夹具定位
第二章 工件在夹具中的定位

Z
Y
X
考虑定位方案时,先分析必须消除哪些自由度,
再以相应定位点去限制。
Z
Z
Y
Y
X X
a) b)
ox方向上没有原始尺寸要求, 因此沿这个方向移动的自由 度。可以不加限制,工件只 要限制五个自由度就够了。 图2-3
只有oz方向上有原始尺寸, 但要保 证此尺寸必须限制三个 自由度,即沿Z轴的移动和绕X 轴、Y轴的转动
“一面两销”的两圆柱销重复限制了沿 x 方向的移动自 由度,属于过定位。由于工件上两孔的孔心距和夹具上两销 的销心距均会有误差,因而会出现上图所示的相互干涉现象。
解决“一面两孔”的定位干涉问题的途径: (1)减小一个销的直径; (2)将一个销做成削边销。
3)定位心轴
主要用于盘套类零 件的定位。心轴定心精 度高,但装卸费时,有 时易损伤工件孔,多用 于定心精度要求高的情 况。定位时,工件楔紧 在心轴上,多用于车或 磨同轴度要求高的盘类 零件,小锥度心轴实际 上起不到定位的作用
2-1. 工件定位原理
(1)六点定位原理
一个自由的物体,它对三 个相互垂直的坐标系来说,有 六个活动可能性,其中三种是 移动,三种是转动。习惯上把 这种活动的可能性称为自由度, 因此空间任一自由物体共有六 个自由度。
图2-1 工件自由度示意图
未定位工件在空间有六个自 由度,定位就是限制其自由度。
合理布置六个定位支承 点,使工件上的定位基面与 其接触,一个支承点限制工 件一个自由度,使工件六个 自由度被完全限制,在空间 得到唯一确定的位置,此即 六点定位原理。
AO AC AO2 AB
' 2
2 2
2
2
2
2
D2 b 1 D 2 min b Tlk Tlx 2 2 2 2 2 2
机械加工工艺规程设计—机床夹具与工件定位

一般情况把夹紧元件和中间传动机构统称为夹 紧机构。有的时候以上三者也会混在一起,很难区 别。
对夹紧装置的基本要求
1) 夹紧时应保证工件的定位,而不能破坏工件的定位。 2) 夹紧力的大小应适宜,既要保证工件在整个加工过程 中位置稳定不变,还不能产生振动、变形和表面损伤。 3) 应根据生产类型设计相应的夹紧机构。 4) 为防止夹紧后自动脱开,夹紧机构须具备良好的自锁 性能。
只考虑切削力(或切削矩)对夹紧的影响,并假设工艺系 统是刚性的,切削过程是稳定不变的,然后找出加工过程中对 夹紧最不利的状态,按静力平衡原理求出夹紧力,最后乘上安 全系数(粗加工取2.5-3,精加工取1.5-2)。
在实际夹具设计中,对于夹紧力的大小并非所有情况都要 用计算确定。如手动夹紧用经验法或类比法。
有些重、大、复杂的工件,往往先在待加 工处划线,然后装上机床,按所划的线进行找 正定位。
适用场合:生产批量较小,毛坯精度较低, 以及大型工件等不宜使用夹具的粗加工中。图4-6 工件划线找正装夹工件的装夹方法
2.机床专用夹具装夹法 所谓机床专用夹具,是 指为某零件的某道工序而专门设计制造的夹具。
2)经验类比法。前面说过,精确计算夹紧力的大小是件很 不容易的事,因此在实际夹具设计中,有时不用计算的方法 来确定夹紧力的大小。如手动夹紧机构,常根据经验或用类 比的方法确定所需夹紧力的数值。但对于需要比较准确地确 定夹紧力大小的,如气动、液压传动装置或容易变形的工件 等,仍有必要对夹紧状态进行受力分析,估算夹紧力的大小。
图4-20 辅助支承应用 1—加工面 2—辅助支承
图4-21 推式辅助支承 1—支承滑柱 2—推杆 3—半圆键 4—手柄 5—钢球
工装夹具设计中的定位分析
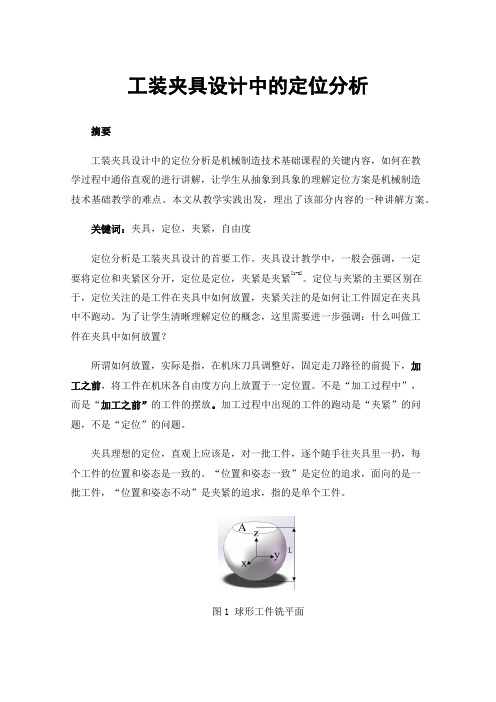
工装夹具设计中的定位分析摘要工装夹具设计中的定位分析是机械制造技术基础课程的关键内容,如何在教学过程中通俗直观的进行讲解,让学生从抽象到具象的理解定位方案是机械制造技术基础教学的难点。
本文从教学实践出发,理出了该部分内容的一种讲解方案。
关键词:夹具,定位,夹紧,自由度定位分析是工装夹具设计的首要工作。
夹具设计教学中,一般会强调,一定要将定位和夹紧区分开,定位是定位,夹紧是夹紧[1-3]。
定位与夹紧的主要区别在于,定位关注的是工件在夹具中如何放置,夹紧关注的是如何让工件固定在夹具中不跑动。
为了让学生清晰理解定位的概念,这里需要进一步强调:什么叫做工件在夹具中如何放置?所谓如何放置,实际是指,在机床刀具调整好,固定走刀路径的前提下,加工之前,将工件在机床各自由度方向上放置于一定位置。
不是“加工过程中”,而是“加工之前”的工件的摆放。
加工过程中出现的工件的跑动是“夹紧”的问题,不是“定位”的问题。
夹具理想的定位,直观上应该是,对一批工件,逐个随手往夹具里一扔,每个工件的位置和姿态是一致的。
“位置和姿态一致”是定位的追求,面向的是一批工件,“位置和姿态不动”是夹紧的追求,指的是单个工件。
图1 球形工件铣平面如图1所示,用立式普通铣床在一批球形工件上加工图示平面,最少需要限制几个自由度?首先需要明确,要加工的是一批工件,不是一个工件,要关注的是:一批工件,逐个放置到已经调好刀的机床上,工件所放位置对待加工尺寸的影响。
待加工尺寸是什么?如图1所示,该案例所指的待加工尺寸是L,需要保证尺寸L,即平面A相对于最低点的距离。
以球心为原点建立工件坐标系,在机床工作台面上建立机床坐标系,工件在机床上的位置和姿态,即转化为工件坐标系相对于机床坐标系的位置和姿态。
列出工件的六个自由度,如图1所示,即 , , , , ,,对六个自由度逐个分析。
对于,考虑当第个球形毛坯放置在机床坐标系的,第(n+1)个球形毛坯放置在的位置时,加工出的平面的定位尺寸会发生变化吗?很明显不会,但是可能会由于放置的位置超出设定的行程,出现“加工不到”的问题,“加工不到”对于定位尺寸的精度没有影响,所以可以不限制。
夹具典型定位、夹紧原理-李军
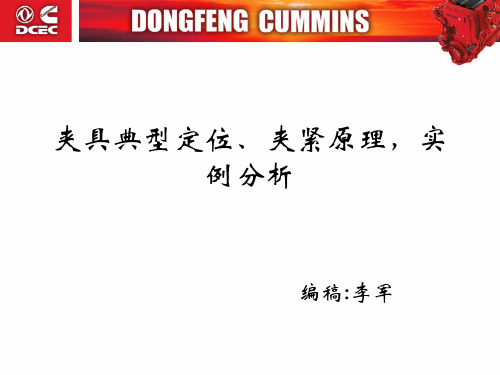
完全定位与不完全定位
• 而图b所示为铣削一个通槽,需限制除了 外的其他5个自由度。
完全定位与不完全定位
• 图中c所示在同样的长方 体工件上铣削一个键槽, 在三个坐标轴的移动和转 动方向上均有尺寸及相互 位置的要求,因此,这种 情况必须限制全部的6个 自由度,即完全定位
欠定位与过定位
• 欠定位: 工件实际定位限制的自由度少于该工序加工 所需限制的自由度数目; • 过定位: 两个或两个以上支承点重复限制同一个自由 度,这样将是工件的位置不确定;
常见的定位方式和定位元件
4.工件以组合表面定位
实际加工过程中,工件往往是以几个表面 同时定位的,称为“组合表面定位”。
常见的定位方式和定位元件
• 1 . 一个孔和一个端面组合 • 一个孔与端面组合定位时,孔与销或心轴定位采 用间隙配合,此时应注意避免过定位,以免造成 工件和定位元件的弯曲变形, 如图 示。
常见的定位方式和定位元件
2.工件以圆孔定位
有些工件,如套筒、法兰盘、拨叉等以孔作为定 位基准.
(1)定位销
常见的定位方式和定位元件
• (2)锥销:工件圆孔与锥 销定位,圆孔与锥销 的接触线是一个圆, 限制工件 、 、 三个 位移自由度,图 a 用 于粗基准,图 b 用于 精基准。
常见的定位方式和定位元件
这里我们将主要介绍具的定位与夹紧
工件定位的基本原理
• 工件定位的实质是什么呢? 使工件在夹具中占有某个确定的位置 • 怎样获得工件的确定位置呢? 通过定位支撑限制相应的自由度来获得 • 工件在空间直角坐标系内有具有几个自由 度? • 6个,如下图
工件定位的基本原理
在空间直角坐标系中,刚体具有六个自由 度,即沿X、Y、Z轴移动的三个自由度和绕 此三轴旋转的三个自由度。
夹具定位方案

-对操作人员进行夹具使用和维护的专业培训,提升其操作技能和问题处理能力。
-提供操作手册和指导资料,帮助操作人员正确使用和维护夹具。
六、结论
本夹具定位方案结合了现代自动化制造的需求和实际生产条件,以合法合规为基础,追求高精度和高效率。通过精细化的管理、严格的实施流程和定期的维护,确保夹具定位系统的长期稳定运行,为企业带来持续的生产效益。
2.定位系统设计
-采用高精度的定位元件,如定位销、定位块等,确保定位精度。
-设计定位系统时,考虑工件的装夹和释放过程,优化操作流程。
-运用计算机辅助设计(CAD)和计算机辅助制造(CAM)技术,提高设计精度和加工效率。
3.定位误差分析
-对可能的定位误差源进行分析,包括夹具制造误差、装配误差、热变形等。
夹具定位方案
第1篇
夹具定位方案
一、项目背景
随着我国制造业的快速发展,自动化设备在生产过程中的应用越来越广泛。在生产线上,夹具作为重要的辅助设备,其作用是对工件进行定位、固定,保证工件在加工过程中位置准确,提高生产效率和产品质量。然而,在实际应用中,夹具的定位问题一直困扰着许多企业。为解决这一问题,本文将结合企业实际情况,制定一份合法合规的夹具定位方案。
(1)定位方式:根据工件特点,选择合适的定位方式,如点定位、线定位、面定位等。
(2)定位元件:选用高精度、高刚性的定位元件,如定位销、定位块、定位孔等。
(3)定位误差分析:分析夹具定位过程中可能出现的误差,如定位元件的制造误差、装配误差、工件本身的形状误差等,制定相应的补偿措施。
(4)定位精度检测:采用高精度的测量仪器,对夹具定位精度进行检测,确保其满足生产要求。
-通过有限元分析(FEA)等技术,模拟夹具在实际工作条件下的应力应变状态,制定相应的补偿措施。
夹具在机床上的定位
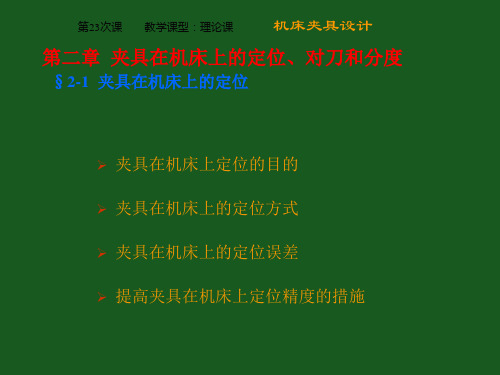
夹具在机床上的定位方式
夹具在机床上的定位误差 提高夹具在机床上定位精度的措施
第23次课
教学课型:理论课
机床夹具设计
第二章 夹具在机床上的定位、对刀和分度
§2-1 夹具在机床上的定位
二、夹具在机床上的定位方式
夹具在工作台面上的连接定位
夹具在主轴上的连接定位
第23次课
教学课型:理论课
第二章 夹具在机床上的定位、对刀和分度
§2-1 夹具在机床上的定位
三、夹具在机床上的定位误差 2.钻床夹具的定位误差
P与B的平行度误
差ΔZ属“位置误差”,
由此造成孔中心线的
垂直度误差为:
Δβ=sin–1(ΔZ/L)。
第23次课
教学课型:理论课
机床夹具设计
第二章 夹具在机床上的定位、对刀和分度
§2-1 夹具在机床上的定位
一、夹具在机床上定位的目的
要保证工件的加工精度,就必须使工艺系统各环 节之间具有正确的位置关系。其中包括工件的定位基 准面与夹具的定位元件表面之间、夹具的定位基准面 与机床的工作台和导轨或主轴轴线之间都必须具有正 确的位置关系,才能使加工表面相对刀具及切削成形 运动处于理想位置。
第23次课
教学课型:理论课
包 括
第23次课
教学课型:理论课
机床夹具设计
第二章 夹具在机床上的定位、对刀和分度
§2-1 夹具在机床上的定位
三、夹具在机床上的定位误差 1.铣床夹具的定位误差
偏斜角Δβ
Δβ=2tg–1(Δmax/L)
是“连接误差”的一 部分,安装时应注意使 夹具靠向T形槽的同一侧。
第23次课
教学课型:理论课
机床夹具设计
⑶以端面和短锥面在主轴上定位
夹具的定位夹紧与夹具设计
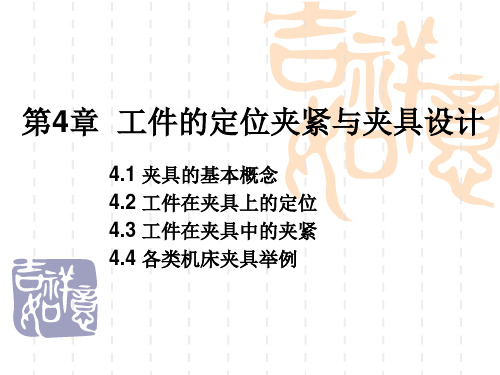
安装一般有三种方式: 1.直接找正安装 工件的定位过程可以由操作工人直接在机床
采用6个按一定规则布置的约束点,可以限制工件 的6个自由度,实现完全定位,称为六点定位原理。
2.典型定位元件及限制的自由度 (1)定位元件:用于代替约束点的定位元件的
种类很多,常用的有:支承钉、支承板、长销、短 销、菱形销、长V形块、短V形块、长定位套、短定 位套、固定锥销、浮动锥销等。
(2)限制自由度以及分析 从表4-2中可以看出,有时候研究定位元件及其 组合能限制哪些自由度不如研究它们不能限制哪些 自由度更方便。
2.工件以圆柱孔定位 工件以圆柱孔定位大都属于定心定位(定位基准
为孔的轴线),夹具上相应的定位元件是心轴和定位 销。
(1)心轴
(2)定位销 圆柱定位销通常限制工件的2个移动自由度。
当要求孔销配合只在一个方向上限制工件自由度 时,可用菱形销,如图4-21(a)所示。
工件也可以用圆锥销定位,如图4-2l(b)和(c)所示。 图示圆锥销定位限制了工件的3个移动自由度。
(5) 随行夹具 用于自动线上,工件安装在随行夹具上,随行夹具 由运输装置送往各机床,并在机床夹具或机床工作 台上进行定位夹紧。
2.从使用机床的类型来分 可分为车床夹具、磨床夹具、钻床夹具(包括钻模)、
镗床夹具(包括镗模)、铣床夹具等。 3.从用途来分 可分为机床夹具、装配夹具和检验夹具等。 4.从动力来源分 可分为手动夹具、气动夹具、液压夹具、气液夹具、
初步认识夹具及定位原理

现一机多能。例如,在车床或摇臂钻床上安装镗模夹具后,就可以对箱体孔系进行镗削加工。
减轻劳动强度:使用专用夹具,特别是自动化程度较高的专用夹具,可以减轻工人的劳
动强度,改善劳动条件,保证安全。
4
二、夹具的组成
机械制造基础
机床夹具的种类虽然繁多,但它们都是由定位元件、夹紧装置、夹具体和其他装置及元件组
3.按夹紧动力源分
按夹紧动力源,夹具可分为手动夹具、液压夹具、气动夹具、电动夹具和磁力夹具等。
10
四、定位原理
1.六点定位原理
机械制造基础
一个自由的物体对3个互相垂直的坐标系来说有6种活动的可能性,它可朝3个方向移动,也可绕3个
方向转动。习惯上把这6种活动的可能性称为自由度。如下页图a所示,一个在空间处于自由状态的物
除上述基本组成部分外,有些夹具根据需要还设置了一些其他装置或元件,如分度装置、 对刀或引导装置和安全保护装置等。如上页图b所示的钻套和钻模板就是为了引导钻头而设置的引
导装置。
7
三、夹具的分类
机械制造基础
1.按使用特点分
按使用特点,夹具可分为通用夹具、专用夹具、成组夹具、组合夹具和拼装夹具等。
(1)通用夹具
爪自定心卡盘和铣床上的台虎钳等。
机械制造基础
2
一、夹具的功用
机械制造基础
工件的装夹方法有两种:① 直接装夹在机床上;② 用夹
具装夹在机床上。 工件直接装夹在机床上时,一般要先按图样要求在工件表面划线,
装夹时用划针或百分表找正后夹紧。这种方法生产率低,且对工人的 技术水平要求较高,一般用于单件和小批生产。成批及大量生产时一 般采用夹具装夹工件。
- 1、下载文档前请自行甄别文档内容的完整性,平台不提供额外的编辑、内容补充、找答案等附加服务。
- 2、"仅部分预览"的文档,不可在线预览部分如存在完整性等问题,可反馈申请退款(可完整预览的文档不适用该条件!)。
- 3、如文档侵犯您的权益,请联系客服反馈,我们会尽快为您处理(人工客服工作时间:9:00-18:30)。
白车身装配夹具的设计标准(尺寸可控性)I.目的使用焊装夹具的二大目的:1)决定钣金件的相对空间位置,2)提供钣金件在此空间位置上的刚度,以抵抗焊枪引起的位移和变形。
II.定位方式1.夹具上的主定位点是由NC定位块,销,托点,和夹紧块来实现的。
定位方式的首选是孔/销定位,其次是形面,如拐角,再其次是边。
2.圆孔/圆销控制四个方向,控制两个方向的是圆孔/菱销,(本公司现在的首选,也是日韩公司的首选。
)或者长孔/圆销,(欧美公司的首选)或者圆孔/双平面圆销(不常见)。
半圆孔/圆销控制三个方向。
III.主定位点的采用1.夹具设计必须严格按产品原设计的主定位点(参考系)来安排定位方式;2.如果实行有困难,必须和主定位点的原设计人员商量才能作改动;3.在延续的工序中,主定位点的采用必须按“一脉相承”的原则,以减少积累误差。
IV.焊接过程中的位移和变形1.虽然,使用焊装夹具的目的是定位和保持此定位。
在焊装过程中,即使在焊装夹具的夹持下,钣金件的位移和变形还是在所难免。
只是数量上是相对微小而已。
2.简单而言,位移和变形是由力和热引起的。
由于尺度管理追求的首要目的是产品的尺寸一致性而非产品精度,应该尽可能的使位移和变形变得一致,从而减少波动误差。
一项非常可取的做法是保持夹紧顺序和焊接顺序的严格一致。
V.定位销/块的要求精度1.NC定位块的位置精度为+0.10毫米,2.NC定位块的位置精度为+0.10毫米,3.NC定位块的位置精度为+0.10毫米,(1.2.3重复)4.定位销的位置精度为+0.10毫米,5.定位销的直径精度为+0.05毫米,(先要确定定位销的直径)6.定位销的圆度精度为+0.01毫米,7.定位销的直度不控制。
8.定位销有效长度要高出制件表面≥5mm(在不顶起外侧的制件(内外两层板)情况下)9.定位销的间距精度:±0.10毫米(对称定位销)10.单个零件的两个定位销的间距精度:±0.10毫米,11.型面可动时,不能与制件干涉(前进、后退及动作途中无干涉),按动作顺序进行。
在后退极限,距车身件端面要有大于15mm的后退间隙。
VI.定位销/块的工艺要求1.NC定位块和定位销有表面防锈处理和硬化处理。
(需要具体要求)2.NC定位块要有符合配合形面的曲面(定位型面与制件的接触面应大于80%)。
VII.定位销/块的尺寸控制能力要求1.定位销的尺寸和与其相配合的钣金件的孔要符合设计精度,(按公司标准XXXXX 执行,而在最差情况下,配合间隙不大于0.2毫米)。
(孔和销的公差和销的位置公差要进行推算,0.2mm很严格的)2.与定位销相配合的钣金件的孔通常具备符合要求的承受能力,孔的尺寸,钣金件的厚度,定位的方位,都是孔承受能力的决定因素。
由此来决定是否应该翻边。
3.定位销/块的刚度决定了在受力状态下保持位置精度的能力。
从定位销/块到基座的连接过长,关节过多都会弱化定位销/块的钢度。
4.整个夹具的刚度也会间接影响定位销/块的尺寸控制能力。
VIII.工件的放入1.所有的固定定位销必须方向一致,方向差超过15度的(15度太大,建议取消此内容),方向不一致应改为活动销。
2.工件的放入如果是由人来执行的,就必须按人机工程的角度来考虑。
通常放入之前会有提起和平移,此两项也必须要可行。
3.放入的首选是由上而下,其次是简单的水平方向的平移。
4.平移加拐弯或扭转都不是好的选择,但是还是可行的。
5.平移的方向应该和钣金件的表面成垂直,如果沿着钣金件的表面,就成了插入,插入不可取。
6.工件的放入的顺序要合理,应避免和其他件的干涉,尤其是多方面的干涉。
7.如果每个具体的动作(平移,拐弯或扭转)的时间可以量化,整个设计就可以优化。
IX.夹具的可夹性1.钣金件上的夹紧点(和测量点一样)要有和XYZ三主轴垂直的小平面,如果不可能设计,夹具就要有符合形面的曲面NC 块。
2.小冲压件的问题一是不容易夹,二是压紧点要和焊接面争空间。
因此,小冲压件上的压紧点要和焊接面尽量分开。
此外,力求推动设计工程师设定特殊形面,以利于来定位。
因为3-2-1的六点定位已经不可能,面定位成为好的选择。
X.夹具的重复性1.应用见证孔检验方法(WITNESS HOLE METHOD)2.应用重复性和重制造性的检验方法(R&R METHOD)XI.夹紧的顺序的优化1.夹紧顺序的设定决定了金属的流动方向,由此而来可能造成钣金表面的皱纹以及工件的位置变化。
因此,为了使钣金件的定位有最大的重复性和一致性夹紧顺序必须优化,2.为了使钣金件的定位有最大的重复性和一致性,应当考虑使用夹而不紧,由此来钝化夹紧顺序的敏感性。
XII.定位不足和过定位1.定位点的设定按3-2-1 原则。
定位不足会使定位没有唯一性,产品没有一致性。
2.钣金件可能有一个方向上刚度相对低一点,应该用过定位来补偿其刚度不足。
3.刚度大的方向要防止过定位。
XIII.夹紧点的密度1.运用过定位来补偿工件刚度不足时,夹紧点的密度应是在空间和刚度之间的平衡,密度高了,刚性提高了,然而,焊枪的活动空间小了。
反之亦然。
2.试制夹具的夹紧点的密度可以适当的高一点。
因为试制时时间不受节拍的限制,可以打开夹紧点来打点。
3.夹紧点可能互相干涉,当夹紧点的密度相对高,冲压件的刚度相对强,以及冲压件的误差相对大时尤其可能发生。
XIV.夹紧点的相互干涉1.夹紧点可能互相干涉;2.当夹紧点的密度相对高,冲压件的刚度相对强,以及冲压件的误差相对大时尤其明显。
3.一旦干涉发生,尺寸控制就有了问题。
4.防止干涉的措施有改进冲压件的尺寸,减少压点,取消或放开非关键的点。
XV.夹紧与夹而不紧力1.为了使夹具的重复性提高,夹具必须让钣金件在夹持状态下仍旧能做一定量的流动。
2.为了使钣金件能流动,大多数的夹持点应该设计为夹而不紧,即留有0.2毫米的缝隙。
当夹而不紧时,夹块将力施加于NC定位块上,而不是钣金件上。
(此处在操作上可能存在困难,还包括夹紧力的选择)3.设计工程师必须明白,在夹紧过程中,钣金件也会有位移,如果夹紧是分批进行,只有最后夹紧可以设计成完全紧固,否则位钣金件位置的一致性就不会是最优的。
4.设计工程师还必须明白,在焊接过程中,钣金件也会有位移。
只有让钣金件流动,才能有利于实现一致性,关键是力求让流动有一致性。
XVI.夹紧力1.与夹紧点的密度相同,夹紧力的强弱应该和钣金件的刚度有关。
钣金件的刚度要求则应该和焊枪可能造成的干扰有关,干扰小,所需要的夹紧力就可以相对弱一些。
(建议夹紧力应该与材料和料厚有关)2.手工焊接,干扰大,夹紧力应该相对大些。
XVII.焊枪可接近性1.焊枪对于焊点的可接近性,已经由同步工程核对过了。
应采用的特殊焊枪也已经确定。
2.焊枪和夹具的关系是干扰问题。
其原则是被焊点要有必要的刚度,如果焊点是决定钣金件位置的话。
XVIII.用来脱离夹具的托架设计1.每个定位销都要有至少一个托点,其与销的距离不能超过100毫米,钣金件相对柔软的部位要额外加点。
2.托面和被托表面形状要相配,托起应同步,使托面与被托表面相同时接触。
其差异不能造成超过15度的偏转(此处应要求与主销轴线方向一致,有偏转将会对定位销精度产生影响)。
XIX.减少焊枪与夹具的干涉1.夹具上焊枪与夹具的干涉是常见的。
2.干涉如果不能在三度空间里解决,就力求在四度空间里解决。
XX.减少工件之间的干涉1.夹具的设计要考虑工件之间的干涉,2.工件放入的方向最好和干涉垂直,3.XXI.减少干涉XXII.焊接顺序的优化1.为了防止出现表面波纹,就必须使钣金件向一个或双向流动,焊点的顺序是依次。
2.对于钣金件的误差,可以采用两种截然不同的方式,一是使误差流向最不敏感的区域,焊点的顺序是还是依次。
二是将误差控制在一定的范围内,通常的焊接顺序就是跳跃式的。
(此处建议固定一种方式,或对不同区域的焊件作不同的要求,如果是夹而不紧,焊接顺序对合件精度的影响就很大,人工操作因人而异的现象就很明显,焊接顺序很重要;如果零件都夹死,焊接顺序对对合件精度的影响就会弱化)3.焊接顺序在设计阶段就由同步工程来决定,夹具设计时优化。
XXIII.夹具控制相对精度的方式1.可以打破惯例,设计一些“无根”(即和夹具基座没有硬性连接)的装置来控制钣金件上的一些相对尺寸要求。
那一类装置可以由链条和夹具相连,而没有和夹具的精确的位置关系。
2.3.XXIV.定位点的选择1.夹具定位销/块的设计必须按照主定位点(参考系)来确定,随意变换会带入误差;2.在冲压件到分总成到总成要严格遵守主定位点(参考系)传递来执行,以减短误差链;3.两主定位孔之间的距离不能过于靠近,以避免定位误差的放大;4.XXV.定位销/块带来的局部的永久性变形1.定位销/块可能对钣金件带来变形。
最为常见的是孔被压拉变大和压块在钣金件表面留下压痕。
2.造成钣金件变形的原因是多种多样的,可能是焊接力过大??,干涉,孔太小,孔位不对,等等;3.处理的方法也是多种多样,可以是加大孔径,该翻边孔,改进夹具精度,去处干涉,调整焊枪和操作方式。
XXVI.压紧装置带来的局部的永久性变形1.当钣金件和夹具不符合时,压紧装置可能会造成钣金件的局部变形;2.有时工程师和夹具调整工会利用夹具来纠正不正确的钣金件,但这会带来应力和反弹,以及尺寸的误差;XXVII.压紧方向的优化1.压紧装置和被压件的表面有个进入角,最佳的应该是垂直;2.当压块同时压两个面时,最佳的进入角应该是两个面形成的夹角的中线(此处应该根据控制面要求的关键程度以某一个面为主,兼顾另一个面,如果以夹角的中线的方式,在实现上存在困难)。
3.XXVIII.XXVVVVBBBB另外要要求:1.夹具底板需刻出间距为200mm的坐标线,并有1~3个基准点。
2.夹具L板、支承座、BASE板的材料、厚度、加工方式、精度、防锈方式作要求3.夹具焊接作业工作面距地面高度为750mm—850m。
4.定位销、定位面要具备独立的、三个方向的可调整性,调整垫片规格按精度要求制定。
5.夹具工作气压应与使用方现场气压(4.5个标准大气压)相一致。
还有等等,最好与夹具的技术协议相通,保持一致。