齿轮检测技术
齿轮磨损检测方法

齿轮磨损检测方法齿轮是一种常见的机械传动装置,广泛应用于各种机械设备中。
然而,长时间的使用和负载使得齿轮容易出现磨损,这将严重影响机械设备的性能和寿命。
因此,及早检测齿轮的磨损程度,对于及时采取维修和修复措施至关重要。
本文将介绍几种常用的齿轮磨损检测方法。
第一种检测方法是使用噪声分析技术。
齿轮在运行时会产生一定的噪声,而磨损齿轮通常会产生特殊的噪声模式。
通过使用声音传感器,可以将齿轮的噪声信号收集并进行分析。
在分析过程中,可以根据噪声的频率和振幅变化来确定齿轮的磨损程度。
这种方法非常简便易行,而且可以在线实时监测齿轮的磨损情况。
第二种检测方法是使用热图像技术。
齿轮磨损会导致能量的散失,进而产生热量。
通过使用红外热像仪,可以观察到齿轮表面的温度分布。
正常的齿轮通常应该有均匀的温度分布,而磨损严重的齿轮则往往会有明显的温度集中区域。
通过这种方法,可以精确地确定齿轮磨损的位置和程度,为维修提供参考依据。
第三种检测方法是使用振动分析技术。
齿轮在运行时会产生一定的振动信号,而磨损齿轮通常会产生与传动频率相关的振动信号。
通过使用振动传感器,可以将齿轮的振动信号收集并进行频谱分析,从而确定齿轮的磨损情况。
这种方法的优点是不需要拆卸齿轮就可以进行检测,非常适用于现场监测和故障诊断。
除了以上几种常用的齿轮磨损检测方法外,还有一些其他的方法也可以用于检测齿轮的磨损程度。
例如,光学检测方法可以使用高倍率显微镜观察齿轮表面的微小磨损痕迹。
电化学检测方法可以通过测量齿轮表面的电化学特性来确定磨损程度。
磁粉检测方法可以利用磁性液体和磁粉检测仪,观察齿轮表面的裂纹和磨损情况。
综上所述,齿轮磨损的检测对于及早发现问题,及时采取维修措施至关重要。
不同的检测方法各有优劣,可以根据具体情况选择适合的方法进行检测。
通过有效的齿轮磨损检测,可以保证齿轮传动装置的正常运转,延长设备的使用寿命,提高生产效率。
第四种检测方法是使用纹影法。
纹影法是一种基于光学原理的非接触式检测方法,通过观察齿轮表面上产生的纹影图案来识别齿轮的磨损程度。
齿轮齿面fft检测原理

齿轮齿面fft检测原理
齿轮齿面FFT检测原理涉及到傅立叶变换和齿轮齿面的表面缺陷检测。
傅立叶变换是一种信号处理技术,它可以将时域信号转换为频域信号,从而揭示出信号中的频率成分。
在齿轮齿面FFT检测中,傅立叶变换被用来分析齿轮齿面振动信号,以便检测表面缺陷和其他问题。
首先,齿轮齿面振动信号被采集并记录下来。
这些信号通常包含了齿轮齿面的振动频率信息,而表面缺陷或故障会导致振动信号发生变化。
接下来,这些振动信号被输入到计算机或专用的FFT分析仪器中进行傅立叶变换。
傅立叶变换将时域的振动信号转换为频域的频谱图,其中包含了信号中各个频率成分的振幅和相位信息。
通过分析这些频谱图,可以识别出齿轮齿面上的不同频率成分,从而检测出表面缺陷产生的频率成分的变化。
在齿轮齿面FFT检测中,工程师可以通过比较正常齿轮和有缺陷齿轮的频谱图来识别出任何异常的频率成分,从而判断齿轮表面是否存在缺陷。
此外,还可以利用傅立叶变换来分析振动信号的幅
值和相位信息,以更全面地评估齿轮齿面的健康状况。
总的来说,齿轮齿面FFT检测原理基于傅立叶变换技术,通过分析齿轮齿面振动信号的频谱图来检测表面缺陷和其他问题,为齿轮设备的健康状态提供重要的信息。
齿轮检测报告

齿轮检测报告一、背景介绍齿轮是机械传动系统中不可或缺的部件,而齿轮的质量直接影响机械传动系统的性能。
由于齿轮制造和装配的复杂性,齿轮检测变得尤为重要,因为它可以为齿轮制造和装配过程提供质量保证。
二、齿轮检测的目的齿轮检测的主要目的是检查齿轮的几何特征,如齿宽、齿高、分度圆直径、齿距等,并确保这些几何特征符合规定的技术标准。
此外,齿轮检测还可以检测齿轮的磨损情况,并为机械传动系统的维护和修理提供支持。
三、齿轮检测的方法常见的齿轮检测方法包括齿轮外形检测、齿轮硬度检测、齿轮精度检测等。
其中,齿轮外形检测通常使用投影仪或三坐标测量仪进行,通过对齿轮表面进行光学扫描等处理,得到齿轮的实际几何形状。
齿轮硬度检测是用来测量齿轮的硬度和韧度,通常使用硬度计或冲击试验机等设备。
齿轮精度检测主要是用来检测齿轮的形位误差和传动误差,通常使用齿轮检测仪器和设备完成。
四、齿轮检测的标准齿轮的检测标准通常是由国际和国家标准制定的,其中,卡氏、ISO和AGMA是齿轮制造和检测领域最常见的标准和规范。
这些标准通过将齿轮的几何特征和质量级别分类,可以确保齿轮符合设计要求,并提供对齿轮质量的可靠保证。
五、齿轮检测报告的重要性齿轮检测报告是检测过程中记录的数据和结果的综合表述。
它提供了齿轮几何特征和质量级别的详细描述,并且可以为齿轮装配和维护过程提供重要参考。
而且,齿轮检测报告通常是齿轮质量问题的法律证明,在法律纠纷中具有重要作用。
六、齿轮检测报告的内容齿轮检测报告的内容通常包括齿轮外观和尺寸测试结果;齿轮硬度测试结果;齿轮精度测试结果;以及其他特殊测试结果等。
其中,齿轮外观和尺寸测试结果通常包括齿轮的几何特征和质量级别。
齿轮硬度测试结果包括齿轮的硬度和韧度等,而齿轮精度测试结果则包括齿轮的形位误差和传动误差等。
此外,齿轮检测报告还应包括齿轮的制造和装配过程,以及任何其他相关信息。
七、结论齿轮检测是机械传动系统中不可或缺的部分。
齿轮的质量直接关系到机械传动系统的性能和寿命。
齿轮的振动测量与简易诊断1齿轮的振动测量

选择
根据实际需求和条件选择合适的测量方法,如精度要求高、 条件允许可选择直接测量法;仅需大致了解振动状态可选择 间接测量法;特殊环境下可选择非接触测量法。
03
齿轮振动测量设备与工具
振动传感器
振动传感器是用于测量齿 轮振动的主要设备,它能 够将机械振动转换为电信 号,以便进一步处理和分 析。
常见的振动传感器类型包 括电涡流式、压电式和电 容式等,每种类型都有其 特定的适用范围和优缺点 。
断齿
振动信号中会出现频率成 分单一、幅值较大的冲击 信号。
齿隙过大
振动信号中会出现频率较 低、幅值较大的周期性信 号。
弯曲或扭转变形
振动信号中会出现频率和 幅值均有所变化的非周期 性信号。
简易诊断技术的优缺点
优点
操作简便、成本低廉、实时性强。
缺点
精度较低、可靠性有待提高、对操作人员经验要求较高。
06
提高生产效率
通过振动测量,可以优化 齿轮的设计和制造过程, 提高齿轮的效率和寿命,
从而提高生产效率。
振动测量技术的发展历程
起步阶段
早期的振动测量技术主要依赖于模拟信号处理和人工分析 ,测量精度和效率较低。
发展阶段
随着数字技术和计算机技术的不断发展,振动测量技术逐 渐实现了数字化和自动化,提高了测量精度和效率。
齿轮振动测量与诊断案例分析
案例一:齿轮箱振动异常的诊断
总结词
通过振动测量技术,发现齿轮箱振动异常,分析原因并采取相应措施。
详细描述
齿轮箱在运行过程中出现异常振动,通过振动测量仪器检测到振动幅值和频率异 常。经过分析,发现齿轮啮合不良、轴承损坏等原因导致振动异常。采取更换轴 承、调整齿轮间隙等措施后,振动问题得到解决。
齿轮的硬度检测方法
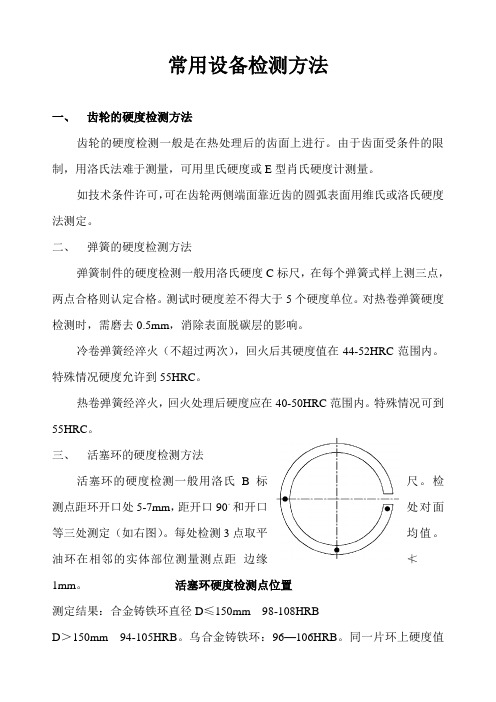
常用设备检测方法一、齿轮的硬度检测方法齿轮的硬度检测一般是在热处理后的齿面上进行。
由于齿面受条件的限制,用洛氏法难于测量,可用里氏硬度或E型肖氏硬度计测量。
如技术条件许可,可在齿轮两侧端面靠近齿的圆弧表面用维氏或洛氏硬度法测定。
二、弹簧的硬度检测方法弹簧制件的硬度检测一般用洛氏硬度C标尺,在每个弹簧式样上测三点,两点合格则认定合格。
测试时硬度差不得大于5个硬度单位。
对热卷弹簧硬度检测时,需磨去0.5mm,消除表面脱碳层的影响。
冷卷弹簧经淬火(不超过两次),回火后其硬度值在44-52HRC范围内。
特殊情况硬度允许到55HRC。
热卷弹簧经淬火,回火处理后硬度应在40-50HRC范围内。
特殊情况可到55HRC。
三、活塞环的硬度检测方法活塞环的硬度检测一般用洛氏B标尺。
检测点距环开口处5-7mm,距开口90。
和开口处对面等三处测定(如右图)。
每处检测3点取平均值。
油环在相邻的实体部位测量测点距边缘≮1mm。
活塞环硬度检测点位置测定结果:合金铸铁环直径D≤150mm 98-108HRBD>150mm 94-105HRB。
乌合金铸铁环:96—106HRB。
同一片环上硬度值差≯3 HRB。
四、焊接接头的硬度检测方法焊接接头及堆焊金属的硬度实验GB2654-89规定:焊接件硬度可用布氏、洛氏、维氏硬度试验方法检测。
试样检测面与支承面应经加工磨平。
厚度小于3mm的焊接接头允许在其表面测定硬度。
测定位置按下图焊接件硬度的测定位置标线进行。
测试时应注意避开焊接缺陷处。
焊接件硬度的测定位置标线五、金属覆盖层检测方法金属覆盖层主要有电沉积层,自催化气度层、喷涂层(包括爆炸喷涂和等离子喷涂层)以及铝材阳极氧化腹膜层等。
1、检测方法覆盖层硬度检测通常是应用显微和小负荷维氏硬度检测方法。
压头除维氏压头外,有时还应选用努普氏压头。
2、检测技术要求检测力大小应慎重选用,因为覆盖层一般都比较薄,如果检测力过大硬度值会受基体材料硬度的影响;如果检测力选用过小,容易引入较大误差,都会影响检测的准确性。
齿轮精度与检测技术手册

齿轮精度与检测技术手册
齿轮精度与检测技术手册
一、齿轮精度的定义
齿轮精度是指齿轮副在正常工作条件下能够符合预定的性能指标。
这
些性能指标包括噪声、振动、传动误差等等。
二、齿轮精度的影响因素
1.加工设备的精度
2.切削工具的质量
3.刀具的刃磨装置和磨削工艺
4.加工工艺参数的控制
三、齿轮精度的分类
1.精密齿轮:一般要求传动误差小于等于1′~2′,噪声级数不高于6级。
2.高精密齿轮:一般要求传动误差小于等于0.5′,噪声级数不高于5级。
3.超精密齿轮:一般要求传动误差小于等于0.3′,噪声级数不高于4级。
四、齿轮的检测方法
1.齿啮度测量法
2.重块法
3.网格法
4.光学测量法
5.声学测量法
五、齿轮的检测标准
1. JB/T5000-2007《齿轮检测规范》
2. GB/T10095-2008《齿轮用数字显示传动误差仪》
3. GB/T10096-2008《齿轮用数字显示噪声仪》
六、齿轮的质量控制
1.加工工艺的控制
2.检测方式的规范
3.配套检测设备的完善
4.数据分析和处理的及时性
以上是齿轮精度与检测技术手册的内容,希望对你有所帮助。
齿轮磨损检测方法
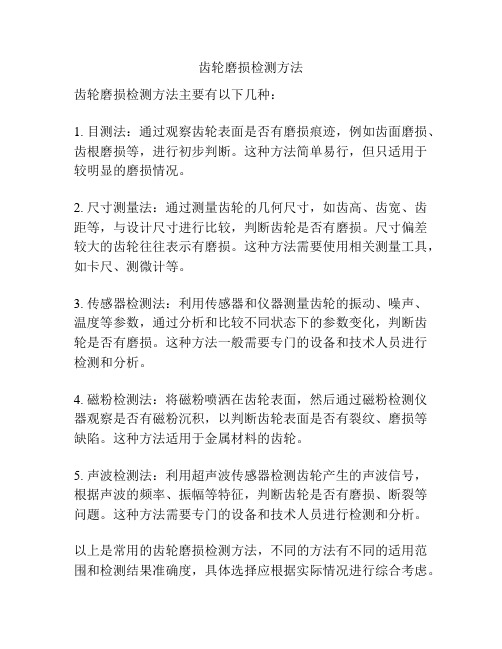
齿轮磨损检测方法
齿轮磨损检测方法主要有以下几种:
1. 目测法:通过观察齿轮表面是否有磨损痕迹,例如齿面磨损、齿根磨损等,进行初步判断。
这种方法简单易行,但只适用于较明显的磨损情况。
2. 尺寸测量法:通过测量齿轮的几何尺寸,如齿高、齿宽、齿距等,与设计尺寸进行比较,判断齿轮是否有磨损。
尺寸偏差较大的齿轮往往表示有磨损。
这种方法需要使用相关测量工具,如卡尺、测微计等。
3. 传感器检测法:利用传感器和仪器测量齿轮的振动、噪声、温度等参数,通过分析和比较不同状态下的参数变化,判断齿轮是否有磨损。
这种方法一般需要专门的设备和技术人员进行检测和分析。
4. 磁粉检测法:将磁粉喷洒在齿轮表面,然后通过磁粉检测仪器观察是否有磁粉沉积,以判断齿轮表面是否有裂纹、磨损等缺陷。
这种方法适用于金属材料的齿轮。
5. 声波检测法:利用超声波传感器检测齿轮产生的声波信号,根据声波的频率、振幅等特征,判断齿轮是否有磨损、断裂等问题。
这种方法需要专门的设备和技术人员进行检测和分析。
以上是常用的齿轮磨损检测方法,不同的方法有不同的适用范围和检测结果准确度,具体选择应根据实际情况进行综合考虑。
齿轮测量方法范文

齿轮测量方法范文齿轮是传动机构中常见的一种零件,齿轮的形状和精度对传动系统的性能和寿命有重要影响。
因此齿轮的测量方法是非常重要的,下面将介绍一些常见的齿轮测量方法。
1.外径测量法齿轮的外径是最常见的尺寸要求之一,可以使用千分尺或者游标卡尺等传统测量工具来测量。
2.齿宽测量法齿宽是齿轮的另一个重要尺寸,可以使用游标卡尺或者外径千分尺来测量。
同时还可以使用齿宽测量仪等专用设备来进行更精确的测量。
3.齿顶高测量法齿顶高是齿轮齿形的一个重要参数,可以使用齿顶高测量仪来进行测量。
齿顶高测量仪是一种具有精确导引机构的测量设备,可以保证测量的准确性。
4.齿根高测量法齿根高也是齿轮齿形的一个重要参数,可以使用齿根高测量仪来进行测量。
齿根高测量仪与齿顶高测量仪原理类似,也具有精确导引机构,可以保证测量的准确性。
5.齿距测量法齿轮的齿距也是一个重要参数,可以使用齿距测量仪来进行测量。
齿距测量仪是一种精密的测量设备,可以直接测量出齿轮齿距的大小。
6.模数测量法模数是齿轮的设计参数之一,可以使用模数测量仪来进行测量。
模数测量仪是一种专用的测量设备,可以测量出齿轮的模数大小。
7.齿轮角度测量法齿轮的角度也是一个重要的测量参数,可以使用角度测量仪来进行测量。
角度测量仪可以测量出齿轮的齿轮片角、压力角等角度参数。
需要注意的是,在进行齿轮测量时,应尽量减小人为误差的影响。
可以通过选择合适的测量工具、合理安装工件以及使用专用测量设备等方式来提高测量的准确性。
此外,随着科技的进步,现代化的测量技术也被广泛应用于齿轮测量中。
例如,光电测量技术、激光测量技术等可以提高测量的精度和效率,为齿轮制造提供更加可靠的测量结果。
综上所述,齿轮的测量方法包括外径测量法、齿宽测量法、齿顶高测量法、齿根高测量法、齿距测量法、模数测量法和齿轮角度测量法等。
不同的测量方法适用于不同的齿轮尺寸和形状,选择适合的测量方法可以提高测量的准确性和效率。
同时,现代化的测量技术也为齿轮测量提供了更多的选择和可能性。
- 1、下载文档前请自行甄别文档内容的完整性,平台不提供额外的编辑、内容补充、找答案等附加服务。
- 2、"仅部分预览"的文档,不可在线预览部分如存在完整性等问题,可反馈申请退款(可完整预览的文档不适用该条件!)。
- 3、如文档侵犯您的权益,请联系客服反馈,我们会尽快为您处理(人工客服工作时间:9:00-18:30)。
公法线平均长度偏差是指在齿轮一周内公法线实际长度平均值与公称值之 差。在生产中普遍采用此偏差的测量作为齿轮副侧间隙的评定指标。
齿距偏差 单个齿距偏差是指在端平面上,在分度圆上,实际齿距与理论齿距之差。它是评 定齿轮几何精度的基本项目。
齿距累积偏差:任意k个齿距的实际弧长与理论弧长的代数差
沿齿轮圆周上同侧齿面间距离作比较测量
2)工件安装误差,造成工件和夹具的端面跳动,直接影响齿向误差。
3) 齿坯加工精度低,主要指齿坯内孔和定位端面的加工精度低。 4)滚切斜齿轮时,走刀丝杠间隙大,走刀窜动,齿面波纹大,从而产生齿向误差 。 5)刀具误差和刀具安装误差,也不同程度地影响齿轮的齿向误差。 6)热处理方面,斜齿轮经渗碳淬火后,其螺旋角β会变小,齿向精度一般会降低。
运动精度 运动平稳性精度 接触精度 齿侧间隙
1.齿轮传动的精度等级及其选择 (1)、齿轮的精度要求(GB10095-88) ① 运动的的准确性(第I公差组) :分齿不均(误差)。 ② 传动的平稳性(第II公差组) :渐开线齿形存在误差。 ③ 载荷分布的均匀性 (第III公差组) 。 (2)齿轮的精度等级:GB10095-88对齿轮精度规定12个等级。 1~2:远景级 3~5:高级精度 6~8:中级精度 9~12:低级精度
(1)齿形轮廓线:渐开线、摆线、圆弧线等。 1.直齿圆柱齿轮的主要参数及尺寸计算 (1)模数m ①分度圆:齿厚e与齿间相等的圆,d ②分度圆周节P:在分度圆上相邻两齿对应点的弧长。 ③由于πd=Pz,令m=P/π,可得d=mz ④模数m的数值已标准化,共50种。
渐开线直齿圆柱齿轮的基础知识
(1) 发生线沿基圆滚过的长度, 等于基圆上被滚过的圆弧长度 (2) 渐开线上任意点的法线恒与 其基圆相切。 (3) 渐开线的形状取决于基圆的 大小。基圆半径越大,其渐开线 的曲率半径也越大。当基圆半径 为无穷大时,其渐开线就变成一 条直线。 (4) 基圆内无渐开线。 (5) 同一个基圆上的任意两条渐 开线,沿公法线方向的对应点之 间的距离处处相等。
第一章 绪论
齿轮测量技术归纳为四种类型: •齿轮单项几何形状误差测量技术 •齿轮综合误差测量技术
•齿轮整体误差测量技术
•齿轮在机测量技术。
齿形加工
齿轮类型 直齿轮、斜齿轮、人字齿轮 螺旋齿轮、蜗轮与蜗杆 内齿轮 齿轮齿条 直齿锥齿轮 应用 平行轴间传动 垂直交错轴间传动 平行轴间同向传动 旋转运动和直线移动的转换 相交轴间传动
径向跳动误差的测量
(1) 测头对误差测量精度的影响 (2) 芯轴径向跳动的影响 (3)偏心影响
齿轮齿向(螺旋线)误差
齿向误差是指在分度圆柱面上,齿宽有效部分范围内,包容实际齿向线且距离为最 小的两条设计齿向线之间的距离。 齿向误差 f 可分为螺旋线波度误差 f f 和螺旋线倾斜误差 f H
齿轮齿形(渐开线)误差 齿形误差定义:在端截面上,齿形工作部分内(齿顶倒棱部分除外),包容实际齿形且距 离为最小的两条设计齿形间的法向距离。
由于齿轮的齿面偏离了正确的渐开线,使齿轮传动中瞬时传动比不稳定,影响 齿轮的工作平稳性。
影响齿轮传动工作平稳性的主要因 素是齿轮的齿形误差和基节偏差。
齿形误差会引起每对齿轮啮合过程 中传动比的瞬时变化; 基节偏差会引起一对齿过渡到另一 对齿啮合时传动比的突变。齿轮传 动由于传动比瞬时变化和突变而产 生噪声和振动,从而影响工作平稳 性精度。
齿形误差测量原理
齿轮转角 和齿面在法线方向上的位移 X 满足以下关系式
X rb
齿形误差可分为齿形形状误差和齿形倾斜误差
齿形误差产生的原因
主要是滚刀刃磨精度和安装精度以及分齿运动的回转精度
(1)保证滚刀刃磨精度,根据对超差原因的分析,滚刀本身的精度对滚齿后的 齿形有很大影响,因此要提高齿形加工精度,必须正确选择滚刀精度等级。更重 要的是在滚刀用钝后刃磨精度要保证合乎要求。 (2) 保证滚刀安装和调整精度在保证了滚刀刃磨精度后,如果在滚刀的安装与调 整时不注意,也往往达不到所需要求的齿形精度。 (3)分齿运动的回转精度分齿运动的回转精度对于新滚齿机问题不大,如果机 床长期使用后有磨损或损伤,就应该进行检修。
齿轮基节不等将使齿轮在一转中多次重复出现撞击、加速、降速,影响运动的平稳 性。主、从动齿轮的实际基节差值越大,引起的振动和噪声也就越大。
影响齿轮传动工作平稳性的主要因素是齿轮的齿形误差和基节偏差。 齿形误差会引起每对齿轮啮合过程中传动比的瞬时变化; 基节偏差会引起一对齿过渡到另一对齿啮合时传动比的突变。齿轮传动由于传动 比瞬时变化和突变而产生噪声和振动,从而影响工作平稳性精度。 齿轮的基节极限偏差主要受滚刀基节偏差的影响。 为减少基节偏差,滚刀制造时应严格控制轴向齿距及齿形角误差,同时对影响 齿形角误差和轴向齿距误差的刀齿前刀面的非径向性误差也要加以控制。
2、齿轮间隙的规定 齿侧间隙:由工作条件决定,与齿轮精度无关,控制齿厚偏差或公法线平均长度偏 差来限制 14个齿厚偏差:C、D、E、F、G、H、J、K、L、M、N、P、R、S 二、齿轮精度的选择 一般情况下三个公差组应选用相同的精度。 机床主轴齿轮:第II公差组高 测量仪器和分度机构的齿轮:第I公差组高 起重机械及矿山机械的齿轮:第III公差组高 6-5-5-F LGB10095-88 6:第I公差组的精度等级 5:第II公差组的精度等级 5:第III公差组的精度等级 F:齿厚上偏差 L:齿厚下偏差
2.滚齿 IT8~IT7,Ra:3.2~1.6μm。 (1)滚齿机和齿轮滚刀 齿轮滚刀:相当于一个右旋螺旋齿轮。
(2)滚齿原理与滚齿运动 滚齿原理:展成法。 滚齿运动: ①:主运动:滚刀旋转。
n工 K ②:分齿运动: n刀 Z
③;垂直进给运动:切出整个齿宽。 ④:径向进给运动:切出整个齿深。 (3)滚齿工作范围 ①滚切直齿圆柱齿轮
三、铣齿
成形法:用与被切齿轮齿槽法向截面形状相符的成形刀具切出齿形。 展成法(包络法、范成法):利用齿轮刀具与被切齿轮的啮合运动, 在专用齿轮加工机床上切出齿形的一种方法。 1.铣削直齿圆柱齿轮 (1)原理:成形法,IT9,Ra:6.3~3.2μm。 M≤20,盘状模数铣刀;M>20,指状模数铣刀。
3.铣齿的工艺特点和应用 (1)生产成本低。 (2)加工精度低。 (3)生产率低。
四、插齿和滚齿
IT8~IT7,Ra:3.2~1.6μm。 1.插齿 (1)插齿机和插齿刀 插齿刀:相当于圆柱齿轮。 (2)插齿原理与插齿运动 插齿原理:展成法。 插齿加工相当于一对无啮合间隙的圆柱齿轮传动。
插齿运动 ① 主运动:插齿刀上下往复运动 ② 分齿运动:强制插齿刀与齿轮坯之 间保持一对齿轮的啮合关系 ③ 径向进给运动:切出齿深。 ④ 圆周进给运动:插齿刀的旋转运动。 ⑤ 让刀运动:防止擦伤。 (3)齿轮坯的安装 ①内孔和端面定位:大批量生产 ②外圆和端面定位:单件小批生产 (4)插齿工作范围 内外直齿圆柱齿轮、间距小的双联和多联齿轮、内外螺旋齿轮
②滚切螺旋齿圆柱齿轮
③滚切蜗轮
3、滚齿与插齿比较 (1)加工原理相同:展成法 (2)加工精度和齿面粗糙度基本相同:精度为8~7级,Ra1.6μm (3)插齿的分齿精度略低于滚齿, 滚齿的齿形精度略低于插齿。 (4)插齿的齿面粗糙度略优于滚齿。 (5)插齿的生产率低于滚齿。 (6)加工范围不同。 插齿:内齿轮和小间隙多联齿轮 滚齿:螺旋齿轮、蜗轮和轴向齿轮较大的齿轮轴 (7)生产类型相同
(2)成形铣刀 同一模数的齿轮铣刀,一般制作8把或15把,表7.1。 表3-4 盘状齿轮铣刀刀号及其加工范围
刀 号 1 2 3 4 5 6 7 8
加工齿 数范围
齿 形
12~13 14~16
17~ 20
21~ 25
26~ 34
35~ 54
55~ 134
135以上及 齿条
2.铣削螺旋齿圆柱齿轮 (1)螺旋齿轮的主要参数 法面模数mn和端面模数mt、法面压力角αn (2)铣削螺旋齿轮铣刀的选择:按法面模数mn和当量齿数zd选择 (3)铣削螺旋齿轮的方法 铣削螺旋齿轮可看作铣削一般螺旋槽和铣削直齿轮两种方法的综合 运用。在万能卧式铣床上进行。
公法线长度变动反映齿轮传递运动的准确性,公法线长度偏差反映了齿侧间隙,都 是齿轮精度检测项目中2个重要指标。
公法线长度变动是指在齿轮一转范围内,实际公法线长度最大值与最小值之差。 其实质是齿廓在圆周上的位置偏差.也是以齿轮一转为周期的转角误差。它反映 齿轮的运动角度,是因机床分度蜗轮传动偏心所造成的切向误差,影响齿轮传动 的准确性。
7)机床、刀具和工件的综合误差对齿向误差的影响。
齿向误差的消除方法
1)重新检查这台机床的精度,必要时拆卸刀具,检查导轨滑动面对母圆的不平行 度,如超差要修刮,并配刮镶条,以创造良好的导向精度条件。 2)提高齿坯的精度,夹紧时的夹紧点要分布多一些,夹紧力要适度,夹紧后检查 齿圈的端面跳动,保证在允许的范围内。 3)正确控制走刀丝杠间隙,防止走刀窜动。 4)提高刀具的安装角精度,保证刀具的精度。因渗碳淬火后,斜齿轮螺旋角有缩 小的趋势,所以刀具安装角增大一点,这样有助于减少斜齿轮渗碳淬火后齿向精 度的下降。 5)对于综合误差的影响,可以采用改变切削速度,或改变工件安装方式加以解决。 6)最好增加轻跑合工序。轻跑合就是将加工过的齿轮装机后,在各个速度档进 行跑合,由很小的载荷逐渐地加入到接近实际工作载荷,这样可修正齿向误差提 高斜齿轮的接触精度。
4 机床的周期误差
公法线平均偏差 模数 X 齿数 = 分度圆直径 . 在二齿轮啮合时,理论上把分度圆直径相切处称节圆. 在该处单齿的齿厚度称弦齿厚.是检测齿轮精度方法之一.但是在加工过程中由于各 种误差累积,单齿检测精度不能保证,而同时采用在节圆处检测多齿间距,称公法线 测量工具的两K脚卡住所取跨测齿数 的相对齿廓上下滑动,既不卡住,又 无间隙,大约在齿廓中点处可测得有 一最大值,即为公法线长度。
插齿机