机械毕业设计英文外文翻译83传动轴简介 (2)
轴类毕业设计英文翻译、外文文献翻译
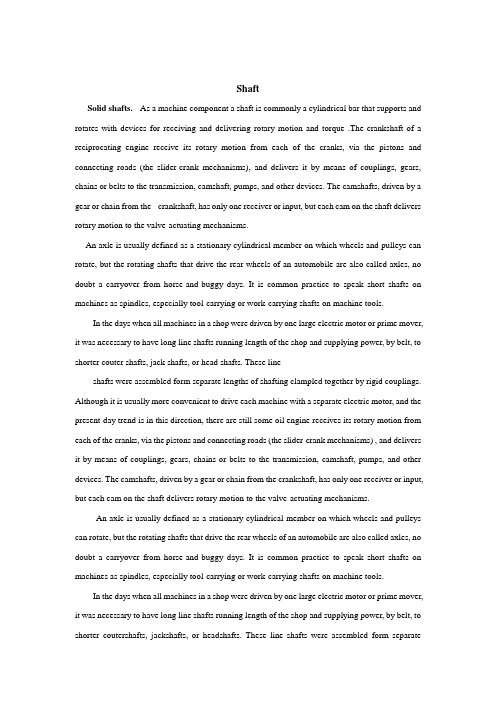
ShaftSolid shafts. As a machine component a shaft is commonly a cylindrical bar that supports and rotates with devices for receiving and delivering rotary motion and torque .The crankshaft of a reciprocating engine receive its rotary motion from each of the cranks, via the pistons and connecting roads (the slider-crank mechanisms), and delivers it by means of couplings, gears, chains or belts to the transmission, camshaft, pumps, and other devices. The camshafts, driven by a gear or chain from the crankshaft, has only one receiver or input, but each cam on the shaft delivers rotary motion to the valve-actuating mechanisms.An axle is usually defined as a stationary cylindrical member on which wheels and pulleys can rotate, but the rotating shafts that drive the rear wheels of an automobile are also called axles, no doubt a carryover from horse-and-buggy days. It is common practice to speak short shafts on machines as spindles, especially tool-carrying or work-carrying shafts on machine tools.In the days when all machines in a shop were driven by one large electric motor or prime mover, it was necessary to have long line shafts running length of the shop and supplying power, by belt, to shorter couter shafts, jack shafts, or head shafts. These lineshafts were assembled form separate lengths of shafting clampled together by rigid couplings. Although it is usually more convenient to drive each machine with a separate electric motor, and the present-day trend is in this direction, there are still some oil engine receives its rotary motion from each of the cranks, via the pistons and connecting roads (the slider-crank mechanisms) , and delivers it by means of couplings, gears, chains or belts to the transmission, camshaft, pumps, and other devices. The camshafts, driven by a gear or chain from the crankshaft, has only one receiver or input, but each cam on the shaft delivers rotary motion to the valve-actuating mechanisms.An axle is usually defined as a stationary cylindrical member on which wheels and pulleys can rotate, but the rotating shafts that drive the rear wheels of an automobile are also called axles, no doubt a carryover from horse-and-buggy days. It is common practice to speak short shafts on machines as spindles, especially tool-carrying or work-carrying shafts on machine tools.In the days when all machines in a shop were driven by one large electric motor or prime mover, it was necessary to have long line shafts running length of the shop and supplying power, by belt, to shorter coutershafts, jackshafts, or headshafts. These line shafts were assembled form separatelengths of shafting clampled together by rigid couplings. Although it is usually more convenient to drive each machine with a separate electric motor, and the present-day trend is in this direction, there are still some situation in which a group drive is more economical.A single-throw crankshaft that could be used in a single-cylinder reciprocating engine or pump is shown in Figure 21. The journals A andB rotate in the main bearings,C is the crankpin that fits in a bearing on the end of the connecting rod and moves on a circle of radius R about the main bearings, whileD andE are the cheeks or webs.The throw R is one half the stroks of the piston, which is connected, by the wrist pin, to the other end of the connecting rod and guided so as to move on a straight path passing throw the axis XX. On a multiple-cylinder engine the crankshaft has multiple throws---eight for a straight eight and for a V-8---arranged in a suitable angular relationship.Stress and strains. In operation, shafts are subjected to a shearing stress, whose magnitude depends on the torque and the dimensions of the cross section. This stress is a measure of resistance that the shaft material offers to the applied torque. All shafts that transmit a torque are subjected to torsional shearing stresses.In addition to the shearing stresses, twisted shafts are also subjected to shearing distortions. The distorted state is usually defined by the angle of twist per unit length; i.e., the retation of one cross section of a shaft relative to another cross section at a unit distance from it.Shafts that carry gears and pulleys are bent as well as twisted, and the magniude of the bending stresses, which are tensile on the convex side of the bend and compressive on the concave side, will depend on the load, the distance between the bearings of the shaft cross section.The combination of bending and twisting produces a state of stress in the shaft that is more complex than the state of pure shears produced by torsion alone or the state of tension-compression produced by bending alone.To the designer of shaft it is important to know if the shaft is likely to fail because of an excessive normal stress. If a piece of chalk is twisted, it will invariably rupture on a plane at about 45 degrees to the axis. This is because the maximum tensile stresses act on this plane, and chalk is weak in tension. Steel shafting is usually designed so that the maximum shearing stress produced by bending and torsion is less than a specified maximum.Shafts with circular cross sections are easier to produce in the steel mill, easier to machine, andeasier to support in bearings than shafts with other cross section; there is seldom any need for using noncircular shapes. In addition, the strength and stiffness, both in bending and torsion, are more easily calculated for circular shafts. Lastly, for a given amount of materials the circular shafts has the smallest maximum shearing stress for a given torque, and the highest torsional rigidity.The shearing in a circular shaft is highest at the surface and drops off to zero at the axis. This means that most of the torque is carried by the material on and near the surface.Critical speeds. In the same way that a violin string vibrates when stroked with a bow, a cylindrical shaft suspended between two bearings has a natural frequency of lateral vibration. If the speed of revolution of the shaft coincides with the natural frequency, the shaft experience a whirling critical speed and become noisy. These speeds are more likely to occur with long, flexible shafts than with short, stiff ones. The natural frequency of a shaft can be raised by increasing its stiffness.If a slender rod is fixed to the ceiling ta one end and supports a heavy disk at the other end, the disk will oscillate back and forth around the rod axis like a torsion pendulum if given an initial twist and let go. The frequency of the oscillations will depend on the torsional stiffness of the rod and the weight of the disk; the stiffer the rod and the lighter the disk the higher the frequency. Similar torsional oscillations can occur in the crankshafts of reciprocating engines, particularly those with many crank throws and a heavy flywheel. Each crank throw and part of the associated connecting rod acts like a small flywheel, and for the crankshaft as a whole, there are a number of ways or modes in which there small flywheels can oscillate back and forth around the shaft axis in opposition to one another and to the main flywheel. For each of these modes there corresponds a natural frequency of oscillation.When the engine is operating the torques delivered to the crankshaft by the connecting rods fluctuate, and if the crankshaft speed is such that these fluctuating impulses are delivered at a speed corresponding to one of the natural torsional frequencies of the shaft, torsional oscillations will be superimposed on the rotary motion of the shafts. Such speed are known as torsional critical speeds, and they can cause shaft failures. A number of devices to control the oscillations of crankshafts have been invented.Flexible shafts. A flexible shaft consists of a number of superimposed tightly wound right-and left-hand layers of helically wound wires wrapped about a single center wire or mandrel. The shaft is connected to source of power and the driven member by special fittings attached to the end of theshaft. Flexible easings of metallic or nonmetallic materials, which guide and protect the shaft and retain the lubricant, are also available. Compared with solid shafts, flexible shafts can be bent to much smaller radii without being overstressed.For transmitting power around corners and for considerable distances flexible shafts are usually cheaper and more convenient than belts, chains, or gears. Most speedometers on automobiles are driven by flexible shafts running from the transmission to the dashboard. When a valve, a switch, or other control devices is in a hard-to-reach location, it can be operated by a flexible shaft from a more convenient position. For portable tools such as sanders, grinders, and drilling machines, flexible shafts are practically indispensable.KEY, SPLINES AND PINSKeys, splines, and pins. When power is being transmitted from a machine member such as a coupling, a gear, a flywheel, or a pulley to the shaft on which it is mounted, means must be provided for preventing relative motion between the shaft and the member. On helical and bevel gears, relative movement along the shaft caused by the thrust(axial) loads is prevented by a step in the shaft or by having the gear contact the bearing directly or through a tubular spacer. When axial loads are incidental and of small magnitude, the members are kept from sliding along the shaft by means of a set screw. The primary purpose of keys, splines, and pins is to prevent relative rotary movement.A commonly used type of key has a square cross section and is sunk half in the shaft and half in the hub of the other member. If the key is made of steel(which is commonly the case)of the same strength as the shaft and has a width and depth equal to one fourth of the shaft diameter(this proportion is closely approximated in practice) then it will have the same torque capacity as the solid shaft if its length is 1.57 times that of the shaft diameter. Another common type of key has a rectangular cross section with a depth to width ratio of 0.75. Both of these keys may either be straight or tapered in depth. The straight keys fit snugly on the sides of the key ways only, the tapered keys on all sides. Gib-head keys are tapered keys with a projection on one end to facilitate removal.Woodruff keys are widely used on machine tools and motor vehicles. The key is a segment of adisk and fits in a keyway in the shaft that is with a special milling cutter. Though the extra depth of these keys weakens the shaft considerably, it prevents any tendency of the key to rotate or move axially. Woodruff keys are particularly suitable for tapering shaft ends.Because they weaken the shafts less, keys with straight or tapered circular cross sections are sometimes used in place of square and rectangular keys, but the keyways, half in the shaft and half in the shaft and half in the hub, must be cut with a drill after assembly,and interchangeability of parts is practically impossible. When a large gear blank is made by shrinking a high-strength rim on a cheaper cast center, circular keys, snugly fitted, are frequently used to ensure a permanent connection.Splines are permanent keys integral with the shaft, fitting in keyways cut in the hub. The dimensions of splined fittings are standardized for both permanent (press) fits and sliding fits. The teeth have either straight or involute profiles;the latter are stronger, more easily measured, and have a self-centring action when twisted.Tapered circular pins can be used to restrain shaft-mounted members from both axial and rotary movement. The pin fits snugly in a reamed tapered hole that is perpendicular to the shaft surface. A number of straight pins that grip by deforming elastically or plastically when driven into straight holes are commercially available.All the keys and pins that have been described are standard driving devices. In some cases they inadequate, and unorthodox means must be employed. For driving small gear in which there is no room between the bore and the roots of the teeth for a longitudinal keyway, a transverse radial slot on the end of the gear can be made to fit a radial protuberance on the shaft. For transmitting moderate loads, a cheaper and effective connection can be made by forming a series of longitudinal serrations on the shaft with a knurling tool and pressing the shaft into the hole in the driven member, it will cut grooves in the hole and provide, in effect, a press-fitted splined connection. Press and shrink fits are also used, and they can provide surprisingly firm connections, but the dimensions of the connected member must be closely controlled.轴实心轴轴作为机械零件通常是一根圆柱形杆,用来支撑部件并随部件一起转动以接受和传递转动和扭矩。
毕业设计论文外文文献翻译机械设计制造及其自动化轴承的摩擦与润滑中英文对照

Friction , Lubrication of BearingIn many of the problem thus far , the student has been asked to disregard or neglect friction . A ctually , friction is present to some degree whenever two parts are in contact and move on each other. The term friction refers to the resistance of two or more parts to movement.Friction is harmful or valuable depending upon where it occurs. friction is necessary for fastening devices such as screws and rivets which depend upon friction to hold the fastener and the parts together. Belt drivers, brakes, and tires are additional applications where friction is necessary.The friction of moving parts in a machine is harmful because it reduces the mechanical advantage of the device. The heat produced by friction is lost energy because no work takes place. A lso , greater power is required to overcome the increased friction. Heat is destructive in that it causes expansion. Expansion may cause a bearing or sliding surface to fit tighter. If a great enough pressure builds up because made from low temperature materials may melt.There are three types of friction which must be overcome in moving parts: (1)starting, (2)sliding,and(3)rolling. Starting friction is the friction between two solids that tend to resist movement. When two parts are at a state of rest, the surface irregularities of both parts tend to interlock and form a wedging action. T o produce motion in these parts, the wedge-shaped peaks and valleys of the stationary surfaces must be made to slide out and over each other. The rougher the two surfaces, the greater is starting friction resulting from their movement .Since there is usually no fixed pattern between the peaks and valleys of two mating parts, the irregularities do not interlock once the parts are in motion but slide over each other. The friction of the two surfaces is known as sliding friction. A s shown in figure ,starting friction is always greater than sliding friction .Rolling friction occurs when roller devces are subjected to tremendous stress which cause the parts to change shape or deform. Under these conditions, the material in front of a roller tends to pile up and forces the object to roll slightly uphill. This changing of shape , known as deformation, causes a movement of molecules. As a result ,heat is produced from the added energy required to keep the parts turning and overcome friction.The friction caused by the wedging action of surface irregularities can be overcome partly by the precision machining of the surfaces. However, even these smooth surfaces may require the use of a substance between them to reduce the friction still more. This substance is usually a lubricant which provides a fine, thin oil film. The film keeps the surfaces apart and prevents the cohesive forces of the surfaces from coming in close contact and producing heat .Another way to reduce friction is to use different materials for the bearing surfaces and rotating parts. This explains why bronze bearings, soft alloy s, and copper and tin iolite bearings are used with both soft andhardened steel shaft. The iolite bearing is porous. Thus, when the bearing is dipped in oil, capillary action carries the oil through the spaces of the bearing. This type of bearing carries its own lubricant to the points where the pressures are the greatest.Moving parts are lubricated to reduce friction, wear, and heat. The most commonly used lubricants are oils, greases, and graphite compounds. Each lubricant serves a different purpose. The conditions under which two moving surfaces are to work determine the type of lubricant to be used and the system selected for distributing the lubricant.On slow moving parts with a minimum of pressure, an oil groove is usually sufficient to distribute the required quantity of lubricant to the surfaces moving on each other .A second common method of lubrication is the splash system in which parts moving in a reservoir of lubricant pick up sufficient oil which is then distributed to all moving parts during each cycle. This system is used in the crankcase of lawn-mower engines to lubricate the crankshaft, connecting rod ,and parts of the piston.A lubrication system commonly used in industrial plants is the pressure system. In this system, a pump on a machine carries the lubricant to all of the bearing surfaces at a constant rate and quantity.There are numerous other sy stems of lubrication and a considerable number of lubricants available for any given set of operating conditions. Modern industry pays greater attention to the use of the proper lubricants than at previous time because of the increased speeds, pressures, and operating demands placed on equipment and devices.Although one of the main purposes of lubrication is reduce friction, any substance-liquid , solid , or gaseous-capable of controlling friction and wear between sliding surfaces can be classed as a lubricant.V arieties of lubricationUnlubricated sliding. Metals that have been carefully treated to remove all foreign materials seize and weld to one another when slid together. In the absence of such a high degree of cleanliness, adsorbed gases, water vapor ,oxides, and contaminants reduce frictio9n and the tendency to seize but usually result in severe wear。
机械专业中英文对照部分
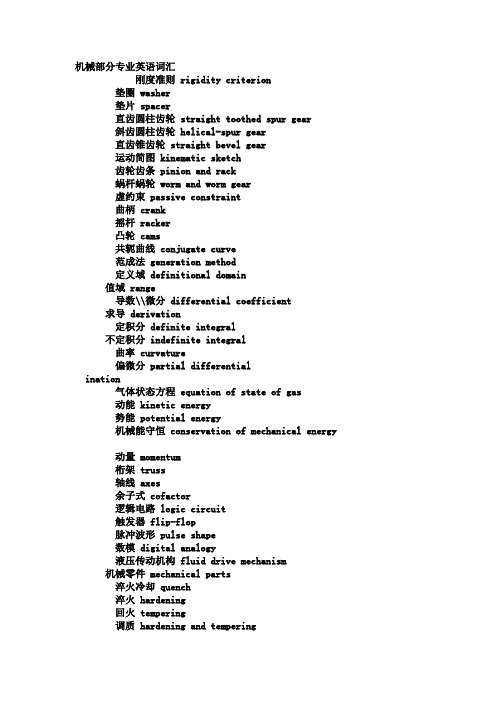
机械部分专业英语词汇刚度准则 rigidity criterion垫圈 washer垫片 spacer直齿圆柱齿轮 straight toothed spur gear斜齿圆柱齿轮 helical-spur gear直齿锥齿轮 straight bevel gear运动简图 kinematic sketch齿轮齿条 pinion and rack蜗杆蜗轮 worm and worm gear虚约束 passive constraint曲柄 crank摇杆 racker凸轮 cams共轭曲线 conjugate curve范成法 generation method定义域 definitional domain值域 range导数\\微分 differential coefficient求导 derivation定积分 definite integral不定积分 indefinite integral曲率 curvature偏微分 partial differentialination气体状态方程 equation of state of gas动能 kinetic energy势能 potential energy机械能守恒 conservation of mechanical energy动量 momentum桁架 truss轴线 axes余子式 cofactor逻辑电路 logic circuit触发器 flip-flop脉冲波形 pulse shape数模 digital analogy液压传动机构 fluid drive mechanism机械零件 mechanical parts淬火冷却 quench淬火 hardening回火 tempering调质 hardening and tempering磨粒 abrasive grain结合剂 bonding agent砂轮 grinding wheel后角 clearance angle龙门刨削 planing主轴 spindle主轴箱 headstock卡盘 chuck加工中心 machining center车刀 lathe tool车床 lathe钻削镗削 bore车削 turning磨床 grinder基准 benchmark钳工 locksmith锻 forge压模 stamping焊 weld拉床 broaching machine拉孔 broaching装配 assembling铸造 found流体动力学 fluid dynamics流体力学 fluid mechanics加工 machining液压 hydraulic pressure切线 tangent机电一体化 mechanotronics mechanical-electrical integration 气压 air pressure pneumatic pressure稳定性 stability介质 medium液压驱动泵 fluid clutch液压泵 hydraulic pump阀门 valve失效 invalidation强度 intensity载荷 load应力 stress安全系数 safty factor可靠性 reliability螺纹 thread螺旋 helix键 spline销 pin滚动轴承 rolling bearing滑动轴承 sliding bearing弹簧 spring制动器 arrester brake十字结联轴节 crosshead联轴器 coupling链 chain皮带 strap精加工 finish machining粗加工 rough machining变速箱体 gearbox casing腐蚀 rust氧化 oxidation磨损 wear耐用度 durability随机信号 random signal离散信号 discrete signal超声传感器 ultrasonic sensor集成电路 integrate circuit挡板 orifice plate残余应力 residual stress套筒 sleeve扭力 torsion冷加工 cold machining电动机 electromotor汽缸 cylinder过盈配合 interference fit热加工 hotwork摄像头 CCD camera倒角 rounding chamfer优化设计 optimal design工业造型设计 industrial moulding design 有限元 finite element滚齿 hobbing插齿 gear shaping伺服电机 actuating motor铣床 milling machine钻床 drill machine镗床 boring machine步进电机 stepper motor丝杠 screw rod导轨 lead rail组件 subassembly可编程序逻辑控制器 Programmable Logic Controller PLC 电火花加工 electric spark machining电火花线切割加工 electrical discharge wire - cutting 相图 phase diagram热处理 heat treatment固态相变 solid state phase changes有色金属 nonferrous metal陶瓷 ceramics合成纤维 synthetic fibre电化学腐蚀 electrochemical corrosion车架 automotive chassis悬架 suspension转向器 redirector变速器 speed changer板料冲压 sheet metal parts孔加工 spot facing machining车间 workshop工程技术人员 engineer气动夹紧 pneuma lock数学模型 mathematical model画法几何 descriptive geometry机械制图 Mechanical drawing投影 projection视图 view剖视图 profile chart标准件 standard component零件图 part drawing装配图 assembly drawing尺寸标注 size marking技术要求 technical requirements刚度 rigidity内力 internal force位移 displacement截面 section疲劳极限 fatigue limit断裂 fracture塑性变形 plastic distortion脆性材料 brittleness material刚度准则 rigidity criterion垫圈 washer垫片 spacer直齿圆柱齿轮 straight toothed spur gear斜齿圆柱齿轮 helical-spur gear直齿锥齿轮 straight bevel gear运动简图 kinematic sketch齿轮齿条 pinion and rack蜗杆蜗轮 worm and worm gear虚约束 passive constraint曲柄 crank摇杆 racker凸轮 cams共轭曲线 conjugate curve范成法 generation method定义域 definitional domain值域 range导数\\微分 differential coefficient求导 derivation定积分 definite integral不定积分 indefinite integral曲率 curvature偏微分 partial differential毛坯 rough游标卡尺 slide caliper千分尺 micrometer calipers攻丝 tap二阶行列式 second order determinant逆矩阵 inverse matrix线性方程组 linear equations概率 probability随机变量 random variable排列组合 permutation and combination气体状态方程 equation of state of gas动能 kinetic energy势能 potential energy机械能守恒 conservation of mechanical energy 动量 momentum桁架 truss轴线 axes余子式 cofactor逻辑电路 logic circuit触发器 flip-flop脉冲波形 pulse shape数模 digital analogy液压传动机构 fluid drive mechanism机械零件 mechanical parts淬火冷却 quench淬火 hardening回火 tempering调质 hardening and tempering磨粒 abrasive grain结合剂 bonding agent砂轮 grinding wheelAssembly line 组装线Layout 布置图Conveyer 流水线物料板Rivet table 拉钉机Rivet gun 拉钉枪Screw driver 起子Pneumatic screw driver 气动起子worktable 工作桌OOBA 开箱检查fit together 组装在一起fasten 锁紧(螺丝)fixture 夹具(治具)pallet 栈板barcode 条码barcode scanner 条码扫描器fuse together 熔合fuse machine热熔机repair修理operator作业员QC品管supervisor 课长ME 制造工程师MT 制造生技cosmetic inspect 外观检查inner parts inspect 内部检查thumb screw 大头螺丝lbs. inch 镑、英寸EMI gasket 导电条front plate 前板rear plate 后板chassis 基座bezel panel 面板power button 电源按键reset button 重置键Hi-pot test of SPS 高源高压测试Voltage switch of SPS 电源电压接拉键sheet metal parts 冲件plastic parts 塑胶件SOP 制造作业程序material check list 物料检查表work cell 工作间trolley 台车carton 纸箱sub-line 支线left fork 叉车personnel resource department 人力资源部production department生产部门planning department企划部QC Section品管科stamping factory冲压厂painting factory烤漆厂molding factory成型厂common equipment常用设备uncoiler and straightener整平机punching machine 冲床robot机械手hydraulic machine油压机lathe车床planer |plein|刨床miller铣床grinder磨床linear cutting线切割electrical sparkle电火花welder电焊机staker=reviting machine铆合机position职务president董事长general manager总经理special assistant manager特助factory director厂长department director部长deputy manager | =vice manager副理section supervisor课长deputy section supervisor =vice section superisor副课长group leader/supervisor组长line supervisor线长assistant manager助理to move, to carry, to handle搬运be put in storage入库pack packing包装to apply oil擦油to file burr 锉毛刺final inspection终检to connect material接料to reverse material 翻料wet station沾湿台Tiana天那水cleaning cloth抹布to load material上料to unload material卸料to return material/stock to退料scraped |\\'skr?pid|报废scrape ..v.刮;削deficient purchase来料不良manufacture procedure制程deficient manufacturing procedure制程不良oxidation |\\' ksi\\'dei?n|氧化scratch刮伤dents压痕defective upsiding down抽芽不良defective to staking铆合不良embedded lump镶块feeding is not in place送料不到位stamping-missing漏冲production capacity生产力education and training教育与训练proposal improvement提案改善spare parts=buffer备件forklift叉车trailer=long vehicle拖板车compound die合模die locker锁模器pressure plate=plate pinch压板bolt螺栓administration/general affairs dept总务部automatic screwdriver电动启子thickness gauge厚薄规gauge(or jig)治具power wire电源线buzzle蜂鸣器defective product label不良标签identifying sheet list标示单location地点present members出席人员subject主题conclusion结论decision items决议事项responsible department负责单位pre-fixed finishing date预定完成日approved by / checked by / prepared by核准/审核/承办PCE assembly production schedule sheet PCE组装厂生产排配表model机锺work order工令revision版次remark备注production control confirmation生产确认checked by初审approved by核准department部门stock age analysis sheet 库存货龄分析表on-hand inventory现有库存available material良品可使用obsolete material良品已呆滞to be inspected or reworked 待验或重工total合计cause description原因说明part number/ P/N 料号type形态item/group/class类别quality品质prepared by制表 notes说明year-end physical inventory difference analysis sheet 年终盘点差异分析表physical inventory盘点数量physical count quantity帐面数量difference quantity差异量cause analysis原因分析raw materials原料materials物料finished product成品semi-finished product半成品packing materials包材good product/accepted goods/ accepted parts/good parts良品defective product/non-good parts不良品disposed goods处理品warehouse/hub仓库on way location在途仓oversea location海外仓spare parts physical inventory list备品盘点清单spare molds location模具备品仓skid/pallet栈板tox machine自铆机wire EDM线割EDM放电机coil stock卷料sheet stock片料tolerance工差score=groove压线cam block滑块pilot导正筒trim剪外边pierce剪内边drag form压锻差pocket for the punch head挂钩槽slug hole废料孔feature die公母模expansion dwg展开图radius半径shim(wedge)楔子torch-flame cut火焰切割set screw止付螺丝form block折刀stop pin定位销round pierce punch=die button圆冲子shape punch=die insert异形子stock locater block定位块under cut=scrap chopper清角active plate活动板baffle plate挡块cover plate盖板male die公模female die母模groove punch压线冲子air-cushion eject-rod气垫顶杆spring-box eject-plate弹簧箱顶板bushing block衬套insert 入块club car高尔夫球车capability能力parameter参数factor系数phosphate皮膜化成viscosity涂料粘度alkalidipping脱脂main manifold主集流脉bezel斜视规blanking穿落模dejecting顶固模demagnetization去磁;消磁high-speed transmission高速传递heat dissipation热传 rack上料degrease脱脂rinse水洗alkaline etch龄咬desmut剥黑膜D.I. rinse纯水次Chromate铬酸处理Anodize阳性处理seal封孔revision版次part number/P/N料号good products良品scraped products报放心品defective products不良品finished products成品disposed products处理品barcode条码flow chart流程表单assembly组装stamping冲压molding成型spare parts=buffer备品coordinate座标dismantle the die折模auxiliary fuction辅助功能poly-line多义线heater band 加热片thermocouple热电偶sand blasting喷沙grit 砂砾derusting machine除锈机degate打浇口dryer烘干机induction感应induction light感应光response=reaction=interaction感应ram连杆edge finder巡边器concave凸convex凹short射料不足nick缺口speck瑕??shine亮班splay 银纹gas mark焦痕delamination起鳞cold slug冷块blush 导色gouge沟槽;凿槽satin texture段面咬花witness line证示线patent专利grit沙砾granule=peuet=grain细粒grit maker抽粒机cushion缓冲magnalium镁铝合金magnesium镁金metal plate钣金lathe车 mill锉plane刨grind磨drill铝boring镗blinster气泡fillet镶;嵌边through-hole form通孔形式voller pin formality滚针形式cam driver铡楔shank摸柄crank shaft曲柄轴augular offset角度偏差velocity速度production tempo生产进度现状torque扭矩spline=the multiple keys花键quenching淬火tempering回火annealing退火carbonization碳化tungsten high speed steel钨高速的moly high speed steel钼高速的organic solvent有机溶剂bracket小磁导liaison联络单volatile挥发性resistance电阻ion离子titrator滴定仪beacon警示灯coolant冷却液crusher破碎机阿基米德蜗杆 Archimedes worm安全系数 safety factor; factor of safety安全载荷 safe load凹面、凹度 concavity扳手 wrench板簧 flat leaf spring半圆键 woodruff key变形 deformation摆杆 oscillating bar摆动从动件 oscillating follower摆动从动件凸轮机构 cam with oscillating follower 摆动导杆机构 oscillating guide-bar mechanism摆线齿轮 cycloidal gear摆线齿形 cycloidal tooth profile摆线运动规律 cycloidal motion摆线针轮 cycloidal-pin wheel包角 angle of contact保持架 cage背对背安装 back-to-back arrangement背锥 back cone ; normal cone背锥角 back angle背锥距 back cone distance比例尺 scale比热容 specific heat capacity闭式链 closed kinematic chain闭链机构 closed chain mechanism臂部 arm变频器 frequency converters变频调速 frequency control of motor speed变速 speed change变速齿轮 change gear change wheel变位齿轮 modified gear变位系数 modification coefficient标准齿轮 standard gear标准直齿轮 standard spur gear表面质量系数 superficial mass factor表面传热系数 surface coefficient of heat transfer表面粗糙度 surface roughness并联式组合 combination in parallel并联机构 parallel mechanism并联组合机构 parallel combined mechanism并行工程 concurrent engineering并行设计 concurred design, CD不平衡相位 phase angle of unbalance不平衡 imbalance (or unbalance)不平衡量 amount of unbalance不完全齿轮机构 intermittent gearing波发生器 wave generator波数 number of waves补偿 compensation参数化设计 parameterization design, PD残余应力 residual stress操纵及控制装置 operation control device槽轮 Geneva wheel槽轮机构 Geneva mechanism ; Maltese cross槽数 Geneva numerate槽凸轮 groove cam侧隙 backlash差动轮系 differential gear train差动螺旋机构 differential screw mechanism差速器 differential常用机构 conventional mechanism; mechanism in common use 车床 lathe承载量系数 bearing capacity factor承载能力 bearing capacity成对安装 paired mounting尺寸系列 dimension series齿槽 tooth space齿槽宽 spacewidth齿侧间隙 backlash齿顶高 addendum齿顶圆 addendum circle齿根高 dedendum齿根圆 dedendum circle齿厚 tooth thickness齿距 circular pitch齿宽 face width齿廓 tooth profile齿廓曲线 tooth curve齿轮 gear齿轮变速箱 speed-changing gear boxes齿轮齿条机构 pinion and rack齿轮插刀 pinion cutter; pinion-shaped shaper cutter 齿轮滚刀 hob ,hobbing cutter齿轮机构 gear齿轮轮坯 blank齿轮传动系 pinion unit齿轮联轴器 gear coupling齿条传动 rack gear齿数 tooth number齿数比 gear ratio齿条 rack齿条插刀 rack cutter; rack-shaped shaper cutter齿形链、无声链 silent chain齿形系数 form factor齿式棘轮机构 tooth ratchet mechanism插齿机 gear shaper重合点 coincident points重合度 contact ratio冲床 punch传动比 transmission ratio, speed ratio传动装置 gearing; transmission gear传动系统 driven system传动角 transmission angle传动轴 transmission shaft串联式组合 combination in series串联式组合机构 series combined mechanism串级调速 cascade speed control创新 innovation creation创新设计 creation design垂直载荷、法向载荷 normal load唇形橡胶密封 lip rubber seal磁流体轴承 magnetic fluid bearing从动带轮 driven pulley从动件 driven link, follower从动件平底宽度 width of flat-face从动件停歇 follower dwell从动件运动规律 follower motion从动轮 driven gear粗线 bold line粗牙螺纹 coarse thread大齿轮 gear wheel打包机 packer打滑 slipping带传动 belt driving带轮 belt pulley带式制动器 band brake单列轴承 single row bearing单向推力轴承 single-direction thrust bearing单万向联轴节 single universal joint单位矢量 unit vector当量齿轮 equivalent spur gear; virtual gear当量齿数 equivalent teeth number; virtual number of teeth当量摩擦系数 equivalent coefficient of friction当量载荷 equivalent load刀具 cutter导数 derivative倒角 chamfer导热性 conduction of heat导程 lead导程角 lead angle等加等减速运动规律parabolic motion; constant acceleration and deceleration motion等速运动规律 uniform motion; constant velocity motion等径凸轮 conjugate yoke radial cam等宽凸轮 constant-breadth cam等效构件 equivalent link等效力 equivalent force等效力矩 equivalent moment of force等效量 equivalent等效质量 equivalent mass等效转动惯量 equivalent moment of inertia等效动力学模型 dynamically equivalent model底座 chassis低副 lower pair点划线 chain dotted line(疲劳)点蚀 pitting垫圈 gasket垫片密封 gasket seal碟形弹簧 belleville spring顶隙 bottom clearance定轴轮系 ordinary gear train; gear train with fixed axes动力学 dynamics动密封 kinematical seal动能 dynamic energy动力粘度 dynamic viscosity动力润滑 dynamic lubrication动平衡 dynamic balance动平衡机 dynamic balancing machine动态特性 dynamic characteristics动态分析设计 dynamic analysis design动压力 dynamic reaction动载荷 dynamic load端面 transverse plane端面参数 transverse parameters端面齿距 transverse circular pitch端面齿廓 transverse tooth profile端面重合度 transverse contact ratio端面模数 transverse module端面压力角 transverse pressure angle锻造 forge对称循环应力 symmetry circulating stress对心滚子从动件 radial (or in-line ) roller follower对心直动从动件 radial (or in-line ) translating follower对心移动从动件 radial reciprocating follower对心曲柄滑块机构 in-line slider-crank (or crank-slider) mechanism 多列轴承 multi-row bearing多楔带 poly V-belt多项式运动规律 polynomial motion多质量转子 rotor with several masses惰轮 idle gear额定寿命 rating life额定载荷 load ratingII 级杆组 dyad发生线 generating line发生面 generating plane法面 normal plane法面参数 normal parameters法面齿距 normal circular pitch法面模数 normal module法面压力角 normal pressure angle法向齿距 normal pitch法向齿廓 normal tooth profile法向直廓蜗杆 straight sided normal worm法向力 normal force反馈式组合 feedback combining反向运动学 inverse ( or backward) kinematics反转法 kinematic inversion反正切 Arctan范成法 generating cutting仿形法 form cutting方案设计、概念设计 concept design, CD防振装置 shockproof device飞轮 flywheel飞轮矩 moment of flywheel非标准齿轮 nonstandard gear非接触式密封 non-contact seal非周期性速度波动 aperiodic speed fluctuation非圆齿轮 non-circular gear粉末合金 powder metallurgy分度线 reference line; standard pitch line分度圆 reference circle; standard (cutting) pitch circle 分度圆柱导程角 lead angle at reference cylinder分度圆柱螺旋角 helix angle at reference cylinder分母 denominator分子 numerator分度圆锥 reference cone; standard pitch cone分析法 analytical method封闭差动轮系 planetary differential复合铰链 compound hinge复合式组合 compound combining复合轮系 compound (or combined) gear train复合平带 compound flat belt复合应力 combined stress复式螺旋机构 Compound screw mechanism复杂机构 complex mechanism杆组 Assur group干涉 interference刚度系数 stiffness coefficient刚轮 rigid circular spline钢丝软轴 wire soft shaft刚体导引机构 body guidance mechanism刚性冲击 rigid impulse (shock)刚性转子 rigid rotor刚性轴承 rigid bearing刚性联轴器 rigid coupling高度系列 height series高速带 high speed belt高副 higher pair格拉晓夫定理 Grashoff`s law根切 undercutting公称直径 nominal diameter高度系列 height series功 work工况系数 application factor工艺设计 technological design工作循环图 working cycle diagram工作机构 operation mechanism工作载荷 external loads工作空间 working space工作应力 working stress工作阻力 effective resistance工作阻力矩 effective resistance moment公法线 common normal line公共约束 general constraint公制齿轮 metric gears功率 power功能分析设计 function analyses design共轭齿廓 conjugate profiles共轭凸轮 conjugate cam构件 link鼓风机 blower固定构件 fixed link; frame固体润滑剂 solid lubricant关节型操作器 jointed manipulator惯性力 inertia force惯性力矩 moment of inertia ,shaking moment惯性力平衡 balance of shaking force惯性力完全平衡 full balance of shaking force惯性力部分平衡 partial balance of shaking force 惯性主矩 resultant moment of inertia惯性主失 resultant vector of inertia冠轮 crown gear广义机构 generation mechanism广义坐标 generalized coordinate轨迹生成 path generation轨迹发生器 path generator滚刀 hob滚道 raceway滚动体 rolling element滚动轴承 rolling bearing滚动轴承代号 rolling bearing identification code 滚针 needle roller滚针轴承 needle roller bearing滚子 roller滚子轴承 roller bearing滚子半径 radius of roller滚子从动件 roller follower滚子链 roller chain滚子链联轴器 double roller chain coupling滚珠丝杆 ball screw滚柱式单向超越离合器 roller clutch过度切割 undercutting函数发生器 function generator函数生成 function generation含油轴承 oil bearing耗油量 oil consumption耗油量系数 oil consumption factor赫兹公式 H. Hertz equation合成弯矩 resultant bending moment合力 resultant force合力矩 resultant moment of force黑箱 black box横坐标 abscissa互换性齿轮 interchangeable gears花键 spline滑键、导键 feather key滑动轴承 sliding bearing滑动率 sliding ratio滑块 slider环面蜗杆 toroid helicoids worm环形弹簧 annular spring缓冲装置 shocks; shock-absorber灰铸铁 grey cast iron回程 return回转体平衡 balance of rotors混合轮系 compound gear train积分 integrate机电一体化系统设计 mechanical-electrical integration system design 机构 mechanism机构分析 analysis of mechanism机构平衡 balance of mechanism机构学 mechanism机构运动设计 kinematic design of mechanism机构运动简图 kinematic sketch of mechanism机构综合 synthesis of mechanism机构组成 constitution of mechanism机架 frame, fixed link机架变换 kinematic inversion机器 machine机器人 robot机器人操作器 manipulator机器人学 robotics技术过程 technique process技术经济评价 technical and economic evaluation技术系统 technique system机械 machinery机械创新设计 mechanical creation design, MCD机械系统设计 mechanical system design, MSD机械动力分析 dynamic analysis of machinery机械动力设计 dynamic design of machinery机械动力学 dynamics of machinery机械的现代设计 modern machine design机械系统 mechanical system机械利益 mechanical advantage机械平衡 balance of machinery机械手 manipulator机械设计 machine design; mechanical design机械特性 mechanical behavior机械调速 mechanical speed governors机械效率 mechanical efficiency机械原理 theory of machines and mechanisms机械运转不均匀系数 coefficient of speed fluctuation机械无级变速 mechanical stepless speed changes基础机构 fundamental mechanism基本额定寿命 basic rating life基于实例设计 case-based design,CBD基圆 base circle基圆半径 radius of base circle基圆齿距 base pitch基圆压力角 pressure angle of base circle基圆柱 base cylinder基圆锥 base cone急回机构 quick-return mechanism急回特性 quick-return characteristics急回系数 advance-to return-time ratio急回运动 quick-return motion棘轮 ratchet棘轮机构 ratchet mechanism棘爪 pawl极限位置 extreme (or limiting) position极位夹角 crank angle between extreme (or limiting) positions 计算机辅助设计 computer aided design, CAD计算机辅助制造 computer aided manufacturing, CAM计算机集成制造系统 computer integrated manufacturing system, CIMS 计算力矩 factored moment; calculation moment计算弯矩 calculated bending moment加权系数 weighting efficient加速度 acceleration加速度分析 acceleration analysis加速度曲线 acceleration diagram尖点 pointing; cusp尖底从动件 knife-edge follower间隙 backlash间歇运动机构 intermittent motion mechanism减速比 reduction ratio减速齿轮、减速装置 reduction gear减速器 speed reducer减摩性 anti-friction quality渐开螺旋面 involute helicoid渐开线 involute渐开线齿廓 involute profile渐开线齿轮 involute gear渐开线发生线 generating line of involute渐开线方程 involute equation渐开线函数 involute function渐开线蜗杆 involute worm渐开线压力角 pressure angle of involute渐开线花键 involute spline简谐运动 simple harmonic motion键 key键槽 keyway交变应力 repeated stress交变载荷 repeated fluctuating load交叉带传动 cross-belt drive交错轴斜齿轮 crossed helical gears胶合 scoring角加速度 angular acceleration角速度 angular velocity角速比 angular velocity ratio角接触球轴承 angular contact ball bearing角接触推力轴承 angular contact thrust bearing角接触向心轴承 angular contact radial bearing角接触轴承 angular contact bearing铰链、枢纽 hinge校正平面 correcting plane接触应力 contact stress接触式密封 contact seal阶梯轴 multi-diameter shaft结构 structure结构设计 structural design截面 section节点 pitch point节距 circular pitch; pitch of teeth节线 pitch line节圆 pitch circle节圆齿厚 thickness on pitch circle节圆直径 pitch diameter节圆锥 pitch cone节圆锥角 pitch cone angle解析设计 analytical design紧边 tight-side紧固件 fastener径节 diametral pitch径向 radial direction径向当量动载荷 dynamic equivalent radial load径向当量静载荷 static equivalent radial load径向基本额定动载荷 basic dynamic radial load rating 径向基本额定静载荷 basic static radial load tating 径向接触轴承 radial contact bearing径向平面 radial plane径向游隙 radial internal clearance径向载荷 radial load径向载荷系数 radial load factor径向间隙 clearance静力 static force静平衡 static balance静载荷 static load静密封 static seal局部自由度 passive degree of freedom矩阵 matrix矩形螺纹 square threaded form锯齿形螺纹 buttress thread form矩形牙嵌式离合器 square-jaw positive-contact clutch 绝对尺寸系数 absolute dimensional factor绝对运动 absolute motion绝对速度 absolute velocity均衡装置 load balancing mechanism抗压强度 compression strength开口传动 open-belt drive开式链 open kinematic chain开链机构 open chain mechanism可靠度 degree of reliability可靠性 reliability可靠性设计 reliability design, RD空气弹簧 air spring空间机构 spatial mechanism空间连杆机构 spatial linkage空间凸轮机构 spatial cam空间运动副 spatial kinematic pair空间运动链 spatial kinematic chain空转 idle宽度系列 width series框图 block diagram雷诺方程Reynolds‘s equation离心力 centrifugal force离心应力 centrifugal stress离合器 clutch离心密封 centrifugal seal理论廓线 pitch curve理论啮合线 theoretical line of action隶属度 membership力 force力多边形 force polygon力封闭型凸轮机构 force-drive (or force-closed) cam mechanism 力矩 moment力平衡 equilibrium力偶 couple力偶矩 moment of couple连杆 connecting rod, coupler连杆机构 linkage连杆曲线 coupler-curve连心线 line of centers链 chain链传动装置 chain gearing链轮 sprocket sprocket-wheel sprocket gear chain wheel联组 V 带 tight-up V belt联轴器 coupling shaft coupling两维凸轮 two-dimensional cam临界转速 critical speed六杆机构 six-bar linkage龙门刨床 double Haas planer轮坯 blank轮系 gear train螺杆 screw螺距 thread pitch螺母 screw nut螺旋锥齿轮 helical bevel gear螺钉 screws螺栓 bolts螺纹导程 lead螺纹效率 screw efficiency螺旋传动 power screw螺旋密封 spiral seal螺纹 thread (of a screw)螺旋副 helical pair螺旋机构 screw mechanism螺旋角 helix angle螺旋线 helix ,helical line绿色设计 green design design for environment马耳他机构 Geneva wheel Geneva gear马耳他十字 Maltese cross脉动无级变速 pulsating stepless speed changes脉动循环应力 fluctuating circulating stress脉动载荷 fluctuating load铆钉 rivet迷宫密封 labyrinth seal密封 seal密封带 seal belt密封胶 seal gum密封元件 potted component密封装置 sealing arrangement面对面安装 face-to-face arrangement面向产品生命周期设计 design for product`s life cycle, DPLC 名义应力、公称应力 nominal stress模块化设计 modular design, MD模块式传动系统 modular system模幅箱 morphology box模糊集 fuzzy set模糊评价 fuzzy evaluation模数 module摩擦 friction摩擦角 friction angle摩擦力 friction force摩擦学设计 tribology design, TD摩擦阻力 frictional resistance摩擦力矩 friction moment摩擦系数 coefficient of friction摩擦圆 friction circle磨损 abrasion wear; scratching末端执行器 end-effector目标函数 objective function耐腐蚀性 corrosion resistance耐磨性 wear resistance挠性机构 mechanism with flexible elements挠性转子 flexible rotor内齿轮 internal gear内齿圈 ring gear内力 internal force内圈 inner ring能量 energy能量指示图 viscosity逆时针 counterclockwise (or anticlockwise)啮出 engaging-out啮合 engagement, mesh, gearing啮合点 contact points啮合角 working pressure angle啮合线 line of action啮合线长度 length of line of action啮入 engaging-in牛头刨床 shaper凝固点 freezing point; solidifying point扭转应力 torsion stress扭矩 moment of torque扭簧 helical torsion spring诺模图 NomogramO 形密封圈密封 O ring seal盘形凸轮 disk cam盘形转子 disk-like rotor抛物线运动 parabolic motion疲劳极限 fatigue limit疲劳强度 fatigue strength偏置式 offset偏 ( 心 ) 距 offset distance偏心率 eccentricity ratio偏心质量 eccentric mass偏距圆 offset circle偏心盘 eccentric偏置滚子从动件 offset roller follower偏置尖底从动件 offset knife-edge follower偏置曲柄滑块机构 offset slider-crank mechanism 拼接 matching评价与决策 evaluation and decision频率 frequency平带 flat belt平带传动 flat belt driving平底从动件 flat-face follower平底宽度 face width平分线 bisector平均应力 average stress平均中径 mean screw diameter平均速度 average velocity平衡 balance平衡机 balancing machine平衡品质 balancing quality平衡平面 correcting plane平衡质量 balancing mass平衡重 counterweight平衡转速 balancing speed平面副 planar pair, flat pair平面机构 planar mechanism平面运动副 planar kinematic pair平面连杆机构 planar linkage平面凸轮 planar cam平面凸轮机构 planar cam mechanism平面轴斜齿轮 parallel helical gears普通平键 parallel key其他常用机构 other mechanism in common use起动阶段 starting period启动力矩 starting torque气动机构 pneumatic mechanism奇异位置 singular position起始啮合点 initial contact , beginning of contact气体轴承 gas bearing千斤顶 jack嵌入键 sunk key强迫振动 forced vibration切齿深度 depth of cut曲柄 crank曲柄存在条件 Grashoff`s law曲柄导杆机构 crank shaper (guide-bar) mechanism曲柄滑块机构 slider-crank (or crank-slider) mechanism 曲柄摇杆机构 crank-rocker mechanism曲齿锥齿轮 spiral bevel gear曲率 curvature曲率半径 radius of curvature曲面从动件 curved-shoe follower曲线拼接 curve matching。
机械外文翻译---关于轴承和轴的相关知识

附录一Knowledge On The Bearings and ShaftThe bearings are fixed and reduce the load coefficient of friction in the process of mechanical transmission components. Can also say that when the other parts on the shaft relative motion, used to reduce the friction coefficient in the process of power transfer and fixed the mechanical parts to maintain the position of the shaft center. Bearings are important parts of modern machinery and equipment. Its main function is to support the mechanical rotating body to reduce the load coefficient of friction of the mechanical equipment in the transmission process. According to the different nature of friction of moving parts, bearings can be divided into two types of rolling bearings and plain bearings.Nano Lake, Italy, found a Roman vessel discovered early instance of ball bearings. The wooden ball bearings are used to support the rotating desktop. Ship construction in 40 BC. It is said that Leonardo da Vinci in the 1500 or so, a ball bearing through description. , There is a very important point is the ball collision, causing additional friction between the ball bearings of all kinds of immature factors. But can put the ball into a small cage to prevent this phenomenon. The 17th century, Galileo fixed ball ", or" cage ball "ball bearings did the earliest description. But then quite a long time, the bearings have been installed on the machine. The first patent on the ball channel the Carmarthen Philip Vaughan in 1794.In 1883, Friedrich Fischer proposed the idea of the use of suitable production machine grinding the same size, roundness accurate ball. This laid the foundation to create an independent bearing industry. In 1962, FAG the trademark has been modified and are still used today and become an integral part of the company in 1979.In 1895, Henry Timken designed the first tapered roller bearings, three years later obtained a patent and the establishment of the Timken Company.In 1907, SKF bearing factory Sven temperature Qwest designed the first modern self-aligning ball bearings.Study its role should be in terms of support, that the literal interpretation is used to bearing axis, but this is only part of its role in supporting its essence is to be able to bear the radial load. Can also be understood that it is used to a fixed axis. A fixed axis so that it can only achieverotation, and control of axial and radial movement. Motor without bearing the consequences is not work at all. Because the axis may be in any direction movement, the motor work requirements shaft only rotation. Impossible to realize the role of the drive, in theory, not only that, bearing also affect the transmission must be achieved in order to reduce this effect in the high speed shaft bearing lubrication, and some bearing lubrication, called pre-lubricated bearings, and the most of the bearing lubricant, the load at high speeds, due to the friction will not only increase energy consumption, even worse, is very easy to damage the bearing. Sliding friction into rolling friction is one-sided to say things because of the kind called plain bearings.Bearing the classification and described as follows:Equipped with a thin and long roller needle bearing (the length of the roller diameter of 3 to 10 times the diameter of generally not more than 5mm), therefore the radial structure is compact, its inner diameter and load capacity with other types of bearing the same minimum outside diameter, especially for supporting the results of radial installation dimensions restricted. needle bearing according to the use of different occasions, can be used without inner ring bearings or needle roller and cage assembly and bearing to match the journal surface directly as a bearing surface and shell holes, outer rolling surface in order to ensure the load capacity and running performance with a ring bearing the same shaft or shell holes on the raceway surface of the hardness, the machining accuracy and surface quality should be the bearing rings. use Combined needle roller bearings to the heart needle roller bearings and thrust bearing parts bearing units of the combination of its compact size, small, high precision rotation, can withstand high radial load to bear certain axial load. And the product structure in various forms, wide adaptability, easy to install. Combined needle roller bearings are widely used in machine tools, metallurgical machinery, textile machinery, printing machinery and other machinery and equipment, and make the mechanical system design is very compact and nimble.Aligning ball bearings Self-aligning ball bearings: two of the inner ring raceway and the raceway between the spherical outer ring, the assembly of the drum-shaped roller bearing. The outer ring raceway curvature center and bearing center line, and therefore have the same aligning and self-aligning ball bearings. Axis, the shell deflection occurs, you can automatically adjust to not increase the burden of bearing. Spherical roller bearings can bear radial load and axial load in two directions. Aligning ball bearing radial load capacity, suitable for a heavy impact loadconditions. The inner diameter is tapered bore bearings can be installed directly. Or use the adapter sleeve, remove the tube installed in the cylinder axis. Cage the use of steel stamping cage, forming polyamide-aligning ball bearings withstand heavy loads and impact loads, precision instruments, low noise motors, automobiles, motorcycles, metallurgy, mill, mining, petroleum, paper, cement, pressed sugar industry and the general machinery.Deep groove ball bearings imported bearings are mainly used for pure radial load, both radial and axial load. Only under pure radial load, the contact angle is zero. Performance of angular contact bearings, deep groove ball bearings with a larger radial clearance, and is subjected to high axial load. Deep groove ball bearings, the friction coefficient is small, the limit speed is also high, especially in a large high-speed operation of the axial load conditions, deep groove ball bearings Thrust ball bearings are more advantages. Deep groove ball bearings are the most representative of the rolling bearings, widely used. For high speed or high speed operation, and is very durable, without regular maintenance. The class has a small coefficient of friction, high limiting speed, simple structure, low manufacturing cost, easy to achieve high manufacturing precision. Size range and diversity, changes in the form used in precision instruments, low noise motors, automobiles, motorcycles and general machinery and other industries, is the machinery industry's most widely used type of bearings. The main radial load, and can withstand a certain amount of axial load deep groove ball bearings can be used for the transmission, instrumentation, motors, appliances, internal combustion engines, transportation vehicles, agricultural machinery, construction machinery, construction machinery and so on.Aligning roller bearing is a spherical outer ring between the two raceways of the inner ring raceway assembly with drum-shaped roller bearings. Aligning roller bearing with two rollers, mainly exposed to the diameter of a load, but also able to withstand the axial load in either direction. High radial load capacity, especially suitable for work overload or vibration loads, but can not afford the pure axial load. This kind of bearing outer ring raceway is spherical shape, aligning performance is good, can compensate concentricity error. Spherical roller bearings have two symmetrical spherical roller outer ring of a common spherical raceway, two bearing axis of inner ring tilt angle of the raceway, has a good aligning properties, when the axis force bearing when bending or install a different heart to continue its normal use, tune concentric with the bearing dimension series vary, generally allow aligning angle of 2.5 degrees, the type of loadbearing capacity, in addition to radial loads The outer bearings can withstand axial load of the two-way role, with good impact resistance, in general, self-aligning roller bearings allowed speed is low. Spherical roller bearings according to the section shape of the roller is divided into two different structures of the symmetrical spherical roller and non-symmetrical spherical roller, asymmetric self-aligning roller bearings are early products, mainly the host repair services, new design host rarely use symmetrical self-aligning roller bearings, the internal structure of the overall improvement of the design and parameters optimization, than with the early production of aligning roller bearings, able to withstand greater axial load, this bearing run lower temperatures, it can adapt to the requirements of high speed, according to whether the inner rib and cage can be divided into two kinds of C and CA, C-type bearing is characterized by the inner wall and the use of steel stamping frame, the CA-bearing characteristics for the inner ring on both sides have ribs machined solid cage in order to improve the lubrication, can provide users with the outer ring with a circular tank, and three hole Spherical roller bearings, set the code to the bearings / W33 can also supply according to the requirements of users with the inner hole of the aligning roller bearings, in order to facilitate customer handling and replacement of bearings, can also be provided within the hole with a taper aligning roller bearings, bearings, tapered bore, taper 1:12 after the set, code-named K, in order to adapt to specific user requirements can also be provided within the taper bearings of 1:30, followed by the set, code-named K30 hole with The taper of the bearing can be used locknut bearing mounted on the conical journal, but also can make use of the adapter sleeve or withdrawal sleeve bearings installed in the cylindrical journal.Combination of bearing: a bearing formed by the combination of bearing structure in the above-mentioned two or more of rolling bearings. Such as needle roller and cylindrical roller thrust bearings, needle roller and thrust ball bearings, needle roller and angular contact ball bearings, etc..Bearing life: under certain loads, the bearings in the number of revolutions or hours before pitting experienced, known as the bearing life.The life of rolling bearings of the number of revolutions (or number of hours worked under a certain speed) is defined: In this life within the bearing, any bearing ring or rolling body on the initial fatigue damage (spalling or defect). But both in the laboratory tests or in actual use, can clearly see the appearance of the same bearing in the same working conditions, to differ materiallyfrom actual life. In addition to the bearing of several different definitions of "life", one of the so-called "working life", it means that the actual life of a bearing can be achieved before the damage from the wear and tear, damage is usually not caused by fatigue, but caused by wear and tear, corrosion, seal damage.Due to differences in manufacturing precision, material uniformity, even if the same material, bearing the same batch of the same size, in the same working conditions, their longevity is not the same. In terms of statistical life is 1 unit relative life expectancy of up to four units, the shortest was 0.1 to 0.2 units, the ratio of the longest and shortest life of 20 to 40 times.The installation of bearings:Bearing installation, good or bad, will affect the accuracy, bearing life and performance. , The installation of the bearing, in accordance with the operating standards include the following items, including the bearing installation.①cleaning bearings and related parts have been greased bearings and bilateral withseals or dust cover, no need to clean before the installation of the ring bearing.② Check the size and finishing conditions of the relevant parts of the③installation method bearing installation should be based on the nature of the bearing structure, size, and bearing components with pressure should be directly added to a tight fit to the ferrule end surface, may not pass the pressure of the rolling element bearing installation generally use the following method: a press-fit bearing inner ring and shaft so tight fit, the outer ring and the bearing hole is loose with the available presses will be bearing the first pressure mounted on the shaft and the shaft together with the bearing with load bearing hole press-fit bearing inner ring side surface, pad assembly sleeve of a soft metal material (copper or mild steel), the assembly casing diameter should be slightly larger than the journal diameter, the diameter of the outer diameter than the bearing inner ring ribs slightly smaller, in order to avoid pressure in the cage. The bearing outer ring and the bearing hole is a tight fit, the inner ring and the shaft is loose with the bearing first pressed into the bearing hole, this time the assembly casing outside diameter should be slightly smaller than the diameter of the bore. If the bearing ring and shaft and housing bore are a tight fit to install the indoor ring and outer ring to be pressed into the shaft and housing bore, the assembly structure of the casing should be able to charge tight end face of the bearing inner and outer rings. (b) heating with heated bearings or bearing, the use of thermal expansionwill be a tight fit to change the installation method for a loose fit.④ bearing installation inspection⑤lubricant added to the installation of high-speed precision angular contact ball bearings, mainly for the load lighter, high-speed rotating occasions, the requirement of bearing high-precision, high speed, low temperature rise Low vibration and service life of high-speed precision angular contact ball bearings. Often for high-speed electric spindle bearing installed in pairs, the key component parts of the inner surface of the grinding machine of high speed electric spindle. The main technical indicators: 1. Bearing accuracy specifications: more than GB/307.1-94 the P4 level precision high-speed performance: dmN value of 1.3 ~ 1.8x 106 / min 3. Life (average):> 1500 hLife of high-speed precision angular contact ball bearings have a great relationship with the installation, you should note the following: ①The bearings shall be installed in a clean, clean room, bearing carefully matching, bearing spacers to go through grinding, maintaining the premise of high-inside and outside the ring spacers, spacer parallelism should be controlled in 1um following; ②The bearings prior to installation should be clean, cleaning inner slopes upward, should be flexible and feel no sense of stagnation, dried and put into the specified amount of grease, in the case of oil mist lubrication should be placed in a small amount of oil mist oil; ③bearing installation should be used specialized tools, even by force, strictly prohibited beating; ④The bearings shall be stored in clean air, corrosive gases, relative humidity of not more than 65 % long-term storage should be periodically rust-proof.Tapered roller bearings, water pump bearing installation:①the installation of bearings: bearing must be installed in a dry, clean environment conditions. Before installation, carefully check the mating surface of the shaft and shell, the face of the convex shoulder trench and connection quality of surface processing. All match the connected surface must be carefully cleaned and remove the burrs, casting raw surface must be in addition to net sand. Bearing installation should be preceded by cleaning with gasoline or kerosene, clean and dry before use, and to ensure good lubrication, bearings are commonly used grease lubrication, oil lubrication can be used. With grease lubrication should be used free of impurities, anti-oxidation, rust and extreme pressure performance superior grease. The grease filling is 30% to 60% of the bearings and the bearing capacity of the container, not too much. Withsealing structure of the double row tapered roller bearings and pump shaft bearing filled a good grease, users can directly use, not for cleaning. Bearing installation, you must exert equal pressure on the circumference of the ferrule end face pressed into the ring not want first-class tools to tap the bearing face, so as not to damage the bearing. Small amount of interference with the sleeve at room temperature, press and hold the bearing ring face hammer to beat the sleeve through the sleeve rings evenly pressed into. If large quantities of installation can be a hydraulic press.②bearing removal: Remove the bearing intend to continue to use, you should use the appropriate removal tool. The demolition of the interference fit of the ring, only to increase the tension in the ring, never to allow demolition of the rolling elements, or the rolling element and raceway will be crushed.③bearing use of the environment: the use of location and conditions of use and environmental conditions to select the specifications of size, accuracy, and with the right bearing is the premise to ensure that the bearing life and reliability. Parts: tapered roller bearings are suitable to withstand the radial load mainly radial and axial joint load, usually paired to two sets of bearings used primarily in the car's front and rear wheel hub, active bevel gear, differential, reducer and transmission parts. Allowable speed: correctly installed, well-oiled environment, allowing the bearing limit speed of 0.3 to 0.5 times. Under normal circumstances, the limit of 0.2 times the speed of the most suitable. Allow the angle of inclination: tapered roller bearings are generally not allowed axis of the relative shell hole tilt, where tilt maximum of not more than 2 '. Allow the temperature: under the normal load, the lubricant has high temperature resistance, and adequate lubrication conditions, the general bearing allows to work in -30 ° C to 150 ° C ambient temperature.Axis function and type:Axis is one of the important parts in the machine, used to support the rotating parts of machinery.Depending on the load bearing axis can be divided into the shaft, drive shaft and spindle three kinds. Shaft only transfer torque to withstand bending moments, such as the gear reducer shaft; drive shaft transmitting torque only not withstand the bending moment or bending moment is small. Such as automotive drive shaft; spindle is exposed only to the moment rather than transmit torque, such as the axis of the rail vehicle, the front axle of the bicycle.The shape of the shaft axis can be divided into: straight axle, crankshaft and flexible wire axis. Crankshaft is commonly used in reciprocating machinery. The flexible wire shaft wire layers close together by layers of flexible torque and rotational movement spread to any location commonly used in vibrators and other devices. This chapter only study the direct axis.Shaft design, manufacturing process according to job requirements and to consider other factors, the appropriate choice of materials, structural design, through strength and stiffness, set the axis of the structure shape and size, if necessary, consider the vibration stability.Axis of the commonly used materials:The axis of the material is often used carbon steel and alloy steel.Carbon steel bearing 35,45,50 high-quality carbon structural steel has higher mechanical properties, more applications, of which the most widely used steel 45. In order to improve its mechanical properties, normalizing or quenching and tempering treatment. Unimportant, or by a smaller force axis, can be used such as Q235, Q275 carbon structural steel.Alloy steel alloy steel has higher mechanical properties, but the price is more expensive, used for special requirements of the shaft. For example: the sliding bearings of high-speed shaft, commonly used in 20Cr, 20CrMnTi low-carbon alloy structural steel after carburizing can improve the wear resistance of the journal; generator rotor shaft in the high temperature, high-speed and overload conditions. must have good high temperature mechanical properties, often to adopt 40CrNi, 38CrMoAlA alloy structural steel. It is worth noting: the type and heat treatment of steel, its elastic modulus is very small. For use of alloy steel or heat treatment to improve the shaft stiffness is no practical results. In addition, the alloy steel higher sensitivity to stress concentration, alloy steel shaft design, more should be structured to avoid or reduce the stress concentration and reduce the surface roughness.Axis rough general round bar or forgings, and sometimes can be cast or ductile iron. For example, made of nodular cast iron crankshaft, camshaft, low cost, better vibration absorption, low sensitivity to stress concentration, good strength, etc..Axis of structural design:The axis of the structure design is to make each part of the axis has a reasonable shape and size. Its main requirements are: 1) axis should be easy processing. Parts of the shaft to be easy disassembly (manufacture and installation requirements); 2) axis and the shaft parts have accurateposition (location); 3) parts to firmly and reliably and relatively fixed (fixed); 4) to improve the force situation, reducing the stress concentration.①The manufacturing installation requirementsIn order to facilitate the assembly and disassembly of the shaft parts, often the shaft made of the ladder. Split the box in the shaft, its diameter from the shaft end and gradually increases toward the middle. As shown above, can turn the gear, the sleeve, the left end bearings, bearing caps and pulley from the axis of the left end assembly and disassembly, and another from the right end of the assembly and disassembly of rolling bearings. Shaft parts is easy to install, should chamfer of the shaft end and the end of the shaft section.Axis grinding shaft section should wheel the more process slots; car threaded shaft section should be undercut.Meet the requirements of the case, the axis of the shape and size should be simple in order to facilitate processing.②The axis positioning of partsLadder shaft cross-section changes a place called the shaft shoulder, since the axial positioning of the role. Shaft shoulder makes gear positioned on the shaft; shaft shoulder pulley positioning; shaft shoulder to the right end of the rolling bearing positioning.Some parts rely on a set of simple positioning, such as above the left end of rolling bearings.③The axis parts of the fixedAxial fixation of the shaft parts, often with the shaft shoulder, sleeve, nut or shaft end of the retaining ring (also known as the plate) and other forms. Gear to achieve the axial two-way fixed. Gear by the axial force, right through the shaft shoulder, by the axis and shoulders in the rolling bearing inner ring; left sleeve top in the rolling bearing inner ring. Can not use the sleeve or sleeves too long, we can use the round nut to be fixed. Pulley axial fixed retaining ring depend on the shaft shoulder and the shaft end.Axis intensity calculated as follows:Axis intensity shall be calculated according to the shaft bearing, using the appropriate method of calculation. The common axis strength calculation method has the following two:① Press the torsional strength calculationThis method applies only to withstand the torque of the drive shaft of accurate calculation, iswell received by the bending moment and torque axis approximate calculation can also be used. Circular section shaft transmitting torque only, the strength condition.Withstand both pass to turn short axis of the bending moment can also be used on the preliminary estimate of the diameter of the design formula:In addition, the empirical formula can be used to estimate the diameter of the shaft. For example, in the general reducer, high-speed input shaft diameter according to its associated motor shaft diameter D estimates, d = (0.8 ~ 1. 2) D; all levels of low-speed shaft of the gear center distance on the shaft diameter according to the same level a estimates, d = (0.3 0.4) a.② According to the synthetic strength of the bending and torsionSingle-stage cylindrical gear reducer design sketches, each symbol indicates the length of the Dimensions. Obviously, when the parts laid out on the sketch, the role of location of the external load and support reaction force can be determined. Thus can be used for mechanical analysis of the shaft and draw the bending moment diagram and torque diagram. Then you can press the synthetic strength of the bending and torsion shaft diameter.For the cross-section of the keyway should be calculated shaft diameter increased by about 4%. Calculated shaft diameter greater than the shaft diameter of preliminary estimates of the structural design, that the strength of the chart axis is not enough, you must modify the structural design; calculated shaft diameter less than the estimates of the structural design of shaft diameter, and the difference is not very generally subject to the structural design of the shaft diameter.For general-purpose shaft designed by the above method can. Important axis, yet further strength check (such as the safety factor method), the calculation method available at the reference.Shaft stiffness calculated as follows:Axis by the bending moment will produce a bending torque role will have the torsional deformation. If the shaft stiffness is not enough, it will affect the normal work of the axis. For example, the deflection of the rotor shaft is too large, will change the rotor and stator gap and affect the performance of the motor. Another example is the rigidity of the machine spindle is enough, it will affect the machining accuracy. Therefore, in order so that the axis is not enough stiffness and failure, must be designed to limit their working conditions under the shaft deformationAxis of the concept of critical speed:Uneven due to structural asymmetries of the rotary parts, materials, processing errors and other reasons, to make the rotation center of gravity is precisely located in the geometric axis, it is almost impossible. In fact, the center of gravity and the geometric axis generally total a slight eccentricity, and thus the centrifugal force generated when rotating the axis by the interference of cyclical loading.Axis suffered external frequency axis since the vibration frequency of the same operation will be unstable vibration occurs, a phenomenon known as the resonance of the shaft. Resonance when the shaft speed is called the critical speed. If the shaft speed is stuck near the critical speed, the axis of deformation increases rapidly, as well as the axis, the extent of the damage or even the whole machine. Therefore, the important, especially high-speed axis to calculate the critical speed, and shaft speed n to avoid the critical speed nc.The shaft critical speed, the lowest one called the first critical speed, the remaining second, third ......Speed is below a first critical speed axis is called the rigid shaft; more than the first critical speed axis is called the flexible shaft.Slender axis machining process characteristics:(1) slender shaft turning the process characteristicsSlender shaft rigidity is poor, turning fashion folder properly, it is easy because of the role of cutting force and gravity bending deformation,Vibration, thus affecting the machining accuracy and surface roughness.The slender shaft of the thermal diffusivity of poor performance, the effect of cutting heat, will produce quite a large linear expansion. If the two ends of the shaft to a fixed support, the workpiece due to the elongation of the top bend.The longer axis, a walk the knife for a long time, tool wear, thus affecting the geometry of the precision of the parts.Car slender shaft supporting the workpiece with the tool holder, the two supporting block inappropriate parts pressure will affect the machining accuracy. If the pressure is too small or do not touch, it does not work, you can not improve the stiffness of the parts; if the pressure is too large, the parts are pressed to the lathe tool, the cutting depth increases, the car out of the diameter is small, continue to move with the turret bearing block support in the small-diameter cylindrical。
机械专业外文翻译(中英文翻译)

Belt Conveying Systems Development of driving system Among the methods of material conveying employed,beltconveyors play a very important part in the reliablecarrying of material over long distances at competitivecost.Conveyor systems have become larger and more complex and drive systems have also been going through a process of evolution and will continue to do so.Nowadays,bigger belts require more power and have brought the need forlarger individual drives as well as multiple drives such as 3 drives of 750 kW for one belt(this is the case forthe conveyor drives in Chengzhuang Mine).The ability to control drive acceleration torque is critical to beltconveyors’ performance.An efficient drive system should be able to provide smooth,soft starts while maintaining belt tensions within the specified safe limits.For load sharing on multiple drives.torque and speed control are also important considerations in the drive system’sdesign. Due to the advances in conveyor drive controltechnology,at present many more reliable.Cost-effective and performance-driven conveyor drive systems covering a wide range of power are available for customers’choices[1].1 Analysis on conveyor drive technologies1.1 Direct drivesFull-voltage starters.With a full-voltage starter design,the conveyor head shaft is direct-coupled to the motor through the gear drive.Direct full-voltage starters are adequate forrelatively low-power, simple-profile conveyors.With directfu11-voltage starters.no control is provided for various conveyor loads and.depending on the ratio between fu11-and no-1oad power requirements,empty starting times can be three or four times faster than full load.The maintenance-free starting system is simple,low-cost and very reliable.However, they cannot control starting torque and maximum stall torque;therefore.they are limited to the low-power, simple-profile conveyor belt drives.Reduced-voltage starters.As conveyor power requirements increase,controlling the applied motor torque during the acceleration period becomes increasingly important.Because motor torque 1s a function of voltage,motor voltage must be controlled.This can be achieved through reduced-voltage starters by employing a silicon controlled rectifier(SCR).A common starting method with SCR reduced-voltage starters is to apply low voltage initially to take up conveyor belt slack.and then to apply a timed linear ramp up to full voltage and belt speed.However, this starting method will not produce constant conveyor belt acceleration.When acceleration is complete.the SCRs,which control the applied voltage to the electric motor. are locked in full conduction, providingfu11-line voltage to the motor.Motors with higher torque and pull—up torque,can provide better starting torque when combined with the SCR starters, which are available in sizes up to 750 KW.Wound rotor induction motors.Wound rotor induction motors are connected directly to the drive system reducer and are amodified configuration of a standard AC induction motor.By inserting resistance in series with the motor’s rotor windings.the modified motor control system controls motor torque.For conveyor starting,resistance is placed in series with the rotor for low initial torque.As the conveyor accelerates,the resistance is reduced slowly to maintain a constant acceleration torque.On multiple-drive systems.an external slip resistor may be left in series with the rotor windings to aid in load sharing.The motor systems have a relatively simple design.However, the control systems for these can be highly complex,because they are based on computer control of the resistance switching.Today,the majority of control systems are custom designed to meet a conveyor system’s particular specifications.Wound rotor motors are appropriate for systems requiring more than 400 kW .DC motor.DC motors.available from a fraction of thousands of kW ,are designed to deliver constant torque below base speed and constant kW above base speed to the maximum allowable revolutions per minute(r/min).with the majority of conveyor drives, a DC shunt wound motor is used.Wherein the motor’s rotating armature is connected externally.The most common technology for controlling DC drives is a SCR device. which allows for continual variable-speed operation.The DC drive system is mechanically simple, but can include complex custom-designed electronics to monitor and control the complete system.This system option is expensive in comparison to other soft-start systems.but it isa reliable, cost-effective drive in applications in which torque,1oad sharing and variable speed are primary considerations.DC motors generally are used with higher-power conveyors,including complex profile conveyors with multiple-drive systems,booster tripper systems needing belt tension control and conveyors requiring a wide variable-speed range.1.2 Hydrokinetic couplingHydrokinetic couplings,commonly referred to as fluid couplings.are composed of three basic elements; the driven impeller, which acts as a centrifugal pump;the driving hydraulic turbine known as the runner and a casing that encloses the two power components.Hydraulic fluid is pumped from the driven impeller to the driving runner, producing torque at the driven shaft.Because circulating hydraulicfluid produces the torque and speed,no mechanical connection is required between the driving and driven shafts.The power produced by this coupling is based on the circulated fluid’s amount and density and the torque in proportion to input speed.Because the pumping action within the fluid coupling depends on centrifugal forces.the output speed is less than the input speed.Referred to as slip.this normally is between l% and 3%.Basic hydrokinetic couplings are available in configurations from fractional to several thousand kW .Fixed-fill fluid couplings.Fixed-fill fluid couplings are the most commonly used soft-start devices for conveyors with simpler belt profiles and limited convex/concave sections.They are relatively simple,1ow-cost,reliable,maintenance free devices that provide excellent soft starting results to themajority of belt conveyors in use today.Variable-fill drain couplings.Drainable-fluid couplings work on the same principle as fixed-fill couplings.The coupling’s impellers are mounted on the AC motor and the runners on the driven reducer high-speed shaft.Housing mounted to the drive base encloses the working circuit.The coupling’s rotating casing contains bleed-off orifices that continually allow fluid to exit the working circuit into a separate hydraulic reservoir.Oil from the reservoir is pumped through a heat exchanger to a solenoid-operated hydraulic valve that controls the filling of the fluid coupling.To control the starting torque of a single-drive conveyor system,the AC motor current must be monitored to provide feedback to the solenoid control valve.Variable fill drain couplings are used in medium to high-kW conveyor systems and are available in sizes up to thousands of kW .The drives can be mechanically complex and depending on the control parameters.the system can be electronically intricate.The drive system cost is medium to high, depending upon size specified.Hydrokinetic scoop control drive.The scoop control fluid coupling consists of the three standard fluid coupling components:a driven impeller, a driving runner and a casing that encloses the working circuit.The casing is fitted with fixed orifices that bleed a predetermined amount of fluid into a reservoir.When the scoop tube is fully extended into the reservoir, the coupling is l00 percent filled.The scoop tube, extending outside the fluid coupling,is positioned using anelectric actuator to engage the tube from the fully retracted to the fully engaged position.This control provides reasonably smooth acceleration rates.to but the computer-based control system is very complex.Scoop control couplings are applied on conveyors requiring single or multiple drives from l50 kW to 750 kW.1.3 Variable-frequency control(VFC)Variable frequency control is also one of the direct drive methods.The emphasizing discussion about it here is because that it has so unique characteristic and so good performance compared with other driving methods for belt conveyor. VFC devices Provide variable frequency and voltage to the induction motor, resulting in an excellent starting torque and acceleration rate for belt conveyor drives.VFC drives.available from fractional to several thousand(kW ), are electronic controllers that rectify AC line power to DC and,through an inverter, convert DC back to AC with frequency and voltage contro1.VFC drives adopt vector control or direct torque control(DTC)technology,and can adopt different operating speeds according to different loads.VFC drives can make starting or stalling according to any given S-curves.realizing the automatic track for starting or stalling curves.VFC drives provide excellent speed and torque control for starting conveyor belts.and can also be designed to provide load sharing for multiple drives.easily VFC controllers are frequently installed on lower-powered conveyor drives,but when used at the range of medium-high voltage in the past.the structure of VFC controllers becomes verycomplicated due to the limitation of voltage rating of power semiconductor devices,the combination of medium-high voltage drives and variable speed is often solved with low-voltage inverters using step-up transformer at the output,or with multiple low-voltage inverters connected in series.Three-level voltage-fed PWM converter systems are recently showing increasing popularity for multi-megawatt industrial drive applications because of easy voltage sharing between the series devices and improved harmonic quality at the output compared to two-level converter systems With simple series connection of devices.This kind of VFC system with three 750 kW /2.3kV inverters has been successfully installed in ChengZhuang Mine for one 2.7-km long belt conveyor driving system in following the principle of three-level inverter will be discussed in detail.2 Neutral point clamped(NPC)three-level inverter using IGBTsThree-level voltage-fed inverters have recently become more and more popular for higher power drive applications because of their easy voltage sharing features.1ower dv/dt per switching for each of the devices,and superior harmonic quality at the output.The availability of HV-IGBTs has led to the design of a new range of medium-high voltage inverter using three-level NPC topology.This kind of inverter can realize a whole range with a voltage rating from 2.3 kV to 4.1 6 kV Series connection of HV-IGBT modules is used in the 3.3 kV and 4.1 6 kV devices.The 2.3 kV inverters need only one HV-IGBT per switch[2,3].2.1 Power sectionTo meet the demands for medium voltage applications.a three-level neutral point clamped inverter realizes the power section.In comparison to a two-level inverter.the NPC inverter offers the benefit that three voltage levels can be supplied to the output terminals,so for the same output current quality,only 1/4 of the switching frequency is necessary.Moreover the voltage ratings of the switches in NPC inverter topology will be reduced to 1/2.and the additional transient voltage stress on the motor can also be reduced to 1/2 compared to that of a two-level inverter.The switching states of a three-level inverter are summarized in Table 1.U.V and W denote each of the three phases respectively;P N and O are the dc bus points.The phase U,for example,is in state P(positive bus voltage)when the switches S1u and S2u are closed,whereas it is in state N (negative bus voltage) when the switches S3u and S4u are closed.At neutral point clamping,the phase is in O state when either S2u or S3u conducts depending on positive or negative phase current polarity,respectively.For neutral point voltage balancing,the average current injected at O should be zero.2.2 Line side converterFor standard applications.a l2-pulse diode rectifier feeds the divided DC-link capacitor.This topology introduces low harmonics on the line side.For even higher requirements a 24-pulse diode rectifier can be used as an input converter.For more advanced applications where regeneration capability is necessary, an active front.end converter can replace thediode rectifier, using the same structure as the inverter.2.3 Inverter controlMotor Contro1.Motor control of induction machines is realized by using a rotor flux.oriented vector controller.Fig.2 shows the block diagram of indirect vector controlled drive that incorporates both constant torque and high speed field-weakening regions where the PW M modulator was used.In this figure,the command fluxis generated as function of speed.The feedback speed is added with the feed forward slip command signal. the resulting frequency signal is integrated and thenthe unit vector signals(cosand sin)are generated.The vector rotator generates the voltageand anglecommands for the PW M as shown.PWM Modulator.The demanded voltage vector is generated using an elaborate PWM modulator.The modulator extends the concepts of space-vector modulation to the three-level inverter.The operation can be explained by starting from a regularly sampled sine-triangle comparison from two-level inverter.Instead of using one set of reference waveforms and one triangle defining the switching frequency, the three-level modulator uses two sets of reference waveforms U r1 and U r2 and just one triangle.Thus, each switching transition isused in an optimal way so that several objectives are reached at the same time.Very low harmonics are generated.The switching frequency is low and thus switching losses are minimized.As in a two-level inverter, a zero-sequence component can be added to each set of reference waveform s in order to maximize the fundamental voltage component.As an additional degree of freedom,the position of the reference waveform s within the triangle can be changed.This can be used for current balance in the two halves of the DC-1ink.3 Testing resultsAfter Successful installation of three 750 kW /2.3 kV three-level inverters for one 2.7 km long belt conveyor driving system in Chengzhuang Mine.The performance of the whole VFC system was tested.Fig.3 is taken from the test,which shows the excellent characteristic of the belt conveyor driving system with VFC controller.Fig.3 includes four curves.The curve 1 shows the belt tension.From the curve it can be find that the fluctuation range of the belt tension is very smal1.Curve 2 and curve 3 indicate current and torque separately.Curve 4 shows the velocity of the controlled belt.The belt velocity havethe“s”shape characteristic.A1l the results of the test showa very satisfied characteristic for belt driving system.4 ConclusionsAdvances in conveyor drive control technology in recent years have resulted in many more reliable.Cost-effective and performance-driven conveyor drive system choices for users.Among these choices,the Variable frequency control (VFC) method shows promising use in the future for long distancebelt conveyor drives due to its excellent performances.The NPC three-level inverter using high voltage IGBTs make the Variable frequency control in medium voltage applications become much more simple because the inverter itself can provide the medium voltage needed at the motor terminals,thus eliminating the step-up transformer in most applications in the past.The testing results taken from the VFC control system with NPC three.1evel inverters used in a 2.7 km long belt conveyor drives in Chengzhuang Mine indicates that the performance of NPC three-level inverter using HV-IGBTs together with the control strategy of rotor field-oriented vector control for induction motor drive is excellent for belt conveyor driving system.中文译文:带式输送机及其牵引系统在运送大量的物料时,带式输送机在长距离的运输中起到了非常重要的竞争作用。
机械专业毕业设计外文翻译--机械传动系统介绍

Transmission System introducedThe important position of the wheel gear and shaft can’t falter in traditional machine and modern machines. The wheel gear and shafts mainly install the direction that delivers the dint at the principal axis box. The passing to process to make them can is divided into many model numbers, used for many situations respectively. so we must be the multilayers to the understanding of the wheel gear and shaft in many ways.In the force analysis of spur gears, the forces are assumed to act in a single plane. We shall study gears in which the forces have three dimensions. The reason for this, in the case of helical gears, is that the teeth are not parallel to the axis of rotation. And in the case of bevel gears, the rotational axes are not parallel to each other. There are also other reasons, as we shall learn.Helical gears are used to transmit motion between parallel shafts. The helix angle is the same on each gear, but one gear must have a right-hand helix and the other a left-hand helix. The shape of the tooth is an involute helicoid. If a piece of paper cut in the shape of a parallelogram is wrapped around a cylinder, the angular edge of the paper becomes a helix. If we unwind this paper, each point on the angular edge generates an involute curve. The surface obtained when every point on the edge generates an involute is called an involute helicoids.The initial contact of spur-gear teeth is a line extending all the way across the face of the tooth. The initial contact of helical gear teeth is a point, which changes into a line as line as the teeth come into more engagement. In spur gears the line of contact is parallel to the axis of the rotation; in helical gears, the line is diagonal across the face of the tooth. It is this gradual of the teeth and the smooth transfer of load from one tooth to another, which give helical gears the ability to transmit heavy loads at high speeds. Helical gears subject the shaft bearings to both radial and thrust loads. When the thrust loads become high or are objectionable for other reasons, it may be desirable to use double helical gears. A double helical gear (herringbone) is equivalent to two helical gears of opposite hand, mounted side by side on the same shaft. They develop opposite thrust reactions and thus cancel out the thrust load. When two or more single helical gears are mounted on the same shaft, the hand of the gears should be selected so as to produce the minimum thrust load.Crossed-helical, or spiral, gears are those in which the shaft centerlines are neither parallel nor interesting. The teeth of crossed-helical fears have point contact with each other which changes to line contact as the gears wear in. for this reason they will carry out very small loads and are mainly for instrumental applications, and are definitely not recommended for use in the transmission of power. There is on difference between a crossed helical gear and a helical gear until they are mounted in mesh with each other. They are manufactured in the same way. A pair of meshed crossed helical gears usually have the same hand; that is, a right-hand driver goes with a right-hand driven. In the design of crossed-helical gears, the minimum sliding velocity is obtained when the helix angle are equal. However, when the helix angle are not equal, the gear with the larger helix angle should be used as the driver if both gears have the same hand.Worm gears are similar to crossed helical gears. The pinion or worm has a small number of teeth, usually one to four, and since they completely wrap around the pitch cylinder they are called threads. Its mating gear is called a worm gear, which is not a true helical gear. A worm and worm gear are used to provide a high angular-velocity reduction between nonintersecting shafts which are usually at right angle. The worm gear is not a helical gear because its face is made concave to fit the curvature of the worm in order to provide line contact instead of point contact. However, a disadvantage of worm gearing is the high sliding velocities across the teeth, the same as with crossed helical gears.Worm gearing are either single or double enveloping. A single-enveloping gearing is one in which the gear wraps around or partially encloses the worm. A gearing in which each element partially encloses the other is, of course, a double-enveloping worm gearing. The important difference between the two is that area contact exists between the teeth of double-enveloping gears while only line contact between those of single-enveloping gears. The worm and worm gear of a set have the same hand of helix as for crossed helical gears, but the helix angles are usually quite different. The helix angle on the worm is generally quite large, and that on the gear very small. Because of this, it is usual to specify the lead angle on the worm, which is the complement of the worm helix angle, and the helix angle on the gear; the two angles ate equal for a 90-deg. Shaft angle.When gears are to be used to transmit motion between intersecting shaft, some ofbevel gear is required. Although bevel gear are usually made for a shaft angle of 90 deg. They may be produced for almost any shaft angle. The teeth may be cast, milled, or generated. Only the generated teeth may be classed as accurate. In a typical bevel gear mounting, one of the gear is often mounted outboard of the bearing this means that shaft deflection can be more pronounced and have a greater effect in the contact of teeth. Another difficulty, which occurs in predicting the stress in bevel-gear teeth, is the fact the teeth are tapered.Straight bevel gears are easy to design and simple to manufacture and give very good results in service if they are mounted accurately and positively. As in the case of squrgears, however, they become noisy at higher values of the pitch-line velocity. In these cases it is often good design practice to go to the spiral bevel gear, which is the bevel counterpart of the helical gear. As in the case of helical gears, spiral bevel gears give a much smoother tooth action than straight bevel gears, and hence are useful where high speed are encountered.It is frequently desirable, as in the case of automotive differential applications, to have gearing similar to bevel gears but with the shaft offset Such gears are called hypoid gears because their pitch surfaces are hyperboloids of revolution The tooth action between such gears is a combination of rolling and has much in common with that of worm gears.A shaft is a rotating or stationary member usually of circular cross section, having mounted upon it such elementsas gears pulleys flywheels, cranks sprockets and other power-transmission elements Shaft may be subjected to bending tension compression or torsional loads acting singly or in combination with one another .When they are combined one may expect to find both static and fatigue strength to be important design considerations since a single shaft may be subjected to static stresses completely reversed, and repeated stresses, all acting at the same timeThe word “shaft” covers numerous wariations, such as axles and spindles. Anaxle is a shaft, wither stationary or rotating nor subjected to torsion load. Ashirt rotating shaft is often called a spindle.When either the lateral or the tosional deflection of shaft must be held to close limits, the shaft must be sized on the basis of deflection before analyzing the stresses The reasonfor this is that if the shift is made stiff enough so that the deflection is not too large, it is probable that the resulting stresses will be safe. But by no means should the designer assume that they are within acceptable limits. Whenever possible the power-transmission elements such as gears or pullets, should be located close to the supporting bearings. This reduces the bending moment, and hence the deflection and bending stress.Although the von Mises-Hencky-Goodman method is difficult to use in design of shaft, it probably come closest to predicting actual failure. Thus it is a good way of checking a shaft that has already been designed or of discovering why a particular shaft that has already been designed or of discovering why a particular shaft has failed in service. Furthermore, there are a considerable number of shaft-design problems in which the dimension are pretty well limited by other considerations, such as rigidity, and it is only necessary for the designer to discover something about the fillet sizes, heat-treatment, and surface finish and whether or not shot peening is necessary in order to achieve the required life and reliability.Because of the similarity of their functions, clutches and brakes are treated together. In a simplified dynamic representation of a friction clutch, or brake, two inertias I1and I2 traveling at the respective angular velocities W1 and W2, one of which may be zero in the case of brake, are to be brought to the same speed by engaging the clutch or brake. Slippage occurs because the two elements are running at different speeds and energy is dissipated during actuation, resulting in a temperature rise. In analyzing the performance of these devices we shall be interested in the actuating force, the torque transmitted, the energy loss and the temperature rise. The torque transmitted is related to the actuating force, the coefficient of friction, and the geometry of the clutch or brake. This is problem in static, which will have to be studied separately for each geometric configuration. However, temperature rise is related to energy loss and can be studied without regard to the type of brake or clutch because the geometry of interest is the hear-dissipating surfaces. The various types of clutches and brakes may be classified as fallows:Rim type with internally expanding shoesRim type with internally contracting shoesBand typeDisk or axial typeCone typeMiscellaneous typeThe analysis of all type of friction clutches and brakes use the same general procedure. The following step are necessary:1. Assume or determine the distribution of pressure on the frictionalsurfaces.2. Find a relation between the maximum pressure and the pressure at any point3. apply the condition of statical equilibrium to find (a) the actuating force, (b) the torque, and (c) the support reactions.Miscellaneous clutches include several type, such as the positive-contact clutches, overload-release clutches, overrunning clutches, magnetic fluid clutches, and others.A positive-contact clutch consists of a shift lever and two jaws. The greatest differences between the various types of positive clutches are concerned with the design of the jaws. To provide a longer period of time for shift action during engagement, the jaws may be ratchet-shaped, or gear-tooth-shaped. Sometimes a great many teeth or jaws re used, and they may be cut either circumferentially, so that they engage by cylindrical mating, or on the faces of the mating elements.Although positive clutches are not used to the extent the frictional-contact type, they do have important applications where synchronous operation is required.Devices such as linear driver or motor-operated screw drivers must run to definite limit and then come to a stop. An over load-release rype of clutch is required for these applications. These clutches are usually spring-loaded so as to release at a predetermined toque. The clicking sound which is heard when the overload point is reached is considered to be a desirable signal.An overrunning clutch or coupling permits the driven member of a machine to “freewheel” or “overrun” because the driver is stopped or because another source of power increase the speed of the driven. This type of clutch usually uses rollers or balls mounted between an outer sleeve and an inner member having flats machined around the periphery. Driving action is obtained by wedding the rollers between the sleeve and the flats. The clutch is therefore equivalent to a pawl and ratchet with an infinite number of teeth.Magnetic fluid clutch or brake is a relatively new development which has two parallel magnetic plates. Between these plates is a lubricated magnetic powder mixture. An electromagnetic coil is inserted somewhere in the magnetic circuit. Bu varying the excitation to this coil, the shearing strength of the magnetic fluid mixture may be accurately controlled. Thus any condition from a full slip to a frozen lockup may be obtained.机械传动系统介绍在传统机械和现代机械中齿轮和轴的重要地位是不可动摇的。
机械制造 毕业设计 外文英文文献 翻译 齿轮和齿轮传动
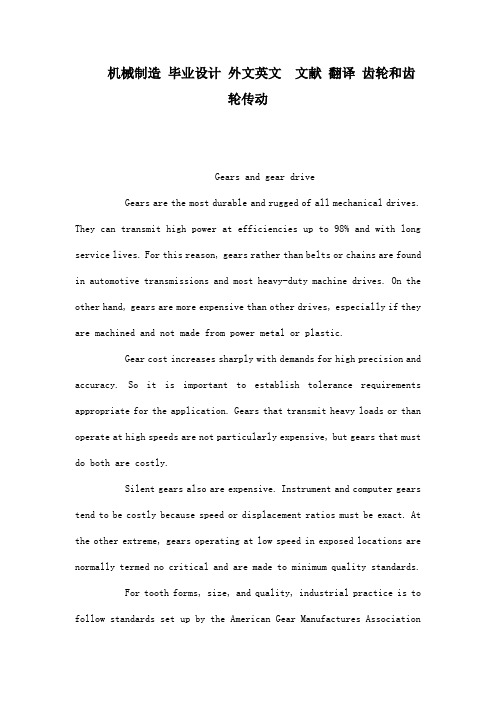
机械制造毕业设计外文英文文献翻译齿轮和齿轮传动Gears and gear driveGears are the most durable and rugged of all mechanical drives. They can transmit high power at efficiencies up to 98% and with long service lives. For this reason, gears rather than belts or chains are found in automotive transmissions and most heavy-duty machine drives. On the other hand, gears are more expensive than other drives, especially if they are machined and not made from power metal or plastic.Gear cost increases sharply with demands for high precision and accuracy. So it is important to establish tolerance requirements appropriate for the application. Gears that transmit heavy loads or than operate at high speeds are not particularly expensive, but gears that must do both are costly.Silent gears also are expensive. Instrument and computer gears tend to be costly because speed or displacement ratios must be exact. At the other extreme, gears operating at low speed in exposed locations are normally termed no critical and are made to minimum quality standards.For tooth forms, size, and quality, industrial practice is to follow standards set up by the American Gear Manufactures AssociationAGMA.Tooth formStandards published by AGMA establish gear proportions and tooth profiles. Tooth geometry is determined primarily by pitch, depth, and pressure angle.Pitch:Standards pitches are usually whole numbers when measured as diametral pitch P. Coarse-pitch gearing has teeth larger than 20 diametral pitch ?usually 0.5 to 19.99. Fine-pitch gearing usually has teeth of diametral pitch 20 to 200.Depth: Standardized in terms of pitch. Standard full-depth have working depth of 2/p. If the teeth have equal addendaas in standard interchangeable gears the addendum is 1/p. Stub teeth have a working depth usually 20% less than full-depth teeth. Full-depth teeth have a larger contract ratio than stub teeth. Gears with small numbers of teeth may have undercut so than they do not interfere with one another during engagement. Undercutting reduce active profile and weakens the tooth.Mating gears with long and short addendum have larger load-carrying capacity than standard gears. The addendum of the smaller gear pinion is increased while that of larger gear is decreased, leaving the whole depth the same. This form is know as recess-action gearing.Pressure Angle: Standard angles are and . Earlier standards include a 14-pressure angle that is still used. Pressure angle affectsthe force that tends to separate mating gears. High pressure angle decreases the contact ratio ratio of the number of teeth in contact but provides a tooth of higher capacity and allows gears to have fewer teeth without undercutting.Backlash: Shortest distances between the non-contacting surfaces of adjacent teeth .Gears are commonly specified according to AGMA Class Number, which is a code denoting important quality characteristics. Quality number denote tooth-element tolerances. The higher the number, the closer the tolerance. Number 8 to 16 apply to fine-pitch gearing.Gears are heat-treated by case-hardening, through-hardening, nitriding, or precipitation hardening. In general, harder gears are stronger and last longer than soft ones. Thus, hardening is a device that cuts the weight and size of gears. Some processes, such as flame-hardening, improve service life but do not necessarily improve strength.Design checklistThe larger in a pair is called the gear, the smaller is called the pinion.Gear Ratio: The number of teeth in the gear divide by the number of teeth in the pinion. Also, ratio of the speed of the pinion to the speed of the gear. In reduction gears, the ratio of input to output speeds.Gear Efficiency: Ratio of output power to input power. includesconsideration of power losses in the gears, in bearings, and from windage and churning of lubricant.Speed: In a given gear normally limited to some specific pitchline velocity. Speed capabilities can be increased by improving accuracy of the gear teeth and by improving balance of the rotating parts.Power: Load and speed capacity is determined by gear dimensions and by type of gear. Helical and helical-type gears have the greatest capacity to approximately 30,000 hp. Spiral bevel gear are normally limited to 5,000 hp, and worm gears are usually limited to about 750 hp.Special requirementsMatched-Set Gearing: In applications requiring extremely high accuracy, it may be necessary to match pinion and gear profiles and leads so that mismatch does not exceed the tolerance on profile or lead for the intended application.Tooth Spacing: Some gears require high accuracy in the circular of teeth. Thus, specification of pitch may be required in addition to an accuracy class specification.Backlash: The AMGA standards recommend backlash ranges to provide proper running clearances for mating gears. An overly tight mesh may produce overload. However, zero backlash is required in some applications.Quiet Gears: To make gears as quit as possible, specify thefinest pitch allowable for load conditions. In some instances, however, pitch is coarsened to change mesh frequency to produce a more pleasant, lower-pitch sound. Use a low pressure angle. Use a modified profile to include root and tip relief. Allow enough backlash. Use high quality numbers. Specify a surface finish of 20 in. or better. Balance the gear set. Use a nonintegral ratio so that the same teeth do not repeatedly engage if both gear and pinion are hardened steel. If the gear is made of a soft material, an integral ratio allows the gear to cold-work and conform to the pinion, thereby promoting quiet operation. Make sure critical are at least 20% apart from operating speeding or speed multiples and from frequency of tooth mesh.Multiple mesh gearMultiple mesh refers to move than one pair of gear operating in a train. Can be on parallel or nonparallel axes and on intersection or nonintersecting shafts. They permit higer speed ratios than are feasible with a single pair of gears .Series trains:Overall ratio is input shaft speed divided by output speed ,also the product of individual ratios at each mesh ,except in planetary gears .Ratio is most easily found by dividing the product of numbers of teeth of driven gears by the product of numbers of teeth of driving gears.Speed increasers with step-up rather than step-down ratios mayrequire special care in manufacturing and design. They often involve high speeds and may creste problems in gear dynamics. Also, frictional and drag forces are magnified which, in extreme cases , may lead to operational problems.Epicyclic Gearing:Normally, a gear axis remains fixed and only the gears rotates. But in an epicyclic gear train, various gears axes rotate about one anther to provide specialized output motions. With suitable clutchse and brakes, an epicyclic train serves as the planetary gear commonly found in automatic transmissions.Epicyclic trains may use spur or helical gears, external or internal, or bevel gears. In transmissions, the epicyclic or planetary gears usually have multiple planets to increase load capacity.In most cases, improved kinematic accuracy in a gearset decreases gear mesh excitation and results in lower drive noise. Gearset accuracy can be increased by modifying the tooth involute profile, by substituting higher quality gearing with tighter manufacturing tolerances, and by improving tooth surface finish. However, if gear mesh excitation generaters resonance somewhere in the drive system, nothing short of a “perfect” gearset will substantially reduce vibration and noise.Tooth profiles are modified to avoid interferences which can result from deflections in the gears, shafts, and housing as teeth engageand disendgage. If these tooth interferences are not compensated for by profile modifications, gears load capacity can be seriously reduced. In addition, the drive will be noisier because tooth interferences generate high dynamic loads. Interferences typically are eliminated by reliving the tooth tip, the tooth flank, or both. Such profile modifications are especially important for high-load , high-speed drives. The graph of sound pressure levelvs tip relief illustrates how tooth profile modifications can affect overall drive noise. If the tip relief is less than this optimum value, drive noise increases because of greater tooth interference; a greater amount of tip relief also increase noise because the contact ratio is decreased.Tighter manufacturing tolerances also produce quietier gears. Tolerances for such parameters as profile error, pitch AGMA quality level. For instance, the graph depicting SPL vs both speed and gear quality shows how noise decreases example, noise is reduced significantly by an increase in accuracy from an AGMA Qn 11 quality to an AGNA Qn 15 quality. However, for most commercial drive applications, it is doubtful that the resulting substantial cost increase for such an accuracy improvement can be justified simply on the basis of reduced drive noise.Previously, it was mentioned that gears must have adequate clearance when loaded to prevent tooth interference during the course of meshing. Tip and flank relief are common profile modifications thatcontrol such interference. Gears also require adequate backlash and root clearance. Noise considerations make backlash an important parameter to evaluate during drive design. Sufficient backlash must be provided under all load and temperature conditions to avoid a tight mesh, which creates excessively high noise level. A tight mesh due to insufficient backlash occurs when the drive and coast side of a tooth are in contact simultaneously. On the other hand, gears with excessive backlash also are noisy because of impacting teeth during periods of no load or reversing load. Adequate backlash should be provided by tooth thinning rather than by increase in center distance. Tooth thinning dose not decrease the contact ratio, whereas an increase in center distance does. However, tooth thinning does reduce the bending fatigue, a reduction which is small for most gearing systems.齿轮和齿轮传动在所有的机械传动形式中,齿轮传动是一种最结实耐用的传动方式。
齿轮和轴的介绍外文翻译

GEAR AND SHAFT INTRODUCTIONAbstract: The important position of the wheel gear and shaft can't falter in traditional machine and modern machines.The wheel gear and shafts mainly install the direction that delivers the dint at the principal axis box.The passing to process to make them can is divided into many model numbers, useding for many situations respectively.So we must be the multilayers to the understanding of the wheel gear and shaft in many ways .Key words: Wheel gear;ShaftIn the force analysis of spur gears, the forces are assumed to act in a single plane. We shall study gears in which the forces have three dimensions. The reason for this, in the case of helical gears, is that the teeth are not parallel to the axis of rotation. And in the case of bevel gears, the rotational axes are not parallel to each other. There are also other reasons, as we shall learn.Helical gears are used to transmit motion between parallel shafts. The helix angle is the same on each gear, but one gear must have a right-hand helix and the other a left-hand helix. The shape of the tooth is an involute helicoid. If a piece of paper cut in the shape of a parallelogram is wrapped around a cylinder, the angular edge of the paper becomes a helix. If we unwind this paper, each point on the angular edge generates an involute curve. The surface obtained when every point on the edge generates an involute is called an involute helicoid.The initial contact of spur-gear teeth is a line extending all the way across the face of the tooth. The initial contact of helical gear teeth is a point, which changes into a line as the teeth come into more engagement. In spur gears the line of contact is parallel to the axis of the rotation; in helical gears, the line is diagonal across the face of the tooth. It is this gradual of the teeth and the smooth transfer of load from one tooth to another, which give helical gears the ability to transmit heavy loads at high speeds. Helical gears subject the shaft bearings to both radial and thrust loads. When the thrust loads become high or are objectionable for other reasons, it may be desirable to use double helical gears. A double helical gear (herringbone) is equivalent to two helical gears of opposite hand, mounted side by side on the same shaft. They develop opposite thrust reactions and thus cancel out the thrust load. When two or more single helical gears are mounted on the same shaft, the hand of the gears should be selected so as to produce the minimum thrust load.Crossed-helical, or spiral, gears are those in which the shaft centerlines are neither parallel nor intersecting. The teeth of crossed-helical fears have point contact with each other, which changes to line contact as the gears wear in. For this reason they will carry out verysmall loads and are mainly for instrumental applications, and are definitely not recommended for use in the transmission of power. There is on difference between a crossed helical gear and a helical gear until they are mounted in mesh with each other. They are manufactured in the same way. A pair of meshed crossed helical gears usually have the same hand; that is ,a right-hand driver goes with a right-hand driven. In the design of crossed-helical gears, the minimum sliding velocity is obtained when the helix angle are equal. However, when the helix angle are not equal, the gear with the larger helix angle should be used as the driver if both gears have the same hand.Worm gears are similar to crossed helical gears. The pinion or worm has a small number of teeth, usually one to four, and since they completely wrap around the pitch cylinder they are called threads. Its mating gear is called a worm gear, which is not a true helical gear. A worm and worm gear are used to provide a high angular-velocity reduction between nonintersecting shafts which are usually at right angle. The worm gear is not a helical gear because its face is made concave to fit the curvature of the worm in order to provide line contact instead of point contact. However, a disadvantage of worm gearing is the high sliding velocities across the teeth, the same as with crossed helical gears.Worm gearing are either single or double enveloping. A single-enveloping gearing is one in which the gear wraps around or partially encloses the worm.. A gearing in which each element partially encloses the other is, of course, a double-enveloping worm gearing. The important difference between the two is that area contact exists between the teeth of double-enveloping gears while only line contact between those of single-enveloping gears. The worm and worm gear of a set have the same hand of helix as for crossed helical gears, but the helix angles are usually quite different. The helix angle on the worm is generally quite large, and that on the gear very small. Because of this, it is usual to specify the lead angle on the worm, which is the complement of the worm helix angle, and the helix angle on the gear; the two angles are equal for a 90-deg. Shaft angle.When gears are to be used to transmit motion between intersecting shaft, some of bevel gear is required. Although bevel gear are usually made for a shaft angle of 90 deg. They may be produced for almost any shaft angle. The teeth may be cast, milled, or generated. Only the generated teeth may be classed as accurate. In a typical bevel gear mounting, one of the gear is often mounted outboard of the bearing. This means that shaft deflection can be more pronounced and have a greater effect on the contact of teeth. Another difficulty, which occurs in predicting the stress in bevel-gear teeth, is the fact the teeth are tapered.Straight bevel gears are easy to design and simple to manufacture and give very good results in service if they are mounted accurately and positively. As in the case of squr gears,however, they become noisy at higher values of the pitch-line velocity. In these cases it is often good design practice to go to the spiral bevel gear, which is the bevel counterpart of the helical gear. As in the case of helical gears, spiral bevel gears give a much smoother tooth action than straight bevel gears, and hence are useful where high speed are encountered.It is frequently desirable, as in the case of automotive differential applications, to have gearing similar to bevel gears but with the shaft offset. Such gears are called hypoid gears because their pitch surfaces are hyperboloids of revolution. The tooth action between such gears is a combination of rolling and sliding along a straight line and has much in common with that of worm gears.A shaft is a rotating or stationary member, usually of circular cross section, having mounted upon it such elementsas gears, pulleys, flywheels, cranks, sprockets, and other power-transmission elements. Shaft may be subjected to bending, tension, compression, or torsional loads, acting singly or in combination with one another. When they are combined, one may expect to find both static and fatigue strength to be important design considerations, since a single shaft may be subjected to static stresses, completely reversed, and repeated stresses, all acting at the same time.The word “shaft” covers numerous variations, such as axles and spindles. Anaxle is a shaft, wither stationary or rotating, nor subjected to torsion load. A shirt rotating shaft is often called a spindle.When either the lateral or the torsional deflection of a shaft must be held to close limits, the shaft must be sized on the basis of deflection before analyzing the stresses. The reason for this is that, if the shaft is made stiff enough so that the deflection is not too large, it is probable that the resulting stresses will be safe. But by no means should the designer assume that they are safe; it is almost always necessary to calculate them so that he knows they are within acceptable limits. Whenever possible, the power-transmission elements, such as gears or pullets, should be located close to the supporting bearings, This reduces the bending moment, and hence the deflection and bending stress.Although the von Mises-Hencky-Goodman method is difficult to use in design of shaft, it probably comes closest to predicting actual failure. Thus it is a good way of checking a shaft that has already been designed or of discovering why a particular shaft has failed in service. Furthermore, there are a considerable number of shaft-design problems in which the dimension are pretty well limited by other considerations, such as rigidity, and it is only necessary for the designer to discover something about the fillet sizes, heat-treatment, and surface finish and whether or not shot peening is necessary in order to achieve the required life and reliability.Because of the similarity of their functions, clutches and brakes are treated together. In a simplified dynamic representation of a friction clutch, or brake, two inertias I1 and I2 traveling at the respective angular velocities W1 and W2, one of which may be zero in the case of brake, are to be brought to the same speed by engaging the clutch or brake. Slippage occurs because the two elements are running at different speeds and energy is dissipated during actuation, resulting in a temperature rise. In analyzing the performance of these devices we shall be interested in the actuating force, the torque transmitted, the energy loss and the temperature rise. The torque transmitted is related to the actuating force, the coefficient of friction, and the geometry of the clutch or brake. This is problem in static, which will have to be studied separately for eath geometric configuration. However, temperature rise is related to energy loss and can be studied without regard to the type of brake or clutch because the geometry of interest is the heat-dissipating surfaces. The various types of clutches and brakes may be classified as fllows:1. Rim type with internally expanding shoes2. Rim type with externally contracting shoes3. Band type4. Disk or axial type5. Cone type6. Miscellaneous typeThe analysis of all type of friction clutches and brakes use the same general procedure. The following step are necessary:1. Assume or determine the distribution of pressure on the frictional surfaces.2. Find a relation between the maximum pressure and the pressure at any point3. Apply the condition of statical equilibrium to find (a) the actuating force, (b) the torque, and (c) the support reactions.Miscellaneous clutches include several types, such as the positive-contact clutches, overload-release clutches, overrunning clutches, magnetic fluid clutches, and others.A positive-contact clutch consists of a shift lever and two jaws. The greatest differences between the various types of positive clutches are concerned with the design of the jaws. To provide a longer period of time for shift action during engagement, the jaws may be ratchet-shaped, or gear-tooth-shaped. Sometimes a great many teeth or jaws are used, and they may be cut either circumferentially, so that they engage by cylindrical mating, or on the faces of the mating elements.Although positive clutches are not used to the extent of the frictional-contact type, they do have important applications where synchronous operation is required.Devices such as linear drives or motor-operated screw drivers must run to definite limit and then come to a stop. An overload-release type of clutch is required for these applications. These clutches are usually spring-loaded so as to release at a predetermined toque. The clicking sound which is heard when the overload point is reached is considered to be a desirable signal.An overrunning clutch or coupling permits the driven member of a machine to “freewheel” or “overrun” because the driver is stopped or because another source of power increase the speed of the driven. This type of clutch usually uses rollers or balls mounted between an outer sleeve and an inner member having flats machined around the periphery. Driving action is obtained by wedging the rollers between the sleeve and the flats. The clutch is therefore equivalent to a pawl and ratchet with an infinite number of teeth.Magnetic fluid clutch or brake is a relatively new development which has two parallel magnetic plates. Between these plates is a lubricated magnetic powder mixture. An electromagnetic coil is inserted somewhere in the magnetic circuit. By varying the excitation to this coil, the shearing strength of the magnetic fluid mixture may be accurately controlled. Thus any condition from a full slip to a frozen lockup may be obtained齿轮和轴的介绍摘要:对齿轮和轴的重要地位不能动摇传统机械和现代机械.齿轮和轴的方向,主要安装在主轴提供的力盒子.经过处理,使它们可以是分为许多型号,分为许多情况下使用。
- 1、下载文档前请自行甄别文档内容的完整性,平台不提供额外的编辑、内容补充、找答案等附加服务。
- 2、"仅部分预览"的文档,不可在线预览部分如存在完整性等问题,可反馈申请退款(可完整预览的文档不适用该条件!)。
- 3、如文档侵犯您的权益,请联系客服反馈,我们会尽快为您处理(人工客服工作时间:9:00-18:30)。
附录附录A外文文献原文A shaft assembly, profileThe shaft axis in two different, even in its working process and relative position between the two shafts changing. According to the important components - shaft, can have the different universal classification. If the direction in reverse universal elastic, whether can be divided into the rigid universal shaft transmission and flexible joints. The former is the hinged on parts of the power transmission link, the latter by elastic parts, and has passed dynamic buffer reduced. Rigid gimbal and can be divided into different speed universal shaft type (such as cross gimbal) and patterned (such as double type gimbal, three pin shaft type gimbal) and patterned (such as ball cage gimbal, fork type gimbal). Patterned constant, and refers to the driven shaft rotation in driving shaft with the rotation Angle, whether of equal velocity, of course, driving shaft and driven shafts is equal to the speed of the average.Lord, the driven shaft axis in two angular change when the Angle between the universal and equal still called patterned or DengJiao velocity universal. They mainly used to drive axles, breaking the wheel transmission device etc, and is mainly used in the power of the car. When the car for a rear wheel drive, oftenusing the universal shaft, on the part of high-grade car, have adopted the isokinetic ball head, When the car for front wheel drive, often USES patterned constant - universal shaft, but also a kind of different appellation.In front of a rear wheel drive motor (or all round the bus driver), due to the automobile suspension in athletic process, main reducer drive shaft transmission (or input shaft and FenDongXiang) output shaft is relative motion between often, in addition to avoid certain institutions or device (not) line, there must be a device to realize the dynamic transfer, then the normal appeared gimbal transmission. Universal must have the following characteristics: the transmission and ensure that the relative position of the two shafts in expected range changes, can reliably transfer power, B, ensure that connects the two shafts could even operation. Due to the universal and additional load Angle, the vibration and noise should be allowed in, C, high transmission efficiency, long service life, simple structure, easy fabrication, easy maintenance. For automobile, due to a cross gimbal output shaft relative to the input shaft (have) is not constant rotation Angle, therefore, must adopt double gimbal (or more), and the universal shaft driving connected with the two cardan arrangement in the same plane and make two equal to the Angle. It is very important. In the design to minimizethe Angle.Shaft assembly imbalance is the transmission of the bending vibration. The cause of the vibration noise is obvious. In addition, the universal joint cardan shaft kiln, axial clearance, the sliding spline shaft assembly precision, peeling ends when high-speed rotary shaft transmission and the elastic deformation of a hot spot balance affecting factors can change the imbalance of shaft assembly. Reducing the imbalance, shaft for cars, especially the high-speed car like (car) is extremely important, otherwise it will cause a lot of relevant fault or damage.The universal shaft rigidity of vehicle drivetrain is in the most widely used, and the long history. Usually say the shaft is generally refers to the universal shaft rigidity type. The axial rigidity of universal is mainly used in the transmission Angle of CAM flange, generally, the shaft needle bearing assembly, cardan joint or sliding fork, fork or spline fork, needle bearing axial fixation. Ashdod, with the gearbox commonly margin fork shaft drive or other such links. Tu margin with a fork is the flange, generally USES the fork form part of the carbon steel or medium-carbon steel forging, also have adopted the ductile iron castings and sand carbon steel or medium-carbon steel high precision castings. Tu margin with a flat binary general, also have brought a flanged end flange of trapezoidtooth. The shaft needle bearing assembly includes four needle bearing, a cross axis, a grease. Roller bearings are generally consists of several needle roller bearings, a bowl, a blade rubber seal (more than with partial skeleton). In some needle bearing, and a belt round bearings, nylon, gasket also adopts copper or other materials, mainly for the decrease of universal shaft axial clearance, improve the quality of dynamic balance. A binary form cardan parts, generally USES medium-carbon steel or carbon steel forging parts, also have adopted the precision casting medium-carbon steel. Needle bearing axial fixation thing is generally holes (or axis) with elastic ring (internal and external), or bearing the cassette, bolt locking plate, etc.Another shaft is an important part of the spline is sliding, internal and external spline (rectangular), and the involute used to convey length change.The universal shaft and sliding swinging Angle of slip is biggest spline is decorated, according to the vehicle shaft and beat the check.Transmission of low carbon steel tube generally made of steel wire coiling of big norms, the tube, also have adopted the cold drawn seamless tube. The tube diameter and wall thickness (or diameter) is based on the maximum transmission torque, highest speed conditions of work. Hollow shaft tube has smaller quality and can deliver large torque, and the same diameter than the solid shaft possesses higher critical speedcharacteristics.Normally, two gimbal centre distance is not more than 1.5 m. When the distance is close, generally by two universal and a sliding spline shaft, no vice. When the distance and make more than 1.5 m shaft length, often divided into two or three roots, using three or four joints, and finally a belt, the rest of the spline vice sliding bearing structure among belt.Typical middle by a supporting general cylindrical ball bearing, a housing, two seal, a rubber pad, a grease mouth. By supporting bracket among middle shaft connecting to the frame beams, transmission line and the middle axis required support among perpendicular to the plane. General layout in supporting shaft transmission system among the first-order critical speed nodes.In use process, generally need timely maintenance. In the joints, sliding bearing etc, among the spline is fat mouth place, want to periodically according to related regulations prescribed grease filling. Also have adopted in maintenance free universal shaft bearings and support in the reserve, need not regular grease filling grease.Second, the universal descriptionUniversal joint is a key component of the car transmission. In front of the rear wheel drive motor vehicle, universal shaft installed in transmission and the output shaft drive between input shaft gearreducer, And lead the front wheel drive motor vehicle omitted, universal shaft driving is responsible for installation in the front axle and be responsible for steering wheels and half shaft.Automobile is a movement of objects. The bus driver, engine, clutch and transmission as a whole, and installed in the frame by elastic suspension frame and drive connections between a distance, the need for connection. The car runs in rough pavement produces change, load or two assembly location, will make the output shaft transmission with the reducer drive shaft Angle between input and the distance change, therefore, to use a "in changing" devices to solve this question, it is the universal.In between, off-road vehicle transmission and the front drive thansfer can turn with half shaft drive between the universal, need to do ". The structure and function of a bit like human limbs, it is allowed to connect the Angle between the parts. But it and body joints and different forms of activities, it only allows the Angle of the change in a certain range.Universal shaft type is the universal, rigid patterned (double axle and three pin shaft type), patterned (ball fork and ball cage), cross gimbal sex. After the car at the most widely used a cross gimbal.Single gimbal cannot make the output shaft and the instantaneous velocity of axle shaft vibration, easy to cause the equal parts, aggravate the damage, produce a lot of noise.Therefore, after the car driver using universal form of transmission shaft double gimbal, is a universal at each end, its function is equal to the transmission Angle, both the output shaft and the instantaneous velocity of axle shaft always equal.In order to satisfy the power transmission, steering and auto operation generated by beating down before the Angle, drive the car drive shaft and the wheel, and also used between universal connected. Due to the limit, the axial dimensions of landform and bigger, request to do, so common universal widely adopted various patterned. In general, the former drive car every half shaft with two patterned, near the speed of universal joint is a half drive axle shaft inside, near the universal shaft lateral velocity is half. In various patterned, common ball cage is universal, it with six steel ball force, driving shaft and driven shafts intersect in any of the circumstances, the ball is located on the intersection of two in two axis, namely the equally intersect, thus ensure the driven shaft, equal angles speed transmission.附录B 外文文献中文翻译传动轴简介传动轴,在不同轴心的两轴间甚至在工作过程中相对位置不断变化的两轴间传递动力。