最新ISO9001:2015+3C质量手册英文版
ISO 9001-2015 中英文对照

ISO 9001:20151 ScopeThis International Standard specifies requirements for a quality management system when an organization:a)needs to demonstrate its ability toconsistently provide product or servicethat meets customer and applicablestatutory and regulatory requirements,andb)aims to enhance customer satisfactionthrough the effective application of thesystem, including processes forimprovement of the system and theassurance of conformity to customer and applicable statutory and regulatoryrequirements.All requirements of this International Standard are generic and are intended to be applicable to all organizations, regardless of type, size and product and service provided.NOTE 1 In this International Standard, the terms “product” or “service” only apply to products and services intended for, or required by, a customer.NOTE 2 Statutory and regulatory requirements can be expressed as legal requirements. 1範圍本國際標準所訂的品質管理系統要求,當一個組織:a)必須展現其提供一致地符合顧客要求和符合適用法令和法規要求之產品或服務的能力。
ISO9001:2015全套文件英文版(含质量手册及全套程序文件)

Ningbo XXX Material TechnologyCo.,LtdISO9001:2015 Quality ManualRevision [A/0] - [2018/3/1](c) [Copyright Year Of 2018] [Ningbo XXX Material Technology Co.,Ltd]; all rights reserved. This document may contain proprietary information and may only be released to third parties with approval of management. Document is uncontrolled unless otherwise marked; uncontrolled documents are not subject to update notification.Revision [A/0] - [2018/3/1]Page 1 of 19TABLE OF CONTENTS0.0 Revision History and Approval ...................................................................................................................... 3 1.0 Welcome to Ningbo XXX Material Technology Co.,Ltd ................................................................................ 4 2.0 XXX Material: Who We Are ........................................................................................................................... 4 2.1 Determining Our Strategic Direction ......................................................................................................... 4 2.2 Scope of the Management System ........................................................................................................... 4 2.2.1 Scope Statement ............................................................................................................................... 4 2.2.2 Facilities Within the Scope ................................................................................................................ 4 2.2.3 Permissible Exclusions ..................................................................................................................... 5 2.2.4 Scope of the ISO9001:2015 Quality Manual ..................................................................................... 5 3.0 Quality Policy................................................................................................................................................. 5 4.0 Management System Structure and Controls ............................................................................................... 5 4.1 Process Approach .................................................................................................................................... 5 4.1.1 Process Identification ........................................................................................................................ 5 4.1.2 Process Controls & Objectives .......................................................................................................... 6 4.1.3 Outsourced Processes ...................................................................................................................... 7 4.2 Documentation & Records ....................................................................................................................... 7 4.2.1 General .............................................................................................................................................. 7 4.2.2 Control of Documents ....................................................................................................................... 7 4.2.3 Control of Records ............................................................................................................................ 7 4.3 Change Management ................................................................................................................................ 8 4.4 Risks and Opportunities ............................................................................................................................ 8 5.0 Management & Leadership ........................................................................................................................... 8 5.1 Management Leadership and Commitment .............................................................................................. 8 5.2 Customer Focus ........................................................................................................................................ 9 5.3 Quality Policy ............................................................................................................................................. 9 5.4 Organizational Roles Responsibilities & Authorities ................................................................................. 9 5.5 Internal Communication ............................................................................................................................ 9 5.6 Management Review .............................................................................................................................. 10 6.0 Resources ................................................................................................................................................... 10 6.1 Provision of Resources ........................................................................................................................... 10 6.2 Human Resources .................................................................................................................................. 10 6.3 Infrastructure ........................................................................................................................................... 11 6.4 Work Environment ................................................................................................................................... 11 6.5 Organizational Knowledge ...................................................................................................................... 11 7.0 Operation ..................................................................................................................................................... 11 7.1 Operational Planning and Control ........................................................................................................... 12 7.2 Customer-Related Activities .................................................................................................................... 12 7.2.1 Capture of Customer Requirements ............................................................................................... 12 7.2.2 Review of Customer Requirements ................................................................................................ 12 7.2.3 Customer Communication ............................................................................................................... 12 7.3 Design and Development ........................................................................................................................ 13 7.4 Purchasing .............................................................................................................................................. 13 7.5 Provision of [Production of adhesive tape] .............................................................................................. 13 7.5.1 Control of Provision of [Production of adhesive tape] ..................................................................... 13 7.5.2 Identification and Traceability .......................................................................................................... 14 7.5.3 Property Belonging to Third Parties ................................................................................................ 14 7.5.4 Preservation .................................................................................................................................... 14 7.5.5 Post-Delivery Activities .................................................................................................................... 14 7.5.6 Process Change Control ................................................................................................................. 15 7.5.7 Measurement and Release of [Production of adhesive tape] ......................................................... 15 7.5.8 Control of Nonconforming Outputs .. (15)Revision [A/0] - [2018/3/1]Page 2 of 198.0 Improvement ............................................................................................................................................... 15 8.1 General .................................................................................................................................................... 15 8.2 Customer Satisfaction ............................................................................................................................. 15 8.3 Internal Audit ........................................................................................................................................... 16 8.4 Corrective and Preventive Action ............................................................................................................ 16 Appendix A: Overall Process Sequence & Interaction ........................................................................................ 17 Appendix B: ISO 9001:2015 Cross Reference . (18)Revision [A/0] - [2018/3/1] 0.0 Revision History and ApprovalRev. Nature of changes Approval DateA/0 Original release. XXX 2018/3/1Page 3 of 19Revision [A/0] - [2018/3/1] 1.0 Welcome to Ningbo XXX Material Technology Co.,LtdNingbo XXX Material Technology Co., Ltd. Was established in 2000, with the UAE businessmen to build the joint venture company; 2004 Ming Shan founded Nissin special adhesive tape and adhesive tape company; 2008 due to the strategic adjustment of 3 company merger and reorganization, the establishment of Ningbo letter mountains adhesive products Manufacturing Co., Ltd..PVC insulation tape is one of China’s national standard drafting unit, the field of adhesive products governing unit of China, Ningbo, adhesives and related products Industry Association, honorary president of the unit.We produce more than 1000 varieties of products of 11 categories. The annual throughput more than 100,000,000 square of the adhesive and 10,000 ton of the adhesive.Our company located in Ningbo which the city of the east China sea, beside 500 kilometers of shanghai, 20 kilometers from Ningbo list airport and 50 kilograms of the Ningbo seaport. The transport is very convenient (Easy to ship to everywhere on the world).2.0 XXX Material: Who We Are2.1 Determining Our Strategic DirectionXXX Material has reviewed and analyzed key aspects of itself and its stakeholders to determine the strategic direction of the company. This involves:∙Understanding our core products and services, and scope of management system (see 2.2 below).∙Identifying “interested parties” (stakeholders) who receive our [Production of adhesive tape], or who may be impacted by them, or those parties who may otherwise have a significant interest in our company. These parties are identified in the document [Requirements and expectations list of interested parties].∙Understanding internal and external issues that are of concern to XXX Material and its interested parties; also identified in the document [Requirements and expectations list of interested parties]. Many such issues are identified through an analysis of risks facing either XXX Material or the interested parties. Such issues are monitored and updated as appropriate, and discussed as part of management reviews.This information is then used by senior management to determine the company’s strategic direction. This is defined in records of management review, and periodically updated as conditions and situations change.2.2 Scope of the Management System2.2.1 Scope StatementBased on an analysis of the above issues of concern, interests of stakeholders, and in consideration of its products and services, XXX Material has determined the scope of the management system as follows:Production of adhesive tapePage 4 of 19Revision [A/0] - [2018/3/1]Page 5 of 192.2.2 Facilities Within the ScopeThe quality system applies to all processes, activities and employees within the company. The facility is located at: Factory Add :XXX Tel :XXX Fax :XXX XXX XXX2.2.3 Permissible ExclusionsThe following clauses of ISO 9001 were determined to be not applicable to XXX Material.∙ 8.3 Design and development of products and services 2.2.4Scope of the ISO9001:2015 Quality ManualThis manual is prepared for the purpose of defining the company’s interpretations of the ISO 9001:2015 international standard, as well as to demonstrate how the company complies with that standard.This manual does not follow the numbering structure of ISO 9001. Instead, Appendix B presents a cross reference between the sections of this manual and the clauses of ISO 9001:2015.This manual presents “Notes” which are used to define how XXX Material has tailored its management system to suit its purposes. These are intended to clarify implementation approaches and interpretations for concepts which are not otherwise clearly defined in ISO 9001:2015. Notes appear in italics, with gray background.Where subordinate or supporting documentation is reference in this manual, these are indicated by bold italics .∙ Quality PolicyThe Quality Policy of XXX Material is as follows:Quality first, customer satisfaction;Scientific management, continuous improvement. ∙ Management SystemStructure and Controls 4.1Process Approach4.1.1 Process IdentificationXXX Material has adopted a process approach for its management system. By identifying thetop-level processes within the company, and then managing each of these discretely, this reduces the potential for nonconforming [Production of adhesive tape] discovered during final processes or after delivery. Instead, nonconformities and risks are identified in real time, by actions taken within each of the top-level processes.Note: not all activities are considered “processes” – the term “process” in this context indicates the activity has been elevated to a higher level of control and management oversight.The controls indicated herein are applicable only to the top-level processes identified.。
ISO90012015记录控制程序英文版
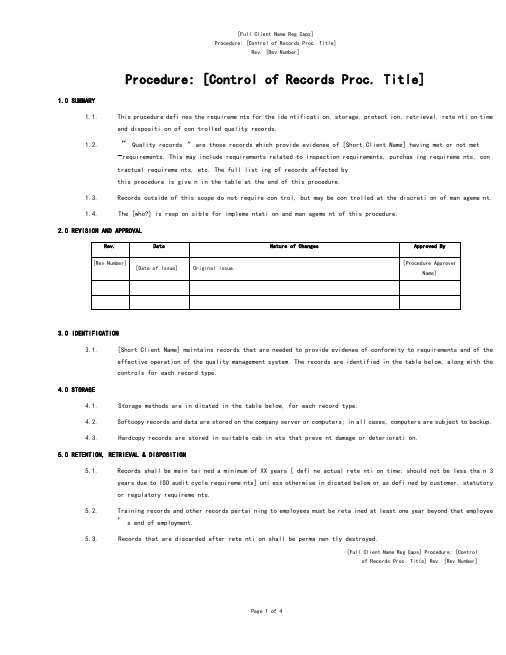
[Full Client Name Reg Caps]Procedure: [Control of Records Proc. Title]Rev. [Rev Number]Procedure: [Control of Records Proc. Title]1.0 SUMMARY1.1.This procedure defi nes the requireme nts for the ide ntificati on, storage, protect ion, retrieval, rete nti on timeand dispositi on of con trolled quality records.1.2.“ Quality records ” are those records which provide evidenee of [Short Client Name] having met or not met-requirements. This may include requirements related to inspection requirements, purchas ing requireme nts, contractual requireme nts, etc. The full list ing of records affected bythis procedure is give n in the table at the end of this procedure.1.3.Records outside of this scope do not require con trol, but may be con trolled at the discreti on of man ageme nt.1.4.The [who?] is resp on sible for impleme ntati on and man ageme nt of this procedure.2.0 REVISION AND APPROVAL3.0 IDENTIFICATION3.1.[Short Client Name] maintains records that are needed to provide evidenee of conformity to requirements and of theeffective operation of the quality management system. The records are identified in the table below, along with thecontrols for each record type.4.0 STORAGE4.1.Storage methods are in dicated in the table below, for each record type.4.2.Softcopy records and data are stored on the company server or computers; in all cases, computers are subject to backup.4.3.Hardcopy records are stored in suitable cab in ets that preve nt damage or deteriorati on.5.0 RETENTION, RETRIEVAL & DISPOSITION5.1.Records shall be main tai ned a minimum of XX years [ defi ne actual rete nti on time; should not be less tha n 3years due to ISO audit cycle requireme nts] uni ess otherwise in dicated below or as defi ned by customer, statutoryor regulatory requireme nts.5.2.Training records and other records pertai ning to employees must be reta ined at least one year beyond that employee' s end of employment.5.3.Records that are discarded after rete nti on shall be perma nen tly destroyed.[Full Client Name Reg Caps] Procedure: [Controlof Records Proc. Title] Rev. [Rev Number]5.4.When archived records are stored offsite or in another location, these shall be stored in a con trolled en vir onmentthat also protects them from damage or deteriorati on.5.5.As required by customer con tract or regulatory requireme nts, quality records shall be made readily available forreview by the requesting authority. Such review is limited to those records applicable to the customer or regulatory authority, and shall not allow for the accidental or inten ti onal release of con fide ntial in formati on to an un authorized party.56 PROTECTION & PRESERVATION5.7.The listed “ con troller sho” n in the table below must en sure their assig ned records rema in legible, readilyidentifiable and retrievable.5.8.In order to en sure protect ion of records, electr onic records are subject to periodic backups, with the backup storedon a separate server. [Add details of backup procedures and methods here; if complex, a separate procedure may be required.]5.9.The [who?] is resp on sible for backup of data.5.10.Quality records data stored on individuals computers must either be backed up through the server (as above), or backedup manu ally onto the server. The in dividual users of such data are responsible when data is not backed up by the server. [Delete if not applicable.]5.11.En tries made by hand on hardcopy forms shall be made in ink.5.12.White-out or correct ion tape is not to be used on any quality records. The correct procedure for maki ng corrections is to cross the error out, make the correct ion and in itial it. Opti on ally, datesen sitive correcti ons should be dated as well.。
ISO 9001 2015 中英文
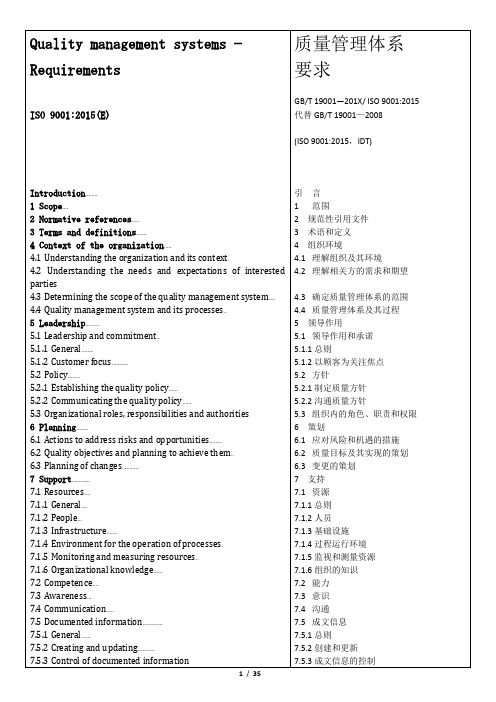
strategic direction of the organization. Management of the processes and the system as a whole can be achieved using the PDCA cycle (see 0.3.2) with an overall focus on risk-based thinking (see 0.3.3) aimed at taking advantage of opportunities and preventing undesirable results.The application of the process approach in a quality management system enables:a) understanding and consistency in meeting requirements; b) the consideration of processes in terms of added value; c) the achievement of effective process performance;d) improvement of processes based on evaluation of data and information.Figure 1 gives a schematic representation of any process and shows the interaction of its elements. The monitoring and measuring check points, which are necessary for control, are specific to each process and will vary depending on the related risks.Figure 1 — Schematic representation of the elements of a single process0.3.2 Plan-Do-Check-Act cycleThe PDCA cycle can be applied to all processes and to the quality management system as a whole. Figure 2 illustrates how Clauses 4 to 10 can be grouped in relation to the PDCA cycle.NOTE Numbers in brackets refer to the clauses in this International 维(见0.3.3)对过程和整个体系进行管理,旨在有效利用机遇并防止发生不良结果。
ISO9001-2015_中英文
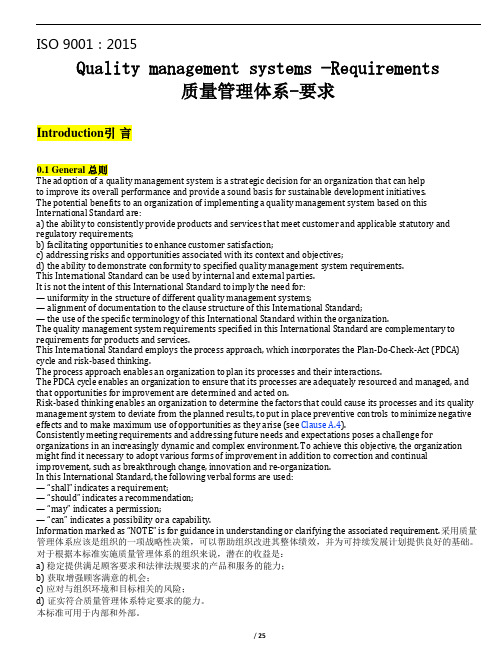
ISO 9001:2015Quality management systems —Requirements质量管理体系-要求Introduction引言0.1 General 总则The adoption of a quality management system is a strategic decision for an organization that can helpto improve its overall performance and provide a sound basis for sustainable development initiatives.The potential benefits to an organization of implementing a quality management system based on this International Standard are:a) the ability to consistently provide products and services that meet customer and applicable statutory and regulatory requirements;b) facilitating opportunities to enhance customer satisfaction;c) addressing risks and opportunities associated with its context and objectives;d) the ability to demonstrate conformity to specified quality management system requirements.This International Standard can be used by internal and external parties.It is not the intent of this International Standard to imply the need for:— uniformity in the structure of different quality management systems;— alignment of documentation to the clause structure of this International Standard;— the use of the specific terminology of this International Standard within the organization.The quality management system requirements specified in this International Standard are complementary to requirements for products and services.This International Standard employs the process approach, which incorporates the Plan-Do-Check-Act (PDCA) cycle and risk-based thinking.The process approach enables an organization to plan its processes and their interactions.The PDCA cycle enables an organization to ensure that its processes are adequately resourced and managed, and that opportunities for improvement are determined and acted on.Risk-based thinking enables an organization to determine the factors that could cause its processes and its quality management system to deviate from the planned results, to put in place preventive controls to minimize negative effects and to make maximum use of opportunities as they arise (see Clause A.4).Consistently meeting requirements and addressing future needs and expectations poses a challenge for organizations in an increasingly dynamic and complex environment. To achieve this objective, the organization might find it necessary to adopt various forms of improvement in addition to correction and continual improvement, such as breakthrough change, innovation and re-organization.In this International Standard, the following verbal forms are used:—“shall” indicates a requirement;—“should” indicates a recommendation;—“may” indicates a permission;—“can” indicates a possibility or a capability.Information marked as “NOTE” is for guidance in understanding or clarifying the associated requirement.采用质量管理体系应该是组织的一项战略性决策,可以帮助组织改进其整体绩效,并为可持续发展计划提供良好的基础。
ISO9001:2015一整套程序文件英文版
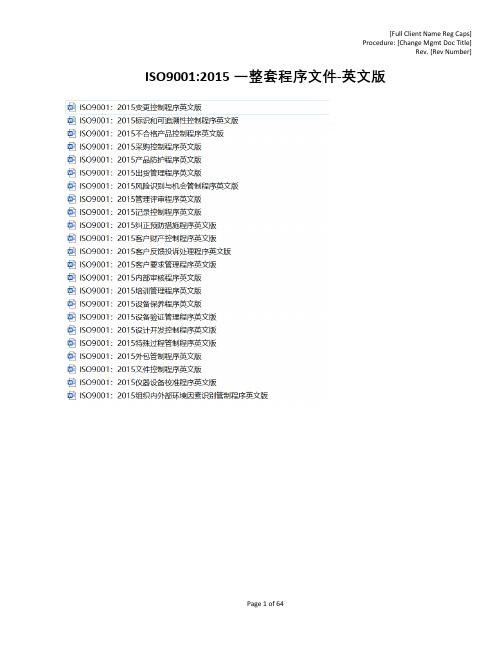
ISO9001:2015一整套程序文件-英文版Procedure: [Change Mgmt Doc Title]1.0SUMMARY1.1.The purpose of this procedure is to define the methods for managing changes to processes andother aspects of the management system in a controlled manner.1.2.Where this document discusses changes to processes, this shall be understood to mean the top-level processes identified in the [Quality Manual Doc Title].1.3.The [who?] is responsible for implementation and management of this procedure.2.0REVISION AND APPROVAL3.0CHANGES TO PROCESSES3.1.Management system processes will undergo changes, typically when:3.1.1.Improvement opportunities have been identified, typically to improve processeffectiveness3.1.2.Nonconformities within a process are identified and require corrective action3.1.3.Conditions in the industry or company change, requiring a process to be updated3.1.4.New processes are added which impact on existing processes, requiring changes3.1.5.Customer requirements result in a need to change processes3.1.6.Any other reason determined by management3.2.In such cases, the process must be changed in a controlled manner to ensure properauthorization and implementation of the changes.3.3.At a minimum, process changes shall include the steps herein:3.3.1.The request for a process change shall be documented, typically in a [CAR Form Name]per the procedure [Corrective Preventive Action Proc. Title]. The justification for thechange shall be recorded.3.3.2.The change shall be reviewed by appropriate management, including the senior mostmanager responsible for the process. Changes must be approved prior toimplementation.3.3.3.The appropriate [Process Definition Doc Title] will be updated to reflect the change.This document will undergo review and approval per the procedure [Control ofDocuments Proc. Title]. The revision indicator of the [Process Definition Doc Title]will be incremented, and the nature of the change recorded. [ Delete last sentenceif you are not using Process Definition documents.]3.3.4.The follow-up verification step of the [CAR Form Name] process shall seek to ensurethe change has had the intended effect, and/or has improved the process. If not, thechange may be rolled back or a new change made to correct any new issues that ariseas a result of the change.4.0CHANGES TO DOCUMENTATION4.1.Management system documents undergo changes when there is a need to revise them.4.2.Changes to documentation are done in accordance with the procedure [Control of DocumentsProc. Title].5.0CHANGES TO ORDERS OR CONTRACTS5.1.Changes to active orders or contracts may occur when the customer changes the requirementsafter the work has begun, or may be initiated by [Short Client Name] when unforeseencircumstances are encountered.5.2.Changes to orders or contracts are done in accordance with the procedure [Quoting and OrdersDoc Title].Procedure: [Identification & Traceability Proc. Title]1. SUMMARY1.1. This procedure defines the methods used to identify and (where applicable) provide uniquetraceability for [Short Client Name] products. This procedure includes methods:1.1.1. To define the methods for identifying products (what they are)1.1.2. To define the methods for identifying products as to their current inspection or teststatus1.1.3. To define the methods for segregating and discriminating between product andtooling when their appearance is similar1.1.4. To define the methods for providing traceability, including unique serialization, orproduct as applicable1.2. The [who?] is responsible for implementation and management of this procedure.2. REVISION AND APPROVAL3. APPLICATION3.1. This procedure applies to all departments which use, handle, transport, store, inspect ormanufacture product, raw materials and tooling, at all [Short Client Name] facilities.3.2. This procedure not only applies to typical product, but also deliverables from services, such asreports, schedules, etc.3.3. Non-critical materials or supplies, which are not incorporated into final product or which serveonly to support facilities or operations, are not subject to this procedure.4. DEFINITIONS4.1. Product4.1.1. “Product” includes any of the following:∙Any part, assembly or item ordered by the customer∙Deliverable reports or documents∙Product may refer to finished product, or work in process (WIP)4.2. Raw Materials4.2.1. “Raw materials” include any of the following:∙Any materials or items (metals, plastics, components, pre-built assemblies, small parts) which become part of the finished product’s physical construction; some ofthese items may sometimes be referred to as “consumables”.∙Coatings, paint, plating, adhesives, chemicals or materials which will be incorporated into (or onto) the final product.4.3. Tooling4.3.1. “Tooling” can include any of the following:∙Devices used by manufacturing for setup or production, including fixtures and jigs.∙Devices used by inspection for determining acceptance of product, including test fixtures.∙Shop aids, which are simple devices (blocks, spacers, shapes) used to assist in production or development, but which are not precision tools and which can be usedfor a variety of applications.4.3.2. Tooling does not include:∙Cutting tools, drill bits, etc.∙Hand tools∙Machining equipment5. PRODUCT5.1. There are many ways to identify product; this procedure presents the most typical, acceptablemethods. Additional product identification methods may be called out in the design orproduction documentation.5.2. Identification typically includes the part number, revision, Work Order # and unique serialnumber (if applicable).5.3. Identification is done through any of the following methods:5.3.1. Part marking, by way of ink marking, etching or some other method.5.3.2. Bag-and-tag methods, especially for small parts.5.3.3. Placement of parts on shelves or in containers that are properly marked, withsignage or other methods.5.3.4. Placement of parts near associated paperwork, for the purpose of identification andtraceability, may be used if the paperwork can clearly be identified as relating to theparts in question, typically by way of the inclusion of a drawing which can becompared to the product.5.3.5. Segregating entire areas of the production floor with belt stanchions and attachedsignage, indicating what type of items are allowed, or disallowed, within theenclosed area.5.4. Where unique serialization is required for traceability, the parts shall be identified with a serialnumber in accordance with customer requirements, or in a manner developed to ensure that no two parts are given the same number. Serial number logs may be used to control this; workorders shall reference the serial numbers under which the unique parts were built.5.5. All product may be assumed to be inspected and/or tested and found to be acceptable for useif identified in accordance with the rules above, unless it is marked as nonconforming product.For the methods of identifying nonconforming product, see procedure [Control of NCP Proc.Title].6. RAW MATERIALS6.1. Raw materials requiring traceability back to heat lot numbers, manufacturer lot or batchnumbers, certificates of conformity or analysis, etc., must be marked in a way that provides this traceability. This is typically done by marking the raw materials with the [Short Client Name]purchase order number under which the items were purchased, and the supplier’s lot number.6.2. When raw materials are used, any remaining material that will be returned to stock and used inthe future must be re-identified before re-entry into inventory.6.3. Raw materials which are determined to require identification and traceability, but which lacksuch identification, may not be used for flight hardware. These may be used for tooling stock or other non-product purposes.6.4. All raw materials may be assumed to be inspected and/or tested and found to be acceptable foruse if identified in accordance with the rules above, unless it is marked as nonconforming. For the methods of identifying nonconforming raw materials, see procedure [Control of NCP Proc.Title].7. PRODUCTION TOOLING7.1. Tooling used for production (fixtures, molds, jigs, setup devices, product supports or stands,etc.) shall be designed and built according to engineering data, and then validated to ensurethe tool performs the intended function without risk or harm to product. Validation of tooling istypically done by using the tooling and inspecting the resulting parts to ensure the toolingresults in parts that meet dimensional or other requirements.7.2. Once validated and approved for use, the tool will be marked with a tooling ID number, which istypically the part number for which the tool is to be used.7.3. Tools that produce production hardware or are used to accept hardware must undergoinspection before release. [QC or QA Preferred Term] must stamp or mark the tool as accepted before it can be used.7.4. Shop aids for setup of production operations, supporting a part temporarily, or other simple ortemporary use, may not require identification with a unique identifier. Instead, these must beidentified as tooling by either marking the item itself as “TOOLING” (or similar language) orplacement in an area, shelf, cabinet or other container that is properly marked as “TOOLING”or “SHOP AIDS”(or similar language). T he marking must allow tooling to clearly bedistinguished from raw material or product (whether flight or development).7.5. Tooling used for lifting shall be proof load tested and include an upper load lift limit, as requiredby regulations.7.6. Tooling found to be nonconforming shall be tagged to prevent use until fixed, repaired ordeemed acceptable. Segregation of nonfonconforming tooling from the production area shouldbe performed when possible.7.7. When approved tooling undergoes modification, the identification must be updated to reflect thechange; this is typically done by editing or re-marking the item with the latest revision of theengineering part number.8. SERVICE DELIVERABLES (← delete if not applicable)8.1. Service deliverables, such as reports and schedules, shall be identified with a title and, ifapplicable, reference to the project or contract under which they are developed.8.2. Customer contracts may indicate additional methods for identification of service deliverables.8.3. In all cases, the deliverable will be identified in a way that makes it clearly understood forwhich contract or project the deliverable is subject to.8.4. As required, service deliverables may be subject to date and revision control, to distinguishearlier versions or submittals.9. STAMP CONTROL (← delete this section if QC stamps are not used)9.1. Quality stamps or employee initials are used to indicate product acceptance or for other quality-related notations. Individual authorities for signing off for inspection, testing and operations aredefined on the Stamp & Signature Control Log; this log is maintained to identify the owner of each stamp.9.2. The [who?] shall maintain the Stamp and Signature Control Log.9.3. Stamps are numbered, and taken out of service for six months after an employee leaves thecompany; after the six-month period, the stamp may be reissued to a different employee.9.4. No employee may use any stamp except that which was issued to them.。
ISO9001-2015-标准中英文
ISO 9001:2015Quality management systems —Requirements质量管理体系-要求Introduction引言0.1 General 总则The adoption of a quality management system is a strategic decision for an organization that can helpto improve its overall performance and provide a sound basis for sustainable development initiatives.The potential benefits to an organization of implementing a quality management system based on this International Standard are:a) the ability to consistently provide products and services that meet customer and applicable statutory and regulatory requirements;b) facilitating opportunities to enhance customer satisfaction;c) addressing risks and opportunities associated with its context and objectives;d) the ability to demonstrate conformity to specified quality management system requirements。
This International Standard can be used by internal and external parties。
ISO 9001 2015 中英文
strategic direction of the organization. Management of the processes and the system as a whole can be achieved using the PDCA cycle (see 0.3.2) with an overall focus on risk-based thinking (see 0.3.3) aimed at taking advantage of opportunities and preventing undesirable results.The application of the process approach in a quality management system enables:a) understanding and consistency in meeting requirements; b) the consideration of processes in terms of added value; c) the achievement of effective process performance;d) improvement of processes based on evaluation of data and information.Figure 1 gives a schematic representation of any process and shows the interaction of its elements. The monitoring and measuring check points, which are necessary for control, are specific to each process and will vary depending on the related risks.Figure 1 — Schematic representation of the elements of a single process0.3.2 Plan-Do-Check-Act cycleThe PDCA cycle can be applied to all processes and to the quality management system as a whole. Figure 2 illustrates how Clauses 4 to 10 can be grouped in relation to the PDCA cycle.NOTE Numbers in brackets refer to the clauses in this International 维(见0.3.3)对过程和整个体系进行管理,旨在有效利用机遇并防止发生不良结果。
ISO9001:2015质量手册英文版(按标准条款)
ISO 9001:2015Quality ManualA quality manual is a document that states the company’s intentions for operating the processes within the quality management system. It can include policies for all areas of the business that affect your ability to make high-quality products and meet your customers’ and ISO’s requirements. These policies define how your department managers will implement procedures within the boundaries specified in the quality manual. The use of Quality Manual are as follows:1.To communicate management’s expectations to employees2.To demonstrate the company’s plan to conform to therequirements of ISO 9001:20153.To demonstrate the fulfilment of Clause 5.3, thatorganizational roles, responsibilities and authorities are assigned, communicated and understood4.To provide a starting point for auditors:1.Internal2.Customer3.ISO Certification BodyTo develop a quality manual, you might consider these steps: 1.List policies to be written (note any ISO requirements thatdo not apply).2.Draft policies based on applicable ISO requirements.3.List operating procedures or refer to them as appropriate.4.Determine the format and structure of the manual andmake the first draft.5.Circulate the draft manual for input from all departmentsand address inadequacies identified.6.Attain a formal approval and release.The contents of your quality manual are completely up to you. But, remember that everything you say you do, you must show evidence that you really do it! So be careful what you include and make sure the policies reflect actual practices. Here are some common topics included in quality manuals.the scope of QMSQuality policyExplanation of the company’s documentation structureOrganizational chartPolicy statements for each applicable ISO requirementReference to operating procedures1) The scope of the Quality Management System. This is in place to identify the limit of the system and is based on the scope agreed with the registrar to be placed on the ISO9001 certificate. This is the explanation of what your company does, be it “Design and Manufacture of the bevel Gear,” “Machining Services for Customers in the oil and service Industry,” or “Providing Fast Food for People in Kuwait city.” The second part of the scope requirement is to identify any exclusions from the standard. In many cases, the Quality Manual will identify none, but the most common exclusion is the requirement of the ISO 9001 standard for “Design & Development” for companies such as a machining shop, which works exclusively from customer drawings and does not design any products itself.2) The documented procedures established for the Quality Management System (or references): ‘Documentation’ means anything written down or captured in some form such as written procedures, policies, checklists, forms, or graphics, drawings, flowcharts, diagrams, IT systems. This is called ‘documentedinformation’ in the current version (2015) of ISO 9001. Confusingly, they have also decided to use the same term for what was formerly called ‘records’ – those things that showed what had been done, such as registers, logs, competed for forms, reports, meeting minutes and so on. ‘Documented information’ in 9001 terms means both the ‘written stuff’ that describe your quality system and say how it should operate (eg, flowcharts, procedures, policies, checklists) and the ‘written stuff’ that shows what was done. A system must be documented to achieve ISO 9001 certification because having certain documented information is required by the Standard. All the documents t needs to control how things are done, whether procedures, flowcharts, checklists, forms, IT systems or any other media or format that work in your business. But note that no mandatory procedures are prescribed. Nor a quality manual. What can confuse people is that actually, you can choose what your documents look like, what format and structure you use, and what to put in them. Provided you meet these requirements. You can use one or many formats, from checklists and flowcharts to intranets, wikis or workflow embedded into IT systems. You can use any media, hardcopy or soft, including intranet, online, internet or wiki. One often used way to do that was with a thingcalled a ‘quality manual’. And you can still do that if you choose. And it can be in hard copy (paper) or softcopy: online documents like web pages, help files or IT systems. And you can write your document in various ways, from easy and user-friendly to bureaucratic, verbose and very hard to follow. And such a manual may be the only document you have for your system, or it may be one of a number of documents. Or something in between.3) A description of the interaction of processes. This is most simply done with a flowchart that identifies all the processes in the organization with arrows showing how they connect. While an in-depth flowchart may help you to better understand the interactions between processes in your organization, a simple top-level flowchart is all that is needed for most people to understand the basics. Example of Quality Manual1.0 Company ProfileInclude your company profile1.1 The mission of the FirmOur mission is to enhance mobility through innovation, leadership and public service. Innovation by providing unparalleled value combined with flexibility and risk-taking ability, leadership by delivering exceptional performance in every domain and corporate responsibility through service to society.1.2 The vision of the FirmTo strive relentlessly with an aim to achieve excellence in all businesses that we venture into, with the objective of becoming an organization that all its employees and associates are proud of.2.0 Organization ScopeDesign, Development of Land, Construction Sales of Residential and Commercial Complexes2.1 Exclusions:NIL2.1 Quality PolicyXXX is committed to delivering quality construction work with promised amenities, in time possession, which meets and exceeds the needs & expectation of our customers. We promise our valued customer’s commitment to excellence in each activity by each employee in the organization by adopting innovative and best in class engineering and management practices with continual improvement in business and quality management system as a part of our efforts for enhancement in customer satisfaction while assuring 100% quality and quantity.2.2 Key ObjectivesTimely completion of projectsIncrease Customer satisfactionReduce Customer Complaint3.0 Glossary & Abbreviations4.0 Context of Organization4.1 Understanding the organization and its context: Shah Promoters and Developers determine external and internal issues that are relevant to its purpose and its strategic direction and that affect its ability to achieve the intended result(s) of its quality management system through PEST and SWOT. The external and internal issues identified throughPEST and SWOT are continuously being monitored and reviewed by CEO.PESTSWOT4.2- Understanding the needs and expectations of interested partiesxxx has determined the interested parties who are relevant to the xxx Quality management system and the requirement of the interested parties in order to prevent the potential effect on the organization’s ability to consistently provide products and services which meet the customer and applicable statutory and regulatory requirements.4.3 Determining the scope of the quality management systemThe organization had determined the scope of the Quality management system by considering external and internal issues, the requirement of relevant interested parties and Product & Service of the organization.The scope of Quality Management System isDesign, Development of Land, Construction Sales of Residential and Commercial ComplexesExclusions:NIL4.4 Quality management system and its processes4.4.1: xxx has determined the processes needed for the quality management system and their application throughout the organization in Process map & Interactions of processes.xxx has determined the inputs required and the outputs expected from each process in individual process map addressed in the documented information of each process.xxx has determined the sequence and interaction of the processes in Process map & Interactions of processes.xxx has determined and applied the criteria and methods (including monitoring, measurements and related performance indicators) needed to ensure the effective operation and control of these processes in the documented information of each process.xxx has determined the resources needed for these processes and ensure their availability in the documented information of Support process.xxx has assigned the responsibilities and authorities for each processxxx has addressed the risks and opportunitiesxxx has been evaluating these processes and implementing any changes needed to ensure that these processes achieve their intended results and improve the processes and the quality management systemImprove the processes and the quality management system4.4.2- xxx is also maintaining documented information to support the operation of its processes and retaining documented information to have confidence that the processes are being carried out as planned.5.0 Leadership5.1 Leadership and commitmentXxx Management has demonstrated leadership and commitment with respect to the quality management system through1.Taking accountability for the effectiveness of the qualitymanagement system by periodical review of qualitymanagement system through management review meeting, Quality objectives review and providing necessary resources.2.Management has established the quality policy andquality objectives for the quality management system and is compatible with the context and strategic direction of the organization.3.Management has determined the organizationalprocesses and integrated with the quality management system requirement through process map & Interaction this can be demonstrated.4.The established procedure for promoting the use of theprocess approach and risk-based thinking.5.Ensuring that the resources needed for the qualitymanagement system are available, this is being periodically reviewed through management review meeting.municating the importance of effective qualitymanagement and of conforming to the quality management system requirements7.Ensuring that the quality management system achievesits intended results8.Engaging, directing and supporting persons to contributeto the effectiveness of the quality management system by providing training, conducting awareness programs and 9.Promoting improvement by introducing the suggestionscheme, Kaizens and conducting meetings.10.Supporting other relevant management roles todemonstrate their leadership as it applies to their areas of responsibility.5.1.2 Customer focusXxx management has demonstrated leadership and commitment with respect to customer focus by ensuring that: 1.Customer and applicable statutory and regulatoryrequirements are determined, understood and consistently met.2.The risks and opportunities that can affect conformity ofproducts and services and the ability to enhance customer satisfaction are determined and addressedc) The focus on enhancing customer satisfaction is maintained and procedure for customer satisfaction is addressed5.2 QUALITY POLICYXXX is committed to delivering quality construction work with promised amenities, in time possession, which meets and exceeds the needs & expectation of our customers. We promise our valued customer’s commitment to excellence in each activity by each employee in the organization by adopting innovative and best in class engineering and management practices with continual improvement in business and quality management system as a part of our efforts for enhancement in customer satisfaction while assuring 100% quality and quantity. We are also committed to serving society as a whole by generating through clean development mechanism (CDM) project.5.2.1 Establishing the quality policyXxx management has established, implemented and maintained a quality policy that:1.is appropriate to the purpose and context of theorganization and supports its strategic direction.2.Provides a framework for setting quality objectives3.Includes a commitment to satisfy applicable requirements4.Includes a commitment to continual improvement of thequality management system5.2.2 Communicating the quality policyThe quality policy is1. Available and be maintained as documented informationmunicated, understood and applied within theorganization through display, Training and periodical review.3.Available to relevant interested parties, as appropriate. 5.3 Organizational roles, responsibilities and authoritiesXxx management has ensured that the responsibilities and authorities for relevant roles are assigned communicated and understood within the organization. While assigning roles, responsibility and authority, top management has considered and ensured that1.The quality management system conforms to therequirements of this International Standard2.The processes are delivering their intended outputs3.Reporting on the performance of the quality managementsystem and on opportunities for improvement, in particular, to top management4.The promotion of customer focus throughout theorganization5.The integrity of the quality management system ismaintained when changes to the quality management system are planned and implemented.Roles, responsibility and authorities assigned are available in process & as per Organization chart wiseDirectorsResponsibilityOverall Responsibility for formulating and communicating Quality Policy & Quality objectives.Formulation of Strategy for continuous up gradation of Business and Quality System.Ensure periodic assessment of the performance of Quality System.Approval of Quality System Manual.Budget Approval for the organization.Overall Responsibility for Business Development & all financial issues.Provision of resources as required.Strategic decisions on developments and technical setups. To provide the leadership for efficient implementations of the system.Authorities:Approval of customers orders, P.O. and Cheque.Sanctioning leaves of all Staff.Approval of funds for Training needs.All the authorities of downline personnel.Chairing Management review meetings.Project PlanningResponsibilities:Overall coordination between client, project managers and office department.Follow up for Schedules.The entire responsibility of Quality.Monitoring Client Satisfaction.Coordination with the consultants.Disciplinary actions against the staff.Prime responsibility for the safety at the siteProvision of a suitable working environmentEnsure the quality system is established, implemented and maintained.Authorities:Appointment of the staff, engineers and tech staff.Sanctioning the Leaves to Staff.All the authorities of downline personnel.Project ManagersResponsibilities:Responsibilities for the entire Project work, i.e. Quality, Quantity and Time.Coordination with consultants and contractors.Coordination with Consultants for drawings.Coordination with the Site engineers.Coordination with the client for the ongoing changes in drawings and projects.Monitoring site engineers work on a daily basis.Reporting to the GM Projects on the above issuesResponsibilities for safety at the site. (Good working environment).Authorities:Make or force a required decision at all levels to achieve project objectives.Initiate actions on the Contractors and consultants for Quality, Quantity and Timeframe issues related to project work.To stop and initiate corrective actions on non–confirming products/services.Site SupervisorResponsibilities:Coordinating with all staff for the Quality related issues of Construction.Daily Labour Handling for Civil Work.Monitoring of Work progress and daily reporting.Preparation of work progress report / Quality Documentation.Control of non – conformities on siteSafety at site / Construction work.Coordination with the Site Contractor for the daily work requirements.Coordination with external agencies for calibration of instruments and material testing.Authorities:Initiate actions on the staff for non-fulfillments of the documentation related qualityTo stop and initiate corrective actions on non–conforming products.Site engineerResponsibilities:Monitoring of site and labour contractors.Monitoring of work progress and daily reportingPreparation of work progress report.Control of non – conformities on site.Ensuring instruments are properly used and are with the status of calibration.Track Project progress & produce regular weekly status reports.Coordinate with all labour contractors to achieve continuous progress at the site as per schedule.Follow up with the Project manager for pending decisions/drawings/building specifications.Communicate management decisions and information to Site subordinate staff.Ensuring the worker’s safety at site and usage of safety equipment.Implementation and follow up and regular monitoring of implemented ISO 9001 system at the site.Coordination with the Quality Person for Quality related issues.Coordinating Material Accountability at siteAuthorities:Initiating the corrective and preventive actions as needed on contractors and consultants.Decision making on during any emergencies at the site.In-charge Marketing:Managing & motivating the sales force towards the achievement of target.Preparation of Sales plan.Annual sales forecast.Monthly sales forecast.Implementation of sales plan.Authorities:Approval of documents as per the Master list of Quality System Document.Authorized to decide corrective & preventive action.Authorized to obtain concessional acceptance for non – conforming product from the customer.InCharge – ADMIN + ACCOUNTResponsibilities:Responsible for tendering activity.Customer order review.Handling and coordinating customersIdentification of resources, as applicable.Document & Data control system pertaining to his department.Maintain all documents related to the quality system.Coordinator for Management reviews.Promoting awareness of customer requirements throughout the Organization.Compliance & effectiveness of the training system.Suitable working environment (cleanliness, ventilation, lighting, safety etc.).Record maintaining for Sales Register, Rent Register, Sale Files, Stationery and Office equipment.Archiving and record keeping of old files.Payroll Monthly: Salary –To release monthly salary of the employees as per policy finalized.Leave – To keep the record of leave as per policy finalized.Annual Allowance – To release annual allowances as per policy finalized.Employee Record – To update employee details as per organization Policy and QMS.To prepare an appointment letter, confirmation letter, experience letter & all employee-related matter as per policy finalized with the help of the Managing Director.Authorities:Approval of customer orders.Approval of documents as per the master list of Quality System Document.Authorized to decide corrective & preventive action.In charge Purchase:Responsibilities:Overall in charge of purchase activities.Identification of resources, as applicable.Purchasing system – Evaluation, selection, purchasing, monitoring.Document & Data control system pertaining to his department.Corrective / Preventive action system (subcontractor non-conformances, in particular.)Control of recordsAuthorities:Authorized to review & approve purchasing documents.Authorized to select & discontinue sub-contractor6.0 Planning6.1 Actions to address risks and opportunities6.1.1Xxx is addressed the issues, requirements the risks and opportunities1.give assurance that the quality management system canachieve its intended result(s)2.Enhance desirable effects3.Prevent, or reduce undesired effects4.achieve improvement6.1.21.actions to address these risks and opportunities2.How to1.integrate and implement the actions into its qualitymanagement system processes2.Evaluate the effectiveness of these actions6.2.2 Quality objectives and planning to achieve them 6.2.1Xxx establish quality objectives at relevant functions, levels and processes needed for the quality management system.The quality objectives shall1.Be consistent with the quality policy2.Be measurable3.Take into account applicable requirements4.Be relevant to the conformity of products and services andto the enhancement of customer satisfaction5.Be monitored6.Be Communicated7.Be updated as appropriate6.2.2 Xxx achieve its quality objectives,1.What will be done?2.What resources will be required?3.Who will be responsible?4.When it will be completed5.How the results will be evaluatedOur Quality Objectives are as below:Timely completion of projectsEnergy Generation Per YearIncrease Customer satisfactionReduce Customer Complaint6.3 Planning of changesXxx determines the need for changes to the quality management system, the changes are carried out in a planned manner1.the purpose of the changes and their potentialconsequences2.the integrity of the quality management system3.the availability of resources4.the allocation or reallocation of responsibilities andauthoritiesXxx has determined the processes needed for the quality management system and their application throughout the organization in Process map & Interactions of processes7 Support7.1 Resources7.1.1 GeneralXxx is determined and provide the resources needed for the establishment, implementation, maintenance and continual improvement of the quality management system. Xxx is consider1.the capabilities of, and constraints on, existing internalresources2.what needs to be obtained from external providersHR determine and provide the resources needed to implement and maintain the quality management system and continually improve its effectiveness and to enhance customer satisfaction by meeting customer requirement. The resources will be in the form ofHuman resources including qualified personnel for verification activities.Manufacturing machines, Test Equipment’s &infrastructure.Provide raw material & other inputs for the realization of the product.Providing funds.The Required resources are identified in the event of new Process Development / Business plan review, Mfg Process Flow, also based on the Organization performance review in MRM and monthly business reviews.7.1.2 PeopleXxx determine and provide the persons necessary for the effective implementation of its quality management system and for the operation and control of its processes. HR along with respective process IN CHARGE ensures that personnel performing work affecting product quality is competent and training to give on the basic operation and control of its processes.7.1.3 InfrastructureXxx is determined, provide and maintain the infrastructure necessary for the operation of its processes and to achieve conformity of products and services. Infrastructure can include1.buildings and associated utilities2.equipment, including hardware and software3.transportation resourcesrmation and communication technologyAt Xxx management determine, provide and maintain the infrastructure needed to achieve conformity to product requirements & in identifying the required resources the PARTNER play a key role based on their day to day interactions with respective IN CHARGE’s and employees 7.1.4 Environment for the operation of processesXxx is determined, provide and maintain the environment necessary for the operation of its processes and to achieve conformity of products and services. A suitable environment can be a combination of human and physical factors1.Social (e.g. non-discriminatory, calm,non-confrontational)2.Psychological (e.g. stress-reducing, burnout prevention,emotionally protective)3.Physical (e.g. temperature, heat, humidity, light, airflow,hygiene, noise).Project in coordination with respective IN CHARGE determines and manages the work environment needed to achieve conformity to product requirement and reviewed ongoing basis.7.1.5 Monitoring and measuring resources7.1.5.1 GeneralXxx is determined and provide the resources needed to ensure valid and reliable results when monitoring or measuring is used to verify the conformity of products and services to requirements. The organization shall ensure that the resources provided1.are suitable for the specific type of monitoring andmeasurement activities being undertaken2.are maintained to ensure their continuing fitness for theirpurposeXxx is retained appropriate documented information as evidence of fitness for purpose of the monitoring and measurement resources7.1.5.2 Measurement traceabilityXxx is measurement traceability is maintained requirement if applicable for the instruments or is considered by them to be an essential part of providing confidence in the validity of measurement results,1.calibrated or verified, or both, at specified intervals, orprior to use, against measurement standards traceable to international or national measurement standards; when no such standards exist, the basis used for calibration or verification shall be retained as documented information2.identified in order to determine their status3.safeguarded from adjustments, damage or deteriorationthat would invalidate the calibration status and subsequent measurement resultsXxx is determined the validity of previous measurement results has been adversely affected when measuring equipment is found to be unfit for its intended purpose, and shall take appropriate action as necessary.Control of Monitoring & Measuring Equipments. Measurement & Monitoring system is well equipped and the system has complete control over the monitoring andMeasuring Equipment. The measurement methods used are evaluated to ensure that they are appropriate and reliable. To ensure that the measuring equipment operates effectively and give reliable results, we have taken the following steps:Equipments are maintained properly and are calibrated & adjusted as and when needed. Necessary safeguards are in place to take care of adjustments that could lead to invalid results.Calibrations are carried out as per national standards (by NABL accredited laboratories only). Where no such standard exists, the basis used for calibration or verification is recorded. The calibration records include the last date of calibration, calibrating agency (for the external agency), calibration result, and frequency of calibration as per the process and/or instrument requirement and the next calibration date. The required accuracy is identified and compared to the measurement that meets expectations. Identification of appropriate equipment is accomplished by tagging, labelling, numbering or by including it in a calibration/maintenance database.。
ISO-9001-2015-中英文
strategicdirection of the organization. Management of theprocesses and the system as a whole can be achieved using thePDCA cycle (see 0.3.2) with an overall focus on risk-basedthinking (see 0.3.3) aimed at taking advantage of opportunitiesand preventing undesirable results.The application of the process approach in a quality managementsystem enables:a) understanding and consistency in meeting requirements;b) the consideration of processes in terms of added value;c) the achievement of effective process performance;d) improvement of processes based on evaluation of data andinformation.Figure 1 gives a schematic representation of any process andshows the interaction of its elements. The monitoring andmeasuring check points, which are necessary for control, arespecific to each process and will vary depending on the relatedrisks.Figure 1 — Schematic representation of the elements of asingle process0.3.2 Plan-Do-Check-Act cycleThe PDCA cycle can be applied to all processes and to the qualitymanagement system as a whole. Figure 2 illustrates how Clauses4 to 10 can be grouped in relation to the PDCA cycle.NOTE Numbers in brackets refer to the clauses in this International维(见0.3.3)对过程和整个体系进行管理,旨在有效利用机遇并防止发生不良结果。
- 1、下载文档前请自行甄别文档内容的完整性,平台不提供额外的编辑、内容补充、找答案等附加服务。
- 2、"仅部分预览"的文档,不可在线预览部分如存在完整性等问题,可反馈申请退款(可完整预览的文档不适用该条件!)。
- 3、如文档侵犯您的权益,请联系客服反馈,我们会尽快为您处理(人工客服工作时间:9:00-18:30)。
Command of issuanceThe quality manual is prepared in accordance with the requirements of ISO9001:2015 quality management system requirements and the implementation rules of compulsory product certification factory quality assurance capability requirements (No.: CNCA-00C-005) and the actual situation of the company. It is hereby released and implemented upon approval."Quality manual" is the regulations that the company's quality activities and quality management system operation should follow. It is used in the internal quality management of enterprises, and is the confirmation file of the quality assurance ability of the factory, and also the commitment to ensure the product quality of customers. The quality system described in this manual and the relevant documents quoted in the manual are binding on all departments and all employees of the plant.The quality manual shall be implemented from the date of release, requiring all employees to follow all provisions of the quality system. The original ISO9001:2008 quality manual shall be repealed at the same time.General manager:Date:Revision notes1.Reasons for amendmentIso9001:2015 standard has been officially issued and implemented. In order to further standardize the quality management level of the company, combine the implementation of the new standard and improve the work efficiency of the company, the original quality manual of the company is hereby revised.2.Purpose and significance of revisionThe revised version of the quality manual meets the requirements of the new version of the standard, further standardizes the company's quality management system file framework, and streamlines the company's quality management workflow, which can improve the company's operation efficiency and standardize the company's quality management.3.Reference files:GB/T19001-2016 IDT ISO9001:2015 quality management system requirementsRules for the implementation of compulsory product certification factory quality assurance capability requirements (No.:CNCA-00C-005)Catalogue1 Company profile (05)2 Scope of quality management system (07)3 Risks and opportunities of quality management system (08)4 Quality policy and objectives (10)5 Organization chart (11)6 Responsibilities and authorities (12)7 Quality management system mode (25)8 Quality management system document structure (26)9 Appendix (26)Appendix I: Quality objective planAppendix 2: Process diagramAppendix 3: Process matrixAppendix 4: Product process flow chartAppendix 5: Table of correspondence between quality management system and standard termsAppendix 6: List of laws and regulations applicable to productsXXXXX Appliance LimitedChapter 1: Company profilepany profileXXXXX Appliance Limited was established in XXXXX. It is mainly engaged in the design, production and service of small household appliances.Since its establishment, the company has been committed to the establishment of an advanced quality management system. In order to ensure that the requirements and wishes of customers are determined and met, under the leadership of the company's senior management and the active participation of all staff, the company has established and established a quality management system in accordance with the requirements of ISO9001:2015 quality management system requirements and the implementation rules for compulsory product certification factory quality assurance capability requirements (No.: CNCA-00C-005) Maintain the quality assurance system based on process method, identify and manage the interrelated processes, so as to improve the effectiveness and efficiency of the quality system.Through the establishment of quality policy and quality objectives, the company makes a commitment to improvement and determines the direction of improvement; through the establishment of data analysis and internal audit process, it explores opportunities for improvement; through corrective and preventive measures, it improves the system of nonconformities and potential nonconformities; through regular management review, it determines the company's new improvement objectives and requirements, so as to establish a continuous improvement system.This manual describes the above system processes and their interrelations of the company, and issues work instructions and requirements to all levels of personnel within the company to provide customers and third-party certification bodies with evidence that the system meets the requirementsAddress: XXXXXTel: XXXX-XXXXXXXXXXXXX Appliance LimitedChapter 2: Scope of quality management system1.This manual specifies the requirements of the quality management system of Dongguan Damei Appliance Limited, which is used to prove the company's ability to meet the requirements of customers and applicable laws and regulations, as well as the evaluation of such ability by relevant parties.2.The main purpose of the provisions and requirements of this manual is to improve the quality management level, product and service quality and customer satisfaction through the effective implementation and continuous improvement of the quality management system.3.The quality management system established by the company in accordance withISO9001:2015 quality management system requirements and the implementation rules of compulsory product certification factory quality assurance capability requirements (No.: CNCA-00C-005).4.The products and services covered by this system include the development, design and production of electric toothbrush, hair clipper, massager and facial care device for export and the production of coffee machine for export.This system covers the whole process of quality management activities and places related to the above products and services.5.The departments covered by this system include: management, HR department, Admin. department, quality department, production department, engineering department, purchasing department, PMC department, warehouse department, marketing department, fixture group and computer department.XXXXX Appliance LimitedChapter 4: Quality policies and objectives1.Quality policy:Improve product quality and customer satisfaction;Improve production efficiency and reduce operation cost;Continuously improve the system and increase the competitiveness of the company.2.Quality objectives:1)The management representative shall organize the preparation or revision of quality management system objectives once a year in accordance with the company's quality policy and the key processes and control requirements of production and management. The objectives shall include meeting product requirements, complying with applicable laws and regulations and other requirements, and commitment to continuous improvement, etc. And keep consistent with the quality policy.2)When formulating or revising the quality objectives, the following shall be considered:A)give priority to expectations of interested parties;B)performance of benchmarking enterprises;C)requirements of laws and regulations applicable to products;D)business management and competition requirements, market conditions and economic conditions;E)factory management review results;F)performance achievement data of the previous year and work focus of the current year.3)when planning how to achieve quality objectives, the organization shall determineA)activities to be implemented;B)required resources;C)responsible person;D)completion time;E)evaluation method of results.See Appendix 1 for quality objective plan.XXXXX Appliance Limited Chapter 6:Responsibilities and authorities1.Description of responsibilities and authorities1.1 Responsibilities of relevant personnel of each department1.1.1 For the responsibilities of various management, execution and verification personnel of the company, please refer to the supporting document organization structure and post responsibilities of each department.1.2 Responsibilities and authorities of management1.2.1 General manager or authorized personA. The top manager of company A shall take charge of the work of the company in an all-round way;B. Formulate quality policies and objectives, implement organizational structure and approve quality manual;C. Ensure that the responsibilities and authorities of the organization are determined and communicated, and ensure that the idea of customer focus and environmental protection is established in the organization;D. Appoint the company's management representative to provide sufficient resources for the effective operation of the quality management system and preside over the quality management review;E. Make long-term development plan for the future of the company.1.2.2 Management representativeA. Ensure that quality policies and objectives are established and aligned with the strategic direction of the organization;B. Ensure that the quality policy is understood and implemented within the organization;C. Ensure that the quality management system requirements are incorporated into the business operation of the organization;D. Improve the awareness of process methods;E. Ensure the acquisition of resources required by the quality management system;F. Convey the importance of effective quality management and meeting the requirements of quality management system, products and services;XXXXX Appliance Limited G. Ensure the expected output of the quality management system;H. Absorb, guide and support employees' participation to contribute to the effectiveness of the quality management system;I. Enhance continuous improvement and innovation;J. Supports other managers to prove their leadership in their areas of responsibility.1.2.3 Factory affairs department (including logistics department)A. Establish and implement the company's administrative system;B. Maintain the company's environmental health and logistics security;C. Is responsible for the disposal of various wastes of the company.1.2.4 Administration and HR departmentA. Establish and implement the personnel system of the company;B. Formulate and implement the quality training system for employees;C. Establish personnel files (including records of education, training, skills and experience of employees);D. Collect laws and regulations and review compliance;E. Is responsible for environmental information exchange inside and outside the company.1.2.5 Financial departmentA. Is responsible for the company's financial management and reasonable arrangement of funds. Do a good job in product cost accounting and improve economic efficiency.1.2.6 PMC DepartmentA. Review customer orders provided by business department and make material demand plan and production schedule;B. According to the material status and production schedule to prepare the production order of each production department;C. Monitor the production progress of relevant production departments to ensure delivery or adjust the corresponding production schedule;D. Communication and coordination of relevant departments.。