工厂设备改善案例
车间改善提案案例大全
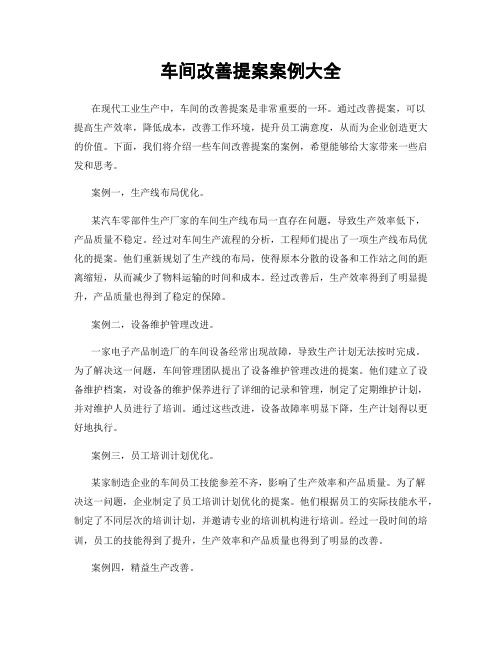
车间改善提案案例大全在现代工业生产中,车间的改善提案是非常重要的一环。
通过改善提案,可以提高生产效率,降低成本,改善工作环境,提升员工满意度,从而为企业创造更大的价值。
下面,我们将介绍一些车间改善提案的案例,希望能够给大家带来一些启发和思考。
案例一,生产线布局优化。
某汽车零部件生产厂家的车间生产线布局一直存在问题,导致生产效率低下,产品质量不稳定。
经过对车间生产流程的分析,工程师们提出了一项生产线布局优化的提案。
他们重新规划了生产线的布局,使得原本分散的设备和工作站之间的距离缩短,从而减少了物料运输的时间和成本。
经过改善后,生产效率得到了明显提升,产品质量也得到了稳定的保障。
案例二,设备维护管理改进。
一家电子产品制造厂的车间设备经常出现故障,导致生产计划无法按时完成。
为了解决这一问题,车间管理团队提出了设备维护管理改进的提案。
他们建立了设备维护档案,对设备的维护保养进行了详细的记录和管理,制定了定期维护计划,并对维护人员进行了培训。
通过这些改进,设备故障率明显下降,生产计划得以更好地执行。
案例三,员工培训计划优化。
某家制造企业的车间员工技能参差不齐,影响了生产效率和产品质量。
为了解决这一问题,企业制定了员工培训计划优化的提案。
他们根据员工的实际技能水平,制定了不同层次的培训计划,并邀请专业的培训机构进行培训。
经过一段时间的培训,员工的技能得到了提升,生产效率和产品质量也得到了明显的改善。
案例四,精益生产改善。
一家机械加工厂的车间存在着材料浪费严重的问题,影响了企业的利润和竞争力。
为了解决这一问题,企业引入了精益生产的理念,提出了精益生产改善的提案。
他们对生产流程进行了精细化的分析,找出了造成材料浪费的根本原因,并采取了相应的改善措施。
经过改善,材料浪费得到了有效控制,企业的利润也得到了提升。
以上案例仅仅是车间改善提案的冰山一角,每个企业的实际情况都有所不同,因此,改善提案也需要因地制宜,因时制宜。
tps改善案例

tps改善案例
以下是一个TPS改善案例:
某制造企业发现其生产线存在生产效率低下、产品质量不稳定等问题。
为了改善这种情况,他们决定引入精益生产(TPS)理念,并实施了一系列改善措施。
首先,他们进行了生产线布局的优化,将生产线上的设备按照工艺流程重新排列,减少了设备之间的距离和物料搬运的时间。
同时,他们还引入了自动化设备,将一些重复性的、简单的操作交由机器来完成,减轻了员工的劳动强度。
其次,他们进行了生产流程的改进。
通过消除生产过程中的浪费,如等待、搬运、检验等,他们提高了生产效率。
同时,他们还引入了看板管理、5S管理等精益管理工具,使生产过程更加透明化和标准化。
最后,他们进行了员工培训和团队建设。
通过培训员工掌握精益生产的理念和方法,他们提高了员工的技能和素质。
同时,他们还开展了团队建设活动,增强了员工之间的沟通和协作能力。
经过一系列的改善措施,该制造企业的TPS得到了显著提升。
生产效率提高了30%,产品质量也得到了稳定和提高。
同时,员工的工作环境和福利待遇也得到了改善,企业的整体竞争力得到了提升。
这个案例表明,精益生产(TPS)是一种有效的生产管理方式,可以帮助企业提高生产效率、降低成本、提高产品质量和竞争力。
自动化设备改善案例
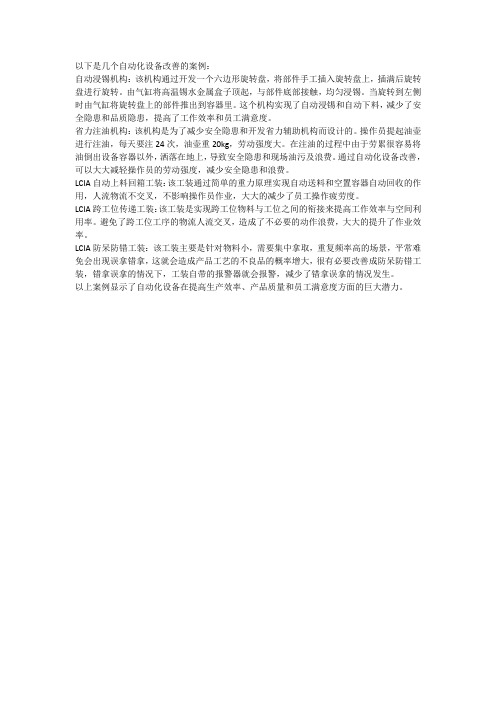
以下是几个自动化设备改善的案例:
自动浸锡机构:该机构通过开发一个六边形旋转盘,将部件手工插入旋转盘上,插满后旋转盘进行旋转。
由气缸将高温锡水金属盒子顶起,与部件底部接触,均匀浸锡。
当旋转到左侧时由气缸将旋转盘上的部件推出到容器里。
这个机构实现了自动浸锡和自动下料,减少了安全隐患和品质隐患,提高了工作效率和员工满意度。
省力注油机构:该机构是为了减少安全隐患和开发省力辅助机构而设计的。
操作员提起油壶进行注油,每天要注24次,油壶重20kg,劳动强度大。
在注油的过程中由于劳累很容易将油倒出设备容器以外,洒落在地上,导致安全隐患和现场油污及浪费。
通过自动化设备改善,可以大大减轻操作员的劳动强度,减少安全隐患和浪费。
LCIA自动上料回箱工装:该工装通过简单的重力原理实现自动送料和空置容器自动回收的作用,人流物流不交叉,不影响操作员作业,大大的减少了员工操作疲劳度。
LCIA跨工位传递工装:该工装是实现跨工位物料与工位之间的衔接来提高工作效率与空间利用率。
避免了跨工位工序的物流人流交叉,造成了不必要的动作浪费,大大的提升了作业效率。
LCIA防呆防错工装:该工装主要是针对物料小,需要集中拿取,重复频率高的场景,平常难免会出现误拿错拿,这就会造成产品工艺的不良品的概率增大,很有必要改善成防呆防错工装,错拿误拿的情况下,工装自带的报警器就会报警,减少了错拿误拿的情况发生。
以上案例显示了自动化设备在提高生产效率、产品质量和员工满意度方面的巨大潜力。
工厂改善提案案例大全
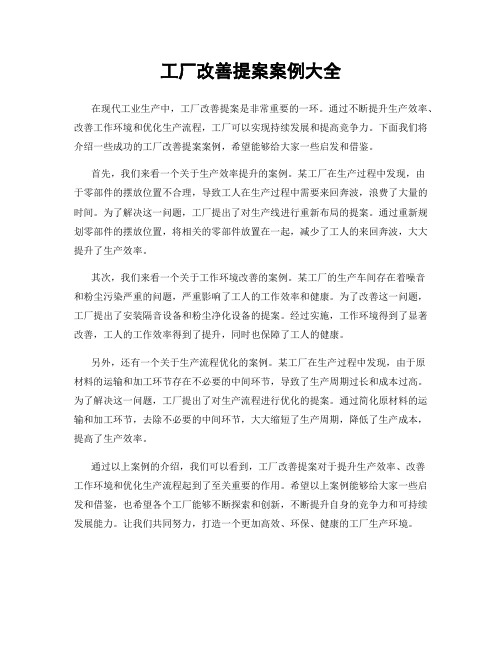
工厂改善提案案例大全在现代工业生产中,工厂改善提案是非常重要的一环。
通过不断提升生产效率、改善工作环境和优化生产流程,工厂可以实现持续发展和提高竞争力。
下面我们将介绍一些成功的工厂改善提案案例,希望能够给大家一些启发和借鉴。
首先,我们来看一个关于生产效率提升的案例。
某工厂在生产过程中发现,由于零部件的摆放位置不合理,导致工人在生产过程中需要来回奔波,浪费了大量的时间。
为了解决这一问题,工厂提出了对生产线进行重新布局的提案。
通过重新规划零部件的摆放位置,将相关的零部件放置在一起,减少了工人的来回奔波,大大提升了生产效率。
其次,我们来看一个关于工作环境改善的案例。
某工厂的生产车间存在着噪音和粉尘污染严重的问题,严重影响了工人的工作效率和健康。
为了改善这一问题,工厂提出了安装隔音设备和粉尘净化设备的提案。
经过实施,工作环境得到了显著改善,工人的工作效率得到了提升,同时也保障了工人的健康。
另外,还有一个关于生产流程优化的案例。
某工厂在生产过程中发现,由于原材料的运输和加工环节存在不必要的中间环节,导致了生产周期过长和成本过高。
为了解决这一问题,工厂提出了对生产流程进行优化的提案。
通过简化原材料的运输和加工环节,去除不必要的中间环节,大大缩短了生产周期,降低了生产成本,提高了生产效率。
通过以上案例的介绍,我们可以看到,工厂改善提案对于提升生产效率、改善工作环境和优化生产流程起到了至关重要的作用。
希望以上案例能够给大家一些启发和借鉴,也希望各个工厂能够不断探索和创新,不断提升自身的竞争力和可持续发展能力。
让我们共同努力,打造一个更加高效、环保、健康的工厂生产环境。
工业工程改善成功案例

工业工程改善成功案例
工业工程改善成功案例是指通过工业工程方法,对企业的生产流程、工艺、设备、人力资源等方面进行改善,提高企业的生产效率、降低成本、提高质量、增强市场竞争力的案例。
以下是几个工业工程改善成功案例的介绍:
1. 某汽车零部件制造企业通过工业工程方法,对生产线进行重新布局和优化,采用自动化设备和机器人代替人工操作,使得生产效率提高了30%,同时降低了废品率和劳动力成本。
2. 某电子产品制造企业通过工业工程方法,对生产流程进行改善,减少了生产中的重复工作和浪费时间的步骤,使得生产周期缩短了50%,同时提高了产品质量和生产效率。
3. 某食品加工企业通过工业工程方法,对生产线进行流程优化和设备改进,使得生产效率提高了20%,同时减少了废品率和人力成本,提高了生产效益和市场竞争力。
4. 某服装制造企业通过工业工程方法,对生产车间进行重新规划和优化,采用自动化设备和机器人代替人工操作,使得生产效率提高了40%,同时降低了废品率和人力成本,提高了生产效益和产品质量。
以上是几个工业工程改善成功案例的介绍,通过工业工程方法的改善,企业可以提高生产效率、降低成本、提高质量、增强市场竞争力,实现可持续发展。
- 1 -。
自动化设备改善案例

自动化设备改善案例
以下是一些自动化设备改善案例:
1. 制造业:许多制造业公司通过引入自动化设备来提高生产效率和质量。
例如,汽车制造商使用机器人进行油漆工作和装配线的其他任务,这大大提高了生产效率,并减少了工人的工作量。
2. 仓储和物流:自动化设备,如自动仓库系统和无人驾驶车辆,可以提高仓储和物流的效率,减少人工错误,并降低劳动力成本。
3. 农业:农业自动化设备,如无人驾驶拖拉机和使用无人机进行播种和喷洒农药,可以提高农业生产效率,减少人工劳动,并提高农作物质量。
4. 医疗保健:在医疗保健领域,自动化设备,如机器人手术系统和自动化药房,可以提高医疗服务质量,减少人工错误,并降低医疗成本。
5. 零售业:零售商使用自动化设备,如自助结账系统和无人驾驶推车,可以提高客户服务,减少人工错误,并提高销售效率。
以上只是一些自动化设备改善案例,具体的效果可能会因行业和公司的具体情况而有所不同。
高效生产设备的工艺改进与应用案例

高效生产设备的工艺改进与应用案例在当今竞争激烈的制造业环境中,提高生产效率、降低成本和提升产品质量是企业追求的核心目标。
而实现这些目标的关键之一,在于对生产设备的工艺进行持续改进,并将成功的改进案例应用到实际生产中。
本文将通过几个具体的案例,探讨高效生产设备工艺改进所带来的显著成果。
一、案例一:汽车零部件生产线的优化在一家汽车零部件制造企业中,生产线上的某一关键设备——冲压机,存在着生产效率低下和废品率较高的问题。
经过深入分析,发现问题主要出在模具的设计和冲压工艺参数的设置上。
首先,技术团队对模具进行了重新设计。
通过采用更先进的CAD/CAE 软件进行模拟分析,优化了模具的结构,使其在冲压过程中受力更加均匀,减少了模具的磨损和变形。
其次,对冲压工艺参数进行了大量的试验和优化。
调整了冲压速度、压力、行程等参数,找到了最佳的组合,从而大大提高了冲压件的成型质量和生产效率。
经过这一系列的工艺改进,该冲压机的生产效率提高了 30%,废品率从原来的 5%降低到了 2%,为企业节省了大量的生产成本,同时提高了产品的市场竞争力。
二、案例二:电子设备组装线的自动化升级在一家电子设备制造企业,组装线的人工操作环节较多,导致生产效率低下,且产品质量容易受到人为因素的影响。
为了解决这个问题,企业决定对组装线进行自动化升级。
引入了先进的机器人手臂和自动化输送系统,实现了零部件的自动上料、组装和检测。
同时,通过优化组装工艺,将原来分散的工序进行整合,减少了中间环节的物料搬运和等待时间。
在软件方面,开发了一套智能化的生产管理系统,能够实时监控生产线上设备的运行状态、生产进度和产品质量,实现了对生产过程的精准控制。
通过这次自动化升级,组装线的生产效率提高了 50%,产品合格率从 95%提升到了 98%,并且大大降低了工人的劳动强度,改善了工作环境。
三、案例三:食品加工设备的节能改造在一家食品加工企业,生产过程中的能源消耗一直是一个较大的成本支出。
生产车间改善提案案例

生产车间改善提案案例生产车间提案案例——设备维护改善为了提高生产车间的设备维护水平和效率,特别针对设备维护过程中存在的问题进行改进提案,具体如下:问题描述:1. 目前设备维护计划安排较为混乱,无明确的时间表和责任人,导致设备维护工作常常推迟或遗漏。
2. 设备维护记录不完整,无法准确追踪设备维修历史和问题原因。
3. 维修人员对设备性能了解不够,维修过程常常比较漫无目的。
4. 维修备件管理混乱,备件库存不清晰,无法及时补充和使用。
5. 设备维修方式单一,无法综合利用维修经验,提高维修效率。
改善方案:1. 设立设备维护管理岗位,负责设备维护计划的制定和实施,明确维护时间和责任人,并与生产计划进行协调。
2. 建立设备维护记录表格,要求每次维护都有详细记录,包括维修时间、维修人员、维修内容、问题原因等信息,以便于后期统计和分析。
3. 组织维修人员参加设备性能培训,增加他们对设备的了解,提高维修效率和质量。
4. 设立专门的备件管理岗位,负责备件库存的管理和补充,确保备件的及时使用和更新。
5. 推行维修经验分享制度,定期召开维修经验交流会,让维修人员分享经验和技巧,并将有价值的维修经验纳入维修手册,供参考使用。
实施计划:1. 第一周:成立设备维护管理岗位,并制定设备维护计划模板。
2. 第二周:组织维修人员参加设备性能培训,并撰写培训总结和笔记。
3. 第三周:建立设备维护记录表格,确定记录要求和填写流程。
4. 第四周:成立备件管理岗位,对备件进行清理和分类,建立备件库存和补充计划。
5. 第五周:召开维修经验交流会,以后每个月定期召开一次。
6. 第六周开始按计划执行设备维护计划和维修记录填写。
效益预期:1. 设备维护计划的制定和实施,将有效解决维护时间混乱和责任模糊的问题,确保设备维修按时进行,提高生产线稳定性。
2. 设备维护记录的完善,将有利于问题的追踪和原因分析,减少设备故障率,提高设备使用寿命。
3. 维修人员的培训和了解度提高,将使维修过程更加专业和高效,减少停机时间,提高生产效率。
- 1、下载文档前请自行甄别文档内容的完整性,平台不提供额外的编辑、内容补充、找答案等附加服务。
- 2、"仅部分预览"的文档,不可在线预览部分如存在完整性等问题,可反馈申请退款(可完整预览的文档不适用该条件!)。
- 3、如文档侵犯您的权益,请联系客服反馈,我们会尽快为您处理(人工客服工作时间:9:00-18:30)。
22
装箱机改善1架限位保护
24
5.5线灌装机堵瓶解决方案
• 5线灌装机出口没有堵瓶检测停机装置, 经常会造成出口输送带堵瓶,灌装机 无法及时停机。造成大量废瓶和水。 • 据统计,每班平均有10多个以上废瓶。 • 每次处理废瓶需15分钟左右时间,假 设每班影响2次生产,影响效率8%左 右。
11
码垛机改造前程序
12
码垛机改造后程序
13
3.4线灌装机改善
对灌装机主要做了两个改善: 1.加装了模拟量输出模块,给水处理提供灌装机液 位信号,满足水处理自动控制比例阀进行PID调 节,实现恒水位供水。 2.原PLC的CPU自带模拟量输入模块已损坏,没有 液位和灌装机速度信号输入,根据公司现有模块, 将原有两位模拟量输入模块更换为8位模拟量模块, 满足生产需求,为公司节约一个CPU费用,大约 一万多元。
7
无压力增加程序1
8
无压力增加程序2
9
无压力增加程序3
10
2.4线码垛机改善
• 对码垛机的改善主要有以下几方面: • (1)原码垛机600ml为6层。我们根据物流 要求,改为7层码垛。刚开始采用人工修改 层数,后经过分析原程序,修改为自动码7 层,无需人工调整。(具体程序见后) • (2)更换继电器,解决拖箱板减速不准问 题。
1
龙门生产线电气介绍
• 龙门5条生产线,电气控制方面大部分采用德国西门 子s7-300PLC控制系统,全冠机采用日本三菱FX2N 系列PLC,SIDEL和3线吹瓶机采用s7-400PLC。 • 目前全厂共有s7-300PLC 40台,s7-200PLC 5台, s7-400PLC 2台,三菱PLC15台,欧姆龙PLC4台, 施耐德PLC 2台。共计使用PLC大约70多台左右。使 用变频器、伺服驱动器共计300多台。 • 系统控制方面,既有单一控制系统,还有以太网控制 系统,ASI总线控制系统,Profibus总线控制系统, MPI总线控制系统。
14
灌装机硬件组态1
15
灌装机改善程序1
16
灌装机硬件组态2
17
灌装机改善程序2
18
灌装机改善程序2
19
灌装机模拟量输入模块接线图
20
灌装机模拟量输出模块接线图
21
4.4线装箱机改善
• 对装箱机的改善主要有两个方面: • 1.装箱机改善1-漏抓检测:原装箱机工作台输送 带上瓶还没有完全满的时候,也会抓瓶,这样容 易造成漏抓。经过改善基本消除了这种现象。 • 2.装箱机改善2-抓瓶头架限位保护:原机没有抓 瓶头架限位保护,正常运行时会造成箱架还没有 降到下限,抓瓶头就放箱,这样很容易撞坏抓瓶 头架。
2
方案论证
• 根据龙门生产线的特点,我们结合DMW解决问题 的方法,近几年对生产线进行了许多行之有效的 改善,由于改善较多,不易一一叙述,下面仅主 要介绍2012年5个典型电气改善案例: • 1.4线无压力输送带倒瓶改善 • 2.4线码垛机层数改善 • 3.4线灌装机液位问题改善 • 4.4线装箱机缺陷改善 • 5.5线灌装机控制改善
27
控制原理电路图s7-300
28
控制原理电路图s7-200
29
输送带增加程序
30
灌装机增加程序
31
总结
• 通过我们的不断努力,龙门工厂5条线的效率不断 提升,1、2线效率目前已稳定在90%以上。3线 效率也接近90%。4线PE由元月份的40.60%提高 到最高的十月份86.19%,5线PE由46%提高到 90%以上,效果是明显的,并且较稳定,再经过 今年的大修,效率达到90%以上应该没有问题。 下面三个图表是3、4、5线12年全年PE变化情况: • 从曲线变化可看出,后期的效率非常稳定。
25
设备介绍及方案
• 5线输送带控制系统采用德国西门子s7-200PLC进行控制。 • 5线灌装机控制系统采用德国西门子s7-300PLC,并配备 操作触摸屏。 • 方案:利用现有输送带停止按钮,实现灌装机堵瓶停机。 • 缺点:1.需人工操作,有在线质检根据实际情况进行。 • 2.控制复杂,需要在输送带和灌装机两台控制柜 之间进行信号控制,需要在两个PLC上更改程序。 • 优点: 1.由于输送带没有缓冲,人工操作对连续生产影响 较小. • 2.不影响贴标机运行状况。 • 3.控制可靠。
3
鱼骨图分析
4
长期解决方案
6
1.4线无压力输送带改善
• 无压力输送带是这条生产线问题最严重的地方之一。 曾经有时候用2、3个操作工专门负责解决倒水问题。 我们主要采取的措施有几个方面: • (1)原设计堵水停机功能不完善,经我们反复分析 原程序,提出了新的解决方案,增加了堵水自动停机 功能。(具体程序见后) • (2)反复调整原生产线的无压力输送带变频器速度, 加、减速时间等形成从前往后逐渐递减的方式,减少 了倒瓶的可能性。 • (3)调整输送带光电开关、接近开关等有关传感器 位置,达到最佳控制状态。
工厂电气设备关键改善
方案背景
• • • •
工厂目前共有5条线生产线。 1、2线是新美星灌包装加全冠吹瓶机。 3线也是新美星灌包装加达意隆吹瓶机。 4线从原深圳工厂搬迁过来的。由于生产线是96年 的设备,后经几家供应商改造,搬迁后设备操作人 员又不熟悉设备,造成生产效率很低,很长时间PE 都在60%左右徘徊。特别是电气方面的故障率很高。 所以,我们12年对4线的改善力度较大。 • 5线采用新美星灌装机,包装采用永创设备,加达 意隆吹瓶机。
26
控制方案及实施步骤
• 1.根据两台PLC的I/O点状态,确定有多余的点数。输送带 输出Q2.0,通过加中间隔离继电器,输入到灌装机PLC输 入点I5.0,控制灌装机在自动状态下的停止。并选择DC24v 继电器作为中间继电器。 • 2.绘制控制原理电路图。 • 3.根据电路图布线、接线。 • 4.分别对两台PLC进行编程。 • 5.两台机送电调试,验证结果正确无误。 • 6.正式生产时还要进行观察,是否对两台机的运行状态有 无影响。
32
3线PE曲线
33
4线PE曲线
34
5线PE曲线
35
改善分享
• 下面是2010-2012年度龙 门工厂一些电气方面的重 点改善案例,供大家参考。
36
2010年电气方面主要改善汇总
37
2011年电气方面主要改善汇总
38
2012年电气方面主要改善汇总
39
结束语
谢谢!
40