注塑模具浇注系统设计
模具基础篇6:注塑模具的浇注系统

模具基础篇6:注塑模具的浇注系统有了模具的成型部分,接下来的问题便是,如何将塑料注⼊模具型腔呢?于是接下来将要揭晓的,是模具的另⼀个重要组成—“浇注系统”(Injection System):“浇注系统”是模具上从注塑机喷嘴⾄模具型腔之间的通路,正是通过这个通路,塑料才能被从注塑机注⼊模腔。
通常我们将“浇注系统”分为两个部分:流道(Runner)与浇⼝(Gate)。
下⾯我们分别来介绍这两个部分:流道:“流道”是模具上介于喷嘴与“浇⼝”间的通道。
其实就注塑本⾝⽽⾔,流道的存在对整个注塑过程没有任何益处,有时甚⾄还会带来⿇烦。
因为,当喷嘴与模腔间出现⼀个额外的中介后,势必会带来熔融塑料的温度与压⼒的损失。
所以,注塑模具流道设计的⾸要原则便是:尽可能降低熔融塑料在流道内温度与压⼒的损失。
(尽量能使注塑过程忽略这⼀部分的存在)但是,由于模具结构、空间、功能等因素,流道在注塑模具中⼜是必不可少的。
在⼤多数情况下,模具上基本没有空间使喷嘴与模腔直接联接;此外,喷嘴与模腔直接接触,喷嘴的⾼热量也就势必传导⾄模具上,使模腔的温度受到影响,这是对注塑⾮常不利。
另外,由于⽣产效率的原因,模具通常不会仅有⼀个模腔。
对于“多腔模”(Multi Cavity Mold)来说,流道就会像树⼀样,将熔料从喷嘴经过主⼲与各个分⽀,最终到达模腔。
此时的流道还会附加⼀个要求,便是熔料在经过流道后,尽量能保证各个模腔内的流动状态⼀致。
这其中,直接与喷嘴连接,也就是熔融最先接触的部分称为“主流道”(Sprue),它通常与模具的主分形⾯垂直,为了防⽌注射压⼒的损失,“主流道”的直径会其它部分略微⼤⼀些。
“主流道”与产品型腔之间的部分,通常称为“分流道”(Runner)。
他们⽤以将熔融塑料分别均匀地送⼊各个不同的型腔。
“流道”与“型腔”之间的部分称为“浇⼝”(Gate),它是料流进⼊型腔的最后门户。
相⽐与“流道”,“浇⼝”的尺⼨要⼩得多,之所以要将其做得⼩,有三个主要原因。
注塑模具设计:第二章:浇注系统

第二章浇注系统注塑机喷嘴中熔融的塑料,经过主流道,分流道,最后通过浇口进入到模具型腔,然后经过冷却固化,得到所需要的制品。
所以注塑模具的浇注系统是指从注塑机喷嘴到型腔为止的塑料熔体的流动通道。
因为热塑性塑料的热传导率较低,流道中冷凝的表皮对芯部熔融的塑料祈祷保温作用,所以保证了流道芯部的塑料继续流动。
来自熔融的塑料的热加上由于流动摩擦二产生的摩擦热等于高温塑料与低温模具热交换所产生的热损失。
如果增加注射速度,冷凝层由于受到流动产生的高摩擦热而会变薄。
即:高速注射与低速注射对于冷凝层厚度影响的差别是比较明显的。
这就是为什么高压、高速注射容易将型腔填充饱满的主要原因之一。
浇注系统的型制与流动性为减少与热量的损失,必须使流道的表面积与体积之比保持最小,因为具有最小表面积与最大体积的形状是圆柱形,所以圆柱形是最优越的流道形状。
主流道从注射机喷嘴到分浇为止的熔融塑料的流动通道。
1)定模部分由整体构成2)定模部分由两块模板所构成3)最普遍常用的主流道结构,是以浇口套的形式镶入模板中,为防止被喷嘴撞伤,采取淬火处理主流道的基本尺寸取决于两个方面:1,塑料的种类,所成型的制品质量和壁厚大小。
2与注射机喷嘴的几何参数有关。
浇口套的求半径比喷嘴的球半径大2~5mm,脱模斜度一般最小不低于1°,最大不超过4°。
因为,主流道的脱模斜度不能过大,否则在注塑时会产生涡流和流速过慢等现象主流道应保持光滑的表面,避免留有影响塑料流动或脱模的尖角毛刺等。
而且在主流道的末端还应设置冷料井以防止制品中出现固化的冷料(最先流入模具的塑料)。
设置冷料井,以便将这部分冷料存留起来。
这一点对分流道也同样重要。
分流道分流道可以理解为从主流道末端开始到浇口为止的塑料熔体的流动通道。
鉴于圆形截面的浇道必须设置在以分型面为界的动、定模两部分,所以对制造工艺要求较高,且启模时,分流道中经过冷却固化的塑料留在动、定模内是随机的。
所以实际制造中,U 性截面分流道或梯形截面的分流道比较常用,虽然热量损失较大一点,但加工制造比较简单,并且启模时,冷料留在动定模哪一部分,将是确定的。
典型注塑模设计-项目1-模块三

1.排气系统
大多数情况下可利用模具分型面或模具零件间的配合间隙自然地排气 ,其间隙值通常为0.01~0.03mm,以不产生溢料为限。
排气与引气系统的设计
相关理论知识
2.引气系统的设计 大型深壳形制品包紧型芯形成真空,难以脱模,需要引气装置。 镶拼式侧隙引气 气阀式引气 相关理论知识
能合理地设计浇注系统
能合理地进行成型零件设计
能正确地绘制模具装配图和零件工作图
1.能设计合理的冷却系统 2.能设计合理的排气系统 3.能绘制合理的冷却水道布置图
学习目标
工作任务
根据图示的塑件零件图以及已确定的总体结构方案,设计本模具的冷却系统和排气系统,并绘制冷却水道布置图。
冷却系统设计
低粘度-低模温
单击此处添加正文,文字是您思想的提炼,为了演示发布的良好效果,请言简意赅地阐述您的观点。您的内容已经简明扼要,字字珠玑,但信息却千丝万缕、错综复杂,需要用更多的文字来表述;但请您尽可能提炼思想的精髓,否则容易造成观者的阅读压力,适得其反。正如我们都希望改变世界,希望给别人带去光明,但更多时候我们只需要播下一颗种子,自然有微风吹拂,雨露滋养。恰如其分地表达观点,往往事半功倍。当您的内容到达这个限度时,或许已经不纯粹作用于演示,极大可能运用于阅读领域;无论是传播观点、知识分享还是汇报工作,内容的详尽固然重要,但请一定注意信息框架的清晰,这样才能使内容层次分明,页面简洁易读。如果您的内容确实非常重要又难以精简,也请使用分段处理,对内容进行简单的梳理和提炼,这样会使逻辑框架相对清晰。
根据图示的塑件零件图以及已确定的总体结构方案,设计本模具的冷却系统和排气系统并绘制冷却水道布置图。
练习
高粘度-高模温
注塑模具浇注系统设计素材

因此,设计时应尽量避免主流道偏离 模具中心,但在侧浇口浇注系统中,常常 由于以下原因,主流道位置必须偏离模具 中心: ①一模多腔中的制品大小悬殊; ②单型腔,制品较大,中间有较大的碰穿 孔,可以从内侧进料。但中间碰穿孔偏离 模具中心。
如果主流道偏离模具中心不可避免,那 么,可以采取三种措施,来避免或减轻不 良后果对模具的影响: ①增加推杆固定板导柱(中托边)来承受顶 棍偏心产生的扭力; ②模具较大时,也可采用双顶棍孔或多 顶棍孔,使推杆固定板受到多点推力的作 用时,较易平衡推出; ③采用倾斜式主流道,避免顶棍孔偏心 (见图)
(2)型腔的数量
它决定分流道的走向、长短和大小。
(3)壁厚及内在外观质量要求
这些因素决定了浇口的位置和形式,最 终决定分流道的走向和大小。 注意:如果要采用自动化注塑,则分流 道必须确保在开模后留在后模,且容易推 落。
分流道的布置
在确定分流道的布置时,应尽量使流道 长度最短。但是,塑料以低温成型时,为 提高成型空间的压力来减少成型制品收缩 凹陷时,或欲得壁厚较厚的成型制品而延 长保压时间,减短流道长度并非绝对可行。 因为流道过短,则成型制品的残留应力 增大,且易产生飞边,塑料的流动不均, 所以流道长度应以适合成型制品的质量和 结构为宜。
(4)主流道应设计在浇口套内
主流道尽量避免直接做在模板内,或采 用镶拼结构,以防塑料进入接缝造成脱模 困难。
(5)主流道应尽量和模具中心重合
避免浇口套位置偏心或采用倾斜式主流 道。
倾斜式主流道设计
倾斜式主流道设计
一般地,要求主流道的位置应尽量与模具中心 重合,否则会有如下不良后果。 ①主流道偏离模具中心时,导致锁模力和胀型 力不在一条线上,使模具在生产时受到扭矩的作 用,这个扭矩会使模具一侧张开产生飞边,或者 使型芯错位变形,最终还会导致磨具导柱,甚至 注射机拉杆变形等严重后果。 ②主流道偏离模具中心时,顶棍孔也要偏离模 具中心,制品推出时,推杆板也会受到一个扭力 的作用,这个扭力传递给推杆后,会导致推杆磨 损,甚至断裂。
注塑模具浇注系统三维参数化设计研究

芯 、 腔 上 自动 产 生 出 浇 注 系 统 , 型 而 浇 注 系 统 的 形 状 、位 置 与 尺 寸
() 圆 弧 C r l 4把 i c e围 成 面 F ,
F  ̄ F c l 的 法 矢 的 反 方 向 扫 沿 ae 面
由注 塑模 CE 件 分析 确 定 。 拟 A软 虚
口之 间 的 整 个 通 道 ,其 功 能 是 使
1主流道的设计 .
主 流 道 是 指 由注 塑 机 喷 嘴 出
口到分 流 道 人 口止 的一 段 通 道 , 主 流道 呈 圆锥 形,以 便充模 时熔
ቤተ መጻሕፍቲ ባይዱ以下值 得 改进 的 地方
() 采 用 二 维 的 设 计 方 法 , 1多 不 仅 视 图 表 示 困 难 ,更 重 要 的 是
口 来 说 为 0) , 并 指 定 一 个 面
Face2;
示 …。 中圆形 流 道 的效 率 最 高 , 其
面 ( 时 只考虑 平面 与 阶梯面 , 暂 未 考虑 自由曲面分 型 面) 进 行 , 上 浇 注 系 统 的 实 体 模 型 与 虚 拟 模 腔 作
( ) 算 两 个 面 F C 1与 3 计 a e
Point ,
果 实体化 。 本 文 采 用 三 维 参 数 化 的 设 计 方 法 , 浇往 系 统作 为设 计 特征 , 把 实 现 浇 注 系 统 与 成 型 零 件 的 同 时 生成,即浇 注 系统 的设 计 在 分型
() 入 小 端 直 径 D 2输 、拔 模 斜
度 a 冷料 井 长度L ( 于直 接 浇 与 对
摘
要 :注 塑模 的浇注 系统 包括 主流 道 、分流道 和浇 口,运 用基 本特 征的 方法 ,把浇 注 系统 作为 设计特 征 ,实 现 了
注塑模具浇注系统设计
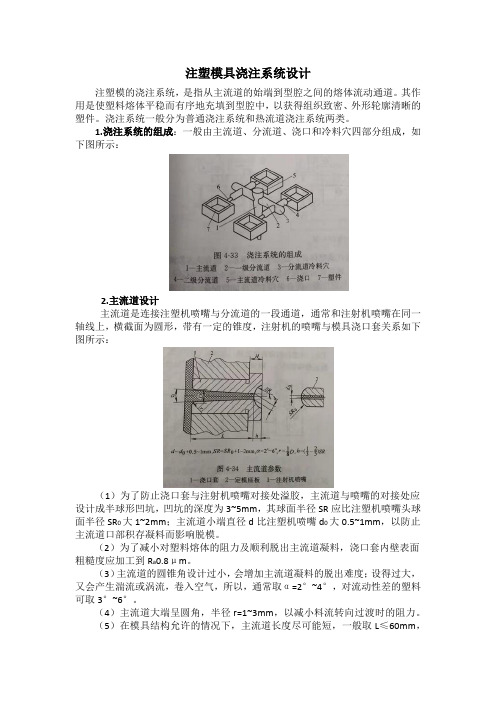
注塑模具浇注系统设计注塑模的浇注系统,是指从主流道的始端到型腔之间的熔体流动通道。
其作用是使塑料熔体平稳而有序地充填到型腔中,以获得组织致密、外形轮廓清晰的塑件。
浇注系统一般分为普通浇注系统和热流道浇注系统两类。
1.浇注系统的组成:一般由主流道、分流道、浇口和冷料穴四部分组成,如下图所示:2.主流道设计主流道是连接注塑机喷嘴与分流道的一段通道,通常和注射机喷嘴在同一轴线上,横截面为圆形,带有一定的锥度,注射机的喷嘴与模具浇口套关系如下图所示:(1)为了防止浇口套与注射机喷嘴对接处溢胶,主流道与喷嘴的对接处应设计成半球形凹坑,凹坑的深度为3~5mm,其球面半径SR应比注塑机喷嘴头球面半径SR0大1~2mm;主流道小端直径d比注塑机喷嘴d0大0.5~1mm,以防止主流道口部积存凝料而影响脱模。
(2)为了减小对塑料熔体的阻力及顺利脱出主流道凝料,浇口套内壁表面粗糙度应加工到R a0.8μm。
(3)主流道的圆锥角设计过小,会增加主流道凝料的脱出难度;设得过大,又会产生湍流或涡流,卷入空气,所以,通常取α=2°~4°,对流动性差的塑料可取3°~6°。
(4)主流道大端呈圆角,半径r=1~3mm,以减小料流转向过渡时的阻力。
(5)在模具结构允许的情况下,主流道长度尽可能短,一般取L≤60mm,过长会增加压力损失,使塑料熔体的温度下降过多,从而影响熔体的顺利充型。
另外,过长的流道还会浪费塑料材料、增加冷却时间。
(6)最常见的主流道的类型有以下几种形式,如下图所示。
由于浇口套在工作时经常与注塑机喷嘴反复接触、碰撞,所以浇口套常用优质合金钢制造,也可以选用T8、T10,并进行相应的热处理,保证足够的硬度,但其硬度应低于与注塑机喷嘴的硬度,以防止喷嘴被碰坏。
(7)对于小型模具,可将主流道浇口套与定位圈设计成整体式,不过大多数情况下,是将主流道浇口套和定位圈设计成两个零件,然后配合固定在模板上面。
注塑模具浇注系统设计

料饼 显示器和电视机前框的浇口形式
M56
5.4 镶件与热流道干涉解决方案参考图片
特殊情况下,热嘴与镶件干涉,热嘴区域钢料较薄,且注射压力高, 拼模线容易产生飞边,影响模具寿命,解决方案如下图。
华威模具设计规范
Aark-canada gate standard
Edge gate
不要大于¢10mm,否则会加长生产周期,请设计人员重点考虑。
另外﹐着重强调一点﹐在注射成型的所有过程中﹐流道的压
力损失是相当大的﹐在流道的所有截面上﹐如果说总体偏小﹐则材料
的充填时必须以高压射出﹐此时﹐会相应带来成品的质量缺陷﹐而流
道截面过大﹐也会浪费材料﹐所以如何取值于流道的粗细大小﹐应以
成品的重量或投影面积为参考﹐这是一个非常重要的一个观点。
华威模具设计规范
浇注系统
1.浇注系统分类﹕冷流道系统﹐热流道系统
2.冷流道系统的组成部分﹕主流道(竖流道)﹐分流道﹐冷料穴﹐浇口
2.1 主流道部分﹐如图 1(A)
SR = Sr+2mm
Sr 为注机喷嘴球半径﹐多数注塑机为 SR19。
ΦD=d+1mm d 为注机喷嘴内孔直径,注塑机型号不同,数据
也不同
4.2 较大产品中一般采用多点浇口时,可以考虑主进浇浇口和辅助进 浇浇口两种综合运用形式,而似乎于按键一类的面产品用冷流道设计 时必须一键一个浇口,这方面着重强调的是各按键的同时进浇,遵守 的是进浇平衡原则.如图 8
华威模具设计规范
4.3 在整个流道的设计中,若从成型角度考虑,设计人员必须尽力缩 短流道的长度,这样, 不但减少了废料,更有利于成型调整,即注塑机 的喷嘴更靠近了,模具的型腔,热量及压力损失可以减小.
注射模的浇注系统名词解释

注射模的浇注系统名词解释I. 引言随着科技的进步和制造技术的不断发展,注塑成型技术在工业生产中扮演着重要角色。
注射模是注塑成型过程中的关键元素之一,而其中的浇注系统更是注射模运行的核心所在。
本文旨在对注射模的浇注系统进行全面解释,介绍其概念、功能和构成要素。
II. 概述1. 注射模的浇注系统简介注射模的浇注系统是指在注塑成型中将熔化的塑料材料通过喷嘴进入模腔的一套管路系统。
它的主要功能是控制塑料材料的流动和充填,确保成型品的质量。
2. 浇注系统的作用与重要性浇注系统是注射模的关键组成部分,直接影响注塑成型过程中的流动性、充填性和冷却性能。
其设计合理与否直接关系到成型品的质量、生产效率和制造成本。
III. 浇注系统的构成要素1. 喷嘴喷嘴是浇注系统中的起始部分,起到将塑料材料从注射机的螺杆推入模腔的作用。
喷嘴主要由喷嘴口、进胶道、断面收缩孔和密封结构组成。
2. 机械式阀门机械式阀门位于喷嘴的末端,其开启与关闭由机械装置控制。
机械式阀门的作用是确保注塑成型过程中喷嘴前后压力的平衡和塑料流动的控制。
3. 热流道系统热流道系统包括热流道板、热流道管和热流道控制装置。
它的作用是在模腔中通过加热使塑料材料保持熔化状态,并控制熔融流动的温度分布,提高成型品的质量和生产效率。
4. 根部系统根部系统主要包括根部冷却装置和根部喷嘴。
根部冷却装置通过冷却水的循环保持注塑模具的温度稳定,以确保成型品的尺寸精度和强度。
IV. 浇注系统的设计准则1. 流动路径优化流动路径的优化是确保塑料材料顺利流动、充填模腔的关键。
在设计中应注意避免死角、尽量减少材料的远距离流动以及控制熔融温度等。
2. 控制冷却效果注射模的浇注系统设计应合理配置冷却装置,以确保成型品在注塑过程中能够得到均匀的冷却与凝固,从而避免变形和缺陷。
3. 提高自动化程度在现代注射模设计中,越来越多的浇注系统采用自动化控制技术,以提高生产效率和稳定性。
自动化控制可通过传感器和控制系统实现浇注参数的实时监控与调整。
- 1、下载文档前请自行甄别文档内容的完整性,平台不提供额外的编辑、内容补充、找答案等附加服务。
- 2、"仅部分预览"的文档,不可在线预览部分如存在完整性等问题,可反馈申请退款(可完整预览的文档不适用该条件!)。
- 3、如文档侵犯您的权益,请联系客服反馈,我们会尽快为您处理(人工客服工作时间:9:00-18:30)。
(3)积要尽量合理,宜小不宜大。
原因是: ①小了加大简单,大了减小很难; ②减少了由于流道产生的废料比例,可以提高
②另外,直径太大时,熔体的热量损失会 增大,流动性降低,注射压力损失增大,造 成成型困难;
③直径太小时,则增加熔体的流动阻力, 同样不利于成型。
侧浇口浇注系统和点浇口系统中的主流道形 状大致相同,但尺寸有所不同。见图。
图中:D1=3.2~3.5mm,E1=3.5~4.5mm, R=1~3mm,α=2°~4°,β=6°~10°。
(4)主流道应设计在浇口套内
主流道尽量避免直接做在模板内,或采 用镶拼结构,以防塑料进入接缝造成脱模 困难。
(5)主流道应尽量和模具中心重合
避免浇口套位置偏心或采用倾斜式主流 道。
倾斜式主流道设计
倾斜式主流道设计
一般地,要求主流道的位置应尽量与模具中心 重合,否则会有如下不良后果。
①主流道偏离模具中心时,导致锁模力和胀型 力不在一条线上,使模具在生产时受到扭矩的作 用,这个扭矩会使模具一侧张开产生飞边,或者 使型芯错位变形,最终还会导致磨具导柱,甚至 注射机拉杆变形等严重后果。
②浇注系统设计时应防止制品出现充填不足、缩痕、飞 边、熔接痕位置不理想、残余应力、翘曲变形、收缩不匀、 蛇纹、抽丝、树脂降解等缺陷。
③浇注系统应能顺利地引导熔融塑料充满型腔各个角落, 使型腔内气体能顺利排出,避免制品内形成气泡。
④浇注系统应能收集温度较低的冷料,防止其进入型腔, 影响制品质量。
注塑模浇注系统设计
注塑模浇注系统设计作用
模具浇注系统的作用是让高温熔体在高 压下高速进入模具型腔,实现型腔填充。
模具的进料料方式、浇口的形式和数
量,往往决定了模架的规格型号。浇注系
统的设计是否合理,将直接影响成型品的
外观、内部质量、尺寸精度和成型周期,
故其重要性不言而喻。
浇注系统概念及分类
模具的浇注系统是指模具中从注塑机喷嘴开始 到型腔入口为止的一段熔体通道,它可分为普通 流道浇注系统和热流道浇注系统两大类型。
模具的经济效益; ③熔体可以在最快的时间内填满型腔,以缩短
成型周期,提高模具的劳动生产率; ④浇注系统内的空气少,减轻了模具的排气负
担; ⑤熔体在流道内的温度和压力损失小,容易保
证制品的成型质量。
(4)不影响自动化生产
若模具要采用自动化生产,则浇注系统 凝料应能自动脱落。
浇注系统设计的内容和步骤
(2)浇口的设计
根据制品的结构、大小和外观要求,确 定浇口的形式、位置、数量和大小。
(3)主流道的设计
确定主流道的尺寸和位置。
(4)分流道的设计
根据制品的结构形状、大小以及塑料品 种,确定分流道的形状、截面尺寸和长短。
(5)辅助流道的设计
根据后续工序或制品结构,确定是否要 设置辅助流道以及辅助流道的形状和大小 的设计。
(1)主流道的长度L越短越好
尤其是点浇口浇注系统主流道,或流动 性差的塑料,主流道更应尽可能短。主流 道越短,模具排气负担越轻,流道料越少, 缩短了成型周期,减少了熔体的能量(温度 和压力)损失。
(2)为便于脱模,主流道在设计上 大多采用圆锥形
两板模主流道锥度取2°~4°,三板模 主流道锥度可取5°~10°(如图10-4所示)。 粗糙度为Ra1.6~0.μm,锥度须适当,太大 造成速度减小,产生斡流,易混进空气, 产生气孔;锥度过小,会使流速增大,造 成注射困难,同时还会使主流道脱模困难。
热塑性塑料的主流道,一般在浇口套内,浇口 套做成单独镶件,镶在定模板上,但一些小型模 具也可直接在定模板上开设主流道,而不使用浇 口套。浇口套可分为两大类:两板模浇口套和三 板模浇口套。
主流道的设计原则
(1)主流道的长度L越短越好 (2)为便于脱模,主流道在设计上大多采用
圆锥形 (3)主流道尺寸要满足装配要求 (4)主流道应设计在浇口套内 (5)主流道应尽量和模具中心重合
(1)选择浇注系统的类型 (2)浇口的设计 (3)主流道的设计 (4)分流道的设计 (5)辅助流道的设计 (6)冷料穴的设计
(1)选择浇注系统的类型
根据制品的结构、大小、形状以及制品 批量大小,分析其填充过程,确定是采用 侧浇口浇注系统,点浇口浇注系统,还是 无流道浇注系统。进而确定是采用点浇口 模架,还是侧浇口模架。
(3)主流道尺寸要满足装配要求
为了保证注射成型时,主流道与注射机 喷嘴之间不溢料而影响脱模,设计时要注 意:主流道小端直径D2要比料筒喷嘴直径 D1大0.5~1mm,一般情况下,D2=3.2~ 4.5mm;大端直径应比最大分流道直径大 10%~20%。一般在浇口套大端设置倒圆角 (R1~3mm),以利于料流。见图10-3。
(1)保证制品的外观质量
任何浇口都会在制品表面留下痕迹,从 而影响其表面质量。为不影响产品外观, 应尽量将浇口设置于制品的隐蔽部位,若 无法做到,则应使浇口容易切除,切除后 在制品上留下的痕迹最小。
(2)保证制品的内部质量
①浇口的形式和数量要选择合理,保证塑料熔体迅速填 充型腔,减少压力与热量损失,使制品内部组织细密。
普通流道浇注系统又分为侧浇口浇注系和点浇 口浇注系统,它们都由主流道、分流道、冷料穴 和浇口组成。如图所示。
热流道浇注系统没有主流道及分流道,熔体 经过热流道板和热射嘴直接由浇口进入型腔。热 流道浇注系统将在后章详细探讨,本章只探讨普 通流道浇注系统。如图所示。
浇注系统的设计原则
(1)保证制品的外观质量 (2)保证制品的内部质量 (3)阻力最小 (4)不影响自动化生产
(6)冷料穴的设计
根据分流道的长短及制品结构形状,确 定冷料穴的位置和尺寸。
主流道设计
主流道的概念
主流道是指紧接注塑机喷嘴到分流道为 止的那一段锥形流道,熔融塑料进入模具 时首先经过它。
主流道直径对注塑的影响
主流道直径的大小与塑料流速及充模时间 的长短有密切关系。
① 直径太大时,则造成回收冷料过多, 冷却时间增长,而流道空气过多也易造成气 泡和组织松散,极易产生涡流和冷却不足。