石膏型精密铸造(石膏粉)
雕塑石膏实体铸型的制作工艺介绍
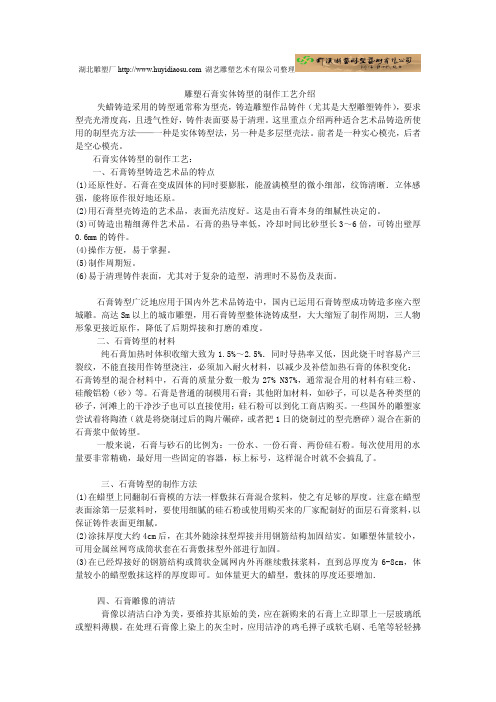
雕塑石膏实体铸型的制作工艺介绍失蜡铸造采用的铸型通常称为型壳,铸造雕塑作品铸件(尤其是大型雕塑铸件),要求型壳光滑度高,且透气性好,铸件表面要易于清理。
这里重点介绍两种适合艺术品铸造所使用的制型壳方法——一种是实体铸型法,另一种是多层型壳法。
前者是一种实心模壳,后者是空心模壳。
石膏实体铸型的制作工艺:一、石膏铸型铸造艺术品的特点(1)还原性好。
石膏在变成固体的同时要膨胀,能盈满模型的微小细部,纹饰清晰.立体感强,能将原作很好地还原。
(2)用石膏型壳铸造的艺术品,表面光洁度好。
这是由石膏本身的细腻性决定的。
(3)可铸造出精细薄件艺术品。
石膏的热导率低,冷却时间比砂型长3~6倍,可铸出壁厚0.6mm的铸件。
(4)操作方便,易于掌握。
(5)制作周期短。
(6)易于清理铸件表面,尤其对于复杂的造型,清理时不易伤及表面。
石膏铸型广泛地应用于国内外艺术品铸造中,国内已运用石膏铸型成功铸造多座六型城雕。
高达Sm以上的城市雕塑,用石膏铸型整体浇铸成型,大大缩短了制作周期,三人物形象更接近原作,降低了后期焊接和打磨的难度。
二、石膏铸型的材料纯石膏加热时体积收缩大致为1.5%~2.5%.同时导热率又低,因此烧干时容易产三裂纹,不能直接用作铸型浇注,必须加入耐火材料,以减少及补偿加热石膏的体积变化:石膏铸型的混合材料中,石膏的质量分数一般为27%N37%,通常混合用的材料有硅三粉、硅酸铝粉(砂)等。
石膏是普通的制模用石膏;其他附加材料,如砂子,可以是各种类型的砂子,河滩上的干净沙子也可以直接使用;硅石粉可以到化工商店购买。
一些国外的雕塑家尝试着将陶渣(就是将烧制过后的陶片碾碎,或者把1日的烧制过的型壳磨碎)混合在新的石膏浆中做铸型。
一般来说,石膏与砂石的比例为:一份水、一份石膏、两份硅石粉。
每次使用用的水量要非常精确,最好用一些固定的容器,标上标号,这样混合时就不会搞乱了。
三、石膏铸型的制作方法(1)在蜡型上同翻制石膏模的方法一样敷抹石膏混合浆料,使之有足够的厚度。
石膏型铸造讲义

石膏型铸造讲义
1
主要内容 概述 1、制石膏型用材料及其组成 2、石膏型精铸工艺
2
概述
1、工艺过程 石膏型精密铸造是20世纪70年代发展起来的一
种精密铸造新技术,其典型工艺过程见图0-1。 它是将熔模组装,并固定在专供灌浆用的砂箱
平板上,在真空下把石膏浆料灌入,待浆料凝结后 经干燥即可脱除熔模,再经烘干、焙烧成为石膏型, 在真空下浇注获得铸件。
3
概述
2、工艺特点
(1) 石膏浆料的流动性很好,又在真空下灌注成型, 其充型性优良,复模性优异,型精确、光洁。该工艺不 像一般熔模精密铸造受到涂挂工艺的限制,可灌注大型 复杂铸件用型。
(2) 石膏型的热导率很低,充型时合金液流动保持 时间长,适宜生产薄壁复杂件。
但铸型激冷作用差,组织粗大,当铸件壁厚差异大 时,厚大处容易出现缩松、缩孔等缺陷。
1.3
0.2
2.1-2.2 0.5 X10-6
3.25 3.1-4.3 X10-6 1.5
0.65
3.08-
5.3 X10-6
2.3
3.4
0.80
3.15
3.2-3.4 5.0 X10-6 2.6
4.6
0.85
3.95-
8.4 X10-6
2.0
3.5
0.65
4.02
5.73 7.2-10 X10-6
除石膏种类外,影响石膏强度的因素还有石膏的 细度、水固比、水温、搅拌时间等。
6
第一节 制石膏型用材料及其组成 2. 填料
为使石膏型具有良好的强度,减小其收缩和裂纹 倾向,需要在石膏中加入填料。
填料应有合适的熔点、耐火度,良好的化学稳定 性、合适的线膨胀率、发气量少,吸湿性小等性能, 常用作填料的材料及其性能见表1-1。
铸造工艺总汇-石膏型铸造与设计

图 1 石膏型精密铸造工艺过程
它是将熔模组装,并固定在专供灌浆用的砂箱平板上,在真空下把石膏浆料灌入,待浆料凝 结后经干燥即可脱除熔模,再经烘干、焙烧成为石膏型,在真空下浇注获得铸件。
7.1.2 工艺特点
1. 石膏浆料的流动性很好,又在真空下灌注成型,其充型性优良,复模性优异,型精确、光 洁。该工艺不像一般熔模精密铸造受到涂挂工艺的限制,可灌注大型复杂铸件用型。
3.2-3.4 3.95-4.02
5.73 4.7-4.9
12.5X10-6 0.5 X10-6 3.1-4.3 X10-6 5.3 X10-6
5.0 X10-6 8.4 X10-6 7.2-10 X10-6 5.1 X10-6
加入填料后石膏混合料强度 (Mpa)
7h 烘干 90℃,4h 焙烧 700℃,1h
取出母模(不可敲动),起模后应立即进行点火喷烧,否则易产生裂纹。 (五)喷烧 起模后应立刻点火并吹压缩空气进行喷烧,而使陶瓷型的表面有一定的强度和硬度。 (六)焙烧 焙烧的目的是使陶瓷型内残存的乙醇、水分和少量的有机物烧去,并使陶瓷层的强度增加。 全部由陶瓷浆料灌制的陶瓷型,焙烧温度可高达 800oC,焙烧时间 2~3h,出炉温度应在 2500C
铜器石膏型失蜡铸造法简介

铜器石膏型失蜡铸造法简介中华文明的历史进程中有很多手工艺的(璀璨发明,失蜡浇铸法就是其中之一。
失蜡浇铸法最早见于商周时代的青铜器加工中,到明清则大为盛行。
其特点:精细入微、毫厘毕现,比较适合于美感要求比较高的工艺品的加工。
到了现代,由于新的现代材料不断出现和引入,目前的失蜡铸造法除始终保持古法的目的和宗旨外,在方式方法上已不完全一样。
以下就目前常用的石膏型失蜡铸造方法作简单介绍。
石膏型失蜡铸造法的基本流程:一制阴模古法的阴模由泥土作成,然后烧制成低温陶性质的阴模,称之为“陶范”,由于烧陶过程中有很多变形的可能,所以现代已不再使用陶范的方式,而改用强度较高的石膏制作阴模:制作时在整体的阳模(现代一般是玻璃钢材质)上,按易于拆分的原则,用石膏浆制作出多块合成的套模(此时特别要注意脱模剂的使用),待石膏型固化冷却后,可将阴模拆解分开,清洁阴模内表面,用水刷7-8分潮湿后背用;二制蜡型将备好的阴模拼合成整体,使之形成需铸造的工艺品的负型(即阴模),然后将调制并加温到一定温度的液态工艺品蜡液涂刷于阴模内表面,涂刷时注意每层尽量整体一次刷完整,待整体都冷却硬化固定后再涂刷下一层,逐层加厚,直到达到所需厚度。
蜡型的厚度视加工件的大小而定,4-10毫米不等。
要求厚薄均匀,附着密实。
蜡型制作完成后,清理内表面的毛刺、将阴模的边口处修理平滑。
备用;三灌内浆将刷制完成的蜡型带石膏阴模一起倒立(大形的还需在阴模外壳加以捆扎,以防灌注时内压过大使蜡模崩裂),如有多个刷蜡口则将其他的次要开口堵住,留主口朝上,将事先混合好的耐火材料用水调制成匀质的泥浆,灌注于蜡型内,要求:灌注到位、不留空泡、操作上一气呵成、避免分层现象。
静置6小时待蜡型内的耐火材料完全硬化后方可进行下阶段的操作;四修蜡模接浇道将已灌注好耐火材料内浆的模型整体正立过来,小心去掉最外面的石膏阴模(要按拼合规律逐次拆分,不可蛮干以免损伤里面的蜡型),全部阴模拆除后用小刀修除模块之间缝隙形成的蜡毛边、毛刺,清洁蜡型表面,如有损伤则用修补软蜡修补完整。
精密铸造法(脱蜡法石膏模法和陶瓷模)

精密铸造(Precision Casting)1 前言精密铸造法是指使用非金属铸模,制品尺寸精度高于普通砂模铸件之铸造法的总称,包括脱蜡法(Lost Wax Casting或Investment Casting),石膏模法(Plaster Mold Casting)和陶瓷模(Ceramic Mold Casting)法三大类。
2 脱蜡法精密铸造2-1 特征与优点(1)铸件的最大界限长度为700mm,易作之长度在200mm以下。
铸件之最大重量约100公斤,一般常为10公斤以下。
(2)铸件之尺寸公差20mm ±0.13mm,100mm ±0.30mm,200mm ±0.43mm,而小件之尺寸精度不易达到±0.10mm以内。
角度公差为±0.5~±2.0度,铸件最小厚度0.5~1.5mm。
铸件表面粗度约Rmax 4S~12S。
(3)铸件材质几无任何限制,如铝合金、镁合金、钛合金、铜合金,各种钢材、钴基和镍基耐热合金,硬材料。
(4)制作形状复杂之工件,尺寸精度良好,切削加工少。
(5)节省材料浪费,并可大量生产。
脱蜡精密铸件广用于喷射引擎、燃气涡轮、蒸汽涡轮、飞机零件、内燃机、车辆、食品机械、印刷机械、制纸机械、压缩机、阀件、帮浦、计测仪、缝纫机、武器、事务机器、及其它机器零件。
2-2 制程脱蜡铸造法有两大类:实心模(Solid Mold)法和陶壳模(Ceramic Shell Mold)法,后者为前者的改良法。
实心模法系在考虑蜡型的冷凝收缩量,铸模的加热膨胀量和熔融金属的冷凝收缩量之后,制作与最终铸件尺寸近似的模具。
将融化的蜡质押灌注入此以金属或硅胶做成之模具内,取出蜡型后,浸入微粉耐火材料与粘结剂混泡而成之浆液。
滴净之后,撒布粗粒耐火材料,使之干燥。
放入铸框,将混练有粘结剂的耐火物粒填满之,然后干燥。
接着加热使蜡质熔化流出来,作成铸模。
以高温加热铸模,烧除少量残余之蜡质并提高其强度,接着注入金属熔液。
石膏型熔模铸造流程
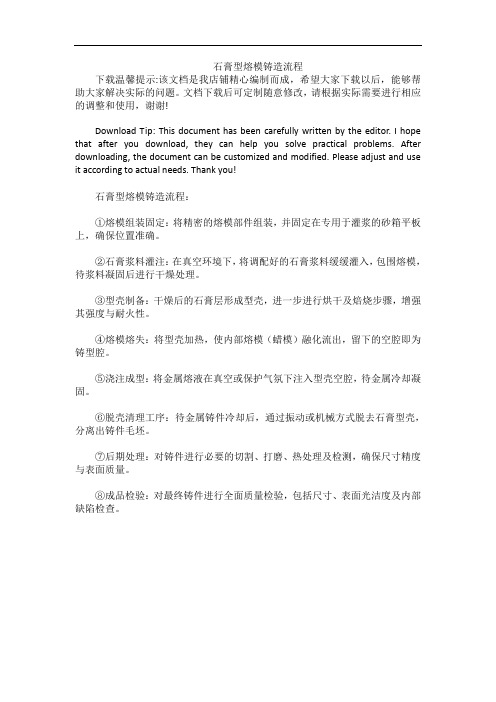
石膏型熔模铸造流程
下载温馨提示:该文档是我店铺精心编制而成,希望大家下载以后,能够帮助大家解决实际的问题。
文档下载后可定制随意修改,请根据实际需要进行相应的调整和使用,谢谢!
Download Tip: This document has been carefully written by the editor. I hope that after you download, they can help you solve practical problems. After downloading, the document can be customized and modified. Please adjust and use it according to actual needs. Thank you!
石膏型熔模铸造流程:
①熔模组装固定:将精密的熔模部件组装,并固定在专用于灌浆的砂箱平板上,确保位置准确。
②石膏浆料灌注:在真空环境下,将调配好的石膏浆料缓缓灌入,包围熔模,待浆料凝固后进行干燥处理。
③型壳制备:干燥后的石膏层形成型壳,进一步进行烘干及焙烧步骤,增强其强度与耐火性。
④熔模熔失:将型壳加热,使内部熔模(蜡模)融化流出,留下的空腔即为铸型腔。
⑤浇注成型:将金属熔液在真空或保护气氛下注入型壳空腔,待金属冷却凝固。
⑥脱壳清理工序:待金属铸件冷却后,通过振动或机械方式脱去石膏型壳,分离出铸件毛坯。
⑦后期处理:对铸件进行必要的切割、打磨、热处理及检测,确保尺寸精度与表面质量。
⑧成品检验:对最终铸件进行全面质量检验,包括尺寸、表面光洁度及内部缺陷检查。
石膏型熔模铸造用铸粉的研究和实践

科技资讯科技资讯S I N &T NOLOGY I NFORM TI ON 2008NO .07SC I ENCE &TECH NO LOG Y I NFOR M A TI O N 工业技术石膏型熔模铸造工艺中使用石膏铸型材料。
单纯使用α-半水石膏并不能进行石膏型铸造,这是因为石膏在烘干及焙烧过程中不断脱水,发生相变,特别当温度高于300℃时,线收缩急剧增加,裂纹倾向增大。
700℃时,α-半水石膏线收缩率达2%以上。
由于收缩过大,裂纹倾向严重,强度急剧降低,为了改善石膏的性能使之适应铸造的要求(如尺寸精度、透气性等),通常在α-半水石膏中加入50%以上的各种矿物粉料。
国内经常使用石英玻璃、莫来石粉、锆石粉等在一定温度范围内线胀系数变化不大的填料。
但这些矿物来源比较稀少,成本很高,对石膏型的机械性能、尺寸精度和热性能的改善还不尽理想。
因此,寻找更为有利的非金属复合矿物粉体材料是石膏型铸造工艺中有待解决的实际课题。
石英粉是常见的耐火材料,价低易得。
石英存在着多种变体,随着温度的变化而产生相变,产生多种晶型,同时伴随有体积和密度的变化。
石英在573℃时由β相转变为α相时,体积膨胀为0.82%;而方石英则在180~270℃时由β相转变为α相时,体积膨胀达2.8%[1]。
资料显示,石英粉是非常优异的石膏铸型填料,随着温度的升高,石英的膨胀可以抵消石膏的大部分收缩。
但是,石英的膨胀来自其晶型转变带来的较大体积变化,其转变温度无法和石膏的转变温度完全吻合,而突然的体积变化很容易造成铸型的开裂,最终无法浇注出合格的铸件。
本实验采用石英粉作为主要的石膏铸型材料,辅以添加了高铝矾土粉、滑石粉、玻璃纤维等,对石膏铸型的性能进行改善,找出能够用于实际生产的铸型配方。
1试验的方法和内容试验的主要原料为:α-半水石膏,300目,湖南应城产;石英细粉,325目,重庆产;高铝矾土粉,180目,贵州产;滑石粉,325目,贵州产。
铝合金石膏型熔模铸造工艺
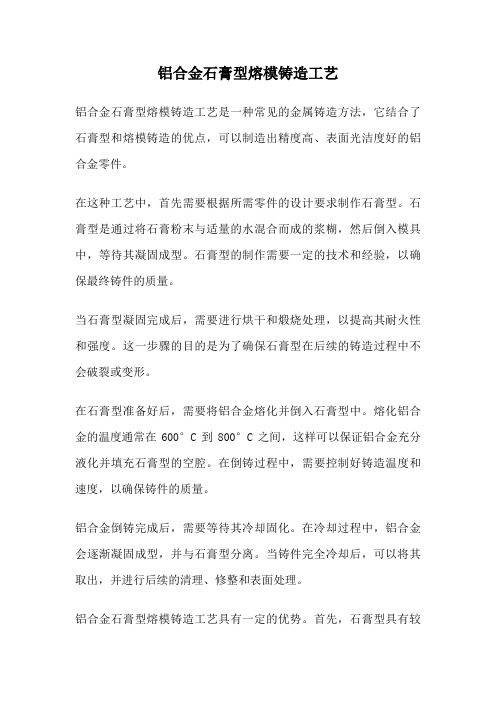
铝合金石膏型熔模铸造工艺铝合金石膏型熔模铸造工艺是一种常见的金属铸造方法,它结合了石膏型和熔模铸造的优点,可以制造出精度高、表面光洁度好的铝合金零件。
在这种工艺中,首先需要根据所需零件的设计要求制作石膏型。
石膏型是通过将石膏粉末与适量的水混合而成的浆糊,然后倒入模具中,等待其凝固成型。
石膏型的制作需要一定的技术和经验,以确保最终铸件的质量。
当石膏型凝固完成后,需要进行烘干和煅烧处理,以提高其耐火性和强度。
这一步骤的目的是为了确保石膏型在后续的铸造过程中不会破裂或变形。
在石膏型准备好后,需要将铝合金熔化并倒入石膏型中。
熔化铝合金的温度通常在600°C到800°C之间,这样可以保证铝合金充分液化并填充石膏型的空腔。
在倒铸过程中,需要控制好铸造温度和速度,以确保铸件的质量。
铝合金倒铸完成后,需要等待其冷却固化。
在冷却过程中,铝合金会逐渐凝固成型,并与石膏型分离。
当铸件完全冷却后,可以将其取出,并进行后续的清理、修整和表面处理。
铝合金石膏型熔模铸造工艺具有一定的优势。
首先,石膏型具有较高的精度和光洁度,可以制造出形状复杂、尺寸精确的铝合金零件。
其次,石膏型可以重复使用,降低生产成本。
此外,由于铝合金的低熔点和良好的流动性,石膏型熔模铸造工艺适用于各种铝合金材料。
然而,铝合金石膏型熔模铸造工艺也存在一些限制。
首先,由于石膏型的制备和处理过程较为复杂,需要一定的时间和技术。
其次,石膏型在高温下容易破裂或变形,需要特殊的处理和保护措施。
此外,由于铝合金的热膨胀系数较大,在铸造过程中需要考虑收缩和变形的问题。
总的来说,铝合金石膏型熔模铸造工艺是一种高精度、高质量的铸造方法。
它不仅可以满足各种复杂零件的制造要求,还能够提高生产效率和降低生产成本。
随着技术的不断进步,铝合金石膏型熔模铸造工艺在各个领域的应用将会越来越广泛。
- 1、下载文档前请自行甄别文档内容的完整性,平台不提供额外的编辑、内容补充、找答案等附加服务。
- 2、"仅部分预览"的文档,不可在线预览部分如存在完整性等问题,可反馈申请退款(可完整预览的文档不适用该条件!)。
- 3、如文档侵犯您的权益,请联系客服反馈,我们会尽快为您处理(人工客服工作时间:9:00-18:30)。
拔模铸造用粉
SRS完美的产品
SRS 在拔模铸造这一精密铸造领域上一直处于世界领先的地位,并且制定出专门控制产品粘度、流动性、胶凝时间以及亚光时间的质量控制流程。
我们的铸粉产品是使用最纯的、经过筛选的原材料。
这种石膏粉是专门应用于木模或硅橡胶拔模铸造而设计的。
SRS铸粉能在生产过程中体现出其稳定性以及可靠性。
适用于大批量短开发周期的生产,拔模铸造是出了熔模、砂型、以及原型压铸外的另一种选择。
其最常见的用途是涡轮增压器叶轮。
SRS 承诺会为你提供最优质的产品。
而这些产品在我们的实验室模拟以及多间铸造厂得到验证。
轮胎模具铸粉
一种专门应用于铝合金轮胎模具的铸粉。
正如我们的其他工业
铸粉一样,这种铸粉也可以根据客户的需求进行调整。
鞋模铸粉
这种铸粉的配方是专门应用于制作铝合金鞋模。
工业铸粉
这是针对于拔模铸造工艺的铝合金铸造而研发出来的。
这种
石膏粉已经在欧洲铸造行业中的多间领头企业使用多年,
尤其是涡轮增压器叶轮方面。