空压机PLC控制方案
空压机联控控制方案

空压机联控控制方案一、背景引言空压机在工业生产中扮演着重要的角色,被广泛地应用于各种领域,如制造业、化工、电力、医药等。
随着工业自动化的发展,空压机联控系统的控制方案变得越来越重要。
本文将介绍一种基于PLC(可编程逻辑控制器)和SCADA(监视、控制和数据采集)技术的空压机联控控制方案。
二、方案介绍1.控制器选择本方案采用PLC作为控制器,PLC具有可编程性、稳定性和可靠性等优点,能够满足空压机联控系统的复杂控制需求。
2.传感器布置3.SCADA系统设计SCADA系统用于监视、控制和数据采集,能够实时显示空压机的各项运行参数,并对其进行远程操作和控制。
SCADA系统通常由上位机和下位机组成,上位机通过网络与下位机通信。
在本方案中,上位机使用HMI (人机界面)来实现用户与系统的交互。
4.控制策略本方案采用PID控制策略对空压机进行控制。
PID控制器是一种经典的控制算法,能够根据实时误差调节输出,使系统的控制精度达到预期效果。
PID控制器的参数可根据实际情况进行调整,并通过SCADA系统进行监测和优化。
三、具体实施步骤1.参数搜集与传感器布置:根据空压机的工艺要求,确定需要搜集的参数,并选择合适的传感器进行布置。
传感器的数据通过模拟量输出接口与PLC进行连接。
2. 控制逻辑设计:根据工艺要求、空压机的实际运行特点和传感器数据,设计空压机的控制逻辑。
将控制逻辑通过Ladder Diagram(梯形图)等方式编写,并上传到PLC中。
3.SCADA系统设计:根据用户需求设计HMI界面,将需要监控和控制的参数进行布局,并与PLC进行通信。
HMI界面应具有实时性、直观性和友好性。
4.控制策略调试:在实际运行中,根据实际情况调整PID控制器的参数,使控制策略达到最佳效果。
通过SCADA系统对控制策略进行监测和优化,以提高系统的控制精度和稳定性。
四、优点和应用1.本方案基于PLC和SCADA技术,灵活可靠,能够满足空压机联控系统的复杂控制需求。
空压机的PLC控制系统探讨

空压机的PLC控制系统探讨摘要:空压机是一种用来压缩气体提高气体压力或输送气体的机械,其用途广泛。
但是,普通空压机在运行中存在电能浪费、空压机元件易损耗等缺点。
在国家大力提倡节能减耗的同时,本文介绍了一种基PLC的空压机控制系统设计, 主要介绍了PLC的定义及特点,空压机控制系统的简要介绍,基于PLC空压机系统的控制要求及具体设计等。
关键词:PLC;空压机;控制系统;在我国能源日益紧张和浪费严重的形势下,高效低耗的节能技术受到人们的关注。
空压机作为制造业最常用的设备之所产生的廉价适用的压縮空气能源备受青睐。
基于PLC的空压机的用途很广,几乎遍及工农业、国防、科技、民用等各个领域。
它可以利用电动机将气体在压缩腔内进行压縮,并使压缩的气体具有一定压力。
一、PLC的定义及特点PLC是一种专门为在工业环境下应用而设计的数字运算操作的电子装置。
它采用可以编制程序的存储器,用来在其内部存储执行逻辑运算、顺序运算、计时、计数和算术运算等操作的指令,并能通过数字式或模拟式的输入和输出,控制各种类型的机械或生产过程。
PLC及其有关的外围设备都应该按易于与工业控制系统形成一个整体,易于扩展其功能的原则而设计。
它的特点表现在以下几个方面:1.可靠性高,抗干扰能力强高可靠性是电气控制设备的关键性能。
PLC由于采用现代大规模集成电路技术,采用专业的生产工艺制造,内部电路采取先进的抗干扰性技术,有很高的可靠性。
同时,PLC具有硬件故障的自我检测功能,当出现故障时,可及时发出警报信息。
在应用软件中,应用者还可以编写外围器故障的诊断程序,使相应的电路及设备获得故障诊断保护,最终整个系统具有极高的可靠性。
2. 配套齐全,功能完善,适用性强迄今为止,PLC已经形成了大、中、小各种规模的产品,可用于各种规模的工业场合。
除了逻辑处理的功能以外,现代PLC大部分数据运算能力,都用于各种数字的控制领域。
近年来,PLC的功能单元大量出现,使PLC进入了温度控制、位置控制、CNC等工业控制中。
S7—200PLC在煤矿空压机变频控制系统中的应用

S7—200PLC在煤矿空压机变频控制系统中的应用针对煤矿空压机系统常规控制方案中存在噪声大、压力波动大、电能风能损耗多、自动化调控性能差等问题,采用先进调控策略进行节能升级改造尤为重要。
基于PLC+变频器的恒压变频调控方案,能够根据系统所需风量经变频器PID实时动态调节风机电机输入电源频率,实现煤矿空压机组的高精度、高可靠性的恒压供气运行,有效提高了空压机系统的综合自动化水平,且具有非常可观的节能降耗效果,系统升级改造应用效果整体较好。
标签:煤矿;恒压供气;变频调速;PLC空压机作为煤矿企业重要的提供压缩空气的动力能源设备,为煤炭开采、传输、转运等过程中的所有气动元件提供必要的动力气源。
由于受传统设计理念、技改水平和技改资金等因素的制约,目前尚有较多的煤矿企业没有针对空压机系统实施自动化升级改造。
空压机作为常年运转设备,其常规的继电器直接控制方式存在启动电流大、运行效率低、电能风能等资源浪费严重、自动化调控性能差、供气可靠性低等问题,直接影响到企业的正常高效生产[1]。
因此,针对煤矿企业空压机系统现存的问题,经过深入研究和探討,对原控制系统进行节能升级改造,具有非常重要的意义。
1 传统继电器控制方式现存主要问题在煤炭生产过程中,需气量会受到生产节奏的影响,当处于用气量少运行工况时,空压机电机长期处于非满负荷甚至是空载运行条件下,供气管网中的气压就会不断增加,当达到系统气压上限时泄压阀就会自动打开,造成大量电能和风能资源浪费[2]。
如:某煤矿企业的1台功率为160kW的空压机,其额定电流为300A,空压机在加载工况下其运行电流为240A,而在空载运行工况下其运行电流为108A,此时电机功率因素直接降到0.4左右,空载工况下的能源消耗约占满载能耗的55%,这就严重影响煤矿供配电系统的供电电能质量,同时还造成大量的电能资源浪费。
传统空压机其控制方式通常采用Y-△降压启动,启动时启动电流是额定电流的几倍甚至十几倍,巨大冲击电流对电网的冲击,严重影响供配电系统的稳定。
空压机联控控制方案

三台空压机联控控制方案
一、系统说明:
用一台汇川PLC作为主站,分别与三台MD380变频器的PLC编程卡(MD38PC1)进行RS485通讯,站号任意标定,实现启动、停止、压力/温度、空压机轮换等控制功能;每台空压机配置一台HMI,和PLC编程卡进行RS422通讯,实时读取变频器的运行状态、电流/功率、压力/温度等显示参数,也可作为在单机模式下独立的控制。
同时PC机可以安装组态软件与PLC通讯,用作后台的监控,实时进行数据读取和发送,来控制系统的运行。
二、系统配置图(如下)
二、系统运行逻辑说明
1、启动运行
设置为联控状态,在所有机器待机的状态下,1#启动,进入打气状态,在设定的联机延时时间到达,如果压力未达到联控压力要求,那么2#机启动,联动延时时间到达,压力还是没有达到用气要求,那么3#机启动。
2、加载运行
空压机加载过程不改变,空压机启动后,根据联控压力进行加载,在加载过程中,另外两台机器均以一号机压力为检测标准。
3、卸载运行
当压力高于联控压力时,此时系统的3号机将进入卸载状态(可任意以条件设定,如总的运行时间等等),联动延时时间到,如果系统压力还是高于联控设定压力,那么继续执行2#机卸载,直至压力平衡。
4、停机状态
在联控状态下,如果手动停止1#主机,联控系统将关闭,其它空压机进入独立运行状态,互补影响,其它空压机手动停止运行后,进入停机状态。
5、空压机轮换状态
假设当前1#机,2#机运行能够满足用气需求,3#就处理待机状态或空载运行状态,再假设2#空压机连续运行时间达到轮换时间,此时3#空压机将启动,2#空压机进入停机状态。
6、单机和联机运行可切换。
MAM-KY02S空压机PLC联动控制说明
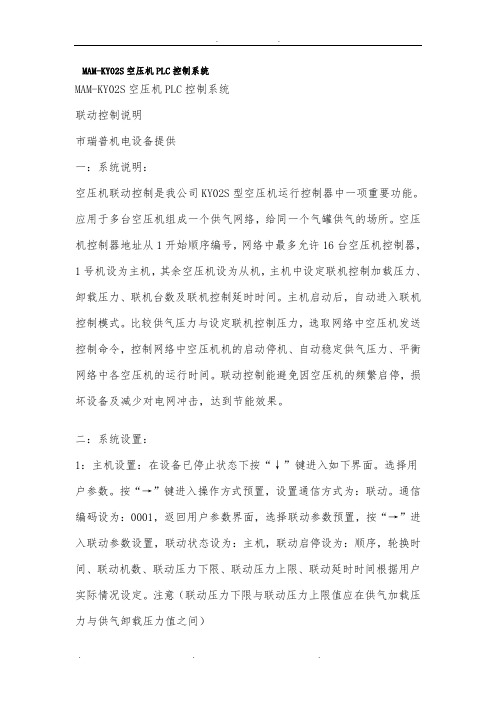
MAM-KY02S空压机PLC控制系统MAM-KY02S空压机PLC控制系统联动控制说明市瑞普机电设备提供一:系统说明:空压机联动控制是我公司KY02S型空压机运行控制器中一项重要功能。
应用于多台空压机组成一个供气网络,给同一个气罐供气的场所。
空压机控制器地址从1开始顺序编号,网络中最多允许16台空压机控制器,1号机设为主机,其余空压机设为从机,主机中设定联机控制加载压力、卸载压力、联机台数及联机控制延时时间。
主机启动后,自动进入联机控制模式。
比较供气压力与设定联机控制压力,选取网络中空压机发送控制命令,控制网络中空压机机的启动停机、自动稳定供气压力、平衡网络中各空压机的运行时间。
联动控制能避免因空压机的频繁启停,损坏设备及减少对电网冲击,达到节能效果。
二:系统设置:1:主机设置:在设备已停止状态下按“↓”键进入如下界面。
选择用户参数。
按“→”键进入操作方式预置,设置通信方式为:联动。
通信编码设为:0001,返回用户参数界面,选择联动参数预置,按“→”进入联动参数设置,联动状态设为:主机,联动启停设为:顺序,轮换时间、联动机数、联动压力下限、联动压力上限、联动延时时间根据用户实际情况设定。
注意(联动压力下限与联动压力上限值应在供气加载压力与供气卸载压力值之间)2:从机设置:在设备已停止状态下按“↓”键进入上图所示界面。
选择用户参数。
按“→”键进入操作方式预置,设置通信方式为:联动。
通信编码从0002到0016,(注意,网络中不允许有两台设备编码相同)。
返回用户参数界面,选择联动参数预置,按“→”进入联动参数设置,联动状态设为:从机。
从机的联动启停,轮换时间,联动机数,联动压力下限,联动压力上限,联动延时时间等不用设置。
三:网络连接:联动控制网络需采用屏蔽效果好的通信线将网络中空压机运行控制器的通信端口A、B并联起来,布线过程中宜尽量避免强电干扰。
信号线与电源线分走不同管道。
网络结构示意图如下图所示:四:运行联动控制:用户确认设定好网络中各空压机的联动控制参数,连接好通信线后,起动主机,系统自动进入联动控制状态。
基于PLC的空压机自动控制系统的设计
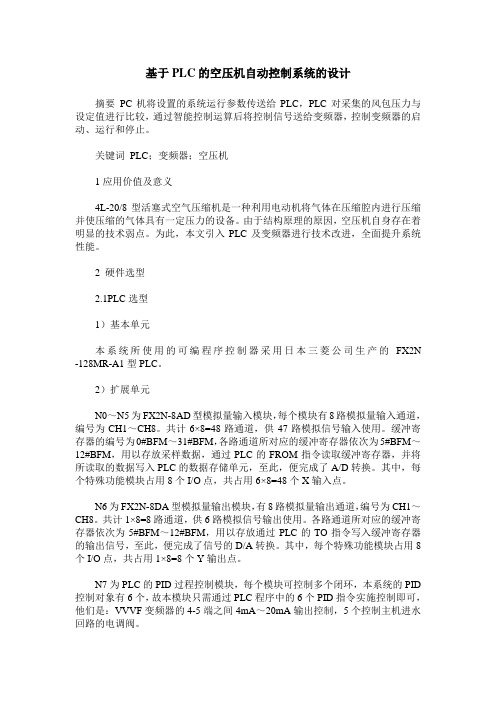
基于PLC的空压机自动控制系统的设计摘要PC机将设置的系统运行参数传送给PLC,PLC对采集的风包压力与设定值进行比较,通过智能控制运算后将控制信号送给变频器,控制变频器的启动、运行和停止。
关键词PLC;变频器;空压机1应用价值及意义4L-20/8型活塞式空气压缩机是一种利用电动机将气体在压缩腔内进行压缩并使压缩的气体具有一定压力的设备。
由于结构原理的原因,空压机自身存在着明显的技术弱点。
为此,本文引入PLC及变频器进行技术改进,全面提升系统性能。
2 硬件选型2.1PLC选型1)基本单元本系统所使用的可编程序控制器采用日本三菱公司生产的FX2N -128MR-A1型PLC。
2)扩展单元N0~N5为FX2N-8AD型模拟量输入模块,每个模块有8路模拟量输入通道,编号为CH1~CH8。
共计6×8=48路通道,供47路模拟信号输入使用。
缓冲寄存器的编号为0#BFM~31#BFM,各路通道所对应的缓冲寄存器依次为5#BFM~12#BFM,用以存放采样数据,通过PLC的FROM指令读取缓冲寄存器,并将所读取的数据写入PLC的数据存储单元,至此,便完成了A/D转换。
其中,每个特殊功能模块占用8个I/O点,共占用6×8=48个X输入点。
N6为FX2N-8DA型模拟量输出模块,有8路模拟量输出通道,编号为CH1~CH8。
共计1×8=8路通道,供6路模拟信号输出使用。
各路通道所对应的缓冲寄存器依次为5#BFM~12#BFM,用以存放通过PLC的TO指令写入缓冲寄存器的输出信号,至此,便完成了信号的D/A转换。
其中,每个特殊功能模块占用8个I/O点,共占用1×8=8个Y输出点。
N7为PLC的PID过程控制模块,每个模块可控制多个闭环,本系统的PID 控制对象有6个,故本模块只需通过PLC程序中的6个PID指令实施控制即可,他们是:VVVF变频器的4-5端之间4mA~20mA输出控制,5个控制主机进水回路的电调阀。
PLC程序设计
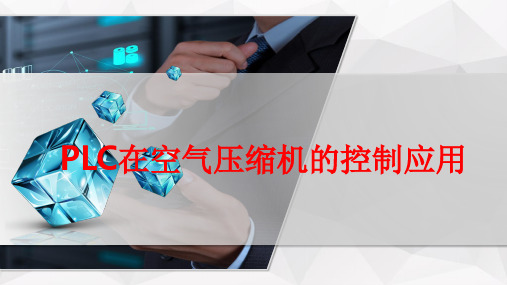
I:开关量
3 压差发信器 检测油精分压差
I:开关量
4 热继电器
检测电机过负荷状态 I:开关量
5 相序器
检测电源相序状况
I:开关量
6 水流量开关 检测冷却水流量
I:开关量
7 起动开关
空压机起动
I:开关量
8 停止开关
空压机停止
I:开关量
9 加载开关
空压机人工加载
I:开关量
1 KM1
主接触器(电机电源) Q:开关量
变频器
M 螺杆 主机
PLC (带PID调节)
温度 传感器
温度 传感器
压力 传感器
储气罐
触摸屏
气网
2、控制系统主要硬件
触摸屏
PLC
AD3203
模拟量输入模块
变频器
压力、温度传感器
减荷阀
压差发信器
相序器
热继电器
1)PLC在变频空压机站中的主要任务
(1)代替调节器,实现PID控制 (2)控制电动机的运行与切换(如有多台空压机) (3)PLC是变频器的驱动控制: 恒压供气空压机站中,变频器采用模拟量控制方式,气压传感器送来的模 拟量信号输入到PLC中,与给定值比较并经PLD处理后的模拟量控制信号,再 传送到变频器中,以此改变变频器的输出频率,从而实现对电机转速的控制。 (4)气站的其他逻辑控制 除了空压机组的运行管理外,气站还有其他逻辑控制工作,如手动、自动 操作转换、气站的工作状态指示、气站工作异常的报警、系统的自检等,这 些都是在PLC的控制程序中实现。
五、PLC程序控制方案
控制要点
空气 压力 控制
排气压力传 感器
P≥8Kg,减荷阀动作, 关闭进气口
P≤5Kg,减荷阀断电, 打开进气口
基于PLC的煤矿空压机控制系统设计设计

基于PLC的煤矿空压机控制系统设计设计煤矿空压机控制系统是煤矿生产过程中必不可少的一个环节,它的稳定性和可靠性对煤矿生产效率和安全性具有重要影响。
基于PLC(可编程逻辑控制器)的煤矿空压机控制系统设计,能够实现对空压机的自动化控制和监测,从而提高系统的稳定性和可靠性。
首先,对于煤矿空压机控制系统设计,我们需要考虑以下几个方面:1.空压机运行状态监测:通过传感器实时监测空压机的运行状态,包括转速、运行时间、温度和压力等参数。
PLC根据这些数据可以进行故障检测和预警,及时提醒操作人员进行维护和保养。
2.控制策略设计:根据煤矿生产需求,设计合理的控制策略。
根据工艺要求,设定压缩空气的压力范围和波动要求。
通过PLC的编程功能,可以设定运行参数和自动调整工作模式,以实现最佳的能耗和性能。
3.带载和无载运行切换:根据实际工作要求,需要设计带载和无载运行切换的功能。
通过PLC的控制,可以实现按需切换运行模式,提高能源利用效率。
4.故障响应和报警机制:针对空压机可能出现的故障情况,设计相应的故障检测和报警机制。
当空压机出现故障时,PLC能够发送报警信号,及时通知维修人员进行处理。
在系统设计过程中,可以采用以下步骤:1.确定功能需求和技术指标:根据具体的煤矿空压机控制要求,确定系统的功能需求和技术指标,包括运行参数、安全要求和可靠性要求等。
2.系统结构设计:根据需求和指标,设计系统的硬件结构和软件框架。
确定PLC的品牌和型号,选择适宜的传感器和执行器,并设计合理的通信接口和数据处理算法。
3.软件编程:根据系统设计要求,进行PLC的软件编程工作。
编写逻辑控制程序,实现各种控制功能和监测功能。
优化程序结构,提高系统的运行效率和可靠性。
4.系统测试和调试:在完成软件编程后,进行系统的测试和调试工作。
通过实际运行测试,验证系统的功能和性能是否满足需求。
根据测试结果进行相应的调整和优化。
5.系统运行和维护:系统投入运行后,进行日常的监测和维护工作。
- 1、下载文档前请自行甄别文档内容的完整性,平台不提供额外的编辑、内容补充、找答案等附加服务。
- 2、"仅部分预览"的文档,不可在线预览部分如存在完整性等问题,可反馈申请退款(可完整预览的文档不适用该条件!)。
- 3、如文档侵犯您的权益,请联系客服反馈,我们会尽快为您处理(人工客服工作时间:9:00-18:30)。
高(紧急停机);压力传感器故障(紧急停机);油过滤器堵塞(警报);油分离器堵塞(警 报);空气滤清器堵塞(警报)。
二.硬件配置方案 硬件配置 1(原配置): 主要的有 NEZA 本体 TSX08CD12R8D+扩展模块 TSX08EA4A2 TSX08H04M 4
行文本屏+接触器+相序保护继电器。 1) 主控器采用施耐德 小型 PLC NEZA 系列 TSX08CD12R8D, 该型号 PLC 性价
比非常高, CPU 单元:8 点输入 / 6 点输出,12 点输入 / 8 点输出 普通 I/O 扩展单元:12 点
输入,8 点输出的扩展结构,最多可连接 3 个扩展单元,可将本地 I/O 点数扩展 至 80 点。 模拟量扩展单元: 4 路 AD 2 路 DA。 4 远程通讯扩展单元: 点输入 / 4 点或 8 点
输出, 一个 RS485 4 通讯端口连接远程 I/O,支持 Modbus 通讯。 编程:中文化界面,Windows 平台。梯形图,指令表编程语言。允许简单编程,语言
80x90x70 80x90x70
100/240 VAC 24 VDC
80x90x70 80x90x70
100/240 VAC 24 VDC
95x90x70 95x90x70
100/240 VAC 24 VDC
混合型模块
4 点 输 TWDDMM8DRT 4
入/4 点
4
输出
16 点输 TWDDMM24DRF 16
压力、时间波动曲线。A、闪烁显示各种警讯并记录以备查询,包括: 相序错误(禁止启动);主机过载(紧急停机);主机温度高(紧急停机);排气温度高(紧 急停机);压力传感器故障(紧急停机);油过滤器堵塞(警报);油分离器堵塞(警报);空 气滤清器堵塞(警报)。起动提示,停机提示。
B、双温度检测保护:除了用 PT100 检测排气口温度。
16 I/O
7
一 体 型 TWDLCDA16DRF 9
16 I/O
7
一 体 型 TWDLCAA24DRF 14
24 I/O
10
一 体 型 TWDLCDA24DRF 14
24 I/O
10
输入 输出 输入 输出 输入 输出 输入 输出 输入 输出 输入 输出
24 VDC 继电器 24 VDC 继电器 24 VDC 继电器 24 VDC 继电器 24 VDC 继电器 24 VDC 继电器
Hale Waihona Puke 硬件配置 2:控制系统主要由模块化主机 TWDLMDA20RT、模拟量扩展模 TWDALM3LT 与 TWDAMI2HT 和文本显示屏 XBTN400(配通讯电缆)组成。其它功能与方案一同。
一 体 型 TWDLCAA10DRF 6
10 I/O
4
一 体 型 TWDLCDA10DRF 6
10 I/O
4
一 体 型 TWDLCAA16DRF 9
6、扩展功能多机联调:(另考虑) 为了合理配置供气系统:既能满足少用气量场合,又能满足用气量波动大的特殊需求。 本系统增加了多机联调功能,即只要客户在上位机中将运行模式设为多机联调模式,同时在 用户参数设定画面输入当前参与联调的设备的数目,系统将根据当前的用气量需求,自动增 减设备运行数目,以达到合理供气,降低运行成本的目的。
(twidoPLC%QW2.0)
附原空压机配线图:
地址 %Q 0.0 %Q0.1 %Q0.2 %Q0.3 %Q0.4
%Q0.5
%Q0.6
%Q0.7
四.硬件配置方案三(选用西门子 S7-200)
方案一、
Cpu224XP : 数字量 I/O 14 入 10 出。2 个模拟量输入,1 个电压输入;1 个模拟量输出,可
1
输入 输出 输入 输出 输入 输出
12 位 0-10 V, 4-20 mA 12 位 0-10 V, 4-20 mA 12 位 0-10 V, 4-20 mA
RTD 、 热 电 偶 输 入 : 12 位 0-10V, 4-20mA 输 出
三.详细 1.扩展单元 i/o分配及接线
对 PLC 的扩展口进行分配,其接 i/o口定义如附表所示。
磁阀、进气口电磁阀打开。) 3) 油压上升到 0.2MPA,且运行时间 1~3 分钟后,按加载启动,加载电磁阀得电加载,卸荷
阀(%Q0.7)开启。(分离油罐内压力升高,当工作压力大于最小压力阀设定的开启压力 时,压缩机排出压缩空气,空压机全负荷加载运行。) 4) 排气压力达到压力开关(系统)设定值,减荷运行;低于压力下限时,加载电磁阀得电, 机组重新加载。 5) 停机: 按下停止按钮,加荷时先转入减荷运行,30S 后,机组停机。 6) 紧急停机:按下按钮,所有输出信号强行终止,停机。 2、安全保护 相序错误(禁止启动); 1) 主机过载保护(紧急停机),轴承温度高报警。 2) 排气温度过高保护,报警上限为 110℃。 3) 环境温度过低保护 设定为-20℃,实际不用。 4) 超压保护:实际排气压力高出设定额定排气压力 0.07MPA,压缩机停机(减荷停机),显示 压力超高信息. 5) 发生水压不足:流量过低时,水流量开关动作,20S 内不能排除,及排气温度大于 110 度时,压缩机减荷停机),并发出指示。 6) 供油电磁阀故障保护 压缩机工作时需要充足的润滑油来冷却密封和润滑。在供油电磁
(现场所用温度变送模块/器为: PT100 量程为-10~200℃,精度 0.3%)
压力传感器:美国 MSI 压力传感器 型号: MSP-300-016-B-5-N-2 ,压力范围为 0~1.6MPA 输出信号:4~20mA
主电机的相序检测采用相序保护继电器 因为在螺杆空压机运用中,是不允许螺杆机头 反转的,一旦反转的话,会导致机头损坏。 当端子通电时,继电器吸合,如果相序正确并 且所有 3 相带电,黄色 LED 灯亮,正常工作(无故障)时继电器吸合,当主电机出现相 序故障或缺相时,切断电机三相电源,并把故障信号接入 PLC 以进行故障报警。
入/8 点
8
输出
输入 输出
输入 输出
24 VDC 可 拆 卸 继电器 端子排
24 VDC 继电器
不可拆 卸端子 排
2 路模拟量输入 1 路模拟量输出 2 路模拟量输入 1 路模拟量输出 2 路温度输入 1 路模拟量输出
TWDAMI2HT 2 TWDAM01HT 1 / TWDAMM3HT 2
1 / TWDALM3LT 2
软件设计软件上将分 PLC 程序设计和人机界面设计两部分。PLC 程序设计包括工艺 动作、报警及警报处理、模拟量采样(温度和压力)、画面更换、通讯等几部分设计;HMI 界 面设计:显示单机信息及运行/停止、模式转换、故障查询及复位、运行/负载时间查询、维 护时间提示、用户参数设定等, 使用编程软件编程。
输入口 起动按钮 减荷停止 加载 电机过载 水流量低
油过滤器 堵 油精分器 堵 进气过滤 器堵 相序错 远程停止 远程起动 急停
地址 %I 0.0 %I0.1 %I0.2 %I0.3 %I0.4
%I0.5
%I0.6
%I0.7
%I0.8 %I0.9 %I0.10 %I0.11
输出口 OK 排污 OK KM1
人机界面采用施耐德 TSX08H04M 4行文本屏,该文本屏功能强大,可通过 MODBUS 连接到 NEZA PLC。该屏在系统中主要用来参数的设定和显示,故障报警等等。NEZA PLC 在空压机系统中担任着集中控制的重要角色,通过采集各种传感器信号,并使用一定的工艺 算法,对执行机构进行控制,以下为接线图
阀两侧安装压差发讯器,故障时发出信号,压缩机组紧急停机。(实际无此信号?) 7) 油过滤器堵塞(警报);空气滤清器堵塞(警报)。油分离器堵塞(警报),压差开关:
压差达 0.1~0.15MPA 时动作.均为压差开关信号. 8) 压力传感器故障(报警) 3.参数设定:
排气压力上下限:上限 7.8BAR,下限 6.7Kg。 排气温度上下限:上限 110,下限-67。 排污阀排污时间: 3 秒, 关闭时间 3 分 电机起动间隔时间: 10 分钟 ;人机介面提示。 远程/本地控制设定; 常压超差显示 : 压力补偿设定: MPA 压力延时停机功能开启/关闭设定: 1111 为开通,2222 为关闭. 正常减荷停机时间设定: 15 秒 保养时间设定:包括整机保养时间设定、油过滤器保养时间设定、油细分离器保养时间 设定、空气过滤器保养时间设定。 4、状态显示: 排气压力/排气温度 空载运行时间/负载运行时间 主机状态:主机运行/主机停止 负载状态:负载运行/空载运行 主机运行/主机停止润滑油使用时间空气过滤器、油过滤器使用时间各种警讯并记录, 包括:相序错误(禁止启动);主机过载(紧急停机);风机过载(紧急停机);排气温度高 (紧急停机);压力传感器故障(紧急停机);油过滤器堵塞(警报);油分离器堵塞(警报); 空气滤清器堵塞(警报)。 以下可考虑增加功能项: 联机运行/单机;手动/自动 剩余保养时间:整机保养剩余时间、油过滤器保养剩余时间、油细分离器保养剩余时间、 空气过滤器保养剩余时间状态显示:排气压力/排气温度空载运行时间/负载运行时间主机状 态: 5、查询功能:(根据上述第 4 点增减) 查询最近故障纪录发生时间、负载加减载运行时间、设备总运行时间、系统保养时间、
自然。 2)模拟量模块采用 TSX08EA4A2 该模块具有 4AI/2AO, 输入与输出都可以连接
0~10V 或 4~20mA 信号,分辨率高达 12 位。 在螺杆式空压机中,温度和压力信号对保障系统安全可靠运行起到关键作用。温度过高,
会影响系统,有可能会导致机头损坏;而压力的的迅速建立,保证空压机的运行效率。本方 案使用模拟量模块来检测温度和压力信号, 但是由于很多 PLC 的供应商并不提供同时接 温度信号如 PT100 热电阻或 K 型热电偶和标准模拟量信号 0~10V 或 4~20mA, 主要用