铸轧机结构力能参数的计算
第五章-轧制压力及力矩的计算

② 冷轧过程中主要考虑变形程度的影响, 通常采用平均变形程 度来确定变形抗力的大小。可查加工硬化曲线或者用数学模型 进行计算。
0.40 0.61
0 -本道次轧前的预变形量
1 -本道次的轧后总变形量 H0 -冷轧前轧件厚度
0 ( H0 H ) / H0
H -本道次轧前轧件厚度
冷轧时: 加工硬化现象明显,变形程度增加,变形抗力增加 热轧时: 小变形(20~30%以下)时,随变形程度增机,变 形抗力增加迅速,中等变形(>30%)以后,增加速度变缓,当 变形程度很大时,则变形抗力又下降。
5 轧制压及力矩的计算
5.1 轧制压力的工程计算
5.1.3 金属变形抗力的确定方法
变形抗力: 轧制过程中金属抵抗变形的力
2.553
2.57
2.586
2.603
2.62
5 轧制压力及力矩的计算
5.1 轧制压力的工程计算
5.1.2 平均单位压力公式
(3).计算平均单位压力的R·B·西姆斯公式
西姆斯假设接触表面摩擦规律为全粘着(
tx
K )的条件确定外摩擦影响系数 2
Hale Waihona Puke n' ,得出如下的平均单位压力公式
p
n' K
(
2
1 arctan
将的表达式 p带入其中得:
fl ' h
2
fl h
2
2CR
e fl' h 1
f K' h
即:
fl' 2
h
2CR
e fl' h 1
f h
K'
fl h
2
轧制力计算案例

原料加厚到135mm 适应性分析根据爱克伦德公式计算各轧机热轧时平均单位压力,然后求出总轧制力,参照板带厂620mm 热带设备性能参数分析运行情况。
爱克伦德公式()()εη++=k m p 1m ——外摩擦对单位压力影响的系数 hH hh R f m +∆-∆=2.16.1η——粘性系数 ()t 01.04.11.0-=η 2mm sN •t ——轧制温度ε——平均变形速度 hH R h v+∆=2ε )4.1)(01.014(8.9Mn c w w t K ++-=2mm Nc w ——以质量分数表示的碳含量 Mn w ——以质量分数表示的锰含量)0005.005.1(t a f -= 对于钢性轧辊a =1,对于铸铁轧辊a =一、首先计算0R 机架:以435135⨯mm 原料为例0R 铸钢轧辊,辊径560mm~650mm mm R 325=半径大 0R 辊缝摆设在105mm~95mm mm S 30=小 0R 速度设定sm v 6.0= 轧件轧前尺寸mm B H H 420135⨯=⨯ (考虑RE0) 轧件轧后尺寸mm b h h 430105⨯=⨯ 轧制温度执行1100℃以上, 1100=t ℃5.0)11000005.005.1(1)0005.005.1(=⨯-=-=t a f179.0105135302.1-303255.06.12.16.1=+⨯⨯⨯=+∆-∆=h H h h R f msmm v 600= 5.53)3.012.04.1)(110001.014(8.9)4.1)(01.014(8.9=++⨯-=++-=Mn c w w t K(普碳)()3.0)110001.04.1(1.001.04.11.0=⨯-=-=t η2mm sN •519.1105135********22=+⨯=+∆=h H R hvε()()61.63)519.13.05.53)(179.01(1=⨯++=++=εηk m p计算总轧制力KN bl p p 266930325243042061.63=⨯⨯+⨯== 同上原理可以计算出 表一同理品种钢以65Mn 为例67.89)165.04.1)(110001.014(8.9)4.1)(01.014(8.9=++⨯-=++-=Mn c w w t K表二结论:0R 工艺参数最大轧制力为4000KN ,原料厚度改变后0R 只能满足普碳钢的生产,不能满足品种钢的生产。
BJ001-铸轧工艺参数计算

读书笔记
铸轧工艺参数计算
铸轧的主要工艺参数
铸轧区长度 铸轧速度 浇注温度 冷却强度 凝固瞬间铝熔体供给所需的静压力
在轧辊直径、铸轧板厚度一定的正常铸轧情况下,上述工艺参数之一有变化,其它工艺参数将随之变 化才可能保持铸轧工艺的稳定性。生产实践表明,在调整各工艺参数之间的关系时,应使凝固区与变形区 的高与长有一定的比例关系,以保证绝对压下量△h 恒定,才能确保铸轧过程的连续性和稳定性,使铸轧 带坯具有优良的组织。
1 铸轧区长度
双辊式铸轧机的铸轧区的建立与铸轧辊的冷却强度、铸轧速度、带坯厚度有直接关系。图 1 为双辊式 连续铸轧机铸轧区示意图,由图可知,铸轧区由铝熔体冷却到结晶温度的冷却区(Z1),铸轧区(Z2)和轧 制变形区(Z3)组成。根据铸轧工艺的不同,各区长度存在一定比例关系。铸轧区长度可按下式计算,其 计算结果与实际情况比较接近。
Z
∆ 2
√∆
式中: Z——铸轧区长度,cm; H——前箱熔体水平面与氧化膜之间的高度差,cm; ρ——熔体密度,kg/—铸轧速度,m/min; v2——平均凝固速度,cm/min; h——带坯厚度,cm; σ——表面张力系数,N·cm-1; Δh——绝对压下量,cm; R——铸轧辊半径,cm。
对于双辊倾斜式连续铸轧机,生产实践表明,铸轧角在 8°~9°范围内变化,铸轧区长度可用式 2 计 算。生产实践证明,双辊倾斜式φ650mm 铸轧机和φ980mm 铸轧机铸轧区最大长度分别为 50mm 和 70mm 左右。
Z Rsinθ
式中: Z——铸轧区长度,mm;
读书笔记
θ——铸轧角,°(度); R——轧辊半径,mm。 2 铸轧力计算公式 p K应宽外 p——铸轧坯对铸轧辊的平均单位压力,MPa; 应——应力状态系数,用来考虑外摩擦和张力对单位压力的影响; 外——外端影响系数,由于轧制外区对轧制区有影响而引入的系数; 宽——宽展系数,轧制时带坯宽展时而引入的对平均单位压力的影响系数; K——铝带坯在铸轧温度时的真实变形抗力,MPa;
轧制力能参数

3、轧制过程变形系数
如前所述,轧制时严格遵守体积不变定律与最小阻力定律。 轧制时,轧件发生塑性变形,尺寸在三个方向上发生变化,
即轧件高度由h0减小到h1;轧件宽度由b0增加到b1;其长度 由L0增加到L1;定义以下三个变形系数及相互之间关系:
1.压下系数: h1 1
um
V1 l
l
/
hm
2平均变形速度
um
Vr l
ln
h0 h1
hm表示轧件的平均厚度;以上分别表示实际轧制中冷轧
与热轧的工况;在冷轧时,轧件较薄而且接触弧长较长, 轧件与轧辊之间产生滑动。而热轧则与之相反,接触弧较 短,而且轧件与轧辊产生粘着。
20
变形速度的计算公式:
2Fv h
u
H(F0
R F)
F0/F——轧件的入口/出口截面积;v——轧辊圆周速度; H——入口厚度;
16
前滑区及后滑区
17
• 前滑的计算公式(德列斯登Draston公式)
前滑值定义:
S V1 Vr 100% Vr
计算:
S
h 4h1
1
2
2
同样公式也清 楚地反映了轧 制参数对前滑 的影响。
• 应用
在连轧中必须保持各架的金属流量即秒流量相等,即:
ViFi=C C为常数 而 Vi=Vri (1+Si) 即:FiVri (1+Si)=C i 为机座数,i =1,2,……n
如α<β成立,则α1<β必然成立。故一旦咬入,
就会继续咬入,形成稳态轧制过程。
实际上,为易于咬入,现场往往采取一些措施, 如:施加水平力强制咬入,在轧辊辊面上刻痕以 增加轧件与辊面的摩擦系数等。
轧钢机械(第二章力能参数)(精)
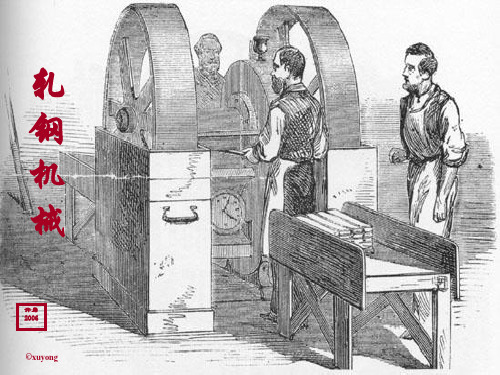
©xuyong
20
§2 接触弧上的单位压力及影响因素
二、轧制时接触弧上px的微分方程式 1、T.Karman px的微分方程式(1925年)
L L
©xuyong
大压下量
小压下量
30
§3 轧制时接触弧上的平均单位压力
, pm= n’n”n”nB
这里介绍几种常用的计算公式
一、采利柯夫公式
三大步: 解Karman方程,求px表达式; 沿接触弧分段积分,求总压力P; 总压力除以面积得pm。
pm= n’K
31
©xuyong
©xuyong
§1 轧制力计算的基本思路与理论
四、金属塑性变形条件——塑性方程式 1、屈服准则 • 屈雷斯卡(H.Trasca)屈服准则 • 蜜赛斯(R.von.Misse)屈服准则
欲使处于应力状态的物体中的某一点进入 塑性状 态,必须使得该点的单位弹性形状变化位能达到材料 所允许的极限值,并且该极限数值与应力状态无关, 而是一个常值。
24
©xuyong
§2 接触弧上的单位压力及影响因素
三、影响单位压力的因素 2、变形阻力的确定 • 金尼克曲线; • 库克曲线; • 北京钢院曲线; • 其他曲线或经验公式。
25
©xuyong
§2 接触弧上的单位压力及影响因素
三、影响单位压力的因素 3、影响应力状态的因素
接触弧上单位摩擦力分布的影响 干摩擦理论 粘着摩擦理论 结论: μ↑则 p↑
4200mm四辊中厚板精轧机力能参数计算详解

4200mm四辊中厚板精轧机力能参数计算摘要中厚板轧机是轧钢行业中的主力轧机,其装备水平及拥有量是一个国家钢铁工业发展水平的重要标志。
因此,中厚钢板是国民经济发展不可缺少的钢材品种,各国对中厚板生产都很重视。
本设计阐述了4200mm四辊中厚板精轧机力能参数机选过程。
主要内容包括:设计方案设定、生产工艺流程、确定轧机主要参数和工艺制度;设计内容包括:生产方案的确定、生产工艺流程、典型产品的工艺计算、本设计以提高生产率、降低生产成本、减轻劳动强度、提高产品质量及综合经济效益为设计原则。
关键词:中厚板,压下规程,力能参数,轧制力,工艺流程目录1、概述 (1)1.1 中厚板轧制发展史 (1)1.2 中厚板轧制技术发展趋势 (1)2、设计方案 (1)2.1工艺方案的选择 (1)2.2 主机型式选择 (1)2.3 相关设备的选择 (1)2.3.1加热炉 (1)2.3.2冷却装置 (2)2.3.3除磷 (2)2.3.4矫直机 (2)3.主要设备的技术参数 (3)4.工艺流程设计 (3)4.1生产工艺流程 (3)4.2轧制制度 (4)5.轧制工艺规程 (4)5.1咬入能力 (4)5.2 压下量校核 (4)6.确定轧制规程 (5)6.1 确定轧制速度 (5)6.2确定轧制延续时间: (5)6.3轧制温度确定 (6)6.4计算各道次变形程度: (7)6.4.1各道次变形速度 (7)6.4.2各道次变形抗力 (8)6.5计算各道次平均单位压力 (9)6.6计算各道次总压力 (10)6.7计算传动力矩 (10)7、车间技术经济指标 (12)7.1各类材料消耗指标 (12)7.2综合技术经济指标 (14)8、结语 (15)参考文献 (16)1、概述1.1 中厚板轧制发展史国内许多中厚板轧机的轧制过程都是采用人工制定轧制规程,然后通过实际轧制状态的变化进行轧制规程的手动调整,以适应轧件和轧辊的变化,这种轧钢方式可以充分发挥操作人员的人工智能,取得了较好的轧制效果。
材料成型工程第五讲轧制压力及力矩计算1
压力垂直分量
后滑区摩察分力
前滑区摩察分力
ψ ------变形区内任一角度; 一般通称的轧制压力或实测的轧制总压力,并非为轧制单位压 力之合力,而是轧制单位压力、单位摩擦力的垂直分量之和。但 式中第二项、第三项与第一项相比,其值甚小,工程上完全可以 忽略。即
• 可知,轧制压力为微分面积上之单位压力 p 与该 微分体积接触表面之水平投影面积乘积的总和。 • 如取平均值形式,则
• 根据力之平衡条件,所有作用在水平轴X 上力分量的代数和应等于零ΣX=0
忽略二阶无穷小量,化解有后滑区式(1)
•
同理,前滑区中金属的质点沿接触 表面向着轧制方向滑动,与上方程 式相同,但摩擦力的方向相反,故 可如上相同的方式,得出下式(2)
求解方程
• 对方程(1)(2)求解,须找出单位压力Px与 应力σx 之间的关系。 • 根据假设,设水平应力和垂直压应力为主应力 • 则可写成 σ1 =-σy
• 分析以上所得接触弧单位压力分布方程,可看 出: 公式中考虑了外摩擦 、 轧件厚度 、压下量 、 轧辊直径 轧件在进出口所受张力的影响 • 根据单位压力分布方程所得的单位压力计 算结果给出的单位压力沿接触弧分布曲线, 用以表示这些因素对单位压力的影响
1)摩擦的影响
• 右图为在压下量一定 的条件下,摩擦系数 不同所得的单位压力 分布曲线。
2)公式推导
• 推导思路
轧制理论中,单位压力的数学 — 力学理论的出发点 是在一定的假设条件下,在变形区内任意取一微分体 分析作用微分体上的各种作用力,在力平衡条件的基 础上,将各力通过微分平衡方程式联系起来 运用屈服条件或塑性方程式 接触弧方程 摩擦规律和边界条件来建立单位压力微分方程并求解。 微分方程式建立过程如下
轧钢机械(2)
二、轧制时接触弧上单位压力微分方程式
• 1.卡尔曼单位压力微分方程式
假设条件:
1)平面变形: b 0, 0, 1.15
2)平断面假设:轧前轧件的垂直平面在轧制过程中 保持不变。 0, x 为主应力,1 - 3 K 且 x 沿高度方向均匀分布。 3)主应力 表示的塑性方程式成立。
(化学成分)及变形条件(变形程度、变
形温度、变形速度),而与应力状态无关。
1 - 2 2 3 3 1
2 2
2
2
2
塑性方程式的物理意义是:在三向应力状 态下,当主应力差的平方和等于金属材料 塑性变形阻力平方的二倍时,物体就开始 产生塑性变形。
v、vr 2 各架轧机轧辊圆周速度; 1
S1、S2 各架轧机轧制时的前滑值。
6.变形速度
变形速度是指单位时间内
的相对变形量,以
u
表示,
uh
为线压缩速度;可表示
vh 为 u h
,h 变形物体的
瞬时高度;
uy
轧制时,在接触弧区间内,变形速度
是变化的。变形区中离轧辊连心线为
x
3、影响应力状态的因素
• ②轧件厚度的影响 • 随着轧件厚度的增加,单位压力相应降低。摩擦 力对水平应力 x 的影响减弱了,因而单位压 力降低。
****************************
• ④ 张力的影响
• 由于存在张力,使变形 区内金属在轧制方向产 生附加拉应力,此拉应 力引起三向压应力状态 的水平方向主应力 x 的减小,从而降低了单 位压力。由于中性面偏 向出口,故后张力影响 大于前张力。
表
二辊轧机力能参数计算-分享
二、轧制压力计算根据原料尺寸、产品要求及轧制条件,轧制压力计算采用斯通公式。
详细计算按如下步骤进行。
1、轧制力计算:首先要设定如下参数作为设计计算原始数据:1.1轧制产品计算选用SPCC ,SPCC 常温状态屈服强度MPa S 200=σ; 1.2成品最大带宽,B=1000mm ;1.3轧制速度,m in /12m in/20m m v MAX 常轧制速度(鉴于人工喂料),正=; 1.4轧辊直径g D ;αcos 1-∆≥hD g轧制时的单道次压下量-∆h ;;数咬入角,取决于摩擦系b μα-;取用煤油作为润滑剂,则轧制摩擦系数,轧制采06.0=-b b μμ ︒=<433.3b actg μα代入数据计算得 35.1=∆h 则mm hD g 17.793cos 1=-∆≥α05.1=∆h 则mm hD g 585cos 1=-∆≥α 2.1=∆h 则mm hD g 705cos 1=-∆≥α取mm D g 860~810= 初定轧辊直径:mm D g 860=2、根据来料厚度尺寸数据,选择最典型的一组进行轧制压力计算,初步道次分配见下表:3、轧制压力计算3.1、第1道次轧制压力计算 3.1.1、咬入条件校核︒=⨯∆=∂2878.3180πR h ,即满足咬入条件 3.1.2、变形区长度lmm h R l 7945.21=∆⨯=3.1.3、平均压下率ε106.04.0εεε⨯+⨯=00=ε 83.201=ε%则,%5.126.04.010=⨯+⨯=εεε经第1道次轧制后材料的变形阻力:MPa S 7.3799.334.2256.01=⨯+=εσ3.1.4、求解轧辊弹性压扁后的接触弧长度l ' 依次求解Y 、Z ,最后得出接触弧长度l 'a-求解诺莫图中Ymh k C Y μσσ)2(210+-=N mm RC /909003=; MPa k S S 335)2(15.110=+=σσ力轧制时的前张力、后张、-10σσ,人工辅助咬入为无张力轧制,前后张力均为零;mm hH h m 375.52=+=代入以上各项数据,得Y=0.0415b-求解诺莫图总Z2⎪⎪⎭⎫ ⎝⎛=mhl Z μ,代入各项数据,得Z=0.105诺莫图由以上a 、b 两项根据诺莫图求交点,得X=0.34 则 mm h X l m84.22=⨯='μ3.1.5、平均单位轧制压力()()m k ee k p m XX m**1σσ-=--= 依次得出,187.134.0171.2134.0=-=-=X e m X m k p ⋅==395.57MPa3.1.6、轧制总压力Pt p l B P 6.90357.39584.2210001=⨯⨯=⨯'⨯=3.2、轧制总压P 的确定依次求解第2、3道次的轧制压力 按照初步道次分配表计算出结果如下:t P 13802= ;t P 16003=轧制压力呈逐步增大,轧制时难以保证轧件发生均匀变形,即压下规程设计不合理。
冶金机械设计理论-2轧制力能参数
轧机转速和速比
转速和速比的变化会影响 轧机的动态特性,从而影 响轧制力能参数。
轧机刚度和稳定性
良好的轧机刚度和稳定性 可以减小振动和误差,从 而减小轧制力能参数的波 动。
05
轧制力能参数的优化和控制
轧制力能参数的优化
优化目标
提高轧制效率,降低能耗,提升产品 质量。
优化方法
优化过程
根据实际生产需求和工艺要求,建立 轧制过程的数学模型,通过仿真实验 和数据分析,找到最优的力能参数组 合,并进行实际生产验证。
针对不同工艺条件和设备类型,可以开展更加细 致的实验研究,以验证和完善轧制力能参数的理 论体系。
未来研究可以进一步探索轧制力能参数与冶金机 械设计理论之间的内在联系,揭示其作用机制和 规律,为实际应用提供更加精准的理论指导。
未来研究可以加强跨学科合作,整合相关领域的 研究成果,推动轧制力能参数研究的系统性和完 整性,为冶金机械设计提供更加全面、可靠的理 论支持。
01
03
通过对轧制力能参数的研究,可以为冶金机械设计提 供更加科学、可靠的理论依据,推动冶金机械行业的
可持续发展。
04
轧制力能参数的研究涉及到多个学科领域,如力学、 热学、材料科学等,需要综合考虑各种因素,建立完 善的理论体系和实验验证体系。
研究展望
随着科技的不断进步和产业升级的需要,轧制力 能参数的研究将更加深入,涉及的领域也将更加 广泛。
冶金机械设计理论-2轧制 力能参数
• 引言 • 轧制力能参数的基本概念 • 轧制力能参数的计算方法 • 轧制力能参数的影响因素 • 轧制力能参数的优化和控制 • 实际应用和案例分析 • 结论与展望
01
引言
主题简介
01
- 1、下载文档前请自行甄别文档内容的完整性,平台不提供额外的编辑、内容补充、找答案等附加服务。
- 2、"仅部分预览"的文档,不可在线预览部分如存在完整性等问题,可反馈申请退款(可完整预览的文档不适用该条件!)。
- 3、如文档侵犯您的权益,请联系客服反馈,我们会尽快为您处理(人工客服工作时间:9:00-18:30)。
铸轧机结构力能参数的计算
3.1铸轧和连铸及连轧以及连铸连轧的区别
3.1.1 连续铸钢简称为连铸
钢的生产过程主要分为炼钢和铸钢两大环节。
炼钢的任务是将有关的原料通过炼钢炉炼成质量合格的钢液,铸钢的任务是将成分合格的钢液铸成适合于轧钢和锻压加工所需的一定形状的钢块(连铸坯成钢锭)。
铸钢作业是衔接炼钢和轧钢之间的一项特殊作业,其特殊表现为它是把钢液变为固体的凝固过程。
当钢液凝固后,在以后的轧钢过程中就不能对质量有本质上的改进了。
因此,铸钢作业对产品质量和成本有重大影响。
铸钢生产可以分为钢锭模浇注(简称模铸)和连续铸钢(简称连铸)两大类。
模铸是将钢液注入铸铁制作的钢锭模内,冷却凝固成钢锭的工艺过程;连铸是将钢液不断地注入水冷结晶器内,连续获得铸坯的工艺过程。
连铸机主要是由钢包运载装置、中间包、中间包运载装置、结晶器、结晶器振动装置、二次冷却装置、拉坯矫直机、引锭装置、切割装置和铸坯运载装置部分组成。
连铸生产过程:
下面以连铸生产使用最多的弧形连铸机为例说明连铸的一般过程:
从炼钢炉出来的钢液注入到钢包内,经二次精练处理后被运送到连铸机上方,钢液通过钢包底部的水口再注入到中间包内。
中间包水口的位置被预先调好的对准下面的结晶器。
打开中间包塞棒(成滑动水口)后,钢液流入下口由引锭杆头封堵的水冷结晶器内。
在结晶器内,钢液沿其周边逐渐冷凝成坯壳。
当结晶器下端出口处有一定厚度时,同时启动拉坯机和结晶器振动装置,使带有液芯的铸坯进入由若干夹辊组成的弧形导向段。
铸坯在此一边下行,一边经受二次冷却区中许多按一定规律布置的喷嘴喷出雾化水的强制冷却,继续凝固。
在引锭杆出拉坯矫直机后,将其切成定尺铸坯,最后又出坯装置将定尺铸坯运往指定地点。
随着钢液的不断注入,铸坯不断向下伸长,并被切割成运走,形成连续浇注的全
过程。
3.1.2 连铸连轧技术
以薄板坯连铸连轧为代表的连铸连轧技术,实现了连铸于连轧的连续化,从而使传统钢铁生产工艺流程进一步缩短,设备布置本身更加紧凑,经济效益更加显著,有力地推动了短流程技术的发展和应用。
3.2 铸轧机的性能指标的确定
3.2.1 铸轧辊辊径
双辊式带钢铸轧中,铸轧辊是铸轧机最关键的组成部分,对铸轧辊辊径的选择,主要是满足一定的液面高度要求,因为液面高度将会影响到熔池的接触弧长。
不同的接触弧长,其铸带的厚度和铸带铸轧速度是不同的,铸轧辊辊径越大,接触弧长越长,液面高度越高,铸轧越稳定,越能保证铸带的质量,从这一点来讲,希望铸轧机设备加重,投资增加。
另外,铸轧棍辊径的大小,将直接影响铸轧速度,辊径大,铸速就快,铸轧机的质量就高。
3.2.2 凝固系数
铸速能否满足产量的要求,主要取决于凝固速率,而凝固速率涉及到铸轧辊与熔融金属之间的传热系数及熔融金属的导热系数,一般可用下式表示:
δ=k t=k v
l/
式中:δ—凝固厚度,mm;
k—凝固系数,mm/min;
t—凝固时间,s;
l—接触弧长,mm;
v—铸带速度,m/,min;
根据铸轧辊与熔融金属之间传热系数及熔融金属的导热系数,对钢液来说k≈20~30mm/min。
带钢铸轧中,凝固带坯的最大相对变形率为:
ε=(h
0-h
1
)/ h
1
=3%~5%
式中:h
—铸轧凝固层的厚度;
h 1—铸带厚度。
通过计算表明,辊径增大后,换热条件得到改善,铸带厚度和铸带的速度相应的提高。
3.2.3 电动机转速的选择
电动机额定转速是根据生产机械的要求而选择的,在确定电动机额定转速时,必须考虑机械减速机构的传动比值,两者相互配合,经过技术,经济全面比较才能确定。
通常,电动机的转速不低于500r/min ,因为当功率一定时,电动机的转速愈低,则其尺寸愈大,价格愈贵,而且效率也愈低,如果选用高速电动机,势必加大机械减速机构的传动比,致使机械传动部分复杂起来。
对于一些不需调速的高,中速机械。
如水泵,鼓风机,空气压缩机等,可选用相应转速的电动机不经机械减速机构直接传动。
需要调速的机械,电动机的最高转速应与生产机械转速相适应。
若采用改变励磁的直流变速电动机时,为充分利用电动机容量,应选好调磁调速的基速。
有如某些轧钢机械,提升机等,工作速度较低,经常处于频繁地正反转运行状态,为了缩短正反转过渡时间,提高生产效率,降低消耗,并减小噪音,节省投资,选择适当的低速电动机,采用无减速机的直接传动更为合理。
要求快速频繁启,制动的机械,通常是电动机的转动惯量与额定转速平方的乘积(即N n J 2D 值)为最小时,能获得启动和制动最快的效果。
在空载(或负载很小可以忽略)情况下启,制动时,为达到快速的目的,按下式考虑最合理:
N n J 2D =m n J 2m
即所谓最价传动比为:
D
m j J J i 式中 D J —D J 电动机转子的转动惯量,kg.2m
2n —电动机额定转速,r/min
m J —生产机械在机械在机械轴上转动惯量,kg.2m
m n —生产机械轴转速,r/min
交流电动机和直流电动机是市场上最常用的电机,对于交流电动机而言结构简单,耐用,可靠,容易维修,价格低。
但是启动和调速性能差,轻载时功率因数低,被一般无调速要求的机械广泛应。
在可变频率电源供电下可平滑调速,但是体积大,价格昂贵。
对于直流电动机而言调速性能好,范围宽,采用电子控制下,能充分适应各种机械负载特性的需要,但是它的造价昂贵,维修复杂,而且需要直流电源,因此直流电动机只在交流电动机不能满足调速要求时才采用它。
本套设备是一般旋转运动的机械。
所以采用交流电动机就可以满足要求,根据实际要求和条件,选择YCT 系列电磁调速三相异步电动机。
可以按照公式: 9550
.D D n T p P ——电动机功率,kw
D T ——电动机转矩,N.m
D n ——电动机转速,r/min
其中: D T =70 N.m
D n =750r/min
可以出计算电机的功率 p=9.8kw
由此可以选择电动机型号:
YCT 系列电磁调速三相异步电动机(JB/T7123-1993)系列中的YCT255—4A
3.2.4 轧制力
在条形材铸轧过程中,铸轧力的大小直接影响到条形材的内在质量和表面质量。
铸轧力过大条形材易产生裂纹;铸轧力过小,铸带内部疏松。
根据国内外有关报道,假设铸轧过程中在理想状态下,即凝固壳仅在辊面形成,侧封面上不形成凝固壳,铸轧力一般由下式计算:
P=σm l 3ζb
式中: σm ——材料的平均变形阻抗力, σm =3~50Mpa; l 3——固相区的长度;
ζ——铸轧压缩力函数,ζ~1.2;
b——铸带宽度。
由铸轧力P的计算公式我们可以看到,在其他参数确定不变后,铸轧力P
是铸轧辊固定相区长度l
3的函数,即P=f(l
3
)。
也就是说,固相区长短对带坯质
量的影响可通过铸轧力反映出来。
于是,我们可以通过调整铸带速度,使铸轧力
保持恒定,固相区的长度l
3
也就是被保持在标准值上。
根据固相区铸轧带坯的相对变形率ε=3%~5%,若辊径,带厚已确定,我们可以求出适当的固相区长
度l
3
,进行求出铸轧力P的大小。
经计算,当辊径D=1200mm,带厚为3~4mm,带宽为600mm时,铸轧力P=300~400kN。
3.2.5 铸速的计算
在辊缝,冷却条件等一定的条件下,浇铸速度应为一定值。
当浇铸速度过低时,在辊缝出带坯早已凝固,即两辊上坯壳凝固结合点(凝固终点)过高,使铸轧辊对带坯的轧制力增大,这样很容易造成铸坯表面质量和内部裂纹。
当浇铸速度过高时,带坯离开铸辊后还没有完成凝固,中间有液芯存在,在钢水静压作用下,易造成膨胀变形。
所以,只有选择合适的浇铸速,才能浇铸出合格质量的带坯。
坯壳冷凝公式为:
δ=k t
式中:δ——凝固坯壳的厚度,mm;
k——凝固系数,取12~16mm/min;
t——坯壳凝固时间,s,t=l/v。
带坯离开铸轧辊时,辊1侧坯壳厚度为:
δ
1=k v
l/
1
=k v
Ra/
辊2侧坯壳厚度为:δ
2=k v
l/
2
=k v/
R
由假设条件知,在带坯离开铸轧辊时刚好完全凝固,此时:
δ=δ
1+δ
2
=h
式中: h——两轧辊辊缝间隙,mm;
R——铸轧辊半径,mm;
从以上两式得v=k2R(a+ )2/h2
我所设计的这台轧机的铸速是2m/min,年产量是2万吨。