尺寸精度设计与检测
精密注塑件尺寸精度的解决方案

精密注塑件尺寸精度的解决方案尺寸精度是评估注塑件质量的重要指标之一。
在精密注塑件创造过程中,尺寸精度的控制对于保证产品质量、满足客户需求至关重要。
本文将介绍精密注塑件尺寸精度的解决方案,包括工艺优化、模具设计和设备控制等方面。
一、工艺优化1. 材料选择:选择合适的注塑材料对尺寸精度的控制至关重要。
根据产品要求和工艺特点,选择具有较低收缩率和较好稳定性的材料,如工程塑料。
2. 注塑工艺参数控制:合理的注塑工艺参数对于尺寸精度的控制至关重要。
包括注射速度、保压时间、模具温度等参数的控制。
通过试模和优化参数,确保注塑过程中的温度、压力和流动速度的稳定性,以保证产品尺寸的一致性。
3. 模具温度控制:模具温度的控制对于精密注塑件的尺寸精度具有重要影响。
通过模具温度控制系统,确保模具温度均匀稳定,避免温度差异引起的尺寸偏差。
二、模具设计1. 模具结构设计:合理的模具结构设计对于尺寸精度的控制至关重要。
包括模腔设计、冷却系统设计等。
通过优化模腔结构,减少应力集中和变形,提高注塑件的尺寸精度。
同时,合理设计冷却系统,确保注塑件在冷却过程中均匀受热,避免尺寸变形。
2. 模具材料选择:选择合适的模具材料对尺寸精度的控制也非常重要。
高硬度、高强度的模具材料可以减少模具的磨损和变形,提高注塑件的尺寸精度。
3. 模具加工精度:模具加工精度对于注塑件尺寸精度的控制至关重要。
通过提高模具加工精度,减小模具尺寸偏差,从而提高注塑件的尺寸精度。
三、设备控制1. 注塑机控制:合理的注塑机控制对于尺寸精度的控制至关重要。
包括注射速度、保压时间、压力控制等。
通过调整注塑机参数,确保注塑过程中的温度、压力和速度的稳定性,以保证注塑件尺寸的一致性。
2. 检测设备控制:使用合适的检测设备对注塑件尺寸进行在线监测和控制。
通过实时监测注塑件尺寸,及时调整工艺参数,保证产品尺寸的稳定性。
3. 数据分析与优化:通过采集和分析注塑过程的数据,找出影响尺寸精度的关键因素,并进行优化。
机械精度设计及检测19第11章尺寸链的精度设计基础
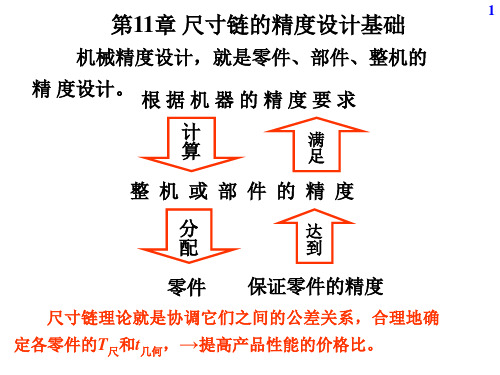
偏差 为
A1
101
0.35 0
A2
50
0.25 0
A3
A5
50 0.048
⑤ 用中间计算方法计算A4的上、下偏差 ES0 ESA1() ESA2() 2EIA3() EI A4()
EIA4() ESA1() ESA2() 2EI A3() ES0
0.35 (0.25) 2(0.048) (0.75)
A3
(4) 校核计算结果
19
∵ ES0=-0.01 , EI0=-0.08 (A1=Φ70 ,
T0 ES0 EI0 = 0.07
41
Ti TA1 TA2 TA3
i 1
2
2
= 0.02+0.03+0.02 = 0.07
3
T0 Ti 0.07
1
∴ 计算无误,则壁厚
A2/2 A0
A2=Φ60 A3=0±0.01)
Ai 的方向与封闭环A0
的方向相同为Ai (-) 。
图11.4尺寸链图
由图可见: A1为A1() , A2、A3为A2()、A3()
例11.2 加工顺序(见图11.5):
9
(1)镗孔A1,(2)插键槽A2,(3)磨内孔A3。 解:(1)按加工顺序画尺寸链图。oA3/2 A1/ Nhomakorabea A2 A0
(2)
判断
对包容面(即孔): 下偏差为零(EI=0)。
如
Φ30
对被包容面(轴): 上偏差为零(es=0)。
Φ30
29
例11.7 图11.10为对开齿轮箱的一部分。 A0=1~1.75, A1=101、A2=50、A3=A5=5、A4=140。 计算各组成环的公差和上、下偏差。
零件尺寸的检测方式

13.2 计量器具的选择
13.3 光滑极限量规的设计
2020/7/3
13.1 概述
13.1.1 检测的两种方式
1. 采用普通计量器具 用有刻线的量具测量得到被测几何量的实际尺 寸;根据该尺寸是否超越零件极限尺寸,来判断尺寸 的合格性。如游标卡尺、千分尺、各种指示表和比较 仪等。 2. 采用极限量规 指没有刻线的专用测量工具,是按被测工件的两 个极限尺寸制造的,用它们与被测的孔与轴进行比较 。这种用于检验零件孔、轴的量规,成为光滑极限量 规。检验孔时,量规做成外尺寸形状,成为塞规;检 202验0/7/轴3 时,量规做成内尺寸形状,成为环规或卡规。
误收会影响产品质量, 误废会造成经济损失,为 防止误收并控制误废率, 更好地保证产品质量和降 低生产成本,必须正确地 确定验收极限和选择计量 器具。 2020/7/3
13.2 计量器具的选择
13.2.1 验收极限和安全裕度A
检验工件尺寸时判断合格与否的尺寸界限 。验收方案: 1.内缩方案 验收极限是从工件规定的最大和最小极限 尺寸分别向工件公差带内移动一个安全裕度A来确定。
偏向的一边,按单项内缩方式确定。
dmax A轴上验收极限来自公差带
下验收极限
Dma
x
上验收极限
孔
公
差
下验收极限
带
A
Dmin
dmin
4)对于非配合尺寸和一般公差的尺寸,其验收极限
2020/7/3
按不内缩方式确定。
13.2 计量器具的选择
13.2.2 计量器具的选择
1.计量器具选用的原则
1)被测件的结构特点:按被测工件的外形、位置、 和尺寸的大小及被测参数的特点来选择计量器具,使选 择的计量器具的测量范围能满足工件的要求。所选测量 器具的测量范围必须大于被测尺寸。对硬度低、材质软 、刚性差的零件,一般选取用非接触测量,如用光学投 影放大、气动、光电等原理的测量器具进行测量。
尺寸的公差、配合与检测

一、基准制的选用
基准制的选用原则: (1)一般情况优先选用基孔制 优点:减少孔的定值尺寸,从而减少定值刀具、量具的规格和数量。 (2)特殊情况选用基轴制 1)冷拉钢轴与相配件的配合
冷拉标准轴,尺寸、形状很准确,表面微观形貌精度也很高,外圆表面 不再加工即可使用。
2)轴形标准件与相配件的配合 3)一轴配多孔且各处松紧要求不同的配合,图3-16。 (3)精度不高且需经常装拆的情况允许采用非基准制,图3-17。
三、有关配合的术语及定义 3、配合公差
三、有关配合的术语及定义
4、配合制
①
配合制 同一极限制的孔和轴组成配合的一种制度称为 配合制。GB/T1800.1-1997规定了两种配合制度:基孔 制配合和基轴制配合。 基孔制配合 基本偏差为一定的孔的公差带与不同基本 偏差轴的公差带形成各种配合的一种制度。基孔制中的 孔为基准孔,其下偏差为零,代号H。 基轴制配合 基本偏差为一定的轴的公差带与不同基本 偏差孔的公差带形成各种配合的一种制度。基轴制中的 轴为基准轴, 其上偏差为零,代号h。
孔 ES=Dmax -D
孔 EI=Dmin -D
轴 es=dmax -D
轴 ei=dmin -D
下偏差 最小极限尺寸减其基本尺寸所得代数差。 极限偏差 上偏差和下偏差的通称。 实际偏差 实际尺寸减其基本尺寸的代数差。 孔Ea=Da -D;轴ea=da-D。 基本偏差 在极限与配合制中,用以确定公差带相对于零线位置的上偏差或下偏 差,数值均已标准化,一般为靠近零线的那个极限偏差。
Da,da表示
孔和轴的实际尺寸的合格条件分别为: Dmin≤Da≤Dmax ;dmin≤da≤dmax
一、有关孔、轴和尺寸的术语及定义
二、有关尺寸偏差、公差的术语及定义
尺寸的检测方法

尺寸检测1.轴类尺寸的检测方法方法一:量规法用量规检测轴径,不能得到具体数值,只能检测轴径尺寸合格与否。
其优点是精度高、检验效率高,在成批生产中广泛使用。
方法二:钢尺法直接用钢直尺进行测量,或者使用卡钳将工件尺寸与钢直尺进行比较。
方法三:卡尺法使用游标卡尺、千分尺、杠杆千分尺等对轴径进行直接测量。
方法四:测微仪法用各种测微仪、测微表与量块进行比较测量。
常用的测微仪(表)有百分表、千分表、扭簧比较仪、电感比较仪等。
方法五:仪器测量法可以用光学计、测长仪、工具显微镜等对轴径进行精密测量。
在工具显微镜上又分为影像法、轴切法、干涉法、灵敏杠杆法等。
在光学计、测长仪上测量可以分为绝对测量和相对测量。
立式光学计测量:用立式光学计测量工件外径,是按照相对测量法进行测量的。
先用组合好的尺寸L的量块组,将仪器的刻度尺调到零位。
再将被测工件放到测头与工作台面之间。
从目镜或投∆,那么被测工件的外径尺寸影屏中可以读出被测工件外径相对于量块组尺寸的差值L+=。
d∆LL⑴测头的选择测头有球形、平面形和刀口形三种。
根据被测零件的几何形状来选择,使测头与被测表面尽量满足点接触。
因此,测量平面或圆柱面时,选用球形测头;测量球面工件时,选用平面形测头;测量小于10mm的圆柱形工件时,选用刀口形测头。
⑵按被测工件外径的基本尺寸组合量块为了减少量块组合的累积误差,应力求使用最小的量块数,一般不超过4块。
每选择一块量块,至少要消去所需尺寸的最末一位数。
量块的正确使用:①选择量块,用竹夹子从量块盒里夹出所需用的量块;②清洗,首先用干净棉花擦洗,再用蘸上汽油的棉花擦洗,最后用绸布把汽油擦干;③组合,首先要搞清量块的测量面。
组合量块时要注意:大尺寸量块在中间,小尺寸量块放在两边,这样的量块组较稳固,而且变形较小。
⑶调整仪器零位①将量块组放置于工作台的中央,并使测头对准量块测量面的中央;②粗调节,松开横臂紧固螺钉,旋转粗调节螺母,直到目镜中看到标尺像,锁紧横臂紧固螺钉;③细调节,松开光管紧固螺钉,旋转微调手轮,从目镜中看到零位指示线,对准零位,锁紧光管紧固螺钉;拨动几次提升器,若此时零位指示线仍偏离零位线,则旋转零位调节手轮,使零位指示线准确对准零位;④抬起提升杠杆,取出量块。
产品尺寸检测报告

产品尺寸检测报告1. 引言此报告旨在对产品的尺寸进行全面的检测和分析。
通过对产品尺寸的测量和比较,可以评估产品制造过程中的精度和一致性,并提供改进产品设计和生产的建议。
2. 检测范围本次尺寸检测覆盖了产品的关键尺寸。
在此过程中,我们使用了专业的测量设备和技术,确保测量结果的准确性和可靠性。
3. 检测方法以下是我们使用的主要检测方法:3.1 直尺测量直尺测量是最基本的测量方法之一。
我们使用高精度的直尺对产品的长度、宽度和厚度进行测量,并记录测量结果。
3.2 卡尺测量卡尺测量是一种常用的精确测量方法。
我们使用数字卡尺对产品的直径、孔径和深度等尺寸进行测量,并记录测量结果。
3.3 高精度测量仪对于一些需要更高精度的尺寸测量,我们使用高精度测量仪,例如投影仪和三坐标测量机。
这些设备可以提供更准确和详细的尺寸数据,确保产品的精度要求得到满足。
4. 检测结果经过精确的尺寸测量,我们得到了以下的检测结果:尺寸测量值(mm)允许误差(mm)长度100.05 ±0.1宽度50.02 ±0.05厚度10.01 ±0.02直径60.00 ±0.1孔径 5.00 ±0.05深度20.10 ±0.1平行度0.05 ±0.02垂直度0.03 ±0.02圆度0.02 ±0.01注:以上数据仅为示例,并非实际测量结果。
5. 结论通过对产品尺寸的全面检测,我们得出以下结论:•产品的尺寸和形状符合设计要求,满足制造标准。
•大部分尺寸的测量结果接近设计要求,并在允许误差范围内。
•少数尺寸的测量结果偏离设计要求,超出允许误差范围。
这可能是由于制造过程中的误差导致的。
6. 建议和改进基于本次尺寸检测的结果,我们提出以下建议和改进措施:•对于尺寸超出允许误差范围的产品,需要对制造过程进行进一步的分析和调整,以提高尺寸的精度和一致性。
•在制造过程中加强对尺寸测量的控制,确保产品尺寸的稳定性和可靠性。
基于机器视觉的零件尺寸检测与测量系统设计

基于机器视觉的零件尺寸检测与测量系统设计随着工业生产的发展,对零件的质量与精度要求越来越高,而传统的人工尺寸检测与测量方法已经无法满足这些要求。
因此,基于机器视觉的零件尺寸检测与测量系统应运而生。
本文将针对这一问题进行探讨。
一、介绍机器视觉技术是一门利用计算机视觉进行模式识别、目标检测和三维重建等方面的技术。
基于机器视觉的零件尺寸检测与测量系统利用计算机视觉技术,可以实现对零件尺寸的高精度检测与测量。
二、系统设计1. 摄像设备选择在设计基于机器视觉的零件尺寸检测与测量系统时,首先需要选择合适的摄像设备。
一般来说,高分辨率的摄像头能够提供更精确的检测结果。
2. 图像采集与处理图像采集是系统中的核心环节之一,通过摄像设备采集零件的图像,并对图像进行处理,提取出需要检测的特征。
图像处理算法可以采用边缘检测、二值化、滤波等方法,以提高图像的清晰度和信噪比。
3. 特征提取与分析在图像处理的基础上,需要进一步提取出零件的特征信息。
可以通过边缘检测算法提取零件的轮廓信息,或者利用模板匹配的方法提取出关键特征点。
4. 尺寸计算与结果输出根据零件的特征信息,结合相应的几何测量原理,可以计算出零件的尺寸参数。
一般来说,可以计算出零件的长、宽、高等尺寸参数,以及一些特殊形状的测量参数。
三、系统优势基于机器视觉的零件尺寸检测与测量系统相比传统的人工测量方法具有以下优势:1. 精度高:机器视觉系统可以实现对零件尺寸的高精度测量,减少了人为因素对测量结果的影响。
2. 自动化程度高:系统可以实现对多个零件的自动化测量,减少了人工测量的工作量,提高了工作效率。
3. 可靠性好:机器视觉系统的测量结果可靠性高,可以避免人工测量过程中的主观误差。
4. 数据可视化:测量结果可以通过电脑显示进行直观展示与分析,方便人们对零件质量进行评估。
四、应用领域基于机器视觉的零件尺寸检测与测量系统在很多领域都有广泛的应用,例如汽车制造、航空航天、电子电气等行业。
精密注塑件尺寸精度的解决方案
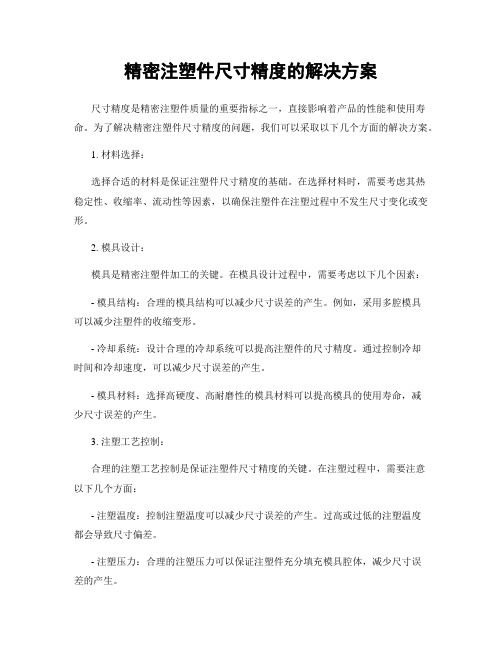
精密注塑件尺寸精度的解决方案尺寸精度是精密注塑件质量的重要指标之一,直接影响着产品的性能和使用寿命。
为了解决精密注塑件尺寸精度的问题,我们可以采取以下几个方面的解决方案。
1. 材料选择:选择合适的材料是保证注塑件尺寸精度的基础。
在选择材料时,需要考虑其热稳定性、收缩率、流动性等因素,以确保注塑件在注塑过程中不发生尺寸变化或变形。
2. 模具设计:模具是精密注塑件加工的关键。
在模具设计过程中,需要考虑以下几个因素:- 模具结构:合理的模具结构可以减少尺寸误差的产生。
例如,采用多腔模具可以减少注塑件的收缩变形。
- 冷却系统:设计合理的冷却系统可以提高注塑件的尺寸精度。
通过控制冷却时间和冷却速度,可以减少尺寸误差的产生。
- 模具材料:选择高硬度、高耐磨性的模具材料可以提高模具的使用寿命,减少尺寸误差的产生。
3. 注塑工艺控制:合理的注塑工艺控制是保证注塑件尺寸精度的关键。
在注塑过程中,需要注意以下几个方面:- 注塑温度:控制注塑温度可以减少尺寸误差的产生。
过高或过低的注塑温度都会导致尺寸偏差。
- 注塑压力:合理的注塑压力可以保证注塑件充分填充模具腔体,减少尺寸误差的产生。
- 注塑速度:控制注塑速度可以减少尺寸误差的产生。
过高的注塑速度会导致注塑件表面出现瑕疵,影响尺寸精度。
4. 检测与测量:对注塑件进行定期的检测与测量可以及时发现尺寸偏差,并采取相应的措施进行调整和修正。
常用的检测与测量方法包括:- 三坐标测量:通过三坐标测量仪对注塑件进行精确的尺寸测量,以确保其符合设计要求。
- 光学投影仪:利用光学原理对注塑件进行放大和测量,以检测尺寸偏差和形状缺陷。
- 量规和卡尺:通过传统的量具对注塑件进行尺寸测量,可以快速检测尺寸偏差。
综上所述,精密注塑件尺寸精度的解决方案包括材料选择、模具设计、注塑工艺控制和检测与测量。
通过合理的控制和调整这些因素,可以有效提高注塑件的尺寸精度,满足产品的质量要求。
- 1、下载文档前请自行甄别文档内容的完整性,平台不提供额外的编辑、内容补充、找答案等附加服务。
- 2、"仅部分预览"的文档,不可在线预览部分如存在完整性等问题,可反馈申请退款(可完整预览的文档不适用该条件!)。
- 3、如文档侵犯您的权益,请联系客服反馈,我们会尽快为您处理(人工客服工作时间:9:00-18:30)。
公差带与 配合的 选用
①
③
④
图3.1 极限与配合标准的基本结构
整理课件
3.1.3 《极限与配合》的基本术语和定义
4
1.有关孔、轴的定义
孔 ——
通常是指圆柱形的内表面,也包括非圆柱形的内表
面[由二平行平面或切平面形成的包容面]。
内表面
整理课件
5
轴 ——
通常是指圆柱形的外表面,也包括非圆 柱形的外表面[由二平行平面或切平面形成的 被包容面]。
外表面
?
整理课件
6
孔(轴)—通常是指圆柱形的内(外)表面,也 包括非圆柱形的内(外)表面[由二平行平面或切平 面形成的包容面(被包容面)]。
即孔(轴)——由单一尺寸确定的包容面 (被包容面)
加工时
测量时
配合时Βιβλιοθήκη 孔 尺寸由小→大轴 尺寸由大→
小
内尺寸 外尺寸
包容面 被包容面
整理课件
7
2. 有关尺寸的术语和定义
③ 孔、轴公差带或符号
整理课件
公称尺寸
18
例3.1 已知D(d)=Φ25, Dmax=Φ25.021, Dmin=Φ25, dmax=Φ24.980, dmin=Φ24.967。
求孔、轴的极限偏差和公差,画出尺寸公差 带图的两种画法,并写出极限偏差在图样上的标 注。
解:孔 (1)尺寸的极限偏差、公差
准化的孔、轴公差带的制度。
(1) 标准公差
标准公差是指国家标准所规定的任一公差值。
(2) 基本偏差
基本偏差是指国家标 准所规定的上极限偏差或
公差带 EI、ei
- 0+
公称尺寸
下极限偏差,它一般为靠
近零线或位于零线的那个 极限偏差。
ES、es 公差带
基本偏差
整理课件
5. 有关配合的术语和定义
21
(1) 配合—
实际 尺寸 数量
数量
1
5 11 9
3
1 30
实际偏差 -0.020 -0.015 -0.010 -0.005
0
+0.005
整理课件
14
(2)尺寸公差(简称公差)
—是指允许尺寸的变动量。 孔: TD = | Dmax–Dmin|
= | (Dmax- D) – (Dmin- D|
= | ES – EI |
下极限偏差(简称下偏差)是指下极限尺寸减其 公称尺寸所得的代数差(EI、ei)。
整理课件
11
用公式表示上、下极限偏差为
孔 : 上偏差 ESDma x D
轴: 上偏差
下偏差
EIDminD
esdmaxd
eidmind
为上偏差和下偏差统称极限偏差。
整理课件
12
② 对实际尺寸减其基本尺寸所得的代数差, 为实际偏差。
ES = Dmax-D = +0.021 EI = 0
TD= | Dmax– Dmax| = |ES–EI| = 0.021 在图样上的标注为 D=Φ25
轴es0.020ei0.033
Td 0.013
整d理=课Φ件25
19
(2) 画尺寸公差带图(见图3-5)
画法1
画法2
整理课件
20
4. 极限制 极限制是指标准化的公差与极限偏差组成标
(1) 尺寸 — 以特定单位表示线性尺寸值的数值。
标准规定,图样上的尺寸以毫米为单位时,
不需标注单位的名称或符号。
(2) 公称尺寸— 是指设计给定的尺寸。
(3) 实际尺寸—
(孔:D、轴:d ) 。
是指零件加工后通过测量获得的某一尺寸。
(Da, d )a整理课件
8
2. 有关尺寸的术语和定义
(4) 极限尺寸— 是指允许尺寸变化的两个极端。 其中允许的最大尺寸为上极限尺寸(最大 极限尺寸);
1
第3章 孔、轴结合尺寸精度设计与检测 内容提要
1. 孔、轴结合的使用要求; 2.《极限与配合》的基本结构; 3.《极限与配合》的基本术语和定义; 4.《极限与配合》标准的构成基本原理——
配合制、 标准公差和基本偏差; 5. 尺寸精度设计的基本内容和基本方法; 6. 未注尺寸公差的特点; 7. 尺寸精度检测的基本整理方课件法。
轴: Td = | dmax– dmin |
= |es–ei|
整理课件
15
(3) 偏差与公差区别:
① 偏差——是代数量,有(+、0、-)符号。
标注单位 偏差在图上标注应注意: 标注方法 公差——是绝对值,不带符号(尺寸公差不
能为零)。
② 偏差有基准 ——公称尺寸为基,公差无基准 。
③ 偏差影响配合松紧。 公差影响配合精度。
对孔 E aD : aD
对轴 ea: dad
实际偏差合格条件为
EIEa ES
eiea es
整理课件
例题
C1
数量:30
公称尺寸
16
0 0.018
13
上偏差 下偏差
极限 dmax 16
40
尺寸 dmin 15.982
实际尺寸 15.980 15.985 15.990 15.995 16.000 16.005
10
3. 尺寸偏差和尺寸公差的术语和定义 (1) 尺寸偏差(简称偏差)—
是指某一尺寸(极限尺寸、实际尺寸等)减其公 称尺寸所得的代数差。
(注标时除“0”外必须带符号)。 ① 对极限尺寸减其公称尺寸所得的代数差为极限
偏差。
上极限偏差(简称上偏差)是指上极限尺寸减其 公称尺寸所得的代数差(ES、es)。
④ 实际偏差是对单件零件的判断: ei ea es
误差是对一批零件的判断:
EI Ea ES
f T 整理课件
(3)尺寸公差带及公差带图
16
尺寸公差带(见图3-3)
是指由代表上偏差和下偏差或上极限尺寸和下极
限尺寸的两条直线所限定的一个区域。
公称尺寸
整理课件
17
尺寸公差带图(见图3-4)
零线—— ① 基本尺寸 ② 极限偏差数值或符号 公差带————
是指公称尺寸相同的,相互结合的孔和轴
公差带之间的关系。
轴公差带
公称尺寸
配合
整理课件
配合条件: 配合性质:
(Dma;xdma)x
允许的最小尺寸为下极限尺寸(最小 极限尺寸) 。
(Dmi;ndmin) 整理课件
9
公称尺 D,d和 寸极限Dm 尺 a,xDm 寸 i;n dma,dxmi,n 是设计给定的。
实际尺D寸 a,da ,
是加工后通过测量得到的。
实际尺寸合格条件为:
Dmin DaDmax d d d min a 整理课件max
2
第3章 孔、轴结合尺寸精度设计
与检测
3.1 概 述 学习本章的重要性:基础 3.1.1 孔、轴结合的使用要求 1. 用作相对运动副 这类结合必须保证有一定的间隙。 2. 用作固定连接 这类结合必须保证有一定的过盈。
3. 用作定位可拆连接 这类结合必须保证间隙不大,过盈也不能大。
整理课件
3
3.1.2 《极限与配合》的基本结构