液压传动课程设计-液压系统设计举例
液压传动课程设计-卧式单面多轴钻孔组合机床动力滑台的液压系统
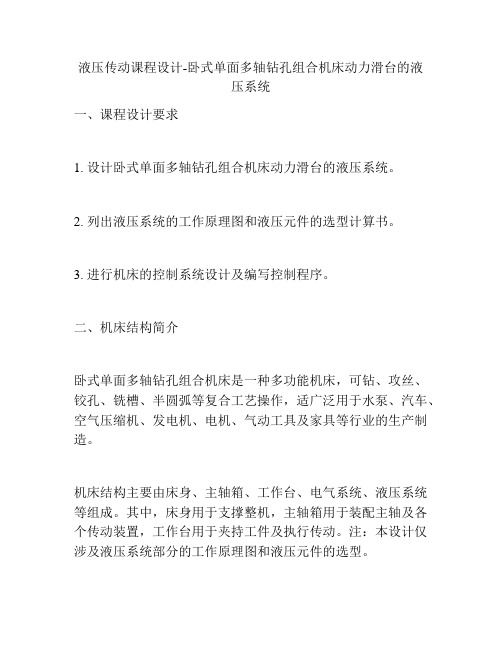
液压传动课程设计-卧式单面多轴钻孔组合机床动力滑台的液压系统一、课程设计要求1. 设计卧式单面多轴钻孔组合机床动力滑台的液压系统。
2. 列出液压系统的工作原理图和液压元件的选型计算书。
3. 进行机床的控制系统设计及编写控制程序。
二、机床结构简介卧式单面多轴钻孔组合机床是一种多功能机床,可钻、攻丝、铰孔、铣槽、半圆弧等复合工艺操作,适广泛用于水泵、汽车、空气压缩机、发电机、电机、气动工具及家具等行业的生产制造。
机床结构主要由床身、主轴箱、工作台、电气系统、液压系统等组成。
其中,床身用于支撑整机,主轴箱用于装配主轴及各个传动装置,工作台用于夹持工件及执行传动。
注:本设计仅涉及液压系统部分的工作原理图和液压元件的选型。
三、液压系统工作原理图液压系统主要用于机床的升降、夹紧、进给等控制操作。
下面的工作原理图展示了该机床的主要液压系统结构。
液压油泵为双联泵,分别提供高压和低压液压油,高压系统主要用于机床的动力传输和工作台的升降,低压系统则用于工作台和主轴箱的夹持、进给和径向递进。
四、液压元件的选型计算本文中设计的液压系统主要包括液压油泵、液压缸、液压阀、液压滤清器、液压压力表等液压元件。
针对所需控制的液压作用,根据相应的公式和数据手册,进行液压元件的选型计算。
液压元件选型计算书如下:五、控制系统设计本设计中,机床的控制系统主要由PLC控制器、触摸屏、传感器、执行器和电磁阀等组成,通过编写相应的控制程序,实现机床的高效稳定运行。
液压系统的控制程序中主要包括如下控制命令:1. 单向液压缸的伸出和缩回控制命令。
2. 双向液压缸的伸出和缩回控制命令。
3. 液压油泵的控制启停命令。
4. 电磁阀的开关控制命令。
5. 液压滤清器的定期清洗命令。
通过不同的控制命令组合,可以实现机床的不同运动状态和操作需求,从而提高机床的生产效率和工作质量。
六、总结本文对卧式单面多轴钻孔组合机床动力滑台的液压系统进行了详细介绍,并给出了液压系统的工作原理图和液压元件的选型计算书,同时简要讲述了机床的控制系统设计流程和控制命令。
液压传动系统设计计算例题
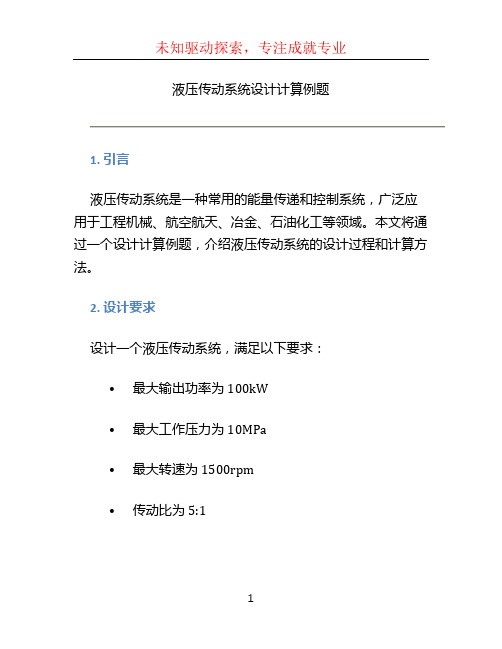
液压传动系统设计计算例题1. 引言液压传动系统是一种常用的能量传递和控制系统,广泛应用于工程机械、航空航天、冶金、石油化工等领域。
本文将通过一个设计计算例题,介绍液压传动系统的设计过程和计算方法。
2. 设计要求设计一个液压传动系统,满足以下要求:•最大输出功率为100kW•最大工作压力为10MPa•最大转速为1500rpm•传动比为5:13. 功率计算根据设计要求,最大输出功率为100kW,转速为1500rpm,可以通过以下公式计算液压机的排量:功率(kW)= 排量(cm^3/rev) × 转速(rpm) × 压力(MPa) × 10^-6由于传动比为5:1,液压泵的排量为液压马达的5倍,因此液压泵的排量为:排量(cm^3/rev) = 功率(kW) / (转速(rpm) × 压力(MPa) × 10^-6 × 5)= 100 / (1500 × 10 × 10^-6 × 5)= 0.133 cm^3/rev4. 泵和马达的选择根据计算结果,液压泵的排量为0.133 cm^3/rev。
在实际中,可以选择一个接近或等于该排量的标准泵来满足需求。
假设我们选择了一台0.15 cm^3/rev的液压泵。
由于传动比为5:1,液压马达的排量为液压泵的1/5,因此液压马达的排量为:排量(cm^3/rev) = 液压泵排量 / 5= 0.15 / 5= 0.03 cm^3/rev同样地,我们可以选择一个接近或等于该排量的标准马达。
5. 油液流量计算油液流量可以通过以下公式计算:流量(L/min) = 排量(cm^3/rev) × 转速(rpm) / 1000液压泵的流量为:流量(L/min) = 0.15 × 1500 / 1000= 0.225 L/min液压马达的流量为:流量(L/min) = 0.03 × 1500 / 1000= 0.045 L/min6. 液压系统元件选择在设计液压传动系统时,除了液压泵和液压马达,还需要选择其他的液压元件,如油箱、油管、阀门等。
液压系统的设计计算举例
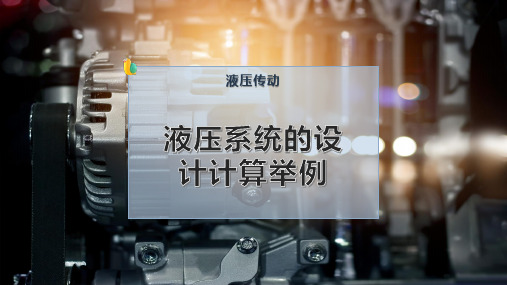
作缸的小腔,即从泵的出口到缸小腔之间的压力损失 Δp = 5.5×105 MPa ,于是小泵出
口压力 pp1 = 21.56×105 MPa (小泵的总效率 η 1 = 0.5 ),大泵出口压力 pp2 =
23.06×105 MPa (大泵的总效率 η 2 = 0.5 )。故电机功率为
P pp1q1 pp2q2 21.56 105 0.167 103 W 23.06 105 0.267 103 W 1 951.5 W
= 0.5 ,大泵出口压力 pp2 = 15.18×105 MPa (大泵的总效率 η 2 = 0.5 )。故电机功率
为
P1
pp1q1 1
pp 2 q2 2
13.68 105 0.167 103 0.5
W 15.18 105 0.267 103 0.5
W
1 267.5 W
(2)工进
小泵的出口压力 pp1 = p1 +Δp1 = 32.19×105 MPa ,大泵卸载,卸载压力取 pp2 =
液压传动
液压系统的设计计算举例
1.1 分析工况及主机工作要求,拟定液压系统方案 1.2 参数设计 1.3 选择元件 1.4 液压系统性能验算
液压系统的设计计算举例
1.1 液分析工况及主机工作要求,拟定液压系统方案
(一) 确定执行元件类型
(二) 确定执行元件的负载、速度变化范围
Fw 18 000 N
1
2
0.5
0.5
综合比较,快退时所需功率最大。据此查产品样本选用Y112M—6型异步电机,
电机功率2.2 kW,额定转速为940 r/min。
(三) 选择液压阀
根据液压阀在系统中的最高工作压力与通过该阀的最大流量,可选出这些元件的 型号及规格。选定的元件列于表中。
液压与气压传动课程设计
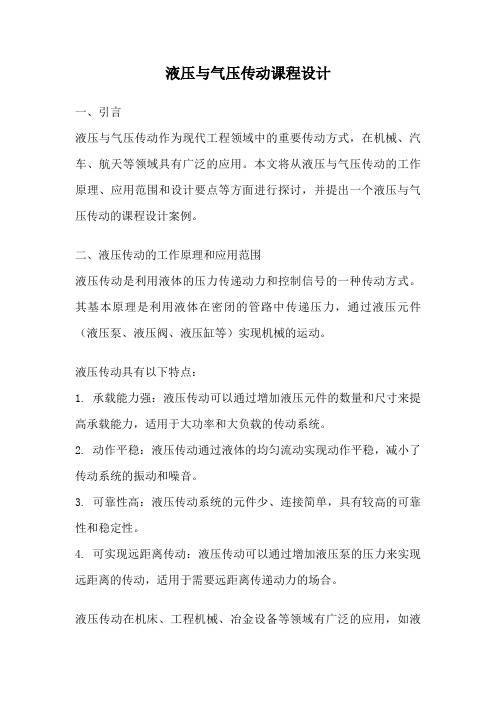
液压与气压传动课程设计一、引言液压与气压传动作为现代工程领域中的重要传动方式,在机械、汽车、航天等领域具有广泛的应用。
本文将从液压与气压传动的工作原理、应用范围和设计要点等方面进行探讨,并提出一个液压与气压传动的课程设计案例。
二、液压传动的工作原理和应用范围液压传动是利用液体的压力传递动力和控制信号的一种传动方式。
其基本原理是利用液体在密闭的管路中传递压力,通过液压元件(液压泵、液压阀、液压缸等)实现机械的运动。
液压传动具有以下特点:1. 承载能力强:液压传动可以通过增加液压元件的数量和尺寸来提高承载能力,适用于大功率和大负载的传动系统。
2. 动作平稳:液压传动通过液体的均匀流动实现动作平稳,减小了传动系统的振动和噪音。
3. 可靠性高:液压传动系统的元件少、连接简单,具有较高的可靠性和稳定性。
4. 可实现远距离传动:液压传动可以通过增加液压泵的压力来实现远距离的传动,适用于需要远距离传递动力的场合。
液压传动在机床、工程机械、冶金设备等领域有广泛的应用,如液压机、液压切割机、液压挖掘机等。
三、气压传动的工作原理和应用范围气压传动是利用气体的压缩和膨胀实现动力传递和控制的一种传动方式。
其基本原理是通过压缩机将气体压缩为高压气体,然后通过气缸或气动执行元件实现机械的运动。
气压传动具有以下特点:1. 压力范围广:气压传动可以实现较高的工作压力,一般可达到10MPa以上,适用于需要较大工作压力的场合。
2. 反应速度快:气压传动的工作介质是气体,其压缩和膨胀的速度比液体快,因此气压传动的反应速度更快。
3. 安全性高:气压传动的工作介质是气体,不易泄漏,因此具有较高的安全性。
4. 环保节能:气体是可再生资源,气压传动具有较低的能耗和较小的环境污染。
气压传动在自动化生产线、工件夹持、物料搬运等领域有广泛的应用,如气动机械手、气动钳工装等。
四、液压与气压传动课程设计案例本文提出一个液压与气压传动的课程设计案例,旨在帮助学生更好地理解和掌握液压与气压传动的原理和应用。
上料机液压课程设计附带图纸
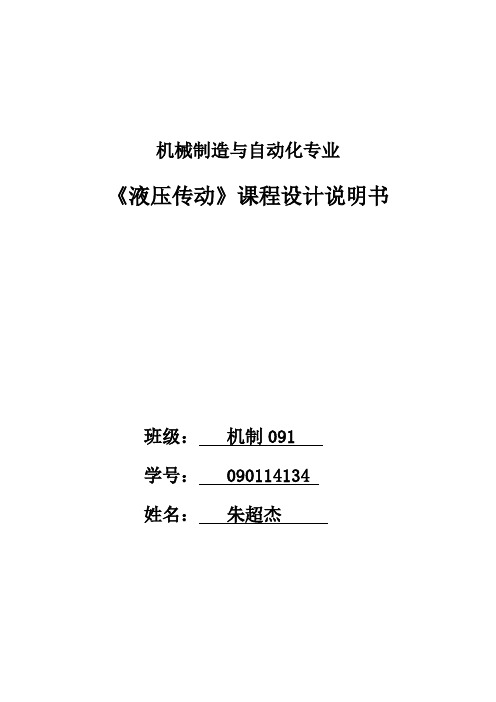
机械制造与自动化专业《液压传动》课程设计说明书班级:机制091学号: *********姓名:***目录1.工况分析及参数确定 (2)1.1工况分析 (2)1.2参数确定 (4)2.液压系统原理图的拟定 (6)3.液压缸结构设计 (8)4.参考文献 (10)5.设计总结 (10)液压课程设计题目题目:设计一台上料机液压系统,要求该系统完成:快速上升——慢速上升(可调速)——快速下降——下位停止的半自动循环。
采用900V型导轨,垂直于导轨的压紧力为60N,启动、制动时间均为0.5s,液压缸的机械效率为0.9。
设计原始数据如下表所示。
试完成以下工作:1、进行工况分析,绘制工况图。
2、拟定液压系统原理图(A3)。
3、计算液压系统,选择标准液压元件。
4、绘制液压缸装配图(A3)5、编写液压课程设计说明书。
上料机示意图如下:1.工况分析及参数确定1.1工况分析液压系统的工况分析是指对液压系统执行元件的工作情况分析,以了解工作过程中执行元件在各个工作阶段中的流量、压力和功率的变化规律,并将其用曲线表示出来,作为确定液压系统主要参数,拟定液压系统方案的依据。
1.运动分析根据各执行元件在一个工作循环内各阶段的速度,绘制其循环图,如下图所示:2.负载分析(1)工作负载:L F =Fg=1000N+5000N=6000N(2)摩擦负载:2sin ∂=Nf fF F F N --运动部件及外负载对支撑面的正压力(N );f --摩擦系数,分为静摩擦系数(f=0.2-0.3)和动摩擦系数(f=0.05-0.1) α——V 形导轨的夹角,这里为90度。
由于工件为垂直起升,所以垂直于导轨的载荷由上可知F N =60N 取0.2,0.1,d fs f == 则有 静摩擦负载:F fs 0.26016.97sin 45N 动摩擦负载:F fd0.1608.49sin 45N(3)惯性负载:惯性负载F a 是由运动部件的速度变化所引起的,可根据牛顿第二定律确定,即 F a =ma=G v X g t G---运动部件的重力(N ) g---重力加速度,29.8mgs△v---速度变化值(s m )△t---速度变化所需时间(s )加速:F a160000.04555.109.80.5G v N g t减速:F a260000.0450.01339.189.80.5G v N g t制动:F a3 60000.01315.919.80.5G v N gt反向加速:F a460000.05567.359.80.5G v N g t下拉制动:F a5467.35a G v F N gt根据以上的计算,考虑到液压缸垂直安放,其重量较大,为防止因自重而自行下滑,系统中应设置平衡回路,因此,在对快速向下运动的负载分析时,就不考虑滑台的重量,则液压缸各阶段中的负载,如下表fs L F F 1fd L a F F F 6063.59fd L F F 6008.492fd L a F F F 5969.31fdL F F6008.493fd L a F F F 5992.584fd a F F75.84 fd F 8.495fda F F-58.861.2参数的确定液压缸工作压力主要根据运动循环各阶段的最大总负载来确定,此外,还需要考虑一下因素:(1)各类设备的不同特点和使用场合(2)考虑经济和重量因素,压力选得低,则元件尺寸大,重量重,压力选得高一些,则元件尺寸小,重量轻,但对元件的制造精度,密封性能要求高。
液压与气压传动液压系统设计实例
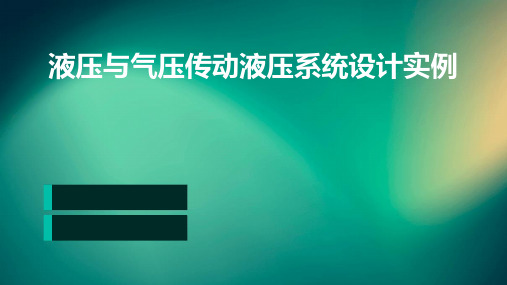
根据系统的工作环境和要求,选择合适的液压介质,如矿 物油、合成油、水等,并确定其清洁度和粘度等参数。
选择合适元件和连接方式
01
选择液压泵和液压马达
根据系统的负载和运动参数,选择合适的液压泵和液压马达,确保其能
够提供足够的流量和压力,并满足系统的效率和精度要求。
02
选择液压缸和阀门
其他常见问题及相应解决方案
气穴现象
产生原因是油液中溶解的气体在低压区析出并形成气泡。解决方案 是减小吸油管路的阻力,避免产生局部低压区。
压力冲击
产生原因是液压阀突然关闭或换向,导致系统内压力急剧变化。解 决方案是在液压阀前设置蓄能器或缓冲装置,吸收压力冲击。
爬行现象
产生原因是液压缸或马达摩擦阻力不均、油液污染等。解决方案是改 善液压缸或马达的润滑条件,使用干净的油液。
关键技术应用
节能环保措施
采用负载敏感技术、电液比例控制技术等 ,提高挖掘机液压系统的控制精度和响应 速度。
通过优化系统设计和选用高效节能元件,降 低挖掘机液压系统的能耗和排放,提高环保 性能。
压力机液压系统性能评估方法论述
评估方法介绍
采用实验测试、仿真分析等方法对压力机 液压系统进行性能评估,获取系统在不同
明确系统的设计目标和约束条件
根据实际需求,明确系统的设计目标,如高效率、 低能耗、高精度等,并考虑成本、空间、重量等 约束条件。
确定系统方案和布局
制定系统原理图
根据设计要求和目标,制定液压系统的原理图,包括液压 缸、液压马达、液压泵、油箱、阀门等元件的连接方式和 控制逻辑。
确定系统布局和安装方式
根据机械设备的结构和空间要求,确定液压系统的布局和 安装方式,包括元件的布置、管路的走向和固定方式等。
液压传动课程设计

【液压传动课程设计说明书设计题目:半自动液压专用铣床液压系统[工程技术系机械设计制造及其自动化4班。
设计者指导教师2016 年 12 月 1 日摘要、液压系统设计计算是液压传动课程设计的主要内容,包括明确设计要求进行工况分析、确定液压系统主要参数、拟定液压系统原理图、计算和选择液压件以及验算液压系统性能等。
现以半自动液压专用铣床液压系统为例,介绍液压系统的设计计算方法。
设计一台多用途大台面液压机液压系统,适用于可塑材料的压制工艺,如冲压、弯曲翻边、落板拉伸等。
要求该机的控制方式:用按钮集中控制,可实现调整,手动和半自动,自动控制。
要求该机的工作压力、压制速度、空载快速下行和减速的行程范围均可根据工艺要求进行调整。
主缸工作循环为:快降、工作行程、保压、回程、空悬。
顶出缸工作循环为:顶出、顶出回程(或浮动压边)。
关键字:液压; 快进; 工进; 快退{前言本课程是机械设计制造及其自动化专业的主要专业基础课和必修课,是在完成《液压与气压传动》课程理论教学以后所进行的重要实践教学环节。
本课程的学习目的在于使学生综合运用《液压与气压传动》课程及其它先修课程的理论知识和生产实际知识,进行液压传动的设计实践,使理论知识和生产实际知识紧密结合起来,从而使这些知识得到进一步的巩固、加深和扩展。
通过设计实际训练,为后续专业课的学习、毕业设计及解决工程问题打下良好的基础。
,(1) 液压传动课程设计是一项全面的设计训练,它不仅可以巩固所学的理论知识,也可以为以后的设计工作打好基础。
在设计过程中必须严肃认真,刻苦钻研,一丝不苟,精益求精。
(2) 液压传动课程设计应在教师指导下独立完成。
教师的指导作用是指明设计思路,启发学生独立思考,解答疑难问题,按设计进度进行阶段审查,学生必须发挥主观能动性,积极思考问题,而不应被动地依赖教师查资料、给数据、定方案。
(3) 设计中要正确处理参考已有资料与创新的关系。
任何设计都不能凭空想象出来,利用已有资料可以避免许多重复工作,加快设计进程,同时也是提高设计质量的保证。
液压与气压传动课程设计-设计一台专用铣床液压系统大学论文

液压与气压传动课程设计说明书专业:机械设计制造及其自动化班级: 13机二学号:姓名:指导教师:常州工学院机械与车辆工程学院2016年1月8日前言液压传动是用液体作为来传递能量的,液压传动有以下优点:易于获得较大的力或力矩,功率重量比大,易于实现往复运动,易于实现较大范围的无级变速,传递运动平稳,可实现快速而且无冲击,与机械传动相比易于布局和操纵,易于防止过载事故,自动润滑、元件寿命较长,易于实现标准化、系列化。
液压传动的基本目的就是用液压介质来传递能量,而液压介质的能量是由其所具有的压力及力流量来表现的。
而所有的基本回路的作用就是控制液压介质的压力和流量,因此液压基本回路的作用就是三个方面:控制压力、控制流量的大小、控制流动的方向。
所以基本回路可以按照这三方面的作用而分成三大类:压力控制回路、流量控制回路、方向控制回路。
液压传动与机械传动,电气传动为当代三大传动形式,是现代发展起来的一门新技术。
《液压与气压传动》课是工科机械类专业的重点课程之一。
既有理论知识学习,又有实际技能训练。
为此,在教学中安排一至二周的课程设计。
该课程设计的目的是:1、综合运用液压传动及其它先修课程的理论知识和生产实际知识,进行液压传动设计实践,从而使这些知识得到进一步的巩固,加深和发展。
2、熟悉和掌握拟定液压传动系统图,液压缸结构设计,液压元件选择以及液压系统的计算的方法。
3、通过课程设计,提高设计、计算、绘图的基本技能,熟悉设计资料和技术手册,培养独立分析问题和解决问题的能力,为今后毕业设计及设计工作打下必要的基础。
目录一任务书 (5)二液压系统设计步骤 (6)1 液压系统的工况分析 (6)2 拟定液压系统原理图 (8)3 液压系统的计算和选择液压元件 (14)3.1 液压缸主要参数的计算 (14)3.2 液压泵的流量、压力的计算和选择泵的规 (17)3.3 液压阀的选择 (19)3.4 确定管道尺寸 (20)3.5 液压油箱容积的确定 (21)4 液压系统验算及技术文件的编制 (22)4.1 压力损失验算和压力阀的调整压力 (22)4.2 系统温升的验算 (25)5 绘制工作图,编制技术文件 (27)三设计体会 (28)四参考文献30任务书设计课题:设计一台专用铣床液压系统。
- 1、下载文档前请自行甄别文档内容的完整性,平台不提供额外的编辑、内容补充、找答案等附加服务。
- 2、"仅部分预览"的文档,不可在线预览部分如存在完整性等问题,可反馈申请退款(可完整预览的文档不适用该条件!)。
- 3、如文档侵犯您的权益,请联系客服反馈,我们会尽快为您处理(人工客服工作时间:9:00-18:30)。
液压系统设计计算举例液压系统设计计算是液压传动课程设计的主要内容,包括明确设计要求进行工况分析、确定液压系统主要参数、拟定液压系统原理图、计算和选择液压件以及验算液压系统性能等。
现以一台卧式单面多轴钻孔组合机床动力滑台液压系统为例,介绍液压系统的设计计算方法。
1设计要求及工况分析1.1设计要求要求设计的动力滑台实现的工作循环是:快进工进快退停止。
主要性能参数与性能要求如下:切削阻力F L=30468N ;运动部件所受重力G=9800N ;快进、快退速度 1 = 3=0.1m/s,工进速度2=0.88 x 10-3m/s ;快进行程L1=100mm,工进行程L2=50mm ;往复运动的加速时间A t=0.2s;动力滑台米用平导轨,静摩擦系数ps=0.2,动摩擦系数屈=0.1。
液压系统执行元件选为液压缸。
1.2负载与运动分析(1) 工作负载工作负载即为切削阻力F L=30468N。
(2) 摩擦负载摩擦负载即为导轨的摩擦阻力:静摩擦阻力F fssG0.298001960 N动摩擦阻力F fd d G0.19800980N(3)惯性负载G98000 11N 500 Ni g t9.80.2(4)运动时间t1L1100;1s快进10.1L250 10 3t22s 56.8s 工进20.88 10t3L1L2(100350) 10s 1.5s快退30.1设液压缸的机械效率n m=0.9,得出液压缸在各工作阶段的负载和推力,如表1所列。
表1工况负载组成液压缸负载F/N液压缸推力F0=F/ n cm/N 启动 F F fs19602180力口速 F F fd F i14801650快进F F fd9801090工进 F F fd F L3144834942反向启动 F F fs19602180力口速 F F fd F i14801650快退F F fd9801090根据液压缸在上述各阶段内的负载和运动时间,即负载/KN<55~1010~2020~3030~50>50工作压力/MPa<0.8〜1 1.5~2 2.5~33~44~5> 5表3机械类型机床农业机械小型工程机械建筑机械液压凿岩机液压机大中型挖掘机重型机械起重运输机械磨床组合机床龙门刨床拉床工作压力/MPa0.8~23~52~88~1010~1820~32 11/1〉0.4”可绘制出负载循环图F-t和速度循环图-t,如图1所示。
2确定液压系统主要参数2.1初选液压缸工作压力所设计的动力滑台在工进时负载最大,在其它工况负载都不太高,参考表2和表3,初选液压缸的工作压力P i=4MPa。
2.2计算液压缸主要尺寸鉴于动力滑台快进和快退速度相等,这里的液压缸可选用单活塞杆式差动液压缸(A i=2A2),快进时液压缸差动连接。
工进时为防止孔钻通时负载突然消失发生前冲现象,液压缸的回油腔应有背压,参考表4选此背压为P2=0.6MPa。
J.-图如表7所列,由此绘制的液压缸工况图如图2所示。
表4系统类型背压力/MPa 简单系统或轻载节流调速系统 0.2~0.5 回油路带调速阀的系统 0.4〜0.6 回油路设置有背压阀的系统 0.5~1.5 用补油泵的闭式回路 0.8~1.5 回油路较复杂的工程机械 1.2~3 回油路较短且直接回油可忽略不计表5工作压力/MPa< 5.0 5.0~7.0 > 7.0 d/D0.5~0.550.62~0.700.7表62/ 11.15 1.25 1.33 1.46 1.61 2 d/D0.30.40.50.550.620.71注:’2—有杆腔进油时活塞运动速度参考表5及表6,得d 0.71D =77mm ,圆整后取标准数值得D=110mm , d=80mm 。
由此求得液压缸两腔的实际有效面积为2 2 2 242d )(0.11 0.8 )m 44.7 10 m4可估算出液压缸在工作循环中各阶段的压力、流量和功率,由式 得piA 1p2A 2cm则活塞直径31448 0.9 (42——m 1064 294 10 m4 94 100.109m 109mmA 1D 2 40.112 2 ------- m 44 2 95 10 4 m 2A 2严2根据计算出的液压缸的尺寸,工况推力F0/N 回油腔压力p2/MPa进油腔压力p1/MPa输入流量q x 10-3/m3/s输入功率P/KW计算公式启动2180—0.43——F0 A Pp1 ~A~快进加速1650p1+A p0.77——q (A AD 1 P P2恒速1090p1+A p0.660.50.33工进349420.6 3.960.84 X 10-20.033Fp2A2 P1 —A T"q A 2P P2启动2180—0.49——Fp2 A1P1 —KT快退加速16500.5 1.43——q A2 3P P2恒速10900.5 1.310.450.59注:1. p为液压缸差动连接时,回油口到进油口之间的压力损失,取侔=0.5MPa。
2.快退时,液压缸有杆腔进油,压力为p i,无杆腔回油,压力为P2。
3拟定液压系统原理图3.1选择基本回路(1) 选择调速回路由图2可知,这台机床液压系统功率较小,滑台运动速度低,工作负载为阻力负载且工作中变化小,故可选用进口节流调速回路。
为防止孔钻通时负载突然消失引起运动部件前冲,在回油路上加背压阀。
由于系统选用节流调速方式,系统必然为开式循环系统。
(2) 选择油源形式从工况图可以清楚看出,在工作循环内,液压缸要求油源提供快进、快退行程的低压大流量和工进行程的高压小流量的油液。
最大流量与取小流量之比q max/q min=0.5/(0.84 X 10-2) 60 ;其相应的时间之比(t1+t3)/t2=(1+1.5)/56.8=0.044。
这表明在一个工作循环中的大部分时间都处于高压小流量工作。
从提高系统效率、节省能量角度来看,选用单定量泵油源显然是不合理的,为此可选用限压式变量泵或双联叶片泵作为油源。
考虑到前者流量突变时液压冲击较大,工作平稳性差,且后者可双泵同时向液压缸供油实现快速运动,最后确定选用双联叶片泵方案,如图2a所示。
(3) 选择快速运动和换向回路本系统已选定液压缸差动连接和双泵供油两种快速运动回路实现快速运动。
考虑到从工进转快退时回油路流量较大,故选用换向时间可调的电液换向阀式换向回路,以减小液压冲击。
由于要实现液压缸差动连接,所以选用三位五通电液换向阀,如图2b所示。
(4) 选择速度换接回路由于本系统滑台由快进转为工进时,速度变化大 (1/ 2=0.1/(0.88 X 10-3) 114),为减少速度换接时的液压冲击,选用行程阀控制的换接回路,如图2c所示。
(5) 选择调压和卸荷回路在双泵供油的油源形式确定后,调压和卸荷问题都已基本解决。
即滑台工进时,高压小流量泵的出口压力由油源中的溢流阀调定,无需另设调压回路。
在滑台工进和停止时,低压大流量泵通过液控顺序阀卸荷,高压小流量泵在滑台停止时虽未卸荷,但功率损失较小,故可不需再设卸荷回路。
将上面选出的液压基本回路组合在一起,并经修改和完善,就可得到完整的液压系统工作原理图,如图3所示。
在图3中,为了解决滑台工进时进、回油路串通使系统压力无法建立的问题,增设了单向阀6。
为了避免机床停止工作时回路中的油液流回油箱,导致空气进入系统,影响滑台运动的平稳性,图中添置了一个单向阀13。
考虑到这台机床用于钻孔(通孔与不通孔)加工, 对位置定位精度要求较高,图中增设了一个压力继电器14。
当滑台碰上死挡块后,系统压力升高,它发出快退信号,操纵电液换向阀换向。
4计算和选择液压件4.1确定液压泵的规格和电动机功率(1)计算液压泵的最大工作压力小流量泵在快进和工进时都向液压缸供油, 由表7可知,液压缸在工进时工作压力最大,最大工作压力为P1=3.96MPa,如在调速阀进口节流调速回路中,选取进油路上的总压力损失刀?p=0.6MPa,考虑到压力继电器的可靠动作要求压差P e=0.5MPa,则小流量泵的最高工作压力估算为Ih>'图2选择的基本回路广73.2组成液压系统WISHp p e 3.96 0.6 0.5 MPa 5.06MPa大流量泵只在快进和快退时向液压缸供油,由表7可见,快退时液压缸的工作压力为p i =1.43MPa ,比快进时大。
考虑到快退时进油不通过调速阀, 故其进油路压力损失比前者小, 现取进油路上的总压力损失 E?p=0.3MPa ,则大流量泵的最高工作压力估算为p p2 p 1 p 1.43 0.3 MPa 1.73MPa(2) 计算液压泵的流量由表7可知,油源向液压缸输入的最大流量为 0.5X 10-3 m 3/s ,若取回路泄漏系数 K=1.1 ,则两个泵的总流量为3 3 3 3q p Kq 11.1 0.5 10 m /s 0.55 10 m /s 33L/min考虑到溢流阀的最小稳定流量为 3L/min ,工进时的流量为0.84 x 10-5 m 3/s =0.5L/min ,则小流量泵的流量最少应为 3.5L/min 。
(3) 确定液压泵的规格和电动机功率根据以上压力和流量数值查阅产品样本,并考虑液压泵存在容积损失,最后确定选取 PV2R12-6/33型双联叶片泵。
其小流量泵和大流量泵的排量分别为 6mL/r 和33mL/r ,当液压泵的转速n p =940r/min 时,其理论流量分别为5.6 L/min 和31L/min ,若取液压泵容积效率n =0.9,则液压泵的实际输出流量为q pq p1qp26 940 0.9/1000 33 940 0.9/1000 L/min 5.1 27.9 L/min 33L/min由于液压缸在快退时输入功率最大, 若取液压泵总效率 n =0.8,这时液压泵的驱动电动机功率为选用规格相近的 Y100L — 6型电动机,其额定功率为1.5KW ,4.2确定其它元件及辅件 (1)确定阀类元件及辅件根据系统的最高工作压力和通过各阀类元件及辅件的实际流量,查阅产品样本,选出的阀类元件和辅件规格如表 8所列。
其中,溢流阀 9按小流量泵的额定流量选取,调速阀 4选用Q —6B 型,其最小稳定流量为 0.03 L/min ,小于本系统工进时的流量 0.5L/min 。
表8P pi PlPpQ pp1.73 106 33 10 360 0.8 103KW 1.19KW根据此数值查阅产品样本, 额定转速为940r/min 。
(2)确定油管在选定了液压泵后,液压缸在实际快进、工进和快退运动阶段的运动速度、时间以及进入和流出液压缸的流量,与原定数值不同,重新计算的结果如表9所列。