磨削力及磨削
磨削机理

δ——单颗工作磨粒顶面积,即工件与工作磨粒的实际接触面积;
p ——磨粒实际磨损表面与工件间的平均接触压强;
因此,可以得到单位宽度法向磨削力F’n,单位宽度切向磨削力F’t公式:
F 'n
1 1 v w P An vw Ce a p 2 d se 2 Fp a p vs 1 vs
1 2
l l q
1
Fn l F p Al N d l dl
0
整个接触弧长度上的法向磨削力大小:
Fn F p C e
,
vw v s
2 1
a d
p se
1
1 1 n 1 n 2
有效磨刃数, 为砂轮以工件的接触弧长度,b为磨削宽度。
Ls
砂轮接触面上的动态磨刃数的磨削力计算公式
关于磨削力计算公式的建立,目前国内外有不少 论述。在这里重点介绍G.Wener等建立的磨削力计算 公式,该公式考虑了磨削力与磨削过程的动态参数关 系。
建立磨削力计算公式时,需要两项参数:
(1)单位砂轮表面上参与工作的磨刃数; (2)砂轮与工件相对接触长度内的平均切削截面积A。
单位砂轮表面上参与工作的磨刃数:N d An Ce
vw v s
ap d se
2
如图,对于弧任意接触长度ι范围内的动态磨刃数Nd(ι)为:
l N d (l ) N d l s
vw A C n e v s
磨削原理
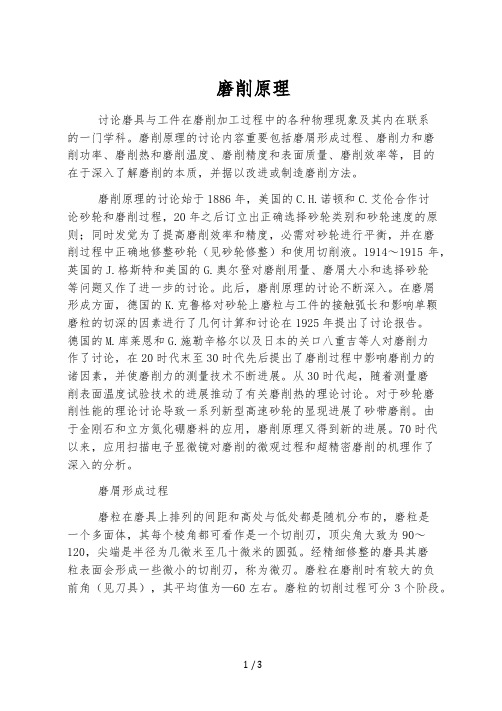
磨削原理讨论磨具与工件在磨削加工过程中的各种物理现象及其内在联系的一门学科。
磨削原理的讨论内容重要包括磨屑形成过程、磨削力和磨削功率、磨削热和磨削温度、磨削精度和表面质量、磨削效率等,目的在于深入了解磨削的本质,并据以改进或制造磨削方法。
磨削原理的讨论始于1886年,美国的C.H.诺顿和C.艾伦合作讨论砂轮和磨削过程,20年之后订立出正确选择砂轮类别和砂轮速度的原则;同时发觉为了提高磨削效率和精度,必需对砂轮进行平衡,并在磨削过程中正确地修整砂轮(见砂轮修整)和使用切削液。
1914~1915年,英国的J.格斯特和美国的G.奥尔登对磨削用量、磨屑大小和选择砂轮等问题又作了进一步的讨论。
此后,磨削原理的讨论不断深入。
在磨屑形成方面,德国的K.克鲁格对砂轮上磨粒与工件的接触弧长和影响单颗磨粒的切深的因素进行了几何计算和讨论在1925年提出了讨论报告。
德国的M.库莱恩和G.施勒辛格尔以及日本的关口八重吉等人对磨削力作了讨论,在20时代末至30时代先后提出了磨削过程中影响磨削力的诸因素,并使磨削力的测量技术不断进展。
从30时代起,随着测量磨削表面温度试验技术的进展推动了有关磨削热的理论讨论。
对于砂轮磨削性能的理论讨论导致一系列新型高速砂轮的显现进展了砂带磨削。
由于金刚石和立方氮化硼磨料的应用,磨削原理又得到新的进展。
70时代以来,应用扫描电子显微镜对磨削的微观过程和超精密磨削的机理作了深入的分析。
磨屑形成过程磨粒在磨具上排列的间距和高处与低处都是随机分布的,磨粒是一个多面体,其每个棱角都可看作是一个切削刃,顶尖角大致为90~120,尖端是半径为几微米至几十微米的圆弧。
经精细修整的磨具其磨粒表面会形成一些微小的切削刃,称为微刃。
磨粒在磨削时有较大的负前角(见刀具),其平均值为—60左右。
磨粒的切削过程可分3个阶段。
①滑擦阶段:磨粒开始挤入工件,滑擦而过,工件表面产生弹性变形而无切屑。
②耕犁阶段:磨粒挤入深度加大,工件产生塑性变形,耕犁成沟槽,磨粒两侧和前端堆高隆起;③切削阶段:切入深度连续增大,温度达到或超过工件材料的临界温度,工件材料明显地沿剪切面滑移而形成磨屑。
磨削加工中的磨削力监测
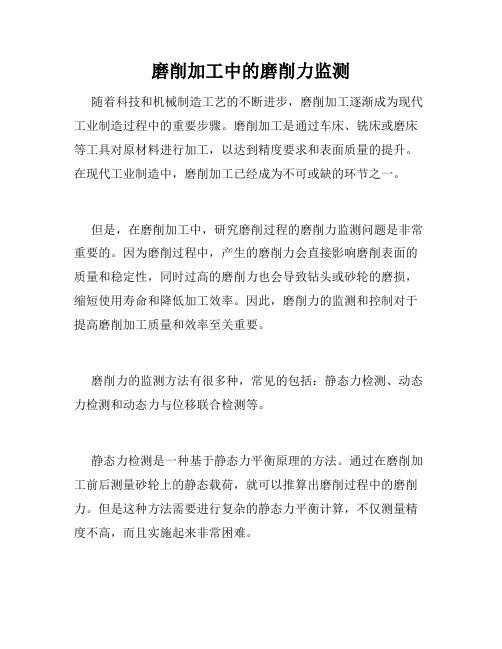
磨削加工中的磨削力监测随着科技和机械制造工艺的不断进步,磨削加工逐渐成为现代工业制造过程中的重要步骤。
磨削加工是通过车床、铣床或磨床等工具对原材料进行加工,以达到精度要求和表面质量的提升。
在现代工业制造中,磨削加工已经成为不可或缺的环节之一。
但是,在磨削加工中,研究磨削过程的磨削力监测问题是非常重要的。
因为磨削过程中,产生的磨削力会直接影响磨削表面的质量和稳定性,同时过高的磨削力也会导致钻头或砂轮的磨损,缩短使用寿命和降低加工效率。
因此,磨削力的监测和控制对于提高磨削加工质量和效率至关重要。
磨削力的监测方法有很多种,常见的包括:静态力检测、动态力检测和动态力与位移联合检测等。
静态力检测是一种基于静态力平衡原理的方法。
通过在磨削加工前后测量砂轮上的静态载荷,就可以推算出磨削过程中的磨削力。
但是这种方法需要进行复杂的静态力平衡计算,不仅测量精度不高,而且实施起来非常困难。
动态力检测是一种直接测量磨削过程中动态力变化的方法。
通过在磨削过程中实时监测磨具上的动态载荷,就可以推算出磨削力的大小和变化趋势。
这种方法可以实现高精度的测量,同时也比较简单易行。
但是,动态力检测只能测量磨削力的大小和变化趋势,对磨削过程中的位移和振动等其他因素无法进行检测。
动态力与位移联合检测是一种综合了动态力和位移测量的方法。
通过在磨削过程中实时监测磨具上的动态载荷和磨具的位移变化,就可以更加精确地推算出磨削力的大小和变化趋势,同时还能够检测磨削过程中的位移和振动。
这种方法可以实现非常高精度的测量,但是相对于动态力检测,它的实施难度和成本也会有所提高。
在磨削加工中,磨削力监测技术的应用已经变得非常普遍。
通过精确的磨削力监测,对磨削过程中的如量切削深度、磨削速度等要素进行优化和管理,就可以有效地提高磨削加工质量和效率,同时也可以有效地保护磨具的使用寿命,降低成本和存储开支。
总之,在现代机械制造领域中,磨削加工监测技术的发展已经成为了行业趋势,同时也为未来的机械制造提供了更广阔的空间和发展机遇。
机械加工中的磨削力分析与优化

机械加工中的磨削力分析与优化引言:机械加工是一种常见的制造工艺,磨削作为机械加工的重要环节之一,对于提高零件加工精度和表面质量至关重要。
然而,磨削过程中的磨削力对机械系统的稳定性和加工效果有着重要影响。
因此,磨削力的分析与优化成为了广大研究者关注的焦点。
一、机械加工中的磨削力分析1. 磨削力的来源磨削力主要由三个方面的因素共同作用产生:磨料与工件之间的相互作用力、磨料与磨削机构之间的相互作用力以及磨削过程中引起的摩擦力。
其中,磨料与工件之间的相互作用力又分为磨削力与进给力两个分力。
2. 磨削力的计算方法磨削力的计算方法主要有经验公式法、静力学法和有限元法等。
经验公式法根据实际生产中的经验数据和统计学方法得出,简单易行,但精度相对较低。
静力学法基于力平衡原理,将磨削力的计算转化为切削力的计算,适用于刀具磨削。
有限元法则是一种仿真方法,通过建立复杂的力学模型和各种约束条件,对磨削力进行精确的计算和预测。
二、磨削力的影响因素分析1. 材料特性被加工材料的硬度、韧性和热导率等物理特性直接影响着磨削力的大小。
一般来说,材料越硬、韧性越高、热导率越低,磨削力越大。
2. 磨料特性磨料的颗粒尺寸、形状和硬度等特性对磨削力有着重要影响。
磨削力随着磨料颗粒尺寸的增加而增加,而随着磨料颗粒硬度的增加而减小。
3. 加工参数磨削过程中的进给速度、切削速度和进给深度等加工参数对磨削力起重要作用。
一般来说,切削速度越大,进给速度越小,磨削力越大。
同时,进给深度的增加也会导致磨削力的增加。
三、磨削力的优化措施1. 选用合适的磨料根据被加工材料的特性选择合适的磨料是降低磨削力的有效措施之一。
对于硬度较高的材料,应选择颗粒较细、形状较锐利的磨料进行磨削,以降低磨削力。
2. 优化加工参数调节磨削过程中的进给速度、切削速度和进给深度等加工参数,是降低磨削力的重要手段。
通过合理选择这些参数,可以使磨削力保持在合适的范围内,同时提高加工效率和加工质量。
磨削过程及磨削原理
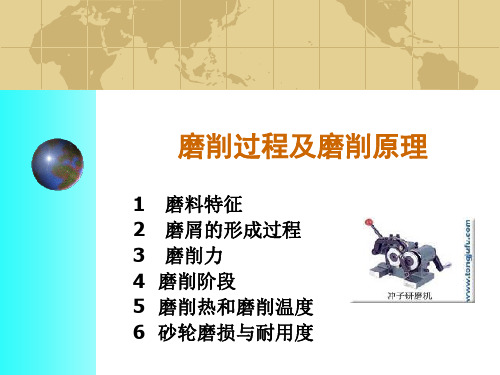
六、砂轮的磨损与耐用度
形态:磨耗磨损(A)、磨粒破碎(B-B) 和脱落磨损(C-C)。 砂轮耐用度:砂轮钝化、变形后加工 质量和效率降低。~用砂轮在两次修 整之间的实际磨削时间度时,工件将发 生颤振,表面粗糙度突然增大,或出 现表面烧伤现象。
由图可知,缩 短初磨阶段和稳定 阶段可提高生产效 率,而保持适当清 磨进给次数和清磨 时间可提高表面质 量。
五 磨削热和磨削温度
1. 磨削温度的基本概念 2. 影响磨削温度的主要因素
砂轮速度V: V ↑→θ↑ 工件速度Vw : Vw ↑→θ↓ 径向进给量fr: fr↑→θ↑ 工件材料: 导热性↓→θ↑ 砂轮硬度与粒度:硬度↓→θ↓ 磨粒大小↑→θ↓
二 磨屑的形成过程
滑擦阶段:磨粒切削厚度非常小,在 工件表面上滑擦而过,工件仅产生弹 性变形。
刻划阶段:工件材料开始产生塑性变 形,磨粒切入金属表面,磨粒的前方 及两侧出现表面隆起现象,在工件表 面刻划成沟纹。磨粒与工件间挤压摩 擦加剧,磨削热显著增加。
切削阶段:随着切削厚度的增加,在 达到临界值时,被磨粒推挤的金属明 显的滑移而形成切屑。
磨削过程及磨削原理
1 磨料特征 2 磨屑的形成过程 3 磨削力 4 磨削阶段 5 磨削热和磨削温度 6 砂轮磨损与耐用度
一 磨料特征
很不规则,大多数呈菱形八面体; 顶尖角大多数为90度~120度,以很大的负前角进行切 削; 磨粒切削刃几乎都存在切削刃钝圆半径; 在砂轮表面分布不均匀,高低也不同。
磨粒常见形状
三 磨削力
➢磨削力的的来源:工件材料产生变形时的抗力和 磨粒与工件间的摩擦力。
➢磨削力的特征: (1) 单位磨削力很大 (2) 径向分力很大---径向力虽不做工,但会使
工件产生水平方向的弯曲,直接影响加工精度。
磨削加工中的磨削力分析

磨削加工中的磨削力分析磨削加工是一种高精度的加工方式,可以用于加工各种材料的零部件。
其原理是使用磨料与加工物体之间的相对运动来去除材料表面的毛刺和瑕疵,制造出精密的表面和形状。
磨削加工的质量和效率与磨削力大小有着密切关系,因此对磨削力的分析和计算是磨削加工过程中极为重要的一环。
一、磨削加工的基本原理磨削加工是利用磨料与工件之间的相对运动,在压力的作用下,去除工件表面的毛刺和瑕疵,进而达到加工目的的过程。
在磨削加工中,磨料既是一个加工工具,也是一种加工介质。
其磨削力主要由切削力、磨合力和磨料轴向力三部分组成。
其中,切削力是主要作用力,因其大小和方向对于磨削加工的影响最为显著。
二、磨削力分析的原则磨削力是磨削加工过程中产生的一种重要力,其大小和方向对于成形精度、加工效率和工件表面质量等方面都有着显著的影响。
因此,了解磨削力的大小和方向,对于进行磨削加工质量的保证和高效率的实现都具有非常重要的作用。
在磨削力分析中,我们需要掌握以下几个基本原则:1.磨削力的大小和方向是磨削加工过程中的重要指标之一,需要进行精确的测量和分析。
2.在磨削加工过程中,应尽量降低磨削力的大小,实现高效率、高精度的加工目标。
3.在磨削力分析中,需要考虑到各个因素的综合影响,不能简单地直接计算或估算。
4.针对不同的磨削加工过程和实际需要,需要采用不同的磨削力分析方法和手段。
三、磨削力的计算方法磨削力的计算方法可以分为两种:经验计算法和基于力学原理的计算方法。
在实际应用中,一般采用经验计算和力学原理相结合的方法进行磨削力的估算。
一般情况下,磨削力的计算方法根据材料的硬度和材料的粘合程度分为两种:理论计算法和实验计算法。
其中,理论计算法以理论分析为基础,通过分析材料硬度和材料粘合程度之间的关系,计算出磨削力的大小和方向。
而实验计算法则以实验结果为依据,通过不同实验条件下的测量结果,计算出磨削力的大小和方向。
在实际应用中,常采用理论计算法和实验计算法相结合的方法,进行磨削力的估算。
4磨削
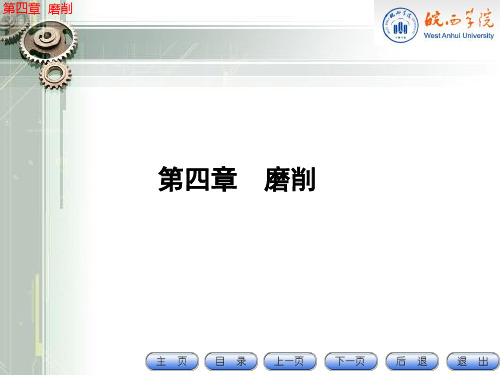
第四章 磨削
二、磨削温度
磨粒磨削点温度θdot 磨粒切削刃与切屑接触部分的温度,是磨削中温度 最高的部位,也是磨削热的热源。它不但影响工件 表面质量,且与磨粒的磨损以及切屑的熔着现象有 密切关系。
f v v
0 . 240 . 26 0 . 13 dot w r
v、vw——分别为砂轮及工件的线速度(m/s); fr——径向进给量(mm)。
工件干磨时常发生这种情况 。
第四章 磨削
二、磨削温度
(2)淬火烧伤 磨削时,工件表面层温度超过相变温度 Ac3 ,如果此时冷 却充分,则表层将急冷形成二次淬火马氏体组织。工件 表层硬度较原来的回火马氏体高,但很薄,其下层因冷 却速度慢仍为硬度较低的回火索氏体和屈氏体。这种情 况称为淬火烧伤。
⑷砂轮的磨损会使磨削力增大。
第四章 磨削
一、磨削力和磨削功率
主运动所消耗的功率定义为磨削功率。
磨削功率:
Pm Fz 1000
第四章 磨削
二、磨削温度
(一)磨削温度的概念 磨削时由于速度很高,且单位切削功率也大(约为车 削的10~20倍)。因此磨削温度很高。 磨削温度 :砂轮与工件接触面的平均温度 磨削温度区分为: 砂轮磨削区温度θA和磨粒磨削点温度θdot。
第四章 磨削
二、磨削温度
烧伤表面的硬度变化
第四章 磨削
二、磨削温度
磨削烧伤的表现形式
磨削烧伤会破坏工件表面层组织,严重的会出现裂纹, 从而影响工件的耐磨性和使用寿命。
(1)退火烧伤
(2)淬火烧伤 (3)回火烧伤
第四章 磨削
二、磨削温度
(1)退火烧伤 在磨削时,如工件表面层温度超过相变温度Ac3,则马 氏体转变为奥氏体,如果此时无冷却液,则表面层硬度 急剧下降,工件表面层被退火,故这种烧伤称退火烧伤。
磨边机的磨削过程的数学模型的研究
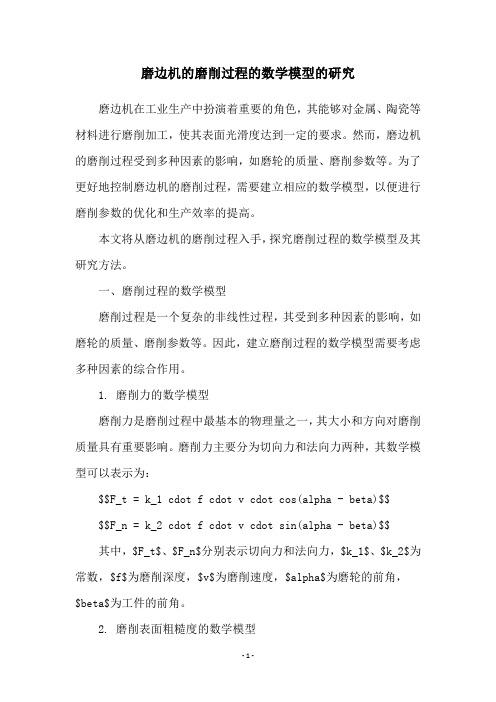
磨边机的磨削过程的数学模型的研究磨边机在工业生产中扮演着重要的角色,其能够对金属、陶瓷等材料进行磨削加工,使其表面光滑度达到一定的要求。
然而,磨边机的磨削过程受到多种因素的影响,如磨轮的质量、磨削参数等。
为了更好地控制磨边机的磨削过程,需要建立相应的数学模型,以便进行磨削参数的优化和生产效率的提高。
本文将从磨边机的磨削过程入手,探究磨削过程的数学模型及其研究方法。
一、磨削过程的数学模型磨削过程是一个复杂的非线性过程,其受到多种因素的影响,如磨轮的质量、磨削参数等。
因此,建立磨削过程的数学模型需要考虑多种因素的综合作用。
1. 磨削力的数学模型磨削力是磨削过程中最基本的物理量之一,其大小和方向对磨削质量具有重要影响。
磨削力主要分为切向力和法向力两种,其数学模型可以表示为:$$F_t = k_1 cdot f cdot v cdot cos(alpha - beta)$$$$F_n = k_2 cdot f cdot v cdot sin(alpha - beta)$$ 其中,$F_t$、$F_n$分别表示切向力和法向力,$k_1$、$k_2$为常数,$f$为磨削深度,$v$为磨削速度,$alpha$为磨轮的前角,$beta$为工件的前角。
2. 磨削表面粗糙度的数学模型磨削表面粗糙度是衡量磨削质量的重要指标之一,其数学模型可以表示为:$$R_a = frac{1}{2pi} int_0^{2pi} h(x) cdot cos(x) dx$$ 其中,$R_a$为磨削表面粗糙度,$h(x)$为表面高度函数。
3. 磨削温度的数学模型磨削过程中会产生大量的热量,磨削温度对磨削质量具有重要影响。
磨削温度的数学模型可以表示为:$$T = T_0 + k_3 cdot f cdot v cdot ln(frac{t}{t_0})$$ 其中,$T$为磨削温度,$T_0$为初始温度,$k_3$为常数,$t$为磨削时间,$t_0$为初始时间。
- 1、下载文档前请自行甄别文档内容的完整性,平台不提供额外的编辑、内容补充、找答案等附加服务。
- 2、"仅部分预览"的文档,不可在线预览部分如存在完整性等问题,可反馈申请退款(可完整预览的文档不适用该条件!)。
- 3、如文档侵犯您的权益,请联系客服反馈,我们会尽快为您处理(人工客服工作时间:9:00-18:30)。
§14—4 磨削力及磨削功率
14-1砂轮的特性和砂轮选择
14-2磨削加工类型和磨削运动
14-3磨削加工表面形成机理和磨削要素
14-4磨削力及磨削功率
一、磨削力的特征
二、磨削力及磨削功率
三、磨削力的测试方法
14-5磨削温度
14-6砂轮的磨损及砂轮表面形貌
14-7磨削表面质量与磨削精度
14-8几种高效和小粗糙度的磨削方法
一、磨削力的特征
尽管砂轮单个磨粒切除的材料很少,但因砂轮表层有大量的磨粒同时工作,而且磨粒的工作角度很不合理,因此总的磨削力仍相当大。
同其他切削加工一样,总磨削力可分解为三个分力:Fc—主磨削力(切向磨削力);Fp—切深抗力(径向磨削力);Ff——进给抗力(轴向磨削力)。
几种不同类型磨削加工的三向分力示如图14—15。
磨削力的主要特征有以下三点:
(1)单位磨削力kc值很大:由于磨粒几何形状的随机性和几何参数不合理,磨削时的单位磨削力kc值很大;根据不同的磨削用量,kc值约在7—20KN/mm2之间,而其他切削加工的单位切削力kc值均在7KN/mm2以下。
(2)三向分力中切深为Fp值最大:原因同上。
在正常磨削条件下,Fp/Fc的比值约为2.0—2.5,而且工件材料的塑性越小,硬度越大时,Fp/Fc的比值越大(见表14—7)。
在磨削深度(切深)很小和砂轮严重磨损致使磨粒刃区圆弧半径增大时,Fp/Fc的比值可能加大到5—10。
(3)磨削力随不同的磨削阶段而变化:由于Fp较大,使机床、工件和夹具产生弹性变形。
在开始的几次进给中,实际径向进给量frac远远小于名义径向进给量frap,即frac<frap。
随着进给次数的增加,工艺系统的变形抗力也逐渐增大,这时实际的径向进给也逐渐增大,直至变形抗力增大到等于名义的径向磨削力Fpap时,实际径向进给量才会等于名义值。
这一过程可用图14—16中的0A一段曲线来表示,称为初磨阶段。
在初磨阶段中,frac<frap。
若机床、工件和夹具的刚度越低,则此阶段越长。
此后,当frac=frap时,即进入稳定阶段AB。
当余量即将磨完时,就可停止进给进行光磨,以提高表面质量,图中BC一段称为光磨阶段。
由上述可知,要提高生产率,就必须缩短韧磨阶段及稳定阶段的时间,即在保证质量的前提下,可适当增加径向进给fr;要提高已加工表面质量,则必须保持适当的光磨进给次数。
二、磨削力及磨削功率
前已述及,磨削过程是磨粒在工件表面上进行滑擦、耕犁和切屑形成的过程。
由于磨削速度很高,所以摩擦在磨削过程中所消耗的能量占的比例相当大。
试验表明:干磨退火碳素钢时,材料剪切所消耗的能量占20%—30%,摩擦所消耗的能量占70%—80%。
所以在磨削力的公式中应能反映出滑擦力的影响。
磨削力的公式表示如下:
(14—9)
(14—l0)
式中Fc、Fp——分别为切向和径向磨削力,N;
Vw—工件速度,m/s;
Vc—砂轮速度,m/s;
fr—径向进给量,mm;
B——磨削宽度,mm;
CF—切除单位面积的切屑所需的力,N/mm2(表14—8);
α—假设磨粒为圆锥形时的锥顶半角;
μ—工件和砂轮间摩擦系数(表14—9)。
磨削功率Pm为:
Pm=Fc•Vc/1000KW(14—11)
式中Fc—一切向磨削力,N;
Vc—砂轮线速度,m/s。
三、磨削力的测试方法
磨削过程很复杂,影响磨削力因素很多,而对磨削的机理研究向有待深入,目前的磨削力计算理论公式精确度不高,所以一般都用实验方法来测定磨削力。
测定磨削力的方法很多,下面只介绍其中的一种。
图14—17所示为测定外圆磨削力的测定装置原理图。
此法是把工件支持在顶尖上。
由于顶尖的圆周上粘有电阻应变片,所以顶尖所受的磨削力可通过应变片的阻值变化而测出。
在工作中,切向磨削力使顶尖下弯,所以用1、2、3、4应弯片来测出Fc。
而径向磨削力是使顶尖前后弯曲,因此Fp可用5、6、7、8应变片测出。
上述电阻应变片式测力装置要进行精确的标定。