稠油集输工艺优化改进
油田集输原油脱水工艺的优化与改进
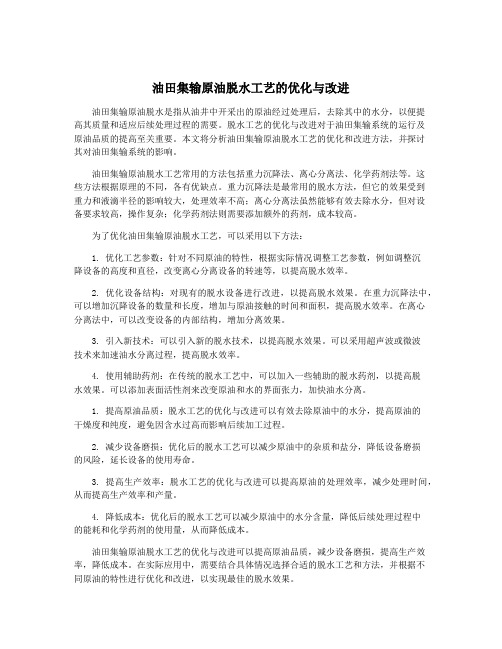
油田集输原油脱水工艺的优化与改进油田集输原油脱水是指从油井中开采出的原油经过处理后,去除其中的水分,以便提高其质量和适应后续处理过程的需要。
脱水工艺的优化与改进对于油田集输系统的运行及原油品质的提高至关重要。
本文将分析油田集输原油脱水工艺的优化和改进方法,并探讨其对油田集输系统的影响。
油田集输原油脱水工艺常用的方法包括重力沉降法、离心分离法、化学药剂法等。
这些方法根据原理的不同,各有优缺点。
重力沉降法是最常用的脱水方法,但它的效果受到重力和液滴半径的影响较大,处理效率不高;离心分离法虽然能够有效去除水分,但对设备要求较高,操作复杂;化学药剂法则需要添加额外的药剂,成本较高。
为了优化油田集输原油脱水工艺,可以采用以下方法:1. 优化工艺参数:针对不同原油的特性,根据实际情况调整工艺参数,例如调整沉降设备的高度和直径,改变离心分离设备的转速等,以提高脱水效率。
2. 优化设备结构:对现有的脱水设备进行改进,以提高脱水效果。
在重力沉降法中,可以增加沉降设备的数量和长度,增加与原油接触的时间和面积,提高脱水效率。
在离心分离法中,可以改变设备的内部结构,增加分离效果。
3. 引入新技术:可以引入新的脱水技术,以提高脱水效果。
可以采用超声波或微波技术来加速油水分离过程,提高脱水效率。
4. 使用辅助药剂:在传统的脱水工艺中,可以加入一些辅助的脱水药剂,以提高脱水效果。
可以添加表面活性剂来改变原油和水的界面张力,加快油水分离。
1. 提高原油品质:脱水工艺的优化与改进可以有效去除原油中的水分,提高原油的干燥度和纯度,避免因含水过高而影响后续加工过程。
2. 减少设备磨损:优化后的脱水工艺可以减少原油中的杂质和盐分,降低设备磨损的风险,延长设备的使用寿命。
3. 提高生产效率:脱水工艺的优化与改进可以提高原油的处理效率,减少处理时间,从而提高生产效率和产量。
4. 降低成本:优化后的脱水工艺可以减少原油中的水分含量,降低后续处理过程中的能耗和化学药剂的使用量,从而降低成本。
油气集输工艺流程优化

油气集输工艺流程优化
油气集输工艺流程优化是指通过对油气集输工艺流程的优化和改进,提高生产效率、降低能源消耗、减少环境污染等方面的指标。
本文将从工艺流程的优化目标、优化方法和优化效果三个方面进行探讨。
一、优化目标
油气集输工艺流程的优化目标主要包括以下几个方面:
1. 提高生产效率:通过优化工艺流程,减少生产中的能源浪费和材料浪费,提高设备的利用率和生产的效率。
2. 降低能源消耗:通过改进工艺流程,减少能源的消耗,实现节能减排的目标。
3. 减少环境污染:通过优化工艺流程,减少废弃物和废气的排放,降低环境污染。
4. 提高产品质量:通过改进工艺流程,提高产品的质量,提高企业的竞争力。
二、优化方法
1. 流程改造:通过对工艺流程的分析和优化,找出存在的问题和瓶颈,进行合理的调整和改造,提高流程的效率。
2. 技术创新:通过引进新的技术和设备,优化工艺流程,提高生产效率和产品的质量。
3. 设备升级:对旧设备进行改造和升级,提高设备的自动化水平和生产效率。
4. 增加监控和控制环节:通过增加监控和控制环节,减少工艺中的误差和波动,提高生产的稳定性和一致性。
5. 优化原料配比:通过优化原料的配比,提高产品的质量和稳定性。
三、优化效果
通过对油气集输工艺流程的优化,可以取得以下效果:
油气集输工艺流程的优化是提高生产效率、降低能源消耗、减少环境污染和提高产品质量的重要手段。
通过对工艺流程的优化,可以实现更高效、更环保和更可持续的生产。
浅析稠油集输工艺优化改进

0 引 言
键设备是掺水泵、 外输泵和 加热炉 。这些 设备 的运行状 况 直 接影响着热采 管理 区的原 油上产工 作 , 因此 , 如 何优化 集输工 艺, 保证接转站设备的优质 高效及平稳运行 有着极 其重要 的意义。 1 接转站的生产现 状 掺水接转站 目前拥有的主要设备有 :油水罐 5座 : 燃 料油 罐 3座 ; 油气 分离缓 冲罐 2座 ; 各类 泵 1 9台 : 空气压
t e c h n o l o g y .
关键词 : 稠 油生产; 掺水压力; 掺水温度 ; 掺水水质 ; 加热炉
Ke y wo r d s : h e a v y o i l p od r u c t i o n ; mi x i n g - wa t e r p r e s s u r e ; mi x i n g - wa t e r t e mp e r a t u r e ; mi x i n g - w a t e r q u li a t y ; h e a t i n g f u r n a c e
e f e c t s t h e o i l p r o d u c t i o n i n he t r ma l ma n a g e me n t a r e a . S t a r t i n g f r o m mi x i n g - w a t e r p r e s s u r e nd a t e mp e r a t u r e a n d w a t e r q u a l i t y , t h e p a p e r d i s c u s s e s he t he t r ma l r e c o v e r y o f h e a v y o i l f r o m na a l y s i s o f i n f l u e n c i n g f a c t o r s a n d i mp r o v i n g me a s u r e s o f g a t h e r i n g a n d t r a n s p o t r a i t o n
油田集输原油脱水工艺的优化与改进
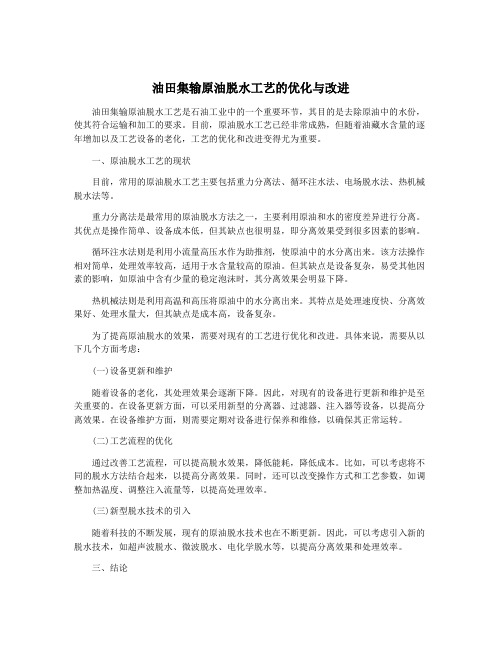
油田集输原油脱水工艺的优化与改进油田集输原油脱水工艺是石油工业中的一个重要环节,其目的是去除原油中的水份,使其符合运输和加工的要求。
目前,原油脱水工艺已经非常成熟,但随着油藏水含量的逐年增加以及工艺设备的老化,工艺的优化和改进变得尤为重要。
一、原油脱水工艺的现状目前,常用的原油脱水工艺主要包括重力分离法、循环注水法、电场脱水法、热机械脱水法等。
重力分离法是最常用的原油脱水方法之一,主要利用原油和水的密度差异进行分离。
其优点是操作简单、设备成本低,但其缺点也很明显,即分离效果受到很多因素的影响。
循环注水法则是利用小流量高压水作为助推剂,使原油中的水分离出来。
该方法操作相对简单,处理效率较高,适用于水含量较高的原油。
但其缺点是设备复杂,易受其他因素的影响,如原油中含有少量的稳定泡沫时,其分离效果会明显下降。
热机械法则是利用高温和高压将原油中的水分离出来。
其特点是处理速度快、分离效果好、处理水量大,但其缺点是成本高,设备复杂。
为了提高原油脱水的效果,需要对现有的工艺进行优化和改进。
具体来说,需要从以下几个方面考虑:(一)设备更新和维护随着设备的老化,其处理效果会逐渐下降。
因此,对现有的设备进行更新和维护是至关重要的。
在设备更新方面,可以采用新型的分离器、过滤器、注入器等设备,以提高分离效果。
在设备维护方面,则需要定期对设备进行保养和维修,以确保其正常运转。
(二)工艺流程的优化通过改善工艺流程,可以提高脱水效果,降低能耗,降低成本。
比如,可以考虑将不同的脱水方法结合起来,以提高分离效果。
同时,还可以改变操作方式和工艺参数,如调整加热温度、调整注入流量等,以提高处理效率。
(三)新型脱水技术的引入随着科技的不断发展,现有的原油脱水技术也在不断更新。
因此,可以考虑引入新的脱水技术,如超声波脱水、微波脱水、电化学脱水等,以提高分离效果和处理效率。
三、结论原油脱水工艺是石油工业中的一个重要环节,其提高分离效果和生成效率对于石油的生产和加工具有重要的影响。
辽河油田典型稠油集输工艺及其优化简化

辽河油田典型稠油集输工艺及其优化简化摘要:辽河油田稠油具有粘度大、密度高、油气比低等特点,在40多年的开发建设过程中,逐渐形成了独具特色的地面集输工艺技术体系,但随着油田开发的深入,开发初期形成的成熟技术与油田生产实际情况不相适应的矛盾日益突出。
本文对辽河油田稠油集输典型流程进行了分析、整理,并提出了如何对现有成熟稠油集输工艺进行优化简化,同时展望了稠油集输工艺技术发展方向。
关键词:稠油粘度集输优化。
1 稠油、超稠油集输工艺1.1 单管加热集输工艺井口来液经加热炉加热后,输往计量站或计量接转站,该工艺集油管线流速通常低于0.5m/s,适用于稠油粘度不大于3000mPa·s(50℃)、单井产液量较高(不小于30t/d)、井口出油温度较高(40℃以上)的稠油集输。
具有流程简单,方便管理,投资少的特点。
1.2 双管掺水集输工艺所谓掺水集输流程即在采油井口加入活性水溶液,达到利用化学药剂降粘、利用水溶液润湿边壁,降阻输送的目的,多用于粘度不大于10000mPa·s的稠油。
回掺水主要利用联合站原油脱出的污水,需建立掺水分输站,掺水比为1.8~2:1(水:油),掺水温度一般在60~65℃。
双管掺水工艺采用集中建站分配水量,减少了掺水泵数量,节约投资和减少耗电量,但掺液量较大,增加集输负荷,油水混合不均,在输送中,当流速较低时,易出现油水分层现象。
1.3 双管掺稀油集输工艺稠油掺稀油是利用两种物性、粘度差别较大,但互溶性好的原油,将其按一定比例互溶在一起,使其具有新的粘度和物性,达到稠油降粘的目的。
稠油掺稀油降粘工艺技术,可以满足任何粘度稠油降粘要求。
应用此工艺需在计量接转站和集中处理站设掺稀油系统,包括稀油的计量、储存、升压、加热、分配等功能。
掺液比为1:0.3~0.7(稠油:稀油),与掺活性水相比,液量减少40%以上,大大减少了集输、脱水、污水处理等工序的负荷,亦相对地减少了设备数量和动力消耗。
油田集输原油脱水工艺的优化与改进

油田集输原油脱水工艺的优化与改进油田集输中的原油脱水工艺是指将原油中的水分去除,提高原油的品质。
原油中的水分会影响原油的质量,降低燃烧效率,同时也会造成管道堵塞和腐蚀等问题。
对油田集输原油脱水工艺进行优化和改进,可以提高生产效率和原油品质的也减少设备维护和管理的成本。
油田集输原油脱水工艺的优化与改进可以从设备选型和操作参数两方面进行考虑。
在设备选型方面,可以选择更先进的脱水设备,如离心脱水机、电磁波脱水机等,提高脱水效率。
还可以考虑引入新的技术和设备,如超声波脱水和湿式电表脱水等,进一步提高脱水效果。
在操作参数方面,应根据不同原油的特性和含水量确定最佳的操作参数,如温度、压力和时间等。
通过调节这些参数,可以改善原油脱水效果,提高脱水率。
还可以考虑引入一些助剂,如表面活性剂和分散剂等,来提高脱水效果,降低能耗。
油田集输原油脱水工艺的优化与改进还可以从工艺流程和设备布置两方面进行考虑。
在工艺流程方面,可以采用多级脱水的工艺流程,将脱水过程分为两个或多个阶段进行,其中每个阶段使用不同的脱水设备和操作参数。
这种多级脱水的工艺流程可以更好地提高脱水效果,降低原油中的水分含量。
在设备布置方面,可以通过合理的布置原油脱水设备来提高脱水效果。
可以将脱水设备放置在靠近水分高的原油的位置,以便更好地去除原油中的水分。
还可以考虑采用多台脱水设备并行工作,以提高脱水效率。
油田集输原油脱水工艺的优化与改进还可以从设备维护和操作管理两方面考虑。
设备维护方面,可以定期对脱水设备进行检查和维护,确保设备的正常运行和脱水效果。
操作管理方面,可以建立完善的操作规程和培训制度,对操作人员进行培训和管理,提高操作人员的技术水平和工作效率。
油田集输原油脱水工艺的优化与改进

油田集输原油脱水工艺的优化与改进油田集输原油脱水工艺是指将含有大量水分的原油经过一系列的处理工艺,使得原油中的水分含量降低到一定的标准要求,从而提高原油的质量和市场竞争力。
优化和改进油田集输原油脱水工艺对于提高生产效率、降低成本以及保护环境都具有重要意义。
下面将从以下几个方面介绍油田集输原油脱水工艺的优化与改进。
油田集输原油脱水工艺的优化与改进可以通过改进物理处理工艺来实现。
传统的物理处理工艺包括沉淀、静置等方法,这些方法操作简单且成本低,但是处理效果有限。
现在的优化和改进工艺中引入了更加先进的技术,如离心分离、螺旋分离、电场和超声波等技术,可以提高原油与水分离的效率,减少水分含量。
还可以采用重力沉降装置和过滤器,使得分离后的水分更加干燥和纯净。
油田集输原油脱水工艺的优化与改进还可以通过改进化学添加剂来实现。
化学添加剂可以在原油与水分离过程中发挥促进分离、抑制乳化和清除杂质等作用。
现在的优化和改进工艺中,常采用的化学添加剂有表面活性剂、分散剂和抗乳化剂等。
这些添加剂可以有效地改善原油与水的界面张力,促进油水分离,减少乳化现象的发生,提高脱水效果。
油田集输原油脱水工艺的优化与改进还可以通过改进设备和工艺流程来实现。
设备上的优化包括增加分离器的数量和尺寸,加大原油流速和流量,增加分离器的升力和沉降筒长度等。
工艺流程上的优化包括提高原油的预处理效果,合理调整油水分离的时间和温度等。
还可以通过人工智能和自动化控制技术来实现工艺的优化和改进,提高生产效率和降低操作人员的工作强度。
油田集输原油脱水工艺的优化与改进还需要注意环境保护。
优化和改进工艺应尽量减少或回收废水和废液的排放,减少对环境的污染。
在选择化学添加剂和设备时,要考虑其对环境的影响和可持续性。
还需要加强设备的运行维护和管理,避免事故和污染的发生。
油田集输原油脱水工艺的优化与改进对于提高原油质量、提高生产效率和保护环境都具有重要意义。
通过改进物理处理工艺、改进化学添加剂、改进设备和工艺流程以及加强环境保护,可以实现油田集输原油脱水工艺的优化与改进。
油田集输原油脱水工艺的优化与改进

油田集输原油脱水工艺的优化与改进
随着我国石油产量的不断增加,油田集输线路中原油脱水工艺越来越受到重视。
脱水对于油田集输线路的稳定运行和原油品质的保证至关重要。
本文旨在探讨油田集输原油脱水工艺的优化与改进。
一、现有脱水工艺存在的问题
1. 传统脱水工艺难以满足高含水原油处理的需求。
传统的原油脱水工艺主要采用重力沉淀、离心分离等方法,需要满足原油含水率小于2%的要求,而对于含水率高于2%的原油,脱水效果较差。
2. 传统脱水工艺的处理效率低。
传统的原油脱水工艺需要长时间的沉淀或离心分离过程,不能快速实现原油脱水的效果,处理效率较低。
3. 传统脱水工艺对设备的要求高。
传统的原油脱水工艺需要大型的脱水设备,设备成本高、占地面积大、维护费用高。
1. 采用新型脱水技术。
如超声波脱水、微波辐射脱水、电场脱水等。
这些技术能够快速实现高含水原油的脱水,并且节约能源,提高脱水效率。
2. 优化脱水设备。
将脱水设备进行分散式分布,进行分层管理,避免使用大型的脱水设备,减少设备成本、占地面积和维护费用等。
三、结语
随着我国石油产业的不断发展,原油脱水工艺的优化与改进已经成为石油企业必须面对的问题。
通过采用新型脱水技术、优化脱水设备和综合运用多种脱水工艺的方法,能够提高原油脱水效率,保证原油品质,为油田集输线路的稳定运行做出贡献。
- 1、下载文档前请自行甄别文档内容的完整性,平台不提供额外的编辑、内容补充、找答案等附加服务。
- 2、"仅部分预览"的文档,不可在线预览部分如存在完整性等问题,可反馈申请退款(可完整预览的文档不适用该条件!)。
- 3、如文档侵犯您的权益,请联系客服反馈,我们会尽快为您处理(人工客服工作时间:9:00-18:30)。
浅析稠油集输工艺优化改进
摘要:胜采一矿热采管理区掺水接转站主要承担着管理区稠油的接收和转输,掺水泵、外输泵和加热炉等关键设备的运行状况直接影响着热采管理区的原油上产工作。
本文从掺水压力、掺水温度及掺水水质等技术指标入手,通过影响因素分析、集输工艺改进措施等方面的阐述,为稠油热采做一番有益的探讨。
abstract: water-mixing and sub pump station of thermal management area in no.1 mine of shengli oil production plant takes the task of receiving and transportation, the operation of key equipment, such as water-mixing pump, sub pump and heating furnace, directly effects the oil production in thermal management area. starting from mixing-water pressure and temperature and water quality, the paper discusses the thermal recovery of heavy oil from analysis of influencing factors and improving measures of gathering and transportation technology.
关键词:稠油生产;掺水压力;掺水温度;掺水水质;加热炉key words: heavy oil production;mixing-water pressure;mixing-water temperature;mixing-water quality;heating furnace
中图分类号:te866 文献标识码:a 文章编号:1006-4311(2013)14-0034-02
0 引言
胜采一矿热采管理区掺水接转站作为管理区三大系统之一,主要承担着管理区稠油的接收和转输,其中的关键设备是掺水泵、外输泵和加热炉。
这些设备的运行状况直接影响着热采管理区的原油上产工作,因此,如何优化集输工艺,保证接转站设备的优质高效及平稳运行有着极其重要的意义。
1 接转站的生产现状
掺水接转站目前拥有的主要设备有:油水罐5座;燃料油罐3座;油气分离缓冲罐2座;各类泵19台;空气压缩机2台;加热炉5台。
具体见下表1。
运行情况:日运行一台150ay67×7型掺水泵、一台js110-170
型外输油泵、两台相变式加热炉及其它部分辅助设备。
见图1。
2 制约稠油生产的主要因素
空心杆掺水制约稠油生产的因素主要有掺水压力、掺水温度和掺水水质三个方面,下面分别论述。
2.1 掺水压力稠油井的平均掺水压力为3mpa,掺水泵的实际运行压力为4.2mpa,管网压降平均达到1.2mpa。
而所需的最佳掺水压力是
3.2mpa,因此,距离最佳掺水压力尚有0.2mpa的差值。
分析原因主要有以下几点:
①掺水管线太长,沿程水力损失较大。
②掺水管线由于受到地理因素限制,沿途拐弯较多,增大了管网的局部磨阻损失,造成压降较大。
③掺水泵的性能参数不能满足目前的生产需要,同时由于运转时间较长,自身性能下降,不能保证稠油生产需求。
2.2 掺水温度稠油井的平均掺水温度为70℃,加热炉的出口温度为70℃,管网温度损失平均达到4-6℃。
稠油井所需最佳掺水温度为70-76℃之间,加热炉能够满足稠油生产需求。
但是存在以下几方面问题:
一是日常运行两台掺水加热炉,冬季更是需要运行三台掺水加热炉,一方面增大了燃油量,增加了成本;另一方面无备用加热炉,一旦加热炉出现故障,就会给生产带来不利影响。
二是掺水加热炉换热器换热效果不好,炉效不高,运行不经济。
三是由于掺水加热炉满负荷运行,一方面缩短了加热炉的使用寿命,另一方面间接增大了空气压缩机、燃料油泵等辅助设备的运转负荷,给日常设备管理带来较大难度。
2.3 掺水水质 2008年,热采管理区共发生堵井97井次,其中因掺水水质不合格造成的堵井有31次,占到了31.96%。
由此产生的措施作业费近48万元。
因此,保证掺水水质合格具有重要的作用。
掺水水质不合格的主要原因有以下几点:①由于注聚产生的聚合物不能很好的分解处理,造成聚合物聚集成块进入空心杆堵井。
②掺水污水中含油及杂质聚集后进入空心杆堵井。
③掺水管线锈蚀及结垢产生的杂质进入空心杆堵井。
3 采取的主要工艺改进措施
针对上述问题,我们结合接转站的生产实际,考虑到热采管理区
后续开发面临的实际问题,有针对性地采取了如下工艺改进措施:一是对掺水泵进行了改型的改造。
2008年年底将1#、3#两台dgi46-50×8型掺水泵改型为150ay67×7型掺水泵。
改造后的掺水泵提高原有掺水泵效4.6个百分点,实现了经济运行。
惨水泵改造前后性能对比见以下表2。
二是对掺水加热炉进行了更新改造。
2008年年底和2009年5月先后将原有1#、3#两台掺水加热炉更换为jm-ftx2500-h/5-y型加热炉,并配套更换改进了换热器。
改造后的加热炉炉效平均提高了6.4个百分点,达到了92.5%左右。
掺水加热炉改造前后性能参数对比见以下表3。
三是改进了宁海污水站的污水处理工艺。
首先向矿提出了限制坨一污水站处理后的污水调入宁海污水站,避免聚合物进入掺水污水中的建议,并进行实施。
其次在今年6月份完善了宁海污水站的气浮处理工艺,净化了掺水水质。
4 下一步的改进措施
改进工艺后,满足了稠油生产需求。
为保证更高效的运行,我们又对接转站的运行现状进行了全面细致的调查分析,认为还有进一步优化的措施,主要有以下几个方面。
在管理方面:强化日常的运行监督,加密巡检,确保问题的及时发现和整改。
在运行方面:一是加强日常运行参数的对比分析,及早发现设备自身性能下降的趋势,采取相应的应对措施;二是强化设备的维护
保养,以确保设备优质高效运行。
在工艺方面:一是建议对掺水泵进行叶轮喷涂的新工艺;二是计划在掺水泵的进口安装高频高能污水处理器。
三是有计划的对站内现有部分工艺流程、设备进行改造。
参考文献:
[1]吴静.无油管空心抽油杆力学行为及井口配套技术研究[d].
中国石油大学,2011.
[2]王桂荣,吴静.数字油田前景分析和保障体系探讨[j].中国管理信息化(综合版),2007(03).
[3]石油工业出版社《油气集输工艺技术与技术知识问答600例》.。