100t EBT高阻抗交流电弧炉简介
电炉偏心炉底出钢EBT

电出钢前的炉渣是氧化性的,出钢过程中,假如这种氧化性炉渣流入钢包,会对精炼效果以及钢水质量造成不利影响:(1)降低钢包精炼渣的脱氧脱硫能力;(2)降低合金回收率,特别是会增加脱氧用铝的消耗;(3)增加对钢包包衬的侵蚀,特别是渣线部位。
1989,蒂森特钢公司与曼内斯·德马克冶金技术公司及丹麦特殊钢厂合作,开发出世界上第一座偏心炉底出钢电炉,也叫EBT(EeentrieBottomTapping)电炉。
这种电炉吸取了中心炉底出钢的经验,把底出钢口移至炉壳的一个向外突出部份。
偏心炉底出钢电弧炉的炉壳上半部仍为圆形,下半部带有突出的圆弧形出钢箱。
传统的电弧炉出钢时,一般需要把炉子倾动45°左右,才能把钢水出完。
为使钢水不接触水冷炉壁,在出钢槽铡钢水面以上400unll这一部分,仍是用耐火材料砌筑的,这是影响炉衬寿命的薄弱环节,对超高功率的电炉来讲,这个问题更为严重。
采用偏心炉底出钢技术后,出钢时炉子倾动最多仅需15度左右,可以避免钢水与水冷炉壁的接触。
这样炉衬可以大面积采用水冷炉壁,从而提高炉衬寿命。
一般采用偏心炉底出钢法,可以使电弧炉水冷壁面积从整个面积的70%~80%扩大到80%~90%。
偏心炉底出钢电弧炉炉底设计成浅盘状,以确保无渣出钢。
当钢水温度、成分达到出钢要求时,即可准备出钢。
出钢过程为:先将钢包车开到出钢箱下面;打开出钢口之前,使炉子向出钢口侧倾斜约5°,形成足够的静压力,防止炉渣从钢水产生的漩涡中流入钢包;打开出钢口盖板,开始出钢,出钢过程中,炉子渐渐地倾斜到12°,以保证出钢口上面的钢水深度基本不变。
大约排出90%钢水后,炉子就以3°/s的速度回倾到原位置,以避免或减少漂在剩余钢水上的炉渣从出钢口流进钢包。
采用ETB或RTB出钢电弧炉冶炼,可以摆脱传统的“老三期”冶炼工艺,为实现超高(或高)功率电弧炉冶炼咔炉外精炼十连铸的现代化炼钢工艺提供良好的冶炼条件。
高阻抗电弧炉的设计特点和应用
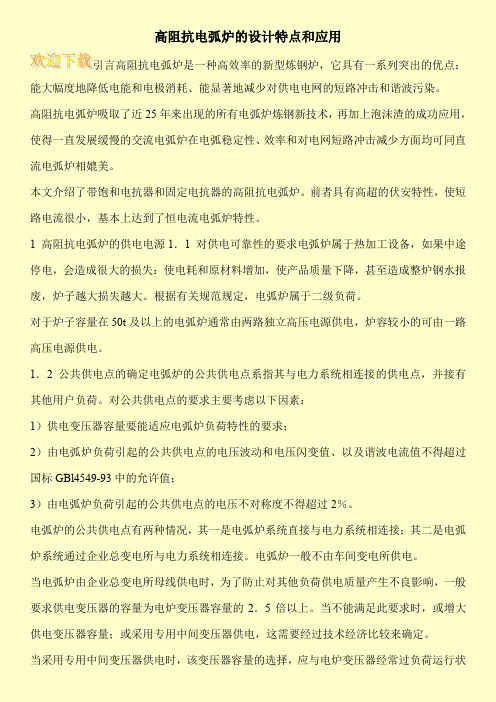
高阻抗电弧炉的设计特点和应用引言高阻抗电弧炉是一种高效率的新型炼钢炉,它具有一系列突出的优点:能大幅度地降低电能和电极消耗、能显著地减少对供电电网的短路冲击和谐波污染。
高阻抗电弧炉吸取了近25年来出现的所有电弧炉炼钢新技术,再加上泡沫渣的成功应用,使得一直发展缓慢的交流电弧炉在电弧稳定性、效率和对电网短路冲击减少方面均可同直流电弧炉相媲美。
本文介绍了带饱和电抗器和固定电抗器的高阻抗电弧炉。
前者具有高超的伏安特性,使短路电流很小,基本上达到了恒电流电弧炉特性。
1 高阻抗电弧炉的供电电源1.1 对供电可靠性的要求电弧炉属于热加工设备,如果中途停电,会造成很大的损失:使电耗和原材料增加,使产品质量下降,甚至造成整炉钢水报废,炉子越大损失越大。
根据有关规范规定,电弧炉属于二级负荷。
对于炉子容量在50t及以上的电弧炉通常由两路独立高压电源供电,炉容较小的可由一路高压电源供电。
1.2 公共供电点的确定电弧炉的公共供电点系指其与电力系统相连接的供电点,并接有其他用户负荷。
对公共供电点的要求主要考虑以下因素:1)供电变压器容量要能适应电弧炉负荷特性的要求;2)由电弧炉负荷引起的公共供电点的电压波动和电压闪变值、以及谐波电流值不得超过国标GBl4549-93中的允许值;3)由电弧炉负荷引起的公共供电点的电压不对称度不得超过2%。
电弧炉的公共供电点有两种情况,其一是电弧炉系统直接与电力系统相连接;其二是电弧炉系统通过企业总变电所与电力系统相连接。
电弧炉一般不由车间变电所供电。
当电弧炉由企业总变电所母线供电时,为了防止对其他负荷供电质量产生不良影响,一般要求供电变压器的容量为电炉变压器容量的2.5倍以上。
当不能满足此要求时,或增大供电变压器容量;或采用专用中间变压器供电,这需要经过技术经济比较来确定。
当采用专用中间变压器供电时,该变压器容量的选择,应与电炉变压器经常过负荷运行状。
100t电弧炉炉壁氧枪技术
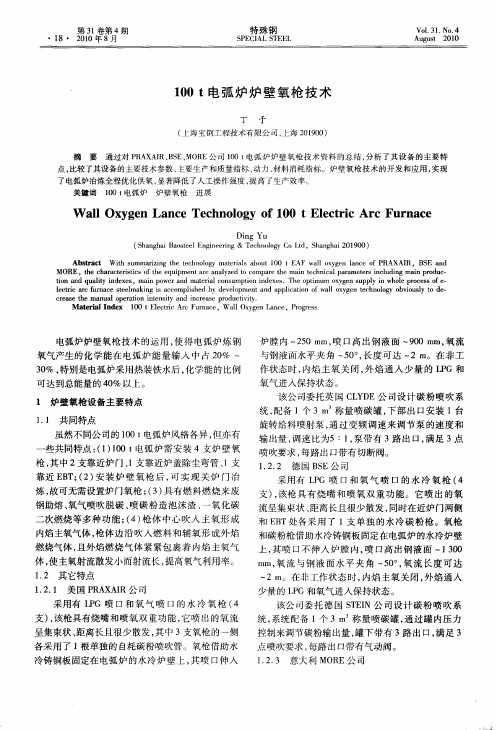
电弧炉 炉壁 氧枪 技术 的运用 ,使 得 电弧 炉 炼 钢 炉 膛 内 ~250 mm,喷 口高 出钢液 面 一900 mm,氧 流
氧气产 生 的化学 能在 电弧炉 能 量 输 人 中 占 20% ~ 与 钢液面水 平夹 角 一5O。,长度 可 达 一2 m。在非 工
Abstract W ith summarizing the technology m aterials about 100 t EAF wall oxygen lance of PRAXAIR , BSE and MORE ,the characteristics of the equipment are analyzed to cmnpare the main technical parameters including main produc— tion and quality indexes,m ain power and material consumption indexes. The optimum oxygen supply in whole process of e— lectf ic arc furnace steelmaking is accomplished by development and application of wall oxygen technolog y obviously to de- crease the m anual operation intensity and increase productivity.
采 用有 LPG 喷 口和 氧 气 喷 口 的 水 冷 氧 枪 (4 支 ),该 枪 具 有烧 嘴 和 喷 氧 双 重功 能 。它 喷 出 的氧 流呈集 束状 、距 离长且很 少散发 ,同时在 近炉 门两侧 和 EBT处各 采 用 了 1支 单 独 的水 冷 碳 粉枪 。氧枪 和碳 粉枪借 助水冷 铸铜板 固定在 电弧炉 的水 冷炉壁 上 ,其 喷 口不 伸人 炉 膛 内 ,喷 口高 出钢 液 面 ~1 300
电弧炉炉体及EBT机构介绍

电弧炉炉体及EBT机构介绍
电弧炉炉体装置一般由炉壳、炉门机构、(出钢槽)、和偏心底EBT机构等组成。
其中炉壳分为上下两部份,即上炉壳与下炉壳。
上炉壳由20g无缝管材焊接而成的园筒形框架结构件,其内壁悬掛有数量不等的无缝管材组成的水冷壁,形成密闭环筒。
水冷板渣线以上部分用钢管制造,水冷板采用独立的水冷。
其与水冷炉盖落下接触后形成一个密闭箱体。
水冷结构上部焊有导向板,便于炉盖对中,使出钢时炉盖不移动。
下炉壳由20g材质钢板组焊为底部球面体结构件。
有工艺要求的还设置了偏心底出钢位置。
下炉壳下部外侧有定位法兰通过定位销固定于倾动平台上。
四个耳轴用于炉壳的吊装。
上下炉壳也通过一组定位销联结定位。
炉渣门机构采用水冷盘管形式(门框及炉门),均安装在上部炉壳上。
通过一个液压缸驱动传动链条来带动渣门上下运动。
该液压缸采用水冷液压缸。
在偏心底出钢口上方的偏心盖上,设置了偏心底出钢口填沙装料装置。
偏心底出钢机构依靠液压缸驱动。
由驱动水冷油缸、旋转轴、接近开关等组成。
在EBT处于关闭位时,设置机械锁定机构,防止因误操作打开EBT,造成跑钢,角度旋转仪控制出钢前后倾动角度。
EBT检修通道一般采用移动式小车,通过电机——减速器——链条传动,运行平稳,无卡阻,便于维修。
EBT检修通道运动由本地操作。
下表为30吨电弧炉炉壳的典型参数。
100吨直流电弧炉烟气净化系统综述

100吨直流电弧炉烟气净化系统综述2000’年第1期大重科技1o0吨直流电弧炉烟气净化系统综述王晓明摘要介绍了我国自行设计制造的100吨超高功率直流电弧炉烟气净化系统,采用第二孔+密闭罩和,屋顶罩切换+LF炉的排烟方式.长袋低压脉冲袋式除尘器净化工艺. 1概述国外现代化电炉炼钢厂普遍采用大容量超高功率(UHP)电炉,炉外精炼,连铸,连轧等先进技术集合的高效短流程工艺,电炉变成了只承担加热,熔化和脱磷的初炼设备.在吹氧强化冶炼的基础上,超高功率等先进技术的应用,使电弧炉的冶炼时间缩短到1小时左右,电炉的发烟量及产尘量随之大增.伴随电弧炉冶炼技术的发展,电炉除尘技术亦日趋完善,直流电弧炉是一种新式炉型,在全世界仅有几十座投入生产,继上海第三钢铁厂,宝钢,苏兴特殊钢公司引进国外直流电弧炉同时配套引进电炉除尘设备之后,上钢五厂又最新引进一套德国直流电弧炉设备,除尘系统及设备均由国内自行设计和制造,于1997 年3月建成投产,运行近三年,各项指标均达到甚至超过设计值.2除尘系统工艺设计2.1除尘系统及设计参数100吨直流电弧炉除尘工艺流程见图1.排烟方式采用第二孔+密闭罩和屋顶罩切换+LF炉,主要以第二孔内排和密闭罩集烟为主,在出钢加料时使用屋顶罩集烟,此时密闭罩打开,整个除尘系统与电炉冶炼工况同时用计算机联机自动控制.电炉吹氧时从炉盖第二孔抽出的炉气..——44.-——量设计值为27500Nm/h,炉气温度为1400℃,经水冷滑套缝隙混入空气燃烧,再经火花捕集器后烟气量增加到110000Nm/h,烟气温度降到500℃~800℃,进入强制机力吹风冷却器后烟气被冷却到200℃左右.随后第二孔烟气与钢包炉排出的烟气以及大密闭罩,屋顶罩排出的烟气混合.各支路混合前的烟气量和烟气温度分别为:电炉第二孔ll0000Nm./h.200℃密闭烟罩400000Nm0/h,70℃屋顶烟罩460000Nm0/h,50℃钢包炉45000Nm/h,160℃混合后总烟气量854390Nm3/h,温度<13O℃混合烟气经两台并联长袋低压大型脉冲除尘器过滤后,进入离心风机最终排入大气,排放烟气含尘浓度≤20mg/Nm3,过滤后的灰尘经刮板输送机,斗式提升机送入储灰罐,定期外运.2.2除尘系统的主要特点2.21炉盖第二孔水冷却弯头排烟炉内排烟系统采用炉盖第二孔水冷弯头排烟,使炉内烟气抽出,进入燃烧室. 2.2.2环形水冷滑套用于控制第二孔水冷弯头与水冷烟道之间的空气进入量.间距根据出炉烟气温度,CO含量等一次性调好.烟气与管外新鲜空气混合,进入燃烧室充分燃烧,防止可燃气体进入除尘器发生爆炸及造成二次污染,另外空气使烟气温度降至一定温度.2.2.3火花捕集器炉内排烟的水冷管道内烟气流速约40m/s,为避免烟气中的火星进入袋式除尘器烧毁滤袋,在风冷器前设置了火花捕集器,消除烟气中的火花,同时在这里沉降大颗粒烟尘.———]匦一排放十匦卤图1除尘系统流程图火花捕集器由两个简体组成.简体之右.间设有带叶片的导流装置.烟气先进入内2.2.6防爆阀及野风阀部简体,在筒体下部经导流装置汇入主管为防止事故(爆炸)时损坏设备,炉内道.大颗粒烟尘落入下部集灰斗,由卸灰排烟系统在燃烧室侧壁,冷却器入口以及阀卸灰,定时用车运出.管道适当位置均安装防爆阀.此外,在机2.2.4机力风冷器,力风冷与内排烟风机之间,袋式除尘器入由十二台轴流通风机对内排烟气进行口前均设有野风阀,以确保进入除尘器烟强力吹风冷却,使烟气温度由550℃左右气温度<130℃.降至200℃以下.2.2.7长袋低压大型脉冲袋式除尘器2.2.5设置内排烟风机烟气净化采用长袋低压大型脉冲袋式因第二孔炉内直排烟系统阻力损失除尘器,分24单元,每单元216条滤袋,滤大,在机力风冷器后设一台增压风机,与总袋规格为120X6000mm,有效过滤面积排烟风机进行接力排烟,这样比采用一台11580m,过滤风速1.38~1.50m/riain,离总排烟风机排烟,系统节省能耗26%左线脉冲喷吹,喷吹压力0.2MPa.设备运一45—行阻力1z00~1600Pa,定压清灰后设备阻力降至600~700Pa,由各单元的u型管压力计亦可读出阻力值.电脑控制系统采用BMC一4型袋式除尘器电脑控制柜,主机为日本三菱公司可编程控制器,配备温度,压差,位置等传感器件,主要功能如下.(1)除尘器清灰控制(停风清灰)有定压差控制和定时控制两种方式,可转换;,(2)进口烟气温度监测,数字显示;(3)除尘器进,出口压差监测,数字显示;(4)脉冲间隔时间,清灰箱体号,脉冲阀号数字显示;(5)每一仓室停风阀开,关位置检测,到位发光管显示;(6)进口烟气温度超限(上限及下限)报警,停风阀故障声光报警.2.2.8采用大型调速风机机组内排烟风机与两台并联的系统总排烟风机均分别与液力耦合器组成大型调速风机机组,采取变负荷调速运行机制,具有如下优越性.(1)电机与风机间为无机械柔性传动,电机可以空载启动,避免了对电网的冲击,又缩短了启动时间;(2)可使风机无级平滑调速,对电机和风机都起到保护作用;(3)隔离和吸收振动,减缓机械冲击;(4)便于对并联同时运转的两台风机进行负载精调,使系统的运行参数均衡稳定;(5)具有极为明显的节电效果,节电率大于30%.2.3除尘系统的监测与控制2.3.1.为保证除尘系统安全运行,设若干个温度,压力测点.经变送器计算机控制系统与相关设备联锁.一46一(1)温度测点.分别设在燃烧室入口;风冷器前后;内排烟风机前;大密闭罩,屋顶烟罩,LF炉烟气管路;除尘器入口前. 一旦温度超过设定值,则打开管道上的野风阀,混入冷风降低烟气温度,必要时移动水冷滑套,加大混风间隙的面积,增加混风量,使烟气温度降低.(2)压力检测点.分别设在燃烧室前;机力风冷前后;风机入口和除尘器入口. 如压力值不正常,操作画面上将出现报警信号,此时操作员将对系统设备的工作状态进行检查,排除故障.2,3.2内排烟风机,除尘主风机均设有轴承温度,轴承振动,电机绕组温度监测装置.风机的液力耦合器设有油温,油压测点.除尘器输灰系统的回转下料器,螺旋输送机,斗式提升机的减速电机均设有转速监测装置.运行中一旦某个部位出现故障,将在计算机画面上发出报警信号并显示出故障部位.2.3.3电炉第二孔+密闭罩排烟,屋顶罩排烟和钢包炉排烟合为一个排烟系统.为保证电炉,钢包炉的排烟效果,同时减少系统的总抽气量,并达到节约电耗的目的,设计了系统总排烟量控制系统.该系统的控制信号取自电炉,钢包炉工艺设备上的限位开关,并代表冶炼工艺的某种操作状态. 通过屋顶罩排烟管道的多叶调节阀,钢包炉排烟管道蝶阀开度的调节以及主风机转速的变化,来实现系统总排烟量的调节,风机转速的变化是由调节液力耦合器来实现的.虽然控制系统复杂,但是通过阀门和风机转速的调节,使除尘系统的运行能耗降低.2.3.4除尘器输灰系统的启动与滤袋的清灰联锁.输灰系统启动按与输灰方向相反的顺序依次进行.若其中某一台设备运(下转第51页)3.2在特殊情况下,如絮凝效果不理想,可适当加大絮凝剂投入量.4结论用复合絮凝剂处理油脂工业废水工程自竣工并投入使用以来,从运行效果看达到了设计要求,废水中油去除率达到94%以上,物理感观如透明度,色素,气味等都有明显改善,外排水PH值在5~8之间,达国家规定的排放标准.对回收的上浮物进行综合利用,制取洗涤皂粉,年产约300吨,可获得一定的经济效益.该工程的实施,对今后处理同类废水提供了技术借鉴.该方法适合于去除油脂工业废水中的油含量,如要将此类废水中GOD去除,需采用生物法加以治理,具体方法有待进一步研究.参考文献1.刘永凇,杨润昌等着.工业废水处理工程.1983.2.顾夏声,黄铭荣.王占生等编着.水处理工程.清华大学出版社,1985.3.井出哲夫等编着.张自杰等译.水处理工程理论与应用.中国建筑工业出版社,1986.4.美国梅特卡夫和埃迪公司.废水工程处理, 处置及回用.第二版.化学工业出版社,1986.5.许保玖编.当代给水与废水处理原理讲义.清华大学出版社.1983.(上接第46页J转不正常,将在计算机画面上显示并报警,输灰系统立刻停止运行.3运行效果经测试,系统风量可达967019m3/h,较设计值提高20%以上,其它测试指标如下: 除尘器漏风率3%粉尘排放浓度12rag/m3电炉炉前平台粉尘浓度7mg/m3电炉炉前平台噪声(密闭罩关)97dB(A)吨钢收尘量X5kg/吨钢系统投入使用后,排烟和除尘效果均良好,在整个冶炼周期内,集烟率很高,电炉操作平台上保持着良好的操作环境.参考文献1.于辉海.国外UHP电炉除尘和新进展.大连特殊钢.1995(5)2.陈隆枢.长袋低压脉冲袋式除尘器净化炼钢电炉烟气的问题探讨.冶金环保情报.1997(4)3.孙一坚.简明通风设计手册.中国建筑工业出版社.199r7.4.国家环境保护局.铜铁工业废气治理.中国环境科学出版社,1992.一51—。
100t高阻抗电弧炉的自动化控制系统

100t高阻抗电弧炉的自动化控制系统
卢海燕;韩星
【期刊名称】《数字通信世界》
【年(卷),期】2007(0)4
【摘要】介绍了采用西门子公司PCS7系统为核心的高阻抗电弧炉自动化控制系统,主要包括有高阻抗电弧炉的主要设计技术参数,控制系统的硬件设计方案及组成,自动化系统的软件设计功能和主要控制对象,按照铸造生产对控制系统的要求,将整个系统划分为若干个控制子单元分别进行功能描述,详细说明了各部分的控制范围及目的,使得该套高阻抗电弧炉的控制系统能够在铸造生产的过程中全面实现工业现代化的操作、监控、信息处理和检修维护,保障了铸造生产设备的安全运行。
【总页数】4页(P754-757)
【作者】卢海燕;韩星
【作者单位】中国人民解放军西安通信学院基础部;西安华兴电炉有限公司技术中心
【正文语种】中文
【中图分类】TG232.3
【相关文献】
1.国产首座100t高阻抗电弧炉研制与生产运行实践 [J], 吴遵生;彭海利;王卫红;陈德明;郭冬实;陈皑
2.100t高阻抗炼钢电弧炉短网电抗的计算 [J], 刁理选
3.100t高阻抗电弧炉泡沫渣工艺分析与优化 [J], 卢斌
4.100t电弧炉短网阻抗特性分析 [J], 薛娜;吕明;吴龙
5.首台国产100t高阻抗电弧炉投产 [J],
因版权原因,仅展示原文概要,查看原文内容请购买。
电弧炉

炉子结构同炼钢电弧炉相似。工作时,电极下端埋在炉料内起弧,除电极与炉料间的电弧发出热量外,电流 通过炉料时炉料电阻也产生相当大的热量。这类电弧炉主要用于矿石的冶炼,因此又称矿热炉。
主要特点
电弧炼钢炉以电能为主要能源。电能通过石墨电极与炉料放电拉弧,产生高达2000 ~ 6000℃以上的高温, 以电弧辐射、温度对流和热传导的方式将废钢原料熔化。在炉料熔化时的大部分时间里,高温热源被炉料所包围, 高温废气造成的热损失相对较少,因此热效率高于转炉等其他炼钢设备。此外,电加热容易精确地控制炉温,可 以根据工艺要求在氧化气氛或还原气氛、常压或真空等任何条件下进行加热操作。
常见
三相 自耗
单相 电阻
这种电弧炉用三相交流电为电源,一般用碳素电极或石墨电极。电弧发生在电极与被熔炼的炉料之间,炉料 受电弧直接加热。电弧长度靠电极升降调节。为提高熔炼质量,大型电弧炉在炉底装有电磁搅拌器,驱使炉内熔 螎金属沿一定方向循环。50吨以上的电弧炉常装有炉体回转机构,炉体能左右旋转一定角度,使炉料受热均匀, 金属液出炉时炉体可以倾斜。三相电弧炉广泛用于炼钢。
可以生产钢种
电弧炼钢炉的原料主要是固体的废钢并配加合金料、调整碳含量用的生铁等,也可以使用直接还原铁或配一 部分热铁水,原料的选择范围广阔;因此,除一些超低碳品种钢,或者必须采用诸如真空处理等特殊手段的品种、 特殊合金材料之外,大部分钢种几乎都可以冶炼。
谢谢观看
电弧炉
电炉
01 介绍
03 分类 05 主要特点
目录
02 发展简史 04 常见 06 可以生产钢种
电弧炉(electric arc furnace)利用电极电弧产生的高温熔炼矿石和金属的电炉。气体放电形成电弧时 能量很集中,弧区温度在3000℃以上。对于熔炼金属,电弧炉比其他炼钢炉工艺灵活性大,能有效地除去硫、磷 等杂质,炉温容易控制,设备占地面积小,适于优质合金钢的熔炼。
高阻抗电弧炉的电气特性

电弧炉冶 炼 所 需 的 电 能 是 通 过 主 电 路 输 入 炉 内 的。从高压电缆到电极的电路称为电弧炉的主电路, 主 电 路 主 要 由 隔 离 开 关 、高 压 断 路 器 、变 压 器 及 低 压 短 网 等 几 部 分 组 成 ,如 图 1 所 示 。
第 3 期 (总 第 172 期 ) 2012 年 6 月
机械工程与自动化 MECHANICAL ENGINEERING & AUTOMATION
文 章 编 号 :1672-6413(2012)03-0175-02
No.3 Jun.
高阻抗电弧炉的电气特性研究
顾秀萍
(山 西 工 程 职 业 技 术 学 院 , 山 西 太 原 030009)
高压电 网 6kV~10kV 的 高 压 电 能 经 过 隔 离 开 关和高压断路器送 至 电 炉 变 压 器 的 一 次 侧 (高 压 侧), 然后通过 变 压 器 转 变 为 低 电 压、大 电 流 输 送 到 电 极。 当电极电流超过允许 值 时,断 路 器 会 自 动 跳 闸 切 除 电 源线路。在变压器的 高 压 侧 配 有 电 压 调 节 装 置,可 进 行无载或有载调压,以 满 足 不 同 工 况 的 电 压 需 要。 短 网是指电弧炉变压器二次侧的引出线至电弧炉电极之 间 的 一 段 三 相 线 路 ,它 由 铜 排 (或 铜 管 )、软 电 缆 和 炉 顶 上的导电铜管3部分组成。短网的正确设计不仅可使 三相电功率不平衡度 降 低,而 且 有 利 于 短 网 装 置 的 维 护和降低电能损失。 2 高 阻 抗 电 弧 炉 的 电 气 特 性
- 1、下载文档前请自行甄别文档内容的完整性,平台不提供额外的编辑、内容补充、找答案等附加服务。
- 2、"仅部分预览"的文档,不可在线预览部分如存在完整性等问题,可反馈申请退款(可完整预览的文档不适用该条件!)。
- 3、如文档侵犯您的权益,请联系客服反馈,我们会尽快为您处理(人工客服工作时间:9:00-18:30)。
~6300kg
3 800mm 最大 1200m3/h 最大 1800m3/h 最大 1200m3/h 0.3~6m/min 3mm
喷粉速度
氧气压力
15~60kg/min
最大 1.5 M Pa
炉壁碳氧枪机构:一支氧枪,最大流量20Nm3 /min;一支碳枪。皆可单独控制
炉体剖面图
EBT出钢口图
炉体主视图
轻废钢 生铁 重废钢 钢屑
电炉进料
进料前炉底先铺加1~2%(料重)的石灰,以便保 护炉底和及早成渣(新炉、冷炉与垫炉后除外)。 将料篮吊至炉体上方,高度为料篮底与炉体上沿大 致为同一平面,料篮中心与炉子中心相重合,快速 打开蛤式料篮,切勿碰撞炉壁水冷板。装料后,若炉 料超高,可用料篮压平凸起钢铁料,但要小心谨慎, 不得挤压水冷炉壁,并避免料篮脱钩。料篮吊走后, 炉沿挂有废钢时,必须清除,炉盖方可旋回,禁用 炉盖推料或压料。多次装料,每次均要切电,因炉 内存有大量的钢液,料筐要抬的更高些,这样既可 避免粘坏料筐,又可减少火焰与钢液的任意喷射与 飞溅,同时还要防止爆炸,潮湿的炉料严禁进入多 次装料的料筐中。
无渣出钢和留钢留渣
无渣出钢的提出,与采用炉外精炼技术后,要求实现无渣出钢,以满足炉外精 炼的还原条件,便于炉外精炼的正常进行有关。而真正实现无渣出钢,归功于 偏心炉底出钢的应用。采用偏心炉底出钢技术实现无渣出钢,则必然导致留钢 留渣。 无渣出钢避免了电弧炉内的氧化性炉渣随着钢水进入钢包内,为下一步进行炉 外精炼进行脱硫、脱氧及合金化创造非氧化条件,从而提高精炼炉内脱硫、脱 氧效果,提高合金收得率,利于钢种化学成分的稳定。无渣出钢杜绝了炉内氧 化性炉渣进入钢包内,从而避免了氧化渣对钢包衬的侵蚀,从而提高包衬的寿 命;还可以减少精炼时加入的造渣量,从而有利于钢包吹氩和搅拌强度的提高。 留钢留渣操作一般在出钢后有10%~ 15 %的钢水和几乎全部的炉渣留在炉内。 这样为下一炉的启弧创造了有利的条件,十分便于启弧操作,从而加速熔化。 同时留下的氧化渣为熔化初期的脱磷创造极有利的条件。此外,通电前在炉底 即有液态熔池存在,提早形成熔池,可以大大提高启弧阶段电弧的稳定性,尽 早且有效的进行吹氧,从而增加炉内功率,提高功率因数,改善对供电系统的 干扰。同时也减少电弧光对炉体的侵蚀。
36.5
37.6 38.7 39.8 41.0 42.3 43.7 45.2 46.8 48.5
50
15
16
716
750
40318
38490
炉门自耗式碳氧枪机构
几何尺寸,不包括枪的导向系统(长×宽×高) ~ 5740×2400×2800
重量
枪的数量(氧枪×2,碳枪×1) 旋转臂升降距离(Max) 氧气流量(1.5MPa) 氧气流量(1.2MPa) 枪管的给进速度 碳粉最大尺寸
100tEBT电弧炉的优点
EBT电炉由于倾动角度小,短网短,因此炉体结构 简单且能降低电的损耗。由于钢流短而成直线状, 所以可降低出钢温度10 ~ 20 ℃,这对于减少出钢 过程的吸气量和减少炉衬被侵蚀而引起的夹杂带入 量十分有利,因此钢液比较纯净。偏心炉底的无渣 出钢,可为炉外精炼提供优质钢液。而留钢留渣操 作,能将10%~ 15 %的钢水和几乎全部的炉渣留在 炉内,这样大大地缩短了下一炉钢铁料的熔化时间, 同时还为早期脱磷创造了良好的条件。又由于炉壁 的水冷面积达到90%,不仅利于超高功率电炉的长 弧操作,而且也节省了大量的耐火材料。
100t电炉供电曲线
800 700 600 547 500
电压/V
50000 716 716 48000 716 716 48000 633 547 45000 48000 46000 44000
45000
547
48000
45000
400 42000 300 200 100 0 起弧 穿井 熔化 起弧 冶炼阶段 穿井 熔化 氧化 氧化末 40000 40000 40000 38000 36000
电流/A
10~ 16档 587
10~ 16档 587 633V
10~ 16档 587
10~ 12档 587
50000 48000 45000
~ 633V 550V
~ 550V
~ 633V 550V
~ 633V 633V
40000
20~ 3 0 N m 3 /M in
35000
8~ 10
2 .0 N m 3 /M in
常规: 15° 最大: 20°
常规: 10° 最大: 15°
60
变压器基本参数
级 数 电 压(V) 电 流(A) 功 率(MW)
1
2 3 4 5 6 7 8 9 10 11 12 13 14
442
455 468 482 496 512 529 547 566 587 610 633 658 686 47324 45604 43872 42081 47700
要得到泡沫渣,需要: A大量CO气体。包括碳与溶解氧的反应、碳与渣中FeO 的反应。当熔池中碳含量达0.25%至0.30%时,泡沫渣才 能形成,因此需要向渣中喷碳粉来满足条件。 B渣子的物化性能,包括高的粘度和低的表面张力。 性能合适的渣可以在气泡产生速度较慢的情况下快速形成泡 沫。否则就只能在熔池中气泡生成较块时才能形成泡沫。熔 池形成后,加足石灰,造好泡沫渣,保持高碱度2.5~3.0左右, 熔化期尽早脱磷。渣子化开后,喷入碳粉,熔渣泡沫化。视 炉内具体情况调整主氧枪枪位,适时喷碳粉,造好泡沫渣。
100t电弧炉基本技术参数
额定容量 (t) 最大出钢量 (t) 残留钢水 量 (t) 变压器 额定容量 (KVA) 石墨电 极直径 (mm) 极心圆 直径 (mm) 出钢倾 动角度 (°) 出渣倾 动角度 (°) 炉盖旋出 角度(°)
100
120
20~25
50000 (+20%)
φ500
φ1250
炉体俯视图
100t电弧炉基本操作流程
进料前各类检查与准备 第一篮进料 通 电
吹氧助熔
第二篮进料
通电、吹氧助熔
吹氧升温、造泡沫渣、去磷
取样、测温
出钢和钢包合金化
电炉的配料配料成分控制按源自下规定(除重要钢种按专用工艺 外): 配碳:碳素钢及锰结构钢应保证熔清后含碳量高 于成品上限0.40~0.60%。配料中P≤0.050%、 S≤0.060%。 熔清后Cu、Ni、Mo应小于该钢种规定。 废钢的技术要求加工废钢最大尺寸不大于 600×600×600(mm);重料废钢单块重量 ≤1000kg 铁合金和辅助原材料均按工艺要求严格配制
电炉的装料
装料规定:专职人员应根据大、中、小料有计划、按顺序装料。先把部分小料装在料 桶底部,然后装入全部大料(最大料应装在中下部),最后余下的全部装中小料。装 料应密实,力求一次装实,尽量减少进料次数。装料后,炉内料应上疏松,中间高, 四周低。大块料不可装在出钢口及炉门口处,不可装在最上面,返回料尽量不要装在 电极下。 力求做到:准确无误、装的致密、布料合理且快速入炉。 第一料篮用轻薄料打底,中小型废钢为主,重料要装在料篮中下部,生铁或电极 块装在重料下部。 第一篮料重为总炉料重的60~65%,但总重不得大于64吨。 第二篮以轻型废钢小型废钢为主,占总重量的35~40%。 生铁配入30%。 原则上二次料,如需三次料,装入量:一次料45%,二次料35%,三次料20%。 钢屑 布料方式图如下:
冶炼过程
供电制度
通电,起弧阶段:电压第8~10档547~587V,电流
35000~4000A,电抗第3档投入55%或第4档投入70%。 熔化阶段:供电8分钟左右,供电曲线调整为电压第10~ 16档587~750V,电流40000~48000A。电抗第3~5档 投入55%~85%。 氧化阶段:大部分炉料熔清后,供电曲线调整为电压 10~12档587~633V,根据磷含量调整电流40000~ 48000A,切除电抗。
2 .0 N m 3 /M i n 8~ 10
2 .0 N m 3 /M in 8~ 10
1 5 ~ 6 0 k g /m in
30000
档 547 ~ 587V
8 m in
氧气压 力控制 在 ≥ 1 .2 M p a , 压 缩空气 ≥ 0 .6 M p a
档 547 ~ 587V
8 m in
档 547 ~ 587V
供氧制度
氧气压力控制在≥1.2Mpa,压缩空气≥0.6Mpa。根据熔清
碳含量,决定碳氧枪操作。主氧枪氧气流量设定在20~ 30Nm3/Min。炉壁氧枪保护气流量设定在2.0Nm3/Min左 右,熔化期流量设定10~15 Nm3/Min,氧化期可视炉内 熔清碳含量设定炉壁氧枪10~20 Nm3/Min。氧化期脱碳 量规定:碳钢、碳结构钢≥0.30%,合金钢≥0.40%。 对于冷炉子,一次料通电20~25分钟可以开启小氧枪助 熔,二次料10~15分钟可以开启小氧枪助熔。如果为热 炉子,小氧枪可以视炉内情况提早开启助熔。
8 m in
纵坐标为电流值,蓝色曲线上标明输入电压值,输入功率为二者成积。图中阴影区为电流 可调节范围,根据钢液温度灵活掌握。蓝色曲线为供氧制度,黄色曲线为喷碳制度。
泡沫渣
长电弧和提高生产能力所需的高的比功率在应用时,如果电极周围没有 废钢就需要用其它手段将电弧埋起来。由此产生了泡沫渣技术的应用, 这项技术获得了大量的正面效果: 增加输入炉内的功率和热效率,且大幅度减少辐射到炉衬的热负荷, 并有利于炉壁热负荷的均匀化。比不采用泡沫渣的热效率提高30%。 同时可以快速升温,达4 ~ 7 ℃/Min ; 降低了电极消耗; 减少了电弧对耐火材料的辐射,从而降低单位了电能消耗;目前电 耗可达440KVh/Min ; 降低了水冷板的消耗; 电弧产生的辐射被渣吸收; 由于电弧稳定,从而增加了平均功率; 泡沫渣埋弧操作包裹电弧,降低电弧产生的噪声10 ~20db; 生成富-CO环境; 可 以进行长弧操作。