后桥纵臂断裂失效分析
大众新速腾后悬架纵臂断裂的原因

大众新速腾后悬架纵臂断裂的原因2015-10-15 15:43 常艳飞宝马汽车维权阅读 1294作者(秋风,高级工程师)(二)、分析和说明新速腾纵臂断裂原因看了以上图片,不难看出,综臂的断裂源都在同一部位,都在纵臂最窄的部位的上段,而且其断裂形状基本都一样,这是什么原因呢?下面我们从新速腾的纵臂结构、形状进行科学分析;1、在上述(一)、新速腾纵臂的基本状况的第1,测出,新速腾纵梁厚度3.00mm;纵臂上部是弧形,纵臂后宽、前窄、中更窄,而下部基本成直线;奥迪100的纵臂为较粗壮的铸造件,尼桑风度纵臂厚度是5mm,而新速腾纵梁厚度是3mm。
大众为了省材料,采用厚度仅3.00mm制造新速腾的纵臂。
为了解决3.00mm片状纵臂的强度,大众把纵臂上、下、中锻的截面压各种曲形形状,原则上是可加强3.00mm片状纵臂的强度;但问题出在,如果纵臂上下基本是直线,通过锻压纵臂上下截面的弯曲度基本一样;可新速腾的纵臂形状,下段基本成直线,上段是头尾相差近一倍宽的弧形。
这种情况下,上下段不可能段压形状相同的曲形。
见下图,新速腾纵梁截面,上段与下段弯曲度不一样,下段的截面似半圆状态、弯曲均匀、圆滑、开口小;而上段的截面,弯曲不均匀、不圆滑、开口大,这决定了上段其抗扭、抗弯、抗变形能力比下段差,也决定了新速腾纵梁的断裂源都在纵梁上段的原因。
2、在弧形工件上受力状态,见下图底部是直线的弧形工件,肯定有一处最窄的部位;下图,最窄的部位就在蓝色虚线B线上。
在底部是直线的弧形工件,最窄的部位是应力集中的部位;根据力学原理,由于构件截面尺寸突然变化而引起应力局部增大的现象,称为应力集中。
纵臂上方蓝虚线部位纵臂截面尺寸突然变化,引起应力局部增大的现象,是应力集中的部位;应力集中处的局部应力值,直接影响了部件的损坏或引发裂纹的重要原因之一。
设计人员为加强3.00mm片状纵臂的强度,把纵臂上下缎压成曲形,这种思路是没错;但是设计人员却疏忽了,底部是直线的弧形工件,在弧形最窄的部位,引起应力局部增大的现象,是应力集中的部位;受力工件承受着压力、扭力、拉力等;受力工件在尺寸突然变化处,是应力集中的部位;加上上述所指,大众悬架不合理的设计,使纵臂的断裂都在纵臂上方,而且裂源都在纵臂最窄的部位。
【精品】汽车零件后桥半轴套管断裂失效分析 (2)
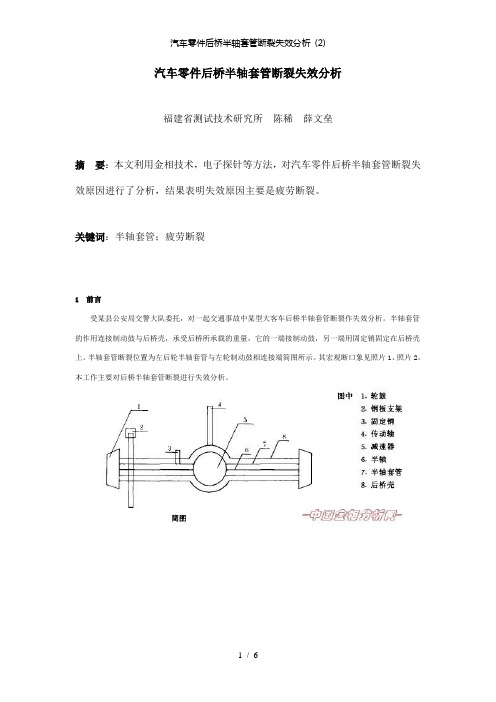
汽车零件后桥半轴套管断裂失效分析福建省测试技术研究所陈稀薛文垒摘要:本文利用金相技术,电子探针等方法,对汽车零件后桥半轴套管断裂失效原因进行了分析,结果表明失效原因主要是疲劳断裂。
关键词:半轴套管;疲劳断裂1 前言受某县公安局交警大队委托,对一起交通事故中某型大客车后桥半轴套管断裂作失效分析。
半轴套管的作用连接制动鼓与后桥壳,承受后桥所承载的重量,它的一端接制动鼓,另一端用固定销固定在后桥壳上。
半轴套管断裂位置为左后轮半轴套管与左轮制动鼓相连接端简图所示。
其宏观断口象见照片1、照片2。
本工作主要对后桥半轴套管断裂进行失效分析。
照片1 照片22 实验方法从半轴套管断口区域用电火花线切割法截取二块试样,取其中一块磨制成金相光片,用4%硝酸酒精腐蚀成金相试块,在OLYMPUS-BHZ型光学显微镜及EPM-810Q电子探针显微分析仪作金相组织检验。
另一块用于断口的宏观和微观检验,称断口试块。
用钻床钻取半轴套管的碎屑若干,用化学分析法测定该种材质中的碳(C)、硅(si)、锰(Mn)、磷(P)和硫(S)元素的质量分数。
用HRBV-187.5型布洛维硬度计测定该样表面硬度。
3 实验结果分析及讨论3.1化学成分经化学分析方法分析,该送检样化学成分见下表,其材质为45Mn2钢,其成分符合ZB/TT06003-1989标准要求。
3.2金相组织分析据目前所查到的标准ZB/TT06003-1989的规定半轴套管的热处理工艺为调质处理,其正常金相组织为回火索氏体组织。
而该送检样在光学显微镜和电子探针显微分析仪下,对金相试块观察到的金相组织为网状不连续的铁素体+珠光体+屈氏体组织,详见照片3、4、5,与标准规定中的金相组织有差异。
说明热处理的工艺存在问题。
照片3 金相组织×265照片4 金相组织×530 照片5 金相组织×5303.3表面硬度测定根据ZB/TT06003-1989中的规定,半轴套管的表面硬度范围为HRC33-48。
关于后纵臂扭梁疲劳断裂问题分析20101115

关于Z200HB 车型后纵臂扭梁疲劳断裂问题问题描述问题描述::路试车辆反馈的问题―――后扭梁左边托臂(圆管柱)开裂,故障发生里程32584km。
图1详见:2010年11月10日发布的众泰汽车《试验产品故障反馈单》(附后)背景信息背景信息::Z200HB 车型是在定远汽车试验场进行道路试验,该试验场面积近7km 2,现拥有4km 椭圆型高速试验环道,2.2km 综合性能试验路,6.6km 凸凹不平试验路,10km 越野路和5km 场区山路,还拥有地形通过性试验设施、城市工况模拟试验广场、淋雨试验台、质心测试平台、标准纵坡(20%~60%)等重要专用试验设施,以及一套完整的、在国内较为先进的测试仪器。
定远场的汽车高速试验环道,是国内第一条长圆形的高速环道,全长4公里,南、北直线段各长1.25公里,东、西弯道(含缓和曲线)各长750米,路面宽12米,分高、中、低3条车道,计算行车速度分别为每小时60、90、120公里,弯道半径为165米。
高速车道安全带横向坡度达42.3°。
图2现场调查现场调查::1观察了定远试验场寄回的三个Z200HB 车型车用的失效扭梁,其左侧均发生了此类失效,有一个右侧发生了明显的失效,另外两个右侧焊缝出现了目视可见的裂纹,沿着焊缝的边缘;图3左侧右侧2断口有光亮的光滑区和暗淡的粗糙区,符合疲劳失效的典型特征;3Z200HB车型的后悬架为纵臂扭梁式:纵臂为无缝圆管,管壁厚3.5毫米,纵臂有效回转长度469.5毫米(注:)。
图4 Z200HB的纵臂表1竞争车型的纵臂长度数据车型纵臂长度(单位:mm)菲亚特熊猫440标志207 450雷诺塞里奥420大众波萝424本田飞度374扭梁采用倒U字形钢板,板厚4.5毫米,扭梁大约处于纵臂的中间位置,扭梁起部分的横向稳定杆作用图5扭梁断面形状在扭梁处又再加了一根横向稳定杆图6 横向稳定杆扭梁与纵臂以及其上的减震器安装支架的焊接工艺是用二氧化碳气体保护焊焊接区域有飞溅,焊缝不饱满。
汽车后驱动桥断裂失效分析

汽车后驱动桥断裂失效分析
李玲;王荣
【期刊名称】《理化检验-物理分册》
【年(卷),期】2007(043)006
【摘要】汽车后驱动桥由多个零件焊接而成,在行驶约790 000 km时该零件发生断裂.通过宏观分析、显微组织分析、化学成分分析以及断口形貌分析后认为,该零件断裂性质为疲劳断裂,主要原因为被焊接的两个零件尺寸差异较大,局部形成应力集中,再加上焊接热影响区存在焊接应力和魏氏体组织,并在汽车行进中不断受到颠簸和震动造成该区域产生裂纹源,进而在运行一定时间后发生疲劳断裂.
【总页数】3页(P305-306,310)
【作者】李玲;王荣
【作者单位】上海材料研究所,上海,200437;上海材料研究所,上海,200437
【正文语种】中文
【中图分类】U463.218
【相关文献】
1.驱动桥壳断裂的失效分析 [J], 赵福森
2.某前驱动桥断裂失效分析 [J], 张振华;周彬;王欢锐
3.汽车驱动桥半轴轴承失效分析 [J], 汪茂根; 方强; 宋寅; 黄高荣
4.汽车驱动桥壳断裂失效分析与优化 [J], 潘运平;姜富山;王浩;吴昌权;廖烈平
5.汽车后驱动桥差速器壳体断裂失效分析 [J], 王雪梅;付宏博
因版权原因,仅展示原文概要,查看原文内容请购买。
汽车右后拖曳臂轴断裂原因分析

汽车右后拖曳臂轴断裂原因分析徐小红【摘要】某汽车仅使用2 d(天)、行驶56 km,其右后拖曳臂轴即发生断裂.采用断口宏观和微观检验、硬度测试、金相检验、化学成分分析等方法,对该右后拖曳臂轴断裂的原因进行了分析.结果表明:该轴断裂性质为沿晶脆性断裂,断裂的主要原因是其锻造组织存在缺陷及未经调质处理,使轴的强度大大降低;次要原因是轴表面因磨削加工过热形成了表面磨削淬火层,增加了轴表面的脆性及拉应力,使微裂纹在轴表面产生.%When an automobile used for two days and traveled 56 km,it was found that the shaft of the right rear trailing arm fractured.The fracture reasons of the shaft of the right rear trailing arm were analyzed by macro and micro fracture examination,hardness testing,metallographic examination,chemical composition analysis and so on.The results show that:the main reasons for the fracture of the shaft were that the defects existed in the forging structure and the quenching and tempering heat treatment didn't carry out,which greatly reduced the strength of the shaft;the secondary reason was that the surface grinding hardening layer formed on the surface of the shaft due to the overheating grinding,which increased the brittleness and tensile stress of the shaft surface,and made the micro cracks appear on the shaft surface.【期刊名称】《理化检验-物理分册》【年(卷),期】2018(054)001【总页数】6页(P55-59,73)【关键词】拖曳臂轴;断裂;组织缺陷;调质热处理;磨削加工【作者】徐小红【作者单位】福建省农业机械化研究所,福州 350005【正文语种】中文【中图分类】TG115.2后拖曳臂是汽车拖曳臂式悬挂系统的重要组成部分,拖曳臂式悬挂系统是专为汽车后轮设计的悬挂系统,其作用是将车轮所受的各种力和力矩传递给车架和车身,并能吸收、缓和路面传来的振动和冲击。
公铁两用长江大桥公路纵梁下翼缘裂缝病害分析

公铁两用长江大桥公路纵梁下翼缘裂缝病害分析洪汉麟摘要:公铁两用桥的公路桥面钢纵梁产生裂缝后,将直接影响大桥的公路与铁路正常运营。
为了防止与处理好此类病害,同时,也为了使今后有类似的公铁两用桥在设计与养护方面有借鉴作用,针对某长江大桥公路纵梁下翼缘产生裂缝的状况进行受力分析,找出真正产生的原因,以便更好的进行加固处理。
一、桥梁的结构形式某长江大桥是一座公铁两用特大桥。
公路桥于1995年6月正式运营,铁路桥于1996年9月正式运营。
其中:正桥是11孔双层钢桁梁,上层是公路桥面,下层是铁路桥面。
正桥采用3跨(162+162+162)m + 3跨(162+161+162)m + 3跨(180+216+181)m + 2跨(126+126)m 共四联的连续钢桁梁。
公路桥面每联之间采用梳形板钢质伸缩缝,每联内按每36M间隔设置一道60型橡胶平板伸缩缝,请见照片1。
公路桥面下是预制的钢筋混凝土行车道板,行车道板是搁置在36m的纵梁上,纵梁又是按4跨连续梁(4*9m)形式搁置在横梁上,请见照片2。
照片1 照片2纵梁端头上方正好是橡胶伸缩缝,纵梁端头下方是工字形钢横梁,并且是两根纵梁端头共用一根钢横梁,请见图一。
二、 病害产生的状况公路桥自1995年6月正式运营以来,一直都比较正常。
到了2000年左右,公路桥面开始出现破损情况,尤其是在伸缩缝附近出现大量的破损开裂。
之后,对伸缩缝进行过多次更换,但经过一段时间之后,伸缩缝附近又会出现大量的破损开裂。
铁路桥管处自1996年9月正式接管运营后,每年都要对桥梁进行春检与秋检。
2004年5月19日首次发现公路桥面下的横梁腹板上出现U 字形裂缝。
裂缝的位置正好在伸缩缝下面的横梁腹板上的加劲板下端头处,请见照片3。
照片3之后,又连续发现了几十处横腹板上U 字形裂缝。
产生这种裂缝的受力状态请见图二。
图一加强板中横联钢支座横梁纵梁行车道板桥面型伸缩缝原设计受力状态图二此拐点产生疲劳裂缝横梁产生裂缝受力状态2012年11月14日下午,在钢桁梁的上平联作业人员首次发现了4E11竖杆所对应的纵梁端头下翼缘出现严重的开裂现象,请见照片3与照片4。
微型汽车后桥半轴力学分析及断裂分析

轴的头部商径很大,另一端花键处到 轴承安装处直径相对很小,如果采用整体 锻造在头部镦出巾124直径是很困难的成
本也较高。所以采用摩擦对焊的工艺对截 面选在弯曲力矩很小的地方。另外在图l所 示的区域进行中频表面淬火,表面硬度 HRC50一60心部硬度HRC25—32,这样可以 提高疲劳强度。半轴材料采用45号钢。
万方数据
科技创业家TECHNOLOGICAL P10NEERs
1 49
有纵向力和侧向力作用,所以半轴只受垂 向弯矩:
垂向力F,,最大,纵向力F。,=O,侧向力 F,,=0:此时垂直力最大值F,:为:
F:2L=F:2R=K(G 2/2一g。)=807l(N) 其中K为动载系数K=1.8,
而魄r=足ב2£×6=282.49(N’m)
该半轴按照工艺规范生产并检验合格 后装车。在试车过程中发生断裂,对断裂件 的原材料成分进行了光谱分析,其结果符 合有关技术标准,为弄清楚该半轴早期断 裂的原因,本文对其硬度、显微组织、宏观 及微观端【J进行了研究。 3.1试验方法
首先l记录并分析断口宏观形貌,然后 用酒精等将端口表面清洗干净.用扫描电 子显微镜做断u微观形貌分析,用光学显 微镜对半轴表层和心部显微组织进行研 究,|一l时测定了其硬度。
4结论 45#汽车后桥半轴中存在较多的铁素
体是造成半轴疲劳断裂的原因。应该在生 产中找出造成调质淬火工艺温度不正确的 原因,并予以改正,使后桥半轴的调质组织 和硬度符合技术要求。
(a)纵向 (a)Lห้องสมุดไป่ตู้ngthwise section
(b)纵向 (b)Transverse section
某驱动桥半轴套管断裂分析和优化设计

某驱动桥半轴套管断裂分析和优化设计发表时间:2018-10-29T10:11:01.057Z 来源:《知识-力量》2018年11月上作者:张瑞华穆玉峰[导读] 后桥是汽车的关键零部件,起着承受载荷和扭矩的作用,一旦出现断裂,将严重影响乘客的生命安全,故对其失效模式分析尤为重要。
本文对一款新型后桥在道路试验过程中发生半轴套管断裂的失效模式进行分析,通(精诚工科汽车系统有限公司,河北保定 071000)摘要:后桥是汽车的关键零部件,起着承受载荷和扭矩的作用,一旦出现断裂,将严重影响乘客的生命安全,故对其失效模式分析尤为重要。
本文对一款新型后桥在道路试验过程中发生半轴套管断裂的失效模式进行分析,通过材质检测及理论计算,对失效因素进行排查。
最终找到失效原因,并提出改进措施,避免再次失效,对提高汽车的安全性意义重大。
关键词:驱动桥;半轴套管;断裂引言驱动桥壳起着支撑汽车载荷的作用,同时还要承受制动载荷、静载荷所引起的较大弯矩和扭矩。
一旦桥壳出现断裂,将会影响整车安全,故对桥壳断裂失效模式分析意义重大。
现某公司有一款新设计后桥在搭配汽车进行道路试验可靠性试验过程中,行驶至强化路的石坏路时,左后驱动桥半轴套管发生断裂,需立刻分析原因并制定整改措施,避免再次失效断裂。
1、基本情况某厂生产的两根不同批号的汽车半轴套管在使用过程中发生断裂,断裂情况类似,均发生于中的R2.5mm过渡圆角处。
对其中一件半轴套管进行了断裂分析。
图纸要求半轴套管采用45Mn2钢管生产,产品硬度要求为220~270HBW。
2、加工工艺分析将该桥的未断裂边拆解后,需对轮毂内轴承颈R角进行测量为4mm,设计要求为4~4.4mm,故该内轴承颈R角是符合设计要求,但在R 角根部与轴承颈之间存在一台阶,此台阶在设计中是不存在的,此处R角仅有1mm,将会引起应力集中,容易产生裂纹。
针对台阶产生的问题进行一番调查后,发现是由于轴承颈需要经过粗车-精车-磨削三个步骤,在实际操作中,磨削轴承颈时并未磨轮毂内轴承颈R角,导致产生台阶。
- 1、下载文档前请自行甄别文档内容的完整性,平台不提供额外的编辑、内容补充、找答案等附加服务。
- 2、"仅部分预览"的文档,不可在线预览部分如存在完整性等问题,可反馈申请退款(可完整预览的文档不适用该条件!)。
- 3、如文档侵犯您的权益,请联系客服反馈,我们会尽快为您处理(人工客服工作时间:9:00-18:30)。
第36卷增刊Vol.36Sup. 2011年9月HEAT TREATMENT OF METALS September2011后桥纵臂断裂失效分析倪娟丽,黄艳灵,高朝乾,刘强,马芳武,赵福全(吉利汽车研究院,浙江萧山311228)摘要:采用断口分析、化学成分分析、拉伸试验、X射线探伤和显微组织检验等方法对某汽车后桥纵臂的断裂进行了失效分析,判断断裂时效的主要原因是样件焊接质量差及基材材质不合格,建议严格把控焊接质量及原材料的品质。
关键词:后桥纵臂;断裂;金相组织检验;化学成分分析;X射线探伤中图分类号:TG142.4文献标志码:AFracture failure analysis of vertical arm of rear axleNI Juan-li,HUANG Yan-ling,GAO Chao-qian,LIU Qiang,MA Fang-wu,ZHAO Fu-quan(Geely Automoblie Research Institute,Xiaoshan Zhejiang311228,China)Abstract:The failure analysis for fracture on vertical arm of rear axle was carried by inspection of fracture,examination of microstructure and macrostructure,tensile test,X-ray detection and analysis of chemical composition.The main causation of fracture was that the welding quality and the chemical composition of the substrate were not qualified.It is suggested that the welding technology and the quality of raw material should be strictly standardized,supervised and controlled.Key words:vertical arm of rear axle;fracture,microstructure examination;analysis of chemical composition;X-ray detection汽车纵臂连接后桥、制动器及减震器,后桥起承载车身的作用,制动器连接车轮,减震器缓冲平衡汽车行驶过程中的颠簸,保证车辆的操稳性。
工作中,纵臂承受扭转力矩及弯曲应力作用,因而常常也伴随有失效问题。
某试验车在一万公里耐久试验过程中,车辆行驶至里程7672km﹙强化坏路7672km﹚时,后桥纵臂发生断裂,图1所示为该车后桥焊接总成,箭头指向断裂的一侧。
图2为后桥纵臂焊接总成,箭头指向裂纹处。
此件采用SAPH400(Q/BQB310-2009[1])钢板,加工工艺为:拉伸—切边—翻边—焊接(采用气体保护焊,焊材ER50-6/1.0;电压:25-30V;电流:180-220A;气体流量:15-20L/min;送丝速度:45-55cm/min)。
本文就断裂样品进行失效分析,判断其断裂的原因,并提出改进措施。
图1后桥焊接总成图2后桥纵臂Fig.1Rear axle Fig.2Vertical arm of rear axle1检测分析1.1断口检测图3所示后桥右后纵臂的断裂部位,照片显示裂纹沿着焊缝的地方开裂。
沿蓝色区域取样,得到图4,可以看出,沿裂纹边缘有很多焊瘤存在,见图中箭头指向。
由于图4中黄色区域部位裂纹尖锐,并且距离制动器安装支架与纵臂的焊接部位及右后纵臂上下板焊接部位最近,故推测此处为断裂源。
将该样品清洗后,进行收稿日期:2011-06-25作者简介:倪娟丽(1984-),女,材料工程师,主要从事金属材料分析工作,E-mail:juanlini@。
增刊倪娟丽,等:后桥纵臂断裂失效分析123扫描观察。
图5~6为断口的低倍形貌,图中箭头指向为裂纹、孔洞、裂纹源。
从宏观分析裂纹,断裂是从焊缝焊趾处产生的,断面始处平坦,肉眼可见部分疲劳纹路;断面有锈蚀现象,且焊接处随处可见较多的焊瘤,焊缝粗糙不平整且可见孔洞类缺陷。
图3断裂部位图4断裂部位的一侧Fig.3Fracture zone Fig.4Parts of fracture zone图5断口低倍形貌,箭头指向裂纹、孔洞、裂纹源Fig.5SEM micrographs of the fracture,showing crack,holes,crack source图6断口低倍形貌,箭头指向裂纹、孔洞、裂纹源Fig.6SEM micrographs of the fracture,showing crack,holes,crack source图7为裂纹源处低倍断裂形貌,照片显示,此处有微裂纹及准解理特征。
对图7中蓝色区域放大得到图8,从图8可以看出,裂纹间隙有球状氧化物产生,如图中箭头指向。
由于此种氧化物在常温下是无法形成的,推图7裂纹源处低倍形貌图8裂纹源处高倍形貌Fig.7Morphology of the crack source at low magnification Fig.8Morphology of the crack source at high magnification第36卷124测此氧化物是钢板在熔炼脱氧过程中脱氧不完全造成的氧化物夹杂,或者是在焊接时形成的,从而推测在焊接的同时此处可能已存在微裂纹。
图9为断面的部分形貌,断面有明显的疲劳纹理,箭头指向疲劳裂纹源。
图10为终断区形貌,具有准解理特征。
图9疲劳裂纹形貌图10终断区形貌Fig.9Morphology of fatigue fracture Fig.10Morphology of the final fracture region1.2成分检测采用SPECTRO MAXx 直读光谱仪(ICP-OES )对基体材料的化学成分进行了分析,检测结果见表2。
将所测结果与标准规定值进行对比分析,发现基体材料的铝含量偏低,不符合标准要求,因而从化学成分含量的角度判定此材料不符合材料定义要求。
表1基体材料(SAPH400)的化学成分(wt%)Table1Chemical composition of the substrate (SAPH400)(wt%)化学成分C Si Mn P S Al 检测值0.170.160.390.0100.0170.005标准值≤0.21≤0.30≤1.40≤0.030≤0.025≥0.010Q/BQB 310-2009判断结果OKOKOKOKOKNG1.3力学性能检测采用CMT5605拉力机对基材样品进行了拉伸试验,其应力应变曲线如图11所示,由图得出其力学性能参数见表4,数据显示,其抗拉强度、屈服强度都符合标准Q/BQB 310-2009中的的规定,而断后延伸率偏低,这是由于钢板在经过冲压成型后存在加工硬化而导致其塑性降低[2]。
图11基材应力-应变曲线Fig.11Tensile stress-strain curve of substrate增刊倪娟丽,等:后桥纵臂断裂失效分析125实测值49534518.5标准值≥400≥255≥34 Q/BQB310-2009判断结果OK OK NG采用3000BLD/T布氏硬度计对基材的硬度进行了测量,测量结果为HBW(2.5/187.5):148/149/149,其平均硬度HBW148.67换算为材料的强度为513MPa,与抗拉强度值相比偏高一点,由于布氏硬度换算强度值本来就偏高,所以认为此数值正常。
1.4射线探伤采用RD2805A设备对后桥纵臂的焊缝进行了X射线检测试验,样品焊缝表面质量很差,有明显的焊接缺陷如孔洞、焊瘤、夹渣等,经X射线探伤后发现焊缝处有明显的未焊透、孔洞、裂缝、裂纹及夹渣等缺陷。
可见,此件焊接工艺很差。
1.5金相组织采用ZEISS AXIO IMAGER.A2M对样品进行了金相观察。
首先对基材夹杂物级别及基体组织进行了评定,表5为非金属夹杂物级别,图12和图13分别为金相显微镜下基材非金属夹杂物照片和基材组织形貌,结果显示,基材中非金属夹杂物级别符合钢板SAPH400夹杂物等级要求,并且其基体组织主要为铁素体及粒状珠光体,晶粒度为8.5级,未发现异常。
1.5 1.0 1.0 1.0 1.5 1.5 1.0 1.0图12非金属夹杂物图13基体金相组织Fig.12Non-metallic inclusions Fig.13Microstructure of substrate 图14为断面始处抛光态形貌,图15为组织形貌,可见断裂始处出现在焊接热影响区;焊肉处抛光态形貌如图15,组织形貌如图16,照片显示,其组织形貌为柱状晶,焊肉处有较多孔洞及未焊透,孔洞大者约0.5mm。
图14断面始处抛光形貌图15断面组织形貌Fig.14The polishing morphology of substrate Fig.15Microstructure of the fracture第36卷126图16焊肉处抛光形貌图17焊肉处组织形貌Fig.16The polishing morphology of welding zone Fig.17Microstructure of the welding zone2失效分析1)从宏观分析裂纹,断裂是从焊缝焊趾处产生的,断面始处平坦,肉眼可见部分疲劳纹路;断面有锈蚀现象,且焊接处随处可见较多的焊瘤,焊缝粗糙不平整且可见孔洞类缺陷;2)从微观观察分析,断面大多源于焊瘤处,可见孔洞、裂纹及疲劳纹路,断面显微组织为准解理及氧化特征,并且裂纹裂缝处存在球状氧化物,推测焊接过程中已有裂纹形成;3)纵臂焊接总成基材铝含量偏低,影响钢板的冲压成形性[3],化学成分不符合材料SAPH400(Q/BQB 310-2009)的定义要求;4)断裂件材料的力学性能中延伸率不符合要求,可能由于加工硬化及铝含量偏低导致其塑性降低;5)肉眼及射线探伤发现焊接品质很差,有明显的焊接缺陷如孔洞、焊瘤、夹渣等;6)基材非金属夹杂物、基体组织及晶粒度并未发现异常;7)金相分析发现断裂始处在焊接热影响区;焊肉处有较多孔洞及未焊透,孔洞大者约0.5mm 。
3结论通过以上分析,此件断裂失效主要由于焊接品质太差,另外原材料品质不合格,建议严格把控原材料品质及焊接质量。