数控铣削加工工艺与编程实例
数控铣床编程30例带图

实例一毛坯为70㎜×70㎜×18㎜板材,六面已粗加工过,要求数控铣出如图3-23所示的槽,工件材料为45钢。
1.根据图样要求、毛坯及前道工序加工情况,确定工艺方案及加工路线1)以已加工过的底面为定位基准,用通用台虎钳夹紧工件前后两侧面,台虎钳固定于铣床工作台上。
2)工步顺序①铣刀先走两个圆轨迹,再用左刀具半径补偿加工50㎜×50㎜四角倒圆的正方形。
②每次切深为2㎜,分二次加工完。
2.选择机床设备根据零件图样要求,选用经济型数控铣床即可达到要求。
故选用XKN7125型数控立式铣床。
3.选择刀具现采用φ10㎜的平底立铣刀,定义为T01,并把该刀具的直径输入刀具参数表中。
4.确定切削用量切削用量的具体数值应根据该机床性能、相关的手册并结合实际经验确定,详见加工程序。
5.确定工件坐标系和对刀点在XOY平面内确定以工件中心为工件原点,Z方向以工件表面为工件原点,建立工件坐标系,如图2-23所示。
采用手动对刀方法(操作与前面介绍的数控铣床对刀方法相同)把点O 作为对刀点。
6.编写程序按该机床规定的指令代码和程序段格式,把加工零件的全部工艺过程编写成程序清单。
考虑到加工图示的槽,深为4㎜,每次切深为2㎜,分二次加工完,则为编程方便,同时减少指令条数,可采用子程序。
该工件的加工程序如下(该程序用于XKN7125铣床):N0010 G00 Z2 S800 T1 M03N0020 X15 Y0 M08N0030 G20 N01 P1.-2 ;调一次子程序,槽深为2㎜N0040 G20 N01 P1.-4 ;再调一次子程序,槽深为4㎜N0050 G01 Z2 M09N0060 G00 X0 Y0 Z150N0070 M02 ;主程序结束N0010 G22 N01 ;子程序开始N0020 G01 ZP1 F80N0030 G03 X15 Y0 I-15 J0N0040 G01 X20N0050 G03 X20 YO I-20 J0N0060 G41 G01 X25 Y15 ;左刀补铣四角倒圆的正方形N0070 G03 X15 Y25 I-10 J0N0080 G01 X-15N0090 G03 X-25 Y15 I0 J-10N0100 G01 Y-15N0110 G03 X-15 Y-25 I10 J0N0120 G01 X15N0130 G03 X25 Y-15 I0 J10N0140 G01 Y0N0150 G40 G01 X15 Y0 ;左刀补取消N0160 G24 ;主程序结束实例二毛坯为120㎜×60㎜×10㎜板材,5㎜深的外轮廓已粗加工过,周边留2㎜余量,要求加工出如图2-24所示的外轮廓及φ20㎜的孔。
数控铣削加工编程图例

数控铣削加工编程图例
练习题1
零件图如图所示,完成下面工作任务:
·选择加工用刀具;用表格说明刀具所用于的加工部位;·在图中画出刀具走刀路线;
·编写加工程序。
零件图如图所示,编写加工程序。
·粗加工用φ30平底铣刀,刀具长度130mm,留1mm精加工余量;·精加工用φ10平底铣刀,刀具长度110mm
如图所示,完成下面任务:·对零件加工进行工艺设计·编写零件加工程序
如图所示,完成下面任务:·对零件加工进行工艺设计·编写零件加工程序
如图所示,完成下面任务:·对零件加工进行工艺设计·编写零件加工程序
如图所示,完成下面任务:·对零件加工进行工艺设计·编写零件加工程序
如图所示,完成下面任务:·对零件加工进行工艺设计·编写零件加工程序
如图所示,完成下面任务:·对零件加工进行工艺设计·编写零件加工程序
编写零件加工程序
图4-129 数控铣削加工综合应用一图例
编写零件加工程序。
数控铣床编程实例.doc
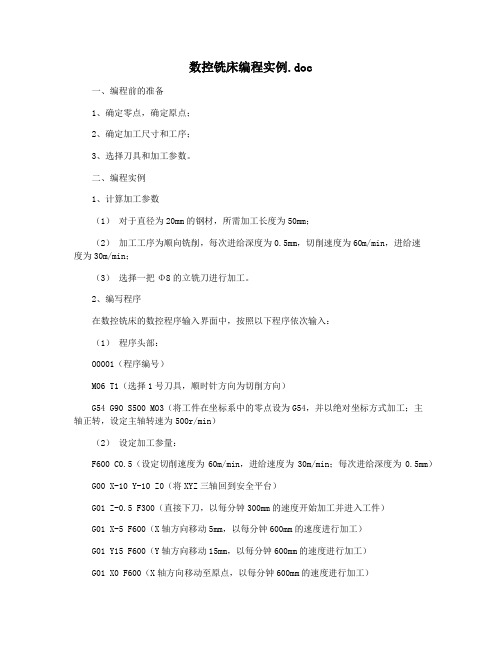
数控铣床编程实例.doc一、编程前的准备1、确定零点,确定原点;2、确定加工尺寸和工序;3、选择刀具和加工参数。
二、编程实例1、计算加工参数(1)对于直径为20mm的钢材,所需加工长度为50mm;(2)加工工序为顺向铣削,每次进给深度为0.5mm,切削速度为60m/min,进给速度为30m/min;(3)选择一把Φ8的立铣刀进行加工。
2、编写程序在数控铣床的数控程序输入界面中,按照以下程序依次输入:(1)程序头部:O0001(程序编号)M06 T1(选择1号刀具,顺时针方向为切削方向)G54 G90 S500 M03(将工件在坐标系中的零点设为G54,并以绝对坐标方式加工;主轴正转,设定主轴转速为500r/min)(2)设定加工参量:F600 C0.5(设定切削速度为60m/min,进给速度为30m/min;每次进给深度为0.5mm) G00 X-10 Y-10 Z0(将XYZ三轴回到安全平台)G01 Z-0.5 F300(直接下刀,以每分钟300mm的速度开始加工并进入工件)G01 X-5 F600(X轴方向移动5mm,以每分钟600mm的速度进行加工)G01 Y15 F600(Y轴方向移动15mm,以每分钟600mm的速度进行加工)G01 X0 F600(X轴方向移动至原点,以每分钟600mm的速度进行加工)G00 Z10(将刀具提起到安全范围内)M05(停止主轴)3、进行加工操作(1)确认加工参数是否准确;(2)将工件放在加工台上;(3)启动数控铣床,选择对应程序;(4)进行自检,检查加工槽的深度是否符合要求;(5)按照程序步骤操作,检查程序是否正确。
数控铣削综合编程实例
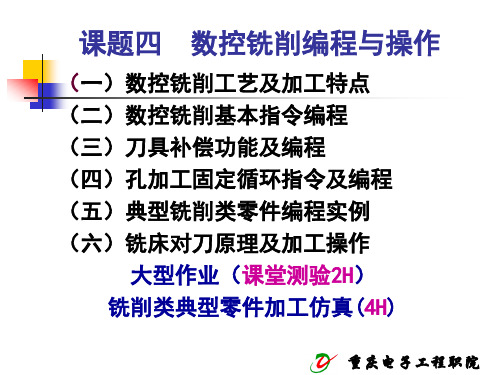
艺 分 析 及
X-75 Y0; G01 Z0 F100; X75; (上平面加工) G00 Z100 M05; G28;
编
程
重庆电子工程职业学院
课题四 数控铣床和加工中心编程
3、程序编制
T02 M06 ;(外轮廓加工)
典 G00 G43 Z5 H02 M03;
型 X-40 Y-40;
零
G41 X-25 Y-40 D02; G01 Z-4 F100;
铣Φ14、Φ35内圆腔
(G41)
O1000 G28 T01 M06 G54 M03 S800 M08 G00 G43 Z20 H01 G99 G81 X0 Y0 Z-1 R3 F100 X12.25 Y0 X17 Y17 X0 Y12.25 X-17 Y17 X-12.25 Y0 X-17 Y-17 X0 Y-12.25 G98 X17 Y-17 G49 G00 Z50 M05 G28 T02 M06 G00 G43 Z20 H02 M03 G99 G81 X0 Y0 Z-5 R3 F100 X12.25 Y0 X17 Y17 X0 Y12.25 X-17 Y17 X-12.25 Y0 X-17 Y-17 X0 Y-12.25 G98 X17 Y-17 G49 G00 Z50 M05
锪4-Φ8孔(G82) 铣Φ14、Φ35内圆 腔
(G41)
重庆电子工程职业学院
课题四 数控铣床和加工中心编程
程序编写
1)T01中心钻9-Φ3
(G43 G81)
2)T02钻头9-Φ6孔
(G43 G81)
数控铣削加工工艺与编程实例
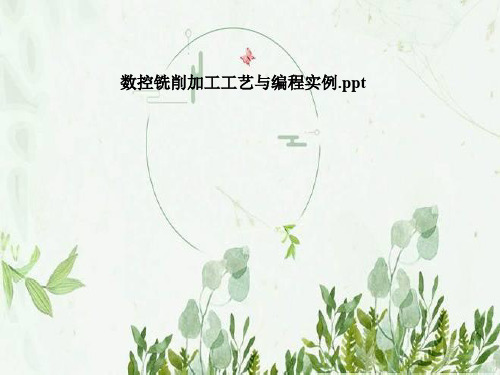
(3)工、量、刃具选择
(4)合理选择切削用量
2.编制参考程序 1)认真阅读零件图,确定工件坐标系。根据工件坐标系 建立原则,X、Y向加工原点选在φ60H7mm孔的中心, Z向加工原点选在B面(不是毛坯表面)。工件加工原点 与设计基准重合,有利于编程计算的方便,且易保证零 件的加工精度。Z向对刀基准面选择底面A,与工件的定 位基准重合,X、Y向对刀基准面可选择φ60H7mm毛坯 孔表面或四个侧面。 2)计算各基点(节点)坐标值。如图3-112所示各圆的 圆心坐标值见表3-32。
子程序:
3.6.4 加工中心零件的编程与操作
图3-105所示为端盖零件,其材料为45钢,毛坯尺寸为 160mm×160mm×19mm。试编写该端盖零件的加工 程序并在XH714加工中心上加工出来。
(1)加工方法 由图3-105可知,该盖板材料为铸铁,故毛坯为铸件,四 个侧面为不加工表面,上下面、四个孔、四个螺纹孔、 直径为φ60mm的孔为加工面,且加工内容都集中在A、 B面上。从定位、工序集中和便于加工考虑,选择A面为 定位基准,并在前道工序中加工好,选择B面及位于B面 上的全部孔在加工中心上一次装夹完成加工。 该盖板零件形状较简单,尺寸较小,四个侧面较光滑, 加工面与非加工面之间的位置精度要求不高,故可选机 用平口钳,以盖板底面A和两个侧面定位,用机用平口 钳的钳口从侧面夹紧。
3)参考程序:数控加工程序单见表3-33。
加工φ160mm中心线上孔的子程序的数控加工程序单见 表3-33。
加工φ100mm中心线上孔的子程序的数控加工程序单见 表3-33。
3.操作步骤及内容 1)机床上电。合上空气开关,按“NC启动”。 2)回参考点。选择“机械回零”方式,按下“循环启动”按钮,完成 回参考点操作。返回零点后,X、Y、Z三轴向负向移动适当距离。 3)刀具安装。按要求将所有刀具安装到刀库,注意刀具号是否正 确。 4)清洁工作台,安装夹具和工件。检查坯料的尺寸,确定工件的 装夹方式(用机用虎钳夹紧)。将机用虎钳清理干净装在干净的工 作台上,通过百分表找正、找平机用虎钳并夹紧,再将工件装正在 机用虎钳上,工件伸出钳口8mm左右。
数控铣床编程实例讲解
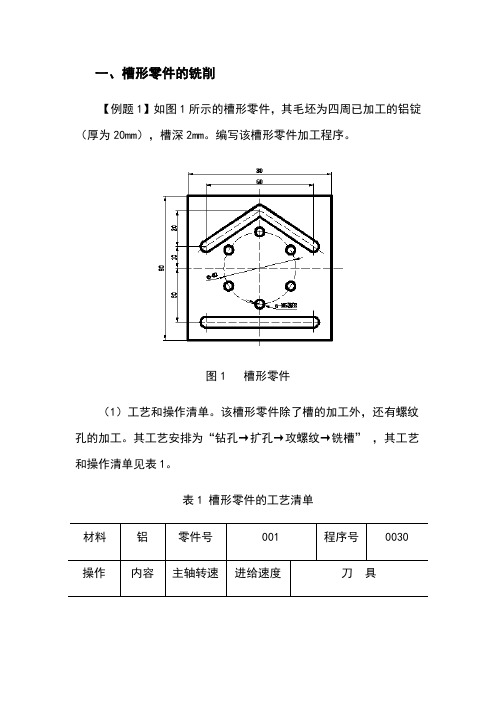
一、槽形零件的铣削【例题1】如图1所示的槽形零件,其毛坯为四周已加工的铝锭(厚为20mm),槽深2mm。
编写该槽形零件加工程序。
图1 槽形零件(1)工艺和操作清单。
该槽形零件除了槽的加工外,还有螺纹孔的加工。
其工艺安排为“钻孔→扩孔→攻螺纹→铣槽”,其工艺和操作清单见表1。
表1 槽形零件的工艺清单材料铝零件号001 程序号0030 操作内容主轴转速进给速度刀具(2)程序清单及说明。
该工件在数控铣钻床ZJK7532A-2上进行加工,程序见表2。
表2 槽形零件的加工程序二、平面凸轮的数控铣削工艺分析及程序编制【例题2】平面凸轮零件图如图2所示,工件的上、下底面及内孔、端面已加工。
完成凸轮轮廓的程序编制。
图2 凸轮零件图解:(1)工艺分析。
从图2的要求可以看出,凸轮曲线分别由几段圆弧组成,内孔为设计基准,其余表面包括4-φ13H7孔均已加工。
故取内孔和一个端面为主要定位面,在联接孔φ13的一个孔内增加削边销,在端面上用螺母垫圈压紧。
因为孔是设计和定位的基准,所以对刀点选在孔中心线与端面的交点上,这样很容易确定刀具中心与零件的相对位置。
(2)加工调整。
零件加工坐标系X、Y位于工作台中间,在G53坐标系中取X=-400,Y=-100。
Z坐标可以按刀具长度和夹具、零件高度决定,如选用φ20的立铣刀,零件上端面为Z向坐标零点,该点在G53坐标系中的位置为Z=-80处,将上述三个数值设置到G54加工坐标系中。
凸轮轮廓加工工序卡见表3。
表3 铣凸轮轮廓加工工序卡(3)数学处理。
该凸轮加工的轮廓均为圆弧组成,因而只要计算出基点坐标,才可编制程序。
在加工坐标系中,各点的计算坐标如下:BC弧的中心O1点: X=-(175+63.8) sin8°59'=-37.28Y=-(175+63.8) cos 8°59'=-235.86EF弧的中心O2点: X2+Y2=692(X-64)2+Y2=212解之得 X=65.75,Y=20.93HI弧的中心O4点: X=-(175+61)cos24°15'=-215.18 Y=(175+61)sin24°15'=96.93DE弧的中心O5点:X2+Y2=63.72(X-65.75)2+(Y-20.93)2=21.302解之得 X=63.70,Y=-0.27B点: X=-63.8sin8°59'=-9.96Y=-63.8cos8°59'=-63.02C点: X2+Y2=642(X+37.28)2+(Y+235.86)2=1752解之得 X=-5.57,Y=-63.76D点: (X-63.70)2+(Y+0.27)2=0.32X2+Y2=642解之得 X=63.99,Y=-0.28E点: (X-63.7)2+(Y+0.27)2=0.32(X-65.75)2+(Y-20.93)2=212解之得 X=63.72,Y=-0.03F点: (X+1.07)2+(Y-16)2=462(X-65.75)2+(Y-20.93)2=212解之得 X=44.79,Y=19.6G点: (X+1.07)2+(Y-16)2=462X2+Y2=612解之得 X=14.79,Y=59.18H点: X=-61 cos24°15'=-55.62Y=61sin 24°15'=25.05I点: X2+Y2=63.802(X+215.18)2+(Y-96.93)2=1752解之得 X=-63.02,Y=9.97根据上面的数值计算,可画出凸轮加工走刀路线图,如图3示。
第7章数控铣削编程与加工应用实例

这种情况下,若用同一把刀进行挖槽加工,则要求刀具在轮 廓边界1上连续切削时,使用一次刀具半径补偿;当刀具在轮廓边界2 上连续切削时,要撤消前次刀具半径补偿,重新建立新的刀具半径补 偿值,粗加工后,根据实测及各自公差的要求对刀补值作不同的修改, 调整后再进行精加工。
上一页 下一页 返回
7.2 挖槽加工实例
4)铣削图7-4(c)所示的凸台轮廓时,亦可看作挖槽加工的特例。 但此时不能用图纸所示的外轮廓作为加工边界,因为将这轮廓作为边 界时,角上的部分材料可能铣不掉,见图7-9(a)所示,1、2、3、4分别 为4个角残留的材料。此时可改为以边界2作为挖槽加工边界,4个角上 就不会留下残余材料。见图7-9(b)所示。
铣削工件外轮廓,通常采用高速钢或硬质合金的立铣刀,下刀点 选择在工件实体外,并使切入点位置和方向尽可能沿工件轮廓切向延 长线方向。刀具切入和切出时要注意避让夹具,并要避免碰到工件上 不该切削的部位。切出工件时仍要尽可能沿工件轮廓切向延长线方向 切出工件,以利于刀具受力平稳同时尽可能保证工件轮廓过度处无明 显接痕。
2)选择加工机床:用立式三坐标数控铣床较为合适 3)加工工序与工步的划分及走刀路线的确定 根据图样分析,凸台加工时材料的切削量不大,而且材料的切削 性能较好,选择φ20的圆柱形直柄立铣刀,材料为高速钢(HSS),沿 轮廓铣削一周即可去处余量,考虑实习用机床主轴刚性不够,深度 6mm,采用分层加工每次切深3mm。
(1)图7-3中基点A的坐标计算
在Rt△O1CD中,
数控铣削加工工艺及编程实例

(2)加工过程 1)粗、精铣B面。平面B采用铣削加工,表面粗糙度Ra 值为6.3μm,依据经济加工精度,选用粗铣→精铣加工 方案。B面的粗、精铣削加工进给路线根据铣刀直径 (φ100mm),确定为沿X方向两次进刀。
2)粗镗、半精镗、精镗φ60H7孔镗孔。φ60H7孔采用镗 削加工,精度等级IT7,表面粗糙度 Ra 值为0.8μm,依 据经济加工精度,选用粗镗→半精镗→精镗三次镗削加 工方案。所有孔加工进给路线按最短路线确定,孔的位 置精度要求不高,所以机床的定位精度完全能保证。
4.评分标准
3.6.2 平面内轮廓零件的编程与操作
平面内轮廓零件如图3-101所 示。已知毛坯尺寸为 70mm×70mm×20mm的长方 料,材料为45钢,按单件生产 安排其数控加工工艺,试编写 出该型腔加工程序并利用数控 铣床加工出该工件。
1.加工工艺方案 (1)加工工艺路线 1)切入、切出方式选择。铣削封闭内轮廓表面时,刀具 无法沿轮廓线的延长线方向切入、切出,只有沿法线方 向切入、切出或圆弧切入、切出。切入、切出点应选在 零件轮廓两几何要素的交点上,而且进给过程中要避免 停顿。 2)铣削方向选择。一般采用顺铣,即在铣削内轮廓时采 用沿内轮廓逆时针的铣削方向比较好。 3)铣削路线。凸台轮廓的粗加工采用分层铣削的方式。 由中心位置处下刀,采用环切的切削方法进行铣削,去 除多余材料。粗加工与精加工的切削路线相同。
图3-103所示为零件,已 知材料为45钢,毛坯尺 寸为 80mm×80mm×20mm, 所有加工面的表面粗糙 度值为Ra1.6μm。试编 写此工件的加工程序并 在数控铣床上加工出来。
1.确定加工工艺 (1)加工工艺分析 按长径比的大小,孔可分为深孔和浅孔两类。 (2)加工过程 确定加工顺序时,按照先粗后精、先面后孔的原则,其 加工顺序为: 1)编程加工前,应首先钻孔前校平工件、用中心钻钻 6×φ8mm的中心孔; 2)同φ10mm铣刀铣削型腔; 3)用φ8mm钻头钻6×φ8mm的通孔,加工路线: L→M→N→I→J→K;
- 1、下载文档前请自行甄别文档内容的完整性,平台不提供额外的编辑、内容补充、找答案等附加服务。
- 2、"仅部分预览"的文档,不可在线预览部分如存在完整性等问题,可反馈申请退款(可完整预览的文档不适用该条件!)。
- 3、如文档侵犯您的权益,请联系客服反馈,我们会尽快为您处理(人工客服工作时间:9:00-18:30)。
编辑ppt
23
第三章 数控铣床与加工中心编程与操作
1.确定加工工艺 (1)加工工艺分析 按长径比的大小,孔可分为深孔和浅孔两类。 (2)加工过程 确定加工顺序时,按照先粗后精、先面后孔的原则,其 加工顺序为: 1)编程加工前,应首先钻孔前校平工件、用中心钻钻 6×φ8mm的中心孔; 2)同φ10mm铣刀铣削型腔; 3)用φ8mm钻头钻6×φ8mm的通孔,加工路线: L→M→N→I→J→K;
编辑ppt
5
第三章 数控铣床与加工中心编程与操作
编辑ppt
6
第三章 数控铣床与加工中心编程与操作
(3)参考程序
编辑ppt
7
第三章 数控铣床与加工中心编程与操作
编辑ppt
8
第三章 数控铣床与加工中心编程与操作
编辑ppt
9
第三章 数控铣床与加工中心编程与操作
编辑ppt
10
第三章 数控铣床与加工中心编程与操作
编辑ppt
14
第三章 数控铣床与加工中心编程与操作
1.加工工艺方案
(1)加工工艺路线
1)切入、切出方式选择。铣削封闭内轮廓表面时,刀具
无法沿轮廓线的延长线方向切入、切出,只有沿法线方
向切入、切出或圆弧切入、切出。切入、切出点应选在
零件轮廓两几何要素的交点上,而且进给过程中要避免
停顿。
2)铣削方向选择。一般采用顺铣,即在铣削内轮廓时采
编辑ppt
24
第三章 数控铣床与加工中心编程与操作
(3)工、量、刃具选择
编辑ppt
25
第三章 数控铣床与加工中心编程与操作
(4)合理切削用量的选择
编辑ppt
26
第三章 数控铣床与加工中心编程与操作
2.参考程序编制 (1)工件坐标系建立 根据工件坐标系建立原则,在六方体毛坯的中心建立工 件坐标系,Z轴原点设在顶面上,六方体上表面的中心 (即O圆的圆心)设为坐标系原点。 (2)基点坐标计算 如图3-104所示各圆的圆心坐标见表3-27。
值,将X、Y向的零偏值输入到工件坐标系G54中;然后将加工所用
刀具装上主轴,再将Z轴设定器安放在工件的上表面上,确定Z向的
零偏值,输入到工件坐标系G54中。
5)设置刀具补偿值。首先将刀具半径补偿值8.3输入到刀具补偿地
址D01;然后将刀具半径补偿值8.0输入到刀具补偿地址D02。
编辑ppt
11
第三章 数控铣床与加工中心编程与操作
编辑ppt
2
第三章 数控铣床与加工中心编程与操作
(2)工、量、刃具选择
编辑ppt
3
第三章 数控铣床与加工中心编程与操作
(3)合理选择切削用量
编辑ppt
4
第三章 数控铣床与加工中心编程与操作
2.参考程序编制 (1)工件坐标系建立: 根据工件坐标系建立原则,在φ40mm圆台中心建立工件 坐标系,Z轴原点设在顶面上,圆台中心设为坐标系原点。 (2)基点坐标计算 如图3-100所示各基点的坐标值见表3-17。
第三章 数控铣床与加工中心编程与操作
3.6 典型零件的编程与操作
3.6.1 平面外轮廓零件的编程与操作
平面外轮廓零件如图3-99所示。 已知毛坯尺寸为 62mm×62mm×21mm的长方 料,材料为45钢,按单件生产 安排其数控加工工艺,试编写 出凸台外轮廓加工程序并利用 数控铣床加工出该零件。
编辑ppt
3.操作步骤及内容
1)开机。开机,各坐标轴手动回机床原点。
2)刀具安装。根据加工要求选择φ16mm高速钢立铣刀,用弹簧夹
头刀柄装夹后将其装上主轴。
3)清洁工作台,安装夹具和工件。将机用虎钳清理干净装在干净的
工作台上,通过百分表找正,再将工件装正在机用虎钳上。
4)对刀设定工件坐标系。首先用寻边器对刀,确定X、Y向的零偏
18
第三章 数控铣床与加工中心编程与操作
编辑ppt
19
第三章 数控铣床与加工中心编程与操作
(3)参考程序
编辑ppt
20
第三章 数控铣床与加工中心编程与操作
编辑ppt
21
第三章 数控铣床与加工中心编程与操作
编辑ppt
22
第三章 数控铣床与加工中心编程与操作
3.6.3 孔类零件的编程与操作
图3-103所示为零件,已 知材料为45钢,毛坯尺 寸为 80mm×80mm×20mm, 所有加工面的表面粗糙 度值为Ra1.6μm。试编 写此工件的加工程序并 在数控铣床上加工出来。
1
第三章 数控铣床与加工中心编程与操作
1.加工工艺方案 (1)加工工艺路线 1)选择切入、切出方式。考虑刀具的进、退刀路线时, 刀具的切出或切入点应在沿零件轮廓的切线上,以保证 工件轮廓光滑;应避免在工件轮廓面上垂直上、下刀而 划伤工件表面;尽量减少在轮廓加工切削过程中的暂停, 以免留下刀痕。 2)选择铣削方向。一般情况下尽可能采用顺铣,即外轮 廓铣削时宜采用沿工件顺时针方向铣削。 3)选择铣削路线。首先粗、精加工环凸台;然后粗、精 加工六棱柱凸台;最后掉头,铣削四棱柱台外轮加工中心编程与操作
4.评分标准
编辑ppt
13
第三章 数控铣床与加工中心编程与操作
3.6.2 平面内轮廓零件的编程与操作
平面内轮廓零件如图3-101所示。 已知毛坯尺寸为 70mm×70mm×20mm的长方 料,材料为45钢,按单件生产 安排其数控加工工艺,试编写 出该型腔加工程序并利用数控 铣床加工出该工件。
6)输入加工程序。将编写好的加工程序通过机床操作面板输入到数 控系统的内存中。 7)调试加工程序。把工件坐标系的Z值沿+Z向平移100mm,按下数 控启动键,适当降低进给速度,检查刀具运动是否正确。 8)自动加工。把工件坐标系的Z值恢复原值,将进给倍率开关打到 低档,按下数控启动键运行程序,开始加工。机床加工时,适当调 整主轴转速和进给速度,并注意监控加工状态,保证加工正常。 9)检测。取下工件,用游标卡尺进行尺寸检测。 10)清理加工现场。 11)按顺序关机。
用沿内轮廓逆时针的铣削方向比较好。
3)铣削路线。凸台轮廓的粗加工采用分层铣削的方式。
由中心位置处下刀,采用环切的切削方法进行铣削,去
除多余材料。粗加工与精加工的切削路线相同。
编辑ppt
15
第三章 数控铣床与加工中心编程与操作
(2)工、量、刃具选择
编辑ppt
16
第三章 数控铣床与加工中心编程与操作
(3)合理切削用量的选择
编辑ppt
17
第三章 数控铣床与加工中心编程与操作
2.参考程序编制 (1)工件坐标系建立 根据工件坐标系建立原则,在六方体毛坯的中心建立工 件坐标系,Z轴原点设在顶面上,六方体上表面的中心设 为坐标系原点。 (2)基点坐标计算 如图3-102所示各点坐标坐标见表3-22。
编辑ppt