浇注系统设计
合集下载
分型面浇注系统设计
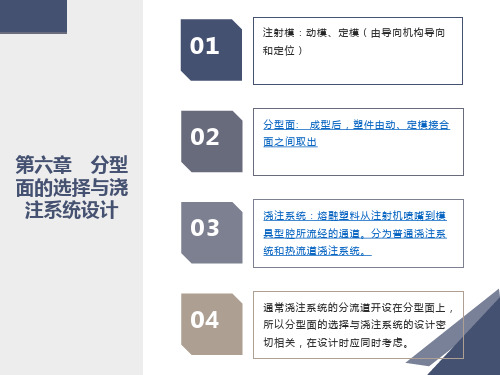
当浇注系统和型腔断面尺寸各处不等时,流动比计算公式为
对于图中所示的直接浇口,流动比为
注意:当计算得到的流动比大于允许值时,这时就需要改变浇口位置,或者增加塑件厚度来减小流动比。防止产生充填不足的现象。
影响最大流动距离比的因素: 熔体的性质、温度和注射压力等,需要经过大量实验来确定。表6-1列出了部分塑料的注射压力与流动距离比。
图a为非平衡式布置:主流道到各型腔浇口分流道长度不同。 图b、c为平衡式布置:主流道到各型腔浇口分流道长度相同
多型腔的排列设计时应注意如下几点:
尽可能采用平衡式排列,以便构成平衡式浇注系统,确保塑件质量的均一和稳定。
型腔布置和浇口开设部位应力求对称,以防止模具承受偏载而产生溢料现象。
02
尽量使型腔排列紧凑一些,以减小模具的外形尺寸。图7-2(b)的布局优于图(a)的布局,(b)的模板总面积小,可节省钢材,减轻模具质量。
梯形截面
优点是制造简便,且热量损失不大。 较常用
对壁厚小于3mm,质量200g以下的塑料制品,还可用如下经验公式确定梯形截面分流道尺寸
”
式中 m——制品质量 g; L——分流道的长度mm; h ——梯形高度mm。
01
按照经验,b可选择5 ~10mm
02
(该式计算的分流道b仅限于在3.2~9.5mm以内)
分流道表面粗糙度
六、浇口的设计
浇口:连接分流道与型腔之间的一段细短通道。
1
作用:调节控制料流速度、补料时间及防止倒流等。
2
按浇口的结构特点,常用浇口有直接浇口、侧浇口、点浇口等等。
常用的有:圆形、梯形、U形、半圆形和矩形等。
01
分流道设计中要减少在流道内的压力损失和热量损失,希望流道的表面积小。所以分流道形状应尽量使其比表面积小(流道表面积与其体积之比)。
对于图中所示的直接浇口,流动比为
注意:当计算得到的流动比大于允许值时,这时就需要改变浇口位置,或者增加塑件厚度来减小流动比。防止产生充填不足的现象。
影响最大流动距离比的因素: 熔体的性质、温度和注射压力等,需要经过大量实验来确定。表6-1列出了部分塑料的注射压力与流动距离比。
图a为非平衡式布置:主流道到各型腔浇口分流道长度不同。 图b、c为平衡式布置:主流道到各型腔浇口分流道长度相同
多型腔的排列设计时应注意如下几点:
尽可能采用平衡式排列,以便构成平衡式浇注系统,确保塑件质量的均一和稳定。
型腔布置和浇口开设部位应力求对称,以防止模具承受偏载而产生溢料现象。
02
尽量使型腔排列紧凑一些,以减小模具的外形尺寸。图7-2(b)的布局优于图(a)的布局,(b)的模板总面积小,可节省钢材,减轻模具质量。
梯形截面
优点是制造简便,且热量损失不大。 较常用
对壁厚小于3mm,质量200g以下的塑料制品,还可用如下经验公式确定梯形截面分流道尺寸
”
式中 m——制品质量 g; L——分流道的长度mm; h ——梯形高度mm。
01
按照经验,b可选择5 ~10mm
02
(该式计算的分流道b仅限于在3.2~9.5mm以内)
分流道表面粗糙度
六、浇口的设计
浇口:连接分流道与型腔之间的一段细短通道。
1
作用:调节控制料流速度、补料时间及防止倒流等。
2
按浇口的结构特点,常用浇口有直接浇口、侧浇口、点浇口等等。
常用的有:圆形、梯形、U形、半圆形和矩形等。
01
分流道设计中要减少在流道内的压力损失和热量损失,希望流道的表面积小。所以分流道形状应尽量使其比表面积小(流道表面积与其体积之比)。
浇注系统设计
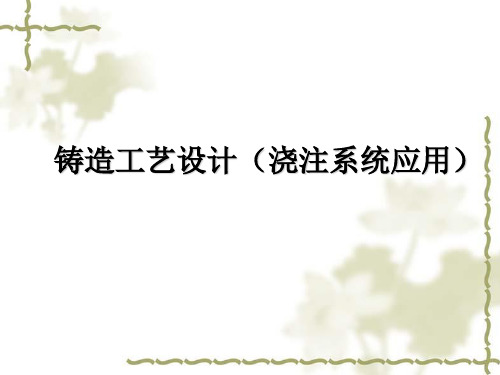
浇注系统设计
一、浇注系统构成 浇注系统由浇口杯(外浇口)、直浇道、横浇道和内浇道等构成。其构造见下图
1—浇口杯;2—直浇道;3—横浇道;4—内浇道
注意点:内浇道形状(提议使用Ⅰ型) ❖ Ⅰ型扁平内浇道易于清理,能提升横浇道旳挡渣效果。当使用宽度受限制时,可
用Ⅱ型。 ❖ Ⅲ型内浇道用于铸件垂直壁处或不宜冲刷处。 ❖ Ⅳ型和Ⅴ型内浇道用于需内浇道凝固较慢旳场合,其清理较困难。 ❖ Ⅵ型内浇道冷却较快、轻易清理。
老式浇系极难胜任三大功能旳两项:挡渣和降低紊流
浇注系统旳主要功能:1. 提供金属液进入型腔旳通道;2. 金属液尽量平稳;3.阻止渣/砂和其他反应产物进入型腔;
过滤器应用
带过滤器旳浇系
The controlling crosssection阻流截面
Downsprue : Runner Bar
:
Runner Bar : Ingate
带有过滤器旳浇注系统
❖ 内浇道和横浇道高度比
1. 内浇道形状扁平梯型;
2. H横=(5-6)H内—预防吸动作用产生杂质进型腔(针对放置在横浇道底部) ❖ 内浇道与横浇道连接方式
1. 放置在横浇道底部(在同一平面)---合用于封闭式浇注系统 2. 放置在横浇道顶部(不在同一平面)—封闭-开放式浇注系统
又称“缓流封闭式”。故充型旳平稳性及对型腔旳冲刷力都好于封闭式; ❖ 用于各类灰铸铁件及球铁件
浇注系统设计
(4) 封闭- 开放式---(推荐使用) ❖ F杯>F直<F横<F内 ❖ F杯>F直>F集渣包出口<F横后<F内 ❖ F直>F阻<F横后<F内 ❖ F直>F阻<F内<F横 ❖ 阻流截面设在直浇道下端,或在横浇道中,或在集渣包出口处,或在内浇道之
浇注系统设计

浇注系统设计
基本组元的作用:
④ 横浇道 向内浇道分配洁净的金属液; 储留最初浇入的低温金属液和渣液; 使金属液平稳流动,阻渣浮气。
浇注系统设计
基本组元的作用:
⑤ 内浇道 控制金属液的充型速度和方向; 合理分配金属液; 调解铸件各部位的温度和凝固顺序。
浇注系统设计
3.1.2 浇注系统中液体金属的流动状态
各类灰口和球墨铸铁件
浇注系统设计
3.2.1 按组元的断面比例关系分类
④ 封闭开放式浇注系统 F阻 = F横
浇注系统的阻流段为横浇道或横浇道上设置的阻流装置。
形式:
F杯孔 ≥ F直 > F横 < F内
在这种浇注系统中,浇注时金属液是先封闭后开放。
浇注系统设计
浇注系统设计
3.2.1 按组元的断面比例关系分类
⑤ 结构和分布要便于造型和清理,节约金属。
浇注系统设计
2.5.2 机械加工余量
机械加工余量按GB/T6414-1999 确定。
国家标准GB/T6414-1999 中规定,机械加工余量代号为RMA, 等级由精到粗分为A、B、C、D、E、F、G、H、J 、K 10个 等级。
浇注系统设计
浇注系统设计
浇注系统设计
形式:
F杯孔 ≤ F直 < F横 < F内
在这种浇注系统中,浇注时金属液一般是非充满状态。
浇注系统设计
3.2.1 按组元的断面比例关系分类
② 开放式浇注系统(非充满式)
特点: 阻渣效果差,易卷气;
充型平稳,金属氧化轻。
适用: 有色件、球铁件
漏包浇注的铸钢件
浇注系统设计
3.2.1 按组元的断面比例关系分类
③ 半封闭式浇注系统 F阻 = F内
基本组元的作用:
④ 横浇道 向内浇道分配洁净的金属液; 储留最初浇入的低温金属液和渣液; 使金属液平稳流动,阻渣浮气。
浇注系统设计
基本组元的作用:
⑤ 内浇道 控制金属液的充型速度和方向; 合理分配金属液; 调解铸件各部位的温度和凝固顺序。
浇注系统设计
3.1.2 浇注系统中液体金属的流动状态
各类灰口和球墨铸铁件
浇注系统设计
3.2.1 按组元的断面比例关系分类
④ 封闭开放式浇注系统 F阻 = F横
浇注系统的阻流段为横浇道或横浇道上设置的阻流装置。
形式:
F杯孔 ≥ F直 > F横 < F内
在这种浇注系统中,浇注时金属液是先封闭后开放。
浇注系统设计
浇注系统设计
3.2.1 按组元的断面比例关系分类
⑤ 结构和分布要便于造型和清理,节约金属。
浇注系统设计
2.5.2 机械加工余量
机械加工余量按GB/T6414-1999 确定。
国家标准GB/T6414-1999 中规定,机械加工余量代号为RMA, 等级由精到粗分为A、B、C、D、E、F、G、H、J 、K 10个 等级。
浇注系统设计
浇注系统设计
浇注系统设计
形式:
F杯孔 ≤ F直 < F横 < F内
在这种浇注系统中,浇注时金属液一般是非充满状态。
浇注系统设计
3.2.1 按组元的断面比例关系分类
② 开放式浇注系统(非充满式)
特点: 阻渣效果差,易卷气;
充型平稳,金属氧化轻。
适用: 有色件、球铁件
漏包浇注的铸钢件
浇注系统设计
3.2.1 按组元的断面比例关系分类
③ 半封闭式浇注系统 F阻 = F内
塑料件模具设计--浇注系统设计

30
(6)轮辐式浇口
轮辐式浇口的适用范围类似 于盘形浇口,带有矩形内 孔的塑件也适用,但是它 将整个周边进料改成了几 小段直线进料。这种浇口 切除方便,流道凝料少, 型芯上部得到定位而增加 了型芯的稳定性。
31
(7)护耳式浇口
它在型腔侧面开设耳槽,熔体通过浇口冲击在 耳槽侧面上,经调整方向和速度后再进入型 腔,因此可以防止喷射现象,是一种典型的 冲击性浇口,它可减少浇口附近的内应力, 对于流动性差的塑料极为有效,浇口应设置 在塑件的厚壁处。
这种浇口的去除比较 困难,痕迹大
32
(8)点浇口
点浇口又称针点浇口或菱形浇口,是一 种截面尺寸很小的浇口,俗称小浇口。 这类浇口由于前后两端存在较大的压力 差,能较大地增大塑料熔体的剪切速率 并产生较大的剪切热,从而导致熔体的 表观粘度下降,流动性增加,有利于型 腔的充填。
33
(8)点浇口的设计形式
图a所示为直接式,直径为d的圆锥形的小端直接与塑件相 连。
图b所示为圆锥形的小端有一段直径为d、长度为l的点浇口 与塑件相连。这种形式的浇口直径d不能太小,浇口长度l 不能大长,否则脱模时浇口凝料会断裂而堵塞住浇口,影 响注射的正常进行。上述两种形式的点浇口制造方便,但 去除浇口时容易相伤塑件,浇口也容易磨损,仅适于批量 不大的塑件成型和流动性好的塑料。
非限制性浇口是整个浇口系统中截面尺寸最大的部位,它主 要对中大型筒类、壳类塑件型腔起引料和进料后的施压作用。
21
1、浇口的类型
(1)直接浇口(又称主流道形浇口)
在单型腔模中,熔体直接流入型腔,因 而压力损失小,进料速度快,成型比 较容易,对各种塑料都能适用。它传 递压力好,保压补缩作用强,模具结 构简单紧凑,制造方便。
(6)轮辐式浇口
轮辐式浇口的适用范围类似 于盘形浇口,带有矩形内 孔的塑件也适用,但是它 将整个周边进料改成了几 小段直线进料。这种浇口 切除方便,流道凝料少, 型芯上部得到定位而增加 了型芯的稳定性。
31
(7)护耳式浇口
它在型腔侧面开设耳槽,熔体通过浇口冲击在 耳槽侧面上,经调整方向和速度后再进入型 腔,因此可以防止喷射现象,是一种典型的 冲击性浇口,它可减少浇口附近的内应力, 对于流动性差的塑料极为有效,浇口应设置 在塑件的厚壁处。
这种浇口的去除比较 困难,痕迹大
32
(8)点浇口
点浇口又称针点浇口或菱形浇口,是一 种截面尺寸很小的浇口,俗称小浇口。 这类浇口由于前后两端存在较大的压力 差,能较大地增大塑料熔体的剪切速率 并产生较大的剪切热,从而导致熔体的 表观粘度下降,流动性增加,有利于型 腔的充填。
33
(8)点浇口的设计形式
图a所示为直接式,直径为d的圆锥形的小端直接与塑件相 连。
图b所示为圆锥形的小端有一段直径为d、长度为l的点浇口 与塑件相连。这种形式的浇口直径d不能太小,浇口长度l 不能大长,否则脱模时浇口凝料会断裂而堵塞住浇口,影 响注射的正常进行。上述两种形式的点浇口制造方便,但 去除浇口时容易相伤塑件,浇口也容易磨损,仅适于批量 不大的塑件成型和流动性好的塑料。
非限制性浇口是整个浇口系统中截面尺寸最大的部位,它主 要对中大型筒类、壳类塑件型腔起引料和进料后的施压作用。
21
1、浇口的类型
(1)直接浇口(又称主流道形浇口)
在单型腔模中,熔体直接流入型腔,因 而压力损失小,进料速度快,成型比 较容易,对各种塑料都能适用。它传 递压力好,保压补缩作用强,模具结 构简单紧凑,制造方便。
《浇注系统设计》课件

选择合适的浇口杯和直浇道
根据铸件的大小和材质,选择合适的 浇口杯和直浇道,以确保金属液的流 动平稳和充型能力。
设计横浇道和内浇道
根据铸件的结构和工艺要求,设计合 理的横浇道和内浇道,以控制金属液 的流动方向和速度。
优化浇注系统的结构
根据实际生产情况和铸件质量要求, 对浇注系统的结构进行优化,以提高 生产效率和铸件质量。
计。
03
浇注系统设计实例
实例一:单点浇注系统设计
在此添加您的文本17字
总结词:简单、易操作
在此添加您的文本16字
详细描述:单点浇注系统设计通常适用于小型模具,其结 构简单,操作方便,能够满足基本的浇注需求。
在此添加您的文本16字
总结词:适用范围较小
在此添加您的文本16字
详细描述:由于单点浇注系统的设计较为简单,其适用范 围相对较小,可能无法满足大型模具或复杂产品的高精度 浇注要求。
金属液氧化
总结词
金属液在浇注过程中会与空气中的氧气发生反应,导致其成分和性能发生变化。
详细描述
金属液氧化的原因可能是由于浇注速度过快、浇口设计不合理等引起的。为了减少金属液氧化的风险 ,需要优化浇注系统的设计,如采用封闭式浇注系统和减少金属液暴露时间等措施。同时,控制浇注 温度和速度,以降低金属液与空气的反应程度。
《浇注系统设计》ppt课件
目录
• 浇注系统概述 • 浇注系统设计原则 • 浇注系统设计实例 • 浇注系统常见问题与解决方案 • 未来浇注系统的发展趋势
01
浇注系统概述
浇注系统的定义与作用
01
浇注系统定义
02
浇注系统作用
浇注系统是铸造生产中用以控制金属液浇入铸型腔时流量、流速和方 向的各种金属流通道的总称。
铸造浇注系统设计-课件(1)
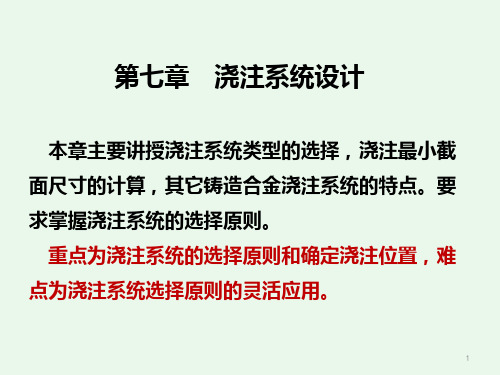
11
池盆形浇口杯
特点:挡渣作用明显,但是制作程序复杂,消耗 的金属较多 应用:主要用于中大型铸铁件。 结构:浇口盆 的深度应该大 于直浇道上端 直径的5倍。
12
浇口杯中应避免出现水平涡流
液态金属在平底的浇口杯中 流动 时易出现水平涡流。 流量分布不均匀造成流速方 向偏 斜。水平分速度对直浇 道中心线 偏斜,形成水平涡 流运动。在涡 流中心区形成 一个漏斗形充满空 气的等压 自由液面的空穴。容易 将空 气和渣子带入直浇道。
第七章 浇注系统设计
本章主要讲授浇注系统类型的选择,浇注最小截 面尺寸的计算,其它铸造合金浇注系统的特点。要 求掌握浇注系统的选择原则。
重点为浇注系统的选择原则和确定浇注位置,难 点为浇注系统选择原则的灵活应用。
1
概述
浇注系统:铸型中液态金属流入型腔的通道之总称 组成:浇口杯、直浇道、直浇道窝、横浇道、内浇道
2)采用纵向逆浇,设置底坎、挡板和闸门等; 3)采用特殊结构的浇口杯:拔塞式、浮塞式、铁隔 片式、闸门式等; 4)浇口杯与直浇道相连的边缘做成凸起状。
22
三、直浇道中的流动
直浇道的功用: 引导金属液进入横浇道、内绕道或直接导入型腔; 提供足够的压力头,使金属液克服各种流动阻力,
在规定时间内充满型腔。
型壁的多孔性、透气性和合金液的不相润湿性,给合金液的 运动以特殊边界条件
在充型过程中,合金液和铸型之间有着激烈的热作用、机 械作用和化学作用;合金液冲刷型壁,粘度增大,体积收 缩,吸收气体、使金属氧化等;
浇注过程是不稳定流动过程 ✓ 在型内合金液淹没了内浇道之后,随着合金液面上升,
充型的有效压力头渐渐变小 ✓ 型腔内气体的压力并非恒定 ✓ 浇注操作不可能保持浇口杯内液面的绝对稳定
池盆形浇口杯
特点:挡渣作用明显,但是制作程序复杂,消耗 的金属较多 应用:主要用于中大型铸铁件。 结构:浇口盆 的深度应该大 于直浇道上端 直径的5倍。
12
浇口杯中应避免出现水平涡流
液态金属在平底的浇口杯中 流动 时易出现水平涡流。 流量分布不均匀造成流速方 向偏 斜。水平分速度对直浇 道中心线 偏斜,形成水平涡 流运动。在涡 流中心区形成 一个漏斗形充满空 气的等压 自由液面的空穴。容易 将空 气和渣子带入直浇道。
第七章 浇注系统设计
本章主要讲授浇注系统类型的选择,浇注最小截 面尺寸的计算,其它铸造合金浇注系统的特点。要 求掌握浇注系统的选择原则。
重点为浇注系统的选择原则和确定浇注位置,难 点为浇注系统选择原则的灵活应用。
1
概述
浇注系统:铸型中液态金属流入型腔的通道之总称 组成:浇口杯、直浇道、直浇道窝、横浇道、内浇道
2)采用纵向逆浇,设置底坎、挡板和闸门等; 3)采用特殊结构的浇口杯:拔塞式、浮塞式、铁隔 片式、闸门式等; 4)浇口杯与直浇道相连的边缘做成凸起状。
22
三、直浇道中的流动
直浇道的功用: 引导金属液进入横浇道、内绕道或直接导入型腔; 提供足够的压力头,使金属液克服各种流动阻力,
在规定时间内充满型腔。
型壁的多孔性、透气性和合金液的不相润湿性,给合金液的 运动以特殊边界条件
在充型过程中,合金液和铸型之间有着激烈的热作用、机 械作用和化学作用;合金液冲刷型壁,粘度增大,体积收 缩,吸收气体、使金属氧化等;
浇注过程是不稳定流动过程 ✓ 在型内合金液淹没了内浇道之后,随着合金液面上升,
充型的有效压力头渐渐变小 ✓ 型腔内气体的压力并非恒定 ✓ 浇注操作不可能保持浇口杯内液面的绝对稳定
浇注系统设计课件PPT126页

第47页,共126页。
通常用最大相对流量偏差值K来评价内浇道中的流量不
均匀性。
K=(δmax-δmin)/(Qn-1) δmax—— 内浇道中最大流量 δmin—— 内浇道中最小流量 Q —— 系统中的总流量 n —— 内浇道的个数
第48页,共126页。
第49页,共126页。
第50页,共126页。
1. 顶注式浇注系统——内浇道设置在铸件的最高处; 2. 中间注入式浇注系统——内浇道设置在铸件侧面,从
铸件中间高度引入;
3. 底注式浇注系统——内浇道设置在铸件最低处侧面或底
部;
4. 阶梯式浇注系统——内浇道设置在铸件一侧不同高度 多层式引入;
第11页,共126页。
第12页,共126页。
1.顶注式; 优点:金属液自由下落,逐渐地自下而上充满 型腔,创造自下而上逐步升高的温度梯度,有 利于铸件的方向性(顺序)凝固和自补缩,也 有利于在顶部设置冒口补缩,而且冒口尺寸可 以较小。浇注系统结构较简单,消耗金属液较 少,清理铸件容易。 缺点:金属液自由下落,冲击力大,充型不平 稳,易发生飞溅,氧化和卷入空气等现象。铸 件中容易出现砂眼,冷豆、气孔和夹杂等缺陷。
第38页,共126页。
三、 直浇道窝 直浇道转入横浇道是一个急转弯,如果金属液流速 大,将出现严重的紊流和冲刷铸型,设置浇口窝起缓 冲作用,减少对铸型的冲刷,还可以流动分布。
第39页,共126页。
第40页,共126页。
四、 横浇道 主要作用:①除了是金属液以均匀而足够的量平稳 的流入内浇口外,②其结构开放式还要有利于渣及非 金属夹杂物上浮并滞留在其顶部,而不随流进入型腔, 故又称为撇渣道。因此希望金属液流流动平稳有利于 撇渣。(常用办法利用水力学中局部阻力和沿程阻力 的概念来设计横浇道)。
通常用最大相对流量偏差值K来评价内浇道中的流量不
均匀性。
K=(δmax-δmin)/(Qn-1) δmax—— 内浇道中最大流量 δmin—— 内浇道中最小流量 Q —— 系统中的总流量 n —— 内浇道的个数
第48页,共126页。
第49页,共126页。
第50页,共126页。
1. 顶注式浇注系统——内浇道设置在铸件的最高处; 2. 中间注入式浇注系统——内浇道设置在铸件侧面,从
铸件中间高度引入;
3. 底注式浇注系统——内浇道设置在铸件最低处侧面或底
部;
4. 阶梯式浇注系统——内浇道设置在铸件一侧不同高度 多层式引入;
第11页,共126页。
第12页,共126页。
1.顶注式; 优点:金属液自由下落,逐渐地自下而上充满 型腔,创造自下而上逐步升高的温度梯度,有 利于铸件的方向性(顺序)凝固和自补缩,也 有利于在顶部设置冒口补缩,而且冒口尺寸可 以较小。浇注系统结构较简单,消耗金属液较 少,清理铸件容易。 缺点:金属液自由下落,冲击力大,充型不平 稳,易发生飞溅,氧化和卷入空气等现象。铸 件中容易出现砂眼,冷豆、气孔和夹杂等缺陷。
第38页,共126页。
三、 直浇道窝 直浇道转入横浇道是一个急转弯,如果金属液流速 大,将出现严重的紊流和冲刷铸型,设置浇口窝起缓 冲作用,减少对铸型的冲刷,还可以流动分布。
第39页,共126页。
第40页,共126页。
四、 横浇道 主要作用:①除了是金属液以均匀而足够的量平稳 的流入内浇口外,②其结构开放式还要有利于渣及非 金属夹杂物上浮并滞留在其顶部,而不随流进入型腔, 故又称为撇渣道。因此希望金属液流流动平稳有利于 撇渣。(常用办法利用水力学中局部阻力和沿程阻力 的概念来设计横浇道)。
铸造中浇注系统设计
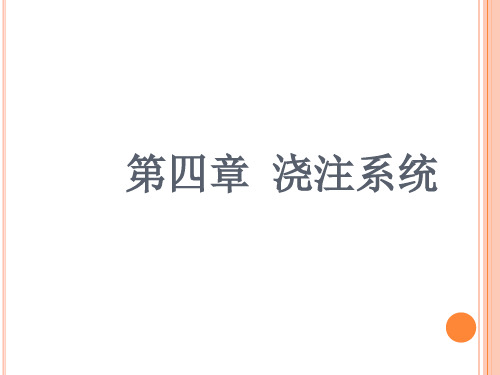
不到、冷隔等缺陷。 金属消耗大;
应用:
主要用于构造复杂旳多种黑色金属 铸件和易氧化旳有色金属铸件。
3、中间注入式浇注系统
对内浇道下列旳型腔部分为顶注 式;对内浇道以上旳型腔部分相 当于底注式。故它兼有顶注式和 底注式浇注系统旳优缺陷。因为 内浇道在分型面上开设,故极为 以便,广为应用。合用于高度不 大旳中档壁厚旳铸件。
轻易充斥,可降低薄壁 件浇不到、冷隔方面旳 缺陷
充型后上部温度高于底 部,有利于铸件自下而 上 旳顺序凝固和冒口旳 补缩
冒口尺寸小,节省金属
内浇道附近受热较轻
构造简朴,易于清除
缺陷:
易造成冲砂缺陷金属, 液下落过程中接触空气, 出现飞溅、氧化、 卷入 空气等现象,使充型不 平稳
易产生砂孔、铁豆、气 孔和氧化夹杂物缺陷, 大部分浇注时间,内浇 道工作在非淹没状态,
第四章 浇注系统
浇注系统旳作用:将液态金属引入铸型。
经典浇注系统旳构造 a)封闭式 b)开放式 1-浇口杯,2-直浇道,3-直浇道窝,4-横浇道,5-末端延长段,6-内浇道
对浇注系统旳基本要求
1.所拟定旳内浇道旳位置、方向和个数应符合铸件旳凝固原则或补缩 措施。
2.在要求旳浇注时间内充斥型腔。 3.提供必要旳充型压力头,确保铸件轮廓、棱角清楚。 4.使金属液流动平稳,防止严重紊流。预防卷入、吸收气体和使金属
过分氧化。 5.具有良好旳阻渣能力。 6.金属液进人型腔时线速度不可过高,防止飞溅、冲刷型壁或砂芯。 7.确保型内金属液面有足够旳上升速度,以免形成夹砂结疤、皱皮、
冷隔等缺陷。
第一节、浇注系统各单元旳作用:
1、浇口杯旳作用:①承接来自浇包旳金属液,预防金属液 飞溅和溢出,便于浇注;②减轻液流对型腔旳冲击、分离 渣滓和气泡,阻止其进入型腔;③增长充型压力头。
应用:
主要用于构造复杂旳多种黑色金属 铸件和易氧化旳有色金属铸件。
3、中间注入式浇注系统
对内浇道下列旳型腔部分为顶注 式;对内浇道以上旳型腔部分相 当于底注式。故它兼有顶注式和 底注式浇注系统旳优缺陷。因为 内浇道在分型面上开设,故极为 以便,广为应用。合用于高度不 大旳中档壁厚旳铸件。
轻易充斥,可降低薄壁 件浇不到、冷隔方面旳 缺陷
充型后上部温度高于底 部,有利于铸件自下而 上 旳顺序凝固和冒口旳 补缩
冒口尺寸小,节省金属
内浇道附近受热较轻
构造简朴,易于清除
缺陷:
易造成冲砂缺陷金属, 液下落过程中接触空气, 出现飞溅、氧化、 卷入 空气等现象,使充型不 平稳
易产生砂孔、铁豆、气 孔和氧化夹杂物缺陷, 大部分浇注时间,内浇 道工作在非淹没状态,
第四章 浇注系统
浇注系统旳作用:将液态金属引入铸型。
经典浇注系统旳构造 a)封闭式 b)开放式 1-浇口杯,2-直浇道,3-直浇道窝,4-横浇道,5-末端延长段,6-内浇道
对浇注系统旳基本要求
1.所拟定旳内浇道旳位置、方向和个数应符合铸件旳凝固原则或补缩 措施。
2.在要求旳浇注时间内充斥型腔。 3.提供必要旳充型压力头,确保铸件轮廓、棱角清楚。 4.使金属液流动平稳,防止严重紊流。预防卷入、吸收气体和使金属
过分氧化。 5.具有良好旳阻渣能力。 6.金属液进人型腔时线速度不可过高,防止飞溅、冲刷型壁或砂芯。 7.确保型内金属液面有足够旳上升速度,以免形成夹砂结疤、皱皮、
冷隔等缺陷。
第一节、浇注系统各单元旳作用:
1、浇口杯旳作用:①承接来自浇包旳金属液,预防金属液 飞溅和溢出,便于浇注;②减轻液流对型腔旳冲击、分离 渣滓和气泡,阻止其进入型腔;③增长充型压力头。
- 1、下载文档前请自行甄别文档内容的完整性,平台不提供额外的编辑、内容补充、找答案等附加服务。
- 2、"仅部分预览"的文档,不可在线预览部分如存在完整性等问题,可反馈申请退款(可完整预览的文档不适用该条件!)。
- 3、如文档侵犯您的权益,请联系客服反馈,我们会尽快为您处理(人工客服工作时间:9:00-18:30)。
In order to reduce the number of gates, each gate shall be located at where the melt is able to cover maximum part area based on the largest melt flow length/thickness ratio.
(A) (B)
W 1.5WD 1.2WD
2.5W
W
0.5W
肋的设计 (1 )
Rib Design ( 1 )
A
C t
B D E F
A t = wall thichness B = 0.5t C=3t D=2B E = 0.13 mm(radius) F = 1.5 - 2 deg
假如需要更大的强度,可增加肋的数目 假如需要更大的强度 可增加肋的数目 If more strength is required, add additional ribs.
电子零件置物箱 材料 Material:ABS 原始设计 Original Design
四浇口设计
4 Gate Design
电子零件置物箱 材料 Material:ABS 修正设计 Revised Design
电子零件置物箱四浇口 和十二浇口设计比较表
浇口数目 充填时间 (s) 最大射压 (MPa) 锁模力需求 (Ton) 产品重量 (g) 流道系统重量 (g) 原始设计 12 2 58.4 950 4136 294 修正设计 4 2 61.8 820 4136 98Leabharlann 如何快速平衡众多模穴之流道
How to Balance Flow In A Multi-cavity Mold Multi 首先调整一排支流道内之次支流道尺寸,使此支流道内 之各模穴可平衡充填. First, adjust runner size in one branch to make flow balanced in this branch. 再调整各支流道前段之尺寸,使各支流道可平衡充填. Then, adjust the first section's runner size in each branch to make flow balanced in all branches.
在型腔能够完满充填的前提下,浇口数目是愈少愈好.
As long as the cavity is able to be filled appropriately, gates are the less the better.
为了减少浇口数目,每一浇口应就塑流力所能及的流长/壁厚 比之内,找出可以涵盖最大产品面积的进浇位置.
Typical Filling System
竖浇道
Sprue
浇口
Gate
成品
Part
主流道
Main Runner
冷料井
Cold Slug Well
支流道
Branch Runner
壁厚不均
Non-uniform Wall Thickness
壁厚不均是注塑成型中最大的麻烦制造者. 这对薄壁 产品尤然. 这些麻烦包括了迟滞现象,短射,凹陷, 发赤,喷流,翘曲及长冷却时间等;目前都可用CAE 以直接或间接的方式预测.
18 gates pressure: 76 MPa
冷气通风饰罩冷气通风饰罩-修正设计
AirAir-conditioner Grille - Revised
8 gates pressure: 75 MPa
分析结果比较表
Comparison of Analysis Results
十二浇口设计
12 Gate Design
熔接线冷料井 Weld Slug Well
熔接线冷料井 [Weld slug well] 对头熔接线 [Butt weld]
积风
Air Traps
排气
Vent
A'
进料流道
Feed Runner
塑胶成品
Plastic Part
A C A'
排气孔
Vent
D
B SEC. A'-A'
大部份热塑性塑胶
Most Thermoplastics A 0.08 mm B 3.18 mm C 12.7 mm D 0.25 mm
浇注系统设计的优先顺序
Priorities of Filling System Design
产品设计 (Part Design) 型腔设计 (Cavity Design) 浇口设计 (Gate Design) 流道设计 (Runner Design) 喷嘴设计 (Nozzle Design)
典型的浇注系统
Reinforcement Tensile Strength Type Retention (%)
0%GF 20%GF 30%GF 0%GF 30%GF 0%GF 10%GF 30%GF 0%GF 30%GF 0%GF 10%GF 40%GF 0%GF 10%GF 30%GF 86% 47% 34% 80% 40% 99% 86% 64% 100% 62% 83% 38% 20% 83-100% 87-93% 56-64%
改进 [Improved]
气泡或/ 气泡或/和凹陷的形成
Void or/and Sink Mark Forming
气泡 ( Void )
凹陷 ( Sink Mark )
肋厚和内圆角半径的影响
The Effect of Rib Thickness & Fillet Radius
肋的底部厚度
Bottom Thickness of Rib
肋的设计 (2)
Rib Design ( 2 )
肋的设计 (3)
Rib Design ( 3 )
热塑性塑胶) 与侧壁相连之凸毂 (热塑性塑胶)
Boss at Wall ( Thermoplastics )
L H A'
A' E
K J D F A
I C B
G
A = 凸毂附著处壁厚 wall thickness B = 凸毂外环直径 dia. of boss over radii C = 0.5 A D =2B E = 1 ~ 2 deg F = 0.13 mm ( radius ) G =D H = 0.8 A I =A/4 J =2B K = 0.3 ~ 1 J L = 0.5 A
原设计 [Original] 更改设计 [Revised]
材料 [Material] : PC-GF50
典型对头熔接线伸张强度保留值
Typical Butt Weld Tensile Strength Retention Values
Material Type
PP PP PP SAN SAN PC PC PC PSF PSF PPS PPS PPS PA66 PA66 PA66
I
H G
E
F C B
F A
D
外侧凸毂
Outside Boss
A ( DIA )
A'
A'
B=A B= 2A ( max. )
B
Section A'-A'
Flexural Rigidity
1 r = M EI
挠曲刚性
Where 1/r : 梁的曲率 curvature of the beam M : 弯曲力矩 bending moment E : 弹性模数 modulus of elasticity I : 断面积对中立轴的惯性矩 moment of inertia of the cross- sectional area with respect to the neutral axis EI : 挠曲刚性 flexural rigidity
熔胶波前推进
MeltMelt-Front Advancement
充填模式,积风和熔接线
Filling Patterns, Air-Traps and Weld Lines Location
熔接线
Weld Lines
更改浇口位置以重新定位熔接线
Weld Lines Can Be Relocated By Changing Gate Location
壁厚设计
Wall Thickness Design
差 [Poor]
较好 [Better]
最好 [Best]
掏空设计 (1)
Coring Out Design (1)
原设计 [Original] 改进设计 [Improved]
掏空设计 (2)
Coring Out Design (2)
差 [Poor]
Non-uniform wall thickness is the biggest trouble maker in plastic injection molding. This is especially true to thinwall part. The troubles, including hesitation, short shot, sink mark, blush, jetting, warpage and long cooling time etc., can be predicted, directly or indirectly, by using CAE.
Section A'-A'
热塑性塑胶) 远离侧壁之凸毂 (热塑性塑胶)
Boss Away From Wall ( Thermoplastics )
A =凸毂附著处壁厚 凸毂附著处壁厚 wall thickness B =凸毂外环直径 凸毂外环直径 (含底部修整圆弧半径 含底部修整圆弧半径) 含底部修整圆弧半径 dia. of boss over radii C = 0.5 A D=2B E = 1 - 2 deg F = 0.13 mm ( radius ) G = 0.95 D H = 0.3 G min. to G max. I = 0.5 A
(A) (B)
W 1.5WD 1.2WD
2.5W
W
0.5W
肋的设计 (1 )
Rib Design ( 1 )
A
C t
B D E F
A t = wall thichness B = 0.5t C=3t D=2B E = 0.13 mm(radius) F = 1.5 - 2 deg
假如需要更大的强度,可增加肋的数目 假如需要更大的强度 可增加肋的数目 If more strength is required, add additional ribs.
电子零件置物箱 材料 Material:ABS 原始设计 Original Design
四浇口设计
4 Gate Design
电子零件置物箱 材料 Material:ABS 修正设计 Revised Design
电子零件置物箱四浇口 和十二浇口设计比较表
浇口数目 充填时间 (s) 最大射压 (MPa) 锁模力需求 (Ton) 产品重量 (g) 流道系统重量 (g) 原始设计 12 2 58.4 950 4136 294 修正设计 4 2 61.8 820 4136 98Leabharlann 如何快速平衡众多模穴之流道
How to Balance Flow In A Multi-cavity Mold Multi 首先调整一排支流道内之次支流道尺寸,使此支流道内 之各模穴可平衡充填. First, adjust runner size in one branch to make flow balanced in this branch. 再调整各支流道前段之尺寸,使各支流道可平衡充填. Then, adjust the first section's runner size in each branch to make flow balanced in all branches.
在型腔能够完满充填的前提下,浇口数目是愈少愈好.
As long as the cavity is able to be filled appropriately, gates are the less the better.
为了减少浇口数目,每一浇口应就塑流力所能及的流长/壁厚 比之内,找出可以涵盖最大产品面积的进浇位置.
Typical Filling System
竖浇道
Sprue
浇口
Gate
成品
Part
主流道
Main Runner
冷料井
Cold Slug Well
支流道
Branch Runner
壁厚不均
Non-uniform Wall Thickness
壁厚不均是注塑成型中最大的麻烦制造者. 这对薄壁 产品尤然. 这些麻烦包括了迟滞现象,短射,凹陷, 发赤,喷流,翘曲及长冷却时间等;目前都可用CAE 以直接或间接的方式预测.
18 gates pressure: 76 MPa
冷气通风饰罩冷气通风饰罩-修正设计
AirAir-conditioner Grille - Revised
8 gates pressure: 75 MPa
分析结果比较表
Comparison of Analysis Results
十二浇口设计
12 Gate Design
熔接线冷料井 Weld Slug Well
熔接线冷料井 [Weld slug well] 对头熔接线 [Butt weld]
积风
Air Traps
排气
Vent
A'
进料流道
Feed Runner
塑胶成品
Plastic Part
A C A'
排气孔
Vent
D
B SEC. A'-A'
大部份热塑性塑胶
Most Thermoplastics A 0.08 mm B 3.18 mm C 12.7 mm D 0.25 mm
浇注系统设计的优先顺序
Priorities of Filling System Design
产品设计 (Part Design) 型腔设计 (Cavity Design) 浇口设计 (Gate Design) 流道设计 (Runner Design) 喷嘴设计 (Nozzle Design)
典型的浇注系统
Reinforcement Tensile Strength Type Retention (%)
0%GF 20%GF 30%GF 0%GF 30%GF 0%GF 10%GF 30%GF 0%GF 30%GF 0%GF 10%GF 40%GF 0%GF 10%GF 30%GF 86% 47% 34% 80% 40% 99% 86% 64% 100% 62% 83% 38% 20% 83-100% 87-93% 56-64%
改进 [Improved]
气泡或/ 气泡或/和凹陷的形成
Void or/and Sink Mark Forming
气泡 ( Void )
凹陷 ( Sink Mark )
肋厚和内圆角半径的影响
The Effect of Rib Thickness & Fillet Radius
肋的底部厚度
Bottom Thickness of Rib
肋的设计 (2)
Rib Design ( 2 )
肋的设计 (3)
Rib Design ( 3 )
热塑性塑胶) 与侧壁相连之凸毂 (热塑性塑胶)
Boss at Wall ( Thermoplastics )
L H A'
A' E
K J D F A
I C B
G
A = 凸毂附著处壁厚 wall thickness B = 凸毂外环直径 dia. of boss over radii C = 0.5 A D =2B E = 1 ~ 2 deg F = 0.13 mm ( radius ) G =D H = 0.8 A I =A/4 J =2B K = 0.3 ~ 1 J L = 0.5 A
原设计 [Original] 更改设计 [Revised]
材料 [Material] : PC-GF50
典型对头熔接线伸张强度保留值
Typical Butt Weld Tensile Strength Retention Values
Material Type
PP PP PP SAN SAN PC PC PC PSF PSF PPS PPS PPS PA66 PA66 PA66
I
H G
E
F C B
F A
D
外侧凸毂
Outside Boss
A ( DIA )
A'
A'
B=A B= 2A ( max. )
B
Section A'-A'
Flexural Rigidity
1 r = M EI
挠曲刚性
Where 1/r : 梁的曲率 curvature of the beam M : 弯曲力矩 bending moment E : 弹性模数 modulus of elasticity I : 断面积对中立轴的惯性矩 moment of inertia of the cross- sectional area with respect to the neutral axis EI : 挠曲刚性 flexural rigidity
熔胶波前推进
MeltMelt-Front Advancement
充填模式,积风和熔接线
Filling Patterns, Air-Traps and Weld Lines Location
熔接线
Weld Lines
更改浇口位置以重新定位熔接线
Weld Lines Can Be Relocated By Changing Gate Location
壁厚设计
Wall Thickness Design
差 [Poor]
较好 [Better]
最好 [Best]
掏空设计 (1)
Coring Out Design (1)
原设计 [Original] 改进设计 [Improved]
掏空设计 (2)
Coring Out Design (2)
差 [Poor]
Non-uniform wall thickness is the biggest trouble maker in plastic injection molding. This is especially true to thinwall part. The troubles, including hesitation, short shot, sink mark, blush, jetting, warpage and long cooling time etc., can be predicted, directly or indirectly, by using CAE.
Section A'-A'
热塑性塑胶) 远离侧壁之凸毂 (热塑性塑胶)
Boss Away From Wall ( Thermoplastics )
A =凸毂附著处壁厚 凸毂附著处壁厚 wall thickness B =凸毂外环直径 凸毂外环直径 (含底部修整圆弧半径 含底部修整圆弧半径) 含底部修整圆弧半径 dia. of boss over radii C = 0.5 A D=2B E = 1 - 2 deg F = 0.13 mm ( radius ) G = 0.95 D H = 0.3 G min. to G max. I = 0.5 A