎣⎦工件发生微小的变化:变化范围为两个数量级,从0.1到10,这使得β从0.9变为0.1。
很明显,当tan /U f φκ⎡⎤⎣⎦工件增长高于10时,β趋于极限,在0.1到0.2之间。
这个结果源于真实剪切平面的有限宽度。
如果tan /10U f φκ⎡⎤>⎣⎦工件,那么图 2.18(a)所表示的含义是主剪切生热的数字模型只需要包括剪切区域的有限厚度,并且只有传入工件内的那部分热量()1β-需要比先前多加10%。
图2.18(a)基于tan /U f φκ⎡⎤⎣⎦工件理论与预测β的曲线;(b)在(U 工件,f )平面中绘制的β曲线(0.150.3β=和),23,1250/m m sκ=和,25φ=︒图2.18(b)表示的是图2.18(a)中所观察到结果的平均值,此时25φ︒=,将他们代入U 工件和f 的关系中,这使得0.150.3β=和,分别取2=3,1250/mm s κ和。
κ的这些取值分别代表了耐热合金(不锈钢,镍和钛合金),碳素钢和低合金钢以及铜铝合金。
切削速度和进给量联合作用与在经济生产(第1章)中使用车削和铣削中的切削速度或进给量的变化一致。
在车削和铣削加工中,0.15β≈是一个合理的近似值(实际中各种切削条件变化将在第3章详细讨论)。
主剪切产生的(1)β-那部分热量,或站到0.85,通常会进入切屑中。
表2.2中的1T ∆给出了当250.85φβ︒≈=和时的主要区域的温度上升值。
对于碳钢和低合金钢,铜合金和镍铬合金来说,这些温升小于金属熔融温度(K )的一半:塑性流动保持在冷加工的范围内。
然而,对于铝合金和钛合金来说温度可以上升到高于金属熔融温度的一半:温度上升可以导致显微结构的变化。
假设主剪切作用在工件上,这些看似简单的考虑在加工铝合金和钛合金时甚至会引起工件的烧伤,即便是使用尖锐锋利的刀具也无法避免。
表2.2中所推推荐的主剪切温升值对于钛合金高达680C ︒是从切削刀具切削刃的角度测量的。
接下来会考虑由于摩擦而引起的切屑和刀具更深层次的切削热。
2.3.2由摩擦所产生的切削热切屑与刀具之间摩擦应力τ已经在第2.2.5章节中讲过了。
它给出了一个切屑/刀具接触的每单元区域的摩擦生热率,即f q U τ=切屑。
其中,一部分摩擦*α会流向切屑,其余的一部分()*1α-则会流向刀具。
第一个问题考虑了切屑的热量,那么*α的值是多大呢?通过了解切屑与刀具接触区域可以得到答案。
无论从刀具的角度或是切屑的角度计算这个温度,都应该是一样的。
通过实际计算,得到一个结论,那就是在接触区域,*α的值随着位置不同而不同。
f q 也是如此。
论证这个问题已经超出了这一部分所介绍的范围。
在这一部分,为了确定这个十分重要的控制*α的平均值的特性和计算接触区域的平均温度,已经做了一些近似的分析。
在整个接触区域中,f q 和*α的值是保持不变的,并且无论从切屑或是刀具的角度计算,*α的值像平均温度一样是相同的。
图2.17(c)表示出在切屑和刀具之间接触长度为l 的长度之间,f q 和*α是恒定不变的。
接触区域有着和接触区域轮廓垂直的深度d (即切削深度)。
只要考虑刀具的情况,热量会通过一个在刀具表面的长为l ,宽为d 的矩形区域传递到刀具中去。
附录A2.2.5考虑的是半无限固体表面矩形热源的平均温度上升。
就机械加工中刀尖来说,这种情况可以认为是半无限固体的扇形区域,附录2中的公式(A2.14)可以用于此处()()*01=s fU lT T K ατ--切屑平均平均刀具接触刀具(2.17)式中,0T 是周围环境的温度,K 是导热率,f s 是接触区域的长宽比的形状影响因素的(/d l ):例如,随着/d l 从1增大到5,这个值就会从0.94增大到1.82。
只要考虑切削的情况,它以速度U 切屑移动通过热源。
它的温度上升规律符合移动热源理论。
在附录A2.3中有所总结。
当佩克莱常数()/4U l κ切屑大于1时,与切屑的厚度相比,热量只传导一个很小的距离,此时,切屑的一个单元通过热源。
在这种情况下,附录2的公式(A2.17b )给出了由于摩擦生热引起的温度上升的平均值。
这之前,切屑已经被主剪切加热得比周围温度高。
()()()1*20=10.75U l k T T C K U l κατγβρ⎛⎫--+ ⎪⎝⎭切屑工件平均平均切屑接触切屑工件工件(2.18) 从公式(2.17)到(2.18),经过轻微的重新排列,可以得到一个关于*α的式子:()()()()12*0.751f f C K U l s s U l k U l K k K ρκτταβγκγ⎡⎤⎛⎫⎢⎥+=-- ⎪⎢⎥⎝⎭⎣⎦工件工件工件平均切屑平均切屑切屑刀具刀具工件 (2.19) 联合公式(2.2),(2.3),(2.6)和(2.13),如前所示,在φ,λ,α和()/m n 的作用线,τ平均与k 相关,l 与f 相关,U 切屑与U 工件相关。
γ也在φ和α的作用之下。
在去除了τ平均,l 和U 切屑,代之以k ,f 和U 工件,公式(2.19)可化为()()1122*cos cos tan 0.751sin tan f K n s K m U f κλφαφαφλαφ⎡⎤⎛⎫⎛⎫-⎢⎥+ ⎪ ⎪ ⎪ ⎪⎢⎥+-⎝⎭⎝⎭⎣⎦工件刀具工件工件 ()()1cos cos 1sin cos tan /f K K s U f βαφλαλφφκ⎛⎫-+-=- ⎪ ⎪⎡⎤⎝⎭⎣⎦刀具工件工件工件 (2.20a ) 这种做法已经介绍了热常数tan /U f φκ⎡⎤⎣⎦工件。
β也随着这个变化(图 2.18(a))。
如果将图2.10,2.14和2.15中φ,λ,α和()/m n 的典型范围代入公式(2.20a ),可得到近似的关系()12*0.450.151tan f K s K U f καφ⎡⎤⎛⎫⎛⎫±⎢⎥+ ⎪⎪ ⎪⎪⎢⎥⎝⎭⎝⎭⎣⎦工件刀具工件工件()()1.350.511tan /fK s K U f βφκ⎛⎫±-≈-⎪ ⎪⎡⎤⎝⎭⎣⎦刀具工件工件工件 (2.20b ) 图2.19(a)表示对*α值的预测源于图2.18(a)中对β值得观察,并且平均值系数0.45和1.35也代入了公式(2.20b )。
这个公式深受tan /U f φκ⎡⎤⎣⎦工件的影响,并且传导率*/K K K =刀具工件也可以看出,还收这形状因素f s 小且重要的影响。
预测值只表明t a n /0.5U f φκ⎡⎤>⎣⎦工件:在较低值时,()1/4U κ切屑也大于1,此时公式(2.18)是无效的;但是无论用什么方式变小也是无效的。