蜗轮蜗杆的设计计算
蜗轮蜗杆传动计算和设计流程

蜗轮蜗杆传动计算和设计流程
蜗轮蜗杆传动的计算和设计流程一般包括以下几个步骤:
1. 确定传动比:根据传动的要求,确定所需的传动比。
传动比可以通过计算Worm轮的齿数与Worm杆的螺旋线数之比来确定。
2. 确定蜗杆的参数:在确定传动比的基础上,确定蜗杆的螺旋线的角度、蜗杆的喉圆距离等参数。
这些参数可以通过蜗杆的传动比、齿数和齿距等来计算。
3. 确定蜗轮的参数:根据蜗杆的参数和传动比,确定蜗轮的齿数和齿形。
根据蜗杆和蜗轮的参数,可以使用蜗轮的设计公式来计算蜗轮的参数。
4. 验证传动性能:根据设计的参数,利用传动计算公式,
验证蜗轮蜗杆传动的传动效率、载荷分配、齿面接触应力
等性能指标,确保传动的可靠性和合理性。
5. 进行材料选择:根据传动性能和使用要求,选择合适的
材料来制造蜗轮和蜗杆,确保传动的强度和耐磨性等要求。
6. 进行结构设计:根据蜗轮和蜗杆的参数和材料,进行结
构设计,包括蜗杆的螺纹加工、蜗轮的齿形加工等。
7. 进行制造和装配:根据结构设计,进行蜗轮和蜗杆的制造,并进行装配。
在制造和装配的过程中,要注意工艺控
制和质量检验,确保传动件的质量和精度。
8. 完成传动系统的调试和测试:在装配完成后,进行传动
系统的调试和测试,检查传动的运行情况,验证设计的正
确性和合理性。
总之,蜗轮蜗杆传动的计算和设计流程就是根据传动要求确定传动比、确定蜗杆和蜗轮的参数,验证传动性能,选择材料,进行结构设计,制造和装配,最后进行调试和测试,以确保传动系统的性能和可靠性。
蜗轮蜗杆设计参数
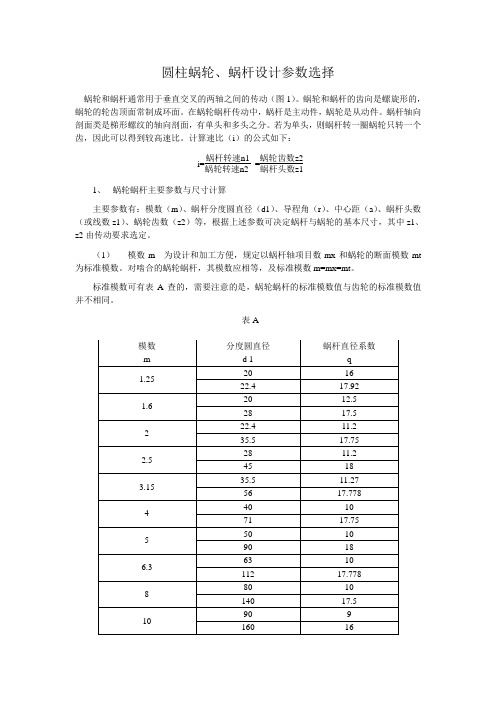
圆柱蜗轮、蜗杆设计参数选择蜗轮和蜗杆通常用于垂直交叉的两轴之间的传动(图1)。
蜗轮和蜗杆的齿向是螺旋形的,蜗轮的轮齿顶面常制成环面。
在蜗轮蜗杆传动中,蜗杆是主动件,蜗轮是从动件。
蜗杆轴向剖面类是梯形螺纹的轴向剖面,有单头和多头之分。
若为单头,则蜗杆转一圈蜗轮只转一个齿,因此可以得到较高速比。
计算速比(i)的公式如下:i=蜗杆转速n1蜗轮转速n2=蜗轮齿数z2蜗杆头数z11、蜗轮蜗杆主要参数与尺寸计算主要参数有:模数(m)、蜗杆分度圆直径(d1)、导程角(r)、中心距(a)、蜗杆头数(或线数z1)、蜗轮齿数(z2)等,根据上述参数可决定蜗杆与蜗轮的基本尺寸,其中z1、z2由传动要求选定。
(1)模数m 为设计和加工方便,规定以蜗杆轴项目数mx和蜗轮的断面模数mt 为标准模数。
对啮合的蜗轮蜗杆,其模数应相等,及标准模数m=mx=mt。
标准模数可有表A查的,需要注意的是,蜗轮蜗杆的标准模数值与齿轮的标准模数值并不相同。
表A图1图2(2)蜗杆分度圆直径d1 再制造蜗轮时,最理想的是用尺寸、形状与蜗杆完全相同的蜗轮滚刀来进行切削加工。
但由于同一模数蜗杆,其直径可以各不相同,这就要求每一种模数对应有相当数量直径不同的滚刀,才能满足蜗轮加工需求。
为了减少蜗轮滚刀数目,在规定标准模数的同时,对蜗杆分度圆直径亦实行了标准化,且与m 有一定的匹配。
蜗杆分度圆直径d1与轴向模数mx之比为一标准值,称蜗杆的直径系数。
即q=蜗杆分度圆直径模数=d1m d1=mq有关标准模数m 与标准分度圆直径d1的搭配值及对应的蜗杆直径系数参照表A (3) 蜗杆导程角r 当蜗杆的q 和z1选定后,在蜗杆圆柱上的导程角即被确定。
为导程角、导程和分度圆直径的关系。
tan r=导程分度圆周长 = 蜗杆头数x 轴向齿距分度圆周长 =z1px d1π =z1πm πm q =z1q相互啮合的蜗轮蜗杆,其导程角的大小与方向应相同。
(4) 中心距a 蜗轮与蜗杆两轴中心距a 与模数m 、蜗杆直径系数q 以及蜗轮齿数z2间的关系式如下:a=d1+d22 =m q(q+z2)蜗杆各部尺寸如表B蜗轮各部尺寸如表C2、 蜗轮蜗杆的画法(1) 蜗杆的规定画法 参照图1图2 (2)蜗轮的规定画法 参照图1图2 (3)蜗轮蜗杆啮合画法 参照图1图2.。
蜗杆蜗轮分度圆计算公式

蜗杆蜗轮分度圆计算公式蜗杆蜗轮传动是一种常见的传动形式,它具有传动比大、传动平稳、噪音小等优点,在工业生产中得到了广泛的应用。
蜗杆蜗轮的设计与计算是蜗杆蜗轮传动的关键,其中蜗杆蜗轮的分度圆计算是设计中的重要环节。
本文将介绍蜗杆蜗轮分度圆的计算公式及其相关知识。
蜗杆蜗轮的分度圆是指蜗轮上的分度圆,它决定了蜗轮的齿数、齿廓等重要参数。
蜗杆蜗轮的分度圆计算公式主要包括蜗杆分度圆的计算和蜗轮分度圆的计算两部分。
首先是蜗杆分度圆的计算。
蜗杆的分度圆直径可以通过以下公式计算:d = m z。
其中,d为蜗杆分度圆直径,m为模数,z为蜗杆的齿数。
模数是蜗杆蜗轮传动中的重要参数,它是齿轮的模型参数,表示齿轮齿数与分度圆直径的比值。
通过选择合适的模数,可以满足传动的强度、精度和传动比等要求。
接下来是蜗轮分度圆的计算。
蜗轮的分度圆直径可以通过以下公式计算:D = m z。
其中,D为蜗轮分度圆直径,m为模数,z为蜗轮的齿数。
与蜗杆分度圆类似,蜗轮的分度圆直径也是通过模数和齿数来计算的。
在实际设计中,需要根据传动比、工作条件等因素来选择合适的模数和齿数,以满足设计要求。
除了分度圆直径的计算公式外,还需要考虑蜗杆蜗轮的齿廓参数。
蜗杆蜗轮的齿廓是蜗杆蜗轮传动中的重要参数,它直接影响着传动的效率和精度。
在实际设计中,需要根据蜗杆蜗轮的齿廓参数来确定蜗杆和蜗轮的齿形,以保证传动的平稳性和精度。
总之,蜗杆蜗轮的分度圆计算是蜗杆蜗轮传动设计中的重要环节,它直接影响着传动的性能和可靠性。
通过合理的计算公式和参数选择,可以设计出性能优良的蜗杆蜗轮传动装置,满足工程应用的要求。
希望本文介绍的蜗杆蜗轮分度圆计算公式及相关知识能够对蜗杆蜗轮传动的设计和应用有所帮助。
蜗轮蜗杆设计计算
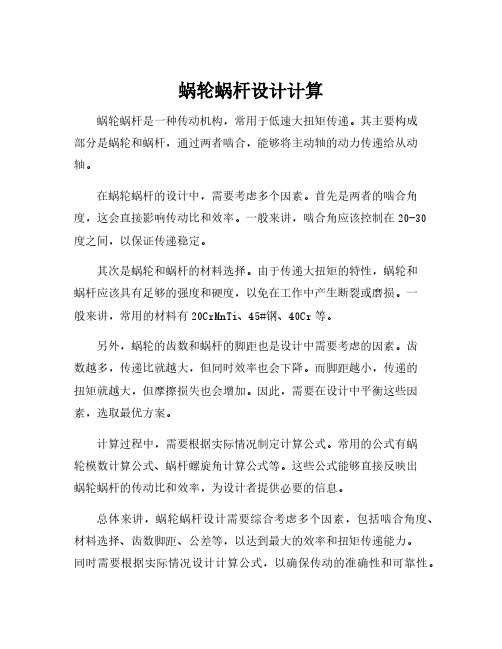
蜗轮蜗杆设计计算
蜗轮蜗杆是一种传动机构,常用于低速大扭矩传递。
其主要构成
部分是蜗轮和蜗杆,通过两者啮合,能够将主动轴的动力传递给从动轴。
在蜗轮蜗杆的设计中,需要考虑多个因素。
首先是两者的啮合角度,这会直接影响传动比和效率。
一般来讲,啮合角应该控制在20-30度之间,以保证传递稳定。
其次是蜗轮和蜗杆的材料选择。
由于传递大扭矩的特性,蜗轮和
蜗杆应该具有足够的强度和硬度,以免在工作中产生断裂或磨损。
一
般来讲,常用的材料有20CrMnTi、45#钢、40Cr等。
另外,蜗轮的齿数和蜗杆的脚距也是设计中需要考虑的因素。
齿
数越多,传递比就越大,但同时效率也会下降。
而脚距越小,传递的
扭矩就越大,但摩擦损失也会增加。
因此,需要在设计中平衡这些因素,选取最优方案。
计算过程中,需要根据实际情况制定计算公式。
常用的公式有蜗
轮模数计算公式、蜗杆螺旋角计算公式等。
这些公式能够直接反映出
蜗轮蜗杆的传动比和效率,为设计者提供必要的信息。
总体来讲,蜗轮蜗杆设计需要综合考虑多个因素,包括啮合角度、材料选择、齿数脚距、公差等,以达到最大的效率和扭矩传递能力。
同时需要根据实际情况设计计算公式,以确保传动的准确性和可靠性。
蜗轮蜗杆设计计算
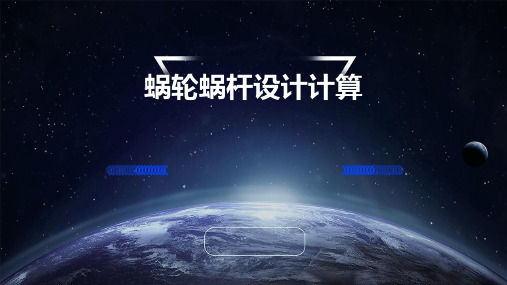
蜗杆传动的效率计算
总结词
根据蜗轮蜗杆的设计参数和工况,计算出蜗杆传动的效率。
详细描述
蜗杆传动的效率计算是评估蜗杆传动性能的重要指标之一。通过分析蜗轮蜗杆的设计参 数和工况,如蜗杆的导程角、模数、转速和载荷等参数,可以计算出蜗杆传动的效率。
蜗轮齿面接触疲劳强度的计算
总结词
根据蜗轮齿面上的载荷分布和材料属性 ,计算出蜗轮齿面的接触疲劳强度。
刚度分析
进行蜗轮蜗杆的刚度分析, 以减小传动过程中的变形 和振动。
可靠性设计
为确保自动化设备的可靠 性,对蜗轮蜗杆进行可靠 性设计和寿命预测。
THANKS
感谢观看
材料应具备较好的抗疲劳性能,以承受交 变载荷的作用;
04
材料应具有良好的工艺性能,易于加工制 造。
04
蜗轮蜗杆设计计算方法
蜗轮齿面载荷分布计算
总结词
根据蜗杆传动的实际工况,通过分析蜗轮齿面上的受力情况,计算出蜗轮齿面上的载荷分布。
详细描述
在进行蜗轮齿面载荷分布计算时,需要考虑蜗杆传动的实际工况,如传动比、转速、载荷大小和方向 等因素。通过分析蜗轮齿面上的受力情况,可以确定蜗轮齿面上的载荷分布,为后续的设计计算提供 基础。
蜗轮蜗杆设计计算
• 蜗轮蜗杆简介 • 蜗轮蜗杆设计参数 • 蜗轮蜗杆材料选择 • 蜗轮蜗杆设计计算方法 • 蜗轮蜗杆设计实例分析
01
蜗轮蜗杆简介
蜗轮蜗杆的定义
01
蜗轮蜗杆是一种常用的传动装置 ,由两个交错轴线、相互咬合的 齿轮组成,其中一个是蜗杆,另 一个是蜗轮。
02
蜗轮蜗杆具有传动比大、传动效 率高、传动平稳、噪音低等优点 ,因此在各种机械传动系统中得 到广泛应用。
VS
蜗轮蜗杆设计
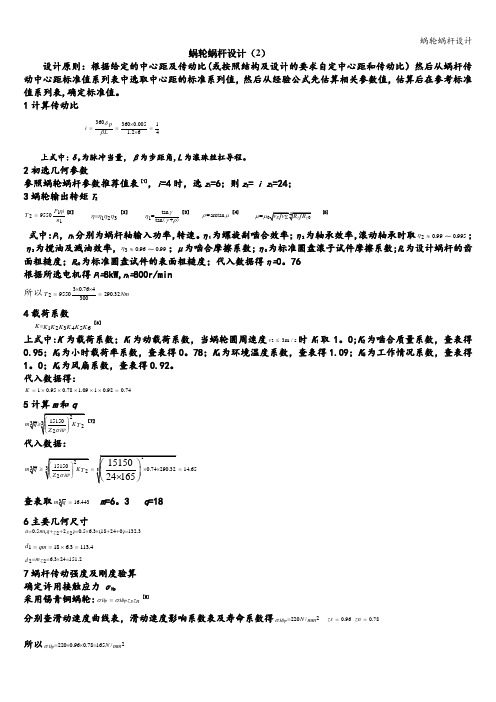
蜗轮蜗杆设计(2)设计原则:根据给定的中心距及传动比(或按照结构及设计的要求自定中心距和传动比)然后从蜗杆传动中心距标准值系列表中选取中心距的标准系列值,然后从经验公式先估算相关参数值,估算后在参考标准值系列表,确定标准值。
1计算传动比上式中:δp 为脉冲当量,β为步距角,L 为滚珠丝杠导程。
2初选几何参数参照蜗轮蜗杆参数推荐值表[1],i =4时,选z 1=6;则z 2= i z 1=24; 3蜗轮输出转矩T 21955021i P T n η=[2]123ηηηη=[3] tan =1tan +γηγρ()[3] =arctan ρμ[4]=μμ[5]式中:P 1, n 1分别为蜗杆轴输入功率,转速。
η1为螺旋副啮合效率;η2为轴承效率,滚动轴承时取0.990.9952η≈;η3为搅油及溅油效率,0.960.993η≈;μ为啮合摩擦系数;η0为标准圆盘滚子试件摩擦系数;R z 为设计蜗杆的齿面粗糙度;R z0为标准圆盘试件的表面粗糙度;代入数据得η=0。
76 根据所选电机得P 1=8kW,n 1=800r/min所以30.7649550290.322300T Nm ⨯⨯==4载荷系数123456K K K K K K K =[6]上式中:K 为载荷系数;K 1为动载荷系数,当蜗轮圆周速度23m /s v ≤时K 1取1。
0;K 2为啮合质量系数,查表得0.95;K 3为小时载荷率系数,查表得0。
78;K 4为环境温度系数,查表得1.09;K 5为工作情况系数,查表得1。
0;K 6为风扇系数,查表得0.92。
代入数据得:10.950.78 1.0910.920.74K =⨯⨯⨯⨯⨯=5计算m 和q7]代入数据:14.65≥==查表取16.443= m =6。
3 q =186主要几何尺寸18 6.3113.41d qm ==⨯= 6.324151.222m d z ==⨯=7蜗杆传动强度及刚度验算 确定许用接触应力σHp采用锡青铜蜗轮:Hp Hbp z z s n σσ=[8]分别查滑动速度曲线表,滑动速度影响系数表及寿命系数得2220/Hbp N mm σ= 0.96z s =0.78z n =所以22200.960.78165/Hp N mm σ=⨯⨯=3603600.00511.264p i L δβ⨯===⨯0.5(2)0.5 6.3(18240)132.322a m q x z =++=⨯⨯++=确定许用接触应力σHH σ=9]代入数据得:2134.57/H mm N σ=== 可见134.57165HHP σσ=<=,所以接触强度足够。
蜗轮蜗杆的设计计算
蜗轮蜗杆的设计计算圆周率π 3.141593 3.14159265 3.141593蜗杆的轴向模数mx 1433蜗杆的头数z1222轴向压力角αx1202020旋向右旋左旋左旋蜗轮的齿数z2202323蜗轮齿顶高系数ha〃111蜗轮的径向变位系数xn20.750.66670径向根隙系数c0.20.20.2啮合中心距A635959蜗杆的螺旋升角λ11.3111.3111.31蜗杆特性系数q9912蜗杆的分度圆直径d1362736蜗杆的齿顶高ha1433蜗杆的齿根高hf1 4.8 3.6 3.6蜗杆的外径da1443342蜗杆的根径df126.419.828.8蜗杆的轴向齿距px112.56649.424777969.42478蜗杆的牙部计算长度L’蜗杆牙部的选用长度L575859齿部轴向厚度sx1 6.283194.71238898 4.71239蜗杆的量棒计算直径dp’1 6.686435.01481961 5.01482蜗杆的量棒选用直径dp1785蜗杆的半径上跨棒距Me’123.101922.721626421.3359直径跨棒距(三针法)Me146.203745.443252942.6718法向压力角αn19.641619.641588919.6416蜗杆法向弧齿厚sn1 6.161174.62087648 4.62088蜗杆法向弦齿厚scn1 6.161174.62087648 4.62088蜗杆法向弦齿高hca1433蜗轮的端面模数mt2433蜗轮的分度圆直径d2806969齿顶高ha27 5.00013齿根高hf2 1.8 1.5999 3.6齿顶圆直径da29479.000275齿根圆直径df276.465.800261.8蜗轮外圆直径Dw210083.500279.5所取蜗轮外圆直径DW2′98蜗轮圆弧包角2γ808182标准中心距A’584852.5直际中心距A635959齿根圆弧面半径R122.817.121.6齿顶圆弧面半径R21410.515轮缘理论宽度B’228.282721.431785627.5545直际轮缘宽度B2323334蜗轮端面分度圆弧齿厚st28.467016.16834271 4.71239蜗轮法向分圆弧齿厚sn28.302586.04855624 4.62088蜗轮法向分圆弦齿厚scn28.287686.04080973 4.61742蜗轮法向分圆弦齿高hca27.215425.13265447 3.07736蜗轮法向固定弦齿厚Sgcn27.36455.36514843 4.09878蜗轮法向固定弦齿高hgca2 5.68584.04268364 2.26857蜗轮端面的基圆直径dbt275.175464.838790864.8388端面齿顶压力角αat236.894934.840849130.1724端面齿顶宽度se2 1.315781.28866817 2.13289外圆压力角39.90617外圆齿顶宽-1.86953。
蜗轮蜗杆参数计算公式
蜗轮蜗杆参数计算公式
蜗轮蜗杆是机械传动的一种经典机构,它的参数计算是传动设计中的重要工作。
本文针对蜗轮蜗杆机构,给出其参数计算公式,供大家参考使用。
关键词:蜗轮;蜗杆;参数计算
1.引言
蜗轮蜗杆机构是一种经典的传动机构,它由蜗杆和蜗轮组成,是机械传动中最常用的机构之一。
它具有传动精度高,传动比容易调节,适应宽范围,工作可靠,使用寿命长等优点,因此得到了广泛的应用。
2.蜗轮蜗杆参数计算
(1)计算内径:
内径rn=Mz/π
其中Mz为蜗杆节距。
(2)计算外径:
外径r0=Mz/π+2H
其中H为蜗杆的系数高度。
(3)计算周长:
周长s=2π[(Mz+2H)/π]
(4)计算节距:
节距Mz=zp[π(r0-rn)]
其中zp为蜗轮的齿数。
- 1 -。
蜗轮蜗杆的计算
蜗轮蜗杆的计算公司标准化编码 [QQX96QT-XQQB89Q8-NQQJ6Q8-MQM9N]蜗轮、蜗杆的计算公式:1,传动比=蜗轮齿数÷蜗杆头数2,中心距=(蜗轮节径+蜗杆节径)÷2 3,蜗轮吼径=(齿数+2)×模数 4,蜗轮节径=模数×齿数5,蜗杆节径=蜗杆外径-2×模数 6,蜗杆导程=π×模数×头数7,螺旋角(导程角)tg β=(模数×头数)÷蜗杆节径 一.基本参数:(1)模数m 和压力角α:在中间平面中,为保证蜗杆蜗轮传动的正确啮合,蜗杆的轴向模数m a1和压力角αa1应分别相等于蜗轮的法面模数m t2和压力角αt2,即 m a1=m t2=m αa1=αt2蜗杆轴向压力角与法向压力角的关系为: tgαa =tgαn /cosγ 式中:γ-导程角。
(2)蜗杆的分度圆直径d 1和直径系数q为了保证蜗杆与蜗轮的正确啮合,要用与蜗杆尺寸相同的蜗杆滚刀来加工蜗轮。
由于相同的模数,可以有许多不同的蜗杆直径,这样就造成要配备很多的蜗轮滚刀,以适应不同的蜗杆直径。
显然,这样很不经济。
为了减少蜗轮滚刀的个数和便于滚刀的标准化,就对每一标准的模数规定了一定数量的蜗杆分度圆直径d1,而把及分度圆直径和模数的比称为蜗杆直径系数q ,即: q=d1/m常用的标准模数m 和蜗杆分度圆直径d1及直径系数q ,见匹配表。
(3)蜗杆头数z 1和蜗轮齿数z 2蜗杆头数可根据要求的传动比和效率来选择,一般取z1=1-10,推荐 z1=1,2,4,6。
选择的原则是:当要求传动比较大,或要求传递大的转矩时,则z1取小值;要求传动自锁时取z1=1;要求具有高的传动效率,或高速传动时,则z1取较大值。
蜗轮齿数的多少,影响运转的平稳性,并受到两个限制:最少齿数应避免发生根切与干涉,理论上应使z2min≥17,但z2<26时,啮合区显着减小,影响平稳性,而在z2≥30时,则可始终保持有两对齿以上啮合,因之通常规定z2>28。
蜗轮蜗杆的计算
蜗轮、蜗杆的计算公式: 1,传动比=蜗轮齿数÷蜗杆头数 2,中心距=(蜗轮节径+蜗杆节径)÷2 3,蜗轮吼径=(齿数+2)×模数 4,蜗轮节径=模数×齿数 5,蜗杆节径=蜗杆外径-2×模数 6,蜗杆导程=π×模数×头数7,螺旋角(导程角)tg β=(模数×头数)÷蜗杆节径 一.基本参数:(1)模数m 和压力角α:在中间平面中,为保证蜗杆蜗轮传动的正确啮合,蜗杆的轴向模数m a1和压力角αa1应分别相等于蜗轮的法面模数m t2和压力角αt2,即 m a1=m t2=m αa1=αt2蜗杆轴向压力角与法向压力角的关系为: tgαa =tgαn /cosγ 式中:γ-导程角。
(2)蜗杆的分度圆直径d 1和直径系数q为了保证蜗杆与蜗轮的正确啮合,要用与蜗杆尺寸相同的蜗杆滚刀来加工蜗轮。
由于相同的模数,可以有许多不同的蜗杆直径,这样就造成要配备很多的蜗轮滚刀,以适应不同的蜗杆直径。
显然,这样很不经济。
为了减少蜗轮滚刀的个数和便于滚刀的标准化,就对每一标准的模数规定了一定数量的蜗杆分度圆直径d1,而把及分度圆直径和模数的比称为蜗杆直径系数q,即:q=d1/m常用的标准模数m和蜗杆分度圆直径d1及直径系数q,见匹配表。
(3)蜗杆头数z1和蜗轮齿数z2蜗杆头数可根据要求的传动比和效率来选择,一般取z1=1-10,推荐 z1=1,2,4,6。
选择的原则是:当要求传动比较大,或要求传递大的转矩时,则z1取小值;要求传动自锁时取z1=1;要求具有高的传动效率,或高速传动时,则z1取较大值。
蜗轮齿数的多少,影响运转的平稳性,并受到两个限制:最少齿数应避免发生根切与干涉,理论上应使z2min≥17,但z2<26时,啮合区显着减小,影响平稳性,而在z2≥30时,则可始终保持有两对齿以上啮合,因之通常规定z2>28。
另一方面z2也不能过多,当z2>80时(对于动力传动),蜗轮直径将增大过多,在结构上相应就须增大蜗杆两支承点间的跨距,影响蜗杆轴的刚度和啮合精度;对一定直径的蜗轮,如z2取得过多,模数m 就减小甚多,将影响轮齿的弯曲强度;故对于动力传动,常用的范围为z2≈28-70。
- 1、下载文档前请自行甄别文档内容的完整性,平台不提供额外的编辑、内容补充、找答案等附加服务。
- 2、"仅部分预览"的文档,不可在线预览部分如存在完整性等问题,可反馈申请退款(可完整预览的文档不适用该条件!)。
- 3、如文档侵犯您的权益,请联系客服反馈,我们会尽快为您处理(人工客服工作时间:9:00-18:30)。
蜗轮蜗杆的设计计算
1、根据GB/10085-1988推荐采用渐开线蜗杆(ZI )。
2、根据传动功率不大,速度中等,蜗杆45钢,因为希望效率高些,耐磨性好,故蜗杆螺旋 齿面要求淬火,硬度45-55HRC ,蜗轮用铸锡磷青铜ZCuSn10P1金属铸造,为节约贵重金的有色金属。
仅齿圈用青铜制造,而轮芯用灰铸铁HT100铸造。
3、按持卖你接触疲劳强度进行设计
a ≥32H 2])]
[(σP E z z KT (1)作用在蜗轮上的转矩2T
按1Z =2 ,η=0.8 2T =9.55⨯610⨯2p /2n =9.55⨯610⨯0.7⨯0.8/62=86258mm ⋅N
(2)确定载荷系数K ,取A K =1.15 βK =1 v K =1.05
所以得K= A K ⨯ βK ⨯v K =1.15⨯1⨯1.05=1.21
(3)确定弹性影响系数E Z =16021MPa (铸锡青铜蜗轮与钢蜗杆相配)
(4)确定接触系数p Z
假设a
d 1=0.35 从表11-18查得p Z =2.9 (5)确定接触应力[H σ]
根据材料ZCuSn10P1,蜗杆螺旋齿面硬度>45HRC ,从表11-7查得蜗轮许用应力
'][H σ=268MPa
N=60j 2n h L =60⨯1⨯62⨯46720=1.74⨯8
10
寿命系数HN K =8871074.110⨯=067则 [H σ] =HN K ⨯'][H σ=0.67⨯268=179.56MPa (6)计算中心距 a ≥32])56
.1799.2160(8625821.1⨯⨯⨯ =88.6 取a=100.因为i-15 故从表11-15中取模数m=5 1d =50mm 这时
a d 1=100
50=0.5 从图11-18,可查的接触系数'Z ρ=2.6<2.9,所以计算结果可用。
4、蜗杆蜗轮的主要参数
(1)蜗杆:轴向齿距Pa=15.7得直径系数q=10 齿顶园直径a1d =60,齿根圆f1d =38,分度圆导角r=11 18 36 ,蜗杆轴向齿厚Sa=5π/2=7.85mm
(2)蜗轮
齿数2Z =31 变位系数2x =-0.500 验算传动比i=2Z /1Z =31/2=15.5 误差为15
155.15-=3.33%,在允许范围内,所以可行。
蜗轮分度圆直径2d =m ⨯2Z =5⨯31=155mm
蜗轮喉圆直径a2d =2d +2a2h =155+2⨯5=165mm
蜗轮齿根圆直径f2d =2d +2f2h =155-2⨯1.2⨯5=143mm
蜗轮喉母圆半径g2r =a-a2d 21=100-1552
1⨯=22.5mm 5、校核齿根弯曲疲劳强度
F σ=m
d d KT 53.12122Fa Y βY ≤][F σ 当量齿数v2Z =
31.11cos 2
Z =31/ cos11.31= 32.88 根据2x =-0.5 v2Z =32.88从图11-19查得齿形系数2Fa Y =3.3 βY =1-r/140=1-11.31/140=0.9192
F σ=][F σFN K ,2从11-8查得ZCuSn10P1制造蜗轮时许用弯曲应力][F σ=56MPa 寿命系
数FN K =98
61074.110⨯=0.564 F σ=5
501558625821.153.1⨯⨯⨯⨯⨯3.3⨯0.9192=11.26MPa ,弯曲强度满足要求。
6、验算效率 η =(0.95~0.96)()
v tan tan ψγγ- 已知r=11.31 v ψ=arctan v f v f 与相对滑动系数s v 有关
s v =γπcos 100060n d 1
1⨯⨯=
31.11cos 100060961
50⨯⨯⨯⨯π=2.564m/s
从表11-18中用插值法查得v f =0.0204 v ψ=1.168代入η=0.86大于原来估计,因此不用从新计算。