瞬时铣削力建模与铣削力系数的粒子群法辨识
数控机床铣削切削力的模拟与实测方法

数控机床铣削切削力的模拟与实测方法摘要:数控机床在现代制造业中发挥着重要作用,铣削切削力的模拟与实测是数控机床加工研究的关键问题之一。
本文将介绍数控机床铣削切削力的模拟与实测方法,包括力学模型的建立、数值仿真和实验测试等方面的内容,以期为相关研究提供参考。
一、引言数控机床作为现代制造业的重要工具,其高精度、高效率的特点受到广泛关注。
而铣削切削力在数控铣床加工过程中起着决定性作用,对加工质量和机床性能具有重要影响。
因此,模拟和实测数控机床铣削切削力成为加工研究的重要内容之一。
二、模拟方法1. 力学模型的建立铣削切削力的模拟首先要建立合适的力学模型。
常用的力学模型包括切削力系数模型和有限元模型两种。
切削力系数模型是通过实验获得相关参数后,根据经验公式计算切削力。
有限元模型则是将加工过程建模为一系列有限元素,通过数值分析计算切削力的分布和大小。
2. 数值仿真数值仿真是利用计算机软件模拟数控机床加工过程和切削力的计算。
常用的仿真软件有Deform、ABAQUS等。
数值仿真可以通过调整刀具几何参数、切削条件和材料性质等因素,预测不同情况下的切削力大小和分布情况,为工艺优化提供指导。
三、实测方法1. 切削力测量设备实测切削力是了解加工过程中切削力的真实情况的重要手段。
常用的切削力测量设备包括力传感器、力加载装置和数据采集系统。
力传感器可以精确测量切削力大小,力加载装置则提供切削力测量所需的切削环境。
数据采集系统可以记录和分析切削力的变化规律。
2. 实验测试方法实验测试是通过具体的切削加工试验获取切削力的实际数值。
实验测试中需要准确控制切削条件,包括切削速度、进给速度和切削深度等。
通过实验测试可以获得不同切削条件下的切削力数值,用于验证模拟结果的准确性。
四、研究进展与展望随着数控机床技术的不断发展,数控机床铣削切削力的模拟与实测方法也在不断改进和完善。
当前的研究重点主要集中在提高模拟精度和实验测试的准确性,并进一步优化数控机床的切削性能。
基于主轴和进给轴电流的铣削力间接预测方法
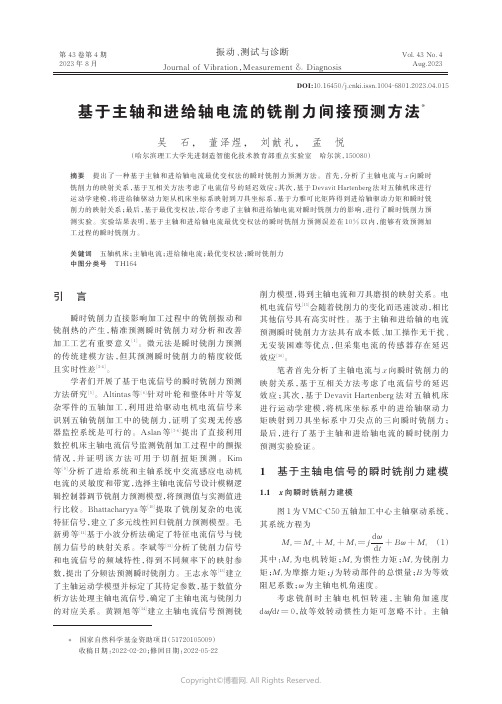
第 43 卷第 4 期2023 年 8 月振动、测试与诊断Vol. 43 No. 4Aug.2023 Journal of Vibration,Measurement & Diagnosis基于主轴和进给轴电流的铣削力间接预测方法∗吴石,董泽煜,刘献礼,孟悦(哈尔滨理工大学先进制造智能化技术教育部重点实验室哈尔滨,150080)摘要提出了一种基于主轴和进给轴电流最优变权法的瞬时铣削力预测方法。
首先,分析了主轴电流与x向瞬时铣削力的映射关系,基于互相关方法考虑了电流信号的延迟效应;其次,基于Devavit Hartenberg法对五轴机床进行运动学建模,将进给轴驱动力矩从机床坐标系映射到刀具坐标系,基于力雅可比矩阵得到进给轴驱动力矩和瞬时铣削力的映射关系;最后,基于最优变权法,综合考虑了主轴和进给轴电流对瞬时铣削力的影响,进行了瞬时铣削力预测实验。
实验结果表明,基于主轴和进给轴电流最优变权法的瞬时铣削力预测误差在10%以内,能够有效预测加工过程的瞬时铣削力。
关键词五轴机床;主轴电流;进给轴电流;最优变权法;瞬时铣削力中图分类号TH164引言瞬时铣削力直接影响加工过程中的铣削振动和铣削热的产生,精准预测瞬时铣削力对分析和改善加工工艺有重要意义[1]。
微元法是瞬时铣削力预测的传统建模方法,但其预测瞬时铣削力的精度较低且实时性差[2‐4]。
学者们开展了基于电流信号的瞬时铣削力预测方法研究[5]。
Altintas等[6]针对叶轮和整体叶片等复杂零件的五轴加工,利用进给驱动电机电流信号来识别五轴铣削加工中的铣削力,证明了实现无传感器监控系统是可行的。
Aslan等[7‐8]提出了直接利用数控机床主轴电流信号监测铣削加工过程中的颤振情况,并证明该方法可用于切削扭矩预测。
Kim 等[9]分析了进给系统和主轴系统中交流感应电动机电流的灵敏度和带宽,选择主轴电流信号设计模糊逻辑控制器调节铣削力预测模型,将预测值与实测值进行比较。
面向球头铣刀多轴铣削加工的铣削力系数辨识

面向球头铣刀多轴铣削加工的铣削力系数辨识王博;黎柏春;杨建宇;王宛山【摘要】提出了一种适用于球头铣刀多轴铣削加工的铣削力系数辨识方法.首先,将剪切力系数考虑为轴向位置角κ的多项式函数,推导了基于平均铣削力的铣削力系数辨识模型.然后,设计了多组刀具轴线与工件表面夹角不同的槽切铣削实验来实现铣削力系数辨识,以保证通过实验辨识得到的铣削力系数包含了球头铣刀不同姿态切削对铣削力的影响因素.最后,通过实验验证了该方法的正确性和可靠性.实验结果表明,该辨识方法相比于基于瞬时铣削力的辨识方法具有更好的抗干扰能力和更高的辨识精度,适用于球头铣刀多轴铣削加工的铣削力预测.【期刊名称】《东北大学学报(自然科学版)》【年(卷),期】2018(039)011【总页数】6页(P1630-1635)【关键词】球头铣刀;多轴铣削;铣削力;铣削力系数;系数辨识【作者】王博;黎柏春;杨建宇;王宛山【作者单位】东北大学机械工程与自动化学院,辽宁沈阳 110819;东北大学机械工程与自动化学院,辽宁沈阳 110819;东北大学机械工程与自动化学院,辽宁沈阳110819;东北大学机械工程与自动化学院,辽宁沈阳 110819【正文语种】中文【中图分类】TH164铣削力是加工过程中的重要物理参数,也是进一步研究铣削加工过程的基础和前提.早在20世纪90年代,Lee等[1]就详细论述了根据正交切削数据预测球头铣刀槽切铣削力的方法,提出的微元切削力模型沿用至今.近年随着球头铣刀多轴铣削加工的广泛应用,铣削力预测的相关研究成为热点 [2-4].可靠的铣削力预测不仅取决于准确的铣削力模型,还依赖于准确的铣削力系数.因此,铣削力系数辨识(求解)对铣削力预测至关重要.铣削力系数与铣削力模型、刀具材料、工件材料、刀具几何形状和切削状态等因素密切相关,难以直接求解,常用方法是通过实验逆解铣削力系数,即铣削力系数辨识.早期的Altintas等[1,5]推导了正交切削数据与铣削力系数之间的关系模型,并利用该关系模型进行了球头铣刀和平底铣刀的铣削力预测研究.Gonzalo等[6]提出了利用瞬时铣削力辨识得到正交铣削的铣削力系数.Cao等[7]提出了考虑铣刀倾角的铣削力系数辨识方法.Wang等[8]通过线性拟合实验测得平均铣削力数据来反解得到铣削力系数.Wojciechowski等[9]提出了根据瞬时铣削力辨识得到铣削力系数的方法.Mithilesh等[10]提出了基于平均铣削力辨识得到球头铣刀铣削力系数的方法.上述相关研究可分为基于平均铣削力和基于瞬时铣削力2种辨识方法.其中,基于平均铣削力的方法可降低干扰、误差对辨识结果的影响,但需进行多次实验测量,而基于瞬时铣削力的方法则正好相反.在基于瞬时铣削力进行面向球头铣刀多轴铣削的铣削力系数辨识研究中发现该方法受干扰较大,存在较大误差[11].因此,为了提高系数辨识的抗干扰能力,本文将在已有研究的基础上,基于平均铣削力的辨识方法进行面向球头铣刀多轴铣削加工的铣削力系数辨识建模和实验研究.1 铣削力系数辨识模型在前期研究中,完成了面向球头铣刀多轴铣削的铣削力建模,并通过实验验证该模型的正确性[11].因此,本文以该模型为基础推导基于平均铣削力的铣削力系数辨识模型.该整体铣削力模型为(1)式中相关符号变量、向量和矩阵的几何意义或计算表达式详见文献[11]中的阐述. 铣削力系数包括犁耕力系数和剪切力系数.大量研究表明,犁耕力系数Kte,Kre,Kae 一般为常数,剪切力系数Ktc,Krc,Kac则是与切削刃微元点位置有关的函数.因此,采用多项式函数的形式将剪切力系数表示为轴向位置角κ的多项式函数:(2)式中:Ktc0,Krc0,Kac0,…,Ktch,Kr ch,Kach均是待辨识的常数;h为剪切力系数多项式的阶次.根据平均铣削力的定义和式(1)所描述的铣削力模型可得到平均铣削力的预测模型为(3)式中:分别为球头铣刀旋转一周时预测的平均铣削力在刀具坐标系下的x,y,z分量;T 为刀具旋转一周的时间,即周期.通过实验测量值可由式(4)计算得到平均铣削力:(4)式中,分别为通过实验测量值计算得到的平均铣削力在刀具坐标系下的x,y,z分量;分别为测量得到的铣削力在刀具坐标系下的x,y,z分量.结合式(1)~式(4),利用预测值和测量值相等可得到铣削力系数辨识模型的基本形式:(5)式中:A为辨识系数矩阵;K为待辨识的系数.(6)(7)由式(5)~式(7)可以看出,一次槽铣的实验数据只能构成3个方程,而待辨识的系数则远多于3个,属于不定方程组.因此,需要进行多组实验以构成方程个数大于或等于待辨识系数个数的方程组为(8)式中:分别为各组槽铣实验中测量铣削力的平均值;A1,A2,…,Ag分别为各组槽铣实验所对应的待辨识系数矩阵.采用多组槽铣实验数据是提高辨识结果精度的有效方法,但同时构成超定方程组.为此可利用最小二乘法寻找最小二乘估计结果即方程组解.(9)2 铣削力系数辨识的实验研究2.1 铣削力系数辨识实验方案为了验证前述建立的铣削力系数辨识模型,选用45号钢(硬度为32HRC)作为加工材料,直径为8 mm的钨钢球头铣刀(含涂层ALTiN,详细参数如图1和表1所示)作为铣削刀具,设计多组槽切铣削加工实验,各组铣削参数如表2所示.图1 球头铣刀的几何形状Fig.1 Geometrical shape of a ball-end milling cutter表1 球头铣刀的几何参数Table 1 Geometrical parameters of a ball-end cutter名称数值名称数值直径/mm8锥角/(°)0球头半径/mm4刃长/mm14刀长/mm60刃数245°处的端刃法前角/(°)5周刃前角/(°)545°处的端刃法后角/(°)5周刃后角/(°)10第一后角面宽/mm0.4公称螺旋角/(°)30表2 铣削参数Table 2 Milling parameters序号主轴转速nr·min-1铣削深度apmm进给速率vfmm·min-1每齿进给量fzmm·z-1倾斜角λf(°)111940.5119.40.0590211940.5238.80.190311941.0119.40.0590411941. 0238.80.190511940.5119.40.0575611940.5238.80.175711941.0119.40.0575 811941.0238.80.175911940.5119.40.05601011940.5238.80.1601111941.011 9.40.05601211941.0238.80.160表2中的倾斜角为铣削时刀具轴线与工件表面的夹角,其详细的几何关系如图2所示.该倾斜角的设置是为了保证铣削力系数辨识过程中球头表面上的切削刃能得到充分考虑,以符合多轴铣削加工时刀轴方向任意变化的情况.2.2 铣削力系数辨识实验设备本文用于铣削力系数辨识实验的设备主要包括机床和铣削力测量系统:机床则采用实验室现有的DMG-DMU50五轴数控机床;铣削力测量系统主要是由Kistler9275三向压电测力仪、Kistler5070电荷放大器和Kistler2855A5数据采集卡组成.各实验设备和铣削力测量系统的连接原理,如图3所示.图2 铣削参数的几何意义Fig.2 Geometrical meaning of milling parameters 图3 实验设备Fig.3 Experimental equipment2.3 铣削力系数辨识实验的测量结果和辨识结果根据上述方案进行槽切实验,图4为进行数次槽切实验后的工件.同时,以4 776 Hz 的采样频率测得表2所对应的12组槽切实验的铣削力数据.由于篇幅所限,此处给出表2中第4组铣削实验测得的铣削力数据如图5所示.图4 实验工件Fig.4 An experimental workpiece对图5所描述的铣削力测量值以及其他的铣削力测量值,进行初步分析和讨论. 1) 根据前述的进给速度(119.4 mm·min-1或238.8 mm·min-1)、槽切行程(40 mm)和刀具半径(4 mm)可计算得到每次槽切铣削的耗时为22.11 s或11.06 s.该耗时即为存在铣削力的时间区域,显然图5中测量铣削力的时间区域与此相符.图5 第4组槽切铣削实验测得的铣削力Fig.5 The forth group of the milling forces acquired in slot milling experiments2) 根据铣削加工的特点可知,槽切铣削是一种周期性的切削过程,其周期为刀具旋转一周的耗时与刀具齿数的比值,由此可计算得到文中槽切实验的周期应为0.025 13 s.该值正是图5中测量铣削力所体现的周期大小.3) 根据文献[11]中建立铣削力模型的论述可定性推断本文的槽铣实验过程中铣削力在测力仪坐标系下的基本情况为:铣削力在y轴上的分量必为负值,在z轴上的分量必为正值.显然图5中的测量值符合该情况.4) 在槽切铣削过程中,由于刀具切入和切出工件时切削状态存在从无到有和从有到无的过程,因此铣削力应在切削开始阶段存在逐渐增大,切削结束阶段存在逐渐减小的情况.显然图5中的铣削力测量值在开始和结束阶段均存在逐渐变化过程.5) 由于测量系统中存在的随机干扰信号以及切削过程中的振动,使得测量的铣削力存在一定的局部波动,但铣削力信号远大于这些局部波动,因此测量铣削力的整体趋势并未受到影响,具有较高的可靠度.综合上述的分析和讨论,铣削力测量值具有较高的可信度,可代入辨识模型中进行铣削力系数辨识.但由于测量铣削力是工件所受作用力在测力仪坐标系下的分量,而辨识模型中的铣削力是刀具所受作用力在刀具坐标系下的分量,为此需根据坐标系之间的变换关系以及作用力和反作用力的原理将计算测量铣削力平均值的式(4)改写为(10)式中,为测力仪坐标系到刀具坐标系的旋转变换矩阵,可根据测力仪坐标系和刀具坐标系的位置关系直接得到(11)将各组测量铣削力分别代入式(10)中可计算出相应的平均铣削力如表3所示.表3 平均铣削力Table 3 Average of milling forces N序号FexFeyFez189.999810.004270.72322129.336012.504799.81593120.076738. 371388.42234194.254659.0185137.4547571.028442.930241.50226104.4495 61.981257.11077130.472472.250859.00208168.0017110.837480.7492935.3 10866.966821.52741047.217297.541429.329311100.1543109.194537.38061 2147.7859174.811253.3666表3为12组槽切铣削实验的平均铣削力,按照表中平均铣削力分量的个数,理论上可辨识得到36个系数,即剪切力系数的多项式可为10次多项式.但为了降低干扰和误差,保证辨识结果的精度,本文取剪切力系数为轴向位置角的4次多项式函数.至此,将实验数据代入辨识模型中可解得铣削力系数为式(12).2.4 铣削力系数辨识结果的实验验证为了验证文中铣削力系数辨识结果的正确性,可将辨识得到的铣削力系数用于多轴铣削的铣削力仿真预测中,同时进行相应的铣削实验,测量实际的铣削力,以实现定量地对比分析和判断.实验验证的铣削仍然以45号钢(硬度为32HRC)作为加工材料,以及直径为 8 mm 的钨钢球头铣刀(含涂层ALTiN,其详细参数如图1和表1所示)作为加工刀具.铣削方式为单向刀具轨迹,顺铣,主轴转速为1 194 r/min,进给速度为119.4 mm/min,切深为0.5 mm.为了考虑多轴铣削,特将工件设计为圆柱曲面,铣削过程以车铣复合的形式进行.由于进行车铣复合的铣削,涉及工作台的旋转,因此平板测力仪已不适用于铣削力的测量.鉴于此,本文选用Kistler 9123C1111压电测力平台对刀具所受的铣削力进行测量,测量过程中设定铣削力信号的采样频率为4 776 Hz.图6为实验中的工件、实验加工效果以及测力仪平台.(12)图6 多轴铣削实验Fig.6 A multi-axis milling experiment根据上述的铣削参数,将本章辨识得到的铣削力系数代入铣削力模型中,可计算得到铣削力的仿真预测值.将仿真预测值和实验测量值进行对比分析,其结果如图7所示. 图7为铣削加工时刀具所受作用力的仿真预测值和测量值在刀具坐标系下的分量.从图中可以看出,虽然铣削力的仿真预测值和实验测量值存在一定误差,但是在整体趋势上具有较高的吻合度.为了进一步定量比较两者之间的误差大小,可根据图7中的数据计算得到预测值和测量值之间的平均铣削力误差为:各轴分量的平均铣削力误差均在几N左右,其误差在合理范围之内.而且相比于文献[11]中基于瞬时铣削力的辨识结果,具有更好的抗干扰能力,提高了辨识结果精度.综合预测值和实验值的吻合度,以及平均铣削力的误差大小可以得出:通过本文建立的铣削力系数辨识模型及设计的铣削力系数辨识实验,可以得到具有较高精度和可靠性的铣削力系数,适用于球头铣刀多轴铣削加工的铣削力预测.图7 铣削力的仿真预测值和实验测量值Fig.7 Simulated and measured milling forces(a)—x方向的铣削力; (b)—y方向的铣削力; (c)—z方向的铣削力.3 结论1) 根据球头铣刀多轴铣削的整体铣削力模型,同时将剪切力系数考虑为切削刃微元点轴向位置角的多项式,建立了基于平均铣削力的铣削力系数辨识模型来提高辨识过程抗干扰能力和辨识精度,取得了良好的效果.2) 本文在设计铣削力系数辨识实验时,引入了铣削力倾斜角来保证在铣削力系数辨识实验过程中球面上的切削刃均能参与切削,从而进一步保证辨识得到的铣削力系数适用于球头铣刀多轴铣削的铣削力预测.3) 通过铣削力系数辨识实验,以及多轴铣削的铣削力仿真预测值和测量值的对比实验,验证了本文的铣削力系数辨识建模和实验研究的正确性和可靠性.同时,实验结果表明,本文的铣削力系数辨识方法适用球头铣刀多轴铣削加工的铣削力预测,具有较好的预测精度.参考文献:【相关文献】[1] Lee P,Altinta Y.Prediction of ball-end milling forces from orthogonal cuttingdata[J].International Journal of Machine Tools and Manufacture,1996,36(9):1059-1072. [2] Abainia S,Bey M,Moussaoui N,et al.Prediction of milling forces by integrating a geometric and a mechanistic model[C]//Proceedings of the World Congress on Engineering.London,2012:4-6.[3] Tuysuz O,Altintas Y,Feng H Y.Prediction of cutting forces in three and five-axis ball-end milling with tool indentation effect[J].International Journal of Machine Tools and Manufacture,2013,66:66-81.[4] Geng L,Liu P L,Liu K.Optimization of cutter posture based on cutting force prediction for five-axis machining with ball-end cutters[J].The International Journal of Advanced Manufacturing Technology,2015,78(5/6/7/8):1289-1303.[5] Altinta Y,Armarego E J A.Prediction of milling force coefficients from orthogonal cutting data[J].Transactions of the ASME,1996,118:216-224.[6] Gonzalo O,Beristain J,Jauregi H,et al.A method for the identification of the specific force coefficients for mechanistic milling simulation[J].International Journal of Machine Tools and Manufacture,2010,50(9):765-774.[7] Cao Q,Zhao J,Han S,et al.Force coefficients identification considering inclination angle for ball-end finish milling[J].Precision Engineering,2012,36(2):252-260.[8] Wang M,Gao L,Zheng Y.An examination of the fundamental mechanics of cutting force coefficients[J].International Journal of Machine Tools and Manufacture,2014,78:1-7. [9] Wojciechowski S.The estimation of cutting forces and specific force coefficients during finishing ball end milling of inclined surfaces[J].International Journal of Machine Tools and Manufacture,2015,89:110-123.[10] Dikshit M K,Puri A B,Maity A,et al.Determining cutting force coefficients from instantaneous cutting forces in ball end milling[J].International Journal of Machining and Machinability of Materials,2016,18(5/6):552-571.[11] 黎柏春,王振宇,王国勋,等.基于瞬时铣削力的球头铣刀铣削力系数辨识[J].东北大学学报(自然科学版),2016,37(5):678-682.(Li Bai-chun,Wang Zhen-yu,Wang Guo-xun,et ling force coefficient identification of ball-end milling based on instantaneous milling forces[J].Journal of Northeastern University(Natural Science),2016,37(5):678-682.)。
一种铣削力系数及偏心参数的标定方法

一种铣削力系数及偏心参数的标定方法铣削力系数及偏心参数是铣削加工中的重要参数,对于加工质量和效率有着重要的影响。
因此,准确地标定这些参数对于提高加工效率和质量至关重要。
一种常用的标定方法是利用力传感器和位移传感器进行实验测量。
首先,将工件夹紧在铣床上,然后在铣削过程中,通过力传感器测量铣削力的大小和方向,同时通过位移传感器测量铣削刀具的位置和偏心量。
根据测量结果,可以计算出铣削力系数和偏心参数。
具体地,铣削力系数可以通过以下公式计算:
Kc = F / (ap * ae * vf)
其中,Kc为铣削力系数,F为铣削力大小,ap为铣削刀具的轴向切削深度,ae为铣削刀具的径向切削深度,vf为铣削进给速度。
偏心参数可以通过以下公式计算:
E = e / D
其中,E为偏心参数,e为铣削刀具的偏心量,D为工件直径。
需要注意的是,在进行实验测量时,应该尽可能地减小误差,以保证测量结果的准确性。
例如,应该选择合适的传感器,保证其精度和灵敏度;同时,应该保证实验环境的稳定性,避免外界因素对测
量结果的影响。
铣削力系数及偏心参数的标定是铣削加工中的重要环节,通过合理的实验测量和计算,可以准确地确定这些参数,从而提高加工效率和质量。
铣削加工中的切削力监测技术

铣削加工中的切削力监测技术随着最近几年数字化制造技术的发展,越来越多的制造企业开始注重生产效率的提高和产品质量的稳定性,而切削力是这两个方面关键因素之一。
在铣削加工中,切削力大小以及方向的变化,会对加工质量和工具寿命产生重要影响。
因此,对于切削力的精确测量和监测,成为了铣削加工过程中的一项重要课题。
切削力是铣削加工中最基本的力学变量之一,它反映了加工材料的剪切特性、加工刀具的切削特性以及铣削刀具与工件之间的接触情况等因素。
因此,对于切削力的测量和监测,可以帮助企业优化生产工艺、提高加工效率以及减少加工成本。
同时,切削力的监测也可以帮助加工工人及时识别加工异常,及时采取相应的调整措施,从而保障加工质量和工具寿命。
目前,工业上常用的切削力测量方法主要是负载细胞法和应变测量法。
其中,负载细胞是用来测量物体重量或受力情况的传感器,通过安装在切削刀具或切削机床上进行力的测量,可以实现对切削力的监测。
而应变测量法则是通过在切削工具或工件上粘贴应变测量片,测量应变量的变化来反映切削力的大小。
这两种方法都具有优缺点,不能完全适用于所有的加工场景。
比如在高速加工和超高速加工场景中,切削力的变化非常快,传统的测量方法难以有效地监测。
因此,研究人员开始探索更加先进的切削力测量方法,以适应快速变化的切削力场景。
近年来,利用人工智能技术来解决切削力监测难题的研究也越来越火热。
利用深度学习技术,可以对切削参数和切削状态进行高效的识别和预测,从而实现对切削力的快速监测和控制。
例如,研究人员通过利用深度学习算法对超高速切削过程中切削力的预测模型进行优化,成功地解决了传统切削力测量方法难以适用于高速加工场景的问题。
这种基于智能算法的切削力监测方法,具有快速响应、精度高、数据处理能力强等优点,可以极大地提高加工效率以及加工质量的稳定性。
总之,切削力的监测对于铣削加工中生产效率和产品质量的提高具有重要作用。
目前,虽然已经有许多先进的切削力测量方法和监测技术被提出,但这项技术的研究和发展远未结束。
基于粒子群优化LS-SVM的车刀磨损量识别技术研究

小二乘支持向量机( L S — S V M) 的刀具磨损识别方法, 并针对支持向量机的惩罚 因子和核参数对模型识别精度影 响较大的问题 , 提 出一种根据个体适应度来调整惯性权重的 自适应粒子群算法进行 自 动参数寻优。以车削加工
为研 究对 象 , 采 集加 工过程 中的切 削 力信 号 , 应 用小波 包分析 技 术提 取 反 映刀 具磨 损状 态的特 征 信 息作 为 识 别 模型 的输入 , 然后利 用训 练好 的 自适应 粒子群 算 法优 化后 的 L S — S V M 识 别模 型进 行 刀具磨 损 量识 别 。 实验 结 果
表明, 该 自适应粒子群优化算法比标准粒子群优化算法参数寻优能力更强; 粒子群优化 L S — S V M模型能高效地
实现 刀具磨 损 量识别 , 与B P神经 网络相 比具 有更 高的精度 , 且所 需样本数 较 少 , 训 练速度 更快 。 关键 词 :刀具状 态监测 ;小波 包分析 ;粒子 群优化 ;最小二 乘支持 向量机
识别 技 术研 究 水
李威霖 ,傅 攀 ,张尔卿
( 西南交通 大 学‘ 机 械 工程 学院 ,成 都 6 1 0 0 3 1 ) 摘 要 :刀具 的磨 损状 态直接 影响 产品加 工质 量 、 成本和效率, 对 刀 具磨 损 量 的 实 时监 测识 别具 有 重要 意 义 。
针对 刀具磨 损状 态先验样 本 少和 常规 神经 网络识 别模 型收 敛速 度慢 、 易陷入 局部 极 小值 等 问题 , 提 出 了基 于最
v i e w o f t h e s e s i t u a t i o n s , i t p r o p o s e d a t o o l w e a r m o n i t o i r n g m e t h o d b a s e d o n l e a s t s q u a r e s s u p p o t r v e c t o r m a c h i n e( L S — S V M) . M e a n w h i l e , i t p r o p o s e d t h e a d a p t i v e p a r t i c l e s w a r m o p t i m i z a t i o n( A P S O) a l g o i r t h m t o s e a r c h o p t i mu m v a l u e o f t h e k e r n e l f u n c —
基于铣削力与稳定性预测的铣削工艺参数优化
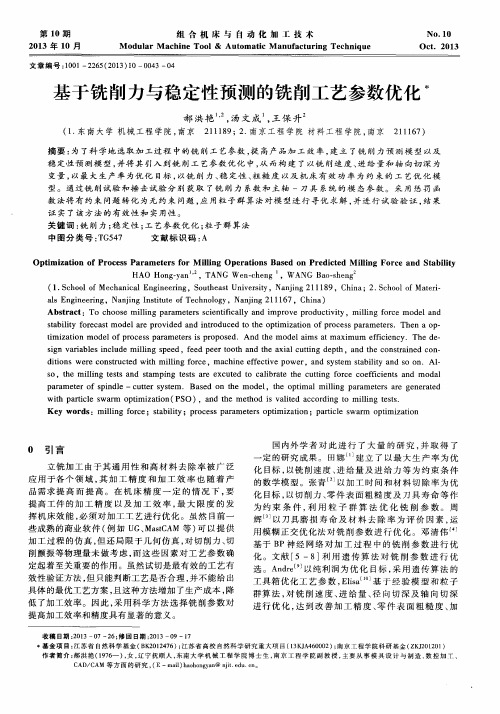
型 。 通 过 铣 削 试 验 和 捶 击 试 验 分 别 获 取 了 铣 削 力 系数 和 主 轴 一刀 具 系 统 的 模 态 参 数 。 采 用 惩 罚 函
数 法将有 约 束 问题 转 化 为无约 束 问题 , 应 用粒子 群 算法 对模 型进 行 寻优 求解 , 并进 行 试验 验 证 , 结 果
周铣加工铣削力模型分析讲解

编号南京航空航天大学毕业设计题目周铣加工铣削力模型分析学生姓名罗金禄学号050430322学院机电学院专业飞行器制造工程班级0504303指导教师庄海军副教授二〇〇八年六月南京航空航天大学本科毕业设计(论文)诚信承诺书本人郑重声明:所呈交的毕业设计(论文)(题目:周铣加工铣削力模型分析)是本人在导师的指导下独立进行研究所取得的成果。
尽本人所知,除了毕业设计(论文)中特别加以标注引用的内容外,本毕业设计(论文)不包含任何其他个人或集体已经发表或撰写的成果作品。
作者签名:年月日(学号):周铣加工铣削力模型分析摘要切削力建模是数控加工物理仿真的基础。
本文主要研究周铣加工中曲率对铣削力的影响,初步建立基于曲率变化的切削力模型。
在周铣加工中,工件不同的曲率处会有不同的加工误差。
研究曲率变化对切削力的影响,对研究复杂零件的加工误差、加工误差补偿策略、关键工艺参数优化以及加工过程的物理仿真具有重要的理论意义。
本文采用数学解析建模的方法进行切削力建模,即分析圆周铣削过程中刀具与工件的几何模型,利用各个参数之间的关系,推导出了切削面积的计算公式,进而得出了切削力与工件曲率的关系式,初步分析了曲率变化对主铣削力的影响,为后续研究提供了一定的参考和帮助。
关键词:周铣加工,工件曲率,几何模型,铣削力模型Analysis On the Cutting Force Model in Peripheral MillingAbstractCutting force modeling is the basis of NC machining physical simulation. The cutting force model based on the curvature in peripheral milling was researched and established in this paper. The machining error varied due to the different curvature in the peripheral milling. Moreover, it has important theoretical value for the research on the machining error , the compensation strategy for the machining error, the optimization of the machining parameters and the NC machining physical simulation to establish the cutting force model. The cutting force model was established by analytical/numerical approach, in which the geometrical relationship between the tool and the workpiece in peripheral milling was analyzed, the expression between the cutting force and the curvature was deduced by calculating the cutting area. The effect of curvature variation on tangential cutting force was initially analyzed. The research achievement is meaningful for the future research.Key Words:Peripheral milling; Workpiece curvature; Geometry model; Cutting force model目录摘要 (ⅰ)Abstract (ⅱ)图表清单 (ⅳ)第一章引言 (1)第二章铣削力建模概述 (4)2.1 经验公式模型 (4)2.2 有限元分析模型 (4)2.3 神经网络模型 (5)2.4 数学分析模型 (6)2.5 周铣铣削力的数学分析建模 (7)第三章周铣加工铣削力建模过程 (9)3.1 坐标系及相关参数定义 (9)3.2 圆周铣削几何模型 (10)3.2.1 工件凸表面 (10)3.2.2 工件凹表面 (11)3.3 瞬时切削厚度与刀齿接触面积 (13)3.4 铣削力模型 (17)3.5 曲率影响分析 (18)第四章总结与展望 (20)4.1 全文总结 (20)4.2 今后工作展望 (20)参考文献 (22)致谢 (24)图表清单图2.1 (6)图2.2 (6)图3.1 (9)图3.2 (10)图3.3 (10)图3.4 (12)图3.5 (14)图3.6 (14)图3.7 (15)图3.8 (16)图3.9 (17)第一章引言机械加工中的切削过程是一个很复杂的多因素过程。
- 1、下载文档前请自行甄别文档内容的完整性,平台不提供额外的编辑、内容补充、找答案等附加服务。
- 2、"仅部分预览"的文档,不可在线预览部分如存在完整性等问题,可反馈申请退款(可完整预览的文档不适用该条件!)。
- 3、如文档侵犯您的权益,请联系客服反馈,我们会尽快为您处理(人工客服工作时间:9:00-18:30)。
基 本一致 。
关键 词 : 时铣 削力 ; 元铣削刃 ; 削力 系数 辨识 ; 瞬 微 铣 粒子群 【 b ta t oo ti a c uaeis na eu iig oc oe, ii freo e e t d ei A src 】T ba nac rt nt tno sm ln f rem d l m ln o c e m n e g s n a l lg f l
W ANG o se g, Z in mi1W ANG -a Ba — h n 1 UO Ja — n , 2 Mu ln
( c ol f c a i l n ier gJ n s nvri ,h ni g 0 , hn ) h o o hnc gn ei , a guU iesy Z ej n 1 C ia S Me aE n i t a 2 1 2 3 ( c ol f t i s nier g N nigIs tt o T cn lg , aj g2 16 , hn ) 2 h o o e a g ei , aj tue f eh o y N ni 1 1 7 C ia S Ma r l E n n n ni o n
aa zd adam dls s b se.cod gt t hr t ii n - ii , m to r oe nl e , oe i e alhd cri e a c r tsfed m l ga e dipo sd y n t i A n o h c a e sc o l h s p n tjde ht r l n mln ii tada p c c om l ig e.n h ai a o ug w e e a e m t ii e im l g r o n sei fr u i n ebs , r h e l g @e s l o n , n e n f as v O t s t is naeu iig oc oefr n - iigidvl e cuigteserfet n luheet nt tnosmln frem dl d mln eeo di ldn ha fc dpog fc a l o e l s p n h e a f .
( ins e aoa r A vn e u r a C nrl eh ooy N ni 1 6 7 C ia 3 a guK yL b rt yo da cdN mei l o t c n lg , aj g2 1 1 , hn ) j o f c oT n
【 摘
要】 建立了微元铣削力模型。依据
第 3期
21 0 2年 3月
文 章 编 号 :0 1 39 (0 2 0 — 0 3 0 10 — 9 7 2 1 )3 0 6 — 3
机 械 设 计 与 制 造
Ma h n r De i n c iey sg & Ma u a t r n f cu e 6 3
瞬 时铣 削力建模与铣 削力 系数 的粒子群 法辨识 冰
立铣h_ 的特点 , 出了 T - 提 微元铣削刃参与铣 削的判断方法, 出了具体的计算公式。在此基础上 , 给 建立
了包含剪切效应和犁入效应的瞬时铣 削力模型。利用粒子群算法收敛速度快的优点, 出了基于粒子 提
群的单位铣削力系数辨识方法, 出了算法的实现步骤。铣削试验结果表明, 给 该方法能够精确辨识出单
r usso a tem to a etytemln frece cetcua lPeie ausui e e h hwtt h ehdcni ni ii o c of i cr e .rdc dv e sn t s h d f h lg f na t y i t l gh
王保升 1 左健 民 汪木 兰 , 2
(江苏大学 机械 工程 学院 , 镇江 2 2 1 )(南京 工程学 院 材料学 院 , 京 2 16 ) 10 3 南 1 7 1 (先 进数控技 术江苏省 高校重点 建设实验 室 , s 南京 2 11 ) 167
l s a t n o s miig f r e mo eig a d c e f in e t ia in t n a e u ln o c d l n o fi e ti n ic t n l n c d f o b s d o a t l wa m p i z t n a e n p r ce s r o t i mia i o
po oe s na e u ii f rem d l r a s t a e ue a e. r sdi t t o m ln oc e el th smea m a rdv u s p na n s lg o a mo e s s l
T kn t acu th S grh d a t e of t o v rec , o fc n e t ct nm to a i i o c o n teP O a oi m a v a s f a n egn e ac e i t d ni a o eh d gn l t n g s c f e i f i i i b e n t g rh r ln rei pee td oteip e na o t saegvnMii s s a do ea oi mf l g c rsne .l , m l t ins p e. ln t t h l t o mii f o s As h e m t e r i lg e