11-第十一章 氢化丁腈橡胶-120216
氢化丁腈橡胶耐温范围

氢化丁腈橡胶耐温范围氢化丁腈橡胶(HNBR)是一种具有出色耐热性能的合成橡胶材料。
它在高温环境下表现出卓越的耐候性、耐油性和抗老化能力。
在本文中,我们将探讨氢化丁腈橡胶的耐温范围、其在不同温度下的特性以及其适用性。
1. 什么是氢化丁腈橡胶?氢化丁腈橡胶是由丁腈橡胶(NBR)经过氢化处理而得到的一种改性橡胶材料。
氢化处理将部分丁腈单体中的双键转变为单键,从而提高了其耐热性能。
它通常以HNBR缩写来表示。
2. 氢化丁腈橡胶的耐温范围HNBR具有良好的耐高温性能,其耐温范围通常在-40°C至150°C之间。
这使得它能够在广泛的工业应用中承受高温环境下的挑战。
相比于一般丁腈橡胶,HNBR可以在更高的温度下保持其物理性能和化学特性。
3. 氢化丁腈橡胶的特性在不同温度下,HNBR表现出不同的特性,这些特性对其在不同应用中的适用性至关重要。
a. 低温特性:HNBR在低温下仍能保持其弹性和柔软性。
在-40°C的极寒环境下,它能保持较好的尺寸稳定性和耐用性。
b. 中温特性:在中温范围内,HNBR表现出较高的可塑性和弹性模量,这使其成为许多密封应用的理想选择。
它在温度为~80°C至100°C之间表现出最佳的物理性能。
c. 高温特性:HNBR在高温环境下仍然能保持良好的弹性和耐久性。
在持续暴露于150°C的高温下,它仍然能够保持其原有的弹性模量和拉伸强度。
4. 氢化丁腈橡胶的应用HNBR由于其出色的耐温性能,在许多工业领域中得到广泛应用。
以下是一些常见的应用领域:a. 汽车工业:HNBR被广泛用于汽车发动机和传动系统的密封件、振动垫圈等部件中,以应对高温和高压的环境要求。
b. 石油和天然气行业:HNBR在石油和天然气开采、输送和处理过程中,用于制造密封件、O型圈和其他耐热部件。
c. 制药和食品工业:HNBR广泛应用于制药和食品加工设备中的密封件,以满足高温和卫生要求。
氢化丁腈橡胶
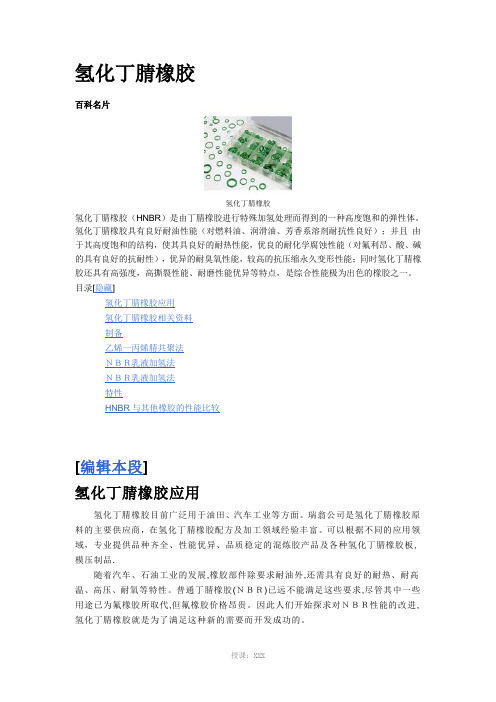
氢化丁腈橡胶百科名片氢化丁腈橡胶氢化丁腈橡胶(HNBR)是由丁腈橡胶进行特殊加氢处理而得到的一种高度饱和的弹性体。
氢化丁腈橡胶具有良好耐油性能(对燃料油、润滑油、芳香系溶剂耐抗性良好);并且由于其高度饱和的结构,使其具良好的耐热性能,优良的耐化学腐蚀性能(对氟利昂、酸、碱的具有良好的抗耐性),优异的耐臭氧性能,较高的抗压缩永久变形性能;同时氢化丁腈橡胶还具有高强度,高撕裂性能、耐磨性能优异等特点,是综合性能极为出色的橡胶之一。
目录[隐藏]氢化丁腈橡胶应用氢化丁腈橡胶相关资料制备乙烯一丙烯腈共聚法NBR乳液加氢法NBR乳液加氢法特性HNBR与其他橡胶的性能比较[编辑本段]氢化丁腈橡胶应用氢化丁腈橡胶目前广泛用于油田、汽车工业等方面。
瑞翁公司是氢化丁腈橡胶原料的主要供应商,在氢化丁腈橡胶配方及加工领域经验丰富。
可以根据不同的应用领域,专业提供品种齐全、性能优异、品质稳定的混炼胶产品及各种氢化丁腈橡胶板,模压制品.随着汽车、石油工业的发展,橡胶部件除要求耐油外,还需具有良好的耐热、耐高温、高压、耐氧等特性。
普通丁腈橡胶(NBR)已远不能满足这些要求,尽管其中一些用途已为氟橡胶所取代,但氟橡胶价格昂贵。
因此人们开始探求对NBR性能的改进,氢化丁腈橡胶就是为了满足这种新的需要而开发成功的。
[编辑本段]氢化丁腈橡胶相关资料HNBR的耐高温性为130~180℃,耐寒性为-55~-38℃且机械性能优良,与其它聚合物相比更能满足汽车工业的要求。
用ZnO/甲基丙烯酸(MAA)补强的HNBR可制作三角带、等规三角带、多用三角环的底层胶、隔振器等;也可制备密封圈、密封件,耐热管等。
在石油钻井中,要求橡胶制品必须耐受高温、高压、酸、胺、H2S、CO2、CH4等蒸汽的考验。
而用HNBR制备的各种制品,可耐酸、耐油、耐溶剂。
用ZnO/MAA补强的HNBR可用于制作钻井保护箱和泥浆泵用活塞.此外,采用打浆法将HNBR制成纸型垫圈可用作石油工业及汽车工业的密封垫圈。
氢化丁腈橡胶的结构与性能_图文(精)

加工・应用合成橡胶工业,2008-03-15,31(2:118~121CH I N A SY NTHETI C RUBBER I N DUSTRY氢化丁腈橡胶的结构与性能朱景芬1,2,黄光速1,李锦山2,胡海华2(11四川大学高分子科学与工程学院,四川成都610065;21中国石油兰州化工研究中心,甘肃兰州730060摘要:考察了丁腈橡胶(NBR氢化过程中聚丁二烯的顺式-1,4-结构、反式-1,4-结构及乙烯基微观结构的变化,讨论了不同氢化度的氢化丁腈橡胶(HNBR的热氧化稳定性、硫化特性和力学性能的差异。
结果表明,在NBR加氢过程中,聚丁二烯的乙烯基加氢速率最快,其次是反式-1,4-结构,加氢速率最慢者是顺式-1,4-结构,腈基未被氢化;氢化度为90%的HNBR的热氧化稳定性远优于NBR,而氢化度为95%的HNBR的热氧化稳定性更优;随着氢化度的增加,HNBR的硫化特性未见明显改变;HNBR硫化胶的拉伸强度高于NBR,而其扯断伸长率则小于NBR,并且随着HNBR氢化度的提高,HNBR与NBR的拉伸强度、扯断伸长率差值增大。
关键词:氢化丁腈橡胶;丁腈橡胶;微观结构;热氧化稳定性;硫化特性;力学性能中图分类号:T Q33317文献标识码:B文章编号:1000-1255(200802-0118-04丁腈橡胶(NBR通过氢化作用使其分子链中聚丁二烯链节上的双键达到饱和,从而得到了高性能的氢化丁腈橡胶(HNBR。
HNBR中的饱和结构赋予其优异的弹性、耐热性、耐氧化性、化学稳定性及低温曲挠性等。
国内外许多学者对HNBR的制备及应用进行了广泛的研究[1-9],但对其结构与性能的研究却涉及较少,且研究的侧重点与本研究有所不同[10]。
本工作主要考察了氢化过程中聚丁二烯的顺式-1,4-结构、反式-1,4-结构及乙烯基3种微观结构的变化规律,讨论了不同氢化度HNBR的热氧化稳定性、硫化特性和力学性能的差异。
1实验部分111原材料氢化度分别为60%,80%,90%,95%,99%的HNBR,采用质量分数为10%的NBR 氯苯溶液,以氯化铑的络合物为催化剂,在温度为70~ 120℃、压力为7~12MPa下进行氢化反应,用甲醇凝聚胶液,真空烘干后即得不同氢化度的HNBR,中国石油兰州化工研究中心中试产品; NBR,牌号为N21,结合丙烯腈质量分数为40%,门尼黏度为82,中国石油兰州石化公司产品;其他均为橡胶工业常用助剂。
氢化丁腈橡胶
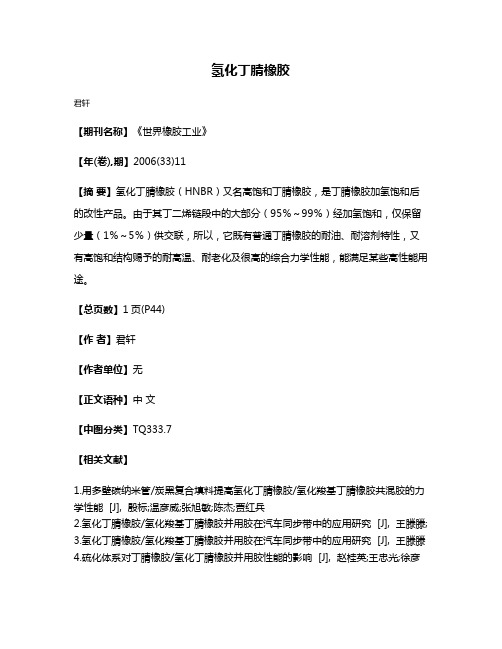
氢化丁腈橡胶
君轩
【期刊名称】《世界橡胶工业》
【年(卷),期】2006(33)11
【摘要】氢化丁腈橡胶(HNBR)又名高饱和丁腈橡胶,是丁腈橡胶加氢饱和后的改性产品。
由于其丁二烯链段中的大部分(95%~99%)经加氢饱和,仅保留少量(1%~5%)供交联,所以,它既有普通丁腈橡胶的耐油、耐溶剂特性,又有高饱和结构赐予的耐高温、耐老化及很高的综合力学性能,能满足某些高性能用途。
【总页数】1页(P44)
【作者】君轩
【作者单位】无
【正文语种】中文
【中图分类】TQ333.7
【相关文献】
1.用多壁碳纳米管/炭黑复合填料提高氢化丁腈橡胶/氢化羧基丁腈橡胶共混胶的力学性能 [J], 殷标;温彦威;张旭敏;陈杰;贾红兵
2.氢化丁腈橡胶/氢化羧基丁腈橡胶并用胶在汽车同步带中的应用研究 [J], 王滕滕;
3.氢化丁腈橡胶/氢化羧基丁腈橡胶并用胶在汽车同步带中的应用研究 [J], 王滕滕
4.硫化体系对丁腈橡胶/氢化丁腈橡胶并用胶性能的影响 [J], 赵桂英;王忠光;徐彦
红;李兰勖;陈宏宇
5.丁腈橡胶和氢化丁腈橡胶与金属的粘合性能研究 [J], 赵晴
因版权原因,仅展示原文概要,查看原文内容请购买。
氢化丁腈橡胶基础配方-概述说明以及解释

氢化丁腈橡胶基础配方-概述说明以及解释1.引言1.1 概述在全球范围内,氢化丁腈橡胶作为一种特殊的合成橡胶材料,具有优异的耐油、耐热、耐寒、耐臭氧性能,被广泛应用于汽车轮胎、橡胶密封制品、橡胶软管等领域。
本文旨在介绍氢化丁腈橡胶的基础配方设计原则和关键要点,以及其在不同应用领域中的具体应用情况,旨在帮助读者更深入地了解氢化丁腈橡胶的特性和应用。
1.2 文章结构本文将分为引言、正文和结论三部分。
在引言中,将介绍本文的背景和目的,帮助读者更好地理解氢化丁腈橡胶基础配方的重要性和应用价值。
在正文部分,将详细介绍氢化丁腈橡胶的特性和基础配方要点,同时探讨其在不同应用领域中的具体应用情况。
最后,在结论部分,将对本文的内容做出总结,并展望未来氢化丁腈橡胶在橡胶工业中的发展方向。
通过整体结构的安排,旨在全面而系统地介绍氢化丁腈橡胶基础配方的相关知识,为读者提供全面的了解和参考。
1.3 目的本文旨在深入探讨氢化丁腈橡胶的基础配方,通过对其介绍、要点和应用领域的详细分析,帮助读者全面了解这种特殊橡胶材料的特性和优势。
同时,通过对氢化丁腈橡胶的研究,可以为相关领域的工程师和科研人员提供参考和指导,促进氢化丁腈橡胶在实际应用中的进一步发展和创新。
我们希望通过本文的撰写,能够为读者带来有益的知识和启发,推动氢化丁腈橡胶在工业领域的广泛应用和推广。
2.正文2.1 氢化丁腈橡胶介绍:氢化丁腈橡胶是一种特殊的合成橡胶,也被称为HNBR。
它是通过对丁腈橡胶进行氢化处理而得到的,氢化处理可以降低橡胶的不饱和度,提高其耐热性、耐油性和耐臭氧性能。
氢化丁腈橡胶具有良好的耐磨耗性、耐高温性、耐油性和耐臭氧性能,因此在汽车、航空航天、石油化工等领域有着广泛的应用。
它可以被用于制造密封件、O型圈、振动吸收器等零部件,以及耐油管道、密封垫等产品。
由于氢化丁腈橡胶具有优异的耐磨损性能和耐化学品性能,因此在一些高要求的工业领域中得到了广泛应用。
氢化丁腈橡胶 (2)

氢化丁腈橡胶简介氢化丁腈橡胶(Hydrogenated Nitrile Butadiene Rubber,HNBR)是一种合成橡胶,由合成橡胶领域的科学家开发出来,以满足特定的工业需求。
氢化丁腈橡胶在耐油性、耐热性、耐化学品等方面具备优异的性能,因此在汽车、航空航天、石油化工等领域得到广泛应用。
本文将介绍氢化丁腈橡胶的特性、制备方法、应用领域以及优缺点。
特性1. 耐油性氢化丁腈橡胶具有极佳的耐油性,可以在高温、高压和恶劣的工作环境下保持其性能稳定。
这使得氢化丁腈橡胶成为汽车发动机密封件、油封等耐油性要求较高的零部件的理想材料。
2. 耐热性HNBR具有优异的耐热性能,在高温环境下仍然可以保持良好的性能。
一般情况下,HNBR的使用温度范围可达-40℃至150℃,在一些特殊的应用场合下,甚至可以达到200℃。
3. 耐化学品性HNBR对于酸、碱等广谱化学物质具有较好的耐受性。
它可以在很多腐蚀性介质中长时间工作,不会因接触化学物质而引发化学反应。
4. 抗老化性HNBR具有较好的抗氧化和抗紫外线性能,其寿命更长。
这使得HNBR在户外设备、气候变化较大的环境下依然能够保持其原有的性能。
5. 弹性良好HNBR具有很好的弹性,即使在高温、高压情况下也能保持较好的弹性变形性能。
这使得HNBR广泛应用于密封件、振动隔离垫等领域。
制备方法氢化丁腈橡胶的合成方法通常是通过在丁腈橡胶的分子链上引入氢原子而实现的。
在这个过程中,需要使用催化剂来催化反应,以实现橡胶分子链上部分或全部丁烯基转化为丁烯基氢化物。
这样一来,氢化丁腈橡胶的分子链就引入了更多的饱和键,提高了其耐热性、耐油性等性能。
应用领域HNBR由于其优异的性能,在许多工业领域得到了广泛应用:1. 汽车行业氢化丁腈橡胶被广泛应用于汽车行业,特别是引擎系统中的耐油密封件。
它可以承受高温高压下的恶劣环境,保护引擎的正常运行。
2. 航空航天在航空航天领域,HNBR广泛应用于液压密封件、燃料储存系统等需要耐热、耐油性能的部件。
氢化丁腈橡胶配方
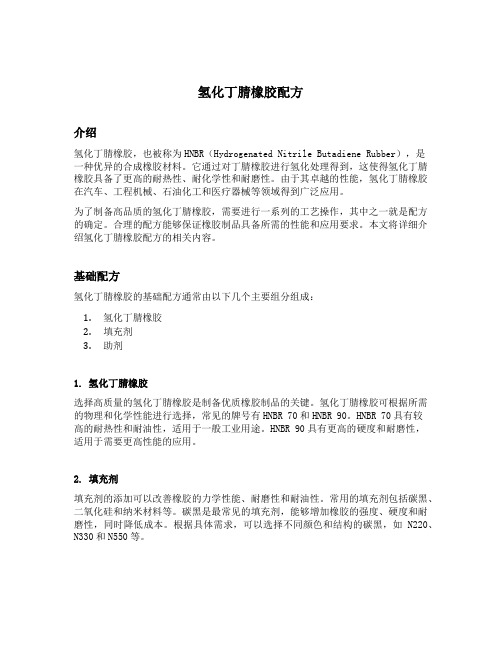
氢化丁腈橡胶配方介绍氢化丁腈橡胶,也被称为HNBR(Hydrogenated Nitrile Butadiene Rubber),是一种优异的合成橡胶材料。
它通过对丁腈橡胶进行氢化处理得到,这使得氢化丁腈橡胶具备了更高的耐热性、耐化学性和耐磨性。
由于其卓越的性能,氢化丁腈橡胶在汽车、工程机械、石油化工和医疗器械等领域得到广泛应用。
为了制备高品质的氢化丁腈橡胶,需要进行一系列的工艺操作,其中之一就是配方的确定。
合理的配方能够保证橡胶制品具备所需的性能和应用要求。
本文将详细介绍氢化丁腈橡胶配方的相关内容。
基础配方氢化丁腈橡胶的基础配方通常由以下几个主要组分组成:1.氢化丁腈橡胶2.填充剂3.助剂1. 氢化丁腈橡胶选择高质量的氢化丁腈橡胶是制备优质橡胶制品的关键。
氢化丁腈橡胶可根据所需的物理和化学性能进行选择,常见的牌号有HNBR 70和HNBR 90。
HNBR 70具有较高的耐热性和耐油性,适用于一般工业用途。
HNBR 90具有更高的硬度和耐磨性,适用于需要更高性能的应用。
2. 填充剂填充剂的添加可以改善橡胶的力学性能、耐磨性和耐油性。
常用的填充剂包括碳黑、二氧化硅和纳米材料等。
碳黑是最常见的填充剂,能够增加橡胶的强度、硬度和耐磨性,同时降低成本。
根据具体需求,可以选择不同颜色和结构的碳黑,如N220、N330和N550等。
3. 助剂助剂的添加可以改善氢化丁腈橡胶的加工性能和终产品的性能。
常见的助剂包括增塑剂、硫化剂、抗老化剂和增黏剂等。
•增塑剂用于调节橡胶的硬度和柔韧性,常见的增塑剂有硫化脂和石蜡等。
•硫化剂用于促进橡胶在加热和压缩的条件下,形成交联结构,提高橡胶的力学性能和耐热性。
•抗老化剂可以延长橡胶制品在使用过程中的寿命,常用的抗老化剂有光稳定剂和热稳定剂等。
•增黏剂用于改善橡胶的粘合性能,常用的增黏剂有甲醇、特氟龙和聚硫化钠等。
配方优化为了制备具有目标性能的氢化丁腈橡胶制品,需要对配方进行优化。
氢化丁腈橡胶配方
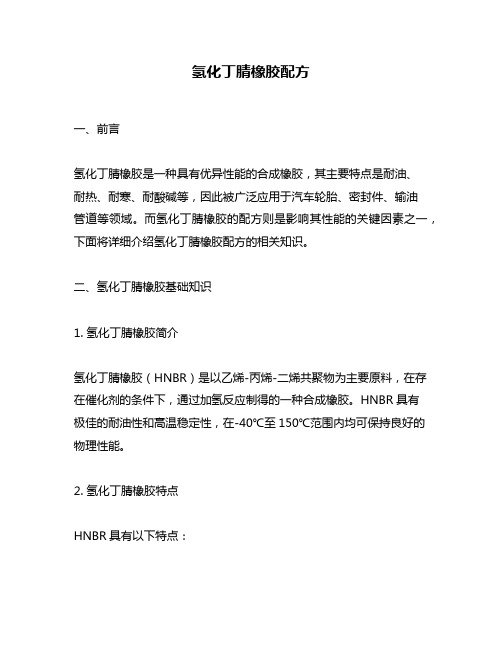
氢化丁腈橡胶配方一、前言氢化丁腈橡胶是一种具有优异性能的合成橡胶,其主要特点是耐油、耐热、耐寒、耐酸碱等,因此被广泛应用于汽车轮胎、密封件、输油管道等领域。
而氢化丁腈橡胶的配方则是影响其性能的关键因素之一,下面将详细介绍氢化丁腈橡胶配方的相关知识。
二、氢化丁腈橡胶基础知识1. 氢化丁腈橡胶简介氢化丁腈橡胶(HNBR)是以乙烯-丙烯-二烯共聚物为主要原料,在存在催化剂的条件下,通过加氢反应制得的一种合成橡胶。
HNBR具有极佳的耐油性和高温稳定性,在-40℃至150℃范围内均可保持良好的物理性能。
2. 氢化丁腈橡胶特点HNBR具有以下特点:(1)优异的耐油性能:HNBR在高温和高压下仍然可以保持良好的耐油性能,因此被广泛应用于汽车、航空、工程机械等领域。
(2)优异的耐热性能:HNBR在高温条件下仍然可以保持较好的物理性能,因此在高温环境下应用广泛。
(3)优异的耐寒性能:HNBR在低温条件下仍然可以保持较好的物理性能,因此在低温环境下应用广泛。
(4)优异的耐酸碱性能:HNBR具有出色的化学稳定性,可以抵抗各种酸碱介质和氧化剂的侵蚀。
三、氢化丁腈橡胶配方1. 氢化丁腈橡胶主要成分氢化丁腈橡胶主要由以下成分组成:(1)乙烯-丙烯-二烯共聚物(2)氢化催化剂(3)填料(4)增塑剂(5)硫化剂和促进剂2. 氢化丁腈橡胶配方设计原则设计氢化丁腈橡胶配方需要遵循以下原则:(1)根据应用领域选择不同的氢化丁腈橡胶种类。
(2)根据应用环境选择不同的填料和增塑剂。
(3)控制硫化剂和促进剂的用量,以达到理想的物理性能。
(4)保证配方稳定性,避免成分变化对产品质量造成影响。
3. 氢化丁腈橡胶配方设计步骤设计氢化丁腈橡胶配方需要遵循以下步骤:(1)确定应用领域和要求。
(2)选择合适的氢化丁腈橡胶种类。
(3)选择填料和增塑剂,控制其用量。
(4)确定硫化剂和促进剂种类及用量。
(5)进行试验验证,优化配方。
四、氢化丁腈橡胶配方试验方法1. 氢化丁腈橡胶物理性能测试氢化丁腈橡胶物理性能测试主要包括:(1)拉伸强度测试:通过试样在拉伸机上施加力来测定其最大拉伸强度、断裂伸长率等指标。
- 1、下载文档前请自行甄别文档内容的完整性,平台不提供额外的编辑、内容补充、找答案等附加服务。
- 2、"仅部分预览"的文档,不可在线预览部分如存在完整性等问题,可反馈申请退款(可完整预览的文档不适用该条件!)。
- 3、如文档侵犯您的权益,请联系客服反馈,我们会尽快为您处理(人工客服工作时间:9:00-18:30)。
第十一章氢化丁腈橡胶一、丁腈橡胶丁腈橡胶又称丁二烯一丙烯腈橡胶,简称NBR,是由丁二烯和丙烯腈经乳液聚合法制得的,平均分子量70万左右。
灰白色至浅黄色块状或粉状固体,相对密度0.95~1.0。
丙烯腈含量为26%的丁腈橡胶玻璃化温度Tg=一52℃,脆化温度Tb=一47℃,而丙烯腈含量为40%的丁腈橡胶玻璃化温度Tg=一22℃。
溶解度参数δ=8.9~9.9,溶于醋酸乙酯、醋酸丁酯、氯苯、甲乙酮等。
丁腈橡胶具有优良的耐油性,其耐油性仅次于聚硫橡胶和氟橡胶,并且具有的耐磨性和气密性。
丁晴橡胶的缺点是不耐臭氧及芳香族、卤代烃、酮及酯类溶剂,不宜做绝缘材料。
耐热性优于丁苯橡胶、氯丁橡胶,可在120℃长期工作。
气密性仅次于丁基橡胶。
丁腈橡胶的性能受丙烯腈含量影响,随着丙烯腈含量增加拉伸强度、耐热性、耐油性、气密性、硬度提高,但弹性、耐寒性降低。
丁腈橡胶耐臭氧性能和电绝缘性能不佳。
耐水性较好。
二、氢化丁腈橡胶氢化丁腈橡胶HNBR是在NBR基础上的高性能橡胶品种。
对NBR链段上丁二烯单元进行选择氢化,不饱和双键加氢反应生成饱和碳-碳单键。
HNBR在分子结构上的特点,使其具有良好的耐热和耐老化性能、耐含腐蚀性添加剂的汽车用油的性能、耐低温性能,以及具有能在高温下仍保持与常温相当的物理机械性能的品质。
三、HNBHNBR工业级产品及应用目前工业化生产主要品种有德国Bayer公司的Therban系列、加拿大Polysar 公司的Tornac系列和日本Zeon公司的Zetpol系列。
HNBR以其优异的耐油、耐热和耐老化性能已在发达国家的汽车、油田等工程领域得到广泛应用。
在汽车工程中的应用:汽车传动系统油封、燃油喷射系统密封件、同步齿轮带、转向油管等部件。
在油田工程中的应用:井口密封、油赛密封、泵定子保护器、钻井平台配套软管等。
在机械工程中的应用:静、动密封场密封件。
其他应用:主要方向为塑料、橡胶的共混改性技术。
四、二硫化钼改性HNBR摩擦学性能及其在特大尺寸转塔密封圈中的应用某型密封圈是大型方位轴承和俯仰轴承及其转塔内机械、电器设备的动态密封屏障,必须具备两项使用性能:(1)密封性好;(2)滑动摩擦阻尼小。
密封圈首先要达到密封要求,尤其是对Y型密封圈要求更高,应达到气密封的要求。
该气密封指标为当密封圈内外压差为10毫巴时气体泄漏量不超过5升/分钟。
密封性依赖于密封圈的密封边变形压紧力是否既大而又持久。
密封圈必须同时具有摩擦阻尼小,不影响轴承的运动灵活性的特点。
这样既要求密封圈材料的摩擦系数要小,又要求Y型密封圈的密封边变形压紧力也要小。
要满足密封圈的良好密封性和低摩擦阻尼性,在密封边变形压紧力的设计上存在矛盾,只能是力求达到密封边变形压紧力适当,在满足气密封要求的基础上,再尽量降低密封边变形压紧力,使得当大转塔的推力滚动轴承摩擦系数不超过0.01时,大转塔的旋转起动力矩不超过1000Nm,达到发射转塔的总体设计要求。
转塔密封圈示意图4.1、材料改性根据密封圈对材料的性能要求,对三种橡胶进行配方设计的系统研究。
对比配方材料的性能采取兼顾强度和弹性、突出压缩永久变形性能、保证低摩擦系数和抗老化性能的原则。
改性前HNBR 与指标要求相比较基座转塔橡胶的滑动摩擦系数通常较大。
为了降低橡胶的摩擦系数,在配方中选用二硫化钼(MoS2)、聚四氟乙烯(PTFE)和石墨等固体润滑剂作为减摩添加剂。
这些减摩剂通常用于塑料的减摩改性,引入橡胶后预期也能降低摩擦系数,同时在密封圈长期使用后失油而干摩擦时,能起到一定的固体润滑保护作用,防止密封圈摩擦和磨损失效。
但是在配方设计和筛选中,必须避免这些减摩剂的加入对橡胶强度和弹性特别是对压缩永久变形的不利影响。
根据动密封的特点,在橡胶材料配方设计上,将硬度预期值定为70~75度(邵尔A型)左右,并且确定硬度的允许范围为65~80度,在橡胶配方筛选中,超出硬度允许范围的配方一般于以舍去。
补强剂采用了活性较大的半补强碳黑和高耐磨碳黑,前者有利于降低压缩永久变形,后者有利于提高耐磨性。
在密封圈的研制阶段中,先后设计了70多种配方,进行了6轮橡胶配方设计、改进和筛选。
配方编号中第一个数字代表胶种,如“7”代表NBR/PVC,“8”代表NBR,“2”代表HNBR。
后两个数字代表不同的配方组成。
首先通过配方材料的强度、弹性和硬度性能的对比,进行三轮配方材料和硫化工艺参数的筛选,选出17种配方,其机械性能试验结果见表1。
然后比较压缩永久变形性能优劣,从中优选出8种配方材料(见表1)。
再进行滑动摩擦磨损性能试验研究,试验结果列于表1。
通过摩擦系数、耐磨性的进一步对比,优选出各种系列的最佳配方各一种,即HNBR系列配方的2-42、NBR系列的8-42和NBR/PVC系列的7-32。
最后对上述三种配方材料进行大车胶料的材料性能全面测试评价,确定2-42的HNBR配方材料性能最佳。
因此,虽然在密封圈研制的试样阶段采用了国产胶料NBR和NBR/PVC的配方材料8-42和7-32,其材料性能除使用寿命外也基本满足技术要求,而从正样开始直至后来的试生产产品,均采用2-42的HNBR材料。
表1. 各种橡胶配方的机械性能对比橡胶材料耐磨粒磨损性能通常是优异的,而本项目密封圈使用时磨损形式为橡胶密封边与轴承的铝合金阳极氧化光滑表面间滑动摩擦磨损。
因此,滑动摩擦磨损试验在瑞士造Amsler摩擦磨损试验机上进行。
摩擦副采用环/块对磨形式,橡胶试样为7×30×2.5(mm),工作表面为7×30(mm)表面,对磨的环为Φ40×10(mm),采用L Y12硬质铝合金表面硬质阳极氧化处理,表面硬度350~400HV,相对滑动线速度0.42m/s,试验负荷50N,试验时间为2hr。
每种配方试样进行3次平行试验,取平均值。
从表2中可见,滴油润滑情况下,摩擦系数很接近,配方不同几乎没有影响,而且都达到项目技术指标的要求;干摩擦和涂润滑脂时,7-32和8-42两种配方材料在各自系列中摩擦系数最低,磨损量最小。
因此,选定7-32和8-42以及2-42配方为下一步大车胶料的材料各项性能试验考核的配方。
表2. 几种橡胶配方材料的滑动摩擦磨损性能** 每小时开始时加一次油共3滴,30#机油。
*** 试验开始前涂锂基润滑脂一次。
4.2 橡胶硫化工艺由于该项目研究的密封圈尤其是Y型密封圈是长期处于压缩变形下的动密封圈,为了保证其动密封特性,在选择胶型和设定硫化体系时,着重考虑不同橡胶牌号和硫化剂对材料压缩永久变形率的影响,再考虑耐温性能、耐磨性能和加工工艺性能等。
分段硫化工艺流程图4.3 密封圈台架试验为了评价d截面设计作为正样密封圈结构的密封可靠性和运转阻尼,防止所设计的截面结构刚性太小,检查密封条试样的压紧力与变形量试验结果是否符合密封圈,按照d截面设计的形状尺寸,设计和制造了相当于正样密封圈1/6~1/4大小的Φ350mm模拟台架试验用密封圈的硫化模具,试制了4只Φ350mm密封圈,其材料采用制造密封圈的2-42配方胶料。
密封圈模拟试验台架是借助于35毫米立式钻床,自行设计制造了上、下密封盘和连接法兰、轴等一套密封机构,并且配置U型水银压力计和充N2气系统。
Φ350mm密封圈嵌装在下盘的槽中,与上盘平面压紧密封,当上盘转动时,密封圈与上盘对磨,上盘材质为45钢,表面光洁度为▽6,密封面涂航空7253润滑脂。
首先进行动态气密封性试验。
密封上盘由钻床驱动,转速68rpm,线速度为1.25m/s。
实际轴承最大转速14rpm,其最大线速度为方位轴承1.56m/s和俯仰轴承1.02m/s,台架试验线速度为两者之平均值。
密封圈和上、下盘围成的空间内充N2气体,达表压15毫巴。
将密封圈压缩变形0.67mm左右,连续转动70分钟,从U型水银压力计的显示可见,始终无气体泄漏;试验后观察密封圈的摩擦接触面,未见有表面磨痕。
然后进行运转阻尼试验。
把15kg重的上盘自由放在密封圈上,缓慢拉转上盘,由弹簧测力器测量出起动摩擦力在16N左右,但随着上盘不停转动,摩擦力逐渐增大到80N左右。
这时若提取上盘可发现密封圈紧紧吸住上盘,表明Y 形状的双密封边的腔内产生气体真空吸附,摩擦力显然受到真空吸附力影响,而且这种影响远远大于变形压紧力的作用,因此运转阻尼过大。
针对Y型双边密封产生真空吸附造成运转阻尼过大的问题,采取将Y形状的内侧密封边剪短2~3mm的措施,使之不再起密封作用,剩余部分相当于Y 型单边密封圈,再进行与上述相同的气密封和运转阻尼模拟台架试验。
动态气密封性能试验仍采用摩擦线速度1.25m/s,充N2表压15毫巴,连续运转70分钟,密封圈压缩变形量定为1.0mm左右,试验结果气体泄漏量为0,密封圈摩擦接触面无磨痕。
这表明Y型单边密封圈的动态和静态密封性能,远远优越于项目技术指标的要求(项目技术指标要求在内外压差为10毫巴时气体泄漏量不超过5立升/分钟)。
试验还证明密封圈材料的耐磨性也较好。
运转阻尼试验结果为,当15kg重的上盘自由放在密封圈上后,密封圈压缩变形量约1.5mm左右,运转阻尼力始终在13N左右。
这就表明密封圈改为单边密封后,密封边滑动摩擦系数约为0.09。
将上述试验结果换算到Φ2134mm方位轴承密封圈上,假定压缩变形量为1.5mm,则运转阻尼力为79N左右,仍在允许范围内。
项目研究小组总结分析了气密封和运转阻尼模拟台架试验结果,向军工主管单位航天机电集团二院206所提出Y型密封圈由双边密封改为Y型长短脚单边密封的重大改进方案,得到批准以后,从正样密封圈开始予以实施。
现设计Y 型密封圈密封边高度20.5mm,非密封边高度为18.5mm。
轴承密封间隙约19.3mm 左右,则密封边压缩变形设计值约为1.2mm。
非密封边对保存润滑脂和结构均衡性仍起到一定作用。
所项目研究小组按照上述新的截面设计方案,重新设计和精密加工大型橡胶硫化模具,4米长整体加工再分割成3米和1米长两套模具,从而保证了密封圈产品截面形状和尺寸精度符合设计要求和项目的技术指标要求,使正样试制和批生产获得成功。