拉伸曲线、成形极限图介绍
拉伸曲线、成形极限图介绍

注:ok:最大力非比例伸长率; oL:最大力总伸长率; om:断后伸长率; on:断裂总伸长率。
11
12
成形极限图(FLD)或成形极限线(FLC)是评定金属板料 局部成形能力重要工具,在分析冲压成形的破裂问题时经 常使用。 FLD:冲压成形时,金属板料上缩颈或破裂区表面应变量称 为表面极限应变量。二维应变坐标系中,用不同应变路径 下表面极限应变量连成曲线或勾画出条带形区域称为冲压 成型时,成形极限曲线(Forming Limit Curve,缩写FLC), 极限应变量与极限曲线共同构成成形极限图(Forming Limit Diagram,缩写FLD) 。
1
2
下图为板材拉伸试样,左图为电子万能 拉伸试验机。将试样装在拉力试验机夹 头上,缓慢加载,通过自动记录装置得 到试样所受载荷P和伸长量△L的关系 曲线称为拉伸图(见下页)
3
P/kN
图中: P:载荷 △L:伸长量 由拉伸图向工程应力-应变曲 线转变的关键Байду номын сангаас式: ε= △L/L0 σ=P/A0 拉伸图
注:屈服强度σs为下屈服应力;当屈服平台不明显时, σs=ReL 取σ0.2(变形量为0.2%时对应的应力)为屈服强度。
8
σ=F/S0 σb
f
e
ε= △L/L0
第5阶段:塑性变形加工硬化阶 段(ef) 特点: (1)试样在塑性变形下产生加 工硬化,应力不断上升,均匀塑 性变形阶段; (2)f点:应力应变曲线的最高 点;对应的应力为抗拉强度σb; (3)加工硬化阶段和位错密度 增加有关,位错在外力作用下发 生交割、增殖、塞积,要使位错 继续滑移,需进一步提高外力;
13
成形极限图(FLD)
14
(4)加工硬化阶段是材料进行冷成型加工工艺的保证。
纤维的拉伸曲线特征
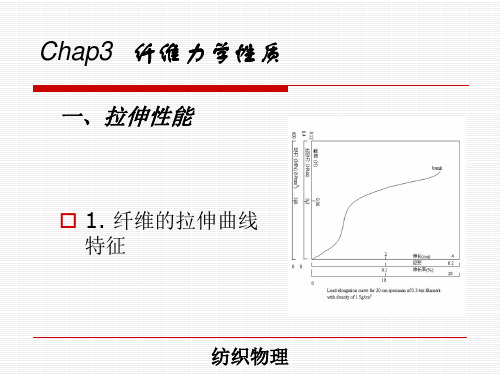
Chap3 纤维力学性质
疲劳
。 小应力长期作用下发生的破坏,就叫疲劳。这是一种最普遍的破坏形式
1
2
0
ab
O
d 5 4
c 3
e
P (a)定负荷 a P0 P0=const
b
O dc e
图5-28 纤维的多次拉伸循环
P (b)定伸长 a
0=const
b
Od c
e
0 0
纺织物理
图5-29 纤维的重 复拉伸疲劳图
0
0 0
cos
sin t
0
0 0
sin
cost
纺织物理
Chap3 纤维力学性质
令 有
0 cos E ' 0
0 sin E '' 0
E' 0 sin t
E '' 0 sin(t
)
2
' sin t '' sin(t )
2
式中E’为动态弹性模量;E’’ 为动态损耗模量。
外力消耗的功为:
t
式中,0为常数, =/E2。 (5) 多元件模型
纺织物理
Chap3 纤维力学性质
4. 玻尔兹曼叠加原理(线性粘弹性行为 的积分表达式)
提出:一物体在任何一瞬间所具有的形变 不仅与在这瞬间所加于物体上的负荷有关, 而且与整个负荷的历史有关;
每个阶段所施加的负荷对最终形变的贡献 是独立的,因此最终的形变是各阶段负荷 所贡献形变的简单加和。
100
纺织物理
Chap3 纤维力学性质
(2)初始模量 ——是指纤维拉伸曲线的起始部分直线段的应力与
应变的比值,即 - 曲线在起始段的斜率。
拉伸曲线分析
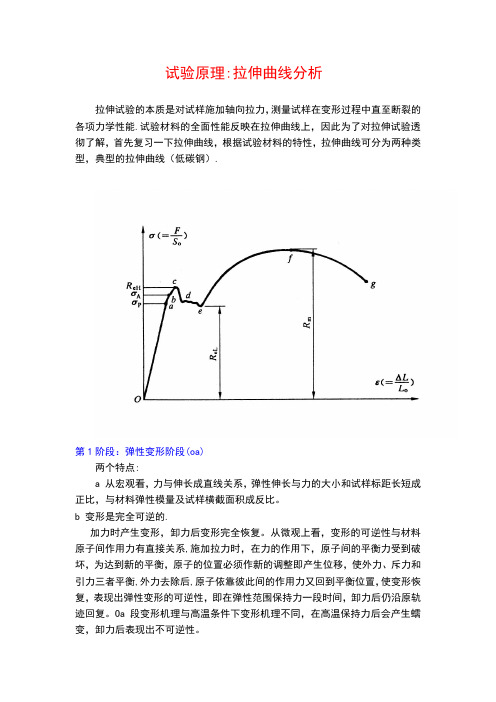
试验原理:拉伸曲线分析拉伸试验的本质是对试样施加轴向拉力,测量试样在变形过程中直至断裂的各项力学性能.试验材料的全面性能反映在拉伸曲线上,因此为了对拉伸试验透彻了解,首先复习一下拉伸曲线,根据试验材料的特性,拉伸曲线可分为两种类型,典型的拉伸曲线(低碳钢).第1阶段:弹性变形阶段(oa)两个特点:a 从宏观看,力与伸长成直线关系,弹性伸长与力的大小和试样标距长短成正比,与材料弹性模量及试样横截面积成反比。
b 变形是完全可逆的.加力时产生变形,卸力后变形完全恢复。
从微观上看,变形的可逆性与材料原子间作用力有直接关系,施加拉力时,在力的作用下,原子间的平衡力受到破坏,为达到新的平衡,原子的位置必须作新的调整即产生位移,使外力、斥力和引力三者平衡,外力去除后,原子依靠彼此间的作用力又回到平衡位置,使变形恢复,表现出弹性变形的可逆性,即在弹性范围保持力一段时间,卸力后仍沿原轨迹回复。
Oa段变形机理与高温条件下变形机理不同,在高温保持力后会产生蠕变,卸力后表现出不可逆性。
由于在拉伸试验中无论在加力或卸力期间应力和应变都保持单值线性关系,因此试验材料的弹性模量是oa段的斜率,用公式求得:E=σ/εoa线段的a点是应力-应变呈直线关系的最高点,这点的应力叫理论比例极限,超过a点,应力-应变则不再呈直线关系,即不再符合虎克定律。
比例极限的定义在理论上很有意义,它是材料从弹性变形向塑性变形转变的,但很难准确地测定出来,因为从直线向曲线转变的分界点与变形测量仪器的分辨力直接相关,仪器的分辨力越高,对微小变形显示的能力越强,测出的分界点越低,这也是为什麽在最近两版国家标准中取消了这项性能的测定,而用规定塑性(非比例)延伸性能代替的原因。
第2阶段:滞弹性阶段 (ab)在此阶段,应力-应变出现了非直线关系,其特点是:当力加到b点时然后卸除力,应变仍可回到原点,但不是沿原曲线轨迹回到原点,在不同程度上滞后于应力回到原点,形成一个闭合环,加力和卸力所表现的特性仍为弹性行为,只不过有不同程度的滞后,因此称为滞弹性阶段,这个阶段的过程很短。
成形极限曲线

成形极限曲线
成形极限曲线,也称为成形极限图,是用于描述物料变形行为的重要工具。
它是一个表格或曲线图,用于表示不同的力量和应变下的物料的变形极限。
成形极限曲线通常用于金属成形领域,可以帮助工程师确定以最小成本和最高效率完成生产所需的参数。
在本文中,将进一步探讨成形极限曲线的理解和应用。
首先,要理解成形极限曲线,必须知道两个概念,一是材料的应力,二是材料的应变。
应力是指外部施加的力对材料的内部反应。
应力以标量形式表示(单位为帕斯卡(Pa)),表示单位面积上的力。
而应变是指材料受到应力作用时发生的形变。
它也以标量形式表示,通常以百分比形式表示。
成形极限曲线表示不同应力和应变下材料的变形极限。
这是一个图表,包括两个轴,一个是应变,一个是应力。
通常,成形极限曲线的上下限由材料的断裂和钢板上的波纹所形成。
材料在达到其形变极限时,将变得脆性,并在达到一定应力值时出现波纹。
成形极限曲线可以用于研究材料在成形过程中的行为。
它可以帮助决定适当的材料选择和成形方法,以确保生产出的成品性能符合特定要求。
成形极限曲线还可以用于解释材料处于特定状态下的变形现象。
采用成形极限曲线可以让工程师对每个材料的可塑性有更深刻的理解,从而更好地预测材料在不同环境下的性能。
在实践中,成形极限曲线可以用于比较不同材料的性能,并确定最适合实际生产的材料。
成形极限曲线可以在钢铁工业中用于选择最适合生产具有特定强度和成品外观的钢板。
成形极限曲线还可以帮助工程师在制造车辆、零部件和工业设备等物品时进行材料选择。
金属拉伸曲线课件
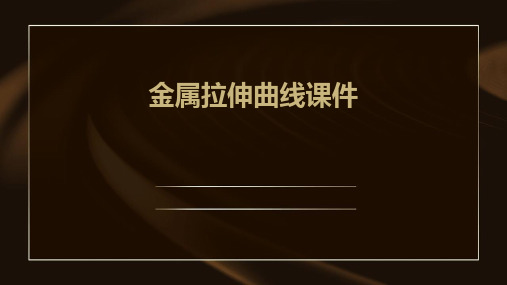
应用指导
金属拉伸曲线可以为实际工程应用提 供指导,例如在结构设计、选材等方 面提供依据。
通过对金属拉伸曲线的分析,可以优 化材料的加工工艺,提高产品的质量 和稳定性。
CHAPTER 02
金属拉伸曲线的形成原理
金属的晶体结构
晶体结构定义
金属的晶体结构是指金属内部原 子或分子的排列方式,决定了金
属的力学、物理和化学性质。
金属拉伸曲线课件
CONTENTS 目录
• 金属拉伸曲线的基本概念 • 金属拉伸曲线的形成原理 • 金属拉伸曲线的实验方法 • 金属拉伸曲线的应用实例 • 金属拉伸曲线的未来发展
CHAPTER 01
金属拉伸曲线的基本概念
金属拉伸曲线的定义
金属拉伸曲线
金属在拉伸过程中,应力与应变 之间的关系曲线。
常见晶体结构
常见的金属晶体结构有体心立方、 面心立方和密排六方等,不同的晶 体结构对金属的拉伸行为产生影响 。
晶体缺陷
在金属的晶体结构中,可能存在各 种缺陷,如空位、位错等,这些缺 陷会影响金属的塑性变形行为。
金属的塑性变形
塑性定义
金属的塑性是指金属在受到外力 作用时发生永久变形的特性。
塑性变形机制
金属制品的加工工艺优化
加工工艺参数优化
通过对金属拉伸曲线的分析,可以确定最佳的加工工艺参数,如拉伸速度、变 形程度等,以提高制品的质量和稳定性。
制品结构设计优化
根据金属拉伸曲线的变化规律,可以对制品的结构设计进行优化,以改善其受 力状况,提高制品的使用寿命。
新材料的研发与探索
新材料性能预测
通过模拟金属拉伸曲线,可以对新材料的基本性能进行预测,为新材料的研发提 供理论依据。
新材料探索与开发
拉伸试验曲线
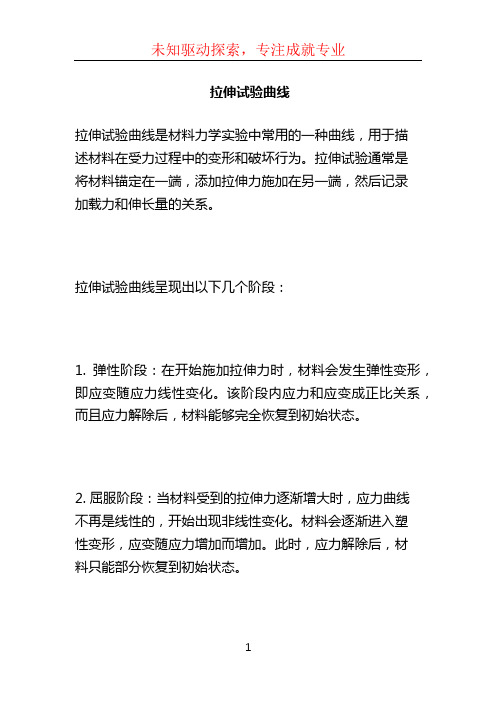
拉伸试验曲线可以通过加载力与伸长量的关系曲线图形来表示。该曲线可用于评估材料的强度、刚度、延性等力学性能,并分析材料的变形和破坏行为。
拉伸试验曲线是材料力学实验中常用的一种曲线,用于描述材料在受力过程中的变形和破坏行为。拉伸试验通常是将材料锚定在一端,添加拉伸力施加在另一端,然后记录加载力和伸长量的关系。
拉伸试验曲线呈现出以下几个阶段:
1. 弹性阶段:在开始施加拉伸力时,材料会发生弹性变形,即应变随应力线性变化。该阶段内应力和应变成正比关系,而且应力解除后,材料能够完全恢复到初始状态。
2. 屈服阶段:当材料受到的拉伸力逐渐增大时,应力曲线不再是线性的,开始出现非线性变化。材料会逐渐进入塑性变形,应变随应力增加而增加。此时,应力解除后,材料只能部分恢复到初始状态。
3. 极限阶段:当拉伸力进一步增加时,材料逐渐接近其极限强。在极限阶段,应力和应变之间关系较为复杂,材料可能发生局部变形和颈缩。
如何分析拉伸曲线
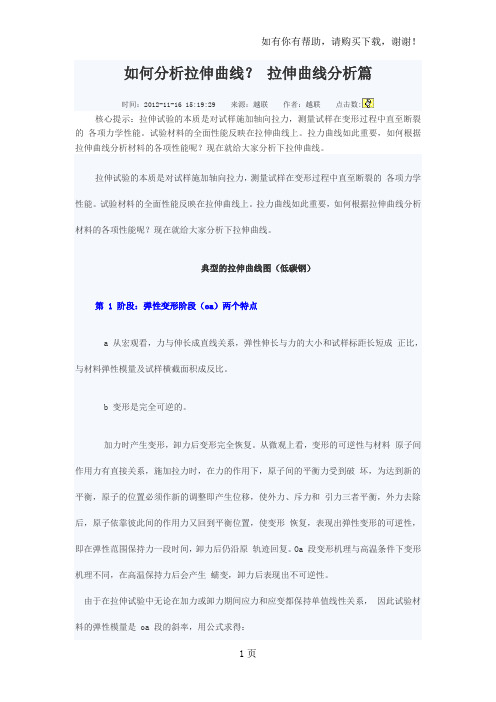
如何分析拉伸曲线?拉伸曲线分析篇时间:2012-11-16 15:19:29 来源:越联作者:越联点击数:核心提示:拉伸试验的本质是对试样施加轴向拉力,测量试样在变形过程中直至断裂的各项力学性能。
试验材料的全面性能反映在拉伸曲线上。
拉力曲线如此重要,如何根据拉伸曲线分析材料的各项性能呢?现在就给大家分析下拉伸曲线。
拉伸试验的本质是对试样施加轴向拉力,测量试样在变形过程中直至断裂的各项力学性能。
试验材料的全面性能反映在拉伸曲线上。
拉力曲线如此重要,如何根据拉伸曲线分析材料的各项性能呢?现在就给大家分析下拉伸曲线。
典型的拉伸曲线图(低碳钢)第 1 阶段:弹性变形阶段(oa)两个特点a 从宏观看,力与伸长成直线关系,弹性伸长与力的大小和试样标距长短成正比,与材料弹性模量及试样横截面积成反比。
b 变形是完全可逆的。
加力时产生变形,卸力后变形完全恢复。
从微观上看,变形的可逆性与材料原子间作用力有直接关系,施加拉力时,在力的作用下,原子间的平衡力受到破坏,为达到新的平衡,原子的位置必须作新的调整即产生位移,使外力、斥力和引力三者平衡,外力去除后,原子依靠彼此间的作用力又回到平衡位置,使变形恢复,表现出弹性变形的可逆性,即在弹性范围保持力一段时间,卸力后仍沿原轨迹回复。
Oa 段变形机理与高温条件下变形机理不同,在高温保持力后会产生蠕变,卸力后表现出不可逆性。
由于在拉伸试验中无论在加力或卸力期间应力和应变都保持单值线性关系,因此试验材料的弹性模量是 oa 段的斜率,用公式求得:E=σ/εoa 线段的 a 点是应力-应变呈直线关系的最高点,这点的应力叫理论比例极限,超过 a 点,应力-应变则不再呈直线关系,即不再符合虎克定律。
比例极限的定义在理论上很有意义,它是材料从弹性变形向塑性变形转变的,但很难准确地测定出来,因为从直线向曲线转变的分界点与变形测量仪器的分辨力直接相关,仪器的分辨力越高,对微小变形显示的能力越强,测出的分界点越低,这也是为什麽在最近两版国家标准中取消了这项性能的测定,而用规定塑性(非比例)延伸性能代替的原因。
成型极限曲线
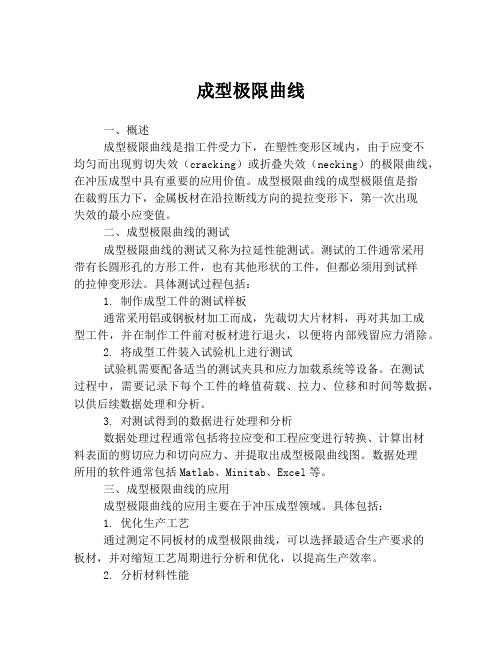
成型极限曲线一、概述成型极限曲线是指工件受力下,在塑性变形区域内,由于应变不均匀而出现剪切失效(cracking)或折叠失效(necking)的极限曲线,在冲压成型中具有重要的应用价值。
成型极限曲线的成型极限值是指在裁剪压力下,金属板材在沿拉断线方向的提拉变形下,第一次出现失效的最小应变值。
二、成型极限曲线的测试成型极限曲线的测试又称为拉延性能测试。
测试的工件通常采用带有长圆形孔的方形工件,也有其他形状的工件,但都必须用到试样的拉伸变形法。
具体测试过程包括:1. 制作成型工件的测试样板通常采用铝或钢板材加工而成,先裁切大片材料,再对其加工成型工件,并在制作工件前对板材进行退火,以便将内部残留应力消除。
2. 将成型工件装入试验机上进行测试试验机需要配备适当的测试夹具和应力加载系统等设备。
在测试过程中,需要记录下每个工件的峰值荷载、拉力、位移和时间等数据,以供后续数据处理和分析。
3. 对测试得到的数据进行处理和分析数据处理过程通常包括将拉应变和工程应变进行转换、计算出材料表面的剪切应力和切向应力、并提取出成型极限曲线图。
数据处理所用的软件通常包括Matlab、Minitab、Excel等。
三、成型极限曲线的应用成型极限曲线的应用主要在于冲压成型领域。
具体包括:1. 优化生产工艺通过测定不同板材的成型极限曲线,可以选择最适合生产要求的板材,并对缩短工艺周期进行分析和优化,以提高生产效率。
2. 分析材料性能不同材料的成型极限曲线各不相同,这也间接反映了材料的不同耐用性、适用范围和加工性能,并为材料和生产工艺的改进提供了信息。
3. 预测零件质量根据成型极限曲线,可以预测制造某一零件的质量和容忍误差,以便在生产过程中及时作出调整。
四、总结成型极限曲线是一个十分重要的概念,在工业生产中具有广泛的应用。
通过测试成型极限曲线,可以优化生产工艺、分析材料性能和预测零件质量等,对于提高生产效率和降低生产成本具有重要作用。
- 1、下载文档前请自行甄别文档内容的完整性,平台不提供额外的编辑、内容补充、找答案等附加服务。
- 2、"仅部分预览"的文档,不可在线预览部分如存在完整性等问题,可反馈申请退款(可完整预览的文档不适用该条件!)。
- 3、如文档侵犯您的权益,请联系客服反馈,我们会尽快为您处理(人工客服工作时间:9:00-18:30)。
7
σ=F/S0
ReH
c d e ReL
ε= △L/L0
第4阶段:屈服阶段(cde) 特点: (1)应力下降,应变增加; (2)Luders Band:在应力 达到c点时产生,试样表面沿 45 °度产生滑移带。 (3)c点:上屈服点 e点:屈服结束点 ce间最低点:下屈服点 (4)微观和Cottrell气团对位错 的定扎和反定扎有关。
注:ok:最大力非比例伸长率; oL:最大力总伸长率; om:断后伸长率; on:断裂总伸长率。
11
12
成形极限图(FLD)或成形极限线(FLC)是评定金属板料 局部成形能力重要工具,在分析冲压成形的破裂问题时经 常使用。 FLD:冲压成形时,金属板料上缩颈或破裂区表面应变量称 为表面极限应变量。二维应变坐标系中,用不同应变路径 下表面极限应变量连成曲线或勾画出条带形区域称为冲压 成型时,成形极限曲线(Forming Limit Curve,缩写FLC), 极限应变量与极限曲线共同构成成形极限图(Forming Limit Diagram,缩写FLD) 。
PS:弹性模量:微观上的意义是原子间的结合力的量度!
6
σ=F/S0 c ab
ReH σa σp
ε= △L/L0
第2阶段:滞弹性阶段(ab) 特点: (1)应力-应变出现非直线关 系; (2)当应力加载至b点后卸载, 仍可回到a点,但不再是直线关 系,而出现应变滞后应力,出现 闭合环。
第3阶段:微塑变阶段(bc) 特点:材料在屈服前发生微小的塑性变形。
△L/mm
其中: △L=L-L0 L:加载后标距间的长度 L0:原始标距 A0:原始横截面积
4
σ=F/S0 σb
f
k ReH σa c b a de ReL
σp
O
工程应力—应变曲线
ε= △L/L0
下面分6个阶段来介绍工程应力—应变图:
5
σ=F/S0
σP
a
o
ε= △L/L0
第1阶段:弹性变形阶段(oa) 特点: (1)应力—应变呈直线关系, 符合胡克定律; (2)a点:材料从弹性变形向 塑性变形的转变点,即比例极限。 (3)材料的弹性模量E: E=σ/ ε (4)弹性模量宏观上即是材料 的刚度,表征材料抵抗弹性变 形能力。
注:屈服强度σs为下屈服应力;当屈服平台不明显时, σs=ReL 取σ0.2(变形量为0.2%时对应的应力)为屈服强度。
8
σ=F/S0 σb
f
e
ε= △L/L0
第5阶段:塑性变形加工硬化阶 段(ef) 特点: (1)试样在塑性变形下产生加 工硬化,应力不断上升,均匀塑 性变形阶段; (2)f点:应力应变曲线的最高 点;对应的应力为抗拉强度σb; (3)加工硬化阶段和位错密度 增加有关,位错在外力作用下发 生交割、增殖、塞积,要使位错 继续滑移,需进一步提高外力;
(4)加工硬化阶段是材料进行冷成型加工工艺的保证。
9
板材在冲压的过程中,凹模弯曲角处变形最为严 重,首先产生加工硬化,提高了该处的强度,该 处变形到一定程度后就不再变形,而将变形转移 至其它部位,这样可以得到厚薄均匀的冲压钢板。
10
σ=F/S0 σb
f g
o
k
L
m
n ε= △L/L0
第6阶段:缩颈变形阶段(fg) 特点: (1)f点:加工硬化与几何软 化达到平衡; (2)不均匀塑性变形; (3)力不再增加,试样最薄弱 的截面出现微孔,连接扩散成小 裂纹,裂纹扩展,形成缩颈,最 终断裂。
1பைடு நூலகம்
2
下图为板材拉伸试样,左图为电子万能 拉伸试验机。将试样装在拉力试验机夹 头上,缓慢加载,通过自动记录装置得 到试样所受载荷P和伸长量△L的关系 曲线称为拉伸图(见下页)
3
P/kN
图中: P:载荷 △L:伸长量 由拉伸图向工程应力-应变曲 线转变的关键公式: ε= △L/L0 σ=P/A0 拉伸图
13
成形极限图(FLD)
14