辽河油田稠油地面集输技术现状及攻关方向
202辽河油田公司集输系统工作会议

202辽河油田公司集输系统工作会议202*辽河油田公司集输系统工作会议202*辽河油田公司集输系统工作会议12月16日上午,油田公司集输系统工作会议在高升采油厂会议中心三楼召开。
油田公司采油工艺处处长孙守国、副处长刘勇、谢加才、高升采油厂厂长陈保钢,以及18家二级单位集输系统主管领导、集输大队长联合站站长共计120余人参加会议。
会议由采油工艺处副处长刘勇主持。
会上,金马、冷家、高采以多媒体的形式,分别做了“落实对标管理强化基础工作全面提升联合站管理水平”“冷家油田稠油处理工艺技术改造工程”“推行精细化管理促进集输系统工作上水平”的典型发言报告。
油气集输科科长王宝峰宣读了第十次“优质低耗联合站”检查情况通报。
采油工艺处长孙守国、厂长陈保钢、采油工艺副处长谢加才采油工艺副处长刘对勇为获得集输系统管理先进单位、优质低耗联合站、优质低耗注水站等获奖单位颁奖。
谢家才副处长提出了202*年的工作思路和工作重点。
202*年污水处理系统主的工作重点就是“2321”。
就是两个零排放,三个重点工程、2两项重点科研项目、推广一项技术应用。
两个零排放:今天我们采油工艺处组织编制了辽河油田整个的水调基本方案。
同是也把曙光和特油两个采油厂的污水平衡方案也已经做完。
明年我们的重点工作就是污水尽量减少排放三项重点工程:1、锦采、华油的外排工程2、曙光地区污水达标外排工程3、欢采低渗透注水工程。
两项科研重点项目:就是低碳专项股份公司重大科技专项。
第二项就是含油污泥资源化处理。
就后一个就是推广应用,就是污水回收技术应用,我们已经研究两年在欢采用两台锅炉实验我们通过注气量的对比实验。
并且在欢采实验获得成功而且这项技术还通过了集团公司的验收。
今年已经开始推广已经见到了效果。
刘勇副处长首先对今年集输系统工作做了简要回顾对明年工作提出具体工作要求:着重讲一下这次专项检查的情况,做一下讲评这次专项检查有几方面的突出,一个是今年注水站是普察的第二个就是污水罐是现场抽检这是过去没有的。
浅析我国稠油开发的技术现状及发展趋势

1741 稠油资源开发概况稠油属于非常规石油资源,是石油中相对分子质量最大、组成和结构最为复杂的部分,但没有严格的范畴,在不同的研究领域含义不同,其主要特点是高黏度、高密度,一般含有沥青质等成分。
我国稠油主要分布在准格尔盆地、松辽盆地、渤海湾盆地等,它们大部分分布在盆地斜坡上,以地层型油藏为主,如富拉尔基、曙光、单家寺、井楼等。
由于稠油粘度高、密度高,所以在开采过程中阻力大,驱动效率低,体积扫油效率也低,因此,常规的石油开采方法不适用于稠油的开采,应采取一些特殊的工艺技术[1]。
我国自20世纪60年代开始开采稠油以来,稠油开采技术有了突飞猛进的发展,目前的稠油开采技术大致可分为热采和冷采两大类。
稠油热采的开采原理在于稠油黏度虽高,但对温度极为敏感,随着温度的增加,稠油的黏度也会下降,大大降低原油渗流阻力;而稠油的“冷采”是则是在稠油油藏开发过程中,针对油藏的特性,通过其它不升温的方法,如加入适当的化学试剂、微生物采油等技术方法,达到降黏的目的,全文对目前稠油热采技术及冷采技术做了详细的阐述,并对未来稠油开发技术趋势做了简单概述。
2 稠油开采的技术现状2.1 稠油热采技术的现状2.1.1 蒸汽吞吐采油技术蒸汽吞吐采油是一种相对简单而成熟的注蒸汽开采稠油的技术,向采油井中注入一定量的蒸汽,随后关井,让蒸汽与油藏进行热交换,然后再开井采油,一般分为三个步骤:注蒸汽、焖井、开井生产,此过程可循环往复进行,这一采油技术的主要原理是用蒸汽加热近井地带原油,使之黏度降低,是我国稠油开发最常见的开发方式之一。
2.1.2 蒸汽驱采油技术蒸汽驱采油,就是由注入井连续不断地往油层中注入高干度的蒸汽,不断加热油层,降低地层原油黏度,将原油驱赶到生产井的周围,并被采到地面上来的一种普通稠油开发方式。
目前普通稠油油藏蒸汽驱开发大多数采用面积井网(反九点井网),虽然取得了较好的开发效果,但在实际开发过程中,常规面积井网也暴露出许多共性问题:平面驱替不均匀,存在死油带,难以动用;由于蒸汽超覆作用,上部油层吸汽好,下部油层吸汽差,导致油气储量动用程度低;蒸汽调控不灵活,蒸汽驱波及体积受限,导致采收率的提高幅度也受到限制。
辽河油田稠油地面集输技术
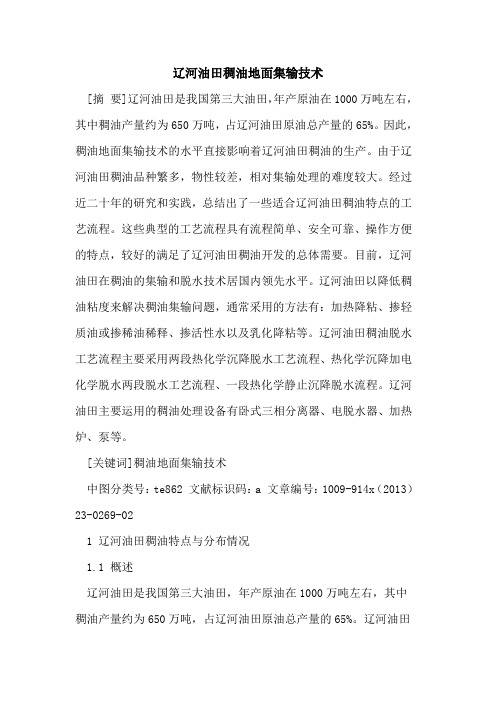
辽河油田稠油地面集输技术[摘要]辽河油田是我国第三大油田,年产原油在1000万吨左右,其中稠油产量约为650万吨,占辽河油田原油总产量的65%。
因此,稠油地面集输技术的水平直接影响着辽河油田稠油的生产。
由于辽河油田稠油品种繁多,物性较差,相对集输处理的难度较大。
经过近二十年的研究和实践,总结出了一些适合辽河油田稠油特点的工艺流程。
这些典型的工艺流程具有流程简单、安全可靠、操作方便的特点,较好的满足了辽河油田稠油开发的总体需要。
目前,辽河油田在稠油的集输和脱水技术居国内领先水平。
辽河油田以降低稠油粘度来解决稠油集输问题,通常采用的方法有:加热降粘、掺轻质油或掺稀油稀释、掺活性水以及乳化降粘等。
辽河油田稠油脱水工艺流程主要采用两段热化学沉降脱水工艺流程、热化学沉降加电化学脱水两段脱水工艺流程、一段热化学静止沉降脱水流程。
辽河油田主要运用的稠油处理设备有卧式三相分离器、电脱水器、加热炉、泵等。
[关键词]稠油地面集输技术中图分类号:te862 文献标识码:a 文章编号:1009-914x(2013)23-0269-021 辽河油田稠油特点与分布情况1.1 概述辽河油田是我国第三大油田,年产原油在1000万吨左右,其中稠油产量约为650万吨,占辽河油田原油总产量的65%。
辽河油田稠油资源主要分布在高升油田、曙光油田、欢喜岭油田、兴隆台油田以及冷家油田等地区。
1.2 稠油分类辽河油田稠油物性差异较大,根据辽河油田目前稠油的生产情况,稠油可分为普通稠油、特稠油和超稠油三类。
1、普通稠油普通稠油粘度大部分在200mpa.s~5000mpa.s之间,这部分稠油约占稠油总产量的70%左右。
2、特稠油特稠油粘度大部分在5000mpa.s~50000mpa.s之间,生产难度较大,这部分稠油约占稠油总产量的15%左右。
3、超稠油超稠油粘度大部分在5×104 mpa.s~20×104mpa.s,这类稠油是近几年才开始规模开采的。
稠油开采技术现状与发展方向采油院.pptx

胜利油田稠油热采产量
探明储量 13.83×108t
已动用 12.63×108t
热采开发3.55×108t 水驱开发9.13×108t
未动用 1.15×108t
特超稠油及薄层稠油油藏
蒸汽吞吐及水驱是稠油油藏的主要开发方式
第2页/共89页
一、前言
胜利油田油藏特点
国内四大主力稠油油田不同深度储量比例对比
Pb/MPa
70 65 60 55 50 45
0
8
6
4
2
界面张力 300
粘弹模量
弹性模量
600
900
时间/(s)
0 粘性模量
-2 1200
模量/(mN/m)
二氧化碳改善热采开发效果机理
✓地层条件下稠油体积膨胀(>15%) ✓降粘作用(>90%) ✓降低油水界面张力
第17页/共89页
表面张力/(mN/m)
波及效率 %
68 80.7 62.6 81.3
驱替效率,%
100.00 80.00 60.00 40.00 20.00 0.00 0.00
2.00
热水驱 热水伴N2驱
4.00 6.00 8.00 10.00
注入体积,PV
热水伴CO2驱 热水伴CO2和薄膜扩展剂驱
二氧化碳同薄膜扩展剂相结 合大幅度提高驱替效率;驱替 效率由30%提高到90%;波及 系数由68%提高到81%,大大 改善热采开发效果。
(1) (2) (3)
普亚超
通 锅 炉
临 界 锅 炉
临 界 锅 炉
(1) (2) (3)
高注全
真 空 隔 热
采 一 体 化 管
密 闭 注 汽 管
国内外稠油开发现状及稠油开发技术发展趋势

Xnag ay fl iC i ad hay rsr i i U id t , ii h v o id n n n t ev o ee os ne S e jn e i e s h a h l e i l v r n t t s a
C n d , V nz e e . h p p r a a a a d eu l t ite e n e a n a . c o e ie p nae r u A p s n, po ut n h o g s sd h ay d v l me t H f& t e tte d ci tcn l i ue fr v ol eo r e h r o e o e d Pr du t 。S GD I su o ut n a d e o ci on A , i C mb si , n t - o n t h P f Se m o dn ,Col u , a f o i t l g e ri tc n l i ae P X T A, ro tl la d w h l St megn eh oo e r V E , I oi n Wel n D noe eam g g s A H H z a , o Ge eao ec T e p lain e h n m n cn i n o al t es n r r . t t h a pct i o m ca i a d o d i s s t o f o h e l f tc n l i h v b e d c se ite p r eh o g s e n u sd h p e. o e a e i s n a T e p r ilfcs te r n d v l m n s ts La h ad na g h p e ma y u o h c r t eo e t u o i e X j n a n o n u e e p t a f o n ii
辽河油田超稠油地面工艺技术的应用与进展
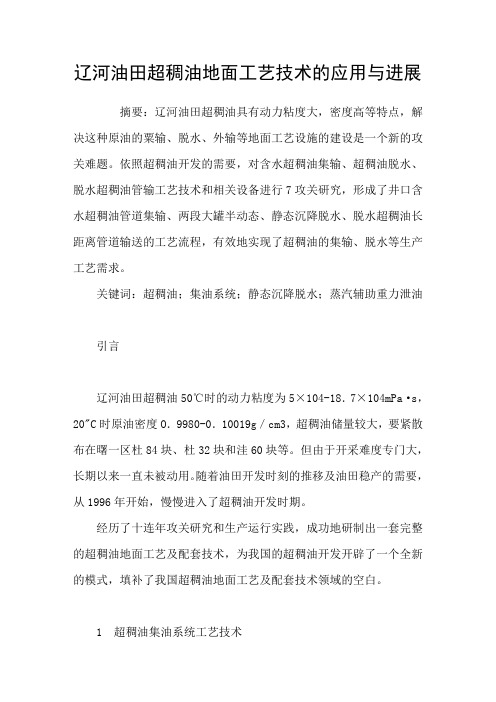
辽河油田超稠油地面工艺技术的应用与进展摘要:辽河油田超稠油具有动力粘度大,密度高等特点,解决这种原油的粟输、脱水、外输等地面工艺设施的建设是一个新的攻关难题。
依照超稠油开发的需要,对含水超稠油集输、超稠油脱水、脱水超稠油管输工艺技术和相关设备进行7攻关研究,形成了井口含水超稠油管道集输、两段大罐半动态、静态沉降脱水、脱水超稠油长距离管道输送的工艺流程,有效地实现了超稠油的集输、脱水等生产工艺需求。
关键词:超稠油;集油系统;静态沉降脱水;蒸汽辅助重力泄油引言辽河油田超稠油50℃时的动力粘度为5×104-18.7×104mPa·s,20"C时原油密度O.9980-0.10019g/cm3,超稠油储量较大,要紧散布在曙一区杜84块、杜32块和洼60块等。
但由于开采难度专门大,长期以来一直未被动用。
随着油田开发时刻的推移及油田稳产的需要,从1996年开始,慢慢进入了超稠油开发时期。
经历了十连年攻关研究和生产运行实践,成功地研制出一套完整的超稠油地面工艺及配套技术,为我国的超稠油开发开辟了一个全新的模式,填补了我国超稠油地面工艺及配套技术领域的空白。
1 超稠油集油系统工艺技术1.1 低含水期集油系统超稠油特点是密度大,粘度高,含胶质、沥青质高,流动性差。
因此,不易输送、脱水。
开采低含水期集油系统采取井口拉油方式,其条件及特点为:产液量小,含水少,管道集输热力、水力条件差,管输温降大、摩阻损失大;适于车运,建设速度快捷。
1.2 高含水期集油系统1.2.1油井平台技术1997年实现了油井平台集油生产工艺,所谓油井平台,是利用丛式井组和水平井组的采油平台。
依照工艺需要,井站集输系统设自压平台、泵平台.中心平台。
自压平台靠井口回压将单井超稠油输送至泵平台或中心平台,泵平台将所辖井和自压平台的超稠油通过提升泵输至中心平台或集输干线。
中心平台所辖井和泵平台的超稠油通过提升泵输至集输干线。
辽河油田典型稠油集输工艺及其优化简化
辽河油田典型稠油集输工艺及其优化简化摘要:辽河油田稠油具有粘度大、密度高、油气比低等特点,在40多年的开发建设过程中,逐渐形成了独具特色的地面集输工艺技术体系,但随着油田开发的深入,开发初期形成的成熟技术与油田生产实际情况不相适应的矛盾日益突出。
本文对辽河油田稠油集输典型流程进行了分析、整理,并提出了如何对现有成熟稠油集输工艺进行优化简化,同时展望了稠油集输工艺技术发展方向。
关键词:稠油粘度集输优化。
1 稠油、超稠油集输工艺1.1 单管加热集输工艺井口来液经加热炉加热后,输往计量站或计量接转站,该工艺集油管线流速通常低于0.5m/s,适用于稠油粘度不大于3000mPa·s(50℃)、单井产液量较高(不小于30t/d)、井口出油温度较高(40℃以上)的稠油集输。
具有流程简单,方便管理,投资少的特点。
1.2 双管掺水集输工艺所谓掺水集输流程即在采油井口加入活性水溶液,达到利用化学药剂降粘、利用水溶液润湿边壁,降阻输送的目的,多用于粘度不大于10000mPa·s的稠油。
回掺水主要利用联合站原油脱出的污水,需建立掺水分输站,掺水比为1.8~2:1(水:油),掺水温度一般在60~65℃。
双管掺水工艺采用集中建站分配水量,减少了掺水泵数量,节约投资和减少耗电量,但掺液量较大,增加集输负荷,油水混合不均,在输送中,当流速较低时,易出现油水分层现象。
1.3 双管掺稀油集输工艺稠油掺稀油是利用两种物性、粘度差别较大,但互溶性好的原油,将其按一定比例互溶在一起,使其具有新的粘度和物性,达到稠油降粘的目的。
稠油掺稀油降粘工艺技术,可以满足任何粘度稠油降粘要求。
应用此工艺需在计量接转站和集中处理站设掺稀油系统,包括稀油的计量、储存、升压、加热、分配等功能。
掺液比为1:0.3~0.7(稠油:稀油),与掺活性水相比,液量减少40%以上,大大减少了集输、脱水、污水处理等工序的负荷,亦相对地减少了设备数量和动力消耗。
从辽河油田高升采油厂看稠油的形成及开采中常见问题1(合集)
从辽河油田高升采油厂看稠油的形成及开采中常见问题1(合集)第一篇:从辽河油田高升采油厂看稠油的形成及开采中常见问题1 从辽河油田高升采油厂看稠油的形成及开采中常见问题作者:孙铭辽河油田公司高升采油厂座落于绕阳河畔的盘山和台安两县交界处。
沈盘公路横穿油区.京沈高速公路、京(秦)沈电气化铁路与厂区擦肩而过。
辖区面积近1000km2,1978年建厂,现有员12551人。
管理着1468口油水井、2座联合站、2座注水站、37座转油站、6座注汽站。
是辽河油田集稀油、稠油和高凝油于一身的多种类油品生产基地。
曾被誉为“出稠油、出经验、出人才”的摇篮。
是中国最早正规开发的稠油油田,自1994年以来已连续15年稳产70×10^4t原油生产规模,创造了辽河油田稠油开发史上稳产时间最长的纪录。
稠油油藏分类稠油油藏的形成主要受地层盆地后期抬升活动细菌生物降解作用,地层水洗和氧化作用,以及烃类轻质分散失等诸因素影响。
而晚期构造运动是主导因素,其他因素是在这一地质背景下的地化过程,按上述因素可将超稠油油藏分为风化削蚀、边缘氧化、次生云移和底水稠度等四种成因。
一、风化削蚀成因超稠油油藏主要分布在后期构造抬升活动强烈发育,盆地具有早期沉陷,后期衰退的特点,早期形成的古油藏抬升而接近地表,或者古油藏盖层封堵条件遭受不同程度破坏,天然气和轻质组分大量溢散,液态烃经受地层水的洗作用成地表风化作用,形成重质油或软沥青。
二、边缘氧化成因超稠油油藏主要分布在盆地和凹陷斜坡边缘,油藏类型以地层型或地层岩性封闭为主,在盆地后期构造运动抬升过程中,盆地边缘急剧上升,边缘斜坡带或为油气大规模运移和聚集的指向,油源主要来自盆地内部重油区,油气沿地层不整合面稳定砂体向上倾方向运移,进入盆地边缘地层水交替带,原油发生严重生物降解程度和物理性质有一个明显的变化规律,下倾部位原油具有原生性,上倾部位原油均发生不同程度生物降解作用,油质变重变稠,甚至在盆地边缘部位形成软沥青,有利于超稠油油藏形成,这类油藏一般规模较大,广泛分布在盆地或凹陷边缘。
辽河稠油火驱开发地面工艺关键技术
0前言
火驱是以空气作为助燃剂,采取电点火或化学点火 等方式,持续燃烧地下原油中的重组分产生热能使重组 分在高温下(600 ~ 700 t)发生裂解,注入的高压空气、 燃烧产生的气体和水蒸气,以及裂解产生的轻质油驱动 原油流向采油井采出,火驱采收率可高达70%。
1辽河油田火驱发展历程
2005年起,辽河油田陆续在杜66块、高3块、锦91 块等区块实施火驱开发m。以辽河油田曙光地区杜66 块火驱为例,2005年首先进行2个井组单层火驱开采现 场试验,2006年增加5个井组进行火驱开采试验,2008 年调整为上层系多层火驱开采现场试验,2010至2012 年外扩20井组,2014年扩大实施火驱,新增114井组,共 进行141井组火驱生产。实际生产表明,对比蒸汽吞吐、 蒸汽驱、热水驱等传统开采方式,杜66块火驱具有较好 增油效果。同时其他火驱区块均实现产量上升,充分证 明火驱开发方式接替的有效性[21。
关键词:火驱;组合增压;系统优化;预脱水;尾气处理;高效溶气浮选 DOI:10. 3969 /j. issn. 1006 -5539. 2019. 04. 005
Key Technology of Fire-Flooding Development of Liaohe Heavy Oil
Lu Hongyuan China Liaoቤተ መጻሕፍቲ ባይዱe Petroleum Engineering Company Ltd, Paxrjin, Liaoning, 124010, China
2火驱地面关键技术
2.1火驱配套注空气技术 2.1.1空气增压技术
往复式压缩机适用于小排量、高压力工况,螺杆机 适用于中低压力、中小排气量工况,为满足现场高压力、 大流量空气注入的需求,创新采用螺杆空压机与往复空 压机组合增压技术,如杜66块火驱注空气站工艺流 程见图1。螺杆压缩机和往复压缩机自动关联启停,结 合杜66块现场运行调试指标,研究最优出口压力配比, 最终确定螺杆压缩机出口压力0. 95 MPa,往复压缩机出 口压力10 MPa,注气量可达到20 x 104 m3 /d,满足空压
稠油目前开采技术与下步技术攻关
稠油目前开采技术与下步技术攻关摘要:稠油在石油资源中所占比例较大,但是常规方法很难开采出来。
本文通过从稠油冷采和稠油热采两个方面介绍稠油开采的当前现状以及发展趋势,提出了一些合理的建议,有助于稠油油藏开发方式上升到一个新的台阶。
关键词:稠油;热采;冷采一、稠油简介稠油是一种高粘度、高密度的原油,成分相当复杂,一般都含有沥青质、胶质成分,是石油烃类能源中的重要组成成份,国外将重油和沥青砂油统称为重质原油。
国内外稠油的分类标准不一致,一般用粘度、密度、重度表示。
稠油分类不仅直接关系到油藏类型划分与评价,也关系到稠油油藏开采方式的选择及其开采潜力。
世界上稠油资源极其丰富,其地质储量远远超过常规原有储量。
而我国稠油资源分布很广,储量丰富,陆上稠油、沥青资源约占石油总资源量的20%以上。
我国陆上稠油油藏多数为中生代陆相沉积,少量为古生代的海相沉积,储层以碎屑岩为主,具有高孔隙度,高渗透率,胶结疏松的特征。
根据稠油油藏的埋藏深度来看,我国绝大多数稠油油藏埋藏深度为10001500m 之间。
稠油粘度高,密度大,开采中流动阻力大,不仅驱动效率低,而且体积扫油效率也低,难于用常规方法进行开采。
稠油的突出特点是含沥青质、胶质较高我国胶质、沥青质含量较高的稠油产量约占原油总产量的70%。
因此,稠油开采具有很大的潜力。
对于稠油油藏,常规方法很难开采,采取一些特殊的工艺措施加强稠油开采很有必要。
二、稠油开采技术稠油开采一般可分为热采和冷采两大类。
稠油粘度虽然高,但对温度极为敏感,每增加10 度,粘度下降约一半。
加热过程中,水、轻质油和稠油粘度的变化表明,增加相同的温度,稠油的粘度比水和轻质油降低的多得多。
热力采油作为目前稠油开发的主要手段,能够有效升高油层温度,降低稠油粘度,使稠油易于流动,从而将稠油采出。
稠油“冷采”是相对“热采”而言的,即在稠油油藏开发中,不是通过升温方式来降低油品的粘度,提高油品的流动性能,而是通过其它不涉及升温的方法,利用油藏特性,采取适当的工艺达到降粘开采的目的。
- 1、下载文档前请自行甄别文档内容的完整性,平台不提供额外的编辑、内容补充、找答案等附加服务。
- 2、"仅部分预览"的文档,不可在线预览部分如存在完整性等问题,可反馈申请退款(可完整预览的文档不适用该条件!)。
- 3、如文档侵犯您的权益,请联系客服反馈,我们会尽快为您处理(人工客服工作时间:9:00-18:30)。
辽河油田稠油地面集输技术现状及攻关方向 齐建华* 张春光 辽宁辽河石油工程有限公司 齐建华等. 辽河油田稠油地面集输技术现状及攻关方向. 石油规划设计,2002,13(6):54~57 摘 要 由于辽河油田稠油品种繁多,物性较差,相对集输处理的难度较大。
辽河油田以降低稠油粘度来解决稠油集输问题,通常采用的方法有:加热降粘、掺轻质油或掺稀油稀释、掺活性水以及乳化降粘等。
稠油脱水工艺流程主要采用两段热化学沉降脱水工艺流程;热化学沉降加电化学脱水两段脱水工艺流程;一段热化学静止沉降脱水流程。
主要运用的稠油处理设备有卧式三相分离器、电脱水器、加热炉、泵等。
主题词 稠油 物理性质 集输 加热 脱水 降粘 工艺流程 设备 稠油分类 辽河油田是我国第三大油田,年产原油约1 400万t,其中稠油产量约为900万t,占辽河油田原油总产量的65%。
辽河油田稠油资源主要分布在高升油田、曙光油田、欢喜岭油田、兴隆台油田以及冷家油田等地区。
辽河油田稠油物性差异较大,根据辽河油田目前稠油的生产情况,稠油可分为普通稠油、特稠油和超稠油3类。
1 普通稠油 普通稠油粘度大部分在200~5 000 mPa・s之间,这部分稠油约占稠油总产量的70%。
2 特稠油 特稠油粘度大部分在5 000~50 000 mPa・s之间,生产难度较大,这部分稠油约占稠油总产量的15%。
3 超稠油 超稠油粘度大部分在5×104~20×104 mPa・s,这类稠油是近几年才开始规模开采的。
这部分稠油约占稠油总产量的15%。
辽河油田超稠油的储量较大,埋深较浅,约在700~800 m之间。
表1 辽河油田稠油的一般性质 项 目 20℃的密度(g/cm3) 粘度50℃(mPa・s) 凝点(℃) 含蜡量(%) 沥青质+胶质(%) 杜32块 1.0019 58191~168700 30 4.07 41.99 冷家油田 0.979 10538~54800 18 9.8 11.2 小洼油田 0.950~1.019 813~6853 3~24 1.5~4 27~40 目前,辽河油田已建成的稠油集中处理站有特油公司杜84块1#集中处理站、特油公司杜32块2#集中处理站、冷一稠油集中处理站、曙光油田曙五联合站、兴隆台油田海一联合站、兴隆台油田洼一联合站、锦州油田锦一联合站等。
* 齐建华,男,1966生,高级工程师,1988年毕业于石油大学(华东)石油储运专业。
现在辽宁辽河石油工程有限公司从事油气储运专业设计。
通信地址:辽宁省盘锦市辽宁辽河石油工程有限公司,124010 稠油地面集输工艺流程 1 单管加热集输流程 该工艺流程只有一条管线,流程比较简单。
该工艺流程主要适用于单井产液量高(一般大于20 t/d),出油温度高(一般在40℃以上),原油粘度一般不超过3 000 mPa・s,油井回压一般控制在1~1.2 MPa的稠油区。
2 掺稀油降粘集输流程 掺稀油降粘集输流程经过多年的生产实践,现已形成稠油掺稀油的双管密闭集输、多级分离、大罐热化学沉降脱水、掺稀油定量分配等较为完备的稠油集输工艺。
该工艺对于低产、高稠、井深,周边有稀油资源的油田非常适用。
掺稀油的部位可选择在井下、井口、站内,主要维持地面集油管线的水力条件,提高脱水质量。
稠油掺稀油流程的平面布局主要有3种:小二级布站(计量站→集中处理站);大二级布站(计量接转站→集中处理站);三级布站(计量站→计量接转站→集中处理站)。
3 平台拉油集中处理集输工艺流程 该工艺流程用于环境条件差,矿区无稀油资源,原油粘度高于几万毫帕秒的特稠油、超稠油的集输。
该工艺流程一般以平台为单元,建高架罐,采用导热油集中伴热。
一个导热油站平均管井约50口,集中布站、管线同架,采用导热油伴热或加热与采用电热带和电加热棒加热比较,提高了热能的利用效率。
4 裂化降粘采、集、输一体化工艺流程 裂化降粘就是在高温下将大分子烃类裂解成小分子烃类,使稠油转化为低粘度的原油。
该流程是单井掺柴油采油和集输,原油在处理站预脱水和高温脱水后再经加热进分馏塔回收和分离出柴油,柴油返输到井口回掺,循环使用。
塔底油经加热进入裂化降粘反应塔,然后经过稳定,降粘外输。
该工艺流程解决了稀释剂的来源,使稠油的开采、集输、处理、降粘各环节紧密配合,节约能源,提高了经济效益。
该工艺适用于稠油资源丰富,且周围无稀油源的稠油区块。
5 超稠油乳化降粘工艺流程 该技术是辽河油田为有效利用超稠油资源,解决国内燃料紧张问题而研究开发的一项技术。
目前,辽河油田已建成曙光金宇乳化油厂、井下乳化油厂、热电厂乳化油厂等多个中小型超稠油乳化装置,初步建成超稠油乳化能力近100×104 t/a。
以曙光油田40×104 t/a乳化油处理站为例来叙述超稠油乳化降粘工艺流程。
首先,汽车拉油卸至卸油槽内,超稠油卸车温度为80~90℃;再经卸油泵升压、换热器升温至95℃左右再进入缓冲罐内;然后由乳化泵升压,予混器混相进入换热器升温至约97℃再进入乳化管内进行乳化。
乳化后的乳化油进入储罐储存,再经装车泵装车外运。
乳化剂的加入量为2%(乳化油与纯油重量比),乳化油含水15%~20%,80℃时粘度为250~600 mPa・s。
此工艺流程目的是通过乳化剂将超稠油乳化制成油包水型乳化油,改善油在燃烧时的雾化效果,增加二次雾化,使燃料充分燃烧,从而改善燃烧效果,提高燃烧效率。
稠油脱水工艺流程 1 两段热化学沉降脱水工艺流程 各小站来油一般含水50%~70%,温度50~60℃,经进站计量后加热至约70℃。
进一段热化学沉降脱水罐脱出游离水,使原油含水达到30%以下。
低含水油溢流至缓冲罐,经脱水泵加压、脱水炉加热后,温度达到80~90℃。
然后进二段热化学沉降罐进行二段沉降脱水,合格油溢流进合格油储罐,经外输泵加压后计量外输。
在油田有伴生天然气的情况下,一段脱水可以采用三相分离器,以提高集输系统的密闭程度。
该流程的关键是沉降时间、脱水温度和化学药剂的选择。
其特点是操作简单、可靠,主要应用于曙光油田、高升油田、海外河油田、欢喜岭油田等集中处理站。
2 热化学沉降加电化学脱水两段脱水工艺流程 各小站来油一般含水50%~70%,温度50~60℃,经进站计量后加热至70℃左右。
进一段热化学沉降脱水罐,脱出游离水,使原油含水达到30%以下。
低含水油溢流至缓冲罐,经脱水泵加压、脱水炉加热后,温度达到80~90℃。
然后进二段电脱水器脱水,合格油进合格油储罐,经外输泵加压后计量外输。
在油田有伴生天然气的情况下,一段脱水可以采用三相分离器,以提高集输系统的密闭程度。
该流程的关键是一段脱水位置和二段电脱水器能否建立起稳定的电场。
其特点是脱水精度高,主要应用于曙光油田、兴隆台油田、小洼油田、锦州油田和冷家坨子里等集中处理站。
3 一段热化学静止沉降脱水流程 此工艺流程用于原油的密度和粘度较大,胶质沥青含量高的原油处理。
该工艺流程的要点在于确定出超稠油热化学沉降的合理工艺参数、脱水温度、沉降时间,采用高效破乳剂和适宜的加药量。
采用多个储罐分别交替静止沉降,浮动出油。
完成沉降脱水的罐转作合格油储罐。
脱水后的净化油含水小于2%,污水含油在1 000 mg/L以下。
该工艺流程在曙一区杜84、杜32块运行良好。
主要稠油处理设备 1 卧式三相分离器 卧式三相分离器的分离过程为高压产出液进分离器之后,先通过减速器降低压力和速度,压力降幅大约为0.07~0.14 MPa。
为了防止液流在进入沉降段后产生波动,加装了防浪板(板上有若干小孔)消泡器,液流从防浪板的小孔进入沉降段,使液流比较稳定。
沉降段的主要分离元件是波纹板聚结器,经聚结器后,原油从溢流板流出,这时原油的含水一般约10%;水则从沉降段的下部排出,水中含油小于350 ppm。
分离出的天然气通过捕雾器从分离器的顶部排出,可100%除掉气体中10 μm的液滴。
产生液的脱水时间大约在30~60 min,控制压力在0.4~0.6 MPa。
因稠油含砂较多,故分离器除具有沉降脱水功能之外,一般都具有水力除砂功能,也是采用在三相分离器的底部,用高压水流冲击沉砂,使之悬浮在水中,同时开启排砂阀将砂排出。
2 稠油电脱水器 辽河油田使用的稠油电脱水器基本是在稀油电脱水的基础上,借鉴国外先进经验技术,自己研制开发的。
该脱水器尺寸为∅3800×16000 mm,设计压力为0.6 MPa,采用直流电极,处理量为80~120 m3/h,进口原油含水小于30%,净化油含水率由2%以上降至1%左右。
排放污水含油率由原来的2.5%降至1.4%,耗电量由0.7 kW・h/t(油)降至0.127 kW・h/t(油)。
辽河油田的稠油电脱水器主要针对稠油的特点在以下几个方面进行了调整。
(1)电极板间距由罐内调节改为罐外调节 在稠油的生产过程中,各不同阶段、不同区块的油品性质差异很大,需要根据具体情况对极板间距进行调节。
这是因为聚结力的大小与极板间距的二次方成正比,对极板间距进行调节可以对聚结力的大小进行调节。
而原有的电脱水器必须停产后在罐内进行调节,很不方便,也影响了生产。
进行改进后即方便了生产,也适应了不同的油品性质。
(2)增加了接地电极板 电脱水器下层板与油水界面形成一个弱电场区。
较高含水量的原油进入电脱水器后,先经过这个区域进行预脱水,它可使较大颗粒的游离水聚结、沉降、分离,以保证高强电场深度脱水的稳定。
但由于油水界面自动控制技术还不十分可靠,因此预脱水能力很低,影响了原油的处理质量。
为了解决这一问题,在底层极板的下方适当增设了接地电极,形成了较稳定的弱电场区,对提高稠油的处理质量有一定的作用。
(3)改进油流分配和集水管结构 原油脱水质量的好坏,与脱水器内液流的稳定程度有直接的关系。
新型稠油电脱水器采用了与罐体直筒段同长双列分配管结构,液流在分配管中均匀的流出,避免个别部位呈喷射状。
集水管也是如此,把原来的单列短管及容易造成砂堵的集水管,改为双列的与油分配管同长的结构,还在集水管上方设置了挡砂板,有效地防止了砂堵,减少了污水含油量。
这种稠油电脱水器经过几年的运行,脱水效果比较理想。
3 加热炉 辽河油田根据辽河油田稠油的特点开发了一种热管炉。
其传热方式及结构特点不同于常规的加热炉,与同负荷的水套炉相比热效率提高10%,达到85%。
另外一个主要优点是盘管的压力损失减少60%~80%,这对稠油集输是非常有利的。
该炉采用了热管技术,在加热方式上采用了两极传热。
首先在主附火筒上装有1型、2型热管共计50支,它们将燃料燃烧的高温烟气和低温烟气的热量,通过热管内部工质的相变换热及火筒壁的传热,将热量传递给壳体内的热媒(软化水),从而使热媒加热到设计温度(120℃)。