轨检车检测技术
轨道检测技术
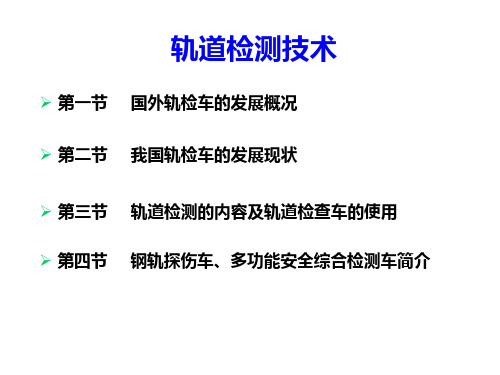
• •
第一节
意大利轨检车发展
国外轨检车的发展概况
意大利“阿基米德号”综合检测列 车
第一节
意大利轨检车发展
•
国外轨检车的发展概况
―阿基米德号”综合检测列车又称 Roger2000,是 MER MEC公司和TECNOGAMMA公司为意 大利铁路设计制造的,检测速度可达220km/h。检测项目包括轨道几何参数、钢轨断面、 钢轨波浪磨耗、接触网及受流状态、通信和信号、车体和轴箱加速度、轮轨作用力等。 车上有57台计算机,每秒钟可处理30G数据,有24个激光器、43个光学摄像传感器、47 个加速度计以及大量的强度速度、定位以及温度传感器,以及用于航空电子领域的惯 性平台。
第二节
• •
我国轨检车的发展现况
为克服 GJ-4型轨检车轨距吊梁存在的上述问题,本世纪初我国铁路从美国 ImageMap公司引进了装备 Laserail轨道测量系统的GJ-5型轨检车。 GJ-5型轨检车采用惯性基准法、非接触式测量方式,由基于摄像原理的轨距轨 向测量系统取代光电伺服机构,所有传感器均安装在悬挂于转向架构架上的检测 梁内,取消了轨距吊梁。由于经过一系列减震,检测梁工作时所受的振动和冲击 大大降低,安全性显著提高,同时也消除了检测设备在特定检测速度下产生共振 的可能性。由于不存在伺服机构的往复运动,检测设备的故Βιβλιοθήκη 率也大大降低。轨道检测技术
轨道测量技术
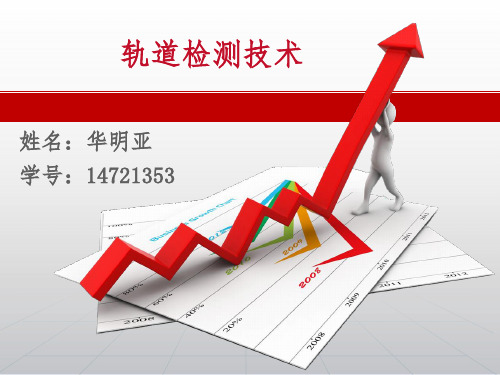
二、检测原理
• 1、系统构成
[2]
公铁2用综合检测车
车辆平台
供电与控制
业务功能模块
通 用 车 辆
轨 道 悬 架
发 电 机
配 电 系 统
定 位 系 统
轨 道 几 何 参 数
钢 轨 断 面
限 界
评价与报表软件模块
2.轨道检测车的工作原理
• 以GJ-5型轨道检测系统为例简述一下检测原理
[3]
GJ-5 型非接触测量系统检测梁
•
三、轨道检测的内容
轨道检测车的基本原理——以GJ-4型轨检车为例(4)
•
方向的检测原理——方向指钢轨内侧面轨距点沿轨道纵向水平位置的变化。 利用左右股轨距测量装置所测的左右股轨距变化或位移,轨距点相对纵向轨 迹—轨向。监测范围±100mm,误差±1.5mm ,模拟弦长18.6米。 扭曲(三角坑)的检测原理:扭曲反映了钢轨顶面的平面性。设轨顶面abcd 四个点不在一个平面上,c点到abd三个点组成的平面的垂直距离h为扭曲。扭 曲会使车轮抬高面悬空,使车辆产生3点支撑1点悬空,极易造成脱轨掉道。 扭曲值h为:h=(a-b)-(c-d),h=△h1-△h2。△h1为轨道横断面I-I的水平值, △h2为轨道断面Ⅱ-Ⅱ的水平值,△h1-△h2为基长L(断面I-I与断面II-II之 间距)时两轨道断面的水平差。水平已经测出,所以只要按规定基长取两断 面水平差即可计算出扭曲值。
现代轨检车: 组成:由检测和数据处理系统、 发电供电系统、空气调 节系统、仪表工作室、瞭望台以及走行转向架等几部分组 成。 检测项目:轨道的高低、水平、三角坑、方向、轨距,以 及里程和行车速度等。有的还能测量曲线超高、曲率,以 及高低方向等轨道不平顺的变化率、曲线通过的均衡速度 等。 优点:提供直观反映轨道状态的波形图,并能提供经车载 计算机处理打印成的轨道状态报告表,以及记录在磁带上 的轨道状态资料等。有的还可在轨道状态严重不良和需紧 急补修的地方,直接在轨道上喷上颜色标记。将磁带记录 送地面计算机进一步处理,便可编制出各种轨道状态管理 图和轨道整修作业计划表
轨道检测技术(之一)

轨道检测技术(之一)轨道检测技术第一章概述【主要内容】我国铁路轨道的特点,线路检测的方法,线路检测对线路保洁修理的促进作用,线路检测的发展历程和现状。
【重点掌控】线路检测的方法。
第一节线路检测对维修工作的意义铁路线路设备就是铁路运输业的基础设备,它常年外露在大自然中,抵挡着风雨冻融和列车荷载的促进作用,轨道几何尺寸不断变化,路基及道床不断产生变形,钢轨、连结零件及轨枕不断磨损,而并使线路设备技术状态不断地发生变化,因此,工务部门掌控线路设备的变化规律,及时检测线路状态,强化线路检测管理沦为保证线路质量、确保运输安全的关键的基础性工作。
一、线路设备的检测方式(一)静态检查静态检查所指在没车轮荷载促进作用时,用人工或轻型测量小车对线路展开的检查。
主要包含轨距、水平、前后多寡、方向、觑吊板、钢轨接点、防爬设备、连结零件、轨枕及道口设备等检查。
线路静态检查是各工务段、车间、工区对线路进行检查的的主要方式之一,工务段段长、副段长、指导主任、检测监控车间主任、线路车间主任和线路工长应定期检测线路、道岔和其他线路设备,并重点检测薄弱处所。
(二)动态检测线路动态检测是在列车车轮荷载作用下通过添乘仪、车载式线路检查仪、轨道检查车等设备对线路进行的检测。
线路动态检测就是对线路展开检查的主要方式之一,也就是我国线路检测技术发展的主要方向。
二、线路检测对养护维修工作的指导作用安全就是铁路永恒的主题。
铁路线路设备就是铁路运输业的基础设备,经常维持线路设备完备和质量平衡,确保列车以规定速度安全、稳定和不间断地运转,并尽量缩短设备的使用寿命就是铁路工务部门的重要职责。
因此,合理保洁线路,保证线路质量就是确保工务部门安全生产的前提,也就是确保铁路运输安全的基础。
它对快速增长企业经济效益、确保人民生命财产安全、提升国民生产总值都存有关键意义。
而线路的检测同意着线路的设备技术状态的变化规律及程度,线路检测技术水平轻易同意着线路的保洁和修理工作的展开。
轨检车检测原理及注意事项
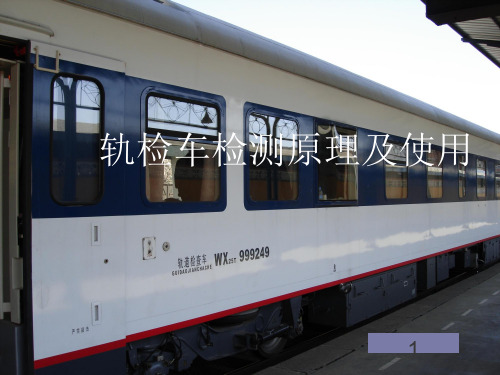
返回目录
轨向正负:顺轨检车正向,轨向向左为正,向右为负; 水平正负:顺轨检车正向,左轨高为正,反之为负; 曲率正负:顺轨检车正向,右拐曲线曲率为正,左拐曲线曲率为负; 车体水平加速度:平行车体地板,垂直于轨道方向,顺轨检车正向,向左为正; 车体垂向加速度:垂直于车体地板,向上为正。
为适应铁路提速和重载不断发展的需要,《铁路线路修理规则》(铁运【2006】146号文)于2006年10月1日正式执行。文中对轨道动态检测标准按V≦120km/h、120km/h<V≦160km/h、V>160km/h划分了四级管理值。缺乏速度≧200km/h以上等级干线管理标准,为适应我国第六次既有线提速改造的需要,以及填补我国《铁路线路修理规则》没有针对既有线200~250km/h区段的养护维修办法和各项检测标准。
返回目录
四.轨道病害成因分析
1.轨距病害的危害及成因分析
轨距病害幅值过大过小,在其他因素作用下,可能会引起列车脱轨或爬轨。影响轨距偏差值主要有以下几个方面: ⑴轨道结构不良:如钢轨肥边、硬弯、曲线不均匀侧磨、枕木失效、道钉浮离、轨撑失效、扣件爬离、轨距挡板磨耗、提速道岔基本轨刨切部分不密贴等。 ⑵几何尺寸不良:如轨距超限、轨距递减不顺、方向不良等。 ⑶框架刚度减弱:扣件扣压力不足、轨道外侧扣件离缝弹性挤开(木枕线路尤其如此)等。
非接触测量设备
惯性测量包安装在激光器/摄像机梁的中部,惯性测量包测量车辆转向架的横向和垂向加速度以及滚动和摇头速率等。
VME计算机系统
返回目录
GJ-5型轨检车检测项目:轨距、左右轨向、左右高 低、水平(超高)、三角坑、曲率(弧度或半 径)、车体横向加速度、车体垂向加速度、轨距变 化率、曲率变化率、车体横向加速度变化率、钢轨 断面等。
高速铁路轨道检测技术的使用指南

高速铁路轨道检测技术的使用指南随着交通运输的快速发展,高速铁路成为了人们出行的首选方式。
作为高速铁路的基础设施,对轨道的运行状况进行及时、准确的检测显得尤为重要。
本文将详细介绍高速铁路轨道检测技术的使用指南,帮助读者更好地了解和应用这些技术。
一、高速铁路轨道检测的意义和目标1. 意义:高速铁路的安全性和舒适性直接依赖于轨道的良好运行状态,及时发现和处理轨道缺陷可以保障列车的正常运行,并减少事故的发生。
2. 目标:高速铁路轨道检测的主要目标是识别轨道上的问题及其所对应的轨道缺陷类型,及时发现和预防问题的发生,从而保障高速铁路的安全运营。
二、高速铁路轨道检测技术的分类和原理1. 分类:高速铁路轨道检测技术可分为物理检测技术和无损检测技术两大类。
- 物理检测技术:包括轴重检测、轨道几何检测、接触网检测等,主要通过对轨道运行状态的直接测量,提供轨道的物理参数数据。
- 无损检测技术:包括超声波检测、磁探伤、红外热像检测等,通过对轨道内部或表面的信号变化进行检测,以获取轨道缺陷等信息。
2. 原理:各种高速铁路轨道检测技术均基于特定的物理原理实现对轨道状态的监测。
- 轴重检测:通过在轨道上设置传感器,实时检测列车通过时的轴重变化,为轨道衰退等问题提供参考依据。
- 轨道几何检测:利用激光测距、摄像技术等,进行轨面高程、水平和曲线半径等参数的测量,判断轨道是否存在几何问题。
- 接触网检测:通过红外线、摄像等技术,检测接触网的高度、弧垂、弧垂变化等,确保接触网的正常运行。
- 超声波检测:利用超声波的声学特性,对轨道内部的缺陷进行检测,例如螺栓松动、锚固不良等。
- 磁探伤:利用磁场的影响,检测轨道表面的裂纹、焊接问题等。
- 红外热像检测:通过红外热像仪,检测轨道表面的温度异常,发现隐患如膨胀缝过大、沉降等。
三、高速铁路轨道检测技术的应用流程1. 准备工作:检测前需清理轨道表面杂物,确保检测信号的准确性;检查检测设备和传感器的工作状态,并进行校准。
【精品】轨道检测技术之二
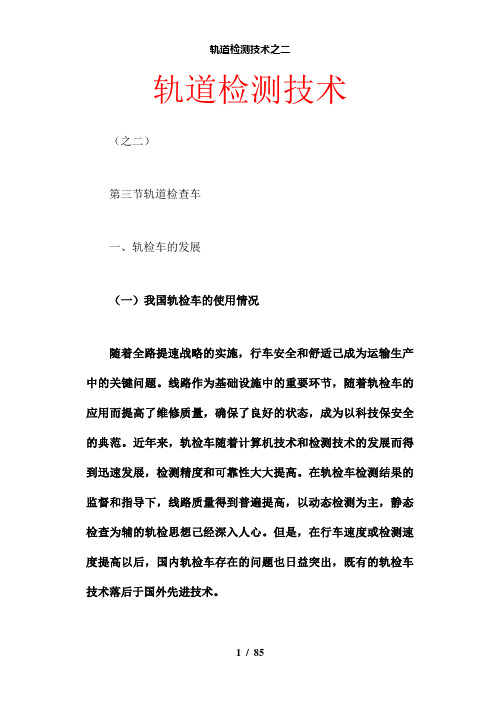
轨道检测技术(之二)第三节轨道检查车一、轨检车的发展(一)我国轨检车的使用情况随着全路提速战略的实施,行车安全和舒适己成为运输生产中的关键问题。
线路作为基础设施中的重要环节,随着轨检车的应用而提高了维修质量,确保了良好的状态,成为以科技保安全的典范。
近年来,轨检车随着计算机技术和检测技术的发展而得到迅速发展,检测精度和可靠性大大提高。
在轨检车检测结果的监督和指导下,线路质量得到普遍提高,以动态检测为主,静态检查为辅的轨检思想己经深入人心。
但是,在行车速度或检测速度提高以后,国内轨检车存在的问题也日益突出,既有的轨检车技术落后于国外先进技术。
轨检车一直是检测轨道病害、指导线路养护维修、保障行车安全的重要手段。
我国铁路从20世纪50年代起就采用1型轨检车每季度检测一次正线线路,该轨检车的特点是采用弦测法,机械传动,可以将轨距、水平、三角坑、摇晃(用单摆测量)项目的幅值绘在图纸上,人工判读超限并计算扣分。
60年代后期研制的2型轨检车仍采用弦测法,但改为电传动,检测项目比1型车增加了长波高低和短波高低,超限判读和扣分计算方式与1型车相同。
80年代初期研制成功的GJ-3型轨检车是我国轨检车技术的一次重大飞跃,其特点是将先进的传感器技术、计算机技术和惯性基准原理应用到轨检车上,可以检测高低、水平、三角坑、车体垂直和水平振动加速度,轨距、轨向则无法检测,传感器信号经过相关处理,直接以电压大小作为不平顺超限判据,计算机采集后,计算超限等级和数量,并计算扣分,以扣分的多少来衡量线路的好坏。
笔式绘图仪记录不平顺波形,GJ-3型轨检车上计算机的作用仅为计算扣分,没有发挥应有的作用。
仪器电路采用的大多是70年代末80年代初的分离元件,稳定性差,加之安装时间跨度大,即使同一种仪器使用的元器件也不尽相同,接口也不完全一样,造成了备件选择和维修上极大的困难,2000年前后,全路GJ-3型轨检车共有17辆,养护、维修难度很大。
轨检车的检测原理
轨检车的检测原理轨检车的检测原理:1、轨距的检测原理:GJ-4型轨检车所采用的轨距检测系统为激光光电伺服跟踪轨距测量装置。
在测量梁上安装激光光电传感器、位移计、驱动马达及伺服机械。
当钢轨产生位移,使轨距变化时,光电传感器感受其变化并输出相关电信号。
经调制解调器处理后,成为与轨距变化成线形比例的电压信号,再经过信号处理器、功放、驱动马达使光电传感器在伺服的推动下,发出的光束投身到左右股钢轨顶面下16mm处(16mm处是有效位置),跟踪钢轨位移。
经计算显示轨距。
(光电头被堵住、就不能检测轨距、同时也不检测方向)。
监测范围1415mm---1480mm +45mm、–20mm,误差为±1mm。
2.曲率的检测原理:曲率为一定弦长曲线轨道(如30米)对应的圆心角a,即、度/30m、度数大、曲率大、半径小。
反之,度数小、曲率小、半径大。
轨检车通过曲线时、测量轨检车每通过30米后车体方向角的变化值,计算出轨检车通过30米后的相应圆心角的变化值。
即曲率。
曲率、曲率变化率是检测曲线圆度的波形通道、仅供参考、不作考核内容。
能正确判断曲线正矢连续差和曲线的圆度。
曲率变化率的波形通道有突变、正矢肯定不好,(50×曲率)=正矢、如:某曲线曲率为0.46、正矢=50×0.46=23mm。
在直线上存在碎弯、小方向或轨距递减不好。
3、水平的检测原理:水平为轨道同一横断面内钢轨顶面之高差。
曲线水平称为超高。
GJ-4型轨检车采用补偿加速度系统测量水平,利用补偿加速度系统测量车体对地垂线滚动角,利用位移计测量车体与轨道相对滚动角,二者结合计算出轨道倾角。
利用两轨道中心线间距(1500mm)计算出水平值。
监测范围±200mm,误差±1.5mm。
4、高低的检测原理:高低是指钢轨顶面纵向起伏变化。
GJ-4型轨检车采用惯性基准的原理测量轨道变化的实际波型,得到高低变化的空间曲线,数据采集处理系统实时采集数据的间隔距离为0.305m,同时可换算成5米、10米、20米或其它弦长之测量法测量。
轨道检测车的运用
1 轨道检测车检测原理GJ-4型轨道检测车(简称轨检车)采用惯性基准测量原理和无接触测量方法,应用伺服跟踪、光电、陀螺、数字滤波等技术,采用先进的模拟-数字混合处理系统,传感器信号首先进入信号转接装置后,送入信号模拟预处理装置进行预处理。
预处理后的信号再通过信号转接及监视装置进入计算机数据处理系统,根据数学模型进行信号解偏、修正、补偿、滤波、合成计算出轨道几何参数,同时进行检测数据统计分析、摘取超限值、存储显示。
几何参数经D/A变换后,再经信号转接及监视装置后送至绘图仪以记录波形。
2 轨检数据说明维保部门反映根据检测缺陷数据在现场找不到对应的缺陷,或是现场根本不存在缺陷,根据轨检车设计原理需要更正几个观念。
2.1 里程误差GJ-4型轨检车使用的缺陷定位方法是人工设置里程,即在轨检车头尾两端各有一个里程设置键盘,检测过程中由操作人员观看现场里程标后在键盘中输入里程,传至检测系统形成缺陷数据里程。
因人为反应时间误差及两头设置里程的原因,致使检测的缺陷里程与现场会产生一定误差(见表1,下行,连续2次检测的同一处缺陷里程最大相差48 m)。
因此,现场核查时应在缺陷里程前后50 m内查找比较可靠。
2.2 正反向误差轨检车设计是根据轨检时面向轨检车发电机端为正方向,背向发电机端为反方向,而在确定左右高低、左右轨向时也与轨检车正方向有关,同时轨检车设计三角坑、水平项目正负也与正方向有关,而不是以轨道通常的上下行、左右轨定义,因此在现场查找缺陷时应先确定轨检车定义的正方向,进而判断缺陷存在的轨边及正负峰值。
轨检系统易受发电机振动影响,一般为不带动力,需要牵引机车牵引或推动检测。
受检测车两转向架轴重存在差异的影响,当机车牵引悬挂端不同,在推行或牵引过程中,由于动力因素作用,会导致设备检测梁产生不同程度的相对钢轨的位移,基于此,检测的轨道几何精度存在误差。
2.3 动态不等同于静态我国对动态检测设备的评价一直以检测精度作为主要指标。
轨检车检测原理及注意事项
测量基准(轨检梁刚体)与钢轨及惯性系统的相互位置关
系定义如下: gL 左轨轨距点相对测量基准的偏移; gR 右轨轨距点相对测量基准的偏移; dL 左轨踏面顶点相对测量基准的偏移; dR 右轨踏面顶点相对测量基准的偏移; wx 轨检梁的滚动角速率; wz 轨检梁的摇头角速率; ay 轨检梁的横向加速度及倾角; aL 轨检梁的垂向加速度; G 轨道踏面中点之间的标准距离,为1511mm; ht 惯性平台相对于轨距测量线的垂直高度; AL 左侧垂直加速度计安装位置相对梁中心的距离;
铁道部结合国外高速铁路的成熟经验以及现场
积累的相关经验,通过多年干线检测数据的大 量分析和研究,提出了针对既有线提速线路 200~250km/h区段轨道动态检测项目和管理标 准,并以此为依据于2007年3月22日铁道部颁布 实施 《既有线提速200~250km/h线桥设备维修 规则》(铁运【2007】44号)。文中对200和 250km/h区段轨道动态管理标准进行了明确, 增加了提速区段高低、轨向、长波长、轨距变 化率、曲率变化率和横加变化率等管理项目。 由此形成了V≦120km/h、120﹤V≦160km/h、 160km/h<V<200km/h、200km/h≦V≦250km/h 四个速度等级的轨道动态管理标准,后经过宜 昌轨检车会议讨论后形成新的轨道动态管理暂 行试验标准如表3所示。
返回目录
轨向正负:顺轨检车正向,轨向向左为正,向右为
负; 水平正负:顺轨检车正向,左轨高为正,反之为负; 曲率正负:顺轨检车正向,右拐曲线曲率为正,左 拐曲线曲率为负; 车体水平加速度:平行车体地板,垂直于轨道方向, 顺轨检车正向,向左为正; 车体垂向加速度:垂直于车体地板,向上为正。
轨道车辆无损检测技术有哪些
轨道车辆⽆损检测技术有哪些根据交通运输部《城市轨道交通设施设备运⾏维护管理办法》(交运规〔2019〕8号)的相关规定,车辆系统架修间隔应不超过5年或80万车公⾥、⼤修间隔应不超过10年或160万车公⾥。
与铁道车辆相⽐,地铁车辆有其鲜明的特点,由于关键零部件的制造⼯艺多由国外引⼊,因此在进⾏⽆损检测时多采⽤ISO、EN、NF等相关国际标准,同时结合相关铁路TB标准,如EN1291:2002 《焊缝磁粉探伤验收等级》、NF F00-090 《铁路制件磁粉探伤》、《铁路客车轮轴组装检修及管理规则》等。
在维修过程中,车辆探伤⼯使⽤的⽆损探伤技术作为轨道车辆探伤的重要检测⼿段,对于轨道车辆⾛形部件、车钩、悬挂件等重要部件内部缺陷的检测及提⾼列车运⾏安全发挥着重要作⽤。
常⽤的⽆损检测技术有磁粉检测(MT)、超声检测(UT)、渗透检测(PT)、射线检测(RT)、涡流检测(ET)等。
1超声波检测超声波探伤是利⽤超声能穿透⾦属材料的特点来检查零件是否有缺陷的检测⽅法。
车辆探伤⼯通过超声波探头发射超声波,经过耦合剂⼊射到⼯件中传播,根据反射回波在荧屏上的位置和波幅⾼低判断缺陷的⼤⼩和位置。
2磁粉检测磁粉探伤是利⽤⼯件表⾯和近表⾯缺陷磁导率和钢铁磁导率的差异,磁化后这些不连续处的磁场将发⽣崎变,从⽽吸引磁粉形成缺陷处的磁粉堆积,来判断破损的位置。
车辆探伤⼯在适当的光照条件下,让被检测⼯件显现出缺陷位置和形状。
磁粉探伤能够检测⼯件表⾯和近表⾯的裂纹、折叠、疏松、冷隔、发纹、⾮⾦属夹杂、未焊透、⽓孔等问题。
3渗透探伤检测渗透探伤检测是⽤于检查表⾯开⼝缺陷的检测⽅法,通过渗透剂渗⼊表⾯开⼝缺陷内,利⽤显像剂的作⽤将缺陷内的渗透剂吸附到⼯件表⾯形成痕迹⽽显⽰缺陷的存在。
车辆探伤⼯采⽤的渗透检测法是最有效的检测⼯件表⾯是否有破损的⽅法,对表⾯点状和线状缺陷的发现有重⼤帮助。
通过这⼏类⽆损探伤技术,车辆探伤⼯能够对列车各个关键部件进⾏多维度深度检查,发现故障点并及时进⾏修复处理,有效排除列车潜在⾏车隐患。
- 1、下载文档前请自行甄别文档内容的完整性,平台不提供额外的编辑、内容补充、找答案等附加服务。
- 2、"仅部分预览"的文档,不可在线预览部分如存在完整性等问题,可反馈申请退款(可完整预览的文档不适用该条件!)。
- 3、如文档侵犯您的权益,请联系客服反馈,我们会尽快为您处理(人工客服工作时间:9:00-18:30)。
一、我国轨道检查车发展
第一代轨检车1953年:铁科院研制开发 的机械式轨检车 第二代轨检车1962年:简易电气式轨检 车 第三代轨检车1986年:铁科院铁建所研 制开发的GJ-3型轨检车 第四代轨检车1987-1995年:通过引进 美国ENSCO公司研制开发的XGJ-1型 轨检车,铁科院铁建所研制开发出了GJ4型轨检车
• 三角坑使车辆产生三点支撑一点悬空,特别是当列车从圆
曲线向缓和曲线运行时,由于超高顺坡不良引起的三角坑, 易造成轮重减载,发生脱轨掉道事故。应引起高度重视和 重点监控。
• 三角坑计算公式为:h=(a-b)-(c-d)=Δh1-Δh2 • 其中Δh1为轨道断面Ⅰ-Ⅰ的水平值。Δh2为轨道断面Ⅱ
-Ⅱ的水平值。h即为基长L(断面Ⅰ-Ⅰ与断面Ⅱ-Ⅱ之 间距)时两轨道断面的水平差。
现代轨道检测技术及其应用
——局轨道检查车
局工务检测所(轨道检查车)
联系电话:061-33975
主要内容
• 一、国内轨道检测技术 • 二、国内轨检车技术应用 • 三、严重威胁行车安全的轨道检测数据 • 四、在判读超限表中遇到的几个问题 • 五、轨道几何尺寸超限与病害对应关系 • 六、怎样判读轨检图纸(几种典型的轨道检测图纸)
12
水平(超高)测量示意图
13
水平(GJ-5)
14
轨距、高低、方向示意图
15
超高示意图
16
曲率示意图
17
曲率
• 曲率测量定义为一定弦长的曲线轨道(如30M)对应之园
心角θ(度/30米)。度数大、曲率大、半径小。反之,度 数ห้องสมุดไป่ตู้,曲率小,半径大。
• 轨检车通过曲线时(直线亦如此),测量车辆每通过30米
术,研制成功XGJ-1型新型轨检车。该车采用惯性基准 检测原理,使用陀螺、光电、伺服马达传感器,采用 信号模拟处理和数字滤波混合技术,经过计算机采集 和信号合成处理,以报告和波形方式输出轨道几何不 平顺超限结果。经过轨道不平顺管理标准的评判,得 出轨道质量评价报告,指导现场掩护维修。
7
我国轨道检查车发展
6
我国轨道检查车发展
GJ-3型轨检车检测设备大多是采用70年代末80年代初
的分离元件,稳定性差,由于安装时间跨度大,同一 种仪器使用的元器件也不尽相同,接口不一致 , 造成 了备件选择和维修上极大的困难,近年来该车型正逐 步被新型检测设备所取代。
1985年我国成功引进美国 ENSC0 公司T-10轨检车技
我国轨道检查车发展
第五代轨检车1999年:通过引进美国ImageMap公司研制 开发的激光摄像技术轨检车
•20世纪50年代末期,铁科院技术人员采用弦测法原理,
通过机械传动方式检测轨道几何尺寸。将轨距、水平、三 角坑、摇晃( 用单摆测量)项目的幅值绘制在图纸上,经过 人工判读超限大小,计算每公里扣分,评价轨道质量。
后车体方向角的变化值,同时测量车体相对两转向架中心 连线转角的变化值,即可计算出轨检车通过30米曲线后的 相应圆心角θ变化值。
18
三角坑
• 三角坑:左右两轨顶面相对于轨道平面的扭曲。用相隔一
定距离的两个横截面水平幅值的代数差度量。
• 三角坑反映了轨顶的平面性。若轨顶abcd四点不在一个平
面上,c点到abd三点组成平面的垂直距离h为扭曲。
XGJ-1型轨检车采用“捷联式”系统结构 , 对
各种误差信号进行补偿修正 , 并使用小型计 算机集中处理全部检测项目数据。检测信号利 用率高,传感器安装方便,对车辆无特殊要求; 检测项目包括轨距、轨向、高低、水平、曲率, 三角坑等轨道几何不平顺,同时,增加了车体 (水平和垂直)、轴箱振动加速度、道岔、道 口及桥梁等地面具有显著特征的标志物检测设 备,用来综合评价线路质量和旅客乘坐舒适性、 指导维修,方便工务人员查找病害。
8
我国轨道检查车发展
• 1995年以XGJ-1型新型轨检车为基础,铁科院经过技术
引进和消化吸收,成功研制出4型车,该车设备国产化 程度达到95%以上。目前已在全国铁路和地铁系统广 泛推广应用。这标志着我国轨检技术和轨检车实现了 质的飞跃。
• 20世纪末期,国外轨检车技术已向着无移动部件、检
测项目齐全、故障判断高智能化、检测系统网络化、 检测数据处理科学化的方向发展。1999年通过国际招 投标方式,积极引进国际先进轨检车检测技术设备, 于2003年完成5型轨检车的验收,已投入到我国既有干 线检测生产和科研试验过程中。该检测设备已达到世 界同类检测水平。
9
二.我国轨检车检测技术
2.1检测项目和意义 2.2检测原理(略)
2.3轨检车技术应用
2.1检测项目和意义
主要包括:轨道几何参数、车体加速度参数、 钢轨断面参数等
轨道几何参数
轨距偏差:在轨道同一横截面、钢轨顶面以下16mm
处、左右两根钢轨之间的最小内侧距离相对于标准轨 距值1435mm的偏差。
19
三角坑示意图
Ⅰ
a
hc
d
b
Ⅱ Ⅰ
20
车体加速度
车体加速度检测的重要性: 众所周知,轨道不平顺引起车辆振动,车辆振动又与轨道
不平顺的幅值、波长、不平顺种类、不平顺的分布有关。 因而车辆振动是对轨道综合质量状态的反映。
高低:指轨道沿钢轨长度方向,在垂向上的凸凹不平
顺。
轨向:指轨顶内侧面沿长度方向的横向凸凹不平顺。 水平:即轨道同一横截面上左右两轨顶面的相对高差。
(曲线上是指扣除正常超高值的偏差部分;直线上是 指扣除一侧钢轨均匀抬高值后的偏差值。)
三角坑:左右两轨顶面相对于轨道平面的扭曲。用相
隔一定距离的两个横截面水平幅值的代数差度量。 “一定距离”指“车辆的轴距或心盘距”
•在保留1型车测量方法(弦测法)的前提下,60 年代后
期研制出2型轨检车,将机械传动改为电传动方式,检测 项目较1型车增加了高低不平顺检测,超限判读和扣分计 算方式与1型车相同。
5
我国轨道检查车发展
80 年代初期自主研制成功了GJ-3型轨检车:采用惯性
基准检测原理,使用先进的电传感器、计算机技术, 完成高低、水平、三角坑、车体垂直和水平振动加速 度的检测。传感器信号经过相关处理,直接以电压大 小作为不平顺超限判据,计算机采集后,计算超限等 级和数量,并计算扣分,以扣分的多少来衡量线路质 量的优劣。 通过笔式绘图仪记录并显示轨道不平顺检 测波形