液压元件的计算与选择
液压系统设计计算实例
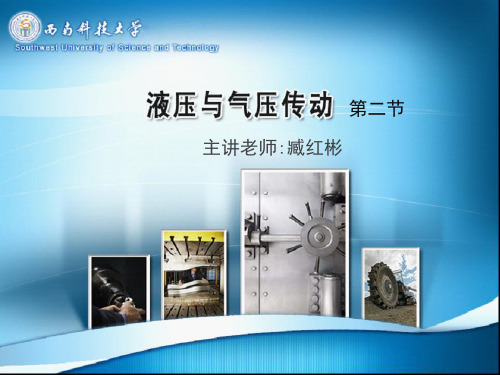
A1=F/(p1-0.5p2)=35511/(4×106-0.5×0.6×106)cm2 ≈96cm2
液压缸内径D就为:D= 4 A= 1 4 ×=9161.06cm
对D圆整,取D=110mm。由dp=0.707Dp,经圆整得 d=80mm。计算出液压缸的有效工作面积A1=95cm2, A2=44.77 cm2。 工进时采用调速阀调速,其最小稳定流量
则液压泵输出压力为2.05MPa。液压泵的总效率ηp=0.8,液压泵流量 40L/min,则液压泵驱动调集所需的功率为:
P=ppqp/ηp=2.05×106×40×10-3W=1708W 据此选用Y112M—6—B5立式电动机,其额定功率为2.2kW,转速为 940r/min,液压泵输出流量为33.84L/min、5.33L/min,仍能满足系统要求 。
1.负载分析与速度分析
1)负载分析
由工作负载Fw =30kN,重力负载FG=0,按启动换向时间和 运动部件重量(F·t=m(v2–v1))计算得到惯性负载Fa=1000N,摩擦 阻力Ff=1960N。
取液压缸机械效率ηm =0.9,则液压缸工作阶段的负载值见表 。
2)速度分析
由快进、快退速度为6m/min,工进速度范围为 20mm/min~120mm/min按上述分析可绘制出负载循环图和速度循环 图(略)。
2.确定参数
1)初选液压缸的工作压力
由最大负载值查教材中表9-3,取液压缸工作压力为4MPa。
2)计算液压缸结构参数
为使液压缸快进与快退速度相等,选用单出杆活塞缸差动连接的方 式实现快进,设液压缸两有效面积为A1和A2,且A1=2 A2,即 d=0.707D。为防止钻通时发生前冲现象,液压缸回油腔背压p2取 0.6MPa,而液压缸快退时背压取0.5MPa。
液压系统设计计算公式
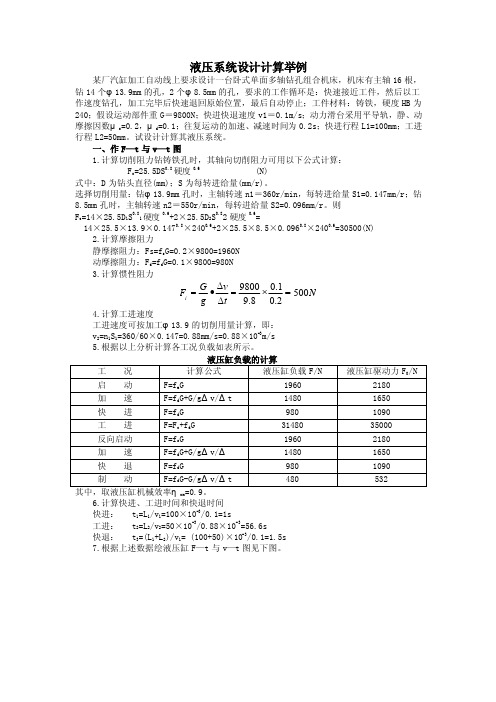
液压系统设计计算举例某厂汽缸加工自动线上要求设计一台卧式单面多轴钻孔组合机床,机床有主轴16根,钻14个φ13.9mm 的孔,2个φ8.5mm 的孔,要求的工作循环是:快速接近工件,然后以工 作速度钻孔,加工完毕后快速退回原始位置,最后自动停止;工件材料:铸铁,硬度HB 为240;假设运动部件重G =9800N ;快进快退速度v1=0.1m/s ;动力滑台采用平导轨,静、动摩擦因数μs =0.2,μd =0.1;往复运动的加速、减速时间为0.2s ;快进行程L1=100mm ;工进行程L2=50mm 。
试设计计算其液压系统。
一、作F —t 与v —t 图1.计算切削阻力钻铸铁孔时,其轴向切削阻力可用以下公式计算:F c =25.5DS 0.8硬度0.6(N)式中:D 为钻头直径(mm);S 为每转进给量(mm/r)。
选择切削用量:钻φ13.9mm 孔时,主轴转速n1=360r/min ,每转进给量S1=0.147mm/r ;钻8.5mm 孔时,主轴转速n2=550r/min ,每转进给量S2=0.096mm/r 。
则F c =14×25.5D 1S 0.81硬度0.6+2×25.5D 2S 0.82硬度0.6=14×25.5×13.9×0.1470.8×2400.6+2×25.5×8.5×0.0960.8×2400.6=30500(N) 2.计算摩擦阻力静摩擦阻力:Fs=f s G=0.2×9800=1960N 动摩擦阻力:F d =f d G=0.1×9800=980N 3.计算惯性阻力4.计算工进速度工进速度可按加工φ13.9的切削用量计算,即:v 2=n 1S 1=360/60×0.147=0.88mm/s=0.88×10-3m/s 5.根据以上分析计算各工况负载如表所示。
液压系统的设计计算2010秋
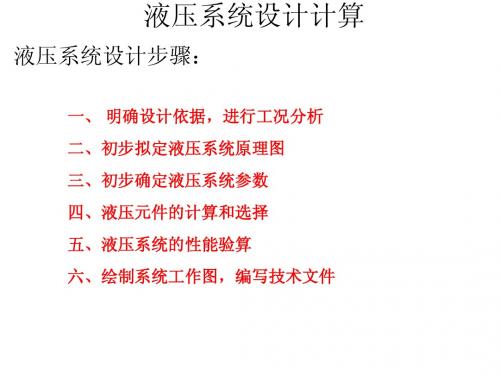
T 式中:Vi—— 系统在整个周期中第i个阶段内的用油量。 ☼如果液压泵的供油量是按工进工况选取时(如双泵供油方案, 其中小流量泵是供给工进工况流量的)其供油量应考虑溢流阀的最 小溢流量。
qp
k Vi
四、液压元件的计算和选择
1、 液压泵和电机功率
(3) 选择液压泵的规格型号
液压泵的规格型号按计算值在产品样本中选取。
许的范围内. 油液温升验算是计算系统的发热量和散热量,使热平衡后 的温度在允许的范围内。
五、液压系统的性能验算
2、系统发热温升验算 (1)系统发热功率Hi 式中,Pi为液压泵输入功率;Po为液压执行元件的输出功率。 如果已知液压系统的总效率 ,则系统发热功率Hi也可按下式 计算: 系统产生的热量要由油箱散热,由于管道散热与吸热基 本平衡,故可忽略不计。油箱散热功率按下式计算:
负载-位移(F-J)曲线表示,称为负载图;将各执行元件在工作循 环中各动作阶段的速度,用速度-时间(v-t )或速度-位移(v-l) 曲线表示,称为速度图。
从图中可明显看出最大负载和最大速度值及二者所
在的工况。这是确定系统的性能参数和执行元件结构参
数 (结构尺寸)的主要依据。
二、初步拟定液压系统原理图 拟定液压系统原理图是整个液压系统设计中重要的 一步,它涉及到所设计系统的性能和设计方案的经济性、
若验算不能满足要求,则A或q的值就必须进行修改。这些结 构参数最后还必须按GB2347--80和GB/T2348一93圆整成标准值。 确定执行元件的结构参数后,根据负载图和速度图,可以计算 出整个工作循环中各阶段的实际工作压力、流量和功率,并绘出 相应的p-l、Q-l和p-l图或p-t、Q-t和P-f图,称为工况图
沿程压力损失Δp 、局部压力损 Δpξ 有关压力损失公式计算。
液压系统设计计算
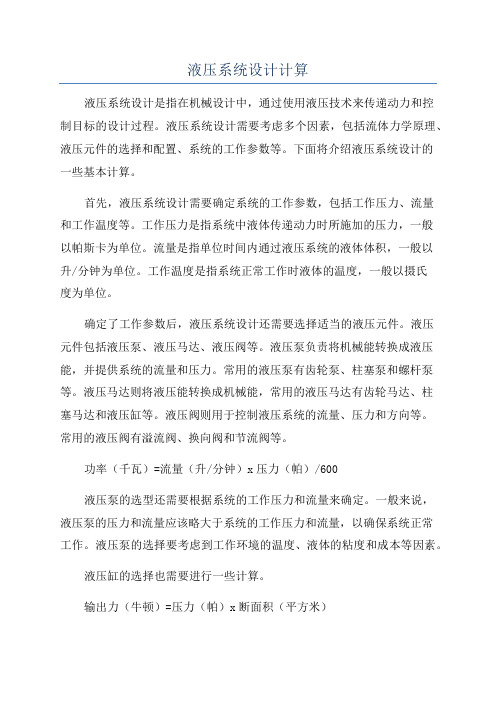
液压系统设计计算液压系统设计是指在机械设计中,通过使用液压技术来传递动力和控制目标的设计过程。
液压系统设计需要考虑多个因素,包括流体力学原理、液压元件的选择和配置、系统的工作参数等。
下面将介绍液压系统设计的一些基本计算。
首先,液压系统设计需要确定系统的工作参数,包括工作压力、流量和工作温度等。
工作压力是指系统中液体传递动力时所施加的压力,一般以帕斯卡为单位。
流量是指单位时间内通过液压系统的液体体积,一般以升/分钟为单位。
工作温度是指系统正常工作时液体的温度,一般以摄氏度为单位。
确定了工作参数后,液压系统设计还需要选择适当的液压元件。
液压元件包括液压泵、液压马达、液压阀等。
液压泵负责将机械能转换成液压能,并提供系统的流量和压力。
常用的液压泵有齿轮泵、柱塞泵和螺杆泵等。
液压马达则将液压能转换成机械能,常用的液压马达有齿轮马达、柱塞马达和液压缸等。
液压阀则用于控制液压系统的流量、压力和方向等。
常用的液压阀有溢流阀、换向阀和节流阀等。
功率(千瓦)=流量(升/分钟)x压力(帕)/600液压泵的选型还需要根据系统的工作压力和流量来确定。
一般来说,液压泵的压力和流量应该略大于系统的工作压力和流量,以确保系统正常工作。
液压泵的选择要考虑到工作环境的温度、液体的粘度和成本等因素。
液压缸的选择也需要进行一些计算。
输出力(牛顿)=压力(帕)x断面积(平方米)液压缸的选择要根据所需的输出力和工作压力来确定。
液压缸的密封性能和机械结构等因素也需要考虑。
另外,液压系统设计中还需要考虑管道的设计和安装。
管道的设计要根据系统的工作温度、压力和流量来确定。
管道的材料和尺寸选择要满足系统的需要,并保持良好的连接和密封性能。
综上所述,液压系统设计涉及到多个方面的计算和选择。
通过合理的设计和计算,可以确保液压系统的性能和可靠性。
因此,在液压系统的设计过程中,需要充分考虑各个因素,并进行适当的计算和分析。
液压系统的设计计算举例
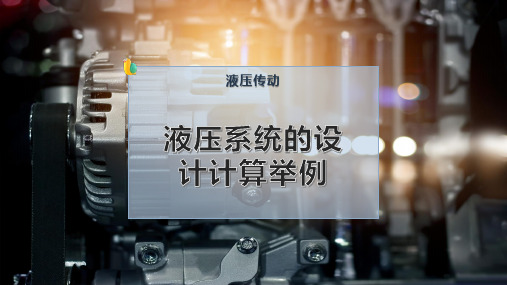
作缸的小腔,即从泵的出口到缸小腔之间的压力损失 Δp = 5.5×105 MPa ,于是小泵出
口压力 pp1 = 21.56×105 MPa (小泵的总效率 η 1 = 0.5 ),大泵出口压力 pp2 =
23.06×105 MPa (大泵的总效率 η 2 = 0.5 )。故电机功率为
P pp1q1 pp2q2 21.56 105 0.167 103 W 23.06 105 0.267 103 W 1 951.5 W
= 0.5 ,大泵出口压力 pp2 = 15.18×105 MPa (大泵的总效率 η 2 = 0.5 )。故电机功率
为
P1
pp1q1 1
pp 2 q2 2
13.68 105 0.167 103 0.5
W 15.18 105 0.267 103 0.5
W
1 267.5 W
(2)工进
小泵的出口压力 pp1 = p1 +Δp1 = 32.19×105 MPa ,大泵卸载,卸载压力取 pp2 =
液压传动
液压系统的设计计算举例
1.1 分析工况及主机工作要求,拟定液压系统方案 1.2 参数设计 1.3 选择元件 1.4 液压系统性能验算
液压系统的设计计算举例
1.1 液分析工况及主机工作要求,拟定液压系统方案
(一) 确定执行元件类型
(二) 确定执行元件的负载、速度变化范围
Fw 18 000 N
1
2
0.5
0.5
综合比较,快退时所需功率最大。据此查产品样本选用Y112M—6型异步电机,
电机功率2.2 kW,额定转速为940 r/min。
(三) 选择液压阀
根据液压阀在系统中的最高工作压力与通过该阀的最大流量,可选出这些元件的 型号及规格。选定的元件列于表中。
机械设计基础液压与气动元件的选型与应用
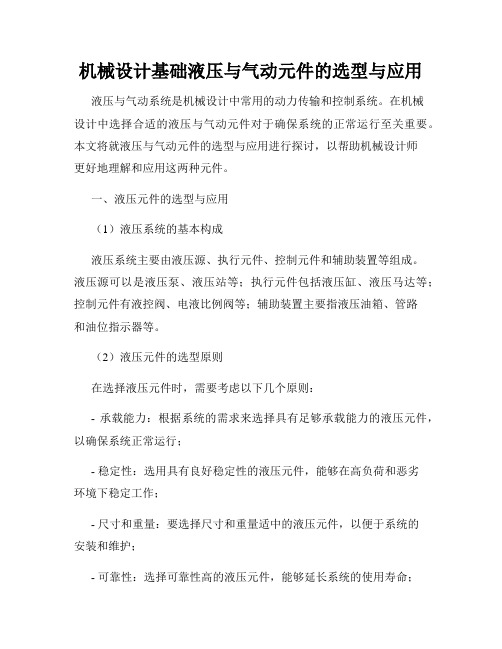
机械设计基础液压与气动元件的选型与应用液压与气动系统是机械设计中常用的动力传输和控制系统。
在机械设计中选择合适的液压与气动元件对于确保系统的正常运行至关重要。
本文将就液压与气动元件的选型与应用进行探讨,以帮助机械设计师更好地理解和应用这两种元件。
一、液压元件的选型与应用(1)液压系统的基本构成液压系统主要由液压源、执行元件、控制元件和辅助装置等组成。
液压源可以是液压泵、液压站等;执行元件包括液压缸、液压马达等;控制元件有液控阀、电液比例阀等;辅助装置主要指液压油箱、管路和油位指示器等。
(2)液压元件的选型原则在选择液压元件时,需要考虑以下几个原则:- 承载能力:根据系统的需求来选择具有足够承载能力的液压元件,以确保系统正常运行;- 稳定性:选用具有良好稳定性的液压元件,能够在高负荷和恶劣环境下稳定工作;- 尺寸和重量:要选择尺寸和重量适中的液压元件,以便于系统的安装和维护;- 可靠性:选择可靠性高的液压元件,能够延长系统的使用寿命;- 经济性:在满足系统需求的前提下,选择价格合理的液压元件。
(3)常用液压元件的应用液压系统中常用的液压元件有液压缸、液压泵、液压阀等。
- 液压缸:液压缸通过液压能将液体的压力转换成机械能,广泛应用于各种液压传动系统中;- 液压泵:液压泵是液压系统的动力源,能够将机械能转换成液体压能;- 液压阀:液压阀用于控制液压系统的流量和压力,是液压系统中的关键元件。
二、气动元件的选型与应用(1)气动系统的基本构成气动系统主要由气源、执行元件、控制元件和辅助装置等组成。
气源一般为压缩空气或惰性气体,执行元件有气缸、电磁阀等;控制元件有手动阀、电液比例阀等;辅助装置包括滤清器、压力表等。
(2)气动元件的选型原则在选择气动元件时,需要遵循以下几个原则:- 输出力和速度:根据系统的要求选择适当的输出力和速度的气动元件;- 稳定性:要选择具有良好稳定性的气动元件,以确保系统的稳定运行;- 维护性:选择易于维护和保养的气动元件,以降低系统的维护成本;- 耐用性:选用耐用且寿命较长的气动元件,能够延长系统的使用寿命;- 经济性:在满足系统需求的前提下,选择价格适中的气动元件。
液压油管选型计算公式
液压油管选型计算公式液压系统是工程领域中常见的一种动力传递系统,它通过液压油管传递压力,驱动液压执行元件完成各种动作。
在液压系统中,液压油管的选型是非常重要的,它直接影响到系统的工作性能和安全可靠性。
在进行液压油管选型时,需要考虑到液压系统的工作压力、流量、工作温度等因素,以确保选用的液压油管能够满足系统的工作要求。
液压油管的选型计算公式是液压系统设计中的重要内容,它可以帮助工程师快速准确地选择合适的液压油管。
下面我们将介绍液压油管选型计算公式的相关内容。
液压油管选型计算公式的基本原理是根据液压系统的工作压力和流量来确定液压油管的内径和壁厚。
在液压系统中,液压油管的内径和壁厚直接影响到油管的承压能力和耐腐蚀性能。
因此,在进行液压油管选型时,需要根据液压系统的工作压力和流量来计算出液压油管的内径和壁厚,以确保油管能够承受系统的工作压力并具有良好的耐腐蚀性能。
液压油管选型计算公式的基本形式如下:内径计算公式,d = (Q × 4) / (π× V)。
壁厚计算公式,t = (P × d) / (2 × S)。
其中,d为液压油管的内径,单位为毫米;Q为液压系统的流量,单位为立方米/秒;V为液压油的流速,单位为米/秒;P为液压系统的工作压力,单位为兆帕;t为液压油管的壁厚,单位为毫米;S为液压油管的安全系数。
在进行液压油管选型计算时,首先需要确定液压系统的工作压力和流量。
工作压力是液压系统设计中的重要参数,它直接影响到液压油管的承压能力和安全可靠性。
流量是液压系统传递动力的重要参数,它直接影响到液压油管的内径大小。
根据液压系统的工作压力和流量,可以通过上述公式计算出液压油管的内径和壁厚。
在进行液压油管选型计算时,还需要考虑到液压油管的材料和制造工艺。
液压油管通常采用碳钢、不锈钢等材料制成,不同材料的液压油管具有不同的承压能力和耐腐蚀性能。
在进行液压油管选型时,需要根据液压系统的工作环境和工作要求来选择合适的液压油管材料,以确保油管具有良好的耐腐蚀性能和承压能力。
液压计算(原件选择)
液压元件的选择一、液压泵的确定与所需功率的计算 1.液压泵的确定(1)确定液压泵的最大工作压力。
液压泵所需工作压力的确定,主要根据液压缸在工作循环各阶段所需最大压力p 1,再加上油泵的出油口到缸进油口处总的压力损失ΣΔp ,即p B =p 1+ΣΔp (9-15)ΣΔp 包括油液流经流量阀和其他元件的局部压力损失、管路沿程损失等,在系统管路未设计之前,可根据同类系统经验估计,一般管路简单的节流阀调速系统 ΣΔp 为(2~5)×105Pa ,用调速阀及管路复杂的系统ΣΔp 为(5~15)×105Pa ,ΣΔp 也可只考虑流经各控制阀的压力损失,而将管路系统的沿程损失忽略不计,各阀的额定压力损失可从液压元件手册或产品样本中查找,也可参照表9-4选取。
B B max 的泄漏确定。
①多液压缸同时动作时,液压泵的流量要大于同时动作的几个液压缸(或马达)所需的最大流量,并应考虑系统的泄漏和液压泵磨损后容积效率的下降,即q B ≥K(Σq)max (m 3/s) (9-16)式中:K 为系统泄漏系数,一般取1.1~1.3,大流量取小值,小流量取大值;(Σq)max 为同时动作的液压缸(或马达)的最大总流量(m 3/s)。
②采用差动液压缸回路时,液压泵所需流量为:q B ≥K(A 1-A 2)v max (m 3/s) (9-17)式中:A 1,A 2为分别为液压缸无杆腔与有杆腔的有效面积(m 2);v max 为活塞的最大移动速度(m/s)。
③当系统使用蓄能器时,液压泵流量按系统在一个循环周期中的平均流量选取,即q B =∑=Z1i V i K/T i (9-18)式中:V i 为液压缸在工作周期中的总耗油量(m 3);T i 为机器的工作周期(s);Z 为液压缸的个数。
(3)选择液压泵的规格:根据上面所计算的最大压力p B 和流量q B ,查液压元件产品样本,选择与P B 和q B 相当的液压泵的规格型号。
液压系统计算公式
液压系统计算公式液压系统是一种利用液压传动能量、控制和执行机械运动的系统。
在液压系统中,计算液压元件的尺寸和性能参数是非常重要的,这样可以确保液压系统的正常工作和高效运行。
1.流量公式:液压流量是指液压系统中单位时间内流过管道或液压元件的液体体积。
液体流量通常用升/分钟(L/min)或立方米/分钟(m³/min)表示。
计算液压流量的公式如下:Q=A×v其中,Q表示流量,A表示液压元件的截面面积,v表示流速。
液压元件的截面面积可以根据元件的形状和尺寸进行计算,流速可以根据工作情况和流量要求进行选择。
2.压力公式:液压系统中的压力是指液体在管道或液压元件中的压力。
计算液压系统中的压力,需要考虑液体的密度、重力加速度和液体高度。
液压压力的公式如下:P=γ×h其中,P表示压力,γ表示液体的密度,h表示液体的高度。
液体的密度可以根据液体的种类和温度进行选择,液体的高度可以根据液压系统的工作条件和需求进行确定。
3.功率公式:液压系统中的功率是指液体对外界做功的能力。
液体的功率可以通过液体的流量和压力来计算。
液压系统的功率公式如下:P=Q×ΔP其中,P表示功率,Q表示流量,ΔP表示压力差。
流量可以通过计算液压元件的截面积和流速得到,压力差可以通过液压系统的设计和工作情况来确定。
4.马力公式:液压系统中的马力是指液体对外界产生的功率,常用于表示液压泵的功率大小。
液压系统的马力公式如下:Hp=Q×ΔP/1715其中,Hp表示马力,Q表示流量,ΔP表示压力差。
流量和压力差的计算方式与功率公式相同。
以上是液压系统计算中常用的一些公式,可以帮助工程师和技术人员合理设计和调整液压系统,确保液压系统的正常工作和高效运行。
当然,液压系统设计和计算还需要考虑其他因素,比如液体的黏度、温度、管道的摩擦损失等,因此在实际应用中还需综合考虑各种因素进行计算和调整。
计算液压缸的的尺寸和所需流量
计算液压缸的的尺寸和所需流量1液压缸的内径和活塞杆的内径工作压力的确定P=3MPa.2计算液压缸尺寸(1)液压缸的有效面积A1A1=F/P=1000KN/16MPa=62500 mm2D=√4 A1/π=282.16 mm取标准值D=280 mm(2)活塞杆直径取速比系数为ψ=1.46d=√ψ-1/ψ=280√1.46-1/1.46=157.17 mm取标准值d=160 mm3缸径、缸径取标准值后的有效面积无杆腔的有效面积:A1=πD2 /4=πx280 2/4=61544 mm2有杆腔的有效面积:A2=πd2 /4=πx160 2/4=41448 mm24 确定缸所需要的流量无干腔:Q1 = A1 v=61544x10-6 x4=246(L/min)有干腔:Q2= A2v=41448x10-6 x4=167(L/min)液压元件的计算和选择1液压泵和电动机的选择前面选择液压系统的压力为16MPa,因此根据机械手册计算泵的额定压力Pb=(1.25~1.6)P=(1.25~1.6)×25Mpa=20~25.6MPa因此泵的额定压力可取为Pb= 25MPa2系统流量的计算液压缸工作时所需流量为Q= Q1 = A1 v=246(L/min)Q系= KQ=1.2×246 =295.2L/min3泵的选择先取电动机的转速为1500r/min则要求泵的几何流量为q B =1500Q=246/1500= 164 ml/r又因为系统要求压力高且可变流量,故选用柱塞式恒功率变量泵查力士乐设计手册选用泵的型号为A4V180泵。
4电动机的选择泵的输入功率为P=PQ/612X0.9=160x295.2/612/0.9=85.75 KW查机械设计手册得电动机的型号为Y280M-4其输出功率为90kw 转速为1480r/min5油箱容积的计算锻压机械油箱的有效容量一般为泵每分钟流量的5~7倍。
所以泵的排量为Q B =nq B =1500r/min ×295.2ml/r ÷1000=442.8L查机械设计手册得油箱的计算公式为V=(5~7)X442.8L=2214~3099.6L系统取V=2500L因此油箱的长宽高分别取800mm 、620mm 、500mm6管路内径的选择吸油管:d=4.6VQ =4.6√295.2/2=55.8≈56mm 吸油管:d=4.6VQ =4.6√295.2/2.5 =49.9 ≈50mm 根据《机械设计手册》表20-8-2,取公称通径d=65mm,外径75mm 。
- 1、下载文档前请自行甄别文档内容的完整性,平台不提供额外的编辑、内容补充、找答案等附加服务。
- 2、"仅部分预览"的文档,不可在线预览部分如存在完整性等问题,可反馈申请退款(可完整预览的文档不适用该条件!)。
- 3、如文档侵犯您的权益,请联系客服反馈,我们会尽快为您处理(人工客服工作时间:9:00-18:30)。
第二节第四节液压元件的计算与选择
一、液压泵
首先依据初选的系统压力选择液压泵的结构类型,一般P<21MPa,选用齿轮泵和叶片泵;P>21MPa,则选择柱塞泵。
然后确定液压泵的最大工作压力和流量。
液压泵的最大工作压力必须等于或超过液压执行元件最大工作压力及进油路上总压力损失这两者之和,液压执行元件的最大工作压力可以从工况图或表中找到;进油路上总压力损失可以通过估算求得,也可以按经验资料估计,见表10-3。
液压泵的流量必须等于或超过几个同时工作的液压执行元件总流量的最大值以及回路中泄漏量这两者之和。
液压执行元件总流量的最大值可以从工况图或表中找到(当系统中备有蓄能器时,此值应为一个工作循环中液压执行元件的平均流量);而回路中泄漏量则可按总流量最大值的10%-30%估算。
在参照产品样本选取液压泵时,泵的额定压力应选得比上述最大工作压力高20%-60%,以便留有压力储备;额定流量则只需选得能满足上述最大流量需要即可。
液压泵在额定压力和额定流量下工作时,其驱动电机的功率一般可以直接从产品样本上查到。
电机功率也可以根据具体工况计算出来,有关的算式和数据见第三章相关部分或液压工程手册。
二、阀类元件
阀类元件的规格按液压系统的最大压力和通过该阀的实际流量从产品样本上选定。
各类液压阀都必须选得使其实际通过流量最多不超过其公称流量的120%,否则会引起发热、噪声和过大的压力损失,使阀的性能下降。
选用液压阀时还应考虑下列问题:阀的结构形式、特性、压力等级、连接方式、集成方式及操纵方式等。
对流量阀应考虑其最小稳定流量;对压力阀应考虑其调压范围;对换向阀应考虑其滑阀机能等。
1.流量阀的选择
选择节流阀和调速阀时还要考虑其最小稳定流量是否符合设计要求,一般中、低压流量阀的最小稳定流量为50ml/min~100ml/min;高压流量阀的最小稳定流量为min~20ml/min。
流量阀对流量进行控制,需要一定的压差,高精度流量阀进、出口约需1MPa的压差。
普通调速阀存在起始流量超调的问题,对要求高的系统可选用带手调补偿器初始开度的调速阀或带外控关闭功能的调速阀。
对于要求油温变化对外负载的运动速度影响小的系统,可选用温度补偿型调速阀。
2.溢流阀的选择
直动式溢流阀响应快,适合作制动阀及流量较小的安全阀,先导式溢流阀的启闭特性好,宜作调压阀,背压阀及流量较大的安全阀用。
先导式溢流阀有二级同心和三级同心之分,二级同心型的泄漏量小,常用于需保压的回路中。
先导式溢流阀的最低调定压力一般只能在~1Mpa范围内。
选择溢流阀时,应按液压泵的最大流量选取,并应注意其许用的最小稳定流量,一般来说,其最小稳定流量应是公称流量的15%以上。
3.单向阀及液控单向阀的选择
选择单向阀时,应注意其开启压力大小,开启压力小作单向阀,开启压力大作背压阀。
液控单向阀有内泄式和外泄式之分,外泄式的控制压力较低,工作可靠,但要多一根泄油油管。
液控单向阀还有带卸荷小阀芯和不带卸荷小阀芯之分,前者控制压力较低,常用于高压系统,有时还可作为液压机的卸压阀用。
4 换向阀的选择
按通流量选择结构型式,一般通流量在190L/min以上时,宜选用二通插装阀,70L/min 以下可选用电磁换向阀,否则需用电液换向阀。
按换向性能等选择电磁铁类型,由于直流电磁铁尤其是直流湿式电磁铁的寿命长,可靠性高,故应尽量选用直流湿式电磁换向阀。
按系统要求选择滑阀机能,详见第五章第四节有关内容。
对于可靠性要求特别高的系统来说,阀类元件的额定压力应高出其工作压力较多。
5 液压阀的配置形式
液压阀的配置形式有管式配置、板式配置和集成式配置,详见第五章第一节。
目前液压系统多采用集成式配置。
下面简要说明集成块的设计。
(1)(1)块体设计集成块的材料一般为铸铁或锻钢,低压固定设备可用铸铁,高压强振场合要用锻钢。
块体加工成正方体或长方体。
对于较简单的液压系统,其液压阀较少,可安装在同一个集成块上。
如果液压系统复杂,阀件较多,就要采取多个集成块叠积的形式。
相互叠积的集成块上下面一般为叠积接合面,钻有公共压力油孔P,公共回油孔T,泄油孔L和四个用于叠积的螺栓孔。
P孔:液压泵输出的压力油经调压后进入公共的压力油孔P,作为供给各单元回路压力油的公共油源。
T孔:各单元回路的回油均通到公共回油孔T,流回到油箱。
L孔:,各液压阀的泄漏油,统一通过公共泄漏油孔流回油箱。
集成块的其余四个表面,一般后面接通液压执行元件的油管,另三个面用以安装液压阀。
块体内部按系统图的要求,钻有沟通各阀的孔道。
(2)集成块结构尺寸的确定外形尺寸要满足阀件的安装,孔道布置及其它工艺要求。
为减少工艺孔,缩短孔道长度,阀的安装位置要仔细考虑,使相通油孔尽量在同一水平面或同一竖直面上。
对于复杂的液压系统,需要多个集成块叠积时,一定要保证三个公用油孔的坐标相同,使之叠积起来后形成三个主通道。
各油孔的内径要满足允许流速的要求,一般来说,与液压阀直接相通的孔径应等于所装液压阀的油孔通径。
油孔之间的壁厚不能太小,一方面防止使用过程中,由于油的压力而击穿,另一方面避免加工时,因油孔的偏斜而误通。
对于中、低压系统壁厚不得小于5mm,高压系统应更大些。
油管规格的确定和油箱容量的估算见本书的第六章。
二、元件的选择和计算
字体[大][中][小]夹带式提升机机尾拉紧装置的布置如图7-17所示。
1.拉紧力和拉紧行程的计算
取T最大=,已知主带的机尾滚筒拉力S2=,盖带机尾滚筒拉力Y2=,则:
S′2=S2/=
Y′2=Y2/=1454N
图7-17 机尾拉紧装置的布置
F拉1=Y2+Y′2=
F拉2=S2+S′2=
取输送带全长L=40m,则拉紧行程L拉紧为:
L拉紧=~L+
取,则:
L拉紧=×40+=
2.液压缸的选择
按L拉紧及F拉最大查液压产品目录,决定采用DG-J63型液压缸,其大端活塞面积为,小端活塞面积为,机械效率η=,压力为:
P拉1=F拉1×4/ηπ(D2-d2)=
P拉2=F拉2×4/ηπ(D2-d2)=
设活塞杆运动速度为4m/min,则流量为:
Q=υA=min
3.泵和电动机的初选
粗估压损为:△p=,则泵的工作压力为:
p额1=p拉1+△p=
p额2=p拉2+△p=
p泵最大=
泵流量的确定:
Q泵≥KQ=×=min
Q泵取为10L。
查《液压手册》,选择CB-C10C-FL型泵,其额定转速为1800r/min,额定压力为p= 。
该泵的驱动功率为,Q泵=min。
选取电动机机械效率η=,则电动机的功率为:
选用Y100LI-4型电动机,功率为。
4.元件的初选
各阀通过实际量,按系统最高压力初步选取,如表7-10所示。
表7-10 元件初选表
序号元件名称实际液量/L规格
1滤油器10XLI-25×200B
2齿轮泵GB-G1016
3截止阀10Q43NS-40
4单向阀10I10-B
5电接触压力表KF-L81E
6截止阀1043NS-40
7节流阀1~3L10-B
8压力继电器PF-B8H
9安全阀10YF-L10H
10截止阀10Q43NS-40
11油缸DG-J63C
已知最大推力F=20kN,最大拉紧行程L=2m,参考液压元件产品目录,最后确定选用型号为DG-J100C型双作用单活塞杆油缸,其油缸直径为100mm,活塞大端面积为,小端面积为,活塞大端长2000mm。
当压力为时,F拉=;当压力为时,F拉=。
由此确定其额定压力为即可。
系统在F=20kN、机械效率η=时,运行压力为:
设定活塞杆运动速度为4m/min,则其油量为:
Q G=vA=min
5.液压油的选择
经上述计算确定p最大=,由液压元件产品查得选用22号汽轮机油(又名透平油),其运动粘度v50=(20~23)×10-6m2/s,取v50=21×10-6m2/s,其密度为× 103kg/m3则其动力粘度为:
μ=ρv=×10-3×21=·s
6.泵的选择及计算
粗估压损△p=,其工作压力为:
p额1=p1+△p=
p额启=p启+△p=
所以油泵最大工作压力p max=。
油泵泄漏系数K=~取K=,则泵流量为:
Q泵≥KQ=×=min
根据液压元件产品目录选择YB-A26B型单级叶片油泵,其额定转速n=1800r/min,额定流量Q=min,驱动功率为,额定压力为。
7.电动机的选择
取电动机的机械效率为,则电动机的工作功率为:
依目录决定选用Y110M-4型电动机,其功率为4kW。
8.元件的选择
各阀依据通过实际流量及系统最高压力选择,如表7-11所示。
表7-11 元件汇总表
序号元件名称实际流量/L运用规格
1滤油器25CS66-11
2齿轮泵CB-C25C-FL
3截止阀25Q73SA
4单向阀25DIF-L10H
5压力表KF-L81E
6截止阀25Q73SA
7节流阀1~3LB10C
8压力继电器PF-L8C
9安全阀25YF-B10C
10截止阀25Q73-SA
11油缸DG-J100C。