离合器设计(金杯)解析
离合器的设计概述
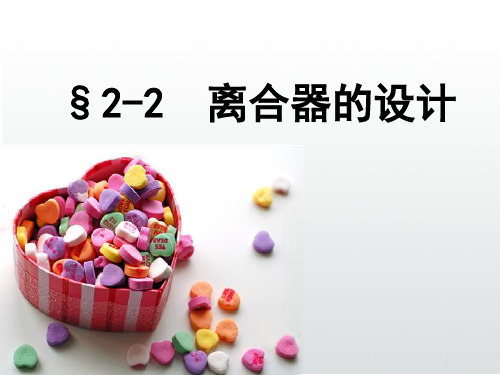
2018/7/30
P0 — 每个弹簧在接合时的载荷
f
p P0 n
— 离合器接合时弹簧的变形量,它为弹簧自 由高度 l 与工作高度 l0 之差,即
f l l0
图2-1
2018/7/30
圆柱螺旋压紧弹簧计算用简图
P —离合器分离时因弹簧附加变形保证分离间隙所引
起的附加载荷,一般 P 0.2 P 0
双片A=0.45~ 0.55,轻型车取上限,重型车取下
限;自卸车、特殊用途车:A=0.19。
摩擦片的厚度b主要有3.2mm、3.5mm和4.0mm
三种。
2018/7/30
要求:
(1)标准化(JB1457-74)。
(2)检查该尺寸是否在发动机飞轮允许尺寸范围内。 (3)大圆周线速度[v]不超过65~70m/s,以免发生飞 离的危险。 D2 neH v [v ] 60
A
( D22 D12 )
4
式中:D2、D1—— 摩擦衬片的外径和内径(m)。
2018/7/30
对湿式离合器而言,摩擦副的面积为扣除油槽 面积Δ A后的有效摩擦工作面面积A1。 对径向油槽ΔA为(0.1~ 0.2)A; 对螺旋油槽ΔA=(0.35~ 0.4)A;对螺旋径向油 槽Δ A为(0.45~ 0.6)A,故 A1=A-ΔA
h
—离合器分离时弹簧附加变形量, h Z , Z是摩擦副数量, 是主动盘与从动盘的分离 间隙(一般单盘式为0.75 ~ 1.25 mm,双盘式 为0.5 ~ 0.9 mm,多盘式为0.2 ~ 0.4 mm);
G m —材料的扭转弹性模量 Gm 82GPa
Dtp , d t —弹簧的中径和钢丝的直径
' ——花键轴导向面与摩擦片
离合器结构设计
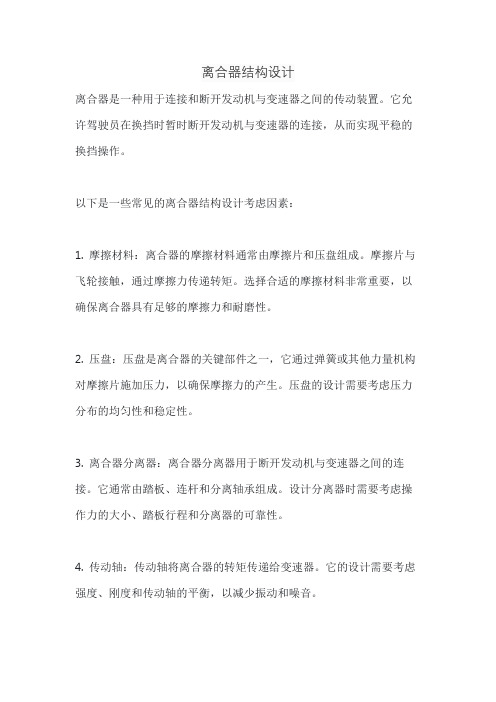
离合器结构设计
离合器是一种用于连接和断开发动机与变速器之间的传动装置。
它允许驾驶员在换挡时暂时断开发动机与变速器的连接,从而实现平稳的换挡操作。
以下是一些常见的离合器结构设计考虑因素:
1. 摩擦材料:离合器的摩擦材料通常由摩擦片和压盘组成。
摩擦片与飞轮接触,通过摩擦力传递转矩。
选择合适的摩擦材料非常重要,以确保离合器具有足够的摩擦力和耐磨性。
2. 压盘:压盘是离合器的关键部件之一,它通过弹簧或其他力量机构对摩擦片施加压力,以确保摩擦力的产生。
压盘的设计需要考虑压力分布的均匀性和稳定性。
3. 离合器分离器:离合器分离器用于断开发动机与变速器之间的连接。
它通常由踏板、连杆和分离轴承组成。
设计分离器时需要考虑操作力的大小、踏板行程和分离器的可靠性。
4. 传动轴:传动轴将离合器的转矩传递给变速器。
它的设计需要考虑强度、刚度和传动轴的平衡,以减少振动和噪音。
5. 润滑:离合器的部件需要适当的润滑,以确保正常的运转和寿命。
设计中需要考虑润滑剂的类型、润滑方式和润滑系统的设计。
6. 热管理:离合器在工作过程中会产生热量,因此需要考虑散热问题。
设计中可以采用散热片、散热孔或冷却系统等方式来有效管理离合器的温度。
7. 轻量化设计:在不影响强度和性能的前提下,尽量减轻离合器的重量可以提高燃油经济性和动态性能。
这只是离合器结构设计的一些基本考虑因素,实际的设计还需要根据具体的应用和要求进行详细的工程分析和优化。
离合器的设计需要综合考虑性能、可靠性、耐久性和成本等因素,以满足车辆的动力传输需求。
汽车设计-离合器设计

第二章离合器设计第一节概述离合器是汽车传动系中直接与发动机相连接的总成,其主要功用是切断和实现对传动系的动力传递,以保证汽车起步时将发动机与传动系平顺地接合,确保汽车平稳起步;在换档时将发动机与传动系分离,减少变速器中换档齿轮之间的冲击;在工作中受到大的动载荷时,能限制传动系所承受的最大转矩,防止传动系各零件因过载而损坏;有效地降低传动系中的振动和噪声。
为了保证离合器具有良好的工作性能,对汽车离合器设计提出如下基本要求:1. 在任何行驶条件下均能可靠地传递发动机的最大转矩,并有适当的转矩储备;2. 接合时要平顺柔和,以保证汽车起步时没有抖动和冲击;3. 分离时要迅速、彻底;4. 离合器从动部分转动惯量要小,以减轻换档时变速器齿轮间的冲击,便于换档和减小同步器的磨损;5. 应有足够的吸热能力和良好的通风散热效果,以保证工作温度不致过高,延长其使用寿命;6. 应使传动系避免扭转共振,并具有吸收振动、缓和冲击和减小噪声的能力;7. 操纵轻便、准确,以减轻驾驶员的疲劳;8. 作用在从动盘上的压力和摩擦材料的摩擦系数在使用过程中变化要尽可能小,以保证有稳定的工作性能;9. 应有足够的强度和良好的动平衡,以保证其工作可靠、寿命长;10. 结构应简单、紧凑,质量小,制造工艺性好,拆装、维修、调整方便等。
摩擦离合器主要由主动部分(发动机飞轮、离合器盖和压盘等)、从动部分(从动盘)、压紧机构(压紧弹簧)和操纵机构(分离叉、分离轴承、离合器踏板及传动部件等)四部分组成。
主、从动部分和压紧机构是保证离合器处于接合状态并能传递动力的基本结构,操纵机构是使离合器主、从动部分分离的装置。
随着汽车发动机转速和功率的不断提高,汽车电子技术的高速发展,人们对离合器的要求越来越高。
从提高离合器工作性能角度出发,传统的推式膜片弹簧离合器结构正逐步地向拉式结构发展,传统的操纵型式正向自动操纵的型式发展,因此,提高离合器的可靠性和使用寿命,适应高转速,增加传递转矩的能力和简化操纵,已成为离合器的发展趋势。
金杯海狮离合器调整(液压式)
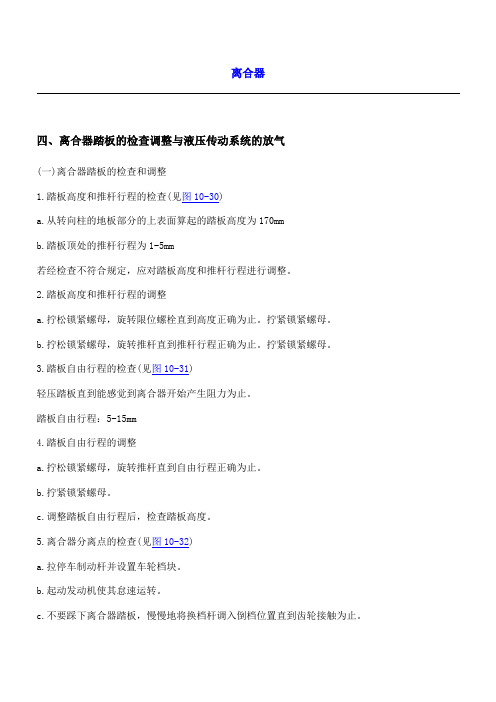
离合器四、离合器踏板的检查调整与液压传动系统的放气(一)离合器踏板的检查和调整1.踏板高度和推杆行程的检查(见图10-30)a.从转向柱的地板部分的上表面算起的踏板高度为170mmb.踏板顶处的推杆行程为1-5mm若经检查不符合规定,应对踏板高度和推杆行程进行调整。
2.踏板高度和推杆行程的调整a.拧松锁紧螺母,旋转限位螺栓直到高度正确为止。
拧紧锁紧螺母。
b.拧松锁紧螺母,旋转推杆直到推杆行程正确为止。
拧紧锁紧螺母。
3.踏板自由行程的检查(见图10-31)轻压踏板直到能感觉到离合器开始产生阻力为止。
踏板自由行程:5-15mm4.踏板自由行程的调整a.拧松锁紧螺母,旋转推杆直到自由行程正确为止。
b.拧紧锁紧螺母。
c.调整踏板自由行程后,检查踏板高度。
5.离合器分离点的检查(见图10-32)a.拉停车制动杆并设置车轮档块。
b.起动发动机使其怠速运转。
c.不要踩下离合器踏板,慢慢地将换档杆调入倒档位置直到齿轮接触为止。
d.渐渐地踩下离合器踏板,测量从齿轮响声停止(分离点开始直到全行程终点的距离。
)标准距离:25mm或更大(从踏板行程终点位置至分离点)如果距离不符合规定要求,则应进行下列的操作项目。
.检查踏板高度。
·检查推杆行程和踏板自由行程(游隙)。
·排出离合器管路内的空气。
·检查离合器罩壳和盘。
(二)离合器液压传动系统的放气注意:a.检修离合器液压传动系或管路内有空气,均应进行放气工作。
b.为避免放气流出的制动液留在涂漆层表面上,应立即洗掉。
1.检查储液箱液面高度应经常检查储液箱制动液液面高度,需要时加以补注。
2.将乙烯树脂管接到放气塞上将管子的另一端插入盛有一半制动液的容器中。
3.离合器液压管路放气(见图10-33)a.上下往复踏几下离合器踏板,最后停留在踏到底的位置。
b.旋松放气螺钉,使系统中空气随制动液喷出。
之后,迅速拧紧放气螺钉,缓慢地放松踏板,使其回位。
(见图10-34)c.按上述程序重复3-5次,直到在工作缸(分离缸)放气螺钉处喷出的制动液不夹有气泡为止。
金杯6480B2汽车离合器分离不彻底,进二档响,倒档有时退不出
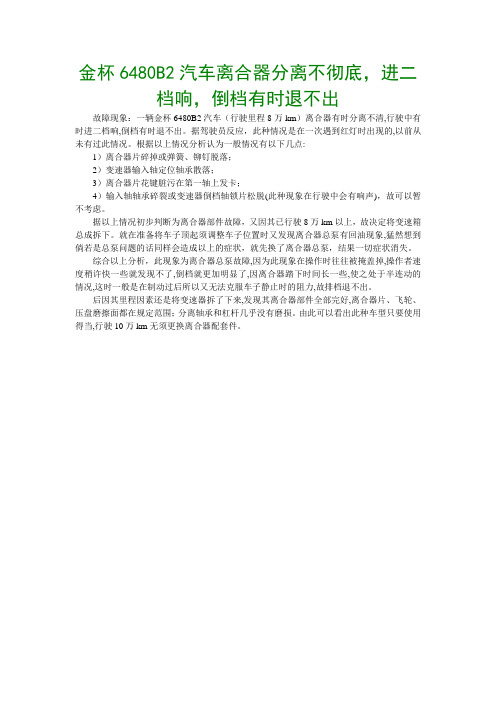
金杯6480B2汽车离合器分离不彻底,进二档响,倒档有时退不出
故障现象:一辆金杯6480B2汽车(行驶里程8万km)离合器有时分离不清,行驶中有时进二档响,倒档有时退不出。
据驾驶员反应,此种情况是在一次遇到红灯时出现的,以前从未有过此情况。
根据以上情况分析认为一般情况有以下几点:
1)离合器片碎掉或弹簧、铆钉脱落;
2)变速器输入轴定位轴承散落;
3)离合器片花键脏污在第一轴上发卡;
4)输入轴轴承碎裂或变速器倒档轴锁片松脱(此种现象在行驶中会有响声),故可以暂不考虑。
据以上情况初步判断为离合器部件故障,又因其已行驶8万km以上,故决定将变速箱总成拆下。
就在准备将车子顶起须调整车子位置时又发现离合器总泵有回油现象,猛然想到倘若是总泵问题的话同样会造成以上的症状,就先换了离合器总泵,结果一切症状消失。
综合以上分析,此现象为离合器总泵故障,因为此现象在操作时往往被掩盖掉,操作者速度稍许快一些就发现不了,倒档就更加明显了,因离合器踏下时间长一些,使之处于半连动的情况,这时一般是在制动过后所以又无法克服车子静止时的阻力,故排档退不出。
后因其里程因素还是将变速器拆了下来,发现其离合器部件全部完好,离合器片、飞轮、压盘磨擦面都在规定范围;分离轴承和杠杆几乎没有磨损。
由此可以看出此种车型只要使用得当,行驶10万km无须更换离合器配套件。
离合器的设计计算及说明

第3章 离合器的设计计算及说明3.1 离合器设计所需数据表3.1 离合器原始数据汽车的驱动形式 6×6汽车最大加载质量 20550 kg 汽车的质量 11450 kg发动机位置 前置发动机最大功率 280KW 发动机最大转速 1400r/min发动机最大扭矩 ≥109kgf.m离合器形式 单片干式GF420气助力操纵形式 液压人力操纵 摩擦片最大外径 f=420mm 踏板行程 150~80mmi g1=13.04 i g2=8.48 i g3=6.04 i g4=4.39 i g5=3.43 i g6=2.47 i g7=1.76 i g8=1.28i g9=1.00 i gR =11.77(R )汽车最大时速85km/h3.2 离合器主要参数的选择后备系数β后备系数β是离合器设计中的一个重要参数,它反映了离合器传递发动机最大转矩的可靠程度。
在选择β时,应考虑摩擦片在使用中的磨损后离合器仍能可靠地传递发动机最大转矩、防止离合器滑磨时间过长、防止传动系过载以及操纵轻便等因素。
乘用车β选择:1.20~1.75 ,本次设计取β = 1.2。
(1)后备系数β是离合器的重要参数,反映离合器传递发动机最大扭矩的可靠程度,选择β时,应从以下几个方面考虑:a. 摩擦片在使用中有一定磨损后,离合器还能确保传递发动机最大扭矩;b. 防止离合器本身滑磨程度过大;c. 要求能够防止传动系过载。
通常轿车和轻型货车β=1.2~1.75。
结合设计实际情况,故选择β=1.5。
则有β可有表3.2查得 β=2.0。
表3.2 离合器后备系数的取值范围车型后备系数β 乘用车及最大总质量小于6t 的商用车 1.20~1.75 最大总质量为6~14t 的商用车1.50~2.25 挂车1.80~4.00摩擦片的外径可有式:max e D T K D (3.3) 求得D K 为直径系数,取值见表3.3 取16=D K 得D=221.11mm 。
(整理)22离合器的结构方案分析.
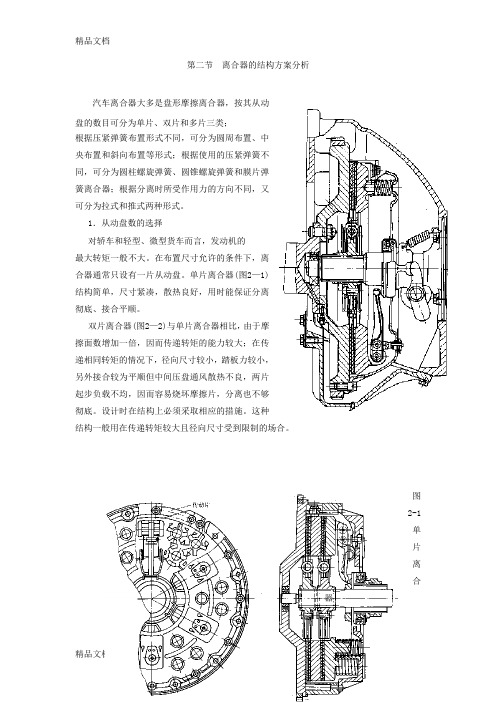
第二节离合器的结构方案分析汽车离合器大多是盘形摩擦离合器,按其从动盘的数目可分为单片、双片和多片三类;根据压紧弹簧布置形式不同,可分为圆周布置、中央布置和斜向布置等形式;根据使用的压紧弹簧不同,可分为圆柱螺旋弹簧、圆锥螺旋弹簧和膜片弹簧离合器;根据分离时所受作用力的方向不同,又可分为拉式和推式两种形式。
1.从动盘数的选择对轿车和轻型、微型货车而言,发动机的最大转矩一般不大。
在布置尺寸允许的条件下,离合器通常只设有一片从动盘。
单片离合器(图2—1)结构简单,尺寸紧凑,散热良好,用时能保证分离彻底、接合平顺。
双片离合器(图2—2)与单片离合器相比,由于摩擦面数增加一倍,因而传递转矩的能力较大;在传递相同转矩的情况下,径向尺寸较小,踏板力较小,另外接合较为平顺但中间压盘通风散热不良,两片起步负载不均,因而容易烧坏摩擦片,分离也不够彻底。
设计时在结构上必须采取相应的措施。
这种结构一般用在传递转矩较大且径向尺寸受到限制的场合。
图2-1单片离合器图2-2 双片离合器多片离合器多为湿式,它有分离不彻底、轴向尺寸和质量大等缺点,以往主要用于行星齿轮变速器换挡机构中。
但它具有接合平顺柔和、摩擦表面温度较低、磨损较小、使用寿命长等优点,主要应用于重型牵引车和自卸车上。
2.压紧弹簧和布置形式的选择周置弹簧离合器的压紧弹簧均采用圆柱螺旋弹簧(图2—1),其特点是结构简单、制造容易,因此应用较为广泛。
此结构中弹簧压力直接作用于压盘上。
为了保证摩擦片上压力均匀,压紧弹簧的数目不应太少,要随摩擦片直径的增大而增多,而且应当是分离杠杆的倍数。
在某些重型汽车上,由于发动机最大转矩较大,所需压紧弹簧数目较多,可将压紧弹簧布置在两个同心圆周上。
压紧弹簧直接与压盘接触,易受热退火,且当发动机最大转速很高时,周置弹簧由于受离心力作用而向外弯曲,使弹簧压紧力下降,离合器传递转矩的能力随之降低。
此外,弹簧靠到它的定位面上,造成接触部位严重磨损,甚至会出现弹簧断裂现象。
浅析轻型货车离合系统的设计和开发
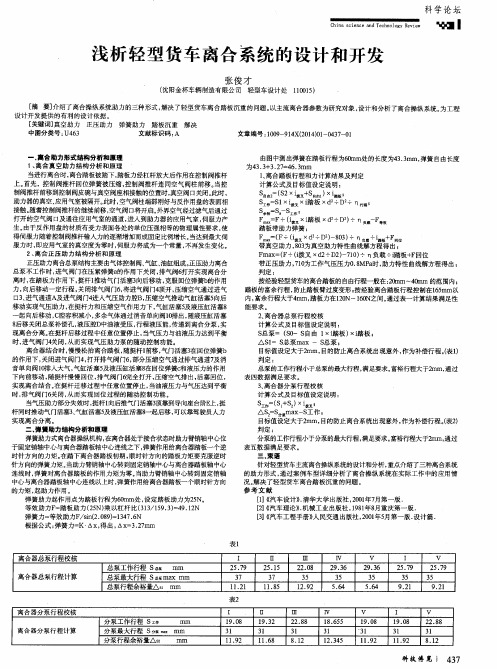
.
F
Байду номын сангаас
正压 助力 离合总 泵结构 主要 由气体控 制阀 、 气缸 、 油缸组成 。 正压 助力 离合 总泵 不工 作 时, 进 气阀 门在压 紧弹 簧a 的作 用下 关闭 , 排气 阀6 打开实 现离 合分 离时, 在踏板力作用下, 挺杆 1 推动气门活塞3 向后移动, 克服回位弹簧b 的作用 力, 向后移动一定行程, 关闭排气阀I " q 6 , 将进气阀f ] 4 N开, 压缩空气通过进气 口3 、 进 气通 道A及进 气阀 门4 进 入气 压助 力腔 B , 压 缩空气 推动 气缸 活塞 5 向后 移动实现气压助力, 在挺杆力和压缩空气作用力下, 气缸活塞5 及液压缸活塞8 起 向后 移 动 , C 腔 容积 减小 , 多余 气体 通过 消音 单向 阀1 0 { { } 出, 随液压 缸 活塞 8 后移 关 闭总泵 补偿 孔 , 液 压腔D中油 液受压 , 行程 液压 能 , 传 递到 离合分 泵 , 实 现 离合分 离 。 在 挺杆 后移 过程 中任意 位置停 止 , 当气压力 与油 液压力 达 到平衡 时, 进 气 阀门4 关闭 , 从 而实 现气压 助 力泵 的 随动 控制 功能 。 离合器 结合 时 , 慢慢 松抬 离合踏 板 , 随挺 杆 1 前移 , 气门活 塞3 在 回位弹簧 b 的作 用下 , 关闭进 气 阀门4 , 打开排 气 阀门6 , 部 分压 缩空 气通 过排气 通道 7 及 消 音单 向 阀l 0 j { } 人 大气 , 气 缸活 塞5 及液压 缸 活塞8 在 回位弹 簧c N 液压力 的作 用 下 向前移 动 , 随挺 杆慢 慢 回位 , 排气 阀 门皖 全 打开 , 压 缩空气 排 出 , 活 塞 回位 , 实现 离合 结合 。 在 挺杆 迁移 过程 中任意 位置停 止 , 当油液压 力与 气压 达到 平衡 时, 排气 阀 门6 关闭 , 从 而实 现 回位 过 程 的随动 控 制功能 。 当气 压助力 部分失 效时 , 挺杆 I 向后推气 门活塞3 顶靠到导 向座 台阶吐 , 挺 杆 同 时推动气 门活塞 3 、 气 缸活塞 5 及液压 缸 活塞8 一起 后移 , 可 以靠 驾驶员 人力 实 现 离合分 离 。 =. 弹 簧助 力 结构分 析 和原 理 弹簧助力式离合器操纵机构, 在离合器处于接合状态时助力臂销轴 中心位
- 1、下载文档前请自行甄别文档内容的完整性,平台不提供额外的编辑、内容补充、找答案等附加服务。
- 2、"仅部分预览"的文档,不可在线预览部分如存在完整性等问题,可反馈申请退款(可完整预览的文档不适用该条件!)。
- 3、如文档侵犯您的权益,请联系客服反馈,我们会尽快为您处理(人工客服工作时间:9:00-18:30)。
目录第一章概述 (1)第二章离合器结构方案分析 (2)2.1离合器的主要结构 (2)2.2离合器结构方案的选择 (3)第三章离合器主要参数的选择 (6)第四章从动盘总成的设计 (8)4.1从动盘毂的设计 (8)4.2摩擦片的设计 (9)4.3从动片的设计 (10)4.4扭转减振器的设计 (10)第五章离合器盖总成的设计 (12)5.1离合器盖的设计 (12)5.2膜片弹簧的设计 (12)5.3压盘的设计.......................... 错误!未定义书签。
5.4传动片的设计........................ 错误!未定义书签。
结论、致谢............................... 错误!未定义书签。
4参考文献. (15)第一章概述对于以内燃机为动力的汽车,离合器在机械传动系中作为一个独立的总成而存在的,它是汽车传动系中直接与发动机相连接的总成。
目前,各种汽车广泛采用的摩擦离合器是一种依靠主、从动部分之间的摩擦来传递动力且能分离的装置。
离合器的主要功用是切断和实现发动机对传动系的动力传递,保证汽车起步时将发动机与传动系平顺的接合,确保汽车平稳起步;换挡时将发动机与传动系分离,减少变速器中换挡齿轮之间的冲击;在工作中收到较大的动载荷时能,能限制传动系所承受的最大转矩,以防止传动系各零部件因过载而损坏;有效的降低传动系中的振动和噪声。
为了保证离合器具有良好的工作性能,设计离合器应满足如下基本要求:(1).在任何形式条件下,既能可靠地传递发动机的最大扭矩,并有适当的转矩储备,又能防止传动系过载。
(2).接合时要完全、平顺、柔和,保证汽车起步时没有抖动和冲击。
(3)分离时要迅速、彻底。
(4)从动部分转动惯量要小,以减轻换挡时变速器齿轮间的冲击,便于换挡和减小同步器的磨损。
(5)应有足够的吸热能力和良好的通风散热效果,以保证工作温度不致过高,延长其使用寿命。
(6)操纵轻便、准确,以减轻驾驶员的疲劳。
(7)作用在从动盘上的总压力和摩擦材料的摩擦因数在离合器工作工程中变化要尽可能小,以保证有稳定的工作性能。
(8)结构应简单、紧凑、质量小,制造工艺性好,拆装、维修、调整方便等。
随着汽车发动机转速、功率的不断提高和汽车电子技术的不断发展,人们对离合器的要求越来越高。
从提高离合器工作性能的角度出发,传统的推式膜片弹簧离合器结构正逐步的向拉式膜片弹簧离合器结构发展,传统的操纵形式正向自动操纵的形式发展。
因此,提高离合器的可靠性和延长其使用寿命,适应发动机的高转速,增加离合器传递转矩的能力和简化操纵,已成为离合器的发展趋势。
1第二章离合器的结构方案分析2.1 离合器的主要结构2.1.1主动部分主动部分包括飞轮、离合器盖、压盘等机件组成。
这部分与发动机曲轴连在一起。
离合器盖与飞轮靠螺栓连接,压盘与离合器盖之间是靠传动片传递转矩的。
2.1.2从动部分从动部分是由单片、双片或多片从动盘所组成,它将主动部分通过摩擦传来的动力传给变速器的输入轴。
从动盘由从动盘本体,摩擦片和从动盘毂三个基本部分组成。
2.1.3扭转减震器离合器结合时,发动机发出的转矩经飞轮和压盘传给了从动盘两侧的摩擦片,带动从动盘本体和与从动盘本体铆接在一起的减震器盘转动。
从动盘本体和减震器盘又通过六个减震器弹簧把转矩传给了从动盘毂。
因为有弹性环节的作用,所以传动系受的转动冲击可以在此得到缓和。
传动系中的扭转振动会使从动盘毂相对于从动盘本体和减震器盘来回转动,夹在它们之间的减震阻尼片靠摩擦消耗扭转振动的能量,将扭转振动衰减下来。
为了使汽车能平稳起步,离合器应能柔和结合,这就需要从动盘在轴向具有一定弹性。
为此,往往在东盘本田圆周部分,沿径向和周向切槽。
再将分割形成的扇形部分沿周向翘曲成波浪形,两侧的两片摩擦片分别与其对应的凸起部分相铆接,这样从动盘被压缩时,压紧力沿翘曲的扇形部分被压平而逐渐增大,从而达到结合柔和的效果。
2.1.4压紧机构压紧机构主要由螺旋弹簧组成,与主动部分一起旋转,它以离合器盖为依托,将压盘压向飞轮,从而将处于飞轮和压盘间的从动盘压紧。
2膜片弹簧离合器的大致组成结构如如图1-1所示:图1-1膜片离合器盖总成零件分解1、离合器盖2、4、支撑环3、膜片弹簧5、压盘6、铆钉7、支撑铆钉2.2 离合器结构方案的选择2.2.1从动盘数及干、湿式的选择单片干式摩擦离合器其结构简单,调整方便,轴向尺寸紧凑,分离彻底,从动件转动惯量小,散热性好,采用轴向有弹性的从动盘时也能结合平顺。
因此,广泛用于各级轿车及微、轻、中型客车与货车,在发动机转矩不大于1000N.M大型客车和重型货车上也有所推广。
当转矩更大时可采用双片干式或双片湿式摩擦离合器。
因本设计的离合器是用于微型货车上的,选用单片干式摩擦离合器。
32.2.2压紧弹簧的结构型式及布置的选择周置弹簧离合器因其结构简单制造容易,因此应用比较广泛。
但在高转速离心力的作用下,周置弹簧易歪斜甚至严重弯曲鼓出而显著降低压紧力:另外,压紧弹簧直接与压盘接触,易受热退火,且当发动机最大转速很高时周置弹簧由于受离心力作用而向外弯曲,是弹簧压紧力下降,离合器传递转矩的能力随之降低。
此外,弹簧靠到它的定为面上,造成接触部位严重磨损,甚至出现弹簧断裂的现象。
中央圆柱螺旋弹簧一般应用于离合器的轴向尺寸较大,而矩形断面的锥形弹簧则可明显缩小轴向尺寸,但其制造却比较困难,故中央弹簧离合器多用在重型汽车上以减轻其操纵力。
根据国外的统计资料:挡在货汽车的发动机转矩大于400~450牛/米时,常常采用中央弹簧离合器。
斜置弹簧离合器是重型汽车采用的一种新型结构。
以数目较多的一组圆柱螺旋弹簧为压紧弹簧,分别以倾角α斜向作用于传力套上,跟着在推动压杆并按杠杆比放大后作用与压盘上。
因此,斜置弹簧离合器与前两种离合器相比,其突出优点是工作性能十分稳定。
与周置弹簧离合器比较,其踏板力可降低35%左右。
膜片弹簧离合器的结构主要特点是采用一个膜片代替传统的螺旋弹簧和分离杠杆。
其结构特点如下:1)膜片弹簧的轴向尺寸较小而径向尺寸很大,这有利于在提高离合器传递转矩能力的情况下离合器的轴向尺寸。
2)膜片弹簧的分离指起分离杠杆的作用,故不需专门的分离杠杆,使离合器结构大大简化,零件数目少,质量轻。
3)由于膜片弹簧轴向尺寸小,所以可以适当增加压盘的厚度,提高热容量;而且还可以在压盘上增设散热筋及在离合器盖上开设较大的通风孔来改善散热条件。
4)膜片弹簧离合器的主要部件形状简单,可以采用冲压加工,大批量生产时可以降低生产成本。
由于膜片弹簧离合器具有上述一系列的优点,并且制造膜片弹簧的工艺水平也在不断地提高,因而这种离合器在轿车及微型和中型客车、货车上得到广泛的应用,而且逐渐扩展到大型货车上。
因此,本设计采用膜片弹簧。
42.2.3离合器的通风散热实验表明,离合器的磨损是随温度的升高而增大的,当压盘工作表面温度超过一定温度时,摩擦片磨损急剧增加。
在正常使用条件下的离合器压盘工作表面温度在180℃。
在特别严酷的使用条件下,压盘表面的瞬时温度有可能高达1000℃。
过高的温度能使压盘受热变形产生裂纹。
为了使摩擦表面温度不致过高,除要求压盘有足够的重量以保证足够的热容量外,还要求通风散热性良好。
改善离合器的通风措施有:1)在压盘上设置散热筋;2)在离合器盖上开较大的通风口,在离合器外壳上设有通风窗;2.2.4膜片弹簧的支承形式推式膜片弹簧支承结构按支承环数目不同可分三种:1)双支承环形式用台肩式铆钉将膜片弹簧、两个支承环与离合器盖定位铆合在一起,结构简单;2)单支承环形式在冲压离合器盖上冲出一个环形凸台来代替后支承环,使架构简单,或在铆钉前侧以弹性当环代替前支承环,以消除膜片弹簧与支承环之间的轴向间隙;3)无支承环形式利用斜头铆钉的头部与冲压离合器盖上冲出的环形凸台将膜片弹簧铆合在一起,取消前后支承环,或在铆钉前侧以弹性当环代替前支承环,离合器盖上的环形凸台代替后支承环,使结构更简化或取消铆钉,离合器盖内边缘处伸出的许多舌片将膜片弹簧与弹性挡环和离合器盖上的环形凸台弯合在一起,结构最为简单。
本次设计选用双支承环式。
2.2.5压盘的驱动方式压盘的驱动方式主要有凸块—窗孔式、传力销式、键块式和弹性传动片式等多种。
前三种的共同缺点是在连接件之间有间隙,在传动中将产生冲击和噪声,而且在零件相对滑动中有摩擦和磨损,降低了离合器的传动效率。
弹性传动片式是最近广泛采用的驱动方式,沿圆周切向布置的三组或四组薄弹簧钢带传动片两端分别于离合器盖和压盘以铆钉或螺栓连接,传动片的弹性允许压盘做轴向移动。
弹性传动片驱动方式简单,压盘与飞轮对中性能好,使用平衡性好,工作可靠,寿命长。
故本次选用弹性传动片式。
5第三章离合器主要参数的选择3.2设计车型的分析其基本参数如下:车型:金杯SY6480B2D发动机:XC4G24整车质量:2290(kg)整备质量:1670(kg)最大功率:90(kw)最大扭矩:200(N.m)一档传速比:4.452主减速比:4.5563.2离合器参数的选择3.2.1后备系数β后备系数保证了离合器能可靠地传递发动机扭矩,同时它有助于减少汽车起步时的滑磨,提高了离合器的使用寿命。
但为了离合器的尺寸不致过大,减少传递系的过载,使操纵轻便等,后备系数又不宜过大。
由于所设计的离合器为膜片弹簧离合器,在使用过程中其摩擦片的磨损工作压力几乎不会变小(开始时还有些增加),再加上小轿车的后备功率比较大,使用条件较好,宜取较小值,由《汽车设计》书表2-1,初取β=1.5。
3.2.2单位压力p决定了摩擦表面的耐磨性,对离合器工作性能和使用寿命有很大影响,选单位压力p取时应考虑离合器的工作条件、发动机后备功率的大小、摩擦片尺寸、材料及其质量和后备取值范围见表系数等因素。
p常用摩擦材料的摩擦系数、许用应力和许用温度6本次设计选取 p= 0.209MPa, f=0.25选用的材料是钢基粉末冶金3.2.3摩擦因数f,摩擦面数Z和离合器间隙△t摩擦片的摩擦因数f取决于摩擦片所用的材料及工作温度及单位压力和滑磨速度等因素。
该设计选用钢基粉末冶金材料,参考上表,取摩擦因数f=0.25摩擦面数Z为离合器从动盘数的两倍,故Z=2离合器间隙一般为3-4mm.取△t=3mm。
7第四章从动盘总成的设计4.1 从动盘毂的设计从动盘毂的花键孔与变速器第一轴前端的花键轴以齿侧定心矩形花键的动配合相联接,以便从动盘毂能作轴向移动。
花键的结构尺寸可根据从动盘外径和发动机转矩按GB1144-2001矩形花键尺寸、公差和检验选取(见表3-1)。
从动盘毅花键孔键齿的有效长度约为花键外径尺寸的(1.0~1. 4)倍(上限用于工作条件恶劣的离合器),以保证从动盘毂沿轴向移动时不产生偏斜。