注塑模具之浇注系统介绍
模具设计-浇注系统

模具设计-浇注系统浇注系统是指模具中从注射机喷嘴开始到型腔为止的塑料流动通道﹐其由主流道﹑分流道﹑浇口及冷料穴组成。
1.1.主流道主流道是指从注射机喷嘴与模具接触的部位起﹐到分流道为止的这一段。
主流道一般设计成圆锥形﹐角度为2°~4°。
1.2.分流道分流道是指主流道与浇口之间的这一段﹐它是熔融塑料由主流道流入型腔的过渡段﹐也是浇注系统中通过断面变化和塑料转向的过渡段﹐能使塑料得到平稳的转换。
1.2.1.分流道的形状有圆形﹑半圆形和梯形等几种﹐从减小压力和热量损失的角度考虑﹐圆形流道是最优越的流道形状。
当分型面是平面或曲面时﹐一般采用圆形流道;细水口模一般选用梯形流道﹐当流道只开在前模或后模时﹐则选用梯形流道。
1.2.2.当塑件采用多浇口进浇以及一模多腔早时﹐要充分考虑进胶的均匀性﹐尽可能做到平衡进胶。
1.2.3.设计分流道大小时﹐应充分考卢制品的大小﹑壁厚﹑材料流动性等因素﹐流动性不好的材料如PC料其流道应相应加大﹐并且分流道的截面尺寸一定要大于制品壁厚﹐同时应选择合适的长度。
流道长则温度降低明显﹐流道短则剩余应力大﹐容易产生“喷池”。
1.2.4.梯形流道﹕W一般为5—8mm﹐H一般为4—6mm﹐H/W=2/31.2.5.分流道表面不要求很光﹐表面粗糙度一般达Ra3.2~1.6即可﹐因为分流道的表面稍有不光滑﹐就能使熔料的冷却皮层固定﹐有利于保温﹔浇口的表面粗糙度不能高于Ra0.4﹐否则易产生摩擦阻力。
1.3.浇口浇口是指分流道与塑件之间的狭窄部分。
它能使分流道输送来的熔融塑料的流速产生加速度﹐形成理想的流态﹐顺序﹑迅速地充满型腔﹐同时还起眷封闭型腔防止熔料倒流的作用﹐并在成型后便于使浇口与塑件分离。
常见浇口类型有直接浇口﹑侧浇口﹑潜伏式浇口﹑点浇口等多种。
设计时对大型单一型腔制品成型效果好﹐需注意唧嘴底部与产品之间是否要隔一段距离。
1.3.2.侧浇口侧浇口设置于制品分型面处﹐制品允许有浇口痕迹才可采用﹐侧浇口包括边缘浇口和搭接浇口﹐其浇口尺寸与制品壁厚﹑大小﹑材料等诸多因素有关﹐一般规格如下图﹕边缘浇口与搭接浇口的选择如下图﹕ 选择浇口位置时﹐就防止制品产生滞留现象﹐应远离厚﹑薄交接处﹐从厚的地方进浇﹐避免浇口正对柱位﹑碰穿位﹐防止型芯因冲击而变形。
模具基础篇6:注塑模具的浇注系统

模具基础篇6:注塑模具的浇注系统有了模具的成型部分,接下来的问题便是,如何将塑料注⼊模具型腔呢?于是接下来将要揭晓的,是模具的另⼀个重要组成—“浇注系统”(Injection System):“浇注系统”是模具上从注塑机喷嘴⾄模具型腔之间的通路,正是通过这个通路,塑料才能被从注塑机注⼊模腔。
通常我们将“浇注系统”分为两个部分:流道(Runner)与浇⼝(Gate)。
下⾯我们分别来介绍这两个部分:流道:“流道”是模具上介于喷嘴与“浇⼝”间的通道。
其实就注塑本⾝⽽⾔,流道的存在对整个注塑过程没有任何益处,有时甚⾄还会带来⿇烦。
因为,当喷嘴与模腔间出现⼀个额外的中介后,势必会带来熔融塑料的温度与压⼒的损失。
所以,注塑模具流道设计的⾸要原则便是:尽可能降低熔融塑料在流道内温度与压⼒的损失。
(尽量能使注塑过程忽略这⼀部分的存在)但是,由于模具结构、空间、功能等因素,流道在注塑模具中⼜是必不可少的。
在⼤多数情况下,模具上基本没有空间使喷嘴与模腔直接联接;此外,喷嘴与模腔直接接触,喷嘴的⾼热量也就势必传导⾄模具上,使模腔的温度受到影响,这是对注塑⾮常不利。
另外,由于⽣产效率的原因,模具通常不会仅有⼀个模腔。
对于“多腔模”(Multi Cavity Mold)来说,流道就会像树⼀样,将熔料从喷嘴经过主⼲与各个分⽀,最终到达模腔。
此时的流道还会附加⼀个要求,便是熔料在经过流道后,尽量能保证各个模腔内的流动状态⼀致。
这其中,直接与喷嘴连接,也就是熔融最先接触的部分称为“主流道”(Sprue),它通常与模具的主分形⾯垂直,为了防⽌注射压⼒的损失,“主流道”的直径会其它部分略微⼤⼀些。
“主流道”与产品型腔之间的部分,通常称为“分流道”(Runner)。
他们⽤以将熔融塑料分别均匀地送⼊各个不同的型腔。
“流道”与“型腔”之间的部分称为“浇⼝”(Gate),它是料流进⼊型腔的最后门户。
相⽐与“流道”,“浇⼝”的尺⼨要⼩得多,之所以要将其做得⼩,有三个主要原因。
注塑模具设计:第二章:浇注系统

第二章浇注系统注塑机喷嘴中熔融的塑料,经过主流道,分流道,最后通过浇口进入到模具型腔,然后经过冷却固化,得到所需要的制品。
所以注塑模具的浇注系统是指从注塑机喷嘴到型腔为止的塑料熔体的流动通道。
因为热塑性塑料的热传导率较低,流道中冷凝的表皮对芯部熔融的塑料祈祷保温作用,所以保证了流道芯部的塑料继续流动。
来自熔融的塑料的热加上由于流动摩擦二产生的摩擦热等于高温塑料与低温模具热交换所产生的热损失。
如果增加注射速度,冷凝层由于受到流动产生的高摩擦热而会变薄。
即:高速注射与低速注射对于冷凝层厚度影响的差别是比较明显的。
这就是为什么高压、高速注射容易将型腔填充饱满的主要原因之一。
浇注系统的型制与流动性为减少与热量的损失,必须使流道的表面积与体积之比保持最小,因为具有最小表面积与最大体积的形状是圆柱形,所以圆柱形是最优越的流道形状。
主流道从注射机喷嘴到分浇为止的熔融塑料的流动通道。
1)定模部分由整体构成2)定模部分由两块模板所构成3)最普遍常用的主流道结构,是以浇口套的形式镶入模板中,为防止被喷嘴撞伤,采取淬火处理主流道的基本尺寸取决于两个方面:1,塑料的种类,所成型的制品质量和壁厚大小。
2与注射机喷嘴的几何参数有关。
浇口套的求半径比喷嘴的球半径大2~5mm,脱模斜度一般最小不低于1°,最大不超过4°。
因为,主流道的脱模斜度不能过大,否则在注塑时会产生涡流和流速过慢等现象主流道应保持光滑的表面,避免留有影响塑料流动或脱模的尖角毛刺等。
而且在主流道的末端还应设置冷料井以防止制品中出现固化的冷料(最先流入模具的塑料)。
设置冷料井,以便将这部分冷料存留起来。
这一点对分流道也同样重要。
分流道分流道可以理解为从主流道末端开始到浇口为止的塑料熔体的流动通道。
鉴于圆形截面的浇道必须设置在以分型面为界的动、定模两部分,所以对制造工艺要求较高,且启模时,分流道中经过冷却固化的塑料留在动、定模内是随机的。
所以实际制造中,U 性截面分流道或梯形截面的分流道比较常用,虽然热量损失较大一点,但加工制造比较简单,并且启模时,冷料留在动定模哪一部分,将是确定的。
塑胶模具浇注系统
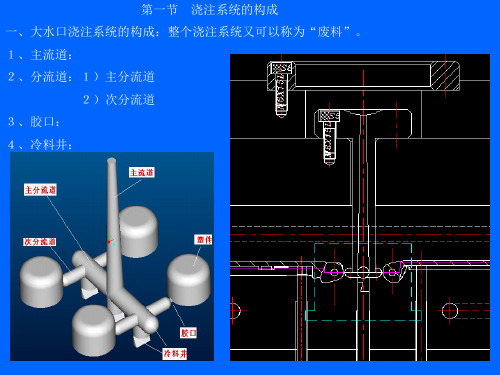
N 0.5 0.6 0.7 0.8
9) 护耳式胶口:用于肉厚大的产品或者透明的塑料来减少流痕.
10)牛角式进胶:也称为”蕉形入水”
11) 针点胶口:
谢谢观看/欢迎下载
BY FAITH I MEAN A VISION OF GOOD ONE CHERISHES AND THE ENTHUSIASM THAT PUSHES ONE TO SEEK ITS FULFILLMENT REGARDLESS OF OBSTACLES. BY FAITH I BY FAITH
5)平逢式胶口:又可称之为“薄片浇口”,适用平板形的产品,例如手表带。可流动的 塑料以较低的速度均匀平稳地进入模具型腔,其料呈平行流动,这样可以避免产品变形。 但去除浇口困难,必须用专业工具将它去除,这会增加产品的成本,还会出现痕迹影响外 观。
平缝式胶口另外一种方式:
L>=1.3 b=(0.75-1)B H=0.7NS
注意:唧嘴是标准件,则主流道的大小尺寸由唧嘴来决定,为了减少“废料”,可以 缩短唧嘴的长度,则保证上图当中的“M”不小于10即可.设计时,就算唧嘴选取 错误了,也不要紧,可以直接更换.
注塑机喷嘴要与模具的唧嘴来配合,注意事项如下:
2、分流道:当模具存在“一模多穴”时,就必须有分流道,它把主流道里面的塑料分别 引入到各个不同的模穴当中。
C、冷料井沉下去4-8毫米即可。
4、浇(胶)口:也可以为“进胶方式“。提问:胶口的作用?
1)大点胶口:也叫做”直接进胶“。它没有分流道,直接用主流道进胶。
它主要适用于大而深的”桶状“类的产品,缺 点就是主流道与产品没有分开,产品注塑出来 之后还要去除胶口,会在进胶位置留下一个很 明显的痕迹,影响产品的外观。
浇注系统介绍
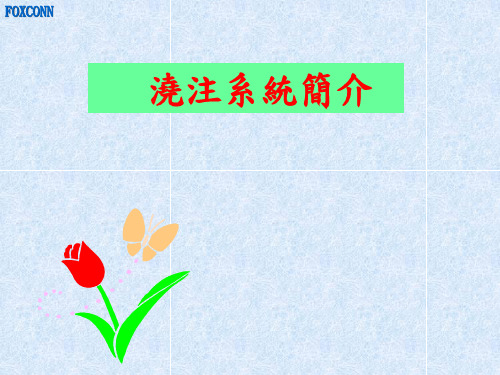
FOXCONN
熱流道注塑動作
閥澆口熱澆道的基本結構 Locating Ring Inlet Extension Valve Actuator Valve Disk Manifold
Manifold Locator Nozzle (Gate insert)
熱流道的優缺 熱流道的優缺點 優點﹕
1.無廢料 2.流動阻力小﹐壓力損失小﹐便于成型 3.塑料溫度容易控制 4.無澆口痕跡﹐產品外觀質量好
收縮(sink marks)
成型品表面產生凹陷的現象. 是體積 收縮所致,通常見於肉厚部分,肋或凸 出的背面,直接澆口肉厚不均的部份. 診斷: 診斷 无足够的材料或较厚肋 •注射压力过低 •射胶时间太短 •机器融胶能力不足 •模温太高 •浇口过小 •流道过长 •產品肋/壁厚比不當 •浇口位置不當 •模具排气不良
澆注系統概述 一. 澆注系統概述
澆注系統:是指熔融塑膠從注塑機噴嘴到達模 具型腔之前在模具中所流經的通道,我們通常 稱之為澆注系統。 作用是將熔體從噴嘴平穩快速地引進模腔,並 在熔體充模和固化定型過程中將注射壓力和保 壓壓力充分傳遞到模腔各部分,澆注系統設計 合理與否直接對制品成型起到決定作用.
Injection Molding 注塑機
銀條(sliver streaks)
診斷: 銀條是在成型品表面或表面附近,沿 診斷 材料流動方向,呈現的銀白色條紋. •材料降解(料筒有热点, 材料在喷
嘴处有死角) •注射压力或速度过低或过高 • •背压过低 •在浇口,机器喷嘴或热流道摩擦烧 焦 •料温过高 •在塑胶粒中有污染 •过多水分
Thanks!!!
Barrel Unit The Reciprocating Screw
Shot
注塑模--浇注系统

注塑模之浇注系统浇注系统定义:溶体从注塑机喷嘴开始流动至模具型腔为止的这个通道就是浇注系统。
浇注系统的作用:引导溶体平稳进入型腔,顺利排出腔内气体,传递压力到腔内各个部位。
一,浇注系统的构成(如图A)浇注系统构成:主流道、分流道、冷料井、浇口。
二,主流道设计主流道定义:溶体从喷嘴流出所经过的第一个通道,就是浇口套里面的那个通道。
浇口套:是标准件,经常用的有三种形式,与定位环组合使用。
常用浇口套直径有12mm,16mm,20mm。
三,分流道设计分流道定义:塑胶溶体从主流道开始到浇口为止的这段流经通道,是从浇口套出来后进入模腔前的过度阶段。
分流道的作用:形状大,壁厚厚,结构复杂的零件设立分流道,使溶体填充均匀。
一模多穴必须设立分流道。
1,分流道的截面分流道从字面意思来理解,就是个通道,就像我们生活中见到管道一样,U形的火车隧道,方形的隧道,圆形的水管通道等,分流道的截面常见有圆形、U形、梯形和半圆形。
(如下图所示)(1),圆形流道(图B)圆形流道是应用最广的分流道形式。
圆形流道的优点:压力和温度损失小,有利于塑胶溶体流动和压力传递。
圆形流道的缺点:圆形流道在分型面的两侧的两块板上,且相互对称,加大加工难度,为啥不在一块板上加工呢?因为在非端面的金属体内加工圆孔,加工不出来。
圆形流道常用尺寸ΦD:直径4、5、6、7、8、9、10、12(mm),其中的偶数直径常用,主流道直径一般比次流道大一个等级。
(2),U形流道(图C)U形流道的特点:粘模力不大,比圆形流道易加工,应为只要在一块板上铣出来就好,不用考虑对称问题。
U形流道常用尺寸ΦD:同圆形流道。
(3),梯形流道(图D)梯形流道的特点:比圆形和U形流道都更好加工,多用于细水口模具。
梯形流道常用尺寸:W常用尺寸4、5、6、7、8、9、10、12(mm),偶数最常用,H常用尺寸3、3.5、4,、5、5.5、6、7、8等。
(4),半圆形流道(图E)半圆形流道特点:加工很方便,尺寸要求同圆形流道,但只开在一侧模板上。
注塑模具浇注系统设计
注塑模具浇注系统设计注塑模的浇注系统,是指从主流道的始端到型腔之间的熔体流动通道。
其作用是使塑料熔体平稳而有序地充填到型腔中,以获得组织致密、外形轮廓清晰的塑件。
浇注系统一般分为普通浇注系统和热流道浇注系统两类。
1.浇注系统的组成:一般由主流道、分流道、浇口和冷料穴四部分组成,如下图所示:2.主流道设计主流道是连接注塑机喷嘴与分流道的一段通道,通常和注射机喷嘴在同一轴线上,横截面为圆形,带有一定的锥度,注射机的喷嘴与模具浇口套关系如下图所示:(1)为了防止浇口套与注射机喷嘴对接处溢胶,主流道与喷嘴的对接处应设计成半球形凹坑,凹坑的深度为3~5mm,其球面半径SR应比注塑机喷嘴头球面半径SR0大1~2mm;主流道小端直径d比注塑机喷嘴d0大0.5~1mm,以防止主流道口部积存凝料而影响脱模。
(2)为了减小对塑料熔体的阻力及顺利脱出主流道凝料,浇口套内壁表面粗糙度应加工到R a0.8μm。
(3)主流道的圆锥角设计过小,会增加主流道凝料的脱出难度;设得过大,又会产生湍流或涡流,卷入空气,所以,通常取α=2°~4°,对流动性差的塑料可取3°~6°。
(4)主流道大端呈圆角,半径r=1~3mm,以减小料流转向过渡时的阻力。
(5)在模具结构允许的情况下,主流道长度尽可能短,一般取L≤60mm,过长会增加压力损失,使塑料熔体的温度下降过多,从而影响熔体的顺利充型。
另外,过长的流道还会浪费塑料材料、增加冷却时间。
(6)最常见的主流道的类型有以下几种形式,如下图所示。
由于浇口套在工作时经常与注塑机喷嘴反复接触、碰撞,所以浇口套常用优质合金钢制造,也可以选用T8、T10,并进行相应的热处理,保证足够的硬度,但其硬度应低于与注塑机喷嘴的硬度,以防止喷嘴被碰坏。
(7)对于小型模具,可将主流道浇口套与定位圈设计成整体式,不过大多数情况下,是将主流道浇口套和定位圈设计成两个零件,然后配合固定在模板上面。
注塑模具的浇注系统
注塑模具的浇注系统浇注系统的定义﹕模具中从注射机喷嘴开始到型腔为止的塑料流动信道。
其由主流道﹑分流道﹑浇口及泠料穴组成。
一、主流道1.定义﹕主流道是指从注射机喷嘴与模具接触的部位起﹐到分流道为止的这一段。
2.设计上的注意事项﹕(1)主流道的端面形状通常为圆形。
(2)为便于脱模﹐主流道一般制作都带有斜度﹐但如果主流道同时穿过多块板子时,一定要注意每一块块子上孔的斜度及孔的大小。
(3)主流道大小的设计要根据塑料材料的流动特性来定(4)主流道在设计上大多采用圆锥形。
制作时要注意﹕A.小端直径D2=D1+(0.5~1mm)B.小端球半径R2=R1+(1~2mm)(其中D1﹑R1分别为注射机射出口的直径及注射头的球半径)3.浇口套由于主流道要与高温塑料及喷嘴接触和碰撞﹐所以模具的主流道部分通常设计成可拆卸更换的衬套﹐简称浇注套或浇口套(1).其作用主要为﹕A.使模具安装时进入定位孔方便而在注塑机上很好地定位与注塑机喷嘴孔吻合﹐并能经受塑料的反压力﹐不致被推出模具B.作为浇注系统的主流道﹐将料筒内的塑料过渡到模具内﹐保证料流有力畅通地到达型腔﹐在注射过程中不应有塑料溢出﹐同时保证主流道凝料脱出方便。
(2)结构形式有整体式和分体式整体式﹕即台肩与构成主流道部份做成一体分体式﹕即台肩与构成主流道部份分开制作中国的工业标准﹕SINO二、分流道定义﹕主流道与浇口之间的一段﹐它是熔融塑料由主流道流入型腔的过渡段也是浇注系统中通过断面面积变化及塑料转向的过渡段﹐能使塑料得到平稳的转换。
1.截面设计A.一般设计截面为圆形B.从加工方便性来看一般设计为U形,V形,梯形,正六边形C.分流道的断面形状及尺寸大小,应根据塑件的成型体积,塑件壁厚,塑件形状,所用塑料工艺特性,注射速率,分流道长度等因素来确定。
2.分流道的布置形式有平衡式进料和非平衡式进料两种形式。
平衡式进料就是保证各个进料口同时均衡地进料,非平衡式进料就是各个进料口不能同时均衡地进料,一般要做模流分析来进行评估。
注射模的浇注系统名词解释
注射模的浇注系统名词解释I. 引言随着科技的进步和制造技术的不断发展,注塑成型技术在工业生产中扮演着重要角色。
注射模是注塑成型过程中的关键元素之一,而其中的浇注系统更是注射模运行的核心所在。
本文旨在对注射模的浇注系统进行全面解释,介绍其概念、功能和构成要素。
II. 概述1. 注射模的浇注系统简介注射模的浇注系统是指在注塑成型中将熔化的塑料材料通过喷嘴进入模腔的一套管路系统。
它的主要功能是控制塑料材料的流动和充填,确保成型品的质量。
2. 浇注系统的作用与重要性浇注系统是注射模的关键组成部分,直接影响注塑成型过程中的流动性、充填性和冷却性能。
其设计合理与否直接关系到成型品的质量、生产效率和制造成本。
III. 浇注系统的构成要素1. 喷嘴喷嘴是浇注系统中的起始部分,起到将塑料材料从注射机的螺杆推入模腔的作用。
喷嘴主要由喷嘴口、进胶道、断面收缩孔和密封结构组成。
2. 机械式阀门机械式阀门位于喷嘴的末端,其开启与关闭由机械装置控制。
机械式阀门的作用是确保注塑成型过程中喷嘴前后压力的平衡和塑料流动的控制。
3. 热流道系统热流道系统包括热流道板、热流道管和热流道控制装置。
它的作用是在模腔中通过加热使塑料材料保持熔化状态,并控制熔融流动的温度分布,提高成型品的质量和生产效率。
4. 根部系统根部系统主要包括根部冷却装置和根部喷嘴。
根部冷却装置通过冷却水的循环保持注塑模具的温度稳定,以确保成型品的尺寸精度和强度。
IV. 浇注系统的设计准则1. 流动路径优化流动路径的优化是确保塑料材料顺利流动、充填模腔的关键。
在设计中应注意避免死角、尽量减少材料的远距离流动以及控制熔融温度等。
2. 控制冷却效果注射模的浇注系统设计应合理配置冷却装置,以确保成型品在注塑过程中能够得到均匀的冷却与凝固,从而避免变形和缺陷。
3. 提高自动化程度在现代注射模设计中,越来越多的浇注系统采用自动化控制技术,以提高生产效率和稳定性。
自动化控制可通过传感器和控制系统实现浇注参数的实时监控与调整。
注塑模具之浇注系统的介绍
注塑模具之浇注系统的介绍注塑模具是制造塑料制品的重要工具,它的质量直接影响到成品的质量。
而注塑模具中的浇注系统对成品的质量也有着重要影响。
浇注系统是指将熔融塑料从注塑机的机筒中注入到模腔中的一系列设备和构造。
1.浇注系统的组成浇注系统由喷嘴、喷嘴喉管、进料口和冷却系统等构成。
其中,喷嘴是熔融塑料进入模腔的通道,它连接着机筒和模腔。
喷嘴内部通道的形状和尺寸会影响塑料的流动情况和填充时间。
喷嘴喉管和进料口是喷嘴和模腔之间的连接部分,起到塑料流动的引导作用。
冷却系统是为了在注塑过程中将模具中的热量迅速带走,确保产品成型的质量和效率。
2.浇注系统的工作原理注塑过程中,熔融塑料通过喷嘴进入模腔,填充整个模具的形状。
当模腔被充满后,喷嘴会迅速封闭,避免塑料溢出。
此时,熔融塑料开始冷却并变得固态,成型的产品在模具中逐渐形成。
冷却系统会通过喷淋冷却或冷却通道等方式将热量迅速带走,保证产品成型的质量。
3.浇注系统的设计要点为了保证产品的质量,并满足不同要求的注塑制品,浇注系统的设计需要注意以下要点:(1)喷嘴和模腔的连接处要保证密封,避免塑料溢出;(2)喷嘴通道的形状和尺寸要能够满足塑料的流动要求,避免注塑短流或短充问题;(3)选择适当的冷却方式和冷却介质,保证产品的尺寸和表面质量;(4)为了避免冷却系统的死角,需要合理配置冷却通道,确保整个模具在注塑过程中的温度分布均匀。
4.浇注系统的改进和优化为了提高产品的质量和生产效率,浇注系统的改进和优化是重要的课题。
一方面,可以通过模具部件的改进来优化浇注系统,例如喷嘴通道的优化、冷却通道的重新设计等。
另一方面,可以通过模具流道分析软件来模拟塑料在注塑过程中的流动情况,进一步优化浇注系统的设计。
此外,一些先进的浇注系统技术,如热流道系统、堆垛模腔技术等也可以运用到注塑模具中。
总结起来,注塑模具的浇注系统是注塑过程中至关重要的一部分,它的设计和优化对产品质量和生产效率有着直接影响。
- 1、下载文档前请自行甄别文档内容的完整性,平台不提供额外的编辑、内容补充、找答案等附加服务。
- 2、"仅部分预览"的文档,不可在线预览部分如存在完整性等问题,可反馈申请退款(可完整预览的文档不适用该条件!)。
- 3、如文档侵犯您的权益,请联系客服反馈,我们会尽快为您处理(人工客服工作时间:9:00-18:30)。
5/17/2019
塑料模具设计
第九章 注塑模浇注系统设计
2.按排位的形状分为O形,H形,X形和S形。
• 塑料模具设计
5/17/2019
第九章 注塑模浇注系统设计
9-3-5 加辅助流道的场合:
1。有镀铬,二次注射等后续工序。 2。辅助流道可以改善制品成型质量。 3。方便包装。 4。为使塑件留于后模。
(1)优点:①位置较灵活; ②浇口可自动脱落; ③既可以潜前模,又可以潜后模。 (2)缺点:适合弹性好的塑料。 (3)潜伏式浇口重要参数:(见图) (4)圆弧形(牛角)潜浇口。
5/17/2019
塑料模具设计
第九章 注塑模浇注系统设计
•3.点浇口(又叫细水口):常用于三板模和无流道模.熔胶可由 型腔任何位置,一点或多点地进入型腔。
1、单点式热流道模具 2、多点式热流道模具
5/17/2019
塑料模具设计
第九章 注塑模浇注系统设计
9-5-3 热流道系统的优点
1.缩短成型周期。减少注射时间和冷却时间,提高了模具的 劳动生产率。
2.减少流道凝料,节约了注塑成本。 3. 减小了熔体的能量损失及排气负担。
4.提高成型质量。 5.易于实现自动化生产。 6.模具动作简化,使用寿命提高。
a
b
c
5/17/2019
塑料模具设计
第九章 注塑模浇注系统设计
5、扇形浇口:适用于平板类、壳形或盒形制 品。 其它浇口还有:环形浇口,爪形浇口,护耳 浇口和轮辐浇口
5/17/2019
塑料模具设计
第九章 注塑模浇注系统设计
9-5 热流道模具设计
5/17/2019
9-5-1概念
热流道模具是在传统的二板模具或三板式模具内的主流道与分 流道部位加设加热装置,
在注射过程中不断加热, 使流道内的塑料始终处于高 温熔融状态,塑料不会冷却 凝固,也不会形成流道与制 品一起脱模,从而达到无流
隔热板 定位圈 面板 隔热垫块 热唧咀 热流道板 二级热唧咀
道凝料或少流道凝料的目的。中心隔热块
A板
B板
前模 后模
定位销
塑料模具设计
第九章 注塑模浇注系统设计
9-5-2 热流道模具的基本形式
•优点:(1)位置有较大的自由度;
•
(2)浇口可自行脱落• ,塑留料模痕具设小计;
•
(3)对桶形、壳形、盒形制品
•及面积较大的平板类胶件非常适用;
•
(4)浇口附近残余应力小。
• 缺点:(1)注射压力损失较大;
•
(2)模具结构较复杂。
•
重要参数。见图。
5/17/2019
第九章 注塑模浇注系统设计
4、直接浇口:用于大而深的桶形、盒形及壳形制品 。
9-4 浇口的设计:连接分流道与型腔之间的一段细短通道。 9-4-1 浇口的作用:
• 塑料模具设计
1、调节及控制料流速度,防止倒流; 2、熔胶经过浇口时,会因剪切及挤压而升温,有利于填充; 3、浇口设计不合理时, 会产生流痕,蛇纹, 夹水纹,啤不满或披 锋等缺陷。
5/17/2019
第九章 注塑模浇注系统设计
5/17/2019
塑料模具设计
第九章 注塑模浇注系统设计
•9-3—6 分流道拉料杆和冷料穴
• 1.拉料杆: •(1)大水口拉料杆。
• 塑料模具设计
•(2) 细水口拉料杆.
•(3) 推板模拉料杆.
5/17/2019
第九章 注塑模浇注系统设计
2、冷料穴:
• 塑料模具设计
5/17/2019
第九章 注塑模浇注系统设计
9-1-3 浇注系统分类
1. 大水口(二板模)浇注系统。 2. 细水口(三板模)浇注系统。 3. 无流道。
5/17/2019
塑料模具设计
第九章 注塑模浇注系统设计
大水口浇注系统模具和细水口浇注系统模具比较:
注射口
• 塑料模具设计
后模
前模
•充填、保压、冷却完毕
后模
前模
开模、顶出产品
分模线 2
分模线 1
料杆; 2、 细水口唧嘴及主流道设计
3、主流道的位置应尽量与模具中心重合。
5/17/2019
塑料模具设计
第九章 注塑模浇注系统设计
9-3 分流道:
连接主流道与浇口的熔胶通道。
9-3-1 设计分流道必须考虑的因素:
1.制品的形状,壁厚及内在外观质量要求;
2、塑料的流动性;
3.是否要自动化啤塑。
9-3-2 分流道设计的一般要求:
1. 分流道的长度应尽量短,截面尺寸应尽
2. 可能小,转角处最好圆弧过渡;
2、分流道较长时,末端应设冷料井和排气槽;
3.一模多腔的分流道截面积应有所不同。
5/17/2019
塑料模具设计
第九章 注塑模浇注系统设计
9-3-3 分流道的截面形状5/17/2019
塑料模具设计
第九章 注塑模浇注系统设计
6-3-4 分流道的布置 1。按特性分为平衡布置和非平衡布置。
塑料模具设计
章注塑模浇注系统设计
海纳百川,有容乃大。 壁立千仞,无欲则刚
5/17/2019
塑料模具设计
第九章 注塑模浇注系统设计
9-1 概述 9-1-1 概念:从主流道始端到型腔之间的进料
通道。 9-1-2 作用:让高温熔胶在 高压下高速进入模具型腔。
5/17/2019塑料模具来自计第九章 注塑模浇注系统设计
•9-4-2 浇口设计要点:
•1、浇口数量尽可能少。
2、浇口位置:
• 塑料模具设计
A 不能影响制品外观。
B 距型腔各部位距离尽量相等。
C 浇口应对着型腔宽畅部位,便于补缩和走胶;
D 应避免冲针或直接冲击薄弱镶件;
E 应减少熔接痕,或使熔接痕产生于制品的不重要 表面及非薄弱部位;
F 浇口位置应有利于模具排气。
G 澆口要便于切除.
5/17/2019
第九章 注塑模浇注系统设计
9-4-4 浇口的分类:
1. 侧浇口(又叫大水口,普通浇口) 优点:加工易,修正易; • 塑料模具设计 缺点(1)去除浇口麻烦且留下明显痕迹。 (2)位置受到一定的限制。
5/17/2019
第九章 注塑模浇注系统设计
2. 潜伏式浇口:
5/17/2019
塑料模具设计
第九章 注塑模浇注系统设计
5/17/2019
注射口
第九章 注塑模浇注系统设计
9-1-4 浇注系统组成:主流道,分流道, 浇口及冷料穴。
9-1-5 浇注系统的设计原则: 1、保证塑件外观和内部质量; 2、提高成型速度缩短成型周期。
5/17/2019
塑料模具设计
第九章 注塑模浇注系统设计
9-2 主流道:浇口套(唧嘴)内的流道。 1. 大水口唧嘴及主流道设计,浇口套规格,拉