厚壁复合压力容器的超声无损检测软件的开发
压力容器检验中TOFD超声成像检测技术应用探讨
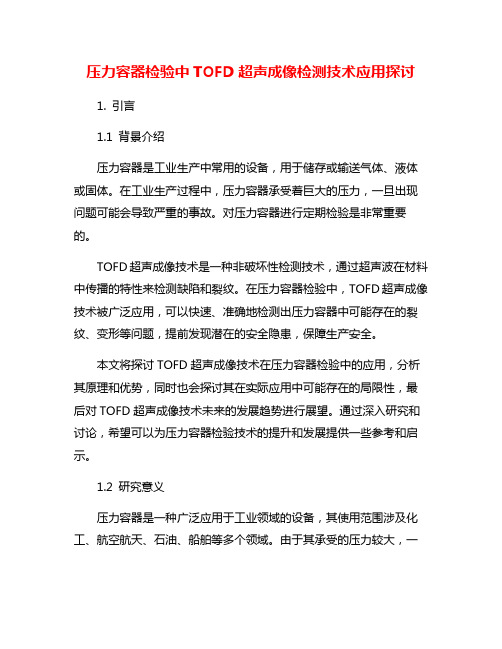
压力容器检验中TOFD超声成像检测技术应用探讨1. 引言1.1 背景介绍压力容器是工业生产中常用的设备,用于储存或输送气体、液体或固体。
在工业生产过程中,压力容器承受着巨大的压力,一旦出现问题可能会导致严重的事故。
对压力容器进行定期检验是非常重要的。
TOFD超声成像技术是一种非破坏性检测技术,通过超声波在材料中传播的特性来检测缺陷和裂纹。
在压力容器检验中,TOFD超声成像技术被广泛应用,可以快速、准确地检测出压力容器中可能存在的裂纹、变形等问题,提前发现潜在的安全隐患,保障生产安全。
本文将探讨TOFD超声成像技术在压力容器检验中的应用,分析其原理和优势,同时也会探讨其在实际应用中可能存在的局限性,最后对TOFD超声成像技术未来的发展趋势进行展望。
通过深入研究和讨论,希望可以为压力容器检验技术的提升和发展提供一些参考和启示。
1.2 研究意义压力容器是一种广泛应用于工业领域的设备,其使用范围涉及化工、航空航天、石油、船舶等多个领域。
由于其承受的压力较大,一旦发生泄漏或爆炸事故,将会带来严重的安全隐患和经济损失。
因此对压力容器进行定期检验和维护显得尤为重要。
研究TOFD超声成像技术在压力容器检验中的应用意义重大。
通过深入探讨该技术在压力容器检验中的实际应用效果和局限性,不仅可以为提高压力容器检验的准确性和效率提供技术支持,还可以为相关行业的安全生产和设备维护提供重要的技术保障。
在未来的研究中,进一步完善TOFD超声成像技术,弥补其在一些特定情况下的局限性,将有助于推动其在压力容器检验中的广泛应用和发展。
2. 正文2.1 TOFD超声成像技术原理TOFD是指时间域衍射聚焦技术,是一种利用超声波传播特性进行缺陷检测和成像的技术。
其原理是通过向被检测物体表面施加短脉冲超声波,然后通过不同接收探头接收由缺陷或界面反射回来的超声波信号。
TOFD技术利用传统超声技术中的发射和接收探头进行双探头扫描,通过测量接收信号的时间差来确定缺陷的位置和大小。
压力容器的超声检测技术及应用
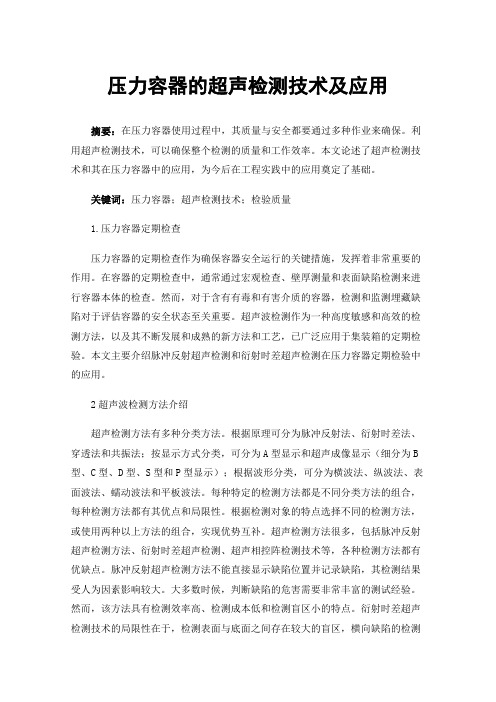
压力容器的超声检测技术及应用摘要:在压力容器使用过程中,其质量与安全都要通过多种作业来确保。
利用超声检测技术,可以确保整个检测的质量和工作效率。
本文论述了超声检测技术和其在压力容器中的应用,为今后在工程实践中的应用奠定了基础。
关键词:压力容器;超声检测技术;检验质量1.压力容器定期检查压力容器的定期检查作为确保容器安全运行的关键措施,发挥着非常重要的作用。
在容器的定期检查中,通常通过宏观检查、壁厚测量和表面缺陷检测来进行容器本体的检查。
然而,对于含有有毒和有害介质的容器,检测和监测埋藏缺陷对于评估容器的安全状态至关重要。
超声波检测作为一种高度敏感和高效的检测方法,以及其不断发展和成熟的新方法和工艺,已广泛应用于集装箱的定期检验。
本文主要介绍脉冲反射超声检测和衍射时差超声检测在压力容器定期检验中的应用。
2超声波检测方法介绍超声检测方法有多种分类方法。
根据原理可分为脉冲反射法、衍射时差法、穿透法和共振法;按显示方式分类,可分为A型显示和超声成像显示(细分为B 型、C型、D型、S型和P型显示);根据波形分类,可分为横波法、纵波法、表面波法、蠕动波法和平板波法。
每种特定的检测方法都是不同分类方法的组合,每种检测方法都有其优点和局限性。
根据检测对象的特点选择不同的检测方法,或使用两种以上方法的组合,实现优势互补。
超声检测方法很多,包括脉冲反射超声检测方法、衍射时差超声检测、超声相控阵检测技术等,各种检测方法都有优缺点。
脉冲反射超声检测方法不能直接显示缺陷位置并记录缺陷,其检测结果受人为因素影响较大。
大多数时候,判断缺陷的危害需要非常丰富的测试经验。
然而,该方法具有检测效率高、检测成本低和检测盲区小的特点。
衍射时差超声检测技术的局限性在于,检测表面与底面之间存在较大的盲区,横向缺陷的检测不可靠。
这种不可靠性主要是由于衍射时差超声检测的非平行扫描图像中横向条带缺陷或平面缺陷的显示容易被误判为点缺陷。
当然,衍射时差超声检测有其独特的优势,主要在于检测结果可以记录并存储在图像中,检测灵敏度高,缺陷高度和深度的测量精度高。
压力容器检测技术的探讨

压力容器检测技术的探讨【摘要】介绍了TOFD超声成像检测技术在压力容器中的应用,TOFD法具有检测效率高、检测周期短、无辐射等优点。
由于其自身优势,从长远来看,在厚壁容器检测方面,必将成为UT、RT的替代技术,国外已经将其广泛地应用到特种设备检验中【关键词】超声成像压力容器检验缺陷1 TOFD超声成像检测技术的原理TOFD超声成像检测技术是20世纪70年代由英国哈威尔无损检测中心首先提出的。
超声波入射到线形缺陷时,在缺陷的两端除普通的反射波外还会产生衍射波,衍射能量可以在很大角度范围内传播,基于这个原理,TOFD技术主要采用一发一收两个探头,发射探头发射横向纵波,沿表面传播的一束声波和工件背面的镜面反射被接收探头接收,形成固有参考信号:焊缝中的横向纵波遇到缺陷后在缺陷尖端产生衍射波,如果缺陷有足够的自身高度,缺陷两端点的信号在时间上将是可分辨的,根据所记录的衍射信号传播时差就可以判定缺陷高度的量值。
2 检测2.1 被检设备要求清除被检设备扫查区域内焊接飞溅、附着物、涂层等影响探头移动、耦合和声束入射的因素。
采用有效且适用于被检材料的介质作为耦合剂,通常使用水、耦合凝胶或软膏、润滑脂和油。
为了改善超声耦合和保护被检工件,可以采用环保润湿剂和防腐剂等水添加剂。
如果被检工件温度低于0℃(320F),可以采用甲醇或相似的介质。
如果被检工件温度过高,应该对被检工件表面或探头进行冷却或使用专门设计的高温耦合剂。
选用的耦合介质应在一定的温度范围内保证稳定可靠的检测。
2.2 检测仪器TOFD检测系统一般由专用计算机系统、软件、探头和探头支架几部分组成,为了适应厚壁容器的检测需要,一般具有多个通道,用于实现探头类型及型号的组合,TOFD检测过程中,一般根据所检工件的材料、厚度选择探头的型号以及组合方式。
(1)探头选择;75mm以下的工件一般使用单探头扫描,检测铁素体钢时可以根据表1选用合适的探头,对于奥氏体或其它高衰减材料,需要降低探头公称频率和增加晶片尺寸。
压力容器检验中TOFD超声成像检测技术应用探讨
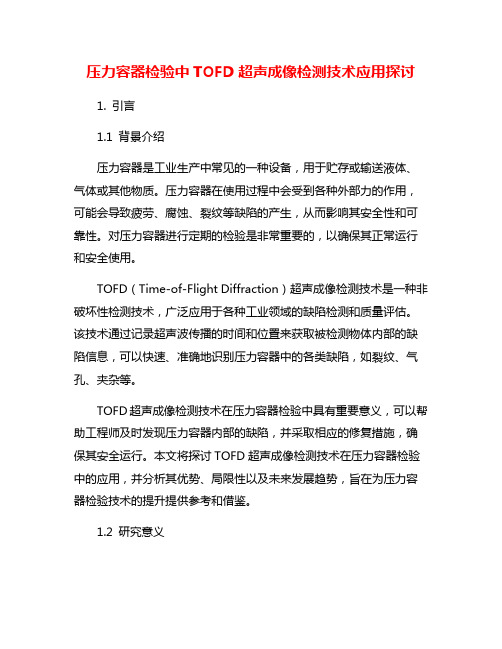
压力容器检验中TOFD超声成像检测技术应用探讨1. 引言1.1 背景介绍压力容器是工业生产中常见的一种设备,用于贮存或输送液体、气体或其他物质。
压力容器在使用过程中会受到各种外部力的作用,可能会导致疲劳、腐蚀、裂纹等缺陷的产生,从而影响其安全性和可靠性。
对压力容器进行定期的检验是非常重要的,以确保其正常运行和安全使用。
TOFD(Time-of-Flight Diffraction)超声成像检测技术是一种非破坏性检测技术,广泛应用于各种工业领域的缺陷检测和质量评估。
该技术通过记录超声波传播的时间和位置来获取被检测物体内部的缺陷信息,可以快速、准确地识别压力容器中的各类缺陷,如裂纹、气孔、夹杂等。
TOFD超声成像检测技术在压力容器检验中具有重要意义,可以帮助工程师及时发现压力容器内部的缺陷,并采取相应的修复措施,确保其安全运行。
本文将探讨TOFD超声成像检测技术在压力容器检验中的应用,并分析其优势、局限性以及未来发展趋势,旨在为压力容器检验技术的提升提供参考和借鉴。
1.2 研究意义压力容器是工业生产中常见的设备,承压工作时需保证安全运行,而压力容器的质量和可靠性直接影响整个生产过程的稳定性和安全性。
对压力容器进行检验是非常重要的。
TOFD超声成像检测技术是一种先进的无损检测技术,通过对工件内部的缺陷和异物进行高分辨率成像,能够对压力容器进行全面、准确的评估。
研究TOFD超声成像检测技术在压力容器检验中的应用意义重大。
TOFD技术可以实现对压力容器内部各个部位的全面扫描,能够及时发现细小缺陷并进行准确定位,有助于预防潜在的安全隐患。
TOFD技术具有高灵敏度和高精度的优势,能够检测出非常小的缺陷,为压力容器的质量控制提供了可靠的技术支持。
TOFD技术对于检测多种类型的缺陷和异物也具有很好的适应性,能够满足不同压力容器的检测需求。
研究TOFD超声成像检测技术在压力容器检验中的应用具有重要的意义,可以提升压力容器检验的效率和准确性,为保障工业生产的安全和稳定性提供有力支持。
大厚壁高强钢复合板13MnNiMoR+S31603压力容器设计、制造、检验
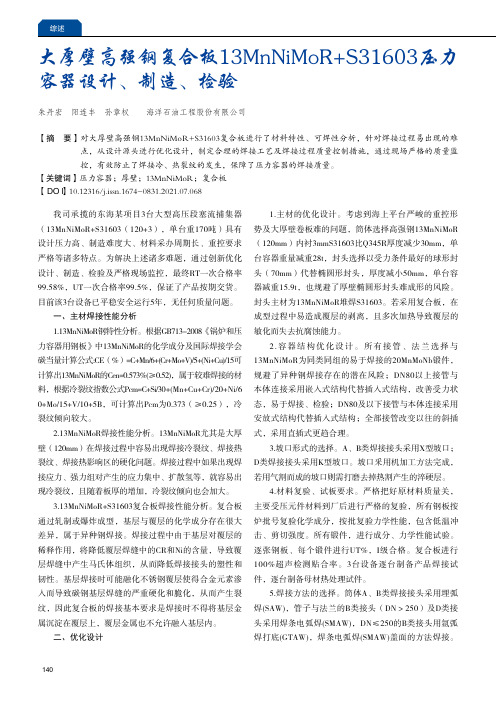
我司承揽的东海某项目3台大型高压段塞流捕集器(13MnNiMoR+S31603(120+3),单台重170吨)具有设计压力高、制造难度大、材料采办周期长、重控要求严格等诸多特点。
为解决上述诸多难题,通过创新优化设计、制造、检验及严格现场监控,最终RT一次合格率99.58%,UT一次合格率99.5%,保证了产品按期交货。
目前该3台设备已平稳安全运行5年,无任何质量问题。
一、主材焊接性能分析1.13MnNiMoR钢特性分析。
根据GB713-2008《锅炉和压力容器用钢板》中13MnNiMoR的化学成分及国际焊接学会碳当量计算公式:CE(%)=C+Mn/6+(Cr+Mo+V)/5+(Ni+Cu)/15可计算出13MnNiMoR的Cen=0.573%(≥0.52),属于较难焊接的材料,根据冷裂纹指数公式Pcm=C+Si/30+(Mn+Cu+Cr)/20+Ni/6 0+Mo/15+V/10+5B,可计算出Pcm为0.373(≥0.25),冷裂纹倾向较大。
2.13MnNiMoR焊接性能分析。
13MnNiMoR尤其是大厚壁(120mm)在焊接过程中容易出现焊接冷裂纹、焊接热裂纹、焊接热影响区的硬化问题。
焊接过程中如果出现焊接应力、强力组对产生的应力集中、扩散氢等,就容易出现冷裂纹,且随着板厚的增加,冷裂纹倾向也会加大。
3.13MnNiMoR+S31603复合板焊接性能分析。
复合板通过轧制或爆炸成型,基层与覆层的化学成分存在很大差异,属于异种钢焊接。
焊接过程中由于基层对覆层的稀释作用,将降低覆层焊缝中的CR和Ni的含量,导致覆层焊缝中产生马氏体组织,从而降低焊接接头的塑性和韧性。
基层焊接时可能融化不锈钢覆层使得合金元素渗入而导致碳钢基层焊缝的严重硬化和脆化,从而产生裂纹,因此复合板的焊接基本要求是焊接时不得将基层金属沉淀在覆层上,覆层金属也不允许融入基层内。
二、优化设计1.主材的优化设计。
考虑到海上平台严峻的重控形势及大厚壁卷板难的问题,筒体选择高强钢13MnNiMoR (120mm)内衬3mmS31603比Q345R厚度减少30mm,单台容器重量减重28t,封头选择以受力条件最好的球形封头(70mm)代替椭圆形封头,厚度减小50mm,单台容器减重15.9t,也规避了厚壁椭圆形封头难成形的风险。
大型压力容器的超声波无损检测.doc
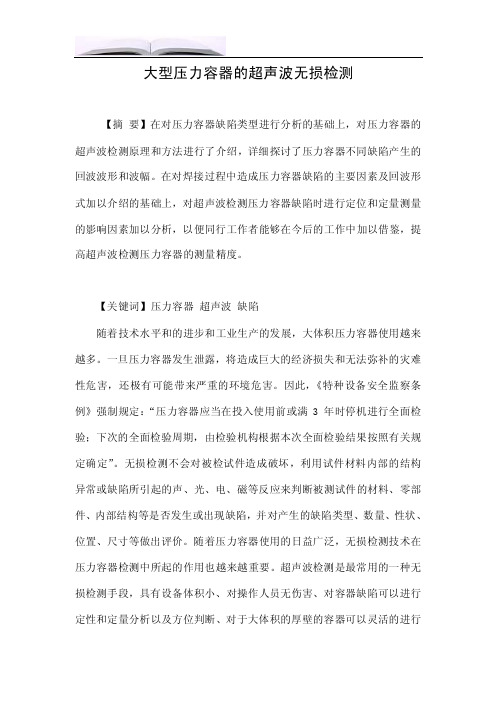
大型压力容器的超声波无损检测【摘要】在对压力容器缺陷类型进行分析的基础上,对压力容器的超声波检测原理和方法进行了介绍,详细探讨了压力容器不同缺陷产生的回波波形和波幅。
在对焊接过程中造成压力容器缺陷的主要因素及回波形式加以介绍的基础上,对超声波检测压力容器缺陷时进行定位和定量测量的影响因素加以分析,以便同行工作者能够在今后的工作中加以借鉴,提高超声波检测压力容器的测量精度。
【关键词】压力容器超声波缺陷随着技术水平和的进步和工业生产的发展,大体积压力容器使用越来越多。
一旦压力容器发生泄露,将造成巨大的经济损失和无法弥补的灾难性危害,还极有可能带来严重的环境危害。
因此,《特种设备安全监察条例》强制规定:“压力容器应当在投入使用前或满3年时停机进行全面检验;下次的全面检验周期,由检验机构根据本次全面检验结果按照有关规定确定”。
无损检测不会对被检试件造成破坏,利用试件材料内部的结构异常或缺陷所引起的声、光、电、磁等反应来判断被测试件的材料、零部件、内部结构等是否发生或出现缺陷,并对产生的缺陷类型、数量、性状、位置、尺寸等做出评价。
随着压力容器使用的日益广泛,无损检测技术在压力容器检测中所起的作用也越来越重要。
超声波检测是最常用的一种无损检测手段,具有设备体积小、对操作人员无伤害、对容器缺陷可以进行定性和定量分析以及方位判断、对于大体积的厚壁的容器可以灵活的进行等特点,本研究针对大体积压力容器尺寸大、焊缝长、一般容器器壁较厚的特点,对使用超声波技术对压力容器各部位缺陷进行无损检测方法做一介绍。
1 压力容器缺陷类型压力容器的缺陷包括表面缺陷和内部缺陷两大类,表面缺陷可以直接观察到,内部缺陷主要是焊接缺陷和材料本身的杂质缺陷。
压力容器缺陷类型和产生原因如表1所示。
2 压力容器超声波检测方法超声波检测压力容器过程中,主要有三种方法:一种是脉冲反射法,另一种是穿透法,还有一种是衍射时差法,各自原理如下。
2.1 脉冲反射法脉冲反射法的检测原理如图1所示。
锅炉压力容器检测中超声波探伤技术应用
锅炉压力容器检测中超声波探伤技术应用锅炉压力容器作为工业生产设备中的重要组成部分,其安全性能直接关系到生产过程中的安全生产。
因此,对锅炉压力容器进行定期的检测和维护,是确保生产安全和生产效益的必要手段之一。
本文讨论了超声波探伤技术在锅炉压力容器检测中的应用。
超声波探伤技术是目前应用最广泛的一种非破坏性检测方法之一,其基本原理是将超声波传入被检测材料中,根据超声波被材料内部结构所反射的信号,来探测材料内部的缺陷和变形情况。
这种技术因为具有高精度、高可靠性、无破坏性等优点,被广泛应用于许多工业领域中,其中包括锅炉压力容器的检测。
1.壁厚检测锅炉压力容器的壁厚是制造过程中关注的重点,因为这直接关系到容器的承受能力。
超声波探伤技术可以通过探测超声波在物体内部的传播速度和反射情况,来测量容器壁厚。
探测设备会将发出的超声波穿过材料,然后记录回波时间和振幅,通过分析回波信息,就能确定壁厚的大小和位置。
2.裂纹检测锅炉压力容器在运行过程中,由于振动、疲劳等因素,容易出现裂纹情况。
这些裂纹虽然看似微小,但随着时间的推移,会逐渐加大,最终引起设备事故。
超声波探伤技术可以通过测量物体内部反射的超声波信号,来检测容器中是否存在裂纹,并对其进行定位和评估。
3.焊接缺陷检测焊接是制造锅炉压力容器的关键步骤之一。
焊接缺陷不仅会降低容器的强度和密封性,还会进一步恶化裂纹等缺陷的发展。
超声波探伤技术可以通过测量焊缝区域内部反射的超声波信号,来检测焊接缺陷的类型和大小,以及判断焊接部位的质量。
在实际的应用中,超声波探伤技术可以结合其它非破坏性检测技术一起使用,以提高检测的准确性和可靠性。
同时,也需要在探测设备的选择、操作方法、探头的选择等方面进行专业的指导和培训,以确保检测结果的有效性和可靠性。
反应堆压力容器厚壁焊缝的相控阵超声检测
核电厂的反应堆压力容器(RPV)属放射性介质的第二道防线,用来包容和固定反应堆堆芯和堆内构件,全寿期均工作在高温、高压、高辐照等极端复杂条件下,是保障核电厂安全运行的重要设备。
核电厂在役检查规范和检查大纲中,RPV焊缝的超声检测是强制性要求,其检测结果是评定RPV结构完整性,进而评估核电设备运行寿命的重要依据。
目前国内通常采用常规超声检测技术进行RPV焊缝检测,该技术需采用多达上百个探头进行组合检测。
前期准备工作(参数设置、探头标定、探头校准等)和现场实施过程(探头安装、更换等)所需时间达到整条焊缝检测总工作量的30%以上,同时大幅度增加了人员受辐照时间和异物引入风险。
随着材料、微加工、电子和计算机技术的飞速发展,相控阵(PA)超声检测技术逐渐广泛应用在无损检测领域,PA超声检测技术在缩短作业人员受辐照时间、提高检测效率、提高检测稳定性等方面具有明显的优势,应用前景巨大。
检测对象RPV筒体对接焊缝(图1中①②)的基体材料通常为6MnD5或SA508-3低合金钢,焊接方式为埋弧自动焊,填充形式为多层多道焊,坡口形式为U形坡口,焊缝厚度常为130~260 mm,如图2所示,同时考虑到耐腐蚀、耐辐照的特殊要求,内壁有约7 mm厚的不锈钢堆焊层。
如何在减少盲区的同时具备足够的穿透力,实现近表面缺陷和远程缺陷的超声检测能力,是RPV超声检测技术的关键。
图1 RPV筒体对接焊缝结构示意图2 RPV筒体对接焊缝坡口结构示意技术分析常规超声检测常规RPV筒体对接焊缝的超声检测工艺通常采用多种探头组合的检测方式,缺陷探测和尺寸定量分别进行。
由于其需采用多个常规超声探头进行组合扫查,故其操作灵活度较差、检测工作量大、零散部件易损坏掉落;尤其是在发现不同深度的超标显示时,需要更换不同聚焦深度的定量探头进行分层检测,极大降低了检测工作的安全性、稳定性和效率性。
相控阵超声检测与常规超声探头采用一个压电晶片产生超声波不同,相控阵超声检测技术基于惠更斯原理,其探头由多个小的压电晶片按照一定序列组成,通过电子控制,按照预定的规则和时序激发部分或全部晶片,能实现各波阵面叠加,达到声束聚焦、声束偏转、声束位移等效果。
超声波检测技术在压力容器检测中的应用
超声波检测技术在压力容器检测中的应用一、超声波检测技术的原理超声波检测技术是利用超声波在材料中的传播和反射特性来对材料内部的缺陷进行检测。
当超声波穿过材料时,会因为材料的密度、硬度、形状等因素而发生反射或折射,从而形成回波。
通过检测这些回波的特性,可以精确地判断材料是否存在缺陷。
在压力容器的检测中,超声波可以穿透容器壁厚,对容器内部的缺陷进行高精度、非破坏性的检测。
超声波检测技术可以检测容器内部的腐蚀、裂纹、疲劳损伤等缺陷,为压力容器的安全运行提供了可靠的保障。
1. 高精度:超声波检测技术可以对压力容器内部的缺陷进行高精度的检测,能够发现微小的裂纹或腐蚀。
2. 非破坏性:超声波检测技术是一种非破坏性的检测方法,可以在不破坏材料的情况下进行检测,不会对压力容器的结构和性能产生影响。
3. 实时性:超声波检测可以实时监测压力容器的内部缺陷,及时发现问题并进行处理,确保了压力容器的安全运行。
4. 适用性广:超声波检测技术适用于各种材料和结构的压力容器,具有很好的通用性和适用性。
5. 环保节能:超声波检测技术无需使用化学试剂或产生废弃物,具有良好的环保性和节能性。
1. 钢制压力容器的裂纹检测:钢制压力容器在长期使用中容易出现裂纹,而超声波检测技术可以对其进行高精度的裂纹检测,确保了压力容器的安全使用。
3. 汽车制动气室的疲劳损伤检测:汽车制动气室在长期使用中容易出现疲劳损伤,超声波检测可以对其进行全面的疲劳损伤检测,确保了汽车的制动系统的安全运行。
当前,随着材料科学、传感技术、数据处理技术的不断发展,超声波检测技术在压力容器检测领域也在不断取得创新和突破。
未来,超声波检测技术在压力容器检测中的发展方向包括以下几个方面:1. 大数据分析:利用大数据分析技术结合超声波检测数据,实现对压力容器内部缺陷的智能识别和预测,提高检测的精度和效率。
2. 联网监测:将超声波检测技术与物联网技术结合,实现对压力容器的远程监测和及时预警,提高了对压力容器安全的响应速度。
压力容器超声检测技术及应用
压力容器超声检测技术及应用摘要:压力容器是存在潜在危险的承压类特种设备,它已被广泛应用于石油、化工、航空和航天等领域,是与人们日常生活密切相关的重要基础设施。
在压力容器的设计、制造、安装和使用等环节中,无损检测作为一种无破坏性的质量检测手段,在质量控制和安全使用中发挥着重要作用。
本文简要论述了超声检测技术及其在压力容器特种设备中的应用。
关键词:压力管道;压力容器;无损检测技术;创新在压力容器定期检验中,超声检测是目前最为简便、有效的检测手段之一,笔者认为,随着检测技术的日益发展,在实际工作中,对缺陷的定位、定量、定性将会更加精确,这对特种设备的安全将会是更大的一层保障。
一、无损检测的技术相关概述(一)无损检测技术定义传统的工业生产运作,往往是在人们固定的经验下按照固化的程序进行。
而无损检测技术的有效应用,大大提高了工业生产过程中各类复杂信息的有效收集与整理,同时能够进行一些编程处理。
一旦工业压力容器及压力管护在生产过程中发生了泄漏等问题,借助无损检测技术,结合对以往运行数据与信息的分析,有效解决这些问题,提高了现代工业生产的安全性、稳定性与高效性。
程序设计是无损检测技术应用的前提,针对压力管道与压力容器的运行情况制定相应的逻辑运算规则,系统在这些规则下进行数据的运算,进而实现对电力系统、工业机械等的自动化控制。
此外,借助无损检测技术还能够根据设定的逻辑关系,在复杂的运行路线中选择最佳的路径,以及在操作方面具备便捷性特征,即便是不了解无损检测技术的工作人员在经过简单的培训之后,便能够根据生产需要进行自行编程。
这也使得无损检测技术在工业领域有着十分广阔的应用前景。
一般来说在压力管道与容器中较为常用的无损检测技术就是超声波检测技术与射线技术两类。
其中在超声波检测技术的原理在于超声波在介质内传递能够保证传播方向的直接性,如若遇到其他介质便会发生折射或是绕射等现象,所以工作人员能够根据超声波的传播方向、反射大小等情况来确定出缺陷的位置与具体类型。
- 1、下载文档前请自行甄别文档内容的完整性,平台不提供额外的编辑、内容补充、找答案等附加服务。
- 2、"仅部分预览"的文档,不可在线预览部分如存在完整性等问题,可反馈申请退款(可完整预览的文档不适用该条件!)。
- 3、如文档侵犯您的权益,请联系客服反馈,我们会尽快为您处理(人工客服工作时间:9:00-18:30)。
DOI: 10.12677/iae.2019.73026
196
仪器与设备
卜宏利 等
Figure 3. Typical signal processing results 图 3. 典型信号处理结果
通过图 3 中时域原始信号与连续小波变换后的信号之间的对比分析,能够很好地提取各波包络(实红 圈)的精确 ToF,也能够区分原始信号中很难分开的波包络(虚红圈)。 2.2.4. 损伤识别与定位
(a)
(b)
(c)
Figure 5. Damage detection results in system; (a) Composite delamination; (b) Interface debonding; (c) Thickness of steel layer 图 5. 损伤检测结果云图;(a) 复合材料层间损伤;(b) 复合材料–钢界面脱粘;(c) 钢层厚度
Figure 2. Parameter settings panel 图 2. 参数设置面板
2.2.2. 外部接口读取缓存 主程序调用数据采集卡的动态链接库(Dynamic Link Library, DLL),取得缓存的控制权。具体实现为:
开始或重启系统时清空缓存内的数据,采集数据时利用队列(Queue)技术读取缓存,结束采集时释放对缓 存的控制权。
DOI: 10.12677/iae.2019.73026
194
仪器与设备
卜宏利 等
LabVIEW 以其开发速度快,易用易学而被广泛应用于数据采集、仪器控制等领域。LabVIEW 和 MATLAB 的混合编程可以使两者发挥各自的优势,方便而高效地实现仪器控制,信号传输与数值计算、分析的结合。
2.1. 软件系统设计的整体思路
Instrumentation and Equipments 仪器与设备, 2019, 7(3), 193-201 Published Online September 2019 in Hans. /journal/iae https:///10.12677/iae.2019.73026
2. 软件系统设计
为了实现高效、可靠的厚壁复合压力容器的超声检测,我们基于 LabVIEW 编程语言设计并开发了集 数据采集、存储、处理、可视化于一体的全自动软件系统,并基于 LabVIEW 与 MATLAB 混合编程的方 法实现了厚壁复合压力容器的缺陷识别、定位与评估。
LabVIEW (Laboratory Virtual Instrument Engineering Workbench)是一种图形化编程语言,采用数据流 编程方式[8]。LabVIEW 包括前面板和程序面板两部分,前面板提供很多传统仪器类控件,用于创建用户 界面。程序面板提供函数和连线,用以编写 VI (Virtual Instrument)程序实现前面板控件、数据流的控制。
卜宏利 等
了多通道超声检测软件系统,提出了适用于超声波的时频信号处理的连续小波变换,实现了厚壁复合压 力容器超声检测结果的自动化分析。
关键词
超声波,无损检测,厚壁复合压力容器
Copyright © 2019 by author(s) and Hans Publishers Inc. This work is licensed under the Creative Commons Attribution International License (CC BY). /licenses/by/4.0/
本文针对厚壁复合压力容器的超声波无损检测方法,基于 LabVIEW 编程语言自行开发了超声检测软 件系统。为了提高超声回波信号的时频分辨率,该软件系统引入了连续小波变换进行信号处理,实现了 超声脉冲反射回波技术在复合材料层中损伤的检测。该软件系统通过对超声波激励的控制与信号提取, 能够实现厚壁复合压力容器的缺陷识别、定位与评估。
将缺陷识别、定位与评估模块嵌入到 For 循环中,每当有信号数据流入,此模块便会识别缺陷类型 并分别提取相应的缺陷信息,生成表征缺陷尺寸大小的云图图块,并计算缺陷位置。最后,所有的图块
DOI: 10.12677/iae.2019.73026
197
仪器与设备
卜宏利 等
根据参数设置的扫描方式一一对应地显示在坐标平面,形成整个区域的缺陷云图,包括复合材料层间损 伤、钢层厚度、复合材料–钢界面脱粘,如图 5 所示。与此同时,采集过程中的缺陷信息也会实时显示 在用户界面中。
Figure 1. Flow chart of ultrasonic testing software system 图 1. 超声检测软件系统流程图
2.2. 软件Βιβλιοθήκη 统的具体实现2.2.1. 信号采集模式相关参数的设置 首先,我们通过建立参数设置面板进行参数设置。参数设置面板是基于 LabVIEW 中的 VI Reference
Keywords
Ultrasonic Wave, Non-Destructive Testing, Thick-Walled Composite Pressure Vessel
厚壁复合压力容器的超声无损检测软件的开发
卜宏利,卢裕文,陈建霖,周文灵,励 争*
北京大学工学院,力学与工程科学系及湍流与复杂系统国家重点实验室,北京
Open Access
1. 引言
厚壁复合压力容器,特别是纤维缠绕的复合材料压力容器,以其轻质、高强、耐磨损、抗疲劳等优 异性能被广泛应用于航空航天、航海、核电、炼油石化等工业领域[1]。然而,厚壁复合压力容器在制造 成型与服役过程中不可避免地产生各种缺陷或损伤,并严重地威胁着工程结构的安全。因此,厚壁复合 压力容器的可靠性与安全性问题越来越受到广泛的关注,发展便捷、可靠、高效的厚壁复合压力容器的 无损检测技术迫在眉睫。然而,由于复合材料各向异性、非均质的材料性质,以及结构多层次等特征, 使得厚壁复合压力容器内部的缺陷形式极其复杂,致使现行的无损检测技术难以满足检测需求。
函数设计而生成。当软件系统启动后,会弹出参数设计界面,提示参数输入。参数的设置主要包括五个
DOI: 10.12677/iae.2019.73026
195
仪器与设备
卜宏利 等
方面:基本信息、存储信息、参与扫描的通道、扫描模式及信号处理部分相关参数、扫描方式信息,如 图 2 所示。其中,基本信息主要包括采集编号、操作人员、采集对象等,用以后期生成报告;存储信息 主要指数据文件的存储路径;参与扫描的通道必须选中,未选中的通道在扫描过程中将被禁用;扫描模 式及信号处理部分相关参数主要包含采集时间间隔、取平均的数据组数、脉冲宽度、滤波器频率、连续 小波变换(CWT)处理频率、接收强度等;扫描方式信息通过多层次设置,逐级定义硬件系统的扫描方式。 如图 2 下方所示,我们将扫描区域分成 2 × 2 个方块区域,每个方块区域为 4 × 4 个测点。扫描时以 2 × 2 的方块(即 8 × 8 个测点)为一个单位,单位内测点由上到下逐排扫描。设置完参数后,通过引用调用将设 置好的参数传入主程序,主程序开始运行。
信号处理完成后,主程序进入缺陷识别、定位与评估模块。图 4 为损伤识别与定位程序模块。此模 块所实现的方式为基于 MATLAB Script 节点的 LabVIEW 和 MATLAB 混合编程。
Figure 4. Damage identification program 图 4. 损伤识别与定位程序
目前,国内外很多学者[2] [3] [4]都纷纷从复合材料的受力分析、强度极限、破坏形式、疲劳寿命及 可靠性分析等方面,进行了复合材料压力容器的优化设计研究,对复合材料压力容器的安全性起到重要 的作用。但是,这些工作多是在压力容器设计之初或破坏之后进行的分析。然而,在实际的压力容器使 用过程中,针对压力容器内部损伤情况的实时检测,更有助于分析在役结构的剩余强度,预测使用寿命, 便于及时采取措施,预防事故的发生。虽然,针对压力容器已经发展了一些无损检测技术[5] [6],但是大 多不适用于厚壁复合压力容器的损伤检测。超声波检测技术具有缺陷定位较准确、灵敏度高、对面积型 缺陷的检出率较高等优点,已应用于压力容器的损伤检测[7]。但是,往往只适用于单一金属材料制造的 压力容器。对于厚壁复合压力容器,采用超声脉冲反射回波技术检测的回波信号非常复杂,特别是其中 的复合材料层的层间缺陷极难识别。因此,迫切需要发展先进的超声波信号分析处理方法,可对较大厚 度范围内的复杂材料构成的压力容器进行检测。
2.2.3. 原始信号处理 读取数据采集卡缓存中的数据后,主程序运行到信号处理模块。原始数据流流入 FFT Power Spectrum
函数进行快速傅里叶变换(FFT),计算信号中心频率。与此同时,原始数据流在 MATLAB Script 节点中 进行连续小波变换处理。典型的信号处理结果,见图 3。
Software System of Ultrasonic Nondestructive Testing Technology for Thick-Walled Composite Pressure Vessel
Hongli Bu, Yuwen Lu, Jianlin Chen, Wenling Zhou, Zheng Li*
图 1 为超声检测软件系统的整体框架。程序开始运行后自动弹出参数设置界面,参数设置完毕后可 以点击对应的按钮开始采集,系统会在用户选定的通道自动进行多通道采集,得到原始信号。为了提取 相对不规则的原始信号中的有效信息,该系统的信号处理模块引入了连续小波变换对原始信号进行处理, 原始信号和经处理的信号都会储存在 TDMS 文件中,也可用 Excel 查看。采集过程中,用户可根据需求 查看和保存波形图。采集结束后,还可得到最终的云图和采集报告。
College of Engineering & LTCS, Peking University, Beijing
Received: Sep. 2nd, 2019; accepted: Sep. 22nd, 2019; published: Sep. 29th, 2019