第五章材料的强化理论
第五章__材料的疲劳性能(1)分析

疲劳微裂纹形成的三种形式
表面滑移带开裂解释 1)在循环载荷作用下,即使循环应力未超过材料屈服强 度,也会在试样表面形成循环滑移带 2)循环滑移带集中于某些局部区域(高应力或簿弱区) 3)循环滑移带很难去除,即使去除,再次循环加载时, 还会在原处再现 (驻留滑移带)
特征: 1)驻留滑移带一般只在表面形成,深度较浅,随循环次数 的增加,会不断地加宽 2)驻留滑移带在表面加宽过程中,会出现挤出脊和侵入 沟,在这些地方引起应力集中,引发微裂纹
四:疲劳裂纹扩展速率
试验表明:测量疲劳裂纹长度和循环周数的关系如图
疲劳裂纹扩展曲线
Δσ2﹥Δσ1
从图可知: 1)曲线的斜率da/dN(疲劳裂纹扩展速率)在整个过程中 是不断增长的 2)当da/dN无限增大,裂纹将失稳扩展,试样断裂 3)应力增加,裂纹扩展加快,a-N曲线向左上方移动,ac相 应减小 结论:裂纹扩展速率da/dN 和应力水平及裂纹长度有关 根据断裂力学: 可定义应力强度因子幅为
特征 1)疲劳源区比较光滑(受反复挤压,摩擦次数多) 2)表面硬度因加工硬化有所提高 3)可以是一个,也可能有多个疲劳源(和应力状态及 过载程度有关)
疲劳裂纹扩展区
是疲劳裂纹亚临界扩展的区域
特征 1)断口较光滑,分布有贝纹线(或海滩花样),有时还有 裂纹扩展台阶 2)贝纹线是疲劳区的最典型特征,贝纹线是以疲劳源为圆 心的平行弧线,凹侧指向疲劳源,凸侧指向裂纹扩展方向 3)近疲劳源区贝纹线较密,远离疲劳源区贝纹线较疏
5.2 疲劳破坏机理
一:金属材料疲劳破坏机理
疲劳裂纹的萌生
1)在材料簿弱区或高应力区,通过不均匀滑移, 微裂纹形成及长大而完成 2)定义裂纹长度为0.05—0.10mm时为裂纹疲劳 核,对应的循环周期为裂纹萌生期
第五章材料力学考试复习重点知识与练习题

从图在该段中的变线段(T即为非粮馆举性段, 压液线可看出即整个拉伸过程可分为以下四个阶段。
* /)称线弹性段,其斜率即为弹性模量E,对应的最高应力值 虎克定律(r=Ec 成立。
而ab 段, 在该段内所产生的应变仍是弹性的, 但它与应力已不成正比。
b点相对立白 勺应力第五早材料力学 主讲:钱民刚 第一节 概论材料力学是研究各种类型构件(主要是杆)的强度、刚度和稳定性的学科,它提供 了有关的基本理论、计算方法和试验技术,使我们能合理地确定构件的材料、尺寸 和形状,以达到安全与经济的设计要求。
♦一、材料力学的基本思路 (一)理论公式的建立 理论公式的建立思路如下:(一)低碳钢材料拉伸和压缩时的力学性质低碳钢(通常将含碳量在0.3%以下 的钢称为低碳钢,也叫软钢)材料拉伸和压缩时的 (7- e 曲线如图5-1所示。
陶度箓n------- 搬面设计为确保构件不致因强度/、丸而破坏, 应使其最——该啊瓯丽于材料的极限应力0- u,物出射和 (力与姻(美系)* 变形外力 T ]表小,即临界前载应力力布1£配IX没有屈服阶段,也酸 _ 曲线的一条割线的斜率,作为其弹性模量。
它 1故衡量铸铁拉伸强度的唯一指标就是它被拉断时/,在较小的拉应力作用下即被拉断,且其延伸率很小,故铸铁TE与拉伸相比,可看出这类材料的抗压能力要比抗拉 事蝌性变形也较为蛾显。
破坏断口为斜断面,这表明试件是因m max对于塑性材料制成的杆,通常取屈服极限①良或名义屈服极限(T该段内应力基本上不变,但应变却在迅速增长,而且在该段内所产生的应变 成分,除弹性应变外,还包含了明显的塑性变形,该段的应力最低点 (7S 称为屈服 极限。
这时,试件上原光滑表面将会出现与轴线大致成 45。
的滑移线,这是由于试 件材料在45。
的斜截面上存在着最大剪应力而引起的。
对于塑性材料来说,由于屈 服时所产生的显著的塑性变形将会严重地影响其正常工作,故(7S 是衡量塑性材料强度的一个重要指标。
《材料科学基础》复习大纲(08级)

《材料科学基础》总结及重点第一章 材料的结构与键合1、金属键、离子键、共价键、分子键(范德华力)、氢键的特点,并解释材料的一些性能特点。
2、原子间的结合键对材料性能的影响。
用金属键的特征解释金属材料的性能—①良好的延展性;②良好的导电、导热性;③具有金属光泽。
3、比较金属材料、陶瓷材料、高分子材料、复合材料在结合键上的差别。
本章重要知识点: 1. 金属键、离子键、共价键、分子键、氢键的特点。
第二章 固体结构1、晶体与非晶体(在原子排列上的区别)2、空间点阵、晶格、晶胞及选取晶胞的的原则、七大晶系及各自的特点,布拉菲点阵(14种) 、晶格常数、晶胞原子数。
3、晶面指数、晶面族、晶向指数、晶向族、晶带和晶带定理、晶面间距、配位数、致密度、八面体间隙、四面体间隙。
各向同性与各向异性、实际晶体的伪各向异性、同素异构转变(重结晶、多晶型性转变) 。
(1)指数相同的晶向.和晶面必然垂直。
如[111]⊥(111)(2)当一晶向[uvw]位于或平行某一晶面(hkl )时,则必然满足晶带定理:h ·w+k ·v+l ·w =04、能绘出三维的体心、面心立方和密排六方晶胞,根据原子半径计算出金属的体心和面心立方晶胞的晶胞常数。
三种典型晶体结构的特征(包括:晶胞形状、晶格常数、晶胞原子数、原子半径、配位数、致密度、各类间隙尺寸与个数,最密排面(滑移面)和最密排方向的指数与个数,滑移系数目等);即:bcc 、fcc 、hcp 的晶格特征及变形能力(结合塑性变形一章的内容你必须知道常用金属材料的滑移面与滑移系的指数)。
给画出晶胞指出滑移面和滑移方向。
能标注和会求上述三种晶胞的晶向和晶面指数。
晶向和晶面指数的一些规律。
求晶面间距d (hkl )、晶面夹角。
5、晶面间距:d (hkl ) 的求法:(1)立方晶系:222)(l k h ad hkl ++= (2)正交晶系:222)(1⎪⎭⎫ ⎝⎛+⎪⎭⎫ ⎝⎛+⎪⎭⎫ ⎝⎛=c l b k a h d hkl (3)六方晶系:2222)()(341⎪⎭⎫ ⎝⎛+++=c l a k hk h d hkl (4)四方晶系:2222)()/(/)(1c l a k h d hkl ++=以上公式仅适用于简单晶胞,复杂晶胞要考虑其晶面层数的增加。
材料强化的主要方法
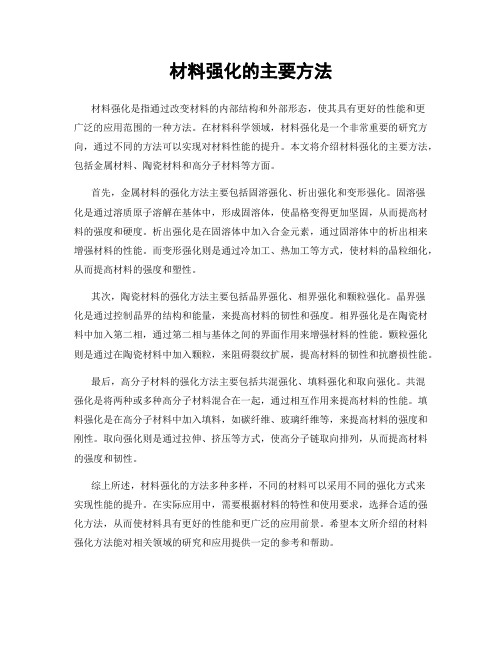
材料强化的主要方法材料强化是指通过改变材料的内部结构和外部形态,使其具有更好的性能和更广泛的应用范围的一种方法。
在材料科学领域,材料强化是一个非常重要的研究方向,通过不同的方法可以实现对材料性能的提升。
本文将介绍材料强化的主要方法,包括金属材料、陶瓷材料和高分子材料等方面。
首先,金属材料的强化方法主要包括固溶强化、析出强化和变形强化。
固溶强化是通过溶质原子溶解在基体中,形成固溶体,使晶格变得更加坚固,从而提高材料的强度和硬度。
析出强化是在固溶体中加入合金元素,通过固溶体中的析出相来增强材料的性能。
而变形强化则是通过冷加工、热加工等方式,使材料的晶粒细化,从而提高材料的强度和塑性。
其次,陶瓷材料的强化方法主要包括晶界强化、相界强化和颗粒强化。
晶界强化是通过控制晶界的结构和能量,来提高材料的韧性和强度。
相界强化是在陶瓷材料中加入第二相,通过第二相与基体之间的界面作用来增强材料的性能。
颗粒强化则是通过在陶瓷材料中加入颗粒,来阻碍裂纹扩展,提高材料的韧性和抗磨损性能。
最后,高分子材料的强化方法主要包括共混强化、填料强化和取向强化。
共混强化是将两种或多种高分子材料混合在一起,通过相互作用来提高材料的性能。
填料强化是在高分子材料中加入填料,如碳纤维、玻璃纤维等,来提高材料的强度和刚性。
取向强化则是通过拉伸、挤压等方式,使高分子链取向排列,从而提高材料的强度和韧性。
综上所述,材料强化的方法多种多样,不同的材料可以采用不同的强化方式来实现性能的提升。
在实际应用中,需要根据材料的特性和使用要求,选择合适的强化方法,从而使材料具有更好的性能和更广泛的应用前景。
希望本文所介绍的材料强化方法能对相关领域的研究和应用提供一定的参考和帮助。
材料科学与工程基础第五章 材料的变形

孪生 在金属的塑性变形中,另一种较常见的形变方式为孪生, 它常作为滑移不易进行时的补充。一些具有密排六方结构的 金属,如镉、锌、镁、铍等,塑性变形常常部分的以孪生的 方式进行;而铋、锑金属的塑性变形几乎完全以孪生的方式 进行。对于有体心立方及面心立方结构的金属,当变形温度 很低,形变速度极快,或由于其它原因使滑移过程难以进行 时,也会通过孪生的方式进行塑性变形。孪生就是在切应力 孪生就是在切应力 孪生 作用下晶体的一部分相对于另一部分沿一定的晶面与晶向产 生的一种均匀切变过程。在孪生变形中, 生的一种均匀切变过程。在孪生变形中,已发生均匀切变的 那部分晶体称为孪晶 孪晶; 那部分晶体称为孪晶;均匀切变区与未切变区的分界面称为 孪晶界;发生均匀切变的那个晶面称为孪生面; 孪晶界;发生均匀切变的那个晶面称为孪生面;孪生面切动 的方向则为孪生方向 孪生方向。 的方向则为孪生方向。
晶体在滑移时的转动 晶体的塑性变形是由于滑移面沿着滑移方向运动产生的,在滑 移的同时,晶体也会发生转变,从而使晶体的空间取向发生了变化。 如果晶体受拉伸产生滑移时,如果两端不受限制,在滑移过程中, 为使滑移面和滑移方向保持不变,晶体轴线就会发生偏移。但是, 拉伸时,在夹头的作用下,晶体轴线不能自由偏斜,这就迫使滑移 面发生转动,使位向发生了改变。
回复 再结晶 晶粒长大
0 0
T1 t1
T2 t2
T3 t3
温度 时间
冷变形金属组织随加热温度及时间的变化示意图
一、回复 回复是指经冷塑性变形的金属在加热时,在光学显微组织发 生改变前,即在再结晶晶核形成前,所产生的某些亚结构和性能 变化的过程。在回复过程中,由于温度的升高,在内应力的作用 下将发生局部塑性变形,金属的屈服强度下降,残余应力将得到 部分消除,所以,冷变形金属进行回复过程的退火称为去应力退 火,它具有即降低金属残余应力又保持加工硬化性能的作用。 回复的组织与结构变化 三个阶段: 低温回复过程 金属中的点缺陷密度明显降低。 中温回复过程 位错相消;形成亚晶界,位错胞也由此转化为规整 的亚晶粒,这一过程称为亚晶规整化过程。 高温回复阶段 位错垂直于滑移面的方向排列成小角度亚晶界, 小角度晶界的两侧为无畸变的亚晶,多边化。
材料力学——精选推荐

材料力学第一章拉压一、构件设计应满足的要求:1、足够的强度:即抵抗破坏的能力;2、足够的刚度:即抵抗变形的能力;3、足够的稳定性:即保持平衡的能力;二、失稳:构件在一定外力的作用下,不能保持原有的平衡形式,称为失稳;细长杆件在压缩中容易产生失稳现象。
三、材料力学的基本假设:1、连续性假设:构件的整个体积内毫无空隙的充满了物质;2、均匀性假设:认为材料是均匀的,其力学性能与构件中的位置无关;(材料在外力作用下表现出来的性能,称为力学性能或机械性能)3、各项同性假设:沿各个方向均具有相同的力学性能;(相反,存在各向异性材料,常见的有碳纤维、玻璃纤维、环氧树脂、陶瓷等四、杆件变形的基本形式:拉伸或压缩、弯曲和扭转。
五、内力:外力作用下,构件内部相连两部分之间的相互作用力。
六、同一杆件在受力方式变化的情况下,即使只受轴向力作用,不同部分的轴向力大小也可能不同,如在杆端和杆中点均受力,切合力为0的情况。
七、设杆件的横截面积为A,轴力为N,且为均匀性材料,则横截面上各点处的正应力均为:Pa、Mpa、Gpa)。
八、圣维南原理:力作用于杆端的方式不同,只会使于杆端距离不大于杆横向尺寸的范围受其影响。
九、拉压杆上的最大剪应力发生在于杆轴成45°的斜截面上,其值为横截面正应力的一半。
十、单位长度的变形,称为正应变。
十一、材料的应力——应变曲线:工程中常用的材料的应力应变曲线分成以下几个阶段:1、线性阶段:在拉伸的初始阶段,应力——应变为一直线;此阶段的应力最高点,为材料的比例极限;2、屈服阶段:超过比例极限之后,应力和应变之间不再保持正比例关系。
此阶段内,应力几乎不变,但变形却极具增长,材料失去抵抗继续变形的能力,此种现象称为屈服。
相应的应力称为材料的屈服应力或屈服极限。
3、强化阶段:经过屈服阶段之后,材料又增强了抵抗变形的能力,此种现象称为强化。
强化节点最高点对应的应力称为材料的强度极限。
如果材料表面光滑,当材料屈服时,试样表面将出现于轴线成45°的线纹,作用有最大剪应力。
第五章塑性理论
硬化材料:
加卸载准则
理想塑性材料:
5.3 流动法则
流动规则用以确定塑性应变增量的方向或塑性应变增量张量的各个分量间的比 例关系。塑性理论规定塑性应变增量的方向是由应力空间的塑性势面g决定。在应力 空间中,各应力状态点的塑性应变增量方向必须与通过该点的塑性势面相垂直。所 以流动规则也叫做正交定律。这一规则实质上是假设在应力空间中一点的塑性应变 增量的方向是惟一的,即只与该点的应力状态有关,与施加的 应力增量的方向无关,亦即
5.2 屈服准则
屈服面是应力空间内弹性状态与弹塑性状态之间的分界面。
f (ij , k) 0
k为状态参数,与硬化/软化参数有关
5.2 屈服准则
弹性 f (ij , k) 0 塑性 f (ij , k)=0 ? f (ij , k)>0
f f T f T k 0
k
5.2 屈服准则
➢压硬性 ➢等压屈服特性 ➢剪胀性 ➢应变软化特性 ➢与应力路径相关性
5.1 基本原理
塑性理论的基本概念:
1、屈服准则(Yield criterion ) 屈服面是应力空间内弹性状态与弹塑性状态之间的分界面。
2、硬化(软化)规律(Harding/Softening rule) 硬化规律是确定加载过程中屈服面位置和大小变化的规律。
3、流动准则(Flow rule) 流动准则用来确定塑性加载过程中塑性应变增量的方向。
不硬化
5.4 硬化规律
等向强化 是指屈服面以材料中所
作塑性功的大小为基础在尺寸上 扩张。
随动强化 假定屈服面的大小保持不变而仅 在屈服的方向上移动,当某个方向的屈服 应力升高时,其相反方向的屈服应力应该 降低。
在随动强化中,由于拉伸方向屈服应力的 增加导致压缩方向屈服应力的降低,所以在 对应的两个屈服应力之间总存 的差值,初 始各向同性的材料在屈服后将不再是各向同f (σ, Ro ) 0
1第五章 材料加工力学基础--简_430108089
2015年春季
2015/5/17
材料加工原理
1
题外话
• 2011年诺贝尔化学奖获奖项目是什么? • 什么是准晶?晶体?非晶体?Amorphous A h state t t
– 晶体:三维周期性有序重复的原子排列,出现1、2、3、4、6次 旋转对称性,不可能出现5次及6次以上的旋转对称性。 – 非晶体:近程有序、无长程序对称性。分玻璃和其他非晶态 – 准晶:具有长程准周期性平移序和非晶体学旋转对称的固态有序 相
2015/5/17
材料加工原理
20
平板对接产生的焊接变形
2015/5/17
材料加工原理
21
金属塑性成形的物理基础
• • • • • • • 金属塑性成形的特点 塑性成形工艺的分类 塑性加工时变形的分类 塑性加工时的附加应力和残余应力 金属的塑性和变形抗力 变形体的模型 塑性变形机制、加工硬化、回复、再结晶、摩擦 和润滑
2015/5/17 材料加工原理
27
变形体的模型 (应力-应变曲线的简化形式)
• • • • • 理想弹塑性模型 弹塑性线性强化模型 幂强化模型 理想刚塑性模型 刚塑性线性强化模型
2015/5/17
材料加工原理
28
塑性变形机制、加工硬化
• 塑性变形机制:单晶体、多晶体 – 单晶体塑性变形的主要机制是滑移和孪生。 单晶体塑性变形的主要机制是滑移和孪生 – 多晶体的塑性变形包括晶内变形和晶间变形两 种方式。除了滑移和孪生外,还有晶界滑动和 除 孪生 有 迁移,以及点缺陷的定向扩散(扩散蠕变)。 • 加工硬化 – 塑性变形造成组织上的变化,组织变化产生性 能上的变化:屈服极限、强度极限、硬度等均 提高,延伸率、截面收缩率、冲击韧性均降低 ;导电性、导热性、抗腐蚀性能均降低,铁磁 金属的磁性也会发生变化。
第五章 行为学习理论
第五章行为学习理论一、巴甫洛夫的经典性条件作用理论Ivan Pavlov (1870—1932) 俄国生理学家、心理学家、高级神经活动学说的创始人。
1904年因消化腺生理学研究的卓越贡献而获诺贝尔奖金。
他一生最突出的贡献是关于高级神经活动的研究。
(一)狗的条件反射作用实验实验结果(1)条件作用之前:给出铃声(条件刺激)并无唾液分泌给出肉(无条件刺激)产生唾液分泌(2)条件作用期间:铃声+肉(条件刺激+无条件刺激),产生唾液分泌(3)条件作用之后:给出铃声(条件刺激),产生唾液分泌(二)经典性条件作用的基本内容一个原是中性的刺激与一个原来就能引起某种反应的刺激相结合,而使动物学会对那个中性刺激做出反应。
●条件反射的四个基本事项:①无条件刺激(UCS):指本来就能引起的某种固定反应的刺激。
②无条件反应(UCR) :指由无条件刺激原本就可以引起的固定反应。
③条件刺激(CS) :原来的中性刺激。
④条件反应(CR) :条件反射形成后由条件刺激引起的反应。
(三)学习规律1. 消退◆条件作用建立之后,如果多次只给条件刺激而不用无条件刺激加以强化,结果是条件作用的反应强度逐渐减弱,最后将完全不出现。
●巴甫洛夫认为,消退并不是条件刺激和相应的反应之间的暂时联系已经消失或中断,而是暂时联系受到抑制。
●条件作用愈巩固,消退速度就愈慢;条件作用愈不巩固,就愈容易消退。
2. 泛化:在条件作用开始建立时,除条件刺激本身外,那些与该刺激相似的刺激也或多或少具有条件刺激的效应。
这种现象称为条件作用的泛化。
3. 分化:只对经常受到强化的刺激产生条件作用,而对其他近似刺激则产生抑制效应。
这种现象称为条件作用的分化。
4.高级条件作用:中性刺激一旦成为条件刺激,可以作为无条件刺激。
另一个中性刺激与其反复结合,可形成新的条件作用,这一过程被称为高级条件作用。
测验失败(中性刺激)批评(条件刺激)——焦虑测验失败——焦虑巴甫洛夫的信号系统理论●巴甫洛夫认为,条件反射是一种信号活动,引起条件反射的刺激是信号刺激。
组织行为学第五章
个人要求发展的内在愿 望
相当于马斯洛的尊重需 要和自我实现的需要
一个人基本物质生 存条件的需要
相当于马斯洛的生理需 要和安全需要
维持人与人之间 关系的需要
相当于马斯洛的安全 需要和社交需要
二、内容型激励理论
2.奥尔德弗的ERG理论
观点
1 生存需要是先天具有的。而相互关系需要和成长发展需要则是通过后
三、过程型激励理论
3.自我决定理论
行为
非自我决定
动机
去动机
外在动机
自我决定 内在动机
调节类型 无调节
外部调节 内摄调节 认同调节 整合调节
内在调节
因果感知轨迹 非个人的 相关调节过程 无意向
无评价
外部的 依从 外部奖惩
较外部的 自我控制 自我卷入
较内部的 个性化 意识评价
内部的 自我整合
内部的 兴趣 内在满足感
教授洛克和他的同事经历了近20年的时间,根据对8个国家、88个企业的4000多位工作者进行 调查研究后总结出来的。洛克在他的试验中发现大多数的激励因素都是通过目标来影响 工作动机的,因此,在管理过程中重视并设置合理的目标是激励员工提高工作积极性的 一种重要方法。
内容
目标设置理论认为,目标是人们行为的最终目的,是人们预先规定的、合乎自己需要 的“诱因”,是激励人们的有形的、可以测量的成功标准。达到目标是一种强有力的 激励,是完成工作的最直接的动机,也是提高激励水平的重要过程。成长、成就和责 任感的需要都要通过目标的达成来满足。
• 波特尔和劳勒的综 合激励模式
• 迪尔的综合激励模式
6.激励的应用实践
• 激励的应用原则
• 激励的方法
一、认识“激励”
1.激励的概念 观点
- 1、下载文档前请自行甄别文档内容的完整性,平台不提供额外的编辑、内容补充、找答案等附加服务。
- 2、"仅部分预览"的文档,不可在线预览部分如存在完整性等问题,可反馈申请退款(可完整预览的文档不适用该条件!)。
- 3、如文档侵犯您的权益,请联系客服反馈,我们会尽快为您处理(人工客服工作时间:9:00-18:30)。
再结晶与回复的不同之处在于机械性能能完全 恢复到冷变形前的状态,加工硬化得以消除。生产 中利用这一点来消除加工硬化,使塑性加工能够顺 利进行下去,这种工艺称为再结晶退火。
(3)晶粒长大
冷变形金属在再结晶刚 完成时,一般得到细小的等 轴晶粒组织。如果继续提高 加热温度或延长保温时间, 将引起晶粒进一步长大,它 能减少晶界的总面积,从而 降低总的界面能,使组织变 得更稳定。晶粒长大的驱动 力来自界面能的降低。
(3) 塑变不均匀性
由多晶体中各个晶粒之间变形的不同时性可知, 每个晶粒的变形量各不相同,而且由于晶界的强度高 于晶内,使得每一个晶粒内部的变形也是不均匀的。
课堂思考讨论题: 1 单晶材料和多晶材料哪个强度高,为什么?
2 晶粒细化能使金属强度提高吗?
1 晶界对滑移有阻碍,各晶粒位向不同。
5.1.2塑性变形对金属组织与性能的影响 1.塑性变形对金属组织结构的影响 (1) 形成纤维组织
(2)再结晶 加热温度升至 1/2 T熔,变形组织的基体 上产生新的无畸变的晶 核,并迅速长大形成等 轴晶粒,逐渐取代全部 变形组织。金属的加工 硬化状态消除,性能基 本上恢复到冷变形之前 的状态。这一过程叫再 结晶。再结晶驱动力来 自储存能,再结晶完成 后,冷变形金属中的储 存能全部释放。
再结晶温度
加工硬化方法举例
3. 塑性变形对金属物理、化学性能的影响 经过冷塑性变形后,金属的物理性能和化学性 能也将发生明显的变化。通常使金属的导电性、 电阻温度系数和导热性下降。塑性变形还使导磁 率、磁饱和度下降,但矫顽力增加。塑性变形提 高金属的内能,使化学活性提高,耐腐蚀性下降。
5.1.3 变形金属在加热时组织与性能的变化 1. 回复和再结晶 冷变形后的金属内能升高,存在储存能,处于不 稳定状态,具有自发恢复到变形前状态的趋势。一旦 受热(加热到0.5T熔温度附近),冷变形金属的组织 和性能就会发生一系列的变化,可分为回复、再结晶 和晶粒长大三个阶段。
(2) 塑变协调性
处于软取向的晶粒不能自由的变形,必须要求相 邻晶粒中取向不利的滑移系也参与变形,否则就不能 保持晶粒之间的连续性而导致材料的断裂。多晶体的 塑性变形是通过各晶粒的多系滑移来保证相互协调性。 根据理论推算,每个晶粒至少需要有五个独立滑移系。 因此,滑移系较多的面心立方和体心立方金属表现出 良好的塑性,而密排六方金属的滑移系少,晶粒之间 的变形协调性很差,故塑性变形能力低。
当一条位错线移到晶体表面时,便在晶体表面留下一个原 子间距的滑移变形。如果有大量位错按此方式不断滑过晶体, 就会在晶体表面形成滑移带。可见,滑移的临界分切应力实际 上是推动位错移动时所需要的力,其大小取决于位错移动时所 遇到的阻力。对单晶体而言,取决于点阵阻力(与原子键合、 晶格类型有关,称为派-纳力),理论计算表明:
2. 热加工特点
在热加工过程中,金属同时进行着两个过程:形变强化 和再结晶软化。塑性变形使金属产生形变强化,而同时发生 的再结晶(称为动态再结晶)又将形变强化现象予以消除。因 此,热加工时一般不产生明显加工硬化现象。
3. 热加工对金属组织与性能的影响 (1) 改善铸态组织缺陷 使铸态组织中的气孔、疏松及微裂纹焊合, 提高金属致密度,还可以使铸态的粗大树枝晶通 过变形和再结晶的过程而变成较细的晶粒,某些 高合金钢中的莱氏体和大块初生碳化物可被打碎 并使其分布均匀等。这些组织缺陷的消除会使材 料的性能得到明显改善。
金属的再结晶过程是通过形核和长大方式完成 的。但它不是相变过程,这与结晶不同。再结晶过 程也不是一个恒温过程,而是自某一温度开始,随 着温度的升高和保温时间的延长而逐渐形核、长大 的连续过程。因而再结晶温度是指冷变形金属开始 进行再结晶的最低温度。通常定义为变形量很大 (≥70%)的金属在1h的保温过程中,能够完成再结晶 的最低温度。大量实验表明,再结晶温度T再与熔点 T熔(以绝对温度表示)之间存在如下近似关系: T再 = (0.35~0.4)T熔 。
Zn晶体中的滑移
(3) 滑移的临界分切应力
当作用在滑移系上的切应力达到某一临界值时, 这一滑移系才能发生滑移,该临界值称为滑移的临界 分切应力,记为τc 。 临界分切应力的大小取决于金属算
当晶体上受到拉力 F作用时,作用在滑移 系上的分切应力为:
τc = σs cosλcosυ
讨论:单晶体的屈服强度是定值吗?为什么?
(4) 滑移的位错机制 整体滑移模型--晶体的一部分相对于另一部 分同时作整体的刚性移动,按此模型计算出的 最小滑移切应力是 : τ= G/2π
比试验值高100~1000倍。
位错滑移模型
通过位错在切应 力作用下沿着滑移面 逐步滑动,这样遇到 的阻力就很小,按此 模型计算的结果与试 验结果在数量级上完 全吻合。位错在很小 的切应力作用下就能 滑动的现象称为位错 的易动性。
第五章 工程材料的塑性变形和强 化理论
强度是材料在外力作用下抵抗塑性变形的能 力,强化的实质就是提高金属抵抗塑性变形的能 力,因此强度与塑性变形的难易程度密切相关。
工程中最常见的强化方法有形变强化、固溶强 化、第二相强化和细晶强化。它们都是围绕提高材 料塑性变形抗力出发来对材料进行强化的,要掌握 强化理论,首先必须先对金属塑性变形规律有充分 的了解。
(3) 亚结构细化 冷变形会增加晶粒中的位错密度。随着变形量 的增加,位错交织缠结,在晶粒内形成胞状亚结构, 叫形变胞。胞内位错密度较低,胞壁是由大量缠结 位错组成。变形量越大,则形变胞数量越多,尺寸 越小。
(4) 点阵畸变严重
金属在塑性变形中产生大量点阵缺陷(空位、 间隙原子、位错等),使点阵中的一部分原子偏离 其平衡位置,而造成的晶格畸变。在变形金属吸收 的能量中绝大部分转变为点阵畸变能,位错密度显 著升高,由105-6升至1011-12。
(5) 产生内应力(残余应力) 第一类内应力(宏观内应力),金属工件各部分间的 变形不均匀而引起的,作用于整个工件。 第二类内应力(微观内应力),各晶粒之间的塑性变 形不均匀而引起的内应力,其作用范围一般不超过 几个晶粒。 第三类内应力(点阵畸变),作用范围很小,在一个 晶粒内部,一般为几十至几百纳米。
5.1 塑性变形和形变强化(加工硬化) 金属材料经塑性变形后,其强度和硬度升高, 塑性和韧性下降,这种现象称为形变强化。
5.1.1金属的塑性变形
1.单晶体塑性变形 (1) 变形基本方式 滑移--在切应力作用下,一部分晶体相对于另 一部分沿着某一晶面和晶向发生相对滑动。滑移 后滑移面两侧晶体的结构类型和晶体取向均末有 改变,它是金属塑性变形的最基本方式。
τc = [2G/(1-υ)]e-2πa/[(1-υ)b]
(5) 孪生 当金属晶体滑移变形难以进行时,其塑性变形还 可能以生成孪晶的方式进行,称为孪生。例如滑移系 较少的密排六方晶格金属易以孪生方式进行变形。
孪生与滑移有什么不同?
2. 多晶体塑性变形特点 多晶体与单晶体有什么不同? 存在晶界,各晶粒位向不同。 (1) 塑变不同时性 在外加应力作用 下,处在软取向的晶 粒的滑移系首先开动, 周围取向不利的晶粒 中的滑移系上的分切 应力还未达到临界值, 这些晶粒仍处在弹性 变形状态。
即:τ= σ cosλcosυ cosλcosυ称为取向因子。
外力方向改变,加在滑移系上的取向因子也会 发生改变,因此外力在不同方向上作用,滑移系上产 生的分切应力是不同的。 取向因子最大的方向称为软取向,取向因子最 小的方向为硬取向。
当分切应力达到临界分切应力时,晶体开始产 生滑移,意味着晶体开始屈服:
(1) 回复 加热温度较低,原子活动能力有限,仅有点缺陷 密度显著下降,而位错密度变化不大,位错只是由缠 结状态改变为规则排列的位错墙(构成小角亚晶界), 位错组态、分布的这一变化过程称为多边化。显微组 织没有变化,晶粒仍是冷变形后的纤维状。金属的机 械性能,如硬度、强度变化不大,塑性略有提高,第 一、二类内应力基本消除, 某些物理、化学性能发生 明显变化,如电导率显著增大,应力腐蚀抗力提高。
合理
不合理
5.2固溶强化
5.2.1 固溶强化现象
定义:溶质原子溶入金属基体而形成固溶体, 使金属的强度、硬度升高,塑性、韧性有所下降, 这一现象称为固溶强化。例如单相的黄铜、单相 锡青铜和铝青铜都是以固溶强化为主来提高合金 强度和硬度的。
在生产中对冷加工的零件,为了保持加工硬 化状态,降低内应力,以减轻变形和翘曲,通 常采用去应力退火即回复退火。例如用冷拉钢 丝卷制弹簧时,在卷成之后要在260℃左右进行 退火,以降低内应力并使之定型,而硬度、强 度基本保持不变。此外,降低铸件和焊接件中 的内应力,防止变形、开裂也是通过回复退火 来实现的。
沿着变形方向晶粒被拉长。当变形量很大时, 晶粒难以分辨,而呈现出一片如纤维丝状的条纹, 称之为纤维组织。
30%
50%
形变量对金属组织的影响
(2) 形成形变织构 随着变形的进行,原处于随机分布的各晶粒的 取向会大致趋于一致,这种由于变形而使晶粒具有择 优取向的组织叫形变织构。
产生择优取向的原因是塑性变形时晶粒发生 了转动。在拉伸时晶粒的滑移面转向平行于外力 的方向,在压缩时转向垂直于外力方向。当变形 量很大时,各晶粒的位向就会趋于一致。
形变量对金属强度的影响
原因 塑性变形过程中,位错在滑移时会产生交互 作用,如相互交割、反应、缠结;同时位错在滑 移时还会产生增殖,位错密度不断升高,导致形 变胞的形成和不断细化,这些都对位错的滑移产 生巨大的阻碍作用,使得位错滑移阻力随着塑性 变形的进行不断升高,在宏观上就表现为金属抵 抗塑性变形的能力随塑性变形的进行不断升高。
残余应力又叫储存能,第一类内应力占0.1%~, 第二类内应力占10~%,第三类内应力占80~90%。
2.塑性变形对金属力学性能的影响 (1) 呈现明显的各向异性 主要是由于形成了纤维组织和形变织构。
制耳现象
(2) 产生形变强化 金属材料经塑性变形后,其强度和硬度升高, 塑性和韧性下降,这种现象称为形变强化(加工硬 化),是金属强化的一种有效手段。