丝杠加工工艺说明书
滚珠丝杠的加工工艺
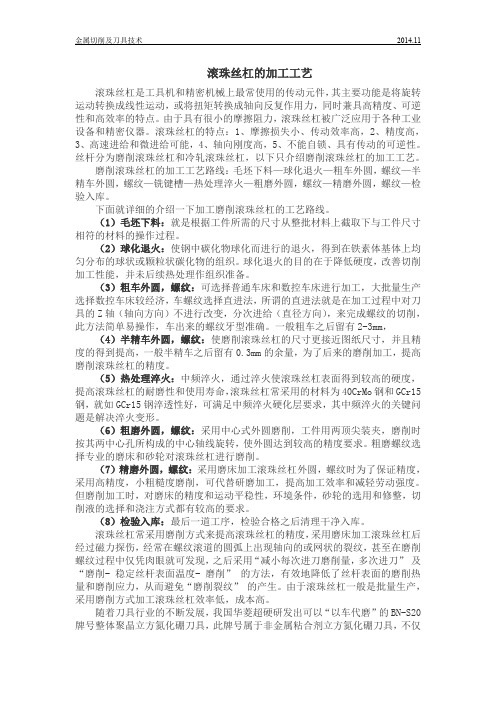
滚珠丝杠的加工工艺滚珠丝杠是工具机和精密机械上最常使用的传动元件,其主要功能是将旋转运动转换成线性运动,或将扭矩转换成轴向反复作用力,同时兼具高精度、可逆性和高效率的特点。
由于具有很小的摩擦阻力,滚珠丝杠被广泛应用于各种工业设备和精密仪器。
滚珠丝杠的特点:1、摩擦损失小、传动效率高,2、精度高,3、高速进给和微进给可能,4、轴向刚度高,5、不能自锁、具有传动的可逆性。
丝杆分为磨削滚珠丝杠和冷轧滚珠丝杠,以下只介绍磨削滚珠丝杠的加工工艺。
磨削滚珠丝杠的加工工艺路线:毛坯下料—球化退火—粗车外圆,螺纹—半精车外圆,螺纹—铣键槽—热处理淬火—粗磨外圆,螺纹—精磨外圆,螺纹—检验入库。
下面就详细的介绍一下加工磨削滚珠丝杠的工艺路线。
(1)毛坯下料:就是根据工件所需的尺寸从整批材料上截取下与工件尺寸相符的材料的操作过程。
(2)球化退火:使钢中碳化物球化而进行的退火,得到在铁素体基体上均匀分布的球状或颗粒状碳化物的组织。
球化退火的目的在于降低硬度,改善切削加工性能,并未后续热处理作组织准备。
(3)粗车外圆,螺纹:可选择普通车床和数控车床进行加工,大批量生产选择数控车床较经济,车螺纹选择直进法,所谓的直进法就是在加工过程中对刀具的Z轴(轴向方向)不进行改变,分次进给(直径方向),来完成螺纹的切削,此方法简单易操作,车出来的螺纹牙型准确。
一般粗车之后留有2-3mm,(4)半精车外圆,螺纹:使磨削滚珠丝杠的尺寸更接近图纸尺寸,并且精度的得到提高,一般半精车之后留有0.3mm的余量,为了后来的磨削加工,提高磨削滚珠丝杠的精度。
(5)热处理淬火:中频淬火,通过淬火使滚珠丝杠表面得到较高的硬度,提高滚珠丝杠的耐磨性和使用寿命,滚珠丝杠常采用的材料为40CrMo钢和GCr15钢,就如GCr15钢淬透性好,可满足中频淬火硬化层要求,其中频淬火的关键问题是解决淬火变形。
(6)粗磨外圆,螺纹:采用中心式外圆磨削,工件用两顶尖装夹,磨削时按其两中心孔所构成的中心轴线旋转,使外圆达到较高的精度要求。
轧制丝杠加工工艺流程
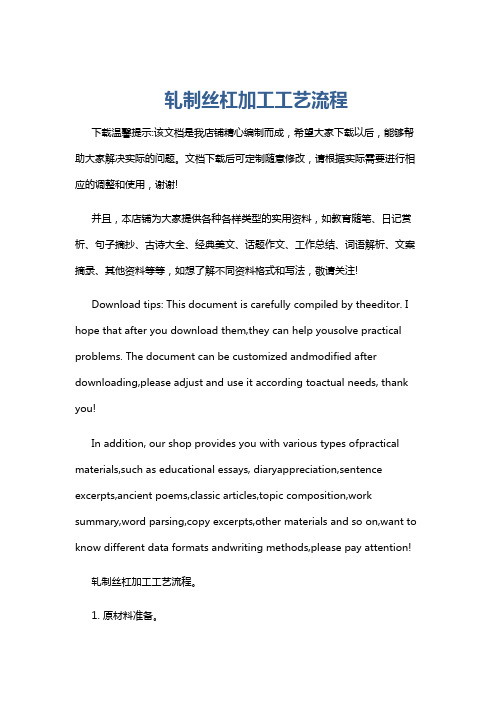
轧制丝杠加工工艺流程下载温馨提示:该文档是我店铺精心编制而成,希望大家下载以后,能够帮助大家解决实际的问题。
文档下载后可定制随意修改,请根据实际需要进行相应的调整和使用,谢谢!并且,本店铺为大家提供各种各样类型的实用资料,如教育随笔、日记赏析、句子摘抄、古诗大全、经典美文、话题作文、工作总结、词语解析、文案摘录、其他资料等等,如想了解不同资料格式和写法,敬请关注!Download tips: This document is carefully compiled by theeditor. I hope that after you download them,they can help yousolve practical problems. The document can be customized andmodified after downloading,please adjust and use it according toactual needs, thank you!In addition, our shop provides you with various types ofpractical materials,such as educational essays, diaryappreciation,sentence excerpts,ancient poems,classic articles,topic composition,work summary,word parsing,copy excerpts,other materials and so on,want to know different data formats andwriting methods,please pay attention!轧制丝杠加工工艺流程。
1. 原材料准备。
选用符合技术要求的钢材,常用的钢材牌号有45号钢、40Cr、38CrMoAlA等。
丝杠机械加工工艺卡片
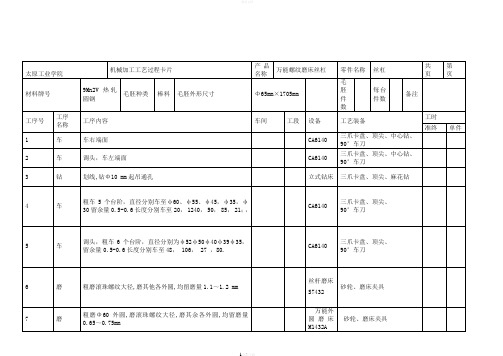
机械加工工序卡片机械加工工序卡片产品型号零件图号产品名称零件名称共(13页第(1)页车间工序号工序名称材料牌号1车左右端面,打中心孔9Mn2V毛坯种类毛坯外形尺寸每毛坯可制件数每台件数1705x65mm 1 1设备名称设备型号设备编号同时加工件数车床车床CA6140 1夹具编号夹具名称切削液三爪卡盘乳化液工位器具编号工位器具名称工序工时 (分) 准终单件工步号工步内容工艺装备主轴转速切削速度进给量切削深度进给次数工步工时r/min m/min mm/r mm 机动辅助1 车左端面、保证全长至尺寸硬质合金车刀158 58 0.56 3.15 1设计(日期)校对(日期)审核(日期)标准化(日期)会签(日期)标记处数更改文件号签字日期标记处数更改文件号签字日期机械加工工序卡片机械加工工序卡片产品型号零件图号产品名称零件名称共(13)页第(2)页2车左右端面,打中心孔9Mn2V毛坯种类毛坯外形尺寸每毛坯可制件数每台件数1705x65mm 1 1设备名称设备型号设备编号同时加工件数车床车床CA6140 1夹具编号夹具名称切削液三爪卡盘乳化液工位器具编号工位器具名称工序工时 (分) 准终单件工步号工步内容工艺装备主轴转速切削速度进给量切削深度进给次数工步工时r/min m/min mm/r mm 机动辅助1车右端面、保证全长至尺寸硬质合金车刀158 58 0.56 3.15 1设计(日期)校对(日期)审核(日期)标准化(日期)会签(日期)标记处数更改文件号签字日期标记处数更改文件号签字日期机械加工工序卡片机械加工工序卡片产品型号零件图号产品名称零件名称共(13)页第(3)页车间工序号工序名称材料牌号3 打通孔9Mn2V毛坯种类毛坯外形尺寸每毛坯可制件数每台件数1705x¢65mm 1 1设备名称设备型号设备编号同时加工件数车床CA6140 1夹具编号夹具名称切削液乳化液工位器具编号工位器具名称工序工时 (分)准终单件工步号工步内容工艺装备主轴转速切削速度进给量切削深度进给次数工步工时r/min m/min mm/r mm 机动辅助1 打孔¢10 麻花钻158 38 0.5 10 1设计(日期)校对(日期)审核(日期)标准化(日期)会签(日期)标记处数更改文件号签字日期标记处数更改文件号签字日期机械加工工序卡片产品型号零件图号产品名称零件名称共(13)页第(4)页车间工序号工序名称材料牌号4 车外圆9Mn2V毛坯种类毛坯外形尺寸每毛坯可制件数每台件数1705x¢65 1 1设备名称设备型号设备编号同时加工件数车床车床CA6140 1夹具编号夹具名称切削液三爪卡盘、顶尖乳化液工位器具编号工位器具名称工序工时 (分)准终单件工步号工步内容工艺装备主轴转速切削速度进给量切削深度进给次数工步工时r/min m/min mm/r mm 机动辅助1 车右端¢60外圆,留余量0.5——0.6mm 硬质合金车刀、顶尖183 57.5 0.26 2.5 22 车¢55外圆,留余量0.5——0.6mm 硬质合金车刀、顶尖183 57.5 0.26 2.5 23 车¢45外圆,留余量0.5——0.6mm 硬质合金车刀、顶尖183 57.5 0.26 2.5 24 车¢35外圆,留余量0.5——0.6mm 硬质合金车刀、顶尖183 57.5 0.26 2.5 25 车¢30外圆,留余量0.5——0.6mm 硬质合金车刀、顶尖183 57.5 0.26 2.5 2设计(日期)校对(日期)审核(日期)标准化(日期)会签(日期)标记处数更改文件号签字日期标记处数更改文件号签字日期机械加工工序卡片产品型号零件图号产品名称零件名称共(13)页第(5页车间工序号工序名称材料牌号5 车外圆9Mn2V毛坯种类毛坯外形尺寸每毛坯可制件数每台件数1705x¢65mm 1 1设备名称设备型号设备编号同时加工件数车床车床CA6140 1夹具编号夹具名称切削液三爪卡盘、顶尖乳化液工位器具编号工位器具名称工序工时 (分)准终单件工步号工步内容工艺装备主轴转速切削速度进给量切削深度进给次数工步工时r/min m/min mm/r mm 机动辅助1 车¢52h6外圆,留余量0.5——0.6mm 硬质合金车刀183 57.5 0.26 2.5 22 车¢50m6外圆, 留余量0.5——0.6mm 硬质合金车刀183 57.5 0.26 2.5 23 车¢40m6外圆, 留余量0.5——0.6mm 硬质合金车刀183 57.5 0.26 2.5 24 车¢39m6外圆, 留余量0.5——0.6mm 硬质合金车刀183 57.5 0.26 2.5 25 车¢35h6的槽完成倒角硬质合金车刀183 57.5 0.26 2.5 2设计(日期)校对(日期)审核(日期)标准化(日期)会签(日期)标记处数更改文件号签字日期标记处数更改文件号签字日期机械加工工序卡片机械加工工序卡片产品型号零件图号产品名称零件名称共(13)页第(6)页车间工序号工序名称材料牌号6 磨外圆9Mn2V毛坯种类毛坯外形尺寸每毛坯可制件数每台件数1702x¢65 1 1设备名称设备型号设备编号同时加工件数磨床M1432A 1夹具编号夹具名称切削液三爪卡盘乳化液工位器具编号工位器具名称工序工时 (分)准终单件工步号工步内容工艺装备主轴转速切削速度进给量切削深度进给次数工步工时r/min m/min mm/r mm 机动辅助1 粗磨Φ60外圆平行砂轮74.5 45.5 0.05 0.1 22 磨滚珠螺纹大径Φ56 平行砂轮74.5 45.5 0.05 0.1 23 磨M39×1.5—7h螺纹大径平行砂轮74.5 45.5 0.05 0.1 24 磨 M33×1.5—7h螺纹大径平行砂轮74.5 45.5 0.05 0.1 25 磨其余各外圆,均留磨量0.65~0.75mm, 平行砂轮74.5 45.5 0.05 0.1 2设计(日期)校对(日期)审核(日期)标准化(日期)会签(日期)标记处数更改文件号签字日期标记处数更改文件号签字日期机械加工工序卡片机械加工工序卡片产品型号零件图号产品名称零件名称共(13)页第(7)页车间工序号工序名称材料牌号7 磨滚珠丝杠螺纹9Mn2V毛坯种类毛坯外形尺寸每毛坯可制件数每台件数1705x¢65mm 1 1设备名称设备型号设备编号同时加工件数丝杆磨床S7432 1夹具编号夹具名称切削液乳化液工位器具编号工位器具名称工序工时 (分)准终单件工步号工步内容工艺装备主轴转速切削速度进给量切削深度进给次数工步工时r/min m/min mm/r mm 机动辅助1磨滚珠丝杠底槽至尺寸,粗磨滚珠丝杠螺纹,留磨量(三针测量仪M=7.01.60-φ量棒直径Φ4.2),齿形用样板透光检查,去不完整牙,完工后垂直吊放专用车床夹具254 80 0.56 5 1设计(日期)校对(日期)审核(日期)标准化(日期)会签(日期)标记处数更改文件号签字日期标记处数更改文件号签字日期机械加工工序卡片机械加工工序卡片产品型号 零件图号产品名称零件名称 共(13)页 第(8)页车间 工序号 工序名称 材 料 牌 号8 磨外圆 9Mn2V 毛 坯 种 类 毛坯外形尺寸 每毛坯可制件数 每 台 件 数1705x ¢65mm 1 1 设备名称 设备型号 设备编号 同时加工件数 数控车床 1夹具编号 夹具名称 切削液乳化液 工位器具编号 工位器具名称 工序工时 (分) 准终 单件工步号 工 步 内 容 工 艺 装 备 主轴转速 切削速度 进给量切削深度 进给次数工步工时 r/min m/min mm/r mm 机动 辅助 1 粗磨Φ60外圆平行砂轮 74.5 45.5 0.05 0.1 3 2 磨滚珠螺纹大径10.0056+φ平行砂轮 74.5 45.5 0.05 0.1 2 3 磨M39×1.5—7h 螺纹大径 平行砂轮 74.5 45.5 0.05 0.1 2 4 磨 M33×1.5—7h 螺纹大径平行砂轮 74.5 45.5 0.05 0.1 2 5 磨其余各外圆,均留磨量0.65~0.75mm, 平行砂轮 74.545.50.05 0.12设 计(日 期) 校 对(日期) 审 核(日期) 标准化(日期) 会 签(日期)标记处数 更改文件号 签字 日 期标记 处数 更改文件号 签字日 期机械加工工序卡片机械加工工序卡片产品型号零件图号产品名称零件名称共(13)页第(9)页车间工序号工序名称材料牌号9 半精磨滚珠螺纹9Mn2V毛坯种类毛坯外形尺寸每毛坯可制件数每台件数1705x¢65mm 1 1设备名称设备型号设备编号同时加工件数丝杆磨床S7432 1夹具编号夹具名称切削液乳化液工位器具编号工位器具名称工序工时 (分)准终单件工步号工步内容工艺装备主轴转速切削速度进给量切削深度进给次数工步工时r/min m/min mm/r mm 机动辅助1半精磨滚珠螺纹, 留精磨余量(三针测量仪M=20.02.59+φ量棒直径Φ4.2),齿形用样板透光检查,完工后垂直吊放专用车床夹具254 80 0.56 5 1设计(日期)校对(日期)审核(日期)标准化(日期)会签(日期)标记处数更改文件号签字日期标记处数更改文件号签字日期机械加工工序卡片机械加工工序卡片产品型号 零件图号产品名称零件名称 共(13)页 第(10)页车间 工序号 工序名称 材 料 牌 号10 磨外圆 GCr19Mn2V 5 毛 坯 种 类 毛坯外形尺寸 每毛坯可制件数 每 台 件 数1705x ¢65mm 1 1 设备名称 设备型号 设备编号 同时加工件数 磨床 M1432A 1夹具编号 夹具名称 切削液乳化液 工位器具编号 工位器具名称 工序工时 (分) 准终 单件工步号 工 步 内 容 工 艺 装 备 主轴转速 切削速度 进给量切削深度 进给次数工步工时 r/min m/min mm/r mm 机动 辅助 1 粗磨Φ60外圆平行砂轮 74.5 45.5 0.05 0.1 1 2 磨滚珠螺纹大径10.0056+φ平行砂轮 74.5 45.5 0.05 0.1 2 3 磨M39×1.5—7h 螺纹大径 平行砂轮 74.5 45.5 0.05 0.1 2 4 磨 M33×1.5—7h 螺纹大径平行砂轮 74.5 45.5 0.05 0.1 2 5 磨其余各外圆,均留磨量0.65~0.75mm, 平行砂轮 74.545.50.05 0.12设 计(日 期) 校 对(日期) 审 核(日期) 标准化(日期) 会 签(日期)标记处数 更改文件号 签字 日 期标记 处数 更改文件号 签字日 期机械加工工序卡片机械加工工序卡片产品型号零件图号产品名称零件名称共(13)页第(11)页车间工序号工序名称材料牌号11 精车螺纹毛坯种类毛坯外形尺寸每毛坯可制件数每台件数1705x¢65mm 1 1设备名称设备型号设备编号同时加工件数车床M1432A 1夹具编号夹具名称切削液乳化液工位器具编号工位器具名称工序工时 (分)准终单件工步号工步内容工艺装备主轴转速切削速度进给量切削深度进给次数工步工时r/min m/min mm/r mm 机动辅助1 精车M39-LH-7H螺纹成240 50 0.56 0.3 12 精车M33x1.5-LH-7H螺纹成240 50 0.56 0.3 1设计(日期)校对(日期)审核(日期)标准化(日期)会签(日期)标记处数更改文件号签字日期标记处数更改文件号签字日期机械加工工序卡片机械加工工序卡片产品型号零件图号产品名称零件名称共(13)页第(12)页车间工序号工序名称材料牌号12 精磨滚珠螺纹毛坯种类毛坯外形尺寸每毛坯可制件数每台件数1705x¢65mm 1 1设备名称设备型号设备编号同时加工件数丝杆磨床S7432 1夹具编号夹具名称切削液乳化液工位器具编号工位器具名称工序工时 (分)工步号工步内容工艺装备主轴转速切削速度进给量切削深度进给次数工步工时r/min m/min mm/r mm 机动辅助1 精磨滚珠丝杠螺纹至图样要求,齿尖倒圆R0.8mm, 240 50 0.56 0.3 1设计(日期)校对(日期)审核(日期)标准化(日期)会签(日期)标记处数更改文件号签字日期标记处数更改文件号签字日期机械加工工序卡片机械加工工序卡片产品型号零件图号产品名称零件名称共(13)页第(13)页车间工序号工序名称材料牌号13 去毛刺毛坯种类毛坯外形尺寸每毛坯可制件数每台件数1705x¢65mm 1 1设备名称设备型号设备编号同时加工件数1夹具编号夹具名称切削液乳化液工位器具编号工位器具名称工序工时 (分)欢迎您的下载,资料仅供参考!致力为企业和个人提供合同协议,策划案计划书,学习资料等等打造全网一站式需求。
冷轧丝杠硬车加工工艺

冷轧丝杠硬车加工工艺一,冷轧丝杠硬车加工问题的提出:在机械加工中,退火是常见的热处理方法,特别是工件料硬且加工余量大时,传统工艺一般是退火后再进行切削加工,或者采用大余量磨削加工;随着华菱超硬BN-S20牌号强力车刀的问世,大余量切削加工热处理后的硬料工件,改变了传统工艺。
省去了退火工艺,消除了退火后再二次淬火的弊端,更解决了采用砂轮进行大余量磨削加工的困难。
二,冷轧丝杠硬车加工工艺参数加工内容:冷轧丝杠轴端硬车,工件硬度HRC60-65;加工余量10mm。
刀片牌号:华菱超硬HLCBN,BN-S20;适合大余量车削加工淬硬钢,可加工硬度范围HRC45-79.切削参数:吃刀深度:刀具吃刀深度可达8mm,粗加工时争取一刀加工完大部分余量,去除硬化层。
线速度:70--90m/min.走刀量:0.1mm/r;具体视机床刚性调整。
三,冷轧丝杠硬车加工的刀具研究BN-S20牌号是华菱超硬采用纯陶瓷作为结合剂的CBN烧结体,经过高温高压合成,具有更好的抗冲击性能;CBN采用纳米级超细晶粒,其耐磨性能更优异。
在加工大余量硬料中,寿命是金属基结合剂CBN刀片的4倍以上。
2007年BN-S20发布会上,其在断续车削淬火齿轮外圆加工中,打破了超硬刀具行业CBN刀具不能用于强断续车削淬硬钢的神话,在刀具学术界引起很大的轰动!目前,随着我司对于陶瓷结合剂CBN刀具的研究进展,在保留CBN刀具抗冲击性能的基础上,增加了其耐磨性能,表现在大量加工淬火料时,它除了刀具韧性保证的同时,更具有优异的耐磨性能,省去了退火工序和二次淬火的工序,更解决了采用砂轮大余量磨削加工的困难。
BN-S20在大余量加工硬料时,实现了“以车代粗磨”,冷轧丝杠硬车加工工艺,取代了传统的退火工序,节省了加工成本,为用户取得了巨大的经济效益。
(资料来源:华菱超硬刀具/news2.asp?id=510)。
丝杠机械加工工艺设计说明书
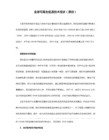
第 1 章 零件的分析
1. 1.1 零件的作用
丝杠是一种精度很高的零件,它能精确地确定工作台坐标位置,将旋转运动 转换成直线运动,面且还要传递一定的动力,所以在精度、强度及耐磨性等方面 都有很高的要求。所以,丝杠的加工从毛坯到成品的每道工序都要周密考虑,以 提高其加工精度。
1.2 零件的结构简介 1.2.1 丝杠的分类
2.3 制订工艺路线
材料 精度等级 工艺过程 9Mn2V 6级 工序内容 1.锻造 2.球化退火 3.车端面打中心孔 4.粗车外圆 5.高温时效 5.牢外圆打中心孔 7.半精车外圆 8.粗磨外圆 9.淬火(t=800℃),中温回 火(t=260℃) 14.研磨两顶尖孔 11.粗磨外圆 12.粗磨出螺纹槽 13.人工时效(t=260℃) 双顶尖孔 双顶尖孔 外圆表面 双顶尖孔 双顶尖孔 外圆表面 双顶尖孔 定位基准
2.1 确定毛坯材料
丝杠材料的选择是保证丝杠质量的关键,一般要求是: (1) 具有优良的加工性能,磨削时不易产生裂纹,能得到良好的表面光洁
度和较小的残余内应力,对刀具磨损作用较小。 (2) 抗拉极限强度一般不低于 588MPa。 (3) 有良好的热处理工艺性,淬透性好,不易淬裂,组织均匀,热处理变形 小,能获得较高的硬度,从而保证丝杠的耐磨性和尺寸的稳定性。 (4) 材料硬度均匀,金相组织符合标准。常用的材料有:不淬硬丝杠常用 T10A, T12A 及 45 等;淬硬丝杠常选用 9Mn2V,CrWMn 等。其中 9Mn2V 有较 好的工艺性和稳定性,但淬透性差,常用于直径≤50mm 的精密丝杠;CrWMn 钢 的优点是热处理后变形小,适用于制作高精度零件,但其容易开裂,磨削工艺性 差。 丝杠的硬度越高越耐磨,但制造时不易磨削。 丝杠材料要有足够的强度, 以保证传递一定的动力;应具有良好的热处理工 艺性(淬透性好、热处理变形小、不易产生裂纹),并能获得较高的硬度、良好的 耐磨性。丝杠螺母材料一般采用 GCrl5、CrWMn、9CrSi、9Mn2V,热处理硬度 为 60~62HRC。整体淬火在热处理和磨削过程中变形较大,工艺性差,应尽可能
丝杆工艺标准规范样本

”丝杆”零件的加工工艺规程目录一、零件的分析 (1)1.1零件的作用 (1)1.2零件的工艺分析 (1)二、工艺规程设计 (2)2.1确定毛坯的制造形式 (2)2.2基面的选择··························· (2)2.3制定工艺路线 (2)2.4机械加工余量、工序尺寸及毛坯尺寸的确定 (4)2.5确定切削用量及基本工时 (5)参考文献 (7)一、零件的分析1.1零件的作用丝杆: 由细长的金属棒制造, 表面光洁度很高, 是用来将旋转运动转化为直线运动; 或将直线运动转化为旋转运动的执行元件, 并具有传动效率高, 定位准确等特点。
滑动丝杠螺母材料的选用原则能够基于温度条件, 运行PV( 压力-速度) 值, 抗磨寿命要求, 使用环境, 以及成本等因素, 例如, 可供选用的材料特性包括: 从-50℃到+150℃的温度允许范围, 高达60,000psi-fpm的可用PV值, 可提供5千万英寸累计工作行程的反向间隙消除能力, 免维护运行, 以及可用于污染和恶劣环境等1.2零件的工艺分析图1-1 proe导出的丝杆零件图1、丝杆的分类机床丝杆按其摩擦特性可分为三类: 即滑动丝杠、滚动丝杠及静压丝杠。
由于滑动丝杠结构简单, 制造方便, 因此在机床上应用比较广泛。
滑动丝杠的牙型多为梯形。
这种牙型比三角形牙型具有效果高, 传动性能好, 精度高, 加工方便等优点。
滚动丝杠可分为滚珠丝杠和滚珠丝杠两大类。
滚珠丝杠和滚珠丝杠相比而言摩擦力小, 传动效率高, 精度也高, 因而比较常见, 可是其制造工艺比较复杂。
静压丝杠有许多的优点, 常被用于精密机床和数控机床的进给机构中。
滚珠丝杠加工工艺
滚珠丝杠加工工艺
滚珠丝杠加工工艺
引言
•简介滚珠丝杠加工工艺的重要性和应用范围。
优点
•高效率:快速完成滚珠丝杠的加工,提高生产效率。
•精度高:滚珠丝杠加工工艺可控性强,能够精确控制加工尺寸。
•耐磨性好:滚珠丝杠经过加工工艺后表面光滑平整,耐磨性大大提高。
工艺流程
1.材料准备:选取适合的材料,满足滚珠丝杠的力学性能要求。
2.细化设计:根据滚珠丝杠的具体要求,进行细化设计,包括螺纹
的规格、长度、槽形等。
3.车削加工:使用车床进行螺纹的车削加工,保证螺纹的精度和表
面光滑度。
4.热处理:进行热处理,提高滚珠丝杠的硬度,增强其耐磨性和耐
腐蚀性。
5.精密磨削:使用磨床进行精密磨削,进一步提高滚珠丝杠的加工
精度。
6.清洗和涂层:清洗滚珠丝杠,去除表面的污垢,并进行防锈涂层。
注意事项
•滚珠丝杠加工工艺需要严格控制各个环节的工艺参数,确保加工质量。
•操作人员要熟练掌握加工设备的使用和维护,保证设备的正常运行。
•加工过程中需注意安全措施,确保操作人员的人身安全。
结论
•滚珠丝杠加工工艺是一项复杂的工艺,通过合理的工艺流程和严格的控制,可以获得高质量的滚珠丝杠产品。
对于滚珠丝杠的生
产企业来说,掌握滚珠丝杠加工工艺是提高产品质量和生产效率
的重要保障。
滚珠丝杠端部加工工艺流程
滚珠丝杠端部加工工艺流程英文回答:CNC Machining End Milling Process for Ball Screws.Introduction.CNC end milling is a highly precise and efficient machining process that is commonly utilized for the fabrication of precision parts and components, including ball screws. This process involves the use of a CNC machine to guide a rotating cutting tool to remove material from a workpiece in a controlled manner.Procedure.The CNC end milling process for ball screws typically involves the following steps:1. CAD/CAM Programming: The first step is to create acomputer-aided design (CAD) model of the ball screw and then convert it into a computer-aided manufacturing (CAM) program. The CAM program generates the instructions that will guide the CNC machine during the milling process.2. Workpiece Preparation: The workpiece material is prepared by cutting it to the appropriate size and shape.It is then securely mounted on the CNC machine's worktable.3. Tool Selection: The appropriate cutting tool is selected based on the material of the workpiece and the desired finish. For ball screws, a high-quality end mill with a sharp cutting edge is essential.4. Tool Setup: The cutting tool is installed in the CNC machine's spindle and aligned with the workpiece. The spindle speed, feed rate, and depth of cut are set according to the specified parameters.5. Machining: The CNC machine executes the CAM program, guiding the cutting tool to remove material from the workpiece. The end mill follows a predetermined path,creating the desired shape and dimensions of the ball screw.6. Inspection: Once the machining process is complete, the ball screw is inspected for accuracy and quality. This may involve using measuring instruments such as calipers, micrometers, or a coordinate measuring machine (CMM).7. Post-Processing: After inspection, the ball screw may undergo additional post-processing steps such as heat treatment, grinding, or polishing to achieve the desired surface finish and properties.Advantages.CNC end milling offers several advantages for the machining of ball screws, including:High precision and accuracy.Consistent repeatability.Efficient and time-saving.Ability to produce complex shapes and features.Suitable for a wide range of materials.中文回答:滚珠丝杠端部加工工艺流程。
丝杆零件的机械加工工艺规程及工艺装备
丝杆零件的机械加工工艺规程及工艺装备引言丝杆是一种常用于传动的零件,广泛应用于机械设备中。
在丝杆的加工过程中,需要遵循一定的工艺规程,使用特定的工艺装备,以保证加工质量和效率。
本文将介绍丝杆零件的机械加工工艺规程及所需的工艺装备。
一、丝杆零件的工艺规程1. 工艺准备在进行丝杆零件的机械加工之前,需要进行充分的工艺准备工作。
首先,根据图纸要求,对工艺过程进行详细分析,确定加工工艺路线和工艺参数。
其次,准备所需的原材料,包括丝杆材料和辅助材料等。
最后,检查加工设备和工具的状况,确保其正常运行。
2. 丝杆的车削加工丝杆零件的加工中,常见的方法是车削加工。
车削加工是利用车床设备对丝杆进行切削,形成所需的外形和螺纹。
具体的加工工艺包括以下几个步骤:•第一步,选取合适的车刀,并进行刀具装夹和调整;•第二步,对工件进行装夹,并进行中心定位和调整;•第三步,根据工艺路线和参数要求,进行车削切削。
其中包括粗车、精车和倒角等工序;•第四步,对车削过程中产生的切屑进行及时清理,以保证加工质量。
3. 丝杆的螺纹加工丝杆零件通常需要进行螺纹加工,以用于螺母或其他连接件的固定。
螺纹加工是利用螺纹加工机床或车削加工进行的。
具体的加工工艺包括以下几个步骤:•第一步,选取合适的刀具,并进行刀具装夹和调整;•第二步,对工件进行装夹,并进行中心定位和调整;•第三步,根据工艺路线和参数要求,进行螺纹切削。
其中包括粗加工和精加工等工序;•第四步,对螺纹加工过程中产生的切屑进行及时清理,以保证加工质量。
4. 丝杆的表面处理为了提高丝杆零件的表面质量和使用寿命,通常需要进行表面处理。
常见的表面处理方法包括镀层、喷涂、热处理等。
具体的表面处理工艺需要根据丝杆的用途和要求来确定。
二、丝杆零件的工艺装备丝杆零件的机械加工需要使用一定的工艺装备,包括车床、螺纹加工机床、刀具等。
下面将介绍常见的丝杆加工工艺装备:1. 车床车床是丝杆加工的主要设备,用于进行车削加工。
滚珠丝杠 生产工艺
滚珠丝杠生产工艺滚珠丝杠是一种常用于机械传动的装置,具有高效、精确和稳定的特点。
它在工业生产中广泛应用于各种机械设备,如数控机床、自动化生产线和机器人等。
本文将介绍滚珠丝杠的生产工艺,包括材料选择、加工工艺和质量控制等方面。
滚珠丝杠的生产过程始于材料的选择。
常见的滚珠丝杠材料有碳钢、合金钢和不锈钢等。
根据不同的应用需求,选择合适的材料可以提高滚珠丝杠的强度和耐磨性。
在材料选择的基础上,进行下一步的加工工艺。
滚珠丝杠的加工工艺主要包括车削、磨削和热处理等环节。
首先是车削工艺,通过车床将滚珠丝杠的外径和螺纹进行加工,确保其尺寸精度和表面质量。
接下来是磨削工艺,利用磨床对滚珠丝杠进行精密加工,提高其表面光洁度和尺寸精度。
最后是热处理工艺,通过控制加热和冷却过程,改善滚珠丝杠的组织结构和力学性能。
在滚珠丝杠的生产过程中,质量控制是非常重要的环节。
通过严格的质量控制措施,可以确保滚珠丝杠的性能和可靠性。
常见的质量控制手段包括尺寸检测、表面质量检验和力学性能测试等。
尺寸检测可以通过测量工具和设备进行,确保滚珠丝杠的尺寸符合要求。
表面质量检验可以通过目视检查和光学仪器进行,检测滚珠丝杠表面是否存在缺陷和磨损。
力学性能测试可以通过拉伸试验和硬度测试等方法进行,评估滚珠丝杠的强度和硬度等性能指标。
除了生产工艺,滚珠丝杠的应用也是非常广泛的。
它可以用于实现精确的位置控制和运动传递,广泛应用于各种机械设备中。
例如,在数控机床中,滚珠丝杠可以实现工件的精确定位和加工运动控制,提高加工精度和效率。
在自动化生产线中,滚珠丝杠可以用于输送和定位装置,实现自动化生产过程的高效运行。
在机器人领域,滚珠丝杠可以用于机械臂的运动控制,实现精确的姿态调整和工作空间扩展。
滚珠丝杠的生产工艺是一个复杂而关键的过程。
通过合理的材料选择、精密的加工工艺和严格的质量控制,可以生产出高质量的滚珠丝杠产品。
滚珠丝杠的广泛应用促进了机械传动技术的发展,推动了工业自动化和智能制造的进步。
- 1、下载文档前请自行甄别文档内容的完整性,平台不提供额外的编辑、内容补充、找答案等附加服务。
- 2、"仅部分预览"的文档,不可在线预览部分如存在完整性等问题,可反馈申请退款(可完整预览的文档不适用该条件!)。
- 3、如文档侵犯您的权益,请联系客服反馈,我们会尽快为您处理(人工客服工作时间:9:00-18:30)。
. ... .课程设计任务书课程名称:机械制造工艺学设计题目:丝杠的工艺设计课程设计容与要求:容:设计一套丝杠的加工工艺设计要求:1.要求绘制零件图一,毛坯图一,设计说明书一份。
2.工艺设计要求合理,有利于提高加工精度,保证加工质量,降低加工成本,提高劳动生产率。
图纸共2说明书共15页目录前言 (2)第1章零件的分析 (3)1.1 零件的作用 (3)1.2零件的工艺分析 (3)第2章工艺规程设计 (5)2.1确定毛坯的制造形式 (5)2.2基面的选择 (6)2.3 制订工艺路线 (6)2.4机械加工余量、工序尺寸及毛坯尺寸的确定 (8)2.5确定切削用量 (10)第3章绘制零件图 (13)总结 (14)致 (15)参考文献 (16)前言机械制造工艺学的研究对象是机械产品的制造工艺,包括零件加工和装配两方面,其指导思想是在保证质量的前提下达到高生产率、经济性。
研究的重点是工艺过程,同样也包括零件加工工艺过程和装配工艺过程。
工艺是使各种原材料、半成品成为产品的方法和过程,它是生产中最活跃的因素,它既是构思和想法,又是实在的方法和手段,并落实在由工件、刀具、机床、夹具所构成的工艺系统中。
第1章零件的分析1.1 零件的作用题目给定的零件是丝杠,丝杠是将旋转运动变成直线运动的传动副零件,它被用来完成机床的进给运动。
机床丝杠不仅要能传递准确的运动,而且还要能传递一定的动力。
所以它在精度、强度以及耐磨性各个方面,都有一定的要求。
其功用为支承传动零件(齿轮、皮带轮等)、传动扭矩、承受载荷,以及保证装在主轴上的工件或刀具具有一定的回转精度。
表面特点:外圆、孔、圆锥、螺纹、花键、横向孔。
1.2零件的工艺分析丝杠是细而长的柔性轴,它的长径比往往很大,一般都在20~50左右,刚度很差。
加上其结构形状比较复杂,有要求很高的螺纹表面,又有阶梯及沟槽,因此,在加工过程中,很容易产生变形。
这是丝杠加工中影响精度的一个主要矛盾。
主要技术要求:1、尺寸精度轴颈是轴类零件的主要表面,它影响轴的回转精度及工作状态。
轴颈的直径精度根据其使用要求通常为IT6~IT9,精密轴颈可达IT5。
2、几何形状精度轴颈的几何形状精度(圆度、圆柱度),一般应限制在直径公差点围。
对几何形状精度要求较高时,可在零件图上另行规定其允许的公差。
3、位置精度主要是指装配传动件的配合轴颈相对于装配轴承的支承轴颈的同轴度,通常是用配合轴颈对支承轴颈的径向圆跳动来表示的;根据使用要求,规定高精度轴为0.001~0.005mm,而一般精度轴为0.01~0.03mm。
此外还有外圆柱面的同轴度和轴向定位端面与轴心线的垂直度要求等。
4.表面粗糙度根据零件的表面工作部位的不同,可有不同的表面粗糙度值,例如普通机床主轴支承轴颈的表面粗糙度为Ra0.16~0.63um,配合轴颈的表面粗糙度为Ra0.63~2.5um,随着机器运转速度的增大和精密程度的提高,轴类零件表面粗糙度值要求也将越来越小。
轴类零件的加工工艺因其用途、结构形状、技术要求、产量大小的不同而有差异。
而轴的工艺规程编制是生产中最常遇到的工艺工作。
轴类零件加工的主要问题:轴类零件加工的主要问题是如何保证各加工表面的尺寸精度、表面粗糙度和主要表面之间的相互位置精度。
具体指标有:(1)单个螺距允差(2)中径圆度允差;(3)外径相等性允差;(4)外径跳动允差;(5)牙形半角允差;(6)中径为尺寸公差;(7)外径为尺寸公差;(8)径为尺寸公差。
第2章工艺规程设计2.1确定毛坯的制造形式题目给定的零件是丝杠,轴类零件可根据使用要求、生产类型、设备条件及结构,选用棒料、锻件等毛坯形式。
对于外圆直径相差不大的轴,一般以棒料为主;而对于外圆直径相差大的阶梯轴或重要的轴,常选用锻件,这样既节约材料又减少机械加工的工作量,还可改善机械性能。
轴类零件的材料和毛坯,合理选用材料和规定热处理的技术要求,对提高轴类零件的强度和使用寿命有重要意义,同时,对轴的加工过程有极大的影响。
1、轴类零件的材料一般轴类零件常用45钢,根据不同的工作条件采用不同的热处理规(如正火、调质、淬火等),以获得一定的强度、韧性和耐磨性。
对中等精度而转速较高的轴类零件,可选用40Cr等合金钢。
这类钢经调质和表面淬火处理后,具有较高的综合力学件能。
精度较高的轴,有时还用轴承钢GCrls和弹簧钢65Mn等材料,它们通过调质和表面淬火处理后,具有更高耐磨性和耐疲劳性能。
对于高转速、重载荷等条件下工作的轴,可选用20CrMnTi、20MnZB、20Cr 等低碳含金钢或38CrMoAIA氮化钢。
低碳合金钢经渗碳淬火处理后,具有很高的表面硬度、抗冲击韧性和心部强度,热处理变形却很小。
2、轴类零件的毛坯轴类零件的毛坯最常用的是圆棒料和锻件,只有某些大型的、结构复杂的轴才采用铸件。
因而结合题目给定车床丝杠零件的作用及工作要求,材料可选用GCr15,毛坯应采用锻件,以保证机械性能。
2.2基面的选择基面的选择是工艺规程设计的重要工作之一,基面选择的正确与合理,可以使加工质量得以保证,生产率得以提高。
否则,加工工艺过程中会问题百出,甚至会造成零件的大批报废,使生产无常运行。
(1)粗基准的选择。
对于本零件而言,按照粗基准的选择原则,以外圆为粗基准是完全合理的。
(2)精基准的选择。
主要考虑到基准重合的问题,和便于装夹,以工件端面中心孔为精基准。
2.3 制订工艺路线工艺路线方案一毛坯(热处理)—校直—车端面打中心孔—外圆粗加工—校直热处理—重打中心孔(修正)—外圆半精加工—加工螺纹—校直、低温时效—修正中心孔—外圆、螺纹精加工。
工序Ⅰ毛坯(热处理)工序Ⅱ校直工序Ⅲ车端面打中心孔工序Ⅳ外圆粗加工工序Ⅴ校直热处理工序Ⅵ重打中心孔(修正)工序Ⅶ外圆半精加工工序Ⅷ加工螺纹工序Ⅸ校直、低温时效工序Ⅹ修正中心孔工序ⅩⅠ外圆、螺纹精加工工艺路线方案二工序Ⅰ锻造(弯曲度不超过5mm)工序Ⅱ球面退火工序Ⅲ车端面打中心孔工序Ⅳ车外圆工序V 粗车梯形螺纹槽工序VI 半精车外圆工序VII 粗磨外圆工序VIII 车梯形螺纹工序IX 半精磨外圆工序X 精车螺纹工序XI 研磨外圆工序XII 终磨外圆工艺方案的比较与分析1、丝杠的校直及热处理:丝杠工艺除毛坯工序外,在粗加工及半精加工阶段,都安排了校直及热处理工序。
校直的目的是为了减少工件的弯曲度,使机械加工余量均匀。
时效热处理以消除工件的残余应力,保证工件加工精度的稳定性。
一般情况下,需安排三次。
一次是校直及高温时效,它安排在粗车外圆以后,还有两次是校直及低温时效,它们分别安排在螺纹的粗加工及半精加工以后。
2、定位基准面的加工:丝杠两端的中心孔是定位基准面,在安排工艺路线时,应一首先将它加工出来,中心孔的精度对加工质量有很大影响,丝杠多选用带有120。
保护锥的中心孔。
此外,在热处理后,最后精车螺纹以前,还应适当修整中心孔以保持其精度。
丝杠加工的定位基准面除中心孔外,还要用丝杠外圆表面作为辅助基准面,以便在加工中采用跟刀架,增加刚度。
3、螺纹的粗、精加工粗车螺纹工序一般安排在精车外圆以后,半精车及精车螺纹工序则分别安排在粗磨及精磨外圆以后。
不淬硬丝杠一般采用车削工艺,经多次加工,逐渐减少切削力和应力;对于淬硬丝杠,则采用“先车后磨”或“全磨”两种不同的工艺。
后者是从淬硬后的光杠上直接用单线或多线砂轮粗磨出螺纹,然后用单线砂轮精磨螺纹。
4、重钻中心孔:工件热处理后,会产生变形。
其外圆面需要增加的加工余量,为减少其加工余量,而采用重钻中心孔的方法。
在重钻中心孔之前,先找出工件上径向圆跳动为最大值的一半的两点,以这两点后作为定位基准面,用车端面的方法切去原来的中心孔,重新钻中心孔。
当使用新的中心孔定位时,工件所必须切会的额外的加工余量将减少到原有值。
由于该丝杠为批量生产,故加工工艺过程按照工序划分阶段的原则,将整个工艺过程分为五个阶段:准备和预先热处理阶段,粗加工阶段,半精加工阶段,精加工阶段,终加工阶段。
为了消除残余应力,整个工艺过程安排了四次消除残余应力的热处理,并严格规定机械加工和热处理后不准冷校直,以防止产生残余应力。
为了消除加工过程中的变形,每次加工后工件应垂直吊放,并采用留加工余量分层加工的方法,经过多道工序逐步消除加工过程中引起的变形。
所以选择方案二为最佳方案。
2.4机械加工余量、工序尺寸及毛坯尺寸的确定(表2-1)2.5确定切削用量工序一:粗车外圆(1)确定背吃刀量粗车外圆,加工余量为5mm,一次走刀。
Asp=5/2=2.5mm.(2) 确定进给量刀杆尺寸16 25,as 3,工件直径为Φ35mm,则f=0.5~0.7。
由《简明手册》表4.2—3查取f =0.56mm。
根据《切削用量简明手册》表 1.11查取:VC=1.33(由182~199HBS、asp=2.5、f =0.56mm/r、车刀为YG硬质合金),由于实际车削过程使用条件的改变,查取切削速度修正系数:K =1.0,K =1.0,K =0.73,K =(190/HBS)1.25=1.0,KSV=0.85,Kkv=1.0。
则VC =VC 60V = VC K K K K KSV K= 1.33 60 1.0 1.0 0.73 1.0 0.85 1.0=49.5n = 157.6r/min按CA6140车床转速(《机械制造工艺设计简明手册》表4.2-2)选择与157.5r/min相近似的机床转速n =183r/min,则实际切削速度V = n /1000=3.14 100 183/1000=57.5m/min。
综上,此工步的切削用量为:a =2.5mm,f =0.56, n =183r/min, V =57.5m/min。
工序二:精车外圆左端(1)确定背吃刀量粗车外圆,加工余量为1.1mm,一次走刀。
Asp=1.1/2=0.55mm.(2) 确定进给量刀杆尺寸16 25,as 1.1,工件直径为Φ35mm,则f=0.2~0.4。
由《简明手册》表4.2—3查取f =0.26mm。
根据《切削用量简明手册》表 1.11查取:VC=1.33(由182~199HBS、asp=2.5、f =0.26mm/r、车刀为YG硬质合金),由于实际车削过程使用条件的改变,查取切削速度修正系数:K =1.0,K =1.0,K =0.73,K =(190/HBS)1.25=1.0,KSV=0.85,Kkv=1.0。
则VC =VC 60V = VC K K K K KSV K= 1.33 60 1.0 1.0 0.73 1.0 0.85 1.0=49.5n = 157.6r/min按CA620车床转速(《机械制造工艺设计简明手册》表4.2-2)选择与157.5r/min相近似的机床转速n =183r/min,则实际切削速度V = n /1000=3.14 100 183/1000=57.5m/min。