冲裁级进模设计.
冲裁模设计实例1

冲裁模设计实例1零件图如下:图2-1 零件零件名称:托板,大批量生产材料:08F钢板 t=2mm2.1 冲裁件的工艺性分析冲裁零件的工艺性是指零件对冲压加工工艺的适应性,即加工过程的难易程度。
良好的加工工艺性是指在满足使用要求的前提下能够用最经济实用的方法将零件给冲压出来。
而级进模由于多工位因素大的存在必须从冲裁件的基准、结构形式、尺寸公差、表面精度、材料性能、模具的工作强度等方面进行分析冲裁件的工艺性。
本设计的冲裁件为托板,其加工的工艺性分析如下:冲件为08F钢板,是优质的碳素结构钢,具有良好的冲压性能;冲裁件结构简单但有90度尖角,为了提高模具寿命故改为R1的工艺圆角,零件图上未标注尺寸偏差,属未标注公差,可按IT14级确定工件尺寸的公差。
经查公差表,各尺寸公差58074.0-,38062.0-,052.0-,044.0-,1422.022.0+-,1722.022.0+-,φ5.3 3.00+为:2.2 确定工艺方案及模具结构形式在冲压工艺方案确定后,模具结构形式的确定也相当重要,因为他直接关系到冲压过程的生产效率、冲压件的质量、尺寸精度、及其模具的寿命。
由上面的分析可知冲裁件尺寸要求不高,尺寸不大形状结构简单,但生产量大,根据材料较厚的特点,为保证孔位精度,冲模有较高的生产率,实行工序集中的工艺方案,采用导正钉进行定位、刚性卸料装置、自然卸料方式的级进模结构形式。
级进模是指在依次排列不同工步的凸模下连续送进坯料,使得压力机的一次行程中在模具的不同部位同时完成数道工序的模具。
级进模可以减少模具和设备的数量,提高生产率,而且容易实现自动化。
但是比简单模具结构复杂、制造麻烦。
成本相对较高。
表2-2冲压批量图批量项目单件小批中批大批大量大件<1 1-2 2-20 20-300 >300中件<1 1-5 5-50 50-1000 >1000小件<1 1-10 10-100 100-5000 >5000模具形式简易模简单模连续模、复合模连续模、复合模连续模、复合模组合模组合模简单模简单模简单模简易模半自动模半自动模设备形式通用压力机通用压力机高速压力机机械高速压力机自动机专用压力机与自动机自动和半自动通用压力机注:表内数字为每年班产量的概略数值(千件)第3章:模具设计计算3.1排样、计算条料宽度及其确定步距在纯冲裁类级进模排样设计时原则上为先冲导正孔和间距精度要求较高的孔。
双耳止动垫片冲孔落料冲裁模具设计【级进模】开题报告

7、制定主要零部件的加工工艺并编制相关数控加工程序。
设计的难点:
1、模具的结构设计和计算。
2、总装配图的绘制。
2.准备情况(查阅过的文献资料及调研情况、现有设备、实验条件等)
在现代化的工业生产中,模具展现出其独领风骚的魅力,其设计与制造的水平在不断进步,日趋完善。就模具的设计与制造的研究现状来说,生产的模具不断地实现大型化、精密化,不断地融进高技术等;而其发展趋势可预见到,将向更大型、更精密、更环保、更多技术含量的方向发展。我很自豪自己选择了机械设计制造及其自动化专业,学习了冲压模具设计与制造的相关知识,而这次双耳止动垫片冲孔落料冲裁模的综合设计刚好是对我大学四年来所学知识的运用能力的检测。根据模具设计流程,先对模具设计种类进行对比选择合适的模具类型。在进行加工零件的工艺分析确定合适的工艺方案。进行模具设计计算和结构设计计算,从而选择标准件的选择。我现在已经基本掌握了模具设计流程和具体设计要求。对设计所需的计算公式已经了解和查找并记录。我也会尝试设计的模具过程中采用工作过程的模拟。。我也会在实习过程中和查阅资料的过程中对毕业设计课题做深刻了解及总结,保证按时高质量地完成双耳止动垫片冲孔落料冲裁模毕业设计。我也会在实习过程中和查阅资料的过程中对毕业设计课题做深刻了解及总结,保证按时高质量地完成双耳止动垫片冲孔落料冲裁模毕业设计。
3、结合模具公司实习实际和参考资料相关知识及设计要求,进行必要的进行相关计算和设计。
4、根据具体计算结果和设计情况,确定具的主体结构,选用合理的标准模架,
及工作零件、送料装置、卸料装置、导料装置及定位装置等,在符合计算和设计要求的基础上尽量选用标准件。
5、用UG三维软件创建设计模具的虚拟模型,然后用三维软件出图(包括总装配图和零件图),再用二维软件稍做修改使其符合国家标准,完成局部成型模具典型结构设计。
冲裁模具设计与制造I一级进工序冲裁

适用范围:
Ah ha!
尺寸精度较低,批量不大的冲 压件
4
级进工序冲压的优缺点
优点:
工件精度较高(IT10~13级),生产 效率高,操作安全性好
缺点:
模具结构较复杂,成本较高,对条 料的定位要求高
适用范围:
工件尺寸及厚度较小,尺寸精度较 高的大批量冲压件
5
冲压工艺性分析
材料:A3钢
普通碳素钢,有一定的塑性和强度,韧性及铸 造性均好,适于冲压和焊接。其力学性能可查 相关材料手册,见下表。
10
相关工艺设计计算——限位板的排样 排样分析:
该零件只有冲孔、落料两种工序 应先安排先冲孔后落料 为了保证孔位间的尺寸精度、节约工步,将三个孔一次冲出 为了保证凹模的强度,在冲孔与落料之间安排一个空工步 该限位板的排样如图
11
相关工艺设计计算——步距的控制
限位板排样分析:
该零件只有冲孔、落料两种工序 应先安排先冲孔后落料 为了保证孔位间的尺寸精度、节约工步,将三个孔一次冲出 为了保证凹模的强度,在冲孔与落料之间安排一个空工步 该限位板的排样如图 定距采用安装于凹 模面上的导正销。
条料尺寸:
查《冲压模具设计与制造》表2.5.2确定搭边值: 工件边缘最小搭边:a=1.8mm,考虑到剪板误差,
实际取a=2.0mm ; 工件间的最小搭边:a1=1.5mm ,考虑到剪板误
差,实际取a1=2.0mm ; 步距为: 22±0.006mm ; 条料宽度:采用无侧压装置送料 B=(D+2a1)-Δ=(50+2×2.0)- Δ =54-0.6 排样图:先学习级进模的排样要点
实验室的冲床J23-63,公称压力为630KN,能 满足要求。
17
冲压模具级进模毕业设计

冲压模具级进模毕业设计冲压模具级进模是一种用于压力成形加工的模具,它能够在一次循环中完成多个工序,提高生产效率和产品质量。
本次毕业设计旨在设计一套适用于冲压模具级进模的工艺和设备,以满足工业生产的需求。
以下是本次毕业设计的具体内容和步骤。
1.需求分析首先,需要对冲压模具级进模的应用场景和要求进行需求分析。
了解冲压模具级进模的工作原理、具体应用领域以及对模具设计和设备要求等方面的信息,从而为后续设计工作提供方向和参考。
2.工艺设计根据需求分析的结果,进行工艺设计。
包括将原始材料加工成所需产品的具体步骤、工序和操作流程等。
在设计过程中,需要考虑模具的装夹方式、进模方式和工装设计等相关问题,确保工艺设计的合理性和可行性。
3.模具设计在完成工艺设计后,进行模具的设计工作。
模具设计主要包括模具结构设计和零件设计两个方面。
模具结构设计需要考虑模具的切削和定位原理,选用适当的材料和成型工艺,确保模具具备足够的强度和刚度。
零件设计需要根据产品尺寸和形状要求进行模具零件的设计,包括上模、下模、导向装置和顶杆等。
4.设备选型和设计在模具设计的基础上,进行设备选型和设计。
设备选型需要考虑工艺要求、生产能力和设备性能等方面的因素,选择适合的设备类型和规格。
设备设计包括设备整体结构设计和相关零部件设计,确保设备功能完善、操作方便和安全可靠。
5.制造和组装将模具和设备的设计图纸转化为实际产品。
制造过程包括原材料的采购、加工和热处理等工序,确保模具和设备的质量和性能。
组装过程则将各个零部件进行装配,确保模具和设备的完整性和一体性。
6.调试和测试对制造完成的模具和设备进行调试和测试。
通过调整参数、检查设备运行情况和模具质量等方面的测试,确保模具和设备的正常工作和满足产品质量要求。
7.结果分析和总结根据调试和测试的结果,对设计和制造过程进行分析和总结。
评估设计和制造的准确性和合理性,发现问题并提出改进措施,为实际生产提供参考。
通过以上步骤的设计和实施,能够完成一套适用于冲压模具级进模的工艺和设备。
级进模冲压工艺设计简述
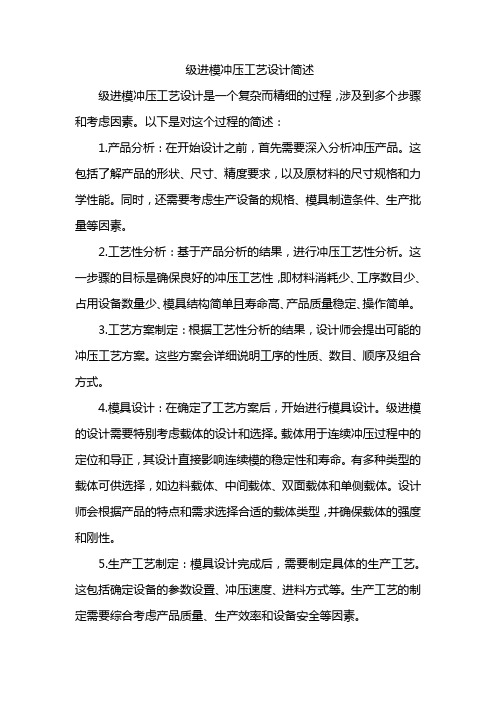
级进模冲压工艺设计简述
级进模冲压工艺设计是一个复杂而精细的过程,涉及到多个步骤和考虑因素。
以下是对这个过程的简述:
1.产品分析:在开始设计之前,首先需要深入分析冲压产品。
这包括了解产品的形状、尺寸、精度要求,以及原材料的尺寸规格和力学性能。
同时,还需要考虑生产设备的规格、模具制造条件、生产批量等因素。
2.工艺性分析:基于产品分析的结果,进行冲压工艺性分析。
这一步骤的目标是确保良好的冲压工艺性,即材料消耗少、工序数目少、占用设备数量少、模具结构简单且寿命高、产品质量稳定、操作简单。
3.工艺方案制定:根据工艺性分析的结果,设计师会提出可能的冲压工艺方案。
这些方案会详细说明工序的性质、数目、顺序及组合方式。
4.模具设计:在确定了工艺方案后,开始进行模具设计。
级进模的设计需要特别考虑载体的设计和选择。
载体用于连续冲压过程中的定位和导正,其设计直接影响连续模的稳定性和寿命。
有多种类型的载体可供选择,如边料载体、中间载体、双面载体和单侧载体。
设计师会根据产品的特点和需求选择合适的载体类型,并确保载体的强度和刚性。
5.生产工艺制定:模具设计完成后,需要制定具体的生产工艺。
这包括确定设备的参数设置、冲压速度、进料方式等。
生产工艺的制定需要综合考虑产品质量、生产效率和设备安全等因素。
总结起来,级进模冲压工艺设计是一个综合性的过程,涉及到产品分析、工艺性分析、工艺方案制定、模具设计和生产工艺制定等多个步骤。
这个过程的目标是确保冲压产品的高质量、高效率和低成本生产。
冲模设计(第10章)级进模

2) 凡属于多次拉深的多工位级进模,由于连续冲压的 原因,其拉深工序的安排、拉深系数的选取应以安 全稳定为原则。
3) 为了便于级进拉深模在试模过程中调整拉深次数和 各次拉深系数的分配,应适当安排几个空位工位, 作为预备工位。
6) 分段切除余料排样中条料,因冲切加工其强度逐 渐变弱,在安排各工位的加工内容时要考虑条料 宽度方向的导向。
7) 应保证条料载体与零件连接处有足够的强度与刚 度。当冲压件上有大小孔或窄肋时,应先冲小孔 (短边),后冲大孔(长边)。
8) 凹模上冲切轮廓之间的距离不应小于凹模的最小 允许壁厚,一般取为2.5t(t为工件材料厚度),但 最小要大于2mm。
2) 当孔到边缘的距离较小,而孔的精度又较高时,冲外轮廓时 孔可能会变形,可将孔旁外缘先于内孔冲出。
3) 应尽量避免采用复杂形状的凸模,并避免型孔有 尖的凸角、窄槽、细腰等薄弱环节。
4) 有严格要求的局部内、外形及位置精度要求高的 部位,应尽量集中在同一工位上冲出,以避免步 距误差影响精度。
5) 对于一些在普通低速压力机上冲压的多工位级进 模,凡是能合并的工位,只要 模具能保证零件的精度,模具 本身具有足够的强度,就不要 轻易分解、增加工位。
(1) 材料利用率。 (2) 模具结构适应性。 (3) 有无不必要的空位。 (4) 冲压件尺寸精度能否保证。 (5) 冲压件的孔和外形是否会产生变形。 (6) 其他还应从载体强度是否可靠、冲压件已成形部
位对送料有无影响、毛刺方向是否有利弯曲变形 、弹性弯曲件的弯曲线是否与材料纹向垂直或成 45°等方面进行分析检查。
9) 轮廓周界较大的冲切,尽量安排在中间工位,以 使压力中心与模具几何中心重合。
《冷冲模工艺与设计》课件——课题八:级进冲裁模的典型结构
课题八:级进冲裁模的典型结构
知识目标: 1、掌握级进模常用的几种典型结构、工作原理及其 优缺点。 能力目标: 1、能够比较单工序模、复合冲裁模和级进冲裁模的 行程中,在模具不同的位置上同时完成多 道冲裁工序(如冲孔、落料、切边)的模具。制件的成型是在级 进过程中逐步完成的。
由于级进模工位数较多,因此要控制冲裁件的孔与外形的相 对位置精度,就必须严格控制条料每次送进的距离(简称歩距)。 在级进模中,毛坯定位是关键问题。
2023/11/2
2.3.1 用固定挡料销和导正销定位的级进冲裁模
图2-9所示为用挡料销和导正销定位的 级进冲裁模,它是冲制垫圈的连续模。 工作时,首先由冲孔凸模和凹模作用冲 出制件的内孔,然后把条料向左送进一 个歩距(送料长度),利用模具左边的 落料凸模和凹模作用落料得制件的外形, 即得到垫圈。落料的同时,冲孔凸模和 凹模又冲出下一个垫圈的内孔。 该模具中条料定位方法是:首次冲裁用 始用挡料销,以后各次冲裁用固定挡料
图2-10 用侧刃定距的冲孔落料级进模
2.3.3 用切舌定距的级进冲裁模
图2-11 切舌尺寸图 图2-13 垫圈
图2-12 切舌定距模结构图
图2-14 垫圈排样图
切舌定义:在胚料上将板料三面切开,一面仍与胚料相连,如同舌头状,切出 的舌头片发生弯曲。切舌尺寸如图2-11所示。 切舌定距模原理:如图2-12所示,条料料头从右端的两导料板之间送入,经过 两个浮动导正销之间,再往前送大于一工步小于两工步的距离(不要求很精 确),实现首次定位,进行首次冲裁。此时完成第一工步的切舌和冲导正孔。 第二次冲裁时,由于切舌后切出的舌片高出条料的平面,继续往前送料时,舌 片侧面被浮动挡料销挡住,不能再前进,这时接着上、下模闭合,在卸料板的 作用下,切出的舌片被压回条料孔中,又与条料平面相平。以此同时,在条料 的右端又切出了新舌片来定距,条料又可越过浮动挡料销往前送进一个歩距, 材料越过浮动挡料销后,由导正销进一步导正,以后的工步接着进行冲孔和落 料。切舌部分刚好在冲孔废料中被冲掉。 应用:大于0.5mm厚板料 特点:与侧刃定距相比节省材料,动作操作可靠。由于对材料刚度有一定的要 求,切舌定距不适宜冲裁薄板。
机械专业综合课程设计报告——双侧刃定距级进冲裁模设计
(封面)XXXXXXX学院机械专业综合课程设计报告——双侧刃定距级进冲裁模设计题目:院(系):专业班级:学生姓名:指导老师:时间:年月日目录1课程设计任务书 (1)2零件工艺分析 (1)2.1 冲压材料 (1)2.2 工序性质 (1)2.3 结构形状 (1)2.4 尺寸精度 (2)3 工艺方案的确定及制定 (2)3.1 工序比较 (2)4 模具结构的选择 (3)4.1 模具形式 (3)4.2送料方式 (3)4.3 卸料以及出件方式 (3)4.4定位方式的选择 (3)4.5模架及导向零件的选择 (4)5 工艺计算 (4)5.1排样设计 (4)5.1.1无搭边排样形式 (4)5.1.2无搭边排样形式 (4)5.1.3材料利用率 (4)5.2 落料凸、凹模刃口尺寸计算 (6)5.2.1冲裁的结构分析 (6)5.2.2刃口计算原则 (6)6冲裁力计算与压力机选择及压力中心确定 (9)6.1冲裁力计算 (9)6.2压力机的选择 (10)6.3压力中心的确定 (10)7凹模设计 (11)7.1凹模孔口结构形式确定。
(11)7.2凹模精度与材料的确定。
(11)7.3凹模外形尺寸计算。
(12)8凸凹模设计计算 (13)8.1凸凹模精度和材料确定 (13)8.2凸模长度确定 (14)8.3模架形式以及上下模座的选择 (15)8.4模具总装配图以及工作原理 (16)总结 (17)1课程设计任务书2零件工艺分析图2.1零件图2.1 冲压材料该冲压件板件,厚度为2mm,大批量生产。
材料为Q235钢,低碳钢,塑性好,易成形,具有良好的可冲裁性能。
2.2 工序性质由零件图可知该零件结构简单,只需冲孔、落料2个工序即可。
2.3 结构形状零件结构简单。
零件中心为一直径为4mm的圆孔,左右两侧各有一个半径为4mm 的半圆弧。
总长为34mm,两半圆弧圆心距为26mm,宽8mm。
2.4 尺寸精度根据设计任务书要求,工件尺寸精度可按照IT14级制造,不需精冲或者其他特殊冲裁。
垫圈级进模冲裁-工艺设计
2008-8
成都航空职业技术学院机械系
1
模具教研室
பைடு நூலகம்
成形工艺设计
工作任务:垫圈冲裁工艺设计
零件名称:垫圈 生产批量:大批 材料:Q215 材料厚度:t=1mm
2
冲压工艺性分析
材料:Q215
普通碳素钢,有一定的塑性和强 度,韧性及铸造性均好,适于冲 压和焊接。其力学性能可查相关 材料手册,见下表。
总
nA1 LB
100%
=1564×235.5÷(750×1000)×100%
=49.1%
即每张板材的材料 利用率为49.1%。
10
相关工艺设计计算——步距的控制
该垫圈采用级进工序冲压,对条料的定距要求比较高, 故定距采用安装于凹模面上的固定挡料销和始用挡料销,
结构比较简单、成本较低。
①特点同序号2,且刃口直壁下面的扩大部分可使 凹模加工简单,但采用下漏料方式时刃口强度不如 序号2的刃口强度高。 ②用于冲裁形状复杂或精度要求较高的中小型件, 也可用于装有顶件装置的模具。
α(`) β(°) 刃口高度h(mm) 备注
15
2
≥4
≥5
≥6
18
表 热砸钢板和钢带的规格尺寸(mm)
公称厚度
尺寸精度
经查标准公差表,零件图上尺寸均为自由公差, 一般按IT14级确定工件的公差,普通冲裁均能满 足其尺寸精度要求。各尺寸公差为:φ10+0.36 , φ20-0.52
生产纲领
大批量生产适合冲压加工。
结论
可以冲裁。
5
冲压工艺方案的确定
综上分析,该垫圈形状简单、尺寸精度低,仅有冲孔、落 料两种工序,
录音机机芯冲裁、弯曲级进模冲压模具毕业设计
此工件是录音机机芯中的零件。
工件形状较复杂,要求精度较高,主要工序有冲孔、落料、成形、弯曲。
冲压材料使用钢带病卷料,材料厚0.8mm。
采用自动养料器送料。
2.2 冲裁方案确定该工件包括冲孔、冲裁、成形、弯曲四个基本工序,根据以上内容可以有以下三种工艺方案:方案一:先冲孔,再冲裁,然后成形,最后弯曲,采用单工序模生产;方案二:先冲孔---冲裁---成形复合模生产,后进行弯曲工序的复合模和单工序模相结合的方式生产;方案三:冲孔---冲裁---成形---弯曲级进冲裁,采用级进模生产。
方案的对比:①采用先冲孔,再冲裁,然后成形,最后弯曲的单工序模生产,这种工艺方案优点在于模具结构简单,但是由于该工件的工序相当多,那样就需要好几套模具,使模具的制造成本大大增加,工件也很小(即尺寸小),采用这种单工序模生产的话,在工件换到下一套模具的时候,工件的定位都难以达到所要求的位置,这样一来模具的质量不能保证,从而导致一整套模具生产出来的产品也不能达到生产技术要求,不仅这样,而且采用手工生产的生产效率也相当的低,不能达到大批大量的生产要求。
②采用先冲孔---冲裁---成形复合模生产,后进行弯曲工序的单工序模和复合模相结合的方式生产。
这样一来,就只需要两套模具,模具的制造成本相比方案一来说要低一些,在第一阶段中,工件的基本尺寸精度也在一定的基础上有了提高,不过这样,在弯曲这一工序的定位还是没有得到很好的解决,仍不能达到理想的尺寸精度,然而从生产效率方面方案二也有一定的提高。
在制造冲孔---冲裁---成形复合模时,增加的制造难度,强度也相对较小,从而影响模具的寿命以及操作的不方便。
③采用冲孔---冲裁---成形---弯曲级进冲裁模这一方案,能够满足工件的尺寸精度要求,生产效率也很高,操作方便,生产质量相对稳定,也适合于批量生产,但是模具制造、安装调整都非常的困难,而且模具的制造成本也非常高。
通过上述的分析比较,该工件的冲压生产采用方案三为最佳。
- 1、下载文档前请自行甄别文档内容的完整性,平台不提供额外的编辑、内容补充、找答案等附加服务。
- 2、"仅部分预览"的文档,不可在线预览部分如存在完整性等问题,可反馈申请退款(可完整预览的文档不适用该条件!)。
- 3、如文档侵犯您的权益,请联系客服反馈,我们会尽快为您处理(人工客服工作时间:9:00-18:30)。
目录1. 冲压件工艺性分析———————————————————(1)2.冲压工艺方案的确定——————————————————(3)3. 主要设计计算(1)排样方式的确定以及计算—————————————————————(3)(2)压力中心的确定及相关计算————————————————————(3)(3)冲压力的计算—————————————————————————(4)(4)工作零件刃口尺寸计算——————————————————————(4)(5)卸料弹簧的设计—————————————————————————(5)4.模具总体设计(1)模具类型的选择————————————————————————(5)(2)定位方式的选择———————————————————————(5)(3)卸料,出件方式的选择—————————————————————(6)(4)导向方式选择—————————————————————————(6)5. 主要零部件设计(1)主要零件的结构设计———————————————————————(6)(2)定位零件的设计—————————————————————————(8)(3)导料板的设计——————————————————————————(8)(4)卸料板部件设计—————————————————————————(8)(5)模架及其他零部件设计——————————————————————(8)6.模具总装图7.冲压设备的选定——————————————————————(8)8.工作零件的加工工艺—————————————————————(8)9. 模具的装配—————————————————————————(10)主要参考文献————————————————————————(12)设计小结——————————————————————————(12)级进模设计说明冲裁级进模设计(08-2班)要求:1、对产品进行工艺性分析,确定工艺方案;2、进行必要的工艺计算,例如:冲裁力、压力中心、刃口尺寸等;3、对工作零件、定位零件、导向零件、卸料和出件装置等进行设计,对装配中使用的标准件进行选取;4、确定各零件尺寸(可列表说明),画出二维或三维级进模装配图、凸模、凹模零件图。
工件图1.冲压件工艺性分析此工件只有冲孔和落料两个工序。
材料为Q235A,具有良好的冲压性能,适合冲裁。
工件结果简单,有1个半径6mm的孔,有2个直径8mm的孔;孔与孔,孔与边缘之间的距离满足要求,工件的尺寸有规定公差,特别是孔的尺寸精度较高。
2。
冲压工艺方案的确定该工件包括落料冲孔两个基本工序,可有以下三种工艺方案:方案一:先落料,后冲孔。
采用单工序模生产。
方案二:落料—冲孔复合冲压。
采用复合模生产。
方案三:冲孔—落料级进冲压。
采用级进模生产。
方案一模具结构简单,但需要两道工序两套模具,成本高而生产效率低,难以满足大批量生产要求。
方案二只需一套模具,工作精度及生产效率都比较高,但制造难度大,并且冲压成品件留在模具上,清理模具上的物料影响冲压速度,操作不方便。
方案三也只需要一副模具,生产效率高,操作方便,设计简单,虽然工件精度要求较高,但综合考虑,基本能满足工件技术要求。
所以经过比较,采用方案三最为合适。
3.主要设计计算(1)排样方式的确定以及计算设计级进模,先要设计条料排样图。
工件图可视为一矩形中间3个孔,直排材料利用率最高。
如图一所示的排样方法,可减少废料。
第一次冲裁使用活动挡料销,然后第二次可用固定挡料销。
搭边值取1mm,壁厚取1.5mm,条料宽度为63.5mm,步距为21mm,一个步距的材料利用率为74%(2)压力中心的确定及相关计算画出凹模型口图如下;通过软件得出压力中心点(-2.89,0)。
(3)冲压力的计算该模具采用级进模,选择弹性卸料,下出件。
冲压力的相关计算见表1根据计算结果,冲压设备拟选择J23-25。
(4)工作零件刃口尺寸计算在确定工作零件刃口尺寸计算方法之前,首先要考虑工作零件的加工方法及模具装配方法。
结合该模具的特点,工作零件的形状相对较简单,适宜采用线切割机床分别加工落料凸模,凹模,凸模固定板,卸料板,这种加工方法可以保证这些零件各个孔的同轴度,使装配简化。
因此工作零件刃口尺寸计算就按分开加工的方法来计算,具体计算见表二所示。
表二工作零件刃口尺寸的计算(5)卸料弹簧的计算5.1弹簧预压力确定。
初步确定弹簧根数为6,按式F预=F卸/n(1.1)计算每根弹簧预压力,即F预=F卸/n=11699.19/6=1949.87N5.2选择弹簧使弹簧最大工作极限负荷F1>F预,弹簧的参数如下表三。
表三弹簧参数5.3校核所选弹簧总压缩量。
弹簧允许最大压缩量h1=H0-H1=27.2mm;弹簧受预压力时的预压缩量h预=h1F预/F1=27.2*1949.87/3119.78=17mm;卸料板工作行程:h工=t+1=2.5+1=3.5mm模具修模量:h修磨=5mm;弹簧总压缩量:h总= h修磨+ h工+ h预=25.5mm;5.4确定弹簧的装配高度。
H2=H0- h预=80-17=63mm。
4. 模具总体设计(1)模具类型的选择由冲压工艺分析可知,采用级进冲压,所以模具类型为级进模。
(2)定位方式的选择因为该模具采用的是条料,控制条料的送进方向采用导料板,无侧压装置。
控制条料的送进步距采用挡料销初定距,导正销精定距。
而第一件的冲压位置可由活动挡料销定距。
(3)卸料,出件方式的选择因为工件料厚2.5mm,相对较薄,卸料力也比较小,故可采用弹性卸料。
又因为是级进模生产,所以采用下出件比较便于操作与提高生产效率。
(4)导向方式选择为了提高模具寿命和工件治疗,方便安装调整,该级进模采用中间导柱的导向方式。
5. 主要零部件设计(1)主要零件的结构设计a.落料凸模结合工件外形并考虑加工,将落料凸模设计成直通式,采用线切割机床加工,2个M8螺钉固定在垫板上,与凸模固定板的配合按H6/m5。
总长L可按公式计算:L=固定板+卸料销+卸料弹簧+t=65.2mm落料凸模结构如下图所示精度要求按计算b.冲孔凸模因为所冲的孔均为圆形,而且都不属于需要特别保护的小凸模,所以冲孔凸c.凹模凹模采用整体凹模,各冲裁的凹模孔均采用线切割机床加工,安排凹模具在模架上的位置时。
要依据计算压力中心的数据,将压力中心与模柄范围内。
其轮廓尺寸可按公式计算:凹模厚度H=kb=0.35x58=20.3,为了方便弹簧安装,取H=25凹模壁厚c=(1.5-2)H=30-40.6,取c=40凹模宽度B=b+2c=58+2x40=138 取B=150凹模长度L取130mm(送料方向)凹模轮廓尺寸为130⨯150⨯25mm,凹模结构如图所示凹模(2)定位零件的设计落料凸模下部设置两个导正销,借用工件直径8mm的的两个孔作为导正孔。
导正销采用H7/r6安装在落料凸模端面,导正销导正部分与导正孔采用H7/r6配合。
(3)导料板的设计导料板内侧与条料接触,外侧与凹模齐平,导料板与条料之间间隙取1mm,这样就可确定了导料板的宽度,导料板厚度取4mm,采用45钢制作,热处理硬度为40-45HRC,用螺钉固定在凹模上。
导料板上有活动挡料销凹槽。
(4)卸料板部件设计a.卸料板的设计卸料板的周界尺寸与凹模的周界尺寸相同,厚度为8mm。
采用45钢制造,淬火硬度为40-45HRC。
b. 卸料螺钉的选用卸料板上设置4个螺钉,公称直径为8mm,螺纹部分为M6⨯4。
(5)模架及其他零部件设计该模具采用对角式导柱模架,导柱分别为Φ28⨯100,导套分别为Φ28⨯42x95。
上模座厚度取40mm ,上垫板厚度取10mm ,固定板厚度取15mm ,下模座厚度取45mm ,那么该模具的闭合高度:闭H =2h H H L H H -++++下模垫上模=40+10+50+25+45-2=168mm 式中:h2为凸模冲裁后进入凹模的深度,h2=2mmL —凸模长度,L=50mm H —凹模厚度,H=25mm可见该模具闭合高度小于所选压力机J23-25的最大装模高度(220 mm ),可以使用。
6.模具总装图通过以上设计,可得如图所示的模具总装图。
模具上模部分主要由上模板、垫板、凸模(3个)、凸模固定板及卸料板等组成。
卸料方式采用弹性卸料,以橡胶为弹性元件/下模部分由下模座、凹模板、导料板等组成。
冲孔废料和成品件均由漏料孔漏出。
条料送进时采用活动挡料销21作为粗定距,在落料凸模上安装2个导正销,利用条料上10Φ的孔作为导正销孔导正,以此作为条料送进的精确定距。
7.冲压设备的选定通过校核,选择开式双柱可倾压力机J23-25能满足要求。
起主要参数如下: 公称压力:250kN 滑块行程:65mm最大闭合高度:270mm 最大装模高度:220mm 连杆调节长度:55mm工作台尺寸(前后x 左右):370x560 mm 垫板尺寸(厚度x 直径):50x200 mm 模柄孔尺寸:Φ40x60 mm 最大倾斜角度:30度8、模具零件的加工工艺本副冲裁模,模具零件加工的关键在于工作零件、固定板以及卸料板。
若采用线切割加工技术,这些零件的加工就变得相对简单。
表四所示为落料凸模的加工工艺过程。
表四9、模具的装配根据倒装复合模装配要点,选凹模作为装配基准件,先装上模,再装下模,并调整间隙,试冲,返修。
具体的情况见表五所示。
表五1.上模座2.导套3.导柱4.紧固螺钉5.沉头螺钉6模柄7.凸模固定板8.卸料螺钉9.垫板10.圆柱销11. 卸料板12.下模座13.圆柱销14.凹模15.冲孔凸模16.落料凸模17.导正销18.卸料橡胶19.挡料销20.导料扳子模具总装图主要参考文献:1、《公差配合与技术测量》,陈于萍,机械工业出版社2、《机械制图》,刘少年主编,机械工业出版社3、《机械制造基础》,胡大超,高等教育出版社4、《金属材料与热处理》,赵先仲,机械工业出版社5、《机械加工工艺基础》,司乃钧,机械工业出版社6、《机械制造技术》,李华,高等教育出版社7、《冲压与成型设备》,孙凤勤主编,高等教育出版社8、《模具制造工艺学》,郭铁良,机械工业出版社9、《冲压模具设计与制造》,刘建超、张宝忠主编,高等教育出版社10、《数控机床加工工艺与设备》,赵长明,机械工业出版社设计小结通过本次冲压模具的设计,让我又对这门课程有了重新的了解。
让我学到了不同与课堂的新东西,增加了自己的动手能力。
虽然我设计的模具不一定好,但是,我觉得通过不断努力,我可以设计一套实用的好模具!!!这次的设计也让我巩固了软件知识,制图知识,收获颇丰!!!。