制定工艺规程步骤和方法(参考)
简述制定工艺规程的步骤
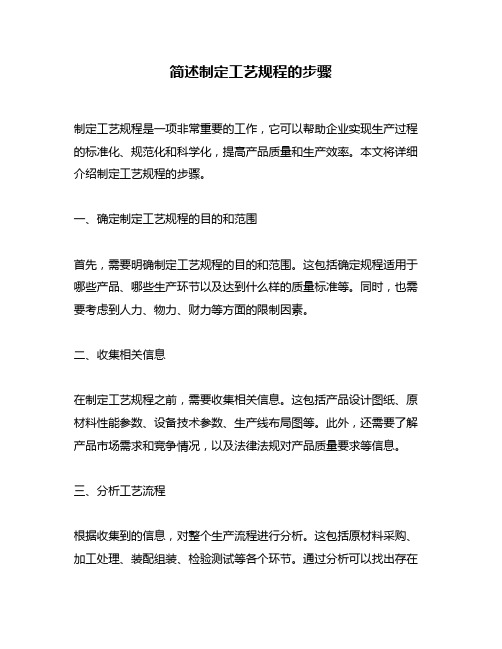
简述制定工艺规程的步骤制定工艺规程是一项非常重要的工作,它可以帮助企业实现生产过程的标准化、规范化和科学化,提高产品质量和生产效率。
本文将详细介绍制定工艺规程的步骤。
一、确定制定工艺规程的目的和范围首先,需要明确制定工艺规程的目的和范围。
这包括确定规程适用于哪些产品、哪些生产环节以及达到什么样的质量标准等。
同时,也需要考虑到人力、物力、财力等方面的限制因素。
二、收集相关信息在制定工艺规程之前,需要收集相关信息。
这包括产品设计图纸、原材料性能参数、设备技术参数、生产线布局图等。
此外,还需要了解产品市场需求和竞争情况,以及法律法规对产品质量要求等信息。
三、分析工艺流程根据收集到的信息,对整个生产流程进行分析。
这包括原材料采购、加工处理、装配组装、检验测试等各个环节。
通过分析可以找出存在问题或不合理之处,并提出改进措施。
四、确定关键控制点在整个生产流程中,有些环节对产品质量影响更大,需要进行特别关注和控制。
这些环节被称为关键控制点。
确定关键控制点可以帮助企业更加精确地掌握生产过程,提高产品质量。
五、编写工艺流程图和操作规程根据分析结果和确定的关键控制点,编写工艺流程图和操作规程。
工艺流程图是生产过程的可视化表达,可以帮助员工更好地理解生产流程。
操作规程则是对每个环节的详细说明,包括操作顺序、注意事项、质量标准等。
六、制定检验标准为了保证产品质量符合要求,需要制定相应的检验标准。
检验标准包括外观、尺寸、性能等方面的要求,并明确检验方法和标准值。
七、实施试生产在完成以上步骤后,需要进行试生产。
试生产是验证工艺规程是否可行的重要步骤。
在试生产过程中发现问题或不足之处需要及时改进。
八、修订工艺规程在试生产过后,根据实际情况修订工艺规程。
修订内容包括调整参数、改进工艺流程、完善操作规程等。
修订后的工艺规程应该更加科学、合理和可行。
九、推广应用完成工艺规程的制定和修订后,需要进行推广应用。
这包括培训员工、建立档案、监控执行情况等方面的工作。
制定工艺规程的步骤

6-3.制定工艺规程的步骤:⒈研究产品的装配图和零件图,进行工艺分析⑴零件的技术要求分析:通过分析产品零件图和装配图,了解零件在产品结构中的作用和装配关系,从而对其技术要求进行审查,确定其是否恰当,工艺上能否实现,找出技术要求的关键问题,以便采取适当措施,为合理制定工艺规程作好必要的准备。
⑵零件结构的工艺分析:所设计的零件在满足使用要求的前提下制造的可行性和经济性。
⒉毛胚的选择:⑴毛胚的种类和选择:锻件﹑铸件﹑焊接件﹑各种型材﹑棒料﹑板料及工程塑料等。
根据工件材料,力学性能形状结构等要求来确定⑵毛胚形状和尺寸确定:是否需要工艺凹台,是否一胚多件,是否用组合毛胚⒊拟订工艺路线:是设计的总体布局,主要任务是:选择零件表面的加工方法确定加工顺序划分工序,在切削加工的工序中,可以选择各工序的工艺基准,确定工序尺寸,设备工装,切削用量和时间定额等。
分阶段加工:粗加工﹑半精加工﹑精加工﹑光整加工(研磨或抛光)定位:工件在机床和夹具中占有正确位置的过程装夹:工件在机床或夹具中定位并夹紧的过程⒋确定各工序加工余量,计算工序尺寸及公差.例:毛胚尺寸:直径26±0.8粗车:直径22.5-0,0.5半精车:直径20.5-0,0.2精加工尺寸:直径20H6(工件尺寸)⒌选择各工序使用的机床设备及刀具﹑夹具﹑量具个辅助工具量具﹑刀具:单件﹑小批.选通用刀具大批﹑大量生产:通用和专用刀具并用夹具:单件﹑小批选用平口钳﹑分度头﹑三爪卡盘大批﹑大量选用各钻模﹑镗模﹑铣夹具辅助工具:镗杆﹑刀盒等⒍确定切削用量及时间定额切削用量:切削速度﹑进给量﹑吃到深度工时定额:安排生产﹑计算成本的依据⒎填写工艺文件工艺过程卡片工艺卡片工序卡片。
制定机械工艺规程的步骤和方法
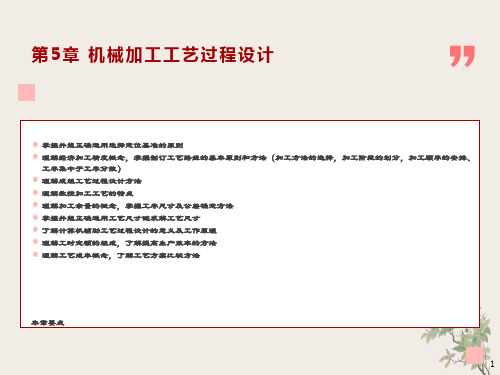
5.1.1 机械加工 工艺规程及其作 用
工艺规程形式(工艺过程卡、 工序卡、工艺卡)
5
5.1.1 机械加 工工艺规程及 其作用
6
5.1.1 机械加 工工艺规程及 其作用
7
5.1.1 机械加工工艺规程及其作用
工艺规程是指导生产的主要技术文件 机械加工车间生产的计划、调度,工人的操作,零件的加工质量检验,加工成本的核算,都是以工艺规程为依据的。
工艺规程中包括各个工序的排列顺序,加工尺寸、公 差及技术要求,工艺设备及工艺措施,切削用量及工时定额等 内容。
3
5.1.1 机械加工工艺规程及其作用
机械加工工艺规程 将制订好的零(部)件的机械加工工艺过程按一定的格式(通常为表格或图表)和要求描述出来,作为指令性技术 文件,即为机械加工工艺规程。 包括: 机械加工工艺过程卡——为说明零件机械加工工艺过程的工艺文件; 工序卡——对每道工序作详细说明、可直接用于指导工人操作的工艺文件; 检验工序卡——对成批或大量生产中重要检验工序作详细说明、指导检验的工艺文件; 机床调整卡——大批量生产中对由自动线、流水线上的机床以及由自动机或半自动机完成的工序,为调整工提供机 床调整依据的工艺文件。
❖ 机械加工工艺过程 采用各种机械加工方法,直接用于改变毛坯的形状、尺寸
、表面质量,使之成为合格零件的全部劳动过程。
❖ 机械加工工艺规程 规定零件机械加工工艺过程和操作方法等的工艺文件
称为机械加工工艺规程。 工艺规程是在具体的生产条件下,最合理或较合理的
工艺过程和操作方法,并按规定的形式书写成工艺文件,经审 批后用来指导生产的。
工艺规程是生产准备工作的主要依据 车间要生产新零件时,首先要制订该零件的机械加工工艺规程,再根据工艺规程进行生产准备。
工艺规程的制定步骤
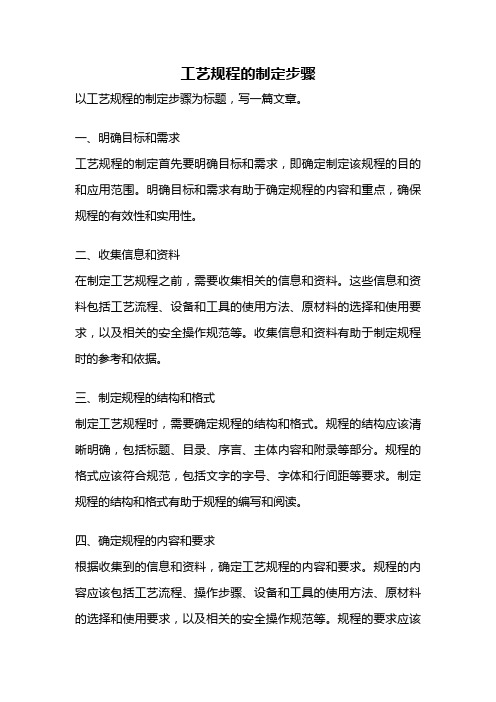
工艺规程的制定步骤以工艺规程的制定步骤为标题,写一篇文章。
一、明确目标和需求工艺规程的制定首先要明确目标和需求,即确定制定该规程的目的和应用范围。
明确目标和需求有助于确定规程的内容和重点,确保规程的有效性和实用性。
二、收集信息和资料在制定工艺规程之前,需要收集相关的信息和资料。
这些信息和资料包括工艺流程、设备和工具的使用方法、原材料的选择和使用要求,以及相关的安全操作规范等。
收集信息和资料有助于制定规程时的参考和依据。
三、制定规程的结构和格式制定工艺规程时,需要确定规程的结构和格式。
规程的结构应该清晰明确,包括标题、目录、序言、主体内容和附录等部分。
规程的格式应该符合规范,包括文字的字号、字体和行间距等要求。
制定规程的结构和格式有助于规程的编写和阅读。
四、确定规程的内容和要求根据收集到的信息和资料,确定工艺规程的内容和要求。
规程的内容应该包括工艺流程、操作步骤、设备和工具的使用方法、原材料的选择和使用要求,以及相关的安全操作规范等。
规程的要求应该明确具体,避免歧义或错误信息。
五、编写规程的草稿在确定规程的内容和要求之后,可以开始编写规程的草稿。
编写规程时,应该注意语句通顺,使用词汇丰富,避免重复和冗长。
草稿的编写可以参考相关的模板和样例,确保规程的规范和一致性。
六、评审和修改规程编写完规程的草稿后,需要进行评审和修改。
评审可以邀请相关的专家和从业人员参与,对规程的内容和要求进行检查和审查。
根据评审的结果,对规程进行适当的修改和完善,确保规程的准确性和可行性。
七、发布和实施规程经过评审和修改后,规程可以发布和实施。
发布规程时,应该将规程的内容和要求向相关的人员和部门进行宣传和培训,确保规程的理解和遵守。
实施规程后,应该进行监督和检查,及时发现和解决问题,确保规程的有效性和持续改进。
八、定期评估和更新规程工艺规程的制定是一个持续改进和更新的过程。
定期评估和更新规程有助于适应技术和市场的变化,确保规程的及时性和有效性。
制订工艺规程的步骤
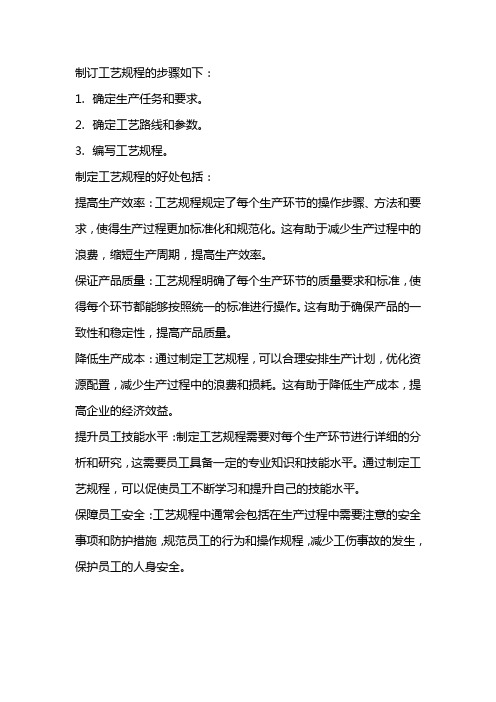
制订工艺规程的步骤如下:
1.确定生产任务和要求。
2.确定工艺路线和参数。
3.编写工艺规程。
制定工艺规程的好处包括:
提高生产效率:工艺规程规定了每个生产环节的操作步骤、方法和要求,使得生产过程更加标准化和规范化。
这有助于减少生产过程中的浪费,缩短生产周期,提高生产效率。
保证产品质量:工艺规程明确了每个生产环节的质量要求和标准,使得每个环节都能够按照统一的标准进行操作。
这有助于确保产品的一致性和稳定性,提高产品质量。
降低生产成本:通过制定工艺规程,可以合理安排生产计划,优化资源配置,减少生产过程中的浪费和损耗。
这有助于降低生产成本,提高企业的经济效益。
提升员工技能水平:制定工艺规程需要对每个生产环节进行详细的分析和研究,这需要员工具备一定的专业知识和技能水平。
通过制定工艺规程,可以促使员工不断学习和提升自己的技能水平。
保障员工安全:工艺规程中通常会包括在生产过程中需要注意的安全事项和防护措施,规范员工的行为和操作规程,减少工伤事故的发生,保护员工的人身安全。
制定机械加工工艺规程的步骤

制定机械加工工艺规程的步骤
1.确定工艺要求
首先要明确加工件的要求和技术要求,并根据加工件的材质、形状和用途等情况,确定加工工艺的可行性和合理性。
2.设计工件图纸
根据加工件的要求和规格,绘制详细的工件图纸,包括工件的尺寸、形状、数量、材质、加工面、加工精度、表面处理等信息。
3.选择加工工艺和工序
根据工件的材质、形状和技术要求,选择适当的加工工艺和工序,包括粗加工、精加工、热处理、表面处理等。
4.编制工艺流程和工序卡
根据所选的加工工艺和工序,编制详细的工艺流程和工序卡,包括每个工序的操作方法、加工参数、工具、夹具、设备和安全注意事项等信息。
5.制定检验方案
根据工件的质量要求和加工精度要求,制定相应的检验方案,并在加工过程中进行质量控制和检验,确保工件的质量符合要求。
6.制定安全措施
根据加工过程中可能存在的危险和安全风险,制定相应的安全措施和操作规程,确保加工过程中的安全。
7.审核和评审
制定完工艺规程后,需要对规程进行审核和评审,并及时调整和完善,确保规程的准确性和可行性。
工艺规程的制定步骤
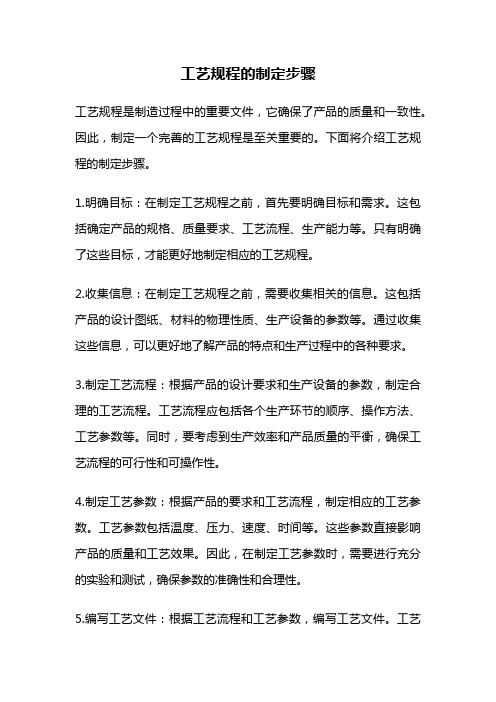
工艺规程的制定步骤工艺规程是制造过程中的重要文件,它确保了产品的质量和一致性。
因此,制定一个完善的工艺规程是至关重要的。
下面将介绍工艺规程的制定步骤。
1.明确目标:在制定工艺规程之前,首先要明确目标和需求。
这包括确定产品的规格、质量要求、工艺流程、生产能力等。
只有明确了这些目标,才能更好地制定相应的工艺规程。
2.收集信息:在制定工艺规程之前,需要收集相关的信息。
这包括产品的设计图纸、材料的物理性质、生产设备的参数等。
通过收集这些信息,可以更好地了解产品的特点和生产过程中的各种要求。
3.制定工艺流程:根据产品的设计要求和生产设备的参数,制定合理的工艺流程。
工艺流程应包括各个生产环节的顺序、操作方法、工艺参数等。
同时,要考虑到生产效率和产品质量的平衡,确保工艺流程的可行性和可操作性。
4.制定工艺参数:根据产品的要求和工艺流程,制定相应的工艺参数。
工艺参数包括温度、压力、速度、时间等。
这些参数直接影响产品的质量和工艺效果。
因此,在制定工艺参数时,需要进行充分的实验和测试,确保参数的准确性和合理性。
5.编写工艺文件:根据工艺流程和工艺参数,编写工艺文件。
工艺文件包括工艺卡、工艺标准、工艺指导书等。
这些文件详细说明了每个生产环节的操作方法、注意事项和质量要求。
工艺文件应具备清晰、简明、易懂的特点,以便操作人员能够准确执行。
6.培训操作人员:在制定工艺规程之后,需要对操作人员进行培训,使其熟悉工艺流程、工艺参数和工艺文件。
培训内容包括理论知识和实际操作,以确保操作人员能够正确地进行生产操作,并严格按照工艺规程执行。
7.实施和监控:在制定工艺规程之后,需要实施和监控工艺过程。
实施包括按照工艺规程进行生产操作,监控包括对生产过程中各个环节和参数的监控和调整。
通过实施和监控,可以及时发现和解决生产过程中的问题,保证产品的质量和一致性。
8.持续改进:工艺规程的制定不是一次性的工作,而是一个持续改进的过程。
在实施和监控过程中,需要不断收集反馈信息,并进行分析和评估。
简述工艺规程制定步骤
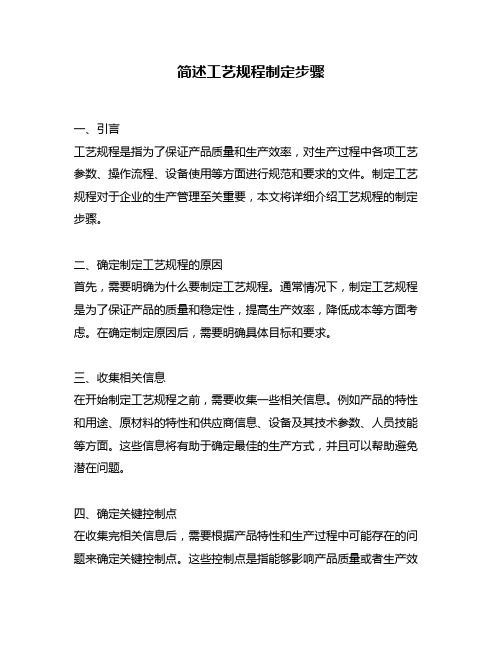
简述工艺规程制定步骤一、引言工艺规程是指为了保证产品质量和生产效率,对生产过程中各项工艺参数、操作流程、设备使用等方面进行规范和要求的文件。
制定工艺规程对于企业的生产管理至关重要,本文将详细介绍工艺规程的制定步骤。
二、确定制定工艺规程的原因首先,需要明确为什么要制定工艺规程。
通常情况下,制定工艺规程是为了保证产品的质量和稳定性,提高生产效率,降低成本等方面考虑。
在确定制定原因后,需要明确具体目标和要求。
三、收集相关信息在开始制定工艺规程之前,需要收集一些相关信息。
例如产品的特性和用途、原材料的特性和供应商信息、设备及其技术参数、人员技能等方面。
这些信息将有助于确定最佳的生产方式,并且可以帮助避免潜在问题。
四、确定关键控制点在收集完相关信息后,需要根据产品特性和生产过程中可能存在的问题来确定关键控制点。
这些控制点是指能够影响产品质量或者生产效率的环节。
例如温度、湿度、压力、速度等方面。
通过对这些关键控制点的监控和控制,可以有效地提高产品质量和生产效率。
五、确定工艺流程在确定关键控制点后,需要根据产品特性和生产过程中的实际情况来确定工艺流程。
工艺流程是指从原材料进厂到最终产品出厂的整个生产过程。
在制定工艺流程时需要考虑每个环节的时间、温度、湿度等参数,并且需要进行合理的安排。
六、编写工艺规程根据确定好的关键控制点和工艺流程,可以开始编写工艺规程了。
在编写过程中需要详细描述每个环节的操作方法、设备使用要求、检验要求等方面,并且需要明确责任人和检验标准。
七、审批和发布在完成工艺规程编写后,需要进行审批和发布。
审批是指对于工艺规程进行审核,确保其符合实际情况并且能够达到预期目标。
发布是指将已经审批通过的工艺规程公布给所有相关人员,并且对于新员工也需要进行培训。
八、执行和监控最后一步是执行和监控。
执行是指按照工艺规程进行生产,确保每个环节都符合要求。
监控是指对于生产过程中的关键参数进行监测和控制,并且及时纠正问题。
- 1、下载文档前请自行甄别文档内容的完整性,平台不提供额外的编辑、内容补充、找答案等附加服务。
- 2、"仅部分预览"的文档,不可在线预览部分如存在完整性等问题,可反馈申请退款(可完整预览的文档不适用该条件!)。
- 3、如文档侵犯您的权益,请联系客服反馈,我们会尽快为您处理(人工客服工作时间:9:00-18:30)。
制定工艺规程步骤和方法
1.分析设计对象
阅读零件图,了解其结构特点、技术要求及其在所装配部件中的作用(如有装配图,可参阅)。
分析时着重抓住主要加工面的尺寸、形状精度、表面粗糙度以及主要表面的相互位置精度要求,做到心中有数。
2.确定毛坯制造方法及总余量,画毛坯图
确定毛坯种类和制造方法时应考虑与规定的生产类型(批量)相适应。
对应锻件,应合理确定其分模面的位置,对应铸件应合理确定其分型面及浇冒口的位置,以便在粗基准选择及确定定位和夹紧点时有所依据。
查手册或访问数据库,确定主要表面的总余量、毛坯的尺寸和公差。
如若对查表值或数据库所给数据进行修正,需说明修正的理由。
绘制毛坯图。
毛坯轮廓用粗实线绘制,零件实体用双点画线绘制,比例尽量取1:1。
毛坯图上应标出毛坯尺寸、公差、技术要求,以及毛坯制造的分模面、圆角半径和拔模斜度等。
3.制定零件工艺规程
零件的结构、技术特点和生产批量将直接影响到所制定的工艺规程的具体内容和详细程度,这在制定工艺路线的各项内容时必须随时考虑到。
(1)表面加工方法的选择
针对主要表面的精度和粗糙度要求,由精到粗地确定各表面的加工方法。
可查阅工艺手册中典型表面的典型加工方案和各种加工方法所能达到的经济加工精度,选择与生产批量相适应的加工方案和加工方法,对其它加工表面也作类似处理。
(2)定位基准的选择
根据定位基准的选择原则,并综合考虑零件的特征及加工方法,选择零件表面最终加工所用精基准和中间工序所用的精基准以及最初工序的粗基准。
(3)拟定零件加工工艺路线
根据零件加工顺序安排的一般原则及零件的特征,拟定零件加工工艺路线。
在各种工艺资料中介绍的各种典型零件在不同产量下的工艺路线(其中已经包括
了工艺顺序、工序集中与分散和加工阶段的划分等内容),以及在生产实习和工厂参观时所了解到的现场工艺方案,皆可供设计时参考。
对热处理工序、中间检验、清洗、终检等辅助工序,以及一些次要工序(或工步)如去毛刺、倒角等,应注意在工艺方案中安排适当的位置,防止遗漏。
(4)选择各工序所用机床、夹具、刀具、量具和辅具
机床及刀、夹、量、辅具类型的选择应与设计零件的生产类型、零件的材料、零件的外形尺寸和加工表面尺寸、零件的结构特点、该工序的加工质量要求以及生产率和经济性等相适应,并应充分考虑工厂的现有生产条件,尽量采用标准设备和工具。
机床及工艺装备的选择可参阅有关的工艺、机床和刀、夹、量、辅具手册,也可访问数据库。
(5)工艺方案和内容的论证
根据设计零件的不同的特点,可有选择地进行以下几方面的工艺论证:
1)对比较复杂的零件,可考虑两个甚至更多的工艺方案进行分析比较,择优而定,并在说明书中论证其合理性。
2)当设计零件的主要技术要求是通过两个甚至更多的工序综合加以保证时,应用工艺尺寸链方法加以分析计算,从而有根据地确定有关工序的工序尺寸公差和工序技术要求。
3)对于影响零件主要技术要求且误差因素较复杂的重要工序,需要分析论证如何保证该工序技术要求,从而明确提出对定位精度、夹具设计精度、工艺调整精度、机床和加工方法精度甚至刀具精度(若有影响)等方面的要求。
4)其它的在设计中需要应加以论证分析的内容。
(6)填写工艺过程卡片
工艺过程卡片的格式可参考附图S0-1。
该工艺过程卡片的格式较工厂所用的工艺过程卡片(实际上各行各业甚至各工厂其卡片格式也不尽相同)有所简化,更适于学习阶段使用。
机械加工以前的工序如铸造、人工时效等在工艺工程卡片中要有所记载,但不编工序号,工艺过程卡片在课程设计中只填写本次课程设计所涉及到的内容。
(7)机械加工工序设计
对于重要的加工工序,要求进行工序设计,其主要内容包括:
1)划分工步根据工序内容及加工顺序安排的一般原则,合理划分工步。
2)确定加工余量用查表法确定各主要加工面的工序(工步)余量。
因毛坯总余量已由毛坯(图)在设计阶段定出,故粗加工工序(工步)余量应由总余量减去精加工、半精加工余量之和而得出。
若某一表面仅需一次粗加工即成活,则该表面的粗加工余量就等于已确定出的毛坯总余量。
3)确定工序尺寸及公差对简单加工的情况,工序尺寸可由后续加工的工序尺寸加上名义工序余量简单求得,工序公差可用查表法按加工经济精度确定。
对加工时有基准转换的较复杂的情况,需用工艺尺寸链来求算工序尺寸及公差。
4)选择切削用量切削用量可用查表法或访问数据库方法初步确定,再参照所用机床的实际转速、走刀量档数最后确定。
(8)填写主要工序的工序卡并画出工序简图
课程设计用简化的工序卡片格式见附图S0-2。
在工序卡上要求绘制出工序简图。
工序简图按照缩小的比例画出,不一定很严格。
如零件复杂不能在工序卡片中表示时,可用另页单独绘出。
工序简图尽量选用一个视图,图中工件是处在加工位置、夹紧状态,用细实线画出工件的主要特征轮廓。
本工序的加工面用粗实线画出。
为使工序简图能用最少视图表达,对定位夹紧表面以规定的符号来表示,见附表S0-3。
最后还要详细标明本工序的加工质量要求,包括工序尺寸和公差、表面粗糙度以及工序技术要求等。
对多刀、多工位加工,还应附有刀具调整示意图。
表S0-1 机械加工工艺过程卡片表S0-2 机械加工工序卡片
表S0-3 常用定位夹紧示意符号(摘自JB/Z174-82)。