圆坯连铸结晶器温度场模拟与坯壳厚度预测
圆坯连铸结晶器内电磁场、流场的数值模拟与实验研究的开题报告

圆坯连铸结晶器内电磁场、流场的数值模拟与实验研究的开题报告一、选题背景连铸技术是钢铁工业生产中重要的工艺环节之一,其直接关系到产品的质量和产量。
圆坯连铸结晶器内流场和电磁场的研究对提高连铸技术的效率和改善产品质量具有重要意义。
因此,本文提出了圆坯连铸结晶器内电磁场、流场的数值模拟及实验研究,以深入了解连铸过程中结晶器内的热传递、流动和结晶行为。
二、研究目的和意义圆坯连铸结晶器内电磁场、流场数值模拟和实验研究旨在:1. 为圆坯连铸结晶器的热流场和结晶行为的研究提供理论基础和实验支持。
2. 分析结晶器内电磁场、流场的特点,为进一步优化结晶器结构、提高产品质量和连铸效率提供基础数据。
3. 提出可以用于优化结晶器中的电磁场和流场的设计建议。
三、研究内容和方法1. 研究结晶器内的电磁场的分布特性,通过建立电磁场的数学模型,利用有限元方法进行数值模拟,验证模型的有效性。
2. 研究结晶器内的流场分布特性,通过建立流场模型,利用计算流体力学(CFD)方法进行数值模拟,验证模型的有效性。
3. 利用热像仪和热电偶等实验手段,对圆坯连铸结晶器内的温度分布情况进行实时监测和记录,验证数值模拟结果的正确性。
4. 基于数值模拟结果和实验数据,分析结晶器内的电磁场、流场与温度分布的关系,并提出结晶器内电磁场、流场优化设计建议。
四、研究进度安排一月份:阐述选题背景和研究目的,并提出研究方法和内容;二月份:对相关领域的文献进行综述和分析,明确研究的重点和难点;三月份:建立连铸结晶器内电磁场的数学模型,进行数值模拟,验证模型的正确性和可行性;四月份:建立连铸结晶器内流场的数学模型,进行数值模拟,验证模型的正确性和可行性;五月份:利用热像仪和热电偶等实验手段,对圆坯连铸结晶器内的温度分布情况进行实时监测和记录;六月份:基于数值模拟结果和实验数据,分析结晶器内的电磁场、流场与温度分布的关系,并提出结晶器内电磁场、流场优化设计建议;七月份:总结研究成果,撰写毕业论文,并进行答辩。
连铸结晶器中坯壳生长有限元分析
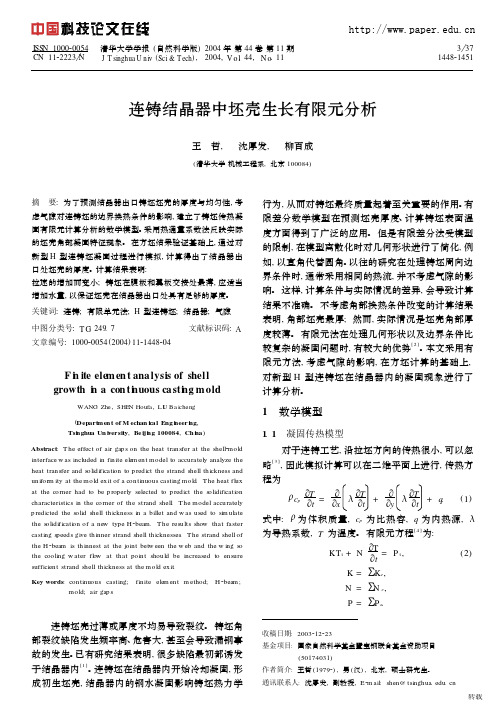
转载
中国科技论文在线
王 哲, 等: 连铸结晶器中坯壳生长有限元分析
式中: K 为温度刚度矩阵, T 为温度列向量, N 为
变温矩阵, P 为常列阵向量, 下标 t 表示某一时刻,
下标 e 表示单元。 对于 3 节点三角形单元, Ke、N e、 P e 中的元素分别如下所示:
kij = Κ(bibj + cicj ) (4∃ ) ,
( i, j = 1, 2, 3) ;
nii = Θcp ∃ 6,
(i = 1, 2, 3) ;
nij = Θcp ∃ 12,
( i, j = 1, 2, 3; i ≠ j ) ;
p i = ∃ qv 3,
( i = 1, 2, 3).
相变潜热作源项处理, 采用修正的方法, 对进入两相
1 数学模型
1. 1 凝固传热模型
对于连铸工艺, 沿拉坯方向的传热很小, 可以忽 略[3], 因此模拟计算可以在二维平面上进行, 传热方 程为
Θcp
9T 9t
=
9 9x
Κ99Tt
+
9 9y
Κ99Tt
+
q.
(1)
式中: Θ为体积质量, cp 为比热容, q 为内热源, Κ
为导热系数, T 为温度。 有限元方程[4]为:
ICSNSN11120202022300N54
清华大学学报 (自然科学版) J T singhua U niv (Sci & T ech) ,
2004 年 第 44 卷 第 11 期 2004, V o l. 44, N o. 11
3 37 144821451
动的影响, Κ取有效导热系数。
板坯连铸机结晶器内三维流场和温度场的有限元分析的开题报告

板坯连铸机结晶器内三维流场和温度场的有限元分析的开题报告1. 研究背景板坯连铸技术在冶金工业中广泛应用,其中结晶器是板坯连铸机的一个重要部件,决定了板坯的质量和直径。
为了进一步提高板坯连铸机生产效率和产品质量,需要对结晶器内部的流场和温度场进行深入研究。
2. 研究内容本研究旨在通过有限元分析方法,对板坯连铸机结晶器内的三维流场和温度场进行分析,探究结晶器内局部的流动规律和热传递特性,为优化连铸机结构和操作参数提供理论支持。
具体研究内容包括:(1)建立板坯连铸机结晶器的三维模型,包括结晶器下部、侧壁和顶部的几何形状和结构特点等。
(2)采用FLUENT软件对结晶器内部的三维流场进行模拟和计算,考虑板坯连续坯流动、自由液面、宽度变化等实际工况因素,研究结晶器内局部流动规律。
(3)基于ANSYS软件对结晶器内的三维温度场进行模拟和计算,分析板坯在连铸过程中的温度分布情况,并研究热传递特性对板坯成形质量的影响。
3. 研究意义通过对板坯连铸机结晶器内部流场和温度场的有限元分析,可以更加深入地了解结晶器的结构特点和板坯成形过程中关键参数的影响规律,为优化连铸机的生产效率和产品质量提供参考和优化建议。
研究成果可为铸造工艺的科学发展提供重要理论支持。
4. 研究方法本研究主要采用有限元分析方法,包括建立结晶器的三维几何模型、采用FLUENT软件模拟结晶器内的三维流场、采用ANSYS软件模拟结晶器内的三维温度场等。
5. 预期成果经过对板坯连铸机结晶器流场和温度场的有限元分析,本研究将得到以下预期成果:(1)结晶器内部的流场和温度场分布规律图;(2)不同结构和操作参数对流场和温度场的影响规律;(3)结晶器内不同部位的流动规律和温度特性分析和优化建议。
6. 研究进度和计划目前,本研究正在进行模型建立和初步模拟,预计在6个月内完成有限元分析计算和数据处理,整理成篇有关结晶器内的流场和温度场分析的研究论文。
具体研究计划如下:(1)第1-2个月:建立板坯连铸机结晶器的三维模型;(2)第3-4个月:采用FLUENT软件模拟结晶器内的三维流场;(3)第5-6个月:采用ANSYS软件模拟结晶器内的三维温度场,并对数据进行分析和处理;(4)第7个月:编写研究论文并进行修改、定稿及提交。
连铸过程中板坯凝固的数值模拟

连铸过程中板坯凝固的数值模拟
QS C PVT
(5-10) 由式(5-9)与式(5-10)等量置换可得
f S C P T / L
(5-11) 此法采用固相率的增加来代替前热的放出,如果 f S 1 ,则表明该领域 V 的 凝固结束。
热焓法
凝固过程金属的焓可定义为
H cdT (1 f s ) L
L ——潜热, J / kg ;
f s ——固相率;
T ——温度, C ;
——时间, s ;
连铸过程中板坯凝固的数值模拟
——导热系数, W /(m K ) ;
x, y ——二维坐标, m 。
对于实用多元和金,要确定固相率和温度的关系,通常可以先采用热分析法 求出凝固开始温度 TL (液相线温度)和结束温度 TS (固相线温度),假定如下: (1)假定为线性分布时
式中, L ——补偿对流换热的等效导热系数;
m ——经验常数,钢液导入区, m 4 ~ 8 ;
S ——静止钢液的导热系数。
热物性参数的数值处理方法
由于导热系数、比热和密度是随温度变化的,其处理方法一般有常数法、线 形函数法和插值法等,在不同的温度区间内用二次曲线拟合的方法得到温度导热系数、温度-比热之间关系的曲线,来确定导热系数、比热值。 对于板坯密度的取值,可在不同相区内取不同的值。 (1) 固相区: S 7.6 10 3 kg / m 3 ;
板坯连铸过程中铸坯凝固壳厚度的测定
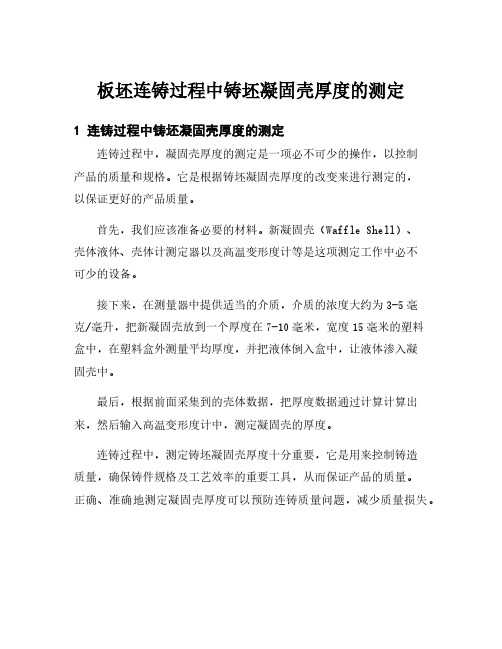
板坯连铸过程中铸坯凝固壳厚度的测定
1 连铸过程中铸坯凝固壳厚度的测定
连铸过程中,凝固壳厚度的测定是一项必不可少的操作,以控制
产品的质量和规格。
它是根据铸坯凝固壳厚度的改变来进行测定的,
以保证更好的产品质量。
首先,我们应该准备必要的材料。
新凝固壳(Waffle Shell)、
壳体液体、壳体计测定器以及高温变形度计等是这项测定工作中必不
可少的设备。
接下来,在测量器中提供适当的介质,介质的浓度大约为3-5毫
克/毫升,把新凝固壳放到一个厚度在7-10毫米,宽度15毫米的塑料
盒中,在塑料盒外测量平均厚度,并把液体倒入盒中,让液体渗入凝
固壳中。
最后,根据前面采集到的壳体数据,把厚度数据通过计算计算出来,然后输入高温变形度计中,测定凝固壳的厚度。
连铸过程中,测定铸坯凝固壳厚度十分重要,它是用来控制铸造
质量,确保铸件规格及工艺效率的重要工具,从而保证产品的质量。
正确、准确地测定凝固壳厚度可以预防连铸质量问题,减少质量损失。
连铸结晶器温度场及热变形的数值模拟

d fr a o n ra e . T e rt fc o i g w tr h r a n u n e o h e e au e f l d t e a e o t n ic e s h ae o o l ae a g e ti e c n t e tmp rt r ed a h r l m i s n s l f i n m
Nu e ia i u a in o e o ma i n a d tm p r t r m rc lSm lto n d f r t n e e a u e o
i l fc ntnu u a tn u d fed o o i o sc si g m o l
K ANG i L ,W A n g n , HE J—h n NG E —a g i e g c
r t n atn p e n t e tmp r t r ed a d d fr t n o l e n e t ae . T e r s s ae a d c i g s e d o h e e u e f l n e o mai f mod w r i v si td h et s a i o e g e s o e h tw e a t g s e d i c e s s h mp r tr n eo ai n as n r a e . W h n t e m伽 l h w d t a h n c si p e n r a e .te t n e e au e a d d fr t l o ic s s m o e e h d
维普资讯
第 5卷 第 3期
20 0 6年 9月
材
料
与 台 金
学
报
Vo. . 15 No 3 S pt e .20 6 0
大圆坯连铸凝固传热过程的数值模拟

表 1 大圆坯连铸机基本参数
项目单位 /
铸 机 基 本 半径 / m
1 铸坯 中心: ) 为轴对称传热,可视为绝热边界 条件 ,
即
技术参数
1 6
一 l.00 f: r> - 刮 0
一
【 ( 8 J )
( 9 )
【 J
铸坯断面直 径/ m m
结晶器 有效长度/ mm
M AO n —in EN n — h Bi g l g ,R a Bi g z i ,HAN iwe 。 Zh — i,CAO in f n Ja -e g ,FE NG Ke
(. i guSn nE up n o p h n su 2 5 0 , hn ; 1 J n s u a q ime t u ,C agh 15 0 C ia a Gr 2 Na o aE gn e n eerhC ne rrn Sel aigPatnert n C o gig 4 0 1 ,C ia . t n l n ier g sa etro o & teM kn l tgao , h n qn 0 0 3 hn ) i i R c f I nI i
宽板坯连铸结晶器流场和温度场的数值模拟

宽板坯连铸结晶器流场和温度场的数值模拟
随着工业生产技术的不断发展,连铸技术已经成为宽板坯的主要生产方式,特别是在钢铁行业中,大量的钢铁产品均采用连铸工艺生产。
宽板坯连铸技术的核心是结晶器,结晶器的流场和温度场是宽板坯质量的关键因素,因此对流场和温度场进行数值模拟研究是必要的。
数值模拟能够对结晶器内部的流场和温度场进行快速、准确的计算,揭示了结晶器内的流场和温度场在宽板坯生产中的重要作用。
本文通过对结晶器内流场和温度场的数值模拟分析,提出了一种优化结晶器设计的方法。
首先,本文基于Navier-Stokes方程和热传导方程,建立了数学模型,考虑结晶器内部的流动载荷、热辐射、传导热和对流换热等因素。
其次,利用Fluent软件进行流场和温度场计算,得到了流场和温度场的数值解。
通过对数值模拟结果的分析,发现结晶器内部的流动较为复杂,主要存在四个涡旋,其中两个涡旋在底部,两个涡旋在上部。
涡旋的存在使得物料在结晶器内部获得了良好的混合,进一步提高了结晶器内物料的质量。
另外,结晶器内部的温度场也十分关键。
通过数值模拟结果可以看出,结晶器内部温度分布不均匀,底部温度较高,而顶部温度较低。
这是由于底部邻近铸坯熔池温度较高,导致底部结晶器的温度较高;而顶部的散热较快,导致顶部结晶器的温度较低。
最后,通过对数值模拟结果的分析得出,改变结晶器底部的形状,减少对流热损失,可以提高结晶器内部的温度分布均匀性,进而提高宽板坯的质量,同时也可以减少不必要的生产成本。
- 1、下载文档前请自行甄别文档内容的完整性,平台不提供额外的编辑、内容补充、找答案等附加服务。
- 2、"仅部分预览"的文档,不可在线预览部分如存在完整性等问题,可反馈申请退款(可完整预览的文档不适用该条件!)。
- 3、如文档侵犯您的权益,请联系客服反馈,我们会尽快为您处理(人工客服工作时间:9:00-18:30)。
件. 设开浇时刻 ( t = 0) 已存在钢液的温度为浇注温
度 ;在浇注过程中 ,所有新浇入的钢液温度为浇注温
度 ,则初始条件已知.
依据结晶器与坯壳的接触模型 , 设定如下的边
界条件.
(i) 铸坯/ 铜板边界 :
-
kc
5 Tc 5r
=
-
ks
5 Ts 5r
=
qc .
(ii) 铸坯中心 :
-
ks
5 Ts 5r
由于计算结果是温度场的离散值 , 并没有直接 得到凝固壳厚度分布 , 因此需要对温度场采用一种 办法进行处理得到凝固壳厚度分布. 大多数研究者 直接取一个在液相线和固相线之间的经验温度值来 处理. 此方法固然简单 , 但是没有考虑到材料成分 的影响. 本文考虑了钢液中碳含量的影响 , 采用 Scheil 方程计算固相率得到坯壳厚度 , 即任意取得 一个面 ,如果能够在离散化的温度场上计算出固相 率 f s 等温线 ,以 f s = 017 为分界线 ,则从 f s = 017 处 直线到外边界的距离就是凝固壳的厚度.
2 模型验证
为校核与验证模型计算结果的可靠性 ,结晶器 温度计算的结果直接可以通过实测的数据进行验 证. 图 1 和图 2 是拉速为 2 m·min - 1 ,在其他工艺参
图 1 结晶器温度计算值与实测值比较曲线 Fig. 1 Comparison of the calculated with measured values of mould temperature
272
钢水密度/ ( kg·m - 3) 7 200
碳质量分数/ %
0136
液相线温度/ ℃ 1 500 铸坯比热容/ (J ·kg - 1 ℃- 1) 680
固相线温度/ ℃ 1 445 导热系数/ ( W·m - 1 ℃- 1) 34
第四排测点 ,即高度为 280 mm 处 , 测量热流又相对 有所回升. 经分析发现高度在 300 mm 左右 ,刚好是 结晶器锥度改变处. 结晶器采用这种特殊的锥度设 计 ,使得从此部位以下形成的气隙宽度减少而引起 热流略有回升. 在结晶器出口处热流的回升 , 是由 于此时铸坯结晶器之间的渣膜大部分呈现固态 , 固 态渣膜尤其是玻璃态的渣膜具有良好的导热性能 , 加速了铸坯向结晶器传热所致.
根据铸坯的温度场 , 由 平 衡 方 程 和 Scheil 方 程[10]分别计算出铸坯的固相率与坯壳厚度如图 5 和图 6 所示. 图 5 是由 Scheil 方程计算得到的内弧 处固相率分布图. 由图 5 可知 , 铸坯根据固相率可 分为三个区 : f s ≤013 划为液相区 , f s ≥017 划为固 相区 ,两固相率之间为液固两相区 ,以初步估算坯壳 的厚度. 图 6 (a) 是结晶器出口内弧处铸坯固相率沿
1 模型描述
根据圆坯形状的对称性特点 , 在圆柱坐标系内 建立传热模型. 首先对铸坯温度场计算模型作如下 假设 :
(1) 铸坯传热以热传导方式为主 , 钢液流动对 传热的影响通过增大钢液导热性来体现 ;
(2) 铸坯为不可压缩材料 , 忽略因粘滞行为而 引起的能耗 ;
收稿日期 : 2006207215 修回日期 : 2006209226 基金项目 : 教育部科技研究重点项目 (No . 03051) 作者简介 : 姚 曼 (1962 —) ,女 ,教授 ,博士
数相同条件下 ,计算的结晶器温度 、热流与实际测量 温度 、热流数据平均值的比较曲线. 其中 , 图 1 中 C 表示结晶器的冷面 , H 表示结晶器的热面.
由图 1 和图 2 对结晶器温度和热流进行比较 , 计算值和实测值大致吻合 , 曲线变化趋势相似. 在 弯月面区域 ,坯壳快速冷凝收缩 ,在铸坯与结晶器之 间很快出现了气隙 ,使得铸坯与结晶器迅速脱离 ,因 此这里热流不大. 随着铸坯向下移动 , 钢液静压力 的作用将铸坯重新压回结晶器 ,使得气隙减小 ,致使 热流迅速升高 , 在第二排测点高度附近达到最大.
图 5 由 Scheil 方程计算的铸坯凝固率分布 Fig. 5 Distribution of solidif ied fraction in the round billet calcu2 lated by the Scheil equation
图 6 结晶器出口处固相率沿半径方向的分布( a) 和坯壳厚度沿 结晶器纵向的变化( b) Fig. 6 Distribution of solidif ied fraction in the round billet at the outlet of the mould ( a) and shell thickness along the mould ( b)
图 3 不同高度位置( a) 和半径( b) 圆坯温度沿纵向变化 Fig. 3 Longitudinal distribution of temperature in the round billet at different heights ( a) and different radii ( b)
第 29 卷 第 11 期 2007 年 11 月
北京科技大学学报 Journal of University of Science and Technology Beijing
Vol. 29 No. 11 Nov. 2007
圆坯连铸结晶器温度场模拟与坯壳厚度预测
姚 曼1) 詹慧英1) 王旭东1) 郭亮亮1) 尹合壁1) 刘 晓2) 于 艳2)
=
0.
(iii) 铸坯/ 保护渣边界 :
-
ks
5 Ts 5z
=
-
kf
5 Tf 5z
=
(
Ts
-
Tf) / R .
式中 , h 为对流换热系数 , k 为导热系数 , qc 为单位 时间单位面积上坯壳通过结晶器传出的热量 , 脚标
c 、f 和 s 分别表示结晶器 、渣 、铸坯 , R 为渣/ 钢界面
接触热阻.
表 1 基本条件及主要工艺参数 Table 1 General conditions and main process parameters
参数
数值
参数
数值
结晶器长度/ mm 780
浇注温度/ ℃
1 523
结晶器厚度/ mm 15
拉速/ ( m·min - 1)
210
圆坯直径/ mm
178
潜热/ ( kJ ·kg - 1)
目前我国已经建设了多台圆坯连铸机 , 而现有 文献的报道常集中在板坯和方坯方面[4- 6 ] , 对圆坯 结晶器内凝壳规律研究不多. 且通常用于预测坯壳 厚度的平方根定律也只是适用于板坯等平面一维的 凝固过程[7 ] ,对于圆坯并不适用. 针对此种情况 , 本 文建立三维圆坯结晶器传热模型 , 计算得到结晶器 与铸坯的温度场 ,并利用实测温度数据进行了验证. 通过固相率的计算获得了坯壳厚度分布状况 , 并分 析了主要参数对结晶器出口处坯壳厚度的影响 , 同 时对利用模型与经验公式计算出的坯壳厚度进行了 对比和分析.
图 4 结晶器与铸坯温度场分布 Fig. 4 Temperature f ields of the mould and round billet
312 铸坯固相率分布与坯壳厚度计算 固相率控制着整个钢液的凝固进程 , 计算中用
到的许多变量都与它相关 ,如凝固潜热的释放 、导热 系数等. 固相率不仅与温度有关 , 而且与材料的成 分相关[9 ] . 由于连铸坯壳在凝固过程中受不同冷却 条件的影响 ,因此非平衡凝固存在于整个凝固过程 中. 同时 ,由于在凝固过程中部分组元在液相中富 集 ,影响了液相线温度. 所以 , 固相率也是精确预测 组织性能的一个重要参数[9 ] .
图 4 中用渐变色显示了圆坯连铸结晶器与铸坯
第 11 期
姚 曼等 : 圆坯连铸结晶器温度场模拟与坯壳厚度预测
·1093 ·
温度场分布 ,左侧与右侧分别为结晶器与铸坯的温 度标示. 由图 4 可以看出 , 铸坯内温度的变化在 1 523~1 000 ℃之间. 弯月面附近的铸坯温度最高 , 接近钢水浇注温度 , 再往下沿拉坯方向温度逐渐 降低.
半径方向的分布. 由图 6 (a) 可知 , 平衡方程计算得 到的固相率比 Scheil 方程的稍高. 这是由于平衡方 程假设固液相均完全混合 , 实际铸坯凝固时固相只 能以有限扩散方式进行. 本文采用 Scheil 方程计算 得到固相率. 图 6 (b) 是坯壳厚度沿结晶器纵向变化 曲线. 由图可知 ,最终坯壳厚度大约在 20 mm 左右.
图 2 结晶器热流密度计算值与实测值比较曲线 Fig. 2 Comparison of the calculated with measured values of mould heat flux
3 计算结果分析
311 结晶器内铸坯温度场分布 对表 1 中给出的计算条件进行数值模拟. 图 3 (a) 所示是在不同半径处铸坯温度沿结晶
(3) 开浇时结晶器钢水温度为浇注温度 ;
(4) 铸坯是稳态导热并以拉速 V 匀速运动.
111 传热微分方程
在温度场计算中 ,采用三维计算模型 ,圆柱坐标
系传热基本方程为 :
15T α 5τ
=
15T r 5r
+
52 5
T r2
+
1 52 T r2 5Φ2
+
52 T 5 z2
+
Q
(1)
式中 , α , W ·
m - 1 ℃- 1 ; C 为比热容 ,J ·kg - 1 ℃- 1 ;ρ为密度 , kg·
m - 3 ; r 、Φ 和 z 为圆柱坐标系三个方向的坐标 , m ;
T 为温度 , ℃; Q 为潜热 , kJ ·kg - 1 . 本文中采用温
度回升法[8 ]进行处理.