冒口系统设计
《冒口系统设计》课件
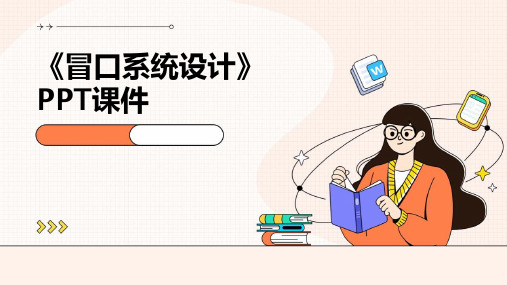
冒口系统是铸造工艺中的重要组成部分,其主要作用是容纳多余的金属液体。一个完整的冒口系统通 常包括冒口本身、溢流槽和保温材料等部分。冒口的设计应考虑金属液的容量、模具的冷却速度等因 素。溢流槽的作用是将多余的金属液引入冒口,保温材料则用于保持金属液的温度。
冒口系统的分类
要点一
总结词
根据用途和结构,冒口系统可分为热冒口和冷冒口两类。
压接焊
通过施加压力使两个金属表面紧密接触,然后加热熔化表面层, 形成连接。
钎焊
使用熔点低于母材的钎料作为填充金属,将母材加热至钎料熔化 ,然后冷却凝固形成连接。
热处理工艺
退火
将金属加热至高温并保持一段时 间,然后缓慢冷却至室温,以消 除内应力、提高塑性和韧性。
正火
将金属加热至高温并保持一段时 间,然后快速冷却至室温,以细 化晶粒、提高强度和韧性。
环保性原则要求在选择冒口材料时,要优先选择可再生、 可回收、低污染的材料,同时还要考虑到冒口系统的冷却 方式、废弃物的处理方式等因素,以实现绿色铸造的目标 。
03 冒口系统设计流程
需求分析
需求调研
深入了解用户需求,明确设计目标, 收集相关数据和信息。
需求整理
对收集到的需Байду номын сангаас进行分类、筛选和整 理,形成详细的需求文档。
方案制定
方案构思
根据需求分析结果,初步拟定设计方 案,包括功能模块、界面布局等。
方案评审
邀请专家或团队成员对方案进行评审 ,提出改进意见,完善设计方案。
详细设计
界面设计
根据方案制定界面风格、色彩搭配、图标和按钮 等视觉元素。
交互设计
确定各个功能模块的交互流程、操作方式和反馈 机制。
球墨铸铁浇冒口系统设计的关键 (一)

球磨铸铁浇冒口设计的关键第一部分浇流道系统设计1.0浇流道系统设计1.1要求快速浇铸:使充型过程中温度损失最小使冶金学性能衰减最小使氧化物最少清洁浇铸:避免浇铸过程中产生炉渣(浮渣)设计的经济性:使铸件产量最大化1.2关键组成:所示的所有组成部分要求炉渣缺陷最小化1.3规划考虑设计基本设计:优化对铸件的空间利用;冒口设计方法的选择;设置分型面以最小化对模芯的需求;铸件设置在上模中;平稳填充;简单对称的设计系统;同一铸件使用相同的浇冒口;可能的话,在多个铸件上使用一个冒口;在分型面上给浇冒口系统留下足够的空间;具体设计如下:1.4阻流阀的作用定义:阻流阀是浇道系统中一块横截面积,它决定充型时间有两个正确的位置设置阻流阀,因此有两个基本的浇道系统:在简单的浇注系统中,1)阻流阀位于流道和浇口的连接处。
2)阻流阀位于直浇道与横浇道的连接处。
1.5 选择浇流系统类型在浇口-横浇道系统中,铸件分别被一个或多个阻流阀或浇口阻挡。
在直浇道-横浇道系统中,很可能几个铸件共用一个阻流阀。
使用直浇道-横浇道系统在一个模具里生产大量小型件,这是不切实际的对每个铸件分别设置阻流阀(阻流阀尺寸非常小),极大的依赖于模具技术及浇注温度大部分情况下是使用浇口-横浇道系统浇口-横浇道系统与直浇道-横浇道系统特点的结合形成混合系统。
这通常用在要求运输铁水到复杂的铸件型腔的流道系统中。
1.6摩擦并非直浇道顶部所有铁水的潜能都可以转换为铸造型腔中的机械能随着铁水与型腔内壁的撞击和铁水之间的撞击,一些潜能损失在摩擦上由于摩擦造成的损失,延长了模型填充时间,必须考虑何时计算阻流阀截面积和浇铸时间。
选择fr,摩擦损失因子,作为能量损失的估计值对于薄壁平板:fr—0.2对于厚重立方体:fr---0.81.7浇铸时间尽可能快的符合人们的能力及生产例程推荐的浇注时间:非常近似的指导,铸件质量+冒口质量1.8阻流阀的横截面积对总的浇铸质量选择最快的实际浇铸时间(t,sec.)选择合适的fr值确定总的浇铸体积/阻气阀(V)V是所有铸件及冒口,特定阻流阀的下游之和体积=质量/密度液态铸铁,密度=0.25磅/立方英尺或0.007KG/cm3Determine effective ferrostatic head in sprue (H.)确定铸件在上模中的高度(b.)根据Torricelli,铁水在阻流阀的流速当铸件完全处在下模,当铸件完全位于上模,当铸件位于上模和下模中,可以从下面的图谱中,选择合适的Ac图谱数据基于平均上模高度(依铸造不同而变化)。
三维铸造工艺CAD冒口系统设计
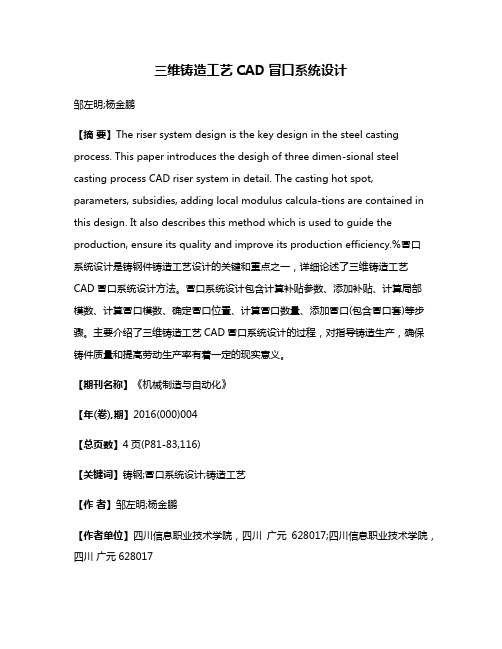
三维铸造工艺CAD冒口系统设计邹左明;杨金鹏【摘要】The riser system design is the key design in the steel casting process. This paper introduces the desigh of three dimen-sional steel casting process CAD riser system in detail. The casting hot spot, parameters, subsidies, adding local modulus calcula-tions are contained in this design. It also describes this method which is used to guide the production, ensure its quality and improve its production efficiency.%冒口系统设计是铸钢件铸造工艺设计的关键和重点之一,详细论述了三维铸造工艺CAD冒口系统设计方法。
冒口系统设计包含计算补贴参数、添加补贴、计算局部模数、计算冒口模数、确定冒口位置、计算冒口数量、添加冒口(包含冒口套)等步骤。
主要介绍了三维铸造工艺CAD冒口系统设计的过程,对指导铸造生产,确保铸件质量和提高劳动生产率有着一定的现实意义。
【期刊名称】《机械制造与自动化》【年(卷),期】2016(000)004【总页数】4页(P81-83,116)【关键词】铸钢;冒口系统设计;铸造工艺【作者】邹左明;杨金鹏【作者单位】四川信息职业技术学院,四川广元628017;四川信息职业技术学院,四川广元628017【正文语种】中文【中图分类】TG24铸造工艺CAD是提高铸造工艺水平、科学化管理铸造工艺图样的有效工具,它能使工艺人员从繁杂的手工劳动和大量的繁琐计算中彻底解放出来,不再需要描图员手工描图,直接用打印机打印透图。
冒口系统智能化设计》软件的开发与应用_图文(精)

《铸件浇冒口系统智能化设计》软件的开发与应用邵建东(无锡环宇精密铸造有限公司在熔模精密铸件的过程中,浇冒口系统设计得科学合理是确保铸件质量的一项核心技术。
浇冒口系统尺寸设计合理与否,将直接影响铸件内在质量的优劣。
尺寸偏小,影响顺序凝固及钢液补给能力,铸件会产生缩孔和疏松,特别是承压零件会产生泄露而报废;尺寸过大,会使企业导致铸造成本增加,能源大量浪费,使企业经济效益下降而失去竞争力。
因此科学合理的设计浇冒口系统,优化铸件内浇口及冒口尺寸,是制约我们每个铸造企业发展的一个重要因素,这个因素也客观反映了一个企业乃至一个国家对铸造工艺技术水平的高低。
特别是在当今铸造材料价格大幅度上涨的情况下,这个问题将尤为重要。
那么如何来提高浇冒口的设计水平,确保企业在激烈竞争的市场经济中占领先地位,使企业立于不败之地呢?针对这个问题,本公司科技人员潜心研究,反复探讨,实践、论证,向传统的铸造浇冒口设计方法挑战,攻克了一个又一个的技术难关,使铸造理论知识与多年来的实践经验,科学地、有机地结合在一起,直至2004年3月份成功开发了《铸件浇冒口系统智能化设计》软件,经过近几年来的应用实践,取得了十分显著的效果,越来越感觉到科学技术的能量和威力。
该软件的特点和作用如下:一.特点:1.改变传统方法,创新铸件浇冒口设计:在铸件浇冒口系统设计过程中,最常用的方法是热节圆比例法,这种方法也是最传统最简单的方法(俗称经验估计法。
这种方法的出发点是以铸件上热节圆截面或直径作为确定内浇口截面尺寸大小的主要依据,如:设计铸件热节圆直径为D节,内浇口直径为d 则:d=K×D节(式中K为比例系数,取值为0.4—0.9. 这种方法对于<1kg以下的小铸件以及铸件几何形状相对比较简单的零件相对成功率较高,但对单件十几公斤,几十公斤或是上百公斤的大铸件,以及形状复杂有交叉壁厚的铸件而言,用这种传统的方法设计浇冒口,则成功率很低。
另外,这种热节圆比例法只能用于铸件内浇口尺寸的确定,对冒口的截面尺寸只能用经验估计方法来完成,然而经验丰富的科技人员成功率相对高一些,反之则低一些。
铝合金砂型铸造案例分析- 浇冒口系统设计

横浇道尺寸 内浇口尺寸
使用以上信息,我们就可以建议一模4件的 初始工艺设计方案。
为什么没有加次冒口2、3?
在初始设计中,我们将验证从主冒口浇注 产生的温度分布变化能否使所有的凝固顺 序都指向主冒口,而不用加次冒口。如果
不行的,再添加冒口或冷铁等。
接下来,对初始设计工艺进行模拟。使用 FLOWCast™模拟充型过程,使用
及最大出品率的冒口尺寸。
联系方式 天津富宇创想科技有限公司
公司网站:
冒口冒口2推荐直径推荐直径15英寸英寸x高高3英寸英寸冒口冒口3尺寸相同直径尺寸相同直径15英寸英寸x高高3英寸英寸接下来使用浇注系统设计向导接下来使用浇注系统设计向导gatingdesignwizard?确定最优浇注时间确定最优浇注时间直浇道横浇道及内浇口尺寸直浇道横浇道及内浇口尺寸最优浇注时间最优浇注时间直浇道形状直浇道形状浇口位置浇口位置浇注系统截面比浇注系统截面比直浇道直径直浇道直径横浇道尺寸横浇道尺寸内浇口尺寸内浇口尺寸使用以上信息我们就可以建议一模使用以上信息我们就可以建议一模4件的初始工艺设计方案
行分析,得到铸件模数*。根据模数就可以
知道铸件每部分的凝固顺序,并用来确定冒 口或浇口放置的最佳位置及给出冒口尺寸。
*注: 传统的模数定义为——体积:表面积,SOLIDCast使用的是热 模数,这比传统的方法要准确的多。
铸件上的模数分布
冒口设计向导(Riser Design Wizard)通 过分析铸件上的模数分布,给出推荐的冒
铸件上的缩松(弥散的缩松)分布
X-Ray View
结论
使用浇注系统设计向导和冒口设计向导, 我们可以很快的设计出铸件工艺方案。使 用FLOWCast和SOLIDCast可以快速验证
冒口系统设计

冒口系统设计一﹑冒口设计1. 冒口设计的基本原则1)冒口的凝固时间应大于或等于铸件(被补缩部分)的凝固时间。
2)冒口应有足够大的体积,以保证有足够的金属液补充铸件的液态收缩和凝固收缩,补缩浇注后型腔扩大的体积。
3)在铸件整个凝固的过程中,冒口与被补缩部位之间的补缩通道应该畅通,即使扩张角始终向着冒口。
对于结晶温度间隔较宽、易于产生分散性缩松的合金铸件,还需要注意将冒口与浇注系统、冷铁、工艺补贴等配合使用,使铸件在较大的温度梯度下,自远离冒口的末端区逐渐向着冒口方向实现明显的顺序凝固2. 冒口设计的基本内容1)冒口的种类和形状(1)冒口的种类⎧⎧⎧⎪⎪⎪⎨⎪⎪⎪⎪⎪⎨⎩⎪⎪⎪⎧⎪⎪⎨⎪⎪⎩⎩⎪⎧⎧⎪⎪⎪⎪⎨⎪⎪⎪⎪⎪⎨⎩⎪⎪⎪⎧⎪⎪⎪⎪⎪⎪⎪⎨⎨⎪⎪⎪⎪⎪⎪⎩⎪⎪⎪⎪⎪⎪⎪⎪⎪⎪⎪⎩⎩顶冒口依位置分侧冒口贴边冒口普通冒口明冒口依顶部覆盖分暗冒口大气压力冒口依加压方式分压缩空气冒口通用冒口(传统)发气压力冒口保温冒口发热冒口特种冒口依加热方式分加氧冒口电弧加热冒口,煤气加热冒口易割冒口直接实用冒口(浇注系统当铸铁件的实用冒口(均衡凝固)⎧⎪⎪⎪⎪⎪⎪⎪⎪⎪⎪⎪⎪⎪⎪⎨⎪⎪⎪⎪⎪⎪⎪⎪⎪⎪⎪⎧⎪⎪⎨⎪⎪⎪⎩⎩冒口)控制压力冒口冒口无补缩 图1 冒口分类(2)冒口的形状常用的冒口有球形、圆柱形、长方体形、腰圆柱形等。
对于具体铸件,冒口形状的选择主要应考虑以下几方面:a)球形 b)球顶圆柱形 c)圆柱形 d)腰圆柱形(明) e)腰圆柱形(暗)图2 常用的冒口形状①冒口的补缩效果: 冒口的形状不同,补缩效果也不同,常用冒口模数(M)的大小来评定冒口的补缩效果(M=冒口体积/冒口散热面积),在冒口体积相同的情况下,球形冒口的散热面积最小,模数最大,凝固时间最长,补缩效果最好,其它形状冒口的补缩效果,依次为圆柱形,长方体形等。
②铸件被补缩部位的结构情祝: 冒口形状的选泽还要考虑铸件被补缩部位的结构形状和造型工艺是否方便。
铸造工艺学冒口设计方案

保温作用:冒口可 以减缓铸件凝固速 度,提高铸件质量
冒口的设计原则
保证补缩量:根据铸件的结 构、尺寸、壁厚等确定冒口 的补缩量
便于操作:冒口的位置应便 于操作,以便于浇注和清理
减少金属消耗:在保证补缩 量的前提下,尽量减少冒口 的金属消耗
避免形成热节:冒口的设计 应避免形成热节,以防止铸 件产生缩孔和缩松等缺陷
计算法
冒口体积计算 冒口直径计算 冒口高度计算 冒口材料选择
实验法
实验目的:确定最 佳冒口尺寸和位置
实验步骤:设计多 种方案,进行实际 铸造实验
实验结果:观察铸 件质量,分析实验 数据
结论:根据实验结 果,确定最佳冒口 设计方案
05 冒口的设计优化
减小冒口体积
优化冒口结构: 采用合理的冒 口结构,如分 片式、组合式 等,以减
冒口的设计原则: 根据铸件的结构、 尺寸、材质等因 素进行设计
冒口的设计方法: 根据铸造工艺学 原理,采用合适 的冒口尺寸、形 状和位置
冒口设计的实际 应用:在铸铁件 生产中,根据实 际情况选择合适 的冒口设计方案, 提高铸件质量和 生产效率
铝合金铸件的冒口设计
口体积
降低冒口高度: 通过减小冒口 高度,减少冒 口体积,同时 保证补缩效果
减小冒口直径: 采用较小的冒 口直径,以减 小冒口体积, 同时保证补缩
效果
改进冒口材料: 采用轻质、高 强度、低热膨 胀系数的材料 制作冒口,以 减小冒口体积
提高冒口补缩效率
确定冒口的位置和数量 选择合适的冒口类型 优化冒口尺寸和形状 控制冒口补缩时间
铸造工艺学冒口设计 方案
,a click to unlimited possibilities
汇报人:
铸造工艺学冒口设计方案

铸造工艺学冒口设计方案引言铸造作为一种重要的制造工艺,在工业领域中得到广泛应用。
冒口设计是决定铸件质量的关键要素之一。
合理的冒口设计可以提高铸件的质量,减少缺陷率,提高生产效率。
本文将介绍铸造工艺学中的冒口设计方案。
冒口设计的基本原则冒口设计的基本原则是确保铸液顺利进入铸型腔体,并使气体和杂质得以排出,同时避免冒口产生不良缺陷。
以下是冒口设计的基本原则:1.冒口应位于铸件最后凝固的部位,以避免冒口残留在最终铸件中。
2.冒口位置应选择在铸件上部,以利于铸液的顺利流入铸型腔体。
3.冒口的形状应考虑冷却过程中的热传递和凝固规律,以避免冷挤缩并保证铸件的凝固完整性。
4.冒口尺寸应根据铸件的大小和冷却速率进行合理的选择。
冒口设计的步骤进行冒口设计时,需要按照以下步骤进行:1.确定铸件的凝固模式:根据铸件的形状和材料特性,确定铸件的凝固模式,例如自上而下凝固、自下而上凝固等。
2.确定冒口位置:根据铸件的凝固模式和形状,选择冒口位置,使冒口尽量位于铸件的上部,以利于铸液的顺利流入铸型腔体。
3.确定冒口形状:根据铸件的形状和凝固规律,选择合适的冒口形状,例如斗形冒口、圆形冒口等。
4.确定冒口尺寸:根据铸件的大小和冷却速率,选择合理的冒口尺寸,以确保铸液足够流动,并使冷却过程中的缩孔最小化。
冒口设计的优化方法为了进一步提高冒口设计的准确性和效果,可以采用以下优化方法:1.模拟计算:利用铸造工艺学软件进行模拟计算,通过模拟铸造过程,预测冒口设计的效果,以减少试验次数和成本。
2.经验参数法:根据类似铸件的经验参数,选择合适的冒口尺寸和形状。
3.图形化分析法:通过绘制铸件的凝固曲线和冷却曲线,分析冒口设计的合理性,并进行必要的调整和优化。
结论冒口设计是铸造工艺学中的重要环节,对铸件的质量和生产效率具有直接的影响。
合理的冒口设计可以提高铸件的质量,减少缺陷率。
在冒口设计过程中,需要根据铸件的凝固模式、形状和材料特性,选择合适的冒口位置、形状和尺寸。
- 1、下载文档前请自行甄别文档内容的完整性,平台不提供额外的编辑、内容补充、找答案等附加服务。
- 2、"仅部分预览"的文档,不可在线预览部分如存在完整性等问题,可反馈申请退款(可完整预览的文档不适用该条件!)。
- 3、如文档侵犯您的权益,请联系客服反馈,我们会尽快为您处理(人工客服工作时间:9:00-18:30)。
冒口系统设计一﹑冒口设计1. 冒口设计的基本原则1)冒口的凝固时间应大于或等于铸件(被补缩部分)的凝固时间。
2)冒口应有足够大的体积,以保证有足够的金属液补充铸件的液态收缩和凝固收缩,补缩浇注后型腔扩大的体积。
3)在铸件整个凝固的过程中,冒口与被补缩部位之间的补缩通道应该畅通,即使扩张角始终向着冒口。
对于结晶温度间隔较宽、易于产生分散性缩松的合金铸件,还需要注意将冒口与浇注系统、冷铁、工艺补贴等配合使用,使铸件在较大的温度梯度下,自远离冒口的末端区逐渐向着冒口方向实现明显的顺序凝固2. 冒口设计的基本内容1)冒口的种类和形状(1)冒口的种类⎧⎧⎧⎪⎪⎪⎨⎪⎪⎪⎪⎪⎨⎩⎪⎪⎪⎧⎪⎪⎨⎪⎪⎩⎩⎪⎧⎧⎪⎪⎪⎪⎨⎪⎪⎪⎪⎪⎨⎩⎪⎪⎪⎧⎪⎪⎪⎪⎪⎪⎪⎨⎨⎪⎪⎪⎪⎪⎪⎩⎪⎪⎪⎪⎪⎪⎪⎪⎪⎪⎪⎩⎩顶冒口依位置分侧冒口贴边冒口普通冒口明冒口依顶部覆盖分暗冒口大气压力冒口依加压方式分压缩空气冒口通用冒口(传统)发气压力冒口保温冒口发热冒口特种冒口依加热方式分加氧冒口电弧加热冒口,煤气加热冒口易割冒口直接实用冒口(浇注系统当铸铁件的实用冒口(均衡凝固)⎧⎪⎪⎪⎪⎪⎪⎪⎪⎪⎪⎪⎪⎪⎪⎨⎪⎪⎪⎪⎪⎪⎪⎪⎪⎪⎪⎧⎪⎪⎨⎪⎪⎪⎩⎩冒口)控制压力冒口冒口无补缩 图1 冒口分类(2)冒口的形状常用的冒口有球形、圆柱形、长方体形、腰圆柱形等。
对于具体铸件,冒口形状的选择主要应考虑以下几方面:a)球形 b)球顶圆柱形 c)圆柱形 d)腰圆柱形(明) e)腰圆柱形(暗)图2 常用的冒口形状①冒口的补缩效果: 冒口的形状不同,补缩效果也不同,常用冒口模数(M)的大小来评定冒口的补缩效果(M=冒口体积/冒口散热面积),在冒口体积相同的情况下,球形冒口的散热面积最小,模数最大,凝固时间最长,补缩效果最好,其它形状冒口的补缩效果,依次为圆柱形,长方体形等。
②铸件被补缩部位的结构情祝: 冒口形状的选泽还要考虑铸件被补缩部位的结构形状和造型工艺是否方便。
球形冒口的补缩效果虽好,但是造型起模困难,在铝、镁合金铸造生产中较少采用,而应用最广泛的是圆柱形明冒口,这种冒口的补缩效果较好,造型起模方便。
有时由于铸件结构形状的需要,亦采用长方柱体和扇形冒口,只是将其四棱的尖角改为较大的圆角,以防止边角效应影响补缩效果。
经改进后的这些冒口就称为椭圆柱体冒口和腰形,冒口。
在铸钢件生产中则经常使用球顶圆柱形暗冒口。
2.冒口的补缩原理1)冒口与铸件间的补缩通道在铸件凝固过程中,要使冒口中的金属液能够不断地补偿铸件的体收缩,冒口与铸件被补缩部位之间应始终保持着畅通的补缩通道。
否则,冒口再大也起不到补缩作用。
2)冒口的有效补缩距离冒口作用区长度和末端区长度之和称为冒口有效补缩距离。
正确确定冒口的有效补缩距离是很重要的工艺间题。
冒口的有效补缩距离与合金种类、铸件结构、几何形状以及铸件凝固方向上的温度梯度有关,也和凝固时析出气体的反压力及冒口的补缩压力有关。
详见《铸造工艺学》p255~257 3)工艺补贴的应用在实际生产中往往有些铸件需补缩的高度超过冒口的有效补缩距离。
由于铸件结构或铸造工艺上不便,难以在中部设置暗冒口,此时单靠增加冒口直径和高度,补缩效果很不明显,况且增大冒口会使大量液流经过内浇道,使铸件在内浇道附近和冒口根部因过热而产生疏松。
在这种情况下,一般采用在铸件壁板的一侧增加工艺补贻的方法,来增加冒口的有效补缩距离,提高冒口的补缩效率(如下图)图3 铸件补贴工艺示意图3. 冒口位置的确定冒口位置的选择对获得优质铸件有着重要的意义。
冒口位置选择不当,不仅不能消除铸件的缩孔和疏松,反而会使铸件产生裂纹,加重冒口附近的疏松,还会给清理、切割等工序带来不便。
1)、冒口位置选择的原则:(1)冒口应就近设在铸件热节的上方或侧旁。
(2)冒口应尽量设在铸件最高、最后的部位。
(3)冒口不应设在铸件重要的、受力大的部位,以防止组织粗大降低强度。
(4)冒口位置不要选在铸造应力集中处,应注意减轻对铸件的收缩阻碍,以免引起裂纹。
(5) 尽量用一个冒口同时补缩几个热节或铸件。
(6)冒口布置在加工面上,可节约铸件精整工时,零件外观好。
(7)不同高度上的冒口,应用冷铁使各个冒口的补缩范围隔开。
2)、冒口数量的确定关于冒口数量,一般是按照冒口有效补缩距离、冒口延续度和工艺出品率进行确定与校核的。
合理施放冷铁,延长有效补缩距离,可以减少冒口个数。
4. 冒口尺寸的确定合理地确定冒口尺寸,在铸造生产中是一个很重要的工艺问题。
目前还缺少一种适合各种合金、各种结构铸件、被大家所公认的确定冒口尺寸的办法,往往都采用在特定条件下根据生产经验总结出来的近似计算法。
因此在应用这些方法时,要注意结合生产的具体情况,才能得到较好的结果。
具体将在后面冒口设计的常用方法中详细说明。
5、评定冒口补缩作用的方法冒口尺寸确定得是否可靠、合理,冒口是否发挥了有效补缩作用、应通过生产实践的检验,其检验或评定的方法主要有以下4种1) 比较铸件实收率铸件实收率又称工艺出品率,常用下式表示a=GcGc+Gr+Gg×100% (1)式中: a——铸件实收率,(%)Gc,Gr,Gg分别为铸件﹑冒口和浇注系统的重量,(kg)将按上式计算的结果与根据生产经验所规定的同类铸件的实收率相比较,若小于经验数据,则说明冒日尺寸过大,应予以适当减小(一般是减小冒口高度)。
反之,如果大于本厂的经验数据,则冒口尺寸可能偏小,应适当加大冒口尺寸或采取其它工艺措施提高冒口的补缩效率。
2) 实际检验铸件质量: 按照有关标准和验收技术文件规定的项目来检验铸件质量,如通过X光透视检查铸件是否有与冒口设计有关的缩孔和缩松缺陷,此种方法对结晶温度范围较窄,易产生集中缩孔的合金铸件比较有利。
3) 检验冒口的缩孔深度4) 测定冒口凝固时间变化率后两种详见《铸造工艺学》p264~2656.提高冒口补缩效率的方法在铸造生产中,冒口的重量约为铸件重量的50%~100%,在铝合金和镁合金砂型铸造中有的冒口重量甚至是铸件重量的二倍以上,铸件实收率很低,冒口的补缩效率不高、去除冒口的劳动量大。
因此,采取措施努力提高冒口的补缩效率,对于节约能量、劳力和降低铸件生产成本具有重要意义。
要提高冒口的补缩效率,最有效的途径是增加冒口的补缩压力和廷长冒口的凝固时间,在工艺上经常采用的措施有:1)大气压力冒口2)保温冒口3)发热冒口4)易割冒口以上措施详细参考《铸造工艺学》p265~p2693.冒口设计的常用方法常用冒口设计方法有以下六种:1)模数法——广泛应用于铸钢件冒口设计中,也适用于铸铁件,非铁合金铸件的冒口设计。
2)周界商法——基于模数理论的铸钢件冒口设计方法。
3)收缩模数法——用于灰铸铁件和球墨铸铁件冒口设计。
4)热节圆法——种经验性方法,以热节圆和补缩液量为依据,适用于各种类型的中﹑小铸钢件冒口设计,也用于铸铁件冒口设计。
5)K值法——它是模数法中比较实用的方法之一,用于铸钢件,铸铁件等铸件冒口设计。
6)比例法——确定冒口尺寸最常用的方法,尤其是在铝、镁合金铸件的生产中得到广泛的应用。
二.冷铁的设计为增加铸件局部冷却速度,在型腔内部及工作表面安放的激冷物称作冷铁.铸造生产中常将冷铁、浇注系统和冒口配合使用,控制铸件的凝固过程,以获得合格铸件。
在此只是简单的介绍。
1.冷铁的分类1)内冷铁将金属激冷物插入铸件型腔中需要激冷的部位,使合金激冷并同铸件熔为一体,这种金属激冷物称为内冷铁,内冷铁主要用于黑色金属厚大铸样。
2)外冷铁外冷铁又分为直接外冷铁和间接外冷铁两类。
(1)直接外冷铁是只与铸件的部分内外表面接触而不熔接在一起的金属激冷物,实际上它成为铸型或型芯的部分型腔表面。
(2)间接外冷铁同被激冷铸件之间有10~15mm厚的砂层相隔,故又称隔砂冷铁、暗冷铁.间接外冷铁激冷作用弱,应用较少。
2.冷铁的作用1)与浇注系统和冒口配合控制铸件的凝固次序。
2)加速铸件的凝固速度,细化晶粒组织,提高铸件的力学性能。
3.冷铁材料的选择可以制作冷铁的材料很多,凡是比砂型材料的热导率、蓄热系数大的金属和非金属材料均可选用。
生产中常用的冷铁材料有铸铁、铝合金、石墨和铜合金等,各种冷铁材料的热物理系数见下表1表1 各种冷铁材料的热物理性能4. 冷铁的设计冷铁的设计是铸造工艺设计的一个重要组成部分,它对获得合格、优质铸件起着很大的作用。
设计冷铁的主要内容是确定冷铁放置的位置,冷铁的形状和尺寸。
1)冷铁安放位置的确定冷铁能否充分发挥作用,关键在于安放的位置是否合理。
确定冷铁在铸型中的位置,主要取决于要求冷铁所起的作用以及铸件的结构、形状,同时还需要考虑冒口和浇注系统的位置。
(1)要求冷铁所起作用的分析:对需要自下而上顺序凝固的铸件,一般将冷铁放在铸型的下部。
对于铸件上的某些局部热节,为使其早凝固或整个铸件同时凝固,冷铁自然应放于热节部位,或热节附近。
结晶温度间隔宽的合金,常在转角处产生热裂和缩松,若在转角处设里冷铁,对防止热裂有明显的作用。
(2)铸件结构的分析:在不宜安放冒口的厚大部位一般均应放冷铁,靠近内浇道处,或被金属液所包围的型芯部位,散热条件很差,也应该放冷铁.壁厚较大的镁合金平板类铸件,水平浇注时,由于水平面积较大,易于燃烧,在铸件底部放冷铁,可以减少铸件的燃烧缺陷。
但对于薄壁平板件,则尽量少用或不用冷铁,即使非用不可时,也不应在大面积上使用冷铁,避免铸件产生浇不到缺陷。
(3)与冒口配合使用由于冷铁没有补缩作用,铸件和热节的补缩仍由冒口供给,所以冷铁位置的确定应和冒口的位置同时考虑。
冷铁位置应与冒口有一定的距离,使铸件凝固时沿着从安放冷铁部位向冒口方向顺序凝固,有人称冷铁与冒口之间的距离为冷铁的作用距离.冷铁作用距离与冷铁材料的热物理性能、铸件的合金种类及壁厚尺寸有关。
合金结晶温度间隔越宽,铸件壁厚越小,铸件技术要求越高,冷铁与冒口之间距离应相应缩小。
(4)浇注系统及引入位置的影响:选择冷铁安放位置时,还要考虑浇注系统及引入位置对铸件温度分布和冷铁作用的影响。
采用底注式浇注系统时,一般均在铸件底部放置冷铁。
采用缝隙式浇注系统时,除在铸件底部放冷铁外,还应在远离缝隙处(两个立缝之间)放置冷铁,增大立筒的横向补缩作用。
2) 冷铁形状的确定冷铁的形状取决于使用冷铁部位铸件的形状和冷铁所应起的作用.常用冷铁分为成型冷铁和平面冷铁两类,其形状如图三所示。
在铸件理论型面及转角处一般使角成型冷铁,冷铁的形状应与放置冷铁的铸件形状相符合。
在铸件底部、端部和平面部分,常放置平面冷铁。
实际生产中常使用长方形、圆形、方形的冷铁。
其厚度一般为10.12,15,20,30mm。
也常制出一批长、宽尺寸不同、直径不同的标准冷铁供生产中选用。
这样有利于管理、有利于缩短试制和全产周期。