铝镁焊接技术难点
铝镁合金焊接常见缺陷_气孔的消除

焊接技术 第 38 卷第 8 期 2009 年 8 月
瓶, 放置作业平台上, 短把线, 坡口、 预热、 焊接方 法均与正式焊接相同, 焊后进行 X 射线探伤, 根据 检测结果决定是否在塔体上正式施焊。 3.4 组对检查
用不锈钢带和缩紧卡扣调整塔体上下口的圆度, 检查组对间隙, 分段对称点固焊。 点固焊焊缝长度约 15 mm, 间 距 200 mm。 组 对 完 毕 后 , 检 查 坡 口 组 对 间隙, 调整后使间隙基本保持一致。 3.5 焊前清理
气孔缺陷依然存在。
!!!!!!!!!!!!!!!!!!!!!!!!!!!!!!!!!!!!!!!!!!!!!!!
的冷裂纹和再热裂纹敏感 性 。 为 此 , 建 议 38 mm 厚
07MnCrMoVR 钢板现场组焊时焊前预热温度应不低于
75 ℃, 并且焊后进行低于 585 ℃的焊后整体热处理。
本研究成果已成功应用于该工程项目, 球罐再次
Welding Technology Vol.38 No.8 Aug. 2009 文 章 编 号 :1002-025X(2009)08-0071-02
·焊工之友· 71
铝 镁 合 金 焊 接 常 见 缺 陷 —— — 气 孔 的 消 除
张朝红
(中国石化集团 第四建设公司, 天津 300270)
摘要: 结合天津大沽化空分装置塔体组对焊接工程, 从焊缝缺陷的出现、 分析、 控制等过程, 找出影响铝镁合金焊接产生缺陷的主要因
焊缝中氢的来源: 氩气中所含少量的水、 氢及碳 氢化合物, 大气中水气浸入, 母材、 焊材表面氧化膜 Al2O3, MgO ( 特 别 是 MgO 存 在 不 很 致 密 的 氧 化 膜 ) 所吸附的水分, 母材、 焊材本身所固溶的氢等。
5052铝镁合金焊接缺陷

5052铝镁合金焊接缺陷5052铝镁合金是一种常用的铝合金材料,具有优良的耐腐蚀性能和高强度,广泛应用于航空、汽车、造船等领域。
然而,在5052铝镁合金的焊接过程中,常常会出现一些缺陷,影响焊接接头的质量和性能。
本文将重点介绍5052铝镁合金焊接中常见的几种缺陷,并探讨其原因和解决方法。
1. 焊缝裂纹:焊缝裂纹是5052铝镁合金焊接中常见的缺陷之一。
裂纹主要出现在焊接热影响区,对接头的强度和密封性产生不良影响。
造成焊缝裂纹的原因主要有焊接过程中的热应力集中、焊接速度过快和焊接材料的选择不当等。
解决焊缝裂纹的方法包括优化焊接参数、采用预热和后热处理等措施。
2. 焊接气孔:焊接气孔是5052铝镁合金焊接中另一个常见的缺陷。
气孔会导致焊缝中的气体和杂质含量增加,降低焊接接头的强度和耐腐蚀性。
气孔的形成主要与焊接过程中的气体溶解度、熔池中的气体释放和保护气体的选择等因素有关。
预防焊接气孔的方法包括提高焊接设备和工艺的精度、选择合适的保护气体和采用真空焊接等。
3. 焊接夹渣:焊接夹渣是指在5052铝镁合金焊接过程中,熔池中残留的夹渣物质。
夹渣会使焊缝的强度和密封性降低,同时还会引起腐蚀和气孔等缺陷的形成。
焊接夹渣的原因主要是焊接电流过小、焊接速度过快和焊接设备的清洁不彻底等。
解决焊接夹渣问题的方法包括增加焊接电流、调整焊接速度和加强设备清洁等措施。
4. 焊接变形:5052铝镁合金焊接过程中,由于焊接热源的作用,会产生热应力和热胀冷缩现象,导致焊接接头的变形。
焊接变形会影响接头的尺寸精度和外观质量,甚至会引起焊缝裂纹和气孔等缺陷的形成。
减少焊接变形的方法包括选择合适的焊接方式、采用预热和后热处理等措施。
5052铝镁合金焊接中常见的缺陷包括焊缝裂纹、焊接气孔、焊接夹渣和焊接变形等。
这些缺陷的形成与焊接过程中的参数选择、焊接材料和设备的质量以及操作技术等因素密切相关。
为了解决这些缺陷,需要优化焊接参数、提高焊接设备的精度和清洁度,同时还可以采用预热和后热处理等措施。
铝镁焊接技术难点

镁合金焊接产生气孔的影响因素铝镁合金焊接产生气孔的影响因素通过实践表明铝镁合金焊缝中的气孔主要是由氢引起的。
氢的来源有:焊丝和板材中溶解的氢及其表面氧化膜吸附的结晶水;氩气中的氢和湿气;焊接时由于保护不好空气中的氢和水气进入焊接熔池等。
氢在铝的熔点温度下溶解度发生突变,并随温度增加而急增。
铝镁合金在焊接时,焊缝中能否产生气泡首先取决于溶入氢的浓度,在溶入氢的浓度小于0.69 cm³/100g时,形成气泡的可能性极小。
但在实际焊接过程中,由于某些因素控制不严,在电弧高温作用下,溶解于铝中氢的浓度就会大于0.69 cm³/100g,此时气孔的产生主要取决于结晶速度:当结晶速度快到恰好抑制了气泡的形成,则氢只能饱和固溶于焊缝金属中,而不以气泡形式逸出,气孔就会发生;当结晶速度足够慢,已形成的氢气泡来得及逸出焊缝溶池时,也不会形成气孔;当结晶速度正好使气泡能够形成而来不及逸出时便产生气孔。
其次铝镁合金的导热性强,在同样的工艺条件下其熔合区的冷却速度是钢的4~7倍,不利于气泡的浮出,实际冷却条件下是非平衡状态。
实际生产中发现铝镁合金对氢的溶解度较大,对气孔的敏感性比纯铝低,出现的气孔比较少。
1 弧柱气氛中水分弧柱空间总是或多或少存在一定数量的水分,尤其在潮湿季节或湿度大的环境里进行焊接时,由弧柱气氛中的水分分解产生的氢,溶入过热的熔融金属中,是焊缝气孔产生的主要原因。
弧柱气氛中的氢形成焊缝的气孔还与其在铝镁合金中溶解度的变化特性有关,如图3-1所示。
在平衡状态下,氢的溶解度沿图中的实线发生变化,在凝固点时可从0.69 mL/100g突降到0.036mL/100g,相差约20倍(在钢中只差不到2倍),这就是形成气孔的重要原因之一。
况且铝镁合金的导热性很强,在同样的工艺条件下,熔合区的冷却速度是高强钢的4~7倍,不利于气泡的浮出,更易促使形成气孔。
而在实际的冷却条件下是非平衡状态,溶解度变化沿a b c或a b’c’变化。
《铝镁系合金强韧性能及焊接性能研究》范文

《铝镁系合金强韧性能及焊接性能研究》篇一一、引言铝镁系合金作为一种轻质高强度的金属材料,因其良好的机械性能、耐腐蚀性以及加工性,被广泛应用于航空、汽车、电子等领域。
本文旨在研究铝镁系合金的强韧性能及焊接性能,为该类合金的进一步应用提供理论支持。
二、铝镁系合金的强韧性能研究1. 合金成分对强韧性能的影响铝镁系合金的强韧性能主要取决于其合金成分。
镁元素的添加可以显著提高铝合金的强度和韧性。
此外,合金中其他元素的含量也会对强韧性能产生影响。
例如,铜、锰等元素的添加可以进一步提高合金的强度,而锌元素的添加则可以改善合金的耐腐蚀性。
2. 热处理工艺对强韧性能的影响热处理工艺是提高铝镁系合金强韧性能的重要手段。
通过固溶处理、时效处理等工艺,可以使得合金中的元素充分溶解、析出,从而提高合金的强度和韧性。
此外,热处理工艺还可以改善合金的微观组织结构,提高其耐腐蚀性和耐磨性。
三、铝镁系合金的焊接性能研究1. 焊接方法及工艺参数的选择铝镁系合金的焊接主要采用熔化焊、压力焊和钎焊等方法。
针对不同的合金成分和厚度,需要选择合适的焊接方法和工艺参数。
在焊接过程中,应控制好焊接速度、电流、电压等参数,以保证焊缝的质量。
2. 焊缝的强韧性能及耐腐蚀性铝镁系合金焊缝的强韧性能和耐腐蚀性是评价焊接性能的重要指标。
研究表明,通过合理的焊接工艺和热处理工艺,可以使得焊缝的强度和韧性达到甚至超过母材的水平。
同时,焊缝的耐腐蚀性也可以通过合理的合金成分设计和表面处理来提高。
四、实验研究及结果分析为研究铝镁系合金的强韧性能及焊接性能,我们进行了以下实验:首先,制备了不同成分的铝镁系合金试样,并通过拉伸试验、冲击试验和硬度试验等方法测试其强韧性能;其次,采用不同的焊接方法和工艺参数对合金进行焊接,并对焊缝的质量和性能进行评估。
实验结果表明,铝镁系合金具有良好的强韧性能和焊接性能。
通过合理的合金成分设计和热处理工艺,可以进一步提高其强韧性能和耐腐蚀性。
镁合金焊接工艺的研究与应用
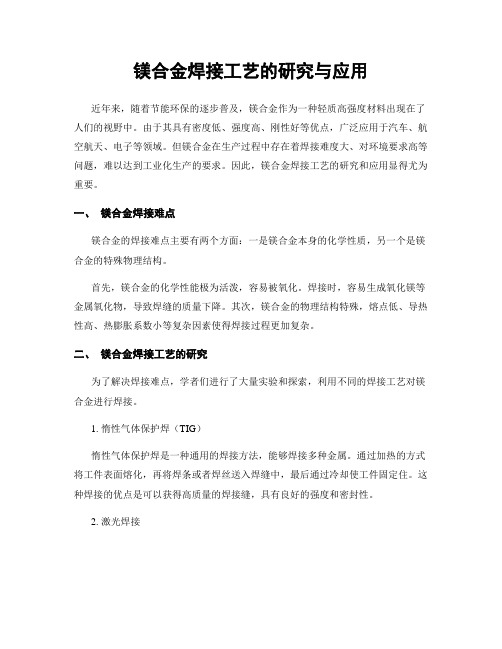
镁合金焊接工艺的研究与应用近年来,随着节能环保的逐步普及,镁合金作为一种轻质高强度材料出现在了人们的视野中。
由于其具有密度低、强度高、刚性好等优点,广泛应用于汽车、航空航天、电子等领域。
但镁合金在生产过程中存在着焊接难度大、对环境要求高等问题,难以达到工业化生产的要求。
因此,镁合金焊接工艺的研究和应用显得尤为重要。
一、镁合金焊接难点镁合金的焊接难点主要有两个方面:一是镁合金本身的化学性质,另一个是镁合金的特殊物理结构。
首先,镁合金的化学性能极为活泼,容易被氧化。
焊接时,容易生成氧化镁等金属氧化物,导致焊缝的质量下降。
其次,镁合金的物理结构特殊,熔点低、导热性高、热膨胀系数小等复杂因素使得焊接过程更加复杂。
二、镁合金焊接工艺的研究为了解决焊接难点,学者们进行了大量实验和探索,利用不同的焊接工艺对镁合金进行焊接。
1. 惰性气体保护焊(TIG)惰性气体保护焊是一种通用的焊接方法,能够焊接多种金属。
通过加热的方式将工件表面熔化,再将焊条或者焊丝送入焊缝中,最后通过冷却使工件固定住。
这种焊接的优点是可以获得高质量的焊接缝,具有良好的强度和密封性。
2. 激光焊接激光焊接是一种高能量、高速度、高温度的焊接方法。
它的优点是焊接速度快,温度高度集中,焊缝精细,可以实现无接触焊接,适用于涉及到较小的、高精度的焊接缝。
3. 熔覆焊熔覆焊是一种将细粉末或丝状金属材料熔化,并喷射到工件的表面来形成焊层的方法。
它的优点是可以通过控制不同金属的喷射速率和温度来实现最终材料的性能。
同时,还可以利用熔覆焊技术来修复镁合金件的损伤或缺陷部位。
三、镁合金焊接应用现状目前,随着焊接技术的不断成熟和发展,镁合金焊接工艺已经得到了广泛的应用。
主要包括以下几个方面:1. 汽车工业由于镁合金的密度低、强度高,可以用来改善汽车的性能和降低油耗。
而汽车制造中又涉及到许多焊接需求,因此镁合金的焊接工艺对汽车制造业尤为关键。
2. 航空航天工业在航空航天工业中,要求零件材料具有轻质、高强度、刚性好等特点,镁合金可以满足这一需求。
铝镁合金在焊接施工中常见缺陷的浅析和对策

铝镁合⾦在焊接施⼯中常见缺陷的浅析和对策铝镁合⾦在焊接施⼯中常见缺陷的浅析和对策黎明(马钢修建⼯程公司设备制造⼆⼚安徽马鞍⼭ 243000)摘要:本⽂通过对空分设备装置采⽤的铝镁合⾦的焊接性分析,得出铝镁合⾦焊接时产⽣⽓孔、未焊透、下凹、烧穿、组织疏松和热裂纹等缺陷的主要原因,针对产⽣的缺陷通过施⼯经验总结出了相应的解决措施。
关键词:铝镁合⾦;焊接;缺陷;对策1.前⾔空分装置采⽤的铝合⾦多数为5A02(LF2)和5183(LF4)铝镁合⾦。
由于铝及其合⾦在焊接时⽆明显颜⾊变化、导热率⾼、热膨胀系数⼤以及在它表⾯很容易形成致密的氧化膜等特点,使得铝及其合⾦的焊接⽬前在我国和世界发达国家的焊接作业中仍然是⼀个重⼤课题。
铝及其合⾦的焊接常见的缺陷主要有:⽓孔、根部未熔合、下凹、热裂纹、组织疏松与渗漏等。
本⽂根据马钢30000m3/h 的制氧机⼯程施⼯实践,重点介绍空分装置所⽤铝镁合⾦焊接时易产⽣的焊接缺陷及避免措施。
2.铝合⾦焊接性2.1铝合⾦分类铝合⾦是在纯铝中适量加⼊各种合⾦元素后获得较⾼强度及其它性能的合⾦。
按合⾦系列分类可分为⼯业纯铝,铝铜系,铝锰系,铝硅系,铝镁系,铝镁硅系和铝锌镁铜系列等;按⼯艺分类可分为变形铝合⾦和铸造铝合⾦[1],其中铝镁系列的焊接性能和⼒学性能都⽐较好,常⽤于制造结构、压⼒管道及压⼒容器上。
2.2 铝镁合⾦特性铝镁合⾦的熔点低,密度⼩,⾯⼼⽴⽅点阵结构,⽆同素异构转变,⽆“延?脆”转变并有优异的低温韧性等⼀系列特性,被⼴泛应⽤到低温设备结构中。
铝镁合⾦的强度随着含Mg%量的增加⽽增加,但随着Mg含量增多会出现脆性β相(Mg2Al3),从⽽降低塑性。
焊接时⼀般应控制含Mg量在5%以下,同时还应控制Si含量,防⽌⽣成Mg2Si这种脆性相物质[2]。
3.铝镁合⾦中常见的焊接缺陷产⽣原因及解决措施铝镁合⾦中常见的焊接缺陷主要有⽓孔、根部未熔合、下凹及烧穿、过烧引起的组织疏松及渗漏和裂纹。
激光焊接铝合金的难点及采取的工艺措施
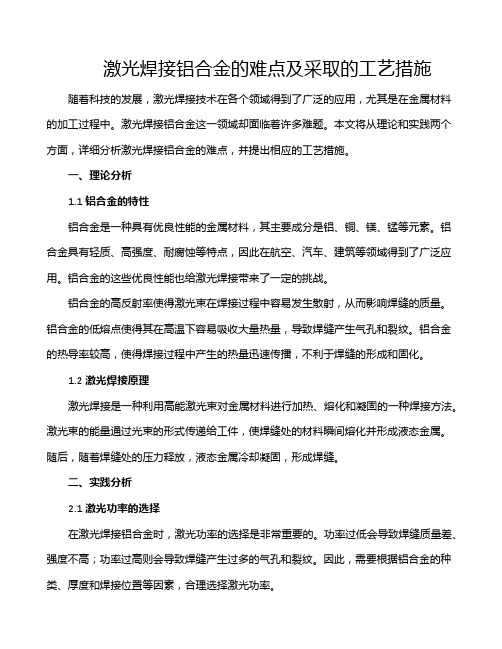
激光焊接铝合金的难点及采取的工艺措施随着科技的发展,激光焊接技术在各个领域得到了广泛的应用,尤其是在金属材料的加工过程中。
激光焊接铝合金这一领域却面临着许多难题。
本文将从理论和实践两个方面,详细分析激光焊接铝合金的难点,并提出相应的工艺措施。
一、理论分析1.1 铝合金的特性铝合金是一种具有优良性能的金属材料,其主要成分是铝、铜、镁、锰等元素。
铝合金具有轻质、高强度、耐腐蚀等特点,因此在航空、汽车、建筑等领域得到了广泛应用。
铝合金的这些优良性能也给激光焊接带来了一定的挑战。
铝合金的高反射率使得激光束在焊接过程中容易发生散射,从而影响焊缝的质量。
铝合金的低熔点使得其在高温下容易吸收大量热量,导致焊缝产生气孔和裂纹。
铝合金的热导率较高,使得焊接过程中产生的热量迅速传播,不利于焊缝的形成和固化。
1.2 激光焊接原理激光焊接是一种利用高能激光束对金属材料进行加热、熔化和凝固的一种焊接方法。
激光束的能量通过光束的形式传递给工件,使焊缝处的材料瞬间熔化并形成液态金属。
随后,随着焊缝处的压力释放,液态金属冷却凝固,形成焊缝。
二、实践分析2.1 激光功率的选择在激光焊接铝合金时,激光功率的选择是非常重要的。
功率过低会导致焊缝质量差、强度不高;功率过高则会导致焊缝产生过多的气孔和裂纹。
因此,需要根据铝合金的种类、厚度和焊接位置等因素,合理选择激光功率。
2.2 保护气体的选用为了防止铝合金在激光焊接过程中产生气孔和裂纹,需要在焊接过程中使用保护气体。
常用的保护气体有氩气、氮气等。
氩气的纯度要求较高,可以有效防止气孔的形成;氮气的成本较低,但可能会导致焊缝的氧化。
因此,在实际应用中需要根据具体情况选择合适的保护气体。
2.3 焊接速度的控制焊接速度对激光焊接铝合金的效果也有很大的影响。
过快的焊接速度会导致焊缝产生裂纹;过慢的焊接速度则会影响焊缝的质量和生产效率。
因此,需要根据铝合金的厚度和焊接位置等因素,合理控制焊接速度。
激光焊接铝合金的难点及采取的工艺措施
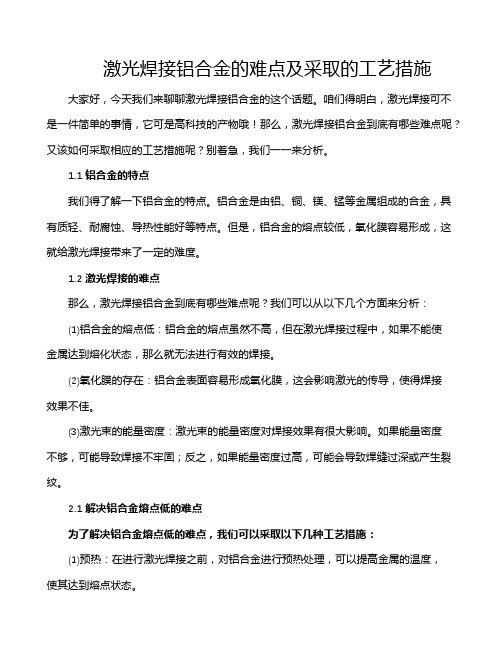
激光焊接铝合金的难点及采取的工艺措施大家好,今天我们来聊聊激光焊接铝合金的这个话题。
咱们得明白,激光焊接可不是一件简单的事情,它可是高科技的产物哦!那么,激光焊接铝合金到底有哪些难点呢?又该如何采取相应的工艺措施呢?别着急,我们一一来分析。
1.1 铝合金的特点我们得了解一下铝合金的特点。
铝合金是由铝、铜、镁、锰等金属组成的合金,具有质轻、耐腐蚀、导热性能好等特点。
但是,铝合金的熔点较低,氧化膜容易形成,这就给激光焊接带来了一定的难度。
1.2 激光焊接的难点那么,激光焊接铝合金到底有哪些难点呢?我们可以从以下几个方面来分析:(1)铝合金的熔点低:铝合金的熔点虽然不高,但在激光焊接过程中,如果不能使金属达到熔化状态,那么就无法进行有效的焊接。
(2)氧化膜的存在:铝合金表面容易形成氧化膜,这会影响激光的传导,使得焊接效果不佳。
(3)激光束的能量密度:激光束的能量密度对焊接效果有很大影响。
如果能量密度不够,可能导致焊接不牢固;反之,如果能量密度过高,可能会导致焊缝过深或产生裂纹。
2.1 解决铝合金熔点低的难点为了解决铝合金熔点低的难点,我们可以采取以下几种工艺措施:(1)预热:在进行激光焊接之前,对铝合金进行预热处理,可以提高金属的温度,使其达到熔点状态。
(2)调节激光功率:根据铝合金的种类和厚度,合理调整激光功率,以确保焊缝的形成和焊点的牢固。
(3)选择合适的焊接参数:根据实际情况,选择合适的焊接参数,如焊接速度、焦距等,以保证焊缝的质量。
2.2 解决氧化膜存在的难点为了解决氧化膜存在的难点,我们可以采取以下几种工艺措施:(1)清理氧化膜:在进行激光焊接之前,对铝合金表面进行清理,去除氧化膜,以保证激光的传导。
(2)使用保护气体:在激光焊接过程中,使用保护气体可以有效防止氧化膜的形成和扩散。
(3)控制焊接速度:适当控制焊接速度,可以避免氧化膜在熔化过程中被烧伤。
2.3 解决激光束能量密度的难点为了解决激光束能量密度的难点,我们可以采取以下几种工艺措施:(1)调整激光功率:根据铝合金的种类和厚度,合理调整激光功率,以保证焊缝的形成和焊点的牢固。
- 1、下载文档前请自行甄别文档内容的完整性,平台不提供额外的编辑、内容补充、找答案等附加服务。
- 2、"仅部分预览"的文档,不可在线预览部分如存在完整性等问题,可反馈申请退款(可完整预览的文档不适用该条件!)。
- 3、如文档侵犯您的权益,请联系客服反馈,我们会尽快为您处理(人工客服工作时间:9:00-18:30)。
镁合金焊接产生气孔的影响因素
铝镁合金焊接产生气孔的影响因素
通过实践表明铝镁合金焊缝中的气孔主要是由氢引起的。
氢的来源有:焊丝和板材中溶解的氢及其表面氧化膜吸附的结晶水;氩气中的氢和湿气;焊接时由于保护不好空气中的氢和水气进入焊接熔池等。
氢在铝的熔点温度下溶解度发生突变,并随温度增加而急增。
铝镁合金在焊接时,焊缝中能否产生气泡首先取决于溶入氢的浓度,在溶入氢的浓度小于0.69 cm³/100g时,形成气泡的可能性极小。
但在实际焊接过程中,由于某些因素控制不严,在电弧高温作用下,溶解于铝中氢的浓度就会大于0.69 cm³/100g,此时气孔的产生主要取决于结晶速度:当结晶速度快到恰好抑制了气泡的形成,则氢只能饱和固溶于焊缝金属中,而不以气泡形式逸出,气孔就会发生;当结晶速度足够慢,已形成的氢气泡来得及逸出焊缝溶池时,也不会形成气孔;当结晶速度正好使气泡能够形成而来不及逸出时便产生气孔。
其次铝镁合金的导热性强,在同样的工艺条件下其熔合区的冷却速度是钢的4~7倍,不利于气泡的浮出,实际冷却条件下是非平衡状态。
实际生产中发现铝镁合金对氢的溶解度较大,对气孔的敏感性比纯铝低,出现的气孔比较少。
1 弧柱气氛中水分
弧柱空间总是或多或少存在一定数量的水分,尤其在潮湿季节或湿度大的环境里进行焊接时,由弧柱气氛中的水分分解产生的氢,溶入过热的熔融金属中,是焊缝气孔产生的主要原因。
弧柱气氛中的氢形成焊缝的气孔还与其在铝镁合金中溶解度的变化特性有关,如图3-1所示。
在平衡状态下,氢的溶解度沿图中的实线发生变化,在凝固点时可从0.69 mL/100g突降到0.036mL/100g,相差约20倍(在钢中只差不到2倍),这就是形成气孔的重要原因之一。
况且铝镁合金的导热性很强,在同样的工艺条件下,熔合区的冷却速度是高强钢的4~7倍,不利于气泡的浮出,更易促使形成气孔。
而在实际的冷却条件下是非平衡状态,溶解度变化沿a b c或a b’c’变化。
在熔池的降温过程中,若冷却速度较大,由于a ~ b间溶解度差所造成的气泡数量虽然不多,但可能来不及逸出,而在上浮途中被“搁浅”,形成粗大而孤立的“皮下气孔”;同样,若冷却速度较小,从a到b’气孔虽然多一些,但可能来得及聚合浮出,在凝固点时,由于溶解度突变 (b ~ c或b’~ c’),伴随着凝固过程可在结晶的枝晶前沿形成许多微小气泡,枝晶晶体的交互生长致使气泡的生长受到限制,并且不利于浮出,因而可沿结晶的层撞线形成均布形式的小气孔,称为“结晶层气孔”。
不同的合金系统,对弧柱气氛中水分的敏感性不同,纯铝对气氛中水分最为敏感。
Al-Mg合金含
Mg量增高,氢的溶解度和引起气孔的临界分压PH2均随之增大,因而对吸收气氛中水分不太敏感。
相比起来,仅对气氛中水分而言,同样焊接条件下,纯铝焊缝产生气孔的倾向要大些。
不同的焊接方法,对弧柱气氛中水分的敏感性也是不同的。
TIG或MIG焊接时氢的吸收速率和吸收数量有明显差别。
在MIG焊接时,焊丝是以细小熔滴形式通过弧柱而落入熔池,由于弧柱温度最高,且熔滴比面积很大,熔滴金属显然最有利于吸收氢;而TIG焊接时,主要是熔池金属表面与气体氢反应,因其比表面积小和熔池温度低于弧柱温度,吸收氢的条件不如MIG焊时有利。
同时,MIG焊的熔池深度一般大于TIG焊时深度,也不利于气泡的浮出。
所以,MIG焊焊接时,在同样的气氛条件下,焊缝气孔倾向要比TIG焊时大些。
2 氧化膜中水分
在正常的焊接条件下,对于气氛中的水分已经尽量加以限制,这时,焊丝或工件的氧化膜中所吸附的水分将是生产焊缝气孔的主要原因。
而氧化膜不致密、吸水性强的铝合金,要比氧化膜致密的纯铝具有更大的气孔倾向。
这是因为铝镁合金的氧化膜是由Al2O3和MgO所构成,而MgO越多,形成的氧化膜越不致密,因而更容易吸附水分。
在MIG焊接时,焊丝表面氧化膜的作用将具有重要意义。
MIG焊接时,由于熔深较大,工件端部的氧化膜迅速熔化掉,有利于氧化膜中水分的排除,坡口氧化膜对焊缝气孔的影响就小得多了。
焊丝表面氧化膜的清理情况对焊缝含氢量的影响是比较大的, Al-Mg合金焊丝,则其影响更显著。
实践表明,在严格限制弧柱气氛水分的MIG焊接条件下,用Al-Mg合金焊丝比用纯铝焊丝时具有较大的气孔倾向。
TIG焊接时,在熔透不足的情况下,母材坡口根部未除净的氧化膜中所吸附的水分,常常是产生焊缝气孔的主要原因。
这种氧化膜不仅提供了氢的来源,而且能使气泡聚集附着。
在刚刚形成熔池时,如果坡口附近的氧化膜未能完全熔化而残存下来,则氧化膜中水分因受热而分解出氢,并在氧化膜上萌生出气泡;由于气泡是附着在残留氧化膜上,不容易脱离浮出,而且还因气泡是在熔化的早期形成的,有条件长大,所以常常造成集中形式的大气孔。
这种气孔在焊缝根部有未熔合是就更严重。
坡口端部氧化膜引起的气孔,常常沿着熔合区原坡口边缘分布,且内壁呈氧化色彩,是其重要特征。
由于Al-Mg合金比纯铝更容易形成疏松而吸水性强的厚氧化膜,所以Al-Mg 合金比纯铝更容易产生这种集中形式的氧化膜气孔。
为此,焊接铝镁合金时,焊前必须特别仔细地清理坡口端部的氧化膜。
顺便提到,母材表面氧化膜也会在近缝区引起“气孔”,主要发现于Al-Mg合金气焊的条件下,实际上用气焊火焰沿板表面加热一道后,也能看到这种现象。
这种“气孔”往往以表面密集的小
颗粒状的“鼓泡”形式呈现出来,也可认为是“皮下气泡”。
关于这种“气孔”的产生机理,还没有比较合理的解释。
3 材料特性
由于液态铝在高温时能吸收大量的氢,冷却时氢在其中的溶解能力急剧下降,在固态时又几乎不溶解氢,致使原来溶于液态铝的氢大量析出,形成气泡。
同时,因铝及铝合金密度小、导热性很强,不利于气泡的逸出,因此,铝及铝合金焊接易产生气孔。
此外,铝镁合金化学活泼性强,表面极易形成熔点高的氧化膜Al2O3和MgO,由于MgO的存在,形成的氧化膜疏松且吸水性强,这就更难避免焊缝中产生密集气孔。
用TIG焊,虽然负半周瞬间氩离子对氧化膜具有“阴极雾化”作用,但并不能去除氧化膜中的水分,因而铝镁合金焊接比纯铝具有更大的气孔倾向。
4 氩气的流量与纯度
氩气的流量是影响熔池保护效果的一个重要参数。
流量过小,氩气挺度不够,排除周围空气能力弱,保护效果差。
但是流量过大,不仅浪费氩气,而且会引起喷出气流层流区缩短,紊流区扩大,将空气卷入保护区,反而降低了保护效果,使焊缝易产生气孔。
这一点在现场施焊时,往往被忽视。
因此,必须选择合适的氩气流量。
氩气流量与喷嘴直径大小有关。
氩气的纯度对焊接质量也有较大的影响。
氩气纯度低、杂质多,可增加弧柱气氛中氢的含量,同时也降低“阴极雾化”效果。
5 焊接工艺
焊件坡口准备、组对方式和焊接工艺参数的选择对防止气孔产生至关重要。
焊件组对时根部留有间隙,可使氧化膜有效地暴露在电弧作用范围内。
改变焊接参数可影响气体逸出和溶入熔池条件。
焊接速度过慢,熔池保留时间长,增加氢的溶入量;焊接速度较快,易产生未焊透和未熔合缺陷。
实践证明,采用较快的焊接速度,并配以较大的焊接电流,可有效防止气孔的产生。
增大焊接电流不仅能保证根部熔合,而且能增加电弧对熔池的搅拌作用,有利于根部氧化膜中气泡的浮出,从而减少气孔的产生。
6 焊接操作技术
掌握熟练的操作技能也是防止气孔的一个重要环节。
铝镁合金管道现场焊接位置一般为全位置焊接,施焊时金属熔池所处空间位置不断改变,操作难度较大。
但焊枪与工件表面后倾角不能随熔
池位置的改变而任意改变。
若夹角过小,其内侧产生紊流,外侧则氩气挺度不够,气体保护熔池效果差。
水平管仰焊接头部位可采用交叉接头法,以避免接头部位产生密集气孔。
此外,钨极伸出长度过长、电弧过长或不稳等,都可能造成保护气体的污染而使焊缝产生气孔。
7 其它影响因素
除上述因素外,还应注意环境因素等方面的影响。
在高湿度的环境下,焊丝或输氩管内壁易吸附结晶水。
因此,环境相对湿度愈低愈好。
环境温度低于5°C施焊时要预热。