3C产品生产工艺控制程序
CCC认证产品质量计划控制程序

CCC认证产品质量计划控制程序1、目的确保CCC认证产品的质量计划以及为确保产品质量的相关过程有效运作和控制需要的文件。
2、适用范围适用于CCC认证产品设计目标、实现过程、检测及有关资源的规定,以及产品获证后对获证产品的变更(标准、工艺、关键件)、标志的使用管理等的规定(以下简称“质量计划”)。
3、定义无4、职责4.1开发部、工程部组织编制CCC认证产品质量计划;4.2开发部、工程部负责人负责审核CCC认证产品质量计划;4.3管理者代表或质量负责人负责批准CCC认证产品质量计划;4.4其它各相关部门负责CCC认证产品质量计划的实施。
5、工作程序5.1编制CCC认证产品质量计划时机:a. 根据《强制性产品认证工厂质量保证能力要求》的质量保证能力不能满足型式试验认证产品相一致时。
b. 现行产品或过程有显著变化,现行体系不足以保证质量活动受到控制时。
c. 顾客要求时。
d. 认证产品与获证产品的标准、工艺、关键零部件的变更时。
5.2 开发部、工程部根据特定产品或过程的质量要求,参照现行质量保证能力要求组织相关部门编制质量计划。
5.3质量计划由开发部、工程部负责人审核,管理者代表或质量负责人批准,当产品获证后对获证产品的变更(标准、工艺、关键零部件等)时,质量计划应提交评审。
5.4根据实际情况,可编写总体质量计划,也可以只编写有关的单项计划,如产品设计目标质量计划、获证产品变更的质量计划。
5.5 产品设计标准或规范应是质量计划的一个内容,其要求应不低于有关该产品的国家标准要求。
5.5质量计划应参照《强制性产品认证工厂质量保证能力要求》相关程序文件及质量手册的有关内容,应符合设计目标、实现过程、检测及有关资源的规定,并与质量管理体系文件中的内容协调一致。
质量计划一般包括但不限于以下内容:a. 目的、适用范围;b. 引用文件、定义;c. 质量目标;d. 资源配置;e. 实施步骤;f. 职责、权限;g. 活动顺序和内容。
玩具CCC程序文件之 设备管理控制程序
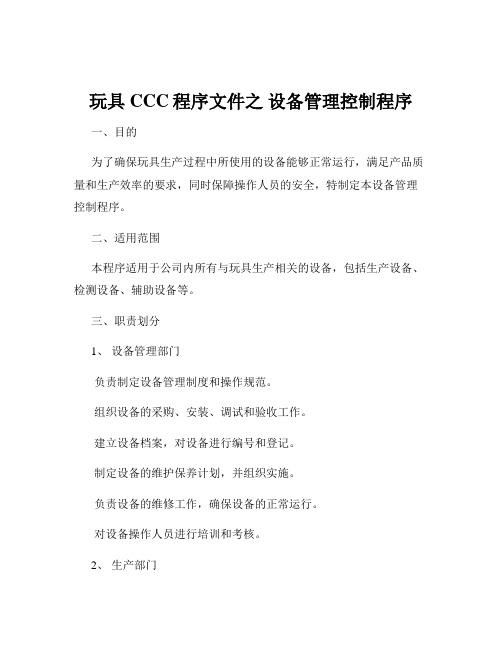
玩具CCC程序文件之设备管理控制程序一、目的为了确保玩具生产过程中所使用的设备能够正常运行,满足产品质量和生产效率的要求,同时保障操作人员的安全,特制定本设备管理控制程序。
二、适用范围本程序适用于公司内所有与玩具生产相关的设备,包括生产设备、检测设备、辅助设备等。
三、职责划分1、设备管理部门负责制定设备管理制度和操作规范。
组织设备的采购、安装、调试和验收工作。
建立设备档案,对设备进行编号和登记。
制定设备的维护保养计划,并组织实施。
负责设备的维修工作,确保设备的正常运行。
对设备操作人员进行培训和考核。
2、生产部门负责设备的日常使用和清洁工作。
按照操作规程正确操作设备,严禁违规操作。
发现设备故障及时报告设备管理部门。
3、质量检测部门负责对检测设备进行定期校准和检定,确保检测数据的准确性。
对设备的运行状况进行监督,发现问题及时通知设备管理部门。
四、设备采购1、设备需求部门根据生产工艺和生产任务的要求,提出设备采购申请,填写《设备采购申请表》,注明设备的名称、型号、规格、技术参数、数量等信息。
2、设备管理部门对采购申请进行审核,结合公司的发展规划和现有设备状况,确定采购的必要性和可行性。
3、采购部门根据审核通过的采购申请,进行市场调研,选择合适的设备供应商,并与其签订采购合同。
4、新设备到货后,设备管理部门组织相关人员进行开箱验收,检查设备的外观、附件、随机技术资料等是否齐全,设备的型号、规格、技术参数等是否符合采购要求。
5、设备安装调试完成后,由设备管理部门组织生产部门、质量检测部门等相关部门进行验收,验收合格后填写《设备验收报告》,设备方可投入使用。
五、设备档案管理1、设备管理部门为每台设备建立档案,档案内容包括设备的采购合同、随机技术资料、验收报告、使用说明书、维护保养记录、维修记录等。
2、设备档案应分类存放,便于查阅和管理。
3、设备档案应定期进行整理和更新,确保档案内容的完整性和准确性。
六、设备标识1、对每台设备进行编号,编号应具有唯一性,便于识别和管理。
3C认证生产工艺流程图

电工用铜线坯
S 原材料试验拉丝 + 退火S Nhomakorabea●
束丝
S
△
S
绝缘挤出
●
R
火花试验
入库
成品包装
出厂检验 R
打印标识 S
备注:“△”表示该工序为质量控制点 “●”表示该工序为关键工序
“S”表示抽样检验
“R”表示例行试验
执行标准:JB/T 8734.4—1998
生产工艺流程图
铜芯聚氯乙烯绝缘绞型安装用软电线
型号: AVRS
“S”表示抽样检验
“R”表示例行试验
执行标准:JB/T 8734.4—1998
生产工艺流程图
铜芯聚氯乙烯绝缘聚氯乙烯护套安装用的软电缆
型号: AVVR
规格:0.12~0.4 mm2
电压:300/300 V
编 号:LS — JS — 02 页 码:第 16 页 共 17 页 执行日期:2009 年 12 月 1 日
型号: RVS
规格:0.5~0.75 mm2
电压:300/300 V
编 号:LS — JS — 02 页 码:第 13 页 共 17 页 执行日期:2009 年 12 月 1 日
电工用铜线坯
S S 原材料检验
拉丝 + 退火
●
束丝
S
△
S
绝缘挤出
●
火花试验 R
S
入库
成品包装
出厂检验 R
对绞 S
打印标识 对绞 S
电工用铜线坯
拉丝+连续退火
绞线
S
●
S
S 原材料检验
入库
成品包装
出厂检验 R
绝缘挤出
ISO9001:2015+3C生产管理控制程序

编制审核批准日期日期日期文件使用部门部门签收部门签收总经办财务部采购生产部品质部研发部仓库人力资源部销售部文件修订记录日期修改类型版本修改原因修改内容修改人批准人1.0 目的:为满足顾客需求,确保产品质量与生产服务在生产全过程中得到有效控制。
2.0范围:本程序适用于生产制造全过程管控。
3.0 职责:3.1研发部负责提供生产技术资料以及生产制程中技术支持;3.2品质部负责来料,制程,出货质量的管控及文件的管理;3.3 采购负责采购计划及物料交期跟进;3.4供应链部负责物料计划的实施,生产物料齐套跟进,物料的发放工作;3.5生产部负责生产计划执行及过程控制。
4.0 定义:(略)5.0 程序:5.1 生产计划制定:5.1.1 销售部依销售订单,将批准生效后的《生产任务单》提供给供应链部;5.1.2 供应链部依据《生产任务单》,参照库存情况,原材料到料情况及产能负荷情况制订《生产计划单》,经相关领导签字审核后,下发给相关部门;5.1.3 供应链部依据《生产任务单》进行生产物料需求核算,并对物料使用状况进行预测,对库存进行核查。
并依据采购周期,物料检验周期完成《物料申购单》;5.1.4 采购部依据《物料申购单》,依据《采购控制程序》进行物料采购,并对物料进度进行控制。
当所采购物料不能预期到料时,应及时通知供应链计划,由计划对生产进行调整或协调相关资源;5.2 生产计划控制:5.2.1 计划员将《生产计划单》交由生产后,由车间领料员开具领料单,物料交接手续必须在仓管,品管及车间领料员在场时完成;5.2.2 生产部依据研发提供的技术要求,对人力,物料和设备等资源进行合理配置,确保生产顺利进行并满足业务交期要求;5.2.3 品质部依据检验规范,控制来料,制程,成品出货的质量及要求,及时发现并反馈不良等异常情况,并督促相关部门及时处理,改善;5.2.4生产部依据每日生产情况,由生产统计员填写《生产日报表》,计划员依据生产进度表,统计生产计划达成情况,并合理调整生产计划,满足交期需求;5.2.5 如因人员,物料及设备等异常原因,导致生产计划不能按期完成,生产部需积极协调并尽快解决相关问题,同时应及时通知供应链。
3C产品设计控制程序

3C产品设计控制程序1.目的控制产品设计开发和设计验证的过程,规定产品设计开发和设计验证的职责,保证设计开发出的产品满足市场需求及有关标准。
2.适用范围本程序适用于新产品开发,现行产品的改进和改型,以及为满足客户特殊要求而对产品进行的更改。
涉及产品开发自研发项目确定阶段至设计确认最后阶段;涉及部门有研发部及与其接口部门,包括市场部、技术部、采购部、品质部、工模部、PMC部、生产部、财务部、平面外形小组、研发总经理。
3.定义3.1 开发设计:指设计研制具有新功能产品的过程。
3.2 改进设计:对现有产品功能改进、产品改型的过程。
4.引用文件4.1QB-03 《顾客要求识别和评审控制程序》4.2QB-07 《采购控制程序》4.3QB-12 《模具控制程序》4.4QB-26 《工程文件控制程序》4.5QB-27 《质量记录控制程序》4.6DXC2-GM-01 《客户样品确认流程》4.7DXC2-GM-02 《市场信息反馈流程》4.8DXC2-GM-03 《外来样品确认流程》4.9DXC2-GM-04 《内部样品确认流程》4.10D XC2-ED-15 《物料编号规则》4.11D XC2-ED-22 《工程文件编号规则》4.12D XC2-DC-01 《发文编号规定》4.13D XC2-DC-09 《样板管理办法》4.14D XC2-DC-13 《工程文件分发表》4.15D XC2-QA-48 《产品安全管理办法》4.16D XC2-QA-49 《可靠性工程实施办法》5.职责5.1 研发部职责5.1.1提出新产品开发要求。
5.1.2搜集产品开发的相关资料、信息,组织可行性分析活动。
5.1.3参加可行性分析评审。
电子产品质量控制工艺流程

电子产品质量控制工艺流程电子产品质量控制工艺流程随着电子产品在人们生活中的普及和重要性的增加,电子产品的质量控制显得格外重要。
本文将介绍一种常用的电子产品质量控制工艺流程,以确保产品的高质量。
1. 原材料检查在电子产品生产的第一步,对原材料进行检查是至关重要的。
原材料包括电子元器件、电路板以及其他必需的组件。
质量控制人员必须先对原材料进行一系列的测试和检验,以确保其符合产品质量要求。
2. 生产设备校准生产过程中的设备是关键,也需要进行定期校准。
质量控制团队应确保生产设备正常工作,并根据需要对其进行调整和校准。
只有在设备正常工作的情况下,才能保证产品生产的质量和稳定性。
3. 组装过程在组装过程中,质量控制人员必须进行中间检查,以确保产品的每一步都得以正确完成。
他们应该检查每个部件和组件的精确性、适配性和质量标准。
如果发现任何问题,应及时进行修复或更换。
4. 原型测试在生产过程的早期阶段,应制作一批原型产品进行测试。
这些原型产品需要经过一系列的测试来验证其功能和性能的稳定性。
原型测试应针对产品的核心功能和特性进行测试,以确保产品在市场上的竞争力和可靠性。
5. 严格的产品测试在组装完成后,每个产品都需要进行严格的产品测试。
这种测试应涵盖产品的所有功能和特性,并应录制和记录测试过程中出现的任何问题。
质量控制人员应使用各种测试设备和工具来确保产品的性能和质量达到设定的标准。
6. 产品检验产品检验是质量控制的最后一道工序。
产品检验应覆盖产品的外观、工艺、包装等方面。
质量控制人员应检查产品是否有任何瑕疵、缺陷或不符合标准的情况。
只有通过产品检验,产品才能被认为是合格的,并准备出货。
7. 客户反馈一旦产品出货,质量控制团队应积极收集客户的反馈和意见。
客户反馈是衡量产品质量的有效参考。
质量控制团队通过分析客户反馈,找出产品存在的问题并作出相应改进。
8. 持续改进质量控制过程是一个持续的迭代过程。
通过不断收集反馈和改进,质量控制团队可以不断提高产品的质量和性能,以满足不断变化的市场需求。
电控柜3c认证生产工艺规程

AAA 有限公司文件 A 版壳体制造工艺规程YJDQ-GY01-2009A/0共1页第1页目的为了使低压成套设备的箱壳体制造符合要求,确保制造质量,制定本工艺规程。
适用范围适用于低压成套设备的壳体的各类制造情况。
( 1)箱壳体:冷轧钢板( 外购 ) ——验收——下料(划线、剪板)——成形(冲工序流程角、冲孔、折弯、拼装焊接)——表面处理——装配——检验( 2)表面处理:酸洗(除锈)——除油——磷化——喷塑(喷漆)依据应符合图纸要求。
工序检验记录自检,不记录。
但应做好《工序控制单》记录。
但是,发现有进货缺陷,应记录并报告。
具体工艺要求工序工艺质量要求工具检验●技术人员,按照箱壳体总装配图纸,编制部件工艺图纸(钣金件展开冷轧钢板图纸),必要时确定具体制造工艺流程和要求;编制箱壳体定额材料清单。
外购、验●供应部门,依据箱壳体定额材料清单规定的材质、厚度和数量,采购收及准备外壳钢板。
●检验员,应验收钢板规格、数量、材质合格证、表面质量和厚度,并专检做好进货验收记录。
●操作工人,应依据图纸要求,在钢板上划线,确保合理利用材料。
冲剪机下料●操作工人,根据冲剪机操作规程,启动并检查设备运转正常。
或冲床首件自(划线、●操作工人,在核对钢板的材质和厚度应与图纸一致后,根据工艺图纸卷尺检剪板)和冲剪工艺流程,冲剪箱体件。
直尺●首件冲剪,应仔细定好标尺,对好冲模;应做首件检验,尺寸无误和公差符合图纸后,方可批量加工。
(1)冲角、冲孔:对下好的箱体件上冲角、冲孔,其尺寸和位置应符合图纸要求。
成形(2)折弯:卷尺(冲角、●对于需折弯的箱体件,根据工艺图纸,用折弯机进行折弯。
直尺冲孔、折●对首件应自检,要求折弯角度,偏差不超过±1°,尺寸定位精确,角尺首件自弯、拼装符合箱体图纸公差要求。
自检合格后,方可批量加工。
检焊接)(3)拼装焊接:电焊机自检●根据图纸要求,进行拼装,然后进行焊接。
●焊接人员,在焊接前,应检查电焊机运行正常;应按照被焊材质和对焊机焊接接头类型,试焊,确定适宜的焊接工艺(如焊条和焊接电流等)。
3C认证产品一致性控制程序
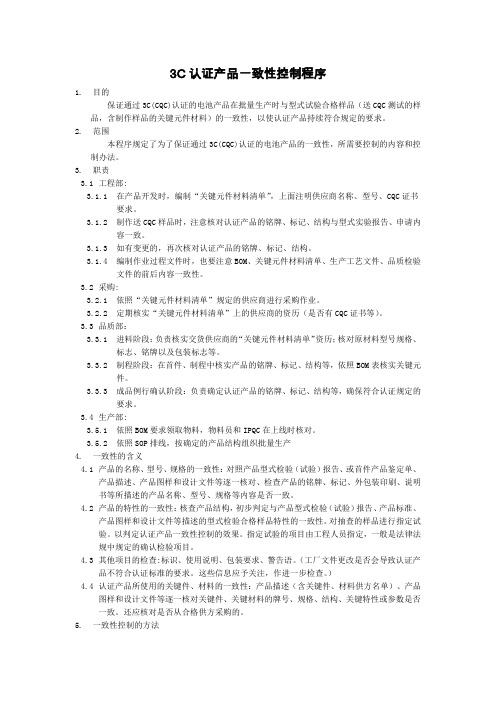
3C认证产品一致性控制程序1.目的保证通过3C(CQC)认证的电池产品在批量生产时与型式试验合格样品(送CQC测试的样品,含制作样品的关键元件材料)的一致性,以使认证产品持续符合规定的要求。
2.范围本程序规定了为了保证通过3C(CQC)认证的电池产品的一致性,所需要控制的内容和控制办法。
3.职责3.1工程部:3.1.1在产品开发时,编制“关键元件材料清单”,上面注明供应商名称、型号、CQC证书要求。
3.1.2制作送CQC样品时,注意核对认证产品的铭牌、标记、结构与型式实验报告、申请内容一致。
3.1.3如有变更的,再次核对认证产品的铭牌、标记、结构。
3.1.4编制作业过程文件时,也要注意BOM、关键元件材料清单、生产工艺文件、品质检验文件的前后内容一致性。
3.2采购:3.2.1依照“关键元件材料清单”规定的供应商进行采购作业。
3.2.2定期核实“关键元件材料清单”上的供应商的资历(是否有CQC证书等)。
3.3品质部:3.3.1进料阶段:负责核实交货供应商的“关键元件材料清单”资历;核对原材料型号规格、标志、铭牌以及包装标志等。
3.3.2制程阶段:在首件、制程中核实产品的铭牌、标记、结构等,依照BOM表核实关键元件。
3.3.3成品例行确认阶段:负责确定认证产品的铭牌、标记、结构等,确保符合认证规定的要求。
3.4生产部:3.5.1依照BOM要求领取物料,物料员和IPQC在上线时核对。
3.5.2依照SOP排线,按确定的产品结构组织批量生产4.一致性的含义4.1产品的名称、型号、规格的一致性:对照产品型式检验(试验)报告、或首件产品鉴定单、产品描述、产品图样和设计文件等逐一核对、检查产品的铭牌、标记、外包装印刷、说明书等所描述的产品名称、型号、规格等内容是否一致。
4.2产品的特性的一致性:核查产品结构,初步判定与产品型式检验(试验)报告、产品标准、产品图样和设计文件等描述的型式检验合格样品特性的一致性。
对抽查的样品进行指定试验。
- 1、下载文档前请自行甄别文档内容的完整性,平台不提供额外的编辑、内容补充、找答案等附加服务。
- 2、"仅部分预览"的文档,不可在线预览部分如存在完整性等问题,可反馈申请退款(可完整预览的文档不适用该条件!)。
- 3、如文档侵犯您的权益,请联系客服反馈,我们会尽快为您处理(人工客服工作时间:9:00-18:30)。
3C产品生产工艺控制程序
1.目的
为确保生产工艺准备充分,生产过程中工艺受到控制,工艺变更有所遵循,产品品质满足规定要求,特制定本程序。
2.适用范围
本程序适用于生产工艺的准备、生产工艺控制及其更改的活动。
3.引用文件
3.1 DXC-08 《生产过程控制程序》
3.2 DXC-26 《工程文件控制程序》
4.职责
4.1技术部负责制定加工工艺、工艺流程、作业指导书、确定工艺参数,设计夹具制作夹具、检具;
4.2品质部负责检具设计、评估;
4.3生产部负责生产场地、设备、人员安排,协助确定工艺参数;
4.4 PMC部负责准备生产物料;
5.程序
5.1工艺流程及作业指导书的制定
5.1.1生产或试产前,由客户或研发部提供如下资料:
a)成品样机三台(一台留技术部制定流程,一台留品质部封样,一台留生产部参照生产);
b)完整BOM一份;
c)完整电路图一份及P.C.B丝印图;
d)完整产品零件图及装配图;
e)测试说明。
5.1.2根据上述资料,技术部审查产品的工艺性,确定加工工艺,合理选择加工设备和测试仪器,编入《工艺流程图》;
5.1.3根据工艺流程图,对关键工序制定《作业指导书》,详细规定作业使用的设备仪器、夹具、检具、物料及操作步骤;
5.1.4试产前,技术部要制定出《工艺流程图》、《作业指导书》的试用版本,发放生产部准备试产,在试产时,技术部生产工程师、品质部品质工程师和生产部生产技术员三方对生产工艺进行评估,确认生产工艺的合理性和可靠性,并提出改善建议,生产工程师根据各部门意见和建议重新整理和制定《工艺流程图》、《作业指导书》,并作为正式版本发放生产部;
5.1.4 《工艺流程图》及《作业指导书》的制定、审批、管理、发放按《工程文件控制程序》执行。
5.2确定主要工艺参数和控制手段
5.2.1试产时,生产工程师根据产品质量、生产效率、安全性、可靠性及操作方便。