石膏型铸造
石膏型铸造讲义

石膏型铸造讲义
1
主要内容 概述 1、制石膏型用材料及其组成 2、石膏型精铸工艺
2
概述
1、工艺过程 石膏型精密铸造是20世纪70年代发展起来的一
种精密铸造新技术,其典型工艺过程见图0-1。 它是将熔模组装,并固定在专供灌浆用的砂箱
平板上,在真空下把石膏浆料灌入,待浆料凝结后 经干燥即可脱除熔模,再经烘干、焙烧成为石膏型, 在真空下浇注获得铸件。
3
概述
2、工艺特点
(1) 石膏浆料的流动性很好,又在真空下灌注成型, 其充型性优良,复模性优异,型精确、光洁。该工艺不 像一般熔模精密铸造受到涂挂工艺的限制,可灌注大型 复杂铸件用型。
(2) 石膏型的热导率很低,充型时合金液流动保持 时间长,适宜生产薄壁复杂件。
但铸型激冷作用差,组织粗大,当铸件壁厚差异大 时,厚大处容易出现缩松、缩孔等缺陷。
1.3
0.2
2.1-2.2 0.5 X10-6
3.25 3.1-4.3 X10-6 1.5
0.65
3.08-
5.3 X10-6
2.3
3.4
0.80
3.15
3.2-3.4 5.0 X10-6 2.6
4.6
0.85
3.95-
8.4 X10-6
2.0
3.5
0.65
4.02
5.73 7.2-10 X10-6
除石膏种类外,影响石膏强度的因素还有石膏的 细度、水固比、水温、搅拌时间等。
6
第一节 制石膏型用材料及其组成 2. 填料
为使石膏型具有良好的强度,减小其收缩和裂纹 倾向,需要在石膏中加入填料。
填料应有合适的熔点、耐火度,良好的化学稳定 性、合适的线膨胀率、发气量少,吸湿性小等性能, 常用作填料的材料及其性能见表1-1。
第2章石膏型精密铸造1

镁合金
1.2
1.6
锰黄铜 1.8~2.0 2.0~2.3
石膏型精密铸件的综合收缩率A可按下式计算:
A% (a c d)%
三、铸造斜度 石膏型精密铸件的铸造斜度可参考熔模铸造斜 度。
2.2.3浇注系统及冒口设计 石膏型精密铸件浇注系统及冒口设计可参考熔
模铸造或砂型铸造。应注意以下几点: 1、石膏导热性差,金属液保持流动时间长, 故浇注系统截面积尺寸可比砂型铸造减少 20%左右。
表2-3 尿素模料配方
序号 尿素
硼酸
硼酸钾 羧甲基纤维素
水
1 97~98 2~3
2 75~85
15~25
3
85
10
5
表2-4 无机盐模料配方
名称
KNO3 NaNO2 NaNO3 Al2(SO4)3 (NH4)2SO4 HO2
亚硝酸盐模料 55
45
—
—
—
—
硝酸盐模料 55
—
45
—
—
—
硫酸盐模料 —
2.1.2工艺特点 1、使用易熔模,不用开箱起模。 2、可制造尺寸精度高(可达CT4~6级)、大型 (1000mm×2000mm)、薄壁 (壁厚为1.5mm,局
部为0.5mm)、形状复杂的精密铸件。表面粗 糙度一般Ra1.6~3.2μm,最高可达0.8μm。 同时石膏型溃散性好,易于清除。
3、石膏型导热系数低,金属液浇入后保持流动 性时间长,铸件的成形性能好,但铸件凝固时间 长,致使铸件产生气孔、针孔、疏松、缩孔的倾 向大。
石膏型精铸专用模料主要有下列三方面要求: (1)模料强度高、韧性好,能承受石膏浆料灌
注的作用力而不变形损坏。 (2)模料线收缩小,保证熔模尺寸精确,防止
铸造工艺总汇-石膏型铸造与设计

图 1 石膏型精密铸造工艺过程
它是将熔模组装,并固定在专供灌浆用的砂箱平板上,在真空下把石膏浆料灌入,待浆料凝 结后经干燥即可脱除熔模,再经烘干、焙烧成为石膏型,在真空下浇注获得铸件。
7.1.2 工艺特点
1. 石膏浆料的流动性很好,又在真空下灌注成型,其充型性优良,复模性优异,型精确、光 洁。该工艺不像一般熔模精密铸造受到涂挂工艺的限制,可灌注大型复杂铸件用型。
3.2-3.4 3.95-4.02
5.73 4.7-4.9
12.5X10-6 0.5 X10-6 3.1-4.3 X10-6 5.3 X10-6
5.0 X10-6 8.4 X10-6 7.2-10 X10-6 5.1 X10-6
加入填料后石膏混合料强度 (Mpa)
7h 烘干 90℃,4h 焙烧 700℃,1h
取出母模(不可敲动),起模后应立即进行点火喷烧,否则易产生裂纹。 (五)喷烧 起模后应立刻点火并吹压缩空气进行喷烧,而使陶瓷型的表面有一定的强度和硬度。 (六)焙烧 焙烧的目的是使陶瓷型内残存的乙醇、水分和少量的有机物烧去,并使陶瓷层的强度增加。 全部由陶瓷浆料灌制的陶瓷型,焙烧温度可高达 800oC,焙烧时间 2~3h,出炉温度应在 2500C
第2章石膏型精密铸造2

1-石英 2-高铝矾土 3-高岭土 4-氧化铝 5-规线石 6-莫来石
三、添加剂 为改善石膏浆料某方面性能,还应加入添加剂。
添加剂分别可作增强剂、促凝剂、缓凝剂、减缩
剂。
1、增强剂—增加石膏型的湿强度、焙烧后强 度和高温强度。这类增强剂有两类:
一类如硫酸镁,以硫酸盐为主体的复合增强 剂,其本身有胶凝特性,能与填料、杂质起作用 促凝石膏; 另一类如硅溶胶,本身为粘结剂,能增强石膏 强度。
表2-11 填料种类对石膏混合料浆体凝时间的影响
填料 硅石粉 硅线石 高岭土 莫来石 高铝 矾土 工业 氧化铝 锆英粉 α 半水石 膏100%
处凝时间 7.0 终凝时间 10.0
8.5 10.5
8.0 10.0
10.0 12.0
12.0 13.5
9.0 11.0
10.0 12.0
8 10
填料种类对石膏混合料线膨胀率的 影响(加入量60%)
填料 灌浆后2h 灌浆后7d 烘干90℃/4h 700℃焙烧后 硅石粉 0.25 0.50 1.30 0.20 硅线石 0.40 1.50 2.80 0.65 莫来石 0.75 2.30 3.40 0.80 高岭土 0.80 2.40 3.80 0.86 高铝矾土 工业氧化铝 1.00 2.60 4.60 0.85 0.80 2.00 3.50 0.65
加水量多少(亦即水固比大小),与多种因素
有关,既受到固态粉料中石膏、填料、添加剂的
品种及其比例的影响,又受粉料粒度、水温等的 影响。
表2-12 石膏浆料配比
序号 石膏 硅石粉砂 1 2 3 4 5 6 7 30 30 30 30 30 30 35.5 35 — 29.0 70 35 20 石英玻璃 — — — — 35 — 35.5 其他材料 — 铝矾土粉砂 35 上店土粉砂 50 莫来石粉砂 70 — 铝矾土粉砂 70 硅藻土2
石膏铸造注意事项

石膏铸造注意事项石膏铸造是一种常见的制造工艺,广泛应用于艺术品制作、建筑装饰、医疗器械、工艺品等领域。
以下是石膏铸造时需要注意的事项:1. 原材料选择:石膏是石膏铸造的主要材料,应选择质量好、无杂质的石膏。
同时,可以根据不同的需求选择不同类型的石膏,如增强型石膏、特种石膏等。
2. 模具设计:模具是石膏铸造中至关重要的一环。
设计模具时需要确保模具结构合理、稳定,能够完整地复制所需的物体。
同时,要注意模具的开口方向以便于浇注和脱模。
3. 浇注粘度控制:控制石膏的粘度是石膏铸造中的关键步骤。
粘度过高会导致石膏流动性差,难以充填模具;粘度过低则容易形成气泡和缺陷。
因此,需要根据具体要求控制石膏的水石比,控制好水的用量,以获得适当的粘度。
4. 前处理:在浇注石膏之前,需要对模具进行预处理。
首先,要保证模具表面干净,没有灰尘和杂质。
其次,可以在模具表面涂抹一层脱模剂,以便于石膏脱模时不易粘连。
5. 浇注操作:浇注时要缓慢、均匀地将石膏倒入模具中,避免产生气泡和未充填的空隙。
同时,要控制浇注的速度和角度,以确保石膏能够充分填充模具。
6. 振动除气:在浇注完成后,可以通过轻轻震动模具来排除石膏中的气泡。
振动过程中要逐渐加大力度,同时避免过度振动导致石膏移位或损坏模具。
7. 固化和硬化:浇注完成后,需要将石膏模具放置在通风干燥的环境中进行固化和硬化。
固化时间通常为数小时到数天,具体时间要根据石膏类型和环境条件而定。
8. 脱模操作:石膏完全固化后,可以进行脱模操作。
需要注意的是,应轻轻敲击模具,使石膏从模具中脱离。
如遇到模具卡住的情况,可以使用适当的工具轻轻拍打或使用少许脱模剂帮助脱模。
9. 后处理:脱模后,可以对石膏制品进行一些修整和润饰。
可以使用砂纸、刀具等工具去除毛边和不平整的地方,使石膏制品表面光滑、细腻。
10. 储存和保护:完成石膏铸造后,要妥善储存和保护石膏制品。
可以使用密封袋或包装纸将石膏制品包裹好,避免受潮、受阳光直射和摩擦。
石膏型熔模铸造流程
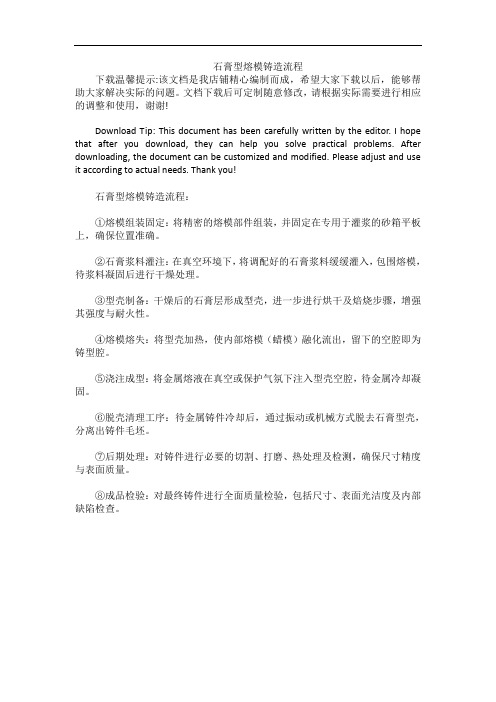
石膏型熔模铸造流程
下载温馨提示:该文档是我店铺精心编制而成,希望大家下载以后,能够帮助大家解决实际的问题。
文档下载后可定制随意修改,请根据实际需要进行相应的调整和使用,谢谢!
Download Tip: This document has been carefully written by the editor. I hope that after you download, they can help you solve practical problems. After downloading, the document can be customized and modified. Please adjust and use it according to actual needs. Thank you!
石膏型熔模铸造流程:
①熔模组装固定:将精密的熔模部件组装,并固定在专用于灌浆的砂箱平板上,确保位置准确。
②石膏浆料灌注:在真空环境下,将调配好的石膏浆料缓缓灌入,包围熔模,待浆料凝固后进行干燥处理。
③型壳制备:干燥后的石膏层形成型壳,进一步进行烘干及焙烧步骤,增强其强度与耐火性。
④熔模熔失:将型壳加热,使内部熔模(蜡模)融化流出,留下的空腔即为铸型腔。
⑤浇注成型:将金属熔液在真空或保护气氛下注入型壳空腔,待金属冷却凝固。
⑥脱壳清理工序:待金属铸件冷却后,通过振动或机械方式脱去石膏型壳,分离出铸件毛坯。
⑦后期处理:对铸件进行必要的切割、打磨、热处理及检测,确保尺寸精度与表面质量。
⑧成品检验:对最终铸件进行全面质量检验,包括尺寸、表面光洁度及内部缺陷检查。
石膏型熔模精密铸造工艺历史
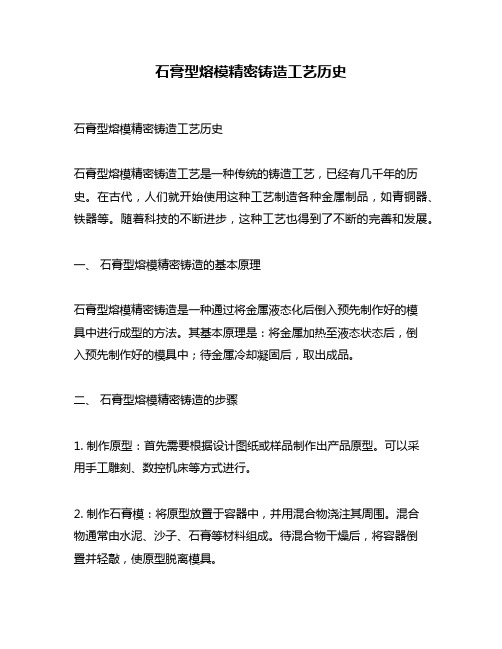
石膏型熔模精密铸造工艺历史石膏型熔模精密铸造工艺历史石膏型熔模精密铸造工艺是一种传统的铸造工艺,已经有几千年的历史。
在古代,人们就开始使用这种工艺制造各种金属制品,如青铜器、铁器等。
随着科技的不断进步,这种工艺也得到了不断的完善和发展。
一、石膏型熔模精密铸造的基本原理石膏型熔模精密铸造是一种通过将金属液态化后倒入预先制作好的模具中进行成型的方法。
其基本原理是:将金属加热至液态状态后,倒入预先制作好的模具中;待金属冷却凝固后,取出成品。
二、石膏型熔模精密铸造的步骤1. 制作原型:首先需要根据设计图纸或样品制作出产品原型。
可以采用手工雕刻、数控机床等方式进行。
2. 制作石膏模:将原型放置于容器中,并用混合物浇注其周围。
混合物通常由水泥、沙子、石膏等材料组成。
待混合物干燥后,将容器倒置并轻敲,使原型脱离模具。
3. 烘干石膏模:将制作好的石膏模放入烤箱中进行加热,以去除其中的水分。
一般需要在200℃左右加热2-3小时。
4. 浇注金属:将金属加热至液态状态后,倒入预先制作好的模具中。
注意要控制好浇注时的温度和速度,以保证成品质量。
5. 取出成品:待金属冷却凝固后,取出成品,并进行后续的加工和处理。
三、石膏型熔模精密铸造的优点1. 精密度高:由于使用了精密的模具,在铸造过程中可以得到高精度、高质量的成品。
2. 适用范围广:可以用于铸造各种形状、大小不同的零件和产品。
3. 成本低:相比其他铸造工艺,该工艺所需材料和设备较少,也更容易操作。
4. 生产效率高:一旦制作好了模具,就可以进行大批量生产,并且生产速度较快。
四、石膏型熔模精密铸造的应用领域石膏型熔模精密铸造工艺广泛应用于各种制造业领域,如航空航天、汽车、电子、医疗器械等。
其中,最常见的应用是在珠宝和首饰制造中。
由于该工艺可以制作出高精度、高质量的成品,因此很受珠宝和首饰行业的青睐。
总之,石膏型熔模精密铸造工艺是一种传统而又实用的铸造方法。
在现代制造业中,它仍然具有重要的地位,并且得到不断地发展和完善。
《陶瓷作品素材》课件——陶瓷石膏浇铸

2021年3月26日
一、石膏浇铸介绍
石膏浇铸(也称注浆成型)是将制备 好的泥浆注入多孔模型(石膏模)内,贴 近模壁的一层泥浆中的水分被模具(如石 膏)吸收后便形成了一定厚度的均匀泥层; 将余浆倒出后,泥坯因脱水收缩而与模型 脱离开来形成毛坯。从广义来说,凡是坯 料具有一定液态流动性,注入模型中凝固 成型的成型方法都可称为注浆成型法。
陶瓷 咖啡 杯绘 制训 练
作业要求:
1.绘制石膏浇铸工艺流程图1张。
2.工艺流程正确。
3.线条清晰明了。
4.画面整洁,题写姓名。
5.把自己完成的作饰计—茶与杯制制作作
泥浆泥浆注入石膏模,石膏模吸水形成薄泥层。 动力:石膏模的毛细管力。毛细管越细,水的表面张力越大,脱水推动力越大。 阻力:石膏模和坯体。 薄泥层的形成:石膏模—颗粒间;颗粒吸附于石膏模,形成薄泥层。
四、注浆成型方法
1. 普通注浆成型 空心注浆(单面注浆)
空心注浆对泥浆性能要求:比重小,稳定性好,触变性较小,细度较好。 空心注浆多用于浇注杯、壶、水箱等类产品的坯体。
四、注浆成型方法
1. 普通注浆成型 实心注浆(双面注浆)
空心注浆对泥浆性能要求:比重小,稳定性好,触变性较小,细度较好。 空心注浆多用于浇注杯、壶、水箱等类产品的坯体。
四、注浆成型方法
2. 强化注浆 压力注浆:用加大泥浆压力的方法加速水分扩散,从而加快吸浆速度。 真空注浆:用真空装置在石膏模外抽真空,或将石膏模放入真空室内。 离心注浆:使模型在旋转情况下注浆,泥浆受离心力左右紧靠模壁面成致密的坯体。
一、石膏浇铸介绍
注浆成型工艺简单,适于生产一些形状复杂且不规则、外观尺寸要求不严格、壁 薄及大型厚胎的制品。
- 1、下载文档前请自行甄别文档内容的完整性,平台不提供额外的编辑、内容补充、找答案等附加服务。
- 2、"仅部分预览"的文档,不可在线预览部分如存在完整性等问题,可反馈申请退款(可完整预览的文档不适用该条件!)。
- 3、如文档侵犯您的权益,请联系客服反馈,我们会尽快为您处理(人工客服工作时间:9:00-18:30)。
5.浇注系统及冒口设计
1. 石膏型精密铸造的浇冒系统应满足下列要求: (1)有良好的排气能力,能顺利排出型腔中气 体,在顶部和易憋气处要开设出气口。 (2)要保证合金液在型腔中流动平稳,顺利充 满型胶,避免出现涡流,卷气现象。 (3)合理设置冒口,保证补缩。 (4)脱模时浇注系统应先蒋先,减小熔模对石 膏型的膨胀力。 (5)浇注系统在铸件凝固过程中应尽可能不阻 碍铸件收缩,以防止件变形和开裂。
7.石膏浆料
1.真空灌浆 为提高浆料的充填能力,应在真空条件 下灌浆。 2.熔模脱除和石膏型烘干 3.石膏型焙烧 石膏型焙烧的主要目的是去除残留于石 膏型中的模料、结晶水以及其它发气物, 同时完成石膏型中一些组成物的相变过程, 使其体积稳定。焙烧炉可用天然气炉、电 阻炉。
4.合金熔炼及浇注 (1) 合金熔炼 石膏型精密铸造以铝合金为主,一般适用于砂 型铸造的铝合金亦能用于石膏型精铸,其中以铝 硅类合金用得最多。为获得优质的铝铸件,一定 要采用最有效的精炼除气工艺和变质处理方法。 (2) 浇注工艺参数 金属液的浇注温度和石膏型温度两者应合理配 合,以取得优良铸件质量,石膏型温度可控制在 150~300℃之间,铝合金浇注温度一般可低于其 它铸造方法,控制在700℃左右,对大型薄壁铸件 浇注温度可适当提高。 5.铸件清整 对大型复杂薄壁铝精铸件必须进行大量细致的 清理、修补和校正等工作。
4.应用范表面 光洁的精密铸件,特别适宜生产大型复杂 薄壁铝合金铸件,也可用于锌、铜、金、 银等合金铸件。铸件最大尺寸达 1000×2000mm、重量0.03~908kg,壁厚 0.8~1.5mm(局部0.5mm)。石膏型精密铸 造己被广泛应用于航空、宇航、兵器、电 子、船舶、仪器、计算机等行业的零件制 造上。
2. 浇注系统类型选择 一般浇注系统可分顶注、中间注、 底注和阶梯注几种。对高度大的薄 壁筒形、箱形件也可用缝隙式或阶 梯式浇注系统。对某些铸件亦可采 用平注和斜注。
3. 内浇口位置选择 石膏型表面硬度不够高、热导率小,因此 内浇口一般不应直对型壁和型芯,防止冲 刷型壁和型芯,而应沿着型壁和型芯设内 浇口。对复杂的薄壁件为防止件变形及裂 纹,内浇口应均匀分布,避免局部过热及 浇不足缺陷。内浇口应尽可能设在铸件热 节处,利于补缩。
石膏型铸造
2011071107 夏天
1 概述
石膏型精密铸 造是用世纪70 年代发展起来 的一种精密铸 造新技术其工 艺过程见图。
2.定义
它是将熔模组装,并固定在专供 灌浆用的砂箱平板上,在真空下把 石膏浆料灌入,待浆料凝结后经干 燥即可脱除熔模,再经烘干、焙烧 成为石膏型,在真空下浇注获得铸 件。
6.石膏浆料的原材料
1. 石膏 天然石膏为CaSO4· 2H20,又称二水石膏。二水 石膏有七种变体。α型半水石膏做石膏型更为合适。 除石膏种类外,影响石膏强度的因素还有石膏的 细度、水固比、水温、搅拌时间等。 2. 填料 为使石膏型具有良好的强度,减小其收缩和裂 纹倾向,需要在石膏中加入填料。填料应有合适 的熔点、耐火度,良好的化学稳定性、合适的线 膨胀率、发气量少,吸湿性小等性能 3. 添加剂 为提高石膏型焙烧后强度、改变石膏型凝结时 间和清理性,改变其线膨胀率等需在石膏浆料中 加人添加物。
3.工艺特点
1. 石膏浆料的流动性很好,又在真空下灌注成型, 其充型性优良,复模性优异,型精确、光洁。该 工艺不像一般熔模精密铸造受到涂挂工艺的限制, 可灌注大型复杂铸件用型。 2. 石膏型的热导率很低,充型时合金液流动保持 时间长,适宜生产薄壁复杂件。但铸型激冷作用 差,当铸件壁厚差异大时,厚大处容易出现缩松、 缩孔等缺陷。 3. 石膏型透气性极差,铸件易形成气孔、浇不足 等缺陷,应注意合理设置浇注及排气系统。