全面生产性维护
TPM全面生产维护
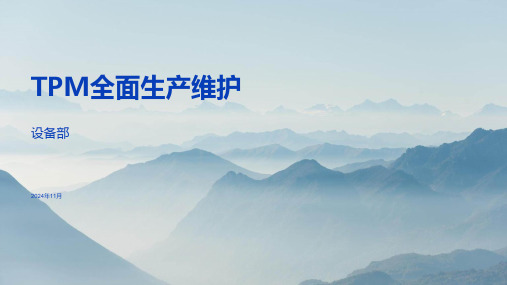
TPM的发展史
1 事后维修 (BM :Breakdown Maintenance)
故障后再维护 1950年以前
2 改良维修 (CM : Corrective Maintenance )
查找薄弱部位对其进行改良 1950年以后
3 预防维修 (PM :Preventive Maintenance)
对周期性故障提出的维护 1955年前后
6 全面生产维护 (TPM: Total Productive Maintenance)全员参加型的保养
1980年以后
5 生产维修 (PM: Productive Maintenance) 综合上述维护方法,系统的维护
方案 1960年前后
4 维修预防
(MP: Maintenance Prevention)
TPM的主要手段——OEE
• TPM使用的主要手段名为设备综合效率 (OEE: Overall Equipment Effectiveness )
• 这个数字与六大损失相关联:
• 1.故障/停机损失
(Equipment Failure / Breakdown Losses)
• 2.换装和调试损失 (Setup and Adjustment)
• 3.空闲和暂停损失 (Idling and Minor Stoppage Losses)
• 4.减速损失
(Reduced Speed Losses)
• 5.质量缺陷和返工 (Quality Defects and Rework)
ቤተ መጻሕፍቲ ባይዱ
• 6.启动损失
(Startup Losses)
• 三个可测量:时间开动率、性能开动率和合格品率。
• 质量缺陷和返工(Quality Defects and Rework)
TPM全生产性维护相关知识

TPM全生产性维护相关知识什么是TPM?•TPM,全称为Total Productive Maintenance,中文意为全生产性维护,是一种供应链管理技术,旨在提高设备可靠性和生产效率的一种方法。
•TPM源自于日本的制造业,最初由日产汽车公司引入,并在20世纪80年代由日本生产管理专家中村治郎提出。
•TPM的目标是通过消除故障、停机时间和生产过程中的浪费,实现设备的最大正常运行时间,从而达到高效的生产。
TPM的原则和目标原则TPM的原则基于以下几个核心概念:1.没有故障:设备保持良好的工作状态,并且不会发生任何故障。
2.零故障:通过预防性维护和故障预测来消除故障的可能性。
3.全面参与:全体员工都参与到设备的维护中,且设备操作人员也是维护专家。
4.持续改进:不断寻找和消除导致故障和浪费的根本原因,实现生产流程的不断改进。
目标TPM的目标主要包括以下几个方面:1.提高设备可靠性:通过预防性维护和故障预测,减少设备故障的发生和停机时间,提高设备的可靠性和稳定性。
2.提高设备使用效率:通过最大限度地减少设备故障和停机时间,实现设备的持续运行,提高生产效率。
3.减少浪费:通过分析生产过程中的各种浪费,如停机时间、材料损耗等,寻找并消除根本原因,从而提高整体生产效率。
4.培养员工技能:通过设备维护的培训和培养,提高员工的技能水平,使其成为设备维护和操作的专家。
TPM的基本步骤准备阶段1.召开启动大会:在这个会议上,公司领导向全体员工阐述TPM的原则、目标和重要性,并明确各个部门的责任。
2.设立TPM委员会:成立由各部门经理和代表组成的TPM委员会,负责制定和执行TPM计划。
3.建立TPM培训计划:制定培训计划,培养员工的技能和意识,以便他们能够有效地参与到设备的维护中。
4.记录设备现状:对所有设备进行评估和记录,包括设备的性能、运行状况和维护记录等。
故障消除阶段1.制定设备维护计划:根据设备的维护需求和生产计划,制定设备的维护计划,并明确各个维护任务的责任人和时间。
TPM全面生产性管理

TPM全面生产性管理概述TPM(Total Productive Maintenance,全面生产性维护)是一种管理方法,旨在通过所有员工的参与和积极的协作,实现生产设备的高效运行和最小化故障率。
这种管理方法中,所有员工都承担责任,不仅负责设备的正常运行和维护,还负责预防故障和提高生产效率的工作。
TPM的目标是通过实施与设备保养和性能改善相关的一系列措施,提高生产设备的可靠性、质量和产能。
TPM的原则TPM的核心原则是通过最小化七大损失来提高设备效能和生产效率。
这七大损失包括:1.设备故障和停机时间的损失2.调整和改装的损失3.停机损失4.下线和速度损失5.质量损失6.批审和返工的损失7.原材料和能源的损失TPM强调通过减少这些损失来提高生产效率,以确保设备始终处于最佳状态,从而最大限度地提高生产能力。
TPM的实施步骤1. 创建执行团队TPM的成功实施需要有一个执行团队来领导和推动整个过程。
这个团队应该由各个部门的代表和具有实施TPM经验的员工组成。
团队负责设定目标、制定计划并监督整个实施过程。
2. 制定实施计划在创建执行团队之后,需要制定一个详细的实施计划。
这个计划应该明确列出每个步骤的时间表、责任人和具体的实施方法。
计划必须根据实际情况进行调整,并确保所有员工都能理解和接受这个计划。
3. 培训和教育为了确保所有员工都能正确理解和实施TPM,必须进行培训和教育。
这种培训可以包括理论知识、实际操作和案例分析等内容。
培训还应该由经验丰富的员工来传授,并与实际工作相结合,以提高培训效果。
4. 制定标准和指导方针在实施TPM的过程中,必须制定一些标准和指导方针,以保证每个员工都按照规定的方法进行工作。
这些标准和指导方针可以包括设备维护的操作程序、故障排除的步骤和性能改善的技术要求等。
5. 实施设备维护活动设备的维护是TPM的重要组成部分。
这些维护活动可以包括日常保养、预防性维护和纠正性维护等。
实施这些维护活动的目的是确保设备始终处于最佳状态,并最大限度地减少故障和停机时间。
精益生产之全面生产维护

精益生产之全面生产维护1. 引言在现代制造业中,为了追求更高的效率和更好的品质,企业普遍采用了精益生产方法。
精益生产以减少浪费和提高价值创造能力为核心,通过全面的生产维护来实现这一目标。
本文将介绍精益生产中的全面生产维护的概念、原则和实施步骤。
2. 全面生产维护的概念全面生产维护(Total Productive Maintenance,简称TPM)是精益生产中的一项重要策略,旨在通过全员参与和持续改进,最大限度地发挥设备的效能,提高设备的可靠性和稳定性,以实现持续生产和不断提高生产效率。
3. 全面生产维护的原则全面生产维护的实施需要遵循以下原则:3.1 以预防为主全面生产维护的核心思想是预防维护,而不是传统的事后维修,即提前检测和排除潜在故障,避免设备故障对生产造成影响。
3.2 全员参与全面生产维护需要全员参与,包括设备操作人员、维修人员和管理人员等。
每个人都应对设备的维护负责,通过培训和奖励机制,激发全员参与的积极性。
3.3 KPI导向全面生产维护的目标是提高生产效率和设备可靠性,因此需要制定明确的关键绩效指标(Key Performance Indicators,简称KPI),对维护工作进行衡量和持续改进。
3.4 持续改进全面生产维护是一个持续改进的过程,通过不断的反馈和学习,及时修正和改进维护计划和操作方法,以最大限度地发挥设备的潜力。
4. 全面生产维护的实施步骤实施全面生产维护需要经过一系列的步骤,以下是其中的几个关键步骤:4.1 制定维护策略和计划根据设备的特点和工艺要求,制定相应的维护策略和计划。
维护策略包括预防性维护、修复维护和改进维护等,维护计划要考虑到设备的维护周期和生产需求。
4.2 培训和教育进行全员培训和教育,使每个员工都了解设备的基本原理、操作方法和维护要点。
培训内容应包括设备故障排查、常见故障处理和维护记录等。
4.3 设备的改造和改进对设备进行必要的改造和改进,以提高设备的稳定性和可靠性。
全面生产维护的作用
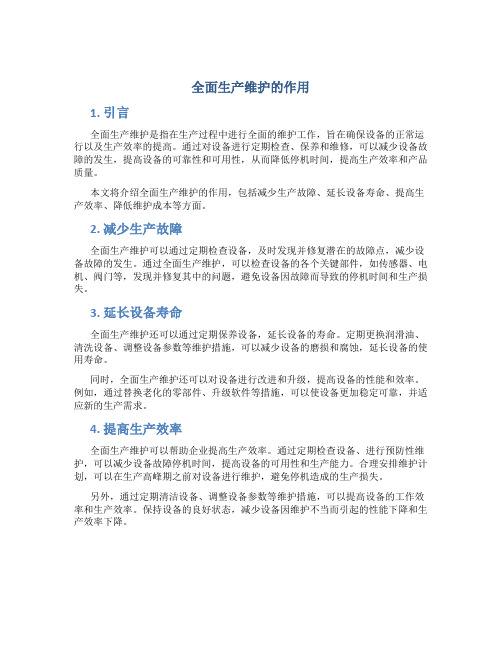
全面生产维护的作用1. 引言全面生产维护是指在生产过程中进行全面的维护工作,旨在确保设备的正常运行以及生产效率的提高。
通过对设备进行定期检查、保养和维修,可以减少设备故障的发生,提高设备的可靠性和可用性,从而降低停机时间,提高生产效率和产品质量。
本文将介绍全面生产维护的作用,包括减少生产故障、延长设备寿命、提高生产效率、降低维护成本等方面。
2. 减少生产故障全面生产维护可以通过定期检查设备,及时发现并修复潜在的故障点,减少设备故障的发生。
通过全面生产维护,可以检查设备的各个关键部件,如传感器、电机、阀门等,发现并修复其中的问题,避免设备因故障而导致的停机时间和生产损失。
3. 延长设备寿命全面生产维护还可以通过定期保养设备,延长设备的寿命。
定期更换润滑油、清洗设备、调整设备参数等维护措施,可以减少设备的磨损和腐蚀,延长设备的使用寿命。
同时,全面生产维护还可以对设备进行改进和升级,提高设备的性能和效率。
例如,通过替换老化的零部件、升级软件等措施,可以使设备更加稳定可靠,并适应新的生产需求。
4. 提高生产效率全面生产维护可以帮助企业提高生产效率。
通过定期检查设备、进行预防性维护,可以减少设备故障停机时间,提高设备的可用性和生产能力。
合理安排维护计划,可以在生产高峰期之前对设备进行维护,避免停机造成的生产损失。
另外,通过定期清洁设备、调整设备参数等维护措施,可以提高设备的工作效率和生产效率。
保持设备的良好状态,减少设备因维护不当而引起的性能下降和生产效率下降。
5. 降低维护成本全面生产维护还可以降低企业的维护成本。
通过定期检查设备、及时维修和更换设备零部件,可以减少设备故障所造成的维修费用和停机损失。
同时,合理安排维护计划,可以减少维护操作的时间和人力成本。
此外,通过对设备进行预防性维护,及时发现并解决潜在问题,可以防止设备在使用过程中发生更大故障,减少更换设备的成本。
6. 结论全面生产维护对于企业的生产运行非常重要。
全员生产性维护(一)
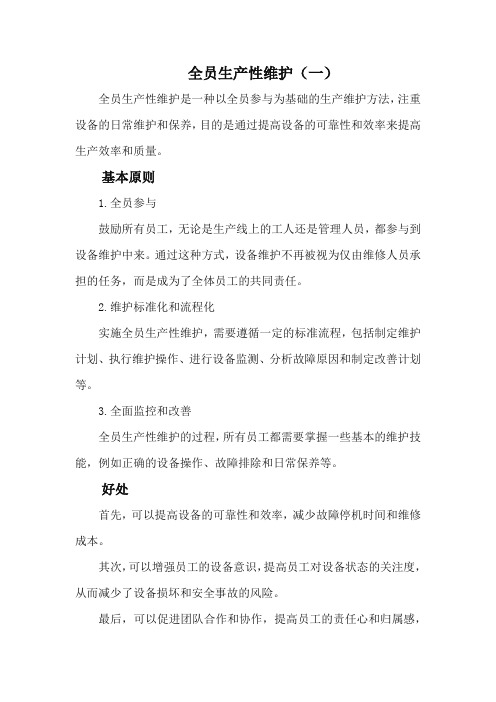
全员生产性维护(一)全员生产性维护是一种以全员参与为基础的生产维护方法,注重设备的日常维护和保养,目的是通过提高设备的可靠性和效率来提高生产效率和质量。
基本原则1.全员参与鼓励所有员工,无论是生产线上的工人还是管理人员,都参与到设备维护中来。
通过这种方式,设备维护不再被视为仅由维修人员承担的任务,而是成为了全体员工的共同责任。
2.维护标准化和流程化实施全员生产性维护,需要遵循一定的标准流程,包括制定维护计划、执行维护操作、进行设备监测、分析故障原因和制定改善计划等。
3.全面监控和改善全员生产性维护的过程,所有员工都需要掌握一些基本的维护技能,例如正确的设备操作、故障排除和日常保养等。
好处首先,可以提高设备的可靠性和效率,减少故障停机时间和维修成本。
其次,可以增强员工的设备意识,提高员工对设备状态的关注度,从而减少了设备损坏和安全事故的风险。
最后,可以促进团队合作和协作,提高员工的责任心和归属感,从而提高整个企业的生产力和竞争力。
关键因素在全员生产性维护的实施过程中,需要注意几个关键因素:第一,需要建立一个有效的维护体系,包括制定明确的维护标准和流程、培训员工掌握维护技能、建立设备档案和记录设备运行数据等。
第二,需要建立一个有效的监测机制,包括定期进行设备检查和监测、建立设备健康状况评估体系、及时发现设备故障和潜在风险等。
第三,需要制定一个有效的改善计划,包括针对设备故障原因制定相应的改善措施、推广最佳实践和经验教训等。
总而言之,全员生产性维护是一种以全员参与为基础的生产维护方法,旨在提高设备可靠性和效率、增强员工的设备意识和责任心、促进团队合作和协作等。
只有通过全体员工的共同努力和积极配合,才能够有效实施全员生产性维护,达到提高企业生产效率和质量的目标。
TPM基础知识介绍
TPM基础知识介绍TPM(Total Productive Maintenance,全面生产维护)是一种以最大限度提高设备设施稼动率为目标的维护管理手段。
它通过预防性维护、设备维护等一系列措施,最大限度地降低生产线故障率和设备损坏,实现全面生产效能的提升。
TPM起源于20世纪60年代的日本,由日本工业界倡导和推广。
它的核心理念是通过员工参与和团队合作,将设备故障率降到最低,达到生产效率的最大化。
TPM在实施过程中注重预防性维护、设备维修和设备管理,以提高设备的可靠性和稼动率,减少停机时间和生产缺陷。
TPM的目标是实现设备的稳定运行,降低故障率和维修次数,减少停机时间,提高生产效率和质量,降低成本和资源浪费。
它强调预防性维护,通过定期检查和保养设备,及时发现和排除潜在问题,避免设备故障和生产线停机。
此外,TPM还强调减少设备损耗,通过改进设备的设计和操作方法,延长设备的使用寿命,减少维护投入和成本。
TPM的实施需要综合考虑团队管理、设备管理和维护管理等多个方面。
其中,团队管理是关键,它涉及到员工的参与和归属感。
TPM鼓励员工参与设备维护和管理活动,培养员工对设备的责任和关注,提高员工技能和意识,形成团队协作的氛围。
设备管理方面,TPM强调设备状态的监测和管理,通过维护计划、定期检查和设备改进来确保设备的可靠性和稳定性。
而维护管理涉及到故障排除、维修保养和备件管理等工作,需要有专业技术和维护流程的支持。
在TPM实施过程中,可以采用一些工具和方法来辅助管理。
比如,OEE(Overall Equipment Efficiency,全面设备效能)是衡量设备绩效的重要指标,它综合考虑设备的开机时间、生产速度和生产合格率,用以评估设备的稼动率和效率。
通过对OEE进行分析,可以找出设备运行中存在的问题和改进的空间,制定相应的措施和改进方案。
此外,还可以运用维护保养计划(Maintenance Plan)、故障模式与效应分析(Failure Mode and Effects Analysis,FMEA)等工具来管理设备的运行和维护。
全面生产维护管理体系讲义
全面生产维护管理体系讲义1. 引言全面生产维护(Total Productive Maintenance,TPM)是一种维护和管理生产设备的方法论,通过最大限度地发挥设备的效能,实现高效生产和高质量产品。
全面生产维护管理体系则是为了有效实施TPM而建立的一套管理体系。
本讲义将介绍全面生产维护管理体系的基本原理、实施步骤和关键要点。
2. 全面生产维护管理体系的基本原理全面生产维护管理体系的基本原理是:以设备为中心,通过预防性维护、故障预测和故障排除,实现设备的高效运行和长期稳定性。
全面生产维护管理体系的核心思想是“设备操作者负责设备维护”。
3. 全面生产维护管理体系的实施步骤全面生产维护管理体系的实施步骤包括以下几个阶段:3.1 制定实施计划在制定实施计划阶段,应明确全面生产维护的目标和范围,确定实施的时间和地点,制定详细的实施计划,明确责任人和工作内容。
3.2 建立设备档案在建立设备档案阶段,应对每台设备进行全面的调查和分析,建立设备档案,包括设备的基本信息、生产能力、维护记录等。
3.3 培训设备操作者在培训设备操作者阶段,应对设备操作者进行培训,使其熟悉设备的基本原理、操作要点和故障排除方法等,并具备一定的维护能力。
3.4 开展预防性维护在开展预防性维护阶段,应制定预防性维护计划,对设备进行定期检查和保养,以减少故障发生的可能性,并延长设备的使用寿命。
3.5 实施故障预测和故障排除在实施故障预测和故障排除阶段,应建立故障预测和故障排除的机制,通过设备状态监测和故障数据分析,及时发现潜在问题并进行处理。
3.6 持续改进持续改进是全面生产维护管理体系的重要环节,通过持续改进,不断提高设备的效率和稳定性,进一步优化生产过程。
4. 全面生产维护管理体系的关键要点全面生产维护管理体系的关键要点包括以下几个方面:4.1 设备操作者的参与设备操作者应积极参与全面生产维护活动,负责设备的日常维护和保养工作,并及时反馈设备运行情况。
实行全面生产性维修以稳定生产过程
实行全面生产性维修以稳定生产过程引言随着工业生产的不断发展,设备和机械的维护保养变得愈发重要。
在生产过程中,设备故障和停机时间常常会导致生产成本的增加和生产效率的下降。
为了稳定生产过程,实行全面生产性维修是一种有效的措施。
本文将介绍全面生产性维修的概念、意义以及实施的步骤和注意事项。
什么是全面生产性维修?全面生产性维修是一种针对设备和机械的维护保养策略,旨在保持设备的正常运行状态和生产能力。
它强调将维修活动纳入生产过程中,实现无缝切换和持续运行。
全面生产性维修不仅局限于设备的修复和维护,还包括预防性维护、计划性停机时间以及维修技术的提升和培训等方面。
全面生产性维修的意义1.提高生产效率:全面生产性维修可以减少设备停机时间,避免由于设备故障造成的生产中断。
通过定期检查和维护,可以提前发现和解决潜在问题,从而确保设备的正常运行,提高生产效率。
2.降低生产成本:设备故障和停机时间不仅会增加维修费用,还会导致生产计划的延误和订单的推迟交付。
全面生产性维修可以减少这些因素的影响,降低生产成本。
3.增强产品质量:设备故障和不良维护可能导致产品质量下降。
通过全面生产性维修,可以保持设备的良好状态,减少产品质量问题,提高客户满意度。
4.增加员工安全和职业健康:设备故障可能会对员工的安全和健康造成威胁。
通过全面生产性维修,可以及时发现和解决设备安全隐患,确保员工的安全和职业健康。
实施全面生产性维修的步骤1. 制定维修计划首先,制定全面生产性维修的计划。
根据设备的种类和数量,制定维修的周期和频率。
重要的设备可以考虑制定更频繁的维修计划,而次要设备则可以考虑更灵活的维修计划。
2. 建立维修团队成立专业的维修团队,包括设备维护人员、工程师和相关技术人员。
确保团队成员具备良好的技术能力和维修经验,并进行定期培训,以适应不断变化的技术和设备。
3. 实施预防性维护在全面生产性维修中,预防性维护是非常重要的一环。
建立设备的保养清单和保养标准,定期对设备进行检查和保养,以预防潜在故障的发生。
tpm全面生产维护
tpm全面生产维护TPM全面生产维护,也就是全面生产维护,是一种灵活的、持续的、系统性的生产维护手段,也是一种优化生产流程,提升企业生产效率和质量的方法。
TPM的目标是全面消除设备故障,实现设备的高效率、高可靠性、高质量运行,并且让设备在整个生命周期内最大程度地发挥作用。
一. TPM全面生产维护的概念TPM全面生产维护是以人、机、料、法、环境五个要素为核心,以实现设备的高效率、高可靠性、高质量以及最大程度地发挥作用为目标,通过维护、保养、修理、改善等手段,实现设备和生产效率的最优化。
TPM全面生产维护着重强调对设备的全面管理,在这个过程中,不仅保证设备顺畅运转以达到高产、高效的生产水平,同时也要提倡工艺流程的不断完善与提高。
这种全面生产维护方法是通过充分发挥工人个人能力、实现设备新旧转换、提高设备利用率、促进质量管理和生产计划逐步的执行,从而在生产流程中消除浪费以及缩短设备故障时间。
TPM全面生产维护的实施,不仅是制造企业走向优质、高效的必经之路,也是“机器蓝领”转换为“机器白领”的途径。
二. TPM全面生产维护的优点1. 提高生产效率: TPM全面生产维护强调定期点检和效益检查,可以减少设备故障率,尽可能保证设备工作的稳定性和效率。
这不仅可以减少损失,还可以减少停机时间,提高生产效率。
2. 提高质量水平: TPM全面生产维护通过优化制造流程和提高设备可靠性,可以减少生产过程中的浪费,提高产品的质量水平。
这可以有效地减少不良品率,提高客户满意度。
3. 提高设备利用率: TPM全面生产维护可以优化设备的性能,延长设备的使用寿命,降低设备的维修费用和停机时间,进而提高设备利用率。
4. 增加工人的参与和责任: TPM全面生产维护要求员工全面参与维护工作,不仅提高员工的素质,还能够提高员工的责任感和自我管理能力。
5. 实行精益生产管理: TPM全面生产维护可以实现精益生产管理,加强管理和工艺流程的优化,从而使生产流程更加有效率。
- 1、下载文档前请自行甄别文档内容的完整性,平台不提供额外的编辑、内容补充、找答案等附加服务。
- 2、"仅部分预览"的文档,不可在线预览部分如存在完整性等问题,可反馈申请退款(可完整预览的文档不适用该条件!)。
- 3、如文档侵犯您的权益,请联系客服反馈,我们会尽快为您处理(人工客服工作时间:9:00-18:30)。
LEAN Practitioner Program
Total Productive Maintenance 全面生產性維護
Belton Confidential
‹#›
Lean Tools 精益工具
Lean Overview 精益概述 Change M & Waste E 改變觀念&消除浪費 Performance Metrics 績效指標 Value Stream Mapping 价值流程圖 Visual Management 目視管理 Error Proofing 防錯法 SMED / Quick Changeover 快速切換 TPM 全面生產性維護 Layout Optimization/Cell 布局優化/Cell Material Control 物料控制 Theory Of Constraints 瓶頸理論 Lean Diagnostic 精益診斷
作員”到“設備是我職責的一部分”
Equipment problems are opportunities for improvement
設備的問題也就是改善的机會
Belton Confidential
‹#›
Training 培訓
To develop a knowledgeable operator 培養有見識的員工
‹#›
Belton Confidential
Introduction 介紹
1980s TOTAL PRODUCTIVE MAINTENANCE
全面生產性維護
“Productive Maintenance with Total Employee Participation”
“全面維護,全員參与”
1970s PRODUCTIVE MAINTENANCE
加強團隊合作和相互關系
Value of Autonomous Maintenance 自主維護的价值 Change of work culture from “I can only operate this machine” to
“machine is a part of my duty” 改變工作文化,從“我是這台設備的操
•Cost 成本
More Effective Use of Manpower Reduced Maintenance Costs Reduced Energy Costs
•Quality 品質
Reduced Defects in Process Reduced Customer Claims
•Morale 士气
Improve Quality 改善品質 Reduced Cycle Time 降低周期時間 Reduce Speed Loss 降低速度損耗 Reduce Equipment Maintenance Cost 降低設備維修成本 Improve team work and cross functional relationship
There are many tools and techniques in the Lean „tool box‟, all suited to different applications and circumstances. 在LEAN工具箱中有許多工具和技巧,它們可以用于各種不同的情況.MAINTENANCE Breakdown 事后維護 “停机維修”
The importance of excellent „asset stewardship‟ is now recognized by the world‟s leading manufacturing companies as a critical success factor. 卓越的固定資產管理目前已被世界領先的制造公司作為一個關鍵的成功因素
Belton Confidential
‹#›
How to achieve Autonomous Maintenance 如何達到自主維護
5S Management 5S管理
Visual Management 目視管理
Standardized Work 標准化作業 Equipment operation skill enhancement
所有毛病和故障都須維修員來處理
It's your problem!!
All equipment have faults and failures
New attitude 新的態度 We share responsibility for caring of our machine, as if they are extensions of our limbs and arms
這些簡單的問題怎樣預防?
To make manufacturing an active partner with process engineering and maintenance for improving overall performance of machines
將生產部變成PE和ME的積极伙伴來改善機器的總效能
我們要分擔責任來看護機器﹐把機器當作我們的四肢
Belton Confidential
‹#›
Benefits of Atuonomous Maintenance 自主維護的好處
Benefits of Autonomous Maintenance include 自主維護的好處
Improve Productivity 提高生產力
清洁和檢查不是員工的責任
all equipment will eventually give faults and failure
所有設備終究會有毛病和故障
all faults and failures of equipment can be rectified by maintenance
Belton Confidential
‹#›
什么是全面生產性維護(TPM)?
Total Productive Maintenance or TPM in short is a concept of optimizing equipment effectiveness through total employee involvement 全面生產性維護(簡稱TPM)是通過全員參与來改善 机器一生的總性能. TPM aims to reduce statistical variability on equipment by improving the equipment performance in order to achieve a more robust and predictable process TPM目的在于改善机器的 績效,降低机器的統計波動, 來達到更可靠的工序.
‹#›
Training Objectives 培訓目的
After completion of this training you should be able to 完成此課程后妳應該能夠:
Understand what TPM is 理解TPM是什么
Have an overview of Autonomous Maintenance activities 有自主維護的概念 Understand Equipment Losses 理解設備損失 Able to focus on equipment improvement using OEE 能用OEE來關注設備的改善
提高設備操作技術
Break down barriers 打破障礙 High level maintenance management 高水平維護管理
Ownership responsibility 主人翁精神 Transfer of PM activities to operator 員工參与技術性的維護活動 All employees involved 全員參与
部門相當于同一輛車上的輪子
Operator 操作員
Maintenance 維修員
‹#›
Belton Confidential
Change Attitude 態度改變
Dramatic change in attitude 在態度上的戲劇性變化 Old attitude 老的態度 it is no the operator„s responsibility to perform cleaning and inspection
生產性維護
“Recognition of Equipment Maintenance Issues at Plant Design Stage”
“在設計階段強調設備維護”
1960s PREVENTATIVE MAINTENANCE
預防維護 “I operate...you fix””我操作...你維修”
Production, maintenance & engineering crew support each other and understand how their roles interact in order to work towards Zero Breakdown, Zero Accident, Zero Defects 生產﹑維修和工程的同事互相支持﹐理解相互的職責﹐共同達 到零故障﹑零事故﹑零不良﹒
How equipment functions? 設備怎么運作? What common problem occurs? 什么樣的常見問題發生?
How to detect problems through five senses/feeling?
怎樣通過五官/感覺來發現問題?
That there is something „FUNNY‟? 有趣嗎? why and how those simple problems can be prevented?