八钢430m2烧结降低工序能耗的实践
降低烧结工序能耗的生产实践
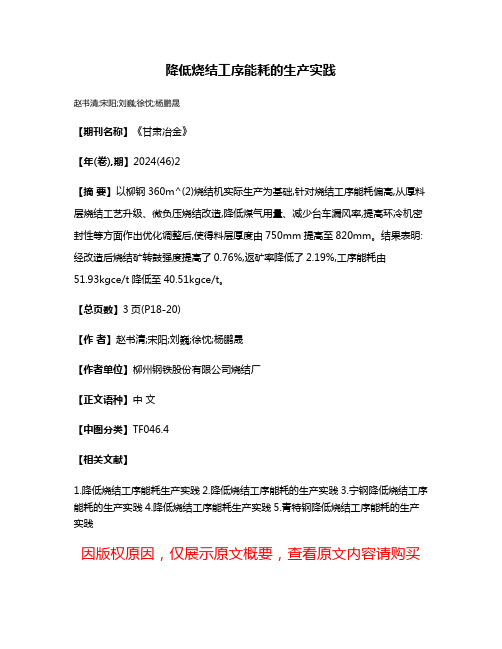
降低烧结工序能耗的生产实践
赵书清;宋阳;刘巍;徐忱;杨鹏晟
【期刊名称】《甘肃冶金》
【年(卷),期】2024(46)2
【摘要】以柳钢360m^(2)烧结机实际生产为基础,针对烧结工序能耗偏高,从厚料层烧结工艺升级、微负压烧结改造,降低煤气用量、减少台车漏风率,提高环冷机密封性等方面作出优化调整后,使得料层厚度由750mm提高至820mm。
结果表明:经改造后烧结矿转鼓强度提高了0.76%,返矿率降低了2.19%,工序能耗由
51.93kgce/t降低至40.51kgce/t。
【总页数】3页(P18-20)
【作者】赵书清;宋阳;刘巍;徐忱;杨鹏晟
【作者单位】柳州钢铁股份有限公司烧结厂
【正文语种】中文
【中图分类】TF046.4
【相关文献】
1.降低烧结工序能耗生产实践
2.降低烧结工序能耗的生产实践
3.宁钢降低烧结工序能耗的生产实践
4.降低烧结工序能耗生产实践
5.青特钢降低烧结工序能耗的生产实践
因版权原因,仅展示原文概要,查看原文内容请购买。
浅谈降低烧结工序能耗的措施
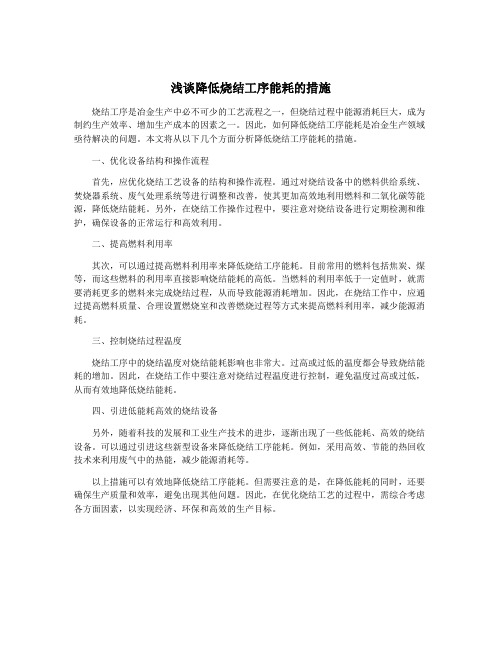
浅谈降低烧结工序能耗的措施烧结工序是冶金生产中必不可少的工艺流程之一,但烧结过程中能源消耗巨大,成为制约生产效率、增加生产成本的因素之一。
因此,如何降低烧结工序能耗是冶金生产领域亟待解决的问题。
本文将从以下几个方面分析降低烧结工序能耗的措施。
一、优化设备结构和操作流程首先,应优化烧结工艺设备的结构和操作流程。
通过对烧结设备中的燃料供给系统、焚烧器系统、废气处理系统等进行调整和改善,使其更加高效地利用燃料和二氧化碳等能源,降低烧结能耗。
另外,在烧结工作操作过程中,要注意对烧结设备进行定期检测和维护,确保设备的正常运行和高效利用。
二、提高燃料利用率其次,可以通过提高燃料利用率来降低烧结工序能耗。
目前常用的燃料包括焦炭、煤等,而这些燃料的利用率直接影响烧结能耗的高低。
当燃料的利用率低于一定值时,就需要消耗更多的燃料来完成烧结过程,从而导致能源消耗增加。
因此,在烧结工作中,应通过提高燃料质量、合理设置燃烧室和改善燃烧过程等方式来提高燃料利用率,减少能源消耗。
三、控制烧结过程温度烧结工序中的烧结温度对烧结能耗影响也非常大。
过高或过低的温度都会导致烧结能耗的增加。
因此,在烧结工作中要注意对烧结过程温度进行控制,避免温度过高或过低,从而有效地降低烧结能耗。
四、引进低能耗高效的烧结设备另外,随着科技的发展和工业生产技术的进步,逐渐出现了一些低能耗、高效的烧结设备。
可以通过引进这些新型设备来降低烧结工序能耗。
例如,采用高效、节能的热回收技术来利用废气中的热能,减少能源消耗等。
以上措施可以有效地降低烧结工序能耗。
但需要注意的是,在降低能耗的同时,还要确保生产质量和效率,避免出现其他问题。
因此,在优化烧结工艺的过程中,需综合考虑各方面因素,以实现经济、环保和高效的生产目标。
多工艺协同降低烧结机工序能耗生产实践

多工艺协同降低烧结机工序能耗生产实践当前国内钢铁产能日趋饱和,原燃料价格上涨明显,给钢铁行业发展带来了很大的挑战,节能降耗逐渐成为钢铁行业发展的必由之路。
我国钢铁行业能耗占整个国民经济的14%以上,其中烧结工序能耗占整个钢铁行业能耗的10%以上[1-2],因此,降低烧结工序能耗意义重大。
针对降低烧结工序能耗前人开展了众多生产研究实践,主要从改善烧结原燃料结构、提升混合料温、热风烧结、漏风治理、控制燃料破碎粒度、厚料层烧结工艺制度等方法进行了实践探究,取得了较好的效果[2 -4]。
但是常规工艺和单一新工艺的改进对降低烧结工序能耗的效果有限。
为更好地解决此问题,本文以中天钢铁550 m2烧结机工艺为基础,从低水低碳厚料层烧结、低热值煤气低负压点火、料面喷吹天然气等多工艺协同处理出发,结合漏风治理、增设边缘压料装置优化烧结料面布料等生产控制措施,试图在改善烧结矿产、质量的同时,取得降低工序能耗的良好效果,为同类工程提供借鉴与参考。
1 降低工序能耗生产工艺1.1 低水低碳厚料层烧结工艺厚料层烧结是降低燃料消耗的重要手段。
宝钢、马钢、首钢京唐、泰钢、天钢、湘钢等企业烧结料厚已达900~1 000 mm 水平。
本文涉及的烧结机台车栏板改造前高度为750mm,设计料层厚度为700~7 50 mm,为充分利用厚料层烧结自动蓄热特点,将点火炉抬高,逐步将料层厚度由800 mm 抬高至920 mm 水平,超烧结机台车栏板高度170 mm(见图1)。
随着料层厚度的提升,烧结机机速放慢,烧结料的高温保持时间增加,液相生成更加充足,烧结矿的转鼓强度由77%提升至78%。
为减少过湿层和燃烧层对厚料层烧结透气性的影响,在实施厚料层后重点采取了低水烧结措施和燃料粒度优化控制:①采取一混多加水、二混少加水;②加装雾化喷头保证原料制粒成球效果;③为消除混合矿槽蒸汽预热不均的问题,采用了蒸汽管道输堵装置;④采用熟熔剂烧结,充分利用生石灰消化放热提升混匀料料温。
QC报告(降低435烧结机煤气消耗)

运用TQC方法,降低煤气消耗一、概况435m2烧结机设计主要参数:年产烧结矿438.21万吨,年作业率为92%,烧结矿的转鼓指数为>78%。
主要工艺流程包括:烧结所用混匀料由第三原料场接受、贮存、混匀,混匀料和固体燃料直接由皮带机运至配料室矿槽前转运站。
燃料破碎系统处理后运输至配料室,各种原料在配料室按照一定比例配料后,经一次混合机、二次混合机送至烧结机焙烧、破碎,在环冷机上冷却到150℃以下,再运往冷筛分室进行整粒,其中+14mm、8-14mm、6-8mm为成品,部分8-14mm作为铺底料回到烧结机,-6mm部分为返矿回到配料室,成品取样后,运往3200m3高炉烧结矿矿槽前转运站。
面对严峻的市场形势,为进一步降本增效,我车间特成立了QC小组,拟降低煤气消耗。
二、QC小组概况1、小组成立时间:2012年1月30日2、小组名称:二烧车间降低煤气消耗3、小组成员概况表制表:庞国朝三、选题理由1、面对严峻的市场形势,为进一步降本增效,公司和炼铁部对我车间的成本提了更高的要求。
2、对微负压点火,我们做的不够,点火煤气还有进一步下降的空间3、料层还有进一步提升的空间,在生产过程中通过工艺改进、设备改造、操作思路的变更,煤气消耗还可以降低。
因此,我们将“降低煤气消耗”作为选题。
、现状调查经过QC小组讨论,我们根据2011年的煤气消耗,分析了具体的原因。
表年的煤气消耗从以上统计结果看出,煤气消耗部分月份能达到5.43m3/t,但由于众多原因,大多数时候仍然高于5.43m3/t,主要存在的问题是设备存在缺陷、生产过程控制出现波动、物料不稳定、人员操作水平偏低,根据这些问题列出了生产情况统计表如下:五、标设定及可行性分析1、目标:435m2烧结机烧煤气消耗达到5.0m3/t o2、可行性分析(1)、我车间有健全的管理制度,管理人员管理经验丰富、技术水平较高,责任心强,富有团队精神。
(2)各级领导对提高烧结矿质量工作非常重视,对QC小组活动给予大力支持。
八钢炼钢系统节能降耗实践
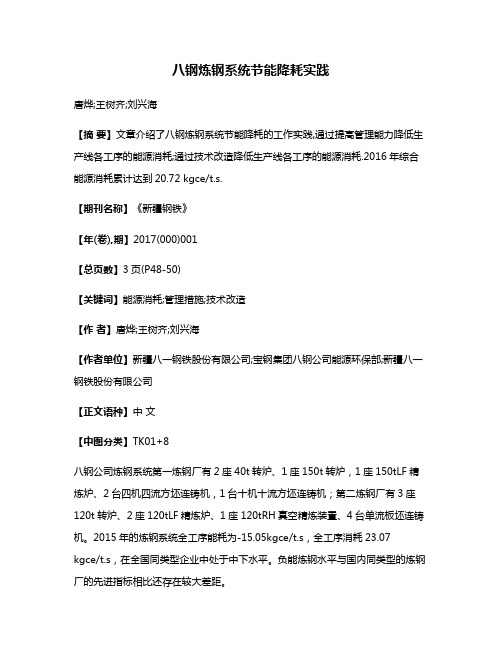
八钢炼钢系统节能降耗实践唐烨;王树齐;刘兴海【摘要】文章介绍了八钢炼钢系统节能降耗的工作实践,通过提高管理能力降低生产线各工序的能源消耗;通过技术改造降低生产线各工序的能源消耗.2016年综合能源消耗累计达到20.72 kgce/t.s.【期刊名称】《新疆钢铁》【年(卷),期】2017(000)001【总页数】3页(P48-50)【关键词】能源消耗;管理措施;技术改造【作者】唐烨;王树齐;刘兴海【作者单位】新疆八一钢铁股份有限公司;宝钢集团八钢公司能源环保部;新疆八一钢铁股份有限公司【正文语种】中文【中图分类】TK01+8八钢公司炼钢系统第一炼钢厂有2座40t转炉、1座150t转炉,1座150tLF精炼炉、2台四机四流方坯连铸机,1台十机十流方坯连铸机;第二炼钢厂有3座120t转炉、2座120tLF精炼炉、1座120tRH真空精炼装置、4台单流板坯连铸机。
2015年的炼钢系统全工序能耗为-15.05kgce/t.s,全工序消耗23.07kgce/t.s,在全国同类型企业中处于中下水平。
负能炼钢水平与国内同类型的炼钢厂的先进指标相比还存在较大差距。
为进一步降低能源消耗,达到国内炼钢的先进水平,八钢炼钢系统采取了多项节能降耗措施。
图1为八钢炼钢生产线2011年至2015年以来的能源消耗的变动趋势。
2016年炼钢的能源消耗目标为21.0kgce/t.s。
采取针对性的措施,努力降低冶炼、精炼、连铸工序的能源消耗,以提高全工序负能炼钢的绝对值-20kgce/t.s。
节能降耗主要从两个方面开展工作:(1)提高管理能力,降低生产线各工序的能源消耗;(2)通过技术改造,降低生产线各工序的能源消耗。
2.1 管理措施分阶段制定能源消耗目标见表1。
(1)完善能源管理制度:修订《炼钢厂能源管理办法》、《炼钢厂煤气回收管理办法》,完善能源管理体系,将能源消耗指标逐级分解到作业区、班组,明确每项能源介质消耗的责任人,同时将能源管理的绩效评价纳入到员工的当月绩效评价,使全厂的全员能源意识得到提升。
浅谈降低烧结工序能耗的措施
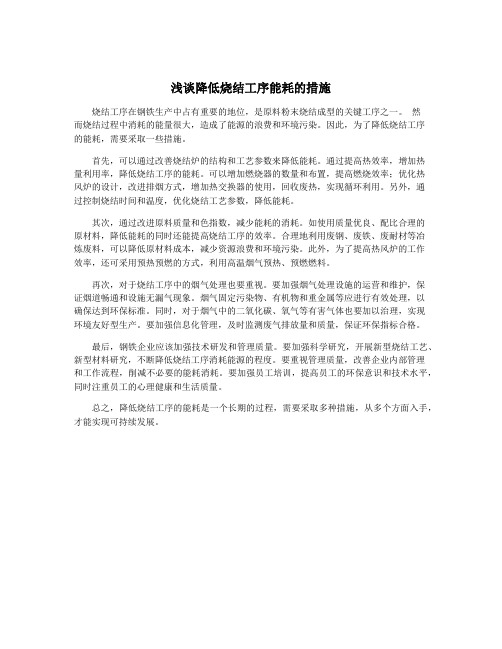
浅谈降低烧结工序能耗的措施烧结工序在钢铁生产中占有重要的地位,是原料粉末烧结成型的关键工序之一。
然而烧结过程中消耗的能量很大,造成了能源的浪费和环境污染。
因此,为了降低烧结工序的能耗,需要采取一些措施。
首先,可以通过改善烧结炉的结构和工艺参数来降低能耗。
通过提高热效率,增加热量利用率,降低烧结工序的能耗。
可以增加燃烧器的数量和布置,提高燃烧效率;优化热风炉的设计,改进排烟方式,增加热交换器的使用,回收废热,实现循环利用。
另外,通过控制烧结时间和温度,优化烧结工艺参数,降低能耗。
其次,通过改进原料质量和色指数,减少能耗的消耗。
如使用质量优良、配比合理的原材料,降低能耗的同时还能提高烧结工序的效率。
合理地利用废钢、废铁、废耐材等冶炼废料,可以降低原材料成本,减少资源浪费和环境污染。
此外,为了提高热风炉的工作效率,还可采用预热预燃的方式,利用高温烟气预热、预燃燃料。
再次,对于烧结工序中的烟气处理也要重视。
要加强烟气处理设施的运营和维护,保证烟道畅通和设施无漏气现象。
烟气固定污染物、有机物和重金属等应进行有效处理,以确保达到环保标准。
同时,对于烟气中的二氧化碳、氧气等有害气体也要加以治理,实现环境友好型生产。
要加强信息化管理,及时监测废气排放量和质量,保证环保指标合格。
最后,钢铁企业应该加强技术研发和管理质量。
要加强科学研究,开展新型烧结工艺、新型材料研究,不断降低烧结工序消耗能源的程度。
要重视管理质量,改善企业内部管理和工作流程,削减不必要的能耗消耗。
要加强员工培训,提高员工的环保意识和技术水平,同时注重员工的心理健康和生活质量。
总之,降低烧结工序的能耗是一个长期的过程,需要采取多种措施,从多个方面入手,才能实现可持续发展。
降低炼钢工序能耗的实践方法探讨
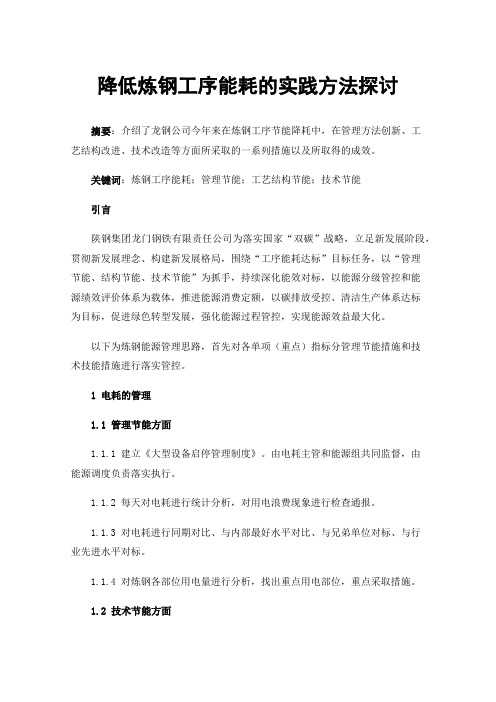
降低炼钢工序能耗的实践方法探讨摘要:介绍了龙钢公司今年来在炼钢工序节能降耗中,在管理方法创新、工艺结构改进、技术改造等方面所采取的一系列措施以及所取得的成效。
关键词:炼钢工序能耗;管理节能;工艺结构节能;技术节能引言陕钢集团龙门钢铁有限责任公司为落实国家“双碳”战略,立足新发展阶段,贯彻新发展理念、构建新发展格局,围绕“工序能耗达标”目标任务,以“管理节能、结构节能、技术节能”为抓手,持续深化能效对标,以能源分级管控和能源绩效评价体系为载体,推进能源消费定额,以碳排放受控、清洁生产体系达标为目标,促进绿色转型发展,强化能源过程管控,实现能源效益最大化。
以下为炼钢能源管理思路,首先对各单项(重点)指标分管理节能措施和技术技能措施进行落实管控。
1电耗的管理1.1管理节能方面1.1.1 建立《大型设备启停管理制度》。
由电耗主管和能源组共同监督,由能源调度负责落实执行。
1.1.2 每天对电耗进行统计分析,对用电浪费现象进行检查通报。
1.1.3 对电耗进行同期对比、与内部最好水平对比、与兄弟单位对标、与行业先进水平对标。
1.1.4 对炼钢各部位用电量进行分析,找出重点用电部位,重点采取措施。
1.2技术节能方面实施了“一次二次风机的自动节能模式”。
在转炉打到“炉后”开关出钢时,一次二次开始降速至25HZ运行;在打到“炉后”开关5分钟后,一次二次开始提速至高速45HZ运行;下枪信号后540秒(吹炼中期和吹炼后期)时,一次二次风机开始降低转速至30HZ运行。
2转炉煤气消耗的管理2.1在管理节能方面2.1.1 对钢包的寿命设立目标,进行分析:2.1.2 对每个烘烤器的煤气消耗量进行统计分析:2.1.3 对各连铸机中间包的寿命设立目标,进行统计分析:2.2在技术节能方面实施了《蓄热式钢包智能烘烤》项目。
对钢包烘烤分4个阶段,4个阶段实现自动调节,既保证了钢包的烘烤温度,又可以降低转炉煤气的空耗。
3氮气的管理3.1在管理节能方面3.1.1 对落料口氮封的流量标准规定为1800m3/h。
探究降低烧结工艺能耗的措施
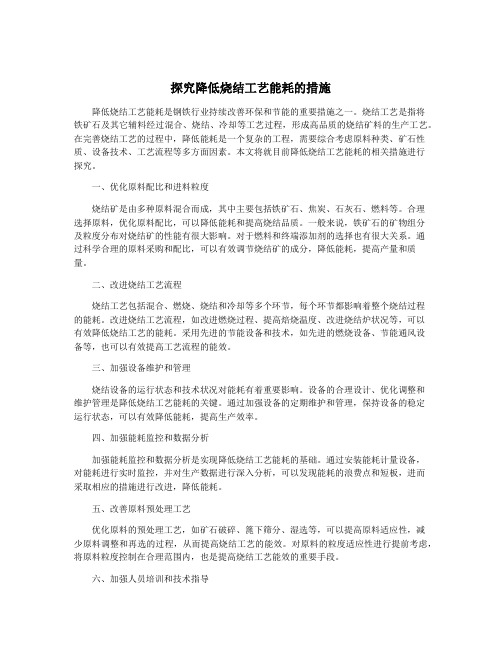
探究降低烧结工艺能耗的措施降低烧结工艺能耗是钢铁行业持续改善环保和节能的重要措施之一。
烧结工艺是指将铁矿石及其它辅料经过混合、烧结、冷却等工艺过程,形成高品质的烧结矿料的生产工艺。
在完善烧结工艺的过程中,降低能耗是一个复杂的工程,需要综合考虑原料种类、矿石性质、设备技术、工艺流程等多方面因素。
本文将就目前降低烧结工艺能耗的相关措施进行探究。
一、优化原料配比和进料粒度烧结矿是由多种原料混合而成,其中主要包括铁矿石、焦炭、石灰石、燃料等。
合理选择原料,优化原料配比,可以降低能耗和提高烧结品质。
一般来说,铁矿石的矿物组分及粒度分布对烧结矿的性能有很大影响。
对于燃料和终端添加剂的选择也有很大关系。
通过科学合理的原料采购和配比,可以有效调节烧结矿的成分,降低能耗,提高产量和质量。
二、改进烧结工艺流程烧结工艺包括混合、燃烧、烧结和冷却等多个环节,每个环节都影响着整个烧结过程的能耗。
改进烧结工艺流程,如改进燃烧过程、提高焙烧温度、改进烧结炉状况等,可以有效降低烧结工艺的能耗。
采用先进的节能设备和技术,如先进的燃烧设备、节能通风设备等,也可以有效提高工艺流程的能效。
三、加强设备维护和管理烧结设备的运行状态和技术状况对能耗有着重要影响。
设备的合理设计、优化调整和维护管理是降低烧结工艺能耗的关键。
通过加强设备的定期维护和管理,保持设备的稳定运行状态,可以有效降低能耗,提高生产效率。
四、加强能耗监控和数据分析加强能耗监控和数据分析是实现降低烧结工艺能耗的基础。
通过安装能耗计量设备,对能耗进行实时监控,并对生产数据进行深入分析,可以发现能耗的浪费点和短板,进而采取相应的措施进行改进,降低能耗。
五、改善原料预处理工艺优化原料的预处理工艺,如矿石破碎、篦下筛分、湿选等,可以提高原料适应性,减少原料调整和再选的过程,从而提高烧结工艺的能效。
对原料的粒度适应性进行提前考虑,将原料粒度控制在合理范围内,也是提高烧结工艺能效的重要手段。
- 1、下载文档前请自行甄别文档内容的完整性,平台不提供额外的编辑、内容补充、找答案等附加服务。
- 2、"仅部分预览"的文档,不可在线预览部分如存在完整性等问题,可反馈申请退款(可完整预览的文档不适用该条件!)。
- 3、如文档侵犯您的权益,请联系客服反馈,我们会尽快为您处理(人工客服工作时间:9:00-18:30)。
八钢430m2烧结降低工序能耗的实践
摘要:八钢430 m2烧结机从设计伊始就综合考虑各种节能措施,从各个工序中的固体燃耗、电耗、水耗、煤气消耗、提高混合料温度等方面阐述降低烧结工序能耗的主要途径、方法。
并总结了八钢烧结分分厂在节能降耗方面所采取的主要措施及取得的效果。
关键词:烧结混合料温度工序能耗措施
烧结工序作为钢铁冶炼的首道工序,其能耗约占钢铁生产总能耗的8~10%,降低烧结工序能耗对于提高钢铁企业的经济效益具有重要意义。
烧结工序能耗包括煤气消耗、固体燃料消耗、电力消耗、动力(压缩空气、蒸气、水等)消耗等,其中固体燃料消耗占75%~80%左右,电力占13%~20%,热能消耗约占5%~10%)。
八钢烧结厂430m2烧结机2009年进行初步设计,2010年4月开始建设,2011年7月投产,设计各项能耗指标。
为降低能耗,430m2烧结机在设计之初就采用各种节能措施,投产后通过不断的科学管理和优化,2012年烧结工序能耗不断下降,达到较好的水平。
1 降低烧结工序能耗的主要措施
1.1 烧结混匀料中配加氧化铁皮、瓦斯灰
氧化铁皮、瓦斯灰作为钢铁冶炼的固体废弃物不易处理,由于其氧化放热可以作为烧结燃料使用,既可废物利用,也能降低烧结固体燃料消耗。
因此,在烧结混匀料中按一定比例配加氧化铁皮、瓦斯灰能够降低固定碳的配加量,从而降低工序能耗。
FeO+O2=Fe2O3+Q
C+O2=CO2+Q
氧化亚铁、瓦斯灰在烧结过程中与氧气发生氧化放热反应。
1.1.1 降低固体燃料的消耗
固体燃料消耗在烧结工序能耗中占的比重最大,达75%~80%,降低工序能耗首先要降低固体燃料的消耗。
在整个烧结工艺过程,影响固体燃料消耗的因素主要有各种含铁原料的物理化学性质、混合料的温度、混合料水分、混合料的粒度组成、固体燃料的粒度组成、烧结料层厚度、生石灰消化、熔剂的性质及添加量等。
1.1.2 提高烧结混合料温度,强化制粒效果
八钢的预热装置由废加热气炉、冷风混气室,蒸气混气室、温度及流量控制系统,废气喷嘴等组成。
自制加热炉利用钢铁厂廉价煤气作为热源,煤气和空气在废气炉内燃烧产生高温废气,温度控制在1200度左右,废气进入冷风混气室,引入一定量的冷风,废气温度降低到一定的范围内,在进入蒸气混气室,使废气达到超饱和蒸气压,在逆料流
方向进入混合机。
进入混合机的是超饱和废气,温度可以达到500°以上,而且温度及流量可根据上料量进行调节,同时不会带走混合料的水分,有利于造球,热交换的效果好可达到80%以上。
(如图1)
八钢烧结厂自从新区投产以来,一直使用生石灰消化作为提高烧结混合料温度的措施强化烧结制粒效果,生石灰要求氧化钙有效成分大于85%,活性度大于310 ml,消化器长度4 m,使得生石灰消化更加充分,不仅可以提高混合料温度,减少或消除过湿层,改善料层透气性,而且生石灰消化生成的消石灰胶体颗粒有凝聚作用,有利于混合料的成球,并提高了料球强度,改善了混合料的透气性,为厚料层烧结创造了条件。
混合制粒分两段,设计时混合制粒机选型时就相对较大,一混采用20000×4000混合机,倾角2.6°,混合制粒时间2.55 min,二混配制二台20000×4000混合机,倾角1.6°,制粒时间4.14 min,通过这些方法,使送往烧结机的烧结料温度可达60℃左右,制粒后混合料中>3 mm粒级达到65%以上,为节能降耗、提高产量创造了条件。
1.1.3 厚料层烧结
八钢烧结厂430 m2烧结机台车为1500×4500×750,烧结混合料料层厚度为700 mm,在抽风烧结过程中,台车上部的烧结饼受空气急剧冷却的影响,结晶程度差,玻璃质含量高,强度差。
随着料层厚度的增加,强度差的所占的比重相应降低,成品率相应提高,返矿率下降,进而减
少了固体燃料消耗。
烧结料层的自动蓄热作用随着料层高度的增加而加强,当料层高度为180~220时,蓄热量只占燃烧带热量总收入的35%~45%,当料层厚度达到400 mm时,蓄热量达55%~60%。
因此,提高料层厚度,采用厚料层烧结,充分利用烧结过程的自动蓄热,降低烧结料中的固体燃料用量。
1.2 降低电耗
电耗在烧结工序能耗中是仅次于固体燃耗的第二大能耗,约占13%~20%,而烧结主抽风机的电耗又占烧结电耗的50%,因此,降低电耗特别是降低主抽风机电耗也是降低烧结工序能耗的重要措施。
为此,利用每次烧结检修对烧结烟道、双层卸灰阀、固定滑道、膨胀节、台车的漏风点逐一排查、焊补、更换。
定期对机头、机尾密封板检查处理。
对机头电除尘的壳体、卸灰阀、人孔门等漏风点仔细检查并焊补更换,从而减少主抽风机的漏风,降低烧结电耗。
1.2.1 汽轮机拖动主抽风机
为降低烧结电耗,430 m2烧结机主抽风机设计之初即采用汽轮机拖动,其主要的优点是:一是钢铁厂产生的各种煤气可直接用于烧锅炉,能源廉价,有利于厂内的能源循环利用;二是由于汽轮机直接推动风机,减少了由热能转化电能在电能转化机械能的中间环节,有利于节约能源。
汽轮机拖动启动和停机过程,由于汽轮运行稳定,故障率低,一般汽轮机不检修。
在烧结产线检修和故障停机时,关闭汽轮机汽门,脱开风
机与汽轮机的离合器,汽轮处于盘车状态或热机状态。
一但启动合上离合器,打开汽门就可以开机,时间较短,为了保证蒸汽的供应,八钢烧结机汽轮机用的锅炉与高炉的汽轮机锅炉共有一个备压锅炉,随时可以调节蒸汽量满足生产需足。
烧结台车和首尾风箱(密封板)、台车与滑道、台车与台车之间的漏风占烧结机总漏风量的80%以上,因此改进台车与滑道之间的密封形式,特别是首尾风箱端部的密封结构形式,可以显著地减少有害漏风,增加通过料层的有效风量,提高烧结矿产量,节约电能。
另外,及时更换、维护台车,改善布料方式,减少台车拦板与混合料之间存在的边缘漏风等,都可以有效地减少有害漏风。
1.3 使用炼钢污水替代清水降低清水消耗
钢铁行业是水资源消耗的大户,如何做好水资源的重复利用,节水减排,也是各厂节能重点工作。
炼钢污水是钢铁工业除炉渣以外产生量比较大的液体废弃物,其资源化利用水平直接影响钢铁企业资源利用率、经济效益、社会效益和环境影响。
炼钢污水理化性能因炼钢工艺、炉况的变化和除尘回收系统的不同而有所差异。
八钢430 m2烧结机配料系统设计了5000×6000×3000污水池,炼钢污水由罐车拉运倒置污水池,油污泥泵将污水定量集中配加到生石灰消化、混合机、制粒机,其主要性能见表3,主要特点是:(1)粒度细,含水量高(80%左右);(2)污水粘性强,成球性好,而且与其他物料混合后,有利于物料造球制粒;(3)TFe品位高,含有CaO、MgO等有用成分,并且碱性物含量也较
高,具有很高的再资源化利用价值,有利于提高钢铁企业提高资源利用效率。
配加炼钢污水后,基本能够满足烧结生产需要,基本不需要增加清水消耗,每天消耗量在500~600 t,而且使用炼钢污水对烧结生产有以下优点:(1)节约生产用水,降低水耗;提高烧结矿全铁品位;(2)减少污水倒运次数,减少倒运成本;(3)废物再利用,节约资源;(4)提高烧结混合料制粒效果,提高烧结产能;(5)减少污水排污,降低环境污染。
2 结语
八钢烧结分厂430 m2烧结机在设计时就考虑了在降低工序能耗上下功夫,混匀料中配加氧化铁皮、瓦斯灰,设计了加热炉、蒸汽、生石灰消化器配水幕除尘对混合料进行加热提高混合料温度及制粒效果,主抽风机采用汽动风机降低电耗,节能点火器、厚料层烧结、设备采用变频调节、充分利用炼钢污水替代清水等一系列节能降耗的手段和措施,通过这些措施2012年烧结工序能耗降低到35.5 kg/t-s。
为企业创造了较好的经济效益和社会效益。