试议配合件的数控加工(doc 10页)
数控技术《配合件的加工工艺》

第三页,共七页。
配合件的加工工艺
立式铣刀虽然底部圆角可以做的很小,但是不削型腔类工件的时候就会在 工件的内腔的底部留下一个圆角,如上图的放大图。 而对于外轮廓的加工那么可以把边缘加工成完整的90° 尖角,这样,内外轮廓的配合时就会由于圆角的原因 而产生配合的不紧密。
钻孔循环与攻丝循环
配合件的加工工艺
第一页,共七页。
配合件的加工工艺
内角与外角配合的配做
图1 图2
图1中内角的半径大于外角的半径,配合时发生了干 预,导致配合不上。
图2中内角的半径小于外圆的半径,配合正常 。
第二页,共七页。
配合件的加工工艺
加工路线确实定
对于本任务来说,件一和件二的外形尺寸是完全相同的,而且铣六面 是数控铣床加工中难度最高、最费时的工序,所以完全可以对此轮廓 合并加工。在加工时把两件毛坯一起装夹的台虎钳上一起来铣削。
第四页,共七页。
配合件的加工工艺
为了解决上述的问题,一般在加工配合件的外轮廓时都 要在外轮廓的边缘进行倒角〔即使图纸没有标注〕以抵 消内腔的底面圆角。外轮廓倒角的尺寸应大于内腔的底 面圆角,这样就不会阻碍配合的紧密性。
第五页,共七页。
谢谢观看
第六页,共七页。
内容总结
配合件的加工工艺。对于本任务来说,件一和件二的外形尺寸是完全相同的,而且铣六面是数 控铣床加工中难度最高、最费时的工序,所以完全可以对此轮廓合并加工。立式铣刀虽然底部圆角 可以做的很小,但是不代表没有底部圆角,一般为了提高刀具刀尖的强度都会做一个圆角,左右, 这样在铣削型腔类工件的时候就会在工件的内腔的底部留下一个圆角,如上图的放大图。外轮廓倒 角的尺寸应大于内腔的底面圆角,这样就不会阻碍配合的紧密性。谢谢观看
浅谈数控车床配合件的加工工艺

浅谈数控车床配合件的加工工艺1)夹具应与加工工件的形状相适应,能够稳定夹紧工件;2)夹具应有足够的刚度,能够承受加工过程中的切削力;3)夹具应有可靠的定位基准,能够确保加工工件的精度;3、刀具的选择刀具的选择应根据加工工件的材料、形状、尺寸和加工方式等因素综合考虑。
在本文所述的工件加工中,可以选择以下刀具:1)加工圆柱面和抛物线时,选择直径为16mm的刀具;2)加工螺纹时,选择丝锥刀;3)加工沟槽时,选择宽度为3mm的刀具;4、切削用量的确定切削用量的确定应根据刀具的材料、形状、尺寸和加工工件的材料、硬度等因素综合考虑。
在本文所述的工件加工中,可以选择以下切削用量:1)加工圆柱面和抛物线时,每次切削深度为0.1mm;2)加工螺纹时,每次切削深度为0.2mm;3)加工沟槽时,每次切削深度为0.1mm;5、加工工艺卡的填写工件名称:数控车床配合件加工工艺路线:车削、铣削、钻孔、螺纹加工、倒角加工顺序:夹紧工件的毛坯伸出卡盘65cm,先粗后精加工抛物线和圆柱面,掉头装夹加工另一端,加工外沟槽,粗精车件二的内孔,加工内螺纹,件一和件二配合加工件二的圆柱面和椭圆,倒角c1,回换刀点程序结束。
刀具选择:直径为16mm的刀具、丝锥刀、宽度为3mm 的刀具、球头铣刀和钻头。
切削用量:每次切削深度为0.1mm或0.2mm。
6、数控加工程序的编写O0001(加工工件一)N10 G90 G54 G17 G40 G49 G80 N20 T01 M06N30 G43 H01 Z50. S500 M03N40 G00 X-25. Z5.N50 G01 Z-10. F0.15N60 G02 X25. Z-50. I25. J0. K0. N70 G01 Z-60.N80 G00 X-25. Z-60.N90 G28 U0 W0O0002(加工工件二)N10 G90 G54 G17 G40 G49 G80 N20 T02 M06N30 G43 H02 Z20. S500 M03N40 G00 X-25. Z5.N50 G01 Z-10. F0.15N60 G02 X25. Z-20. I25. J0. K0.N70 G01 Z-30.N80 G00 X-25. Z-30.N90 G28 U0 W0通过以上工艺分析和数控加工程序的编写,可以实现数控车床配合件的高效、精确加工。
数控车削编程配合零件加工

材料为45钢。
项 目 七 配 合 件 的 加 工
图7.1 配合件零件图
相关知识
配合件加工的要求
项 目 七
〔一〕配合件加工的根本要求 配合件的尺寸要求:属于间隙配合的配合件中孔类工件一般采用上偏差,
相关知识
项
3.切削用量 在零件精加工时切削用量的选择是否合理直接影响外表加工质量,
目 七
如果精加工余量已经很小,当精车达不到粗糙度要求时,再采取技术措施精车 一次就有尺寸超差的危险。因此加工时要注意以下几点:
〔1〕精车时选择较高的主轴转速和较小的进给量,以提高外表粗糙度。
配 合 件 的 加 工
〔2〕对于硬质合金车刀,要根据刀具几何角度,合理留出精加工余量。例如, 正常角的刀具加工时,精加工余量要小;负前角的刀具加工时,精加工余量要 适当大一些。又如刀尖圆角半径对外表粗糙度的影响较大,精加工时应该有较 小的刀尖圆角半径和较小的进给量,建议精加工时刀尖圆角半径, 进给量。
X27
R110=2 R111=0.15
Z-35
R112=0.08
X25
LCYC95
G00Z200
G0 Z200
X150
X150
M03S800
M3S800
G0X20Z3
R105=7 R106=0
G70P25Q40
LCYC95
G01X25
G0 Z200
G0Z200
X150
T4D0
项
目
M5
七
M30
L002.SPF
N075
配合件的数控加工

配合件的数控加工作者:惠骁晨来源:《现代职业教育·中职中专》2017年第07期[摘要] 改革开放以来,我国机械制造行业已经迅猛发展,尤其是数控加工方面的应用尤为发展迅速,机加工企业对数控加工技术的要求也更高了。
以数控车工配合件加工为例,从加工工艺分析、设备的选择、刀具选择、配合精度要求、切削用量的选择、夹具的选择,都经过了详细考量。
最终确定合理工艺方案,保证工艺设计要求及工件的加工精度要求,以达到各项加工要求,最终完成零件的加工。
[关键词] 数控车工;加工工艺分析;加工方法[中图分类号] G712 [文献标志码] A [文章编号] 2096-0603(2017)20-0150-01一、加工件技术的分析我们都知道,机械中的最小单位是零件,而机构是由零件配合组成的,机械是机构之间的配合组成的,一台机器要能够正常运作,发挥其相应作用,那么是否能够达到零件与零件之间的配合要求是保证其正常运作的关键。
随着我国机电一体化、机械制造技术的迅猛发展,数控机床在机加工企业里已相当普及了。
加之对配合的零件之间的要求,零件的位置精度、表面粗糙度等要求不断提高,普通机床很难达到,那么就需要在数控机床完成。
车削配合件的关键是加工工艺方案的制定、基准零件的选择及切削过程中的配车和配研。
合理制定配合件的加工顺序和加工工艺,能保证配合件的加工精度和装配精度,而各零件的加工精度直接影响配合件的装配精度,其中基准零件加工精度对配合精度的影响尤为突出。
因此,在制定配合件的加工工艺方案和组合加工时,要注意以下几点:(一)根据配合件的装配关系,确定基准零件。
(二)加工时,应先车削基准零件,然后根据装配关系,依次车削配合件中的其余零件。
(三)车削基准零件时的注意事项:1.要重点控制配合部分的尺寸精度。
2.车削有圆球配合时,车刀刀尖与球心轴线等高,避免产生两零件圆弧面的贴合度达不到配合要求。
3.螺纹应车制成型,不允许使用板牙、丝锥加工。
机械零件数控加工.doc

金华职业技术学院机械零件加工(铣)实训指导书章跃洪编写二OO九年九月课题一数控铣床基本操作一.面板操作1.如何开机?机床开关,CNC开关,急停开关。
(关机相反)2.如何加油?3.如何回零?通常先回Z再回X、Y。
4.手轮如何使用?(注意进给方向与手轮倍率)5.手动方式下如何改变刀具移动速度?进给倍率↑、进给倍率↓(10%、20%……150%)快速倍率:F0、25%、50%、100%(初学置于25%)6.开机后如何设置一个主轴转速?MDI(录入)→程序→S××输入→循环启动7.手动方式下如何改变主轴转速?8.录入方式下如何操作?MDI(录入)→程序→指令输入→循环启动9.编辑方式下如何建立一个新程序?或打开一个已有程序?删除一个已有程序?建立:O××××,插入(或EOB)。
打开:O××××,下光标。
删除:O××××,删除。
10.如何输入、修改、删除程序字?11.如何检索程序或字?先输入要检索的程序或字,按下光标。
(上光标)12.通过哪些方式可以进行调试程序?13.自动方式下如何启动、暂停、中止加工程序?14.自动方式下如何对进给速度、快速速度及主轴转速进行调整?15.遇到撞刀等紧急情况,如何处理?按急停练习程序:(也可以自编)O0001;N10G90G40G69G15 N20G91G28G00Z00;N30 M03 S500;N40G90X20Y20.;N50G43Z5H1;N60G01Z-5F100N70X-20N80Y-20;N90X20.;N100Y20;N100G91G28G00Z00N110M05;N120M30;位置程序刀具偏置换档取消输入系统信息图形修改插入删除上页下页帮助复位图所示长方体工件,编程坐标(工件坐标)原点在长方体的顶面中心位置,长度方向为X方向,宽度方向为Y方向,高度方向为Z方向。
试议配合件的数控加工(

配合件的数控加工摘要:随着数控加工技术的发展, 大量高精度多坐标数控机床的出现,机械加工已越来越倾向使用数控加工。
数控加工主要有以下两个优点:精度高,可以加工任何复杂的自由曲面且精度很高,可以满足结构复杂、高精度的需要。
操作简单,传统加工方法对工艺及操作人员的技术要求很高,稍有不慎就有可能导致零件报废。
现代数控加工技术只需机床操作人员在加工前输入相应的数控程序,机床就会严格按照数控程序进行加工。
可以预测,在未来几年内机械加工部分将继续以数控加工为主。
本文以配合件加工为例,从数控加工工艺分析,设备的选择,配合精度,刀具、夹具的选择,切削用量的选择,都经过了慎重考虑。
配合件种类繁多,范围太广,所以以车削,铣削为主,以轴承套、箱体为例,分析零件气概经过数控加工,确定合理工艺技术方案,保证工件的精度和工艺设计要求,以达到配合要求,最终完成的零件的加工。
关键词:工艺分析;加工方法;数控加工零件是机械中的最小单位,零件的配合组成了机构,机构之间的配合组成了机械,一部机器要能正常工作,发挥应有的作用,那么零件与零件之间的配合是保证的关键。
如今,随着机电一体化技术的迅速发展,数控机床已经日走趋普及。
加之对配合的零件之间的要求,零件表面的粗糙度,位置度等要求不断提高,普通机床很难达到,那么就需要在数控机床完成。
下面以数控车削加工的典型零件-盘套类零件,铣削为主的箱体类零件为例讨论配合件的加工。
(一)数控车削的典型零件-盘套类配合件的加工盘套类零件在机器设备中用得非常普遍,多与同属回转体零件的轴类零件配合,由于其功能不同,盘套类零件结构和尺寸有着很大的差别,但其结构仍有共同点,零件的主要表面为同轴度要求较高的内外圆表面,零件壁的厚度较薄且易变形,盘套类零件的结构一般由孔,外圆,端面,沟槽及内螺纹和外螺纹,内锥面和内型面组成。
常见的有轴承套,衬套,齿轮,带轮,轴承端盖等。
盘套类零件表面精度要求除尺寸外、形状精度外,内孔一般要作为配合和装配的基准,孔的直径尺寸等级一般为IT7,精密轴套可以取IT6,孔的形状精度应控制在孔径公差内,,一些精密套筒控制在孔径的公差的二分之一到三分之一,对于长度较长的轴套零件,除了圆度要求以外,还应注内孔面的圆柱度,端面对内孔轴线的圆跳动度和垂直度,以及两端面的的平行度等要求,为了保证零件的功用和提高其耐磨性,孔的表面粗糙度值Ra1.6-0.16um,甚至更高。
配合零件的数控加工

配合零件的数控加工摘要:目前采用数控加工是解决该类零件圆弧曲面、锥面和高精要求圆柱面最有效的加工方法。
数控加工的工序内容比普通机床的加工的工序内容复杂。
这是因为数控机床价格昂贵,若只加工简单的工序,在经济上不合算,所以在数控机床上通常安排较复杂的工序,甚至是在通用机床上难以完成的那些工序。
数控机床加工程序的编制比普通机床工艺规程编制复杂。
这是因为在普通机床的加工工艺中不必考虑的问题,如工序内工步的安排、对刀点、换刀点及走刀路线的确定等问题,在数控加工时,这一切都无例外地都变成了固定的程序内容,正由于这个特点,促使对加工程序的正确性和合理性要求极高,不能有丝毫的差错,否则加工不出合格的零件。
配合零件的数控加工中涉及到零件图样工艺分析、加工方法和加工顺序的确定、装夹方案和夹具的选择、选择刀具及确定切削用量等关键技术。
通过对这些技术的链接和研究,完成了配合零件的数控加工。
关键词:配合零件;数控加工工艺;数控编程前言数控技术是数字控制(Numerical Control)技术的简称。
它采用数字化信号对被控制设备进行控制,使其产生各种规定的运动和动作。
利用数控技术可以把生产过程用某中语言编写的程序来描述,将程序以数字形式送入计算机或专用的数字计算装置进行处理输出,并控制生产过程中相应的执行程序,从而使生产过程能在无人干预的情况下自动进行,实现生产过程的自动化。
采用数控技术的控制系统称为数控系统(Numerical Control System)。
根据被控对象的不同,存在多种数控系统,其中产生最早应用最广泛的是机械加工行业中的各种机床数控系统。
所谓机床数控系统就是以加工机床为控制对象的数字控制系统。
CAD/CAM技术是现代制造技术领域中的重要组成部分。
经历半个多世纪的发展,至今已形成了比较完整的科学技术体系,并在高新技术领域占有很重要的位置。
随着CAD技术的发展,CAD/CAM一体化成为可能。
从20世纪90年代起,CAD/CAM技术向标准化、智能化的方向发展。
配合件的数控车加工实施课程标准
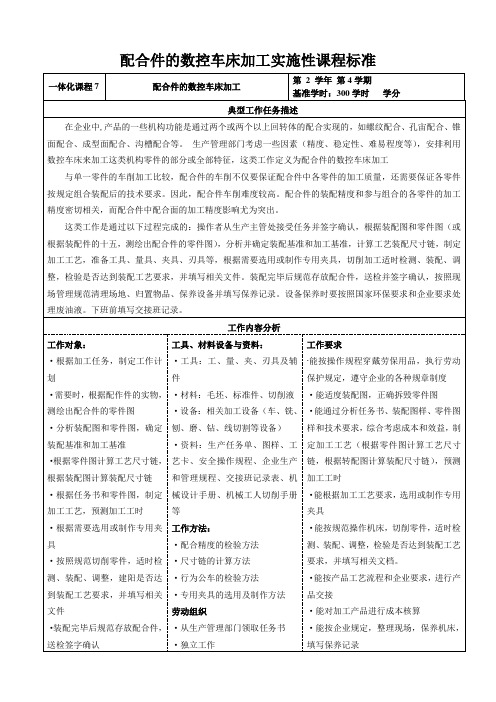
一体化课程名称
零件的数控车床加工
学习任务3名称
螺纹锥度配合三件套
学习任务3学时
40
学习任务情境
某企业定制的一批零件,数量为30件,生产主管部门将生产任务交予我车间,交货期5天,来料加工,现车间安排我们数控车工组完成此加工任务。
学习目标
1按照数控车间安全防护规定,穿戴劳保用品,执行安全操作规程、
工作内容分析
工作对象:
·根据加工任务,制定工作计划
·需要时,根据配作件的实物,测绘出配合件的零件图
·分析装配图和零件图,确定装配基准和加工基准
·根据零件图计算工艺尺寸链,根据装配图计算装配尺寸链
·根据任务书和零件图,制定加工工艺,预测加工工时
·根据需要选用或制作专用夹具
·按照规范切削零件,适时检测、装配、调整,建阳是否达到装配工艺要求,并填写相关文件
3、根据加工螺纹轴要求,列出所需的加工准备清单。
4、根据本任务查阅国家标准相关资料,计算螺纹轴有关尺寸,制定数控加工工艺,填写工艺卡片。
5、能根据加工工艺,完成数控车程序编制。
6、能根据模拟加工的路径,进行数控车程序优化。
7、能独立完成螺纹轴的数控车加工任务。
8、能对螺纹轴进行正确的测量,评估与判断零件质量是否合格,并提出观赏性改进措施。
·能按产品工艺流程和企业要求,进行产品交接
·能对加工产品进行成本核算
·能按企业规定,整理现场,保养机床,填写保养记录
·能与他人进行有效的专业交流
·能按照国家环保要求和企业要求处置废油液等废弃物
课程目标
1.能根据加工任务,讨论并制定合理的工作计划。
2.能根据配作件的实物,测绘出配合件的零件图。
3.能根据任务书、装配图和零件图,确定装配基准和加工基准,在图样上标记,计算工艺尺寸链和装配尺寸链,并讨论、制定加工工艺,预估加工工时。
- 1、下载文档前请自行甄别文档内容的完整性,平台不提供额外的编辑、内容补充、找答案等附加服务。
- 2、"仅部分预览"的文档,不可在线预览部分如存在完整性等问题,可反馈申请退款(可完整预览的文档不适用该条件!)。
- 3、如文档侵犯您的权益,请联系客服反馈,我们会尽快为您处理(人工客服工作时间:9:00-18:30)。
试议配合件的数控加工(doc 10页)与同属回转体零件的轴类零件配合,由于其功能不同,盘套类零件结构和尺寸有着很大的差别,但其结构仍有共同点,零件的主要表面为同轴度要求较高的内外圆表面,零件壁的厚度较薄且易变形,盘套类零件的结构一般由孔,外圆,端面,沟槽及内螺纹和外螺纹,内锥面和内型面组成。
常见的有轴承套,衬套,齿轮,带轮,轴承端盖等。
盘套类零件表面精度要求除尺寸外、形状精度外,内孔一般要作为配合和装配的基准,孔的直径尺寸等级一般为IT7,精密轴套可以取IT6,孔的形状精度应控制在孔径公差内,,一些精密套筒控制在孔径的公差的二分之一到三分之一,对于长度较长的轴套零件,除了圆度要求以外,还应注内孔面的圆柱度,端面对内孔轴线的圆跳动度和垂直度,以及两端面的的平行度等要求,为了保证零件的功用和提高其耐磨性,孔的表面粗糙度值Ra1.6-0.16um,甚至更高。
以数控车加工的典型零件盘套类零件,轴承套为例,讨论配合件的数控加工。
轴承套数控车削加工工艺(单件小批量生产),所用机床为CJK6240 一、零件图工艺分析1)编程时取基本尺寸。
但由于要求配合,则有的配合尺寸需取中间值。
2)先确定基准,先加工左、右端面。
保证零件的长度尺寸。
3)内孔尺寸较小,镗1﹕20锥孔、φ32孔及15°斜面时需掉头装夹。
4)右端有螺纹,所以放在最后加工,由于高速车削挤压引起螺纹牙尖膨胀变形,因此外螺纹的外圆应车到最小极限尺寸,螺纹加工前,先将加工表面加工到实际直径尺寸,M45×1.5的螺纹,加工前的外圆直径为:D外≈D-(0.1~0.2165)P =45-0.2*1.5=44.7一般数控车床推荐车螺纹时的最高转速为:n≤1200P-k (k是保险系数,一般为80)加工螺纹时,长度应包括切入切出的空行程量,切入量一般取2-5mm,切出量一般取0.5-1mm。
也可无退刀曹轴承套的零件图二、确定装夹方案1)内孔加工时以外圆定位,用三爪自动定心卡盘夹紧。
2)加工外轮廓时,需要设一圆锥心轴装置,用三爪卡盘夹持心轴左端,心轴右端留有中心孔并用尾座顶尖顶紧。
外轮廓车削装夹方案三、加工顺序走刀路线依照基孔先行的原则,先加工内孔各表面,需要调头加工,由于右边有螺纹,所以放在最后加工。
再加工外轮廓表面。
由于该零件为单件小批量生产,外轮廓表面车削走刀路线可沿零件轮廓顺序进行。
加工前,先手动加工通孔。
四、走刀路线由于该零件为单件小批量生产,外轮廓表面车削走刀路线可沿零件轮廓顺序进行。
采用装夹,刀具集中原则,划分工序。
五.刀具选择序号刀具号刀具规格名称数量加工表面刀尖半径1 TO1 45°硬质合金端面车刀1 车端面0.42 TO2 镗刀 1 镗内孔表面0. 43 T03 93°外圆车刀 1 车各外圆0. 44 T04 60°外螺纹车刀1 车M45螺纹5 尾座¢28mm钻头 1 钻底孔六. 切削用量的选择序号刀具号切削用量背吃刀量直径mm主轴转速R/min进给速度mm/r1 T01 3 1000 0.22 T02 2 800 0.1 精0.053 T03 3 800 0.3 精0.154 T04 500 1.55 尾座400 手动七.加工程序O0001;G99 T0101; 选45°硬质合金端面车刀M03S600; 主轴正转G00X85 Z2;GO1ZO F0.1; 先加工左面,车端面X-1;GOOX100 Z150;T0101; 换镗刀G00X82 Z2;G71U2R0.5; 利用复合指令车外圆各面G71P1Q2U0.5W0.2F0.3 S800;N1 GOO G42X46;GO1 Z2 F0.1;X49.97 Z-2;Z-30;X58;G02 X68Z-35 R5;GO1X74X78Z-37;N2 G40 Z-60;G70P1Q2S1000;GOOX100Z100;T0202; 换内孔镗刀车内孔GOOX25Z2;G71U2R0.5;G71P1Q2U-1W0.5F0.2 S600;N1GOOG41X35.1;GO1Z0 F0.05;X32Z-10;Z-29;G02X30Z-30 R1;N2G40X28;G70P1Q2;MO5; 主轴停M30 程序停止准备掉头加工右面(方法同左边加工相同,程序略)(二) 铣削为主的箱体类配合件的加工。
箱体类零件一般指是具有一个以上的孔系,内部有一定型腔或空腔,在长宽高方向有一定比例的零件,这类零件在机械,汽车,飞机制造业用得多,如汽车的发动机缸体,变速箱体,机床主轴箱,齿轮泵壳体等。
一.数控机床的选用方面。
箱体类零件一般是其它零件配合的载体。
都需要进行多工位孔系、轮廓及平面加工,公差要求较高,特别是形位公差要求较为严格,通常要经过铣、钻、扩、镗、铰、锪、攻丝等工序。
需要刀具多,在普通机床上加工难度大,工装套数多,费用高,加工周期长,需要多次装夹,找正,手工测量次数多,加工时还要频繁的换刀,工艺难制定,更重要的是精度难以保证。
这类零件在加工中心上加工,一次装夹可完成普通机床的60%--95%工序内容,零件各项精度一致性好,质量稳定,同时节约费用,缩短加工周期。
加工中心与数控铣床铣削加工是型腔模具加工的重要手段。
数控铣床是一种加工功能很强的数控机床,数控铣床是一种加工功能很强的数控机床,在数控加工中占据了重要地位。
现在数控铣床已全面向多轴化发展。
目前迅速发展的加工中已全面向多轴化发展。
目前在数控铣床和数控镗床的基础上产生了加工中心和柔性制造单元也是在数控铣床和数控镗床心和柔性制造单元。
铣削加工是型腔模具加工的重要手段。
并且现今产生了高速铣削,而高速铣削具有工件温升低、切削力小、加工平稳、加工质量好、加工效率高及可加工硬材料等,且高速铣削加工不仅可提高效率,而且也可提高表面质量,从而减轻了精加工负担,缩短了工期。
诸多优点。
因而在模具加工中日益受到重视。
加工箱体类零件的加工中心,当加工工位较多是时,需要工件台多次旋转角度才能完成的零件,一般选用卧式加工中心,当工位较少,且跨度不大时,可选用立式加工中心。
二.箱体零件加工方法。
(一)当既有孔,又有面时,应先铣面,后加工孔。
(二)所有孔系都应先完成所有孔的粗加工,再精加工。
(三)一般情况下,直径大于30的孔都应先铸出毛坯孔,在普通机床上完成毛坯孔的粗加工,给加工中心留4-6mm的加工余量,再上加工中心进行孔和面的加工,通常分为“粗镗—半精镗—孔端倒角—精镗”四个工步完成。
(四)直径小于30的孔,可以不铸出毛坯孔,但孔和孔的端面全部都得在加工中心上完成,可分为“锪平端面—打中心孔—钻—扩—孔端倒角—精镗”工步完成。
有同轴度要求的小孔,须采用“多锪平端面—(打中心孔)—钻—半精镗—孔端倒角—精镗”工步完成。
(五)在孔系加工中,先加工大孔,再加工小孔,特别是在大小孔相距很近的时候,更要采用这种方法。
(六)对于跨度较大的箱体的同轴孔加工,尽量采用调头加工的方法,以缩短刀辅具的径比,增加刀具刚性,提高加工质量。
(七)螺纹的加工方法,一般情况下,M6—M20的螺纹也可以在加工中心上完成攻螺纹。
M6以下和M20以上的螺纹可在加工中心上完成底孔,攻螺纹通过其它手段加工,因为加工中心的自动加工方式在攻小螺纹时,不能随机的控制加工状态,小丝锥容易折断,从面产生废品,由于刀具,辅具等因素的影响,在加工中心上攻M20以上的螺纹有一定的难度。
但可以通过特定程序,用镗刀片完成螺纹的切削。
(八)分析零件的形状及原材料的热处理状态,是否会在加工过程中变形,哪些部位最容易变形。
因为数控铣削最忌讳工件加工时变形,这这种变形不但无法保证加工质量,而且经常造成加工不能正常进行,这时应该考虑一些必要的工艺措施预防。
如对钢件进行调质处理,对铸件进行退火处理,对不能用热处理方法解决的问题,也可考虑粗加工,精加工及对称去余量的方法,此外,还要分析加工后的变形问题,采取工艺措施解决。
三.加工工序的划分在数控机床上加工箱体等配合件,工序比较集中,一般只需要一次装夹即可完成所有加工,通常可按照从简单到复杂的原则,先加工平面、沟槽,再加工内腔、外形,最后加工曲面,先加工精度要求低的,再加工精度要求较高的。
为了提高机床的使用寿命,保证数控机床的精度,降低零件的加工成本,通常把零件的粗加工,特别是零件的定位面在普通机床上加工。
四.铣削中刀具夹具的选择选择刀具的重要依据是被加工零件的几何形状和材料。
加工曲面类零件时,一般用球头刀,粗加工用两刀刃铣,半精加工和精加工用四刃铣刀。
刀刃娄还与刀具直径有关,铣较大平面时,一般采用刀片镶嵌式租车形面铣刀。
铣小平面或台阶时,一般采用通用铣刀,铣键槽时,一般用两刃键槽铣刀。
孔加工时,可采用钻头、镗刀、铰刀等孔加工刀具。
箱体的装夹和夹具的选择,在数控机床上加工中,既要保证加工质量,又要减少辅助时间,提高加工效率。
因此要选用能准确和迅速定位并夹紧的工件的装夹方法和夹具。
零件的定位基准应尽量与设计基准及测量重合,以减少定位误差为了不影响进给和切削加工在装夹工件时一定要将加工部位敞开,选择夹具时应尽量做到在一次装夹中将要求加工的面都加工出来。
五. 箱体零件的加工编程一般情况下,零件如尺寸少,相对确定,可以人工编程,如几何形状复杂的零件。
或有复杂曲面的零件,或几何形状并不复杂,但程序量很大的零件,这种加工编程计切削用量的选择必须在机床主传动功率。
进给传动功率以及主轴转速范围,进给范围内。
机床-刀具-工件系统的刚性是限制切削用量的重要因素。
切削用量的选择应使机床-刀具-工件系统不发生较大的振动。
如果机床的稳定性好,工件的热变形小,刀具材料性能好,可适当的加大切削用量。
铣削加工切削用量包括:切削速度,进给速度,背吃刀量,及侧吃刀量,从刀具寿命的角度出发,切削用量的选择方法是:先选择背吃刀量,侧吃刀量,其次选择进给速度,最后确定切削速度。
专业班级姓名论文题目指导教师初审成绩评定内容论文选题资料利用学术造诣知识掌握科研能力完成情况写作能力写作规范总分数成绩评分标准10分10分20分20分10分10分10分10分100分实际评分评阅教师评阅成绩评定内容论文选题资料利用学术造诣知识掌握科研能力完成情况写作能力写作规范总分数评分标准10分10分20分20分10分10分10分10分100分实际评分答辩成绩评定内仪态仪语言写作规完成情科研能应用价创新观答辩效总分数评分标10分10分10分10分10分20分10分20分100分实际评评语 指导教师评语:评阅教师评语:答辩小组评语: 指导教师 __________ 年 月 日 评审教师 __ 年 月 日答辩负责人__________ 年 月 日。