炼钢原辅料
钢铁工业原料、辅料分类表

钢铁工业原料、辅料分类表钢铁工业原料、辅料分类(一)铁矿石1. 原矿(1)入炉矿(2)入选矿2. 成品矿(1)炼钢块矿(2)炼铁块矿(3)铁富粉矿(4)铁精矿粉3. 成品矿按含铁量分(1)炼钢块矿(2)炼铁块矿(3)铁富粉矿(4)铁精矿粉(二)人造富铁矿1. 烧结铁矿(1)普通(2)高碱度2. 球团铁矿(1)普通(2)酸性(3)其它3. 其它(三)锰矿石1. 原矿2. 成品矿(1)块矿(2)粉矿(3)锰精矿(四)铬矿石2. 成品矿(1)富铬块矿(2)铬精矿(五)石灰石1. 原矿2. 成品矿(1)冶金用(2)水泥用(3)其它用(六)硅石1. 原矿2. 成品矿(七)萤石1. 原矿2. 成品矿(1)冶金用(2)其它用3. 萤石精粉(八)耐火粘土1. 原矿2. 成品矿(1)高铝粘土(2)硬质粘土(3)软质粘土(4)其它3. 耐火粘土熟料(1)高铝质(2)硬质(九)菱镁矿1. 原矿2. 成品矿(1)冶金砂用(2)其它用3. 煅烧镁砂4. 镁砂(1)煅烧冶金用(2)煅烧制砖用(3)煅烧镁铁砂(4)轻烧(5)电熔(十)白云石1. 原矿2. 成品矿(十一)生铁1. 炼钢生铁2. 铸造生铁3. 含钒生铁(十二)废钢1. 企业发生废钢2. 外购废钢(十三)焦炭1. 生产:机焦(含冶金焦)型焦土焦2. 沥青焦(十四)铁合金1. 按生产方法分(1)高炉铁合金(2)电炉铁合金(3)转炉铁合金(4)其它铁合金2. 按品种分(1)硅铁(2)碳素锰铁(3)中低碳锰铁(4)特种铁合金:碳素铬铁中低碳铬铁微碳铬铁钨铁钼铁钒铁钛铁磷铁电解锰金属锰稀土铁合金(十五)碳素制品1. 石墨电极类:特种石墨电极不透性石墨2. 炭电极类3. 炭块类4. 炭糊类:阳极糊电极糊(十六)耐火材料1. 耐火砖:粘土砖硅砖高铝砖镁砖及镁质砖其它砖2. 不定型耐火砖3. 特种耐火材料(十七)炼焦化学产品1. 煤焦油2. 硫酸铵3. 硫酸4. 粗苯5. 轻苯6. 重苯7. 粗轻吡啶8. 甲苯9. 二甲苯10.轻溶剂油11.洗油12.木材防腐油13.二蒽油14.工业萘15.萘油16.粗蒽17.煤沥青18.纯吡啶19.精萘20.纯苯。
工业炼钢的原理初中化学

工业炼钢的原理初中化学一、炼钢基本原理炼钢的主要目的是降低生铁中含有的含碳量,同时去除磷、硫等有害元素,并调整钢中的合金元素含量。
生铁炼成钢的实质是降低生铁中的含碳量,而含碳量的降低则是通过加入氧化剂将生铁中过多的碳和其他杂质转化为气体或炉渣除去。
二、原料与辅料炼钢的主要原料是铁水,即转炉或电炉炼铁得到的含碳量较高的铁水。
辅料主要包括造渣材料(如石灰石、白云石等),用于形成炉渣去除杂质;氧化剂(如氧气、铁矿石等),用于氧化铁水中的碳和其他杂质;以及脱氧剂和合金剂,用于调整钢的成分。
三、炼钢炉种类1. 氧气转炉:主要利用氧气作为氧化剂,吹入熔化的铁水中,使碳和其他杂质氧化成气体排出。
2. 平炉:通过向炉内加入燃料进行燃烧,产生热量熔化铁水,并加入氧化剂进行脱碳和其他杂质。
3. 电炉:利用电能产生高温熔化铁水,并加入氧化剂进行脱碳和杂质去除。
四、氧气转炉炼钢氧气转炉炼钢是现代炼钢的主要方法。
在转炉中,通过吹入高压氧气与铁水中的碳和杂质发生氧化反应,生成CO等气体排出,从而达到降碳的目的。
五、平炉炼钢法平炉炼钢法是一种较为传统的炼钢方法。
在平炉中,通过加入燃料燃烧产生的高温熔化铁水,并加入氧化剂进行脱碳和杂质去除。
平炉炼钢法的特点是炉内温度均匀,适合生产优质钢。
六、电炉炼钢法电炉炼钢法是利用电能熔化铁水并进行脱碳和杂质去除的方法。
电炉炼钢法适用于生产特种钢和合金钢,因为它能够精确地控制炉温和加入合金元素的时间。
七、炉渣与脱磷在炼钢过程中,通过加入造渣材料形成炉渣,炉渣可以将磷等杂质带出炉外,从而实现脱磷的目的。
炉渣的成分和性质对于炼钢过程的稳定性和钢的质量有重要影响。
八、脱硫与脱氧脱硫主要是通过加入脱硫剂(如石灰石)与铁水中的硫发生反应,生成硫化物进入炉渣中从而去除。
脱氧则是为了防止钢在凝固过程中产生裂纹,通过加入脱氧剂(如硅铁、铝铁等)与钢中的氧发生反应,生成不溶于钢的氧化物或硫化物。
总结:工业炼钢是一个复杂的过程,需要精确控制各种工艺参数和操作条件,以确保生产出高质量的钢材。
炼钢金属原料的种类及对铁水、废钢、铁合金的要求

【本章学习要点】本章学习炼钢金属原料的种类及对铁水、废钢、铁合金的要求,常用的铁合金的作用,非金属料的种类、作用及其要求。
原材料的质量和供应条件直接影响炼钢的技术经济指标。
保证原材料的质量,既指保证原材料化学成分和物理性质满足技术要求,还指原材料化学成分和物理性质保持稳定,这是达到优质、高产、低耗的前提条件。
炼钢原材料可分为金属料和非金属料两大类。
第一节金属料炼钢用的金属料主要有铁水、废钢、生铁、原料纯铁、海绵铁、中间合金材料和铁合金。
一、铁水铁水是转炉炼钢最主要的金属料,一般占转炉金属料70%以上。
铁水的成分、温度是否适当和稳定,对简化、稳定转炉操作,保证冶炼顺行以及获得良好的技术经济指标都十分重要。
转炉炼钢对铁水有如下要求:1)温度:温度是铁水带入炉内物理热多少的标志,是转炉炼钢热量的重要来源之一。
铁水温度过低,将造成炉内热量不足,影响熔池升温和元素的氧化过程,不利于化渣和去除杂质,还容易导致喷溅。
一般要求入炉铁水温度不低于l250℃,而且要稳定。
2) 硅:铁水中硅的氧化能放出大量的热量,生成的Si02是渣中主要的酸性成分,是影响熔渣碱度和石灰消耗量的关键因素。
铁水含硅高,则转炉可以多加废钢、矿石,提高钢水收得率,但铁水含硅量过高,会因石灰消耗量的增大而使渣量过大,易产生喷溅并加剧对炉衬的侵蚀,影响石灰熔化,从而影响脱磷、脱硫。
如果铁水含硅量过低,则不易成渣,对脱磷、脱硫也不利。
因此,要求铁水含硅质量分数在0.2%~0.6%。
3)锰:锰是钢中有益元素,对化渣、脱硫以及提高炉龄都是有益的。
但冶炼高锰生铁将使高炉焦比升高,为了节约锰矿资源和降低炼铁焦比,一般采用低锰铁水,锰质量分数为0.2%~0.4%。
4)磷:磷是一个强发热元素。
一般讲磷是有害元素,但高炉冶炼中无法去除磷。
因此,只能要求进入转炉的铁水含磷量尽量稳定,且铁水含磷越低越好。
5)硫:硫也是有害元素。
炼钢过程虽然可以去硫,但会降低炉子生产率,增加原材料消耗。
炼钢工艺步骤和流程

炼钢工艺步骤和流程炼钢是将生铁或钢水经过一系列工艺步骤,使其成分、温度、质量等指标达到一定要求的过程。
炼钢工艺步骤和流程对于钢铁生产至关重要,下面将介绍炼钢的一般工艺步骤和流程。
1. 原料准备。
炼钢的原料主要包括铁矿石、焦炭和石灰石。
在炼钢工艺开始之前,首先需要对原料进行准备。
铁矿石经过破碎、磨矿、浸出等工艺处理,得到高品位的铁矿石粉末;焦炭经过煤泥浸出、煤泥干燥、粉碎等工艺处理,得到高品位的焦炭粉末;石灰石经过破碎、磨矿、煅烧等工艺处理,得到高品位的石灰石粉末。
原料准备工作的好坏将直接影响炼钢的成品质量。
2. 炼铁。
炼钢的第一步是炼铁。
炼铁是将铁矿石还原成生铁的过程。
首先将原料铁矿石、焦炭和石灰石按一定比例混合,然后经过高温煅烧,使铁矿石中的氧化铁还原成金属铁。
炼铁的质量和效率对后续的炼钢过程有着直接的影响。
3. 转炉炼钢。
转炉炼钢是目前主要的炼钢方法之一。
在转炉炼钢过程中,首先将炼铁和废钢放入转炉中,然后加入适量的废钢、铁合金和石灰石。
通过高温燃烧,将废钢中的杂质燃尽,使废钢中的铁与炼铁混合,形成合金。
在燃烧的同时,石灰石中的氧化钙与炼铁中的磷、硫等杂质反应生成渣,将杂质排除。
经过一系列处理,最终得到合格的炼钢产品。
4. 电弧炼钢。
电弧炼钢是另一种常用的炼钢方法。
在电弧炼钢过程中,首先将炼铁和废钢放入电弧炉中,然后通过高压电弧加热炉内物料,使其熔化。
然后加入适量的废钢、铁合金和石灰石。
通过高温燃烧和电弧加热,将废钢中的杂质燃尽,使废钢中的铁与炼铁混合,形成合金。
在燃烧和电弧加热的同时,石灰石中的氧化钙与炼铁中的磷、硫等杂质反应生成渣,将杂质排除。
经过一系列处理,最终得到合格的炼钢产品。
5. 连铸。
连铸是炼钢的最后一道工艺环节。
在连铸过程中,将炼钢液体倒入连铸机中,经过连铸机的一系列处理,将炼钢液体冷却凝固成坯料。
然后通过切割、冷却等工艺处理,得到成品钢材。
总结。
炼钢工艺步骤和流程是一个复杂而又精密的过程,需要各个环节的配合和协调。
炼钢原材料知识介绍

炼钢原材料知识介绍原材料分类按性质分类,转炉原材料分为金属料和非金属料两类。
金属实包括铁水(生铁)、废钢、铁合金;非金属实包括石灰、萤石、白云石、合成渣剂、氧气、氩气、氮气,此外还有耐火材料等。
按用途分类,原材料分为金属料、造渣剂、化渣剂、氧化剂、冷却剂和增碳剂等。
1、金属料(1)、铁水(生铁)铁水是转炉的主要金属料,占金属装入量的70%~100%。
为了保证冶炼过程顺利,铁水必须满足要求。
①、铁水温度温度是铁水带入炉内物理热多少的标志,这部分热量是转炉热量的重要来源之一。
对转炉,铁水温度过低将造成炉内热量不足,影响熔池升温和元素氧化进程,同时不利于化渣和去除杂质,还容易导致喷溅。
因此转炉通常要求铁水温度必须大于1250℃。
②、铁水成分硅硅是铁水中主要发热元素之一,生成的Si O2是渣中主要的酸性成分,是决定炉渣碱度和石灰消耗量的关键因素。
通常,在铁水不经深度预处理时,转炉铁硅含量以在0.3%~0.8%为宜,前后波动应为0.15%。
锰锰是钢中的有益元素,铁水中的锰含量高对炼钢有好处,但是冶炼高锰生铁将导致高炉焦比提高,生产率下降。
锰在炼钢中的作用是:加速石灰的熔化,促进成渣并减少萤石用量;有利于减少顶枪粘枪和提高炉龄;有利于提高终点钢水残锰量,和提高脱硫效果。
(2)、废钢废钢是转炉主要金属料之一,它还是冷却效果比较稳定的冷却剂。
增加转炉废钢用量可以降低炼钢成本、能耗和炼钢辅助材料消耗。
废钢按来源可分为:本厂废钢、社会废钢废钢质量对转炉冶炼技术经济指标有明显影响,从合理使用和冶炼工艺出发,对废钢的要求是;①、不同性质废钢应分类存放,以避免贵重元素损失和熔炼出废品。
外观相似而成分不同的废钢不能邻近堆放。
在多数钢种中两种元素不常同时存在的两类废钢不能邻近堆放。
②、废钢入炉前应仔细检查,严防混入封闭器皿,爆炸物和毒品;严防混入钢种成分限制的元素和铅、锌、铜等金属。
③、废钢应清洁干燥、少锈,应尽量避免带入泥土沙石、油污、耐火材料和炉渣等杂质。
炼钢常用原辅料清单
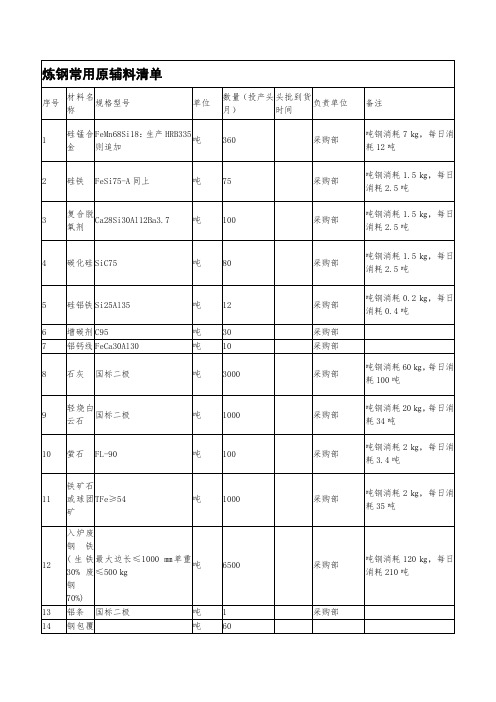
萤石
FL-90
吨
100
采购部
吨钢消耗2㎏,每日消耗3.4吨
11
铁矿石或球团矿
TFe≥54
吨
1000
采购部
吨钢消耗2㎏,每日消耗35吨
12
入炉废钢铁(生铁30%废钢70%)
最大边长≤1000㎜单重≤500㎏
吨
6500
采购部
吨钢消耗120㎏,每日消耗210吨
13
铝条
国标二极
吨
1
采购部
14
钢包覆盖剂
吨
60
15
中包覆盖剂
吨
60
16
(冷却用)废钢
最大边长≤400㎜单重≤25㎏
吨
100
17
(开炉用)焦炭
冶金焦
吨
10
注:在不影响生产的情况下,上述订货数额可分批到货,但头批需在投产前15天到
序号
材料名称
规格型号
单位
数量(投产头月)
头批到货时间
负n68Si18:生产HRB335则追加
吨
360
采购部
吨钢消耗7㎏,每日消耗12吨
2
硅铁
FeSi75-A同上
吨
75
采购部
吨钢消耗1.5㎏,每日消耗2.5吨
3
复合脱氧剂
Ca28Si30Al12Ba3.7
吨
100
采购部
吨钢消耗1.5㎏,每日消耗2.5吨
4
碳化硅
SiC75
吨
80
采购部
吨钢消耗1.5㎏,每日消耗2.5吨
5
硅铝铁
Si25Al35
吨
12
采购部
吨钢消耗0.2㎏,每日消耗0.4吨
炼钢原材料

炼钢原材料可分为金属料和非金属料两大类。
第一节金属料炼钢用的金属料主要有铁水(转炉)、废钢、生铁、原料纯铁、海绵铁、中间合金材料和铁合金。
二、废钢废钢是电炉炼钢最主要的金属料,其用量约占金属料的70%~90%。
按来源,废钢分为返回废钢、拆旧废钢、加工工业的边角余料及垃圾废钢等。
返回废钢属于优质炉料。
它是在炼钢、轧钢与锻压或精整过程中产生的,如炼钢车间的短尺、废锭、汤道、注余和轧钢或锻压车间的切头、切尾及其他形式的废品等。
返回废钢的加工准备工作量小,并均按元素及其含量的多少分类分组保管,因此可随时随地回炉使用。
在电炉钢生产上,使用返回废钢具有很大的经济意义,这是因为利用返回废钢作为炉料,可采用不氧化法或返吹法进行冶炼,不仅能够大量地回收贵重合金元素,而且也能降低成本、缩短冶炼时间,进而提高电炉的生产率。
返回废钢的种类繁多,各个厂家根据钢种、成分、用途等均进行严格的分类分组。
从合理使用的角度出发,分得越细越好,这样才能保证冶炼能够顺利的进行。
拆除各种废旧机器、汽车、轮船、报废的钢轨与建筑物的构件、各种废旧武器及工具等所获的废钢称为拆旧废钢。
工业越高度发达的国家或地区,拆旧废钢占废钢总量的比例越大,然而它的返回周期较长,往往需要几年,甚至几十年才能回炉使用。
在钢铁制品的制造过程中,产生的各种边角余料、车屑及料头等,也是废钢的主要来源之一。
除车屑外,加工工业的废钢如果没有混入其他杂质及有害元素,只要经过简单的打包、压块等处理,就可很快的回炉使用。
垃圾废钢主要是从城市的垃圾中回收罐头筒轻薄料,它们之中含有较高的Sn或Zn;在使用前须将其分离。
废钢按形状、尺寸和对它的成分及密度的要求,可粗略地分为重型废钢、中型废钢、小型废钢、轻型废钢、渣钢和车屑等类。
不同性质的废钢应分类存放。
为了准确掌握外来废钢的化学成分。
通常是采用多点取样进行分析,并以分析的平均成分作为配料计算的依据。
试样的分析方法有火花鉴别和手提光谱仪及化学分析等多种。
炼钢的工艺流程
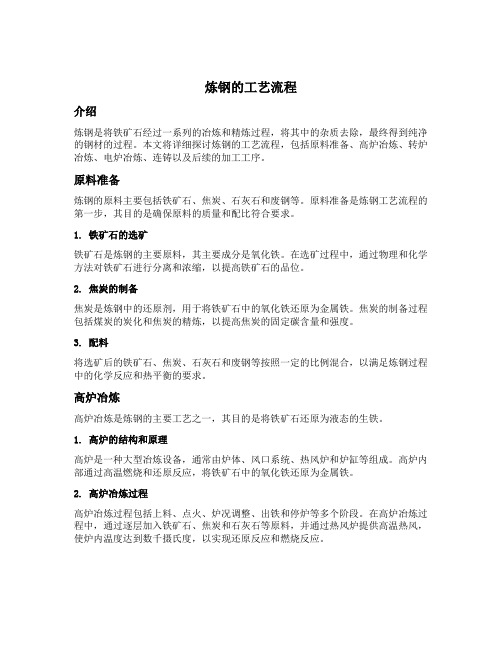
炼钢的工艺流程介绍炼钢是将铁矿石经过一系列的冶炼和精炼过程,将其中的杂质去除,最终得到纯净的钢材的过程。
本文将详细探讨炼钢的工艺流程,包括原料准备、高炉冶炼、转炉冶炼、电炉冶炼、连铸以及后续的加工工序。
原料准备炼钢的原料主要包括铁矿石、焦炭、石灰石和废钢等。
原料准备是炼钢工艺流程的第一步,其目的是确保原料的质量和配比符合要求。
1. 铁矿石的选矿铁矿石是炼钢的主要原料,其主要成分是氧化铁。
在选矿过程中,通过物理和化学方法对铁矿石进行分离和浓缩,以提高铁矿石的品位。
2. 焦炭的制备焦炭是炼钢中的还原剂,用于将铁矿石中的氧化铁还原为金属铁。
焦炭的制备过程包括煤炭的炭化和焦炭的精炼,以提高焦炭的固定碳含量和强度。
3. 配料将选矿后的铁矿石、焦炭、石灰石和废钢等按照一定的比例混合,以满足炼钢过程中的化学反应和热平衡的要求。
高炉冶炼高炉冶炼是炼钢的主要工艺之一,其目的是将铁矿石还原为液态的生铁。
1. 高炉的结构和原理高炉是一种大型冶炼设备,通常由炉体、风口系统、热风炉和炉缸等组成。
高炉内部通过高温燃烧和还原反应,将铁矿石中的氧化铁还原为金属铁。
2. 高炉冶炼过程高炉冶炼过程包括上料、点火、炉况调整、出铁和停炉等多个阶段。
在高炉冶炼过程中,通过逐层加入铁矿石、焦炭和石灰石等原料,并通过热风炉提供高温热风,使炉内温度达到数千摄氏度,以实现还原反应和燃烧反应。
转炉冶炼是炼钢的另一种常用工艺,其主要特点是采用氧气吹炼,将生铁转化为钢水。
1. 转炉的结构和原理转炉是一种承压容器,通常由炉体、氧气吹炼系统和倾炉机构等组成。
转炉内部通过氧气吹炼和搅拌,将生铁中的碳和其他杂质氧化除去,从而得到低碳钢水。
2. 转炉冶炼过程转炉冶炼过程包括预热、装料、吹炼、倾炉和取样等多个阶段。
在转炉冶炼过程中,通过预热转炉、加入生铁和废钢等原料,并通过氧气吹炼和搅拌,使炉内温度升高并实现氧化还原反应,最终得到符合要求的钢水。
电炉冶炼电炉冶炼是一种利用电能将废钢和生铁等原料进行冶炼的工艺,其主要特点是能够灵活调整炉温和合金成分。
- 1、下载文档前请自行甄别文档内容的完整性,平台不提供额外的编辑、内容补充、找答案等附加服务。
- 2、"仅部分预览"的文档,不可在线预览部分如存在完整性等问题,可反馈申请退款(可完整预览的文档不适用该条件!)。
- 3、如文档侵犯您的权益,请联系客服反馈,我们会尽快为您处理(人工客服工作时间:9:00-18:30)。
目前使用状态
吨钢消耗
优点
是否推荐
钢水深脱氧
未使用
不增硅、不增氮、改善钢水 流动性、吸附夹杂物
是
12、增碳剂
用途
目前使用状态
吨钢消耗
优点
是否推荐
增碳
使用
0.5 kg/t
S、P含量低,增碳效果好, 碳的收得率咼
是
13、转炉终渣改质
用途
目前使用状态
吨钢消耗
优点
是否推荐
调整转炉终渣的停用
使终渣成为熔点高、粘性较是
碱度
大的炉渣,便于溅渣护炉
精炼前后的终脱
停用
依据脱氧兀素的实际脱氧
是
氧处理
效果有机组合的复合产品
4、钒氮合金
用途
目前使用状态
吨钢消耗
优点
是否推荐
钒兀素的添加剂
使用钒铁
具有较咼的钒利用率
特殊钢种需
要
5、铝质脱氧剂
用途
目前使用状态
吨钢消耗
优点
是否推荐
去除渣中T[0]
停用
改善精炼渣系,有利于吸附 夹杂和控制夹杂,提高脱硫
是
6、锰碳合金球
未使用
适于转炉炼钢脱氧,能有效 改善钢水流动性
是
9、硅锰合金
用途
目前使用状态
吨钢消耗
优点
是否推荐
合金
使用
4.65kg/t
脱氧效果好,产生脱氧产物
是|
易上浮。
10、硅钙合金
用途
目前使用状态
吨钢消耗
优点
是否推荐
脱氧剂、脱硫剂
使用(硅钙线)
0.6 kg/t
能充分提高钙在脱氧和非 金属夹杂性处理中的作用
是
11、硅钙铝复合脱氧剂
用途
目前使用状态ቤተ መጻሕፍቲ ባይዱ
吨钢消耗
优点
是否推荐
咼效增碳材料
未使用过
密度大、纯度高,可达到较 高稳定的回收率
是
7、MnO基无氟复合造渣剂
用途
目前使用状态
吨钢消耗
优点
是否推荐
化渣剂
未使用
全程化渣,不喷溅、不返干、 不粘枪、缩短冶炼周期,提 高产量
是
&多功能脱氧剂(硅钙碳)
用途
目前使用状态
吨钢消耗
优点
是否推荐
强脱氧、脱硫
沙钢转炉炼钢原辅料使用情况
1、硅铝钡钙铁合金
用途
目前使用状态
吨钢消耗
优点
是否推荐
咼效复合脱氧剂
停用
能充分提高钙在脱氧和非 金属夹杂性处理中的作用
是
2、硅铝钡合金
用途
目前使用状态
吨钢消耗
优点
是否推荐
脱氧、脱硫
停用
比单独使用铝块或硅铁等 单一合金效果会更显著
是
3、复合脱氧剂
用途
目前使用状态
吨钢消耗
优点
是否推荐