丁二烯抽提工艺技术路线选择
丁二烯的生产工艺与技术路线的选择

丁二烯的生产工艺与技术路线的选择2.1 丁二烯的合成工艺目前,世界丁二烯的来源主要有两种,一种是从乙烯裂解装置副产的混合C4馏分中抽提得到,这种方法价格低廉,经济上占优势,是目前世界上丁二烯的主要来源。
另一种是从炼油厂C4馏分脱氢得到,该方法只在一些丁烷、丁烯资源丰富的少数几个国家采用。
世界上从裂解C4馏分抽提丁二烯以萃取精馏法为主,根据所用溶剂的不同生产方法主要有乙睛法(ACN法)、二甲基甲酰胺法(DMF法)和N-甲基吡咯烷酮法(NMP法)3种。
2.1.1 乙腈法(ACN法)乙腈法最早由美国Shell公司开发成功,并于1956年实现工业化生产。
它以含水10%的ACN为溶剂,由萃取、闪蒸、压缩、高压解吸、低压解吸和溶剂回收等工艺单元组成。
1977年Shell公司在改造中增加了冷凝器和水洗塔,并将闪蒸和低压解吸的气相合并压缩,其中约8%经冷凝送往水洗塔洗去溶剂,塔顶气相返回原料蒸馏塔,这样就除去了C4烃中的C5烃。
其余气体一部分送往高压解吸塔,另一部分送往萃取蒸馏塔塔底作为再拂气体提供热能,从而省去了一台再沸器,降低了蒸汽用量。
水洗塔底溶剂约1%送往溶剂回收精制系统,以保证循环溶剂的质量。
该法对含炔烃较高的原料需加氢处理,或采用精密精馏、两段萃取才能得到较高纯度的丁二烯。
该方法以意大利SIR工艺和日本JSR工艺为代表。
……采用ACN法生产丁二烯的特点是:……2.1.2 二甲基甲酰胺法(DMF法)DMF法又名GPB法,由日本瑞翁(Geon)公司于1965年实现工业化生产,并建成一套4.5万t/a生产装置。
该生产工艺包括四个工序,即第一萃取蒸馏工序、第二萃取蒸馏工序、精馏工序和溶剂回收工序。
原料C4汽化后进入第一萃取精馏塔,溶剂DMF由塔的上部加入。
溶解度小的丁烷、丁烯、C3使丁二烯的相对挥发度增大,并从塔顶分出,而丁二烯、炔烃等和溶剂一起从塔底导出,进入第一解吸塔被完全解吸出来,冷却并经螺杆压缩机压缩后进入第二萃取精馏塔进一步分离。
碳四抽提丁二烯
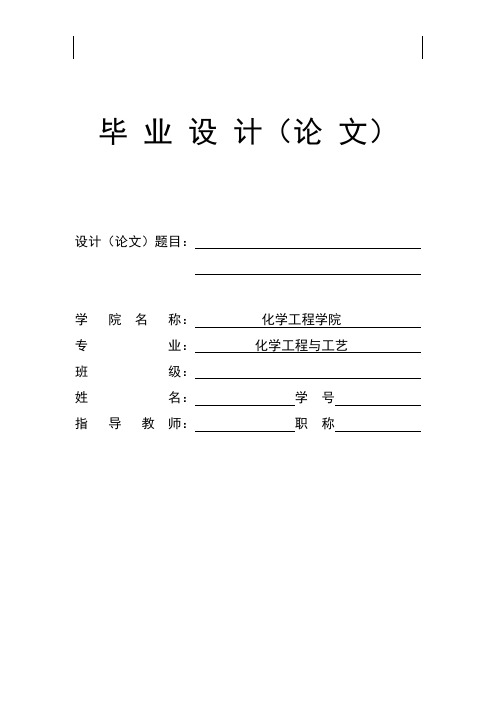
毕业设计(论文)设计(论文)题目:学院名称:化学工程学院专业:化学工程与工艺班级:姓名:学号指导教师:职称摘要丁二烯是一种具有广泛用途的化工产品,其生产、制备的研究进行了数十年。
目前仍然未停止对其工艺的调整与改进。
工业生产中常用在碳四馏分中加入一种溶剂进行萃取的特殊精馏来实现对C4馏分的分离。
本设计以从碳四中抽提丁二烯为目的,依据经济、节约、环保、科学的理念,制定出抽提段的工艺。
目前世界上大规模工业化生产丁二烯-1的方法主要有三种:乙腈法(ACN)、二甲基甲酰胺法,3(DMF)和N-甲基砒硌烷酮法(BASF)。
工艺采用DMF法,从碳四混合物中抽提出符合工艺要求的丁二烯。
设计中对DMF法抽提丁二烯的原理、工艺、操作规范、物料衡算、废物处理等发面进行了阐述。
DMF抽提丁二烯装置可分为两个部分:萃取部分和精馏部分。
萃取部分包括第一萃取精馏系统和第二萃取精馏系统,碳四原料中的丁烷、丁烯等在第一萃取精馏系统中脱除,乙烯基乙炔、一部分乙基乙炔等组分在第二萃取精馏系统中脱除;精馏部分包括丁二烯净化和溶剂精制两系统,除去其中的二甲胺、甲基乙炔、水、顺丁烯-2等杂质,得到丁二烯成品;而溶剂精制系统是将循环溶剂中的水分,二聚物等轻组分及焦油等重组分除去,保持循环溶剂的质量。
设计结果科学、合理,实用、经济,比较好的完成了当初所设定的目标任务。
关键词:碳四;丁二烯;抽提;DMFABSTRACTButadiene is a widely used chemical products, its production, research on the preparation for decades. At present, still did not stop the process of adjustment and improvement. Special rectification commonly used in industrial production in four fractions of carbon with a solvent extraction to achieve separation of C4 fractions. The design for the purpose of butadiene extraction from carbon 4, on the basis of the economic, environmental protection, conservation, scientific ideas, develop process extraction section. The large-scale industrial production of butadiene with -1, there are three main methods: acetonitrile (ACN), two methyl formamide (DMF) and N- methyl pyrrole azululanone method (BASF). Process using DMF method, is proposed to meet the process requirements of the butadiene extraction from carbon four mixture. The design of DMF butadiene extraction principle, process, operation, material balance, waste disposal and other aspects are discussed. DMF Extraction Butadiene device can be divided into two parts: the extraction and distillation. The extraction part includes the first extractive distillation system and the second system of extractive distillation, carbon four of raw materials, such as butane butene in the first extraction distillation system removal, vinyl acetylene, a part of ethyl acetylene and other components removal in second extraction distillation system; distillation part includes the butadiene purification and solvent refining two system, remove the two -, methyl acetylene, water, CIS butene -2 impurities, butadiene get finished products; and solvent refining system is the circulation of water in the solvent, two dimers and other light components and tar and other restructuring removed, maintain the quality of circulating soluble agent. The design result is scientific and reasonable, practical, economic, better to complete the target mission set.Key Words:Butadiene;C4 Fractions;Extraction;DMF目录1 引言 (1)1.1丁二烯来源 (1)1.2丁二烯性质与用途 (1)2 工艺路线 (2)2.1生产的基本原理 (2)2.2工艺路线的对比与选择 (2)2.3DMF法碳四抽提丁二烯装置的特点 (3)2.4物料衡算 (4)2.5装置工艺流程图 (4)2.6工艺流程说明 (5)2.6.1 第一萃取精馏部分 (5)2.6.2 第二萃取精馏部分 (6)2.6.3 丁二烯净化部分 (7)2.6.4 溶剂净化部分 (8)2.7各项参数控制、检测 (9)2.7.1 主要原材料性质和控制指标 (9)2.7.2 产品、副产品的性质和质量监控 (9)2.7.3 辅助原材料物化性质和控制指标 (10)2.7.4 辅助材料作用和使用量 (12)2.8工艺控制 (12)2.8.1 原料质量变化对产品的影响及调节方法 (13)2.8.2 主要工艺条件的变化对产品质量的影响 (14)致谢 (18)参考文献 (19)附录 (20)1.主要原料、辅助原材料单耗及公用工程单耗(/T产品,年) (20)2.三废治理、综合利用表 (21)3.工业用丁二烯(GB/T13291-2008)生产指标 (21)1 引言1.1 丁二烯来源从油田气、炼厂气和烃类裂解制乙烯的副产品中都可获得碳四馏分。
丁二烯抽提工艺技术路线选择概述课件

丁二烯抽提工艺技术路线选择
1.1 NMP法
•
NMP法工艺流程:
• 裂解碳四汽化后进入主洗塔底部,含水的N-甲基吡咯烷酮萃取剂进入该塔塔顶下的几块塔 板处,丁二烯和更易溶解的组分及部分丁烷、丁烯被吸收,抽余碳四从塔顶出装置。
• 主洗塔底部的富溶剂进入精馏塔,在该塔中,溶剂吸收的丁烷丁烯被更易溶的丁二烯-1,3、 甲基乙炔和碳四炔烃置换出来,含有碳四炔烃和甲基乙炔的丁二烯-1,3物流,从精馏塔的 侧线以气态排出,进入后洗塔。在后洗塔中,用新鲜溶剂进行萃取,比丁二烯-1,3更易溶
第10页/共26页
丁二烯抽提工艺技术路线选择
2.2 溶剂性能
N-甲基吡咯烷酮(NMP)、二甲基甲酰胺(DMF) 和乙腈(ACN)三种溶剂性能对比见表3-2。
序号
项目
N-甲基吡咯烷酮NMP
二甲基甲酰胺DMF
乙 腈ACN
1
50℃时的相对溶解度
对1,3-丁二烯
1
1
1
对顺丁烯-2
1.63
1.56
1.43
对1,2-丁二烯
第7页/共26页
丁二烯抽提工艺技术路线选择
1.3 ACN法
• 二级乙腈法的生产过程基本与DMF法相同, 其不同之处在于采用含水10%的溶剂,因乙 腈沸点低,又与丁二烯形成共沸物,所以须 增设水萃取回收并提浓乙腈的系统。
• 乙腈法具有萃取剂易于获得,工艺可靠,能 阻止双烯烃热聚,工艺流程中不需要压缩机 等优点。但由于乙腈沸点低,蒸汽压较高, 运转过程中损失较大。毒性也较大。
第4页/共26页
丁二烯抽提工艺技术路线选择
1.2 DMF法
• DMF法又称GPB法,系日本瑞翁公司研究开发,于 1965年工业化。由于该技术比较先进、成熟可靠,世 界各国相继采用,目前是生产丁二烯的各种方法中吨 位较高的一种。我国燕山石化公司于1976年首次从日 本引进一套年产4.5万吨的丁二烯装置,随后扬子、齐 鲁、南京、金山、抚顺、广州又陆续与乙烯装置一起 引进6套。经过消化吸收,现已建成投产国产化装置5 套(包括扬子石化一套),单套生产能力约5万吨/年。 至今我国利用DMF法共建成12套生产装置,总计生产 能力约占全国丁二烯抽提生产能力的70.2%。
丁二烯抽提终版工艺流程简介

第一萃取蒸馏部分在DMF存在的情况下,凡与丁二烯相比其相对挥发度高于1.0的组分,都在这部分除去。
这部分设备有:原料汽化罐,第一萃取蒸馏塔(分为两个塔,共有238块塔板)以及装有14层塔板的第一汽提塔。
C4原料从乙烯装置A单元进入原料储罐后用泵送来经流量控制进入原料汽化罐。
原料汽化罐的热源由第一、第二汽提塔底的热溶剂提供。
汽化的C4原料送至第一萃取蒸馏塔的中部(进料板104层,114层,125层)。
DMF溶剂经流量控制进入T -1101A顶部第230层塔板上,溶剂进料温度约40℃,蒸汽压约9毫米汞柱。
塔顶8层塔板用于丁烷丁烯馏分中完全脱除溶剂的精馏段。
塔的操作压力约为0.38MPa(表压),塔顶操作温度约为43.5℃。
根据进料组成的变化,适当调节溶剂进料量和回流量,以控制丁二烯的损失量和塔釜液的组成,丁烷丁烯馏出液的1,3-丁二烯含量保持在0.3%(重量)以下。
塔顶丁烷丁烯抽余液直接送至MTBE装置或A单元罐区。
萃取蒸馏必要的回流经流量调节,经过上述8层塔板的精馏段,向下流至溶剂进料塔板。
顺2-丁烯是比1,3-丁二烯难溶解的一种组分,在第一萃取蒸馏塔中它是最难于分离出来的。
按GPB工艺,通常第一萃取蒸馏塔底的顺2-丁烯含量约为总烃的2.5%,而反2-丁烯含量约为总烃的0.05%。
顺2-丁烯在第二分馏塔(T-1302)随塔底物料脱除,但反2-丁烯不易在直接蒸馏部分脱除。
因此,第一萃取蒸馏塔的分离效果对最终丁二烯产品的纯度有影响。
在GPB工艺中提纯丁二烯的经济方法是在第一萃取蒸馏部分脱除全部反2-丁烯,随之脱除部分顺2-丁烯。
而在第二分馏塔脱除剩余的顺2-丁烯。
在第一萃取蒸馏塔(T-1101B)的C-3层塔板上,含烃(主要是含丁二烯和易溶组分)的溶剂被预热到86℃。
这些溶剂先通过第一萃取蒸馏塔的第一、第二溶剂再沸器,被来自汽提塔底的热溶剂加热到120℃。
然后,在第一萃取塔蒸汽再沸器中把它进一步加热到大约130℃。
丁二烯的生产—乙腈法生产丁二烯的工艺流程

乙腈法生产丁二烯的工艺流程
两级萃取流程
C4:丁烷(正丁烷,异丁烷) 、丁烯(1-丁烯,异丁烯,2-丁烯(顺式,反式) 、丁二烯、炔烃(丁炔,乙烯基乙炔)
溶剂
丁烷 丁烯 丁二烯 炔烃
丁烷 丁烯
丁二烯 炔烃 溶剂
丁二烯 炔烃
溶剂
丁二烯 溶剂炔烃 溶剂第一级萃取精馏第二级萃取精馏
丁二烯蒸出
炔烃 溶剂
炔烃蒸出
乙腈法生产丁二烯的工艺流程
乙腈法生产丁二烯的流程示意图
项目八 丁二烯的生产
石油化工产品生产技术
任 务 四
流 程 的 组 织
生 产 工 艺
乙腈法生产丁二烯的工艺流程
乙腈法生产丁二烯的工艺流程
萃取剂乙腈的特点
①选择性高,明显提高组分的相对挥发度。加入乙腈后,组分的挥 发度顺序为炔烃<二烯烃<单烯烃<烷烃。
②乙腈沸点81.6℃,比碳四馏分任一组分都高,挥发性小,不易混 入塔顶产品中,却易于与其他组分分离回收,损耗小。与其它萃 取剂比较沸点较低,可在较低温度下操作,降低能量损耗,回收 分离时也可以避免塔釜温度过高。
丁二烯生产流程
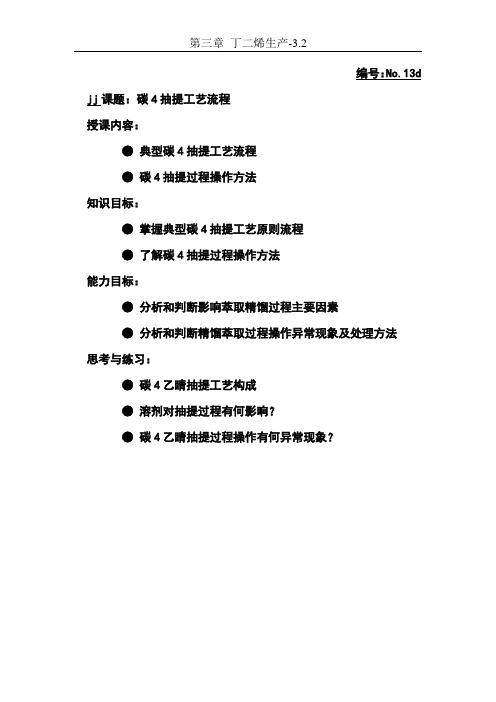
编号:No.13d jj课题:碳4抽提工艺流程授课内容:●典型碳4抽提工艺流程●碳4抽提过程操作方法知识目标:●掌握典型碳4抽提工艺原则流程●了解碳4抽提过程操作方法能力目标:●分析和判断影响萃取精馏过程主要因素●分析和判断精馏萃取过程操作异常现象及处理方法思考与练习:●碳4乙睛抽提工艺构成●溶剂对抽提过程有何影响?●碳4乙睛抽提过程操作有何异常现象?授课班级:授课时间:年月日三、工艺流程1、乙腈法(ACN法)乙腈法是以含水5%~10%的乙腈为溶剂,以萃取精馏的方法分离丁二烯。
我国于1971年5月由兰化公司合成橡胶厂自行开发的乙腈法C4抽提丁二烯装置试车成功。
该装置采用两级萃取精馏的方法,一级是将丁烷、丁烯与丁二烯进行分离,二级是将丁二烯与炔烃进行分离。
其工艺流程见图3—1。
由裂解气分离工序送来的C4馏分首先送进碳三塔(1)碳五塔(2),分别脱除C3馏分和C5馏分,得到精制的C4馏分。
精制后的C4馏分,经预热汽化后进入丁二烯萃取精馏塔(3)。
丁二烯萃取精馏塔分为两段,共l20块塔板,塔顶压力为0.45Mpa,塔顶温度为46℃,塔釜温度114℃.C4馏分由塔中部进入,乙腈由塔顶加入,经萃取精馏分离后,塔顶蒸出的丁烷、丁烯馏分进入丁烷、丁烯水洗塔(7)水洗,塔釜排出的含丁二烯及少量炔烃的乙腈溶液,进入丁二烯蒸出塔(4)。
在塔(4)中塔釜排出的乙腈经冷却后供丁二烯萃取精馏塔循环使用,丁二烯、炔烃从乙腈中蒸出去塔顶,并送进炔烃萃取精馏塔(5)。
经萃取精馏后,塔顶丁二烯送丁二烯水洗塔(8),塔釜排出的乙腈与炔烃一起送入炔烃蒸出塔(6)。
为防止乙烯基乙炔爆炸,炔烃蒸出塔(6)顶的炔烃馏分必须间断地或连续地用丁烷、丁烯馏分进行稀释,使乙烯基乙炔的含量低于30%(摩尔),炔烃蒸出塔釜排出的乙腈返回炔烃蒸出塔循环使用,塔顶排放的炔烃送出用作燃料。
在塔(8)中经水洗脱除丁二烯中微量的乙腈后,塔顶的丁二烯送脱轻组分塔(10)。
丁二烯生产工艺流程
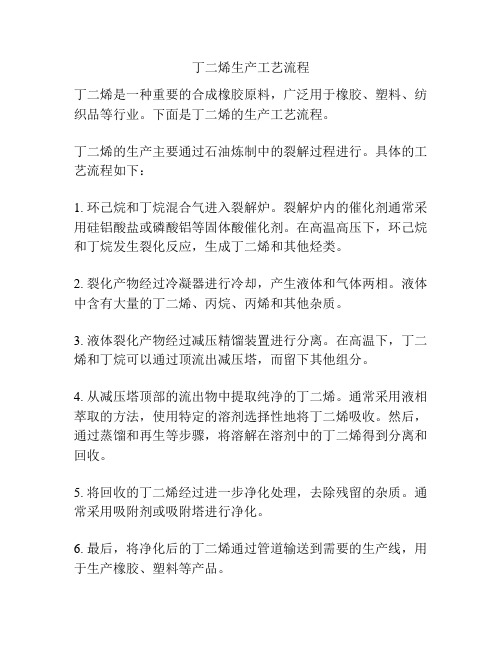
丁二烯生产工艺流程
丁二烯是一种重要的合成橡胶原料,广泛用于橡胶、塑料、纺织品等行业。
下面是丁二烯的生产工艺流程。
丁二烯的生产主要通过石油炼制中的裂解过程进行。
具体的工艺流程如下:
1. 环己烷和丁烷混合气进入裂解炉。
裂解炉内的催化剂通常采用硅铝酸盐或磷酸铝等固体酸催化剂。
在高温高压下,环己烷和丁烷发生裂化反应,生成丁二烯和其他烃类。
2. 裂化产物经过冷凝器进行冷却,产生液体和气体两相。
液体中含有大量的丁二烯、丙烷、丙烯和其他杂质。
3. 液体裂化产物经过减压精馏装置进行分离。
在高温下,丁二烯和丁烷可以通过顶流出减压塔,而留下其他组分。
4. 从减压塔顶部的流出物中提取纯净的丁二烯。
通常采用液相萃取的方法,使用特定的溶剂选择性地将丁二烯吸收。
然后,通过蒸馏和再生等步骤,将溶解在溶剂中的丁二烯得到分离和回收。
5. 将回收的丁二烯经过进一步净化处理,去除残留的杂质。
通常采用吸附剂或吸附塔进行净化。
6. 最后,将净化后的丁二烯通过管道输送到需要的生产线,用于生产橡胶、塑料等产品。
总结起来,丁二烯的生产工艺主要包括裂解、冷却冷凝、减压分离、萃取净化和输送等步骤。
这些步骤可以在工业化设备中连续进行,实现大规模丁二烯的生产。
DMF萃取精馏法分离丁二烯的工艺流程模拟与分析
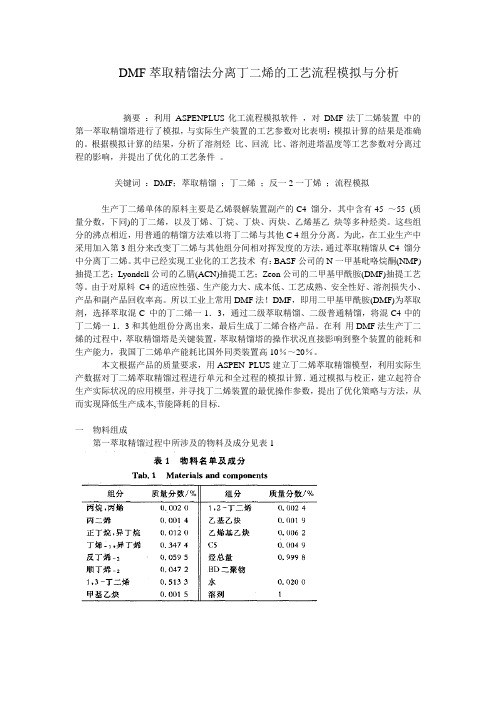
DMF萃取精馏法分离丁二烯的工艺流程模拟与分析摘要:利用ASPENPLUS化工流程模拟软件,对DMF法丁二烯装置中的第一萃取精馏塔进行了模拟,与实际生产装置的工艺参数对比表明:模拟计算的结果是准确的。
根据模拟计算的结果,分析了溶剂烃比、回流比、溶剂进塔温度等工艺参数对分离过程的影响,并提出了优化的工艺条件。
关键词:DMF;萃取精馏;丁二烯;反一2一丁烯;流程模拟生产丁二烯单体的原料主要是乙烯裂解装置副产的C4 馏分,其中含有45 ~55 (质量分数,下同)的丁二烯,以及丁烯、丁烷、丁炔、丙炔、乙烯基乙炔等多种烃类。
这些组分的沸点相近,用普通的精馏方法难以将丁二烯与其他C 4组分分离。
为此,在工业生产中采用加入第3组分来改变丁二烯与其他组分间相对挥发度的方法,通过萃取精馏从C4 馏分中分离丁二烯。
其中已经实现工业化的工艺技术有:BASF公司的N一甲基吡咯烷酮(NMP)抽提工艺;Lyondell公司的乙腈(ACN)抽提工艺;Zeon公司的二甲基甲酰胺(DMF)抽提工艺等。
由于对原料C4的适应性强、生产能力大、成本低、工艺成熟、安全性好、溶剂损失小、产品和副产品回收率高。
所以工业上常用DMF法!DMF,即用二甲基甲酰胺(DMF)为萃取剂,选择萃取混C 中的丁二烯一1.3,通过二级萃取精馏、二级普通精馏,将混C4中的丁二烯一1.3和其他组份分离出来,最后生成丁二烯合格产品。
在利用DMF法生产丁二烯的过程中,萃取精馏塔是关键装置,萃取精馏塔的操作状况直接影响到整个装置的能耗和生产能力,我国丁二烯单产能耗比国外同类装置高10%~20%。
本文根据产品的质量要求,用ASPEN PLUS建立丁二烯萃取精馏模型,利用实际生产数据对丁二烯萃取精馏过程进行单元和全过程的模拟计算.通过模拟与校正,建立起符合生产实际状况的应用模型,并寻找丁二烯装置的最优操作参数,提出了优化策略与方法,从而实现降低生产成本,节能降耗的目标.一物料组成第一萃取精馏过程中所涉及的物料及成分见表1二工艺流程DMF法丁二烯抽提装置工艺流程的最大特点是加入了萃取剂(溶剂),而且萃取剂的用量较大(时被分离组分的5~l7倍),沸点又高,在操作过程中每一层塔板上都要维持一定的溶剂浓度,一般为70%~80%左右,而且要使被分离组分和萃取剂完全互溶,严防分层,否则会使操作恶化,破坏正常的汽、液平衡,达不到预期的分离效果DMF法萃取精馏丁二烯是经过2段萃取精馏和2段普通精馏,整个萃取精馏过程如下图1所示。
- 1、下载文档前请自行甄别文档内容的完整性,平台不提供额外的编辑、内容补充、找答案等附加服务。
- 2、"仅部分预览"的文档,不可在线预览部分如存在完整性等问题,可反馈申请退款(可完整预览的文档不适用该条件!)。
- 3、如文档侵犯您的权益,请联系客服反馈,我们会尽快为您处理(人工客服工作时间:9:00-18:30)。
丁二烯抽提工艺技术路线选择
1.2 DMF法
该法工艺的特点是: A. 工艺成熟可靠,操作周期长,对安全生产、
设备保运、化学品使用和异常现象的处理等 都有相应的技术措施; B. 国产化程度高,改进了工艺流程,优化了 工艺条件; C. 对原料的适应性较强,丁二烯回收率高, 产品纯度较高; D. 操作容易,维修方便; E. 溶剂DMF性能优良,价格相对比较便宜。
丁二烯抽提工艺技术路线选择
1.3 ACN法
ACN法即乙腈法,由美国壳牌公司开发,于 1956年工业化。我国自行开发的二级乙腈法 抽提丁二烯装置,1971年于燕化建成投产, 随后吉林、兰州和齐鲁等相继建成同类装置。 为了节能降耗,1986年吉化引进日本JSR节 能技术,对原装置进行改造。目前,我国的 二级乙腈法生产装置经多次改造和扩建,单 套生产能力已由原来的1.25万吨/年提高到4 万吨/年。我国利用ACN法共建成8套丁二烯 抽提生产装置,总计生产能力约占全国丁二 烯抽提生产能力的22.6%。
本文中装置规模均表示丁二烯产量。
丁二烯抽提工艺技术路线选择
1.1 NMP法
NMP法由德国BASF公司开发,于1968年工业化,生 产能力为7.5万吨/年。世界现有生产能力中NMP法占 27.7%,DMF法和ACN法分别占40%和23.6%。我国 1995年北京东方化工厂首次从德国引进一套3万吨/年 的装置,同年新疆独山子引进一套2.75万吨/年的装置。 目前,上海塞科又采用一套9万吨/年的NMP法装置,引 进基础设计,预计2005年投产。
一种溶剂的各种性能对工艺的影响有正面的也有反面 的,不能只从其选择性和溶解度来判断该工艺的优缺 点,从目前的性能比较来看三种溶剂的性能都能满足 萃取精馏的要求。
丁二烯抽提工艺技术路线选择
2.3 经济技术指标
目前,我国采用DMF法、NMP法和ACN法三种技术都建有丁二烯抽提装置。 我国及国外三种技术装置的技术指标比较见表3-3-1。
ACN
DMF
NMP
3.13
3.43
3.66
1.92
2.17
2.38
1.59
1.76
1.90
1.45
1.56
1.63
1.00
0.70
0.806
1.00
1.00
1.00
0.731 0.720
0.737
0.481 0.424
0.418
0.389 0.229
0.208
注:混合物中主要含有丁烯和丁二烯(比例为1:1)。
丁二烯抽提工艺技术路线选择
2 工艺技术比较
3.1 产品质量(主要指标) 表3-1-1 NMP法、DMF法及CAN法丁二烯产品主要指标比较表
项目
NMP法 设计值 保证值
丁二烯纯度(wt%) ≥99.7 ≥99.7
总炔(10-6)
≤20 ≤20
VA (10-6)
≤5
≤5
水值(10-6)
≤20 ≤20
DMF法
98.29
93.00
溶剂消耗 (kg/t)
2.90
0.95
1.55
1.87
4.00
冷却水消耗 (t/t)
296
295
223
334
203
196
98.1
98.24 99.00
0.84
0.40
0.25
102Biblioteka 230182电耗 (kWh/t)
124
146
275
230
77
108
100
64
178
蒸汽消耗 (t/t)
丁二烯抽提工艺技术路线选择
2.2 溶剂性能
从上表可见,在C4馏分无限稀释情况下(接近于第一 萃取塔操作条件),比丁二烯轻的组分容易脱除的顺 序为NMP>DMF>ACN。在C4馏分30%情况下(接近 于第二萃取塔操作条件),比丁二烯重的组分容易脱 除的顺序也为NMP>DMF>ACN。相对来说,NMP溶剂 对萃取精馏操作是最适合的,其次是DMF,ACN最差。
1.92
综合能耗 (t/t)
0.21
设备相对台数
溶剂相对价格
C4中丁二烯含量的 适用范围
可开车负荷范围
再生溶剂占总溶剂 比例
连续运行时间
裂解碳四汽化后进入主洗塔底部,含水的N-甲基吡咯烷酮萃取剂进入该塔塔顶下的几块塔 板处,丁二烯和更易溶解的组分及部分丁烷、丁烯被吸收,抽余碳四从塔顶出装置。
主洗塔底部的富溶剂进入精馏塔,在该塔中,溶剂吸收的丁烷丁烯被更易溶的丁二烯-1,3、 甲基乙炔和碳四炔烃置换出来,含有碳四炔烃和甲基乙炔的丁二烯-1,3物流,从精馏塔的 侧线以气态排出,进入后洗塔。在后洗塔中,用新鲜溶剂进行萃取,比丁二烯-1,3更易溶 解的组分进入溶剂中,粗丁二烯由后洗塔顶离开,并进入冷凝器,液化后进入蒸馏工段。 后洗塔塔釜的富溶剂返回精馏塔的中段。
B. 萃取蒸馏的塔板效率和物料的粘度成反比,所以萃 取蒸馏的塔板效率,ACN最高,DMF次之,NMP最低。
C. 为降低丁二烯和炔烃自聚的可能性,应尽一切可能 降低系统温度。对ACN和NMP来说,含10%的水可显 著降低溶剂沸点,这三种工艺实际的解吸塔塔底温度 是:DMF 163℃,NMP 148℃,ACN 130℃。
指标 技术或生产商
上海石化 引进DMF
燕山石化 引进DMF
国内
独山子 北京东方 引进NMP 引进NMP
吉化 引进ACN
齐鲁石化 引进ACN
DMF ZEON
国外
ACN JSR
NMP BASF
生产规模(万t/a)
5.0
5.6
2.7
3.0
3.0
3.0
丁二烯收率( %)
98.1
98.79
97.17
91.60
丁二烯抽提工艺技术路线选择
1.2 DMF法
DMF法又称GPB法,系日本瑞翁公司研究开发,于 1965年工业化。由于该技术比较先进、成熟可靠,世 界各国相继采用,目前是生产丁二烯的各种方法中吨 位较高的一种。我国燕山石化公司于1976年首次从日 本引进一套年产4.5万吨的丁二烯装置,随后扬子、齐 鲁、南京、金山、抚顺、广州又陆续与乙烯装置一起 引进6套。经过消化吸收,现已建成投产国产化装置5 套(包括扬子石化一套),单套生产能力约5万吨/年。 至今我国利用DMF法共建成12套生产装置,总计生产 能力约占全国丁二烯抽提生产能力的70.2%。
该法工艺的特点是: A. 溶剂NMP性能优良,沸点高,蒸汽压低,不易水解
或热降解,性质稳定,无毒,溶剂本身及其与水的混 合物无腐蚀性。因此,操作过程中溶剂损失少,设备 材质可用碳钢; B.对原料的适应性强,适用于从裂解碳四中分离丁 二烯,丁二烯回收率高; C. 装置排出的废水中所含的微量NMP,在污水生化处 理装置中很容易被降解,处理效果好; D. 工艺技术先进、成熟可靠,操作周期长,装置能耗、 物耗低; E. 设备台数少,操作和维修费用低; F. 产品纯度可达99.7%以上,质量好。
约为总溶剂量0.2%的汽提后的溶剂进入加热的搅拌釜中,该釜在真空下操作,溶剂从顶部 蒸出,经冷凝得到再生溶剂,循环使用,釜底残渣作为废物排出。
NMP法的基本流程与DMF法相同。其不同之处在于溶剂中含有5%~10%的水,使其沸点降 低,有利于防止聚合物生成。
丁二烯抽提工艺技术路线选择
1.1 NMP法
E. 三种溶剂在生产过程中都很稳定,但DMF仍有少量 分解产物二甲胺进入产品,对聚合有影响,因此DMF 工艺仍需设置水洗塔。
F. NMP无毒性。DMF和ACN都有毒,ACN毒性最大。
丁二烯抽提工艺技术路线选择
2.2 溶剂性能
50 ℃时C4馏分在三种溶剂中相对挥发度比较见表3-2-2。
烃类
正丁烷 1-丁烯 反-2-丁烯 顺-2-丁烯 丙炔 1,3-丁二烯 1,2-丁二烯 1-丁炔 乙烯基乙炔
丁二烯抽提工艺技术路线选择
2.2 溶剂性能
DMF和NMP由于常压下沸点很高,为了使解吸塔顶和 脱气塔顶的物料进入第二萃取蒸馏塔,必须设置压缩 机;ACN由于沸点低,可使解吸塔顶保持较高压力仍 可保证一定的塔底温度,所以不必设置压缩机。
D. 溶剂沸点越低,回收越容易,但沸点低的溶剂也易 从萃取精馏塔、解吸塔塔顶带出,损失量多。为防止 溶剂对产品的污染,ACN工艺必须设置水洗塔。NMP 沸点高,仅依靠塔顶少量回流就可防止对产品的污染 和损失,不必设置水洗塔。
设计值 保证值
≥99.7 ≥99.5*
≤20
≤20
≤5
≤5
≤20 ≤50 * *
ACN法
设计值 保证值
≥99.5 ≥99.5
≤20 ≤50
≤5
≤5
≤20 ≤20
注: *:实际值大于99.5%可以满足下游装置的要求,因此运行 时采用此值。
**:化验分析水值≤50(10-6)。实际水值≤20(10-6)。满 足下游装置要求。
丁二烯抽提工艺技术路线选择
2.1 产品质量
由上表可见,NMP法和DMF法两种工艺技术 产品质量指标保证值一致,均能满足用户要 求。但ACN法由于溶剂的原因,处理炔烃能 力相对困难。虽然ACN法也能保证纯度在 99.5%,但采用国产化设计的国内装置较难 保证。采用引进的ACN技术,在保证产品纯 度满足顺丁橡胶装置的需要上也存在不确定 性。因此以下比较以NMP法和DMF法两种工 艺技术为主。
溶剂浓度70%
ACN(含水) DMF NMP(含水)
2.63
2.44
2.29
1.78
1.82
1.80
1.49
1.48
1.42
1.30
1.30