粉末高速钢的研究进展_闫建新
粉末冶金高速钢的组织和性能研究
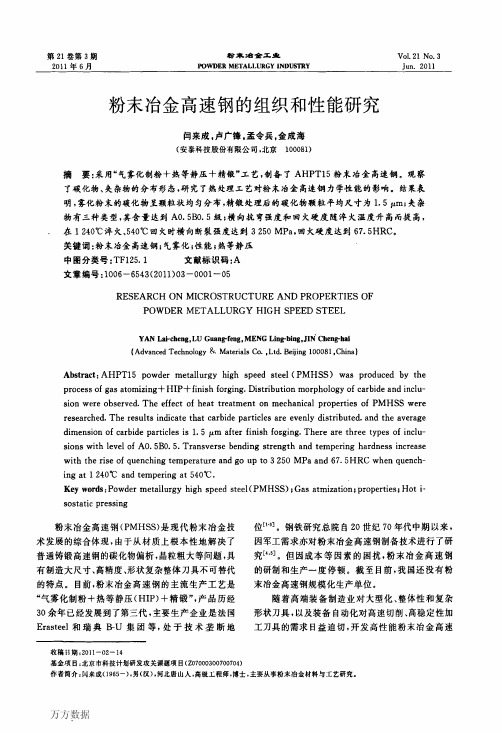
了碳化物、夹杂物的分布形态,研究了热处理工艺对粉末冶金高速钢力学性能的影响。结果表 明,雾化粉末的碳化物呈颗粒状均匀分布,精锻处理后的碳化物颗粒平均尺寸为1.5肛m;夹杂 物有三种类型,其含量达到A0.5BO.5级;横向抗弯强度和回火硬度随淬火温度升高而提高, 在1 240℃淬火、540℃回火时横向断裂强度达到3 关键词:粉末冶金高速钢;气雾化;性能;热等静压 中图分类号:TFl25.1 文献标识码:A
性能。
2
筛分前后d*均在40ftm左打.耗度土耍分柑在小r
38
r栅的范俐.详虬击^。
¥3^HpTl5雾化%丰戚HI质■nnI
1雨—1・—石——r——订——1丁——可—广
Hale Waihona Puke —i—T面——ii2 1 6l
1……212{㈣O“㈣110
i砸—丽ji—i而—iiii—iii『_
2l碱化物纰磬!与品粒艘
万方数据
H*m*:”^☆☆RⅫw∞mm自n**R
女日AHPTl 5;*#¥Ⅱ#∞*目∞*№
0《##Hn∞%m
图2足精锻后AHPT J 5试样的址微组纵,其巾 碳化物主要足Mc型(晴版色颗粒)和M:c刊(¨亮 色颗粒)…,在晶界和晶内呈均匀盎分巾-甲均尺t 为l
5
2 2
2夹杂物 根据美AsTM
E45
A(20。5)椅测杯准,采用屁
微浊对夹杂物进行了定性分析和评价。粉未精金高 速钢坯料巾主要含有姒r儿娄m盘届克杂:lj型刊 D型(钮化物)、c型(硅酸盐).详见图3。经成分椅 删和衍射分析认为.n类和c类夹杂f^l。()。和硅触 纳)主要由中问包?j染带_^,属于牯结类耐火材料。 D类央杂为金属氧化物.包括基体Fe的氧化物.氧 化铁为雾化粉末我面氰化所毁。 通过对r述夹杂物成因丹析认为,粉末冶金高 建钢巾央杂物主要取决干母台盒的纯净度。n雾化 制粉环节虽然受中闸包和褥眼等材料影响,但足经 过】‘装优化后.基本淌除了乖环节产隹的夹杂物, 幅且依据AsTM E45^f2㈨5)标准,对后续粉末暗 盒高速钢坯料的不lⅫ类型吏朵物的分柑形态和数量
粉末冶金工具钢的高硬度与高强度研究

粉末冶金工具钢的高硬度与高强度研究概述粉末冶金作为一种广泛应用的制造工艺,已经成为了制造工具钢的主要方法之一。
其制备工艺简单且能够生产出具有高硬度与高强度的工具钢。
本文将探讨粉末冶金工具钢的制备方法,研究其高硬度与高强度的原因,并讨论对其性能的影响因素。
引言粉末冶金工具钢是通过将金属粉末进行压制和烧结制备而成的,相比于传统的熔融冶金工艺,具有以下优势:材料损耗小、能耗低、成本较低、原料适用范围广等。
同时,粉末冶金工具钢还具有高硬度与高强度的特点,使其成为众多行业所青睐的材料。
制备方法粉末冶金工具钢的制备方法主要包括粉末制备、粉末成型和烧结三个步骤。
粉末制备:粉末制备是粉末冶金的关键步骤之一,直接影响工具钢的质量和性能。
常用的制备方法有机械合金化、雾化法、化学还原法等。
其中,机械合金化法是一种常用的方法,通过机械研磨和球磨使金属粉末和合金元素粉末充分混合,得到均匀的粉末混合物。
粉末成型:粉末成型是将粉末进行压制成型的过程。
常用的粉末成型方法有压制成型、注射成型和挤出成型等。
其中,压制成型是最常见的方法,将混合物放入模具中,施加足够的压力使之形成所需形状的制品。
烧结:烧结是指在一定的温度和压力下使粉末颗粒发生结合的过程。
烧结过程中,粉末颗粒之间会发生固态扩散,形成颗粒之间的原子结合,从而形成坚固的金属材料。
烧结温度和时间的选择对最终材料的密度、硬度和结构等性能有着重要的影响。
高硬度与高强度的原因粉末冶金工具钢具有高硬度与高强度的原因主要有以下几点:1. 物理特性:粉末冶金工具钢的颗粒大小和形状均匀,由于在制备过程中没有液体相的形成,使得材料的致密性和硬度得到了提高。
2. 合金元素的添加:在粉末制备过程中,可以根据需要添加合金元素来增加工具钢的硬度和强度。
例如,添加钴、钼等合金元素可以提高工具钢的硬度和耐磨性。
3. 压制成型和烧结过程:压制成型和烧结过程中施加的压力和温度可以改变粉末颗粒的结构和性质,从而影响到最终材料的硬度和强度。
粉末高速钢的碳化物粗化浅析
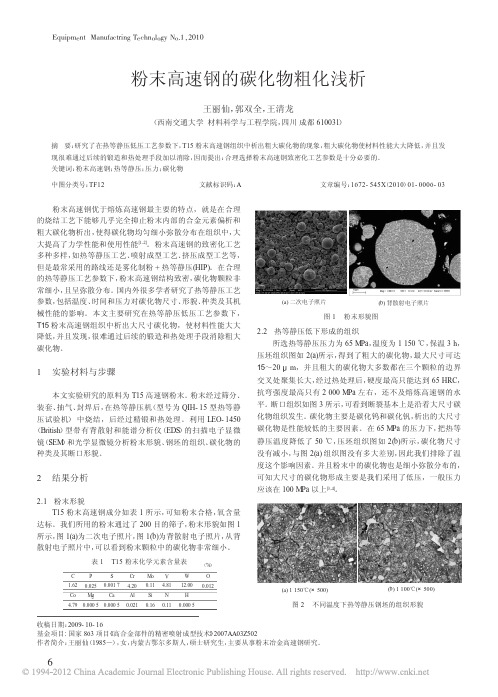
为 3:1 时锻造后的组织,与热等静压压坯组织相比,碳化物尺
寸几乎没有减小,于是我们加大锻造比改为 5:1,有局部地方
出现了锻裂的情况,但是组织中的碳化物尺寸还有没有多大
变化,如图 8(b)所示。因此,通过锻造手段对于在粉末冶金致
密化过程中形成的碳化物尺寸的减小,几乎不起作用。
(a) 锻造比为 3:1 (×500)
(b) 锻造比为 5:1(×500)
图 8 锻造组织图
7
Equipment Manufactring Technology No.1,2010
(2)热处理。正确的热处理工艺,对于提高粉末高速钢的 性 能 是 非 常 必 要 的 ,T15 粉 末 高 速 钢 的 淬 火 温 度 大 概 为 1 230~1 260 ℃,我们选择了 1 240 ℃,希望通过延长淬火保 温时间来溶解大尺寸的碳化物。我们取了直径为 10 mm 的小 样,分别保温 0.5 h、1 h 和 1.5 h 作为对比,图 9 为淬火后的组 织图。由图 9(a)可以看到,保温 0.5 h 晶粒未长大,但是碳化物 尺寸并没有减小;由图 9(b) 可以看到,保温 1 h 后晶粒明显长 大,但是碳化物尺寸没有改变;而图 9(c) 保温 1.5 h 后,晶粒明 显长大,并且伴随着少量的晶界熔化,而碳化物尺寸仍然没有 减小的趋势。由此我们可以知道,延长热处理保温时间对减小 碳化物的尺寸,也是没有效果的。由于大尺寸的碳化物主要分 布在颗粒边界处,颗粒边界由于氧化物等杂质元素富集,这些 都增加了碳化物溶解的阻力。
压坯组织图如 2(a)所示,得到了粗大的碳化物,最大尺寸可达 15~20 μm,并且粗大的碳化物大多数都在三个颗粒的边界 交叉处聚集长大,经过热处理后,硬度最高只能达到 65 HRC, 抗弯强度最高只有 2 000 MPa 左右,还不及熔炼高速钢的水 平。断口组织如图 3 所示,可看到断裂基本上是沿着大尺寸碳 化物组织发生。碳化物主要是碳化钨和碳化钒,析出的大尺寸 碳化物是性能较低的主要因素。在 65 MPa 的压力下,把热等 静压温度降低了 50 ℃,压坯组织图如 2(b)所示,碳化物尺寸 没有减小,与图 2(a) 组织图没有多大差别,因此我们排除了温 度这个影响因素。并且粉末中的碳化物也是细小弥散分布的, 可知大尺寸的碳化物形成主要是我们采用了低压,一般压力 应该在 100 MPa 以上[3~4]。
高速钢制备和热处理工艺的研究现状及发展趋势

**高速钢制备和热处理工艺的研究现状及发展趋势**随着工业化和现代化进程的不断推进,高速钢作为一种耐磨、高强度的金属材料,在机械制造、汽车制造、航空航天等领域发挥着重要作用。
然而,高速钢的制备和热处理工艺至关重要,直接影响着材料的性能和使用寿命。
本文将从制备工艺和热处理工艺两个方面,探讨高速钢的研究现状和发展趋势。
**一、高速钢制备工艺**高速钢的制备工艺一直是材料科学研究的热点之一。
目前,主要有粉末冶金法、真空熔炼法和传统冶金法等几种制备工艺。
其中,粉末冶金法因其能够精确控制合金成分、均匀分布合金元素和优异的成形性能而备受关注。
其制备过程大致包括粉末混合、压制成型和烧结等步骤。
然而,粉末冶金法在提高材料密度、提高热稳定性和改善材料性能等方面仍存在一定挑战,需要进一步研究和改进。
近年来,纳米技术和表面工程技术的发展也为高速钢的制备提供了新思路。
通过控制纳米结构和表面处理,可以进一步改善高速钢的硬度、耐磨性和抗疲劳性能。
在未来的研究中,可将纳米技术和表面工程技术与高速钢的制备相结合,以期取得更好的性能提升。
**二、高速钢热处理工艺**高速钢的热处理工艺对其组织和性能有着重要影响。
热处理工艺包括退火、正火、淬火、回火等多个环节,每个环节都需要精确控制温度、时间和冷却速度等参数。
目前,传统的高速钢热处理工艺已经十分成熟,但在提高高速钢的耐磨性、高温硬度和抗疲劳性能方面仍有待突破。
近年来,激光表面处理、等离子氮化等新型热处理技术的出现为高速钢的热处理提供了新选择。
这些新技术不仅可以提高高速钢的表面硬度和耐磨性,还可以有效抑制变形和提高工件质量。
未来的热处理工艺研究将着重于新技术的应用和改进,以期实现高速钢材料性能的进一步提升。
**三、发展趋势**在未来的研究中,高速钢的制备和热处理工艺将继续向精细化、智能化方向发展。
随着人工智能、大数据和云计算等新技术的应用,高速钢制备和热处理工艺将实现智能化控制,从而更好地保证材料的品质和稳定性。
粉末冶金综述

粉末冶金高速钢的研究及应用摘要高速工具钢被广泛应用于机械加工行业的刀具、加工成型的模具以及一些要求高耐磨或耐高温的零部件上。
粉末冶金高速钢具有独特的优势,本文主要介绍了粉末冶金的工艺,粉末冶金高速钢的生产流程和工艺比较,粉末冶金高速钢的应用。
关键词:高速钢,粉末冶金,PH MSS1.引言随着汽车、航天、航空、军工、信息技术产业及机械制造业的迅速发展,对切削刀具有越来越高的要求,为此开发用于刀具制造的优质材料就非常重要。
高速钢作为机械加工最常使用的一种工具材料,在钢铁材料尤其是特殊钢中占有非常重要的位置。
高速钢具有高达63-67HRC的硬度,并且在550・600℃时仍可保持60HRC以上的硬度、耐磨性和耐热性,因此被广泛应用于机械加工行业的刀具、加工成型的模具以及一些要求高耐磨或耐高温的零部件上囚。
高速工具钢属于高碳高合金莱氏体钢,采用传统的冶炼、铸锭、锻轧等生产工艺容易产生碳化物偏析,碳化物尺寸为2・12. m,严重影响其使用寿命的进一步提高口。
20世纪60年代后,粉末冶金高速钢逐步兴起,粉末冶金是节材、节能、高效、环境友好、适合大批量生产的金属成形匚艺。
粉末冶金法避免了熔炼法所带来的碳化物偏析而引起的机械性能的降低和热处理变形,在一定程度上能够提高速钢的强度和韧性,因而使高速钢的使用寿命得以提高。
采用粉末冶金的方法, 使得碳化物组织不受高速钢钢材尺寸的影响,最大尺寸的碳化物一般为3闻口m, 通常低于2|Jm。
随着粉末冶金技术和先进设备的快速发展,粉木高速钢中不存在碳化物偏析•,合金元素充分溶解到基体中,从而提高了高速钢的性能。
2.粉末冶金工艺简介粉末冶金工艺的主要组成是粉末的制取一一原料粉末的配料和混合一一成形一一固结。
可以根据对材料性能的要求和零件使用性能,在很宽的范围内组合材料成分。
主要的粉末冶金产业是铁基机械零件。
基于其工艺特点,还可制备高熔点金属,如鸨、铝等;金属陶瓷材料,如硬质合金、锲基高温材料等;假合金,如鸨铜、铜石墨等;多孔材料,如含油轴承、过滤材料、固一一液一一气分离材料等;多组元特殊材料,如摩擦材料、金刚石工具超硬材料等;微观或宏观复合材料,如颗粒弥散材料、磁粉芯、纤维(或晶须)增强材料、梯度材料、多层复合材料等。
球磨时间及预氧化方式对粉末冶金M3:2高速钢组织及力学性能的影响
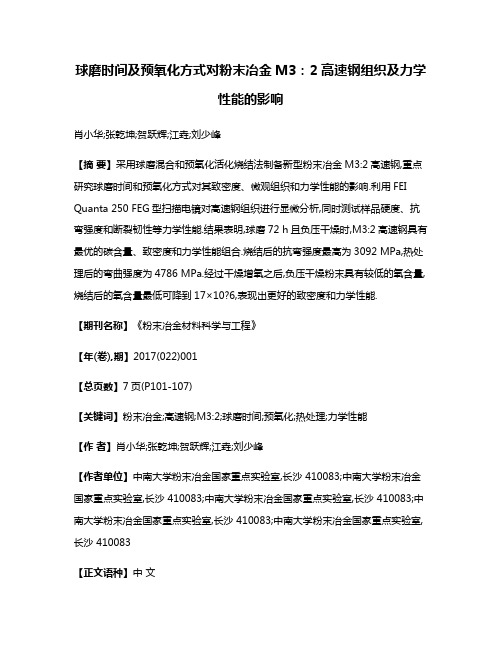
球磨时间及预氧化方式对粉末冶金M3:2高速钢组织及力学性能的影响肖小华;张乾坤;贺跃辉;江垚;刘少峰【摘要】采用球磨混合和预氧化活化烧结法制备新型粉末冶金M3:2高速钢,重点研究球磨时间和预氧化方式对其致密度、微观组织和力学性能的影响.利用FEI Quanta 250 FEG型扫描电镜对高速钢组织进行显微分析,同时测试样品硬度、抗弯强度和断裂韧性等力学性能.结果表明,球磨72 h且负压干燥时,M3:2高速钢具有最优的碳含量、致密度和力学性能组合.烧结后的抗弯强度最高为3092 MPa,热处理后的弯曲强度为4786 MPa.经过干燥增氧之后,负压干燥粉末具有较低的氧含量,烧结后的氧含量最低可降到17×10?6,表现出更好的致密度和力学性能.【期刊名称】《粉末冶金材料科学与工程》【年(卷),期】2017(022)001【总页数】7页(P101-107)【关键词】粉末冶金;高速钢;M3:2;球磨时间;预氧化;热处理;力学性能【作者】肖小华;张乾坤;贺跃辉;江垚;刘少峰【作者单位】中南大学粉末冶金国家重点实验室,长沙 410083;中南大学粉末冶金国家重点实验室,长沙 410083;中南大学粉末冶金国家重点实验室,长沙 410083;中南大学粉末冶金国家重点实验室,长沙 410083;中南大学粉末冶金国家重点实验室,长沙 410083【正文语种】中文【中图分类】TG156.31高速钢自 1900年问世以来, 大多采用传统的铸锭-锻轧工艺生产[1]。
由于高速钢的合金含量高,化学成分复杂,铸锭尺寸大,冷却速度缓慢等,在钢液凝固时不可避免地会产生粗大的莱氏体偏析组织,进而导致其加工性能和综合力学性能偏低,限制高速钢的应用和发展[2]。
1965年出现的雾化-热等静压粉末冶金高速钢很好地解决了熔炼高速钢一次碳化物粗大和成分偏析的问题[3-5]。
粉末高速钢具有成分偏析程度低、组织均匀细小、热处理变形小、硬度均匀、韧性和耐磨性好等诸多优点[6-9],广泛用于制造难加工材料切削工具,尤其适合制作大型拉刀、立铣刀、滚刀和剃齿刀等[10]。
高速钢刀具材料的发展和实验研究
7 机械工程师 2007 年第 11 期
F 专题论坛 FORUM ON S P ECIAL TOP IC
和 国 内 自 行 研 制 的 钢 种 , 有 高 钴 、含 钴 、含 铝 、高 钒 等 类 别。经济型高速钢中钨、钼含量较少, 性能低于通用型甚 多, 主要用于家用工具, 不宜用于机械加工, 这种钢的产 量也很大。
63 ̄66
经济型
HYW3 ( W3Mo2Cr4V2Si)
-
-
HYM42
W2Mo9Cr4VCo8
M42
高钴
HYM35 W6Mo5Cr4V2Co5
M35
或
HYT15
W12Cr4V5Co5
TБайду номын сангаас5
高 含钴 性
YCo10 ( W10Mo4Cr4V3Co10)
M48
能
HYM2Al W6Mo5Cr4V2Al
-
型 含铝
HYW9Al ( W9Mo3Cr4VAl)
-
67 ̄69 65 ̄68
- -
67 ̄69
HYM3
W6Mo5Cr4V3
M3- 2
-
高钒 HYW9V3 ( W9Mo3Cr4V3)
-
-
HYV4
( W12MoCr4V4)
-
-
河冶公司已开始生产粉末冶金高速钢, 其产品见表2。 Erasteel 是生产高速钢的国际著名公司, 制造粉末冶金高 速钢尤为擅长。表 2 中列出的粉末高速钢成分中, 钒含量 都很高, 达 3% ̄5%。由于消除了碳化物偏析和夹杂物, 刀 具刃磨并不困难。河冶公司推出粉末冶金高速钢产品, 必 将对国内外的应用发挥重要作用。
( 1) 通用型高速钢 早年, 中国从前苏联引进了 P18 通 用 型 高 速钢 , 即 W18Cr4V。多年中, W18Cr4V 几乎是中国唯一的一种高速 钢钢种, 得到广泛的应用。后来, 发展了 W6Mo5Cr4V2和 W9Mo3Cr4V。 ( 2) 高性能高速钢 中 国 引 进 了 美 国 高 性 能 高 速 钢 M42、M35 等 钢 种 , M42( 110W1.5Mo9.5Cr4VCo8) 综合性能很好, 刃磨也不难, 得到较多应用。但 M42 含钴量较多, 价格较贵。中国缺少钴 资源, 多依靠进口, 故发展了多种无钴或少钴的高性能高
粉末高速钢的制备及组织性能的研究
粉末高速钢的制备及组织性能的探究本文探究了粉末高速钢的制备及组织性能。
接受球磨法制备了Fe、Cr、Mo、W、V等元素的混合粉末,并通过热压技术制备出粉末高速钢。
对制备过程中的球磨时间、热压温度和压力等工艺参数进行了优化。
接受X射线衍射仪、扫描电镜等测试手段对制备后的粉末高速钢进行了表征。
结果表明,球磨时间为10h,热压温度为1190℃,压力为45MPa时,制备的粉末高速钢具有较优良的物理性能,硬度达到HRC67,耐磨性和耐蚀性也较好。
此外,分析了制备过程中的微观结构变化,探究了不同热处理温度对粉末高速钢性能的影响。
关键词:粉末高速钢;制备;组织性能;球磨;热压1. 绪论在工业生产中,钢材广泛应用于机械、汽车、建筑等领域。
其中,高速钢作为一种重要的材料,在切削加工领域有着广泛的应用。
传统的高速钢制备方法主要是接受熔炼和铸造的方式,但该方法存在成本高、耗能大等缺点。
粉末冶金技术是近年来出现的一种新的制备高速钢的方法,其优点在于制备工艺简易、成本低廉、能够得到匀称细小晶粒等。
2. 粉末高速钢的制备本探究接受球磨-热压法制备粉末高速钢。
起首,选取Fe、Cr、Mo、W、V等元素,按照一定的比例配制混合粉末。
然后,将混合粉末放入高能球磨机进行球磨,球磨时间和热压参数对制备的粉末高速钢的性能有着重要的影响。
因此,在球磨过程中需要对球磨时间、球磨介质、球磨速度等进行优化,以获得较优良的混合粉末。
在进行热压制备时,也需要对热压温度、压力等参数进行优化,以得到具有良好物理性能的粉末高速钢。
3. 粉末高速钢的组织性能探究对制备后的粉末高速钢进行了组织性能探究,使用了X射线衍射仪、扫描电镜等测试手段。
结果表明,制备出的粉末高速钢晶粒细小、匀称,且硬度明显高于传统高速钢。
通过对不同球磨时间、热压温度和压力下制备的样品进行比较,得出最佳制备条件为球磨时间10h、热压温度为1190℃、压力为45MPa时,制备出的粉末高速钢硬度达到HRC67。
世界粉末冶金高速钢的研究和生产现状
[ 8]
。
( 5) 抗疲劳性能好。细小均匀的内部组织大大 改善了粉末冶金高速钢的延展性 , 因而, 在与其他钢 种的耐磨性能一样的情况下, 粉末冶金高速钢的抗 疲劳性能更为优越。 Meurling
[ 9]
等人详细比较了粉
末冶金高速钢 ASP2023 、 ASP2014 和传统高速钢 M2 以及冷作工具钢 VANADIS10 的疲劳性能, 发现粉末 冶金高速钢 ASP2014 和 ASP2023 的抗疲 劳性能最 好 , 明显优于传统高速钢 M2 的抗疲劳性能。
增材制造用金属粉末制备技术研究现状及展望
增材制造用金属粉末制备技术研究现状及展望下载提示:该文档是本店铺精心编制而成的,希望大家下载后,能够帮助大家解决实际问题。
文档下载后可定制修改,请根据实际需要进行调整和使用,谢谢!本店铺为大家提供各种类型的实用资料,如教育随笔、日记赏析、句子摘抄、古诗大全、经典美文、话题作文、工作总结、词语解析、文案摘录、其他资料等等,想了解不同资料格式和写法,敬请关注!Download tips: This document is carefully compiled by this editor. I hope that after you download it, it can help you solve practical problems. The document can be customized and modified after downloading, please adjust and use it according to actual needs, thank you! In addition, this shop provides you with various types of practical materials, such as educational essays, diary appreciation, sentence excerpts, ancient poems, classic articles, topic composition, work summary, word parsing, copy excerpts, other materials and so on, want to know different data formats and writing methods, please pay attention!增材制造用金属粉末制备技术研究现状及展望1. 引言增材制造技术作为一种革命性的制造方法,正在快速发展并广泛应用于航空航天、医疗、汽车工业等领域。
- 1、下载文档前请自行甄别文档内容的完整性,平台不提供额外的编辑、内容补充、找答案等附加服务。
- 2、"仅部分预览"的文档,不可在线预览部分如存在完整性等问题,可反馈申请退款(可完整预览的文档不适用该条件!)。
- 3、如文档侵犯您的权益,请联系客服反馈,我们会尽快为您处理(人工客服工作时间:9:00-18:30)。
0.80~2.60 3.75~5.00 4.00~13.0 1.00~7.30 2.70~8.20 0.50~16.5
3 S390-PM(-MOD) 1.55~1.75 4.50~6.35 9.50~11.00 2.00~3.40 4.00~5.20 7.60~8.30
4
HS*-PM
0.75~1.35 3.80~4.50 9.00~18.50 0.50~3.90 1.40~4.50 4.50~10.5
继第一代 PM HSS 之后, 各生产厂对设备和生 产工艺进行了改进和更新, 如 1991 年法国 Erasteel 公司对其瑞典厂的制备气雾化前钢液的熔炼工艺做 了 改 进 ,称 为 ESH 法(Electro-Slag- Heating 电 渣 加 热法)。 所谓 ESH 技术就是带有电渣加热和吹 Ar 设 备的中间钢包系统,2 个石墨电极浸入碱性电渣内。 电流通过钢水表面的活性渣产生热量, 可保证 3 h 内高速钢钢水雾化过程中温度稳定, 又可使钢水脱 硫、脱氧。同时自钢包底吹 Ar 搅拌,使中间钢包钢水 温度均匀化,又促进钢水净化反应。 采用 ESH 方法 生产的 PM HSS 称为第二代 PMHSS,其产品商标也 改 为 ASP2000 系 列 (如 ASP 2030, 以 前 第 一 代 称 ASP 30), 它比第一代的 PM HSS 钢材更为纯净,非 金属夹杂物含量可减少 90%,淬回火后的钢材韧性 可提高 20%。 钢材的质量和性能对化学成分的波动 非常敏感, 通常要求成分的波动范围愈小愈好 。 [1,12] 第二代钢较第一代钢达到了更高的技术水平, 成分 波动范围比第一代缩小近 50%。 此外, 第二代 PM HSS ASP 2000 系列 钢材的纵向 与横向 抗 弯 强 度 相 差较小约为 22%~32%, 而 普通熔炼 HSS(M2、M42) 的相应值达 200%以上,并随钢材直径而变化,直径 愈大,纵向和横向抗弯强度相差值也愈大。这一点正 是大尺寸、高应力刀具使用 PM HSS 的理由之一。 2.3 第三代 PM HSS
是高速钢中的上品,它的特点在于无论尺寸大小和形 状如何,粉末高速钢材均具有碳化物颗粒细小、夹杂 物含量少、分布均匀等的显微组织特点,使高速钢的 抗弯强度、硬度和切削性能得到显著提高[2-3]。 近年全 世界 PM HSS 的年产量约 1 万吨, 西方工业发达国 家约占高速钢总产量的 1/6。 我国在上世纪 80 年代 初,已有几个科研院所研制成功了 PM HSS,但由于 用户认识不够、机械工业不够景气、价格昂贵和质量
作 者 简 介 :闫 建 新 ,男(1985-) ,主 要 从 事 不 锈 钢 研 究 。 通信联系人简介:李在元,男(1964-),主要从事冶金与材料物理化学研究,E-mail: lizy@ smm. ueu. edu. cn
第 27 卷
闫建新 李在元:粉末高速钢的研究进展
·317·
不够稳定等原因, 导致 PM HSS 的发展几乎完全停 性、红硬性、可加工性等方面均优异于常规铸、轧、锻
!!!!"
!"
!"
第 27 卷第 5 期 Vol.27 No.5
!!!!" 综合评述
doi:10.3969/j.issn.1003-7292.2010.05.012
硬质合金 CEMENTED CARBI(1.东北大学材料与冶金学院,辽宁沈阳 110004; 2.太原钢铁(集团)有限公司,山西太原 030030)
2010 年 10 月 Oct.2010
Development of PM High Speed Steel
Yan Jianxin1,2 Li Zaiyuan1
(1. School of Materials and Metallurgy, Northeastern University, Shenyang Liaoning 110004, China; 2. Taiyuan Iron and Steel (Group) Co. Ltd., Taiyuan Shanxi 030030, China)
法(雾化法制粉)在实验室制成高速钢的研究。 研究 细小甚至达到纳米级,使高速钢的硬度、耐磨性和易
表明, 用这种方法制成的高速钢其显微组织要比一 切削等物理性能都有了显著的提高, 克服了超硬材
般熔炼的钢材好,制成钻头的使用寿命长。 PM HSS 料的难加工或不可加工性,在加工铁基高温合金、钛
尽管具有产业化的希望, 可惜当时只能停留在研究 合金、超高强钢等难加工材料时发挥了重要的作用。
顿下来。令人欣慰的是,在第十届中国国际机床展览 材料,使其广泛应用于冶金、机械等行业。 我国科技
会(C1MT2007)上看到了国产 PM HSS 产品并且随着 人员的研究工作在 80 年代初也陆续展开并取得了
经济形势的改变,PM HSS 产业迅速发展并壮大,逐 一些成果,但是没能形成规模。
步在高速钢行业站稳了脚跟, 成为工具钢领域的佼
90 年 代 之 后 世 界 PM HSS 的 科 研 和 生 产 发 展
佼 者 [4-6]。
势头十分迅猛,随着冶金、机械等行业对切削刀具的
性能与寿命要求的日益苛刻以及市场需求量的增
1 PM HSS 的发展历程
加,高速工具钢粉末的制备方法也日趋成熟。在一些
关 键 工 艺 和 设 备 上 都 有 了 新 的 突 破 ,PM HSS 实 现
刀具在许多场合受到了限制。 此时,PM HSS 受到了 ASP2080 等)[11],表 1 为 PM HSS 主要牌号及成分范围。
各行业的瞩目。 70 年代初至 80 年代,瑞典、美国、日
经过近半个世纪的发展, 粉末高速钢的生产已
本和苏联等国相继用氮气雾化-热等静压工艺成功 逐步积累了很多经验,其制粉、成形以及烧结等技术
摘 要 粉末高速钢是通过特殊方法把高速钢微细粉末成形并烧结而制成的高速钢材 产品,简称 PM HSS。 粉末高速钢具有碳化物颗粒细小、夹杂物含量少、分布均匀等的显 微组织特点,使高速钢的抗弯强度、硬度和切削性能得到了显著提高。 本文综述了粉末 高速钢的发展历程、钢种开发以及高速钢粉末制备技术和成形等方面的研究中一些引 人注目的研究进展和发展动向。 关键词 综述; 粉末高速钢; 研究趋势; 进展
了各种烧结致密的技术, 使材料能够适应各种加工 新型 PM HSS。
过程(锻、轧 、切 削),并 在 合 金 系 的 开 发 中 也 发 现 了 2.1 第一代 PM HSS
规律性的变化 。 [4,8] 由于粉末高速钢制品在成分均匀
上世纪 70 年代 工 业 化 生 产 的 PM HSS 由 美 国
地制造出性能优良的粉末高速钢, 并进入工业化生 都日趋成熟。按其生产工艺技术的演变发展及质量、
产, 如瑞典的 Stora-ASEA 粉末冶金高速钢投产,电 性 能 等 不 同 ,PM HSS 大 致 可 分 为 第 一 代 PM HSS、
渣重熔高速钢开始用于大截面钢材生产。 其间发展 第二代 PM HSS、第三代 PM HSS 以及近年来研发的
5
CPM10V*
2.35~2.55 4.75~5.50 max0.50 1.10~1.45 9.3~10.25 max0.50
注:上表中 M*-PM 系列有 M2-PM、M3-PM、M4-PM、M7-PM、M-35PM、M42-PM、M48-PM、M50-PM、M-61PM 等;ASP* 系 列 有 ASP2015、ASP2017、ASP2130、ASP2053、ASP2060、ASP2080 等 ;HS*-PM 系 列 有 HS10-4-3-10PM、HS18-1-2-5PM、HS12-1-4-PM 等。
表 1 PM HSS 主要牌号及成分
序号
牌号
w(C) / % w(Cr) / % w(W) / % w(Mo) / % w(V) / % w(Co) / % 其它
1
M*-PM
0.88~1.85 3.75~5.00 5.50~12.9 4.25~10.0 0.95~5.25 0.50~10.0
2
ASP*
素,其应用范围还很窄,没能在工具钢领域推广开,
但却为 PM HSS 在以后的发展奠定了基础, 为工具
传统熔炼过程生产的高速钢牌号均可运用粉末
钢的开发研究指明了方向。
冶金方法生产,而高钒、高钴等高性能高速钢牌号是
随着冶金、机械加工等领域的发展,传统的切削 粉 末 冶 金 高 速 钢 所 独 有 的 牌 号 ( 如 ASP 2060、
阶 段 [7]。
就目前发展形势来看,PM HSS 的总趋势是向超细、
直到 1965 年,美国 的 Crucible Steels 公司自 主 超纯、粉末特性可控以及含氮高速钢[10]方向发展。
研发了用粉末冶金法生产高速钢的新技术并初步实
现了小规模产业化。由于技术水平低、认识不够等因 2 PM HSS 钢种开发
·318·
硬质合金
第 27 卷
Crucible 厂和瑞典 Stora 厂(现属法国 Erasteel 公司) 相继投产,此为第一代的 PM HSS。 第一代 PM HSS 生产者使用 1~2 t 的中间钢包, 其钢材夹杂物含量 相当电弧炉+LF 钢包精炼钢的水平,但是第一代 PM HSS 的抗弯强度较普通熔炼高速钢提高了约 1 倍。 第一代 PM HSS 在我国市场上具有代表性的是乌克 兰 DSS 厂生产的产品。 该厂 1980 年从瑞典引进设 备和技术,自 1985 年以来未做过技术改进,钢材的 氧含量小于 150×10-6, 售价便宜。 2002 年以前 DSS 厂一直为美国 Crucible 厂做贴牌生产[1]。 此外日本日 立金属、台湾荣钢(用 DSS 厂钢粉生产 PMHSS)生产 的 PM HSS 也达到第一代粉末冶金高速钢的质量水 平。 2.2 第二代 PM HSS
PM HSS 技术是高速钢制造领域划时代的新技 了高合金冶炼, 一些新钢种热处理硬度可达 70~72